Miyachi AX5000 Quick start guide

0 Document #107-00092-001 Dec, 2013
MIYACHI AMERICA CORPORATION
The World Leader in Hermetic Sealing Systems
A 5000
Operational
Manual

Document #107-00092-001 1
AX5000 Operational Manual
Miyachi America Corporation
1820 S. Myrtle Ave
Monrovia, CA 91017
Phone 626.303.5676 • Fax 626.359.7930
R E V I S I O N R E C O R D
Rev E O Date Basis of Revision
001
None
December
2010
None. Original edition.
002
None
March 2011
Add possible faulty component to
Error Table
003
None
November 2011
Add new
graphics
00
4
None
D
ecember
201
3
Update
c
omp
any name

Document #107-00092-001 2
FOREWORD
The purpose of this manual is to supply operating, maintenance and service personnel with the
information needed to operate the Miyachi America A 5000 gloveboxes.
Should questions arise, or if you have suggestions for improving this manual, please contact:
Miyachi America Corporation
1820 S. Myrtle Ave
Monrovia, CA 91017
Phone 626.303.5676 • Fax 626.359.7930
NOTI E
Miyachi America may be released from all
warranty obligations if repairs or modifications
are made by persons other than its own service
personnel, or its authorized representatives,
unless such repairs or modifications are
specifically authorized in writing by Miyachi
America orporation.

Document #107-00092-001 3
Table of ontents
GETTING STARTED WITH THE GLOVEBOX........................................................ 4
POWERING UP THE GLOVEBOX..................................................................................................... 4
POWERING DOWN THE GLOVEBOX............................................................................................. 4
RUNNING THE GLOVEBOX........................................................................................ 4
START THE GLOVEBOX APPLICATION ....................................................................................... 4
LOG IN USING YOUR ASSIGNED USERNAME AND PASSWORD............................................ 4
GLOVEBOX STATUS WINDOW INFORMATION ......................................................................... 5
RUN AN OVEN SCHEDULE................................................................................................................ 6
CREATE AND EDIT AN OVEN SCHEDULE.................................................................................... 7
EDITING AND CREATING OVEN SCHEDULE.............................................................................. 8
ADD A NEW SEGMENT................................................................................................................................................................10
EDIT AN EXISTING SEGMENT .................................................................................................................................................11
DELETE AN EXISTING SEGMENT...........................................................................................................................................11
CREATE A NEW SCHEDULE........................................................................................................... 12
DELETE AN EXISTING OVEN SCHEDULE.................................................................................. 12
CREATE AND EDIT A PUMP DOWN SCHEDULE....................................................................... 13
CREATE A NEW PUMP DOWN SCHEDULE..........................................................................................................................13
EDIT AN EXISTING PUMP DOWN SCHEDULE....................................................................................................................14
DELETE AN EXISTING PUMP DOWN SCHEDULE.............................................................................................................14
ENVIRONMENT SETTINGS....................................................................................... 15
ENVIRONMENT PRESSURE SETTINGS ....................................................................................... 15
MOISTURE SETTINGS...................................................................................................................... 16
OXYGEN SETTINGS .......................................................................................................................... 16
HELIUM SETTINGS........................................................................................................................... 17
CHAMBER SETTINGS................................................................................................. 17
GRAPHICAL DATA DISPLAY................................................................................... 18
VIEW REAL TIME GRAPH DATA .................................................................................................. 18
VIEW HISTORY GRAPH DATA....................................................................................................... 19
EXPORT TO CSV FORMAT.............................................................................................................. 19
BATCH REPORT........................................................................................................... 20
BATCH REPORT................................................................................................................................. 20
BATCH SETTING................................................................................................................................ 21
VERSION ........................................................................................................................ 21
USING THE LOGIN ADMINISTRATOR (PASSWORD ADMINISTRATION) .. 22
ADD USER ............................................................................................................................................ 23
EDIT USER ........................................................................................................................................... 24
CHANGE USER (TO SIGN-ON TO A DIFFERENT USER ID)..................................................... 25
DELETE USER..................................................................................................................................... 26
GLOVEBOX CONFIGURATOR................................................................................. 27
CREATE A NEW CHAMBER............................................................................................................ 28
REMOVE AN EXISTING CHAMBER.............................................................................................. 28
ERROR TABLE.............................................................................................................. 29
DIGITAL AND ANALOG I/O...................................................................................... 32
DIGITAL AND ANALOG I/O GALIL DMC SMART TERMINAL DISPLAY
DATA RECORD SCREEN............................................................................................ 34

Document #107-00092-001 4
Getting Started with the GLOVEBOX
Powering up the GLOVEBOX
Verify the electrical service input requirements are met, and all power
connections are plugged in.
Verify the proper line pressures for all gases are correct and that all tube
connections are tight.
Check to see that the power connection is made.
Verify that all component circuit breakers are in the “OFF” position, and proceed
to energize the system by turning on the “CB1” main circuit breaker. Then turn
on all the remaining component circuit breakers.
Next turn on the computer power and log on to the system.
Powering down the GLOVEBOX
Stop all oven cycles.
Close down the Windows application software. Shut down the computer. Wait
for the computer to shut down.
De-energize the system by turning off the “CB1” main circuit breaker.
Next turn on the computer power and log on to the system.
Running the GLOVEBOX
Start the GLOVEBOX application
Double-click the GloveBox icon on the desktop to start up the GLOVEBO user interface. The
Login Window will be presented (see
Figure 1 Login Screen
).
Log in using your assigned username and password.
Different user groups have different levels of access to the GLOVEBO system. The
administrator users can access all the GLOVEBO functions, whereas the operator users only
have access to very limited functions. The system is configured on shipment with a single
administrator account with user name of “admin”. Other user names can be added by starting the
GloveBox software and logging on to the system using this user name and the associated
password. The details are explained in the log on section.

Document #107-00092-001 5
Figure 1 Login Screen
GloveBox Status Window nformation
After entering a valid User Name and Password, the GLOVEBO application establish
communication with the system’s controller, which monitors and controls all GloveBox status.
Then it tries to turn on the oven temperature controllers and puts them in the standby mode.
The main Glovebox display window will be presented which has five pull down menu choices:
File, Logon, Glovebox, Batch and Help (see Figure 2).
The oven temperatures, oven vacuum pressures, enclosure pressure, moisture, Oxygen and
Helium levels are displayed on this window. If the communications with the Galil controller and
the oven temperature controllers are established successfully, these parameters are updated
dynamically.
In addition, the environment enclosure purging status (on or off), the left and right chamber
working statuses (Pumping Down, Backfilling or Standby), the chamber cleanness status (clean or
need pump down) and the inner/outer door statuses (open or close) are also updated dynamically
on this window.
At the bottom of this status window, there are four square-shaped alarms designed to alert the
operator of any unfavorable moisture, oxygen, helium and process conditions of the enclosure.
Under normal conditions, the color of these alarms is green. If any one of these four parameters
goes beyond the preset safe limits, the color of the corresponding alarm turns red.

Document #107-00092-001 6
Figure 2 GLOVEBO Main window and the GloveBox Status window.
At the upper center of the GloveBox status window is information on GloveBox
activities, controls and errors. f none of these are present or happening, this area
of the window is blank.
For each chamber, the status of the outer door and inner door is shown. If the outer door lock is
engaged, a closed lock icon is shown to the left of the graphical pressure level. If the outer door
lock is disengaged, the lock icon is open. If the inner door is closed, a graphical line is in the lower
position to the right of the graphical pressure level. If the inner door is not closed, then the
graphical line is above the lower position.
Run an oven Schedule
When the GLOVEBO program is started, as mentioned previously, the oven temperature
controllers are turned on and are put in the standby mode. The left or right oven can be started by
first selecting an oven schedule and then click the corresponding Start Oven button. To select an
oven schedule for the left or right oven, click the drop down list box under the Label “Left Oven
Schedule” or “Right Oven Schedule” and then highlight the schedule you would like to use. The

Document #107-00092-001 7
selected oven schedule will become active. If batch report is not active, the oven will start
immediately after the Start Oven button is pressed. If batch report is active, the user will be
promped to enter the operator name and batch id.
As soon as the oven is started, the text for the Start Oven button changes to Stop Oven. The
current segment number in the schedule and the time remaining for that segment are displayed in
the corresponding text boxes under the Stop Oven button.
An oven schedule is a series of programmed steps that complete an entire vacuum bake-out
process.
For a wall heated oven, there are four temperatures displayed just under the label “Left Oven
Temperatures” or “Right Oven Temperatures” for the left or right oven, each representing the
temperature of side (left or right), top, bottom and rear walls of the oven. The temperatures are
updated every second.
The oven stops when the oven schedule is done or when the Stop Oven button is pressed. The
text of the Stop Oven button changes back to “Start Oven” after the oven stops.
If the user presses the Start Oven Button when the selected oven schedule is empty, a message
will be issued telling the operator that the schedule is empty and ask the operator to select a
different oven schedule to run.
If an oven is currently running an oven schedule, any attempt to open the inner or outer door of
that oven is denied and a message is displayed. At the completion of the oven schedule, the
operator is allowed to open the oven’s inner door to pass the parts in the oven to the enclosure.
Access to the outer door is allowed only after the inner door is opened at least once at the
completion of an oven schedule.
If the oven is stopped prematurely by pressing the Stop Oven button, then access to either the
inner door or the outer door is allowed.
reate and Edit an Oven Schedule
An oven schedule defines the required oven states and the time duration for each state for a
particular bake-out cycle. The oven states in an oven schedule include oven temperature, oven
vacuum or backfill condition, and oven chamber vacuum pressure. Each oven state and its time
duration in an oven schedule are called a segment. Generally, an oven schedule contains one or
more segments.
A segment consists of four to five parameters depending on the Segment Condition parameter
setting. The first parameter in a segment is the Segment Number starting from one for the first
segment in the schedule. The second parameter is the Temperature Set Point in degree centigrade
for the segment. The third parameter is the Time Duration of the segment in hours. The fourth
parameter is the Segment Condition parameter. The Segment Condition can be set to Vacuum or
Backfill. The last parameter is the Vacuum Pressure Set Point, with pressure units of Torr, and is
only valid if the Segment Condition for the segment is set to Vacuum.
There is one more parameter in an oven schedule called Oven Control Method, which controls
how the time duration for each segment is calculated. This parameter can be set to one of three

Document #107-00092-001 8
choices; Time or Temperature or Temperature & Pressure. This parameter applies to all the
segments in a given oven schedule. If this parameter is set to Time, the time duration is counted
from the start of the oven schedule (for the first segment) or from the completion of the previous
segment (for segments other than the first segment). If this parameter is set to Temperature, the
time duration is counted from the time when the oven temperature, averaged over the oven walls
or heated shelves, depending on if the oven has wall or shelf heating, rises above the Temperature
Set point. If this parameter is set to Temperature & Pressure, the time duration is counted from
the time when both the oven temperature and pressure reach their respective set points.
Oven Type determines which type of oven the glovebox currently have. Depending on the types
of oven, there are usually 3-5 heating zones.
OverTemp SP Abort can be set to a certain temperature where the oven schedule will abort if the
oven temperature overshoots by the amount of the temperature value. To disable this feature,
simply put 0 as the temperature value.
Check the Batch Log to generate batch report for the selected schedule.
Oven Assignment determines which oven can use the selected schedule. Selecting all means all
ovens can use the schedule.
The following (Figure 3) is an example oven schedule containing one segment and the control
method is set to Time. The Segment Condition is set to Backfill for 1 hour and then Vacuum for
another hour.
Figure 3 Example Oven Schedule
Editing and Creating Oven Schedule
Oven schedules are created and edited using a visual schedule editor (Figure 4). The Schedule
Editor is accessed by clicking the “GloveBox” Main window menu, then select “Pump Down and
Oven Settings”. The user must have schedule editing “password rights” to be able to change the
oven schedule parameters or create new schedules.

Document #107-00092-001 9
Figure 4 Pump Down and Oven Settings Screen
Please note that the Oven Schedule Editor and the Pump Down Schedule Editor are both located
on the same USER INTERFACE SCREEN shown above.
To edit an existing oven schedule, first select the schedule by highlighting it in the Oven Schedule
list box located at the lower left part of the USER INTERFACE SCREEN. The selected oven
schedule is then displayed next to it on the right on the USER INTERFACE SCREEN. Each
segment in an oven schedule can be removed (deleted) or edited and a new segment can also be
added to the schedule using the Remove, Edit and Add buttons.
After you have made all the desired changes, click the SAVE button located at the bottom of the
Pump Down and Oven Settings USER INTERFACE SCREEN to save the changes to the oven
schedule.
Click the Save As button to generate a new schedule using with the parameters of the current
schedule.
The import button is used to create a new schedule from a .T T file created by user. The export
button is used to save as the selected schedule into a .T T file.
Click the View/Print button to display the schedule information as shown below. This can also be
used to print the schedule information.

Document #107-00092-001 10
Figure 5 Schedule Report Screen
Add a New Segment
Click the Add button to add a new segment at the selected segment position and push the
selected segment one position lower in the schedule. If no segment is selected before clicking the
Add button, the new segment will be appended at the end of the schedule. Clicking the Add
button opens the following Add New Segment Dialog box:
Figure 6 Add New Segment

Document #107-00092-001 11
Change the default parameters as necessary and then click the “OK” button to finish.
Edit an Existing Segment
Select the segment to be edited by highlighting that segment and then click the Edit button. The
following edit window shows up as a result:
Figure 7 Edit Segment Screen
Select the numeric up-down control or the drop down list desired and use the middle mouse
button or the keyboard or the up and down arrow of the control to change the value for that
parameter. Then click the OK button to end the segment editing. Please note that changing the
segment number will move the segment up or down in the schedule.
Delete an Existing Segment
Select the segment to be removed and then click the Remove button. The selected segment will
be removed from the oven schedule.

Document #107-00092-001 12
Create a New Schedule
If you wish to create a new schedule, press the New button on the Pump Down and Oven
Setting USER INTERFACE SCREEN. The following dialog window with all the default
parameter values appears.
Figure 8 Create New Oven Schedule Screen
Enter a name for the new oven schedule and make changes to the default parameter values as
necessary. Then click OK. A new oven schedule with the specified name and containing a single
segment is created and added to the GLOVEBO schedule database. The new schedule will be
displayed in the list box under the “Oven Schedule” label located at the lower left part of the
Pump Down and Oven Setting USER INTERFACE SCREEN.
After this point, you can edit this new oven schedule to add more segments or to change the
parameters in an existing segment or even delete an existing segment as described in the previous
sections.
mportant: Save Schedule After Entry of 500 New Schedule Steps
The Microsoft Windows XP Operating System has a memory limitation. The user should execute the
following steps when entering a schedule with a large number of steps:
After entering 500 schedule steps, user must save the schedule, close the Schedule Edit
Screen and then reopen theSchedule Edit Screen toenter additional schedule steps.
If the user enters more than 500 schedule steps without saving, a Windows Operating System error
may occur. If that error occurs user should then close the Glovebox software application and then
restart the Glovebox software.
Delete an Existing Oven Schedule
To delete an existing schedule in the GLOVEBO schedule database, highlight the schedule in
the Oven Schedule list box and click the Delete button located at the bottom of the USER
INTERFACE SCREEN. A dialog box shows up asking you if you are sure to delete this oven
schedule. Click OK will delete this oven schedule from the GLOVEBO schedule database.

Document #107-00092-001 13
reate and Edit a Pump Down Schedule
A Pump Down schedule is used to evacuate gas in an oven/interchange chamber with vacuum,
and backfill the chamber with process gas to prevent contamination of the enclosure
environment. In order to completely get rid of the wet gas in an oven/interchange chamber,
multiple evacuate and backfill cycles may be needed.
The two important parameters in a Pump Down schedule are the Vacuum Set Point, which is
used in the evacuate process, and the Evacuate/Backfill Cycles. In order to effectively remove wet
gas from the oven/interchange chamber, two additional parameters are included in a pump down
schedule, namely the Backfill Hold Time and the Vacuum Hold Time. See Figure 8 for an
example of the pump down schedule.
Backfill Hold Time – the time duration that a backfill process lasts.
Vacuum Hold Time – the time duration from the time that the chamber vacuum level reaches
the preset vacuum set point to the time when a subsequent backfill starts.
Figure 9 Example Pump Down Schedule
Create a New Pump Down Schedule
Pump Down schedules are created and edited using a visual schedule editor (Figure 4). The visual
schedule editor is accessed by clicking the “GloveBox” main window menu, and select “Pump
Down and Oven Settings”. The user must have schedule editing “rights” to be able to change the
pump down schedule parameters or create new schedules.
To create a new pump down schedule, click the New button located on the upper half of the
Pump Down and Oven Settings USER INTERFACE SCREEN (see Figure 4). The Create New
Pump Down Schedule dialog window (Figure 9) with all default settings shows up. Enter a
schedule name, change the default parameter values as necessary and click OK to add this new
schedule to GLOVEBO database. After the OK button is clicked, the new schedule will
displayed in the Pump Down Schedule list box on the upper-left part of the visual schedule editor
USER INTERFACE SCREEN.

Document #107-00092-001 14
Figure 10 Create New Pump Down Schedule Screen
Edit an Existing Pump Down Schedule
Select the pump down schedule to be edited from the Pump Down list box in the Schedule editor
USER INTERFACE SCREEN. The selected pump down schedule is displayed on the USER
INTERFACE SCREEN. Then change the schedule parameter as necessary and click the Save
button to save the changes to the GLOVEBO database.
Delete an Existing Pump Down Schedule
To delete an existing pump down schedule in the GLOVEBO database, highlight the schedule
in the Pump Down Schedule list box and click the Delete button. A dialog box shows up asking
you if you are sure to delete this pump down schedule. Click OK will delete this pump down
schedule from the GLOVEBO database.

Document #107-00092-001 15
Environment Settings
The Environment Settings dialog window is accessed by clicking the “GloveBox” Main window
menu and select “Environment Settings”. The user must have proper “rights” to be able to
change the environment setting parameters.
Figure 11 Environment Settings Screen
The Environment Settings USER INTERFACE SCREEN is shown in Figure 10. There are as
many as 14 environment control parameters that can be set from this USER INTERFACE
SCREEN. These parameters are stored in the GLOVEBO database and downloaded to the
controller when the GLOVEBO program is started or when the settings are updated. To
update these settings, enter the new values in the desired fields and then press the OK button.
The following is a description of these parameters.
Environment Pressure Settings:
Control Capability: The GloveBox maintains an over pressure condition inside the GloveBox.
High Limit – The enclosure over pressure valve opens when the differential enclosure pressure
exceeds this setting. The units are inches of water column.
Low Limit – The enclosure gas inlet valve opens when the differential enclosure pressure drops
below this setting. The units are inches of water column.

Document #107-00092-001 16
NOTE:
The High Limit setting is always at least 0.5 greater than the Low Limit setting. This is enforced
by the GLOVEBO software to ensure that the system works smoothly.
Moisture Settings:
Alarm Level – The color of the moisture alarm turns red when the dew point temperature of the
enclosure exceeds this setting and turns back to green when the dew point temperature drops
below this setting.
Purge On Setpoint – The purging process starts when the dew point temperature of the
enclosure goes above this setting.
Purge Off Setpoint - The purging process stops when the dew point temperature of the
enclosure drops below this setting.
Weld nhibit Level – GLOVEBO software will send out a HIGH signal if the dew point
temperature exceeds this setting to stop production equipment, such as a seam welder, from
conducting further operation under the unfavorable condition.
NOTE:
The moisture Purge On Setpoint is always greater than the moisture Purge Off Setpoint and
smaller than the Weld Inhibit Level. The GLOVEBO software prevents the user from entering
moisture purge settings that do not follow this sequence, to ensure the smooth operation of the
system.
Oxygen Settings:
Note: An optional oxygen analyzer needs to be installed for these parameters to be active.
Alarm Level – The color of the Oxygen alarm turns red when the Oxygen level in the enclosure
exceeds this setting, and turns back to green when Oxygen level drops below this setting.
Purge On Setpoint – The purging process starts when the Oxygen level in the enclosure goes
above this setting.
Purge Off Setpoint - The purging process stops when the Oxygen level in the enclosure drops
below this setting.
Weld nhibit Level – GLOVEBO software will send out a HIGH signal if the Oxygen level in
the enclosure exceeds this setting to stop production equipment, such as a seam welder, from
conducting further operation under the unfavorable condition.
NOTE:
The Oxygen Purge On Setpoint is always greater than the Oxygen Purge Off Setpoint and smaller
than the Weld Inhibit Level. The GLOVEBO software prevents the user from entering oxygen
purge settings that do not follow this sequence, to ensure the smooth operation of the system.
The unit for the values are either in % or ppm depending on the type of oxygen analyzer installed.

Document #107-00092-001 17
Helium Settings:
Note: An optional helium analyzer needs to be installed for these parameters to be active.
Alarm Level – The color of the Helium alarm turns red when the Helium level in the enclosure
drops below this setting, and turns back to green when the Helium level exceeds this setting.
Weld nhibit Level – GLOVEBO software will send out a HIGH signal if the Helium level in
the enclosure drops below this setting to stop production equipment, such as a seam welder, from
conducting further operation under the unfavorable condition.
hamber Settings
The current system oven/interchange chamber settings can be viewed by clicking the
“GloveBox” menu from the GLOVEBO main window and selecting the “Chamber Settings”
menu item. The following is an example Chamber Setting screen (Figure 12):
Figure 12 The Chamber Settings Screen
The settings can only be viewed from here. If you would like to update the settings please use the
GloveBox Configurator tool explained in a previous section to do so.

Document #107-00092-001 18
Graphical Data Display
GLOVEBO monitors the statuses of the oven/interchange chambers and GloveBox enclosure,
and logs the relevant important parameters. These parameters include enclosure environment
pressure, enclosure Helium level, enclosure Oxygen level, enclosure moisture level, left chamber
vacuum pressure, left oven temperature, right chamber vacuum pressure and right oven
temperature. Some of these parameters may not be available depending on the configuration of
the system. All these time dependent parameters can be viewed graphically from the
GLOVEBO graph data viewer.
To access the GLOVEBO Graph data viewer, select the “Graph Data” item from the File
menu of the GLOVEBO main window. The following is a graph data viewer screen:
Figure 13 The GLOVEBO Graph Data Viewer Screen
View Real Time Graph Data
To view the current process parameters in real time, click the Real Time button and the
environment pressure parameter will be displayed automatically. Then you can select any other
parameters to display from the Process Parameter list box located at the lower-right corner of the
Graph Data Viewer window. Re-select an already selected process parameter from the Process
Parameter list box will un-display that parameter. The most recent 10 minutes graph data are
displayed and the graphs are updated dynamically.

Document #107-00092-001 19
View History Graph Data
To view history graph data, click the history button, then select the year, month and date of the
graph data you would like to view from the Year, Month and Date list box respectively. Finally
select the process parameters of interest. The entire graph data for the selected date will be
displayed.
Please note that today’s graph data can also be accessed this way. A static graph of today’s data
will be displayed if today’s date is selected from the Year, Month and Date list boxes.
Export to CSV Format
The graph data can be exported to CSV format by pressing the “Export to CSV” button. CSV
format is the comma separated value file format and can be opened and processed by Microsoft’s
Excel program.
Table of contents
Other Miyachi Welding System manuals
Popular Welding System manuals by other brands

Northern Industrial
Northern Industrial ARC 200 Operator's manual
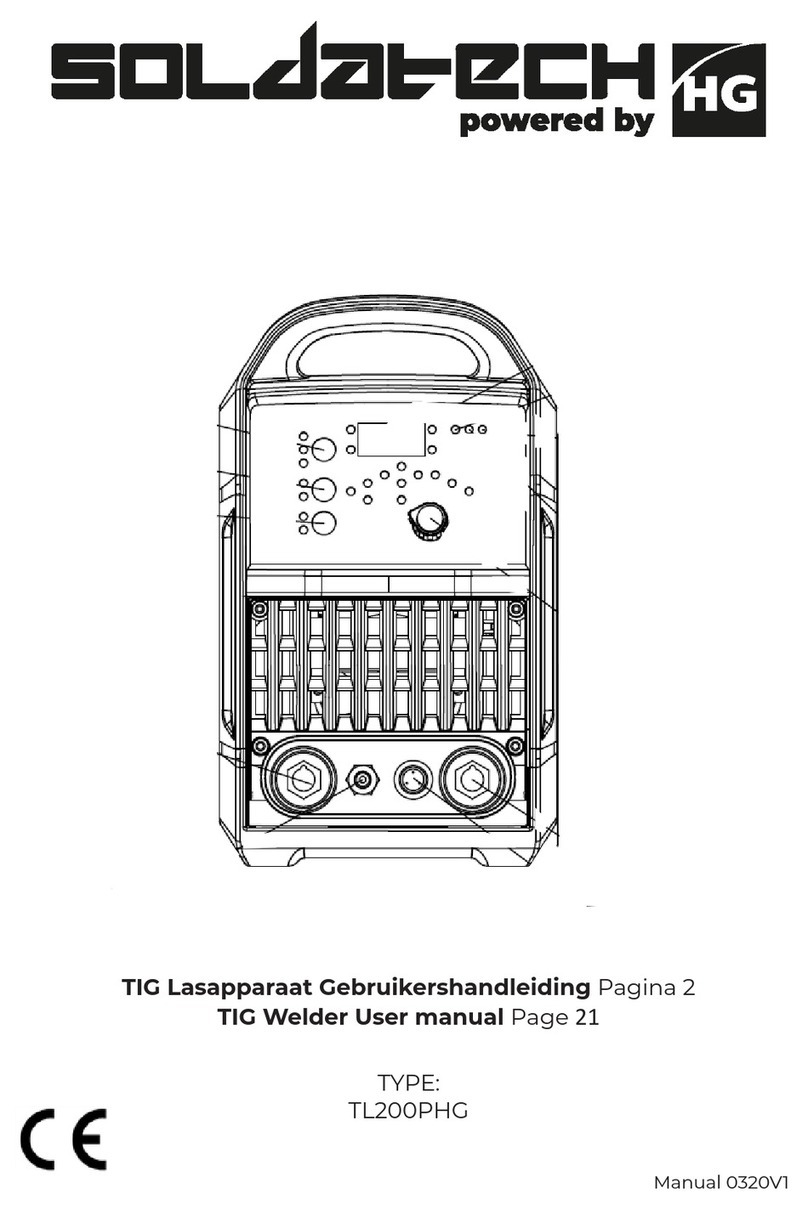
HG
HG Soldatech TL200PHG user manual

Kühtreiber
Kühtreiber MAKin 160 MMA user manual
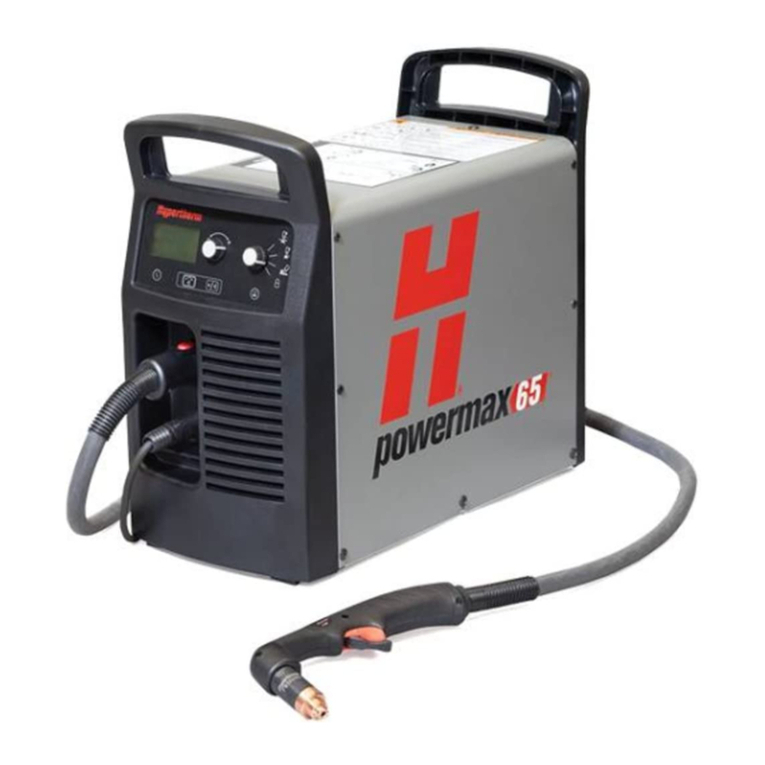
Hypertherm
Hypertherm powermax65 Field Service Bulletin
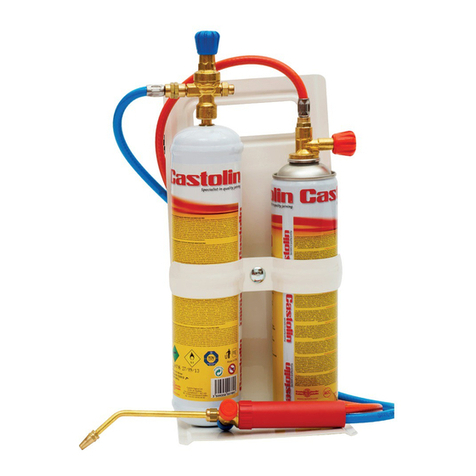
Castolin
Castolin 2000 FLEX Instructions for use and maintenance
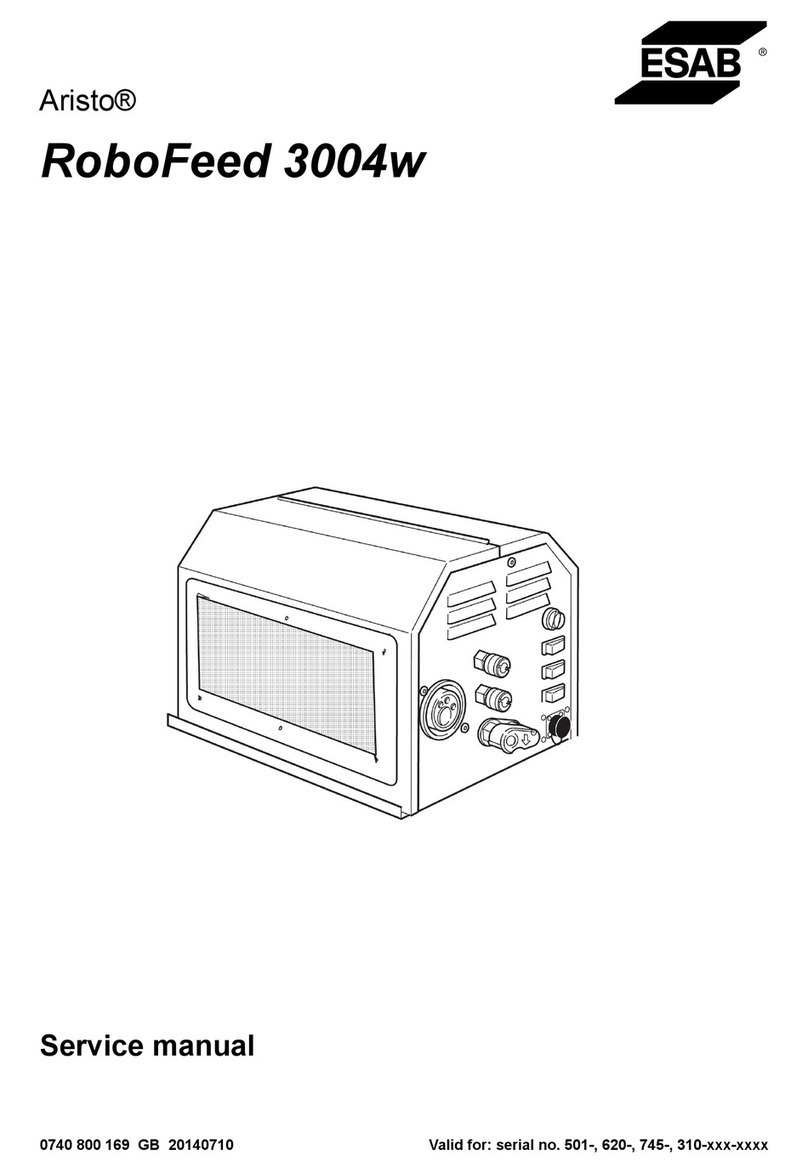
ESAB
ESAB Aristo RoboFeed 3004w Service manual