MicroLux Laserkinfe 2525 Manual

What’s included in the cartons:
1 – LaserKnife 2525 ngraving/Cutting Machine
1 – Metal honeycomb platen
1 – Air pump
1 – xhaust fan
1 – Corrugated plastic exhaust duct, 100 mm dia. with clamp
1 – Water pump
1 – USB Key
1 – Lens focus gauge
1 – Power cord
1 – Ground wire
3 – Spare Fuses
1 – USB cable
8 – Magnets
5 – Pieces of 6” x 9” chipboard
1 – Piece of scribed siding with 1/16 spacing, 10” long
2 – Piece of scribed siding with 3/32 spacing, 10” long
1 – Piece of 10” x 10” x 1/16” acrylic
1 – Owners manual
What’s included on the Micro-Mark web site:
1 – CorelLAS R software 1 – Set of sample part drawings
What you’ll need to provide:
1 – Computer running Windows 2000 or later
1 – CorelDRAW software version 11 or later
1 – 5 gallon plastic bucket containing 3 gallons of
distilled water
Your own drawing files, created in, or importable into,
CorelDRAW versions 11 or later
1 – 220vAC power: either at a wall outlet with two-prong
urope standard socket or adapter to same.
We alternately suggest a transformer to change
110vAC wall power to 220vAC power needed to run
the machine, like Micro-Mark #86127 (sold separately).
MM031615
TM
OWNERS MANUAL & INS RUC IONS FOR USE

CAUTION!
READ HE FOLLOWING SAFE Y PRECAU IONS
BEFORE SE ING UP AND USING HIS MACHINERY.
Warning: Normal use of t is product can expose t e user to materials (wood smoke) known to t e State of
California to cause cancer and birt defects or ot er reproductive arm, or ot er Proposition 65 listed c emicals.
To prevent bodily injury to yourself or others, please use common sense when using a machine, such as this
one, that employs high voltage electronics, laser beams, motors and other mechanisms. These instructions
cannot cover every situation you may encounter when using this machine, but the following information,
which you must read before using this machine, will help you understand its workings and help avoid
personal injury. If you need further explanations of specific concern, please call our technical service department
at 908-464-1094 for more information.
This machine employs an invisible beam of high energy light to cut through soft materials, such as wood and
plastic. It will easily cut and/or burn human flesh and will cause injury if you are not careful to avoid contact
with the laser beam. Do NOT reach into the cabinet unless the machine is switched off and the power control
knob is turned all the way off (turned all the way counterclockwise). To avoid injury, do not place any part of
your body in the beam’s line of action (at the output end of the laser, between mirrors, and/or under the lens).
To avoid fracturing the glass laser tube, cooling water MUST be circulating before power up. Make sure the
cooling water is flowing through the system by checking the return line (labeled Water Out) to the water bucket
for water flow.
The front-right chamber of the cabinet contains high voltage electrical connections. Do NOT reach into this
chamber unless the power cord is disconnected from the machine.
Avoid contact with any connections to the laser tube unless the power cord is disconnected from the machine.
Since this machine uses an electric-driven water pump which circulates water through the product, the use of
GFI circuitry to protect from electric shock is MANDA ORY.
2
(GFI PROT CT D)
GENERAL
EQUIPMEN LAYOU

The cabinet includes three chambers: one containing a laser tube and mirror, one containing electronic circuits/power
supply, and one main chamber for cutting out wood, card, plastic and acrylic sheet materials, and for engraving (burning)
images into surfaces.
The laser emits a powerful, concentrated beam of light that, when reflected by mirrors and focused through a lens, is
capable of cutting through a piece of wood, paper, cloth, acrylic sheet, and many other non-metallic materials. A
computer-controlled motorized carriage, suspended above the workpiece, moves the mirrors and the lens with pin-point
accuracy. This motion, combined with computer-controlled powering of the laser, enables the machine to easily cut out
intricate, tight-tolerance parts or engrave high definition images into the surface of the workpiece.
Note: A personal computer (not included), running Windows 2000 or later MS operating systems plus CorelDRAW
version 11 or later, is required to control the LaserKnife 2525. A USB port on the side of the cabinet connects to the
computer via the supplied cable.
he control panel includes the following:
• Master (ON-OFF) Switch, which, when lit, energizes the power supply, control circuits, and powers up the ancillary
equipment (see below).
• Current regulating knob, which controls the amount of current available to the laser tube and, subsequently, the cutting power.
• Current meter, which displays the laser current in milliamps, thereby giving a corresponding indication of cutting power.
• Test button, which energizes a burst of the laser beam and indicates the laser current setting on the meter.
• Cutting button, which, by pressing it, allows you to toggle the laser beam ON/OFF while the carriage continues to
function normally.
• Lighting switch, which toggles the lamp in the main chamber ON or OFF whenever the main power cord has power (no
matter whether the position of the Master switch is set to ON or OFF).
Ancillary equipment provided with the machine includes:
• A small air pump to blow debris away from the cutting/engraving location
• A red L D laser beam location pointer
• A small water pump to circulate cooling water through the laser tube
• An exhaust fan to draw any smoke from the cabinet and send it outside through the provided 100 mm diameter plastic duct
All equipment (except the personal computer) is designed to operate on 220vAC line voltage (a step-up transformer is
available separately from Micro-Mark to convert regular 110vAC line voltage from the wall outlet to the 220vAC needed
for the machine). The use of GFI circuitry to protect from electric shock is MANDA ORY. All ancillary equipment is
controlled by one flick of the ON-OFF Master Switch.
The purchaser will need to supply a 5-gallon plastic bucket containing about 3 gallons of distilled water at room
temperature for cooling the laser tube.
Note: Failure to provide circulating cooling water to t e laser tube will most-likely cause irreparable damage to t e
equipment and will definitely void t e warranty. Before powering t e laser, make sure t e water is flowing from t e
bucket, t roug t e laser tube, and back to t e bucket. See t e detailed instructions for more information about water
pump operation.
Running t e laser at continued ig current will eventually over eat t e cooling water and laser tube and reduce its
lifetime; water temperature must be monitored by t e user and t e laser s ut off if it gets too warm. T is mac ine is
intended for private ome use . . . for making parts used for obby craft-type projects. T is equipment as not been
designed to wit stand t e rigors of production/manufacturing operations, and suc use will void any warranty.
See t e owners’ manual and user instructions for explicit details on ow to operate t e equipment properly.
LaserKnife 2525…How it Works
3

Unpacking
The machine is heavy; please ask someone to help you lift the machine out of the carton and onto your workbench or other
sturdy table (with the work surface 30 to 36 inches off the floor) so you can remove the packing materials. It’s a good idea
to use a table equipped with casters or is otherwise easy to move…especially with the machine placed on it…as access to
the back side of the machine will be necessary. Ideally, your work table will have space between it and the wall.
Save the packing materials; they were designed for safe transport of the machine. If the machine ever needs service, it will
travel best in its original packing.
Install the Exhaust Fan and Duct
The exhaust fan slides into the “pocket” located on the back side of the cabinet. After removing the loose ends of any
tubing stored in that area for shipment, orient the 100 mm output fitting in a convenient direction for connection to the
exhaust duct. The top edge may be sealed with tape, or you may choose a more-permanent installation by installing a
couple of self-tapping screws (not included) in the top corners to draw the fan housing against the laser tube access lid (we
prefer this latter method, but be careful to avoid piercing the lid too deeply and damaging equipment located within). You
may remove the lock screw and open the laser tube access lid to see what’s inside and where it’s located before drilling
through the cabinet. Attach the exhaust duct to the fan outlet with the provided clamp and direct the exhaust outside the
building into the open air; this last part of the exhaust installation is to be devised by the user (Note: The 100 mm exhaust
tube is a bit smaller than a standard 4” diameter USA dryer duct; some adaptation may be required, or substitute a 4” dryer
duct from your hardware/home improvement retailer). Plug the exhaust fan power cord into the socket on the rear of the
cabinet labeled “Fan” or “ xhaust.” Note: this equipment operates on 220vAC; do not plug into 110vAC wall outlet.
Tip: if the equipment plugs enter the sockets a bit too loosely, you may use a plier to gently bend the prongs
slightly for a more-secure fit and good electrical connection.
Set Up
Before installing ancillary equipment, you will need to open the large lid (the one with the window) and carefully remove
the 100 mm diameter plastic exhaust duct from the main chamber; set it aside for later use. Remove any protective
covering from the lid’s plastic window. Look for and carefully remove any packing materials, such as foam, that secure the
inner workings of the carriage, mirrors and other mechanical devices. Gently push the carriage and lens housing around a
little bit to confirm freedom of movement; otherwise, damage may occur when the machine is powered up.
Note: Do not touch the surface of the mirrors.
There are two lever-actuated micro-switches located inside the main chamber at the carriage end stops. Make sure they
are in working order; that is, no packing materials or debris has fouled the actuator levers.
The machine has been tested at the factory and at the Micro-Mark warehouse. If you find any cuttings from this testing, or
other debris from the manufacturing process, you may remove them with a vacuum cleaner equipped with a small brush or
thin nozzle. This equipment should be handled with care. It contains sensitive motors, switches and controls essential for
precision operation. To obtain the optimum satisfaction with your LaserKnife 2525, please handle and use the machine
carefully and gently.
Access to the back side of the machine will be necessary in order to make water, air, exhaust and
electrical connections to ancillary equipment.
DO NOT CONNECT THE MAIN POWER CORD TO THE MACHINE UNTIL LATER (WE’LL LET YOU KNOW WHEN TO DO SO).
LaserKnife 2525 Hardware (the machinery) Set Up Instructions
Do not connect the line cord to the machine before
reading and performing ALL of the instructions below.
4

Install the Air Pump
Connect the output fitting (usually brass) of the air pump to the plastic tube marked “Air In” (usually orange) and place the
air pump on the floor or small table. The pump will vibrate and may “wander around” while it is running; make sure it does
not wander across the table and fall to the floor! Plug the air pump power cord into the socket on the rear of the cabinet
labeled “AIR PUMP.” Note: this equipment operates on 220vAC; do not plug into 110vAC wall outlet.
Tip: The pump makes noise that can be damped by placing it on a piece of foam rubber, which will also keep it from
wandering around. Do not enclose the pump in a sound-proof box; it needs ventilation to keep from overheating.
Install the Water Pump
Connect the outlet of the water pump to the tubing marked “Water in” and place the pump inside a 5 gallon bucket
containing about 3 gallons of distilled water that you can purchase at your local grocery store. Secure the power cord in
such a way that a minimum amount of wire (and especially any factory-spliced wire connection) is not submerged in
water. Place the return water tube (marked “Water Out”) inside the bucket so that the open end is below the surface of
the water; in that way, once air is purged from the system, no air can flow back into the cooling lines and cause the
system to lose its “prime.” Secure the tubing so that it does not move from its ideal position as just described. It’s also a
good idea to cover the bucket to reduce evaporation; cut a small slot in the cover to clear the tubes and power cord. Plug
the water pump power cord into the socket on the rear of the cabinet labeled “WAT R PUMP.” Note: this equipment
operates on 220vAC; do not plug into 110vAC wall outlet. When power is turned on (later), the pump should pick up the
water and circulate it through the system. You can verify that the water is circulating by momentarily lifting the end of the
return tubing out of the water and visually checking for flow. If the water does not circulate after several seconds, check
the connection of the tubing to the pump for leakage. IMPOR AN : You may also have to gently lift the pump out of
the water and set it back in to “prime” the pump for proper water flow, which is critical to the life of the laser tube.
Connect the Main Power
Attach the included ground wire between the machine cabinet and a solid electrical ground, such as a metal water pipe or
ground circuit in the electric supply socket box.
NOW: Make sure the master ON-OFF switch is set to OFF. Then plug the main power cord into the socket located on the
right side of the cabinet. Note that the other end of this cord is to be plugged into a 220vAC power source. The cord has
an unusual plug that will remind you of this requirement. If your shop is equipped only with 110vAC outlets, then we
suggest the use of a separate transformer to convert to 220vAC. See the Micro-Mark web site for such a device.*
Cycle the Lighting switch and verify that the internal lamp is turning on and off. (Yes...even with the master switch set to OFF).
Turn on the main power switch located on the control panel and confirm that the air pump, water pump and exhaust fan
are running. The carriage may index itself (move) to the left-rear corner of the main chamber…the 0,0 (zero-zero)
position. This is normal. If it doesn’t move to that location, do not worry; we’ll index it later.
If the water is not circulating back to the bucket, gently lift the water pump out of the water for a second or two, and it
should then start to flow.
Now, shut off the main power.
*T e power source MUST be GFI protected.
Connect to your Personal Computer
Use the provided cable to connect a USB port on your computer to the USB port located on the right side of the machine
in the rectangular hole near the power cord connection. Note: The USB cable should be arranged so that the end closer
to the ferrite choke (that cylindrical object surrounding the cable at one point) is plugged into the laser cutter. Be careful to
orient the USB plug properly; that is, do not force it into the socket located on the printed circuit board. If it does not enter
the socket easily, rotate it 180 degrees and try again.
This completes the hardware set up.
Please proceed to the LaserKnife 2525 Software Set-Up Instructions.
Hardware Set Up Instructions (continued)
5

CorelLASER Installation
Please follow the software download
sheet included elsewhere in this manual.
After the software is downloaded to your computer,
you’ll need to reset or confirm certain settings of
CorelLAS R so that the computer can communicate
with and control the LaserKnife 2525. Proceed as
follows:
Insert the USB “key” into a USB port on your computer.
Start CorelLAS R (give it time to load) and you
should ultimately see the CorelLAS R controls in the
upper right corner of the Corel window…just below
the blue bar. This means CorelDRAW is open and
functioning and the CorelLAS R plug-in is operating.
The LaserKnife 2525 is controlled by a plug-in program for CorelDRAW called CorelLAS R, which is included with the
purchase of the machine and downloaded from the Micro-Mark web site at http://www.micromark.com/downloads.dlp.
It has been designed to work with CorelDRAW versions 11 and later, including X3, X4, X5, X6, etc. (Version X3 is version
13, X4 is 14, and so on) running on Windows 2000 and later operating systems.
Please note: CorelLASER software is not compatible with Home & Student versions of CorelDRAW.
CorelDRAW must be loaded onto the computer before CorelLAS R can be downloaded. The user needs to supply the
CorelDRAW program. It is available for download from the Internet. To prevent unauthorized use of CorelLAS R, a USB “key”
is provided with the LaserKnife 2525. After the software is in place, be sure to plug the key into a USB port on your computer
or CorelLAS R will not be accessible. A warning message or window will pop up in case you forget. Don’t lose the “key!”
LaserKnife 2525 Software Set Up
Click on the green pencil (the bubble should say CorelDRAW setting) and a window will open that looks like the
following:
For the initial use of the LaserKnife 2525, we
suggest you use the pull-down menus to choose
settings that match those at left. Later, you can
change the settings based on the type of files
you are using, and whether or not you want the
machine to engrave/cut everything on the page
or only what you have selected.
You can later experiment with the effects of
changing the various settings… a rather fun
exercise!
Click OK to accept and save.
6

7
Software Set Up (continued)
Next, click on the gear icon (third to the right of the green pencil you clicked on before). You should see a window
that looks like the following:
Check the settings, and use the pull-down
menus to change them to what’s shown at
left.
Notice the field in the lower left corner
…“Device ID.”
IMP RTANT:You’ll need to
enter your specific machine
identification number in this
field.
This number can be found on a label
located above the opening in the machine
cabinet through which you plugged in the
USB cable. If you do not enter or replace
any existing number with the correct ID, the
machine will not respond to the computer
commands. For future reference, take a
moment now to write the machine ID
number on the following line:
WARNING! You must be certain that the PageSizeX and PageSizeY are set to a
maximum of 250.000 mm as shown above.
A higher setting will cause the machine to run the carriage into the end stops and may damage the machine. A lower setting
will do no harm, other than restrict the overall size of the image you will cut or engrave.
Be sure to click OK to accept and save your settings. If so instructed, “X-out” and then restart the CorelLAS R application to
activate the new device ID and initialize installation of the software.
OK, now it’s time to open a drawing file and cut out some parts. We’ve included a couple of simple sample files to get you
started.
In the upper left corner of the CorelDRAW window, click on File, then Open. Navigate to LaserKnife demonstration files,
double-click and select Laser Cut HO shanty Demo by double-clicking the file name. A set of wall outlines should appear.
(Notice that additional CorelDRAW functions also appear). Click on an object line, hold the mouse key down, and drag
the image to a location near the top of the page. Release the mouse button. If the object stays selected (black squares
appear around the outline), don’t touch it. If it is not selected, click on an image line to do so. Because of previous settings to
cut “only selected,” you need to select the image, which we’ve grouped together for you, for the machine to accept for cutting.
Tip: You can also “select all>objects” under Edit.
Turn ON the LaserKnife Master ON-OFF switch and verify that the water is flowing by lifting the return water line out of
the water in the bucket and visually checking for flow. If water is flowing, place the return tube back under the water. If no
water is flowing, correct the problem before continuing.
You may also turn on the chamber light using the lighting switch on the control panel.
Let’s ry Cutting Out Some Parts
ID:

Now…With the image selected, click on the icon to the left of the gear in the upper right corner of the main window
(callout says “cutting”). Click OK on any windows that pop up until you arrive at the following screen…the ngraving Manager.
Tip: The Refer-X and Refer-Y settings will vary from the screen shot above based on the location of the starting
point (the intersection of the cross-hairs…see below) for the laser head.
Tip: There are a few places were the Page Size can be entered. ne is on the CorelDRAW main screen, so that you
can see the outline of the material you will be using; the other is in the CorelLASER Machine Properties screen.
To prevent placing objects “out of bounds,” match the settings, and in no case should either dimension exceed
250 mm (9.84 inches).
Tip: The Common Parameter “Release” button allows the lens to be pushed by hand out of the way. Make sure
power to the laser is off before doing so. See the safety instructions if you are not sure how to do this, or see below.
Tip: The “Do not back” button determines whether or not the lens will visit the origin position after the job is
complete. Make sure to check this when making multiple passes.
Make sure the “cutting” switch on the machine control panel is set so the button is popped up (which is the OFF position)
and that the current dial is turned all the way to the left (minimum) position. Although the cabinet lid has a safety switch, we
like to make sure the laser cannot fire while you’re loading material to be cut or engraved.
Let’s ry Cutting Out Some Parts (continued)
8

For the initial test, let’s load a piece of the provided 6” x 9” chipboard onto the honeycomb platform as shown below; that is,
all the way to the left edge, and centered in the lens’ range of motion from front-to-back.
Tip: We put a couple of dots of white paint on our
platform frame to help reload subsequent chipboards in
the same location. This will avoid having to reset the
starting crosshair position. You may prefer to use a
couple of the supplied magnets along the bottom edge
of the piece as a location guide.
Use the provided magnets to hold the chipboard tight to
the platform so that the laser stays focused.
Notice the tiny red dot projected onto the chipboard. This
is not the laser beam. This is an L D marker that shows
where the laser beam is aimed. The laser beam will
ultimately be seen as a bright white flash of light.
Close the lid. Turn the dial to the half-way position and
depress the “cutting” switch to its down position (this
allows the laser to fire). Now, quickly press and release the
“Test” button. Notice the burst of white light that the laser
fires at the chipboard. The little burned-through spot
should align with the projected red dot. If not, turn off the cutting switch and current dial, then reach into the chamber to
adjust the projector/L D housing so they are aligned when you again perform a test fire. In this way, you’ll be able to
pinpoint the starting point of the laser.
Going back to the computer screen…
In the upper left corner of the object image, two dotted cross-hairs will be visible.
Tip: Depending on the type of monitor and its resolution settings, small objects may appear as white outlines,
which you can see if you move your head to the side a bit.
You can click and drag the image to locate the cutting
head (the lens) in a good starting spot on the chipboard
(you should see the carriage move inside the machine) so
that the entire image can be cut out without running off the
board or across the magnets. If you think you’re in a good
location, click on “Starting” (under the Properties button . . .
if you forgot to install the USB “key,” you’ll be reminded
right here) and let the machine go through the cutting
routine (while the laser is still off). Watch the red pointer to
verify the correct travel. If the start position is okay, then at
the end of this “dry run,” depress the “cutting” button to its
down position, and turn up the dial to about 1/3 full current.
Then, click on “starting” again and the machine should cut
out the parts.
If all went well, and you have the sound turned on, the
computer will play a “TA-DA” when the cutting operation is
finished. Congratulations!
Remove the parts and the sheet. We suggest using a
vacuum cleaner to clean out stray cuttings from the cabinet.
Let’s ry Cutting Out Some Parts (continued)
9

Now, if you want to make parts to assemble into a real scale model, substitute the provided piece of scribed siding (use the
1/16” spacing for HO, 3/32” for O scale) for the chipboard and cut again, but use a setting of about 60% of full current for
the thicker wood sheet.
Hint: Use the “release” button on the ngraving/Cutting Manager window to release the carriage for movement by hand
with the laser turned off as described above. D N T F RGET T TURN FF THE LASER AND TURN THE CURRENT
T ITS L WEST SETTING BEF RE REACHING INSIDE THE CABINET! You can now slide the lens left and right while
watching the alignment of the red pointer with the scribed lines in the sheet of wood; otherwise, the scribed lines will be
angled on the building.
With everything lined up, loaded and locked, cut out the parts.
If the parts did not cut all the way through, you need to turn up the current. If they are too energetically burned through,
cut back the current. It’ll take a bit of trial and error to learn the best settings for the various kinds of materials.
Remember…you can always cut again, so build up the current slowly, rather than start out too high.
An O scale version of the shanty is included.
You’ll have to tinker a bit with a few of the settings and positioning of the materials, but you should have been quite
successful at this point. An alignment fixture can be laser cut using a computer file available online at:
http://www.micromark.com/downloads.dlp
Turn off the laser. Remove the parts and remainder of the sheet from the cabinet…if the remainder of the sheet has room
for more parts, go back to the object design screen and select only the parts you want. Then, position the pointer where to
start and go again.
This is a good time to experience the ease at which you can make changes. For example, on the drawing, click on the rear
wall outline and then press Ctrl+U on your keyboard to Ungroup its features. Click the window on the rear wall drawing and
press Delete on your keyboard. Select the rear wall and cut again in a blank spot on the material. The window opening is no
longer cut into the wall! For another example, try dragging the window to a different location, or change its size, and cut again.
Let’s ry Cutting Out Some Parts (continued)
here you go! Mastering CorelDRAW is up to you, but basic shapes are quite easy. Of particular benefit is the
ability to resize parts for perfect fit, and duplicate them for multiple cutting…like a row of windows.
10
Ready to try engraving (an image burned into the surface of the chipboard)? Then, follow along…
Load another sheet of chipboard into the chamber and again use magnets to hold it down to the platform.
Use file/close to wipe the page clean of the shanty drawing, then import the file called ngravingDemo.jpg
Drag the protractor icon to create a box about 3.5” wide. Then release the mouse button. You should see an image of a
trolley car. Click on the engraving icon (first one to the right of the green pencil icon). Click OK to get to the
ngraving Manager window. Notice that the settings have changed to those that are better for engraving (the speed is
higher and the style has changed to engraving). Make sure “Sunken” is checked.
Position the pointer same as before so the image will engrave into the surface of the chipboard. Use the Test button to
set the current knob to about 4 mA, and click on “starting.” The carriage should oscillate left and right about 10 times
faster than the cutting speed, and slowly travel back-to-front while the image is engraved. If the laser beam is cutting
through the material, reduce the current. The picture may take many minutes to completely engrave, so be patient!
At the end of the job, the machine will stop. TA-DA! You’ve engraved an image.
You can now use the software controls to change the image contrast and engraving settings for the picture you’re
engraving and for the material on which you’re engraving it. You may also un-check the “Sunken” box and see how the
image changes. If the material changes in thickness, don’t forget to re-focus the lens (see instructions shown later in this
manual).
Let’s ry Engraving

LaserKnife 2525 ips & ricks
WARNING!
NEVER REACH IN O HE CU ING CHAMBER WHEN HE LASER BEAM IS IN AN
AC IVE S A E OR COULD SUDDENLY BE AC IVA ED BY MACHINE SOF WARE.
• Laser cutting is defined by vector-based objects (example file type .cdr). Laser engraving is defined by raster-based
images (example file type .jpg).
• Vector mode moves the laser beam in continuous straight lines, at many angles. Raster mode scans the image area, moving
the laser beam back and forth, firing at points where the image should be, to construct the image out of a matrix of dots.
• Setting the CorelDRAW Default style to HAIRLIN , NO FILL, BLACK color will save a lot of work and avoid aggravation.
• Hairline is a CorelDRAW setting. It tells the laser beam to ignore line width and make only one pass (see next paragraph,
as well). If your CorelDRAW line width is set wider than Hairline, then the laser will make multiple passes in an attempt to
cut a wider line. Also, if the object has a fill, the laser may try to make the fill, as well; this comes in handy to cut patterns
at low power into the surface of the material.
• Cutting and engraving line widths are highly influenced by the laser power, speed of cut, workpiece material and
thickness. You will need to determine the best settings through trial and error…experience being the best teacher.
• In the ngraving/Cutting Manager window, under Common Parameters, Frame indicates the outline shape of your
engraved image.
• If Unidir is unchecked, the laser will cut in both directions (back and forth). If it is checked, the laser will cut in only one direction.
• If your laser cuts the same line repeatedly instead of moving to the next object, it’s usually because the object line width
is set to other than HAIRLIN , or the object has a fill of some kind. Also, verify the CorelDRAW Data setting screen has
the Cutting data setting as PLT – HP-GL/2 Plotter File
• Colors other than black will cut or engrave differently based on color. You’ll need to experiment to find out.
• Use magnets to hold thin material flat on the laser bed plate. Positioning magnets around the edges of the material and
in the center, as well (obviously avoiding the cut lines), will help hold the material from shifting after being cut. Adding
“frets” to the drawing will keep parts from shifting or dropping out. See instructions elsewhere in this manual.
• Thick materials cut best in multiple passes.
• When cutting plywood, the best results are usually obtained by using a faster speed, lower power, and multiple passes.
This avoids overheating the glue inside the plywood, which would then stick itself back-together.
• Acrylic (Plexiglas) cuts very well. Protective film does not have to be removed. Cutting acrylic produces some noxious fumes,
which should be exhausted from the cutting chamber with the cabinet lid closed for 30 seconds after cutting is completed.
• Avoid cutting PVC or any chlorinated plastic. These materials give off chlorine gas, which harms the machine’s parts
and people’s insides.
• Styrene sheet may be cut cleanly using low power and multiple passes. If the power is set too high, the material may
melt at the cut line and weld itself back-together.
• Gaterfoam cuts very cleanly, but the foam enclosed by the wood veneer may shrink from the cut line.
• In CorelDRAW, change the document size to match the LaserKnife 2525 bed plate, which is 9.8” x 9.8”.
• The laser cutting process produces smoke and very fine ash-debris, which eventually accumulates on the lens and
mirrors. Occasionally, clean these machine elements G NTLY with a cotton swab and cleaning fluid.
• xhausting smoke from the cabinet is important to reduce odors and contamination of the workshop. Make sure the
exhaust system is free of debris and blockage that would reduce air flow and/or cause a fire. Let the smoke clear before
opening the cutting chamber lid.
• Bubbles in the cooling water line could cause your laser tube to fail prematurely. Make sure the water is flowing strongly
and no bubbles are present when using the laser.
• Do not go near the red wire feeding the laser. It is pressurized to about 22,000 volts and can cause bodily harm.
• Blowing smoke and debris away from the cutting location is important to obtaining good results. Make sure the air pump
is working properly.
• The machine must be connected to a GFI protected power source.
11

12
LaserKnife 2525 ips & ricks (continued)
• Be sure the laser machine is electrically grounded by attaching a wire between the machine cabinet and a household
ground, like a water pipe or ground connection in a wall outlet.
• xperiment with contrast settings for the picture you’re engraving to see how it affects the resulting image. Adjust the
laser current and speed to produce the best image or cut line width. xperiment to learn what works best for the variety
of images and materials you’re using.
• If the thickness of the material you’re engraving or cutting changes, re-focus the lens. Set it for the mid-point of the thickness
you are going to cut. Obtain a scrap piece that is half the thickness of the material you will be cutting and place the focus
gauge on top of that. Check the focus at various points on the bed plate. If the variation from one point on the bed plate to
another is excessive, remove the bed plate (4 screws through the frame) and shim as necessary to minimize the variation.
• The location of the starting point of the cutting process, and typically of the object to be cut, is in the top-left position, but
can be reset by software.
• Tiny parts may fall through the honeycomb bed plate. Be sure to draw duplicate parts in various locations so that some
will remain. After cutting, you can collect them with a piece of tape before removing the larger parts from the bed plate.
• A vacuum cleaner makes fast work of cleaning scraps out of the cabinet. Adding “frets” to the drawing will keep parts
from shifting or dropping out. See instructions elsewhere in this manual.
• When designing a rectangular hole for fitting a plastic window, use scrap material to test the hole size before cutting
good material.
• Use the red L D pointer to align materials when placing them on the bed plate. With the laser deactivated, move the
lens left-to-right and back again to check the placement of the material. A R L AS button can be clicked in the
ngraving Manager window to allow lens movement if otherwise restrained by the system drive belts/motors.
• If you will be cutting multiple pieces of material in the same pattern, devise a little fixture to position new pieces of material
when loading the cutting chamber. (See our web site for a sample file). You can use the provided magnets as stop blocks,
or use them to hold a fixture in place.
• Be sure to save your drawings in the CorelDRAW version you are using.
• A great deal of additional helpful techniques and tips can be viewed on the Internet at www.engrave.com and many
other web sites.
• Draw your outlined shape (object) with CorelDRAW.
• Select the object you’ve drawn and navigate to
Arrange>Convert to Curves; this breaks the object up into
individual pieces.
• In the Object Properties tab, uncheck “Close Curve” and
click the Apply button. (Do not miss this step!).
• Select the eraser tool, and set the desired width and
shape of the fret (round or square; square is recommended
for most applications; suggested width to start is .025”).
• With the object selected, drag the eraser tool through the
shape’s outline where you wish to place a fret; the outline
will now appear broken.
• Repeat as needed until all frets have been added.
• Proceed with cutting as usual.
Frets are little bridges in the cut lines that keep parts from falling out of the sheet. Frets can be any size you like, and you
can place them wherever you desire. For scale model parts, we usually make the fret about .025” wide.
Having the frets is handy to the guy who manufactures kits; in that way, he can be sure that all the parts are in the sheet
and packing the kit is easy.
For the model maker, the frets can be a pain. You have to cut through the fret to release the part, then sand off the nub that
remains; however, cleaning all the pieces out of the machine is also a pain…especially if they’re small. You sometimes can
use a piece of masking tape to pick them up.
Frets are especially handy if the parts are tiny; it keeps them from falling through the platen. They’re also handy to keep the
“donut holes” from falling out of the donuts, like when cutting out text…the letters A, P, Q, B, O, etc.
Here’s how you go about adding frets to your laser designs:
Creating “Frets” for Laser Cutting Using he CorelDRAW Eraser ool

13
Frequently Asked Questions
What is the typical life of the laser tube?
The life expectancy of the laser tube depends on the amount and kind of use it gets, and, in particular, its power setting.
When used carefully at “normal” power (50% of maximum current) and with proper cooling water circulating through the
tube, the laser tube is expected to last for several hundred hours of cutting time. Replacements are available from the
Micro-Mark product service department; installation is the responsibility of the purchaser.
Will the machine cut plastic other than acrylic?
Yes. Acrylic (sometimes sold under the trade name Plexiglas) cuts best. Other plastics, including styrene, can be
successfully cut by taking multiple passes (repeats) at low power settings and faster speeds to avoid melting the plastic
so that cut lines weld back together. We’ve had only moderate results with polycarbonate and had to use a scroll saw or
knife to finish the cut.
Can I cut thick materials?
Yes, you can, but we recommend you do so in several passes (sometimes called “repeats”). CorelLAS R software
(supplied with the machine) has a provision for making multiple passes. We’ve successfully cut ¼” thick cherry in 6
passes. We suggest you avoid too high a laser current so that the life of the laser tube is not compromised.
My machine will not respond to the computer. What’s wrong?
Most-likely, the Device ID entered under machine properties does not match the number on the CorelLAS R PCB
located in the electrical chamber. Check the label on the outside of the cabinet by the USB port. Also check that the USB
cable is still connected properly and the machine is powered-up.
If the laser tube is replaced, or the machine experiences strong shock and no longer cuts
properly, is there a fix?
Yes. Most-likely, the laser tube and/or mirrors have shifted from the original factory alignment and the mirrors will need to
be re-aligned to direct the beam properly to the lens. See the attached procedure for doing so.
he lens sometimes moves to the extreme right side and/or front of the chamber and goes
“bump-bump-bump.” Will this damage the mechanism and how do I prevent this?
Verify that the settings for the ngraving Machine Properties Logic Page Initialize are set as follows:
PageSizeX: 250.000 mm
PageSizeY: 250.000 mm
If the settings are larger than these numbers, the software thinks the machine is larger than it really is and tries to send
the carriage beyond its mechanical limits. If the machine goes bump, immediately turn off the power switch.
Cutting does not match the drawing…especially with repeated shapes all in a row. What’s wrong?
Usually, the cutting speed is set too high on the ngraving Manager window and the computer cannot keep up with the
machine. A good starting point is 16.00 mm/s (millimeters per second). This gives the software enough time to manage
the lens position and move it to the next place properly. Use scrap materials or paper to test how high the speed can be
set for the design you’re cutting. Also, smoother cuts are obtained with slow speeds, but reduce the power to avoid
burning the material.
When I click on Cutting or Engraving, nothing appears on the Manager window. Why?
If your setting is for “Only Selected,” you have to click on the object you want to cut or engrave to get it to appear.

14
Frequently Asked Questions (continued)
Must I draw the location of every hole I want to cut?
No. Draw just one hole. Then, on your material, mark the starting point of each hole you want to cut. Place this mark
under the red dot and make the cut. Move the material, then cut again, and so on…
When making multiple passes, the cut lines are not in exact registration
For best regsitration, be sure “Do Not Back” is checked.
he engraved image is too light or too dark. What can I do to improve this?
xperiment a bit on scrap pieces to find the right combination of speed and laser current for the material you’re cutting.
he machine cuts in a wild pattern…more like the way I drew it, rather than taking an efficient
route. What can I do to improve this?
In the Manager window, select Style of “Shortest route.”
I want to move the carriage out of the way so I can load and unload my workpieces.
How do I do that?
First, make sure the laser current switch is turned all the way counterclockwise; then make sure the cutting switch is
popped up. Then, in the Manager window, click on “release” and wait a few seconds. The carriage is now free to move.
Before starting up the machine again, it’s a good idea to move the carriage back to its position before you moved it so it
can index to the starting point without much trouble.
When I cut materials of different thickness, the cutting or engraving isn’t as “sharp” as it
should be. Can I compensate for this?
The lens can be shifted up or down to accommodate workpieces of different thickness. See the attached instructions for
setting the lens position (focus). Also try reducing the laser current.
Tip: Learning the following CorelDRAW functions in the following order will help you to rapidly make great use of the
LaserKnife (see the Help menu for instructions):
• Setting page size
• Setting hairline as the default line width
• Drawing and sizing a rectangular shape
• Selecting objects
• Dragging objects to locate them
• Making sure objects are not filled
• Grouping/ungrouping objects
• Drawing and sizing an elliptical/circular
object
• Deleting objects
• Duplicating objects
• Aligning and distributing objects
• Rotating objects
• Zooming the view
Cutting curved shapes, even complex ones, and objects with very thin sections, such as model window sash, can be
accomplished quickly and accurately; certainly beyond that which can be cut with a standard modelers’ knife.
Be sure to check the Micro-Mark web site for additional drawing files. Many other drawings are available on the Internet for
free download.
Refining the use of the LaserKnife 2525 goes beyond the intent of these instructions, but we hope that you will share your
designs on our web site, where we will collect and share, over time, an assortment of fantastic drawings that Micro-Mark
customers can use with their LaserKnife 2525.
Beyond “ he Basics”

LaserKnife 2525 Machine Adjustments
Adjusting the Mirrors
There are 3 mirrors that must be aligned properly to direct
the laser beam into the lens. We shall refer to them as
mirrors #1, #2 and #3 as follows:
Mirror #1 is located in the chamber containing the laser tube,
and is located in the rear left corner of the cabinet at the
output end of the laser tube. It does not move, but can be
adjusted like the others.
Mirror #2 is located at the extreme left end of the carriage
and moves forward and backward only.
Mirror #3 is located above the lens and moves not only
forward and backward, but also from left to right.
The beam travels from the laser output into Mirror #1, where
it is directed to Mirror #2 and subsequently to Mirror #3,
which directs it downward through the lens.
Note: These are front-surface mirrors, and they should not be touched with tools or fingers. The reflective surface is
N T protected by a glass surface and can be easily damaged.
The mirrors are to be adjusted in sequence: first #1, then #2, and finally #3. The basic procedure works as follows: Tape
a piece of paper directly in front of the mirror and, with the lid closed, press the “Test” button to fire the laser. Note the
position of the burn mark with respect to the mirror outline and adjust each mirror, in sequence, using the jack screws and
lock nuts, so that the burn mark is centered in the outline. This will assure full laser output is reaching the lens and,
subsequently, the surface of the workpiece.
Adjusting the Lens Focus
Laser cutters/engravers work best when the lens is focused
properly. A clear plastic gauge has been supplied with the
machine. It helps you set the proper distance between the
bottom of the lens and the surface of the workpiece for
optimum focus (see below for details). To reposition the lens,
loosen the knurled screw and gently lift or lower the lens
housing. Retighten the screw to hold the lens in place. Be sure
to adjust each time you change material thickness.
For engraving and for cutting thin materials, use the gauge
to set the distance from your workpiece’s top surface.
For cutting thick materials, use the gauge on top of a piece
of scrap material that is half the thickness of the material you
intend to cut. Then adjust the lens position as above. The
illustration at left shows this situation.
When cutting or engraving very thin materials, you may not
be able to lower the lens far-enough to satisfy the focus gauge
measurement, and the brass lock screw may not engage the
lens barrel properly. In this case, simply put a piece of flat
scrap material (perhaps 1/4” thick) under the workpiece to
raise the top surface to a more-suitable position for focusing
the lens.
15

T H E S M A L L T O O L S P E C I A L I S T S
340 Snyder Avenue, Berkeley Heights, NJ 07922
www.micromark.com • Tech Support: 908-464-1094, weekdays, 1pm to 5 pm T • [email protected]

How the Software Works
The MicroLux LaserKnife is controlled by a program called CorelLAS R, which is a plug-in that adds functionality to a
drawing program called CorelDRAW. CorelDRAW is available for download off the Internet or purchase from a local
computer software dealer; CorelLAS R is compatible with CorelDRAW versions 11 or later (Home & Student versions of
CorelDRAW are not compatible). Install CorelDRAW on your Windows 2000 or later operating system before proceeding
with CorelLAS R installation.
After you purchase the LaserKnife, CorelLAS R can be downloaded from the Micro-Mark web site at:
http://www.micromark.com/downloads.dlp . The LaserKnife cartons include a “key” that you insert into a USB port on
your computer; CorelLAS R will not send control signals to the LaserKnife unless the USB key is inserted.
You create your object drawings in CorelDRAW (you can also import images from other compatible programs) and save
them, usually as a .cdr file for a drawing or a .jpg for an image, like a picture. Then, when you’re ready to cut out your
objects or engrave a picture, start CorelLAS R, open the saved file, open the ngraving/Cutting Manager window and
run the LaserKnife.
How to Download and Prepare CorelLASER for use with the LaserKnife
Go to http://www.micromark.com/downloads.dlp and download the files to your computer under the default settings,
which should put the zip files into your Documents>Downloads folder of your computer.
Double left-click CorelLAS RMasterFiles.zip
Double left-click CorelLAS RMasterFiles
Double left-click CorelLAS R XXXX.XX.exe (Note: The X’s represent release dates shown in the file name)
Click OK for the nglish selection
Follow the on-screen instructions for installation. Be sure to install CorelLAS R in the default 3WCAD folder.
After installation, when you start CorelLAS R, you may see a window advertising other CorelLAS R-type products. Just
close this window.
Micro-Mark programmers have created a few revised CorelLAS R operating files to make the program more user-
friendly. To incorporate these files, please do the following:
Navigate to Start>MyComputer>Local Disk (C:)>ProgramFiles>3WCAD>CorelLAS R>Languages
Right-click nglish.ini and Select Rename. Type nglishOld.ini and press nter. Leave this window open.
Navigate to Start>MyDocuments>My Downloads>CorelLAS RMasterFiles.zip>CorelLAS RMasterFiles
Click and hold the mouse button on the nglish.ini file and drag it into the Languages window you left open. Release the
mouse button. The nglish.ini file should now appear in the Languages folder.
Close all the windows.
CorelLASER is now ready to go to work for you!
DE AILED INS RUC IONS FOR LOADING LASERKNIFE SOF WARE
In the following instructions, please note that a distinction is made between CorelDRAW and CorelLASER.
MM031615
TM
Table of contents
Popular Measuring Instrument manuals by other brands
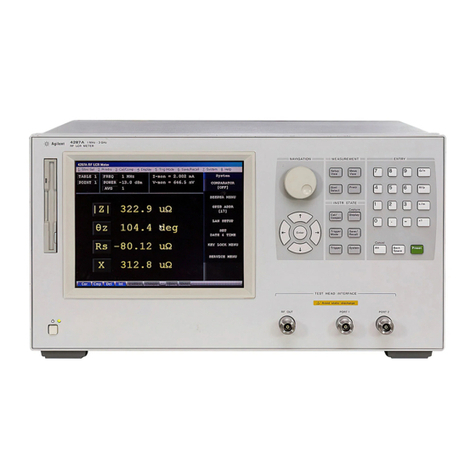
Agilent Technologies
Agilent Technologies Twelfth 4287A RF LCR Operation manual
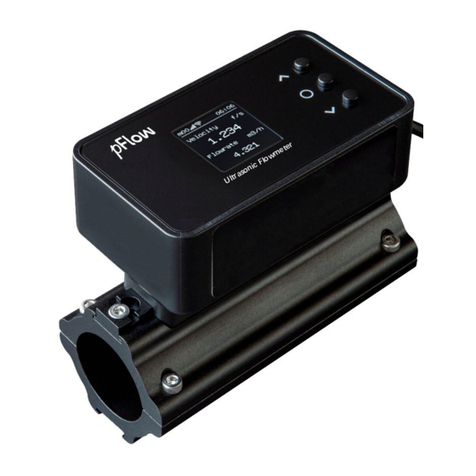
PFlow Industries
PFlow Industries F2 instruction manual
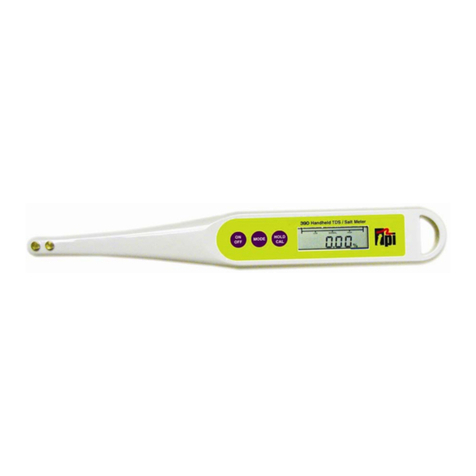
TPI
TPI 390 Operation manual

Endress+Hauser
Endress+Hauser Proline Promag W 500 operating instructions
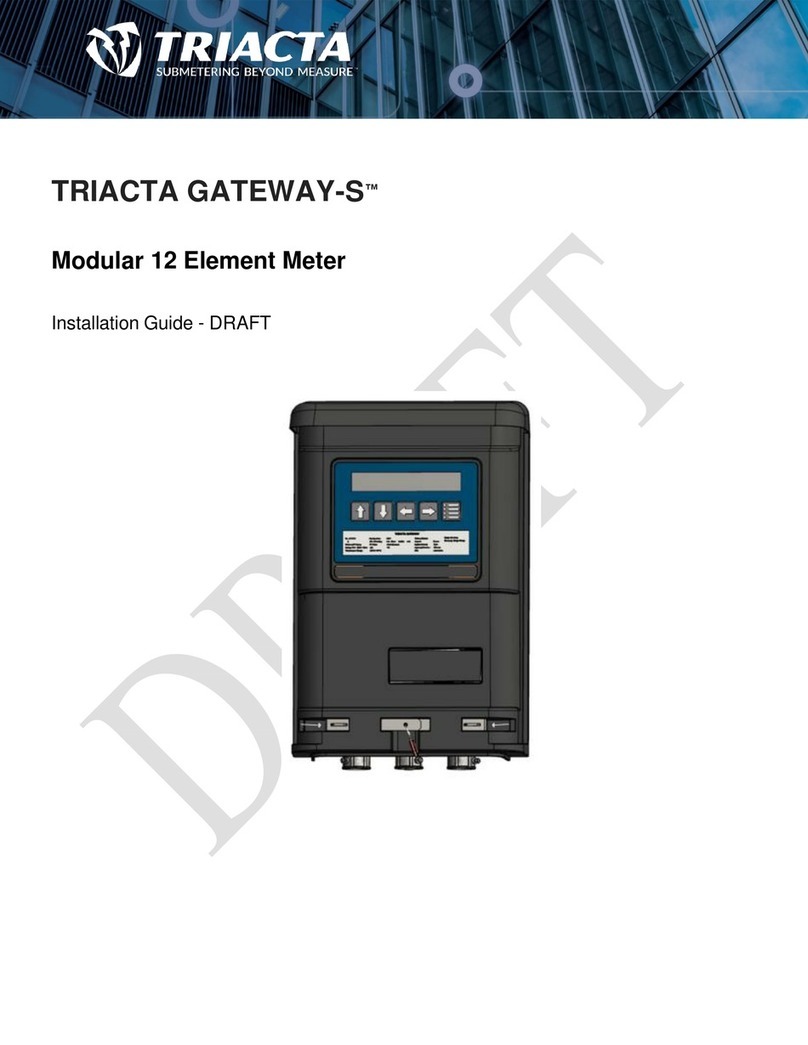
Triacta
Triacta GATEWAY-S installation guide
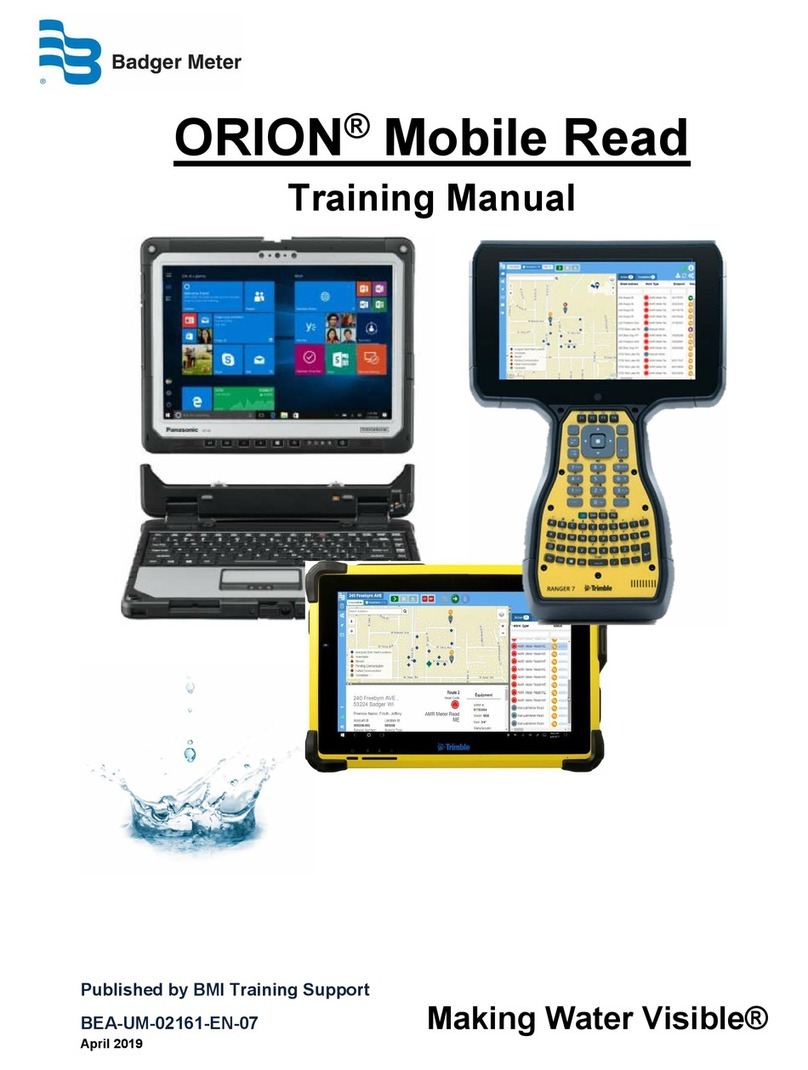
Badger Meter
Badger Meter ORION Mobile Read Training manual