Mathey Dearman DB-724 User manual

WHERE THERE’S PIPE, THERE’S MATHEY
Dearman Sleeve Clamp
Parts & Operating Manual
Revised: 3/2016
P. O. Box 472110, Tulsa, OK 74147-2110 USA
Toll Free: 800-725-7311
918-447-1288 Office
918-447-0188 Fax
www.mathey.com
STANDARD SLEEVE CLAMP
HEAVY DUTY SLEEVE CLAMP
MODEL # ______________________
SERIAL # ______________________

pg. 2
ALL WARNINGS PROVIDED IN THIS MANUAL MUST BE READ AND ALL PROCEDURES FOLLOWED
IN AN EFFORT TO PREVENT INJURY OR DEATH TO PERSONNEL AND / OR DAMAGE TO THE
EQUIPMENT.
ONLY QUALIFIED AUTHORIZED PERSONNEL should operate Mathey Dearman equipment. This
manual includes safety instructions throughout the operation instructions as well as those
noted on this Safety Instruction page. Throughout this manual these warnings will be noted by
theses warning symbols.
Operation of this equipment should be in accordance with the instructions provided in this
manual. No Mathey Dearman equipment should ever be used in a manner other than as
described in this manual.
Operators should wear approved PPE at all times while using this equipment. PPE includes hard
hat, ANSI approved eye protection, gloves, steel toe boots and protective clothing. Do not wear
loose clothing that can become entangled in the equipment.
SAFETY INSTRUCTIONS
Mathey Dearman Equipment
S
A
F
E
T
Y
F
I
R
S
T
A
L
W
A
Y
S BE SAFE AT ALL TIMES. WEAR PPE.

pg. 3
•IN ADDITION TO THE ABOVE WARNINGS ALL NATIONAL AND INTERNATIONAL SAFETY RULES FOR
THE USE OF THE DEARMAN SLEEVE CLAMP MUST BE FOLLOWED TO PREVENT ANY INJURIES OR
DEATH AS A RESULT OF IMPROPER CLAMPING PROCEDURES.
•TO REDUCE THE RISK OF SERIOUS OR INJURY DEATH THE DEARMAN SLEEVE CLAMP SHOULD
NEVER BE USED TO LIFT THE PIPE UNDER ANY CIRCUMSTANCES. The pipe must have an external
source of support at all times when the Dearman Sleeve Clamp is being installed and during use.
•ONLY QUALIFIED, TRAINED AND AUTHORIZED PERSONNEL should operate the Dearman
Sleeve Clamp. Other personnel should NOT be allowed to
set‐up, operate or maintain the
Dearman Sleeve Clamp.
•When using the Dearman Sleeve Clamp, basic safety precautions must always be followed to
reduce the risk of personal injury.
•The Dearman Sleeve Clamp should be inspected for defects such as cracks, nicks,
arc marks, and
abrasions prior to use and during scheduled maintenance.
•Maintenance personnel must read and understand the parts and operating manual of the
Dearman Sleeve Clamp prior to attempting maintenance on the clamp.
•The Dearman Sleeve Clamp should be tested for proper function prior to use
including the
alignment of sleeve, or other appropriate pipe fittings.
•The operator should insure that the area around the Dearman Sleeve Clamp is
clear of debris
and other hazards that may pose a trip hazard to personnel during
operation.
•To avoid the risk of electrical shock the operator must insure that the Dearman Sleeve Clamp is
within a safe distance from power lines or other electrical sources.
•Never use the Dearman Sleeve Clamp as a ground for any purpose.
•Make sure loose clothing, tools, belts, etc. do not become entangled in the Dearman Sleeve Clamp.
•The periodic maintenance instructions must be followed in the Dearman Sleeve Clamp parts
and
operating manual to avoid serious injury.
•The pipe must be secured from rotation, prior to mounting the Dearman Sleeve Clamp on the pipe
and/or sleeve.
•Make sure the Dearman Sleeve Clamp is in full contact with the mating pipe, sleeve, fitting or
valve.
•Never use the Dearman Sleeve Clamp for any operation other than its intended purpose.
•Pressure required to clamp the pipe sleeves to the outside diameter of the pipe will vary
depending on pipe diameter, pipe wall thickness, and tensile strength of the pipe sleeve. If in
doubt with regards to the necessary clamping requirements, contact Mathey Dearman Inc. at
(800) 725‐7311.
•Always use the Safety Whip check included when operating the Dearman Sleeve Clamp.
S
A
F
E
T
Y
F
I
R
S
T
A
L
W
A
Y
S
SAFETY INSTRUCTIONS CONT’D
DEARMAN SLEEVE CLAMP OPERATION
S
A
F
E
T
Y
F
I
R
S
T
A
L
W
A
Y
S

pg. 4
Table of Contents
Safety 2-3
Warranty 5
Warnings 6
1.0 Publications 7
2.0 General Description 8
3.0 Work Instruction 12
4.0 Storage 20
5.0 Recycling of Components 20
6.0 Maintenance 20
APPENDIX: A 21
APPENDIX: B 22

pg. 5
WARRANTY INFORMATION
For Warranty Information visit www.mathey.com

pg. 6
WARNINGS
WARNING: The Dearman Sleeve Clamp is designed for holding any weldable sleeve or fitting to the
outside diameter of the pipe during the welding process. It is not intended to lift the sleeve or fitting,
nor lift and / or support the pipe. Any attempt to do so can result in damage to the device, pipe, sleeves,
and serious injury and / or death.
WARNING: The clamping capacity the Dearman Sleeve Clamp is dependent on the sleeve
diameter, wall thickness, and tensile strength. Refer to Table 1. Call Mathey Dearman (at 1-800-
725-7311 or 1-918-447-1288) with any questions.
WARNING: Under no circumstances should additional chain be added to the Dearman Sleeve Clamp to
increase its operating range without contacting Mathey Dearman at 1-800-725-7311 or 1-918-447-1288.
WARNING: Do not use any hand pump other than the D106-Kit with the DB-724, DB-724SS, DB-
748, or DB-748SS. Doing so can lead to damage to the device, pipe, sleeves, and serious injury
and/or death.
WARNING: Avoid weld or direct heat damage to the chain clamp or any chain clamp component,
hydraulic hand pump, hydraulic cylinder, and hose during the welding process. Recommended safe
welding distance from the components listed above is a minimum 2” (50mm). Failure to do so can
result in damage to the device, pipe, sleeves, and serious injury and/or death.
WARNING:Failure to put the locking pin and (in the heavy duty sleeve chain clamp) the safety
pin in place can result in damage to the device, pipe, sleeves, and serious injury and / or death.
WARNING: Failure to use the supplied safety whip check can result in serious injury and / or
death.

pg. 7
1.0 – PUBLICATIONS
•Refer to the following standards or their latest revisions for more information:
•OSHA, SAFETY AND HEALTH STANDARDS, 29CFR 1910, obtainable from the Superintendent of Documents, U.S.
Government Printing Office, Washington, D.C. 20402
•ANSI Standard Z49.1, SAFETY IN WELDING AND CUTTING, obtainable from the American Welding Society, 550 N.W.
LeJeune Rd, Miami, FL 33126
•NIOSH, SAFETY AND HEALTH IN ARC WELDING AND GAS WELDING AND CUTTING, obtainable from the Superintendent
of Documents, U.S. Government Printing Office, Washington, D.C. 20402
•ANSI Standard Z87.1, SAFE PRACTICES FOR OCCUPATION AND EDUCATIONAL EYE AND FACE PROTECTION, obtainable
from American National Standards Institute, 1430 Broadway, New York, NY 10018
•ANSI Standard Z49.2, FIRE PREVENTION IN THE USE OF CUTTING AND WELDING PROCESSES, obtainable from American
National Standards Institute, 1430 Broadway, New York, NY 10018
•AWS Standard A6.0, WELDING AND CUTTING CONTAINERS WHICH HAVE HELD COMBUSTIBLES, obtainable from
American Welding Society, 550 N.W. LeJeune Rd, Miami, FL 33126
•NFPA Standard 51, OXYGEN-FUEL GAS SYSTEMS FOR WELDING, CUTTING AND ALLIED PROCESSES, obtainable from the
National Fire Protection Association, Batterymarch Park, Quincy, MA 02269
•NFPA Standard 70, NATIONAL ELECTRICAL CODE, obtainable from the National Fire Protection Association,
Batterymarch Park, Quincy, MA 02269
•NFPA Standard 51B, CUTTING AND WELDING PROCESSES, obtainable from the National Fire Protection Association,
Batterymarch Park, Quincy, MA 02269
•CGA Pamphlet P-1, SAFE HANDLING OF COMPRESSED GASES IN CYLINDERS, obtainable from the Compressed Gas
Association, 1235 Jefferson Davis Highway, Suite 501, Arlington, VA 22202
•CSA Standard W117.2, CODE FOR SAFETY IN WELDING AND CUTTING, obtainable from the Canadian Standards
Association, Standards Sales, 178 Rexdale Boulevard, Rexdale, Ontario, Canada M9W 1R3
•NWSA booklet, WELDING SAFETY BIBLIOGRAPHY obtainable from the National Welding Supply Association, 1900 Arch
Street, Philadelphia, PA 19103
•ANSI Standard Z88.2, PRACTICE FOR RESPIRATORY PROTECTION, obtainable from American National Standards
Institute, 1430 Broadway, New York, NY 10018

pg. 8
2.0 – GENERAL DESCRIPTION
The purpose of the Dearman Sleeve Clamp is to clamp a variety of pipe sleeves to the outside diameter of a pipe. The
Dearman Sleeve Clamp is available in a Standard models (DB-724 & DB-748), as well as a Heavy Duty models (DC-724 and
DC-748). The standard Sleeve Clamp uses a 5000 PSI (344 bar) hydraulic hand pump to tighten the sleeves over and around
the main pipe. The heavy duty sleeve clamp uses a 10,000 PSI (689 bar) hydraulic hand pump to tighten the sleeves over
the main pipe. Table 1 illustrates which sleeve clamp variant is recommended to use on a known list of sleeves. If the
operator is using the Dearman Sleeve Clamp on an unlisted sleeve, please contact Mathey Dearman Technical Sales for
application support at (918) 447-1288 or toll free (800) 725-7311.
Table 1: Sleeve Chain Clamp Compatibility Table

pg. 9
Figure 1: Standard Dearman Sleeve Clamp Components
Figure 2: Heavy Duty Dearman Sleeve Clamp Components
WARNING: The clamping capacity of the Dearman Sleeve Clamp is dependent on
the sleeve diameter, wall thickness, and tensile strength. Refer to Table 1. Call
Mathey Dearman (at 1-800-725-7311 or 1-918-447-1288) with any questions.
WARNING: Under no circumstances should additional chain be added to the
Mathey Dearman Sleeve Clamp to increase its operating range without contacting
Mathey Dearman at 1-800-725-7311 or 1-918-447-1288.

pg. 10
Table 2: Sleeve Chain Clamp Assembly Components by Model
Figure 3: Standard Sleeve Chain Clamp Main Block Figure 4: Heavy Duty Sleeve Chain Clamp Main Block
Model
Main
Block
(B1)
Chain Adj.
Mech.
(B2)
Spring
(B3)
Chain
Lock pin
(B4)
Socket Head
Cap Screw
(B8)
Lock Nut
(B9)
Safety
Pin
(B10)
DB-724
DB-724SS
DB-748
DB-748SS
DB-101 DB-102 DB-103 DB-131 11-12C0-300 1L-12C0-000 N/A
DC-724
DC-724SS
DC-748
DC-748SS
DC-101 DC-102 DB-103 DC-131 11-58C0-312 1L-58C0-000 DC-120
Table 3: Main Block Components
Model
Main
Block
Qty. – 1
Chain
Feet of
Chain
Required
Connecting
Link
Required
Qty. – 1
Hydraulic
Cylinder
Qty. – 1
Ram
Qty. – 1
Puller
Assembly
Qty. – 1
Threaded
Stud
Qty. – 1
Hydraulic
Hand
Pump Kit
Qty. – 1
Tool
Box
Qty. – 1
STANDARD SLEEVE CHAIN CLAMP
DB-724
DB-100
DB-300
6 1/2
DB-301
DD-200
DB-702
DB-703
DB-704
D106-KIT
D862
DB-724SS
DB-100
DB-300S
6 1/2
DB-301S
DD-200
DB-702
DB-703
DB-704
D106-KIT
D862
DB-748
DB-100
DB-300
15
DB-301
DD-200
DB-702
DB-703
DB-704
D106-KIT
D862
DB-748SS
DB-100
DB-300S
15
DB-301S
DD-200
DB-702
DB-703
DB-704
D106-KIT
D862
HEAVY DUTY SLEEVE CHAIN CLAMP
DC-724
DC-100
DC-300
6 1/2
DC-301
DC-701
DC-702
DC-703
N/A
D105-KIT
D862
DC-724SS
DC-100
DC-300S
6 1/2
DC-301S
DC-701
DC-702
DC-703
N/A
D105-KIT
D862
DC-748
DC-100
DC-300
15
DC-301
DC-701
DC-702
DC-703
N/A
D105-KIT
D862
Dc-748SS
DC-100
DC-300S
15
DC-301S
DC-701
DC-702
DC-703
N/A
D105-KIT
D862
B3
(Not Shown)

pg. 11
Figure 5: Chain Illustrations
(Note: The different chain materials are not captured by this picture. It merely illustrates the difference between a DB chain and a DC
chain).
Chain
Connecting
Link Standard Chain Clamp
DB-300 DB-301 DB-724, DB-748
DB-300S DB-301S DB-724SS, DB-748SSS
DC-300 DC-301 DC-724, DC-748
DC-300S DC-301S DC-724SS, DC-748SS
Chain
Chain Stop
Kit
(E1, E2, & E3)
Spacer
(E1)
Machine Screw
or Socket Head
Cap Screw
(E2)
Lock Nut
(E3)
DB-300, DB-300S DB-CS-KIT DB-320 14-01C0-212 1L-01C0-000
DC-300, DC-300S DC-CS-KIT 01-0185-004 10-38C0-234 1L-38C0-000
Clamp
Safety Whip
Check
DB-7XX, DB-7XXSS
DC-7XX, DC-7XXSS D101.09
DB-300, DB-300S
DC-300, DC-300S
Table 4: Chain and Connecting Links
Corresponding To Each Sleeve Chain Clamp
Table 5: Chain Stops Associated With Each Chain
Figure 6: Chain Stop Illustration
Table 6: Safety Whip Check

pg. 12
3.0 – Work Instructions
Before using the Dearman Sleeve Clamps, install top and bottom sleeves on pipe in accordance with proper safety
methods/protocol. Keep the lifting and retention device of the lower sleeve fully engaged until (on all of the Dearman
Sleeve Clamps) the slack has been taken out of the chain and the locking feature is engaged. Failure to do so can result in
serious injury and/or death.
Consult with the safety team for the appropriate number of sleeve chain clamps to use on a given pair of pipe sleeves.
Mathey Dearman recommends a minimum number for a given sleeve length below in Table 6, equally spaced from each
other and the ends of the sleeves.
Pipe Sleeve Length
Recommended Minimum Number
of Sleeve Chain Clamps
Up to 5’ (1.5m)
2
5’ to 8’ (1.5 to 2.5m)
3
Minimum 8’ (2.5m)
4
Table 7: Recommended Number of Sleeve Chain Clamps
3.1 Unpacking
1. Ensure that all components described in this Parts and Operating Manual are included in the box within which
each Dearman Sleeve Clamp kit is shipped.
2. Each Dearman Sleeve Clamp kit will contain two major components (see Figure 7).
a. The hydraulic cylinder with chain attached and the opposite end of the chain fed through the main block
assembly (locking feature engaged)
b. The hydraulic pump assembly w/ hose and quick disconnect fittings installed
WARNING:The Dearman Sleeve Clamp is designed for holding the weldable sleeve to the
outside diameter of the pipe during the welding process. It is not intended to lift the
sleeve, nor lift and / or support the pipe. Any attempt to do so can result in damage to
the device, pipe, sleeves, and serious injury and / or death.

pg. 13
Figure 7: Mathey Dearman Sleeve Chain Clamp components
3. Remove each component from the provided box. Perform a visual inspection on each component. Look for any
signs of damage and/or hydraulic fluid leaks. If any damage is discovered, DO NOT PROCEED. Take photographs
and contact Mathey Dearman Sales at (918) 447-1288 or (800) 725-7311.
a. If the Dearman Sleeve Clamp is either a DB-724, DB-724SS, DB-748, or DB-748SS model, verify that the
hand pump is the D106‐KIT (rated to 5,000 psi, 344 bar). The hand pump on the D106-KIT will be clearly
marked.
WARNING:Do not use any hand pump other than the D106-Kit with the DB-724, DB-
724SS, DB-748, or DB-748SS. Doing so can lead to damage to the device, pipe, sleeves,
and serious injury and/or death.

pg. 14
4. Verify the reservoir to the hydraulic cylinder is closed off by turning the pressure relief valve clockwise until it stops
(see Figure 8). If it has not been closed off, hold the hydraulic hose vertical (with the open connector pointing up)
while the reservoir is open, allowing the hydraulic fluid to drain back into the reservoir. Then, close off the
reservoir by turning the pressure relief valve clockwise.
Figure 8: Pressure relief valve
5. Provided all components are included and there are no visible signs of damage or hydraulic leaks, proceed to
installing the clamps over the sleeves.

pg. 15
3.2 Installation
1. Verify that the lifting and/or retention device for the sleeves is still properly engaged before proceeding.
2. Allow the hydraulic cylinder to hang down; place the main block on top of the top sleeve, as illustrated in Figure 9.
Figure 9: Main block placement
Crush / Pinch Hazard: From this step forward, crush and pinch hazards exist at:
-point where roller chain contacts the repair sleeve
-point where main block contacts the repair sleeve
-point where Jackscrews meet the repair sleeve
-the sliding point of the Universal Jackbar
Keep fingers and hands free from these areas.

pg. 16
3. Pull the hydraulic cylinder underneath the pipe, and wrap around the pipe/lower half of the sleeve, placing the
cylinder in the main block such that the cylinder/piston head is resting in its engagement position (see Figure 10).
Figure 10: Cylinder position after Step 3
4. Lock the cylinder in place on the main block by inserting the locking pin over the chain on the main block, as
illustrated in Figure 11.
Figure 11: Cylinders locked into position by Step 4
(for all model variants)

pg. 17
5. Pull the free end of the lifting chain through the main block until the slack between the chain and the sleeves has
been removed as illustrated in Figure 12.Do not remove the sleeve lifting and retention device yet.
Figure 12: Removing Excess Chain Slack
a. For the heavy duty sleeve chain clamp, ensure the safety pin to the DC-100 main block is in place before
proceeding.
Figure 13: DC‐100 main block with safety pin in place
Pinch Hazard: Both the locking pin and safety pin represent a potential pinch hazard.
WARNING:Failure to put the locking pin and (in the heavy duty sleeve chain clamp) the safety
pin in place can result in damage to the device, pipe, sleeves, and serious injury and / or death.

pg. 18
6. Attach included safety whip check onto hydraulic connection on cylinder. Ensure the rubber ring on the safety
whip check is positioned tight against the loop.
Figure 14: Safety Whip Check added to Hydraulic Cylinder
7. Attach safety whip check to hand pump hose. Ensure the rubber ring on the safety whip check is positioned tight
against the loop.
Figure 15: Safety Whip Check added to Hand Pump Hose
8. Attach the hand pump with the hose to the cylinder by inserting the male connector into the female connector
until they snap firmly together.
Figure 16: Hand Pump Hose connected to Hydraulic Cylinder

pg. 19
3.3 Operation
1. On each of the Dearman Sleeve Clamps, pump the handle on the hand pump assembly until the chain pulls tight
and the cylinder visually indicates it has started to extend its ram.
2. Hold for 30 seconds. Visually check for hydraulic leaks before proceeding further. If leaks exist, open up the
hydraulic reservoir on the hand pump to relieve the pressure and investigate further. If no leaks exist, proceed to
step 3.
Provided no leaks exist on any of the Dearman Sleeve Clamps (see Table 6for recommended minimum number
of sleeve clamps), it is safe to remove the lower sleeve lifting and retention device at this point.
3. Continue to increase pressure in the cylinders of each Dearman Sleeve Clamp until the desired weld gap has been
achieved. Always check for visual indications of hydraulic leaks. If a leak should be discovered at any time, re-
insert the original sleeve lifting and retention device and inspect the cylinder & hand pump connections.
4. Prior to welding, verify the hand pump and hose of each Dearman Sleeve Clamp is safely separated from the pre-
heat and/or welding device.
5. Proceed with preheat or welding as required.
6. Once the sleeves have been securely welded in place, open up the pressure relief valve on each cylinder.
7. Remove the Dearman Sleeve Clamp in the reverse order it was installed.
8. Close off the pressure relief valve on the hand pump reservoir.
9. Disconnect the hand pump / hose from the hydraulic cylinder, keeping the hose vertical with the connector
pointing upwards; thereby minimizing any loss of hydraulic fluid.
10. Keeping the hose vertical with the connector pointing upwards, open up the pressure relief valve on the hand
pump, allowing the excess hydraulic fluid to return to the well. Afterwards, close the pressure relief valve off for
storage.
11. Return all components to provided storage box.
WARNING
:Avoid weld / heat damage to the hydraulic hand pump and / or hose during the
welding process. Failure to do so can result in damage to the device, pipe, sleeves, and serious
injury and / or death.

pg. 20
4.0 – STORAGE
•Store the Dearman Sleeve Clamp in a clean, dry, and safe environment.
•Use the provided storage box if all possible to prevent damage to any of the components.
•Do not lay the chain clamp portion of the sleeve clamp on top of any hydraulic component (Hand Pump, Hydraulic
Cylinder, Hydraulic Hose, and Pressure Gauge if installed).
5.0 – RECYCLING OF COMPONENTS
5.1 ‐ Separation of the components
•Separate the components by category for a possible re-use or separate waste.
•Reference local regulations concerning disposal of components.
•The components of Chain Clamp are:
oStainless Steel:
Jackscrew swivel pad, main block, stainless steel roller chain, stainless steel Connecting Link
oCarbon Steel:
Threaded portion of Jackscrew, Ram Assembly, Puller Assembly, Threaded stud, Hydraulic Cylinder,
Handpump with reservoir, roller Chain, connecting link
6.0 – MAINTENANCE
•Follow manufacturer’s maintenance instructions for hydraulic cylinder & hand pump.
•Regular scheduled maintenance & inspections should be done before every use to ensure safe working order of
the clamp and should include:
oInspect clamp main block assembly for:
Cracks
oInspect Chain for:
Nicks
Arc marks
Abrasions
This manual suits for next models
7
Table of contents
Other Mathey Dearman Power Tools manuals
Popular Power Tools manuals by other brands
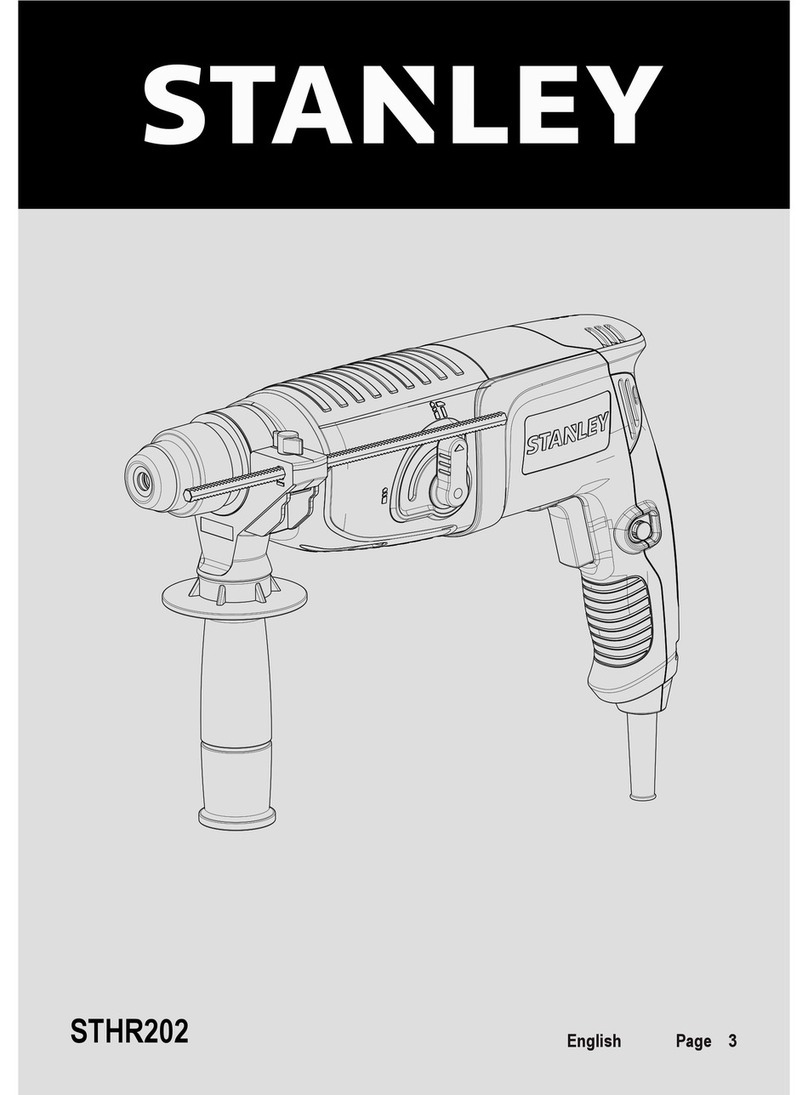
Stanley
Stanley STHR202 Original instructions
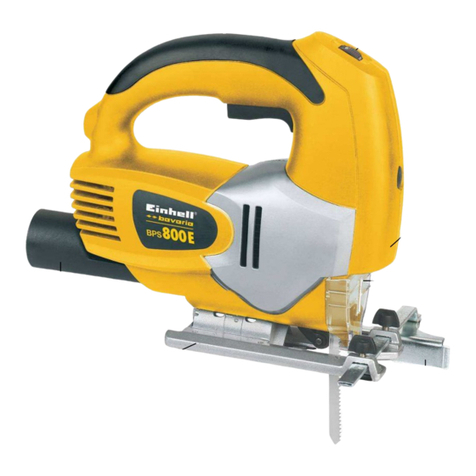
EINHELL Bavaria
EINHELL Bavaria BPS 800 E operating instructions
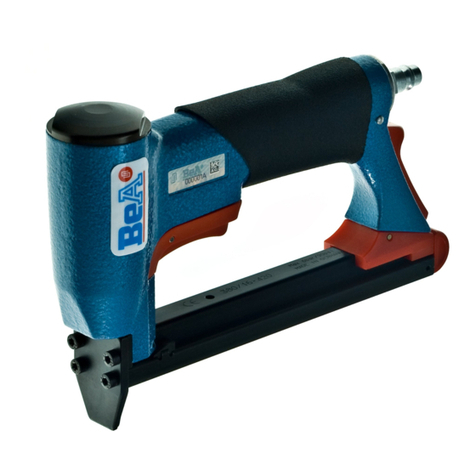
BEA
BEA 71/16-421 Operator's manual

Holzmann
Holzmann SB2516H user manual
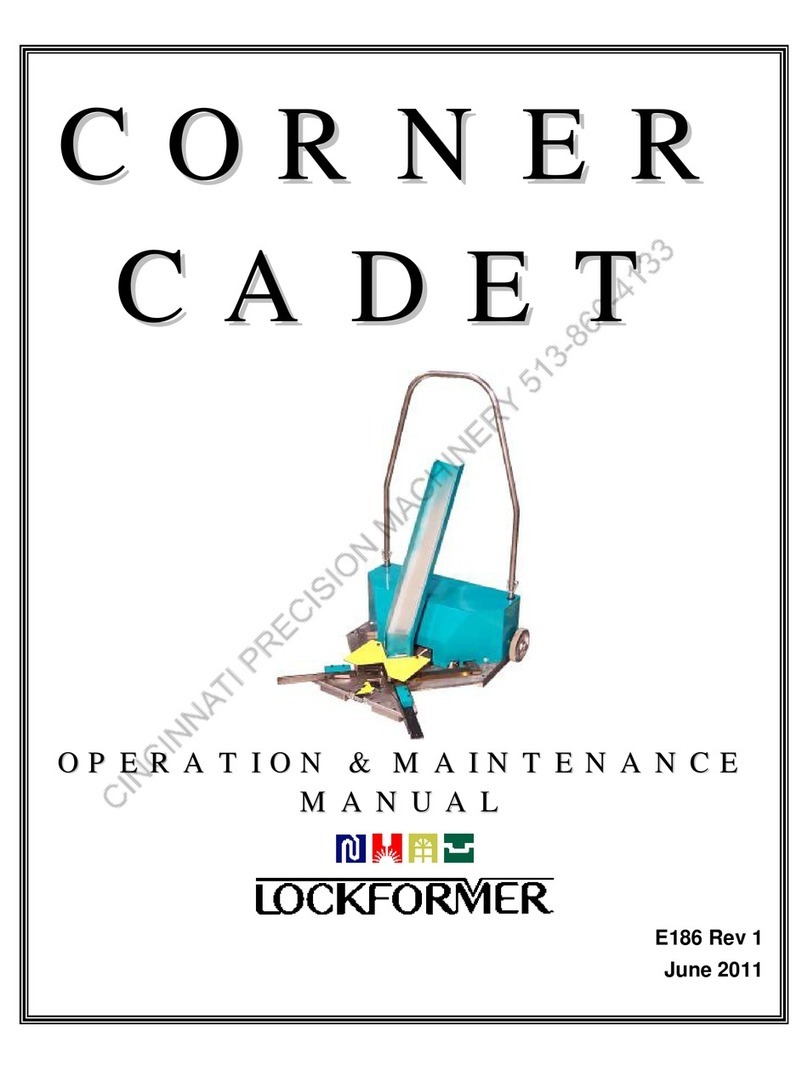
Lockformer
Lockformer Corner Cadet Operation & maintenance manual

Vigor Equipment
Vigor Equipment V2510 operating instructions