matson MA98411 User manual

Matson Programmable Voltage
Sensitive Relay
MA98411

Matson Programmable Voltage Sensitive Relay
The MPVSR is a ‘solid state’ electronic relay which is activated by sensing
the voltage of the circuits it is connected to. The voltages at which it will
either open or close are able to be programmed by the user, meaning this
product is suitable for a huge variety of applications. An example of this is
variable voltage output alternators increasingly found in modern vehicles.
This unit can be programmed to suit the characteristics of almost all 12
volt charging systems, and handle currents of up to 150amps continuous
(at 12VDC). The ‘cut in’ and ‘cut out’ activations are also able to be time
delayed to prevent VSR ‘chatter’, as well as being able to program an
alarm activation at a user dened voltage level.
The MPVSR is truly the next generation of charging control.
Primary Applications
Parallel Charging – Combining separate batteries or banks of batteries
together to charge from a single source or power.
Low Voltage Disconnect – Automatically switching off an electrical
load once the battery reaches a user dened voltage.
Automatic paralleling of batteries – Automatically combines two
battery banks for emergency power situations.
Automatic load switching – Using the control terminals, the MPVSR
can be a switch that will allow a load through it as long as the supply
voltage is between the user dened ranges.
A Heavy Duty Relay – For switching loads up to 150Amps.

FEATURES
• Solid state design means no moving parts to fail
• Fully user programmable to set voltage and time delays
• User programmable to set as either normally open or normally closed
• Isolated design means circuit cannot ‘backfeed’
• Isolation between control and load circuits
• LED indicators and display
• Alarm output for remote peace of mind
• Water and dust resistant enclosure
• Can be mounted in any orientation
• Over temperature protection
• Separate emergency over-ride connection
• 5 year warranty
WARNING
• Make sure you are familiar with the operation and installation
requirements of the MPVSR before installing or using.
• Please take into account the environmental limitations of the product.
The device is water and dust resistant, but is not designed to be
installed in wet or excessively dusty environments. These inuences
may shorten the life of the product and are not covered by warranty.
• Never leave the load terminals uncovered, there is a high risk of short
circuit, which may damage the device and it’s surroundings, including
people.
• The device should not be operated by children.
• Electricity can be dangerous! Short circuits can create sparks which
will ignite any present ammable substances. It is critical to ensure the
unit is installed in a well ventilated area AWAY FROM ANY SOURCES
OF FLAMMABLE SUBSTANCES. This includes batteries and fuel!

LAYOUT

INSTALLATION
Correct installation is critical for trouble free operation of the MPVSR.
Failure to properly install the unit may cause it to not work correctly, and
may also void its warranty. For best results please observe the following
instructions.
Choose a suitable location where the MPVSR can be mounted. Make
sure there is adequate ventilation to allow the unit to dissipate heat, and
try to install it in an area that is not too hot. Engine bays are not ideal, but
if adequately mounted it is an alternative. If mounting in an engine bay,
be sure to shield the unit from heat, dust and water. In other applications,
avoid moisture, dust and high vibration areas.
The unit can be mounted in any orientation (even upside down) but
must be on a hard at surface. Make sure you maintain at least 5cm of
clearance between the unit and any other objects. Utilise all four mounting
points, using appropriate fasteners for the application. Do not over tighten.
WIRING
It is very important to use the correct cable for your application. If the
cable gauge is too small you will suffer voltage drop, reduced current,
over heating of cabling and general poor performance, even failure. If
you have any doubts, consult the place of purchase for the cable, the
cable manufacturer, or an auto electrician. They will advise you on the
continuous load the cable can carry. This MUST match the load of your
application. Generally, when it comes to cable, bigger is better, and there
is no substitute for good quality cable and terminals.
Make sure the supply current or power is disconnected before connecting
anything to the MPVSR!
It is recommended that you install an inline fuse or circuit breaker as the
load protection. The fuse or circuit breaker should be rated to suit the
application, and should not exceed 150amps or the maximum rating of the
load cable being used.
Connect the required wiring to the control terminals, MAKING SURE TO
USE THE CORRECT POLARITY! Connecting the polarity incorrectly will
damage the unit and it will either need to be repaired or replaced. This is
not covered by warranty. Note; if you do not require an alarm or manual
over-ride switch, you do not need to connect anything to these terminals.

Note: It is very important to use appropriate terminations on your cables.
Poor connections can result in overheating, damaging the MPVSR. For
advice on termination please contact the place of purchase, an auto
electrician, or The Matson Group.
See below for termination examples.
CRIMP TERMINALS
FOR CONTROL
TERMINATION
COPPER LUG FOR
LOAD TERMINATION

INITIAL SET UP
Once the control wires are connected to the MPVSR and a power source,
the device is ready to be programmed to the user’s desired settings. It is
worth keeping in mind that you may not need to alter the factory settings,
which are listed in the table below.
12 Volt DC
Upper Voltage Limit 13.7 Volts
Upper Time Delay 5 Seconds
Lower Voltage Limit 12.8 Volts
Lower Time Delay 5 Seconds
Alarm Voltage Limit 12.0 Volts
Alarm Time Delay 10 Seconds
State of Contacts Normally Open (n - o)

CONTROL PANEL
To adjust the settings, observe the following
procedure:
NOTE; the buttons need to be pressed rmly in the centre or they will not
register. This is to avoid accidental changes to programming by bumping
the buttons.
Press the “SET” button once, the screen will show “OFF”
Press the “SET” button a second time. The screen will show the current
setting, relating to whichever LED is illuminated around the screen. The
rst to come up will be the UPPER LIMIT IN VOLTS. If this setting does
STATE
SET SELECTED
CONTROL ACTIONS
RESET
PUSH BUTTONS TO
SELECT CONTROL
ACTIONS
LCD DISPLAY

not need to be changed you can cycle through the parameters using the
“UP” and “DOWN” arrows.
To change a value:
When the value you want to change is displayed on the LED screen, press
the “SET” button and the value on the screen will begin to ash. While the
screen is ashing, use the “UP” and “DOWN” buttons to change the value.
Pressing “SET” again will stop the screen ashing and save the value.
Use the “UP” and “DOWN” buttons to cycle through to the next setting you
would like to change, and repeat the process.
Once you have set all the values to your requirements, take your hands off
the unit. After 10 seconds of inactivity the unit will switch off.
To reset the unit to the factory settings, follow the procedure above, cycle
through the settings until you reach “RESET”. Press the “SET” button
and see “NO” ashing. If you would like to reset the unit, use the “UP” or
“DOWN” button to cycle through to see “YES” and press “SET”. This will
restore the unit to factory settings and the screen will read “RST”.

COMMON APPLICATIONS
Dual Battery Charging
One of the major uses of the MPVSR is in dual battery charging
applications. The MPVSR is used to put the two batteries or banks of
batteries into parallel once the primary battery or bank reaches a certain
voltage. In a 4x4 application, where a secondary battery is used for
accessories such as lights, fridges or winches, it is important to protect the
vehicles starting battery from being attened by the accessories, making
sure you can always start the vehicle and drive away. The MPVSR,
installed between the starting battery and the secondary battery, can put
the batteries in parallel once the starting battery is charged, or reaches
a user dened voltage, allowing charging of both batteries to occur while
the vehicle is driving. If a load is placed on the batteries whilst in parallel,
and the starting battery drops to a pre-determined voltage, the MPVSR will
disconnect the two batteries, allowing the secondary battery to power the
accessories and protecting the starting battery.
The ability to determine the cut-in and cut-out voltages of the
MPVSR, specic to the vehicle, makes this product perfect for
modern vehicles with VARIABLE VOLTAGE OUTPUT ALTERNATORS.
Setting Guide: (note, this setup requires the MPVSR bet programmed
‘normally open’)
UPPER LIMIT IN VOLTS: This is the voltage that, when reached by
the starting/primary battery, the MPVSR will put the batteries in parallel
and charge both batteries. For vehicles with a VARIABLE VOLTAGE
ALTERNATOR, this will need to be set relatively low, at a point just below
the higher voltage output of the alternator. You will need to contact the
manufacturer or dealership to nd this information.
LOWER LIMIT IN VOLTS: This is the voltage level that, when reached by
the starting/primary battery, the MPVSR will disconnect the batteries from
the parallel circuit and isolate the starting/primary battery. This needs to be
set at a voltage level greater than the minimum voltage level required to
start the vehicle
UPPER DELAY IN SECS: This setting, in seconds, is the amount of delay
the MPVSR will wait to put the batteries in parallel, after the primary/
starting battery reaches the UPPER LIMIT IN VOLTS. This delay stops
VSR ‘chatter’, caused by the primary battery voltage dropping when the
batteries are put in parallel and the VSR continuously connecting and

disconnecting the batteries. If VSR chatter is experienced, increase the
delay in 20 second increments.
LOWER DELAY IN SECS: This setting determines how long the primary/
starting battery will be allowed to remain at the lower limit in volts before
the MPVSR cuts out and isolates the primary/starting battery. A delay is
useful here because the voltage of the starting battery may drop below
this point for a few seconds when starting the vehicle, but return to a safe
level quickly. In this scenario you would not need to isolate the primary/
starting battery.
DUAL BATTERY WIRING EXAMPLE
+ SENSE WIRE
12 Volt Primary
Battery
(Sensing)
12 Volt Secondary
Battery
(Charging)
BUZZER
MUTE
SWITCH
(OPTIONAL)
REMOTE
OVERRIDE
SWITCH

Low Voltage Disconnect
The MPVSR can be used as a low voltage cut-out device when wired
in line between the load and the power source. This would be used in
situations where it is important to make sure the power source is not
drained too far, like a starting battery in a car, or a lithium battery being
used as a power supply. In the car example, a attened battery means you
can’t start the engine and you are stuck. The lithium battery power supply
can be destroyed easily if it is discharged too far. In both case, low voltage
protection will allow for peace of mind and longer life expectancy for the
products involved.
Setting Guide: (note, this setup requires the MPVSR bet programmed
‘normally open’)
UPPER LIMIT IN VOLTS: This is the setting that determines when the
power would be re-connected and allow operation to resume once the
power source has returned to an acceptable level. In the car example,
this would be when the battery has been charged back to a safe voltage
to start the vehicle. It can be as little as 0.1V above the LOWER LIMIT IN
VOLTS.
LOWER LIMIT IN VOLTS: This is the voltage level where you want to
disconnect the load from the power source to prevent it getting too low. In
the car scenario, this would be the voltage level where if it got any lower
the battery would not be able to start the car.
UPPER DELAY IN SECS: This is the delay setting for re-connecting the
load to the power source. Delaying the re-connection allows the voltage at
the power source to stabilise before the load is connected again. This is
more important when the power supply is a battery.
LOWER DELAY IN SECS: This is the delay setting for disconnecting
the load. In the car scenario, without a delay set, the MPVSR might
disconnect the load when you try to start the vehicle, as the large load
when starting can drop the battery voltage signicantly for a few seconds.
After starting the voltage would generally rise again to a safe level,
meaning it would not be necessary to disconnect the load from the battery.
In this situation it could even prevent you starting the vehicle.

LOW VOLTAGE DISCONNECT WIRING EXAMPLE
12 Volt Primary
Battery
(Sensing)
BUZZER
LOAD
150A
MAX
MUTE
SWITCH
(OPTIONAL)
REMOTE
OVERRIDE
SWITCH
+ SENSE WIRE

AUTOMATIC PARALLELING OF BATTERIES
The MPVSR can be programmed to connect two batteries or banks
together in parallel if the voltage of the primary battery gets to a pre-
determined voltage. For example, if the starting battery on a boat was
going at, the MPVSR could automatically connect it to the secondary or
house batteries to enable it to start the motor.
CAUTION: This functionality must be thought through carefully. If your
starting battery is going at, and you automatically connect your house
batteries to it, and it continues to go at without you knowing, you will be
stuck with two at battery banks! It is highly recommended to use an alarm
when using this function, so you know when the batteries are in parallel.
Setting Guide: (note, this setup requires the MPVSR bet programmed
‘normally closed’)
UPPER LIMIT IN VOLTS: This is the setting where the batteries will be
disconnected from each other after the primary battery reaches a sufcient
charge voltage.
LOWER LIMIT IN VOLTS: This is the setting that determines when the
batteries will be connected in parallel. This should be set at the point
where the starting battery might no longer be able to start the motor, and
would require assistance from another battery bank.
UPPER DELAY IN SECS: This is the delay, in seconds, before the
batteries are disconnected after the starting battery reaches a sufcient
voltage level.
LOWER DELAY IN SECS: This is the delay, in seconds, before the
batteries are connected into parallel. This should be around the 10 second
mark to accommodate for the voltage sag of the battery under a starting
load.

AUTOMATIC PARALLELING WIRING EXAMPLE
+ SENSE WIRE
12 Volt Primary
Battery
(Sensing)
12 Volt Secondary
Battery
(Charging)
BUZZER
MUTE
SWITCH
(OPTIONAL)

AUTOMATIC LOAD SWITCHING
The MPVSR can be programmed to perform automatic load switching,
by using the control terminals for sensing a desired voltage range. This
is particularly useful in remote or unmanned situation where equipment
needs to be operated, but also protected from over-voltage and under-
voltage damage scenarios. For example, a ashing light on a remote
tower needs to be activated at night, but it is powered by a lithium battery
bank that is very expensive. Wiring the light switch in series with the
control terminals (positive or negative) and setting the upper and lower
voltage limits to the desired range means that the light can be switched on
and off as needed, but only if the battery voltage is within the safe range
set by the user.
Setting Guide: (note, this setup requires the MPVSR bet programmed
‘normally open’)
UPPER LIMIT IN VOLTS: This is the setting where the voltage would be
re-connected to the light to allow it to operate as required again. In this
example it would be the safe voltage level for the batteries to operate
again.
LOWER LIMIT IN VOLTS: This is the voltage level at which the light
would be disconnected from the power source so as not to over-discharge
the battery bank. This setting would be determined by the battery
manufacturers guidelines.
UPPER DELAY IN SECS: This is the delay setting for re-connecting the
load to the power source. Delaying the re-connection allows the voltage at
the power source to stabilise before the load is connected again.
LOWER DELAY IN SECS: This is the delay, in seconds, before the power
is disconnected from the light after the voltage reaches the LOWER LIMIT
IN VOLTS. A delay here can be useful to prevent VSR chatter due to
transient voltages and slight dips in power levels.

AUTOMATIC LOAD SWITCHING WIRING
EXAMPLE
LOAD
150A
MAX
FLOAT
SWITCH

CONVENTIONAL HEAVY DUTY RELAY
The MPVSR can be used as a conventional heavy duty relay for switching
loads up to 150Amps continuous current at 12VDC. The control device
is wired in series with the control wires and activated as required. The
voltage settings should be programmed out of any range that would affect
operation. Also, the relay can be set to either normally closed or normally
open depending on requirements.
CONVENTIONAL HEAVY DUTY RELAY WIRING
EXAMPLE
LOAD
150A
MAX
CONTROL
SWITCH

SPECIFICATIONS
Part Number MA98411
Application Voltage 12 Volt DC and 24 Volt DC
Operating Voltage Sensing: 9V DC Minimum, 38V DC Maximum
Switching: 33V DC Maximum
Continuous Contact
Rating
150 Amps Maximum (rated at 40oC)
Momentary Contact
Rating
500 Amps DC for a period of 10 seconds at
10% duty cycle (rated at 40oC)
Contact State User selectable normally open or closed
Environmental
protection
To IP66
Electrical Protection Thermal overload shutdown
Standby Current Draw 10mA at 13.5V DC and 23mA at 27.0V DC
Standby Current Draw 35mA at 13.5V DC and 55mA at 27.0V DC
Operating Temperature Ideally -25oC to +50oC
Alarm Output Signal Equal to input voltage to 200mA maximum
Operating Humidity Ideally should not exceed 95%
Enclosure Housing E-coated A360 (ADC 3) die cast aluminium
Enclosure Cover and
Terminal Protector
Injection moulded electrical grade ABS/PC
Load Terminals Tin plated copper stud
Control Terminals Tin plated brass contact
Dimensions 135mm L x 85mm W x 65mm H
Weight 0.55kg

DIMENSIONS
H
65mm
L
135mm
W
85mm
Table of contents
Popular Relay manuals by other brands
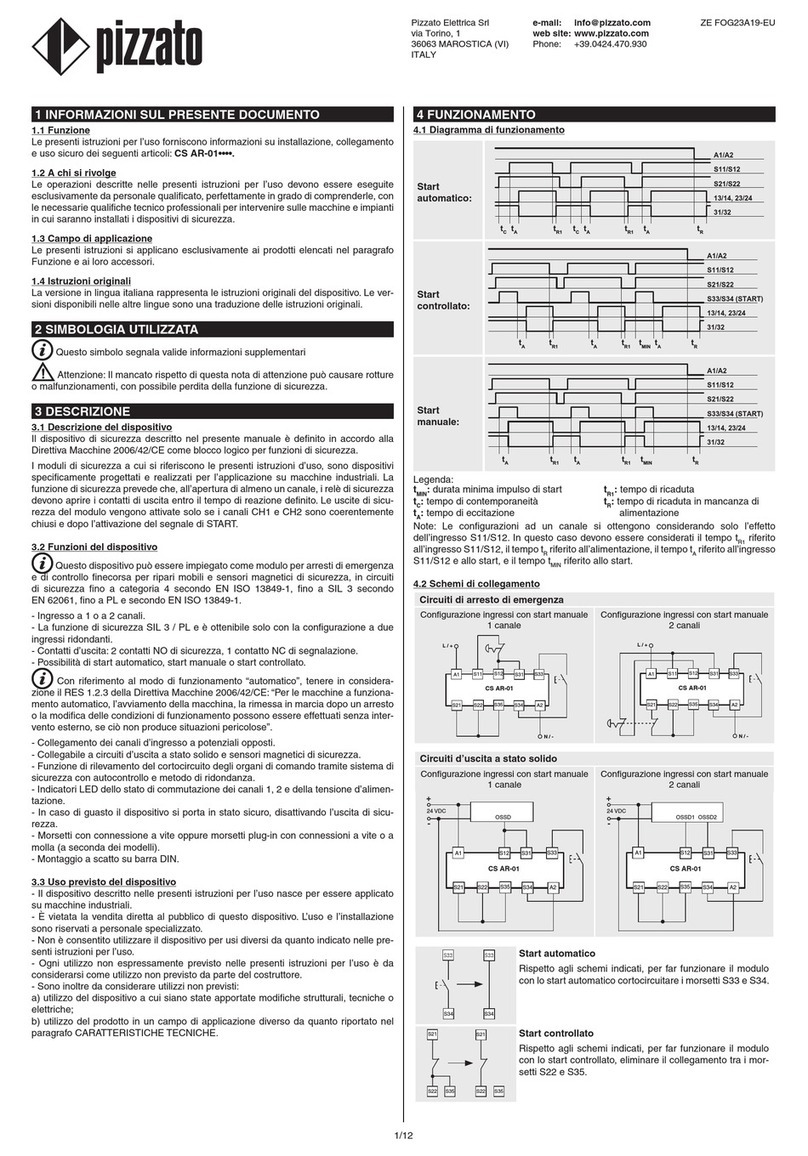
pizzato
pizzato CS AR-01 Series operating instructions
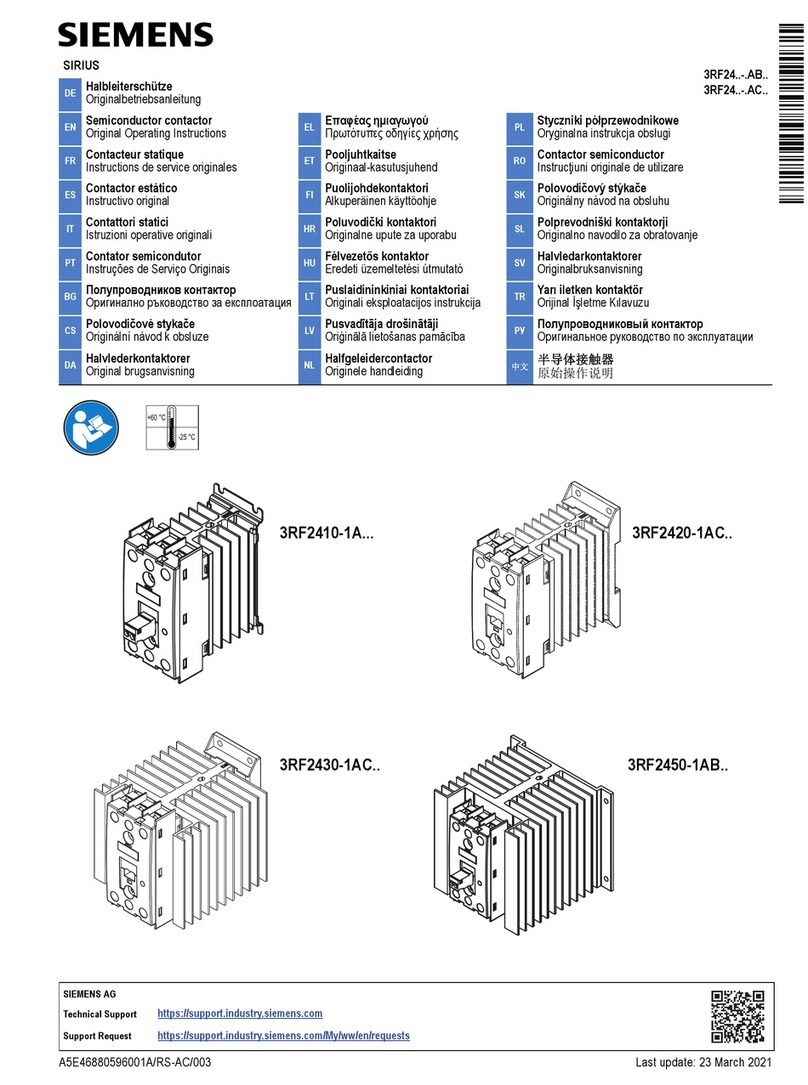
Siemens
Siemens SIRIUS 3RF24 AB Series operating instructions
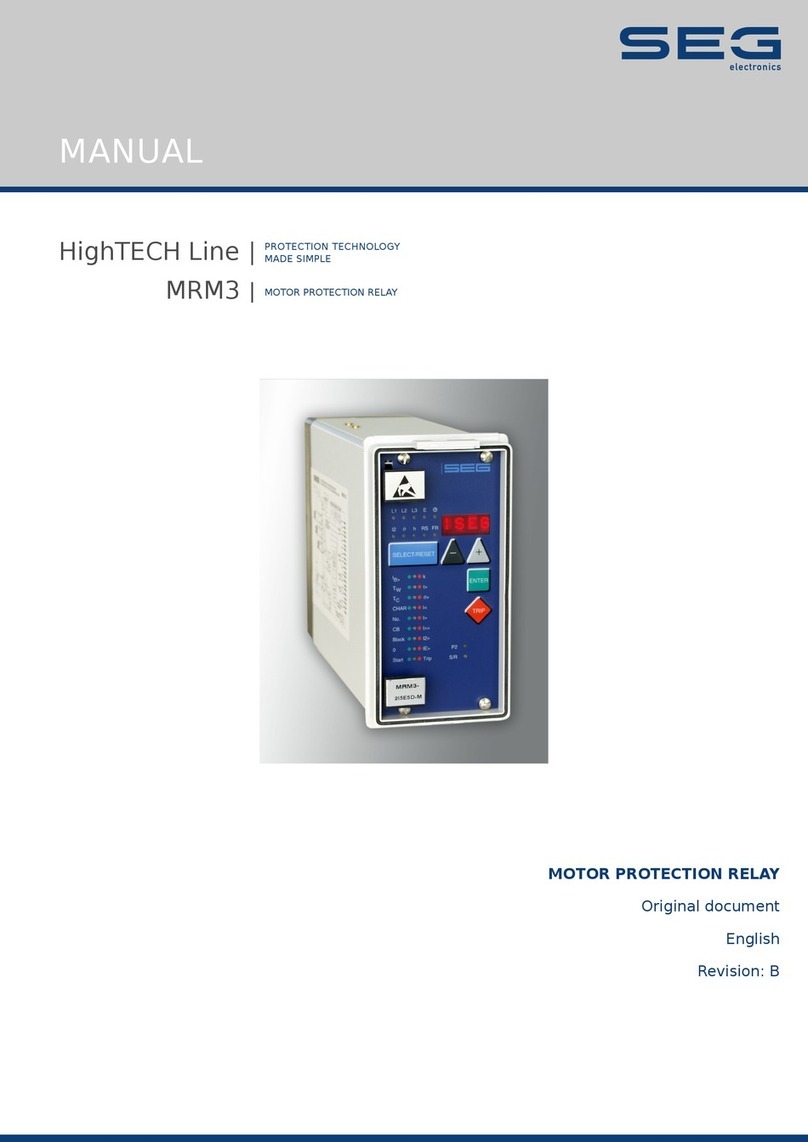
Seg
Seg MRM3 manual
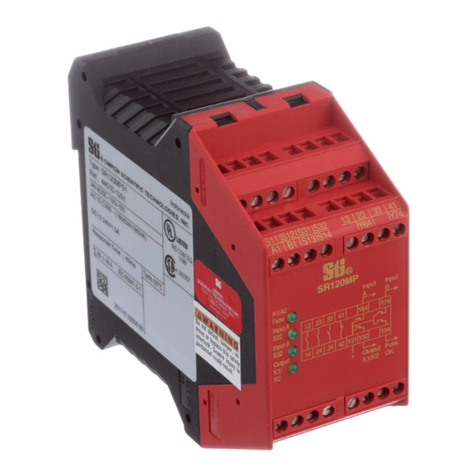
Omron
Omron Sti SR120MP operating instructions
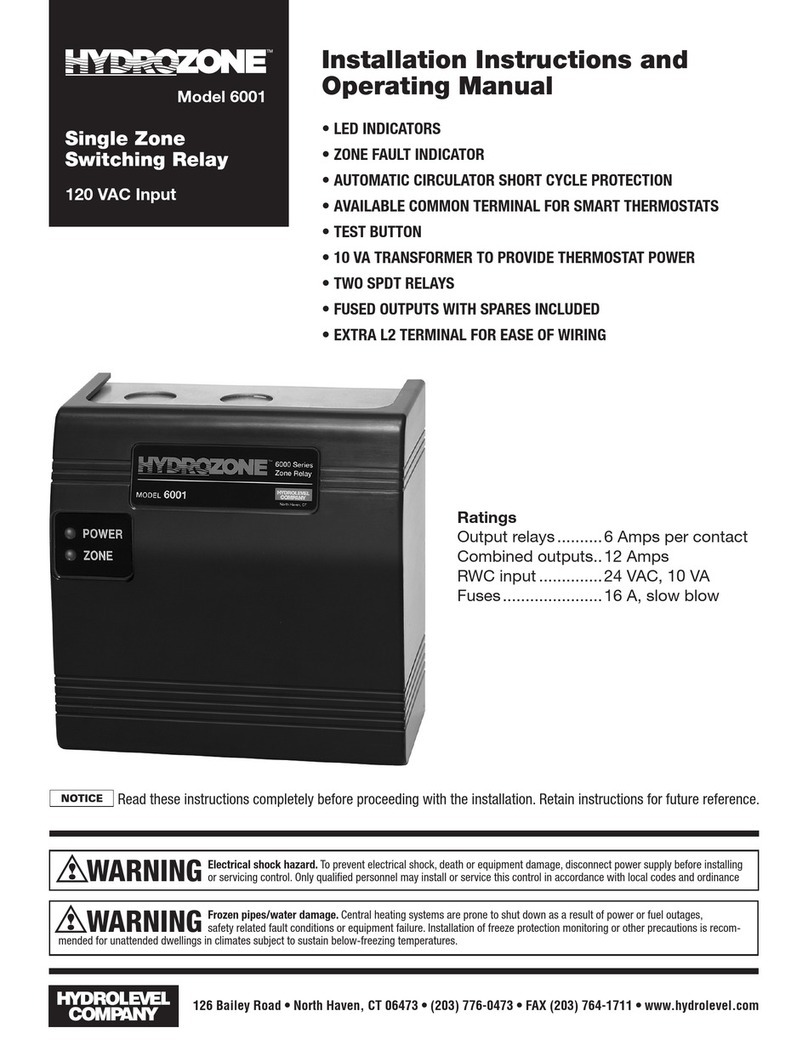
Hydrolevel Company
Hydrolevel Company HYDROZONE 6000 Series Installation instructions and operating manual
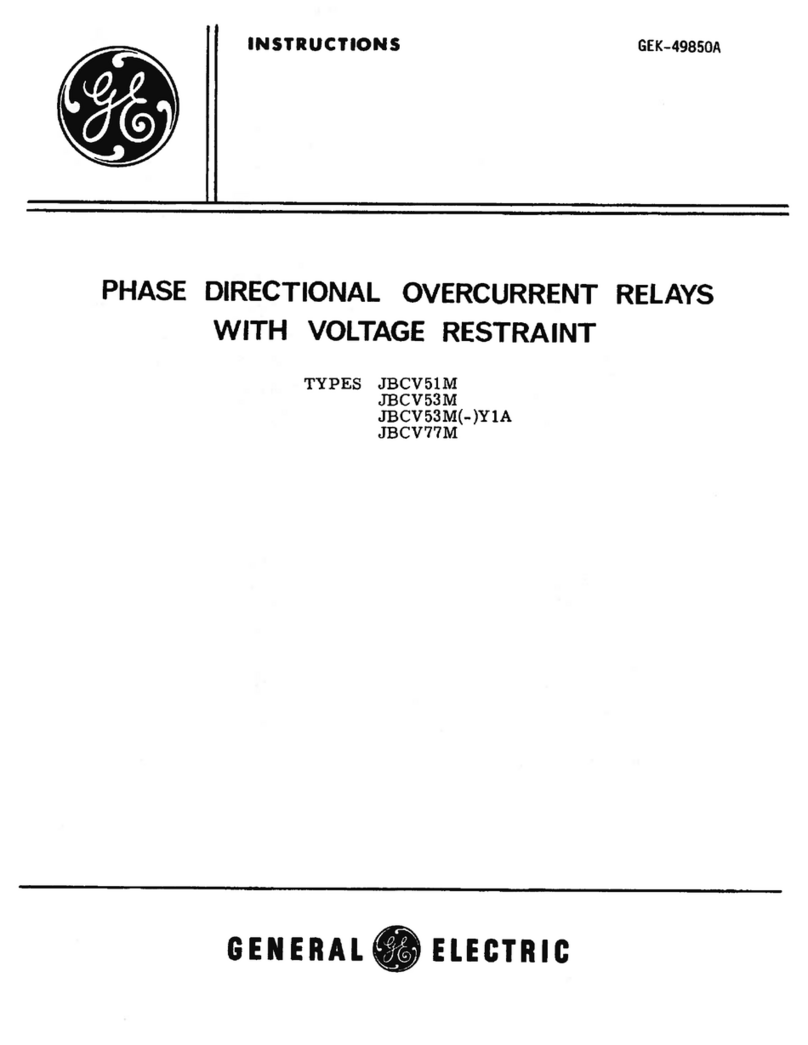
GE
GE JBCV51M instructions