Nelsen Corporation AIO Plus Connected Series User manual
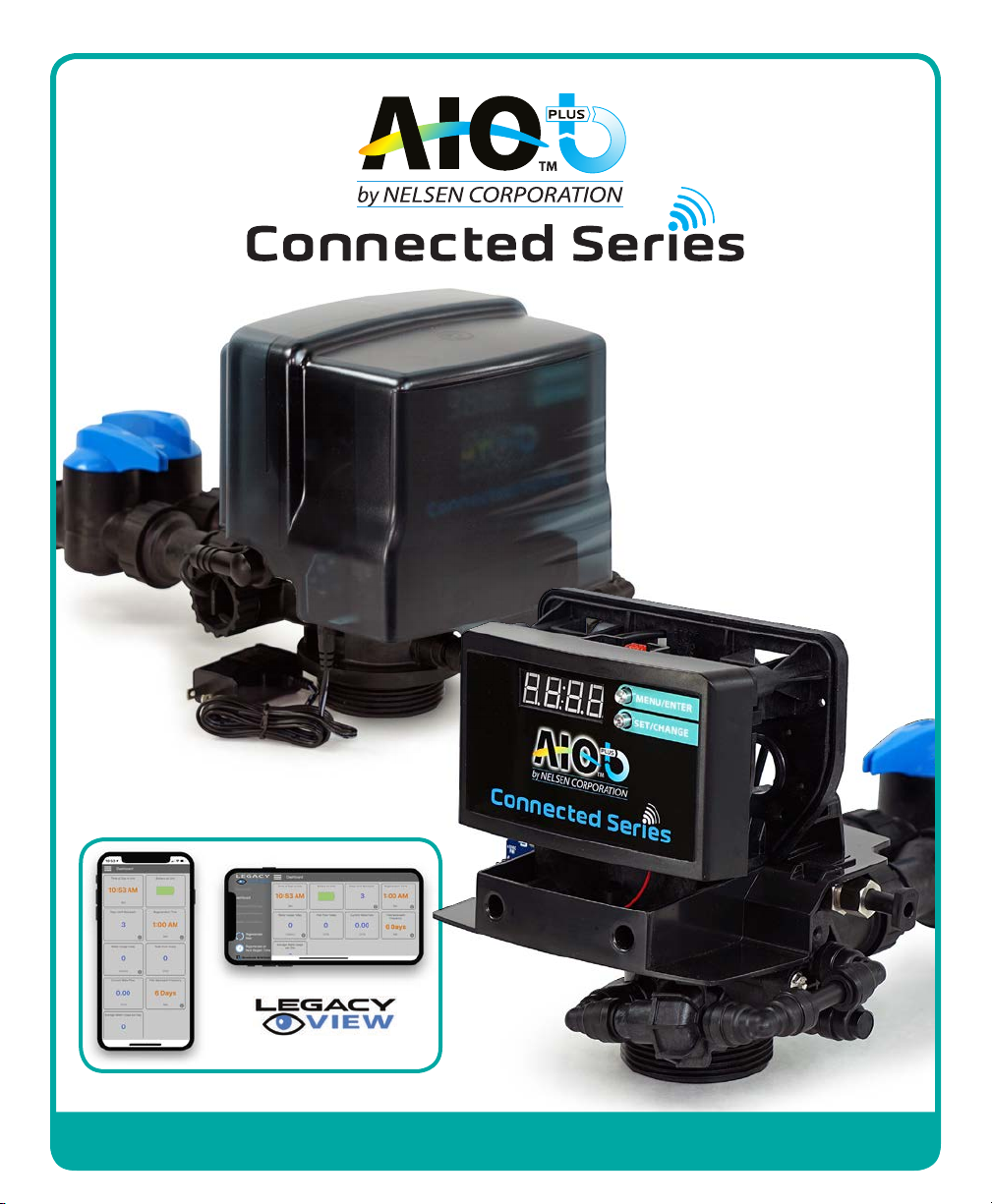
Installation & Operation Manual

General Warnings...................................................................................................................................................................................................................................Page 1
Installation Requirements..............................................................................................................................................................................................................Page 2 - 4
Installation Procedure........................................................................................................................................................................................................................Page 5
Utilizing Bluetooth..................................................................................................................................................................................................................................Page 6 - 8
Programming the Control Valve...............................................................................................................................................................................................Page 9 - 11
Powerhead Assembly........................................................................................................................................................................................................................Page 12
Valve Body Assembly ........................................................................................................................................................................................................................Page 13
Valve Body Assembly Parts List.............................................................................................................................................................................................Page 14
Bypass Assembly..................................................................................................................................................................................................................................Page 14
Service Instructions.............................................................................................................................................................................................................................Page 15 - 16
Troubleshooting........................................................................................................................................................................................................................................Page 16
Error Codes ...................................................................................................................................................................................................................................................Page 17
Warranty Information.........................................................................................................................................................................................................................Page 18
Index AIO Plus Connected Series

1
WARNING
Lubricants
Do NOT use Vaseline, oils, hydrocarbon lubricants or spray silicone anywhere! Petroleum base lubricants will
cause swelling of o-rings and seals. The use of other lubricants may attack plastic Noryl®. It is recommended
that Dow Corning®silicone grease be used as a lubricant for all control valves. Dow Corning®7 Release Com-
pound is used in the manufacture of the control valves. (Part # DOW-7)
Sealants
Pipe dope and liquid thread sealers may contain a carrier that attacks some plastic materials. It is recommended
that Teflon®tape be used to seal plastic Noryl®threaded fittings.
NORYL is a registered trademark of SABIC Innovative Plastics IP B.V.
AIO Plus Connected Series General Warnings

2
INSTALLATION REQUIREMENTS
Locate a level floor position ahead of piping into water heater for placement.
Unit must be installed at least 10 feet ahead of the inlet to a water heater to prevent damage due to back-up hot
water. DO NOT install the unit in an area of direct sunlight or where freezing temperatures may occur!
Locate the unit near an unswitched, 120 volt / 60 Hz grounded electrical outlet.
Check for distance and proper drain installation (e.g. floor drain, washing machine standpipe). Determine type and
size of piping required for filter connection (e.g. copper, galvanized, PVC plastic).
NOTE: If household plumbing is galvanized and you intend to make the installation with copper (or vice versa),
obtain dielectric unions to prevent dissimilar metal corrosion.
CAUTION: If sweat soldering copper pipe (remember to always use lead free solder and flux), cover yoke and
bypass valve with wet rags to prevent heat damage to connections and control valve. If using PVC or plastic pipe,
primers and solvent cements specifically recommended for use with potable water are required.
NOTE: All plumbing lines not requiring “soft” water should be connected “upstream” of the softener, if installed.
(See Typical Installation Diagrams.)
TYPICAL TWO SYSTEM ILLUSTRATION
(Incoming Water From Left Side)
Installation Requirements AIO Plus Connected Series

3
INSTALLATION PROCEDURE
Water Supply Connection and Bypass Valve
To allow for filter servicing, swimming pool filling or lawn sprinkling, a manual Bypass Valve has been installed at the
factory. The Bypass allows raw water to be manually routed around the filter.
1. Position filter at desired location for installation. If a water softener is to be installed, the filter should be
positioned first and then the softener. (See Installation Diagrams.)
2. The filter material is shipped separately from the mineral tank. The tank must be loaded with material after tank
has been placed at the desired location.
A. Remove the control valve by unscrewing from the tank.
B. Place a media funnel in hole on top of tank.
C. Block distributor tube to prevent material from entering the tube while filling.
D. Pour several gallons of water in the tank. (Fill tank about 1/3 full.)
E. Pour in the required filter media. The required quantity and type of media is listed in the filter specifications.
F. After filling the tank with material, use a garden hose or several buckets to fill the tank with water. This will
permit the filtering media to become soaked while preparing the installation and will prevent the control valve
from being plugged with floating material on initial backwash.
G. Remove funnel and clean filter media from tank threads.
H. Remove cap from distributor tube.
I. Replace control valve on mineral tank.
3. Turn OFF main water supply and OPEN nearest faucet to relieve pressure.
4. Cut main line and install appropriate elbows and extensions.
CAUTION: Raised arrows located on the sides of control valve body and bypass valve indicate proper direction
of water flow. Install inlet and outlet piping in direction of arrows. It is recommended that a vacuum breaker be
installed on the inlet plumbing.
Drain Line Installation
1. The drain line flow control assembly is pre-assembled for your convenience. Should you choose to hard plumb
the drain line, please remove the barb fitting. The flow control housing can be removed by removing the clip and
pulling straight out on housing.
NOTE: When re-installing the drain line flow control housing, be sure you hear and feel the O-Ring pop into place
before inserting the clip.
2. Install 1/2" I.D. drain line tubing (not included) from hose barb to an open drain. A 4" gap between end of the drain
line and the open drain is required to prevent waste water back-flow. Keep the drain line as short as possible.
An overhead drain line can be used if necessary, but should discharge below the control valve. A siphon trap
(taped loop) at the outlet of the drain line is advisable to keep the drain line full and to assure correct flow during
backwash. Elbows or other fittings must be kept at a bare minimum.
NOTE: Where the drain line is elevated above the control valve or exceeds 20 feet in length, 3/4" I.D. drain line
tubing should be used.
AIO Plus Connected Series Installation Requirements

4
Electrical Connection
1. Connect the power cord and plug power supply into a 120 volt / 60 Hz receptacle.
NOTE: Do not plug into an outlet controlled by a wall
switch or pull chain that could inadvertently be turned off
Electronic Connections
P = POWER SUPPLY
B = POWERED IN BACKWASH STEP ONLY (CYCLE #1)
S = POWERED FOR ENTIRE REGEN. CYCLE
SYSTEM START-UP PROCEDURE
Service Off Bypass
IMPORTANT NOTE: Tank should be filled with water and media and must have been soaking for at least 1 hour
before initial pressurization.
1. After all plumbing and drain line connections have been made, confirm the Bypass Valve is in
the BYPASS position.
2. Turn main water supply back on and check for leaks.
3. Cycle the control valve to RAPID RINSE. Once the rapid rinse step is reached, leave the OUTLET side of the
Bypass Valve in the CLOSED position. Slowly open the Bypass Valve INLET side to the Service position, allowing
air to escape and water to flow down through mineral tank and out the drain line. Let it continue to run for the
entire rapid rinse step. There may be colored water or media fines during this initial flow.
4. Once the rapid rinse ends, open a cold, treated watertap. Slowly place Bypass into Service. Let water run to home
for several minutes to allow air and any media fines to be released from the lines. Once air is evacuated and water
runs clear, close the tap.
NOTE: Any time media (other than very fine mineral on initial startup) is apparent in the service lines, it usually
indicates one of the following problems:
A.The unit is plumbed in backward allowing the media to be carried in the service line.
B.The distributor tube inside the tank is not seated inside the valve or is damaged.
5. No further regeneration should be necessary at this time. If left at the default settings, the filter will automatically
initiate an air replenish cycle each night and will backwash every six days. If desired, these settings can be
changed in the main menu, or from the “advanced settings” screen in the Legacy View App.
Installation Requirements AIO Plus Connected Series

5
Final Check
1. Be certain that the bypass valve is in Service position and main valve is completely on.
2. Check electrical supply to be certain the cord is connected to an uninterrupted 120 volt outlet.
3. Leave this manual with the homeowner.
IMPORTANT NOTE: The plumbing system, piping, pressure tank, hot water tanks, softeners, etc. that have
been exposed to iron bearing water may need to be cleaned of the precipitated iron that has been collected in
them or iron bleed through may be a problem. We suggest all tanks be drained and flushed thoroughly.
Annual Maintenance
Annual replacement of the seal kit is required in all single tank air systems due to air drying of the seals over time.
Potential performance issues will result if this maintenance interval is not performed. Any system problems associ-
ated with this required system maintenance not being accomplished will not be covered by the factory warranty.
AIO Plus Connected Series Installation Procedure

6
For simplified set up and control, please install the
Legacy View App on a compatible Bluetooth 4.0+
enabled smartphone or tablet.
1. Download and install the
Legacy View App from the
Google Play Store, Apple App
Store
2. Open the Legacy View App
• You must be within 50’ of the device you wish to
set up for it to be available on your phone.
• Choose a valve device at any time from the list of
available devices to connect to by clicking on it.
• If the valve you want to connect to doesn’t show
up, or there is a problem connecting to a device,
you can press the “Scan for Devices” button or the
Legacy View logo at any time to refresh the list and
start the process over.
• If the valve device is a Bluetooth Legacy Enabled
(BTLE) valve and it has a password other than the
default password, the first time you connect to it
the app will ask you to enter the password. After
entering it the first time you should not need to
enter it again unless it changes.
3. BTLE Valve devices can be updated by the app. When
the app is updated from the Google Play Store or the
Apple App Store, it may contain an updated firmware
program for the valve devices. These updates could
contain new features or operational improvements.
It is up to the user to allow these updates to be sent
to the valve device. Uploading a new program takes
approximately 1 minute.
Utilizing Bluetooth®Control AIO Plus Connected Series
DASHBOARD
NOTE: Consult your dealer before making
any changes.
From the Dashboard, all items in ORANGE can
be changed while blue fields are informational
only.
If you are unsure about the function of the
field, click the icon for more information.
Both Landscape and Portrait views are
supported.
• In portrait view the navigation menu may
be collapsed.
• In landscape view the navigation pane will
be shown by default.

7
1. Set Unit Time (Press “ok” to set time automatically
based on device time).
2. Set Filter Backwash Frequency - This sets the
number of days between backwash cycles.
3. Set Regeneration Time - Example: Midnight, just type
12 then press OK.
Advanced Settings
NOTE: Consult your dealer before making any changes.
We do not recommend changing Advanced Settings
unless you have a good understanding of the system
operation.
From the Advanced Settings, all items in ORANGE with
a “set” button can be changed.
AIO Plus Connected Series Utilizing Bluetooth®Control

8
Status and History
From the Status and History, all items in ORANGE can be reset.
Touch any table to explode a
detailed list of the last 60 days.
1. Start a regeneration or backwash cycle
Option 1: Click the “Regenerate Unit Now.”
If you would like to force the unit into the next cycle step click
“Go to Next Regeneration Step”.
Option 2: “Regenerate Unit at Next Regen Time” button.
This will take the system into a backwash cycle at the next regeneration time.
FCC ID: SWPLV-019 or SWPEV-019-BLE
Name of Grantee: CHANDLER SYSTEMS, INC.
Equipment Class: Part 15 Low Power Communication Device Notes: Legacy View Valve
This device complies with part 15 of the FCC Rules. Operation is subject to the following conditions: (1) this device may not cause
harmful interference, and (2) this device must accept any interference received, including interference that may cause undesired
operation. Changes or modifications not expressly approved by the party responsible for compliance could void the user’s authority
to operate the equipment. NOTE: This equipment has been tested and found to comply with the limits for a Class B digital device,
pursuant to Part 15 of the FCC Rules. These limits are designed to provide reasonable protection against harmful interference in
a residential installation. This equipment generates, uses and can radiate radio frequency energy and, if not installed and used
in accordance with the instructions, may cause harmful interference to radio communications. However, there is no guarantee
that interference will not occur in a particular installation. If this equipment does cause harmful interference to radio or television
reception, which can be determined by turning the equipment off and on, the user is encouraged to try to correct the interference by
one or more of the following measures:
- Reorient or relocate the receiving antenna.
- Increase the separation between the equipment and receiver.
- Connect the equipment into an outlet on a circuit different from that to which the receiver is connected.
- Consult the dealer or an experienced radio/TV technician for help.
Utilizing Bluetooth®Control AIO Plus Connected Series

9
Main Menu
1. To enter Main Menu, press the Menu/Enter button. (Time of Day will flash)
2. To set the Time of Day, press the Set/Change button.
(First digit will flash) Example: (12:00)
- To change digit value, press the Set/Change button.
- To accept the digit value, press the Menu/Enter button.
- Next digit will flash to begin setting.
- Once the last digit display is accepted, all digits will flash.
3. To set A.M. or P.M., press the Menu/Enter button.
- To change digit value, press the Set/Change button. Example: (A)
- To accept the digit value, press the Menu/Enter button.
- Once A.M. or P.M. is accepted, the next menu item will flash.
4. Days Between Backwash
- Press Menu / Enter Button. This display is used to set the maximum amount of time (in days) the unit can be
in service without a backwash. This option setting is identified by the letter ‘A’ in the left digit. Backwash will
begin at the set Backwash Time. A “0” setting will cancel this feature. The Max Value for this item is 29.
Example: Backwash every 7 days (A-07) (Factory Setting)
Cancel setting (A-00)
To Adjust this Value Press the Set / Change Button.
To Accept the Digit Value Press the Menu / Enter Button.
5. To set the Number of Days between Air Draw Cycles (d), press the Set/Change Button
- Repeat instructions from step
Example: (d-01)
NOTES:
1) Maximum value is 9.
2) If value set to 0, air draw is turned off, but an air cycle will still be completed when backwash cycle occurs.
If the Number of Days between Air Draw Cycles is set to a higher number of days than the Number of Days
between Backwash Cycles, it will have no effect. In order to turn off all cycles, both the Days between
Backwash and Days between Air Draw Cycles must be set to 0.
3) Default setting is 1 day.
6. To Exit Main Menu, press the Menu/Enter button.
NOTE: If no buttons are pressed for 60 seconds, the Main Menu will be exited automatically.
AIO Plus Connected Series Programming the Control Valve
12:00 MENU/ENTER
SET/CHANGE

10
Normal Operation
1. Home Display
a. Alternates between the display of Time of Day and Number of Days until the Next Backwash. (Metered
Softeners will alternate between time of days and gallons remaining until next regeneration).
- Days Remaining until the Next Backwash will count down from the entered value until it reaches 1 day
remaining.
- A Backwash Cycle will then be initiated at the next designated regeneration time.
2. Battery Back-Up (Uses a standard 9-volt alkaline battery. Not included.)
Features of Battery Back-Up:
• During power failures, the battery will maintain the time of day as long as the battery has power. The display
is turned off to conserve battery power during this time. To confirm that the battery is working, press either
button and the display will turn on for five (5) seconds.
• If power failure occurs while system is regenerating, the system will motor to a shut off position to prevent
constant flow to drain. After power is restored, the system will return and finish the cycle where it left off prior
to the power interruption.
• When used without battery back-up during a power failure, the unit stops at its current point in the regeneration
position and then restarts at that point when the power is restored. The time will be offset by the increment
of time the unit was without power, so it is necessary to reset the time of day on the unit. No other system
settings will be affected.
Programming the Control Valve AIO Plus Connected Series

11
AIO Plus Default Cycle Step Times Minutes
Step 1 Air Release (non-adjustable) 6
Step 2 Backwash 10
Step 3 Rest 5
Step 4 Air Replenish 20
Step 5 Rapid Rinse 5
Starting Extra Regeneration Cycle
1. To Start Delayed Extra Cycle: Example: [1]
- If Days Remaining Until Next Regeneration does not read ‘1’, press and hold the Set/Change button for 3
seconds until the display reads ‘1
- Regeneration cycle will initiate at the next designated regeneration time.
2. To start Immediate Extra Cycle: First complete above step.
- Press and hold the Set/Change button.
- After 3 seconds, the regeneration cycle will begin.
3. To Fast Cycle through regeneration: First complete above 2 steps.
Press and hold the Set/Change button for 3 seconds to advance to the next cycle step.
NOTE: Fast Cycle is not necessary unless desired to manually step through each cycle step.
(Repeat until valve returns to the home display)
Regeneration Cycle
NOTE: Depending upon system pressure and other factors, it is possible to observe flow to drain in the rest cycle.
-When the valve is between positions, the display will flash the number of the step it is moving towards.
-The default time at which regeneration will occur is 12:00 a.m.
The motor’s run direction during a particular regeneration cycle step is indicated by the rotation direction of the
last 2 digit displays.
Example: 5-
AIO Plus Connected Series Programming the Control Valve

12
Powerhead Assembly AIO Plus Connected Series
3
4
2
5
6
7
8
10
11
15
14
13
18
17
12
16
E
1
EPM
P
M
F
9
LETTERS IN DIAGRAM REPRESENT WIRING CONNECTIONS
Ref Description Part# Qty
0 Powerhead Assembly 20010N100 1
1 Circut Board Assembly
CS-BOARD ENCLOSURE
1
2 Encoder 20001X124 1
3 Front Plate 20001X004 1
4 Encoder Wheel 20001X007 1
5 Main Gear 21001X120 1
6 Power Supply CS-TRANS 1
7 Back Plate 20001X005 1
8
Lower Front Base for Cover
20111X002 1
9 Motor 20016X006 1
10
Lower Back Base for Cover
20111X003 1
11 Slide Cover 20111X017 1
12 Motor Screw SC2 2
13 Screw SC9 2
14 Screw SC10 3
15 Piston Screw 20001X003 1
16 Valve Hex Screw 20001X001 2
17 Circuit Board Washer 20111X014 1
18 Piston Washer 20001X002 1

13
AIO Plus Connected Series Valve Body Assembly
VALVE PARTS LIST ON FOLLOWING PAGE
29
28
27
26
26
25
22
23
24
22
22
21B
21A
20
19
18
17
17
16
15
14
13
12
11 10
9
8
6
5
4
3
2
1

14
Valve Body Assembly - Parts AIO Plus Connected Series
Bypass Assembly
Ref Description Part# Qty
1 Piston Assembly CS-PISTON 1
2 10-24 X 13/16 Hex Head 20001X001 5
3 Seal and Spacer Kit CS-SEALS 1
4 Bottom Spacer N/A 1
5 DLFC 5.0 Button 20251X272 1
5 DLFC 7.0 Button 20251X273 1
6 Drain Line Flow Control Housing 20017X268 1
8 DLFC Clip 20017X214 1
9 Brine Valve 20009X225 1
10
Brine Line Flow Control (BLFC) SS
20009X228 1
11 Brine Line Ferrule 20251X305 1
12 3/8" Plug 20009X005 1
13 10-24 X 1 Hex Screw 20001X226 2
14 3/8" Push Lock Plug 20009X010 1
15 Injector Cap 20009X001 1
16 Injector Cap Seal 20001X224 1
17 Injector Plug 20009X001 2
18 Injector Screen 20001X222 1
19 Tank O-Ring 20561X205 1
20 Distributor Tube O-Ring 20561X204 1
21a Flow Meter CS-METER 1
21b Flow Meter Plug 20017X201 1
22 3/8" Push Lock 90 Elbow GA-Q0620626BV 3
23 External Air Injection Assembly 20017X010 1
24 Injector w/o Check Ball 20017X219 1
25 Stem Adapter GA-S0660416B 1
26 Stem Elbow GA-T0620666B 2
27 Inlet Check Valve 20017X293 1
28 Extension 20017X292 1
29 Valve Body Complete VH2-A-BT-N-D15 1
Ref Description Part#
1 Bypass CS-BYPASS
2 1" Female Straight Slip (set of 2) CS-10S-PVC-SLIP
3 1" NPT Elbow (set of 2) CS-10E-PVC-MIPT
4 1" NPT Straight (set of 2) CS-10S-PVC-MIPT
5a Elbow, Vertical Adapter Blank
(set of 2) CS-10-90-PVC-BVA
5b Elbow, Vertical Adapter 1/4” NPT
Tapped (set of 2) 20017X294
3/4" Male NPT Straight (set of 2) CS-07S-PVC-MIPT
3/4" Brass Sharkbite Straight
(set of 2) CS-07-SHARK

15
A.General Preliminary Instructions
PERFORM BEFORE ALL SERVICING OPERATIONS
1. Turn off water supply to conditioner.
• If the conditioner installation has a “three valve” bypass system, first open the valve in the bypass line, then
close the valves at the conditioner inlet and outlet.
• If the conditioner has an integral bypass valve, put it in the bypass position.
• If there is only a shut off valve near the conditioner inlet, close it.
2. Remove cover and relieve water pressure in the conditioner by stepping the control into the backwash position
momentarily. Return the control to the service position.
3. Unplug electrical cord from outlet.
B.To Replace Powerhead
1. Remove the control valve cover and disconnect the power supply.
2. Disconnect the meter cable from circuit board and feed back through control (if existing meter is being re-used).
3. Remove lower back base screws and detach lower back base.
4. Remove screw and washer at drive yoke. Remove powerhead mounting screws. The entire powerhead
assembly will now lift off easily.
5. Put new powerhead on top of the valve. Be sure the drive pin on main gear engages slot in drive yoke (wide side
of drive yoke upright must face to the left away form the motor).
6. Replace powerhead mounting screws. Replace screw and washer at drive yoke.
7. Reattach lower back base.
7. Reconnect meter signal, wire and power supply.
8. Reinstall cover.
C.To Replace Piston Assembly
1. Follow steps A1 - A3.
2. Disconnect the meter signal wire from the circuit board.
3. Remove lower back base screws and detach lower back base.
4. Remove screw and washer at piston drive yoke. Remove powerhead mounting screws. The entire powerhead
assembly will now lift off easily.
5. Remove piston retaining plate screws.
6. Pull upward on end of piston yoke until assembly is out of valve.
7. Inspect the inside of the valve to make sure that there is no foreign matter that would interfere with the valve
operation.
8. Install new seals and spacers.
9. Take new piston assembly and push piston into valve by means of the end plug. Twist drive yoke carefully in a
clockwise direction to properly align it with drive gear. Reinstall piston retaining plate screws.
10. Follow steps B5 - B9.
D.To Replace Seals and Spacers
1. Follow steps A1 - A3.
2. Disconnect the meter signal wire from the circuit board.
3. Remove screw and washer at piston drive yoke. Remove powerhead mounting screws. The entire powerhead
assembly will now lift off easily. Remove piston retaining plate screws.
4. Pull upward on end of piston rod yoke until assembly is out of valve. Remove seals and spacers. (Note: Special
end spacer must be reused)
5. Lubricate new seals with silicone lubricant included in the seal and spacer kit. Make sure the special end spacer
is properly seated in the valve body. Install new seals and spacers individually, pressing around the outer edge
of each seal to make sure it is seated. (When all seals and spacers are seated properly, you will have a 1/4" of
space between the top seal and the top of the valve body).
6. Follow Steps C9 - C10.
AIO Plus Connected Series Servicing Instructions

16
F. To Replace Meter
1. Follow steps A1 - A3.
2. Unplug meter cable from front of circuit board.
3. Unscrew meter assembly nut from valve body.
4. Remove meter from valve body and clean or replace as necessary.
5. Reinstall meter, nut and cable.
Troubleshooting Guide AIO Plus Connected Series
1. Fails to Regenerate
Automatically
Power supply plugged into intermittent or
dead power source Connect to constant power source
Improper control valve programming Reset program settings
Defective power supply Replace power supply
Defective Drive motor Replace motor
2. Regeneration at
Wrong Time
Time of day improperly set, due to power
failure
Reset time of day programming and install
9-volt battery
Regeneration time set improperly Reset regeneration time programming
3. Poor Water Quality
Check items listed in #1 and #2
Bypass valve open Close bypass valve
Channeling Check for too slow or high service flow
Check for media fouling
Lack of aeration in water
Program valve to draw air more frequently
Increase number of minutes in air draw
cycle
Clean injection assembly and screen
4. Loss of Water Pressure
Scaling / fouling of inlet pipe Clean or replace pipeline
Pre-treat to prevent
Fouled media Clean media
Pre-treat to prevent
Improper backwash setting Backwash more frequently
5. Continuous Flow To Drain
Foreign material in control Call dealer
Clean valve and replace pistons and seals
Internal control leak Same as above
Valve jammed in backwash or rapid rinse
position Same as above
Motor stopped or jammed
Check for jammed piston
Replace piston and seals
Replace motor if motor is unresponsive
6. Media in Service Line Plumbed in backward Re-plumb the system properly
Internal leak in unit Call dealer
7. Media Flows to Drain
Media did not soak long enough Re-soak the media for a longer length
Incorrect or missing drain flow control Check for proper flow control
Call dealer, if problems persist
Symptom Problem Cause Correction

17
Control Valve Error Code Diagnosis
Under normal operating conditions, when the control valve is in the “in service” position, the display should alternate
between the current time of day and the number of days remaining (for filters and time clock softeners) or gallons re-
maining (for metered softeners) until the next regeneration. This is the “home display.” If the valve is currently going
through a regeneration cycle, the display will show the cycle step on the left side of the display and the number of
minutes remaining in that step on the right side of the display. If any other information is being displayed, then the
valve is informing you of an issue. There are five error codes which could indicate an issue with the control valve.
When an error is being displayed, the valve will be in a stopped position, and the buttons will not respond to being
pressed. Even if the cause of the error code is corrected, the error code will not clear until the power supply has
been disconnected and reconnected (this will be referred to as “cycling” the power). All error codes are displayed as
the letters “Err” followed by a flashing number 2-6:
Error 2 - Valve is searching for homing slot. - Allow valve to continue running. If the homing slot is found, the valve
will return to the home display, otherwise, another error code will appear.
Error 3 - No encoder slots are being seen. - This occurs when the motor is running, but the encoder is not seeing any
of the slots in the encoder wheel. This can happen if the encoder has been disconnected, but most commonly occurs
when debris in the valve body has stopped the piston, causing the encoder wheel to be unable to turn.
1. Check encoder connection. If the encoder is plugged in and snapped into place, skip to step #2 below. If
encoder is disconnected, reconnect it and cycle power to clear the error.
2. Disconnect powerhead from valve body, cycle power to clear the error code. Manually cycle the powerhead
through the regeneration cycle steps to verify that the motor can cycle properly while the powerhead is
disconnected from the valve body. If the error 3 does not reappear, skip to step #3 below. If the error 3 does
reappear, order a board & motor kit to replace the circuit board & motor.
3. Remove piston and seals from the valve body and inspect valve body for debris. Replace the seal & spacer kit.
Inspect piston and replace piston if Teflon coating is worn
Error 4 - Unable to find homing slot.
1. Check encoder wheel for debris.
2. Cycle power. Valve should either find home or go to a different error code. If error 4 returns, replace powerhead
assembly.
Error 5 - Motor overload. - This occurs when the motor current is too high. This could be caused by an issue with the
motor itself, but is typically caused by friction in the valve body
1. Disconnect powerhead from valve body and cycle power to clear the error code.
2. If the error 5 returns, replace the motor. Otherwise, manually cycle the powerhead through the regeneration
cycle steps to verify that the motor can cycle properly while the powerhead is disconnected from the valve
body. Either way, proceed to the next step.
3. Remove piston and seals from the valve body and inspect valve body for debris. Replace the seal and spacer kit.
Inspect piston and replace piston if Teflon coating is worn.
Error 6 - No motor current. - This typically occurs if the motor cable has come unplugged from the circuit board.
Check that the motor cable is plugged into the circuit board and attached to the motor. If this is not the issue, the
motor or circuit board may need to be re-placed.
No Display - If your display is blank, there is no power going to the circuit board due to one of the following factors:
• The electrical outlet is not powered or is switched off.
• The power cable has come unplugged from the circuit board.
• The power supply has come unplugged from your electrical outlet.
• The power supply has come unplugged from the control valve.
• The power supply is not working.
AIO Plus Connected Series Error Codes

18
Warranty AIO Plus Connected Series
Water Conditioner Limited Warranty
We warrant this water conditioner, when installed according to factory recommendations, to be free from defects in
materials and workmanship as follows:
Limited Warranty
This water conditioner unit is assembled from the finest industry components available. Each individual
component used in the assembly of our equipment is covered by the original equipment manufacturer’s
warranty. All components, except those specifically listed below, are warranted for a period of one (1) year from
date of installation to the original purchaser to be free of defects in materials and workmanship subject to the
manufacturer’s conditions and/or the conditions shown below.
Mineral Tanks
The fiberglass, polyglass or composite mineral tanks used in the assembly of this unit are warranted to be free of
defects in materials and workmanship for a period of ten (10) years on 6" - 13" size tanks, and five (5) years on 14"
and larger size tanks used for softener/filtration applications, subject to the original manufacturer’s conditions and/
or the conditions shown below. Warranty does not cover sandblasting of tank caused by faulty distribution systems,
fractures caused by external impact and exposure to vacuum.
Control Valves
The control valve (if used in the assembly of the unit) is warranted to be free of defects in materials and
workmanship for a period of seven (7) years subject to the original manufacturer’s conditions and/or the additional
conditions shown below.
Conditions
1. This warranty only covers water conditioners installed for residential use. Water conditioners installed for
commercial or industrial applications are guaranteed for one (1) year from the date of installation.
2. Installation must be made in accordance with legal or local codes and manufacturer’s recommendations.
3. Failure must not result from misuse, alteration, fire, lightning, power surges or neglect.
4. Water pressure must not exceed 100 p.s.i. and water temperature must not exceed 100 degrees.
5. Damage or failure of a Product or Part caused by friction, wear, chemical attack, or debris build-up on wear parts.
“Wear Parts” include, but not limited to: pistons, piston rods, seals spacers, end cap quad rings and brine valve
on all piston operated valves, as well as valve disk flappers on Autotrol valves, and parts requiring replacement
under recommended maintenance procedures, such as filter housing o-rings and gaskets.
Subject to the above terms and conditions we will replace and/or repair, at our option, any parts of the water
conditioner found defective in materials and workmanship. Defective parts must be returned, freight pre-paid, by
your dealer, who will supply a replacement furnished by the company. This warranty does not cover labor, shipping
charges, damages caused by delays of consequential damages or other causes beyond our control.
This warranty is to the original purchaser and is not transferable after the third year to any subsequent owner(s).
No other guarantee or warranty, expressed or implied,
is applicable to our product. No repair or replacement
made under the terms of the warranty shall extend this
warranty.
Product Warranty
Residential Mineral Tank 10 Years
AIO Plus Connected Series Control Valve 7 Years
Other Accessories and Parts 1 Years
Part No: CS-AIO-PLUS-PROG GUIDE ©Nelsen Corporation - 0619
Table of contents
Other Nelsen Corporation Control Unit manuals
Popular Control Unit manuals by other brands
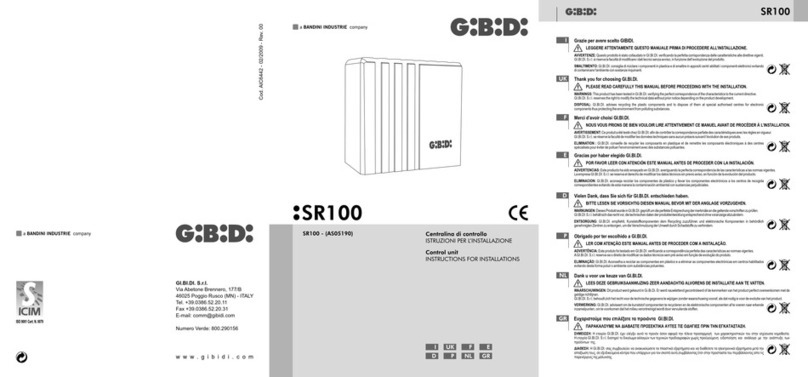
Bandini Industrie
Bandini Industrie GI.BI.DI. SR100 Instructions for installations

Emerson
Emerson SM-I/O 24V Protected user guide
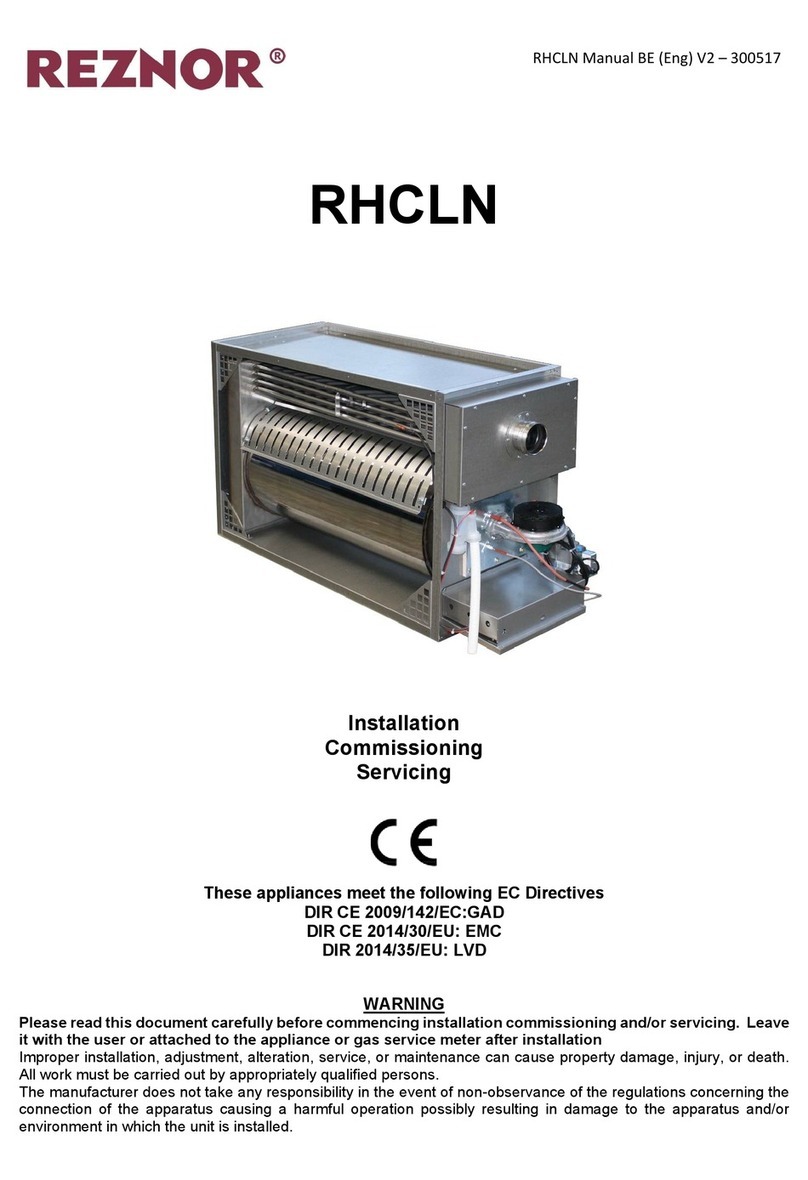
Reznor
Reznor RHCLN Installation, commissioning, servicing
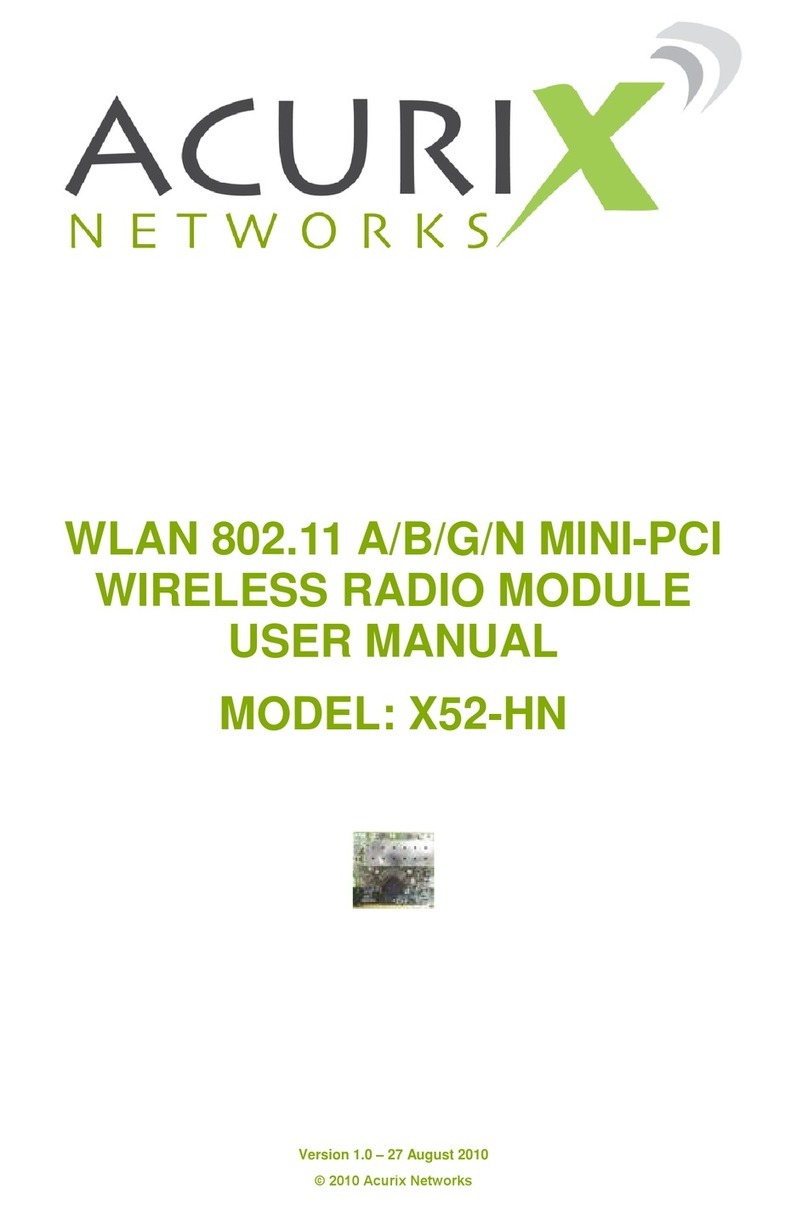
Acurix
Acurix X52-HN user manual

spartan scientific
spartan scientific 35KR Series Application and installation guide

Burkert
Burkert 3360 operating instructions
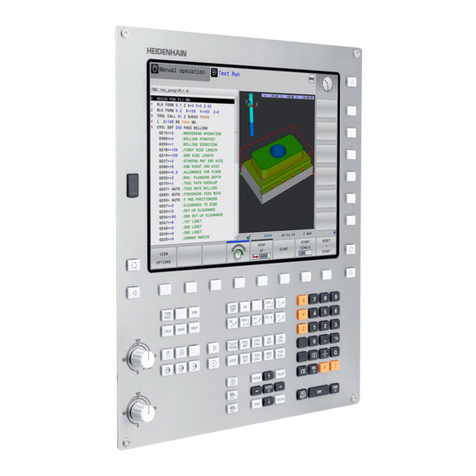
HEIDENHAIN
HEIDENHAIN TNC 320 Programming Station User's manual for cycle programming
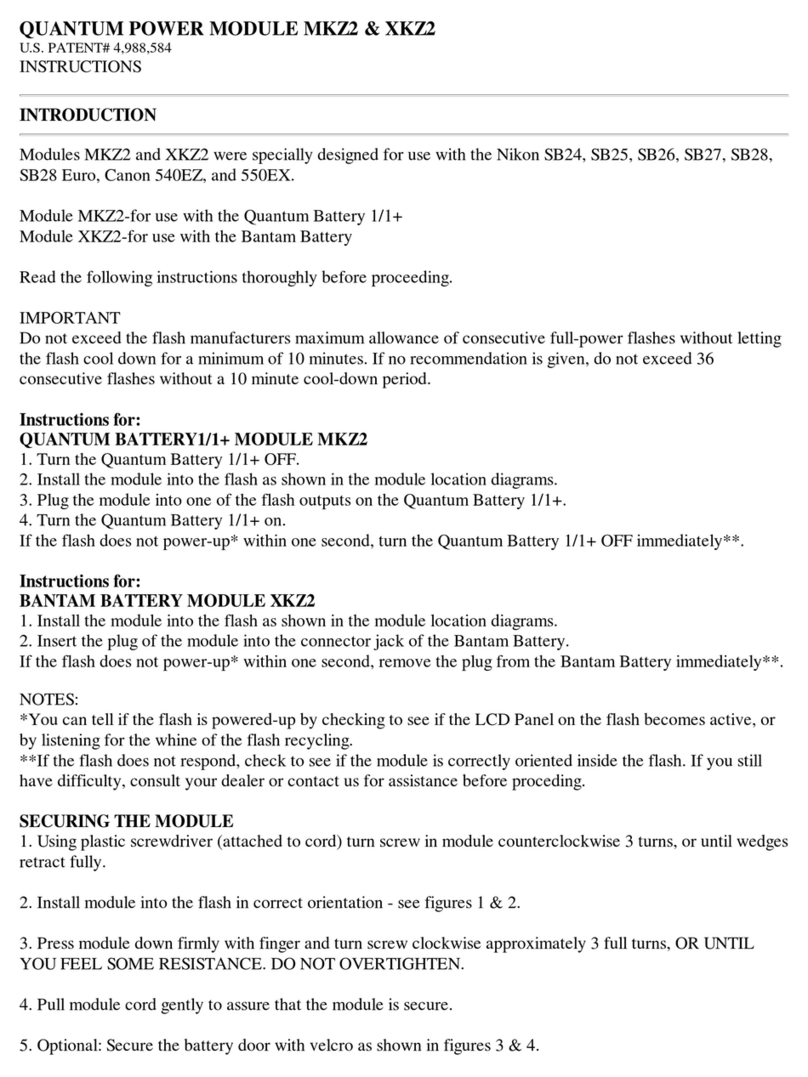
Quantum
Quantum MKZ2 Instructions for use
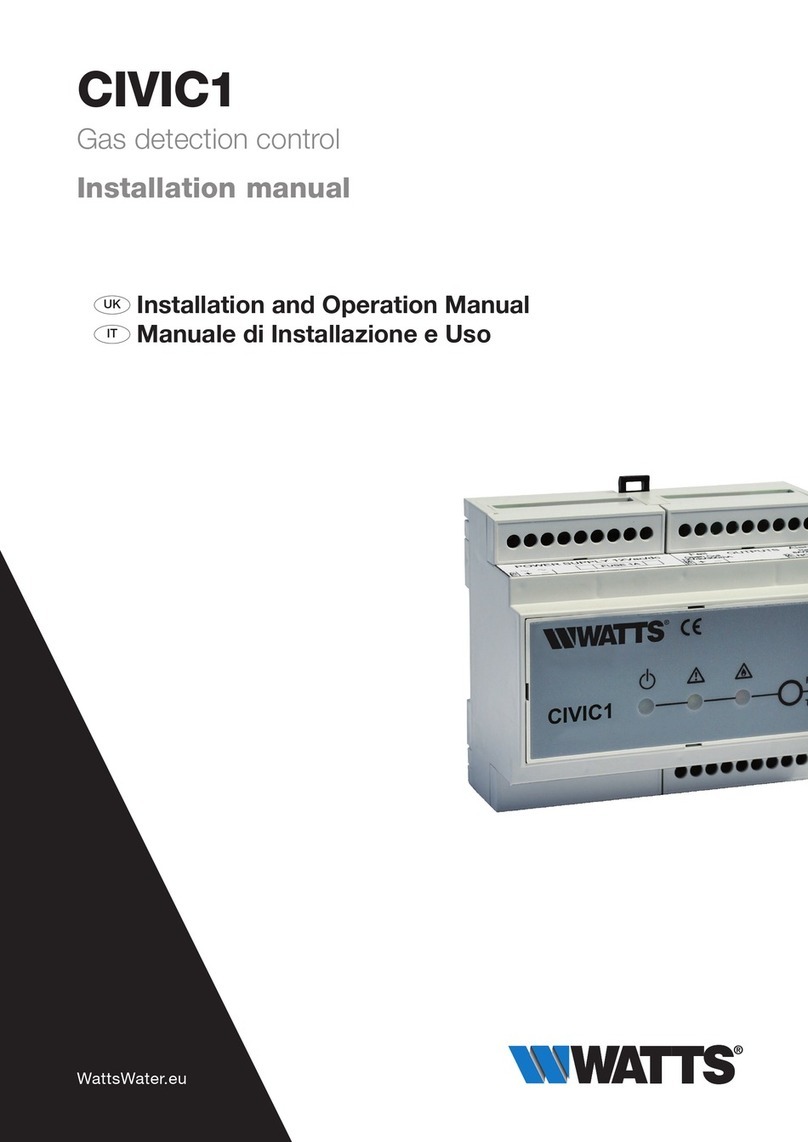
Watts
Watts CIVIC1 Installation and operation manual

IFM Electronic
IFM Electronic ecomot 300 AC2219 operating instructions

Marmitek
Marmitek LW12 user guide
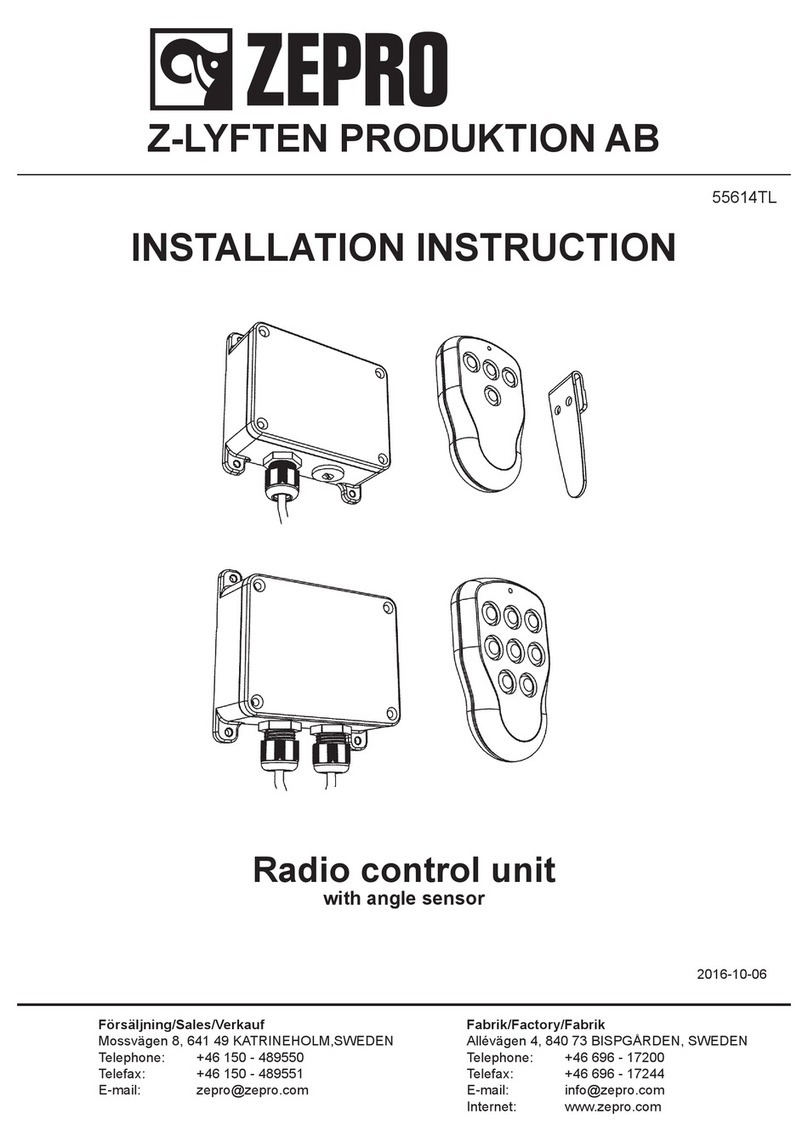
Zepro
Zepro T60 Installation instruction