Microflex MicroLink-HM 101-0035 User manual

Setup Software
Installation
Operation
& Specifications
Manual
620-0021 R2 © Microflex 2016-2021
101-0035
RS-485 MicroLinK HM
RS-485 HART Protocol Modem
HART Device to Modbus Accumulator
DIN Rail Mount
The RS-485 MicroLink-HM 101-0035 is an RS-485 to HART® protocol modem with managed HART master ming to
funcon as either a primary or secondary HART master - eliminang the need for external CD monitoring and RTS
control. It can also be used as a HART to Modbus Concentrator polling up to 16 HART devices. An external 5 to 30
volts DC power supply is required to power the unit.
When used as a HART protocol modem it provides the hardware interface between Highway Addressable Remote
Transducer devices (HART) and an RS-485 network. Serial port baud rates can be set from 1200 to 57,600 and parity
can be odd, even, or none. HART protocol communicaons between the RS-485 MicroLink-HM and HART devices is
always 1200 baud, odd parity.
RS-485 MicroLink-HM can be configured to poll up to 16 HART devices and save the HART device data into modbus
registers. Modbus RTU commands can then be used to read the HART device data. Configuraon is simple using
the included HM Configuraon soware. Sengs are saved in modus registers so modbus RTU commands can also
be used to edit the MicroLink sengs. No special configuraon cable is needed for setup as communicaon is done
using the RS-485 port A and B. For configuraon your PC will need an RS-485 port or a suitable converter, such as
the Microflex 101-0020 USB to RS-485 converter or the Microflex 101-0009 RS-232 to RS-485 converter.

Finding the COM Port Number
You will need to know the COM port number the RS-485 MicroLink-HM modem is connected to. To see a list of COM
ports installed on your PC, open the Device Manager and select View > Devices by Type. Expand Ports (COM & LPT) to
see the list of available COM ports. RS-485 MicroLink-HM is compable with RS-485 to USB or RS-232 serial converters.
HART Protocol Modem
The RS-485 MicroLink-HM ships configured to operate as a HART protocol modem. Connect the A and B terminals to
an RS-485 port and provide a power supply. Power must be supplied by an external 5 to 30 volts DC power supply.
Refer to the Power Supply secon in this manual for details. If your PC does not have an RS-485 port you will need to
use an RS-485 converter. Microflex offers the 101-0020 USB to RS-485 converter and the 101-0009 RS-232 to RS-485
converter.
RS-485 MicroLink-HM is compable with most HART configuraon and test soware. Included on the CD is the
PACTware FDT frame, HART Protocol DTM, and Microflex Generic DTM soware. For informaon on installing PACTware
and the DTM, please reference the PACTware Quick Start Guide.
To funcon as a HART protocol modem the serial port is typically set to 1200 baud, odd parity. Most HART soware
will require this seng. It is possible to set the serial port to other baud rates and parity sengs. This is helpful when
connecng the RS-485 MicroLink-HM to a device that does not offer 1200 baud. In this case RS-485 MicroLink-HM will
receive the HART command at the higher baud rate then transmit the HART data at 1200 baud, odd parity onto the
HART loop. The 1200 baud, odd parity HART reply packet is received by the RS-485 MicroLink-HM modem and then
transmied back at the higher baud rate.
If the RS-485 MicroLink-HM is configured to Fill Modbus Registers and it detects a HART packet on the network, RS-485
MicroLink-HM will temporarily switch to HART mode and stop polling devices. HART protocol packets always begin
with the hex FF preamble character. Modbus packets begin with the slave address. If no HART commands are received
over the serial port, RS-485 MicroLink-HM will return to polling and filling modbus registers aer 30 seconds. Also, if a
modbus command is received MicroLink will exit HART mode and return to polling and filling modbus registers.
Connecting to the HART Loop
Connect the two screw terminals to the HART device
or HART loop. Microlink provides electrical isolaon
between the HART loop and the serial port so it is safe
to ignore grounding and polarity issues when making
the HART connecons. The HART protocol requires a
loop resistance of 230 to 600 ohms, typically 250 ohms.
Refer to your equipment installaon instrucons for
details on connecng a HART master or configuraon
device to the loop.
HART Status LED Operation
The LED on the front panel of the RS-485 MicroLink-HM
is used to monitor HART communicaons acvity. The
LED will be green while transming or sending a packet
to your HART protocol devices, and will be red when
HART protocol replies are received.
LOOP
POWER
SUPPLY HART
DEVICE
250Ω
LOOP
POWER
SUPPLY HART
DEVICE
250Ω
Figure 1. Connecng HART modem to device loop.
Connecting across the loop resistor.
Connecting across the HART device.

Mounting
The DIN rail mounng clip is compable with widely used 35mm EN 50022 rails. It can be snap mounted and removed
from the mounng rail without tools for quick installaon and servicing.
Power Supply
The RS-485 MicroLink-HM is powered through an external power supply. You should use a DC power supply in the 5 to
30Vdc range connected to the posive side on Pin 1, and the negave side to Pin 2. Maximum supply current ranges
from 2mA at 30 volts to 10.5mA at 5 volts.
Power
Supply
RS-485
Transceiver HART
Modem
Microcontroller
Modbus Register
Tables
TX
RX
CD
RTS
1 - DC (+)
2 - DC (-)
3 - GND
4 - RS-485 B
5 - RS-485 A
5-Pin
Terminal Block
HART Loop
Terminals
HART Status LED
RS-485 MicroLink-HM Block Diagram
Connecting to a PC for Configuration
The configuraon sengs, baud rate, parity, slave address, polling devices, etc; are set using the Microflex HM
Configuraon soware. Before you add the MicroLink HM to your RS-485 network bus, connect it to a Windows PC or
laptop and make the necessary sengs.
Connect the A and B terminals to an RS-485 port. If your PC does not have an RS-485 port you will need to use an RS-
485 converter. Microflex offers the 101-0020 USB to RS-485 converter and the 101-0009 RS-232 to RS-485 converter.
Power must be supplied by an external 5 to 30 volts DC power supply. Refer to the Power Supply secon in this manual
for details.
RS-485 Network Bus
After configuring the MicroLink-HM it can be connected to an RS-485 network bus. An RS-485 bus consists of mulple
RS-485 devices connected in parallel to a bus cable. To eliminate line reflecons, each cable end is terminated with a
terminaon resistor whose value matches the characterisc impedance of the cable. This method, known as parallel
terminaon, allows for higher data rates over a longer cable length.
Connect terminal Ato the RS-485 bus A or (-) wire and terminal Bto the RS-485 bus B or (+) wire.
Connect terminal Gto the RS-485 bus shield or ground wire.
MicroLink-HM does not provide isolation between the RS-485 port and power supply ground.
The G terminal is internally connected to the power supply (-) terminal.

Setup COM Port
The RS-485 MicroLink-HM soware must be set to use the same
COM port that the modem is connected to. From the top menu
select Setup>Com Port. Choose the COM port number from the list of
available ports. Aer choosing, click Connect to aempt to connect
using the sengs selected. The connecon process will first try the
last good baud rate and parity sengs. If it fails to connect the
process will work through
other sengs to try to
find the correct RS-485
MicroLink-HM sengs for
communicaons. If it sll
does not connect - verify
that you have chosen the
correct COM number,
connecons are correct,
and power is on before
trying again.
RS-485 MicroLink-HM HART - Modbus Accumulator
In addition to being an RS-485 HART Protocol Modem, the MicroLink HM can be set to collect and store process
variable information from up to 16 HART devices. HART devices are continuously polled and variable information is
accumulated into a table of Modbus registers. Using the RS-485 MicroLink-HM serial port, the registers can be read
using Modbus RTU command 3. Variable data can be read as 16 bit integers or 32 bit floating point. Up to 4 variables for
each polled HART device.
In the accumulate mode, RS-485 MicroLink-HM will function as a HART master (primary or secondary) polling devices
and storing variable values into registers. No additional HART software is needed. The HART loop may contain a single
device or up to 16 devices. When more than one device is in the loop each HART device must have a unique HART
polling address. The address for each device is set before wiring the device into the multi-drop loop. The device polling
address for each device is stored in the RS-485 MicroLink-HM using the RS-485 MicroLink-HM configuration software.
Modbus slave address, baud rate, parity, and other settings are set using the RS-485 MicroLink-HM configuration
software. Configuration is done using the same connection that Modbus will use, so no additional setup cable is re-
quired. After the configuration is completed, the port is connected to the Modbus controller. At power on the RS-485
MicroLink-HM will begin polling and accumulating values. Modbus RTU command 3 is used to read the accumulated
values.
MicroLink HM Installation - Windows
The RS-485 MicroLink-HM configuraon soware is included on a CD with the unit. Simply insert the CD and follow the
on-screen prompts to install the soware. If AutoRun is not configured to run the CD file when the CD is inserted you
will need to navigate to the Msetup.exe file on the CD and double-click the file name to run it.
Aer Installaon the HM Configurator icon will be added to your system.
Don’t have a CD drive?
Download the HART Protocol CD image from www.microflx.com/pages/support
Home Screen
The home screen displays a summary of the RS-485 MicroLink-HM
status, HART modem sengs, and Modbus sengs. Use the top drop-
down menus to configure the RS-485 MicroLink-HM modem.
Figure 3. COM Port List. Figure 4. RS-485 MicroLink-HM Setup home screen.

HART Protocol Settings
With Fill Modbus Registers unchecked, RS-485 MicroLink-HM will funcon as a standard HART protocol modem and
not poll HART devices to fill Modbus registers. In this mode HART packets are received and then retransmied at the
HART 1200 baud, odd parity. Received reply packets are retransmied at the selected baud rate. RTS ming and carrier
detect are handled internally by the RS-485 MicroLink-HM allowing
RS-485 communicaons at higher than 1200 baud. HART loop data
is handled at the standard HART protocol 1200 baud, odd parity
but because RS-485 MicroLink-HM buffers the data, it can be set for
higher rates as well as odd, even, or no parity. Port sengs can be
set in the Modbus Sengs secon.
Since RS-485 MicroLink-HM manages network ming it needs to
be configured for either a primary or secondary master. Portable
configuraon modems are typically set to be secondary masters.
Polling HART Devices - Fill Modbus Registers
To enable Modbus register accumulaon, check the Fill Modbus Registers opon. The Hart Protocol Sengs window will
expand to show the Polled Devices sengs.
Retries
If a HART devices is polled but does not respond, or errors are detected, RS-485 MicroLink-HM can retry up to 3 mes
before indicang a bad device. If a device is not responding the Modbus values are filled with Hart Device Failed
register values - setup is done in the Modbus configuraon secon.
Polled Devices
In the example screen shot (Figure 5), RS-485 MicroLink-HM is set to poll one HART device using polling address 0 and
will retry 1 me before reporng a communicaons error. The Device Variables (Modbus Register Values) box on the right
displays the register values for the acve polled device. Click Add Device to add a polled HART device. Be sure to set
the Polling Address
for each device.
Each device must
have a unique HART
polling address.
Polling addresses
must be setup for
each HART device
before it can be
connected to a
mul-drop HART
loop and can be set
from 1 to 63.
Address 0 can only
be used when one
device is in the HART
loop.
Polling addresses
16-63 should only be
used with HART re-
visions 6 and higher.
For HART 3-5 use
addresses 1-15 for
multi-drop systems.
Figure 5. HART protocol sengs dialog when filling modbus registers is enabled.

Modbus - RTU Setup
Modbus-RTU Sengs can be accessed and changed by clicking Setup>Modbus from the top drop-down menu.
Modbus Address
Each device on a Modbus network must have a unique address. Set
this to match the address that your Modbus master will use to com-
municate with the RS-485 MicroLink-HM. The Modbus address
can be set to any value from 1 to 247. The RS-485 MicroLink-HM
configuration software will discover this address as part of the
connection process.
Baud Rate & Parity
The RS-485 MicroLink-HM baud rate and parity must be set to the
same settings as your Modbus master. If you are using the RS-485
MicroLink-HM as a HART protocol modem these should be set to
1200 baud, odd parity. Click Use HART Protocol Settings to set the
correct values for a HART modem.
Holding Registers Map
Accumulated data is stored in Modbus registers that are grouped
or mapped by HART device or by variable type. Choose the register
map that best fits your applicaon. Register maps can be viewed
using the RS-485 MicroLink-HM configuraon soware. From the
top drop-down menu select View -> Modbus Registers Maps (Figure
7.)
Decimal Places
When device data is stored into a 16 bit signed Modbus register the value can range from -32768 to 32767. To allow
the 16 bit integer to represent a smaller number and include fraconal informaon, the number of decimal places is
stored in a separate Modbus register and applied later. The number of decimal places can be set from 0 to 5. Decimal
places can be set for each variable. The Device Variables box shows the effect of the decimal place seng. Decimal place
sengs are not used for the Modus floang point register values.
Figure 6. Modbus sengs dialog.
Figure 7. Menu for viewing modbus register maps.
Floating Point Byte Order
Modbus 32 bit floang point numbers are stored in two
consecuve 16 bit registers using the IEEE-754 standard
big endian byte order (AB-CD). The most significant byte
(A) is sent first. For compability with some modbus
systems you may need to use the word swapped format
(CD-AB).
HART Device Failed Register Value
If a polled HART device fails to respond, or has
communicaons errors, it will retry for the number of
mes set in the HART Protocol Sengs dialog. If aer
retries the device does not respond you can choose to
hold the last value, set to a preset number, or set to
the IEEE-754 NaN floang point value. This can help the
modbus master determine when a HART device is no
longer responding.

Setup Registers
The RS-485 MicroLink-HM configuraon can be changed using the setup and configuraon soware or by wring to
modbus registers using modbus-RTU commands 6 or 16. Command 6 writes to a single register and command 16
writes to a range of modbus registers. The configuraon register values are saved in nonvolale memory and are not
lost when RS-485 MicroLink-HM power is removed.
HART Settings
Bits 9, 8 - HART failed mode. 0 = Hold last value after HART retries
1 = Preset to register 772 value after HART retries
2 = Preset to IEEE-754 NaN (0 for integers)
Bits 7, 6 - HART poll retries. Sets number of HART device poll retries from 1 to 3.
After poll retries the HART failed mode value is stored in the variable register.
Bit 5 0 = Fill Modbus registers, 1= HART modem mode
Bits 3 - 0 Number of polled devices-1 Range is 0 to 15. 0 = 1 polled device. 15 = 16 polled devices.
ϭϱϭϰϭϯϭϮϭϭϭϬϵϴϳϲϱϰϯϮϭϬ
,Zd&ĂŝůĞĚDŽĚĞ;ŝƚϭͿ
,Zd&ĂŝůĞĚDŽĚĞ;ŝƚϬͿ
,ZdZĞƚƌŝĞƐ;ŝƚϭͿ
,ZdZĞƚƌŝĞƐ;ŝƚϬͿ
Ϭс&ŝůůZĞŐŝƐƚĞƌƐϭс,ZdDŽĚĞŵ
ϭсWƌŝŵĂƌLJϬс^ĞĐŽŶĚĂƌLJDĂƐƚĞƌ
EƵŵďĞƌŽĨƉŽůůĞĚĚĞǀŝĐĞƐͲϭ
ϬсϭWŽůůĞĚĞǀŝĐĞ;ϬƚŽϭϱͿ
ϳϳϯͲ,Zd^ĞƚƚŝŶŐƐ
DŽĚďƵƐ
ZĞŐŝƐƚĞƌ ĞƐĐƌŝƉƚŝŽŶ;ŚŝŐŚďLJƚĞůŽǁďLJƚĞͿ
ϳϳϮ ,Zd&ĂŝůĞĚŽĚĞWƌĞƐĞƚsĂůƵĞ
ϳϳϯ ,ZdDŽĚĞ^ĞƚƚŝŶŐƐ
ϳϳϰ DŽĚďƵƐ^ĞƚƚŝŶŐƐ
ϳϳϱ DŽĚďƵƐWŽƌƚ^ĞƚƚŝŶŐƐ
ϳϳϲ ,ĂƌĚǁĂƌĞZĞǀ^ŽĨƚǁĂƌĞZĞǀ
ϳϳϳ WŽůůĞĚĚĞǀŝĐĞƐƚĂƚƵƐ

Serial Port Settings
ϭϱϭϰϭϯϭϮϭϭϭϬϵϴϳϲϱϰϯϮϭϬ
ϭсKĚĚƉĂƌŝƚLJ
ϭсǀĞŶƉĂƌŝƚLJ
ĂƵĚ;ďŝƚϯͿ
ĂƵĚ;ďŝƚϮͿ
ĂƵĚ;ďŝƚϭͿ
ĂƵĚ;ďŝƚϬͿ
ϳϳϱͲDŽĚďƵƐWŽƌƚ^ĞƚƚŝŶŐƐ
DŽĚďƵƐ^ůĂǀĞĚĚƌĞƐƐ;ϭͲϮϰϳͿ
Bits 13,12
00 = No parity
01 = Even
10 = Odd
Mode Settings
Bit 9 - Floating point value byte order 0 = Standard byte order (AB - CD)
1 = Swapped words (CD - AB)
Bit 8 - Modbus device map 0 = Map register data by HART device
1 = Map register data by variable type
ϭϱϭϰϭϯϭϮϭϭϭϬϵϴϳϲϱϰϯϮϭϬ
ϬсĨůŽĂƚďLJƚĞŽƌĚĞƌϭс
ϬсďLJĞǀŝĐĞDĂƉϭсďLJsĂƌŝĂďůĞDĂƉ
ϳϳϰͲDŽĚĞ^ĞƚƚŝŶŐƐ
Bits 11-8
1 = 1200 Baud
2 = 2400
3 = 4800
4 = 9600
5 = 14400
6 = 19200
7 = 38400
8 = 57600
9 = 115200

,Zd DŽĚďƵƐ
ĞǀŝĐĞ ZĞŐŝƐƚĞƌ ĞƐĐƌŝƉƚŝŽŶ;ŚŝŐŚďLJƚĞůŽǁďLJƚĞͿ
ϭ ϳϬϬ WƌĞĂŵďůĞƐDĂŶŽĚĞŽƌdLJƉĞ
ϳϬϭ ĞǀŝĐĞdLJƉĞ/ϭ
ϳϬϮ /Ϯ/ϯ
Ϯ ϳϬϯ WƌĞĂŵďůĞƐDĂŶŽĚĞŽƌdLJƉĞ
ϳϬϰ ĞǀŝĐĞdLJƉĞ/ϭ
ϳϬϱ /Ϯ/ϯ
ϯ ϳϬϲ WƌĞĂŵďůĞƐDĂŶŽĚĞŽƌdLJƉĞ
ϳϬϳ ĞǀŝĐĞdLJƉĞ/ϭ
ϳϬϴ /Ϯ/ϯ
ϰ ϳϬϵ WƌĞĂŵďůĞƐDĂŶŽĚĞŽƌdLJƉĞ
ϳϭϬ ĞǀŝĐĞdLJƉĞ/ϭ
ϳϭϭ /Ϯ/ϯ
ϱ ϳϭϮ WƌĞĂŵďůĞƐDĂŶŽĚĞŽƌdLJƉĞ
ϳϭϯ ĞǀŝĐĞdLJƉĞ/ϭ
ϳϭϰ /Ϯ/ϯ
ϲ ϳϭϱ WƌĞĂŵďůĞƐDĂŶŽĚĞŽƌdLJƉĞ
ϳϭϲ ĞǀŝĐĞdLJƉĞ/ϭ
ϳϭϳ /Ϯ/ϯ
ϳ ϳϭϴ WƌĞĂŵďůĞƐDĂŶŽĚĞŽƌdLJƉĞ
ϳϭϵ ĞǀŝĐĞdLJƉĞ/ϭ
ϳϮϬ /Ϯ/ϯ
ϴ ϳϮϭ WƌĞĂŵďůĞƐDĂŶŽĚĞŽƌdLJƉĞ
ϳϮϮ ĞǀŝĐĞdLJƉĞ/ϭ
ϳϮϯ /Ϯ/ϯ
ϵ ϳϮϰ WƌĞĂŵďůĞƐDĂŶŽĚĞŽƌdLJƉĞ
ϳϮϱ ĞǀŝĐĞdLJƉĞ/ϭ
ϳϮϲ /Ϯ/ϯ
ϭϬ ϳϮϳ WƌĞĂŵďůĞƐDĂŶŽĚĞŽƌdLJƉĞ
ϳϮϴ ĞǀŝĐĞdLJƉĞ/ϭ
ϳϮϵ /Ϯ/ϯ
ϭϭ ϳϯϬ WƌĞĂŵďůĞƐDĂŶŽĚĞŽƌdLJƉĞ
ϳϯϭ ĞǀŝĐĞdLJƉĞ/ϭ
ϳϯϮ /Ϯ/ϯ
ϭϮ ϳϯϯ WƌĞĂŵďůĞƐDĂŶŽĚĞŽƌdLJƉĞ
ϳϯϰ ĞǀŝĐĞdLJƉĞ/ϭ
ϳϯϱ /Ϯ/ϯ
ϭϯ ϳϯϲ WƌĞĂŵďůĞƐDĂŶŽĚĞŽƌdLJƉĞ
ϳϯϳ ĞǀŝĐĞdLJƉĞ/ϭ
ϳϯϴ /Ϯ/ϯ
ϭϰ ϳϯϵ WƌĞĂŵďůĞƐDĂŶŽĚĞŽƌdLJƉĞ
ϳϰϬ ĞǀŝĐĞdLJƉĞ/ϭ
ϳϰϭ /Ϯ/ϯ
ϭϱ ϳϰϮ WƌĞĂŵďůĞƐDĂŶŽĚĞŽƌdLJƉĞ
ϳϰϯ ĞǀŝĐĞdLJƉĞ/ϭ
ϳϰϰ /Ϯ/ϯ
ϭϲ ϳϰϱ WƌĞĂŵďůĞƐDĂŶŽĚĞŽƌdLJƉĞ
ϳϰϲ ĞǀŝĐĞdLJƉĞ/ϭ
ϳϰϳ /Ϯ/ϯ
Polled HART Devices Long Address Table
Device ID informaon is read from each polled device using the devices polling address and HART command 0. The
reply to command 0 for each polled device is used to populate the long address table. When RS-485 MicroLink-HM
needs to poll for the device variables, using HART command 3, this table holds the informaon needed to build the
5-byte long address. Table values can be read using modbus-RTU command 3. Only the polled device you have
configured will contain valid informaon. The table is updated aer each valid device poll.

DŽĚďƵƐ ,ZdĞǀŝĐĞWŽůůŝŶŐĚĚƌĞƐƐ
ZĞŐŝƐƚĞƌ ;ŚŝŐŚďLJƚĞůŽǁďLJƚĞͿ
ϳϰϴ ĞǀŝĐĞϭĞǀŝĐĞϮ
ϳϰϵ ĞǀŝĐĞϯĞǀŝĐĞϰ
ϳϱϬ ĞǀŝĐĞϱĞǀŝĐĞϲ
ϳϱϭ ĞǀŝĐĞϳĞǀŝĐĞϴ
ϳϱϮ ĞǀŝĐĞϵĞǀŝĐĞϭϬ
ϳϱϯ ĞǀŝĐĞϭϭĞǀŝĐĞϭϮ
ϳϱϰ ĞǀŝĐĞϭϯĞǀŝĐĞϭϰ
ϳϱϱ ĞǀŝĐĞϭϱĞǀŝĐĞϭϲ
HART Device Polling Address Table
The polling address for each polled device is stored in this table. Two polling addresses in each 16 bit register. If
address 0 is used then only one device can be polled and Device 1 should be set to 0. Address 0 is not valid in mul-
drop systems. For HART devices with HART revision 3 through 5 you should use polling addresses 1 - 15. Addresses
16-63 require HART revision 6 or higher.
,Zd DŽĚďƵƐ EƵŵďĞƌŽĨĞĐŝŵĂůWůĂĐĞƐ
ĞǀŝĐĞ ZĞŐŝƐƚĞƌ ĞƐĐƌŝƉƚŝŽŶ;ŚŝŐŚďLJƚĞůŽǁďLJƚĞͿ
ϭ ϳϱϲ WsͲ^dsͲ&s
Ϯ ϳϱϳ WsͲ^dsͲ&s
ϯ ϳϱϴ WsͲ^dsͲ&s
ϰ ϳϱϵ WsͲ^dsͲ&s
ϱ ϳϲϬ WsͲ^dsͲ&s
ϲ ϳϲϭ WsͲ^dsͲ&s
ϳ ϳϲϮ WsͲ^dsͲ&s
ϴ ϳϲϯ WsͲ^dsͲ&s
ϵ ϳϲϰ WsͲ^dsͲ&s
ϭϬ ϳϲϱ WsͲ^dsͲ&s
ϭϭ ϳϲϲ WsͲ^dsͲ&s
ϭϮ ϳϲϳ WsͲ^dsͲ&s
ϭϯ ϳϲϴ WsͲ^dsͲ&s
ϭϰ ϳϲϵ WsͲ^dsͲ&s
ϭϱ ϳϳϬ WsͲ^dsͲ&s
ϭϲ ϳϳϭ WsͲ^dsͲ&s
Number of Decimal Places Table
When storing the HART variable data in 16-bit modbus registers the maximum range is -32768 to 32767. To increase the possible resoluon, the
variable value read from the HART device is decimal posion adjusted before being saved in the 16-bit register. When the register is read, the value
must be corrected by the number of decimal placed to produce the correct value. The number of decimal places for each variable occupies 4-bits in
the register with one register for each polled device.
Decimals Variable Range
0 -32768 to 32767
1 -3276.8 to 3276.7
2 -327.68 to 327.67
3 -32.768 to 32.767
4 -3.2768 to 3.2767
5 -0.32768 to 0.32767

ZĞŐŝƐƚĞƌ ĞƐĐƌŝƉƚŝŽŶ
ϳ >ŽŽƉƵƌƌĞŶƚ/ŶƚĞŐĞ
ƌ
ϮϱϰϮϱ
ϱ
>ŽŽƉƵƌƌĞŶƚ&ůŽĂ
ƚ
ĞǀŝĐĞϰ
ZĞŐŝƐƚĞƌ ĞƐĐƌŝƉƚŝŽŶ ZĞŐŝƐƚĞƌ ĞƐĐƌŝƉƚŝŽŶ
Ϭ Ws/ŶƚĞŐĞƌ Ϯϰ Ws/ŶƚĞŐĞƌ
ϭ ^s/ŶƚĞŐĞƌ Ϯϱ ^s/ŶƚĞŐĞƌ
Ϯ ds/ŶƚĞŐĞƌ Ϯϲ ds/ŶƚĞŐĞƌ
ϯ &s/ŶƚĞŐĞƌ Ϯϳ &s/ŶƚĞŐĞƌ
ϰ ,Zd^ƚĂƚƵƐ Ϯϴ ,Zd^ƚĂƚƵƐ
ϱ D^сWshKD>^с^shK
D
Ϯϵ D^сWshKD>^с^shK
D
ϲ D^сdshKD>^с&shK
D
ϯϬ D^сdshKD>^с&shK
D
ϮϱϲϮϱ
ϳ
Ws&ůŽĂƚ ϮϴϬϮϴ
ϭ
Ws&ůŽĂƚ
ϮϱϴϮϱ
ϵ
^s&ůŽĂƚ ϮϴϮϮϴϯ ^s&ůŽĂƚ
ϮϲϬϮϲ
ϭ
ds&ůŽĂƚ ϮϴϰϮϴ
ϱ
ds&ůŽĂƚ
ϮϲϮϮϲϯ &s&ůŽĂƚ ϮϴϲϮϴ
ϳ
&s&ůŽĂƚ
ĞǀŝĐĞϮ ĞǀŝĐĞϱ
ϴ Ws/ŶƚĞŐĞƌ ϯϮ Ws/ŶƚĞŐĞƌ
ϵ ^s/ŶƚĞŐĞƌ ϯϯ ^s/ŶƚĞŐĞƌ
ϭϬ ds/ŶƚĞŐĞƌ ϯϰ ds/ŶƚĞŐĞƌ
ϭϭ &s/ŶƚĞŐĞƌ ϯϱ &s/ŶƚĞŐĞƌ
ϭϮ ,Zd^ƚĂƚƵƐ ϯϲ ,Zd^ƚĂƚƵƐ
ϭϯ D^сWshKD>^с^shK
D
ϯϳ D^сWshKD>^с^shK
D
ϭϰ D^сdshKD>^с&shK
D
ϯϴ D^сdshKD>^с&shK
D
ϮϲϰϮϲ
ϱ
Ws&ůŽĂƚ ϮϴϴϮϴ
ϵ
Ws&ůŽĂƚ
ϮϲϲϮϲ
ϳ
^s&ůŽĂƚ ϮϵϬϮϵ
ϭ
^s&ůŽĂƚ
ϮϲϴϮϲ
ϵ
ds&ůŽĂƚ ϮϵϮϮϵϯ ds&ůŽĂƚ
ϮϳϬϮϳ
ϭ
&s&ůŽĂƚ ϮϵϰϮϵ
ϱ
&s&ůŽĂƚ
ĞǀŝĐĞϯ ĞǀŝĐĞϲ
ϭϲ Ws/ŶƚĞŐĞƌ ϰϬ Ws/ŶƚĞŐĞƌ
ϭϳ ^s/ŶƚĞŐĞƌ ϰϭ ^s/ŶƚĞŐĞƌ
ϭϴ ds/ŶƚĞŐĞƌ ϰϮ ds/ŶƚĞŐĞƌ
ϭϵ &s/ŶƚĞŐĞƌ ϰϯ &s/ŶƚĞŐĞƌ
ϮϬ ,Zd^ƚĂƚƵƐ ϰϰ ,Zd^ƚĂƚƵƐ
Ϯϭ D^сWshKD>^с^shK
D
ϰϱ D^сWshKD>^с^shK
D
ϮϮ D^сdshKD>^с&shK
D
ϰϲ D^сdshKD>^с&shK
D
ϮϳϮϮϳϯ Ws&ůŽĂƚ ϮϵϲϮϵ
ϳ
Ws&ůŽĂƚ
ϮϳϰϮϳ
ϱ
^s&ůŽĂƚ ϮϵϴϮϵ
ϵ
^s&ůŽĂƚ
ϮϳϲϮϳ
ϳ
ds&ůŽĂƚ ϯϬϬϯϬ
ϭ
ds&ůŽĂƚ
ϮϳϴϮϳ
ϵ
&s&ůŽĂƚ ϯϬϮϯϬϯ &s&ůŽĂƚ
ĞǀŝĐĞϭ
Modbus Register Map - Grouped by HART Device (1 of 3)

Modbus Register Map - Grouped by HART Device (2 of 3)
ĞǀŝĐĞϳ ĞǀŝĐĞϭϬ
ZĞŐŝƐƚĞƌ ĞƐĐƌŝƉƚŝŽŶ ZĞŐŝƐƚĞƌ ĞƐĐƌŝƉƚŝŽŶ
ϰϴ Ws/ŶƚĞŐĞƌ ϳϮ Ws/ŶƚĞŐĞƌ
ϰϵ ^s/ŶƚĞŐĞƌ ϳϯ ^s/ŶƚĞŐĞƌ
ϱϬ ds/ŶƚĞŐĞƌ ϳϰ ds/ŶƚĞŐĞƌ
ϱϭ &s/ŶƚĞŐĞƌ ϳϱ &s/ŶƚĞŐĞƌ
ϱϮ ,Zd^ƚĂƚƵƐ ϳϲ ,Zd^ƚĂƚƵƐ
ϱϯ D^сWshKD>^с^shK
D
ϳϳ D^сWshKD>^с^shK
D
ϱϰ D^сdshKD>^с&shK
D
ϳϴ D^сdshKD>^с&shK
D
ϯϬϰϯϬ
ϱ
Ws&ůŽĂƚ ϯϮϴϯϮ
ϵ
Ws&ůŽĂƚ
ϯϬϲϯϬ
ϳ
^s&ůŽĂƚ ϯϯϬϯϯ
ϭ
^s&ůŽĂƚ
ϯϬϴϯϬ
ϵ
ds&ůŽĂƚ ϯϯϮϯϯϯ ds&ůŽĂƚ
ϯϭϬϯϭ
ϭ
&s&ůŽĂƚ ϯϯϰϯϯ
ϱ
&s&ůŽĂƚ
ĞǀŝĐĞϴ ĞǀŝĐĞƌϭϭ
ϱϲ Ws/ŶƚĞŐĞƌ ϴϬ Ws/ŶƚĞŐĞƌ
ϱϳ ^s/ŶƚĞŐĞƌ ϴϭ ^s/ŶƚĞŐĞƌ
ϱϴ ds/ŶƚĞŐĞƌ ϴϮ ds/ŶƚĞŐĞƌ
ϱϵ &s/ŶƚĞŐĞƌ ϴϯ &s/ŶƚĞŐĞƌ
ϲϬ ,Zd^ƚĂƚƵƐ ϴϰ ,Zd^ƚĂƚƵƐ
ϲϭ D^сWshKD>^с^shK
D
ϴϱ D^сWshKD>^с^shK
D
ϲϮ D^сdshKD>^с&shK
D
ϴϲ D^сdshKD>^с&shK
D
ϯϭϮϯϭϯ Ws&ůŽĂƚ ϯϯϲϯϯ
ϳ
Ws&ůŽĂƚ
ϯϭϰϯϭ
ϱ
^s&ůŽĂƚ ϯϯϴϯϯ
ϵ
^s&ůŽĂƚ
ϯϭϲϯϭ
ϳ
ds&ůŽĂƚ ϯϰϬϯϰ
ϭ
ds&ůŽĂƚ
ϯϭϴϯϭ
ϵ
&s&ůŽĂƚ ϯϰϮϯϰϯ &s&ůŽĂƚ
ĞǀŝĐĞϵ ĞǀŝĐĞϭϮ
ϲϰ Ws/ŶƚĞŐĞƌ ϴϴ Ws/ŶƚĞŐĞƌ
ϲϱ ^s/ŶƚĞŐĞƌ ϴϵ ^s/ŶƚĞŐĞƌ
ϲϲ ds/ŶƚĞŐĞƌ ϵϬ ds/ŶƚĞŐĞƌ
ϲϳ &s/ŶƚĞŐĞƌ ϵϭ &s/ŶƚĞŐĞƌ
ϲϴ ,Zd^ƚĂƚƵƐ ϵϮ ,Zd^ƚĂƚƵƐ
ϲϵ D^сWshKD>^с^shK
D
ϵϯ D^сWshKD>^с^shK
D
ϳϬ D^сdshKD>^с&shK
D
ϵϰ D^сdshKD>^с&shK
D
ϯϮϬϯϮ
ϭ
Ws&ůŽĂƚ ϯϰϰϯϰ
ϱ
Ws&ůŽĂƚ
ϯϮϮϯϮϯ ^s&ůŽĂƚ ϯϰϲϯϰ
ϳ
^s&ůŽĂƚ
ϯϮϰϯϮ
ϱ
ds&ůŽĂƚ ϯϰϴϯϰ
ϵ
ds&ůŽĂƚ
ϯϮϲϯϮ
ϳ
&s&ůŽĂƚ ϯϱϬϯϱ
ϭ
&s&ůŽĂƚ

Modbus Register Map - Grouped by HART Device (3 of 3)
ĞǀŝĐĞϭϯ ĞǀŝĐĞϭϱ
ZĞŐŝƐƚĞƌ ĞƐĐƌŝƉƚŝŽŶ ZĞŐŝƐƚĞƌ ĞƐĐƌŝƉƚŝŽŶ
ϵϲ Ws/ŶƚĞŐĞƌ ϭϭϮ Ws/ŶƚĞŐĞƌ
ϵϳ ^s/ŶƚĞŐĞƌ ϭϭϯ ^s/ŶƚĞŐĞƌ
ϵϴ ds/ŶƚĞŐĞƌ ϭϭϰ ds/ŶƚĞŐĞƌ
ϵϵ &s/ŶƚĞŐĞƌ ϭϭϱ &s/ŶƚĞŐĞƌ
ϭϬϬ ,Zd^ƚĂƚƵƐ ϭϭϲ ,Zd^ƚĂƚƵƐ
ϭϬϭ D^сWshKD>^с^shK
D
ϭϭϳ D^сWshKD>^с^shK
D
ϭϬϮ D^сdshKD>^с&shK
D
ϭϭϴ D^сdshKD>^с&shK
D
ϯϱϮϯϱϯ Ws&ůŽĂƚ ϯϲϴϯϲ
ϵ
Ws&ůŽĂƚ
ϯϱϰϯϱ
ϱ
^s&ůŽĂƚ ϯϳϬϯϳ
ϭ
^s&ůŽĂƚ
ϯϱϲϯϱ
ϳ
ds&ůŽĂƚ ϯϳϮϯϳϯ ds&ůŽĂƚ
ϯϱϴϯϱ
ϵ
&s&ůŽĂƚ ϯϳϰϯϳ
ϱ
&s&ůŽĂƚ
ĞǀŝĐĞϭϰ ĞǀŝĐĞϭϲ
ϭϬϰ Ws/ŶƚĞŐĞƌ ϭϮϬ Ws/ŶƚĞŐĞƌ
ϭϬϱ ^s/ŶƚĞŐĞƌ ϭϮϭ ^s/ŶƚĞŐĞƌ
ϭϬϲ ds/ŶƚĞŐĞƌ ϭϮϮ ds/ŶƚĞŐĞƌ
ϭϬϳ &s/ŶƚĞŐĞƌ ϭϮϯ &s/ŶƚĞŐĞƌ
ϭϬϴ ,Zd^ƚĂƚƵƐ ϭϮϰ ,Zd^ƚĂƚƵƐ
ϭϬϵ D^сWshKD>^с^shK
D
ϭϮϱ D^сWshKD>^с^shK
D
ϭϭϬ D^сdshKD>^с&shK
D
ϭϮϲ D^сdshKD>^с&shK
D
ϯϲϬϯϲ
ϭ
Ws&ůŽĂƚ ϯϳϲϯϳ
ϳ
Ws&ůŽĂƚ
ϯϲϮϯϲϯ ^s&ůŽĂƚ ϯϳϴϯϳ
ϵ
^s&ůŽĂƚ
ϯϲϰϯϲ
ϱ
ds&ůŽĂƚ ϯϴϬϯϴ
ϭ
ds&ůŽĂƚ
ϯϲϲϯϲ
ϳ
&s&ůŽĂƚ ϯϴϮϯϴϯ &s&ůŽĂƚ

Modbus Register Map - Grouped by Variable Type
ZĞǀϭ
ϭϭϮ
ϮϱϰϮϱϱ
,Zd Ws ^s ds &s ,Zd hKD hKD
ĞǀŝĐĞ /ŶƚĞŐĞƌ /ŶƚĞŐĞƌ /ŶƚĞŐĞƌ /ŶƚĞŐĞƌ ^ƚĂƚƵƐ Ws^s ds&s
ϭ Ϭ ϭϲ ϯϮ ϰϴ ϲϰ ϴϬ ϵϲ
Ϯ ϭ ϭϳ ϯϯ ϰϵ ϲϱ ϴϭ ϵϳ
ϯ Ϯ ϭϴ ϯϰ ϱϬ ϲϲ ϴϮ ϵϴ
ϰ ϯ ϭϵ ϯϱ ϱϭ ϲϳ ϴϯ ϵϵ
ϱ ϰ ϮϬ ϯϲ ϱϮ ϲϴ ϴϰ ϭϬϬ
ϲ ϱ Ϯϭ ϯϳ ϱϯ ϲϵ ϴϱ ϭϬϭ
ϳ ϲ ϮϮ ϯϴ ϱϰ ϳϬ ϴϲ ϭϬϮ
ϴ ϳ Ϯϯ ϯϵ ϱϱ ϳϭ ϴϳ ϭϬϯ
ϵ ϴ Ϯϰ ϰϬ ϱϲ ϳϮ ϴϴ ϭϬϰ
ϭϬ ϵ Ϯϱ ϰϭ ϱϳ ϳϯ ϴϵ ϭϬϱ
ϭϭ ϭϬ Ϯϲ ϰϮ ϱϴ ϳϰ ϵϬ ϭϬϲ
ϭϮ ϭϭ Ϯϳ ϰϯ ϱϵ ϳϱ ϵϭ ϭϬϳ
ϭϯ ϭϮ Ϯϴ ϰϰ ϲϬ ϳϲ ϵϮ ϭϬϴ
ϭϰ ϭϯ Ϯϵ ϰϱ ϲϭ ϳϳ ϵϯ ϭϬϵ
ϭϱ ϭϰ ϯϬ ϰϲ ϲϮ ϳϴ ϵϰ ϭϭϬ
ϭϲ ϭϱ ϯϭ ϰϳ ϲϯ ϳϵ ϵϱ ϭϭϭ
,Zd Ws ^s ds Ys
ĞǀŝĐĞ &ůŽĂƚ &ůŽĂƚ &ůŽĂƚ &ůŽĂƚ
ϭ ϮϱϲϮϱϳ ϮϴϴϮϴϵ ϯϮϬϯϮϭ ϯϱϮϯϱϯ
Ϯ ϮϱϴϮϱϵ ϮϵϬϮϵϭ ϯϮϮϯϮϯ ϯϱϰϯϱϱ
ϯ ϮϲϬϮϲϭ ϮϵϮϮϵϯ ϯϮϰϯϮϱ ϯϱϲϯϱϳ
ϰ ϮϲϮϮϲϯ ϮϵϰϮϵϱ ϯϮϲϯϮϳ ϯϱϴϯϱϵ
ϱ ϮϲϰϮϲϱ ϮϵϲϮϵϳ ϯϮϴϯϮϵ ϯϲϬϯϲϭ
ϲ ϮϲϲϮϲϳ ϮϵϴϮϵϵ ϯϯϬϯϯϭ ϯϲϮϯϲϯ
ϳ ϮϲϴϮϲϵ ϯϬϬϯϬϭ ϯϯϮϯϯϯ ϯϲϰϯϲϱ
ϴ ϮϳϬϮϳϭ ϯϬϮϯϬϯ ϯϯϰϯϯϱ ϯϲϲϯϲϳ
ϵ ϮϳϮϮϳϯ ϯϬϰϯϬϱ ϯϯϲϯϯϳ ϯϲϴϯϲϵ
ϭϬ ϮϳϰϮϳϱ ϯϬϲϯϬϳ ϯϯϴϯϯϵ ϯϳϬϯϳϭ
ϭϭ ϮϳϲϮϳϳ ϯϬϴϯϬϵ ϯϰϬϯϰϭ ϯϳϮϯϳϯ
ϭϮ ϮϳϴϮϳϵ ϯϭϬϯϭϭ ϯϰϮϯϰϯ ϯϳϰϯϳϱ
ϭϯ ϮϴϬϮϴϭ ϯϭϮϯϭϯ ϯϰϰϯϰϱ ϯϳϲϯϳϳ
ϭϰ ϮϴϮϮϴϯ ϯϭϰϯϭϱ ϯϰϲϯϰϳ ϯϳϴϯϳϵ
ϭϱ ϮϴϰϮϴϱ ϯϭϲϯϭϳ ϯϰϴϯϰϵ ϯϴϬϯϴϭ
ϭϲ ϮϴϲϮϴϳ ϯϭϴϯϭϵ ϯϱϬϯϱϭ ϯϴϮϯϴϯ
>ŽŽƉƵƌƌĞŶƚͲ/ŶƚĞŐĞƌ
>ŽŽƉƵƌƌĞŶƚͲ&ůŽĂƚ
ϯϮͲďŝƚ&ůŽĂƚZĞŐŝƐƚĞƌƐ
ϭϲͲďŝƚ^ŝŐŶĞĚZĞŐŝƐƚĞƌƐ ϭϲͲďŝƚhŶƐŝŐŶĞĚ

Enclosure
Polycarbonate plasc with Stainless Steel Cover
Weight................................................................................................ 5 ounces
Mounng............................................................................35mm DIN Rail Clip
Terminal Block
Connector..........................................5-Pin 3.81 mm Pluggable Terminal Block
+ Power Supply (+)....................................................................................Pin 1
- Power Supply (-) ....................................................................................Pin 2
G RS-485 Ground Internally connected to Supply (-) ................................Pin 3
B RS-485 (+)..............................................................................................Pin 4
A RS-485 (-)...............................................................................................Pin 5
RS-485
Baud Rates ......1200, 2400, 4800, 9600, 14400, 19200, 39400, 57600
Parity ......................................................................................None, Odd, Even
Driver Output Voltage ............................2V Min Unloaded, 1.5V Min RL= 54Ω
ΔInput Threshold Receive Voltage....................................................... +/- 0.2V
Receiver Input Hysteresis .................................................................35 mV Typ
Receiver Input Current .................................................................+/- 1mA Max
Surge Protecon............................................600W Silicone Avalanche Diodes
• Does not include RS-485 terminaon resistor
• Auto transmit control
• Power Up/Down glitch-free permits live inseron or removal
• Common mode range permits +/-7V ground difference
Specifications
PP
PP
PP
+$57/223
:,5(6&5(:7(50,1$/
PP
PP',15$,/&/,3
67$786/('
563257
'&32:(5
6&5(:7(50,1$/
Modbus RTU
Floang point byte order ...................................... AD-CD or CD-AB (swapped)
Number of polled HART devices.............................................................1 to 16
Variables per polled HART device........................................... (4) PV, SV, TV, FV
Supported Modbus Commands ............................................................3, 6, 16
HART
Terminaon ........................................ Pluggable Screw Terminals, 26-12 AWG
Connecon Method ......................... Transformer Isolated, Capacitor Coupled
DC Loop Voltage.............................................................................. 50Vdc Max
Demodulaon Jier............................................................12% of 1 bit Typical
Carrier Detect Threshold........................................................... 100mV Typical
Leakage to Process Loop ................................................................ ±10μA Max
Default Settings
RS-485 ...............................................................1200 Baud, Odd Parity, 1 Stop
Modbus Address .............................................................................................1
Fill Modbus Registers ..........................................................................Disabled
Status LED
Green........................................................................Transming HART packet
Red ............................................................................... Receiving HART packet
Environmental
Operang Temperature.................................... -30ºC to 60ºC (-22ºF to 140ºF)
Storage Temperature........................................ -40ºC to 85ºC (-40ºF to 185ºF)
Humidity.................................................................0 to 95% (non-condensing)

Conformity in accordance with Part 2, and Part 15, Subparts A and B of
the Federal Communications Rules and Regulations, and ICES-003 of the
Industry Canada standards.
This device complies with part 15 of the FCC rules. Operation is subject to
the following two conditions: (1) This device may not cause harmful interfer-
ence, and (2) this device must accept any interference received, including
interference that may cause undesired operation. Changes or modifications
not expressly approved by Microflex could void the user’s authority to oper-
ate this equipment.
Emissions EN55022: 1998
Electrostatic Discharge EN61000-4-2: 1995, A1: 1998, A2: 2001
Radiated Immunity EN 61000-4-3: 2002
Safety Compliance EN 60950-1: 2002
This device does not have protection from over-voltages which may exist
on RS-232 ports of computers and relies on the protection existing in a host
computer.
This device is not intended for connection to the phone line through the
appropriate converters and shall not be connected to telecommunication
lines because it has no protection against over-voltages which may exist in
these lines.
The user shall ensure the protection of the operator from access to areas
with hazardous voltages or hazardous energy in their equipment.
The user shall ensure that the connection port of the field device and the
modem is separated at least by basic insulation from any primary circuit
existing in the field device.
Safety Considerations

Limited Warranty
Microflex, LLC warrants this unit against defects in materials and workmanship for a
period of one year from the date of shipment. Microflex, LLC will, at its option, repair or
replace equipment that proves to be defective during the warranty period. This warranty
includes parts and labor.
A Return Materials Authorization (RMA) number must be obtained from the factory
and clearly marked on the outside of the package before equipment will be accepted for
warranty work.
Microflex, LLC believes that the information in this manual is accurate. In the event that
a typographical or technical error exist, Microflex, LLC reserves the right to make changes
without prior notice to holders of this edition. The reader should consult Microflex, LLC
if any errors are suspected. In no event should Microflex, LLC be liable for any damages
arising out of or related to this document or the information contained in it.
EXCEPTAS SPECIFIED HEREIN, MICROFLEX, LLC MAKES NO WARRANTIES OR
MERCHANTABILITY OR FITNESS FOR A PARTICULAR PURPOSE. CUSTOMER’S
RIGHT TO RECOVER DAMAGES CAUSED BY FAULT OR NEGLIGENCE ON THE
PART OF MICROFLEX SHALL BE LIMITED TO THE AMOUNT THERETOFORE
PAID BY THE CUSTOMER. MICROFLEX, LLC WILL NOT BE LIABLE FOR
DAMAGES RESULTING FROM LOSS OF DATA, PROFITS, USE OF PRODUCTS,
OR INCIDENTAL OR CONSEQUENTIAL DAMAGES, EVEN IF ADVISED OF THE
POSSIBILITIES THEREOF. This limitation of the liability of Microflex, LLC will apply
regardless of the form of action, whether in contract or tort, including negligence. Any
action against Microflex, LLC must be brought within one year after the cause of action
accrues. The warranty provided herein does not cover damages, defects, malfunctions, or
service failures caused by owners failure to follow Microflex, LLC’s installation, operation,
or maintenance instructions; owners modification of the product; owner’s abuse, misuse, or
negligent acts; and power failure or surges, fire, flood, accident, actions of third parties, or
other events outside reasonable control.
Microflex, LLC
35900 Royal Road
Pason, Texas 77423
USA
The HART protocol is supported by the FieldComm Group in Ausn Texas, www.fieldcommgroup.org.
HART is a registered trademark of the FieldComm Group.
Phone 281-855-9639
Fax 832-422-4391
www.microflx.com
Table of contents
Other Microflex Modem manuals
Popular Modem manuals by other brands
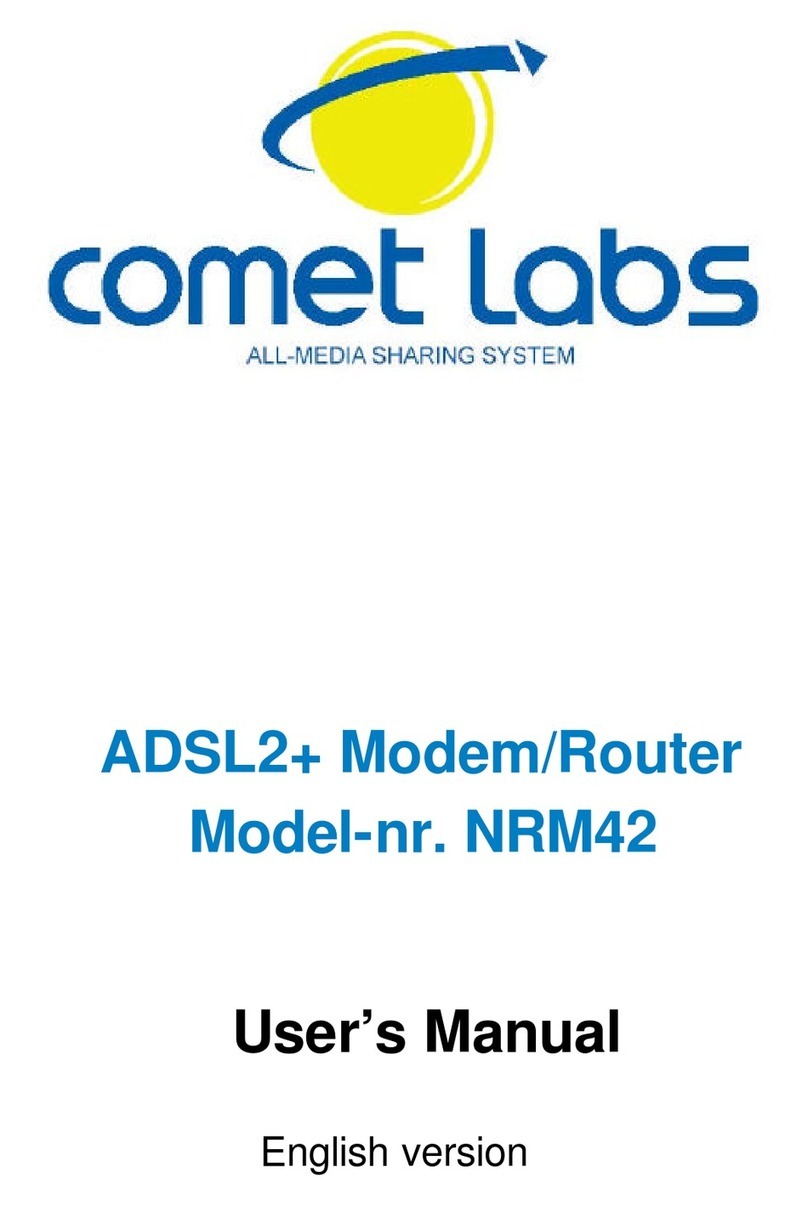
Comet Labs
Comet Labs NRM42 user manual
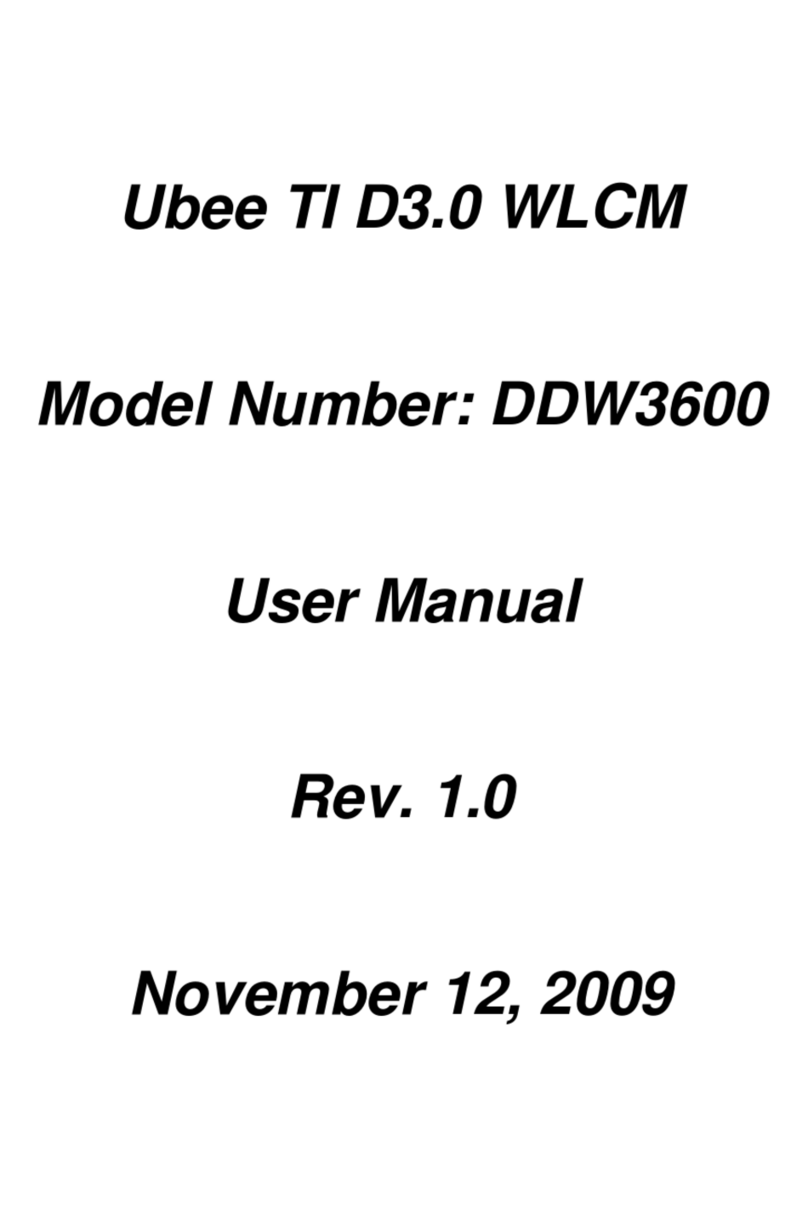
Ubee
Ubee DDW3600 user manual

Paradyne
Paradyne COMSPHERE 3820Plus installation instructions
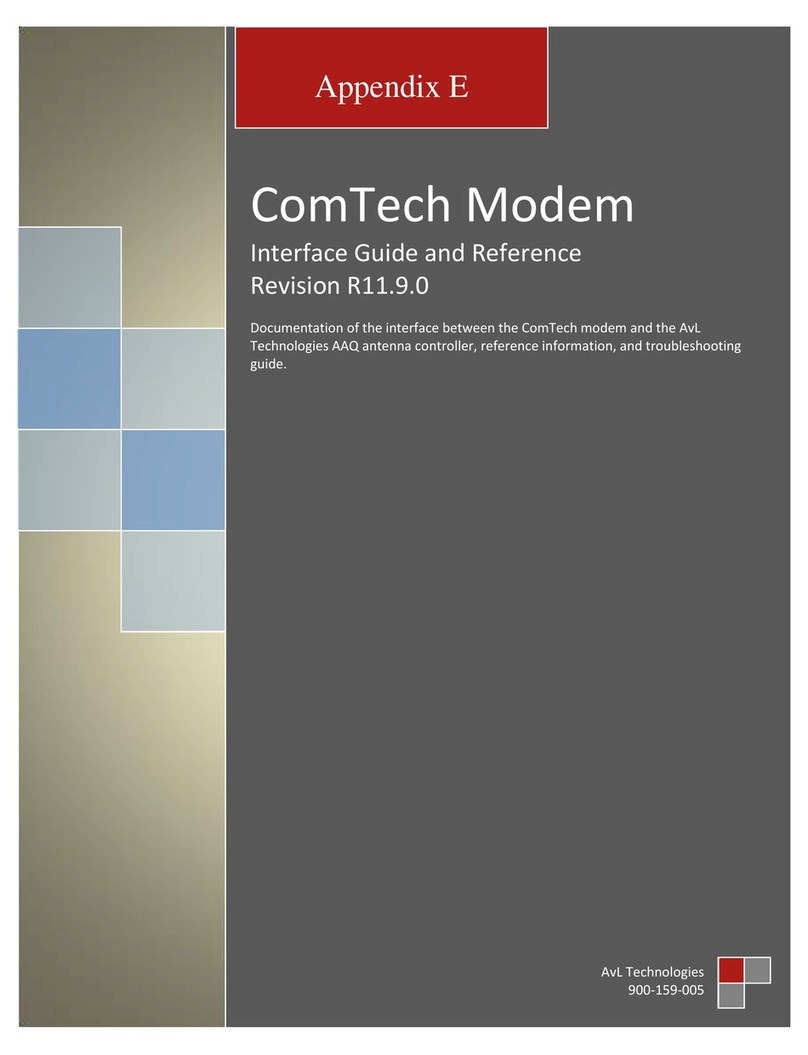
AvL Technologies
AvL Technologies ComTech Interface Guide and Reference
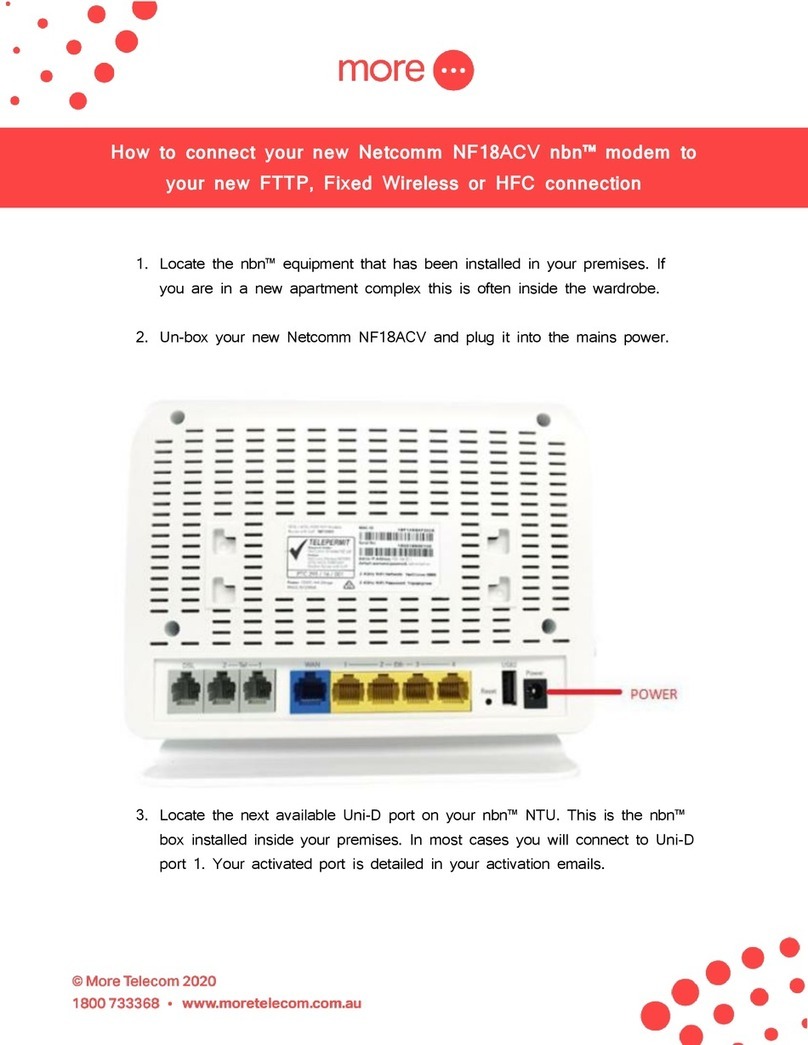
More
More Netcomm nbn NF18ACV How-to
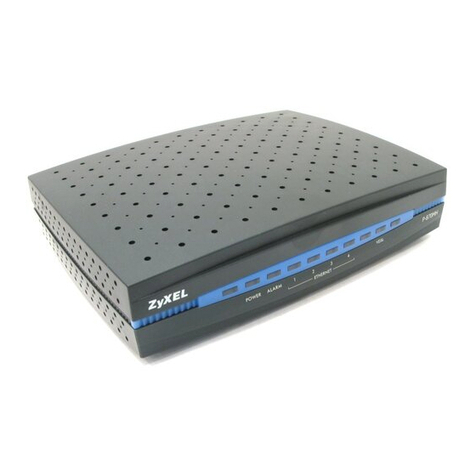
ZyXEL Communications
ZyXEL Communications P-870MH-C1 quick start guide