Memsic DMU380SA Series User manual

Roll, Pitch, Heading, Rate,
Acceleration, Mag and BIT
9-32VDC @ < 350mW
AHRS380SA
UAV Flight Control
Uncertified Avionics
Power Sensing Solutions for a Better Life
AHRS380SA
ATTITUDE HEADING REFERENCE SYSTEM
The MEMSIC AHRS380SA is a standalone fully-
integrated Attitude & Heading Reference System
offering a complete dynamic measurement solution
in a miniature environmentally protected package.
The AHRS380SA offers a highly-effective solution
for cost-sensitive demanding applications.
Features
Complete 9DOF Inertial System
Roll/Pitch/Heading Outputs
RS-232 or RS-422 Interface
Update Rate, 1Hz to 100Hz
Miniature Package, 41 x 48 x 22mm
Wide Input Voltage Range, 9-32VDC
Low Power Consumption < 350 mW
Wide Temp Range, -40C to +85C
High Reliability, MTBF > 50k hours
Environmentally Protected Enclosure
The MEMSIC AHRS380SA integrates highly-reliable
MEMS 6DOF inertial sensors and 3-axis magnetic sensors
with extended Kalman filtering in a miniature factory-
calibrated module to provide consistent performance
through the extreme operating environments in a wide
variety of dynamic control and navigation applications.
Applications
Unmanned Vehicle Control
Uncertified Avionics
Platform Stabilization
Robotics Control

Performance
AHRS380SA-200
Heading
Range (º)
± 180
Accuracy (º)
< 3.0 3, < 1.0 4
Resolution (º)
< 0.02
Attitude
Range: Roll, Pitch (º)
± 180, ± 90
Accuracy (º)
< 1.0 3, < 0.2 4
Resolution (º)
< 0.02
Angular Rate
Range: Roll, Pitch, Yaw (º/sec)
± 200 (± 400 High Range Model)
Bias Instability (º/hr) 1,2
< 10
Bias Stability Over Temp (º/sec)
< 0.1
Resolution (º/sec)
< 0.02
Scale Factor Accuracy (%)
< 0.1
Non-Linearity (%FS)
< 0.1
Angle Random Walk (º/√hr) 2
< 0.75
Bandwidth (Hz)
5-50 (user-configurable)
Acceleration
Range: X, Y Z (g)
± 4 (± 8 High Range Model)
Bias Instability (mg) 1,2
< 0.02
Bias Stability Over Temp (mg)
< 5
Resolution (mg)
< 0.5
Scale Factor Accuracy (%)
< 0.1
Non-Linearity (%FS)
< 0.1
Velocity Random Walk (m/s/√hr) 2
< 0.05
Bandwidth (Hz)
5-50 (user-configurable)
Magnetic Field
Range: X, Y Z (Gauss)
± 4
Resolution (mGauss)
< 5
Noise Density (mGauss /√Hz)
< 1
Bandwidth (Hz)
5
Specifications
Environment
Operating Temperature (ºC)
-40 to +85
Non-Operating Temperature (ºC)
-55 to +105
Enclosure
Aluminum (Gold Chem Film - ROHS)
Electrical
Input Voltage (VDC)
9 to 32
Power Consumption (mW)
< 350
Digital Interface
RS-232 or RS-422 (user-configurable)
Output Data Rate
2Hz to 100Hz (user-configurable)
Physical
Size (mm)
41 x 48 x 22
Weight (gm)
< 30
Interface Connector
9-Pin Micro-D
Ordering Information
Model
Description
AHRS380SA-200
Attitude and Heading Reference System (Standard Range)
AHRS380SA-400
Attitude and Heading Reference System (High Range)
AHRS380SA
ATTITUDE HEADING REFERENCE SYSTEM
NAV-VIEW
Configuration and Display Software
NAV-VIEW provides an easy to use
graphical interface to display, record,
playback, and analyze all of the
AHRS380SA Attitude & Heading
Reference System parameters.
NAV-VIEW can also be used to set a
wide range of user-configurable fields
in the AHRS380SA to optimize the
system performance for highly
dynamic applications.
NAV-VIEW software is available for
download from MEMSIC’s website at:
www.memsic.com/support
This product has been developed exclusively for commercial applications. It has not been tested
for, and makes no representation or warranty as to conformance with, any military specifications
or its suitability for any military application or end-use. Additionally, any use of this product for
nuclear, chemical or biological weapons, or weapons research, or for any use in missiles,
rockets, and/or UAV’s of 300km or greater range, or any other activity prohibited by the Export
Administration Regulations, is expressly prohibited without the written consent and without
obtaining appropriate US export license(s) when required by US law. Diversion contrary to U.S.
law is prohibited. Specifications are subject to change without notice.
1Allan Variance Curve, constant temperature. 21-sigma error. 3 RMS error under all dynamics.
4 RMS error under static conditions over full temperature range.
Other Components
The AHRS380SA evaluation kit
includes an AHRS380SA,
interface cable and USB cable,
allowing direct connection to a
PC for use with NAV-VIEW
display and configuration
software.
Support
For more detailed information
please refer to the DMU380SA-
Series User’s Manual available
online at:
www.memsic.com/support
Document P/N: 6020-3824-01

DMU380SA Series
USER MANUAL
Document Part Number: 7430-0026-01
MEMSIC, Inc., 1759 McCarthy Blvd, Milpitas, CA 95035
Tel: 408-964-9700, Fax: 408-854-7702

WARNING
This product has been developed by MEMSIC exclusively for commercial applications. It
has not been tested for, and MEMSIC makes no representation or warranty as to
conformance with, any military specifications or that the product is appropriate for any
military application or end-use. Additionally, any use of this product for nuclear,
chemical, biological weapons, or weapons research, or for any use in missiles, rockets,
and/or UAV's of 300km or greater range, or any other activity prohibited by the Export
Administration Regulations, is expressly prohibited without the written consent of
MEMSIC and without obtaining appropriate US export license(s) when required by US
law. Diversion contrary to U.S. law is prohibited.
©2014 MEMSIC, Inc. All rights reserved. Information in this document is subject to
change without notice.
MEMSIC, SoftSensor, INS380SA, AHRS380SA, VG380SA, and IMU380SA are
registered trademarks of MEMSIC, Inc. Other product and trade names are trademarks or
registered trademarks of their respective holders.

DMU380SA Series User’s Manual
Doc# 7430-0026 Rev. 01
Page i
Table of Contents
1Introduction..................................................................................................................1
Manual Overview .................................................................................................11.1
Overview of the DMU380SA Series Inertial Systems..........................................21.2
Summary of Major Changes from the 440 Series and the 350 Series ..................31.3
1.3.1 Mechanical Size and Footprint......................................................................3
1.3.2 Connector Pin Out & Operating Voltage, Current ........................................3
1.3.3 Software Compatibility..................................................................................3
1.3.4 Operating Performance and Accuracy...........................................................3
2Connections..................................................................................................................4
Connections ..........................................................................................................42.1
I/O Cable...............................................................................................................42.2
Power Input and Power Input Ground ..................................................................42.3
Serial Data Interface .............................................................................................52.4
Serial GPS Interface (INS380SA) ........................................................................52.5
External GPS Aiding (VG380SA and AHRS380SA)...........................................52.6
1 PPS Output Interface (INS380SA) ....................................................................62.7
Sync Pulse Input Interface (IMU, VG, and AHRS380SA)...................................62.8
GPS Antenna Connection (INS380SA)................................................................72.9
No Connection ..................................................................................................72.10
Quick Digital interface connection ...................................................................72.11
3Installation and Operation of NAV-VIEW ..................................................................9
NAV-VIEW Computer Requirements..................................................................93.1
3.1.1 Install NAV-VIEW........................................................................................9
Connections ..........................................................................................................93.2
Setting up NAV-VIEW.......................................................................................103.3
Data Recording...................................................................................................103.4
Data Playback.....................................................................................................113.5
Raw Data Console ..............................................................................................113.6
Horizon and Compass View...............................................................................123.7
Packet Statistics View.........................................................................................123.8
Unit Configuration..............................................................................................133.9
Advanced Configuration.................................................................................143.10
Bit Configuration ............................................................................................153.11
Mag Alignment Procedure..............................................................................163.12
3.12.1 Hard Iron/Soft Iron Overview .....................................................................16

DMU380SA Series User’s Manual
Page ii
Doc# 7430-0026 Rev. 01
3.12.2 Mag Alignment Procedure Using NAV-VIEW...........................................17
Read Unit Configuration.................................................................................193.13
4Theory of Operation...................................................................................................21
DMU380SA Series Default Coordinate System.................................................244.1
4.1.1 Advanced Settings.......................................................................................25
IMU380SA Theory of Operation........................................................................254.2
4.2.1 IMU380SA Advanced Settings ...................................................................26
4.2.2 IMU380SA Built-In Test.............................................................................27
VG380SA Theory of Operation..........................................................................274.3
4.3.1 VG380SA Advanced Settings .....................................................................29
4.3.2 VG380SA Built-In Test..............................................................................30
AHRS380SA Theory of Operation.....................................................................31
4.4
4.4.1 AHRS380SA Magnetometer Calibration and Alignment ...........................32
4.4.2 AHRS380SA Advanced Settings ................................................................33
4.4.3 AHRS380SA Built-In Test..........................................................................36
INS380SA Theory of Operation.........................................................................374.5
4.5.1 INS380SA Magnetometer Calibration and Alignment................................39
4.5.2 INS380SA Advanced Settings.....................................................................39
4.5.3 INS380SA Built-In Test..............................................................................40
5Application Guide......................................................................................................42
Introduction.........................................................................................................425.1
Fixed Wing Aircraft............................................................................................425.2
Rotorcraft............................................................................................................435.3
Land Vehicle.......................................................................................................435.4
Water Vehicle.....................................................................................................445.5
6Programming Guide...................................................................................................46
General Settings..................................................................................................466.1
Number Formats.................................................................................................466.2
Packet Format.....................................................................................................476.3
6.3.1 Packet Header..............................................................................................47
6.3.2 Packet Type .................................................................................................47
6.3.3 Payload Length............................................................................................48
6.3.4 Payload........................................................................................................48
6.3.5 16-bit CRC-CCITT......................................................................................48
6.3.6 Messaging Overview...................................................................................48
7Communicating with the DMU380SA Series............................................................51
Link Test.............................................................................................................517.1

DMU380SA Series User’s Manual
Doc# 7430-0026 Rev. 01
Page iii
7.1.1 Ping Command............................................................................................51
7.1.2 Ping Response..............................................................................................51
7.1.3 Echo Command ...........................................................................................51
7.1.4 Echo Response.............................................................................................51
Interactive Commands........................................................................................517.2
7.2.1 Get Packet Request......................................................................................51
7.2.2 Algorithm Reset Command.........................................................................52
7.2.3 Algorithm Reset Response ..........................................................................52
7.2.4 Calibrate Command.....................................................................................52
7.2.5 Calibrate Acknowledgement Response.......................................................53
7.2.6 Calibration Completed Parameters Response..............................................53
7.2.9 Error Response ............................................................................................54
Output Packets (Polled) ......................................................................................547.3
7.3.1 Identification Data Packet ...........................................................................54
7.3.2 Version Data Packet ....................................................................................54
7.3.3 Test 0 (Detailed BIT and Status) Packet......................................................55
Output Packets (Polled or Continuous)...............................................................557.4
7.4.1 Scaled Sensor Data Packet 0 .......................................................................55
7.4.2 Scaled Sensor Data Packet 1 (Default IMU Data).......................................56
7.4.3 Angle Data Packet 1 (Default AHRS Data) ................................................57
7.4.4 Angle Data Packet 2 (Default VG Data) .....................................................58
7.4.5 Nav Data Packet 0 .......................................................................................59
7.4.6 Nav Data Packet 1 (Default INS Data)........................................................60
8Advanced Commands ................................................................................................62
Configuration Fields...........................................................................................628.1
Continuous Packet Type Field............................................................................628.2
Digital Filter Settings..........................................................................................638.3
Orientation Field.................................................................................................638.4
User Behavior Switches......................................................................................648.5
Hard and Soft Iron Values..................................................................................658.6
Heading Track Offset..........................................................................................658.7
Commands to Program Configuration................................................................668.8
8.8.1 Write Fields Command................................................................................66
8.8.2 Set Fields Command....................................................................................67
Read Fields Command........................................................................................688.9
Read Fields Response .....................................................................................688.10

DMU380SA Series User’s Manual
Page iv
Doc# 7430-0026 Rev. 01
Get Fields Command.......................................................................................688.11
Get Fields Response........................................................................................698.12
9Advanced BIT............................................................................................................70
Built In Test (BIT) and Status Fields..................................................................709.1
Master BIT and Status (BITstatus) Field............................................................729.2
hardwareBIT Field..............................................................................................739.3
hardwarePowerBIT Field....................................................................................739.4
hardwareEnvironmentalBIT Field ......................................................................739.5
comBIT Field......................................................................................................739.6
comSerialABIT Field..........................................................................................749.7
comSerialBBIT Field..........................................................................................749.8
softwareBIT Field...............................................................................................74
9.9
softwareAlgorithmBIT Field...........................................................................759.10
softwareDataBIT Field....................................................................................759.11
hardwareStatus Field.......................................................................................759.12
comStatus Field...............................................................................................759.13
softwareStatus Field........................................................................................769.14
sensorStatus Field............................................................................................769.15
Configuring the Master Status.........................................................................769.16
9.16.1 hardwareStatusEnable Field ........................................................................76
9.16.2 comStatusEnable Field................................................................................77
9.16.3 softwareStatusEnable Field .........................................................................77
9.16.4 sensorStatusEnable Field.............................................................................77
10 Appendix A. Mechanical Specifications................................................................78
11 Appendix B. NMEA Message Format ...................................................................80
GGA - GPS fix data ........................................................................................8011.1
12 Appendix C. Sample Packet-Parser Code ..............................................................82
Overview.........................................................................................................8212.1
Code listing .....................................................................................................8312.2
13 Appendix D. Sample Packet Decoding ..................................................................89
14 Warranty and Support Information ........................................................................92
Customer Service............................................................................................9214.1
Contact Directory............................................................................................9214.2
Return Procedure.............................................................................................9214.3
14.3.1 Authorization...............................................................................................92
14.3.2 Identification and Protection .......................................................................92
14.3.3 Sealing the Container...................................................................................93

DMU380SA Series User’s Manual
Doc# 7430-0026 Rev. 01
Page v
14.3.4 Marking .......................................................................................................93
14.3.5 Return Shipping Address.............................................................................94
Warranty..........................................................................................................9414.4

DMU380SA Series User’s Manual
Page vi
Doc# 7430-0026 Rev. 01
About this Manual
The following annotations have been used to provide additional information.
NOTE
Note provides additional information about the topic.
EXAMPLE
Examples are given throughout the manual to help the reader understand the terminology.
IMPORTANT
This symbol defines items that have significant meaning to the user
WARNING
The user should pay particular attention to this symbol. It means there is a chance that
physical harm could happen to either the person or the equipment.
The following paragraph heading formatting is used in this manual:
1 Heading 1
1.1 Heading 2
1.1.1 Heading 3
Normal

DMU380SA Series User’s Manual
________________________________________________________________________
Doc# 7430-0026 Rev.01 Page 1
1Introduction
Manual Overview1.1
This manual provides a comprehensive introduction to MEMSIC’s DMU380SA Series
Inertial System products. For users wishing to get started quickly, please refer to the three
page quick start guide included with each shipment. Table 1 table highlights the content
in each section and suggests how to use this manual.
Table 1. Manual Content
Manual Section
Who Should Read ?
Section 1:
Manual Overview
All customers should read sections 1.1 and 1.2.
Section 2:
Connections
Customers who are connecting the DMU380SA Series products into a system
with their own power supply and cable.
Section 3:
Installation and Operation of NAV-
VIEW
Customers who are installing the DMU380SA Series products into a system and
need details on using NAV-VIEW.
Section 4:
Theory of Operation
All customers should read Section 4.
As the DMU380SA Series products are inter-related, use the chart at the
beginning of Section 4 to ensure that you get an overview of all of the functions
and features of your DMU380SA Series system. For example, if you have
purchased a INS380SA, you should read not only the section on the INS380SA,
but also familiarize yourself with the theory of operation for the IMU380SA,
VG380SA, and AHRS380SA. The INS380SA builds on the capabilities of the
IMU380SA, VG380SA and AHRS380SA.
Section 5:
Application Guide
Customers who want product configuration tips for operating the DMU380SA
Series Inertial Systems in a wide range of applications –fixed wing, rotary wing,
unmanned vehicles, land vehicles, marine vessels, and more, should review the
part of Section 5 that is relevant to your application. Note: INS and AHRS
DMU380SA Series units are preconfigured for airborne applications with
“normal” dynamics. VG380SA Series units are preconfigured for land
applications with “automotive testing” dynamics. All DMU380SA Series products
allow for complete flexibility in configuration by the user.
Section 6-9:
Programming, Communicating,
Advanced Commands and BIT
Customers who wish to communicate with the DMU380SA Series system for
sensor and navigation data, should review Section 6 and 7. Section 8 is for
users who wish to configure the DMU380SA Series operating parameters (e.g.,
baud rate or power-up output rate) without NAV-VIEW.

DMU380SA Series User’s Manual
________________________________________________________________________
Doc# 7430-0026 Rev. 01 Page 2
Overview of the DMU380SA Series Inertial Systems1.2
This manual provides a comprehensive introduction to the use of MEMSIC’s
DMU380SA Series Inertial System products listed in Table 2. This manual is intended to
be used as a detailed technical reference and operating guide for the DMU380SA Series.
MEMSIC’s DMU380SA Series products combine the latest in high-performance
commercial MEMS (Micro-electromechanical Systems) sensors and digital signal
processing techniques to provide a small, cost-effective alternative to existing IMU
systems and mechanical gyros.
Table 2. DMU380SA Series Feature Description
Product
Features
IMU380SA
6- DOF Digital IMU
VG380SA (-200,-400)
6-DOF IMU, plus Roll and Pitch
AHRS380SA (-200, -400)
9-DOF IMU (3-Axis Internal Magnetometer) plus Roll, Pitch, and Heading Standard Range, High
Range
INS380SA (-200, -400)
9-DOF IMU (3-Axis Internal Magnetometer) and Internal WAAS Capable GPS Receiver plus
Position, Velocity, Roll, Pitch, and Heading Standard Range, High Range
The DMU380SA Series is MEMSIC’s fourth generation of MEMS-based Inertial
Systems, building on over a decade of field experience, and encompassing thousands of
deployed units and millions of operational hours in a wide range of land, marine,
airborne, and instrumentation applications.
At the core of the DMU380SA Series is a rugged 6-DOF (Degrees of Freedom) MEMS
inertial sensor cluster that is common across all members of the DMU380SA Series. The
6-DOF MEMS inertial sensor cluster includes three axes of MEMS angular rate sensing
and three axes of MEMS linear acceleration sensing. These sensors are based on rugged,
field proven silicon bulk micromachining technology. Each sensor within the cluster is
individually factory calibrated for temperature and non-linearity effects during
MEMSIC’s manufacturing and test process using automated thermal chambers and rate
tables.
Coupled to the 6-DOF MEMS inertial sensor cluster is a high performance
microprocessor that utilizes the inertial sensor measurements to accurately compute
navigation information including attitude, heading, and linear velocity thru dynamic
maneuvers (actual measurements are a function of the DMU380SA Series product as
shown in Table 2). In addition, the ARM processor makes use of internal and external
magnetic sensor and/or GPS data to aid the performance of the inertial algorithms and
help correct long term drift and estimate errors from the inertial sensors and
computations. The navigation algorithm utilizes a multi-state configurable Extended
Kalman Filter (EKF) to correct for drift errors and estimate sensor bias values.
Another unique feature of the DMU380SA Series is the extensive field configurability of
the units. This field configurability allows the DMU380SA Series of Inertial Systems to
satisfy a wide range of applications and performance requirements with a single mass
produced hardware platform. The basic configurability includes parameters such as baud
rate, packet type, and update rate, and the advanced configurability includes the defining
of custom axes and how the sensor feedback is utilized in the Kalman filter during the
navigation process.
The DMU380SA Series is packaged in a fully sealed lightweight housing which provides
EMI, vibration, and moisture resistance to levels consistent with most land, marine, and
airborne environments. The DMU380SA Series utilizes an RS-232 serial link for data
communication, and each data transmission includes a BIT (Built-In-Test) message

DMU380SA Series User’s Manual
________________________________________________________________________
Doc# 7430-0026 Rev.01 Page 3
providing system health status. The DMU380SA Series is supported by MEMSIC’s
NAV-VIEW, a powerful PC-based operating tool that provides complete field
configuration, diagnostics, charting of sensor performance, and data logging with
playback.
Summary of Major Changes from the 440 Series and the 350 Series1.3
1.3.1 Mechanical Size and Footprint
The mechanical footprint of MEMSIC’s new DMU380SA Series Inertial Systems is
significantly smaller compared to the prior generation Inertial Systems including
MEMSIC’s 440 Series (IMU440, VG440, AHRS440 and INS440), and 350 series
products. The mounting plate foot print is the smaller and the connector is miniature. For
detailed mechanical and installation drawings, see appendix A of the manual.
1.3.2 Connector Pin Out & Operating Voltage, Current
The micro-DB9 female socket connector on MEMSIC’s DMU380SA Series Inertial
Systems is new to MEMSIC’s product lines, and provides a significant size reduction and
performance improvement. The DMU380SA Series has a secondary optional-use
communications port for internal or external GPS.
1.3.3 Software Compatibility
MEMSIC’s DMU380SA Series Inertial Systems are software compatible with the
MEMSIC 440 series products and 350 series products. The DMU380SA Series products
utilize the same extensible communication protocol as the 440 series and 350 series
products. The protocol is documented in section 7 of this manual.
1.3.4 Operating Performance and Accuracy
The DMU380SA Series has been characterized in a wide range of land and airborne
applications. In the qualification testing, the dynamic accuracy of the DMU380SA Series
has shown improved performance when compared to the equivalent model of 440 and
350 series products, reducing attitude estimation errors in half during certain critical
dynamic maneuvers without the use of GPS aiding. With GPS aiding in the INS380SA,
attitude estimation is improved over the 440 series products. Recommended product
configuration settings are discussed in Section 5, and theory of operation is discussed in
Section 4.

DMU380SA Series User’s Manual
________________________________________________________________________
Doc# 7430-0026 Rev. 01 Page 4
2Connections
Connections2.1
The DMU380SA Series has a micro-DB9 female connector as shown in Figure 1. The
signals are as shown in Table 3.
Figure 1. 9 Pin Micro-DB Connector Female Pinout
Table 3. Connector Pin Assignments
Pin
Signal
1
Power Input
2
Power Return
3
+RX RS-232 / RS-422
4
-RX RS-422
5
+TX RS-232 / RS-422
6
-TX RS-422
7
Mode Select (RS-232 Short / RS-422 Open)
8
GPS 1PPS Output (INS380SA) / Sync Pulse Input (IMU, VG and AHRS380SA)
9
Signal Return
I/O Cable2.2
The user must provide a shielded cable with the shield connected to the I/O connector
shell in order to provide improved EMI protection. The cable sent with the unit is
intended to provide the user with the ability to test the unit right out of the box, and will
not provide adequate shielding for all environments.
WARNING
The cable sent with the unit is intended to provide the user with the ability to test the unit
right out of the box, and will not provide adequate shielding for all environments.
Power Input and Power Input Ground
2.3
Power is applied to the DMU380SA Series on pins 1 and 2. Pin 2 is ground; Pin 1 should
have 9 to 32 VDC unregulated at 350 mW. If you are using the cable supplied with the
DMU380SA Series, the power supply wires are broken out of the cable at the DB-9
connector. The red wire is connected to the positive power input; the black wire is
connected to the power supply ground.
WARNING

DMU380SA Series User’s Manual
________________________________________________________________________
Doc# 7430-0026 Rev.01 Page 5
Do not reverse the power leads or damage may occur.
Serial Data Interface2.4
The main serial interface is standard RS-232, 9600, 19200, 38400, or 57600 baud, 8 data
bits, 1 start bit, 1 stop bit, no parity, and no flow control and will output at a user
configurable output rate. Pins 3 and 5 are designated as the main RS-232 interface pins.
The secondary serial interface is also standard RS-232, 9600, 19200, 38400, or 57600
baud, 8 data bits, 1 start bit, 1 stop bit, no parity, and no flow control, and is used by
INS380SA models to output internal GPS data. Pins 4 and 6 are designated as the
secondary RS-232 interface pins used by the INU380SA models. The user may opt to set
the output to RS-422 using pin 7. When Pin7 is shorted to ground, the standard RS-232
ports will be available. When Pin 7 is left open, then only the main serial interface will
be available and it will be standard RS-422 , 9600, 19200, 38400, or 57600 baud, 8 data
bits, 1 start bit, 1 stop bit, no parity, and no flow control and will output at a user
configurable output rate. Pins 3 and 4 are used for the RS-422 +Rx and –Rx, and pins 5
and 6 are used for the RS-422 +Tx and –Tx. These settings allow interaction via a
standard PC serial port. The serial data settings can be configured on a DMU380SA
Series unit with NAV-VIEW. In order to set the serial data interface, select Unit
Configuration, under the Menu Tab.
Serial GPS Interface (INS380SA)2.5
The internal GPS receiver in INS380SA products outputs data in NMEA-0183 format as
defined by the National Marine Electronics Association (NMEA), Standard For
Interfacing Marine Electronic Devices, Version 2.20, January 1, 1997.
The packets are sent at 9600 Baud, 8 data bits, 1 start bit, 1 stop bit, no parity bit, and no
flow control and are output over the secondary serial interface (RS-232 on pins 4 and 6).
The GPS receiver outputs the following messages as shown in Table 4. (Refer to
Appendix B for the detailed message format)
Table 4. GPS Output Packet Format
NMEA Record
Description
GGA
Global positioning system fixed data
RMC
Recommended minimum specific GNSS data
VTG
Course over ground and ground speed data
External GPS Aiding (VG380SA and AHRS380SA)2.6
The VG380SA/AHRS380SA allows the use of an external GPS receiver to be connected
to the secondary serial interface (RS-232 on pins 4 and 6) port. The user is required to
configure the GPS receiver to output the GPS messages that the DMU380SA Series
expects. The table below shows the supported GPS protocols and guidelines for
configuration. Note that the details of the GPS messages can be found in the respective
GPS protocol documents. The user must configure the VG/AHRS380SA to accept
external GPS information using NAV-VIEW as described in Chapter 3. If the
VG/AHRS380SA is parsing valid external GPS data and the GPS receiver has 3D lock,
then the comStatusnoExternalGPS flag will be zero, otherwise it will be one. See
section 9 for a complete description of system status indications.
Since NMEA protocol does not provide vertical velocity, the vertical velocity that the
DMU380SA Series estimates (based upon GPS altitude changes) may not be sufficient
for airborne applications (See Table 5). Therefore, the NMEA protocol is not
recommended for airborne applications.

DMU380SA Series User’s Manual
________________________________________________________________________
Doc# 7430-0026 Rev. 01 Page 6
Table 5. Configuration of An External GPS Receiver for VG380SA/AHRS380SA
Protocols
Required Messages
Required Message Rate
Baud rate
Ublox binary
NAV-LLH, NAV-VELNED,
NAV-STATUS
4 Hz
9600, 19200, 38400,
57600$
NovAtel OEM4 and
OEMV Binary
BestPosB, BestVelB
4Hz
9600, 19200, 38400,
57600$
NovAtel OEM4
ASCII
PosVelNavDopA
4Hz
19200, 38400, 57600$
NMEA*
GPGGA, GPVTG
4Hz
9600, 19200, 38400,
57600$
*Not recommended for airborne applications.
$57600 is the preferred baud rate for optimum performance
The GPS serial communication port should be configured to 8 data bits, 1 start bit, 1 stop
bit, no parity bit, and no flow control.
1 PPS Output Interface (INS380SA)2.7
The 1PPS output signal on pin 8 is provided by the internal GPS receiver (when GPS
timing is known) on INS380SA products. The 1PPS output signal is open-collector and
should be interfaced to a rising-edge trigger with pull up resistor between 1k and 10k
ohms.The INS380SA Series products synchronize sensor data collection to this 1PPS
signal internally when available. Therefore, the 100Hz navigation algorithm will run
exactly 100 times each second with no slip when locked to 1PPS. Packet data is valid on
the rising edge of 1PPS and 10ms boundaries thereafter. There is, however, up to 500µs
of additional latency in sensor data collection. If 1PPS is provided by the internal GPS
receiver in NAV products, then the rising edge of 1PPS will correspond to the UTC
second boundary. When the system is synchronized to 1PPS, the
hardwareStatusunlocked1PPS flag will be zero, otherwise, it will be one.
Figure 2 shows the sequential order of the signal present at 1 PPS OUT pin.
The 1 PPS signal is aligned to the sampling clock of 23.104 MHz. This results in a timing
resolution of 43 ns.
Figure 2. 1PPS Output Signal
Sync Pulse Input Interface (IMU, VG, and AHRS380SA)2.8
The Sync Signal Input signal allows the user of IMU, VG, and AHRS 380 products to
force synchronization of sensor data collection to an external synchronization signal (1
KHz). The signal must maintain 0.0-0.2 V zero logic and 3.0-5.0 volts high logic.

DMU380SA Series User’s Manual
________________________________________________________________________
Doc# 7430-0026 Rev.01 Page 7
GPS Antenna Connection (INS380SA)2.9
The GPS receiver needs to receive signals from as many satellites as possible. A GPS
receiver doesn’t work properly in narrow streets and underground parking lots or if
objects or human beings cover the antenna. Poor visibility may result in position drift or a
prolonged Time-To-First-Fix (TTFF). A good sky visibility is therefore a prerequisite.
Even the best receiver can’t make up for signal loss due to a poor antenna, in-band
jamming or a poor RF cable.
The DMU380SA Series unit ships with an external active antenna that must be connected
properly to SMA jack located next to the DB-15 connector. Placing the antenna on a 4
inch or larger ground plane is highly recommended.
IMPORTANT
Place the antenna with optimal sky visibility and use a ground plane. Route the GPS
Antenna RF cable away from sources of radiated energy (i.e. switching power supplies).
No Connection2.10
During normal operation of the DMU380SA Series, no connection is made to the factory
test pins. These pins have internal pull-up mechanisms and must have no connections for
the DMU380SA Series to operate properly.
Quick Digital interface connection2.11
On a standard DB-9 COM port connector, make the connections as described in Table 6

DMU380SA Series User’s Manual
________________________________________________________________________
Doc# 7430-0026 Rev. 01 Page 8
Table 6. DB-9 COM Port Connections
COM Port Connector
DMU380SA Series Connector
Pin #
Signal
Pin #
Signal
2
RxD
5
TxD
3
TxD
3
RxD
5
GND
9
GND

DMU380SA Series User’s Manual
________________________________________________________________________
Doc# 7430-0026 Rev.01 Page 9
3Installation and Operation of NAV-VIEW
NAV-VIEW has been completely redesigned to allow users to control all aspects of the
DMU380SA Series operation including data recording, configuration and data transfer.
For the first time, you will be able to control the orientation of the unit, sampling rate,
packet type, hard iron calibration and filter settings through NAV-VIEW.
NAV-VIEW Computer Requirements3.1
The following are minimum requirements for the installation of the NAV-VIEW
Software:
• CPU: Pentium-class (1.5GHz minimum)
• RAM Memory: 500MB minimum, 1GB+ recommended
• Hard Drive Free Memory: 20MB
• Operating System: Windows 2000™, or XP™,
• Properly installed Microsoft .NET 2.0 or higher
3.1.1 Install NAV-VIEW
To install NAV-VIEW onto your computer:
1. Insert the CD “Inertial Systems Product Support” (Part No. 8160-0063) in the CD-
ROM drive.
2. Locate the “NAV-VIEW” folder. Double click on the “setup.exe” file.
3. Follow the setup wizard instructions. You will install NAV-VIEW and .NET 2.0
framework.
Connections3.2
The DMU380SA Series Inertial Systems products are shipped with a cable to connect the
DMU380SA Series to a PC Serial port.
1. Connect the 9-pin micro-DB connector end of the digital signal cable to the port on
the DMU380SA Series product.
2. Connect the 9-pin sub-DB end of the cable marked to the serial port of your
computer.
3. The additional black and red wires on the cable connect power to the DMU380SA
Series product. Match red to (+) power and black to (-) ground. The input voltage
can range from 9-32 VDC with a maximum current draw of 350 mA.
4. Allow at least 60 seconds after power up for the DMU380SA Series product to
initialize. The DMU380SA Series needs to be held motionless during this period.
WARNING
Do not reverse the power leads! Reversing the power leads to the DMU380SA Series
can damage the unit; although there is reverse power protection, MEMSIC is not
responsible for resulting damage to the unit should the reverse voltage protection
electronics fail.

DMU380SA Series User’s Manual
________________________________________________________________________
Doc# 7430-0026 Rev. 01 Page 10
Setting up NAV-VIEW3.3
With the DMU380SA Series product powered up and connected to your PC serial port,
open the NAV-VIEW software application.
1. NAV-VIEW should automatically detect the DMU380SA Series product and
display the serial number and firmware version if it is connected.
2. If NAV-VIEW does not connect, check that you have the correct COM port
selected. You will find this under the “Setup” menu. Select the appropriate COM
port and allow the unit to automatically match the baud rate by leaving the
“Auto: match baud rate” selection marked.
3. If the status indicator at the bottom is green and states, , you’re ready
to go. If the status indicator doesn’t say connected and is red, check the
connections between the DMU380SA Series product and the computer, check the
power supply, and verify that the COM port is not occupied by another device.
4. Under the “View” menu you have several choices of data presentation. Graph
display is the default setting and will provide a real time graph of all the
DMU380SA Series data. The remaining choices will be discussed in the
following pages.
Data Recording3.4
NAV-VIEW allows the user to log data to a text file (.txt) using the simple interface at
the top of the screen. Customers can now tailor the type of data, rate of logging and can
even establish predetermined recording lengths.
To begin logging data follow the steps below (See Figure 3):
1. Locate the icon at the top of the page or select “Log to File” from the “File”
drop down menu.
2. The following menu will appear.
Figure 3. Log to File Dialog Screen
3. Select the “Browse” box to enter the file name and location that you wish to save
your data to.
4. Select the type of data you wish to record. “Engineering Data”records the
converted values provided from the system in engineering units, “Hex Data”
provides the raw hex values separated into columns displaying the value, and the
Table of contents
Popular Control System manuals by other brands

Bosch
Bosch Rexroth IndraDrive Mi KCU01 operating instructions
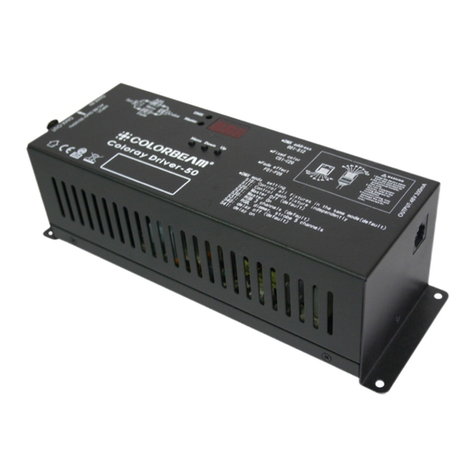
Colorbeam
Colorbeam CORLORAY DMX 50W user guide

Raven
Raven RCM-Sprayer Hawkeye 2 installation manual

Allen-Bradley
Allen-Bradley 1734-8CFG manual

Mi-Light
Mi-Light MIBOXER LDRF-RGB6-TC4 quick start guide

Mitsubishi Heavy Industries
Mitsubishi Heavy Industries Smart M-Air Setup Quick Guide