Makita Maktec MT92A Manual

PRODUCT
CONCEPT AND MAIN APPLICATIONS
P 1/ 9
Specification
Standard equipment
Dimensions: mm (")
Width (W)
Height (H)
Length (L)
MT92B
250 (9-7/8)
439 (17-1/4)
MT92A
200 (7-7/8)
141 (5-9/16)
Note: The standard equipment for the tool shown above may vary by country.
These maktec brand angle grinders MT92A and MT92B have been
designed for price competitive markets.
New maktec design is employed to eliminate white printing
and polygonal line from maktec logo/ elastomer from handle
for the cost effectiveness.
Optional accessories
No
Model No.
Description
MT92A, MT92B
Angle Grinders 180mm (7"), 230mm (9")
Lock nut wrench 35 ...................... 1
Grip 36 complete .......................... 1
L
H
W
240 50/609.6 2,200 1,700
220 50/6010.5 2,200 1,700 2,900
2,900
230 50/6010.0 2,200 1,700 2,900
Continuous Rating (W)
Voltage (V) Cycle (Hz) Input Output Max. Output (W)Current (A)
No load speed: min.ˉ¹= rpm
180 (7)
22.23 (7/8)
Weight according to
EPTA-Procedure 01/2003*: kg (lbs) 5.0 (11.0)
*with Wheel cover, Inner flange, Lock nut, and Side grip
Model No.
Diameter
Hole diameterWheel size: mm (")
MT92A
8,500
Protection against electric shock Double insulation
Specification
Power supply cord: m (ft) 2.0 (6.6)
230 (9)
22.23 (7/8)
6 (1/4)Max. thickness 6 (1/4)
5.3 (11.6)
MT92B
6,600
Double insulation
2.0 (6.6)
The above image
is Model MT92A.
TECHNICAL INFORMATION

P 2/ 9
Repair
[3] DISASSEMBLY/ASSEMBLY
[3] -1. Difference of Gears between MT92A and MT92B
[1] NECESSARY REPAIRING TOOLS
CAUTION: Repair the machine in accordance with “Instruction manual” or “Safety instructions”.
Code No. Description Use for
[2] LUBRICATION
Apply Makita grease N No.1 to the following portions designated with the black triangle to protect parts and product
from unusual abrasion.
Fig. 1
Item No. Description
Spiral bevel gear 53A for Model MT92A
Spiral bevel gear 53B for Model MT92B
Bearing box
Amount
approx. 60g
Portion to lubricate
Retaining ring R pliers RT-2E
1R004 Retaining ring pliers ST-2 disassembling/ assembling Ring spring 13
1R006
1R026
1R269
1R282
disassembling/ assembling Retaining ring R-32
Bearing setting pipe 16-8.2 removing Spiral bevel gear 53A or 53B
removing Ball bearingsBearing extractor
Round bar for Arbor 8-50
4
4
Gear housing Gear room for smooth engaging of Spiral bevel gears
Model No. Small spiral bevel gear
(Gear on Armature shaft)
Large spiral bevel gear
(Gear on Spindle)
Refer to the following gears. They are not interchangeable.
MT92A
MT92B
Number of teeth: 16
Spiral bevel gear 16
Spiral bevel gear 12 Spiral bevel gear 53B
Spiral bevel gear 53A
Number of teeth: 12
24.5 mm
19mm
Spiral bevel gear 16 for Model MT92A
Spiral bevel gear 12 for Model MT92B
grooved
not grooved

P 3/ 9
Repair
[3] DISASSEMBLY/ASSEMBLY
[3]-2. Small spiral bevel gear, Armature, Ball bearings 6201DDW and 629ZZ
DISASSEMBLING
1. Remove Brush holder caps and Carbon brushes from Motor housing,
then separate Gear housing together with Armature from Motor
housing by unscrewing four 5x35 Tapping screws.
(1) Separate Gear housing from Motor housing and remove Bearing box section from Gear housing. ( Fig. 2)
2. Remove Bearing box section
by unscrewing four 5x35
Hex socket head bolts.
Fig. 2
Brush holder cap Carbon brush
Brush holder cap
Armature
5x35 Tapping
screw (4 pcs)
Carbon brush
Gear housing
Motor housing
Bearing box
section
5x35 Tapping
screw (4 pcs.)
(2) Disassemble Armature and Small spiral bevel gear. (Fig. 3)
Wrench 13 for holding
M7 Hex nut M7 Hex nut
2. Pull off Armature while holding
Small spiral bevel gear.
Small spiral bevel gear
M7 Hex nut
Armature
Fig. 3
1. While holding M7 Hex nut with Wrench 13,
turn Armature counterclockwise by hand.
M7 Hex nut can be removed.
Note: If it is difficult to pull off Armature by hand, do the following steps.
1. Lubricate Small spiral bevel gear and Armature shaft with spray lubricant.
2. Wrap the gear with a cloth to protect the gear teeth.
3. By
using Water pump pliers, firmly grip the gear wrapped with a cloth, and then turn and pull Armature.

P 4/ 9
Repair
DISASSEMBLING
ASSEMBLING
(3) Disassemble Ball bearings 6201DDW and 629ZZ. (Fig. 4)
Note: The removed Armature and small Spiral bevel gear are employed as repairing tools when removing
Ball bearing 6201DDW from Gear housing.
(1) Armature can be also used as an assembling jig for Ball bearing 6201DDW to Gear housing. (Fig. 5)
Retaining
ring R-32
1. Remove Retaining ring
R-32 with 1R006.
2. Assemble Armature into Gear housing,
then set Small spiral bevel gear and
M7 Hex nut in place on Armature
shaft temporarily.
1R006
Ball bearing
6201DDW
Ball bearing 6201DDW
M7 Hex nut
Small spiral
bevel gear
3. Tap the end of Gear housing
with a plastic hammer.
Ball bearing 6201DDW can be
removed together with Armature.
4. Remove M7 Hex nut and Small spiral bevel gear again.
Ball bearing 6201DDW can be removed by hand.
M7 Hex nut
O rig 32
1R269
Ball bearing
6201DDW
Ball bearing 629ZZ
5. Remove Ball bearing 629ZZ with 1R269.
Small spiral bevel gear
Fig. 4
Fig. 5
2. Set Ball bearing 6201DDW to Armature temporarily and Assemble the bearing
into Gear housing by using with Armature as a jig, then pull off Armature from
the bearing. And then assemble Retaining ring R-32 with 1R006.
Ball bearing 6201DDW
1R006
Retaining
ring R-32
Ball bearing
6201DDW
1. Make sure that O ring 32
is set in Bearing box of
Gear housing in advance.
(2) Assemble Spiral bevel gear 16 or 12 and M7 Hex nut to Armature shaft by reversing the disassembly procedure.
(Fig. 3)
[3] DISASSEMBLY/ASSEMBLY
[3]-2. Small spiral bevel gear, Armature, Ball bearings 6201DDW and 629ZZ (cont.)

P 5/ 9
Repair
[3] DISASSEMBLY/ASSEMBLY
[3]-3. Large spiral bevel gear, Ball bearing 6202DDW and Ball bearing 607ZZ
DISASSEMBLING
(1) No need to separate Motor housing from Gear housing. Separate Bearing box section from Gear housing,
and remove Ball bearing 607ZZ and Ring spring 13 from Spindle. (Fig. 6)
1. Remove Bearing box section
by unscrewing four 5x35 Hex
socket head bolts.
2. Remove Ball bearing
607ZZ with 1R269.
Fig. 6
3. While opening Ring spring 13 with 1R004,
lift Ring spring 13 up from the opposite
side of 1R004 with Slotted screwdriver
and remove the spring from Spindle.
1R269
Ball bearing
607ZZ
Ring spring 13
Slotted screwdriver
1R004
Large spiral bevel gear
(2) Disassemble Spindle. (Fig. 7)
Fig. 7
1R026
1R026
4. Strike 1R026 carefully with Ram
until Spindle is slightly shifted
as drawn below.
5. Remove 1R026.
6. Set 1R282 onto Spindle,
and remove Spindle
by pressing down with
Arbor press.
Ram of
Arbor press
1. Put Bearing box onto Turn base of
Arbor press with its Large spiral
bevel gear side faced to Turn base.
2. Insert 1R026 over Spindle.
3. Set the ram of Arbor press to 20mm
higher position than the top of 1R026.
Bearing box
Turn base of Arbor press
Spindle 1R282
20mm
Large spiral
bevel gear
Note: Do not reuse Ball bearing 6203DDW when Bearing box section
is disassembled. It is inevitably damaged.

P 6/ 9
Repair
DISASSEMBLING
ASSEMBLING
(3) Disassemble Ball bearing 6202DDW. (Fig. 8)
1. Remove Bearing retainer
by unscrewing three M4x13
Pan head screws.
2. Put Bearing box onto Turn base of Arbor press with its Ball bearing
mounting side faced to Turn base.
Set Spindle on Ball bearing 6202DDW by using with Spindle as a jig,
then remove the bearing with Arbor press.
Note: Do not reuse Ball bearing 6202DDW when removing Spindle in
the step of Fig. 7. It is inevitably damaged.
Fig. 8
Bearing
retainer
Assemble Bearing box section as follows:
(1) Mount Ball bearing 6202DDW to Bearing box. And mount Bearing retainer. (Refer to Fig. 8)
(2) Mount Spindle by pressing it with Arbor press. (Refer to Fig. 7)
(3) Assemble large Spiral bevel gear and secure it with Ring spring 13. And mount Ball bearing 607ZZ to Spindle.
(Refer to Fig. 6)
M4x14
Pan head
screw (3pcs.)
[3] DISASSEMBLY/ASSEMBLY
[3]-3. Large spiral bevel gear, Ball bearing 6202DDW and Ball bearing 607ZZ (cont.)
Ball bearing 6202DDW
Spindle

P 7/ 9
Repair
[3] DISASSEMBLY/ASSEMBLY
[3]-4. Shaft Lock
DISASSEMBLING
(1) Remove Bearing box section from Gear housing complete. (Fig. 2)
(2) Disassemble Shaft lock mechanism as drawn in Figs. 9 and 10.
Set the machine on 1R350, then apply 1R268 to Shoulder pin 5
through the small Hole on Pin cap, and then tap 1R268 with
Plastic hammer.
Shoulder pin 5 comes out from Gear housing complete.
Release 1R268 from Pin cap carefully
so that Pin cap does not be slung by
Compression spring 12.
Shoulder Pin 5
Pin Cap
Pin Cap
Compression
Spring 12
1R268
1R350
Fig. 9 Fig. 10
ASSEMBLY
Fig. 11 Fig. 12
(1) Be sure to use a new Pin cap for replacement and to remove all the plastic dust on Shoulder pin 5. (Fig. 11)
(2) Assemble the Parts for Shaft lock mechanism as drawn in Fig. 12.
Plastic Dust
Shoulder Pin 5
Shoulder Pin 5
2. Assemble Compression spring 12
and Pin cap by pressing them to
Shoulder pin 5.
1. Insert Shoulder pin 5 through
the hole of Gear housing complete.
Remove Plastic dust from
the constricted part of
Shoulder pin 5.
Pin Cap
Compression
Spring 12

Circuit diagram
Wiring diagram
P 8/ 9
MT92A, MT92B
Fig. D-1
Fig. D-2
White
Power supply
cord
This Lead wire is black
for some counties.
This Lead wire is white
for some counties.
Switch
Field
Field viewed from
Commutator side
Noise
suppressor
Handle set (L) side
Handle set (R) side
Color index of lead wires' sheath
Black Blue
Brown
2
2
1
1
Wiring of Field Lead Wires
Hook
Noise suppressor is not used
for some countries.
Pass Field lead wire
through hook.
Pass Field lead wire
through hook.

Wiring diagram
P 9/ 9
Fig. D-3
Fig. D-4
Wiring to Switch
Wiring in Handle Set (L)
Rib A
Rib B
Power supply cord
Rib C
Noise suppressor
(if it is used)
Connect connectors for Field lead wires
to Switch terminals of Handle set (L) side
while facing their Wire connecting portions
to Motor housing side.
Switch
Field lead wire
Noise suppressor
Connect Noise suppressor’s lead wires to Switch terminal
from the same direction as Field lead wires while facing
their wire connecting portions to Handle set(L) side.
Note: Noise suppressor is not used for some countries.
Put Lead wire (black or brown)
between Ribs A and B.
Do not put Noise suppressor’s
Lead wires (2 whites) on
Field Lead wires (2 blacks).
Put the slag portion of Field lead wires in this position.
Note: The slag portion can be also put in the space for
Noise suppressor if it is not used.
Pass Field lead wires (2 blacks)
through the groove.
Do not slag Field lead wires
(2 blacks) in Motor housing.
Put Noise suppressor’s Lead wire
(white) and Field Lead wire (black)
between Ribs A and C.
This manual suits for next models
1
Table of contents
Other Makita Grinder manuals
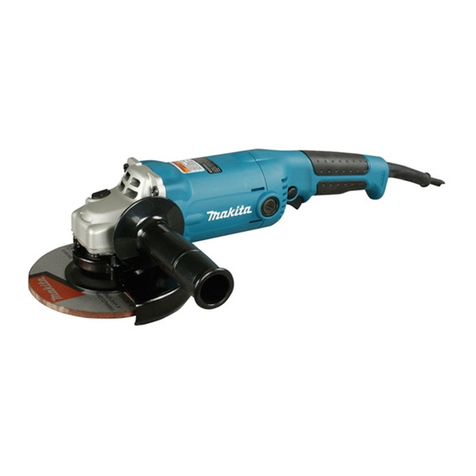
Makita
Makita GA5010 User manual
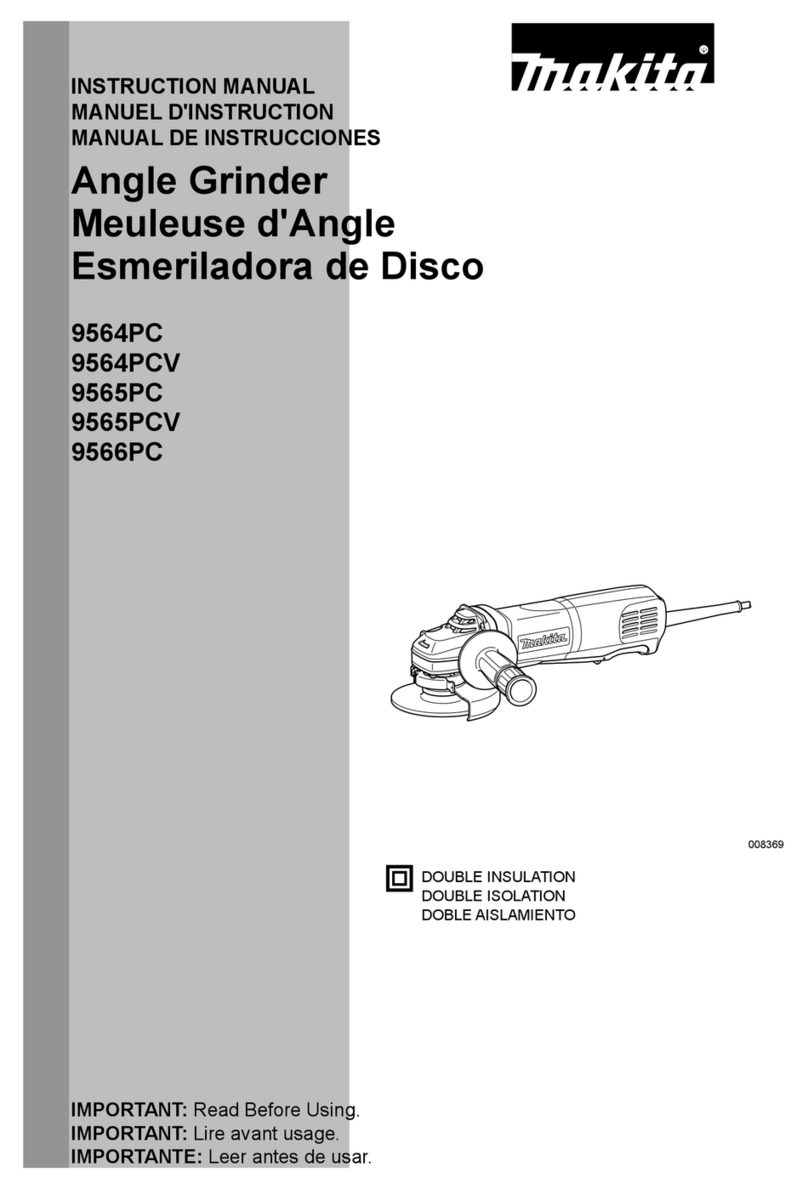
Makita
Makita 9564PC User manual
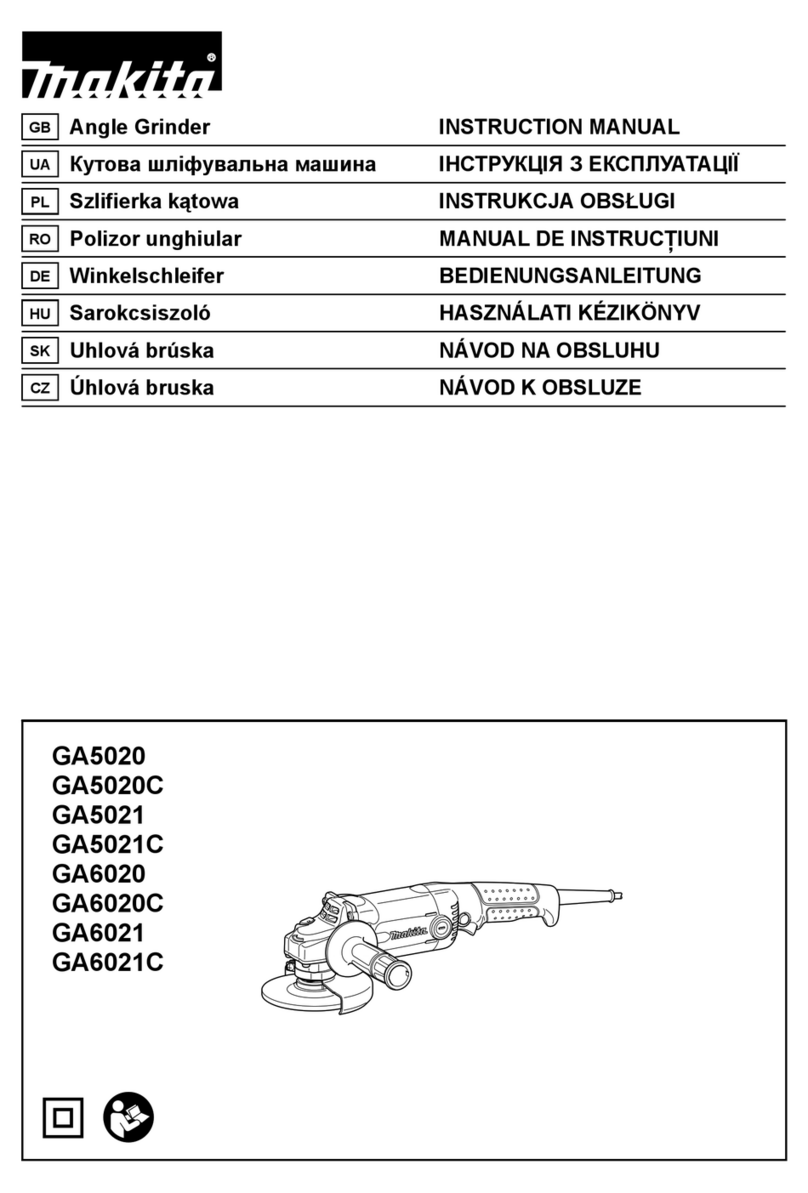
Makita
Makita GA5020 User manual
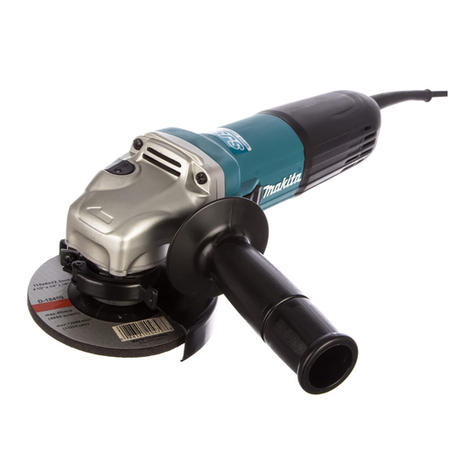
Makita
Makita GA4540 User manual

Makita
Makita 906 User manual

Makita
Makita M908 User manual
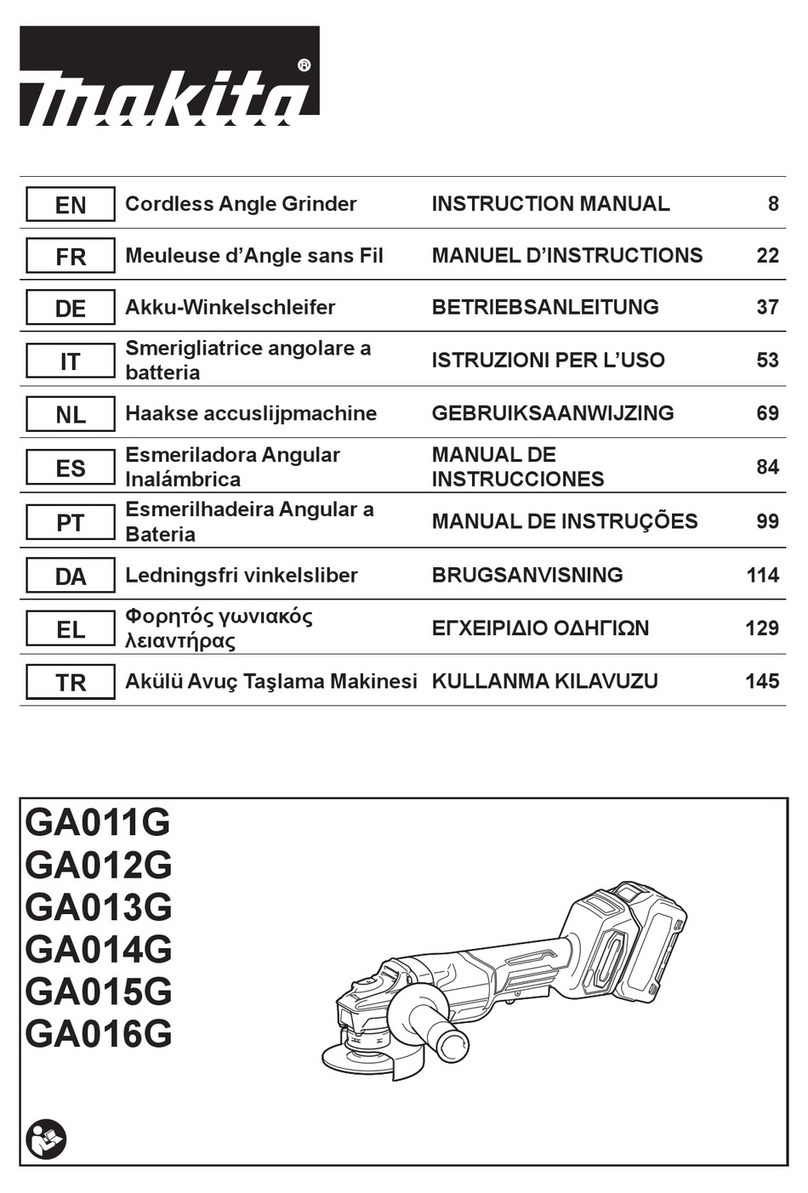
Makita
Makita GA011G User manual

Makita
Makita GA011G User manual
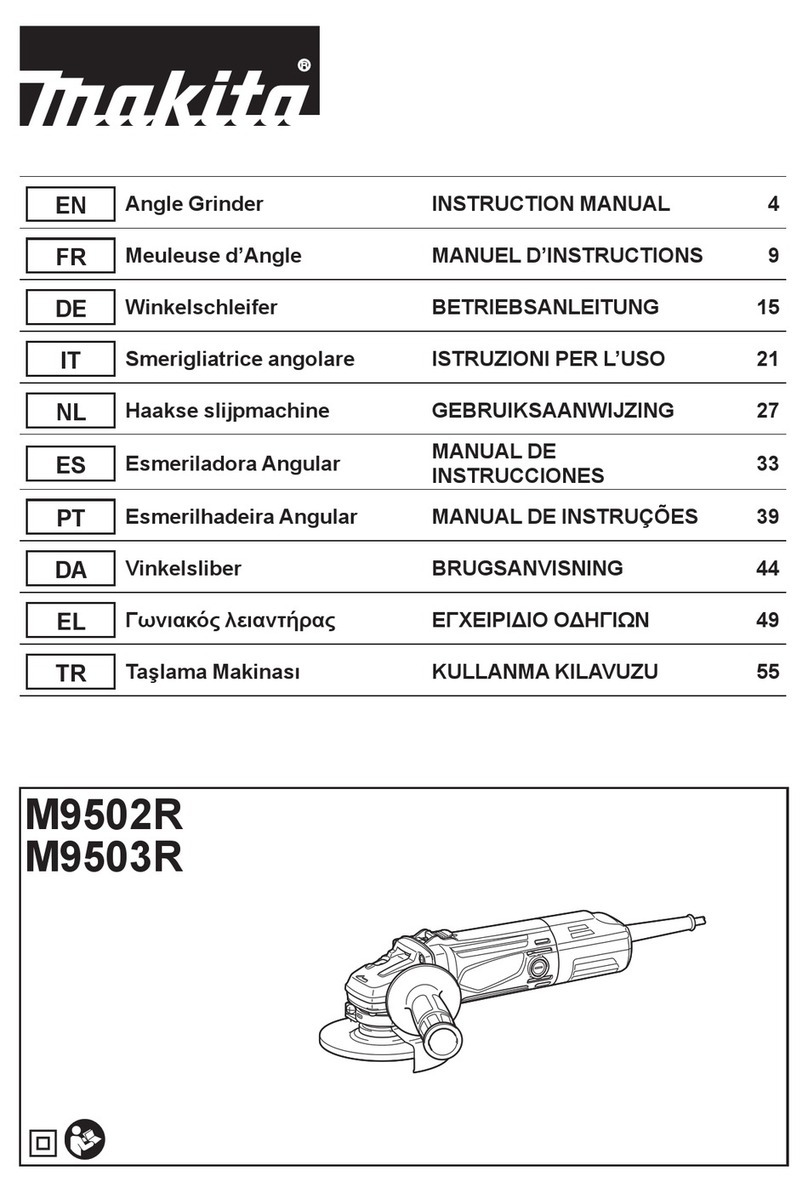
Makita
Makita M9502R User manual
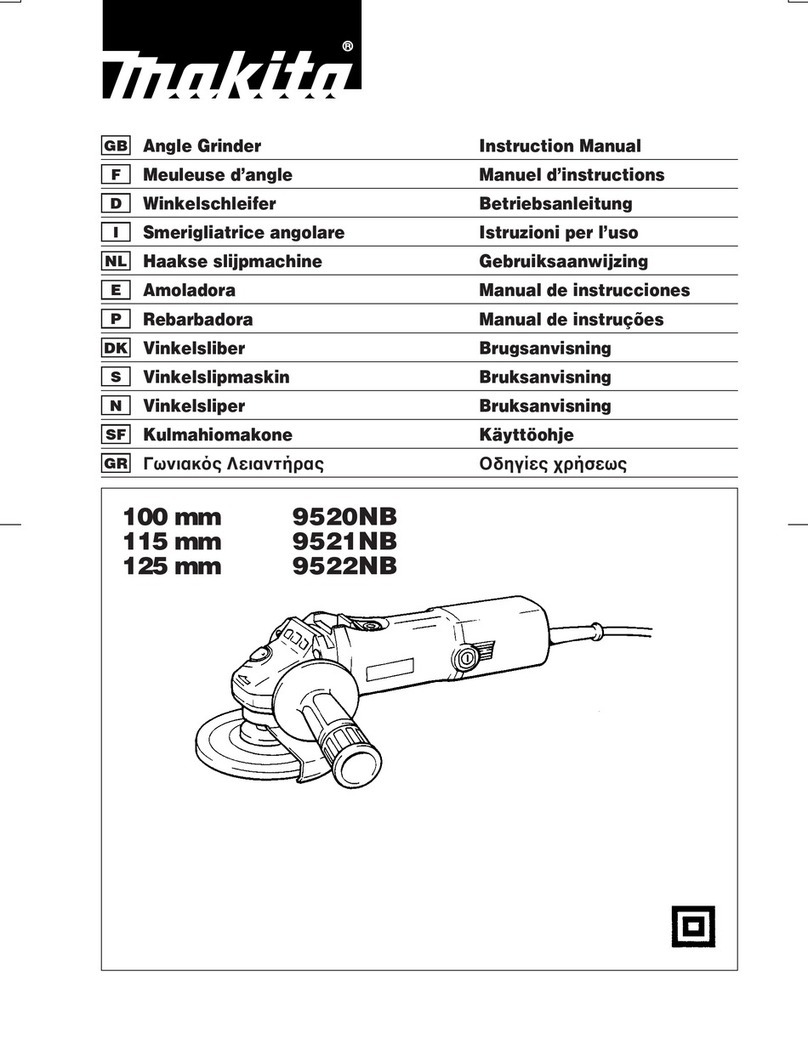
Makita
Makita 9520NB User manual
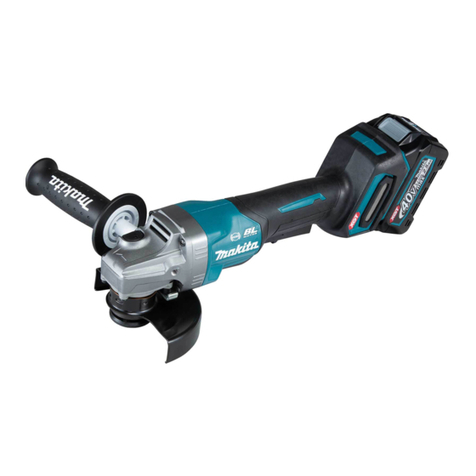
Makita
Makita GA011G User manual
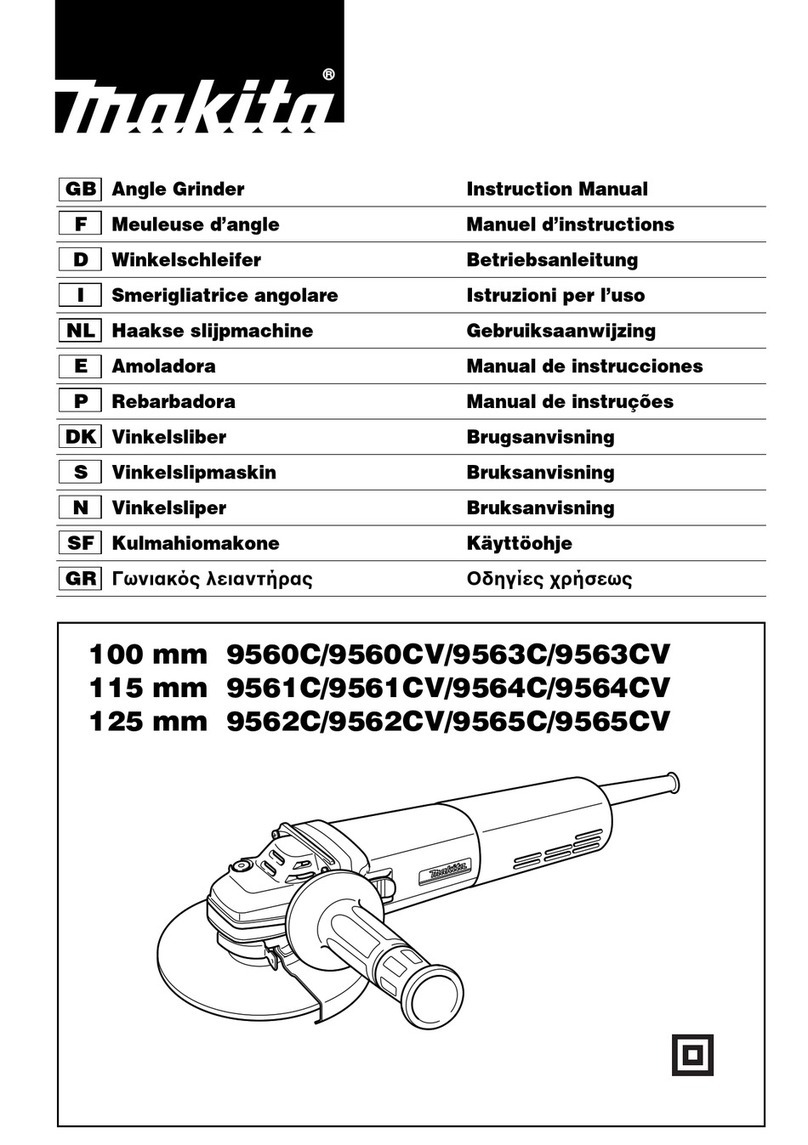
Makita
Makita 9560C User manual
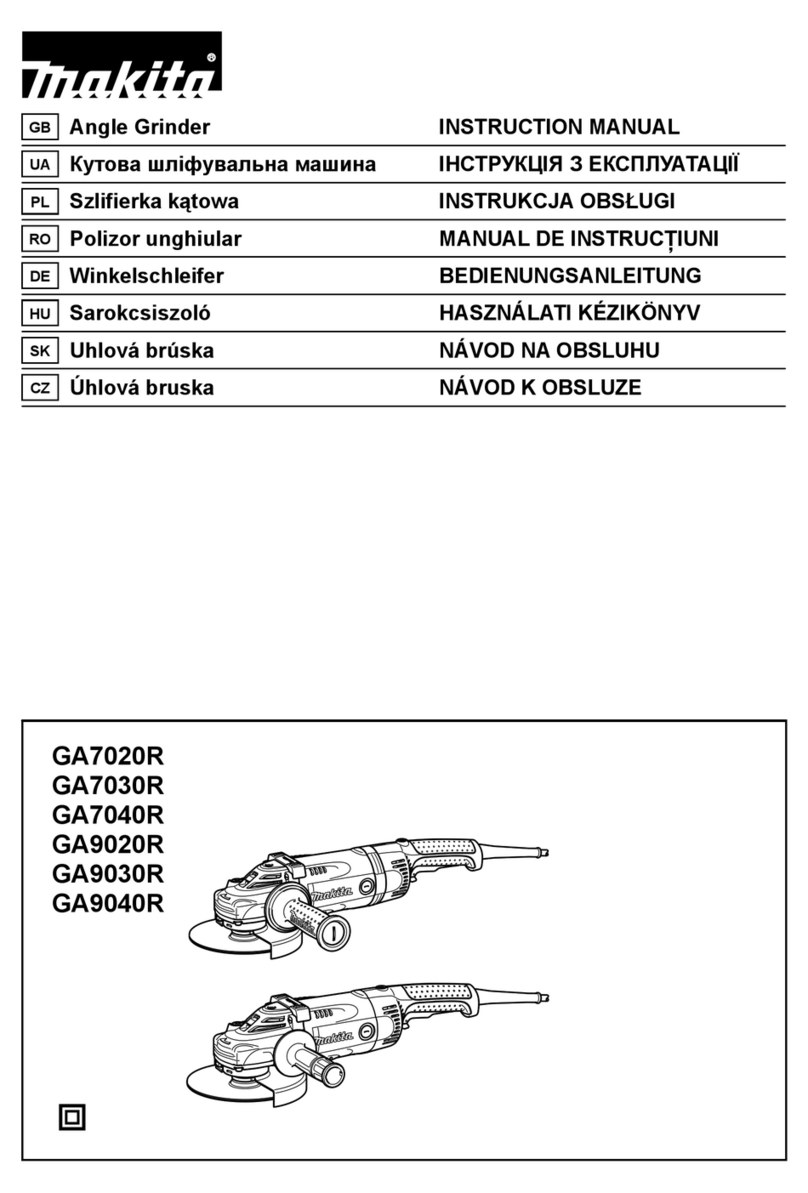
Makita
Makita GA7020R User manual

Makita
Makita GA028G User manual

Makita
Makita GA4593 User manual

Makita
Makita 9561CH User manual

Makita
Makita 9527PB Quick start guide
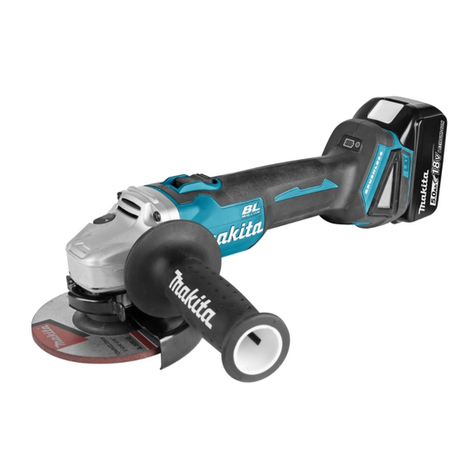
Makita
Makita DGA504RTJ User manual

Makita
Makita 9005B User manual
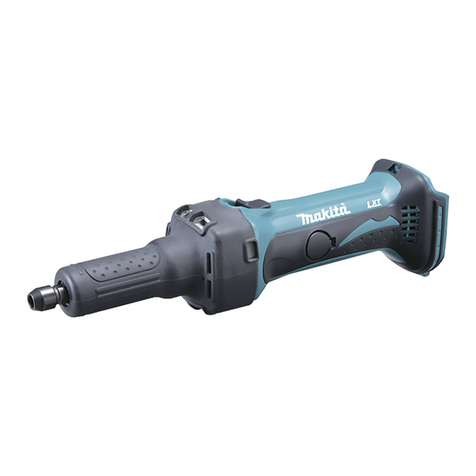
Makita
Makita DGD800 User manual