MID BT Series User manual

Thank you for choosing MID products
Before using any machine please be sure to read the entire manual
BT Series
ID-Mounted Pipe Beveling Machine
Operation Manual
MID Industrial Tools INC

2
TABLE OF CONTENTS
PART 1 EQUIPMENT INSTRUCTIONS
PART 2 SAFETY INSTRUCTIONS
PART 3 MACHINE SPECIFICATIONS
PART 4 INSTALLATION AND OPERATION
PART 5 IMPORTANT NOTES
PART 6 DIAGRAM OF BEVELING TOOL BIT
PART 7 DIAGRAM OF EXPANDING BLOCK
PART 8 TROUBLE SHOOTING
PART 9 EXPLODED VIEWS AND PARTS LIST
PART 10 ORDERING INFORMATION
PART 11 WARRANTY CARD

3
PART 1 EQUIPMENT INTRODUCTION
BT Series
ID-Mounted Pipe Beveling Machine.
FEATURES:
1. Cutter can hold 3 tool bits at one time
Automatic welding require OD Beveling, facing and internal beveling
Only using 3 bits at one time can guarantee the precision of beveling
2. New expanding structure
Newly designed expanding structure makes the machine more stable
3. New design main shaft fixation
Smaller gap from the machine to pipe.
Smoother beveling with less vibration
FAST SETUP
l Set up and operate from storage case to pipe in 1 minute
l Expanding nut makes the installation quickly
l One adjustment, universal three-leg chuck centers the machine in pipe I.D. automatically
l Install and adjust tool bits in seconds
l Can be installed any direction: horizontal, vertical or slant
EASY OPERATION
l The miniaturized design is suitable for low-clearance applications
l Ratchet wheel design makes tool feed easy, absorbs torque, reduces operator fatigue and
increases safety
l In-feed structure with scale for precise measurement

4
TUBE O.D
TUBE I.D
TUBE O.D
TUBE I.D
TUBE O.D
TUBE I.D
TUBE O.D
TUBE I.D
TYPICAL FUNCTION DESIGN
l Aluminum housing, light weight
l The equipment can machine V and U welding seam
l High strength mandrel and large-area expanding block improves the rigidity
l Two/three bevel tools can be installed on cutter, pipe can be worked synchronously
TYPICAL Buttwelding seam
PACKAGE
l The machine is packaged in a portable heavy duty plastic case with machine, expanding
blocks, beveling tools, O-rings, tools, operation manual and packing list.

5
PART 2 SAFETY INSTRUCTIONS
We take great pride in manufacturing safe, quality products. Please comply with the following safety
rules and instructions before operating the equipment.
Read the following content before working
READ THE OPERATION MANUAL
Before operating, you should read the manual and make sure you understand all setup and operating
instructions, it can help you save time and avoid injury to the operator and damage to the machine
INSPECT MACHINE & ACCESSORIES
Before starting the machine, look for loose bolts or nuts, leaking lubricant, and any other physical
conditions that may affect operation. Properly maintaining the machine can greatly decrease the
chances for injury.
ALWAYS READ SIGNS AND LABLES
Please read the marks and signs. All the marks and signs should be clear and easy to read.
DANGER! ELECTRIC SHOCK
Always disconnect machine from power source before moving or removing motor
.
CAUTION HAND INJURY
Keep hands, arms and fingers clear of all moving parts
WEAR SAFETY GOGGLES
Eye protection required when using equipment,
Please wear safety goggles.

6
PART 3 MACHINE SPECIFICATIONS
Drive option: Air, Electric
Air requirement: 900-1500L Per minute @ 0.6/0.7Mpa
Electric requirement:120V60HZ
MODEL BT1 BT3 BT6 BT8 BT14
Machine Performance Ranges
Working range inside
diameter to outside diameter
16-33.4mm 25-88.9mm 60-168.2mm 65-219.0mm 145-355.6mm
0.62-1.3'' 1-3.5'' 2.3-6.5'' 2.5-8.6'' 5.7-14''
Wall Thickness
≤8mm ≤15mm ≤20mm ≤20mm ≤20mm
≤0.3" ≤0.6" ≤0.78" ≤0.78" ≤0.78"
Rotation speed pneumatic 0-66RPM 0-66RPM 0-61RPM 0-50RPM 0-18RPM
Pneumatic motor
Recommended air pressure
90PSI 90PSI 90PSI 90PSI 90PSI
6.2BAR 6.2BAR 6.2BAR 6.2BAR 6.2BAR
Recommended volume
30CFM 30CFM 30CFM 41CFM 41CFM
0.9m3/Min 0.9m3/Min 0.9m3/Min 1.2m3/Min 1.2m3/Min
Electric motor
Electric motor BOSH, 1.38HP(1.05kw), 60HZ,120V
1.6HP(1.2kw)
60HZ
2HP(1.5kw) 60HZ
Measure
Machine weight
Pneumatic, Complete
machine
15.4lbs 18.7lbs 35.2lbs 57.2lbs 101.2lbs
7kgs 8.5kgs 16kgs 26kg 46kgs
Electric, Complete machine
17.6lbs 19.8lbs 37.4lbs 61.6lbs 105.6lbs
8kgs 9kgs 17kgs 28kg 48kg
Shipping weight
Pneumatic 14kg(30.8lbs) 15kgs(33lbs) 29kgs(63.8lbs) 41kg(90.2lbs) 68kgs(149.6lbs)
Electric 16kg(35.2lbs) 16kgs(35.2lbs) 31kgs(68.2lbs) 44kg(96.8lbs) 70kgs(154lbs)
Dimensions
Length (L x W x H)
21*16*6.7" 21*16*6.7" 22*21.6*10" 22*11*10" 32.6*17*16"
540*410*170mm 540*410*170mm
560*550*250mm
speed electric
Rotational Drive System
0-65RPM 0-65RPM 0-65RPM
650*280*250mm 830*430*410mm
0-24RPM
Rotation 0-20RPM

7
Tool feed position
Tool back position
PART 4 INSTALLATION AND OPERATION
SECTION 1
TOOL FEED / BACK INSTRUCTION
A. BT1/BT3/BT6 tool feed / back hand wheel
See figure:
Tool F ee d : rotate c l o c k w i s e
Tool B ac k : rotate counterclockwise
B. BT8/VBT14 adopt tool feed/back ratchet spanner
See below figure:
Tool F ee d : P r e s s paw l clo ck w i s e , pull s p a n n er c lockwise
Tool B ac k : P re ss paw l counterclockwise, pull spanner counterclockwise
OPERATION PROCEDURE
1. Measure the ID of the pipe, and then choose the proper expanding block according to the diagram
of expanding blocks, (see the figure on the expanding blocks), choose proper block, fix them on
the wedge block, and tighten.
2. Install the proper tool bit on the cutter. Make sure the tool bit is clockwise.
Caution: The tool bit can not touch the spindles; otherwise may damage the machine
3. Back the travel of tool bit by tool feed using hand wheel (tool feed/back ratchet spanner). Insert
the expandable mandrel into the pipe, fasten the expansion nut lightly, shake the machine (in
order to center, and make the expanding block properly contact the ID pipe), the machine will be
centered, Then fasten the expansion nut tightly, make sure the equipment and the pipe are fixed
solid.
Caution: The expandable mandrel should not be inserted too deep, it’s better to keep a 2-3mm

8
distance between tool bit and pipe end high point.
4. Turn on the motor then turn off, let the cutter rotate 1 circle, in order to confirm the machine and
tool bit are installed correctly before cutting, Turn on the motor, rotate the tool feed hand wheel
(tool feed/back ratchet spanner) manually until the tooling makes contact with the pipe.
Caution:
4.1 Manually feed the tool bit with an even motion.
4.2 Continue to spray coolant (saponification oil) while working This will make the beveling
smooth and prolong the tool bit life
4.3 If the tool bit becomes dull, sharpen it or replace with a new one
4.4 While working, avoid scrap-iron from going into the motor.
5. After beveling is completed, back the travel of tool bit by tool feed hand wheel (tool feed/back
ratchet spanner) first, then turn off the motor, loosen the expansion nut, and take off the machine.
Caution: If you do not back the travel of tool first, the feed wheel may be damaged, resulting in
the expansion nut and feed wheel getting stuck.. Please repeat the above, if the machine is for
continuous working, in order to make sure the machine operates normally.
6. After the tool bit is installed , the machine can be moved and continue processing from one pipe
to another same size pipe, no need to adjust the tool bit again, only back the travel of tool bit.
Loosen the expansion nut, and fix it on another pipe.
Caution: When loosening the expansion nut, and taking the machine out or adjusting the location
of machine, do not let it slip into the pipe.This may damage the tool blade
NOTES FOR PNEUMATIC SERIES
1. Compressed air required: Dehydrated and filtered air
Required air treatment: air filter, regulator and atomized lubricator (FRL system)
An air filter makes the compressed air dry and clean, avoiding rust and damaging the air motor.
Atomized lubricator lubricates the air motor internals
If you do not have a FRL system, add lubricating oil (engine oil and kerosene 1:1) at air in-inlet
every time before and after use, and clean the motor parts regularly
Caution: This is a remedy and not recommended use, Recommend the air filter and atomized
lubricator to maintain air motor
2. While working, if the tool feed speed is too fast or low air pressure makes the cutter stop rotating,
turn off the air valve and back the tool immediately. Fix air supply issues before continuing work.

9
Tool bit
(1)
Tool bit
Pipe
(2)
Pipe
PART 5 IMPORTANT NOTES
1. The carbon brush was adjusted before dispatch, they can feed automatically. Please do not adjust;
Note: After 100 working hours, check the wear condition. Replace the carbon brush if needed. If
the carbon brush wears out, please turn off the machine immediately, otherwise the motor will be
damaged. We suggest: when carbon brush wears 2/3, replace the carbon brushto aviod motor
damage.
2. If the tool bit is dull, bevel resistance will increase and spline shaft and/or motor and reducer
parts will be damaged. Please sharpen tool bit or replace with a new one.
If you sharpen the tool bit, one tool bit can be used multiple times
If the tool bit is dull and tool feed is too much it may cause the motor to stop. Turn off the power
immediately, otherwise the motor and machine may be damaged.
How to check if the tool bit is dull or sharp:
Figure 1: tool bit is sharp, scrap-iron is a strip
Figure 2: tool bit is dull, scrap-iron is fragment
3. Continue to spray coolant (saponification oil) while working to make the beveling smooth and
prolong the tool bit life
4. Before beveling, please remove the rough edge and other incidentals after flame cutting with
hammer. If the pipe end surface is full of bumps and holes, start at the high point, and feed the
tool bit carefully.
5. When working with small size tube, please use a bench clamp or other tool to fix the tube
6. BT6 and BT14 adopt a tool feed/back ratchet spanner, it is convenient for operator, but must
control the feed speed. If you feed too much it may damage machine.
7. Motor may stop which is caused by a dull tool bitor tool feed is too fast Cut-off the power supply
immediately, otherwise will damage the motor.
8. Operator must read this manual completely before operation, the damage caused by improper
operation will not be covered under warranty.

10
PART 6 DIAGRAM OF BEVELING TOOL BIT
M42 Tooling Chart
Facing tools
Description
Part Number
Application
Sketch
Facing tool
Material:AISI M42
Width:22mm
Thk:6mm
Step type
42F-0622S
BT1
Facing tool
Material:AISI M42
Width:22mm
Thk:8mm
Step type
42F-0822S
BT3, BT6, BT8
Facing tool
Material:AISI M42
Width:22mm
Thk:8mm
42F-0822
BT3, BT6, BT8
Facing tool
Material:AISI M42
Width:25mm
Thk:10mm
42F-1025
BT14
Beveling tools
Description
Part Number
Application
Sketch
Beveling Tool
Material:AISI M42
Width:22mm
Thk:6mm
Step type
42B-0622S-30°
BT1
a is beveling angle required
42B-0622S-37.5°
42B-0622S-a
Beveling Tool
Material:AISI M42
Width:22mm
Thk:8mm
Step type
42B-0822S-30°
BT3, BT6, BT8
a is beveling angle required
42B-0822S-37.5°
42B-0822S-a
Beveling Tool
Material:AISI M42
Width:22mm
Thk:8mm
42B-0822-30°
BT3, BT6, BT8
a is beveling angle required
42B-0822-37.5°
42B-0822-a

11
Beveling tools
Description
Part Number
Application
Sketch
Beveling Tool
Material:AISIM42
Width:25mm
Thk:10mm
42B-1025-30°
BT14
a is beveling angle required
42B-1025-37.5°
42B-1025-a
Inner Beveling tools
Description
Part Number
Application
Sketch
Inner
Beveling tool
Material:AISI M42
Width:22mm
Thk:8mm
Step type
42IB-0822S-12°
BT3, BT6, BT8
a is beveling angle required
42IB-0822S-15°
42IB-0822S-a
Inner
Beveling tool
Material:AISI M42
Width:22mm
Thk:8mm
42IB-0822-12°
BT3, BT6, BT8
a is beveling angle required
42IB-0822-15°
42IB-0822-a
Inner
Beveling tool
Material:AISI M42
Width:25mm
Thk:10mm
42IB-1025-12°
BT14
a is beveling angle required
42IB-1025-15°
42IB-1025-a
* Consult with us for special applications
Note:
For inconel, duplex, please consult with us.

12
PART 7 DIAGRAM OF THE EXPANDING BLOCK
Expanding block (extension legs)
Model
BT1
BT3
BT6
BT8
BT14
No Block
15-17
25-29.5
60-70
65-75
Plus pad 145-155
145-185
1
17-19
29.5-34
70-80
75-85
Plus pad 155-165
185-225
2
19-21
34-38.5
80-90
85-95
Plus pad 165-175
225-265
3
21-23
38.5-43
90-100
95-105
Plus pad 175-185
265-305
4
23-25
43-47.5
100-110
105-115
Plus pad 185-195
305-345
5
47.5-52
110-120
115-125
Plus pad 195-205
6
52-56.5
120-130
125-135
Plus pad 205-215
7
56.5-61
130-140
135-145
8
61-65.5
140-150
9
65.5-70
150-160
10
70-74.5
150-160
11
74.5-79
Note:
Can supply stainless steel expanding blocks

13
PART 8 TROUBLE SHOOTING
Trouble
Possible reason
Remedy
Machine does not work
The cable is not connected
properly ; Air motor drive may
have a connection problem
Check the cable and the air
supply device to see if it is
properly installed
Machine waves when working
The expansion structure is not
fastened or the expanding block
is the wrong size;
Cutter screw loose
Check the expansion screw or
change to the proper expanding
block
Check the screw on the cutter
Working face not good
The bevel tool bit is dull or
damaged
Sharpen the tool bit or replace
with new tool bits
Air Motor weak
The motor vane(blade) wear
Replace with new motor vane
Air Motor does not work
Dirt jam;
Parts rusted
Clean the air motor and use the
air treatment (filter / regulator /
lubricator) for compressed air
Electric motor burnt out
scrap-iron or water inside;
unsteady power voltage;
Tool bit dull, resulting in high
load;
Replace with new motor rotor or
stator;
Replace complete motor
Note:
If there is a problem not listed in the chart, stop operation and contact us for additional instructions

14
PART 9 EXPLODED VIEWS AND PARTS LIST
Important Note:
When needing a replacement part, please advise machine Model No. & Part No.
BT1 BT3 BT6 P Air Motor Assembly
Part No.: AMA136
No.$
Part$No.$
Description$
Qty$
No.$
Part$No.$
Description$
Qty$
1"
AMA13601"
Housing"
1"
11"
AMA13611"
Exhaust"cover"
1"
2"
AMA13602"
Deep"groove"ball"bearing"
1"
12"
AMA13612"
Motor"rear"cover"
1"
3"
AMA13603"
Rotor"front"cover"
1"
13"
AMA13613"
Pin"
1"
4"
AMA13604"
Eccentric"stator"
1"
14"
AMA13614"
Cylinder"spring"
1"
5"
AMA13605"
Motor"rotor"
1"
15"
AMA13615"
Rotation"Switch"
1"
6"
AMA13606"
Blade"
5"
16"
AMA13616"
Valve"element"
1"
7"
AMA13607"
Rotor"rear"cover"
1"
17"
AMA13617"
Taper"spring"
1"
8"
AMA13608"
Deep"groove"ball"bearing"
1"
18"
AMA13618"
Nut"
1"
9"
AMA13609"
O"ring"
2"
19"
AMA13619"
Quick"coupling"
1"
10"
AMA13610"
O"ring"
1"
"
"
"
"

15
BT8 P Air Motor Assembly
Part No.: AMA8
No.$
Part$No.$
Description$
Qty$
No.$
Part$No.$
Description$
Qty$
1"
AMA801"
Housing"
1"
11"
AMA811"
Exhaust"cover"
1"
2"
AMA802"
Deep"groove"ball"bearing"
1"
12"
AMA812"
Motor"rear"cover"
1"
3"
AMA803"
Rotor"front"cover"
1"
13"
AMA813"
Pin"
1"
4"
AMA804"
Eccentric"stator"
1"
14"
AMA814"
Cylinder"spring"
1"
5"
AMA805"
Motor"rotor"
1"
15"
AMA815"
Rotation"Switch"
1"
6"
AMA806"
Blade"
5"
16"
AMA816"
Valve"element"
1"
7"
AMA807"
Rotor"rear"cover"
1"
17"
AMA817"
Taper"spring"
1"
8"
AMA808"
Deep"groove"ball"bearing"
1"
18"
AMA818"
Nut"
1"
9"
AMA809"
O"ring"
2"
19"
AMA819"
Quick"coupling"
1"
10"
AMA810"
O"ring"
1"
"
"
"
"

16
BT14 P Air Motor Assembly
Part No.: AMA14
No.$
Part$No.$
Description$
Qty$
No.$
Part$No.$
Description$
Qty$
1"
AMA1401"
Housing"
1"
9"
AMA1409"
O"ring"
2"
2"
AMA1402"
Deep"groove"ball"bearing"
1"
10"
AMA1410"
O"ring"
1"
3"
AMA1403"
Rotor"front"cover"
1"
11"
AMA1411"
Exhaust"cover"
1"
4"
AMA1404"
Eccentric"stator"
1"
12"
AMA1412"
Motor"rear"cover"
1"
5"
AMA1405"
Motor"rotor"
1"
13"
AMA1413"
Ball"Valve"
1"
6"
AMA1406"
Blade"
5"
14"
AMA1414"
Switch"handle"
1"
7"
AMA1407"
Rotor"rear"cover"
1"
15"
AMA1415"
Quick"coupling"
1"
8"
AMA1408"
Deep"groove"ball"bearing"
1"
"
"
"
"

17
Electric Motor Adaptor
BT1
BT1 BOSCH motor
1-7 Assembly Part No. EA1B
8-21 Assembly Part No. V1BPC
BT1 Bosch Motor
No$
Part$No.:$
Description$
Qty$
No$
Part$No.:$
Description$
Qty$
1"
EA1B01"
Shell"back"cover"
1"
12"
EA1B12"
Helical"gear"shaft"
1"
2"
EA1B02"
Stator"
1"
13"
EA1B13"
Flat"key"
1"
3"
EA1B03"
Carbon"brush"
2"
14"
EA1B14"
Bearing"
2"
4"
EA1B04"
Stator"housing"
1"
15"
EA1B15"
Helical"gear"
1"
5"
EA1B05"
Rotor"
1"
16"
EA1B16"
Reducer"casing"front"cover"
1"
6"
EA1B06"
Bearing"
1"
17"
EA1B17"
Allen"screw"
3"
7"
EA1B07"
Rotor"helical"gear"
1"
18"
EA1B18"
Bearing1"
1"
8"
EA1B08"
Reducer"casing"
1"
19"
EA1B19"
Internal"clip"
1"
9"
EA1B09"
Bearing3"
2"
20"
EA1B20"
Flat"key"
1"
10"
EA1B10"
Allen"screw"
4"
21"
EA1B21"
Straight"gear"shaft"
1"
11"
EA1B11"
Helical"gear"
1"
"
"
"
"

18
Electric Motor Adaptor
BT3
BT3 BOSCH motor
1-7 Assembly Part No. EA3B
8-21 Assmbly Part No. V3BPC
BT3 Bosch Motor
No.$
Part$No$
Description$
Qty$
No.$
Part$No$
Description$
Qty$
1"
EA3B01"
Shell"back"cover"
1"
12"
EA3B12"
Helical"gear"shaft"
1"
2"
EA3B02"
Stator"
1"
13"
EA3B13"
Flat"key"
1"
3"
EA3B03"
Carbon"brush"
2"
14"
EA3B14"
Bearing"
2"
4"
EA3B04"
Stator"housing"
1"
15"
EA3B15"
Helical"gear"
1"
5"
EA3B05"
Rotor"
1"
16"
EA3B16"
Reducer"casing"front"cover"
1"
6"
EA3B06"
Bearing"
1"
17"
EA3B17"
Allen"screw"
3"
7"
EA3B07"
Rotor"helical"gear"
1"
18"
EA3B18"
Bearing1"
1"
8"
EA3B08"
Reducer"casing"
1"
19"
EA3B19"
Internal"circlip"
1"
9"
EA3B09"
Bearing"
2"
20"
EA3B20"
Flat"key"
1"
10"
EA3B10"
Allen"screw"
4"
21"
EA3B21"
Straight"gear"shaft"
1"
11"
EA3B11"
Helical"gear"
1"
"
"
"
"

19
Electric Motor Adaptor
BT6
BT6 BOSCH motor
1-7 Assembly Part No. EA6B
8-21 Assmbly Part No. V6BPC
BT6 Bosch Motor
No$
Part$No.:$
Description$
Qty$
No$
Part$No.:$
Description$
Qty$
1"
EA6B01"
Shell"back"cover"
1"
12"
EA6B12"
Helical"gear"shaft"
1"
2"
EA6B02"
Stator"
1"
13"
EA6B13"
Flat"key"
1"
3"
EA6B03"
Carbon"brush"
2"
14"
EA6B14"
Bearing"
2"
4"
EA6B04"
Stator"housing"
1"
15"
EA6B15"
Helical"gear"
1"
5"
EA6B05"
Rotor"
1"
16"
EA6B16"
Reducer"casing"front"cover"
1"
6"
EA6B06"
Bearing"
1"
17"
EA6B17"
Allen"screw"
3"
7"
EA6B07"
Rotor"helical"gear"
1"
18"
EA6B18"
Bearing1"
1"
8"
EA6B08"
Reducer"casing"
1"
19"
EA6B19"
Internal"circlip"
1"
9"
EA6B09"
Bearing3"
2"
20"
EA6B20"
Flat"key"
1"
10"
EA6B10"
Allen"screw"
4"
21"
EA6B21"
Straight"gear"shaft"
1"
11"
EA6B11"
Helical"gear"
1"
"
"
"
"

20
Electric Motor Adaptor
BT8
Assembly Part No.: ED10
No."
Part"No.:"
Description"
Qty"
No."
Part"No.:"
Description"
Qty"
1"
ED1001"
Screw"M4X25"
4"
18"
ED1018"
Rotor"shaft"gear"
1"
2"
ED1002"
spring"washer4"
4"
19"
ED1019"
Reducer"
1"
3"
ED1003"
ventilation"cover"
1"
20"
ED1020"
spring"washer5"
3"
4"
ED1004"
Motor"cover"
1"
21"
ED1021"
Screw"M5X30"
3"
5"
ED1005"
Bearing"628"
1"
22"
ED1022"
Locating"pin"
2"
6"
ED1006"
Screw"M4X10"
2"
23"
ED1023"
Bearing618-8"
4"
7"
ED1007"
Carbon"brush"
2"
24"
ED1024"
Motor"input"helical"gear"
1"
8"
ED1008"
Motor"switch"
1"
25"
ED1025"
Key4x10"
1"
9"
ED1009"
Carbon"brush"holder"
2"
26"
ED1026"
Motor"output"helical"shaft"
1"
10"
ED1010"
Electromotor"shell" "
1"
27"
ED1027"
Motor"output"helical"gear"
1"
11"
ED1011"
Stator"
1"
28"
ED1028"
Hole"with"ring28"
1"
12"
ED1012"
Screw"M4X40"
2"
29"
ED1029"
Key4x8"
1"
13"
ED1013"
Rotor"
1"
30"
ED1030"
Bearing6001"
2"
14"
ED1014"
Screw"M5X16"
4"
31"
ED1031"
spring"washer6"
3"
15"
ED1015"
Bearing629"
1"
32"
ED1032"
Screw"M6X20"
3"
16"
ED1016"
BearingL-2090KKMTR"
1"
33"
ED1033"
Bearing"block"
1"
17"
ED1017"
Woodruff"key"
1"
34"
ED1034"
Motor"output"shaft"
1"
1 2 3 4 5 6 7 8 9 10 11 12 13 14 15 16 17 18 19 20 21
22 23 24 25 26 27 28 29 30 31 32 33 34
This manual suits for next models
5
Table of contents
Popular Power Tools manuals by other brands

Milwaukee
Milwaukee FSPE 110X Original instructions
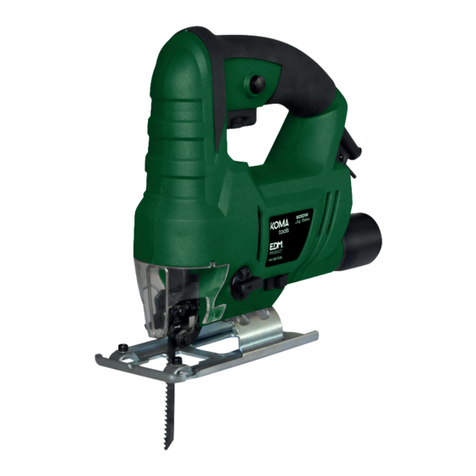
EDM Product
EDM Product 08705 instruction manual

Silverline
Silverline 430787 Original instructions
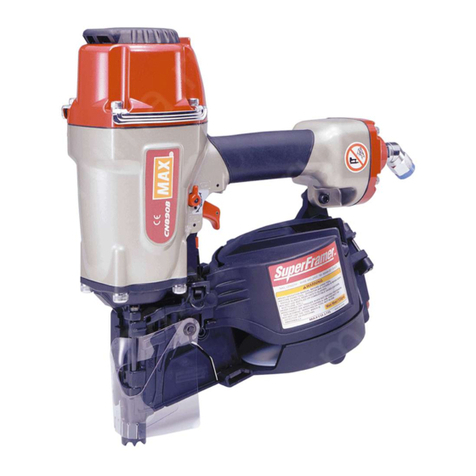
Max
Max CN890B Operating and maintenance manual
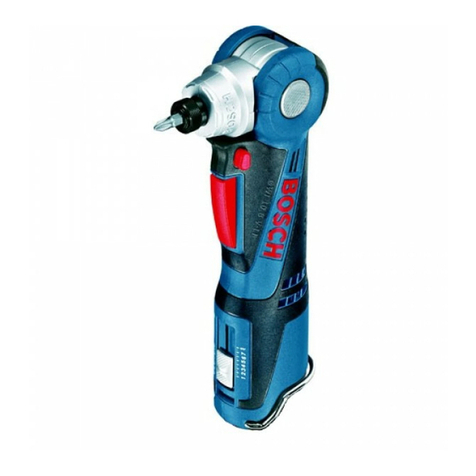
Bosch
Bosch Professional GWI 12V-5 Original instructions
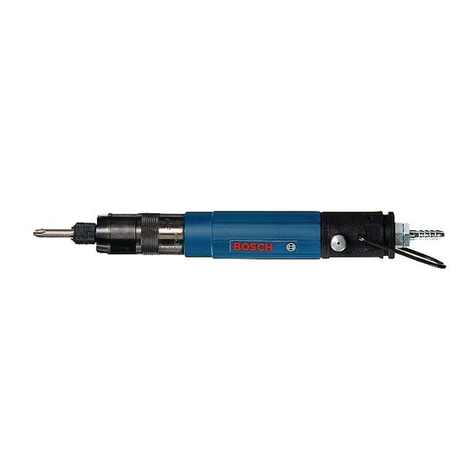
Bosch
Bosch DL 0 607 453 4 Series Original instructions