MR VACUTAP VV-Ex Installation and operation manual

On-load tap-changer
VACUTAP® VV-Ex
Installation and commissioning instructions
4983703/01 EN

© All rights reserved by Maschinenfabrik Reinhausen
Dissemination and reproduction of this document and use and disclosure of its content are strictly prohibited
unless expressly permitted.
Infringements will result in liability for compensation. All rights reserved in the event of the granting of patents,
utility models or designs.
The product may have been altered since this document was published.
We reserve the right to change the technical data, design and scope of supply.
Generally the information provided and agreements made when processing the individual quotations and orders
are binding.
The original operating instructions were written in German.

Table of contents
Maschinenfabrik Reinhausen GmbH 2020 34983703/01 EN VACUTAP® VV-Ex
Table of contents
1 Introduction......................................................................................................................... 7
1.1 Manufacturer....................................................................................................................................... 7
1.2 Completeness..................................................................................................................................... 7
1.3 Safekeeping........................................................................................................................................ 7
1.4 Notation conventions .......................................................................................................................... 7
1.4.1 Hazard communication system .............................................................................................................................7
1.4.2 Information system................................................................................................................................................9
1.4.3 Instruction system .................................................................................................................................................9
2 Safety................................................................................................................................. 11
2.1 Appropriate use ................................................................................................................................ 11
2.2 Inappropriate use.............................................................................................................................. 12
2.3 Fundamental safety instructions ....................................................................................................... 12
2.4 Standards and regulations................................................................................................................ 14
2.4.1 Application range of the on-load tap-changer .....................................................................................................14
2.4.2 Standards and regulations ..................................................................................................................................16
2.5 Measures for ensuring compliance with explosion protection requirements .................................... 17
2.5.1 Measures taken by the manufacturer..................................................................................................................17
2.5.2 Measures to be taken by the transformer manufacturer/operator.......................................................................17
2.6 Personnel qualification...................................................................................................................... 20
2.7 Personal protective equipment ......................................................................................................... 22
3 Product description.......................................................................................................... 23
3.1 Scope of delivery .............................................................................................................................. 23
3.2 On-load tap-changer......................................................................................................................... 23
3.2.1 Function description ............................................................................................................................................23
3.2.2 Setup/models ......................................................................................................................................................24
3.2.3 Nameplate and serial number .............................................................................................................................27
3.2.4 Protective devices ...............................................................................................................................................27
3.3 Drive shaft......................................................................................................................................... 30
3.3.1 Function description ............................................................................................................................................30
3.3.2 Design/Model ......................................................................................................................................................32
3.3.3 Identification plate ...............................................................................................................................................34

Table of contents
Maschinenfabrik Reinhausen GmbH 202044983703/01 ENVACUTAP® VV-Ex
4 Packaging, transport and storage .................................................................................. 35
4.1 Packaging ......................................................................................................................................... 35
4.1.1 Suitability.............................................................................................................................................................35
4.1.2 Markings..............................................................................................................................................................36
4.2 Transportation, receipt and handling of shipments........................................................................... 36
4.3 Storage of shipments........................................................................................................................ 37
4.4 Unpacking shipments and checking for transportation damages ..................................................... 38
5 Mounting ........................................................................................................................... 39
5.1 Installation information...................................................................................................................... 39
5.2 Preparatory work .............................................................................................................................. 40
5.2.1 Fitting mounting flange on transformer cover......................................................................................................40
5.2.2 Fitting stud bolts on mounting flange ..................................................................................................................40
5.3 Installing the on-load tap-changer in the transformer (standard version) ......................................... 41
5.3.1 Fastening on-load tap-changer to transformer cover ..........................................................................................41
5.3.2 Connecting the tap winding and on-load tap-changer take-off lead....................................................................49
5.3.3 Performing transformer ratio test before drying ..................................................................................................50
5.3.4 Performing DC resistance measurement on transformer....................................................................................51
5.3.5 Drying on-load tap-changer in autoclave ............................................................................................................51
5.3.6 Drying on-load tap-changer in transformer tank..................................................................................................53
5.3.7 Filling the oil compartment of the on-load tap-changer with insulating fluid........................................................56
5.3.8 Performing transformer ratio test after drying .....................................................................................................57
5.4 Installing on-load tap-changer in transformer (bell-type tank version).............................................. 58
5.4.1 Inserting on-load tap-changer into supporting structure......................................................................................58
5.4.2 Connecting the tap winding and on-load tap-changer take-off lead....................................................................60
5.4.3 Performing transformer ratio test before drying ..................................................................................................60
5.4.4 Performing DC resistance measurement on transformer....................................................................................61
5.4.5 Drying on-load tap-changer in autoclave ............................................................................................................62
5.4.6 Lifting top part of on-load tap-changer head off supporting flange (bottom part) ................................................64
5.4.7 Attaching the bell-type tank and connecting the on-load tap-changer to the top part of the on-load tap-changer
head ....................................................................................................................................................................67
5.4.8 Drying on-load tap-changer in transformer tank..................................................................................................72
5.4.9 Filling the oil compartment of the on-load tap-changer with insulating fluid........................................................75
5.4.10 Performing transformer ratio test after drying .....................................................................................................76
5.5 Fitting protective devices and drive components.............................................................................. 77
5.5.1 Electrically connecting the temperature sensor ..................................................................................................77
5.5.2 Installing protective relay in piping and connecting.............................................................................................77

Table of contents
Maschinenfabrik Reinhausen GmbH 2020 54983703/01 EN VACUTAP® VV-Ex
5.5.3 Fitting motor-drive unit ........................................................................................................................................87
5.5.4 Fitting drive shaft.................................................................................................................................................87
5.5.5 Centering on-load tap-changer and motor-drive unit ........................................................................................111
5.5.6 Making the electrical connections for the motor-drive unit ................................................................................111
6 Commissioning............................................................................................................... 112
6.1 Commissioning the on-load tap-changer at the transformer manufacturer's site ........................... 112
6.1.1 Bleeding on-load tap-changer head and suction pipe.......................................................................................112
6.1.2 Grounding the on-load tap-changer ..................................................................................................................114
6.1.3 Checking motor-drive unit .................................................................................................................................115
6.1.4 High-voltage tests on the transformer ...............................................................................................................116
6.2 Transporting transformer to the operating site................................................................................ 116
6.2.1 Transport with drive removed............................................................................................................................116
6.2.2 Transport with full transformer tank and without oil conservator.......................................................................117
6.2.3 Transport with empty transformer tank .............................................................................................................118
6.3 Commissioning transformer at operating site ................................................................................. 120
6.3.1 Filling the oil compartment of the on-load tap-changer with insulating fluid......................................................120
6.3.2 Bleeding on-load tap-changer head and suction pipe.......................................................................................121
6.3.3 Checking motor-drive unit .................................................................................................................................123
6.3.4 Checking protective relay..................................................................................................................................124
6.3.5 Commissioning the transformer ........................................................................................................................125
7 Fault elimination ............................................................................................................. 126
7.1 Tripping the protective relay and re-commissioning the transformer.............................................. 128
7.1.1 Flap valve in OPERATION position ..................................................................................................................128
7.1.2 Flap valve in OFF position ................................................................................................................................129
7.1.3 Re-commissioning the transformer ...................................................................................................................129
8 Technical data................................................................................................................. 130
8.1 Permissible ambient conditions ...................................................................................................... 130
8.2 Technical data for protective relay.................................................................................................. 130
8.2.1 Protective relay with several dry-reed magnetic switches.................................................................................132
8.2.2 Tests .................................................................................................................................................................133
8.3 Limit values for dielectric strength and water content of insulating fluids ....................................... 134
9 Drawings ......................................................................................................................... 135
9.1 External view (737774) ................................................................................................................... 135
9.2 On-load tap-changer head without oil suction pipe (898863) ......................................................... 136

Table of contents
Maschinenfabrik Reinhausen GmbH 202064983703/01 ENVACUTAP® VV-Ex
9.3 On-load tap-changer head with oil suction pipe (737060) .............................................................. 137
9.4 Installation drawing (738902).......................................................................................................... 138
9.5 Oil suction pipe (739172)................................................................................................................ 139
9.6 Dimensions of oil suction pipe (not supplied by MR, 734342) ........................................................ 140
9.7 Tracing template for on-load tap-changer head (893787) .............................................................. 141
9.8 Mounting drawing (898866) ............................................................................................................ 142
9.9 Mounting with bell-type tank installation (899110).......................................................................... 143
9.10 Position of on-load tap-changer (899409) ...................................................................................... 144
9.11 Position of connection contacts (899051)....................................................................................... 145
9.12 Tap-change supervisory control (733469) ...................................................................................... 146
9.13 Bevel gear CD 6400, dimensional drawing (892916) ..................................................................... 147
Glossary .......................................................................................................................... 148

1 Introduction
Maschinenfabrik Reinhausen GmbH 2020 74983703/01 EN VACUTAP® VV-Ex
1 Introduction
This technical file contains detailed descriptions of the safe and proper in-
stallation, connection, and commissioning of the product.
It also includes safety instructions and general information about the prod-
uct.
Information about operation can be found in the operating instructions.
This technical file is intended solely for specially trained and authorized per-
sonnel.
1.1 Manufacturer
The product is manufactured by:
Maschinenfabrik Reinhausen GmbH
Falkensteinstraße 8
93059 Regensburg
Tel.: (+49) 9 41/40 90-0
E-mail: [email protected]
Further information on the product and copies of this technical file are avail-
able from this address if required.
1.2 Completeness
This technical file is incomplete without the supporting documents.
The following documents are considered supporting documents:
▪ Unpacking instructions
▪ Supplement
▪ Routine test report
▪ Connection diagrams
▪ Dimensional drawings
▪ Order confirmation
1.3 Safekeeping
Keep this technical file and all supporting documents ready at hand and ac-
cessible for future use at all times.
1.4 Notation conventions
1.4.1 Hazard communication system
Warnings in this technical file are displayed as follows.

1 Introduction
Maschinenfabrik Reinhausen GmbH 202084983703/01 ENVACUTAP® VV-Ex
1.4.1.1 Warning relating to section
Warnings relating to sections refer to entire chapters or sections, sub-sec-
tions or several paragraphs within this technical file. Warnings relating to
sections use the following format:
WARNING Type of danger!
Source of the danger and outcome.
► Action
► Action
1.4.1.2 Embedded warning information
Embedded warnings refer to a particular part within a section. These warn-
ings apply to smaller units of information than the warnings relating to sec-
tions. Embedded warnings use the following format:
DANGER! Instruction for avoiding a dangerous situation.
1.4.1.3 Signal words and pictograms
The following signal words are used:
Signal word Definition
DANGER Indicates a hazardous situation which, if not avoided, will result in
death or serious injury.
WARNING Indicates a hazardous situation which, if not avoided, could result
in death or serious injury.
CAUTION Indicates a hazardous situation which, if not avoided, could result
in minor or moderate injury.
NOTICE Indicates measures to be taken to prevent damage to property.
Table1: Signal words in warning notices
Pictograms warn of dangers:
Pictogram Definition
Warning of a danger point
Warning of dangerous electrical voltage

1 Introduction
Maschinenfabrik Reinhausen GmbH 2020 94983703/01 EN VACUTAP® VV-Ex
Pictogram Definition
Warning of combustible substances
Warning of danger of tipping
Warning of danger of crushing
Table2: Pictograms used in warning notices
1.4.2 Information system
Information is designed to simplify and improve understanding of particular
procedures. In this technical file it is laid out as follows:
Important information.
1.4.3 Instruction system
This technical file contains single-step and multi-step instructions.
Single-step instructions
Instructions which consist of only a single process step are structured as fol-
lows:
Aim of action
üRequirements (optional).
► Step 1 of 1.
ðResult of step (optional).
ðResult of action (optional).
Multi-step instructions
Instructions which consist of several process steps are structured as follows:

1 Introduction
Maschinenfabrik Reinhausen GmbH 202010 4983703/01 ENVACUTAP® VV-Ex
Aim of action
üRequirements (optional).
1. Step 1.
ðResult of step (optional).
2. Step 2.
ðResult of step (optional).
ðResult of action (optional).

2 Safety
Maschinenfabrik Reinhausen GmbH 2020 114983703/01 EN VACUTAP® VV-Ex
2 Safety
▪ Read this technical file through to familiarize yourself with the product.
▪ This technical file is a part of the product.
▪ Read and observe the safety instructions provided in this chapter.
▪ Read and observe the warnings in this technical file in order to avoid func-
tion-related dangers.
▪ The product is manufactured on the basis of state-of-the-art technology.
Nevertheless, risks to life and limb for the user or impairment of the prod-
uct and other material assets due to the function may arise in the event of
improper use.
2.1 Appropriate use
The product is an on-load tap-changer and adjusts the transmission ratio of
transformers without interrupting the load flow. The product is designed
solely for use in electrical energy systems and facilities. If used as intended
and in compliance with the requirements and conditions specified in this
technical file as well as the warning notices in this technical file and attached
to the product, then the product does not present any danger to people,
property or the environment. This applies throughout the service life of the
product, from delivery, installation and operation to removal and disposal.
The following is considered appropriate use:
▪ Use the product only with the transformer specified in the order.
▪ Only operate the product with the versions of the motor-drive unit, drive
shaft and protective relay that have been approved for use in explosive ar-
eas.
▪ The serial numbers of on-load tap-changer and on-load tap-changer ac-
cessories (drive, drive shaft, bevel gear, protective relay, etc.) must match
if the on-load tap-changer and on-load tap-changer accessories are sup-
plied as a set for one order.
▪ You will find the standard valid for the product and the year of issue on the
nameplate.
▪ Operate the product in accordance with this technical file, the agreed-
upon delivery conditions and the technical data.
▪ Ensure that all necessary work is performed by qualified personnel only.
▪ Only use the equipment and special tools included in the scope of delivery
for the intended purpose and in accordance with the specifications of this
technical file.
▪ The on-load tap-changer is not intended to be used with an oil filter unit.
▪ The measures described in this technical file must be taken in order to
comply with explosion protection requirements.
Permitted electrical operating conditions
In addition to the design data in accordance with the order confirmation, ob-
serve the following limits for the through-current and the step voltage:

2 Safety
Maschinenfabrik Reinhausen GmbH 202012 4983703/01 ENVACUTAP® VV-Ex
In the standard version, the on-load tap-changer is designed for sinusoidal
50/60 Hz alternating current with a curve form symmetrical to the zero axis
and can switch 1.5 times the rated through-current Ir at its rated step voltage
Uir.
Exceeding the rated step voltage Uir for a short period by up to 10% is per-
mitted if the rated through-current Ir is not exceeded.
The highest voltage for equipment Um is limited to 245kV.
2.2 Inappropriate use
Use is considered inappropriate if the product is used in a way other than as
described in the "Appropriate use" section. In addition, observe the following:
Prohibited electrical operating conditions
All operating conditions that do not comply with the design data in accor-
dance with the order confirmation are prohibited.
Prohibited operating conditions may arise due to short circuits as well as due
to inrush current impulses when energizing transformers or other electrical
machines. This applies to the affected transformer itself just as it does to
transformers electrically connected in parallel or serially or other electrical
machines.
Higher voltages may occur due to transformer overexcitation following load
shedding, for example.
Operations outside of the permitted operating conditions can lead to injury to
persons and damage to the product.
▪ Prevent any such operations outside of the permitted operating conditions
by taking suitable measures.
2.3 Fundamental safety instructions
To prevent accidents, malfunctions and damage as well as unacceptable ad-
verse effects on the environment, those responsible for transport, installa-
tion, operation, maintenance and disposal of the product or parts of the prod-
uct must ensure the following:
Personal protective equipment
Loosely worn or unsuitable clothing increases the danger of becoming
trapped or caught up in rotating parts and the danger of getting caught on
protruding parts. This poses a danger to life and limb.
▪ Wear appropriate personal protective equipment such as a helmet, work
gloves, etc. for the respective activity.
▪ Never wear damaged personal protective equipment.
▪ Never wear rings, necklaces, or other jewelry.
▪ If you have long hair, wear a hairnet.

2 Safety
Maschinenfabrik Reinhausen GmbH 2020 134983703/01 EN VACUTAP® VV-Ex
Work area
Untidy and poorly lit work areas can lead to accidents.
▪ Keep the work area clean and tidy.
▪ Make sure that the work area is well lit.
▪ Observe the applicable laws for accident prevention in the relevant coun-
try.
Working during operation
The product may only be operated in a sound, operational condition. Other-
wise it poses a danger to life and limb.
▪ Regularly check the operational reliability of safety equipment.
▪ Comply with the inspection work, maintenance work and maintenance in-
tervals described in this technical file.
Explosion protection
Highly flammable or explosive gases, vapors and dusts can cause serious
explosions and fire.
▪ Do not install the product in potentially explosive areas or in potentially ex-
plosive atmospheres.
Safety markings
Warning signs and safety information plates are safety markings on the
product. They are an important aspect of the safety concept.
▪ Observe all safety markings on the product.
▪ Make sure all safety markings on the product remain intact and legible.
▪ Replace safety markings that are damaged or missing.
Ambient conditions
To ensure reliable and safe operation, the product must only be operated
under the ambient conditions specified in the technical data.
▪ Observe the specified operating conditions and requirements for the in-
stallation location.
Auxiliary materials and operating materials
Auxiliary materials and operating materials not approved by the manufac-
turer can lead to personal injury, damage to property and malfunctions of the
product.
▪ For the on-load tap-changer oil compartment, use insulating fluids that
meet the requirements in accordance with IEC 60296.
▪ If approved by the transformer manufacturer, you can use synthetic esters
in accordance with IEC61099.

2 Safety
Maschinenfabrik Reinhausen GmbH 202014 4983703/01 ENVACUTAP® VV-Ex
▪ It is imperative that you consult with Maschinenfabrik Reinhausen GmbH
because specific operating conditions apply to alternative insulating fluids.
▪ Only use conductive and grounded hoses, pipes, and pump equipment
that are approved for flammable liquids.
▪ Only use lubricants and auxiliary materials approved by the manufacturer.
▪ Contact the manufacturer.
Modifications and conversions
Unauthorized or inappropriate changes to the product may lead to personal
injury, material damage and operational faults.
▪ Only modify the product after consultation with Maschinenfabrik Rein-
hausen GmbH.
Spare parts
Spare parts not approved by Maschinenfabrik Reinhausen GmbH may lead
to physical injury, damage to the product and malfunctions.
▪ Only use spare parts that have been approved by Maschinenfabrik Rein-
hausen GmbH.
▪ Contact Maschinenfabrik Reinhausen GmbH.
2.4 Standards and regulations
2.4.1 Application range of the on-load tap-changer
The on-load tap-changer is certified for II 3G Ex ec oc IIC T3 Gc. Refer to
the following overview for the resulting application range.
12345678
II 3G Ex ec oc IIC T3 Gc
Table3: Example of the application range
Number Meaning
1 Sign for explosion protection
2 Equipment group
3 Equipment category
4 Ex: Symbol for explosion-protected equipment
5 Ignition protection type
6 Explosion group
7 Temperature class
8 EPL (equipment protection level)

2 Safety
Maschinenfabrik Reinhausen GmbH 2020 154983703/01 EN VACUTAP® VV-Ex
Equipment groups (number 2)
I Equipment in this category is intended for use in underground
parts of mines as well as those parts of surface installations of
such mines endangered by firedamp and/or combustible dust.
II Equipment in this category is intended for use in other areas in
which explosive atmospheres may be present.
Table4: Equipment groups
Equipment category / zone classification (number 3)
Designation
for gases
Designation
for dusts
Definition
1G
(0)
1D
(20)
Equipment in this category is intended for use in ar-
eas in which explosive atmospheres caused by mix-
tures of air and gases, vapors or mists or by air/dust
mixtures are present continuously, for long periods
or frequently.
2G
(1)
2D
(21)
Equipment in this category is intended for use in ar-
eas in which explosive atmospheres caused by
gases, vapors, mists or air/dust mixtures occur oc-
casionally.
3G
(2)
3D
(22)
Equipment in this category is intended for use in ar-
eas in which explosive atmospheres caused by
gases, vapors, mists, or air/dust mixtures are un-
likely to occur or, if they do occur, are likely to do so
only infrequently and for a short period only.
Table5: Equipment category / zone classification
Ignition protection types (number 5)
d Pressure-proof enclosure
e Increased safety
i Intrinsic safety (ia, ib)
m Encapsulation
o Liquid immersion
Protection level "ob": Equipment protection level (EPL) "Gb" for
zone 1 and zone 2
Protection level "oc": Equipment protection level (EPL) "Gc" for
zone 2
p Pressurized apparatus
q Powder filling
n Ignition protection type "n"
Table6: Ignition protection types

2 Safety
Maschinenfabrik Reinhausen GmbH 202016 4983703/01 ENVACUTAP® VV-Ex
Explosion group (number 6)
EN/IEC Gases, vapors (examples) Min. ignition energy
(mJ)
IIA Ammonia -
IIA Acetic acid, acetone, benzene, diesel,
ethane, ether, fuel oil, hexane, meth-
ane, petrol, petroleum, propane
0.18
IIB Ethylene, isoprene, town gas 0.06
IIC Acetylene, carbon disulfide, hydrogen 0.02
Table7: Explosion groups
Temperature classes (number 7)
Temperature
class
Maximum equipment surface tem-
perature
Ignition temperature of
the flammable sub-
stances
T1 450°C > 450°C
T2 300°C > 300°C < 450°C
T3 200°C > 200°C < 300°C
T4 135°C > 135°C < 200°C
T5 100°C > 100°C < 135°C
T6 85°C > 85°C < 100°C
Table8: Temperature classes
Equipment protection level (EPL) (number 8)
The EPL indicates the level of protection defined for a device based on the
level of probability of ignition and taking into account the differences be-
tween potentially explosive gas atmospheres, potentially explosive dust at-
mospheres, and potentially explosive atmospheres in mine workings af-
fected by firedamp.
2.4.2 Standards and regulations
The following standards and regulations apply to explosion-proof on-load
tap-changers:
▪ EN/IEC 60079-0: Equipment – General requirements
▪ EN/IEC 60079-6: Equipment protection by liquid immersion "o"
▪ EN/IEC 60079-7: Equipment protection by increased safety "e"

2 Safety
Maschinenfabrik Reinhausen GmbH 2020 174983703/01 EN VACUTAP® VV-Ex
2.5 Measures for ensuring compliance with explosion
protection requirements
2.5.1 Measures taken by the manufacturer
Maschinenfabrik Reinhausen has taken the following measures for ensuring
compliance with explosion protection requirements. You do not need to take
any special measures in this regard.
2.5.1.1 Quality of the insulating oil in the on-load tap-changer
The quality of the insulating oil required by IEC 60296 and the quality of the
synthetic esters required by IEC 61099 in the oil compartment of the on-load
tap-changer is ensured by using vacuum cells with transition resistors.
2.5.1.2 Monitoring the oil temperature in the diverter switch oil compartment
A temperature sensor is provided in the on-load tap-changer head cover for
monitoring the oil temperature in the diverter switch oil compartment. The
corresponding temperature monitoring relay is in the TAPMOTION® ED-Ex.
Temperature monitoring prevents further switching of the on-load tap-
changer when the maximum permitted temperature is reached. This maxi-
mum permitted temperature is factory-configured for each specific order for
all on-load tap-changer types (maximum 130 °C) and secured against acci-
dental incorrect adjustment.
2.5.2 Measures to be taken by the transformer manufacturer/operator
The following measures for ensuring compliance with explosion protection
requirements must be taken by the transformer manufacturer/operator.
2.5.2.1 Prescribed protective and drive components
Operate the on-load tap-changer only in conjunction with the following com-
ponents:
▪ Ex protective relay
▪ Ex motor-drive unit
▪ Ex drive shaft

2 Safety
Maschinenfabrik Reinhausen GmbH 202018 4983703/01 ENVACUTAP® VV-Ex
2.5.2.2 Setting up the on-load tap-changer oil system
Operate the on-load tap-changer only with a suitable oil system. This di-
verter switch oil system consists of the diverter switch oil compartment, pro-
tective relay, and oil conservator of the on-load tap-changer. It ensures that
enough insulating oil is present in the diverter switch oil compartment at all
times.
Figure1: On-load tap-changer oil system
1 Diverter switch oil compartment 5 Signaling contacts
2 Temperature sensor 6 Oil conservator
3 Protective relay 7 Dehydrating breather
4 Level indicator
2.5.2.3 Oil conservator to be used
The oil conservator of the on-load tap-changer ensures that sufficient insu-
lating oil is present in the on-load tap-changer oil system at all times during
operation.
Therefore, operate the on-load tap-changer only with a oil conservator that
fulfills the following requirements:

2 Safety
Maschinenfabrik Reinhausen GmbH 2020 194983703/01 EN VACUTAP® VV-Ex
2.5.2.3.1 Dehydrating breather
The oil conservator must be equipped with a dehydrating breather in accor-
dance with VDE 0532-216-5 with downward-leading outlet and a protection
degree of at least IP66 in accordance with IEC60529.
2.5.2.3.2 Level indicator
The oil conservator must have a level indicator from which the minimum oil
quantity required and the maximum quantity permitted, as well as the current
oil level, can be read.
2.5.2.3.3 Level monitoring
The oil level in the oil conservator must be monitored at all times during op-
eration. Therefore, loop the signaling contact for falling below the minimum
oil level in the on-load tap-changer's oil conservator to the tripping circuit of
the circuit breaker so that the circuit breaker will immediately de-energize the
transformer when the oil level in the oil conservator falls below this minimum.
2.5.2.3.4 Insulating oil to be used
When filling the diverter switch oil compartment and its oil conservator, use
only new mineral insulating oil for transformers in accordance with IEC
60296 (Specification for unused mineral insulating oils for transformers and
switchgear) or synthetic ester in accordance with IEC 61099 (Specifications
for unused synthetic organic esters for electrical purposes).
2.5.2.3.5 Checking the quality of the insulating oil in the Ex transformer
During the tap changes, polarity sparks (low energy) may occur at the tap
selector of the on-load tap-changer in the transformer tank. In this regard,
observe Section 5.1.6 and 5.1.7 in the on-load tap-changer standard IEC
60214.
Therefore, check the quality and dielectric strength of the insulating oil in the
transformer tank on a regular basis and comply with the service intervals for
the oil change.

2 Safety
Maschinenfabrik Reinhausen GmbH 202020 4983703/01 ENVACUTAP® VV-Ex
2.5.2.4 Corrosion protection measures
Because further installation steps are required before operation of the on-
load tap-changer, sufficient corrosion protection cannot be provided at cer-
tain interfaces to the transformer when the device leaves the factory.
Figure2: On-load tap-changer head
1 Sealing surface on piping connec-
tion flange
3 Contact surface on on-load tap-
changer head
2 Air-vent valve 4 Through-holes
The sealing surfaces on the piping connection flange are zinc-plated ex fac-
tory. The through-holes are zinc-plated and partially painted.
The contact surface of the on-load tap-changer head is primed ex factory.
The through-holes are primed and partially painted.
The transformer manufacturer is responsible for the design of the mating
surfaces on the transformer and piping and that of the screw connections
needed for these attachments.
1. Provide suitable sealing to prevent electrolytes from entering sealing sur-
faces and holes.
2. Design screws, washers, nuts etc. in A4 in accordance with ISO 3506-1/
ISO 3506-2 standard.
3. If the painted surfaces are damaged, note repair instructions. These can
be requested from Maschinenfabrik Reinhausen GmbH's Technical Ser-
vice department.
2.6 Personnel qualification
The person responsible for assembly, commissioning, operation, mainte-
nance and inspection must ensure that the personnel are sufficiently quali-
fied.
Table of contents
Other MR Transformer manuals
Popular Transformer manuals by other brands
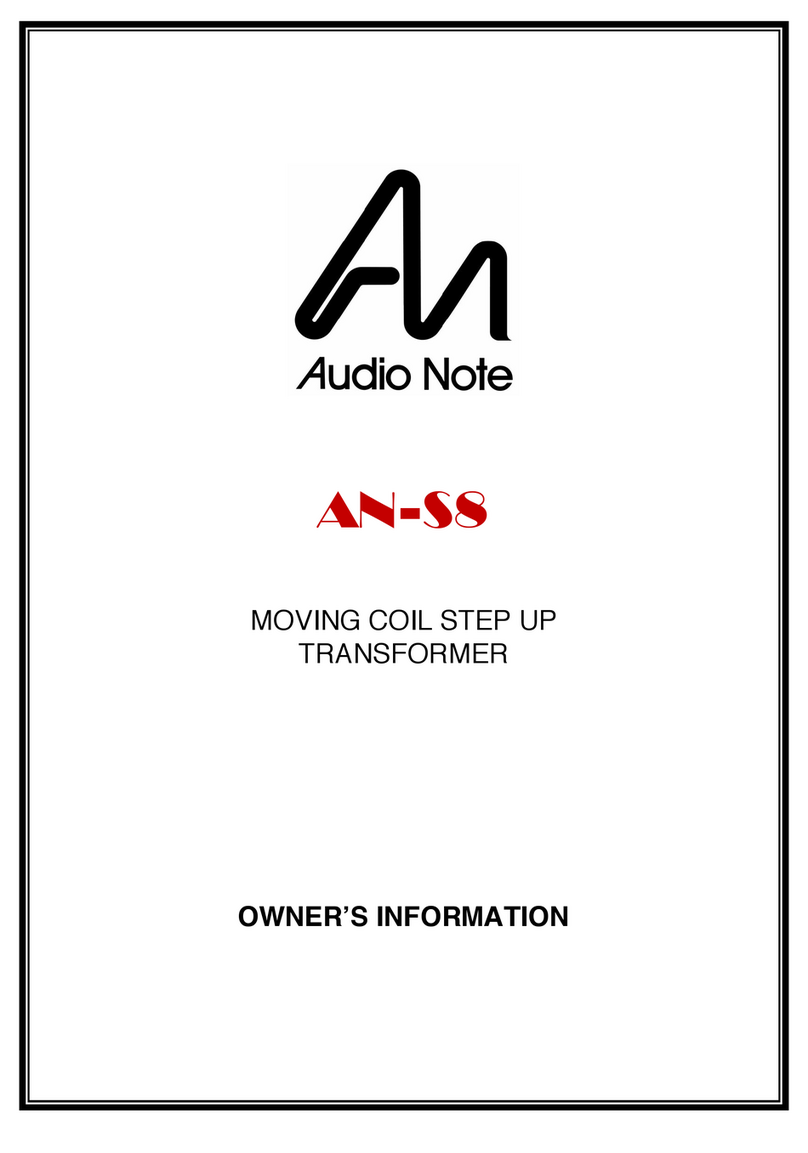
Audio Note
Audio Note AN-S8 Owner's Information
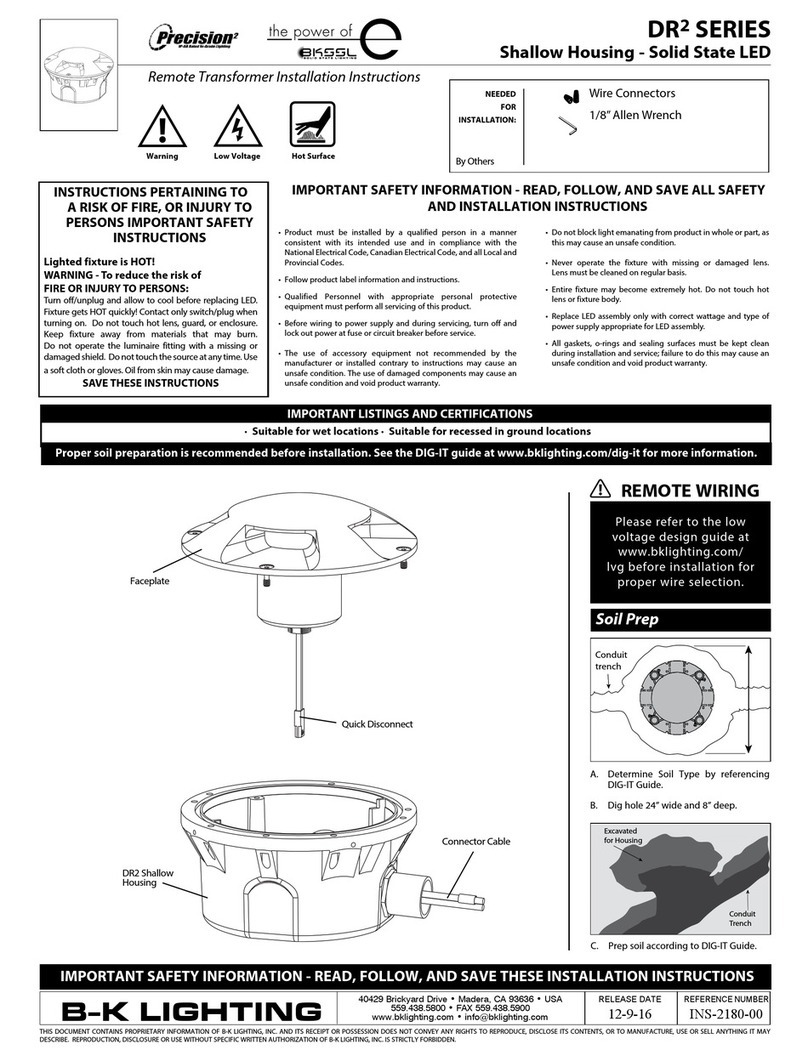
B-K lighting
B-K lighting BKSSL Precision2 DR2 Series installation instructions

LGB
LGB 50080 Instruction
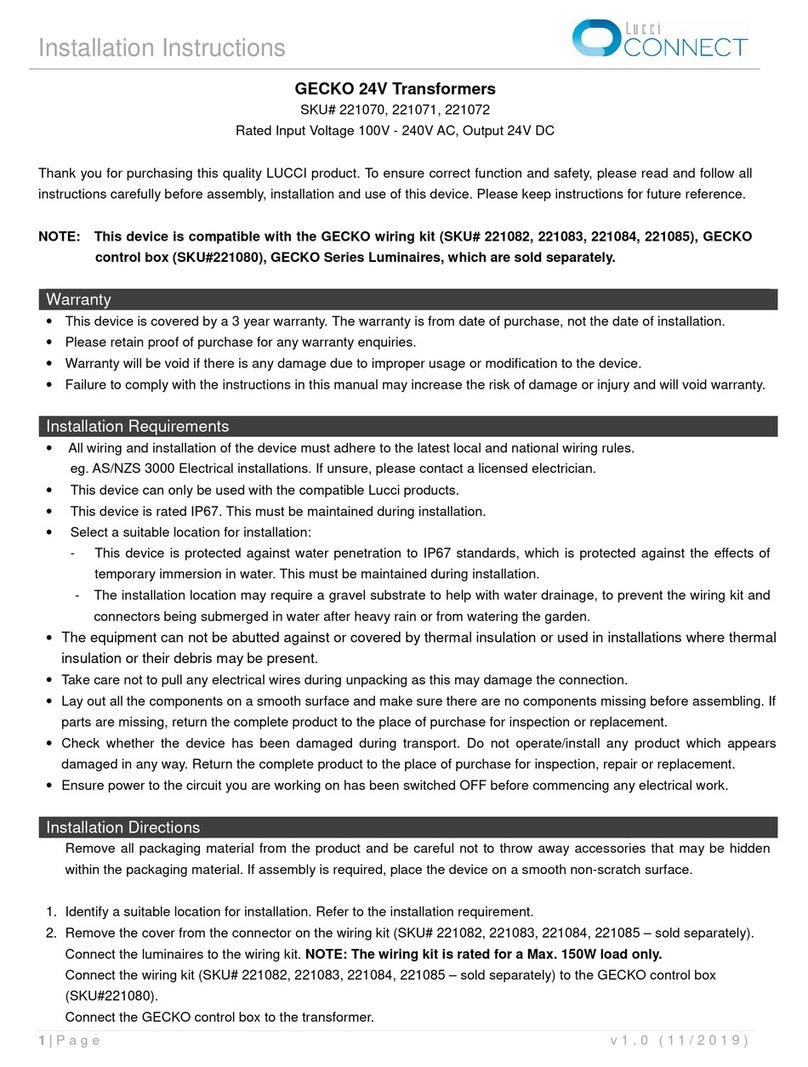
Lucci CONNECT
Lucci CONNECT GECKO 221070 installation instructions
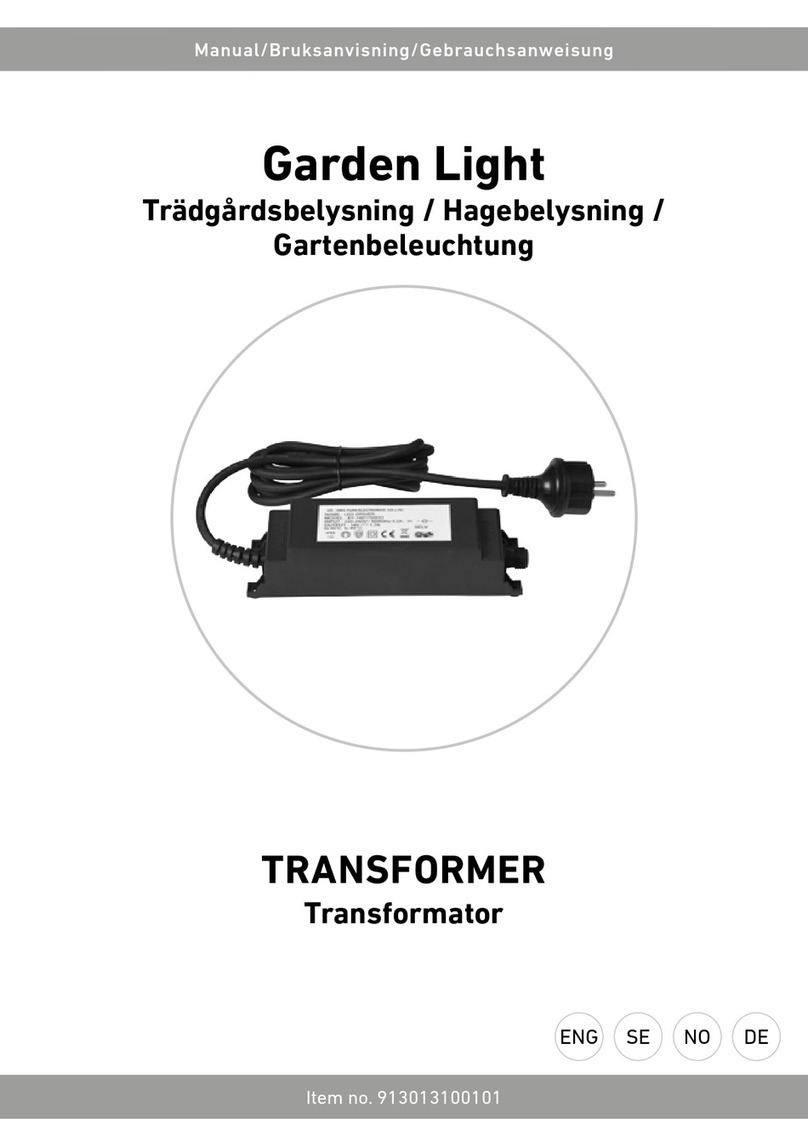
RUSTA
RUSTA 913013100101 manual
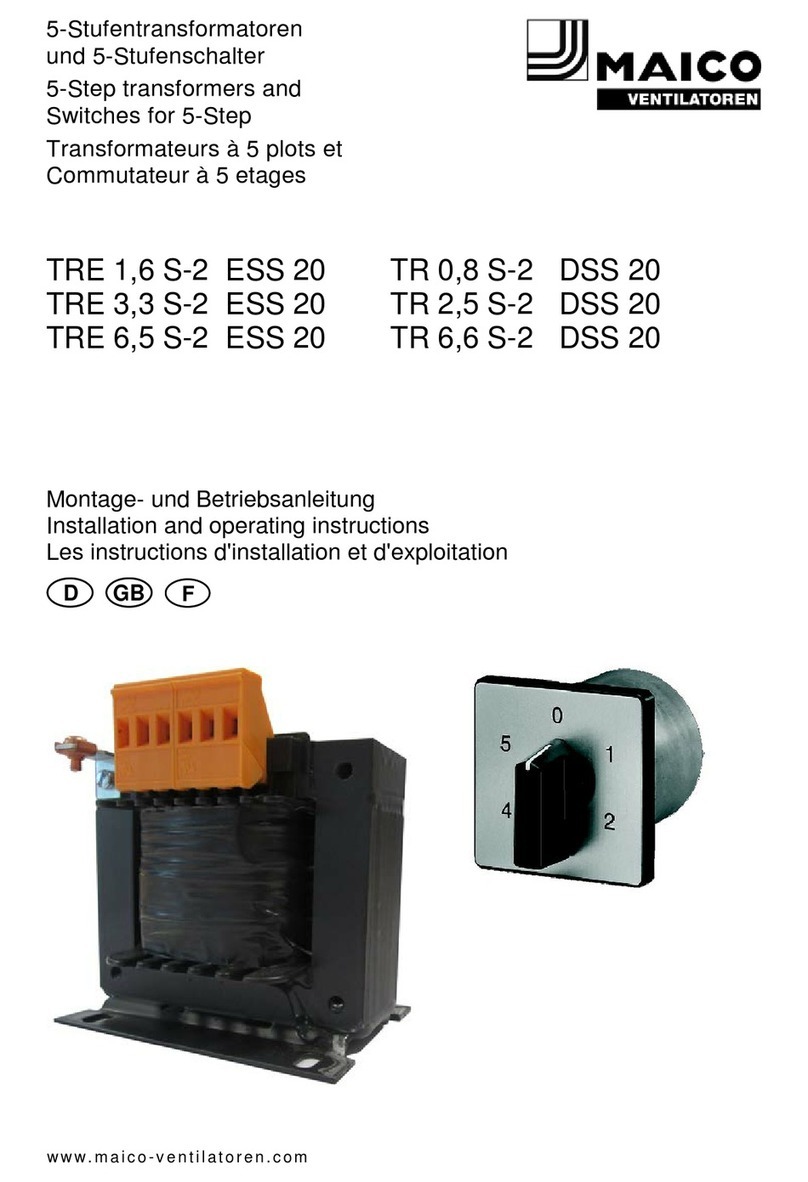
Maico
Maico TRE 1,6 S-2 ESS 20 Installation and operating instructions