Mountz TM200fi User manual


Model TM200fi
Operation Manual
V ersion 1.0
Mountz Incorporated
1080 N. 11th S treet
San Jose, CA 95112
Phone: 408-292-2214
Customer Service: 800-456-1828
Fax: 408-292-2733
Copyright ' 1998 Mountz Incorporated
Allright s reserved. No p art of this document may be reproduced, distributed, or
transmitted in any form, or by any means (graphic, electronic, or mechanical, including
photocopying, t aping or information and retrieval systems now known or as may be
hereaf ter developed) without the specific written permission of Mountz Incorporated.
Mountz and it s logo are registered trademarks.
Information cont ained herein is subject to change without prior notice.
Printed in U.S.A.
1

T able of Contents
Introduction ....................................................4
Parts Check List ................................................5
Features ...................................................... 6-7
Before Y ou Begin ................................................8
Operation ....................................................9-13
Changing Modes .................................................9
Changing Numbers ...............................................9
Pause (Paus) Mode .............................................. 10
Unit of Measure .....
............................................ 10
Mode of Operation ......
.........................................11
Setting Tolerances ............................................... 12
Joint Rate ............
......................................... 13
SET-UP Mode ..........
.....................................14-16
Data in Memory, Download Data in Memory, Clear Dat a in Memory ........ 14
Manual & Auto Clear, T ransducer #, Calibrate, Filters ................... 15
Fast Calibration .................................................16
Transducers ................................................17-18
Select T ransducer Cables .....................................
.... 17
Calibration Notes ...............................................
. 17
Schematic Diagram ..............................................18
Transducer Calibration ....................................... 19-21
Fast Cal, T rue Cal ............................................... 19
Zeroing ........................................................ 20
Intervals .......................................................21
2

T able of Contents (cont.)
Charging The Batteries .........................................22
Application Notes ...........................................23-25
Impulse and Power Tool Testing ...............
.....................23
Breakaway Torque Methods .............................
..........24
Calibrating Torque Wrenches ...................................... 25
Sending Data ..
................................................. 25
Filters .
....................................................... 26
Accessories ................................................ 27-29
Perriferals .................................................
....27
Part Numbers ..............................................
....29
Specifications ................................................. 30
3

Introduction
The TM200 can be used for many torque applications in virtually any Engineering dep artment or envi -
ronment. The TM200 is modeled, in style, af ter the Fluke (trademark symbol) meter and was designed
for ease of use and port ability. Here are a few common applications for the TorqueMate and an appro-
priate torque sensor (transducer).
EXAMPLES OF USAGE:
Production Applications - Hand Use: Use a Mountz TWX or SMX torque sensor connected to the
TorqueMate to apply torque to any assembly.The TWX is suited for wrench style applications, while
the SMX is perfect for screwdriver or socket style functions. The unit has a Go/No Go light and alarm
system to notify the operator when they obt ain the low tolerance setting or exceed the high tolerance
setting. The TM200 can also be used with other strain gauge torque sensors for applying torque
and/or torque and angle.
Production Applications - Power Tool Use: Use a Mountz RTSX or RTSX with angle (rot ary trans -
ducer) att ached to a power tool to measure applied torque of an actual dynamic rundown. The unit
has a Go/No Go light and alarm system to notify the operator when they obt ain the low tolerance set -
ting or exceed the high tolerance setting. The TM200 can be used with a strain gauge rot ary sensor
for applying torque and/or torque and angle.
Quality Control Applications - Inspection/Auditing: Use any strain gauge torque sensor and the
TM200 to measure or check the applied torque by using First Movement method (listed in this man -
ual). Readings can be saved to memory for st atistical recall and record keeping or cleared at the
touch of one key.
Quality Control Applications - Joint Evaluation and Test: Use the TM200 with a torque sensor with
optical encoder and apply torque and angle to a joint. Also, use it for determining joint rate (hard,
medium or soft) by setting unit to Angle mode and measuring the amount of torque and rot ation
(angle). This can be done both st atically (with a hand device) or dynamically (with a power drive or
rot ating device) depending on torque sensor selection. Using the TM for joint rate testing is explained
in this manual.
Calibration or Gauge Laboratory Applications: Use the TM200 with Mountz torque sensors to verify
or calibrate hand torque wrenches and screwdrivers or power driven torque tools. The TorqueMate
can be used in any measurement system at the touch of a key and provide an accuracy that allows
use as a main st andard.
R&D and Design Applications: Use the TM200 with proper torque sensor to determine make up of
joint s, strength of fasteners, clamp force or tension.
4
i
Note: Transducer Selection
It is recommended that the TorqueMate be used with Mountz torque or
torque and angle sensors. However, the unit has been developed to
accept a range of 1.000-4.000mv/v input and therefore can be used with
most strain gauge torque sensors whether Mountz brand or other
.

5
Part s Check List
Check to make sure that you have all of the following accessories. Ret ain the p acking materials in case
you need to send the unit in for service or to be calibrated with a transducer using Dead W eight s.
TM200
Power Adapter/Charger
RS232 Cable
9 Pin Serial Adapter
Operation Manual &
Quick Start Card
Certification &
W arranty Card
Carrying Case
(Cardboard)
TM200
Power Adapter/Charger
(available for Europe or other)
Operation Manual & Quick Start Card
W arranty Card and Certifications
RS232 cable with 9 Pin Computer Adapter
i
Note: Please Send in Warranty Card
Complete and return warranty card to validate purchase date.
If this is not done warranty period becomes ef fective on date when
distributor/reseller received shipment.

Features
6
B
TorqueMate 200
Track
Peak
Power Tool
First Peak
Angle Tolerance
High Low
Go No Go
lbf.ft
lbf.in
ozf.in
N.m
Kgf.m
Download Set-up
Data in Memory
ENTER
Units
Tolerance Mode
Scroll
Right Scroll
Up
Zero
Set-Up
Unit s change key
For Set-Up press Tolerance
and Mode keys simult aneously
Five dif ferent engineering
unit s of torque measure
Small window can display -
angle, second peak torque
reading or dat a number
depending upon mode
Mode change key
For Zero press Scroll Right
and Scroll Up simult aneously
Sealed membrane
keypad for any
environment
Use Scroll Right key to
change active digit when
setting numbers
Use Scroll Up key to move
through the menus or
increase value when setting
numbers
Tolerance change
key
Go No Go LED s
Large window displays
torque reading
Five Modes of Operation for
Production, Quality Control,
Calibration Laboratory and
Joint Analysis
X Ducer RS232 Charge On/Off
Top View

Features (cont.)
Accuracy: + .25% of reading from 10% to 100% of full scale – 1 digit - Accurate enough for any cali -
bration laboratory yet economical and port able enough for any production or quality control requirement.
Output: RS-232C port for dat a transfer to printer , dat a logger or computer .
Engineering Units:5dif ferent unit s of torque measure are available. lbf.f t., lbf.in., ozf.in., N.m., Kgf.m
(Other measurement units available as special order)
Battery Operated: NiMH batteries provide long life, without memory . Up to 8 hours of
operation per charge. Low battery indicator turns on when battery is low. Automatically shut s down
when battery is critically low .
Memory: Stores up to 1000 torque and/or angle values. Simply press the Enter Key to store dat a in
memory.
Up To 15 Transducers: Program & calibrate transducers for a variety of applications.
High Impact Plastic Housing: Provides port able belt or bench mounting.
Set (Go/No Go) Tolerance: Easily set user high and low limit s for Torque and Angle with green and red
Go/No Go LED s and an audible buzzer.
Auto Reset: Automatically reset s the display when a new torque cycle is sensed (Peak & First Peak
mode). Reset s in 3 seconds (Power Tool Mode).
Manual Display Reset: Data is held on the display until: 1. The Enter key is pressed clearing the
display and storing the dat a in memory or 2. The Scroll Right key is pressed clearing the display without
storing the dat a in memory.
Calibration: Fast Calibration allows the user to quickly enter and store the full scale mv/v and range
value of each transducer. T rue Calibration allows the user to apply torque with dead weight s and cap -
ture and store 3 calibration point s in each direction.
Both calibration procedures are quick and user
friendly .
Filters: Three sof tware select able filters allow the user to filter out unwanted noise , minimizing non-
torque spikes that can occur when testing pulse or power tools.
7

Before Y ou Begin
Transducer Number
Y ou must have a calibrated transducer with a transducer number assigned to it. Always make sure the
TM200 is set to the transducer number that you have att ached. Every time you turn on the TM200 the
current transducer number and it s associated range will be displayed (depicted by c-XX where XX is
the transducer number). Press Enter to confirm that the proper transducer is att ached. If it is not the
proper transducer number you must change it to the correct number or you will be using incor -
rect calibration data. To change the number press the Scroll Right key once - this will activate the
Scroll keys . Now press the Scroll Up or Scroll Right keys until the proper transducer number is dis -
played. Press Enter to select and go into the operation mode.
Charging
Always leave the TM200 turned on when charging. The microprocessor monitors the charging cycle of
the NimH batteries and must be turned on to do so. The TM200 will go into battery saving PAUSE
mode after 5 minutes without use, but will still be charging. The TM200 can be used when the batteries
are low and the AC adapter is plugged in. See more on charging on p age 22.
Transducer Selection
T ransducer selection is very import ant. Whenever possible, select a transducer range that is approxi -
mately 2 times the range to be used or tested. If you are typically using the tester at 50 lbf.f t., select a
100 lbf.f t. transducer . This significantly reduces the chance that you will overload and damage the
transducer.
8
IMPORTANT
!
i
Note: When Programming Transducers
The torque range and the measurement units of the transducer are
also shown. The torque range will default to 3333 if a transducer
has never been assigned to the number displayed.

Operation
The TM200 is an accurate, user friendly torque display that allows a user to quickly change functions
and features without getting lost in a menu structure. Any change made after pressing the enter key
returns you directly to the operation mode.
CHANGING MODES AND UNITS
W ith the Scroll and Enter Keys - The most used functions are changed by simply pressing the key
labeled with the feature you want to modify. Change the value easily with the Scroll Up. Once you have
selected the new setting or feature simply press the Enter key to accept and return to operation with the
new setting.
FOR EXAMPLE - to change the operation mode
from T rack to First Peak, press the Mode key( 5 )
once and then press the Scroll Up key( 3 ) until the
display icon point s to the First Peak mode( 7 ). Press
Enter( 1 ) to accept and return to the operation mode
in the First Peak setting. The Mode icon will point to
First Peak.
CHANGING NUMBERS
W ith the Scroll and Enter Keys - To change numbers
such as the high and low tolerance, the TM200 is
much like setting an alarm clock. The active digit
(blinking) is changed with the Scroll Up key, to move
to the next digit, simply press the Scroll Right key
(the next digit will now blink). T o set all the Digit s in
the same manner, press Enter again and the num -
ber is set.
FOR EXAMPLE - to set a tolerance when in peak
or first peak mode, press the Tolerance key( 4).
The display will show the Low tolerance set point.
The first digit will be flashing. Change the value of
the flashing digit by pressing the Scroll Up key( 3 ).
Change to the next digit by pressing the Scroll Right
key( 6 ). When the value is reached press the Enter
key( 1 ). To set the High tolerance value, follow the
same procedure as with setting Low tolerance.
Press Enter( 1 ) when the high value is set and you
will be returned to the operation mode.
9
B
TorqueMate 200
Track
Peak
Power Tool
First Peak
Angle Tolerance
High Low
Go No Go
lbf.ft
lbf.in
ozf.in
N.m
Kgf.m
Download Set-up
Data in Memory
ENTER
Units
Tolerance Mode
Scroll
Right Scroll
Up
Zero
Set-Up
7
6
25
1
3
4

Operation (cont.)
PAUSE (PAUS) MODE
The TM200 automatically conserves battery power af ter 5 minutes without use.
The display will show PAUS . Pressing the Enter key returns the TM200 to the operation mode.
UNIT OF MEASURE (Engineering Units)
To change the unit of measurement:
1. Press the Unit ( 2 ) key on the front p anel.
2. Press the Scroll Up ( 3 ) key until the arrow on the right side of the display
point s to the desired unit s.
3.
Press Enter ( 1 ) to accept the new torque unit s and return to the operation
mode.
10
lbf.ft
lbf.in
ozf.in
N.m
Kgf.m
B
TorqueMate 200
Track
Peak
Power Tool
First Peak
Angle Tolerance
High Low
Go No Go
lbf.ft
lbf.in
ozf.in
N.m
Kgf.m
Download Set-up
Data in Memory
ENTER
Units
Tolerance Mode
Scroll
Right Scroll
Up
Zero
Set-Up
2
1
3

Operation (cont.)
11
MODE OF OPERATION
To change the mode of operation:
1. Press the Mode key.
2. Press the Scroll Up key until the mode arrow point s to the desired mode of operation:
a) Track Mode: The display tracks the applied torque in clockwise and counterclockwise directions.
b) Peak Mode: The display holds the highest peak torque applied.
c) Power Tool Mode: Used for measuring torque with power tools such as nutrunners and impulse
tools. Always use a quality joint rate simulator (run down adapter) when testing power tools in a
simulated application. If you do not use a joint rate simulator, damage to the transducer and
or erratic readings might occur.
d) First Peak Mode: The display holds the first peak torque applied and disregards any further input.
This function is primarily used for testing and calibrating click type mechanical torque wrenches by
hand (without a calibration loading bench).
The TM200 captures the point the wrench clicks, and disre -
gards any further input from the operator. Second peak, if
any is shown in the window on the display.
e) Angle Mode: Combined with a transducer with angle
encoder, the TM200 measures the angle of rot ation of a
fastener (with high and low angle tolerance) af ter a programmed threshold torque has been
reached. This feature is used when an angle is specified rather than a final torque. Joint rate and
breakaway torque can also be measured. (See application notes.)
3. Press the Enter key to accept the new mode of operation.
Examples of Mode Applications
Track Mode: Use for reading, running or varying torque on motors and machinery. Use for calibrating
Dial type wrenches on a calibration loading bench.
Peak Mode: Use for calibrating any hand type torque (dial, beam, screwdriver) wrench except hand
testing of clicker type wrenches. Use Peak Mode with the Go/No Go feature. Not for use with power
tools.
Power Tool Mode: Use Power Tool Mode whenever testing dynamic tools such as nutrunners, electric
screwdrivers and impulse tools.
First Peak Mode: Designed exclusively for manually calibrating clicker type torque wrenches (by hand).
Reads the point at which the wrench clicks (first peak), and the point when the operator stopped apply -
ing torque (second peak). Also good for operator training. Apply torque smoothly to avoid false first peak
readings.
Angle Mode: Use Angle Mode to apply a specified angle to a fastener af ter reaching a threshold torque.
Also used to verify break away torque of a fastener and to determine the joint rate of a fastener
(see p age 12 and applications notes for det ailed information on Angle mode usage).
B
Download Set-up
Data in Memory

Operation (cont.)
SETTING GO AND NO/GO TOLERANCE (High/Low) LIMITS
In the Peak, Power Tool or First Peak mode:
1. Press the Tolerance key (the arrow icon will point to Low Tolerance).
2. Change the value of the flashing digit by pressing the Scroll Up key (and the decimal will be fixed).
3. Scroll to the next digit by pressing the Scroll Right key .
4. Press Enter to save the low limit and display the High Tolerance limit.
5. Repeat to set the High limit. Press Enter when finished.
The TM200 will now activate the Green LED and buzzer when reaching a peak over the low limit, and
will activate the Red LED and buzzer when going over the high limit.
In Angle mode:
First enter the threshold torque then the angle tolerance.
1. Press the Tolerance key to display the threshold torque (depicted by torque
threshold in window).
2. Change the value of the flashing digit by pressing the Scroll Up key.
3. Change to the next digit by pressing the Scroll Right key.
4. Press the Enter key when the correct digit s are selected for torque thresh -
old.
5. Now set the angle high/low tolerance.
6. Set the low angle tolerance with the Scroll Keys.
7. Press Enter to save the low angle limit.
8. Repeat for the high angle limit.
9. Press Enter to save the high angle limit and return to the operation mode.
The TM200 display will now track the applied torque until the threshold torque
is reached and then begin monitoring the angle. W hen the low angle is limit is
reached the green LED will illuminate. When the High angle limit is reached the Red LED will illuminate.
When the peak angle is reached the torque at that angle will now be displayed.
Break Away ( Using the Angle mode)
To check breakaway (first movement) of a fastener: The TM200 will enter a special breakaway sensing
mode when you set the low angle tolerance to a small value, usually 1 to 3 degrees, and the high angle
tolerance to zero . Apply torque to an already tightened fastener, when the TM200 senses the threshold
torque (set at approximately 50% of the expected torque) it will st art looking for the fastener to move the
number of degrees set as the low tolerance. When this number of degrees has been reached it will
automatically capture the torque at that point and will disregard any further torque input, even if you keep
turning the fastener .
12
ENTER
Units
Tolerance Mode
Scroll
Right Scroll
Up
Zero
Set-Up
iNote: Use of Go/NoGo
Be sure to set a tolerance if you want to use the Go/No Go feature.
The Go/No Go feature is not active when in the T rack Mode.

13
i
Note: Pressing The Wrong Key
If at any time you press the wrong key, and you do not want to
make changes to the function you incorrectly selected simply press
the Enter key to keep the current setting (you can also turn the
TM200 off and on again). If you press the wrong key while calibrat -
ing turn the unit of f then on again and st art over (dat a is not saved
until the final operation is entered).
Operation (cont.)
T o check the joint rate:
Check the rate of a joint (sof t, medium or hard) by tightening the fastener to the specified torque and
measuring the rot ation angle of the fastener from 50% to 100% of the torque applied.
Set the threshold to 50% of expected torque.
Set the low angle tolerance to zero.
Set the high angle tolerance to a high value (over 900 ).
T esting of the Joint Rate:
Determine if the application joint is a hard, medium or sof t joint. This is determined by measuring the
angle of rot ation of the fastener from approximately 50% of the final torque to the final torque. If the
angle is less than 30 degrees the joint is considered hard. If the angle is 30 to 360 degrees the angle is
considered medium. If the angle is 360 degrees or more it is considered sof t.
A quick method to do this is to use the TM200 with a hand held transducer in Peak Mode. First tighten
the application fastener to 50% of the required torque with the TM200 in peak mode. Now mark the
head of the fastener so you can roughly determine the angle of further rot ation. Once again place the
TM200 wrench on the fastener and tighten to the final desired torque. Measure or approximate the
angle of rot ation. Y ou do not need to know the exact angle, only the range. This angle of rot ation should
be simulated on the test fixture, with a joint rate simulator , when testing pulse tools (or any power tool).
Clearing Numbers On The Display During Operation - When a reading is on the display, press the
Enter key to clear the number and send it to memory and out the RS 232C port. If you want to clear the
display and byp ass sending the dat a to memory press the Scroll Right key.
IfAuto Clear is set to ON and the TM200 is in Peak or First Peak mode, the unit will automatically clear
it self upon sensing additional torque saving you the step of having to press the Scroll Right key. Ifyou
want to save the dat a on the display in memory, press the Enter K ey before you apply a new torque
value or the unit will automatically clear the display and you will lose the data.
When in power tool mode, and Auto Clear is ON, the display automatically clears in 3 seconds. So you
must press the Enter key within three seconds to save the dat a to memory.
If this is not enough time, set Manual Clear to ON and press the Enter key to clear the display and send
the dat a to memory, or the Scroll Right key to clear the display and byp ass sending the dat a to memory.

Set-Up Mode
Enter the Set-Up mode by pressing the Tolerance and Mode key simultaneously (the Set-Up icon
will turn on). Scroll through the various Set-Up functions by pressing the Scroll Up key. When you get
to the option you want to change press the Enter key. Upon changing any option, you will be returned
to the operation mode.
The following seven p aragraphs (DISP, DOWNLOAD, CLR, MANUAL/AUTO CLEAR, TRANSDUCER
CODE, CAL, FIL) is the sequence of functions in the Set-Up menu:
1. DISP - DATA I N MEMORY
(Display The Values Stored In Memory)
DISP and the Dat a in Memory icon will be shown.
a. Press Enter to select this option.
b. The number of data in memory will be displayed on the large digit s.
c. Press the Scroll Right key to view the last dat a in memory. Press Scroll Up to read the next higher
data number. Ifthe dat a number has both Torque and Angle associated with it then the TM200 will
first display the torque value and then the Angle (as shown by the Torque or Angle Icon in the
W indow).
c. Press the Scroll Right key to read the next lower dat a number (i.e., 100, 99...98). The Scroll Up key
will not scroll from the last dat a number to the first (i.e., 100 to 1).
d. Press Enter to exit and return to normal operation.
2. DOWNLOAD DATA IN MEMORY
(Downloads Data In Memory To A Computer or Printer)
Make sure an RS232 cable is att ached and press the Enter key to download
dat a to a computer. The dat a number will count down on the torque window
as the values are downloaded to a dot matrix printer or computer. Press the
Enter key at any time to stop the transfer of dat a. Dat a is sent in the following
stream: Dat a #,Torque, Unit s,Angle. The protocol is 8, 1, n at 4800bp s.
3. CLR - DATA I N MEMORY
(Clears the dat a In memory)
a. Press the Enter Key to select the Clear Memory (Clr) option
(Clr flashes on the LCD and the Dat a in Memory icon is shown).
b. Press the Scroll Right key and the Scroll Up key simult aneously to
clear the memory. Press the Enter key to avoid clearing memory,
and return to the operation mode.
14

Set-Up Mode (cont.)
4. MANUAL CLEAR/AUTO CLEAR
(Select s The Reset (Clear) Mode For The Display)
a. Press Enter to select this option.
b. Press the Scroll Up key to toggle between Manual Clear ON or
Auto Clear ON.
c. Press Enter to save and exit.
During operation, if you have selected the Auto Clear mode, and you want to save dat a to memory, you
must press the Enter key before applying additional torque, otherwise the dat a will be lost when you
apply additional torque (auto clear).
5. c -XX ( c stands for Code Number)
(Select s The Att ached Transducer Number)
The transducer number, full scale range and the unit s icon will show in the
window.
If the W indow shows a range of 3333 (indicates an open cell which can be
programmed to the transducer) the associated transducer number has never been calibrated.
a. Press Enter to select this option.
b. Press Scroll-Up to select available transducer numbers (1-15).
c. When the number corresponds to the att ached transducer, press the Enter key. The TM200 will now
use the appropriate torque calibration dat a for that transducer (if it has been previously calibrated).
6. CAL
(Calibration)
See the calibration section of this manual.
7. FIL
(Select s One of Three Electronic Low Pass Filters)
a. Press Enter to select this option.
The display shows the current filter setting:
Fil 1 = 500 (Hz)
Fil 2 = 1500 (Hz)
Fil 3 = 3600 (Hz)
b. Scroll to the desired filter setting and press enter to accept the new filter .
If you do not know what filter to use, set filter to 1500 Hz.
15

Set-Up Mode (Fast Cal)
Quickly Entering Calibration Data For A T ransducer (Fast Cal)
To quickly enter calibration dat a for a transducer you must know the mv/v signal output at full scale
and the range of the transducer (both should be marked on the transducer).
If the transducer is not marked with this information then contact manufacturer of the
transducer to obtainit.
Turn the TM200 on and press Enter when it shows the current cell number .
1. Enter Set-up by pressing the Mode and Tolerance key simult aneously.
2. Press the Scroll Up key until the display shows CAL .
3. Press the Enter key. Now press the sequence: Enter, Scroll Right, T olerance.
4. Select the proper unit s with the Scroll Up key then press the Enter key.
5.
Select the cell number for the transducer to be calibrated (1-15) with the Scroll Up key, then press
Enter.
6. Enter the full scale range of the new transducer (default is 3333). Use the Scroll Up key to change
the digit value, the Scroll Right key to select a dif ferent digit. Do not worry if the decimal is wrong,
you will change that next. Press Enter when the numbers are correct.
7. Now set the decimal place with the Scroll Right key. Press Enter to save the decimal place.
8.
Now enter the mv/v range of the transducer at full scale (default 2.000). Use the Scroll Up and the Scroll
Right key as you did with the range (you cannot change the decimal place). Press Enter when finished.
Note: The
TM200
will always display 2.000, even if you have previously programmed a dif ferent value.
9. The display will now show Fast (F AST) Cal. Press Enter.
10.
The transducer is now coded and calibrated using mv/v and range. The calibration dat a will be writ -
ten to memory. Whenever you select the corresponding code number the TorqueMatefi Plus will use
the calibration dat a that was saved.
16
i
Note: Calibration Security
To ensure that inadvertent alteration of calibration dat a does not
occur a Key Sequence Override is required to be entered at the CAL
prompt. Af ter hitting Enter to activate the Cal Menu the Key Sequence
Override is accomplished by pressing Enter, Scroll Right & T olerance.
Press these keys in exact order to access the CAL menu.
i
Note: Setting Decimal Place
Always enter the range value st arting with the first decimal place.
For example 10 f t.lb. transducer should be programmed to 10.00 not
010.0 or 0010.

Transducers
The TM200 can be used with 1 to 4 mv/v transducers. Simply assign a code number to the transducer
(1-15) and calibrate it with dead weight s (True Cal), or enter the known mv/v at full scale and the range
(Fast Cal). The TorqueMatefi Plus will store the calibration dat a in memory for that transducer under
the code number you assigned.
SELECTING TRANSDUCER CABLES
The TM200 is delivered with a cable that has a 10 pin modular jack to go into the TM200 and bare wires
on the other end. Adapt your third p arty transducers to the bare wires using the following graphic for
pin-out specifications.
If you have a transducer that has a special connector Mountz can make a custom connector for the
TM200. For example, if your transducer has a Bendix type connector you can order a cable with the
TorqueMatefi Plus 10 pin connector on one end and a Bendix connector on the other. (See list of cables
below)
Calibration Notes
When using the Fast Cal option on the TM200, the TM200 will t ake the mv/v entry that you manually
programmed during transducer calibration, and adjust the gain and sp an automatically. For example, if
the transducer has a mv/v signal of 2.010 at a full range of 50 lbf.f t. then the TM200 will assume when it
senses 2.010 mv/v of output from the transducer that a torque of 50 lbf.f t. is being applied (the display
will show 50 lbf.f t.).
When using the True Cal option, the TM200 will t ake an actual reading of the output of the transducer
when certified dead weight s are applied.
Configuration Part Number
Connections to the TorqueMatefi Plus
1. R TSX to TorqueMate (6 pin Bendix) 065138
2. BTSX to TorqueMate (4 pin Bendix) 065123
3. TorqueMate connector/no connector 065145
(to connect to other transducers)
4. GSE (with Angle indication and 10 pin Bendix) 065151
5. RTSXA (with Angle indication and 10 pin Bendix) 065152
17
IMPORTANT
!

The TM200 and transducers are instruments that should be handled with care. Never overload trans-
ducers above full cap acity . A void using imp act tools on transducers*. Before use, load the transducer to
full scale in the direction to be used, then zero the display to compensate for any zero of fset. Zero of f-
set is a normal characteristic of transducers.
The TM200 will accept transducers with up to 2% zero of fset. If the transducer has more than 2% of fset
the transducer is most likely damaged due to overload. This may result in the inability to zero the display
of the TM200.
*
If testing imp act tools select a transducer that is twice the expected range of the imp act tool and use for reference only .
Do not expect to receive repeat able result s when testing imp act type wrenches.
18
Transducers (cont.)
IMPORTANT
!

Transducer Calibration
Always calibrate the TM200 with the unit plugged into the AC power adapter and make sure the
batteries are fully charged.
Calibration dat a for up to 15 transducers can be memorized by the TM200.
There are two options available for calibrating a transducer:
1. FAST - Fast Cal means that you do not use dead weight s for calibration. The TM200 will assume the
mv/v signal entered is accurate and automatically sp an the range of the transducer and store it in
memory.
2. TRUE -T rue Cal means that you use calibration arms and dead weight s to calibrate the transducer .
The TM200 will t ake three readings in each direction and create a calibration t able in memory.
Procedure for Calibration
Att ach the transducer to be calibrated.
Enter Set-up by pressing the Mode and Tolerance keys at the same time. The Set-up icon will show
and the display will be blank.
Press the Scroll Up key until the LCD shows CAL.
Press Enter to select this option. The Unit s icon will be flashing.
Press Enter to select this option. See not below .
Press the Scroll Up key to select the unit s that you will be calibrating this transducer to. Press Enter to
select the Unit s.
The display will now show the expected transducer number (c-1 to c-15). Press the Scroll Up key until
the desired transducer number is displayed. If the TM200 transducer number has never been used it
will show 3333 for the range (default). This will change as soon as you assign a range to the trans -
ducer. Press Enter to select the proper transducer number .
Enter the range of the transducer to be calibrated. Press the Scroll Up key to change the value of the
flashing digit. Press the Scroll Right key to select a dif ferent digit. When the desired value has been
selected press Enter to accept. Now set the decimal by pressing the Scroll Right key. Press the
Enter key to save the range of the transducer.
19
i
Note: Calibration Security
To ensure that inadvertent alteration of calibration dat a does not
occur a Key Sequence Override is required to be entered at the CAL
prompt. Af ter hitting Enter to activate the Cal Menu the Key Sequence
Override is accomplished by pressing Enter, Scroll Right & T olerance.
Press these keys in exact order to access the CAL menu.
This manual suits for next models
1
Table of contents
Other Mountz Measuring Instrument manuals
Popular Measuring Instrument manuals by other brands
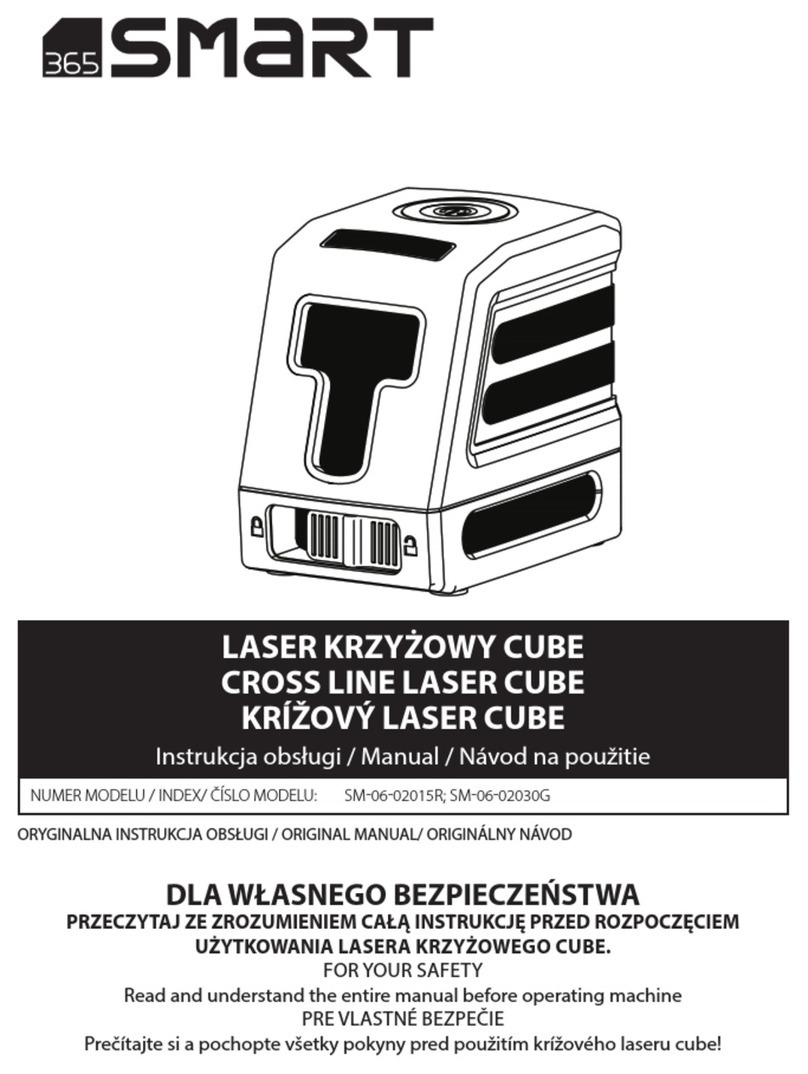
365SMART
365SMART SM-06-02015R Original manual

Teledyne Lecroy
Teledyne Lecroy HVFO103 Operator's manual
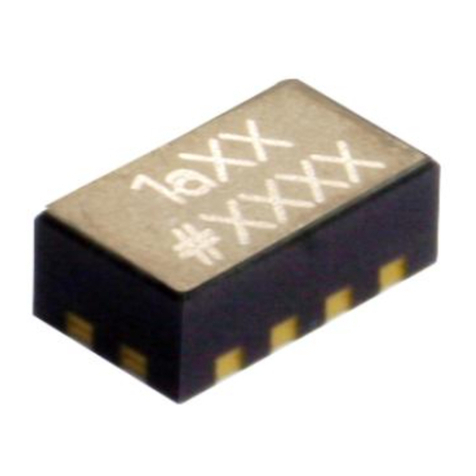
PCB Piezotronics
PCB Piezotronics 3501A2020KG Installation and operating manual
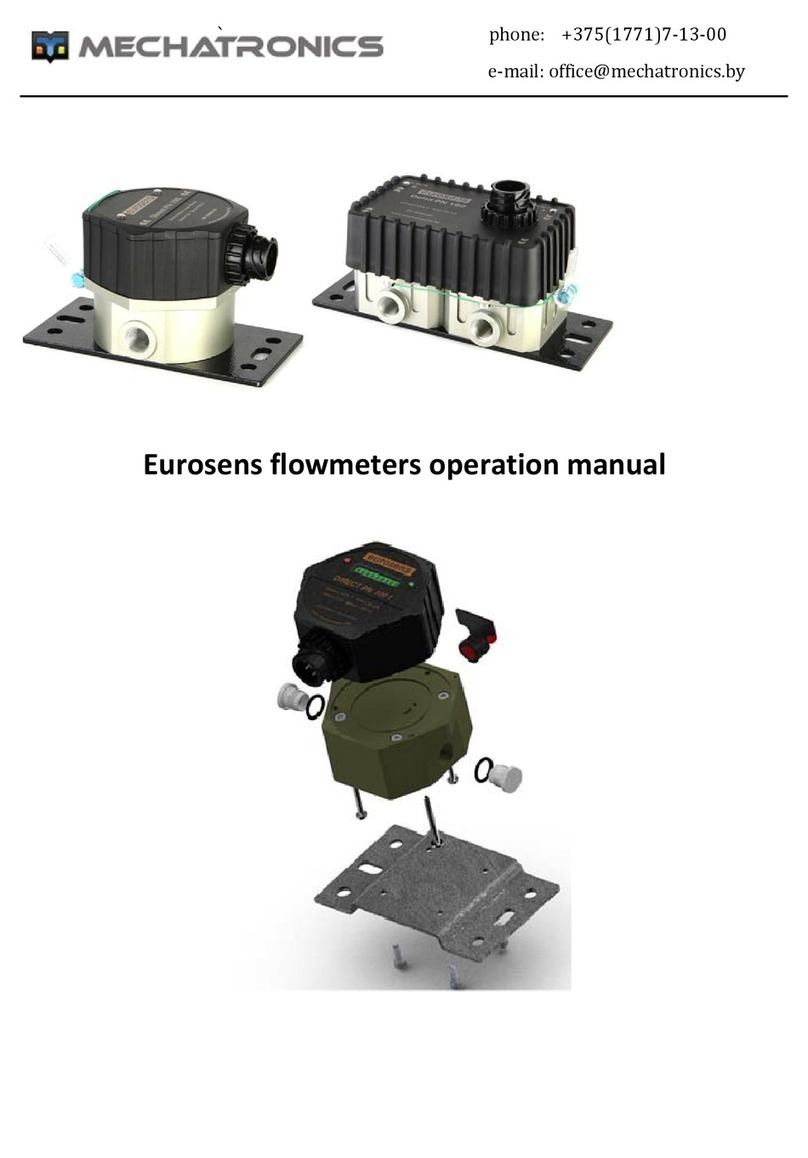
Mechatronics
Mechatronics Eurosens Direct PH 100 Operation manual
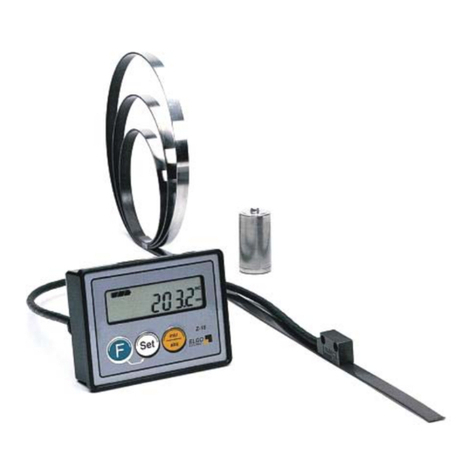
ELGO Electronic
ELGO Electronic Z16 Series Operation manual
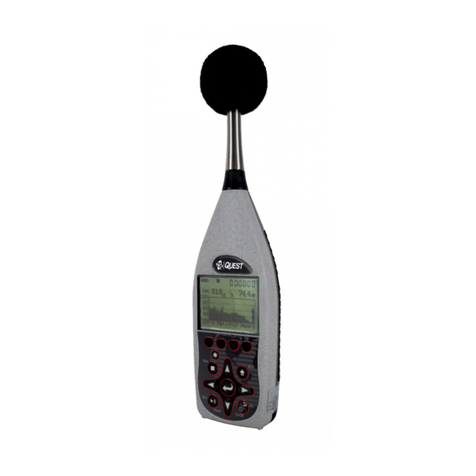
3M
3M SoundPro SE Series Data Addendum Manual