Mentor radio M2115RCU Series User manual

Phone: (216) 265-2315 Fax: (216) 267-2915
www.mentorradio.com
1
Wireless Solutions for Advancing Communications
M2115RCU
RADIO CONTROLLER
OWNER’S MANUAL

Phone: (216) 265-2315 Fax: (216) 267-2915
www.mentorradio.com
2
Wireless Solutions for Advancing Communications
This owner’s manual applies to the following specific models:
AVIATION: M2115RCU-XXX
MARINE: M2115RCU-M
Mentor Radio produces a family of radio control units, also known as, Pilot Controlled Lighting (PCL),
or Pilot Activated Lighting (PAL) systems. This manual covers both aviation and marine band
versions for both the 25kHz and 8.33kHz channel spacing. The aviation band version is a VHF radio
that operates from 118-137MHz and the marine version is a VHF radio that operates in the frequency
range from 155-157MHz.
SAFETY
“Warnings” represent safety issues that if disregarded could cause serious injury or death to people.
“Cautions” represent safety concerns that if disregarded could damage equipment or cause personal
injury.
WARNINGS
This unit can be configured for operation from many different power sources. (10 to 30 VDC or
115 VAC or 230 VAC) Depending on the individual installation, dangerous voltages may be
present inside the unit’s printed circuit board mounting case. It is the user’s responsibility to
operate the unit safely for a particular installation.
1. High Voltage may be present inside the case when opened.
2. If installed outside, do not operate, test or power up the controller unit in the rain
with the NEMA enclosure opened and/or the case cover removed.
3. Maintenance of unit should be performed only by personnel qualified in electrical
safety.
4. Disconnect all electrical power prior to removing or performing maintenance on the
circuit board or on DIN rail mounted components.
5. Do NOT connect any external circuits rated with voltage higher than 230VAC to relay
contacts.
CAUTIONS
1. Do not connect electrical equipment to the controller with power applied.
2. When connecting the computer (PC) to the controller, ensure the power switch is
turned off.
3. Do NOT connect any input power other than that identified for the unit.

Phone: (216) 265-2315 Fax: (216) 267-2915
www.mentorradio.com
3
Wireless Solutions for Advancing Communications
Table of Contents
1. Safety Warnings 2
2. Component Layout 4
3. Controls Layout 5
4. Basic Features 6
5. Theory of Operation 7
6. General System Operation 7
7. Dip Switch Configuration Options 8
8. Installation 9
9. Testing, Programming and Adjustments 13
10. Periodic Maintenance 20
11. Troubleshooting 22
12. Schematics 25
13. Board Layout 30
14. Optional Accessories 31
15. Limited Warranty 32

Phone: (216) 265-2315 Fax: (216) 267-2915
www.mentorradio.com
4
Wireless Solutions for Advancing Communications
Component Layout
(Includes optional items)
AC Line Lightning Protector (opt)
Antenna Lightning Protector (opt)
Sensitivity Pot
DIN Rail with AC power plug
and CB's (opt)
Reset Switch Test Switch Communications Port
NEMA 4 Enclosure
(opt)

Phone: (216) 265-2315 Fax: (216) 267-2915
www.mentorradio.com
5
Wireless Solutions for Advancing Communications
Controls Layout
Antenna
Input – BNC (6)
Sensitivity
Potentiometer (5)
Reset Button (1)
Power Switch (4)
Test Button
(2)
3 Click Relay (9)
5 Click Relay (8)
7 Click Relay (7)
Communications Port (3)
GND (10)

Phone: (216) 265-2315 Fax: (216) 267-2915
www.mentorradio.com
6
Wireless Solutions for Advancing Communications
Basic Features
Channel Spacing: 25kHz or 8.333 kHz
Synthesized Tuning - Customer programmable. Utilizing a standard DB-9 serial cable
(included) use your PC to program the operating frequency using custom PC software.
Password authentication required to change operating frequency for increased security and to
prevent inadvertent changes.
Indicator lights - Colored LED’s light up to display relay activation. A STATUS LED flashes
once per second to indicate normal operation. A WINDOW LED turns on to indicates a mic
click has been detected and the unit is waiting for more clicks. Relays can only be energized
with the WINDOW LED is on.
Relays reactivate after power restoration – Automatically energizes those relays that were
energized prior to the moment power was lost. If the power is restored the timeout period is
reset to a full timeout period.
Operates from wide range of power sources – The controller can operate with any power
from 10VDC, 12VDC, 24VDC, 30VDC, 115VAC, or 230VAC. Conversion from DC to AC
power sources requires sending the unit back to the factory for re-configuration. Remote
locations may find it convenient to power the unit from a solar panel with a battery back-up to
simplify remote installations.
Test Button - Test relays and controller circuits without radio inputs.
Reset Button - De-energize relays before timeout expiration.
8 Different Time Out Values - No timeouts, 10 seconds, 5, 10, 15, 30, 45 & 60 minutes.
Available in 8 and 12 hour timeouts intervals upon special request.
Optional Weatherproof Enclosure - Unit fits into a 12”x6” fiberglass enclosure with built-in
mounting capability.
Optional Lightning Protection - Available for both AC line input and antenna input.
Power Status - Indication built into the STATUS LED.
Receiver Sensitivity Adjustment - Potentiometer adjustment allows setting receiver
sensitivity within the range of about 1 uV to more than 10,000 uV.

Phone: (216) 265-2315 Fax: (216) 267-2915
www.mentorradio.com
7
Wireless Solutions for Advancing Communications
Theory of Operation
The M2115RCU radio control unit consists of a radio receiver and a microprocessor-based
decoder/controller assembly. The receiver detects microphone “clicks”—short radio transmissions
when a user presses the push-to-talk (PTT) switch on an external VHF radio. The decoder operates
relays according to the patterns of clicks. The receiver is based on the model M15
receiver/transmitter. Except for the oscillator circuit, the transmitter circuits are not installed; the
oscillator is used to generate a test signal to check operation of the receiver and decoder/controller
assembly.
The receiver is a frequency synthesized dual conversion super heterodyne. It contains two mosfet
dual-gate mixers. The first local oscillator is frequency synthesized and operates at 400 mHz above
the channel frequency. The second local oscillator operates at 455kHz. The filtered output of the
receiver’s diode detector is connected to the input of the decoder/controller board where it is digitized.
The click detection and relay control logic is performed by the embedded microcontroller. The
microcontroller software determines if the signal is a valid radio click. If a valid click is received the
controller opens a window for the configured time interval to allow more clicks to be received. The
controller responds to 3, 5 or 7 pulses within the “window” time and energizes up to three relays. The
relay contacts are connected to the terminal strip on the decoder/controller board for controlling lights
or other external electrical equipment. For protection, relay contact connections from the
decoder/controller to external load circuits may optionally pass through three 5-ampere fuses or
circuit breakers.
The optional antenna lightning protector includes a replaceable gas discharge tube. The AC line
lightning protector also includes an LED which is normally illuminated indicating that the line protector
is operating properly. This LED will remain on even when the unit is turned off.
General System Operation
In order for a pilot to turn on the runway lights, he first sets his radio to the channel frequency used by
the airport radio control unit (M2115RCU). He then briefly presses and releases his push-to-talk
(PTT) microphone switch to produce a sequence of short “clicks”. The first microphone “click” starts
the “window” timer, after which the operator has either 3 or 5 seconds to complete the desired
sequence; either 3, 5 or 7 clicks. On the first click, the microprocessor turns on the “WINDOW” LED,
starts a timer and waits for more pulses. Once the “WINDOW” timer expires, the “WINDOW” LED is
turned off and the received pulse count is reset. During the time the window is open, any additional
clicks are received, and the response of the unit is governed by the selection of the various dip switch
settings. If three pulses are received, the 3-click relay is energized. On the 5th pulse, the 5-click relay
is energized, and on the 7th pulse the 7-click relay is energized. All energized relays remain
energized for the configured timeout period. At the end of this timeout period, all relays deactivate.

Phone: (216) 265-2315 Fax: (216) 267-2915
www.mentorradio.com
8
Wireless Solutions for Advancing Communications
During any time-out period, another series of microphone clicks may be transmitted, decoded and the
corresponding relays are energized provided the relay “deactivate disable dip switch” (switch 5) is not
enabled. The configuration of the following sections define how the unit will perform.
Dipswitch Configuration Options
To aid in the configuration, there is a visual aid in the PC software included to allow viewing the
switches that are set and the interpretation of their behavior. The testing of this behavior can be
performed from either the controller or the PC.
Timeout Period (Dipswitch 1, 2, and 3)
The following chart determines the switch settings for the corresponding time out period.
Timeout Period
SW 1
SW 2
SW 3
No Timeout ON ON ON
10 Second OFF ON ON
5 Minute ON OFF ON
10 Minute OFF OFF ON
15 Minute ON ON OFF
30 Minute OFF ON OFF
45 Minute ON OFF OFF
60 Minute OFF OFF OFF
Window Time (Dipswitch 4)
Off - 5 Second Window
On - 3 Second Window
Relay Deactivate Disable (Dipswitch 5)
Off – Normal Operation
On – Enable Function
With this feature enabled the only way to de-energize energized relays is at the end of the timeout
period.

Phone: (216) 265-2315 Fax: (216) 267-2915
www.mentorradio.com
9
Wireless Solutions for Advancing Communications
Mutually Exclusive Configuration (Dipswitch 6 Off)
This mode is programmed to allow only one of the relays to be energized at any one time. For
example, as before, the first click starts the configured “Window” timer. (3 seconds or 5 seconds). If 3
clicks are received before the “Window” timer is expired this causes the 5-click and 7-click relays to
drop out. On a fifth click, the second relay will pull-in again, and on a seventh click the third relay will
pull-in again. In this way, a pilot can change the lighting or which loads are controlled, if desired,
without waiting for the end of the time-out period. A new time-out period will begin at the end of the 5
second window.
Mutually Exclusive Disabled Configuration (Dipswitch 6 On)
This is the normal operating mode. This allows the relays to all be energized during the timeout
period. When each new sequence of clicks is received the corresponding number of relays energizes
without de-energizing any other relays. For example, the 3-click relay stays energized upon the
receipt of the 5th new click at which time the 5-click relay energizes.
Click-Off Function Configuration (Dipswitch 7 On, 8 Off)
5 Click-Off Enabled Configuration (Dipswitch 7 Off, 8 Off)
This configuration is primarily suited for customers who only want to turn one set of lights or
equipment on and off. The normal configuration will not allow the user to manually de-energize the
relays once the timeout period is started. This 5 click off option allows that. If only the 3-click relay is
installed to control one item, the user can turn on the equipment with 3 clicks and turn off the
equipment by clicking 5 times.
7 Click-Off Enabled Configuration (Dipswitch 7 Off, 8 On)
This is the same configuration as the 5 click-off, except that it allows the use of 2 different relays to be
controlled and allow the pilot to manually turn off both with 7 clicks. .
Installation
Depending on which model M2115RCU you purchased, installation can vary. To protect your
investment, we recommend lightning protection for all models installed outdoors. The following
considerations apply to every M2115RCU model.

Phone: (216) 265-2315 Fax: (216) 267-2915
www.mentorradio.com
10
Wireless Solutions for Advancing Communications
Choose a proper site*: The M2115RCU may be installed either indoors or outdoors.
Considerations about antenna placement, power input availability and relay connection requirements
should be taken into consideration when selecting a suitable installation location. (*Note: See installation
instructions for each model listed for individual recommendations.)
NOTE: When the M2115RCU is mounted outside, a location should be selected so that the antenna
is not “shadowed” by buildings or other obstructions in the direction from which aircraft may approach.
For maximum radio range, mount the antenna as high as practical. For outdoor operation use, a
optional NEMA enclosure is required. Application of a waterproof sealant over external coaxial
connectors is recommended along with all electrical wires connecting between the internal relays and
external equipment.
Configuration: This step is only required if the unit is not configured at the factory or if changing the
configuration dip switches is required. Connecting a PC to the enclosed DB-9 serial communications
port will allow the user to change the operating frequency. NOTE: only authorized persons are
allowed to change the operating frequency in the computer program. Access to this functionality is
password protected. The PC software also allows the user to test the new dip switch settings before
physically changing the switches on the radio control unit. Once the relay performance is verified the
new switch settings are to be made permanent, click the button “Get Physical Dip Switch
Settings.”(NOTE: 8.333Hz channel spacing requires 2 software programs to set the functionality; one
for setting the frequency and the other to set the performance “dip switch” settings.) Both are included
on the CD that is included with each unit.
Testing: After configuration, test the controller using the “Test” button in the PC board.
Installation for each model M2115RCU is as follows:
M2115RCU-BNC
1. Choose a location where:
No metal or other conductive particles could come in contact with the printed circuit
board of the M2115RCU-BNC radio control unit.
No fluids could splash onto printed circuit board of the M2115RCU-BNC.
Unit will not be exposed to severe temperature changes. (near furnaces or air
conditioners)
2. Connect relay and power wires to green connector. If unit is configured for AC power,
connect your power ground to the plate ground stud.
3. Connect antenna to printed circuit board BNC RF connector using adapter (included).

Phone: (216) 265-2315 Fax: (216) 267-2915
www.mentorradio.com
11
Wireless Solutions for Advancing Communications
M2115RCU-ALC
Aluminum case with external terminal boards on the rear and an antenna input BNC connector on the
front.
1. Remove the four case screws and mount the case to an appropriate mounting fixture so
that the unit is secure before connecting wires.
2. Connect control relay wires to 9 terminal strip as follows.
Pin 1 : K1-NO
Pin 2 : K1-C
Pin 3 : K1-NC
Pin 4 : K2-NO
Pin 5 : K2-C
Pin 6 : K2-NC
Pin 7 : K3-NO
Pin 8 : K3-C
Pin 9 : K3-NC
3. Connect power wires to 3 pin terminal strip. If connecting M2115RCU-ALC to 10-30VDC
Pin 1 : DC + (pos)
Pin 2 : DC - (minus)
Pin 3 : GND (earth ground)
If connecting M2115RCU-ALC to 115VAC
Pin 1 : AC-Line
Pin 2 : AC-N
Pin 3 : AC-GND
4. Connect antenna to printed circuit board BNC RF connector using adapter (included).

Phone: (216) 265-2315 Fax: (216) 267-2915
www.mentorradio.com
12
Wireless Solutions for Advancing Communications
M2115RCU-STC
1. Install case to appropriate mounting fixture.
2. Install control relay and power wires through the NEMA case and attach to green PCB
mating connector as follows.
Pin 1: K1-NO
Pin 2: K1--C
Pin 3: K1-NC
Pin 4: K2-NO
Pin 5: K2-C
Pin 6: K2-NC
Pin 7: K3-NO
Pin 8: K3-C
Pin 9: K3-NC
Pin11: AC-N (for a DC configuration connect to –DC).
Pin 12: AC Line (for DC configuration connect to +DC).
3. Connect power input ground to enclosure ground terminal board.
4. Install antenna to exterior UHF feed thru connector on NEMA enclosure.
M2115RCU-FGC
1. Installation procedure is the same as M2115RCU-STC. (See above procedure).
Connections
Antenna Connector: Standard UHF coaxial antenna.
Power and Control:
The electrical connections for power and control are normally made via two 7/8” holes in the
enclosure. Wiring may be connected through conduits, or as required by local electrical codes. The
contacts of the relays on the decoder assembly are rated for 5 amperes at 120 VAC or 2.5A at
240VAC.
Follow manufacturer’s installation instructions to install antenna. Depending on the model of
M2115RCU purchased, an adapter may be necessary. If the antenna provides a UHF style
connector, it will be necessary to install a UHF female to BNC male adapter in order to connect the
antenna coax to the M2115RCU antenna input connector. Each radio controller comes with a coaxial
cable (6”) with a BNC connector that attaches to the controller’s electrical board on one end and a
UHF connector on the other end.

Phone: (216) 265-2315 Fax: (216) 267-2915
www.mentorradio.com
13
Wireless Solutions for Advancing Communications
When the M2115RCU is mounted outside, a location should be selected so that the antenna is not
“shadowed” by buildings or other obstructions in the direction from which aircraft may approach. For
maximum radio range, mount the antenna as high as practical. For outdoor operation, use of an
optional NEMA enclosure is required. Application of a waterproof sealant over external coaxial
connectors is recommended along with all electrical wires connecting between the internal relays and
external equipment.
Testing, Programming and Adjustments
Testing
Testing consists of operating the unit such that the control relays energize and de-energize to verify
that equipment connected to the relays are operating correctly. Testing the relays consists of either
actual energizing of the physical relays or performing a simulated energizing of the relays to test logic
and timing. To test the actual energizing of the relays, the test may be performed with or without the
aid of a PC or radio. In order to test the receiver portion of the controller any aviation band transceiver
may be used to produce the necessary microphone clicks. Customers may also test the physical
energizing of the relays and the controller/decoder's ability to energize the relays by performing a test
by pushing a test button installed on the front panel. The reset button cancels remaining timeout
interval and de-energize all relays.
Connecting a PC to the M2115RCU and running “test” using the M2115RCU-PC windows based
program allows users the ability to run tests from the controller. Further, the operating frequency may
be read directly from the controller and viewed on the PC to verify the correct operating frequency.
(NOTE: Please use correct programming software (25kHz or 8333kHz channel spacing) to verify the
correct operating frequency. Use the 25kHz programming software to verify the functionality of the
dip switch.)

Phone: (216) 265-2315 Fax: (216) 267-2915
www.mentorradio.com
14
Wireless Solutions for Advancing Communications
Testing using radio:
Press the microphone button 3, 5 & 7 times each to verify relays energize and de-energize according
to dip switch configuration settings. (Allow time for window LED to extinguish before starting next
series of clicks.)
Testing using Test button on M2115RCU:
1. Verify that the STATUS LED on the Controller PCB assembly is on and blinks at a rate of
once per second.
2. Press test button 3, 5 & 7 times each to verify relays energize and de-energize according to
dip switch configuration settings. (Allow time for window LED to extinguish before starting
next series of clicks)
Testing using M2115RCU-PC program:
1. Connect PC communications port cable.
2. Connect the software using the following section procedure “Programming” steps 1-6 and
“Configuration” step 10. Select “Test From PTT on Controller” as “Test Target”.
3. Click PC Test button 3, 5 & 7 times each to verify relays energize and de-energize
according to dip switch configuration settings. (Allow time for window LED to extinguish
before starting next series of clicks)
Simulated Testing using M2115RCU-PC program may be performed the same as testing using
M2115RCU-PC program above except select “Test from Computer” as “Test Target”.

Phone: (216) 265-2315 Fax: (216) 267-2915
www.mentorradio.com
15
Wireless Solutions for Advancing Communications
Programming
The programming procedure is required to change the operating frequency. Once set this should not
need to be changed, but may be viewed to ensure correct programming of the operating frequency.
The configuration procedure is available to aid customers when changes to the dip switch settings are
desired or needed.
For programming, simulated testing and adjustments, the enclosure door must be
opened. WARNING. Since the enclosure may contain 120 VAC or higher power present
on exposed terminals, the following should be done only by persons trained in safety
precautions for these conditions.
1. Gain access to the M2115RCU Communications Port connector. (See Component Layout
diagram - page 5)
2. Connect serial cable between computer and controller. Ensure that the controller power is
off before connecting the cable.
3. Run M2115RCU-PC software.
4. Set the communications port to the correct serial port. If this is the first time the
M2115RCU-PC software is run or the serial cable is connected to a different physical port
that the last time it was run, click Communications Port Select, and then click on the
corresponding port for the physical connection to the controller serial cable. If the
M2115RCU-PC software was previously run and the same port is currently being used, this
step is unnecessary.
Software Connection to M2115RCU
1. From M2115RCU-PC main screen click Configuration Connect.
2. To initiate communications with the controller press and hold the controller “Test” button
before turning on the controller power switch. After turning on the power switch, release
the “Test” button. The M2115RCU-PC menu configuration should change from gray to
black (enabled) to indicate that you are connected to the PC. NOTE: it is normal for the
RCU to not blink the STATUS LED when connected to a PC.
Changing the Frequency (25 KhZ Channel Spacing)
1. Click M2115RCU-PC Configuration | Sign In. If this is the first time the software is used, “Sign
In” will be disabled. Go to Configuration | Create New Password to create a password. This
password is used to authenticate the user to allow changing the operating frequency. If a
password did not exist before, and it was created with “Create New Password”, pass step 8
because the user is now signed in. If a password already existed, click Sign In.

Phone: (216) 265-2315 Fax: (216) 267-2915
www.mentorradio.com
16
Wireless Solutions for Advancing Communications
2. Click “View/Set Frequency”. Enter the appropriate operating frequency. Click the “Save
Frequency” button to write the frequency to the controller. NOTE: The frequency can only be
changed after the user is “signed in”.
Changing the Frequency (8.333 KhZ Channel Spacing)
The software is a self-contained executable file that can be run from any directory in a computer
storage system. (NOTE: the software will program any Mentor Radio RCU frequency and not only
8333Hz versions.)
Make sure that the “COM” port is installed on the computer before running the programming software.
The program scans for COM ports upon running, but will not detect them if they are installed after the
program starts.
1. Turn on the M2115RCU while holding down the “test button,” this is the same as the other
software for 25 kHz.
2. Connect the serial cable to the DB9 connector on the M2115RCU.
3. Run the executable file. The following dialog box should appear. (Figure 1)
4. Click on the pull down box under the ”Choose the COM port:” label.
5. Choose the COM port that will be connected to the RCU.
Figure 1

Phone: (216) 265-2315 Fax: (216) 267-2915
www.mentorradio.com
17
Wireless Solutions for Advancing Communications
6. Press the “Put in Program Mode” button. (Figure 2)
7. Enter the desired frequency in the Frequency box. Frequency must be entered in Hz format.
There should be 9 digits for each frequency. (Figure 3)
Figure 3
Figure 2

Phone: (216) 265-2315 Fax: (216) 267-2915
www.mentorradio.com
18
Wireless Solutions for Advancing Communications
8. Press the “Send” button. (Figure 4)
The M2115RCU will change frequency right after the ”Send” button is pressed. Multiple frequencies
can be entered, but only the last one entered before the M2115RCU is turned off will be remembered.
9. Turn the power to the M2115RCU off. The frequency is now programmed.
The table below, figure 5, shows all the frequencies that are allowable in the range of between every
100 kHz in the total frequency range of 118MHz to 137MHz.
Figure 5
The frequency that can be entered takes the format of: 1XXX + one number in table.
For example, a valid frequency would be 124583333. Where 1245 is the 1XXX part and the 8333 Hz
is a frequency in the table.
Frequencies available between 'Kilo
hertz'
08333 16667 25000
33333 41667 50000
58333 66667 75000
83333 91667
Figure 4

Phone: (216) 265-2315 Fax: (216) 267-2915
www.mentorradio.com
19
Wireless Solutions for Advancing Communications
Configuration
This section describes how the software may aid the customer in selecting the physical dipswitch
settings to ensure the controller is operating as expected. This procedure may be used with the 25
kHz software whether the controller is connected to the PC or not. Using the software without the
controller allows the user to test a new dipswitch setting without actually affecting the actual controller
relays or stressing the connected control circuits. If the user wishes to test new configuration settings
without connecting to the RCU, simply perform step 3, disregarding steps 1-2, and steps 4-9.
1. Click under Configuration “Run Tests”. Then click the tab “Current Settings”. Then select
the settings that you want to be tested (See “DIPSWITCH CONFIGURATION OPTIONS”
for the description of these settings). To select where to test from, select the “Test Target”
menu option. To enter the test, click on the “Enter Test Mode” button. If testing from the
computer, press the “Test” button in the program. If testing from the controller, press the
“Test” button on the controller. In both cases, operation reflecting the “Current Settings” will
be seen on both the controller and PC. If the “Current Config” is desired as the normal
controller configuration, click on the “Dipswitch Visual” tab. Use the image of the “Current
Dipswitch” as a guide and set the controller dip switches.
2. Verify your switch settings by clicking the “Press to get your Physical Configuration” button
on the dipswitch visual tab. The display for the physical dipswitch should change to reflect
the new dipswitch settings. The images between the Physical and Current Dipswitch
settings should be in agreement. You can also confirm the physical switch settings by
clicking the “Physical Dipswitch Config” tab. The settings should agree with your desired
settings from the “Current Config” tab.
3. Click “Back” and then “Exit” to shut down M2115RCU-PC program.
4. Turn off the controller.
5. Disconnect serial cable.
NOTE: If the user wishes to test the controller using actual radio clicks, it is necessary to disconnect
the M2115RCU-PC software. To disconnect the software, click back, but do not click “Exit” on the
main screen. Click “Communications Disconnect”. The STATUS LED should blink. The controller
is now operating normally
After the complete M2115RCU is installed, it is essential that daytime tests be conducted to confirm
that the system operates as expected. Results from these tests may require adjusting the sensitivity
potentiometer to achieve desired performance.

Phone: (216) 265-2315 Fax: (216) 267-2915
www.mentorradio.com
20
Wireless Solutions for Advancing Communications
Adjustment
Setting the Sensitivity Potentiometer (5) requires no tools. To adjust the sensitivity potentiometer, (5).
simply turn the shaft of the potentiometer (5) counter-clockwise (CCW) to increase sensitivity and
clockwise (CW) to decrease sensitivity.
Periodic Maintenance
Periodic maintenance/inspection is recommended. Customer may determine appropriate time
interval for their installation. Check the following items:
1. Remove accumulated dust, dirt, and moisture from inside of the enclosure.
2. Inspect all electrical connections and wires. All connections should be secure and free from
corrosion.
3. Test per section “Testing” (page 12)
4. If AC line lightning protection is installed: Verify that the LED on the AC Line protector is
ON. CAUTION: Failure to routinely inspect for and correct this condition may result in
damage to the unit in the event of a lightning strike. If at the time of inspection the green
LED is blinking four times per second rather than the normal once per second, the
microprocessor’s “watchdog” feature has detected an error in its operation, but has
corrected the problem. If it blinks sixteen times per second the error was caused by a
power “brown out”; that is, the 120 VAC line voltage at some time has fallen below the 98-
132 v operating range. NOTE: these fast blinking rates are intended to alert users to a past
problem that has been self corrected, not that there is an existing problem. These problems
may have been of such short duration that they were not noticed. The blinking LED may be
reset to once per second either by pressing the small reset switch button near the LED, or
by moving the on-off slide switch briefly to off, then back on.
This manual suits for next models
4
Table of contents
Popular Controllers manuals by other brands
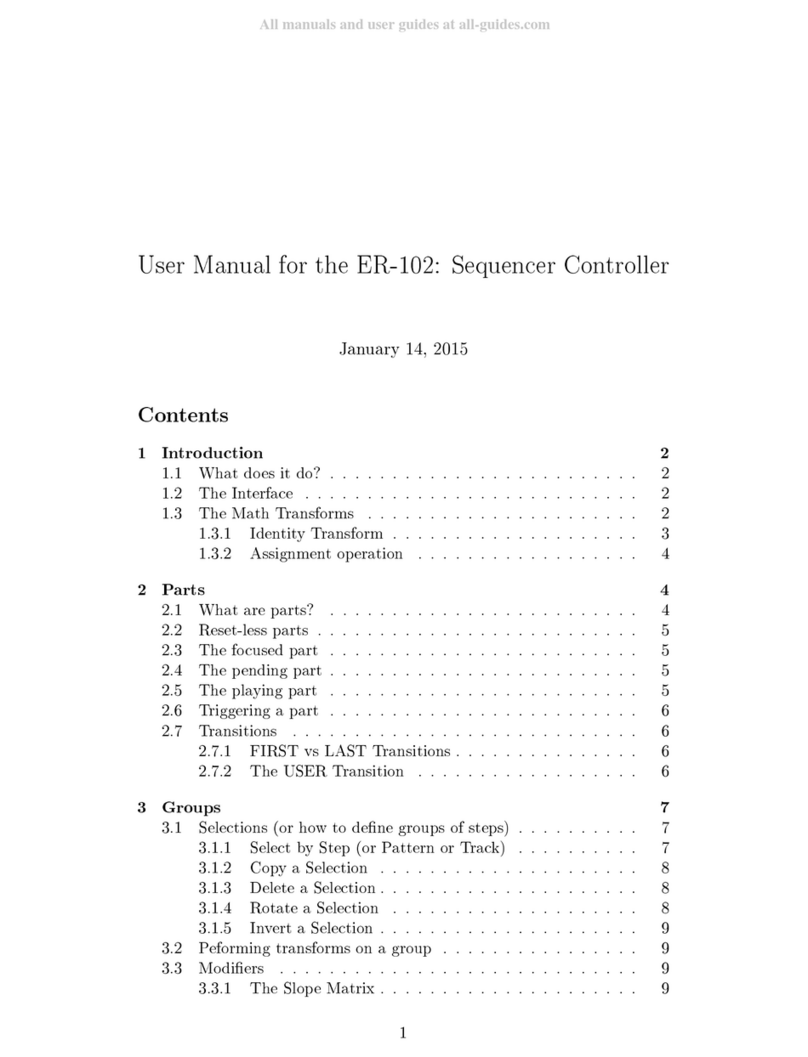
Orthogonal Devices
Orthogonal Devices ER-102 user manual
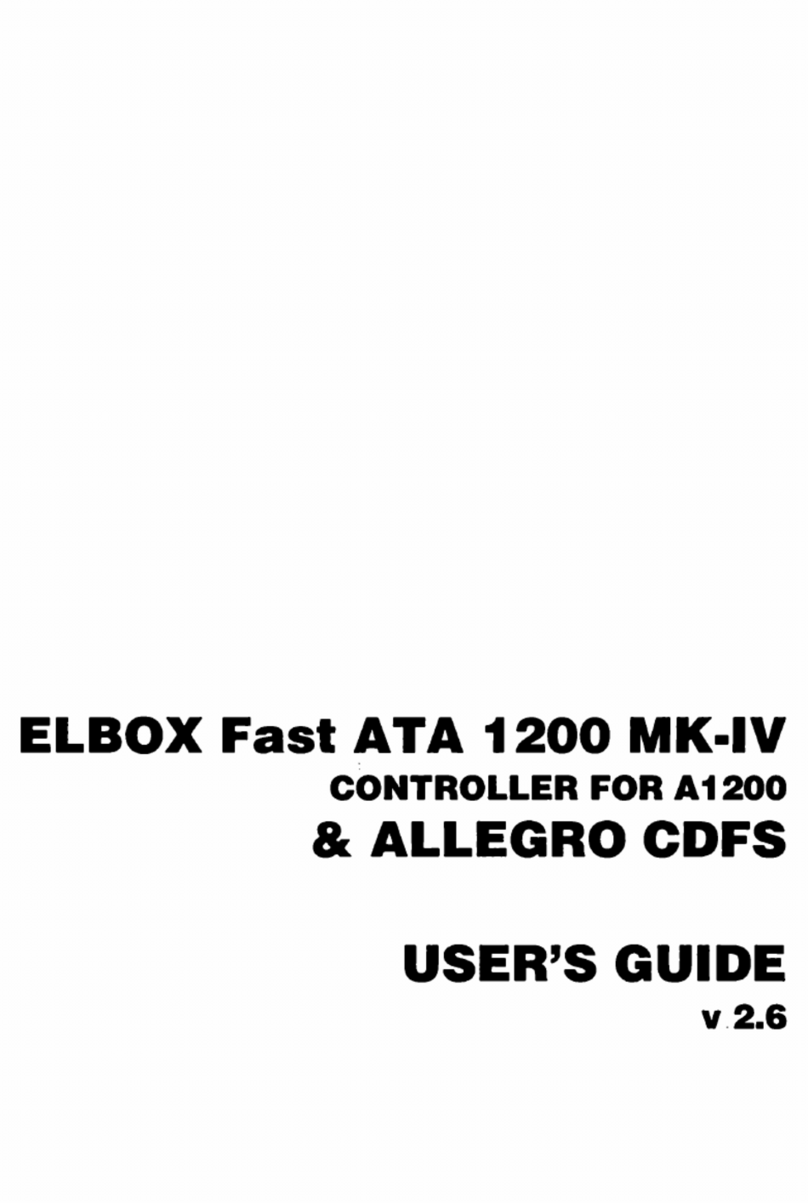
ELBOX
ELBOX Fast ATA 1200 MK-IV user guide
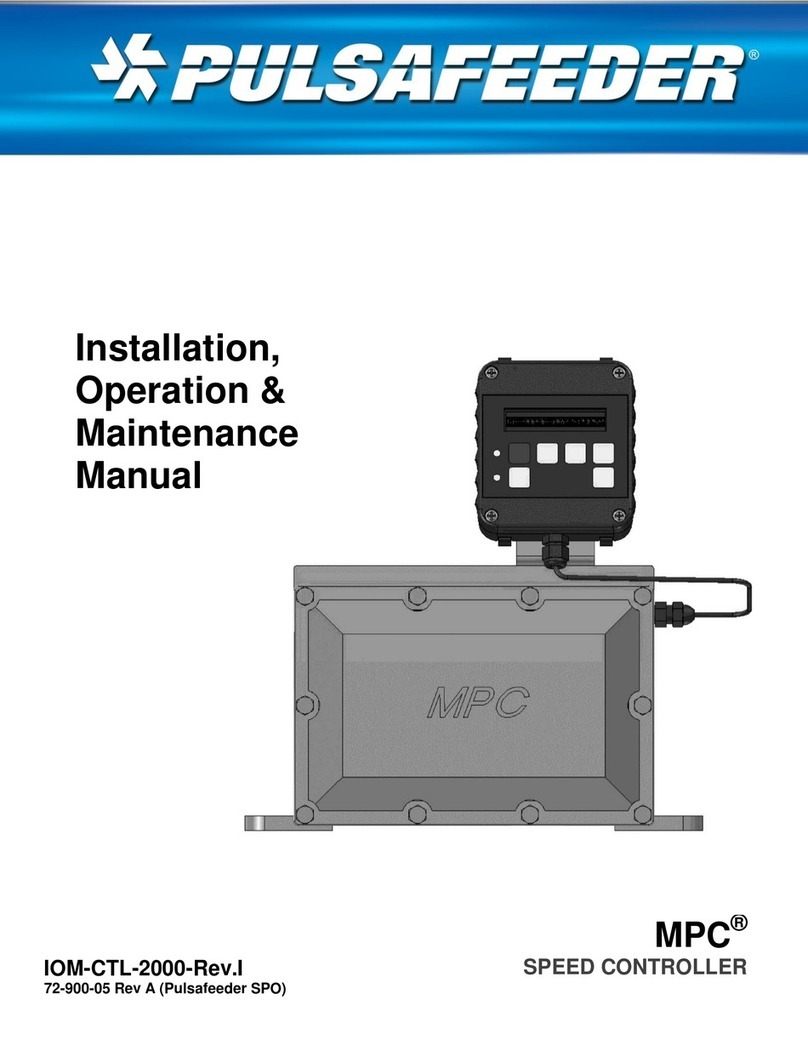
Pulsafeeder
Pulsafeeder MPC Installation, operation & maintenance manual
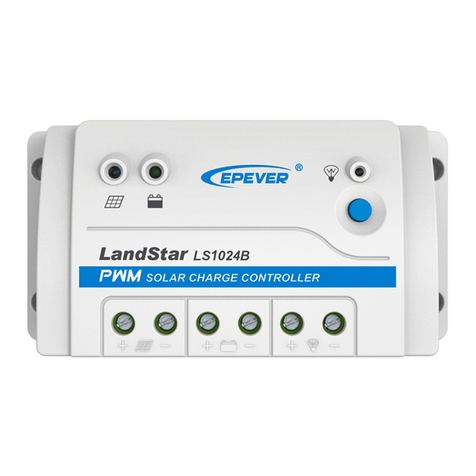
Epever
Epever LS-B Series quick start guide
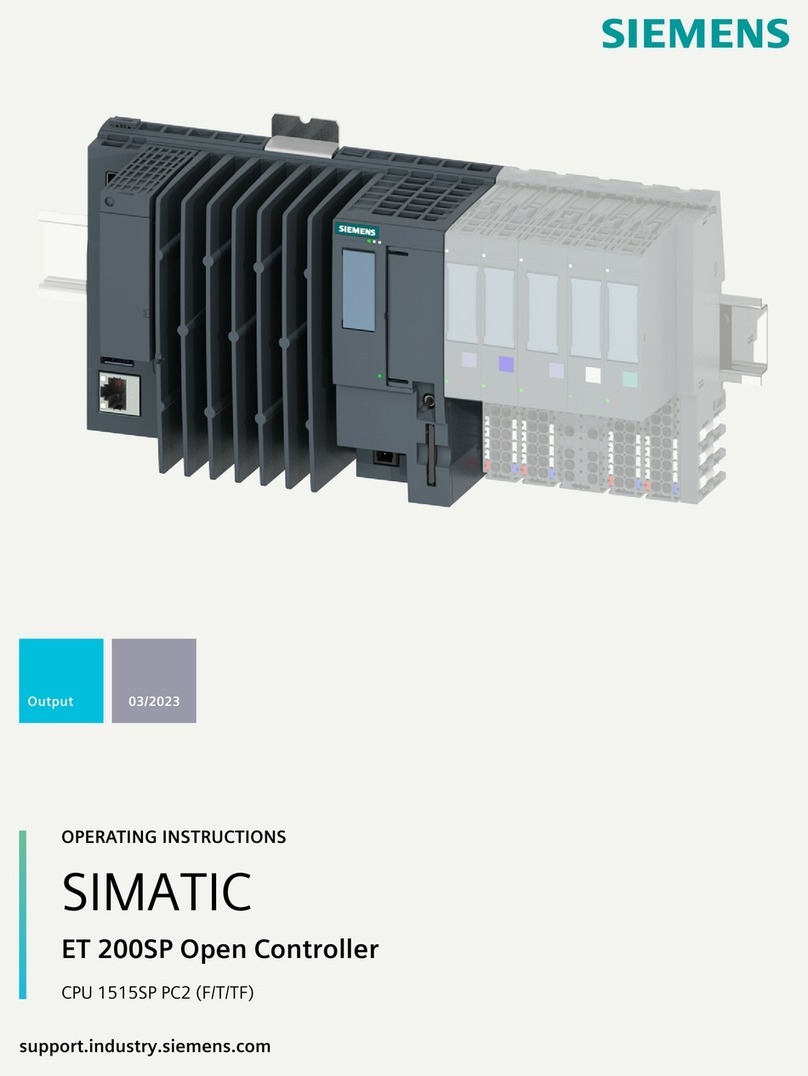
Siemens
Siemens SIMATIC ET 200SP operating instructions
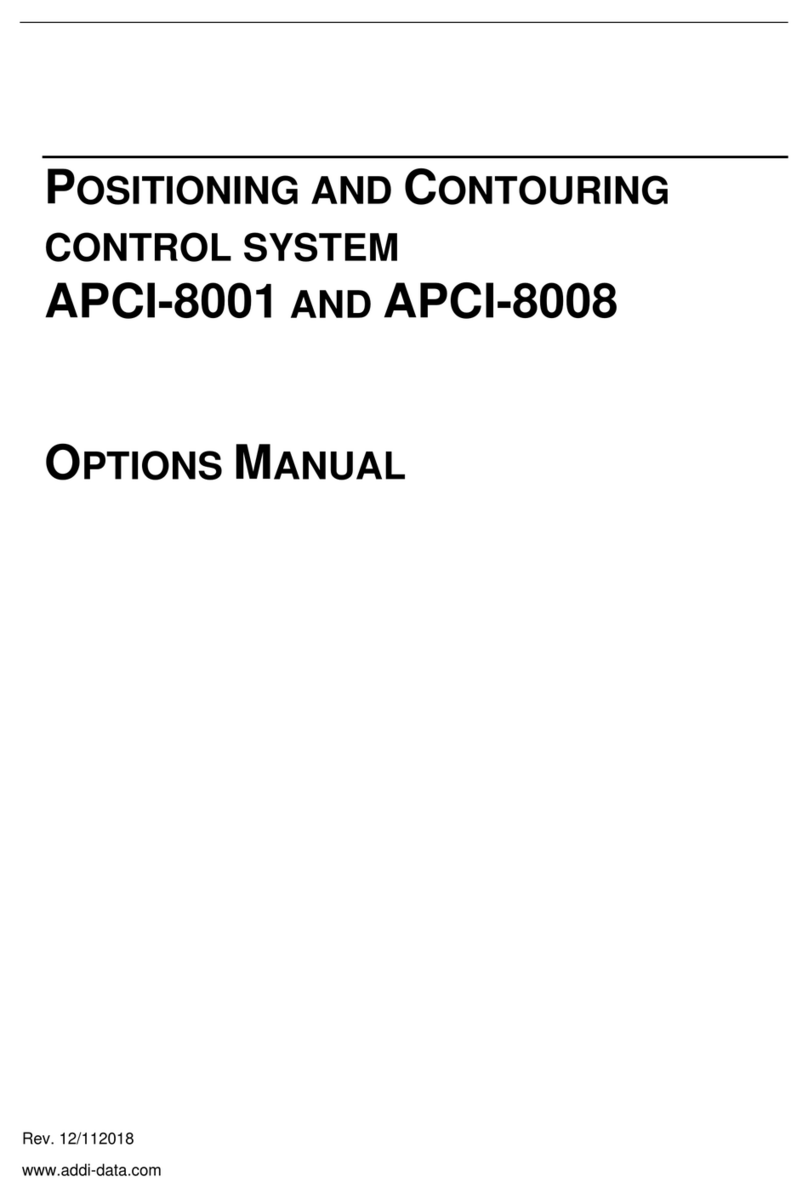
Addi-Data
Addi-Data APCI-8001 Option manual
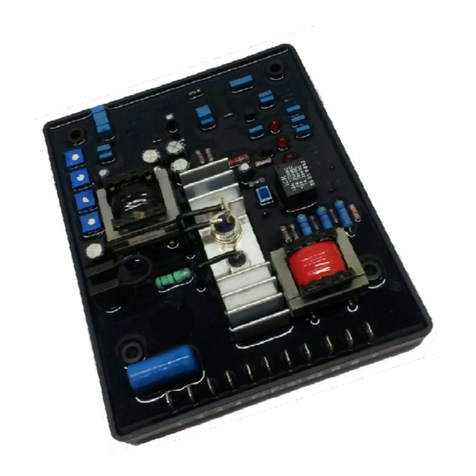
WEG
WEG AVR-A-OPT-07 Installation, operation and maintenance manual
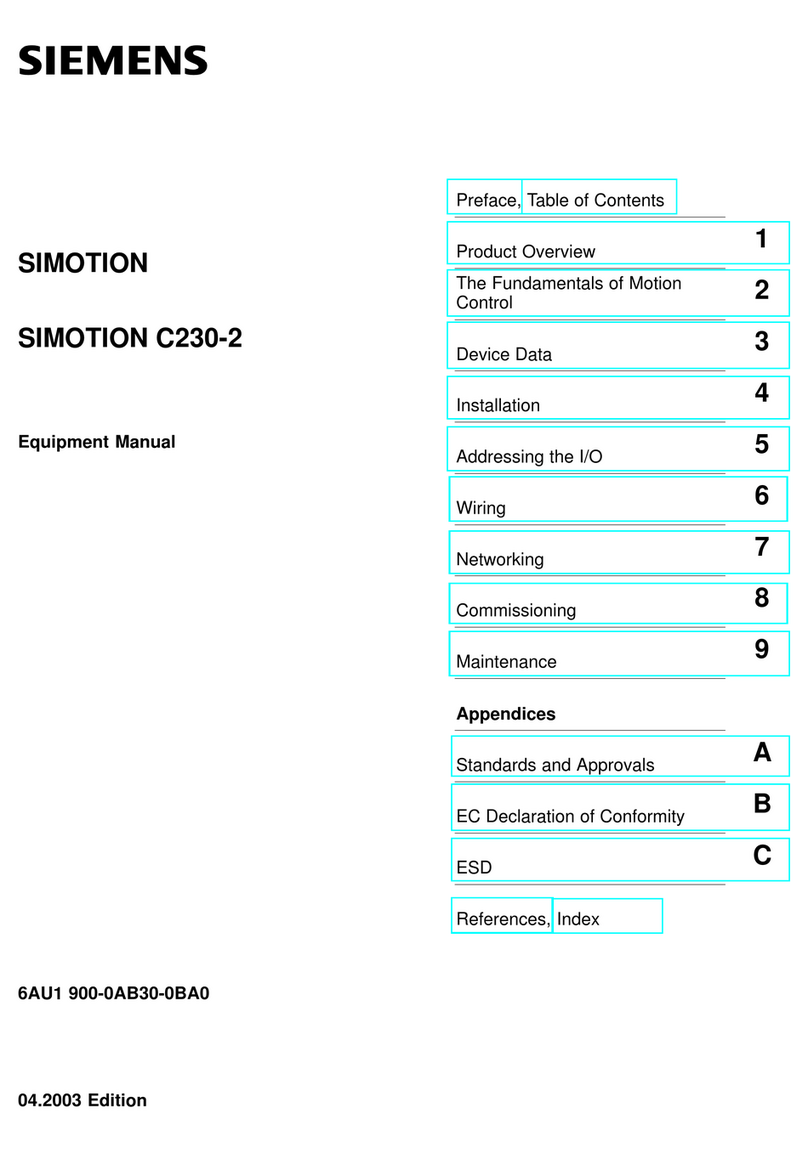
Siemens
Siemens SIMOTION C230-2 Equipment manual
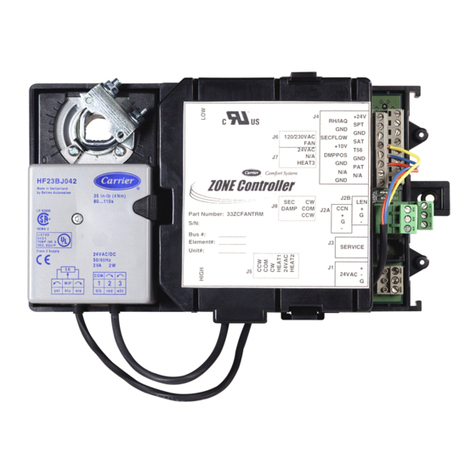
Carrier
Carrier 33ZCFANTRM Installation, Start-Up and Service Instructions

Swagelok
Swagelok RHPS Series user manual
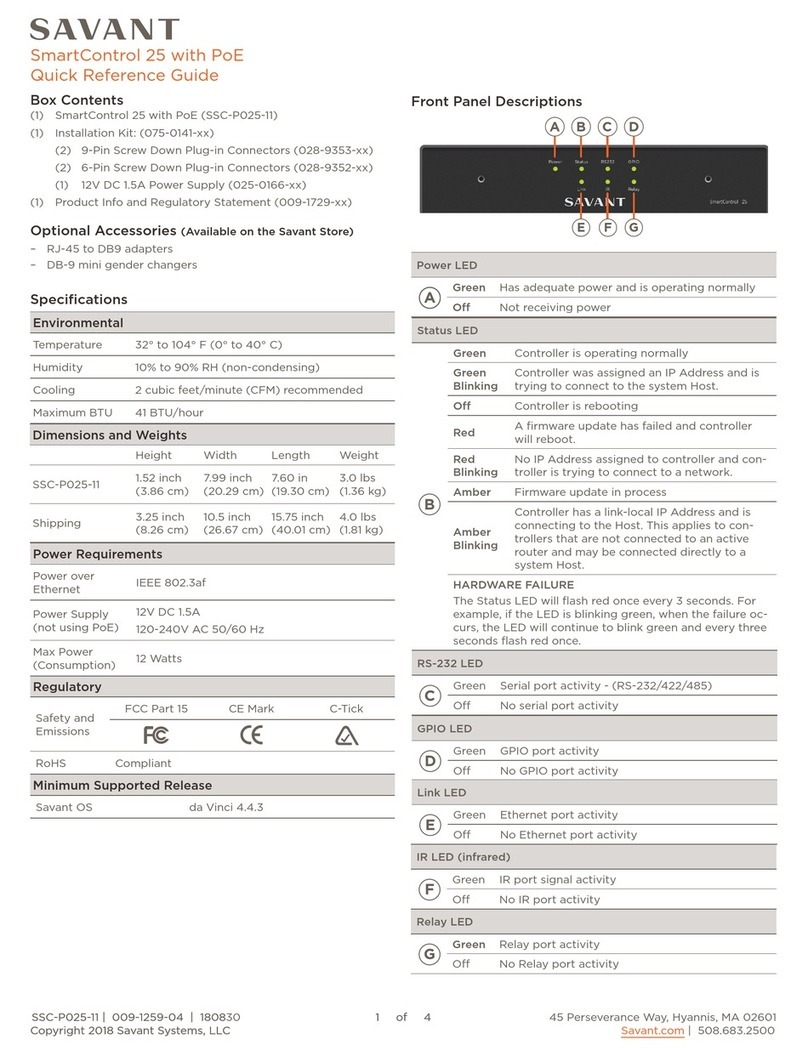
Savant
Savant SmartControl 25 Quick reference guide
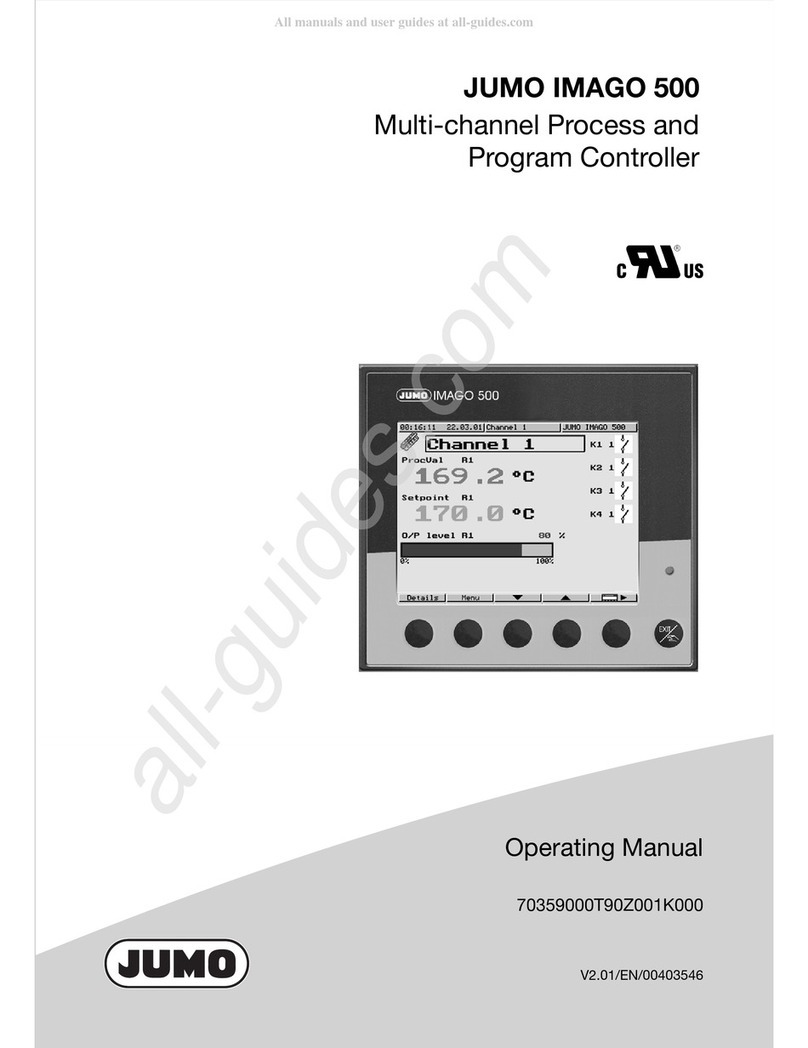
JUMO
JUMO IMAGO 500 operating manual