Omnex T150 User manual

T150 / R150 User Guide
STEP 1
Install Batteries
Remove the battery cover on the
back of the T150, and install the
four AA alkaline batteries as
shown in Figure 1.
STEP 2
T150
R150
T
his device complies with the requirements of the Federal Communication Commission (FCC) as specified in document CFR47 Part 15.247 and Industry and
Science Canada (ISC), as specified in document RSS 210. The device is permitted only on a no-interference, no-protection basis, that is, it must cease operation
when it is determined that it causes harmful interference to the services authorized by the FCC or the ISC.
Changes or modifications to the equipment not expressly approved by OMNEX will void the warranty.
Power Up T150
Activation of any switch will cause the T150 to power up. However as a
safety feature, the [EStop] switch must be pressed and released, or if
already pressed, released within 10 seconds for unit to remain powered
up.
Using The T150
The ACTIVE LED will flash two times per second indicating that the T150
is transmitting to the R150. When a function switch is used, the ACTIVE
LED will flash brightly upon activation of the switch and return to flashing at
a rate of two times per second when there is no switch activity.
During normal operation the LOW BATT. LED will flash to indicate a low
battery condition.
The [EStop] button is used for both an emergency shutdown as well as a
safe way of powering down the T150 after operation.
Each switch has a device specific label to identify its function.
The Trigger is a Proportional Control switch used in conjunction with a
function switch (i.e. [ROT CW]). The type of Proportional Control output is
dependent on the option of the receiver but will generally be either a
Voltage, PWM or Current Control.
STEP 3
Rev. 1.03
Figure 1
DMAN-2293-01 Bldg. 74 – 1833 Coast Meridian Road, Port Coquitlam, BC, Canada V3C 6G5
www omnexcontrols com

Setting ID Codes
Current Control Module Calibration
Permits the user to adjust minimum and maximum currents
1. Release the
[EStop] on the T150.
2. Turn the
T150 ON by toggling the [SW5] switch to the UP position.
3. While holding the
[SW5] switch in the UP position, press and release the [EStop] switch. This enables the
“Download Password” mode.
4. Release the
[SW5] switch. The ACTIVE LED will flash once per second.
5. Toggle the switches in sequence: [SW3],[SW1],[SW4] and then [SW4] to the DOWN position to enter the
password code (3144), followed by toggling the [SW5] switch to the UP position. The ACTIVE and LOW BATT.
LED’s will flash alternately once per second. This confirms the T150 is sending “Calibration Data” to the R150.
6. Select and hold one of the “Proportional Functions” (i.e. [SW4] or [ROT CW]).
7. With the trigger OFF (fully released), the “MIN” level is set. The “MIN” level may be increased by toggling the
[SW5] switch up or decreased by toggling the [SW5] switch down.
8. With the trigger ON (fully engaged), the “MAX” level is set. The “MAX” level may be increased by toggling the
[SW5] switch up or decreased by toggling the [SW5] switch down.
9. To reset the “MIN” and “MAX” settings to the factory default, hold the [SW5] switch in either the UP or DOWN
position for 5 seconds.
10. To exit, press the [EStop] switch.
Required when replacing either the Transmitter or Receiver
The Transmitter has its ID Code factory programmed. Its matching receiver needs to have this same code
programmed into it. To do this, the Receiver needs to have its cover removed – refer to Figure 2. Follow the
procedure below to program the Receiver ID Code to match its corresponding Transmitter.
1. Release the
[EStop] switch on the T150.
2. Turn the
T150 on by toggling the [SW5] switch to the UP position.
3. While holding the
[SW5] switch in the UP position, press and release the [EStop] switch. This enables the
“Download Password” mode.
4. Release the
[SW5] switch. The ACTIVE LED will flash once per second.
5. Toggle the switches in sequence: [SW3], [SW1], [SW4] and then [SW2] to the UP position to enter the
password code (3142), followed by toggling the [SW5] switch to the UP position. Both the ACTIVE and LOW
BATT. LED’s will flash twice per second. This confirms the unit is in the “Ready to Download” state.
6. Press and hold the [SETUP] button on the R150 for 5 seconds. The STATUS LED on the R150 will flash once
per second while depressed and then begin flashing rapidly indicating that the R150 is ready to receive
“Configuration Data” from the T150. Continue holding the [SETUP] button after the STATUS LED begins
flashing rapidly.
7. Momentarily toggle the [SW5] switch to the UP position; this enables the T150 to send “Configuration Data” to
the R150.Release [SW5] and release the [SETUP] button.
8. Press the [EStop] switch to power down the T150, and restart the T150 – refer to STEP 2.

SW 5
SW 1 SW 2 SW 3 SW 4
SW 6
EStop
Transmitter / Receiver Replacement and Service
In order to program the R150 or replace the fuse, you will first need to
remove the circuit board from the housing of the R150. This is done by
releasing the two side tabs on the housing, and sliding the connector block
and circuit board out of the housing until the four STATUS LED’s are
visible and the [SETUP] SW1 button is accessible. See Figure 2.
Also refer to Setting ID Codes for a step by step procedure of setting ID
Codes to match on both the Transmitter and the Receiver.
Fuse Status LED’s
[SETUP] SW1
Figure 2
Switch Number Position Output Control Pin Assignment Color Code Function
UP Output 9 B3 Green
DOWN Output 10 B4 Green (Black/White)
UP Output 7 B1 White (Red/Black)
DOWN Output 8 B2 Red (Black/White)
UP Output 5 A10 Orange (Black)
DOWN Output 6 A12 Orange (Red)
UP Output 3 A9 White (Red)
DOWN Output 4 A11 Blue (Red)
UP Output 11 B5 White
DOWN Output 12 B6 Orange
UP Output 1 A7 Orange (Green)
DOWN Output 2 A8 Red (Green)
Released
Engaged
EStop EStop Output A5
Driver Power Driver Power Input A2 ]-- Jumpered Externally
Proportional Control
9 to 30VDC
Ground
A6
A3
Red
Black
T150 / R150 Switch Function Table
A4 Green (Black)Output 13
SW5
SW6
Trigger
SW1
SW2
SW3
SW4
Power
Ground

R150 Relay Outputs
A4
B1
A7
A8
A9
A11
A10
A12
B2
B3
B4
B5
B6
Power
EStop
R150 Internal
Ground
A3
Internal Power A6
A5
A2
Internally Fused
1
13
EStop Out
Driver Power Input
Jumpered on wiring harness
Troubleshooting Inputs and Outputs
Replaceable Parts
Inputs 4 x 0-5VDC analog inputs (factory
configurable only)
Outputs
Option 1 13 x Form Arelay, monitored, 3A max.
each, total combined current 10A
Option 2 12 x Form Arelay, monitored, 3A max.
each, total combined current 10A max.
1 x Proportional Control
Fuse MINI® Fuse Type,10A LittelFuse
OMNEX (p/n F0047) or equiv.
Mating Plugs OMNEX (p/n’s J0418 / J0419)
Pins OMNEX (p/n J0417)
Sealing Plug OMNEX (p/n J0421)
Wedge OMNEX (p/n J0420)
Switches OMNEX (p/n S0042)
EStop Switch OMNEX (p/n S0072)
EStop Contact Block OMNEX (p/n S0071)
Batteries OMNEX (p/n B0010) 4 x AA
I/O Diagram Deutsch Connector Pin Assignments
Bldg. 74 – 1833 Coast Meridian Road, Port Coquitlam, BC, Canada V3C 6G5
5.13”
4.00”
AB
4.92”
7.87”
4.13”
Dimensions
WARRANTY
OMNEX Control Systems Inc. Warrants to the original purchaser that the OMNEX
products are free from defects in materials and workmanship under normal use and
service for a period of ONE YEAR, parts (EXCLUDING: SWITCHES, CRYSTALS, OR
PARTS SUBJECT TO UNAUTHORIZED REPAIR OR MODIFICATION) and labor
from the date of delivery as evidenced by a copy of the receipt. OMNEX’s entire
liability and your exclusive remedy shall be, at OMNEX’s option, either the (a) repair
or (b) replacement of the OMNEX product which is returned within the warranty period
to OMNEX freight collect by the OMNEX APPROVED carrier with a copy of the
purchase receipt and with the return authorization of OMNEX. If failure has resulted
from accident, abuse or misapplication, OMNEX shall have no responsibility to repair
or replace the product under warranty. In no event shall OMNEX be responsible for
incidental or consequential damage caused by defects in its products, whether such
damage occurs or is discovered before or after replacement or repair and whether or
not such damage is caused by the negligence of OMNEX Control Systems Inc.
Neither OMNEX nor its Distributors shall be liable for any delay or failure of the
performance of any of its obligations under this agreement caused by acts of God,
labor disputes, embargoes, boycotts, shortage of parts or any cause beyond its
reasonable control.
Neither OMNEX nor its Distributors shall be responsible for incurred costs associated
with border clearance or with the delay of the OMNEX products in transit to OMNEX.
Any charges associated with the return of the OMNEX products may be subject
to billing to the original purchaser in the event that the OMNEX products are
NOT covered by the warranty as noted above.
Output 6
Output 4
Output 5
Output 3
Output 2
Output 1
Input 1
Driver Power
GND
Output 13
EStop Output
Power
2
3
4
5
6
1
12
11
10
9
8
7
6
5
4
3
2
1Output 7
Output 8
Output 9
8
9
10
11
12
7
Output 10
Output 11
Output 12
Connector A (Grey) Connector B (Black)
Factory Configurable Only
RS485 EN
RS485 A
RS485 B
Input 3
Input 4
Input 2
The R150 has 4 LED’s that are used to indicate device status:
ESTOP LED !
!!
!!!!
GREEN – indicates RUN
RED – indicates ESTOP
Flashing RED – indicates fuse blown or relay fault
FUNCTION/FAULT LED !!
!!
!!!
GREEN – indicates function ON, no fault
RED – indicates no voltage to relay, short to ground or blown
fuse
Flashing RED – indicates short to supply or shorted output relay
Not lit – indicates no function
LINK LED !!!
!!
!!
GREEN – indicates Link
RED – indicates No Link
STATUS LED !!!!
!!
!
GREEN – indicates STATUS OK
RED – indicates unrecoverable fault; requires factory authorized
service
Flashing RED – indicates low battery
The T150 has 2 LED’s that display the mode and status of the device
ACTIVE LED !
!!
!"
""
"!
!!
!
Momentarily ON or Flashing indicates Power Up procedure or
Programming status. LED will flash with each function during
normal operation indicating Transmit Status to the R150 is good
LOW BATT. LED !
!!
!"
""
"!
!!
!
Momentarily ON or Flashing indicates Power Up procedure or
Programming status
During normal operation, this LED will only flash to indicate
battery low
ACTIVE and LOW BATT. LED’s !
!!
!"
""
"!
!!
!
Both LED’s flashing in sync indicates one of the switches is stuck
NOTE: The Current Control Module may be
installed as an option giving the user Proportional
Control on output 13 of the R150 - refer to Current
Control Module Calibration for Proportional
Calibration procedures.
The Proportional Control option is available from
the factory in either Voltage Control, PWM or
Current Control.
R150
The R150 is internally fused as
shown using a 10A MINI® fuse.
Follow the steps in Transmitter /
Receiver replacement to open
the R150 for fuse replacement.
Other manuals for T150
2
This manual suits for next models
1
Popular Control System manuals by other brands
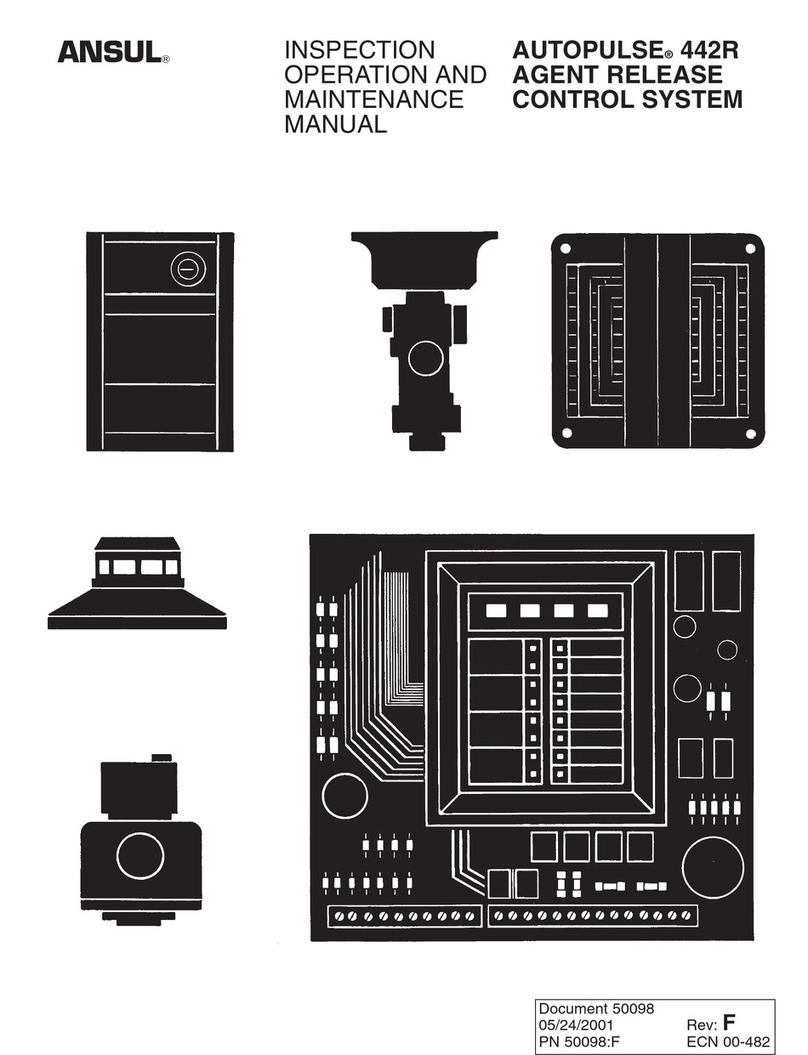
Ansul
Ansul AUTOPULSE 442R Inspection, Operation, and Maintenance Manual

VIPA
VIPA SM 231 manual
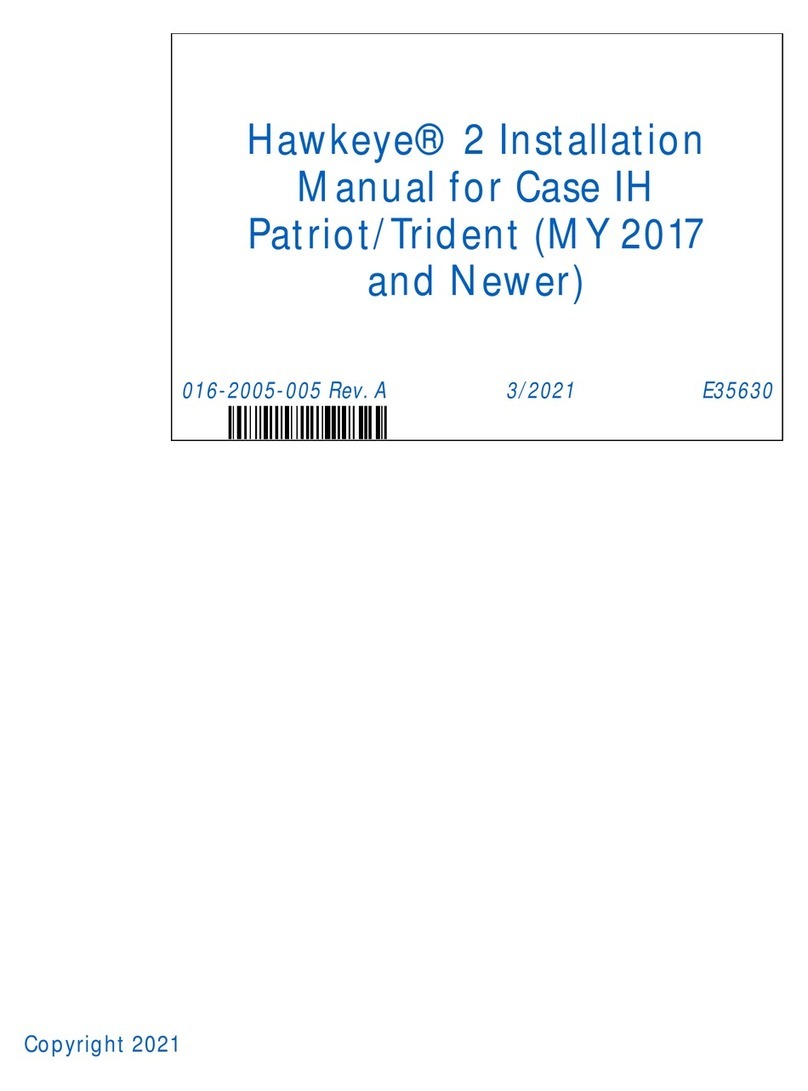
Raven
Raven RCM-Sprayer Hawkeye 2 installation manual
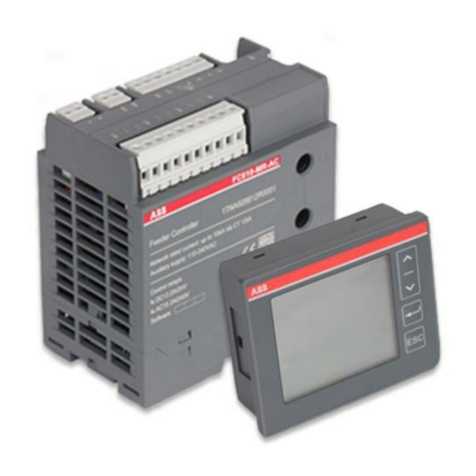
ABB
ABB LVS Digital FC610 user manual
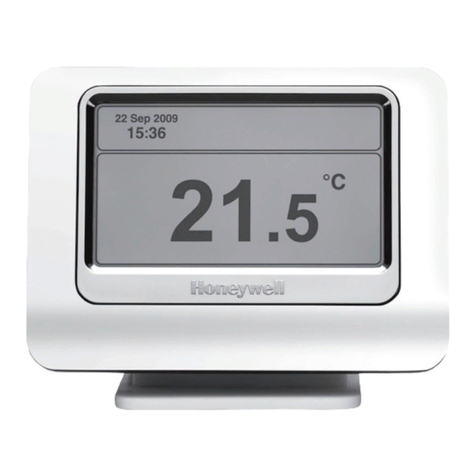
Honeywell
Honeywell EVOTOUCH CONTROLLER Installation
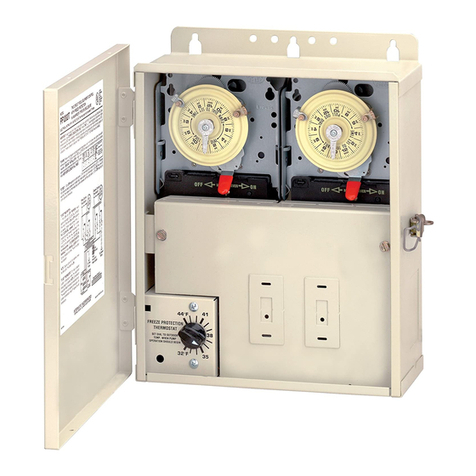
Intermatic
Intermatic PF1202T Installation, operation & service manual