Mitek TWIN-AXIS Technical Document

COMPONENT AUTOMATION
Equipment
Manual
TWIN-AXIS™
SHEATHING SAW
001059 DRAFT
CAUTION: MiTek recommends printing this manual in high resolution using color ink. Many of the graphics
may be unclear and may create an unsafe condition if this recommendation is not followed.

COMPONENT AUTOMATION
Equipment
Manual
Part # and Rev. 001059 DRAFT
Print Date 23 February 2021
Effectivity Frame 7
Revision Date
Revised By
Orig. Release Date 02/22/2021
Created By A. McIntire
TWIN-AXIS™
SHEATHING SAW
Copyright © 2021 MiTek®.
All rights reserved.
Patented. See Legal Notice for list of patents.
Manual applies to United States equipment.

Original Instructions: 001059 DRAFT iii
Patents
Made and sold under one or more of the following patents:
Other patents pending. Other patents may apply.
U.S. 4,986,052 U.S. 5,837,014 U.S. 6,219,975
U.S. 5,385,339 U.S. 5,854,747 U.S. 6,260,263
U.S. 5,493,834 U.S. 5,873,567 U.S. 6,317,980
U.S. 5,568,862, U.S. 5,884,448 U.S. 6,389,762
U.S. 5,630,697 U.S. 5,885,731 U.S. 6,401,422
U.S. 5,636,494 U.S. 5,906,264 U.S. 6,412,246
U.S. 5,638,658 U.S. 5,934,866 U.S. 6,418,601
U.S. 5,640,832 U.S. 5,947,460 U.S. 6,539,615
U.S. 5,655,399 U.S. 5,987,828 U.S. 6,666,367
U.S. 5,678,395 U.S. 5,996,303 U.S. 6,702,269
U.S. 5,702,095 U.S. 6,048,165 U.S. 6,758,022
U.S. 5,707,204 U.S. 6,112,968 U.S. 6,817,392
U.S. 5,735,087 U.S. 6,134,775 U.S. 6,834,470
U.S. 5,810,341 U.S. 6,170,688 U.S. 6,907,820
U.S. 5,819,412 U.S. 6,205,637 Other patents may apply
U.S. 5,833,222 U.S. 6,212,849
These patents may apply to saws and infeed or outfeed equipment for saws:
U.S. 6,539,830 U.S. 6,702,096
These patents may apply to presses:
U.S. RE37,797 U.S. 6,079,325 U.S. 6,651,306
U.S. 5,454,687 U.S. 6,145,684 U.S. 6,807,903
U.S. 5,553,375 U.S. 6,330,963
U.S. 5,468,118 U.S. 6,405,916
These patents may apply to stackers: U.S. 6,969,054 B2
Legal Notice

Original Instructions: 001059 DRAFT iv
Return Goods Policy
Return goods cannot be accepted without prior authorization and are subject to a
restocking charge. The Seller certifies the articles specified herein were produced
in compliance with all provisions of the Fair Labor Standards Act of 1938, as
amended, including Section 12.—Rev. 6/98.
Corrections and Improvements
To report errors or recommend improvements to this manual, please complete the
Document Evaluation Form in the appendices. Mail or fax the form to:
MiTek Machinery Division
301 Fountain Lakes Industrial Drive
St. Charles, MO 63301
Attn: Engineering Manager, Fax: 636-328-9218
Use this page to record service bulletins and notices that you receive to keep your manual
updated.
Number Date Title
Legal Notice

Chapter 2
Original Instructions: <part # and rev> v
Safety (English) vii
Safety Indicator Signal Words . . . . . . . . . . . . . . . . . . . . . . . . . . . . . . . . . . . vii
General Safety & Equipment Rules . . . . . . . . . . . . . . . . . . . . . . . . . . . . . . . viii
Safety Rules . . . . . . . . . . . . . . . . . . . . . . . . . . . . . . . . . . . . . . . . . . . . . . . . . . . viii
General Warnings . . . . . . . . . . . . . . . . . . . . . . . . . . . . . . . . . . . . . . . . . . . . . . . . xi
E-Stop Locations . . . . . . . . . . . . . . . . . . . . . . . . . . . . . . . . . . . . . . . . . . . . . . . . . xi
Lockout/Tagout . . . . . . . . . . . . . . . . . . . . . . . . . . . . . . . . . . . . . . . . . . . . . . xii
Lockout/Tagout Guidelines . . . . . . . . . . . . . . . . . . . . . . . . . . . . . . . . . . . . . . . . xii
Electrical Lockout/Tagout Procedures. . . . . . . . . . . . . . . . . . . . . . . . . . . . . . . . xiii
Hydraulic or Pneumatic System Lockout/Tagout Procedure . . . . . . . . . . . . . . . xvi
Troubleshooting with an Energized Machine . . . . . . . . . . . . . . . . . . . . . . . xvii
Safety Tests . . . . . . . . . . . . . . . . . . . . . . . . . . . . . . . . . . . . . . . . . . . . . . . . xvii
Inspecting the Twin-Axis Sheathing Saw . . . . . . . . . . . . . . . . . . . . . . . . . . . . xvii
E-Stop Test . . . . . . . . . . . . . . . . . . . . . . . . . . . . . . . . . . . . . . . . . . . . . . . . . . . xviii
Restricted Zone . . . . . . . . . . . . . . . . . . . . . . . . . . . . . . . . . . . . . . . . . . . . . . xix
Marking the Restricted Zone . . . . . . . . . . . . . . . . . . . . . . . . . . . . . . . . . . . . . . . xix
Safety Symbol Definitions . . . . . . . . . . . . . . . . . . . . . . . . . . . . . . . . . . . . . . xx
Declaration of Safety Conformity . . . . . . . . . . . . . . . . . . . . . . . . . . . . . . . xxvii
Introduction 1
Introduction to the Manual . . . . . . . . . . . . . . . . . . . . . . . . . . . . . . . . . . . . . . . 1
Understanding the Manual . . . . . . . . . . . . . . . . . . . . . . . . . . . . . . . . . . . . . . . . . 2
Additional Resources . . . . . . . . . . . . . . . . . . . . . . . . . . . . . . . . . . . . . . . . . . . 3
Website . . . . . . . . . . . . . . . . . . . . . . . . . . . . . . . . . . . . . . . . . . . . . . . . . . . . . . . . 3
Contact Us. . . . . . . . . . . . . . . . . . . . . . . . . . . . . . . . . . . . . . . . . . . . . . . . . . . . . . 3
General Information 4
Introduction to the Equipment . . . . . . . . . . . . . . . . . . . . . . . . . . . . . . . . . . . . 4
Purpose of the Equipment . . . . . . . . . . . . . . . . . . . . . . . . . . . . . . . . . . . . . . . . . . 4
Description of the Equipment . . . . . . . . . . . . . . . . . . . . . . . . . . . . . . . . . . . . . . . 4
Safety Compliance of the Equipment . . . . . . . . . . . . . . . . . . . . . . . . . . . . . . . . . 4
Main Components . . . . . . . . . . . . . . . . . . . . . . . . . . . . . . . . . . . . . . . . . . . . . . . . 5
Graphical Overview . . . . . . . . . . . . . . . . . . . . . . . . . . . . . . . . . . . . . . . . . . . . . . . 5
Main Component Descriptions . . . . . . . . . . . . . . . . . . . . . . . . . . . . . . . . . . . . . . 5
Technical Specifications. . . . . . . . . . . . . . . . . . . . . . . . . . . . . . . . . . . . . . . . . 6
Operation 8
Safety Operating Notes . . . . . . . . . . . . . . . . . . . . . . . . . . . . . . . . . . . . . . . . . 8
Safety-Related Operating Procedures . . . . . . . . . . . . . . . . . . . . . . . . . . . . . . 9
Stopping Methods . . . . . . . . . . . . . . . . . . . . . . . . . . . . . . . . . . . . . . . . . . . . . . . . 9
Interlocked Doors or Guards . . . . . . . . . . . . . . . . . . . . . . . . . . . . . . . . . . . . . . . 11
Operational Indicators on the Machine . . . . . . . . . . . . . . . . . . . . . . . . . . . . . . . 12
Operator Hardware Controls . . . . . . . . . . . . . . . . . . . . . . . . . . . . . . . . . . . . 13
Operating the Machine or System . . . . . . . . . . . . . . . . . . . . . . . . . . . . . . . . 14
Powering Up or Down . . . . . . . . . . . . . . . . . . . . . . . . . . . . . . . . . . . . . . . . . . . . 14
Software Overview . . . . . . . . . . . . . . . . . . . . . . . . . . . . . . . . . . . . . . . . . . . . . . 15
Table of Contents

Original Instructions: <part # and rev> vi
<machine name only>: <chapter title>
Using the Toolbar . . . . . . . . . . . . . . . . . . . . . . . . . . . . . . . . . . . . . . . . . . . . . . . 16
Using the Status Menu . . . . . . . . . . . . . . . . . . . . . . . . . . . . . . . . . . . . . . . . . . . 17
Operating Modes . . . . . . . . . . . . . . . . . . . . . . . . . . . . . . . . . . . . . . . . . . . . . 18
Using Semi Auto Mode . . . . . . . . . . . . . . . . . . . . . . . . . . . . . . . . . . . . . . . . . . . 18
Using Auto Mode . . . . . . . . . . . . . . . . . . . . . . . . . . . . . . . . . . . . . . . . . . . . . . . . 19
Options Menu Overview . . . . . . . . . . . . . . . . . . . . . . . . . . . . . . . . . . . . . . . . . . 20
Software Tips. . . . . . . . . . . . . . . . . . . . . . . . . . . . . . . . . . . . . . . . . . . . . . . . . . . 21
Additional Operating Procedures . . . . . . . . . . . . . . . . . . . . . . . . . . . . . . . . . 21
Restart After E-Stop Procedure. . . . . . . . . . . . . . . . . . . . . . . . . . . . . . . . . . . . . 21
Maintenance 23
Introduction to Maintaining Your Machine . . . . . . . . . . . . . . . . . . . . . . . . . . 23
Overview Graphics. . . . . . . . . . . . . . . . . . . . . . . . . . . . . . . . . . . . . . . . . . . . 24
Cleaning and Inspecting. . . . . . . . . . . . . . . . . . . . . . . . . . . . . . . . . . . . . . . . 24
Cleaning . . . . . . . . . . . . . . . . . . . . . . . . . . . . . . . . . . . . . . . . . . . . . . . . . . . . . . 24
Inspecting . . . . . . . . . . . . . . . . . . . . . . . . . . . . . . . . . . . . . . . . . . . . . . . . . . . . . 25
Calibrating . . . . . . . . . . . . . . . . . . . . . . . . . . . . . . . . . . . . . . . . . . . . . . . . . . 25
Lubricating . . . . . . . . . . . . . . . . . . . . . . . . . . . . . . . . . . . . . . . . . . . . . . . . . . 25
Motors and Gearboxes. . . . . . . . . . . . . . . . . . . . . . . . . . . . . . . . . . . . . . . . . 26
Saw Blades . . . . . . . . . . . . . . . . . . . . . . . . . . . . . . . . . . . . . . . . . . . . . . . . . 28
Direction of Blade Teeth . . . . . . . . . . . . . . . . . . . . . . . . . . . . . . . . . . . . . . . . . . 28
Specs for New or Used Saw Blades . . . . . . . . . . . . . . . . . . . . . . . . . . . . . . . . . 28
When to Replace the Saw Blades . . . . . . . . . . . . . . . . . . . . . . . . . . . . . . . . . . . 28
Replacing a Saw Blade . . . . . . . . . . . . . . . . . . . . . . . . . . . . . . . . . . . . . . . . . . . 28
Bearings . . . . . . . . . . . . . . . . . . . . . . . . . . . . . . . . . . . . . . . . . . . . . . . . . . . . 30
Carriage Bearings . . . . . . . . . . . . . . . . . . . . . . . . . . . . . . . . . . . . . . . . . . . . . . . 30
Aligner Bearings . . . . . . . . . . . . . . . . . . . . . . . . . . . . . . . . . . . . . . . . . . . . . . . . 30
Applying Bearing Lubricant . . . . . . . . . . . . . . . . . . . . . . . . . . . . . . . . . . . . . . . . 31
Chains . . . . . . . . . . . . . . . . . . . . . . . . . . . . . . . . . . . . . . . . . . . . . . . . . . . . . 31
Lubricating Chains. . . . . . . . . . . . . . . . . . . . . . . . . . . . . . . . . . . . . . . . . . . . . . . 31
Adjusting Chain Tension . . . . . . . . . . . . . . . . . . . . . . . . . . . . . . . . . . . . . . . . . . 32
Pneumatic System . . . . . . . . . . . . . . . . . . . . . . . . . . . . . . . . . . . . . . . . . . . . 34
Removing Pressure from the Pneumatic System . . . . . . . . . . . . . . . . . . . . . . . 34
Maintaining the Filter / Regulator. . . . . . . . . . . . . . . . . . . . . . . . . . . . . . . . . . . . 34
Cylinders . . . . . . . . . . . . . . . . . . . . . . . . . . . . . . . . . . . . . . . . . . . . . . . . . . . . . . 36
Electrical System . . . . . . . . . . . . . . . . . . . . . . . . . . . . . . . . . . . . . . . . . . . . . 38
Electrical Enclosure . . . . . . . . . . . . . . . . . . . . . . . . . . . . . . . . . . . . . . . . . . . . . . 38
Sensors . . . . . . . . . . . . . . . . . . . . . . . . . . . . . . . . . . . . . . . . . . . . . . . . . . . . . . . 38
VFD (Variable Frequency Drive) . . . . . . . . . . . . . . . . . . . . . . . . . . . . . . . . . . . . 40
Safety Controller . . . . . . . . . . . . . . . . . . . . . . . . . . . . . . . . . . . . . . . . . . . . . . . . 41
PLC (Programmable Logic Controller . . . . . . . . . . . . . . . . . . . . . . . . . . . . . . . . 41
Other Maintenance. . . . . . . . . . . . . . . . . . . . . . . . . . . . . . . . . . . . . . . . . . . . 42
Roller Brushes . . . . . . . . . . . . . . . . . . . . . . . . . . . . . . . . . . . . . . . . . . . . . . . . . . 42
Dust Removal . . . . . . . . . . . . . . . . . . . . . . . . . . . . . . . . . . . . . . . . . . . . . . . . . . 43
Glossary 44

Chapter 1
Original Instructions: 001059 DRAFT vii
Safety Indicator Signal Words
The following signal words and colors are used throughout this document to
indicate safety hazards. Pay careful attention when you see them. The level of
severity differs for each signal word and color.
Signal words are accompanied by graphics showing what personnel should or
should not do. The graphics are called safety symbols and are defined starting on
page xx, but more specific text is provided every time a graphic is used throughout
the manual. Everyone near the machine must be trained on how to read these
safety indicators.
Failure to comply with the instructions accompanying each signal word may result
in property damage, personal injury, or even death. Personnel must follow all
safety procedures and practices to ensure the safest possible operation of this
equipment. However, at no time is this document a substitute for common sense.
Personnel must ensure that the work environment is safe and free of distractions.
Danger Indicates an imminently hazardous situation which, if not avoided, is
likely to result in death or serious injury.
Warning Indicates a potentially hazardous situation, which, if not avoided,
may result in death or serious injury.
Caution Indicates a potentially hazardous situation which, if not avoided,
may result in minor or moderate injury.
Notice Calls attention to information that is significant to understanding the
operation at hand or the potential for property damage.
Environmental Applies to conditions that may affect the environment but do not
have an immediate, direct effect on personnel or equipment.
Signal words are used in conjunction with safety symbols
to give hazard messages throughout this manual.
Common safety symbols are defined starting on page 12.
Safety (English)

Original Instructions: 001059 DRAFT viii
Twin-Axis Sheathing Saw: Safety
General Safety & Equipment Rules
Because it is impossible to anticipate every circumstance that might involve a
hazard, the safety information provided in this equipment manual and on the
machine is not all-inclusive. If this machine is operated or serviced using a
procedure not specifically recommended by the manufacturer, the procedure shall
be approved by a professional engineer to ensure it will not render the equipment
unsafe. Use extreme caution and common sense at all times.
Safety Rules
Know Your Equipment
• Read this manual completely before using or maintaining the equipment. Do
not operate this machine unless you have a thorough knowledge of the
controls, safety devices, emergency stops, and operating procedures
outlined in this manual.
• Read and follow all safety notes. Failure to comply with these instructions
may result in economic loss, property damage, and/or personal injury
including death.
• Refer to the lockout/tagout guidelines on the following pages to safely
perform maintenance and troubleshooting of this equipment.
• Observe and obey all safety labels. Replace worn labels immediately.
• Use this equipment solely for the purpose described in this manual.
• Only qualified personnel should attempt to operate or perform maintenance
on this equipment. “Qualified personnel” is defined as:
...a person or persons who, by possession of a recognized degree or certificate of
professional training, or who, by extensive knowledge, training, or experience,
has successfully demonstrated the ability to solve problems relating to the subject
matter and work—ANSI B30.2-1983
...one who has skills and knowledge related to the construction and operation of
the electrical equipment and installations and has received safety training on the
hazards involved—NEC 2002 Handbook
Personal Safety
• Always wear safety glasses and hearing protection in an industrial
environment.
• Utilize a filtering face piece (dust mask) when working near sawdust.
• Wear proper clothing and appropriate personal protective equipment (e.g.,
safety glasses and hearing protection.) Do not wear loose clothing or
jewelry. Confine long hair by tying it back.
• Use caution when lifting heavy parts or material.

Original Instructions: 001059 DRAFT ix
Twin-Axis Sheathing Saw: Safety
Installing the Equipment
• Follow installation instructions completely.
• Use proper lifting equipment rated for the proper weight.
• This equipment is not for use in a residential area.
Keeping a Safe Environment
• Pay attention to your surroundings.
• Keep children away. All visitors should be kept a safe distance from the
work area. Hazards may not be apparent to individuals unfamiliar with the
machine.
• Keep work areas well lit.
• Keep the work area clean and free of any trip or slip hazards.
• Do not use the equipment in damp or wet locations, or expose it to rain or
snow.
• Minimize dust clouds and protect your equipment by cleaning dust in this
manner:
a) Shut down electrical power and sources of ignition
b) Vacuum dust prior to blowing with air
c) Powered cleaning equipment such as vacuums must be consistent
with local governmental codes for use in dusty conditions.
Operating and Maintaining the Equipment
• Ensure that all people, tools, and foreign objects are clear of the restricted
zones before operating this equipment. The restricted zones are shown
on page xix.
• Perform safety tests to ensure all E-stops are working properly before
operating the equipment at the initial startup, after performing any
maintenance, and in accordance with the maintenance schedule.
• Always push an E-stop button before approaching a machine for any
reason. An E-stop may cause components to move without warning.
• Only use procedures described in this manual. Any other procedures should
be discussed with MiTek to verify it is done safely. For topics not covered in
this manual or online, contact MiTek for advice.
• In case of machine malfunction, stop the machine immediately using an E-
stop, lockout/tagout, and report the malfunction to a supervisor.
NOTICE
Never use compressed air inside an electrical enclosure. It
may force contaminants into electrical connections.
Use a vacuum to remove dust from electrical enclosures.
Canned air is acceptable after vacuuming.

Original Instructions: 001059 DRAFT x
Twin-Axis Sheathing Saw: Safety
• Never leave the machine running unattended. Turn the power off! Do not
leave the machine until all parts have come to a complete stop and all
electrical power has been shut off.
• Check for worn or damaged parts regularly. Repair or replace them
immediately.
• Only use exact replacement parts specified. Using unapproved parts may
void the warranty and can be a safety risk.
• Keep the hydraulic, pneumatic, and electrical systems in good working
order at all times. Repair leaks and loose connections immediately. Never
exceed the recommended pressure or electrical power.
• Check that all guards and safety devices are in place and in working order
before each shift starts. All protective guards and safety devices must be in
place before and during use of the machine. Never disconnect or bypass
any safety device or electrical interlock.
• Torque bolts and fasteners to the specifications given by MiTek. If no torque
specification is given, use industry standards.
• Only qualified maintenance personnel shall make adjustments or remove,
repair, or install safety devices. Only qualified electricians should perform
electrical work.
• Periodically inspect the quality of the finished product.
• Document all preventive and repair maintenance over the life of the
machine to improve machine efficiency and reduce the risk of accidents.
Electrical Safety Notes
• Do not use any liquids in the interior of electrical cabinets.
• When using solvents on and around the machine, remove power to the
machine to eliminate the chance of sparking, resulting in explosion or fire.
Wear a respirator approved for use with solvents.

Original Instructions: 001059 DRAFT xi
Twin-Axis Sheathing Saw: Safety
General Warnings
E-Stop Locations
Refer to Emergency Stops (Hardware) on page 10 for location of E-stops.
!WARNING
HIGH VOLTAGE ELECTRICITY!
May cause serious personal injury or death. Ensure only qualified
electricians perform electrical service work.
!WARNING
Read the equipment manual, safety labels, and all safety information
provided before operating or maintaining this equipment.
!WARNING
CRUSH OR CUT HAZARD
Guards must always be in place during operation to avoid serious
injury and possibly death.
Always replace guards after completing maintenance and before
removing the lockout/tagout device.
!WARNING
Many components are manufactured from high carbon, heat-treated
steel. Do not attempt to straighten, bend, or weld these components,
as they may fail under load causing serious personal injury or death.

Original Instructions: 001059 DRAFT xii
Twin-Axis Sheathing Saw: Safety
Lockout/Tagout
Lockout/Tagout Guidelines
Lockout/tagout all energized systems before performing maintenance on them.
All lockout/tagout guidelines must be met according to OSHA 29 CFR
1910.147. A specific procedure should be included in your company’s energy
control program. This manual is not intended to replace your company’s de-
energizing or lockout/tagout procedure required by OSHA, but merely to provide
general guidance.
The term “lockout,” as used in this manual, means placing a lockout device, such
as a keyed padlock, on any and all energy sources to ensure that the energy
isolating device and the equipment being controlled cannot be re-energized or
operated until the lockout device is removed. The photos on page xiii show where
the electrical disconnects are located for this machine.
• Energy sources include electrical, mechanical, hydraulic, pneumatic,
chemical, thermal, or other energy.
• In the case of electrical energy sources, the main power and control power
to the machinery must be turned off and physically locked in the Off position.
• Before performing maintenance on the pneumatic or hydraulic systems,
bleed the lines prior to lockout/tagout to eliminate pressure.
If more than one person is working in a restricted zone, use a group lockout
device that will allow each person to use a lock that can be removed only by the
person performing the maintenance.
“Tagout” means that a prominent warning is securely fastened to an energy-
isolating device to indicate that the equipment shall not be operated.
Whenever you see this symbol, lockout/tagout!

Original Instructions: 001059 DRAFT xiii
Twin-Axis Sheathing Saw: Safety
Electrical Lockout/Tagout Procedures
Working on a Machine Outside the Machine’s Main Electrical Enclosure
Before performing maintenance on any machine with electrical power, lockout/
tagout the machine properly. When working on a machine outside of the
machine’s main electrical enclosure, not including work on the electrical
transmission line to the machine, follow your company’s approved lockout/tagout
procedures which should include, but are not limited to the steps here.
1. Engage an E-stop on the machine.
2. Turn the disconnect switch handle to the Off position. See Figure 1-1.
Figure 1-1: Disconnect Switch in Off Position
3. Attach a lock and tag that meet OSHA requirements for lockout/tagout.
See Figure 1-2.
4. Restrain or de-energize all pneumatic components, hydraulic components,
and other parts that could have live or stored power.
If you are working on the electrical transmission line to the
machine, follow the procedure on page xv.
!WARNING
ELECTROCUTION HAZARD.
When the disconnect switch is off, there is still live power within
the disconnect switch’s enclosure. Always turn off the power at
the building’s power source to the equipment before opening this
electrical enclosure.

Original Instructions: 001059 DRAFT xiv
Twin-Axis Sheathing Saw: Safety
Figure 1-2: Sample of a Lockout/Tagout Mechanism on an Electrical Enclosure

Original Instructions: 001059 DRAFT xv
Twin-Axis Sheathing Saw: Safety
Working on a Machine Inside the Machine’s Main Electrical Enclosure or
in the Electrical Transmission Line to the Machine
Before opening the main electrical enclosure, or attempting to repair or
replace an electrical transmission line to the machine, lockout/tagout the
machine properly. Follow your company’s approved lockout/tagout procedures
which should include, but are not limited to the steps here.
1. Engage an E-stop on the
machine.
2. Shut the power to the
machine off at the
machine’s power source
which is usually an electrical
service entry panel on the
facility wall. One example of
a locked-out power source
panel is shown in Figure 1-
3.
3. Attach a lock and tag that
meets OSHA requirements
for lockout/tagout.
4. Open the door to the
enclosure in which you need
access, and using a
multimeter, verify that the
power is off.
Figure 1-3: Sample of a Lockout/
Tagout Mechanism on a Power
Source Panel

Original Instructions: 001059 DRAFT xvi
Twin-Axis Sheathing Saw: Safety
Hydraulic or Pneumatic System Lockout/Tagout Procedure
Before working on or near hydraulic or pneumatic components, bleed the lines of
pressure. See Removing Pressure from the Pneumatic System for further
instruction.
When Lockout/Tagout Is Not Required
If working on components other than the hydraulic or pneumatic system, but that
requires you to be near the vicinity of movable hydraulic or pneumatic
components, you must, at a minimum, physically restrain those components from
moving. If this is not possible, lockout/tagout the entire hydraulic or pneumatic
system.
When Lockout/Tagout Is Required
Before attempting repair or performing maintenance on a hydraulic or pneumatic
line or component, lockout/tagout the machine properly. Follow your company’s
approved lockout/tagout procedures.
Figure 1-4: How to Lockout/Tagout the Pneumatic System-
Figure 1-5: Sample of a Lockout/Tagout on a Pneumatic System
On
Position
Off
Position
Push Blue Tab Out
for Lockout/Tagout

Original Instructions: 001059 DRAFT xvii
Twin-Axis Sheathing Saw: Safety
Troubleshooting with an Energized Machine
Only a qualified electrician, using the personal protective equipment and following
the procedures recommended in NFPA 70E should ever attempt service or repair
of or near an energized area or component of the machine.
Whenever maintenance is performed while the equipment is electrically
energized, there is a potential electric arc flash hazard. Refer to NFPA 70E for the
personal protective equipment required when working with electrically energized
components. Pneumatic and hydraulic components may move unexpectedly if not
de-energized. Physically restrain any components capable of movement when
working on or near those components.
Safety Tests
This test procedure MUST be performed by qualified personnel at startup and
after ANY maintenance, adjustment, or modification. Testing ensures that the
safety system and machine control system work together to stop the machine
properly.
Inspecting the Twin-Axis Sheathing Saw
1. Lockout/tagout the machine.
2. Check the Twin-Axis Sheathing Saw for debris or tools that would block
the path of parts. Remove any that you may find. The following locations
are especially important:
• Infeed conveyor and aligner
• Outfeed conveyor and ejectors
• Saw chamber
3. Check the physical condition of the Twin-Axis Sheathing Saw. The
following are especially important:
• Both the cross-cut and the rip saw blades should be in the home
position
• The infeed aligner and the outfeed ejector should be in a retracted
position
• The conveyor chain should be on the guide and properly tensioned
• The carriage chains (2) should be on the guides and properly tensioned
4. Remove lockout/tagout and return electrical power and pneumatic
pressure to the machine.
5. Press the blue Reset button. Verify the machine has power by checking if
E-stops are illuminated green.
6. The filter / regulator gauge should match the pressure recommendation
specified in Maintaining the Filter / Regulator on page 34.
7. Verify all doors are closed and locked.

Original Instructions: 001059 DRAFT xviii
Twin-Axis Sheathing Saw: Safety
E-Stop Test
1. Verify there is no material on the infeed end of the saw or inside the saw
chamber.
2. Initiate a cut cycle in Semi Auto mode. The conveyors and the saw blades
will begin to rotate.
3. Actuate an E-stop. Verify that the following happens when the pushbutton
is depressed:
• the conveyors and the saw blades stop moving
• the active E-stop should blink red
• all other illuminated E-stops should turn solid red
4. Twist the E-stop to release it.
5. Press the blue Reset button.
6. Start operation.

Original Instructions: 001059 DRAFT xix
Twin-Axis Sheathing Saw: Safety
Restricted Zone
Figure 1-6: Know the Restricted Zone
Marking the Restricted Zone
The restricted zone must be marked so everyone near the equipment can clearly
see the area where danger may exist.
!DANGER
Stay out of the restricted zone when equipment is in use. Serious
injury or death may result if personnel are in the restricted zone.
Always look for personnel in the restricted zone before operating
equipment.
Infeed
Conveyor
Saw
Chamber
Outfeed
Conveyor

Original Instructions: 001059 DRAFT xx
Twin-Axis Sheathing Saw: Safety
Safety Symbol Definitions
The safety symbols shown in this section are found throughout the manual to
indicate hazards related to this machine. All personnel expected to operate or
maintain this machine should be familiar with these safety symbols and their
meanings.
User caution. It indicates a condition where equipment damage
resulting in injury could occur if operational procedures are not
followed. To reduce risk of damage or injury, refer to accompanying
documents, and follow all steps or procedures as instructed.
Electrical hazard. It indicates dangerous high voltages inside of an
enclosure and/or the presence of a power source. To reduce the risk
of fire or electric shock, do not attempt to open the enclosure or gain
access to areas where you are not instructed to do so. Refer
servicing to qualified service personnel only.
This equipment should be operated only from the type of source
indicated on the manufacturer’s identification label. Installation
should be in compliance with applicable sections of the national
electric code. Consult your local building code before installing.
Crush hazard. Keep hands and other body parts clear.
Noise hazard. Equipment produces loud noise in excess of 100 DBA
during operation. Use appropriate PPE to protect hearing when in
the vicinity of this equipment.
Table of contents
Other Mitek Saw manuals
Popular Saw manuals by other brands

Costway
Costway ET1300US user manual

KENTMASTER
KENTMASTER BANDMASTER BM-V-LD operation, instruction, installation, maintenance and partsbook
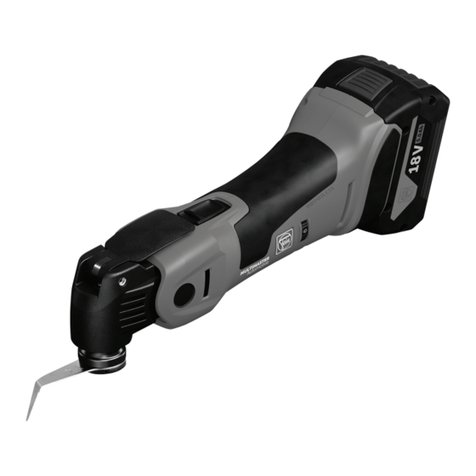
Fein
Fein AMM 700 1.7 Q AS instruction manual
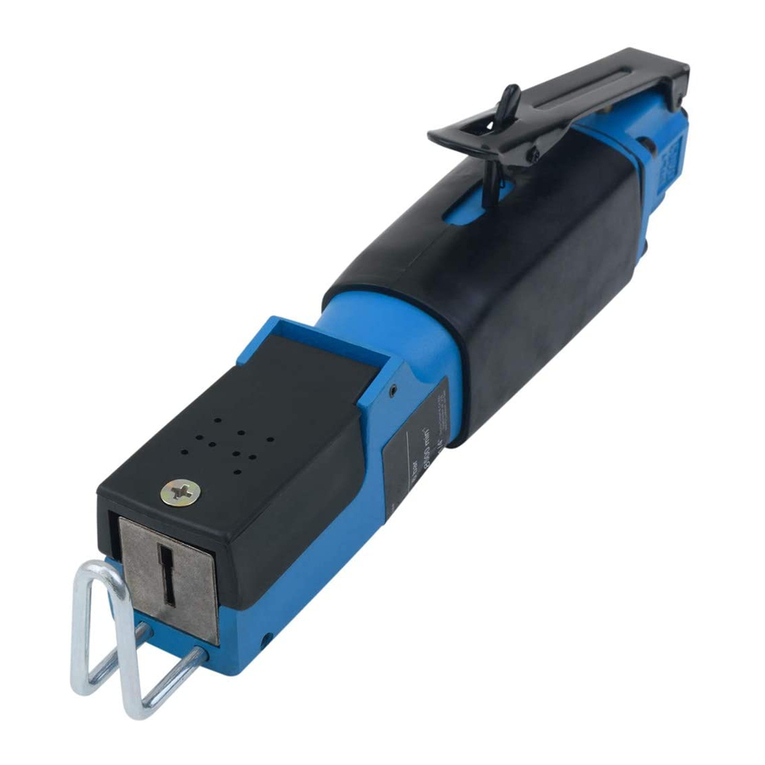
Monzana
Monzana DBDL005 instructions

Bosch
Bosch Professional TCO 2000 manual
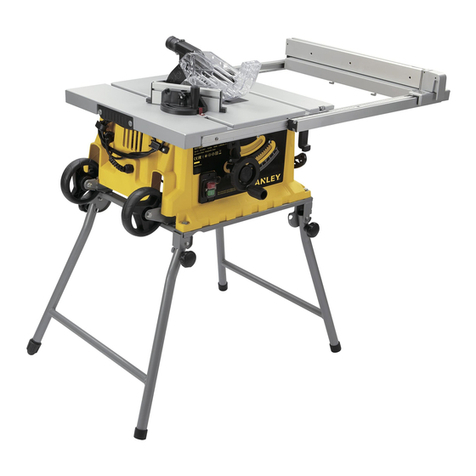
Stanley
Stanley SST1800 Original instructions