MD MD-800 SERPENTINE Manual

MAINTENANCE
AND
SERVICE MANUAL
MODEL MD-800 SERPENTINE
CHASSIS
DYNAMOMETERS
MUSTANG DYNAMOMETER
Revision Release Date Initial
A 21 SEPT 18 NK

MODEL MD-800 SERPENTINE DYNAMOMETER SERVICE MANUAL
ii MODEL MD-800 SERPENTINE MAINTENANCE AND SERVICE
Information in this document is subject to change without notice. No
part of this document may be reproduced or transmitted in any form
or by any means, electrical or mechanical, for any purpose, without
the express written permission of Mustang Dynamometer.
Copyright 2018
Ganzcorp Investments, Inc. dba Mustang Dynamometer
All rights reserved
Mustang Dynamometer
2300 Pinnacle Parkway
Twinsburg, Ohio 44087 USA
Telephone: (330) 963-5400 * Fax: (330) 425-3310

MUSTANG DYNAMOMETER
MODEL MD-800 SERPENTINE MAINTENANCE AND SERVICE iii
NOTICE
This manual has been designed and written to provide useful information
about Mustang Dynamometer equipment and systems. Every effort has
been made to make this manual as complete as possible, but no
warranty or fitness is implied.
The information contained in this manual is provided on an “as is” basis.
Neither the author of this manual nor the management and owners of
Mustang Dynamometer shall have either liability or responsibility to any
person or entity with respect to any loss or damages arising from the
information contained in this manual.

MODEL MD-800 SERPENTINE DYNAMOMETER SERVICE MANUAL
iv MODEL MD-800 SERPENTINE MAINTENANCE AND SERVICE
WARRANTY
LIMIT OF LIABILITY
Mustang warrants that the product(s) that is the subject of this sale is free from defects in
material. The duration of this warranty is one year from date of shipment on all Mustang-related
components. Components not manufactured by Mustang will carry the original manufacturer’s
warranty, typically 90 days for all electronic-related components. All warranty claims must be
processed through Mustang.
If a problem arises within the applicable warranty period, it is the responsibility of the purchaser
to (a) promptly notify Mustang in writing (b) obtain a RMA Number from Mustang (c) return to
Mustang the component(s) that are claimed to be defective (transportation charges must be
prepaid by the purchaser). RMA Number must be clearly marked on outside of package(s).
Within a reasonable time after such notification, Mustang will correct any defect(s) in
component(s). If Mustang is unable to repair the component after a reasonable number of
attempts, or if Mustang determines at any time the repair is impracticable, Mustang will provide
a replacement with like or similar component(s). The purchaser is responsible for all
transportation expenses to and from Mustang and all labor expenses associated with removal and
replacement of the component(s) as well as labor involved to repair component(s). Mustang will
bear the expense of parts only. These remedies are the Purchaser’s sole remedies for breach of
warranty.
The expiration of the warranty period, use of the product for purposes other than those for which
it is designed, other abuse or misuse, unauthorized attachments, modifications, or disassembly,
or mishandling of the product during shipping, shall end all liability of Mustang.
In no case shall Mustang be liable for any special, incidental, or consequential damages based
upon breach of warranty, breach of contract, negligence, strict tort, or any other legal theory.
Such damages include but are not limited to, loss of profits, loss of savings or revenue, loss of
use of the product or any associated equipment, cost of capital, cost of any substitute equipment,
facilities or services, downtime, the claims of third parties including customers, and injury to
property.
Unless modified in writing and signed by officers of both parties, this agreement is understood to
be the complete and exclusive agreement between the parties, superseding all prior agreements,
oral or written and all other communications between the parties relating to the subject matter of
the agreement.
GANZCORP INVESTMENTS INC. dba MUSTANG DYNAMOMETER

MUSTANG DYNAMOMETER
MODEL MD-800 SERPENTINE MAINTENANCE AND SERVICE v
DANGER
Keep limbs, hair, jewelry and clothing away from
the moving rolls. When operating a vehicle on the
machine, remain inside vehicle until the rolls have
stopped. Cover the rolls when the equipment is not
in use.
DANGER
Do not operate or perform any maintenance on your
equipment until you have carefully read this manual
in its entirety making sure that you understand all
of the material presented in each section.
CAUTION
Unsafe operating practices can lead to potentially
dangerous situations when your machine is running.
Only properly trained and responsible personnel
should attempt to operate this machine.
CAUTION
Removal and disassembly instructions in this manual
have been reduced to a minimum for ease of
readability.
Only experienced maintenance personnel should
attempt to install and/or make repairs to this
machine.

MODEL MD-800 SERPENTINE MAINTENANCE AND SERVICE 1-1
SECTION
INTRODUCTION 1
CONTENTS
1.1 DESCRIPTION................................................................................................... 1-3
1.2 GENERAL SAFETY ISSUES ................................................................................. 1-4
1.3 OPERATIONAL SAFETY ISSUES........................................................................... 1-4
1.4 MAINTENANCE SAFETY ISSUES .......................................................................... 1-5
1.5 ENVIRONMENTAL DATA ..................................................................................... 1-6
1.6 INSTALLATION DATA ......................................................................................... 1-6
1.7 NAMEPLATE DATA............................................................................................ 1-6
1.8 IF YOU NEED HELP........................................................................................... 1-6

MODEL MD-800 SERPENTINE DYNAMOMETER SERVICE MANUAL
1-2 MODEL MD-800 SERPENTINE MAINTENANCE AND SERVICE

SECTION 1-INTRODUCTION MUSTANG DYNAMOMETER
MODEL MD-800 SERPENTINE MAINTENANCE AND SERVICE 1-3
1.1 DESCRIPTION
This manual contains maintenance and service information for Model MD-800-SE-DR
Serpentine Chassis Dynamometers. Most maintenance and service procedures are similar for all
model dynamometers.
Major system components include the dynamometer, and the control system. Major
dynamometer components include the frame, rolls, wheelbase adjustment system, drive belt and
Power Absorber Unit (PAU).
Refer to Figure 2.1 for an illustration of the major components of the MD-800 Serpentine
Dynamometer.

MODEL MD-800 SERPENTINE DYNAMOMETER SERVICE MANUAL
1-4 MODEL MD-800 SERPENTINE MAINTENANCE AND SERVICE
1.2 GENERAL SAFETY ISSUES
Be Knowledgeable ... Do not attempt to operate, maintain or service your Mustang Chassis
Dynamometer System until you have familiarized yourself with the equipment by reading the
instructions in this manual.
Act Responsibly ... Exercise caution and discretion when operating or performing maintenance
on the dynamometer. Always observe typical, common sense test area precautions.
Beware of Projectiles ... Tires that are rotating can throw off stones and other projectiles. Wear
approved safety glasses when in the vicinity of the vehicle being tested.
Protect Your Ears ... Always wear approved ear protection when working near the
dynamometer.
Beware of Being Grabbed ... Keep limbs, hair, jewelry, and clothing away from the moving
dynamometer components.
Pay Attention ... Maintain acute awareness when the dynamometer rolls are in motion.
1.3 OPERATIONAL SAFETY ISSUES
For ALL
Vent Engine Exhaust ... Provide adequate room ventilation. High concentrations of engine
exhaust can be deadly. Do not operate your dynamometer without proper ventilation. The
ventilation system should provide four (4) air changes an hour in the shop and six (6) air
changes an hour for the pit.
types of testing, use chains, straps, Ratchet binders or strap ratchet binders of suitable
size with floor anchors to safely perform testing. Be careful not over-tension the chains or
straps. All of these safety devices should be used when testing a vehicle. The above items are
not supplied by Mustang Dynamometer. We recommend a minimum of 3/8” diameter chain with
3/8” Ratchet binders. For front wheel drive vehicles, two chains and binders should be used to
restrain the front axle and a minimum of one chain/binder for the rear axle. For rear wheel drive
vehicles, 2 chains/binders should be used to secure the rear axle.
Monitor Carbon Monoxide ... Make sure you have installed a carbon monoxide monitor in the
dynamometer bay.
Guarding ... Provide floor markings and protective guard railings for customer/operator
protection. NEVER operate the dynamometer with any cover panels removed unless specifically
directed to do so elsewhere in this manual.
Keep Clear of Rolls ... Stay away from the rolls when in operation.
Check Tires ... Before driving the test vehicle onto the dynamometer, be sure to check the
vehicle’s tires for proper inflation. Inspect the tires for any signs of damage and remove any
embedded objects from the tread.
Restrain Vehicle Movement ... During dynamometer operation, make sure that the restraints
are in position.
Proper Clearance ... Always ensure that there is a clearance of at least four (4) feet to the
front, rear, and sides of the dynamometer.
Stay Seated ... The vehicle operator MUST remain in the driver’s seat at all times during a
drive-cycle test. Do NOT attempt to get in or out of the vehicle when the dynamometer rolls are
moving.
If in Doubt, STOP! ... Stop the equipment immediately if you have any doubt about the safe
operating condition of the dynamometer and/or the correctness of any procedures that you are
performing.

SECTION 1-INTRODUCTION MUSTANG DYNAMOMETER
MODEL MD-800 SERPENTINE MAINTENANCE AND SERVICE 1-5
1.4 MAINTENANCE SAFETY ISSUES
Electrical Shock Hazard ... Turn off electrical service to the system before performing any
maintenance activity. Turn off the main breaker in your breaker box before working on anything
related to the PAU or motor.
No Jewelry ... Remove any jewelry before performing any electrical or mechanical
troubleshooting, repair, etc. on the dynamometer.
Cover Panels ... Use extreme caution around drive mechanisms and moving parts when
operating the dynamometer with any of its cover panels removed from the chassis assembly.
Avoid Straining Yourself ... Be careful when lifting dynamometer cover panels. Be careful
when replacing belts, couplings, or bearings.
Air Pressure ... Make sure that there is no shop air to the dynamometer when working on lift
plates or air bags.
Watch Your Hands ... Never put your hand between the lift plate and roll when shop air supply
is connected to the dynamometer.
NEVER, NEVER, NEVER! ... Never pull on the drive belt in order to spin the rolls.
Check Tightness ... Make sure that all bolts on the dynamometer are tight and all couplings are
properly secured.

MODEL MD-800 SERPENTINE DYNAMOMETER SERVICE MANUAL
1-6 MODEL MD-800 SERPENTINE MAINTENANCE AND SERVICE
1.5 ENVIRONMENTAL DATA
This equipment is rated for the following environmental conditions:
Indoor use only.
Temperature: -10o to 49oC
Maximum Relative Humidity: 95% Noncondensing
Altitude:Up to 2000 meters
Pollution Degree 1 in accordance with IEC 664
1.6 INSTALLATION DATA
It is recommended that the circuit breaker supplying power to the dynamometer equipment be
located in close proximity to the dynamometer, at minimum, within the same room.
Installation and mounting hardware are provided with every Dynamometer and shall be used
regardless of a Pit or Floor mount installation. Hardware provided is 5/8 X 4.5” Thunderstud
concrete anchors (MD# 20013614). Anchor stud holes should be located to match the holes in the
mounting feet on the dynamometer frame.
Tools Required: 1 - Hammer Drill with 5/8” concrete or Masonry bit. 1 - Hammer. 1 - 3/4” Open
end wrench. Various sizes flat Steel shim stock. 1 - 4’ level.
Using hammer drill mark and drill holes in concrete a minimum of 4.5” deep for 4.5” thunderstud.
Ensure holes are clean of any debris prior to attempting installation of Thunderstud. Place
Dynamometer into pit or onto floor at installation site. Check level of dynamometer, use flat steel
shim stock (customer supplied) as necessary to level dynamometer to floor. Level dynamometer in
two planes; (1) Place level on top of rolls parallel with a roll and (2) place level across a front roll
and rear roll. Shim unit by positioning shim near all the anchor locations as well as every 12”
under the main frame rails. Insert thunderstud with flat washer and nut attached into anchor foot
and hole previously drilled into concrete. Using hammer, pound thunderstud into hole until nut is
flush with anchor foot. Ensure anchor foot is also in contact with dynamometer frame. Using ¾”
wrench, tighten nut to 50 ft-lbs.
Take care not to over tighten the nuts, as this may cause damage to the frame of the dynamometer,
the thunderstud, or the concrete.
1.7 NAMEPLATE DATA
The nameplate on the dynamometer frame contains valuable information should it be necessary to
contact Mustang. Besides the model number, date manufactured, and revision level data, the
nameplate contains the dynamometer serial number. Have this number handy when contacting
Mustang Dynamometer.
1.8 IF YOU NEED HELP
Much effort has been extended to make this manual complete and accurate. However, if there
are any questions please contact a Mustang Dynamometer representative at:
Mustang Dynamometer
2300 Pinnacle Parkway
Twinsburg, Ohio 44087 USA
Telephone: (330) 963-5400
Fax: (330) 425-3310

MODEL MD-800 SERPENTINE MAINTENANCE AND SERVICE 2-1
SECTION
PREVENTIVE MAINTENANCE 2
CONTENTS
2.1 INTRODUCTION................................................................................................. 2-3
2.2 PREVENTIVE MAINTENANCE............................................................................... 2-5
2.3 LUBRICATION................................................................................................... 2-6
2.4 INSPECTION ..................................................................................................... 2-8

MODEL MD-800 SERPENTINE DYNAMOMETER SERVICE MANUAL
2-2 MODEL MD-800 SERPENTINE MAINTENANCE AND SERVICE

SECTION 2-MAINTENANCE MUSTANG DYNAMOMETER
MODEL MD-800 SERPENTINE MAINTENANCE AND SERVICE 2-3
2.1 INTRODUCTION
This section contains information and procedures for preventive maintenance of the
dynamometer. Refer to Table 2.1 for a list of recommend tools and Table 2.2 for a list of
consumable items necessary for maintenance of the dynamometer. A Preventive Maintenance
Time Table, Table 2.3, provides recommended service intervals. Preventive maintenance
procedures follow. Figure 2.1 below identifies the major components of the dynamometer.
FIG 2.1
MAJOR DYNAMOMETER COMPONENTS

MODEL MD-800 SERPENTINE DYNAMOMETER SERVICE MANUAL
2-4 MODEL MD-800 SERPENTINE MAINTENANCE AND SERVICE
Table 2.1
L
IST OF
R
ECOMMENDED
T
OOLS
ITEM
USE ON
(2) 1-1/8-inch combination
wrenches
Brake Pad Replacement
Idler Attachment bolts
15/16-inch socket
15/16-inch wrench
2 and 2-3/16-inch Pillow Block Bearing Bolts
PAU Bracket Bolts
Pulley Bolts
3/4-inch socket
3/4-inch wrench
1-1/2-inch Pillow Block Bearing Bolts
Load Cell Bolts
1/8-inch Allen wrench
Coupling set screws
9/64-inch Allen wrench
Speed sensor
5/32-inch Allen wrench
1-1/2-inch Pillow Block Bearing Set Screws
3/16-inch Allen wrench
2 and 2-3/16-inch Pillow Block Bearing Set Screws
1/4-inch Allen wrench
Coupling set screws
Torque wrench, 0-250 inch-pounds.
Torque Measurements
Torque wrench, 0-100 foot-pounds.
Torque Measurements
Pipe wrench
Brake Pad replacement
Feeler gauges
Speed Sensor
Belt Tension Tester
Belt Tension
Straight Edge
Belt Tension
Digital Multi-Meter
Electrical signals and connections
Table 2.2
L
IST OF
C
ONSUMABLE
I
TEMS
Item
Mustang Part Number
Designation
Coupling Grease 20010651 Mobil Mobilith AW 2
PAU Grease 20010651 Mobil Mobilith AW 2
Bearing Grease 20014314 Polyrex EM
Brake Cleaner 20014315 Brake cleaner
Thread Lock 20010654 Locktite 262
Teflon Tape 20014810 1/4-inch Teflon tape

SECTION 2-MAINTENANCE MUSTANG DYNAMOMETER
MODEL MD-800 SERPENTINE MAINTENANCE AND SERVICE 2-5
2.2 PREVENTIVE MAINTENANCE
The activities listed in Table 2.3, Preventive Maintenance Time Table, should be performed at
the time intervals indicated. Perform initial startup inspections after installation, after 8 hours of
operation, and after the first forty hours of operation. After startup inspections are complete and
the dynamometer is operating satisfactorily, perform the regular preventive maintenance
inspections and lubrications as indicated.
Table 2.3
Preventive Maintenance Time Table
Maintenance Procedure Initial
Startup
Inspections
Every
Month Every
Three
Months
Every
Six
Months
LUBRICATION
Lubricate Pillow Block Bearings •
Lubricate Couplings •
Lubricate PAU •
INSPECTION
Inspect Bearings ••
Inspect Couplings ••
Inspect Brake Pads •
Check Belt Tension •
Check PAU Bracket Bolts ••
Inspect Pulley Bolts ••
Inspect Idler Assembly ••
Inspect Restraint Assembly ••
Inspect Roll Lock Assemblies ••
Inspect Air Bags •
Inspect Air Lines and Solenoid Valve •
Inspect PAU Load Cell Assembly ••
Inspect PAU Bearings •
Inspect PAU Clearance •
Inspect Speed Sensors ••
Inspect and Clean Dynamometer •
Inspect and Clean Pit •

MODEL MD-800 SERPENTINE DYNAMOMETER SERVICE MANUAL
2-6 MODEL MD-800 SERPENTINE MAINTENANCE AND SERVICE
2.3 LUBRICATION
CAUTION
Bearings and couplings must be lubricated with
recommended lubricants. Lubricants must be fresh and
free from contamination. Failure to lubricate or to use
incorrect or contaminated lubricants will result in reduced
life expectancy and/or damage to bearings and couplings.
Too much grease can change parasitic losses of the
dynamometer and will cause overheating of roll and PAU
bearings in high-speed operation of the dynamometer.
Adequate lubrication is essential for satisfactory operation of the dynamometer. Lubrication of
the dynamometer pillow block bearings, couplings, and PAU should be done as a part of a
planned maintenance schedule. The recommended lubrication intervals in the Preventive
Maintenance Time Table should be used as a guide to establish this schedule. These intervals
are based on 24 hours of actual machine usage per week. For extreme or unusual operating
conditions, lubricate more often. Even if the dynamometer is used less than 24 hours per week,
the lubrication schedule should be followed in order to purge the system of potential
contaminants.
2.3.1 LUBRICATE PILLOW BLOCK BEARINGS
Remove the plug or temperature probe and replace it with a zerk fitting.
Using a hand pump grease gun filled Polyrex EM grease, insert the gun into the fitting and add
three grams of grease while rotating the dynamometer rolls by hand. Experiment with your
particular grease gun to determine how many pumps equate to three grams of grease. It should
be roughly equivalent to three pumps using a normal grease gun.
Remove the zerk fitting and carefully replace the plug or temperature probe.
Repeat for each of the 20 pillow block and flange mount bearings on the dynamometer.
Dynamometers equipped with an optional second PAU will have 22 bearings to lubricate
When finished with greasing all the pillow block bearings, run the dynamometer with a vehicle
properly restrained at approximately 20 mph for 15 minutes to evenly distribute the grease.
Run warm-up, parasitic, and coastdown tests.

SECTION 2-MAINTENANCE MUSTANG DYNAMOMETER
MODEL MD-800 SERPENTINE MAINTENANCE AND SERVICE 2-7
2.3.2 LUBRICATE COUPLINGS
Remove the two (2) grease plugs from the coupling sleeves and insert a grease fitting into one
of the holes.
Using a hand pump grease gun filled with Mobilith AW 2 grease, insert the gun into the grease
fitting and pump the handle until grease comes out of the other hole.
Replace both grease plugs.
Tighten all plugs until they are snug and are approximately 1/16-inch above the surface - DO
NOT OVER-TIGHTEN THE PLUGS. The plugs should not be flush with the coupling sleeves.
If the plug falls below the surface of the coupling sleeve, remove it, wrap the threads with
Teflon tape, and reinstall.
Remove excess grease.
2.3.3 LUBRICATE PAU
Locate the grease fitting located on the stator frame of the PAU. Wipe off any dirt or other
contaminates that may be on the grease fitting.
Using a hand pump grease gun filled with Mobilith AW 2 grease, insert the gun into the fitting
located on the PAU. Pump while rotating the power absorber until grease appears on the power
absorber vent. Remove excess grease.
It is normal for the PAU to expel grease out of the vent tube, especially when hot.
2.3.3 LUBRICATE ADJUSTMENT ASSEMBLY GEARBOX
The wheelbase adjustment gearbox is factory filled with long life lubricant. Under normal
operating conditions no additional lubrication is required.
Inspect gearbox for oil leaks when lubricating other items.

MODEL MD-800 SERPENTINE DYNAMOMETER SERVICE MANUAL
2-8 MODEL MD-800 SERPENTINE MAINTENANCE AND SERVICE
2.4 INSPECTION
Table 2.4
Torque Chart
Description Bolt
Size Socket/Key
Size Qt
y. Torque
1-1/2-inch Pillow Block Bearing
Set Screws
5/16-
24
5/32 Allen
4
140 inch-pounds.
2-inch and 2-3/16-inch Pillow
Block Bearing Set Screws
3/8-24
3/16 Allen
18
250 inch-pounds.
Coupling Set Screws
1/2-20
1/4 Allen
10
50 foot-pounds.
Coupling Set Screws
(Wheelbase Adjust)
1/4-28 1/8 Allen 4 75 inch-pounds
1-1/2-inch Pillow Block Bearing
Bolts
1/2-13
3/4
4
50 foot-pounds.
2-inch Pillow Block Bearing Bolts
5/8-11
15/16
4
70 foot-pounds.
2-3/16-inch Pillow Block Bearing
Bolts
5/8-11
15/16
32
70 foot-pounds.
2-3/16-inch Flange Mount
Bearing Bolts
5/8-11
15/16
6
70 foot-pounds.
PAU Bracket Bolts
5/8-11
15/16
4
70 foot-pounds.
Pulley Bolts
5/8-11
15/16
9
135 foot-pounds.
Refer to procedure
for torque method.
Pulley Set Screws
5/8-11
5/16 Allen
3
135 foot-pounds
Idler Attachment Bolts
3/4-10
1-1/8
4
240 foot-pounds.
Air Bag Mounting Bolts
5/8-11
15/16
4
70 foot-pounds.
Load Cell Bolts
1/2-13
3/4
4
50 foot-pounds.
2.4.1 INSPECT PILLOW BLOCK BEARINGS
NOTE
Three different size pillow block bearings are used. 1-1/2-inch
bearings are used in two places on the adjustment assembly. Two 2-
inch bearing are used on the PAU, and sixteen 2-3/16-inch bearings
are used on the rolls and belt sheave and idler shafts.
Using a torque wrench with a 3/4-inch socket, check that the 1-1/2-inch roll bearing mounting
bolts are torqued to 50 foot-pounds.
If bolts are loose, remove bearing mounting bolts and bearing plate, clean threads with brake
cleaner, apply a few drops of Locktite 262, reassemble plate and bolts and torque to 50 foot-
pounds.
Using a 5/32-inch Allen wrench, check to make sure all bearing set screws are tight.
If set screws are loose, remove, clean with brake cleaner, apply a drop of Locktite 262, insert
set screws, and torque to 140 inch-pounds.
Using a torque wrench with a 15/16-inch socket, check that the 2-inch and 2-3/16-inch pillow
block bearing mounting bolts are torqued to 70 foot-pounds.
If bolts are loose, remove bearing mounting bolts and bearing plate, clean threads with brake
cleaner, apply a few drops of Locktite 262, reassemble plate and bolts and torque to 70 foot-
pounds.

SECTION 2-MAINTENANCE MUSTANG DYNAMOMETER
MODEL MD-800 SERPENTINE MAINTENANCE AND SERVICE 2-9
Using a 3/16-inch Allen wrench, check to make sure all bearing set screws are tight.
If set screws are loose, remove, clean with brake cleaner, apply a drop of Locktite 262, insert
set screws, and torque to 250 inch-pounds.
2.4.2 INSPECT CONDITION OF COUPLINGS
Using a 1/4-inch Allen wrench, check to make sure both set screws in each coupling hub is tight
(five coupling assemblies).
If set screws are loose, clean with brake cleaner, apply a drop of Locktite 262, insert set screws,
and torque to 50 foot-pounds.
Using a 1/8-inch Allen wrench, check to make sure the set screw in each coupling hub in the
wheelbase adjustment assembly is tight (two coupling assemblies).
If set screws are loose, clean with brake cleaner, apply a drop of Locktite 262, insert set screws,
and torque to 75 inch-pounds.
2.4.3 INSPECT BRAKE PADS
WARNING
Make sure that the roll lock arms will not be accidentally
raised while performing this inspection. Failure to turn off
shop air may allow the roll lock arms to raise and cause
injury.
Lower the brake arm and disconnect the shop air supply to the dynamometer.
Visually inspect the brake pads for wear.
If the average brake pad thickness is less than 1/8 inch or if any spot is less than 1/16 inch,
replace the brake pad.
2.4.4 CHECK BELT TENSION
Visually inspect the drive belt to ensure that there are no signs of wear, damage, or
deterioration. The belt should have a snug fit, neither too taut nor too loose. Observe the belt
during the dynamometer calibration sequence. The belt should not slip.
Using a belt tension tester, check the tension in the belt between the two roll pulleys when the
moving rolls are placed in the longest wheelbase position. The belt should deflect 2.00 inches
when a load of 30 pounds is applied to the middle of the belt span
2.4.5 INSPECT PAU BRACKET BOLTS
Using a torque wrench with a 15/16-inch socket, check that four (4) PAU bracket bolts are
torqued to 70 foot-pounds.
If bolts are loose, remove bolts, clean with brake cleaner, apply a few drops of Locktite 262,
reassemble bolts and torque to 70 foot-pounds.
2.4.6 INSPECT PULLEY BOLTS
Using a torque wrench with a 15/16-inch socket, check that the three (3) bolts on each pulley
are torqued to 135 foot-pounds.
If bolts are loose, remove bolts, clean with brake cleaner, apply a few drops of Locktite 262,
reassemble bolts and torque to 135 foot-pounds.
Table of contents
Other MD Measuring Instrument manuals
Popular Measuring Instrument manuals by other brands
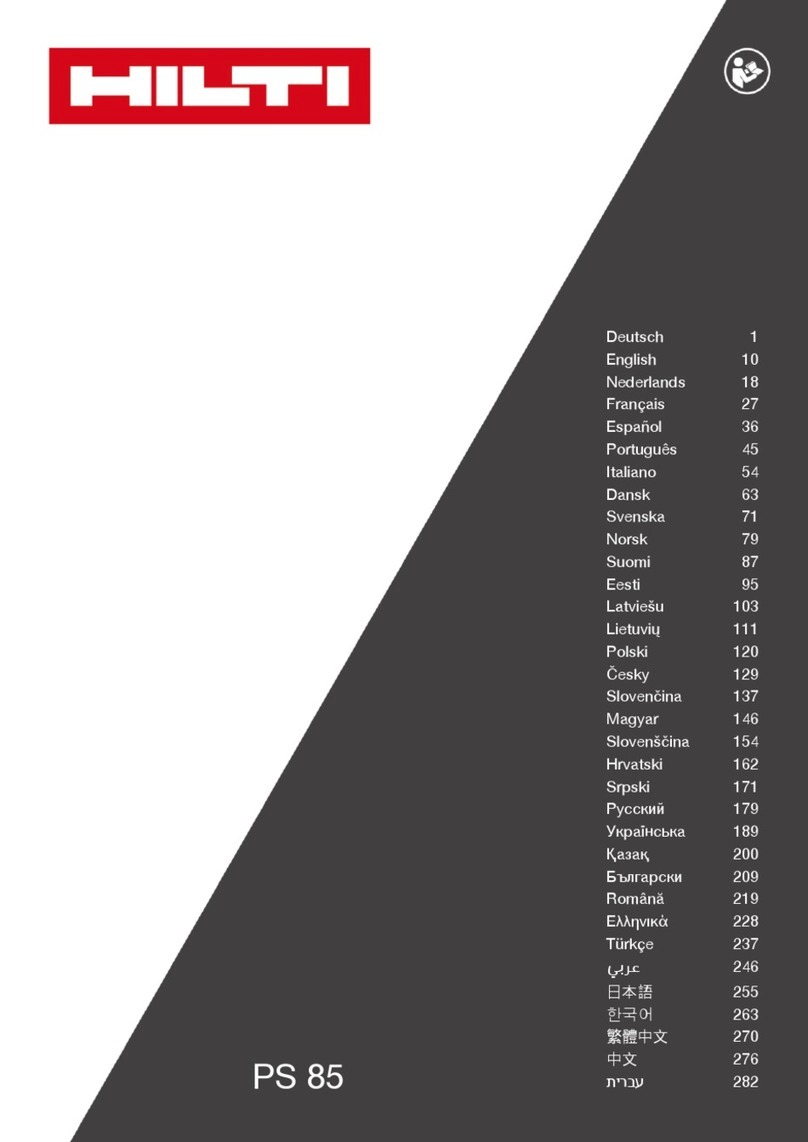
Hilti
Hilti PS 85 Original operating instructions

Conrad Electronic
Conrad Electronic 2884220 operating instructions

RT Systems
RT Systems TM3 Installation and user manual
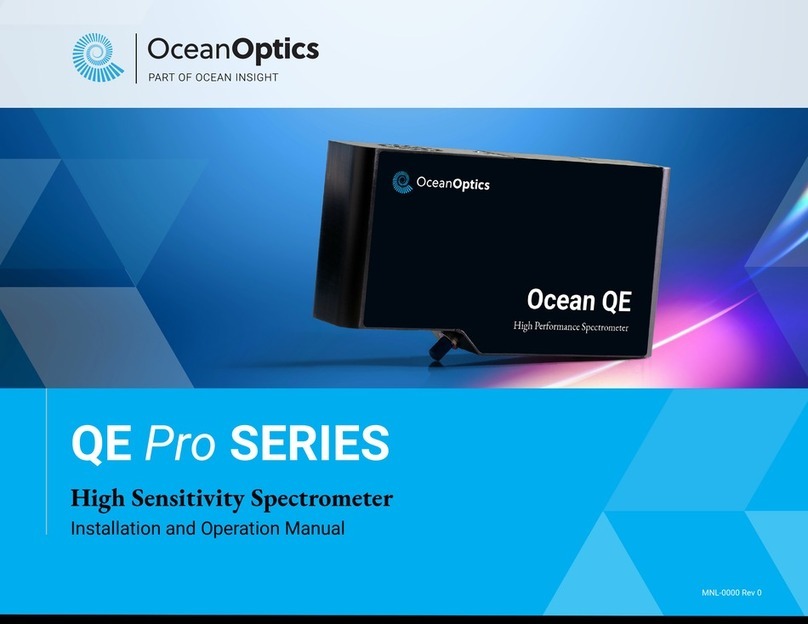
Ocean Optics
Ocean Optics QE Pro Series Installation and operation manual
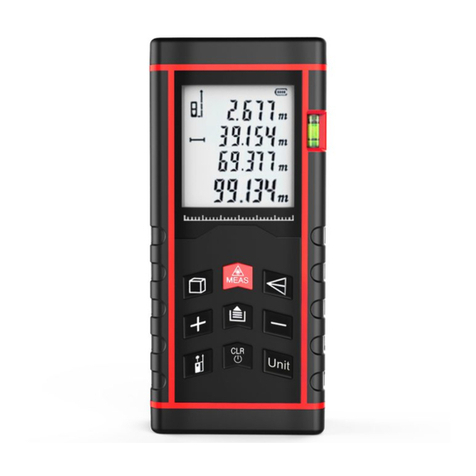
hecht
hecht 2003 TRANSLATION OF ORIGINAL INSTRUCTIONS FOR USE
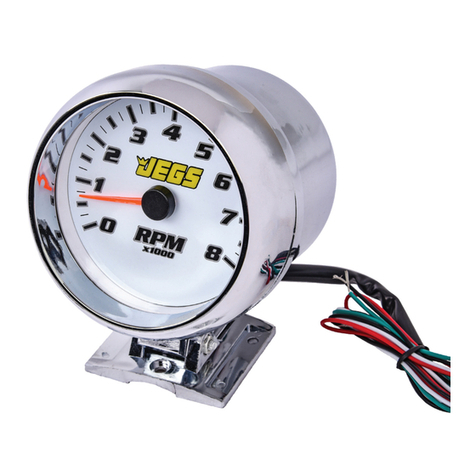
Jegs
Jegs 41307 installation guide