Makita HP331D Operating instructions

Model No.
Description
PRODUCT
P 1/ 18
HP331D
Cordless Hammer Driver Drill
CONCEPT AND MAIN APPLICATIONS
Specification
Standard equipment
Optional accessories
TECHNICAL INFORMATION
Battery BL1015*6
Battery BL1020B*6
Battery BL1040B*6
Battery BL1016*1
Battery BL1021B*1
Battery BL1041B*1
Charger DC10SA*6
Charger DC10WC*6
Charger DC10SB*1
Charger DC10WD*1
Driver bits
Socket bits
Belt clip
Bit holder
Holster
We are going to launch a new 10.8V (12V max*1) platform. The new platform
has been developed based on the current one, and features newly developed
slide Li-ion battery instead of stick one; use of the new battery provides stable contact
between battery and tool and the same ergonomic handle as LXT series models
to obtain more satisfaction from professional users.
Model HP331D is one of the first new 10.8V (12V max*1) platform models
to launch.
The main features and benefits are:
• Increased motor power for higher application speed and max tightening torque
• Best possible ergonomic handle for drilling/driving applications
Dimensions: mm (")
Width (W)
Height (H)
Length (L)
66 (2-5/8)
201 (7-7/8)
209 (8-1/4)*2
228 (9)*3
Battery
Specification Model
Energy capacity: Wh
Voltage: V
Capacity: Ah
Weight according to
EPTA-Procedure 01/2003: kg (lbs)
Cell Li-ion
Charging time: min 50, 70, 130 with DC10WC
22, 30, 60 with DC10SA
10.8
HP331D
1.1 (2.5)*2
1.3 (2.9)*3
170Max output power: W
18 stages + drill mode
0.5 (4) - 3.5 (30)
Torque setting
1.5, 2.0, 4.0
No load speed:
min-ı= rpm
2nd (High)
1st (Low)
0-1,700
0-450
Impacts per minute:
min-ı= ipm
2nd (High)
1st (Low)
0-25,500
0-6,750
17, 22, 44
Battery*4
Charger*4
Battery cover*5
Belt clip
*4 Battery, charger and plastic carrying case are not supplied with “Z” model.
*5 Supplied with the same quantity of extra Battery.
Note: The standard equipment may vary by country or model variation.
*2 With BL1015/ BL1020B
*3 With BL1040B
Capacity of drill chuck: mm (") 0.8 (1/32) - 10 (3/8)
10 (3/8)
21 (13/16)Capacity: mm (")
Steel
Wood
Masonry 8 (5/16)
Clutch torque setting: N·m (in·lbs)
28 (250)
Yes
Yes (2-speed)
14 (130)
Max lock torque: N·m (in·lbs)
Max tightening
torque: N·m (in·lbs) Soft joint
Hard joint 30 (270)
Electric brake
Variable speed control
Mechanical speed control
Reversing switch
LED job light
Yes (by trigger)
Yes
Yes
L
H
W
Phillips bit 2-45 (for N-type areas) or 2-50 (for M-type areas)
Plastic carrying case*4
Type Slide
*6 For all countries except Asia, Central and South America, Australia and North America
*1 For Asia, Central and South America, Australia and North America
September 2015
OFFICIAL USE
for ASC & Sales Shop

October 2015
CORDLESS HAMMER DRIVER DRILL
HP331D
CORDLESS DRIVER DRILL
DF331D
CORDLESS DRIVER DRILL
DF031D
REPAIR MANUAL
2 / 18

October 2015
CONTENTS
1. Exploded diagram .................................................................................................................................................................. 4
About This Manual......................................................................................................................................................................... 7
2. Repair..................................................................................................................................................................................... 7
2.1. NECESSARY REPAIRING TOOLS ...................................................................................................................................... 7
2.2. DISASSEMBLY/ASSEMBLY .............................................................................................................................................. 8
2.2.1. DRILL CHUCK (Only for HP331D, DF331D) ............................................................................................................. 8
2.2.1.1. Disassembling ................................................................................................................................................ 8
2.2.1.2. Assembling................................................................................................................................................... 10
2.2.2. Gear ass’y and motor section .............................................................................................................................. 10
2.2.2.1. Disassembling .............................................................................................................................................. 10
2.2.2.2. Assembling................................................................................................................................................... 12
2.2.3. Bit installation portion of Gear ass'y.................................................................................................................... 13
2.2.3.1. Disassembling .............................................................................................................................................. 13
2.2.3.2. Assembling................................................................................................................................................... 14
2.2.4. Speed change lever ass’y ..................................................................................................................................... 14
2.2.4.1. Assembling................................................................................................................................................... 14
2.2.5. leaf spring ............................................................................................................................................................ 15
2.2.5.1. Assembling................................................................................................................................................... 15
3. Circuit diagram..................................................................................................................................................................... 16
3.1. Repair of LED circuit..................................................................................................................................................... 17
4. Wiring diagram .................................................................................................................................................................... 18
3 / 18

October 2015
1. EXPLODED DIAGRAM
Figure 1
4 / 18

October 2015
Figure 2
5 / 18

October 2015
Figure 3
6 / 18

October 2015
ABOUT THIS MANUAL
The number in the parenthesis () is the item number on the exploded diagram (Figure 1, Figure 2, Figure 3).
2. REPAIR
Repair the machine in accordance with “Instruction manual” or “Safety instructions”.
2.1. NECESSARY REPAIRING TOOLS
Code No. Description Use for
1R003 Retaining ring pliers ST-2N removing Ring spring 10
1R212-A Tip for retaining ring pliers use with 1R003 in order to remove/ assemble Ring spring 10
1R212-B Plate set (with screws)
1R231 1/4 " H ex. shank bit for M8 disassembling Drill chuck (10)
1R359 Chuck removing tool disassembling Drill chuck (10)
If it is impossible to remove as per the illustration in 3-2-1, refer
to Repair Tool List.
- Hex wrench 8 disassembling Drill chuck (10)
- Bit adapter disassembling Drill chuck (10)
7 / 18

October 2015
2.2. DISASSEMBLY/ASSEMBLY
2.2.1. DRILL CHUCK (ONLY FOR HP331D, DF331D)
2.2.1.1. DISASSEMBLING
1. Remove M6x22(-) Flat head screw by turning it clockwise
with Impact driver.
Note:
M6x22(-) Flat head screw: HP331D
M5x22(-) Pan head screw: DF331D
Stable operation is available if you tighten claws of Drill
chuck with a Round -bit in advance.
Figure 4
2. Set Speed change lever to Low speed mode designated
with 1.
Fix the shorter leg of Hex wrench 8 in the jaws of Drill
chuck.
In order not to break Spindle, be sure to put the three
circled portions of the tool on a workbench.
Hit the other end of Hex wrench 8 with Plastic hammer
to remove Drill chuck.
Figure 5
3. If it is difficult to remove, follow the steps below.
Set 1R231 to Bit adapter and fix it in Drill chuck.
Insert DTW450 into Bit adapter.
Hold the body tightly.
Push the upside of Switch to turn 1R231
counterclockwise.
or
Push the upside of Switch to remove Drill chuck.
Figure 6
Hex wrench 8
DTW450
1R231
Bit adapter
8 / 18

October 2015
Figure 7
4. Use 1R359 to remove Keyless drill chuck if it cannot be removed in the previous step.
Gear case
Washer 13
Pin 3.5 (x2)
Lock
cam
Pin 4 (x6)
Motor bracket
Pin 1.2 (x4)
Change lever
Steel ball 4 (x6)
Carrier complete
Spur gear 11 (x3)
Internal gear 34
Spur gear 14 complete
Pin 3 (x2)
Flat washer 11
Spur gear 15 (x3)
Internal gear 42
Spur gear 13
complete
Spur gear 12 (x4)
Internal gear 35
5. The component of Gear assembly is as follows.
6. Apply a small amount of Makita grease FA No. 2 if needed.
Lock
ring
9 / 18

October 2015
2.2.1.2. ASSEMBLING
1. Turn Drill chuck clockwise until it seats on the end of the
threaded portion of spindle.
2. Fix Hex wrench 8 as shown.
Note: L-shaped portion of Hex wrench 8 must be fixed
securely.
3. Housing R must be touched on the side surface of
workbench.
Note: Battery portion must not be touched.
4. Pull Switch trigger slowly with Drill mode/Speed change1/
Forward (clockwise) rotation until spindle is locked.
Note: Release the trigger of Switch just after Spindle is
locked. Do not keep on pulling the trigger for longer
than one second.
5. If you reuse the Screw removed from Drill chuck, apply
ThreeBond 1342 or Loctite 243 to the thread of the
Screws.
Note: M6x22(-) Flat head screw: HP331D
M5x22(-) Pan head screw: DF331D
Figure 8
2.2.2. GEAR ASS’Y AND MOTOR SECTION
2.2.2.1. DISASSEMBLING
It is required to remove Drill chuck when replacing Gear assembly.
1. Remove Housing R (2) by loosening 3x16 Tapping screw
(4) (x9).
Figure 9
(4)
(2)
10 / 18

October 2015
2. Remove Gear ass'y (11), Motor (12) and Speed change
lever (1) from Housing L (14) at a time.
Figure 10
3. Remove Speed change lever ass’y (1) from Gear ass'y
(11).
Note: Be careful not to lose Compression springs 4.
Figure 11
4. Set the speed change lever of Gear ass’y (11) to High
speed mode.
Turn DC Motor (12) counterclockwise to pull it out.
Figure 12
5. Remove Motor bracket by unscrewing two M3x6 Pan
head screws (13) when you replace DC Motor.
Figure 13
(14)
(1)
(11)
(12)
Remove
(1)
(11)
Compression spring 4
(11)
(12)
(13)
Motor
bracket
11 / 18

October 2015
2.2.2.2. ASSEMBLING
1. Set the Speed change lever ass’y of Gear ass’y (11) to High
speed mode.
2. Remove Motor bracket by turning Gear ass'y (11)
counterclockwise when you replace it.
Figure 14
Figure 15
3. Fix with two M3x6 Pan head screws (13) while facing Motor bracket's protrusion side to the Red mark side of +
terminal when replacing motors (12).
4. Set the Speed change lever of Gear ass’y (11) to High
speed mode.
5. Aligning the Speed change lever of Gear ass'y (11) with
Red mark (plus terminal) of DC motor (12), turn DC motor
(12) clockwise to assemble it.
Note:
If Gear ass'y (11) and DC Motor (12) cannot be assembled,
assemble them by turning Fan by hand.
Figure 16
Motor bracket
Red mark
(13)
(12)
(11)
(12)
Red mark
(plus
terminal)
Fan
Motor
bracket
(11)
12 / 18

October 2015
6. Fit the concave portion of F/R change lever (6) to the
projection of Switch (7).
Figure 17
2.2.3. BIT INSTALLATION PORTION OF GEAR ASS'Y
2.2.3.1. DISASSEMBLING
1. Remove Ring spring 10 while checking the following
points.
A) Press the top of Bit sleeve with thumb so as not to
pop out Compression spring 13.
B) Expand the end gap of Ring spring 10 with 1R003,
1R212-B and 1R212-A.
Figure 18
2. Bit holder section can be disassembled as shown in the
figure on the left:
Ring spring 10
Flat washer 11
Compression spring 13
Bit sleeve
Steel ball 3 (x2)
Figure 19
Projection of switch (7)
Concave portion of F/R
change lever (6)
1R212-A 1R212-B
1R003
Ring spring 10
Steel ball 3 (x2)
Bit sleeve
Compression
spring 13
Flat washer 11
Ring spring
10
13 / 18

October 2015
2.2.3.2. ASSEMBLING
Assemble by reversing the disassembly procedure.
2.2.4. SPEED CHANGE LEVER ASS’Y
2.2.4.1. ASSEMBLING
Assemble by reversing the disassembly procedure.
1. Assemble Compression spring 4 (x2) as drawn.
Note:
Hook one roll of the spring to the notches of Speed
change lever.
Figure 20
2. Fit Pin on the lever of Speed change lever into
Compression spring 4 while pushing Speed change lever
ass’y in the direction of the arrow.
Push Compression spring 4 with projection of Speed
Note:
Hook one roll of the spring to the notches of Speed
change lever.
Figure 21
3. Shift Speed change lever in the either direction.
Figure 22
Compression spring 4 (x2)
Projection of Speed
change lever
Pin on the lever
of Speed change
lever
Gear ass’y
Speed change lever
ass’y
Pin on the lever of
Speed change lever
Projection of
Speed change ever
14 / 18

October 2015
2.2.5. LEAF SPRING
2.2.5.1. ASSEMBLING
1. Assemble Leaf spring as shown.
Figure 23
(14)
Leaf spring
Face projection
inside.
15 / 18

October 2015
3. CIRCUIT DIAGRAM
Color index of lead wires' sheath
Black
Red
Blue
White
Yellow
Figure 22
16AWG
16AWG
Line filter
B
φ
10-20mm
(if used)
DC Motor
Red mark
Resistor
B-B+
M2
M1
Terminal
Line filter
A
φ
10-11mm
(if used)
T terminal
24
AWG, UL1685
AWG
16
AWG
22
16AWG
Straight receptacles
W
ith lock
(#
187, t=0.8)
LED
circuit
Flag receptacle
s
w/o lock
(#
187, t=0.5)
Flag receptacle
W
ith lock
(#
250, t=0.8)
Flag receptacle
W
ith lock
(#
187, t=0.8)
+
-
AWG: American wire gauge
16 / 18

October 2015
3.1. REPAIR OF LED CIRCUIT
Use Non-insulated connector and Polyolefin tube (inner diameter: ø4.0mm) as shown below.
When repairing, put terminals in the designated position shown in Figure 24. (Cut lead wires if necessary.)
Cut Lead wire in the position shown on the left.
Figure 24
Color index of lead wires' sheath
Black
Red
Figure 25
Cutting position of Red lead wire
(
The same surface as the root of Tab terminal)
Cutting position of Black lead wire
(
The end face of Polyolefin tube)
AWG: American wire gauge
LED circuit
Switch
Non-insulated
connector
Non-insulated
connector
Shrink of Polyolefin tube
Shrink of Polyolefin
tube
2mm or more
2mm or more
End face of
Non-insulated
connector
End face of
Polyolefin tube
End face of
Polyolefin tube
AWG24
AWG24
AWG24
AWG24
Resistor
17 / 18

October 2015
4. WIRING DIAGRAM
Figure 26
Assemble receptacles to Motor as drawn.
Motor connector portion
LED
Put LED lead wire between Boss and
Rib D, Rib B and Rib C.
Red mark
Connector
Do not put Receptacle
(with Black lead wire)
over Rib A.
Receptacle
(
with Black lead wire)
Bend motor terminal as
drawn.
Rib A
DC Motor
Line filter A (if used)
Terminal
Be careful not to put Lead wires on Rib E.
Rib E
Line filter B (if used)
Do not put Lead wires between these
Receptacles and Housing L.
Receptacle
Housing set
Switch
Side view of Switch
Pass Lead wire (Red)
between this receptacle
and Housing L
; under
the receptacle.
Put Line filter A (if used) in this space.
Rib B
Switch
Put LED lead wire in this Lead
holder.
Rib C
Boss
Do not pass Lead wire under Gear case.
Rib D
Gear ass’y
Non-insulated terminals protected by
Polyolefin tube (when repairing LED circuit)
Put Non-insulated terminals protected by
Polyolefin tube (when repairing LED circuit)
inside the dotted line.
18 / 18
Other manuals for HP331D
7
This manual suits for next models
2
Table of contents
Other Makita Drill manuals
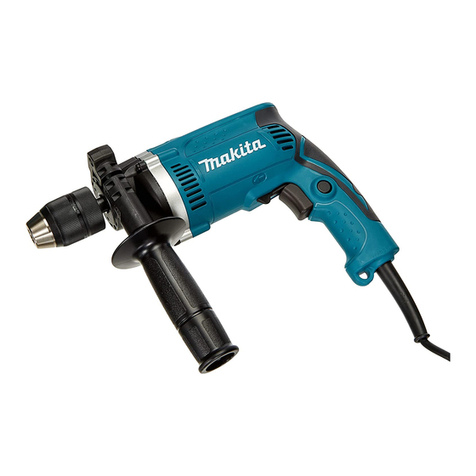
Makita
Makita HP1631KX3 User manual
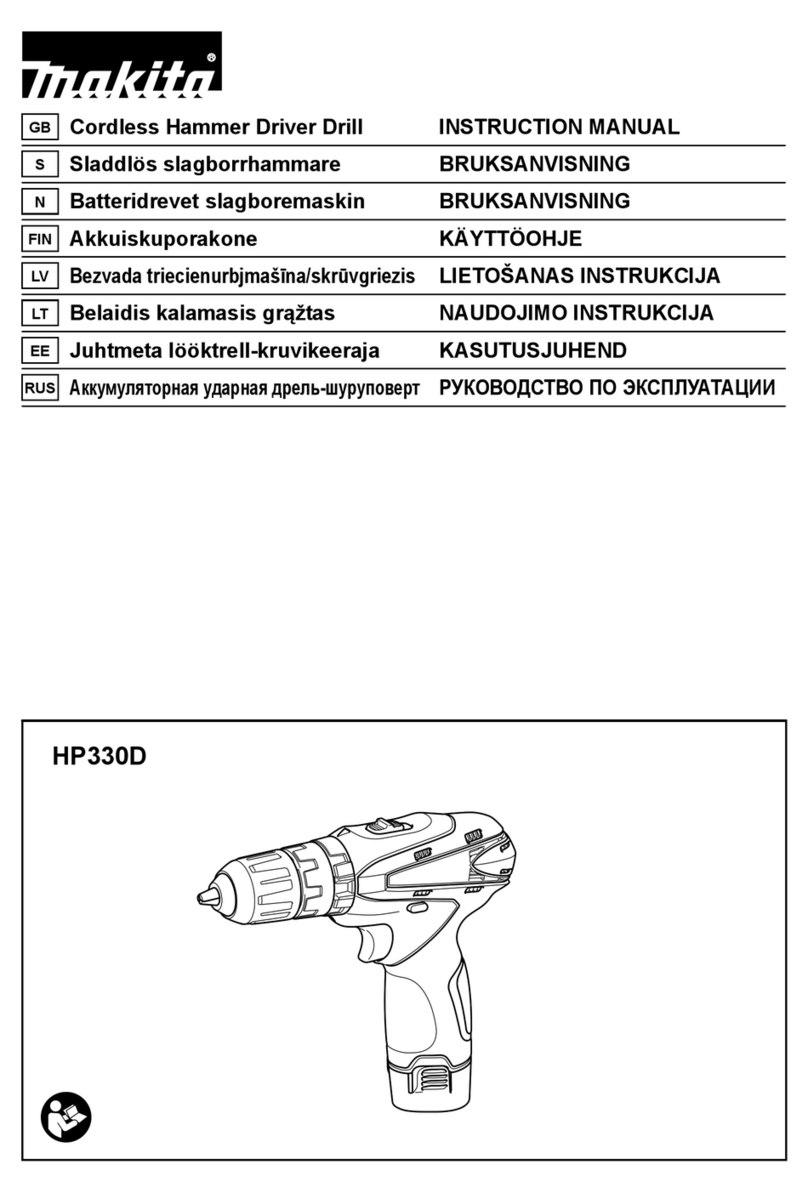
Makita
Makita HP330D User manual

Makita
Makita HP002G User manual
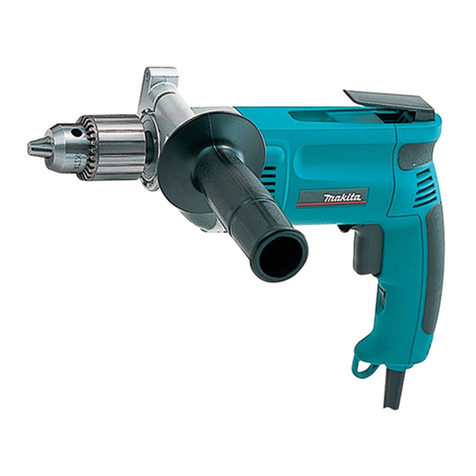
Makita
Makita DP3002 User manual

Makita
Makita DHP448 User manual

Makita
Makita DHP487YX2B User manual

Makita
Makita 6281D User manual
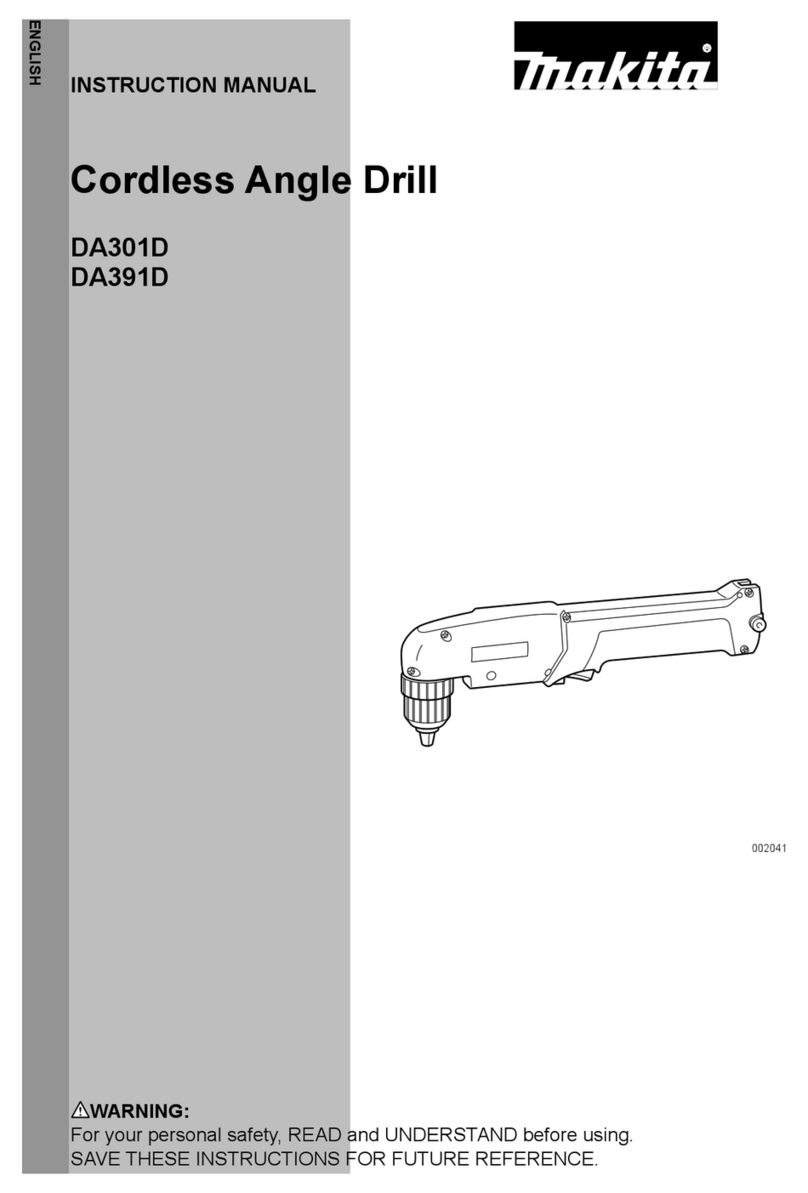
Makita
Makita DA301D User manual

Makita
Makita DHP481ZJ User manual
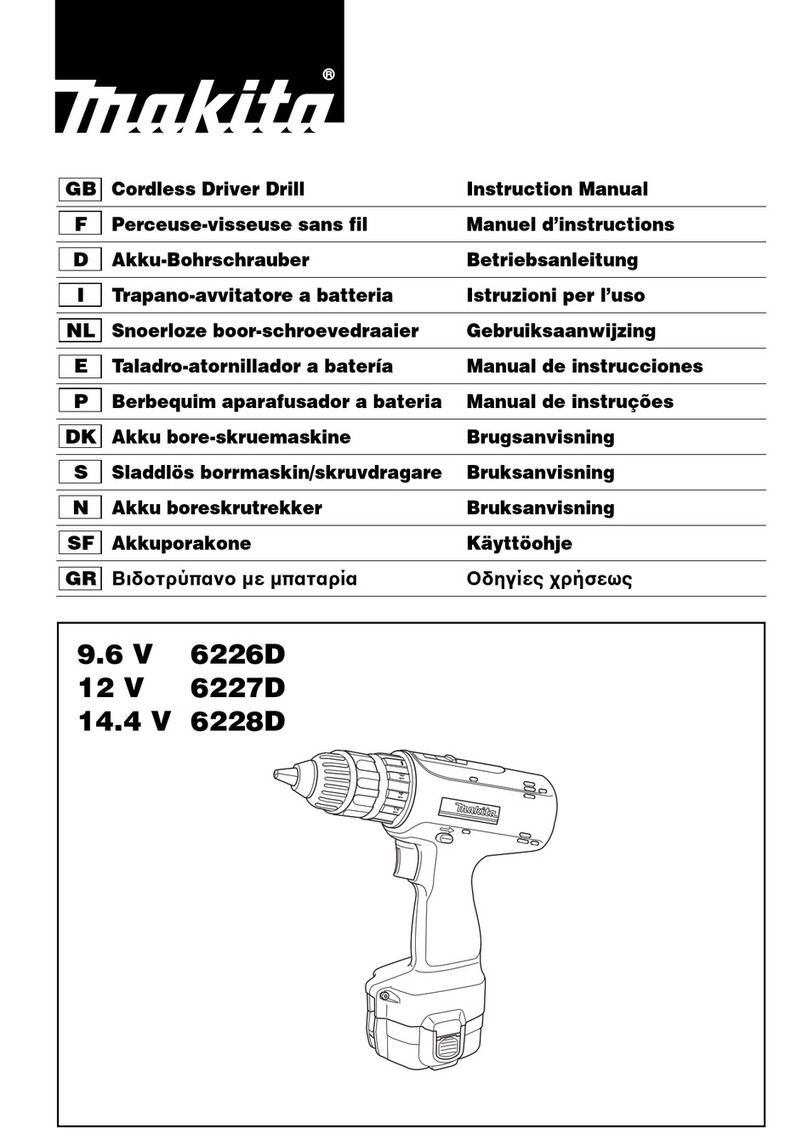
Makita
Makita 6227D User manual
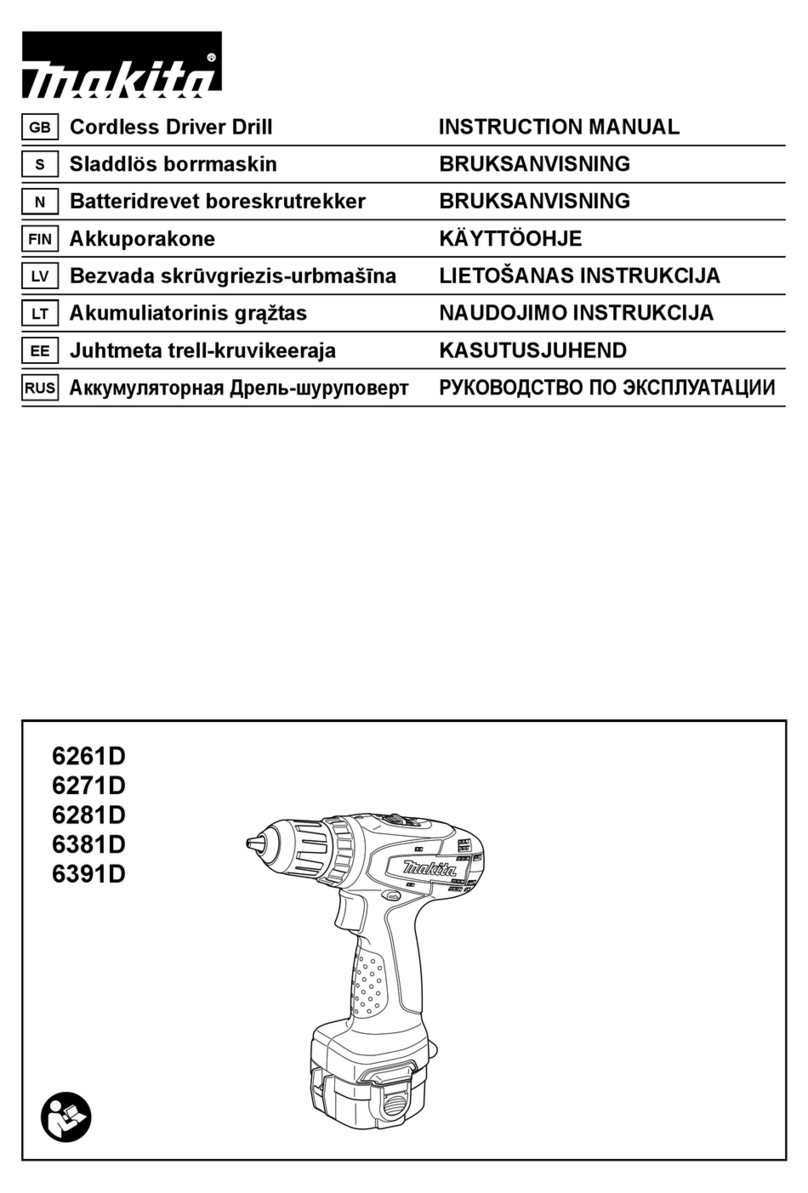
Makita
Makita 6261D User manual
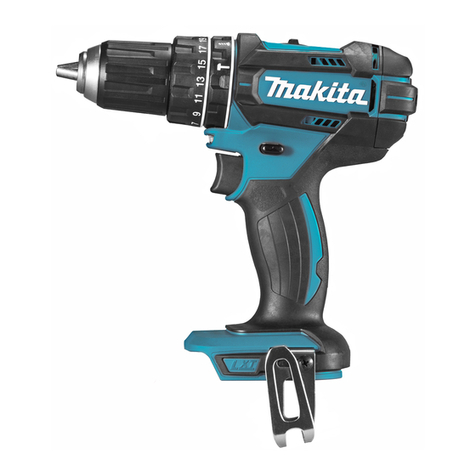
Makita
Makita DHP482ZJ User manual

Makita
Makita 6411 User manual
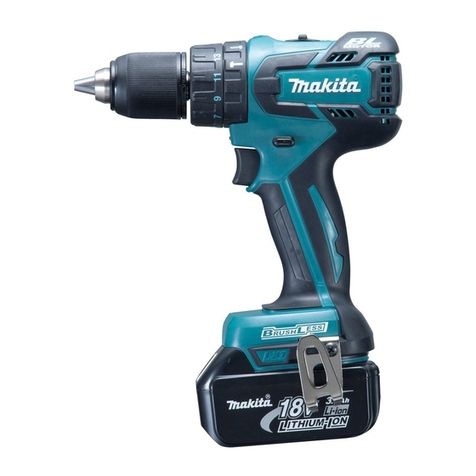
Makita
Makita BHP459ZJ User manual
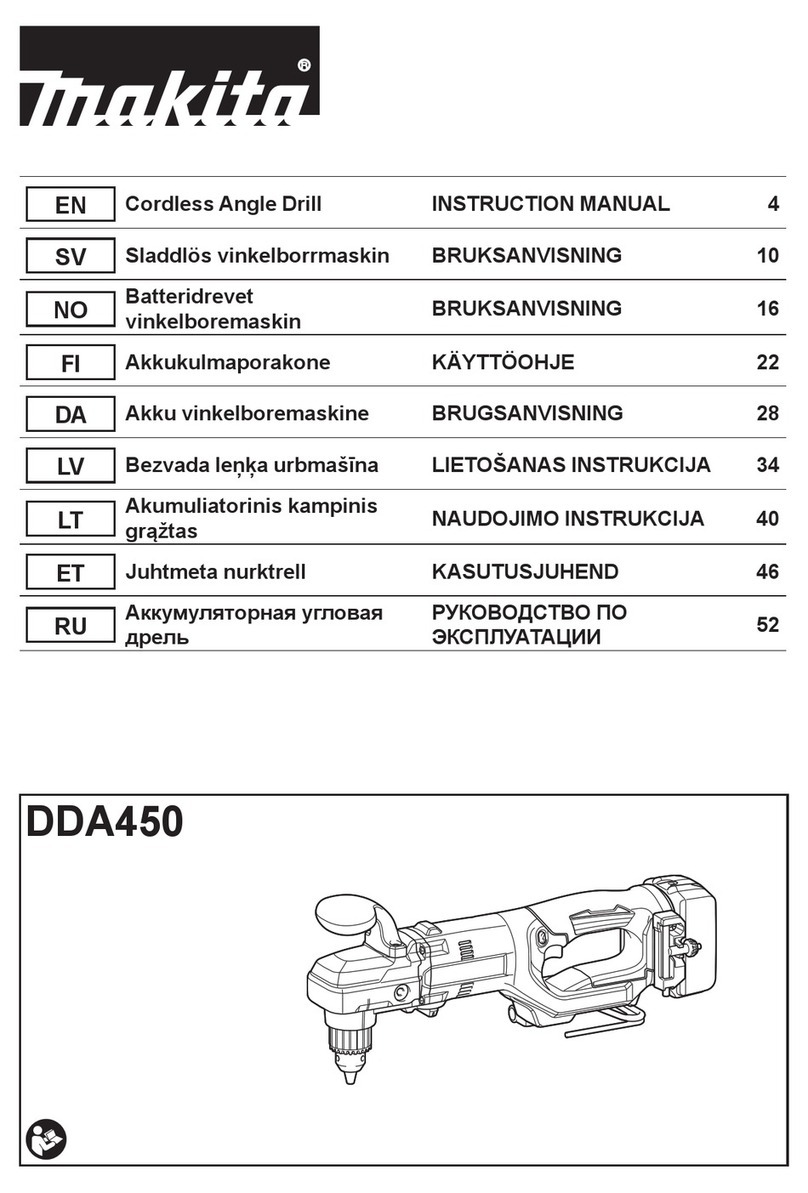
Makita
Makita DDA450 User manual
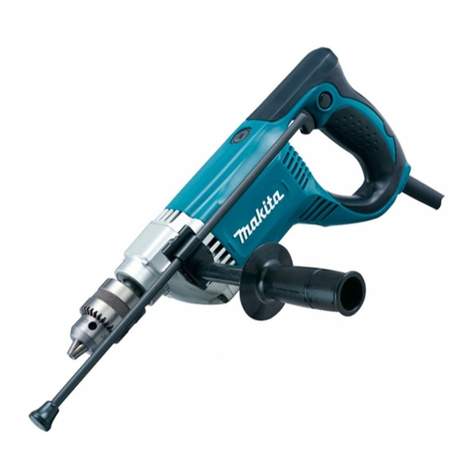
Makita
Makita 6305 User manual
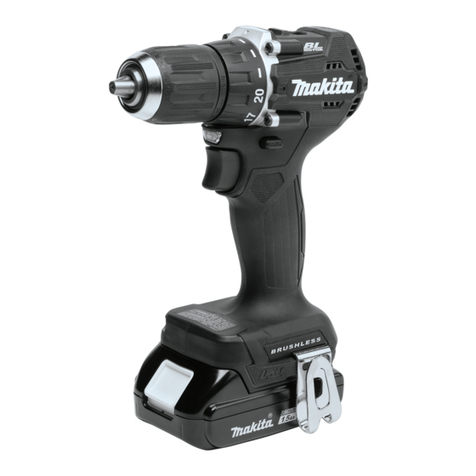
Makita
Makita XFD15 User manual
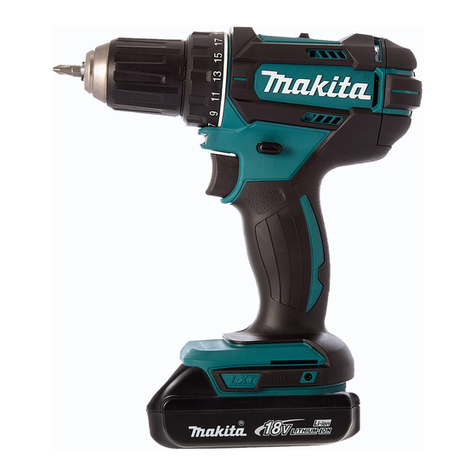
Makita
Makita DDF482 User manual

Makita
Makita HP2050 User manual

Makita
Makita DHR202 User manual