Mueller HYDRO GATE HG561 Instruction Manual

CAUTION:
This manual describes the recommended procedures for installation, adjustment,
operation and maintenance of Hydro Gate gates. When it is used in conjunction with
installation drawings that have been supplied by us, this manual will be sufcient for
most installations. Proper care and precautions must be taken in handling and storing
the gates at the delivery site. For further details on the handling, storing, and installation
of a specic project, contact the Hydro Gate headquarters.
Precise and accurate installation is critical to satisfactory operation. We assume no
liability, expressed or implied, for interpretation of the contents of this manual. If
you have any questions concerning the interpretation of the contents of this manual
or installation procedures in general, you should contact the Hydro Gate facility in
Colorado. We expressly disclaim all liability, expressed or implied, for faulty installation
of any gate or associated equipment and for any direct, consequential, or incidental
damages that may result.
F 13922 1/19
TABLE OF CONTENTS PAGE
General Information 2
Installation 2-8
Operation 9
Maintenance 10-11
Leakage / Troubleshooting 12-13
Storage 13
Parts 14-16
HG561 Fabricated
Slide Gates
OPERATING INSTRUCTIONS MANUAL

The purpose of this Installation,
Operation, and Maintenance
Manual is to provide information
on the correct procedures for
installation, adjustment, operation,
and maintenance of Hydro Gate
HG561 Fabricated Stainless Steel
Gates and their component parts.
The gate, lift, and accessories were
accurately machined, fabricated,
assembled, adjusted, and
inspected before leaving the Hydro
Gate factory. For best results, read
and follow the applicable parts of
this Manual carefully, including
thorough cleaning and lubrication
of moving parts and final wedge
adjustment. If the gate will not be
installed immediately, consult the
long-term storage instructions.
NOTE: DO NOT disassemble the
gate or lift for installation.
Safety Precautions
To help ensure your workers’
safety, We recommend the
personnel responsible for
installation, operation, and
maintenance of the gates for
this project read and study the
instructions and precautions in
the Installation, Operation, and
Maintenance Manual, and follow all
directions carefully. The following
are major items associated with
safe installation, operation, and
maintenance of this slide gate.
• DO NOT operate equipment
before carefully reviewing the
Installation, Operation, and
Maintenance Manual.
• Always use proper equipment
when lifting or unloading heavy
items.
• DO NOT stack equipment too
high for storage. Always use heavy
wood blocking between equipment.
Refer to the storage instructions
contained herein for details.
• Adequately support and brace
2
OVERVIEW
INSTALLATION
Note: Installation and/or
operation of the gate lift and stem
without proper lubrication will void
the equipment warranty. Thorough
cleaning of the stem and sealing
surfaces is required before gate
operation. Details are described
in the appropriate sections of this
Manual.
Spare Parts
We do not recommend the stocking
of spare parts. If spare parts are
required see “Spare Parts List”
(page 14). Replacement parts are
readily available for worn or broken
parts. Contact us or our Hydro Gate
representative in your area.
Special Tools
Special tools are not required
to operate and/or maintain the
heavy items during placement of
equipment.
• Wear proper personal protective
equipment (PPE) and clothing when
working on or around gates, (e.g.,
hard hats, heavy boots, safety
glasses, and breathing apparatus,
if necessary).
• NEVER place bodily obstructions
in the path of moving parts. When
operating gates and accessories,
stand clear of all moving parts.
Serious injury can result from
contact with moving parts.
• Use caution when performing
operations and maintenance.
Watch for loose or damaged
parts. Stop all functions until any
damage has been corrected.
• DO NOT use any mechanical
devices other than the factory-
supplied equipment to operate the
gates for this project.
• DO NOT attempt operational
procedures other than set forth
in the Installation, Operation and
Maintenance Manual.
equipment supplied by us on this
project.
Parts List
Prices for individual parts and/or
assemblies may be obtained from
Hydro Gate sales at the time that
they are needed.
Disassembly
We do not recommend the
disassembly/reassembly of any of
the equipment on this project.
Emergencies
Emergency/shutdown procedures
do not differ from normal operating
procedures for this project. If
you should need assistance,
please contact the Hydro Gate
Field Service Department at
303.288.7873.
• Contact your Hydro Gate
representative with any questions
you may have regarding safety in
installing, operating, and handling
Hydro Gate products.
To Ensure Proper Installation
We recommend that personnel
study these instructions and
installation drawings and follow
the installation directions carefully.
This gate is shop adjusted, quality
checked, and designed for low
leakage. Attention must be given
to proper storage, careful handling,
and accurate location of embedded
items for this gate to operate as
designed.
1. Read and follow the Installation
instructions and drawings in this
Manual.
2. Carefully inspect the gates
and accessories when received,
before unloading trucks or cars.
Report ALL shortages or suspected
damage by marking the bill of
lading and receiving reports at this
time. Latent shortages must be
HG561 FABRICATED SLIDE GATE
General Information / Installation

reported in writing within 30 days
of shipment.
3. Store gates evenly on planks or
timbers. Even large fabrications are
subject to permanent warpage if
unevenly blocked during storage.
4. Support full length of stems and
protect threads during storage and
handling.
5. Accurately locate and brace
embedded items during placement
of concrete.
6. Contact your Hydro Gate
representative with questions
regarding this gate. We have 100
years combined experience in the
water control industry.
7. DO NOT disassemble the gates
for installation.
8. DO NOT allow excess concrete
to overlap gate thimble or frame.
9. DO NOT Tighten nuts for studs
unevenly, or try to pull a gate frame
tightly against an uneven wall
surface. This, in most cases, will
cause excessive leakage.
10. DO NOT operate gates with
concrete and debris on them.
11. DO NOT operate gate stem dry
(without grease).
Gate Mounting
HG561 Fabricated Stainless Steel
Gates are most commonly mounted
on stud anchor bolts and grout
pads; however, they may also be
mounted on a fabricated thimble
or flange or on machined flanges
and thimbles. The gate flange
is not machined. A thick layer of
hard setting mastic is required
between gate and the thimble or
pipe flange. Recommended mastic
is polyurethane sealant such as
Sika-Flex 1A or equivalent. See
manufacturer requirements for
curing. Fast cure polyurethane
sealants, such as Loctite marine
grade, are available. They are a
good alternative; however, their
fast setting property requires
quick, well-planned installation and
cleanup of hardened material is
difficult.
3
Foam (Polyurethane) gasket may
also be used. Consult the Hydro
Gate engineering department for
additional information.
NOTE: Mastic is not furnished
by us.
Flanges for gate mounting must be
flat (non-warped) within +/- 1/16”.
The gate can function with some
twist/warp/non-flat conditions. The
larger the gate, the more out-of-
plane conditions can be tolerated.
Consult factory for extreme limits.
Mounting the Gate on Concrete
Surface with Adhesive Type Stud
Anchors
1. Use only adhesive-type or
epoxy-grouted studs. Mechanical
wedge studs are not recommended
and gate performance cannot be
guaranteed with wedge-type studs.
We usually furnish the all-thread
studs but does not furnish the
adhesive capsules or cartridges.
IMPORTANT: Adhesive such as
Hiti HY200 or HIT-RE 500-SD
are not supplied by us due to its
stringent storage requirements
and limited shelf lifetime.
2. Accurately layout positions
of studs or use the gate as a
template.
3. Drill holes to diameter and depth
required for size studs used. If
rebar is encountered during drilling
causing an impossible completion
of hole, consult the owner’s site
engineer for instructions on how
to proceed; cutting of rebar may
not be permitted. In some cases,
a new hole (or holes) may be
field drilled in the gate frame to
compensate for out of position
studs. Consult the Hydro Gate
engineering department for advice
and limitations.
4. Blow and brush all holes clean
according to adhesive system
instructions and place studs
with adhesive. Maintain proper
projection and alignment and allow
sufficient cure time, particularly in
cold weather.
CAUTION: Because of the
dynamic/reversing load on the
gates involving unseating or
seating loads and the use of front
and back nuts for alignment,
wedge studs are not satisfactory
since they require tension in
them at all times to “grip” the
concrete. The loss of “tension” in
the wedge stud may cause them
to fail.
5. Two nuts are provided for each
stud bolt (Fig. A). These are for
precise plumbing and alignment
with a nut on both sides of the
gate flange.
HG561 FABRICATED SLIDE GATE
Installation
A.
Slide Plate
Adjusting Bolt Assembly
Gate Frame
Side Seal Retainer
Grout
Epoxy Anchor
Side Seal
Load Pad
Top Nut
Adjusting Nut
TOP VIEW OF STUD BOLT MOUNTING
!

4
6. Check the placement and
plumbness of pattern of stud bolts.
Fit check the gate onto stud bolts.
Perform minor bending adjustment
to studs, as needed.
7. Clean stud bolt threads. Apply
anti-galling compound (anti-seize)
and run one nut on each stud up to
or near the concrete.
8. Establish a plumb/vertical plane
with back nuts starting with the two
upper corner stud bolt back nuts.
Leave room for grout and some in/
out adjustment from the wall. With
plumb line or builder’s level and
straight edge, bring all other nuts
to a vertical plane established by
upper corner nuts.
9. Being sure flange of gate is
clean, place the assembled gate
over/on the stud bolts. Run the
front nuts on stud bolts until they
touch the gate flange.
10. Take note of how well the
gate frame fits the previously
established flat vertical plane of
back nuts on studs. Some variation
of the free-hanging gate flatness
is normal (1/8” in small/medium
sized gates; 1/4” in large gates).
11.Tighten the front nuts on side
studs until frame contacts back
nuts. Tighten the frame flange
between the two nuts.
12. Note that the gate slide should
be in tight contact with seals at
horizontal frame members. Some
curvature or non-flatness of frame
member may be required for good
seal contact with the slide. Tighten
front and back nuts up to the
flange while observing that no gap
between the slide and horizontal
frame seal exists or develops.
13. Grouting of gate frames is not
recommended until after the lift
and stem has been installed and
gate has been cycled open/close
to ensure smooth operation.
14. After operation has been
verified, carefully pack the space
between the gate and the wall
around the opening with “non-
shrink” grout. Alternatively, the
space may be formed and slurry
grouted with concrete. Grouting
behind the frame guide (legs)
extensions is not necessary.
15. Be sure the frame extension
stud bolts are in place and front
and back nuts are tight and hold
the frame stable.
Wall Thimble Installation
1. Place the wall thimble in the
correct position in the forms
and block it in this position. The
top centerline of the thimble is
stamped on its flange face. The
bottom centerline is also marked.
2. Plumb the front face of the
thimble using the marks indicating
top and bottom centerline. This
face should be plumbed with
respect to final location of the
gate, stem, and lift. “Plumb” is a
relative term, more precisely the
thimble gate and operating system
consisting of stem, stem guides
and lift must be in close co-linear
alignment. Alignment tolerance
is +/- 1/8” over the travel of
gate (gate opening height). True
or perfect plumb is primarily for
aesthetics and simplification of
installation and alignment.
3. Studs furnished for attaching
the gate may be used in the
attachment of the thimble to the
forms. If these studs are not used,
threaded holes in the thimble must
be plugged to prevent concrete
from entering them.
4. Use timbers or other bracing
material on the inside opening of
the thimble while concrete is being
poured (Fig. B).
NOTE: Use extreme care in
placing of these supports to
prevent warping of the thimble.
5. Pour concrete, being careful not
to tilt the thimble from its original
position in the forms.
6. Remove forms and bracing.
Installation on Thimble or Flange
with Machined or Non-machined
Face
1. Clean face of thimble with
scrapers and stainless steel wire
brush so no sand, concrete, dirt, or
foreign material are present
(Fig. C).
2. Check for plumb, flatness, and
warp with builder’s level or straight
edges. Flatness should be within
+/- 1/16”. If not, consult the
Hydro Gate engineering department
or field service department for
recommendations.
3. Install mounting studs in
thimble/flange face.
5
HG561 FABRICATED SLIDE GATE
Installation
B.
FRONT AND SIDE VIEW OF THIMBLE
SHOWING BRACING
Provide timber blocking as
required to support thimble
during pouring.
Plumb thimble in forms
using top and bottom.
C.
FRONT CROSS SECTION OF “F” WALL
THIMBLE – TYPICAL INSTALLATION
Clean Front
Machine Face of Thimble
Tapped Hole in
Thimble
Concrete
or Grout

5
4. Fit check the gate onto the
thimble to be certain the gate sits
well on its face without obstruction
from surrounding concrete.
5. Apply heavy layer of hard-setting
mastic so entire contact face
of frame flange will be covered.
A layer 1/16” to 1/8” thick is
usually sufficient. Excessive
thickness results in more cleanup;
too thin may result in flange
leaks. Recommended mastic is
polyurethane sealant such as
“Sika-Flex 1A”, “Bostik 920 marine
grade polyurethane”, “Devcon
Flexane 80 trowelable grade
putty”, or equivalent. Asphalt (tar)
mastic may be used in lieu of
polyurethane except in potable
water.
NOTE: See manufacture
instructions for proper cure times
before submerging. Fast cure
polyurethane sealants such as
“Bostik 920 Fast Set” or “ADCO
Fast Cure” are available. These
are a good alternative, however,
their fast setting property requires
quick, well-planned installation
and cleanup of hardened material.
Rubber gaskets may be used for
thimble mounting in conjunction
with sealants consult the Hydro
Gate engineering department for
additional information.
NOTE: Mastic is not supplied
by us.
6. Mount the gate over studs,
install nuts and tighten. Anti-seize
compound is recommended. See
Torque Table for approximate bolt
nut tightening. Precise torque
tightening is not required.
7. Check the squeeze-out of mastic
on the inside and outside of the
flange and clean off excess. No
squeeze-out indicates insufficient
mastic and likelihood of future
leak.
8. Allow sufficient cure time of
mastic before applying water
pressure to the gate. (see
manufacturer instructions).
Installation Of Flush Bottom
Closure Gates
Gates that are to be installed with
bottom frame members embedded
in the concrete are furnished with
a rubber seal attached to the
invert of the gate frame (Fig. D).
The top surface of the rubber seal
is installed at the same elevation
as the invert of the gate opening.
Refer to the Hydro Gate installation
drawing.
1. Form a recess for the bottom
of the gate in the original pour
of concrete. The dimensions of
this recess are shown on the
installation drawing.
2. After the forms are stripped,
install the gate as shown for
other types of installations in this
Manual.
3. After installation is completed,
non-shrink grout in around seals
and frame. Ensure the flush
bottom seal is free and clear of
any foreign material.
HG561 FABRICATED SLIDE GATE
Installation
TABLE 1. Torque for Tightening Nuts or
Hex Bolts Used for Assembly
CAP SCREW
DIAMETER
TORQUE TO BE
APPLIED (lbs-ft)
3/8" 20
1/2" 45
5/8" 75
3/4" 125
7/8" 200
1" 300
1-1/8" 450
1-1/4" 500
1-1/2" 600
D.
Adjusting Nut
Grout
Gate Frame
Support Gusset
Epoxy Anchor
Seal Retainer
Retainer Screw
Top Nut
VIEW OF GATE SLIDE AND INVERT SURFACE
Slide Plate
Bottom Seal

6
Installation of Gate Stem and
Guides
1. Install the stud bolts for the lift
and stem guides as shown on the
installation drawings. Check for
proper alignment of the lift, stem
guides, and gate. The lift stem and
gate stem block must be in vertical
alignment within 1/8" per each 10
feet of distance.
2. Provide opening with adequate
clearance in the lift platform for
the gate stem as noted on the
installation drawing.
3. Install stem guide brackets on
studs, but DO NOT tighten nuts.
Leave them loose so the bracket
can be moved for later alignment.
Loosen all assembly bolts
holding the collars to the bracket.
Stem guide collars are 2-piece
construction.
4. When more than one gate is
to be installed, stems may be of
different diameters or lengths.
Stems are marked and/or tagged
for each installation. Separate
the stems per individual gate
installation.
Note: Exercise care when handling
and installing threaded stems;
nicks or burrs will damage lift nut
threads.
5. Insert the stem block into the
gate slide pocket, if applicable.
6. Stems may be in more than
one piece to facilitate shipment
and installation. If two or more
pieces are furnished, they must
be installed in their proper order
from bottom to top to place splices
in correct location so they will not
interfere with the stem guides
when the gate is opened or closed.
Measure the stem section lengths
and install.
7. Lower the bottom section of the
stem into place through the hole
of the gate slide and thread it all
the way into the block and align
the keyways (Fig. E) or insert stem
connection bolt(s).
Note: Immediately insert the key
to lock the bottom section of the
stem to the block. (The key is
omitted on non rising stem gates.)
8. Place all of the succeeding
stem sections. Double-check the
installation drawings to ensure that
the stem guide collars are in the
correct locations. Join together with
splices as provided (Fig. F).
Note: Insert all bolts or keys in
each stem splice immediately
after sections are installed and
aligned to prevent one section
disconnecting from another when
the gate is operated.
9. Immediately before lowering the
lift over the threaded portion of
the stem, thoroughly clean off all
foreign material.
10. Lubricate stem threads with
recommended lubricants. Do not
leave lubricated stem exposed to
contamination before completing
the installation.
Lift Installation and Adjustment of
Stem Guides
1. Clean the threaded section
of the stem, removing all foreign
material, and lubricate with
recommended lubricant as
described in the “Gate Stem and
Guide” section of this Manual.
Note: Operation of the gate
assembly without proper
lubrication of the stem will void
the equipment warranty.
2. Raise the lift and lower it
over the previously installed and
lubricated threaded stem section.
When starting threaded stem into
the bottom of lift nut, care must
be taken to avoid damage to the
threads. Rough handling may result
in damage to the bottom edge of
the threaded lift nut and prevent
the stem from being threaded
into the lift nut freely. Hold the lift
to prevent its rotation. Turn the
handwheel or crank to lower the
pedestal onto its stud bolts.
Note: When all parts are cleaned,
the threaded lift nut will turn onto
the threaded stem with very little
effort.
3. Using shims, double nuts on
studs, or other leveling devices
under the lift, align the centerline
of the lift nut until parallel with the
stem centerline. Vertical alignment
of gate stem and the gate slide
stem block must be within 1/8"
per 10 feet of distance. Tighten
nuts on the studs uniformly.
HG561 FABRICATED SLIDE GATE
Installation
7
STEM CONNECTIONS TO GATE
Key
Stem Block
Stem
E.
STEM WITH SPLICE
Key
Stem
Splice
Stem
Stem
F.

7
4. The crank should turn freely for
two or three turns in each direction
until the clearance between the
top or bottom of the stem block in
the gate slide is taken up. If any
binding occurs during operation
of the lift with the slight vertical
movement of the gate slide, the
stem alignment should be checked.
Slight misalignment will cause
undue wear to the threaded lift
nut. When binding is not caused
by misalignment, recheck to be
certain all threads on the stem and
in lift nut are clean.
5. Place the two-piece stem
guide collars around the stem
above each bracket. Place the
bolts through the projection of
the bracket and the ends of the
collars. DO NOT tighten the bolts.
6. Grout under the lift (if required).
After the grout has set, tighten the
stud bolts uniformly.
Note: Before opening the gate,
clean all grout, stones or other
foreign material from the top of
the gate (or bottom in the case
of a downward opening gate),
and ensure gate stem and lift are
properly lubricated.
7. Turn the lift crank or handwheel
to open the gate, until the gate
slide has moved at least 2". The
stem is now in tension. Check the
stem to be certain it is straight.
Tighten the nuts on the studs
through the stem guide brackets,
center the stem guide collars
around the stem, and tighten the
assembly bolts holding the collars
in position on the brackets.
8. Move the gate to its fully
opened position and check the
position of the stems. If the stem
is being deflected by the collars, a
stem alignment problem exists and
must be corrected, indicating the
gate may not be plumb. Consult us
for ways to correct or compensate
for this condition.
9. Lower the gate to fully closed
position. Run the stop nut down
on top of the projecting threaded
stem until it contacts the top of
the lift nut or stem cover holder.
Back the nut up until 1/16" to
1/8" gap appears between the lift
and the stop nut to allow complete
gate closure as sliding and bearing
surfaces wear in.
10. Tighten the setscrews through
the stop nut to hold it in place (Fig.
G & H).
11. Install the stem cover,
indicator, etc., as required.
12. Check to see if the gate slide
is making full contact across the
bottom invert seal.
HG561 FABRICATED SLIDE GATE
Installation
G.
HANDWHEEL AND STOP NUT
Handwheel
Pedestal
Stem Stem Nut
Order ID Tag
H.
REMOVABLE CRANK
Stem Cover Adapter
Stop Nut
Sealed Gearbox
Lift Nut
Cast Iron Pedestal
Revolving Handle
Hand Crank

8
Installation of Tandem Stems
Some gates have wide openings
with relatively short gate heights.
When the installation drawings
show tandem lifts, install each lift
in accordance with the preceding
steps 1 – 5. After each lift has
been installed and each stem is
connected to the gate slide at
the bottom and the lift at the top,
proceed as follows:
1. Turn the input shaft of each lift
in the direction to open the gate
until each stem makes firm contact
with the top of its connection on
the gate slide.
2. Place a level on the top of the
gate slide and move one stem or
the other of the gate up or down
until the slide is completely level.
3. A tandem interconnecting shaft
is furnished to connect the two lifts
and cause them to act in unison
for raising or lowering the gate.
Loosen the fasteners on one of
the jaws of the flexible coupling
and slide it toward the center of
the shaft until the shaft can be
connected between the two lifts.
Complete the connection and
retighten all fasteners.
4. Move the gate slide up and
down by turning the input shaft
of one lift. Ensure the gate is
installed with its top level and that
the gate is moving freely.
5. Complete the installation of
any stem guides, lubricate the
stem, adjust the stop nuts, etc, as
described in the preceding steps
1 – 9 in the section entitled Lift
Installation and Adjustment of
Stem Guides for gates not self-
contained.
Gate Adjustment
This gate is equipped with low-
friction polyethylene (UHMWPE)
seats and guides. The seats
rest on a neoprene (rubber) pad
for cushioned gasketing to the
frame. Sealing at the side is
accomplished by pinching the
seal lips against the slide plate
using the compression of the
rubber gasket pad. Top horizontal
member seal (and also bottom, if
seals are 4-sided) are loaded by
the compression pad and assisted
with ensured hook-type wedges
on medium and larger width gates
(Fig. A & J).
This gate has been factory
adjusted. However, if the shake-
proof nuts have been loosened,
readjustment may be required.
Visual Tightness of the Seat
against the Side
No light should be visible through
the seat or measurable gaps
between the slide plate and the
seat. A .004" gauge may be
used to check the seat gap as a
starting point; however, the best
test and proof of performance
is an unseating hydrostatic
test. This gate is required to
comply with AWWA C561 leakage
specifications.
HG561 FABRICATED SLIDE GATE
Installation
9
J.
Gate Frame
Grout
Anchor
Slide Plate
SIDE VIEW OF BOTTOM SECTION SHOWING SEAL ARRANGEMENT
Wedge Adjustment Bolt
Adjusting Nut
Top Nut
UHMW
Polymer
Seal
Neoprene Load Pad
Cast Stainless Steel Wedge

9
HG561 FABRICATED SLIDE GATE
Operation
General Operation Information
HG561 Fabricated Stainless Steel
Gates are used to control flow of or
retain a volume of water, effluent,
or other fluids. Typical applications
include industrial water treatment
facilities, municipal water
treatment facilities, irrigation,
dams, flood control, and many
other applications that require
tight, low leakage closing.
The simplicity of a slide gate
makes it a popular choice when
designing flow controls. From the
basic hand-cranked manual model
to the microprocessor-controlled,
fully integrated electric slide gate,
actuation consists of the basic
open or closed, or modulating
operation.
Depending on size, most slide
gates can operate without error
in diverse conditions. Some
extenuating circumstances may
include large amounts of ice or
other solids that will obstruct the
travel path of the gate. In most
cases, when the obstruction is
removed, normal operation can be
resumed without adjustment to the
gate.
Slide Gate Operation Procedures
The following sections cover the
general operating procedures
associated with two manual-
operation systems (handwheel
and handcrank). Read and follow
the operating procedures for the
applicable system. If you have
any questions concerning safe
operation of this HG561 Fabricated
Stainless Steel Slide Gate, contact
us immediately.
H2B Series Actuator (Manual
Handwheel)
OPENING – To open this slide gate
observe the direction of rotation
noted on the handwheel. Turn in
the direction of opening until the
desired gate position has been
achieved. Observe the relative
position of the top of the stem in
relation to the Mylar decal on the
stem cover (if equipped.) When
the top of the stem is equal to the
OPEN or 100% indicator the gate
is considered to be FULL open and
should not be opened further.
CAUTION: DO NOT over-open
the gate. Serious damage to the
gate stem and sealing surfaces
can result.
CLOSING – To close this slide
gate turn the handwheel in the
direction opposite of the “Open”
indicator until the stop nut on the
stem is 1/8" to 1/16" from the
top of the lift (see installation
instructions). When the top of
the stem is equal in height to the
bottom/ zero height indicator,
the gate is considered to be
FULL CLOSED and should not be
closed further. Should the gate
or stop nut require adjustment,
refer to the appropriate section
of the Installation, Operation, and
Maintenance Manual or call us
before any adjustments are made.
CAUTION: DO NOT attempt
to adjust the position of the stop
nut to achieve additional closing
stem travel without understanding
the function of the stem, stop nut
and gate closing system. Serious
damage to the gate stem and
sealing surfaces can result.
Manual Hand-Crank
OPENING – To open this gate
observe the direction of rotation
noted on the lift housing. Crank in
the direction of opening. If the gate
has been closed for an extended
period the gate may be difficult to
“unseat.” If several attempts at
turning the wheel to crack the gate
open have no result, apply heavy
pressure and wait for a period of
time. Allow the pressure in the
stem to unseat the gate. Continue
to turn the handcrank until the
desired gate position has been
achieved.
CAUTION: DO NOT over-open
the gate. Serious damage to the
gate stem guides and gate can
result. Do not use excessive
force.
CLOSING – To close this gate
turn the crank in the direction
opposite of the Open indicator
until the stop nut on the stem is
1/8" to 1/16" from the top of the
lift (see installation instructions).
After the gate has been closed as
noted on the indicator, the gate is
considered to be FULL CLOSED.
Then reverse the rotation of the
crank and relieve the pressure on
the stem and lift. Should the gate
or actuator require adjustment,
refer to the appropriate section
of the Installation, Operation, and
Maintenance Manual or call us
before any adjustments are made.
CAUTION: DO NOT attempt
to adjust the position of the stop
nut to achieve additional closing
stem travel. Serious damage to
the gate stem guide and gate can
result.
NOTE: For electrically or
hydraulically operated gates
please refer to manufacturer
Operation and Maintenance
Manuals.
OPERATION
!
!
!
!

10
MAINTENANCE AND LUBRICATION
HG561 FABRICATED SLIDE GATE
Maintenance
General Information
Occasional adjustment and
lubrication of Hydro Gate slide gate
components will be required. The
frequency will depend upon how
often the gate is used, location,
and operating conditions. Periodic
inspection, adjusting, and cleaning
are recommended as conditions at
the site permit.
Lift and Stem Maintenance
Maintenance of the threaded
operating portion of the gate stem
is critical and should be performed
as frequently as the operating
environment requires.
IMPORTANT: Failure to maintain
stem thread lubrication causes
operating difficulties and
premature failure of the lift nut
and stem threads.
Recommended inspection
frequency and procedures are
listed on the maintenance
schedule:
• Initial inspection at the time of
installation and again at the date
of commissioning.
A “cycle” of gate operation is
operation of the gate slide from
closed to open to closed position.
At each inspection, verify the
following items:
• Inspect the stem threads and
lift nut threads for wear and verify
the trueness and dimension of the
thread form. See wear checking
procedure.
• Check the amount and condition
(diary and day) of lubricant
remaining and add if necessary.
• Relubricate if necessary –
threads should be cleaned and
relubricated with fresh lubricant.
More severe conditions or
operating modes require a slightly
different schedule of inspection
and service. For example:
Modulating gates with electric
motor operators may make position
changes several times a day but
seldom go full stroke. There is a
portion of the stem that gets a
lot of use. These stems should
be inspected at least weekly. The
lubricant on the stem threads
should be monitored closely.
As the lubricant is depleted and
becomes contaminated, it should
be cleaned and replenished.
When excess dried grease or other
foreign material is carried into the
threads of the lift nut, extremely
hard operation will result. If serious
binding occurs, the only way to
correct it is to remove the threaded
stem from the lift nut and clean
the thread interior. If this foreign
material is not cleaned from the
interior threads of the lift nut,
heavy pulls on the handcrank or
seizure will result.
Stem threads may be cleaned with
solvent, rags, and brushes. Run
the gate open. While in the process
of opening (running the stem out
above the lift nut), clean off the
old grease. Inspect the threads
for roughness. If the threads
are rough, they may be filed and
polished. Be careful to keep filings
and grit out of the lift nut. Rough
stem threads accelerate the wear
of the lift nut threads.
Relubricate stem threads by
brushing or smearing grease
onto/into the threads as the
gate is closing (the stem is going
into the lift). This puts fresh
lubricant into the lift nut and
carries out the old contaminated
grease. It is recommended that
the contaminated grease be
cleaned from the stem as it exits
underneath the lift where the
stem is accessible from below.
Replenish grease on the underside
stem.
The recommended stem thread
lubricant is Schaeffer’s 238 ultra-
supreme.
Recommended for potable water
is a vegetable-based lubricant,
Shaeffer’s (XXXXXX).
Lifts may be furnished with a
stem lubricator Zerk Fitting which
is located in the “stem cover
adapter” to facilitate lubrication
of stem threads with pressure
greasing equipment. To be
effective, lubricant should be
injected while the stem is moving
through the lift.
Manual crank lifts have sealed
thrust bearing and do not require
lubrication.
Exercise of infrequently operated
lifts and gates is recommended.
A Semi-annual (every 6 months)
exercise will ensure the gate
is operable when needed and
the lubrication condition will be
maintained.

11
HG561 FABRICATED SLIDE GATE
Maintenance
Removal of the stem nuts for
thread inspection or check with
the wear checking procedure of
frequently modulated gates is
recommended.
Lubrication Equivalents
We consider any of the following
greases/lubricants to be acceptable:
• Fiske Brothers “Lubriplate” No.
630 AAA or AA
• Sta-Lube “Sta-Lube” No. 3121
• Conoco “All Purpose Superlube”
• Texaco “Multi Fak Heavy Duty”
No. 2
• Shell Gadus Grease (formerly
known as Alvania)
• Mobil “Mobilux EP2"
• BP Energrease LS 2
Replacement or spare nuts
can be ordered from us. Spare
parts are usually not needed or
recommended, because they are
readily available on short notice
We recommend the following pipe
thread sealants with Teflon:
• La-Co Slic-Tite Paste
• Dayton Pipe Thread Sealant with
Teflon
• McMaster-Carr Pipe Thread
Sealant with Teflon
• Any other commercially available
pipe thread sealants containing
Teflon
from us. In those cases where
equipment operation or downtime
is critical and the gate is operated
extremely often, a spare lift nut
may be pertinent to
have on hand.
For potable water treatment plants,
we recommends using a vegetable-
based lubricant such as:
• Lubriplate Super FML-2
• Rocol Foodlube Multi-Paste
(European product)
• Petro-Canada Purity-FG
Activity Frequency Lubricant
General Cleaning and Inspection As often as conditions require or
permit, or every 6 months.
N/A
Stem Thread and Lift Nut Wafer
Inspection
Initial inspection after 10 cycles.
Subsequent inspection after 25
cycles. Operational inspection after
each 50 cycles, or every 6 months.
N/A
Stem Thread Lubricant and Cleaning
Inspection
Every 3 months, quarterly, or 6
months. Clean grease if dried or
contains foreign material every 6
months. More frequent intervals
required for modulating duty.
Schaeffer's 238 Ultra-Supreme
TABLE 2. Maintenance Schedule and Lurbication Summary –HG561 Fabricated Slide Gates and Manual Lifts

12
LEAKAGE
HG561 FABRICATED SLIDE GATE
Leakage / Troubleshooting
The most frequent cause of excess
leakage through a newly installed
gate is improper installation and/or
failure to make final adjustments
to the gate before operation.
When you encounter this problem,
first verify that the Hydro Gate
installation instructions have been
carefully followed and that final
adjustments and greasing have
been accomplished. If not, then
follow step-by-step the adjustment
procedures as outlined in the
appropriate instructions.
Another important check is
to ensure the gates were not
disassembled for installation. The
outside of our installation booklet
states, “DO NOT DISASSEMBLE
GATE FOR INSTALLATION”. This
is repeated in the text of this
Installation, Operation, and
Maintenance manual at several
critical locations. Occasionally,
we still find that gates are
disassembled for easier handling,
painting, etc. When it is absolutely
necessary to partially disassemble
a gate or remove the slide to
facilitate installation, use extreme
care in handling the parts,
particularly the frame. As pointed
out above and in our installation
instructions, the amount of
leakage through the gate is highly
dependent upon the quality of the
installation.
CAUTION: Without the slide
in place, the frame is very fragile.
We cannot be responsible for
performance problems caused by
rough handling and damage to
gate parts.
AWWA C561 standard for
fabricated slide gates for seating
and unseating head is 0.1 gallons
per minute per foot of sealing
perimeter. A correctly installed
and adjusted HG561 Fabricated
Stainless Steel Gate are designed
to meet or exceed the allowable
AWWA leakage rate.
Troubleshooting Tips
Most fabricated slide gates depend
on water pressure with a slight
deflection of the gate slide to seal.
Proper installation and cleaning of
seating faces are still necessary
for the gate to be as watertight as
possible.
Excessive Localized Leakage
Check by opening the gate slide
to its FULL UP position. Use thin
wire, string, or straight edge to
check the gate frame. Stretch
the wire along each side. If there
is significant (1/32" or more)
variation in the seating face,
excess leakage will result in
those locations where warpage
has occurred. Also, stretch the
wire corner-to-corner across the
opening. If the strings do not touch
at the center, then one corner, or
the other, has been pulled back
considerably from the plane. To
repair this faulty installation, it is
necessary to loosen bolts, push
the frame out as required and align
it before tightening or regrouting.
Dirty Seating Faces
Excess leakage can also be caused
by foreign material on seating
faces of the gate frame or slide.
Check for drops of paint, cement
runs on seating faces, or other
construction grime. To correct,
remove foreign material from the
perimeter of the seating faces on
both slide and frame, and reseat
the gate.
Excessive Leakage near Top of
Slide
If leakage occurs primarily at
the top near the stem, there is
probably excess compression in
the stem, which is pulling the
gate slide from its frame. Check
by turning the handwheel or
handcrank in the direction to open
the gate. When excess pressure
on the stem is removed, the slide
will spring back into position.
Reset the top nut, and refer to
Electrical Actuator Operating and
Maintenance Manual to adjust
torque and limit switches as
needed.
Excessive Leakage near Top of
Slide, Frame Not Warped
If leakage occurs primarily at the
top and the slide is not warped
or pushed out of position, then
ensure the top frame member is
not pulled against the concrete.
This is most likely on gates wide
enough for expansion studs in
the top frame member. To correct
misalignment, loosen the bolts into
the cinch studs and shim behind
the top frame member to push
it away from the concrete. Use a
straight edge or thin wire stretched
along the upper frame member to
set the member straight. Check
seal contact or fit with the slide
before regrouting. This space may
also be packed with polyurethane
sealant or epoxy grout.
Leakage across Bottom of Flush
Bottom Gates
If a sheet of water is coming
from the bottom of the gate, the
gate is not completely closed.
To completely close the gate,
the stop nut or limit switch may
need to be reset. When properly
closed, the slide will be embedded
approximately 1/16" into the flush
bottom seal and a .005" gauge will
not fit between the flush bottom
seal and the bottom of the slide.
Use of a flashlight or a trouble
light on the opposite side will also
indicate if good contact is being
made.
Excessive Leakage through Seats
Top and Sides
This indicates that either the
cover bar or hook wedges are too
loose or the gate has damaged
seats. For the loose fitting
components simply re- tighten and
for the damaged seats attempt
blending localized damage; tighten
adjustment nuts and wedges;
!

replace seats and carefully fit and
seal the joints.
Stem Bends when Gate Is Closed
(Hand-Operated Lifts)
1. Ensure stem guide collars are
properly located to hold the stem
in alignment. Bolts on collars must
be tightened so the collar is not
slipping on the guide bracket.
2. Ensure stem guides are all
located properly. If the spacing
exceeds that shown on the
installation drawing, the stems may
be deflecting before the gates are
tightly closed.
3. If stem guides are correctly
located and collars are tight, then
the load being applied to the stem
by the lift is in excess of that
needed to close the gate, or the
load recommended for a particular
stem size. Reset the stop nut to
prevent an excess load from being
applied to the stem after the gate
is closed.
Long-Term Storage Instructions
for HG561 Fabricated Gates, Lifts,
Stems and Accessories
1. Gate assemblies shall be stored
horizontally and flat, with the
back side (flange side) down. The
storage area must be flat, graded,
comprised of compacted soil,
concrete, or asphalt.
2. Place timber, minimum 4" x 4",
to provide substantially complete
perimeter support under the gate
frame assembly. Longitudinal
timbers, spaced a maximum of 4',
may also be used.
3. Stacking of gates is permissible.
The stacked height should not
exceed 3/4 of the bottom gate’s
width or height. Stack gates
of different sizes in a pyramid
fashion. DO NOT stack large gate
on top of smaller gates.
4. Stacked gates should be
separated with timber. The
separating timbers should form
Excess Force Is Required on
Handwheel or Crank
1. Ensure the stem is lubricated as
recommended.
2. If a simple application of
lubricant does not appear to solve
the problem, check for foreign
material jammed in the nut threads
by either disassembly or working
back and forth with generous
application of penetrating oil and
grease.
3. If the stem is properly greased
and the lift nut does not appear
to be dirty or binding, ensure the
stem, stem guides, and lift are
in proper alignment. On most
installations, the stem will be
installed in the vertical position. A
carpenter’s level can be used to
verify that it is in vertical plane in
both directions. Check for binding
through individual stem guides.
Check the pedestal to ensure it is
vertical in both directions and the
a flat and level base for the gate
above.
5. Wall thimbles may be stored
similar to above. They may be
stored with machined flange face
up or down. Substantial level
blocking is essential. Uneven
support of gate assemblies and
thimbles causes the gate or
thimble to warp and voids the
manufacturer’s warranty.
6. Store the lift assemblies either
upright with plastic plugs/caps in
place to keep dirt out of the nut
threads or leave in original shipping
cartons. DO NOT store the lifts
directly on the ground.
7. Stems and stem covers should
be stored horizontally on timbers
spaced 4 to 8 feet apart. Protective
sleeves should be left on all stem
threads and stem covers.
8. Miscellaneous accessories and
hardware should be stored off the
ground.
stem threads are straight through
the lift nut.
4. In locations where the stem is
not installed vertically, such as
on the face of a dam, alignment
can be checked using a thin wire
stretched tightly between the top
of the slide and the bottom of the
lift. Realign by adjusting the stem
guides and/or shimming one side
of the lift as required.
5. Check the frame guide grooves:
Remove any foreign material,
loosen if necessary, reposition,
or replace if rolled over, torn, or
wadded up.
9. Bronze stem blocks, wedges,
lift nuts, and stainless steel
accessories are targets for theft
and resale as scrap. Report all
shortages at once and note on
shipping papers. We cannot be
held responsible for theft and loss
of equipment stored on the job
site.
10. Inside dry storage is the
best for all equipment. Covering
equipment stored outside with
tarpaulins is recommended to
minimize degradation of paint from
rain and sunlight, until finish paint
is applied. Uncovered outdoor
storage may result in staining of
painted surfaces from rain and
sunlight.
NOTE: The Hydro Gate standard
warranty applies to this order, and
can be found at www.hydrogate.
com/support.
13
HG561 FABRICATED SLIDE GATE
Storage
STORAGE

14
PARTS LIST
HG561 FABRICATED SLIDE GATE
Parts
ID DESCRIPTION MATERIAL QTY.
1Frame Weldment Stainless Steel 1
2 Load Pad Neoprene 1
3 Bottom Seal Neoprene 1
4 Left-Side Seal UHMW 1
5 Right-Side Seal UHMW 1
6 Top Seal UHMW 1
7 Bottom Seal Retainer Stainless Steel 1
8 Side Seal Retainer Stainless Steel 2
9Side Weldment Stainless Steel 1
10 Top Wedge – 4
11 Top Washer Plate – 4
12 1/2" Locking Hex Nut Stainless Steel 8
13 5/8" Locking Hex Nut Stainless Steel 20
14 3/8" x 2" Hex Bolt Stainless Steel 4
15 3/8" Jam Nut Stainless Steel 4
16 3/8" x 1-1/4" F/H Screw Stainless Steel 7
6
10
8
1
14
15
16
7
3
13
2
11
4
12
9
5
SPARE PARTS
How To Order Replacement Or
Spare Parts
Parts may be ordered from your
local Hydro Gate representative or
direct from us.
Please have the following
information:
1. Hydro Gate sales information
found on the blue anodized tag
located on the gate lift or pedestal.
2. The item and/or tag number
must be relayed to us.
3. Description of replacement
part(s).
IMPORTANT: Check size of parts
before attempting to store them.
Spare parts should be stored
in clean, dry and protected
warehouse until ready for
installation.
SPARE PARTS LIST
1 Stop Nut
2 Stop Collar
3 Lift Nuts
4 Stem Cover
5 Thrust Bearing for Gate Lift

6
1
12
14
2
17
4
9
10
8
16
15
7
11
13
19
18
3
20
5
15
PARTS LIST
HG561 FABRICATED SLIDE GATE
Parts - Manual Handwheel Model H2B
ID DESCRIPTION QTY.
1 Lift Nut 1
2Ball Trust Bearing 2
3 Keeper 1
4ID Tag 1
5 Zerk Fitting 1
6 Pedestal 1
7 #11 – 5/8" x 2-1/2" Hex Head Screw 2
85/8" Flat Washer 2
95/8" Lock Washer 2
10 #11 – 5/8" Hex Nut 2
11 18"Ø, 24"Ø, or 30"Ø Handwheel 1
12 #13 – 1/2" Hex Nut 1
13 #13 – 1/2" x 1-1/2" Square Head Screw 1
14 Stop Nut 1
15 #16 – 3/8" x 3/8" Set Screw 2
16 Stem Cover 1
17 Stem Cap Cover 1
18 3/8" Flat Washer 2
19 #16 – 3/8" Hex Nut 2
20 3/8"Ø U-Bolt 1

14
1
19
22
2
21
11
10
18
7
15
13
16
17
3
13
20
24
23
8
12
2
2
3
2
6
5
9
4
MUELLER® | ECHOLOGICS® | HYDRO GATE® | HYDRO-GUARD® | JONES® | MI.NET® | MILLIKEN® | PRATT® | SINGER® | U.S. PIPE VALVE & HYDRANT
1.800.423.1323 – www.hydrogate.com – moreinfo@hydrogate.com
INTERNATIONAL – 1.423.490.9555 – www.mueller-international.com – international@muellercompany.com
Mueller refers to one or more of Mueller Water Products, Inc., a Delaware corporation (“MWP”), and its subsidiaries. MWP and each of subsidiaries are
legally separate and independent entities when providing products and services. MWP does not provide products or services to third parties. MWP and
each of its subsidiaries are liable only for their own acts and omissions and not those of each other. MWP brands include Mueller®, Echologics®, Hydro
Gate®, Hydro-Guard®, Jones®, Mi.Net®, Milliken®, Pratt®, Singer®, and U.S. Pipe Valve & Hydrant. Please see www.muellerwp.com/about to learn more.
Copyright © 2019 Mueller Water Products, Inc. All Rights Reserved. All Rights Reserved. The trademarks, logos and service marks displayed in this document
are the property of Mueller Water Products, Inc., its afliates or other third parties. Products above marked with a section symbol (§) are subject to patents or patent applications. For details, visit www.
mwppat.com. These products are intended for use in potable water applications. Please contact your Mueller Sales or Customer Service Representative concerning any other application(s).
PARTS LIST
HG561 FABRICATED SLIDE GATE
Parts - Manual Lift Type IB
ID DESCRIPTION QTY.
1 Lift Nut 1
2 Thrust Washer / Race 4
3 Thrust Bearing 2
4 O-Ring 1
5 O-Ring 1
6 Spigot Ring 1
7 IB Gearbox 1
8ID Tag 1
9 Pedestal 1
10 5/8" Flat Washer 4
11 #11 –5/8" Hex Nut 4
12 AWWA 2" Square Crank Adapter 1
13 #16 – 3/8" x 3/8" Set Screw 4
14 24"Ø or 30"Ø Handwheel 1
15 Square Head Set Screw 1
16 AWWA 2" Square Crank Nut – 15" 1
17 Square Head Set Screw 1
18 Stem Cover Adapter with Zerk 1
19 Stem Nut 1
20 Stem Cover 1
21 Stem Cap Cover 1
22 3/8"Ø U-Bolt 1
23 3/8"Ø Washer 2
24 #16 – 3/8" Hex Nut 2
Table of contents
Other Mueller Other manuals
Popular Other manuals by other brands
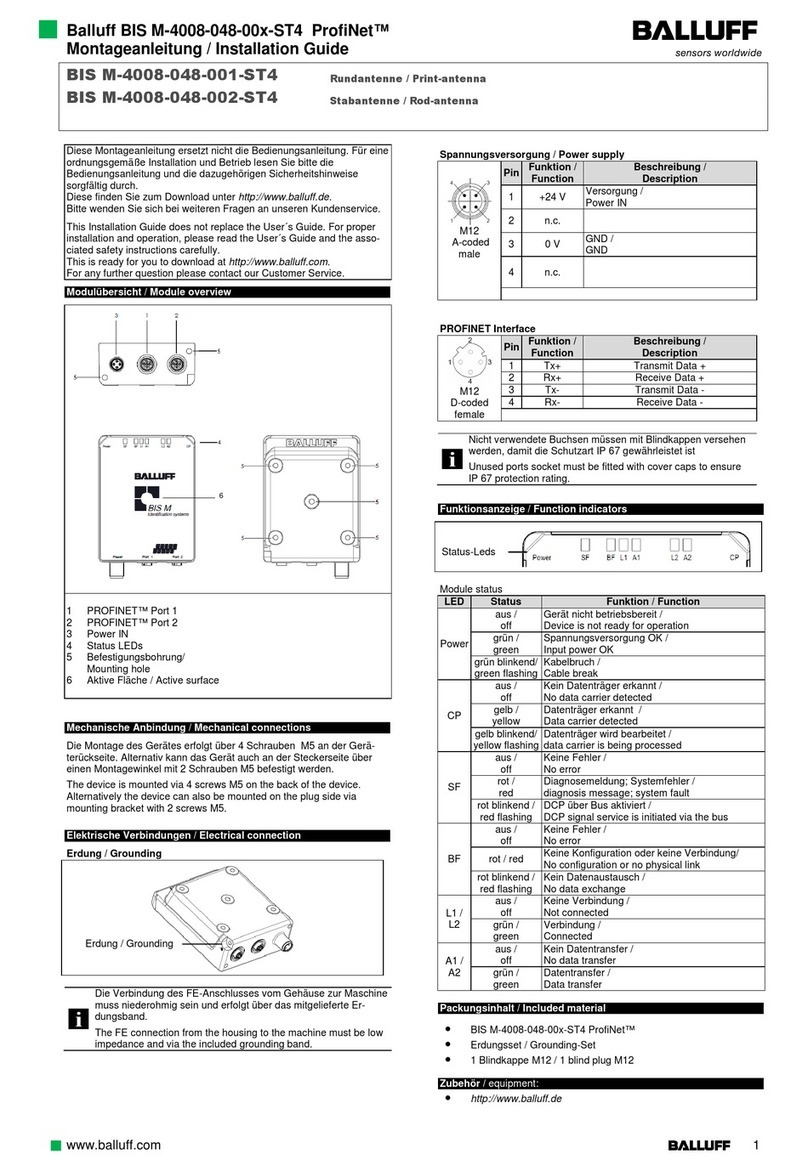
Balluff
Balluff ProfiNet BIS M-4008-048-001-ST4 installation guide
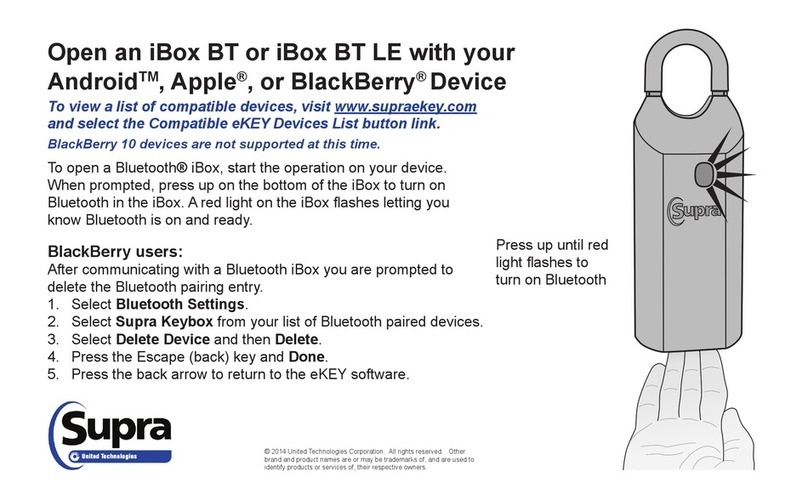
Supra
Supra iBox BT LE manual
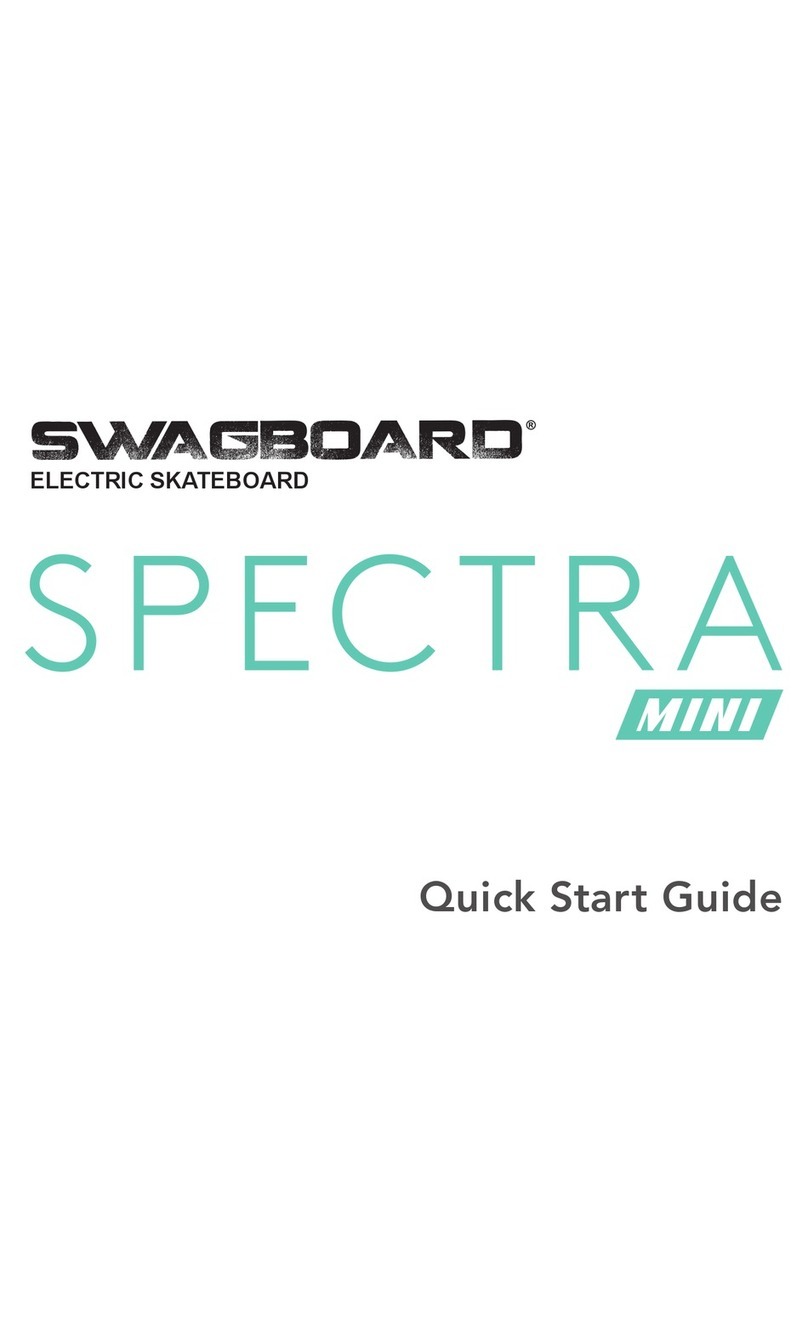
SWAGBOARD
SWAGBOARD Spectra Mini quick start guide
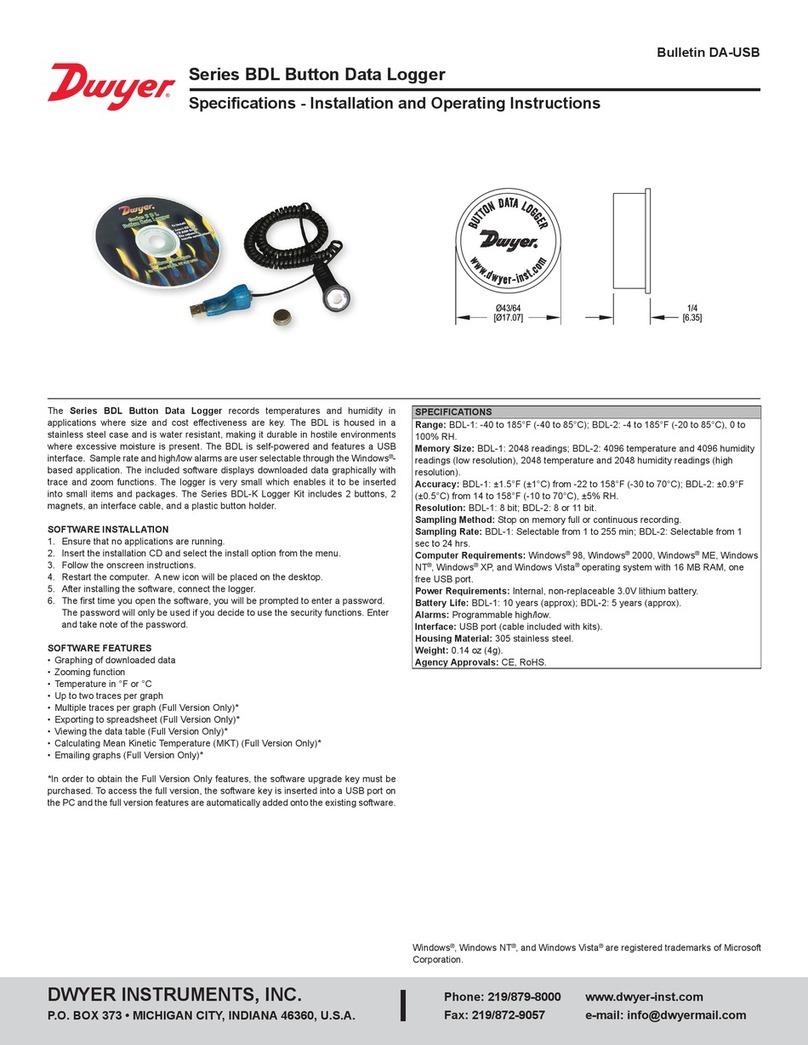
Dwyer Instruments
Dwyer Instruments BDL-1 Specifications-installation and operating instructions
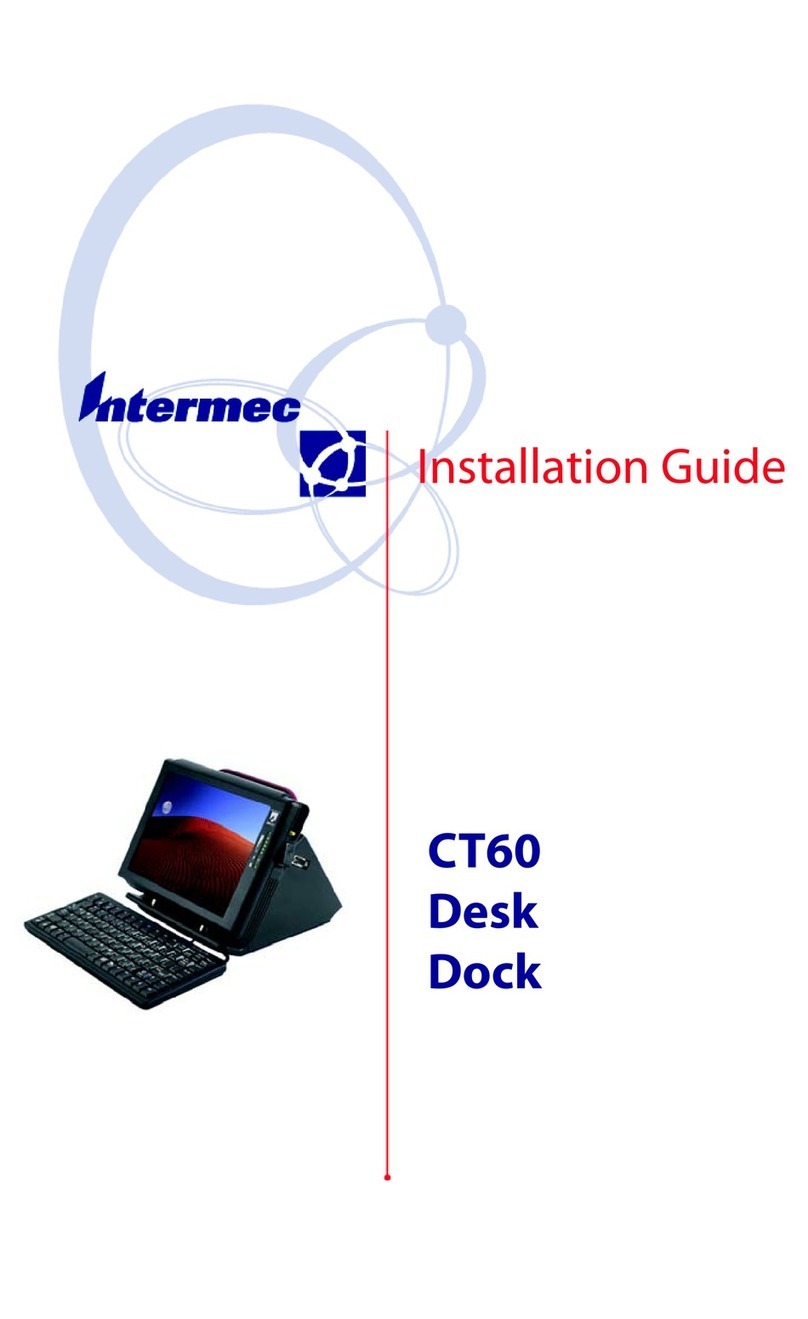
Intermec
Intermec CT60 installation guide
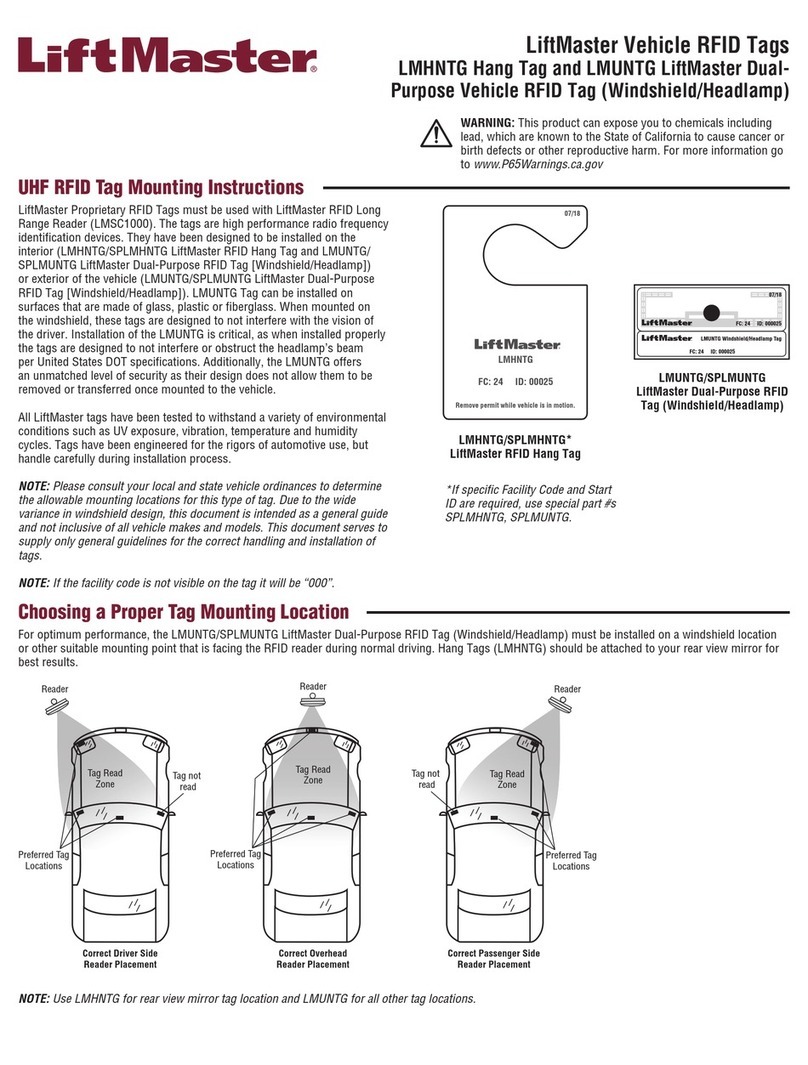
Chamberlain
Chamberlain LMHNTG manual