Mitek Cyber Reference manual

MiTek Machinery
Service Bulletin
MiTek
301FountainLakes Industrial Dr.
St. Charles, MO63301
Phone(800) 523-3380
Fax(636) 328-9222
www.mii.com
Product(s)
Affected Cyber®, Cyber®A/T, SmartSet®, SmartSet®Pro,
EasySet®, and CombiSet®Saws
Description Installation of a Wedge Scraper
Date 05/16/2003
SB 133
Rev —
Created by rr
Reviewed by
Approved by gm

11/1/06 1 of 5
Service Bulletin 133
Product(s)
Affected Cyber®, Cyber®A/T, SmartSet®, SmartSet®
Pro, EasySet®, and CombiSet®Saws
Description Installation of a Wedge Scraper
Date 05/15/2003
The enclosed wedge scraper assembly is to be installed on quadrant #3 of MiTek®component cutting
saws. Figures 1 and 2 show the wedge scraper mounted on a Cyber®A/T saw. This Service Bulletin pro-
vides detailed instructions on how to mount the assembly onto quadrant #3 of all MiTek component cut-
ting saws.
Table 1: Parts Provided in SB133KIT
PART # QTY PART DESCRIPTION
365115 2 Washer, Flat 1/4”
364034 2 Lock Washer, 1/4”
327153 2 Hex Head Screw, 1/4”-20x1/2”
365123 3 Washer, Flat 3/8”
364042 4 Lock Washer, 3/8”
361605 2 Hex Nut, 3/8”-16
327261 4 Hex Head Screw, 3/8”-16x1”
78833 & 34 1 Scraper and Rubber Pad (pre-assembled)
78832 1 Mounting Bracket
78835-501 2 pgs Drawings
Table 2: Supplies Needed
Measuring Tape Countersink Cutting/Tapping Fluid
Center Punch 9/16” Socket Tap Handle
1/8” Drill Rags Small Square
5/16” Drill Gloves Pencil or Fine Marker
3/8” Drill Shop Vacuum 3/8”-16 UNC
Hand (Bottom) Tap
Drill Motor Compressed Air

Service Bulletin 133
11/1/06 2 of 5
Installation Instructions
If your saw does not have a touch screen, please refer to your equipment manual to determine
how to fulfill steps #1-4 manually. If your saw does have a touch screen, you will need to be in
“Manual” mode to follow these instructions.
1. Refer to pages 1 and 2 of the attached drawing, 78835-501, for detailed illustrations of the wedge
scraper and its position on quadrant #3.
2. Move the carriage hold-down horizontally until it is approximately 30 inches away from the saw
blade. On a touch screen, do this by pressing the correct arrow button under Hold Downs until the
number reads “30”.
3. Move the carriage infeed conveyor horizontally until it is approximately 27 inches away from the
saw blade. On a touch screen, do this by pressing the correct arrow button under Infeeds until the
number reads “27”.
4. Move the centerline of Blade 3 until the reading or scale shows approximately 10 inches, so the
work area is at a comfortable height. On a touch screen, the centerline buttons are the two right
buttons under Blade 3.
Figure 1: Operator’s View of Quadrant Figure 2: View of Quadrant from the Back
Motor
Blade
Hub
Slide
Mounting
Bracket
Motor
Mount
Plate
Casting
Wedge
Scraper
Motor
Blade
Slide
Wedge Scraper
Mounting
Bracket
Saw
Blade
Brake
Casting

Service Bulletin 133
11/1/06 3 of 5
5. Adjust the angle of the saw blade on quadrant #3 (the quadrant closest to the operator’s controls) to
95º. On a touch screen, adjust the angle by pressing the left buttons under Blade 3 until the reading
reaches 95º.
6. Move quadrant #4 so it is out of the way by adjusting the blade to approximately 105º with a 15
inch centerline. On a touch screen, choose the “out of cut” position or manually adjust.
7. Turn off, lockout, and tagout all power to the saw.
a) Activate an emergency stop and disconnect all power from the saw at the main power source
to the machine. Follow all lockout and tagout procedures to ensure power is disconnected
before opening the enclosure.
b) Open the main enclosure and verify that all incoming power to the enclosure has been discon-
nected by using a voltmeter or multimeter set to read “volts”.
c) Lockout and tagout the main power switch.
8. Using a pencil or fine-point marker, mark the location of the mounting holes, as seen in Figure 3.
a) Measure 2 3/4” from the bot-
tom edge of the motor mount-
ing plate, and mark a line that is
parallel to the edge of the plate.
b) Measure 4 3/4” from the bot-
tom edge of the motor mount-
ing plate, and mark a line that is
parallel to the edge of the plate.
c) Measure 5 3/8” over from the
edge of the casting, and draw a
line parallel to the edge.
9. Use a center punch to mark the two
(2) hole locations where the vertical
line intersects with the two (2) horizontal lines. They are shown as in Figure 3.
!
CAUTION
THE BLADE MUST BE AT 95º TO AVOID HITTING
THE SLIDE OR OTHER PARTS WHEN DRILLING
THROUGH THE CASTING.
WARNING
ELECTRICAL HAZARD!
ALL ELECTRICAL WORK MUST BE PERFORMED
BY A QUALIFIED ELECTRICIAN.
FOLLOW APPROVED LOCKOUT AND TAGOUT
PROCEDURES (OSHA 29 CFR 1910.147).
Motor
Mounting
Bracket
Motor
Mount
Plate
2 3/4" 4 3/4"
(measure from
bottom edge)
5 3/8"
Wedge
Scraper
Edge of
Casting
Parallel
Figure 3: Location of Mounting Holes

Service Bulletin 133
11/1/06 4 of 5
10. Ensure that the drill will clearly miss anything located behind the casting before beginning to drill.
11. Drill a pilot hole completely through the slide with the 1/8” drill at each marked location.
12. Using the 5/16” drill, drill holes at the same two (2) locations, using the pilot holes as guides.
13. Lightly countersink the drilled holes to remove burrs and provide a lead-in for the tap and screw.
14. Tap each hole to full depth using the 3/8”-16 UNC tap.
15. Thoroughly clean both sides of the casting where the mounting holes were drilled.
a) Use a shop vacuum to remove all loose metal shavings, chips, and filings.
b) Place a rag on the operator’s side of the slide and blow compressed air into the two holes.
c) Wipe both surfaces with a clean rag to remove any remaining particles.
16. Using the two (2) 3/8”-16x1” UNC hex head screws (PN327261), check that the screws can easily
thread into the mounting holes.
17. If they do not easily thread into the holes, use the 3/8”-16 UNC tap to remove any burrs and repeat
steps #12-14.
18. Using a 9/16” socket, mount the wedge scraper assembly to the quadrant #3 casting with one
3/8”-16x1” UNC hex head screw (PN327261), a lock spring washer (PN364042), and a flat washer
(PN365123) in each hole. See Figure 4.
19. The holes in the wedge scraper bracket are slotted to allow for easy adjustment. Allow a 1/16” to 1/4”
gap between the edge of the wedge scraper and the back surface of the saw blade, and tighten the
screws firmly.
!
CAUTION
FAILURE TO REMOVE ALL METAL CHIPS AND
FILINGS FROM THE QUADRANT MAY CAUSE
DAMAGE TO THE SAW WHICH WILL RESULT IN
COSTLY AND TIME CONSUMING REPAIRS.
!
WARNING
PROPER ADJUSTMENT OF THE
WEDGE SCRAPER IS
NECESSARY TO ENSURE THE
SCRAPER DOES NOT COME INTO
CONTACT WITH THE BLADE. IF
THE BLADE HITS THE SCRAPER,
CARBIDE TEETH FROM THE
BLADE MAY BREAK LOOSE
WHICH MAY ENDANGER THE
OPERATOR.
Motor
Wedge
Scraper
1/16" to 1/4"
Gap
Blade

Service Bulletin 133
11/1/06 5 of 5
Figure 4: Wedge Scraper Assembly
20. Using the 9/16” socket, loosen the two (2) hex head 3/8”-20x1/2” bolts (PN327261) on the wedge
scraper, labeled “Bolts to Adjust Angle of Scraper” in Figure 4.
21. Adjust the angle of the scraper so that the back of the wedge scraper plate is near but not touching
the saw blade brake mechanism. See Figure 2 for the location of the brake.
22. Retighten the “Bolts to Adjust Angle of Scraper” labeled in Figure 4.
23. While wearing protective gloves, manually release the saw blade brake.
a) Take hold of the air supply hose connected to the drain cock closest to the quadrant casting.
b) Push the green ring forward while pulling back on the air supply hose.
c) Hold the air supply hose tightly to control the direction of the forced air.
24. Using your free hand, spin the blade. If the blade is touching the wedge scraper at any point, adjust
the scraper away from the blade by repeating steps #18-19.
25. Reengage the saw blade brake by inserting the air supply hose back onto the drain cock.
26. Ensure that all personnel are a safe distance from all blades, and restore power to the saw.
a) Remove the lock and tag on the main power switch in the enclosure.
b) Turn on the main power switch in the enclosure, and close the enclosure door.
c) Reconnect power at the main power source to the machine.
d) Restore power to the touch screen, if applicable.
27. During the first week of operation, inspect the blade on quadrant #3 and the wedge scraper to
ensure the wedge scraper is still in place and is not contacting the blade or brake mechanism.
Wedge
Scraper
Bolts to Adjust
Angle of Scraper
Wedge
Scraper
Mounting
Bracket
Bolts to
Mount
Assembly
Side View of Wedge Scraper Assembly Front View of Wedge Scraper Assembly
This manual suits for next models
5
Table of contents
Other Mitek Saw manuals
Popular Saw manuals by other brands

Costway
Costway ET1300US user manual

KENTMASTER
KENTMASTER BANDMASTER BM-V-LD operation, instruction, installation, maintenance and partsbook
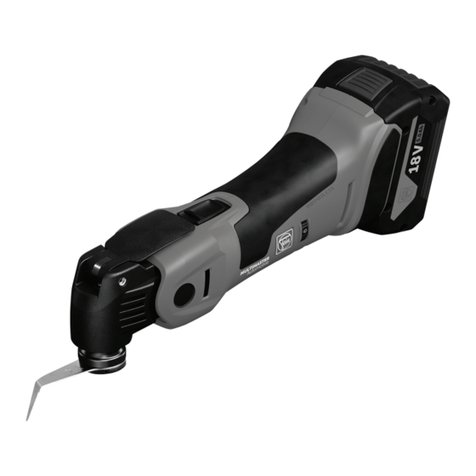
Fein
Fein AMM 700 1.7 Q AS instruction manual
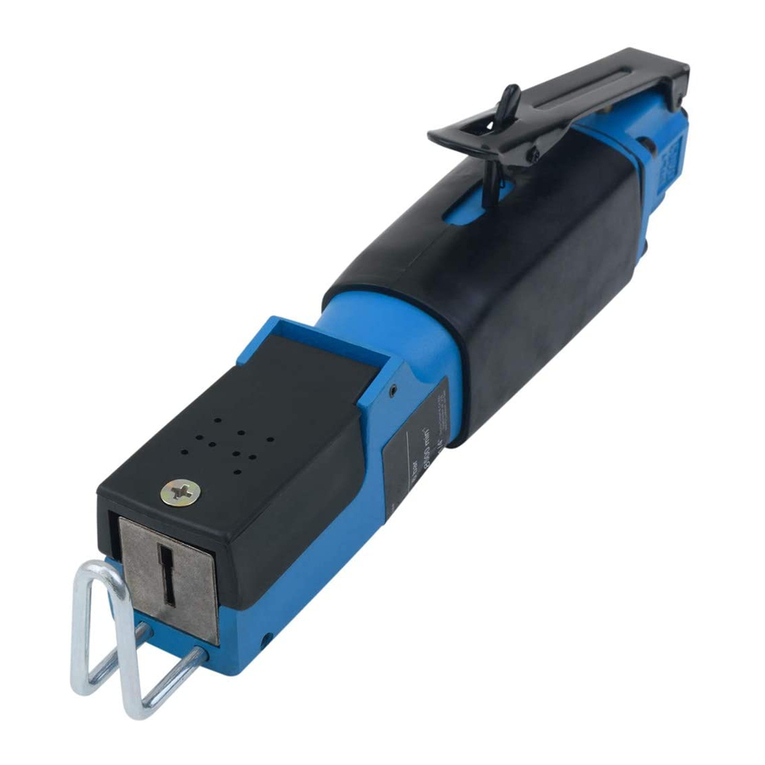
Monzana
Monzana DBDL005 instructions

Bosch
Bosch Professional TCO 2000 manual
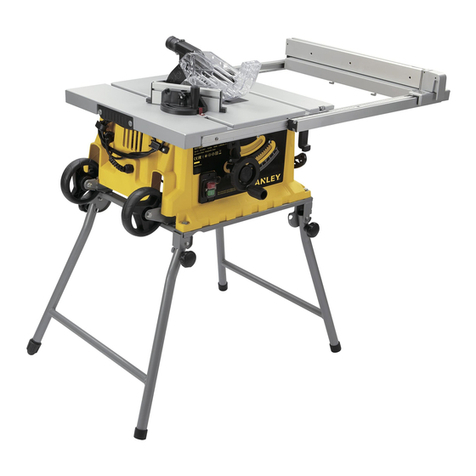
Stanley
Stanley SST1800 Original instructions