Mannol HC-2197 User manual

Pneumatic Oil Extractor
Operation Manual
Model No. : HC-2197
To prevent serious injury, Read and understand all
Warnings and instructions before use. Operators
must obey all safety procedures & instructions

2
INDEX
Specifications..................................................................................................................3
Save this manual.............................................................................................................3
General safety rules ........................................................................................................3
Safety Warnings and Precautions...................................................................................3
Specific safety rules for this product..............................................................................4
Warning ..........................................................................................................................5
Transport and unpacking................................................................................................5
Features...........................................................................................................................6
Assembly instructions.....................................................................................................6
Operation instructions.....................................................................................................7
Trouble shooting...........................................................................................................11
Inspection, Maintenance, and Cleaning........................................................................11
Exploded drawing.........................................................................................................13

3
Specifications
Function collect waste oil from vehicle gear box or engine
Power Compressed air
Air Consumption About 200L/min
Air Inlet Pressure 87~116PSI/6~8Bar
Oil ejection pressure 10~14PSI/0.7~1Bar
Vacuum Degree 0 ~ -14PSI/0~-1Bar
Tank Capacity 70L
Perspex cylinder Capacity(Practicable/total) 9/10L
Collect tray capacity 16L
Height About 1350mm~1750mm
Working Temperature 40~60 (for engine oil)℃
Save this manual
You will need the manual for the safety warnings and precautions, assembly instructions, operating and
maintenance procedures, parts list and diagram.
Keep your invoice with this manual.
Write the invoice number on the inside of the front cover.
Keep the manual and invoice in a safe and dry place for future reference.
General safety rules
WARNING!
READ AND UNDERSTAND ALL INSTRUCTIONS. Failure to follow all
instructions listed below may result in electric shock, fire, and/or serious
injury. SAVE THESE INSTRUCTION
Safety Warnings and Precautions
WARNING: When using tool, basic safety precautions should always be followed
to reduce the risk of personal injury and damage to equipment.
1. Keep work area clean. Cluttered areas invite injuries.

4
2. Observe work area conditions. Do not use machines or power tools in damp or wet locations. Don’t
expose to rain. Keep work area well lighted. Do not use electrically powered tools in the presence of
flammable gases or liquids.
3. Keep children away. Children must never be allowed in the work area. Do not let them handle machines,
tools or extension cords.
4. Store idle equipment. When not in use, tools must be stored in a dry location to inhibit rust. Always lock
up tools and keep out of reach of children.
5. Avoid Unintentional Starting. Be sure the air pressure is in the off position when not in use and before
making hose connection.
6. Stay alert. Watch what you are doing, use common sense. Do not operate any tool when you are tired.
7. Check for damaged parts. Before using any tool, any part that appears damaged should be carefully
checked to determine that it would operate properly and perform its intended function. Check for
alignment and binding of moving parts; any broken parts or mounting fixtures; and any other condition
that may affect proper operation. Any part that is damaged should be properly repaired or replaced by
a qualified technician. Do not use the tool if any control or switch does not operate properly.
8. Replacement parts and accessories. When servicing, use only identical replacement parts. Use of any
other parts will void the warranty. Only use accessories intended for use with this tool.
9. Do not operate tool if under the influence of alcohol or drugs. Read warning labels if taking prescription
medicine to determine if your judgment or reflexes are impaired while taking drugs. If there is any
doubt, do not operate the tool.
10. Maintenance. For your safety, service and maintenance should be performed regularly by a qualified
technician.
Note: Performance of this tool may vary depending on variations in air pressure and compressor capacity.
Specific safety rules for this product
This equipment is designed be operated by qualified personnel. It should only be operated after reading and
understanding the safety warnings and operating procedures in thisinstructionmanual.
1. Do not smoke near this equipment.
2. Use in a well ventilated area.
3. When leaks are found in the equipment or hoses, immediately turn the air pressure off and repair the leaks.
4. Do not exceed the recommended operating air pressure. This could damage equipment.
5. Keep a type ABC fire extinguisher nearby in case of fires.

5
6. Always protect your skin and eyes from contact with oil and solvents.
7. Do not start engine during the time of oil extraction. Otherwise it will cause the damage of extraction probes
and injuries of people.
8. Be careful for the oil extracted out from the vehicle, as temperature of oil is high, always between 40~60℃.
9. Used oil should be properly disposed or recycled. Please contact with your local waste liquid/solid authority
for information on recycling.
10. Can be used with other mechanical engine oil, lubricants as well as temporary storage. Brake fluid, gasoline,
diesel and other liquid contains methanol and ketones or flammable is strictly prohibited.
Warning
1. Please read this Manual Book carefully and fully understand it before operation.
2. In order to avoid the aging of the rubber parts, do not expose the machine in the sunshine; do not deposit the
machine in a moist place, it must be stored in a dry place with good ventilation. Because of the multi functions,
the machine is equipped with many accessories, it must be cared by a special technician.
3. This machine has been tested strictly before leaving our factory, but the operator must obey our operation
regulations. Please do not try to take apart and repair it by yourself, if you meet with any faults, please contact
our local distributors or our company.
4. After using, always cut off connection with air compressor and recover all the pipe to its original place.
5. Do not lower than the min. air inlet required pressure. Do not exceed the max. air inlet required pressure.
6. Do not dismantle this machine by unqualified or unauthorized personnel. Otherwise will avoid warranty.
7. If you have any inquiries, please contact our local distributors or service offices.
8. Air inlet & Oil drain: Ball valve must be closed operation confirmation.
Transport and unpacking
When unpacking, check to make sure that all the parts are included. Refer to the Assembly section, and the
Assembly Drawing and Parts List at the end of this manual.
For transport of the packaged product, refer to Fig.1 below
Once the product has been unpacked, check that the instructions manual is there, that the material is complete and

6
there are no parts which have been visibly damaged. If any
parts are missing or broken, please contact with local
distributor as soon as possible. Remove the contents of the
packages and place them in a storage area inaccessible to
children or animals.
In the package, you will find:
a) One Complete Oil Tank/Reservoir
b) One Complete Measuring Glass/Cylinder
c) One Oil Collecting Bowl/tray
d) One Strainer
e) Probes 6 pcs with sleeve
f) User’s Manual
Features
This type measuring glass uses the explosion-proof equipment, can effectively protect the machine and
operator's security, with Exclusive patent. holds the exclusive patent. Imitation is not permitted.
Assembly instructions
Setup Cylinder(FIG.2)
1. Refer to right FIG.2 install the cylinder to the
oil tank base.
2. In order not to damage the seal ring, it is
recommended to apply a little oil to the joint.
3. Tighten the screw. Note: The extraction oil
hose is close to the tool box.
Oil Tray(FIG.3)
1. Open the carton to take out the oil tray, check to see if there is any damage. If so, please contact with your
distributor immediately.
FIG.2
FIG.1

7
2. Pull out the lift pole and install the oil tray on the lift pole.
3. Install and fix the oil tray, strain, extension funnel together.
4. Ensure the lift pole is perpendicular to the equipment.
5. Please lift up the oil tray above cylinder with 1cm height during installation of cylinder. Fix the lifting pole to
position to avoid rubbing against each other.
6. Insert the extension funnel pieces into its bump slot one by one, push it to the button till each pieces are even.
7. Tighten the screw.
Operation instructions
Oil Collections(FIG.4)
1. Lift the vehicle up, then Push the machine to the place right under the engine oil
outlet.
2. Turn on ball valve ④at first.
3. Open the ball valve ⑦ under the oil tray and unscrew the oil drain plug of
engine. FIG.4
FIG.3

8
4. Then oil transferring from oil tray to oil tank.
5. Screw on the drain plug of vehicle.
Vacuum Generation
Operating air pressure: 87~116PSI /6~8 bar
Consumption of air: 52 Gallons/min (about 200L/min.)
If only measuring glass to be vacuum(FIG.9)
1. Turn off the machine ball valve ○
3 and the extraction valve ○
6 (fix on the extraction hose)
2. Connect the compressed air to the machine air inlet ○
1.
3. Gradually turn on the air inlet valve(which equipped by customer himself) for vacuum generation.
4. When finger reaching to the MAX area on the vacuum gauge○
2 , turn off the air inlet valve (Estimated time
for vacuum generation within 20~30seconds, If continuously extraction required, please let it open).
5. Now it is ready for extraction
Vacuuming both measuring glass and tank(FIG.9)
1. Turn off all valves before vacuuming.
2. Connect the compressed air to the machine air inlet ○
1.
3. Open the ball valve○
3.
4. Gradually turn on the air inlet valve(which equipped by customer himself) for vacuum generation.
5. When finger reaching to the MAX. area on the vacuum gauge○
2 , turn off the air inlet valve (estimated time
for vacuum generation within 4~5 minutes) (If continuously extraction required, please let it open)
6. Now it is ready for extraction
Tips
1. Benefits for gradually and slowly turn on air inlet valve for reducing of air-consumption and a quicker
speed for vacuum-generation.
2. Benefits for vacuum generation of both cylinder and oil tank is fasting the speed of oil transferring.
3. We suggest extract both to be vacuum when the machine need to be used to the place without air
compressor. Which will benefit long time continuously working.
Oil Extraction(FIG.9)
1. After vacuum, choose suitable probe (which is the largest
diameter one can be inserted into the engine) and tightly connect
it to the extraction pipe connector.
2. Insert the end of the probe into the engine oil inlet hole of the FIG.5

9
engine.
3. Turn on the ball valve○
6.
4. If waste oil only extracted into the cylinder. Please make sure the ball valve ○
3 is closed.
5. If waste oil extracted to the oil tank through the cylinder. Please open the ball valve ○
3 accordingly.
Warning: Also the oil tank need to be vacuum before extraction operation.
6. After finish extraction, turn off the ball valve ○
6 on the extraction pipe.
Note: Extraction of hot-oil, max. temperature for oil 60 . Please do not℃exceed 60 . Please hold the black℃
sleeve to avoid scald.
Ejection(FIG.9)
Oil ejection from cylinder to underside oil tank
1. When the oil level reached cylinder ‘STOP’ warning line, please empty the cylinder with oil ejection.
2. Turn on ball valve ○
7 at first.
3. Turn on ball valve○
3,at the same time turn on mini ball valve ○
6 from the hose to release cylinder pressure
and oil drain into the oil tank.
4. Turn off valves ○
3 and○
6 after ejection.
More about oil ejection from cylinder
1. Turn on valve ○
3 , if vacuum existed in the tank, and then oil from cylinder will be fast transferred into the
tank.
2. If no vacuum existed in the tank, turn on the ball valve ○
7 and○
6 for helping making a quicker
transferring of waste oil into the tank.
3. Turn off valve ○
3 and ball valve ○
6 after ejection finished.
4. Continuously repeating above operation steps for oil ejection before oil contained in the cylinder reaching
“STOP” level on the sticker of cylinder.(Which is eject oil before cylinder reaching full)
FIG.6 FIG.7 FIG.8

10
Tips
It will be faster for transferring of waste oil from transparent measuring glass into oil tank, if vacuum
generated in both transparent measuring glass and oil tank.
Tank Emptying
When the oil retained in tank near full(see oil window), You need to eject oil out into a disposal tank and resolve
the waste oil accordingly to the instruction of local government.
1. Turn off all the valves.
2. Hold the ejection hook and insert it into the external disposal tank.
3. Connect the air compressor with the air inlet ○
4.
4. Turn on wing valve ○
5 for oil ejection.
5. Turn on the mini ball valve ○
4 gradually, adding tank pressure, turn off air compressor when pressure reach
to desired pressure. (The safety valve will automatically release pressure when the tank pressure reach 1.0
bar/14PSI, turn off the mini ball valve ○
4 immediately and quickly drop the tank pressure below
1.0bar/14PSI, otherwise it could lead to serious incident).
6. Cut off air source after ejection, empty tank pressure and turn off all valves.
Notice: The tank capacity is 70L. It suggest to drain the waste oil
from the tank before the volume of waste oil reach the scale at
55L STOP position.
Note: The space at top of the tank is reserved for air. During the
oil drain process, the tank will contain pressure after the air is
compressed. Air pressure cannot be over 1Bar, so that it will
accelerate the oil draining.
Suggestion: After drain oil from the tank, please release
remaining air in the tank.
WARNING!!!
1. The ball valve ○
3 (FIG.9) must be closed in order to prevent air enter causing transparent measuring
glass damaged.
2. Please hold the end of Ejection Hook to avoid waste oil spattering out, cause an injury of
eye, dirty of clothes.
3. Before disconnect extraction/ejection tube with fast couple (male), making sure no any pressure existed

11
in the tank. Otherwise, oil will spray out.
Safety Device
1. A safety valve on the top of the tank will release pressure when pressure is over 14PSI/1bar during ejection.
2. A safety device was fixed on the top of the cylinder which could avoid the cylinder exploding while the
compressed air enter the cylinder.
Trouble shooting
1. Vacuum gauge don’t work
Check the air pressure: standard air pressure through “air inlet valve "should between 87~116PSI
/6~8bar; Air consumption is about 200L/Min.
Make sure all the valves are on the correct place.
Check vacuum operator-to-tank seal.
2. There is a figure showed on the vacuum gauge but the machine don’t working and extracting
Check extraction hose-to-probe seal.
Temperature of waste oil is too low or not?(ordinary temperature of oil should between 40~60 .℃)
Extract grease oil or other oil with high density, which is, avoided.
Make sure that extraction pipe open.
Make sure that extraction pipe do not block off and probe don’t touch the bottom of tank.
Make sure that the silencer haven’t been blocked.
Inspection, Maintenance, and Cleaning
1. Before each use, inspect the general condition of the machine Check for loose screws, air and oil leakage,
misalignment or binding of moving parts, cracked or broken parts, and any other condition that may affect its
safe operation. If abnormal noise or vibration occurs, have the problem corrected before further use. Do not
use damaged equipment.
2. Periodically recheck all hoses, valves, nuts, bolts, and screws for tightness.
3. For a long time to use, please check the adapter/O seals of the adaptors for leakage.
4. It’s necessary to drain the waste oil as soon as possible in case of the corroding of tank.
5. Store in a clean and dry location.
6. All maintenance and repairs must be completed by a qualified technician.

12
FIG.9

13
Exploded drawing

14

15
Table of contents
Popular Scrubber manuals by other brands

Electrolux Professional
Electrolux Professional WHB5 500H user manual
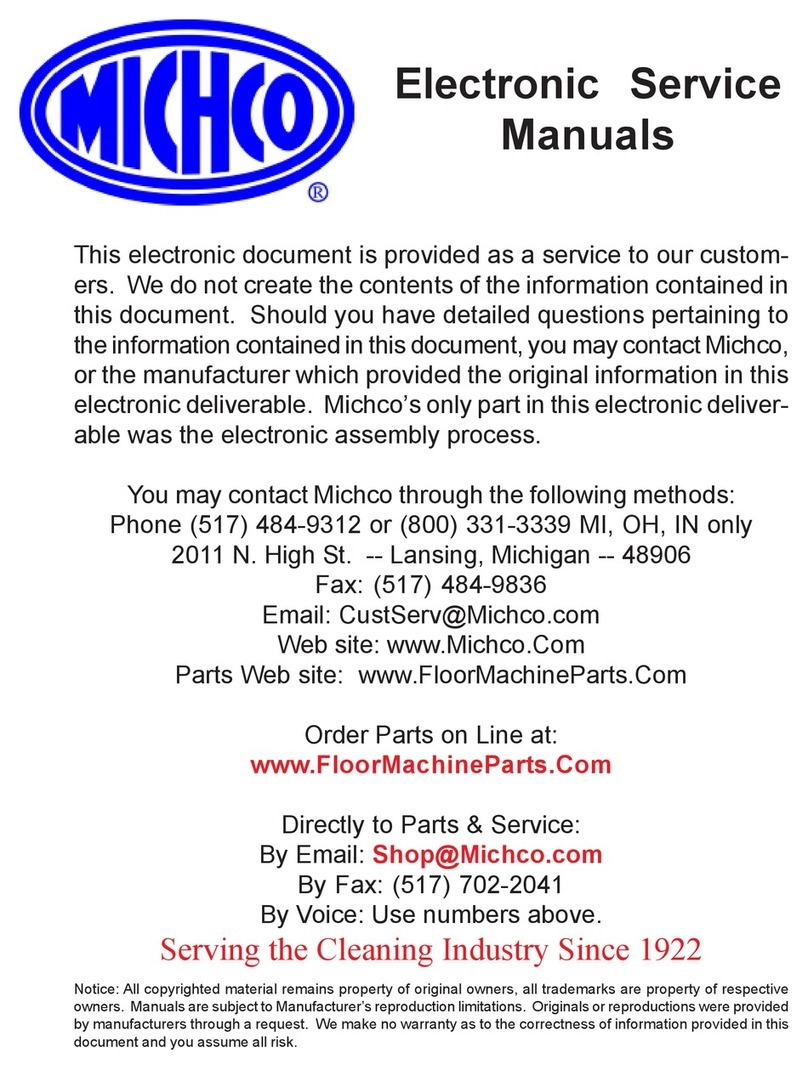
Pacific
Pacific ScrubMaster 20B Operating & maintenance instructions
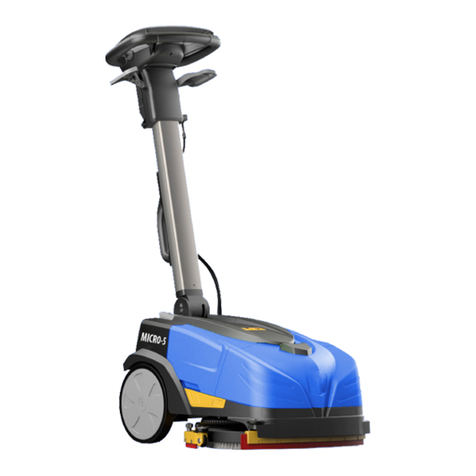
Dustbane
Dustbane Micro-5 quick guide

Truvox International
Truvox International Cimex Cyclone CR38 user manual

Plymovent
Plymovent ECONOMY ARM Installation and user manual
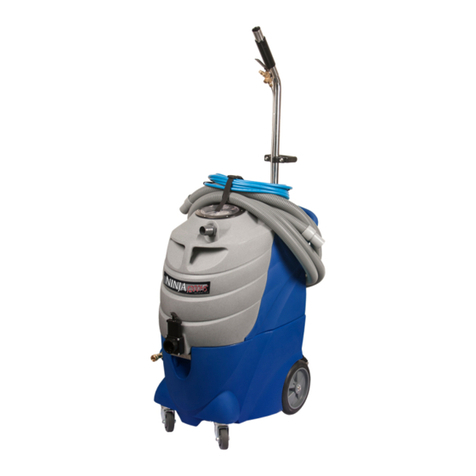
Ninja
Ninja 1200MS user manual