Neumo EGMO TWISTMax User manual

Pneumatic Rotary Actuators
Installation and Maintenance Instructions
EGMO Ltd.
Tel: +972 (0) 4 9855 176/111 |Fax: +972 (0) 4 9855 175
618-00327 06/2016 Edition: 3 EGMO Ltd. Marcom Department
Table of contents
1.
General information
2.
Safety and warnings
3.
Working principle
4.
Operating and storage conditions
5.
Installation
6.
Maintenance
7.
Troubleshooting
8.
Guarantee compact shape
!Make sure you read this guide fully, before using the actuator
!Store this guide safely so that you can use it in the future

1
1. General information
The following document contains information on how to install,
operate and perform maintenance of TWISTMax pneumatic
actuators. Product users and maintenance personnel should
thoroughly review this document along with installation,
operation and maintenance instructions of any valve that
actuated by TWISTMax pneumatic actuator.
2. Safety and warnings
Serious injuries or death can be caused or property can be
damaged due to improper usage of this product. Users and
maintenance personnel must read this document before using
this product and strictly adhere it at all times. For additional
information contact EGMO.
2.1.
The system designer and user have the sole responsibility for
selecting products suited to their application requirements and
ensuring the proper installation, operation and maintenance
of the product. Please consider application details, material
compatibility and product ratings when making your selection.
Improper selection or use of products can cause serious injuries,
death or property damage.
2.2.
Product users and maintenance personnel must have deep
understanding of any national and/or local safety laws and
regulations.
2.3.
The product must be used only at operating conditions EGMO
and as it stated on product nameplate.
2.4.
The product does not require maintenance of internal
components. DO NOT DISASSEMBLE THE PRODUCT. THE
PRODUCT HAS PRELOADED SPRING INSIDE.
2.5.
Before performing any installation or maintenance works insure
that all pressure or electrical sources are not connected to
product.
2.6.
Before performing any installation or maintenance works
including valve actuation insure that you deeply understand in
system.
2.7.
Before servicing any installed valve you must depressurize and
drain the system.
2.8.
Before servicing any installed valve you must cycle it.
2.9.
Note that residual material may be left in the valve and system.
2.10.
Do not rotate manually an actuator’s shaft.
2.11.
Do not leave any grip key or shaft connection attached to the
actuator during functional testing.
2.12.
Keep hands, hair and clothing away from moving parts while
actuating the actuator.
2.13.
Only train and qualied users, who have read this document,
are allowed to install, operate and perform maintenance of this
product.
2.14.
EGMO does not bear responsibility for accessories, attached to
the actuator, which were not provided by EGMO.

2
2.15.
It is allowed to actuate the actuator only with medium which
designated by EGMO. For additional information contact EGMO.
DO NOT ACTUATE THE ACTUATOR WITH OXYGEN AND
HYDROGEN.
3. Working principle
3.1.
DA - Double Acting Actuator: Air supplied through Port A forces
the piston and moves it downwards. Shaft forced by spiral guide
rotates in CCW direction. Air supplied through Port B forces the
piston and moves it upwards. Shaft forced by spiral guide rotates
in CW direction.
3.2.
SR - Spring Return Actuator: Air supplied through Port A forces
the piston, moves it downwards, and compresses the spring.
Shaft forced by spiral guide rotates in CCW direction. Upon
release of air pressure, the spring forces the piston upwards.
Shaft forced by spiral guide rotates in CW directions.
Port A
Piston
Spring
Guide Curve
Port B
Shaft
SR
Port A
Piston
Guide Curve
Port B
Shaft
DA
Port A
CCW
Side
View
Top
View
Port B
Port B
Port A
D
CW

3
4. Operating and storage conditions
4.1.
Technical data:
Housing material * AISI 304
Internal components material * AISI 304
Spring material Chrome silicon alloy (coated)
Piston material Engineering polymer
Seal material * Engineering elastomers
Operating temperature * -10°c to +60°c
SR Operating pressure 5 - 8 bar
DA Operating pressure 4 - 8 bar
Rotation 90°±5°
Torques See catalogue
Pneumatic interface * Metric
Control devices interface VDI/VDE 3845 (optional)
Control media* Filtered air according to DIN
ISO 8573-1/class 4
Air ltration rate 30 micron (or less)
Usage Indoor / Outdoor / Corrosive
environment
* For other options contact EGMO
4.2.
Storage:
4.2.1.
Store the actuators inside their original package.
4.2.2.
Store the actuators indoors, in dry and clean place.
4.2.3.
It is recommended to cycle the actuators during long
period storage.
4.3.
Unpacking:
4.3.1.
Before unpacking the actuator, insure that product
received comply with packing list.
4.3.2.
Inspect the actuator to any damages (contact your
shipper if damages found).
4.3.3.
Remove protection plugs close as possible to installation.
Installation

4
5. Installation
Basic
No. Description Qt'y Material
1 Proximity Switch sensor 2 N/A
2 Universal bracket for ball valve 1 SS304
3 Bracket safety cover 1 PC
4 Button Head Cap Screw 2 SS304
5 Nut M12 4 SS304
6 Spring washer* 4 SS304
7 HEX Head bolt* 4 SS304
8 Coupling for ball valve
(for inductive sensors)
1 SS304
9 Ball valve 1 STD
10 Buttery valve 1 STD
11 Valve tightening bolt ** 2 SS304
12 Coupling for buttery valve (for
inductive sensors)
1 SS304
13 Bracket for buttery valve 1 SS304
14 Air connection 1 STD
15 O-Ring # 2-009/ 2-014*** 1 STD
* See size in catalogue.
** According to valve size (dened by valve manufacturer)
*** See 5.2.1.5
14
27
5
1
13
12
6
7
11
10
5
7
6
9
8
1
2
3
4

5
14
27
5
1
13
12
6
7
11
10
5
7
6
9
8
1
2
3
4
Advanced
No. Description Qt'y Material
16 NAMUR pad adapter 1 Aluminum,
hard anodized
17 Socket head screw M5x20 2 SS304
18 VDI/VDE 3845 Plate 1 SS304
19 Flat head socket M5x10 2 SS304
20 VDI/VDE 3845 Adapter 1 SS304
21 Spiral pin 3mm x 16mm 1 SS304
22 Control unit 1 N/A
23 Sliding washer 1 PTFE
24 Upper visual position indicator 1 Plastic
25 Spiral pin 3mm x 32mm 1 SS304
26 TWISTMax Advanced quarter turn
pneumatic actuator
1 N/A
27 TWISTMax Basic quarter turn
pneumatic actuator
1 N/A
* See size in catalogue.
** According to valve size (dened by valve manufacturer)
26
25
24
23
22
21
20
18
5
1
13
12
6
7
11
10
5
7
6
9
8
1
19
2
4
3
17
16 15 14

6
5.1.
Actuator installation:
5.1.1.
Prior to installation make sure that there is enough space
for installation / removal and connection of actuator (26,
27).
5.1.2.
When SR actuator (26, 27) used it is recommended to
mount lter on port B in order to avoid particles entrance
into the actuator.
5.1.3.
When SR actuator (26, 27) used in system that being
washed periodically by water (or any other uid) it is
recommend to mount elbow faced downwards on Port
B in order to prevent water (or any other uid) entrance
into the actuator.
5.1.4.
Actuator (26, 27) and valve (9, 10) must be properly
aligned. Failure to do so may lead to valve malfunction or
medium leak.
5.1.5.
After the installation check visually alignment of coupling
(8, 12) and actuator (26, 27).
5.1.6.
DO NOT BLOCK Port B at all times. The actuator (26, 27)
will stop if port B is blocked.
5.1.7.
It is recommended to connect the actuator (26, 27) to the
bracket (2, 13) rst and only to connect the bracket (2, 13)
to the valve (9, 10).
5.1.8.
After nal tightening of installation bolts (7, 11) on valve
(9,10) and actuator (26,27) check that the coupling (8, 12)
has small axial movement.
WHEN PERFORMING THIS OPERATION INSURE THAT THE
ACTUATOR (26,27) IS NOT CONNECTED TO PRESSURE
SUPPLY.
5.1.9.
After the installation insure proper tightening of all bolts.
5.1.10.
Prior to installation verify correct valve’s (9, 10) position
(NO - Normally Opened or NC - Normally Closed)
according to system design and rotate valve’s (9, 10) stem
accordingly.
5.1.11.
Insure valve’s (26,27) body tightening torque according to
valve’s manufacturer instructions.
5.1.12.
TWISTMax actuator (26,27) can be mounted at any
orientation.
5.1.13.
For actuator (26,27) installation use suitable, fault free
accessories and tools.
5.1.14.
Apply lubricant on threads in order to prevent galling.
5.1.15.
After the installation use soap solution to make sure all air
connections (14, 16) are leak free.
5.1.16.
It is recommended to mount on TMX4 Advanced
actuator (26,27) air connection (14) with ø10mm (ø⁄”)
outside diameter.
5.1.17.
Note that TMX4 actuator’s (26,27) connection interface is
not according to ISO5211. For more details see catalogue.

7
5.2.
Accessories installation (applicable only for advanced type):
5.2.1.
NAMUR Pad (15).
5.2.1.1.
Apply grease on o-ring (15).
5.2.1.2.
Install supplied o-ring (15).
5.2.1.3.
Tighten installation bolts (17).
5.2.1.4.
5.2.1.4 Use soap solution to insure that the
installation is leak free.
5.2.1.5.
O-Rings sizes:
NAMUR Pad for O-Ring # Mat’l
TMX-4 2-009 NBR
TMX-5 to 11 2-014 NBR
5.2.2.
VDI/VDE 3845 AA1 Plate (18) and VDI/VDE 3845 Adapter
(20):
5.2.2.1.
Remove spiral pin 3mm x 32mm (25) (hole diameter
ø3mm / 0.12”).
5.2.2.2.
Remove upper visual position indicator (24).
5.2.2.3.
Install sliding washer (23).
5.2.2.4.
Install VDI/VDE 3845 Adapter (20) and insure that
alignment of holes in actuator’s (26) shaft and VDI/
VDE 3845 Adapter (20).
5.2.2.5.
Insert spiral pin 3mm x 16mm (21).
5.2.2.6.
Install VDI/VDE 3845 Plate (18) and tighten at head
socket screws (19).
5.2.3.
Mounting bracket (2, 13) and travel adjustment (hard
stop) of actuator (26, 27) and valve (9, 10):
Mounting bracket , has slots on its connection surfaces in order
to allow performance of actuator’s , travel adjustment.
6. Operating and storage conditions
TWISTMax actuator does not require maintenance of internal
components. It is recommended to perform steps as follows
every six months in order to insure actuator’s proper operation.
WARNING: To avoid serious injuries, death or property
damage the following steps should be performed when
pressure supply is disconnected.
6.1.
Observe the actuator for correct fail-safe action.
6.2.
Examine the actuator for damage caused by corrosive fumes and
process drippings.
6.3.
If possible, stroke the actuator and check for a smooth, full-stroke
operation.
WARNING: To avoid serious injuries, death or property
damage, keep hands, hair and clothing away from all
moving parts while operating the actuator. If the actuator
failed during testing, do not disassemble it. Contact
EGMO customer service. Disassembling the actuator is a
dangerous operation.
DO NOT DISASSEMBLE THE ACTUATOR IN ANY CASE!

8
6.4.
Make sure the positioner mounting bolts, linkage and stem
clamp are fastened securely.
6.5.
Ensure all accessories, brackets and associated bolting is
fastened securely.
6.6.
Clean any dirt or foreign material from actuator’s surfaces.
6.7.
If an air lter is mounted, isolate the air lter, then check and
clean or replace the element if necessary.
7. Troubleshooting
7.1.
Problem: Pressure supplied to actuator but it does not move.
Probable cause Corrective action
1.
Leaks in pressure supply
system.
Check pressure supply system
for leaks.
2.
Incorrect pressure supply
system design.
Check pressure supply system
design.
3.
Supply pressure (to actuator)
too low.
Check supplied pressure (to
actuator).
4.
Malfunctioning control
device.
Check control device.
5.
Actuator internal components
failure.
Replace actuator.
6.
Valve’s body bolts are over
tightened.
Tight valve’s body bolts
according to manufacturer
instructions.
7.
Incorrect installation. Refer to installation
procedure as described in this
document.
8.
Port B blocked. Unblock port B.
7.2.
Problem: Pressure supplied, actuator and valve are operating but
process is incorrect (when connected to 3 way ball valve).
Probable cause Corrective action
1.
Valve malfunctioning. Replace or x valve.
7.3.
Problem: Excessive leakage through valve’s seat.
Probable cause Corrective action
1.
Improper travel adjustment. Perform travel adjustment.
2.
Valve malfunctioning. Replace or x valve.
7.4.
Problem: Valve does not operate when actuator operate.
Probable cause Corrective action
1.
Valve malfunctioning. Replace or x valve

9
7.5.
Problem: Valve does not operate when actuator operate.
Probable cause Corrective action
1.
Pressure supply system
malfunction.
Check pressure supply system.
2.
Incorrect installation. Refer to installation
procedure as described in this
document.
3.
Valve malfunctioning. Replace or x valve.
4.
Actuator malfunctioning. Replace actuator.
8. Guarantee
Our liability, with respect of any defect or failure of the goods
supplied or for any loss, injury or damage attributable onward is
limited to the replacement or repair of the defects which under
proper use appear therein and arise solely from faulty materials
and workmanship. This guarantee is for a period of 12 calendar
months after the original goods were rst shipped. No other
warranty is either expressed or implied.
Eu Machinery Directive Declaration Of Conformity Actuators:
The rotary pneumatic actuator range manufactured by EGMO,
together with add-on units (Limit switches, positioners, solenoid valves,
etc), all described in sales catalogue, conform to the requirements of
the Machinery Directive 2006/42/EC, and to the essential health and
safety requirements imposed by this directive.
Name: Ronen Cohen
Position: Q.A. Manager
Signature:
Although EGMO Ltd. can provide general guidelines, it cannot provide specic data and warnings
for all possible applications. The purchaser/user must therefore assume the ultimate responsibility
for the proper sizing and selection, installation, operation, and maintenance of EGMO Ltd. products.
The purchaser/user should read and understand the Installation Operation Maintenance (IOM)
instructions included with the product, and train its employees and contractors in the safe use
of EGMO Ltd. products in connection with the specic application. While the information and
specications contained in this literature are believed to be accurate, they are supplied for informative
purposes only and should not be considered certied or as a guarantee of satisfactory results by
reliance thereon. Nothing contained herein is to be construed as a warranty or guarantee, express or
implied, regarding any matter with respect to this product. EGMO Ltd. is continually improving and
upgrading its product design, Therefore the specications, dimensions and information contained
herein are subject to change without notice. Should any question arise concerning these provisions,
the purchaser/user should contact EGMO Corporation at any one of its worldwide operations or
oces. For more information about EGMO Ltd. Corporation, contact www.egmo.co.il
Table of contents
Popular Controllers manuals by other brands
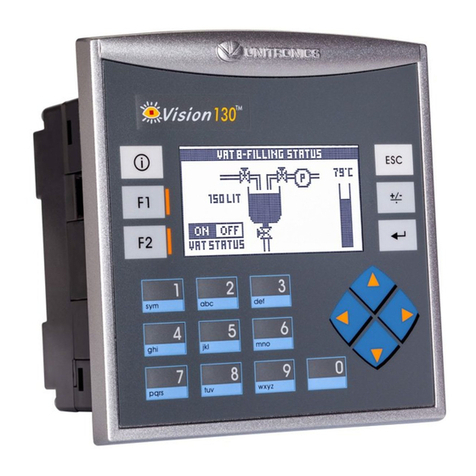
Unitronics
Unitronics Vision OPLC V130-J-TR20 installation guide
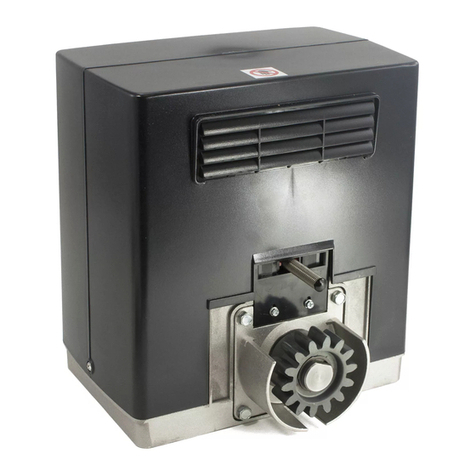
BFT
BFT DEIMOS BT Installation and user manual
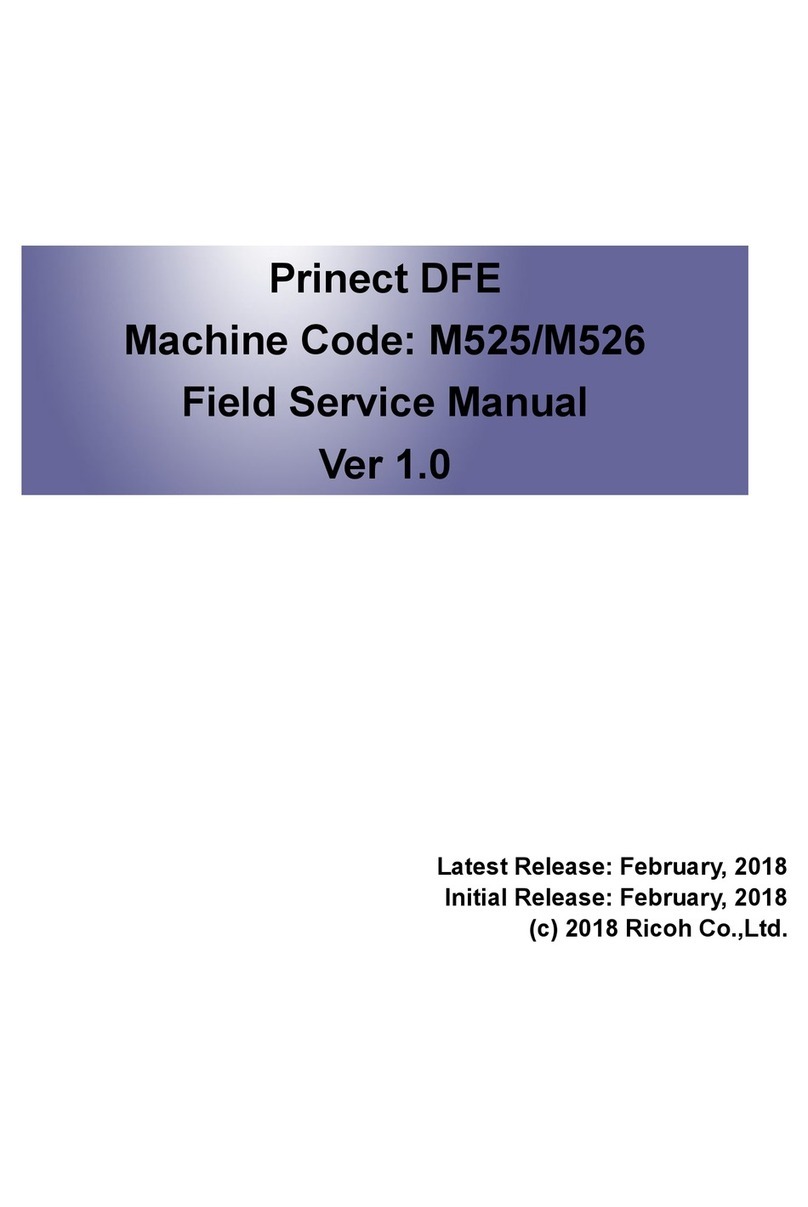
Ricoh
Ricoh Prinect DFE Field service manual
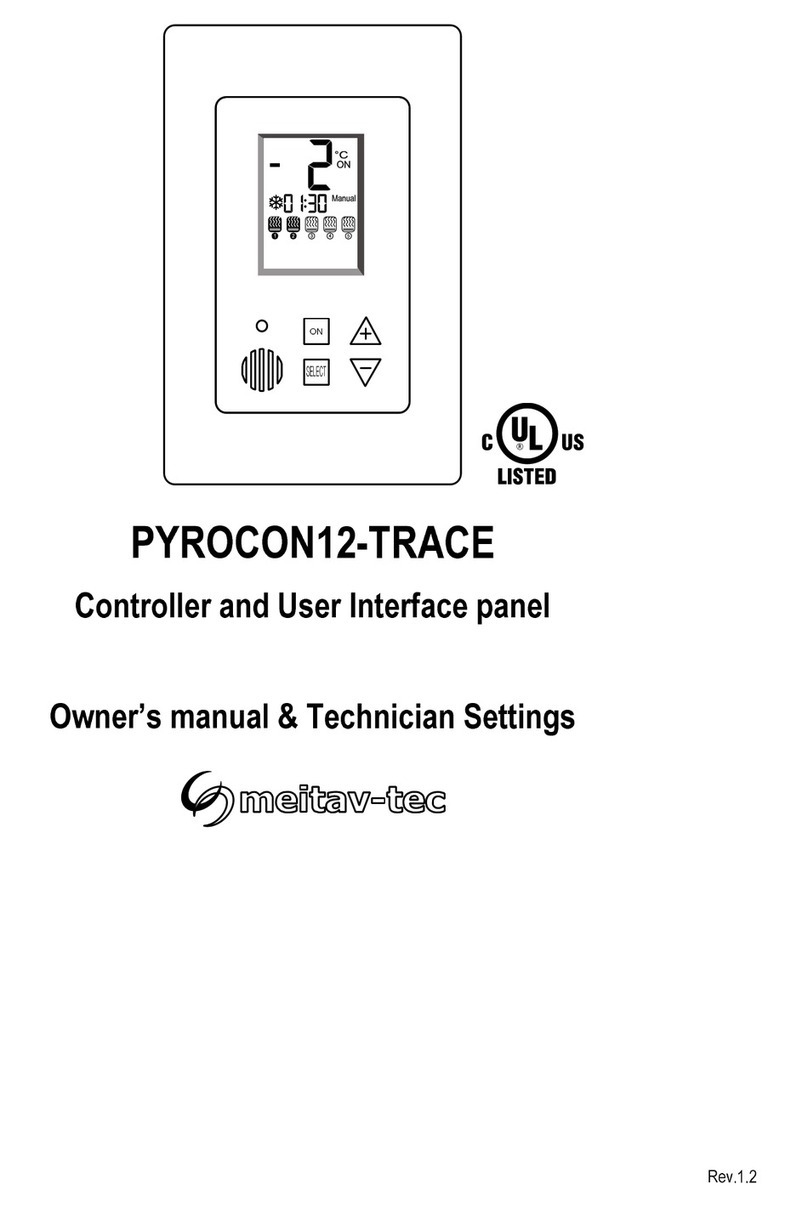
meitav-tec
meitav-tec PYROCON12-TRACE owner's manual
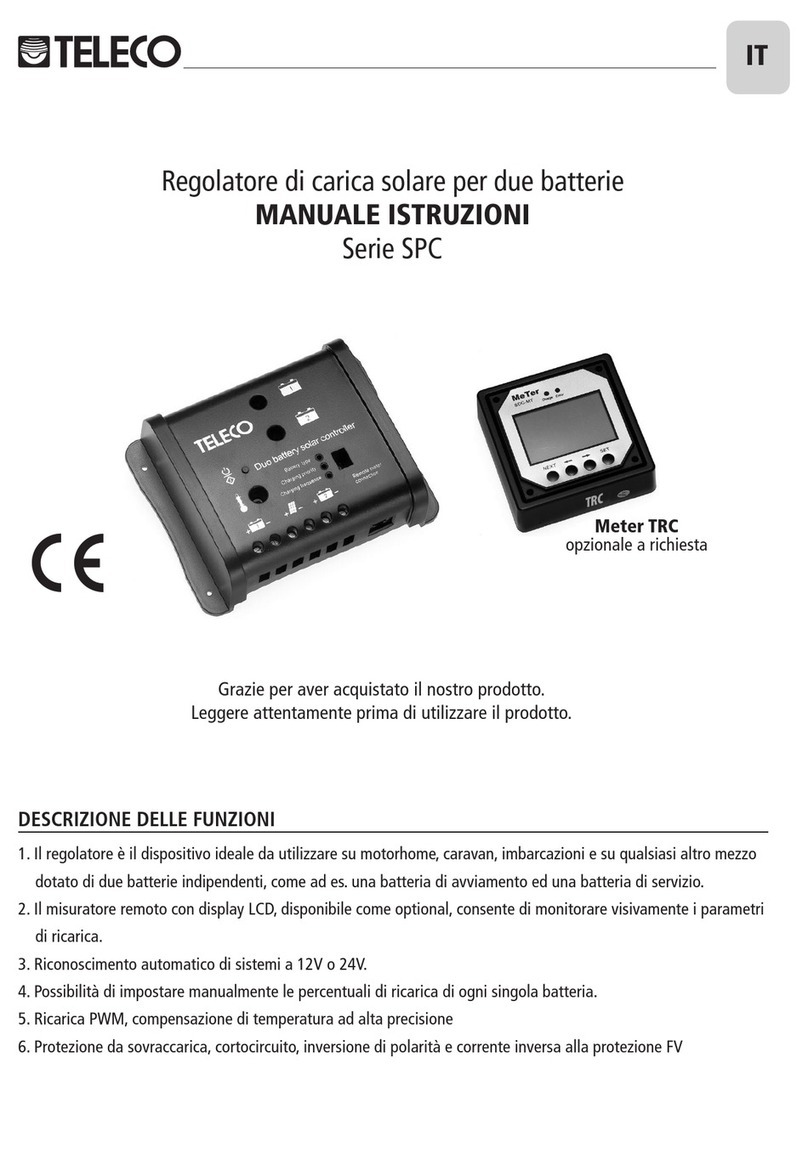
Teleco
Teleco SPC Series instruction manual
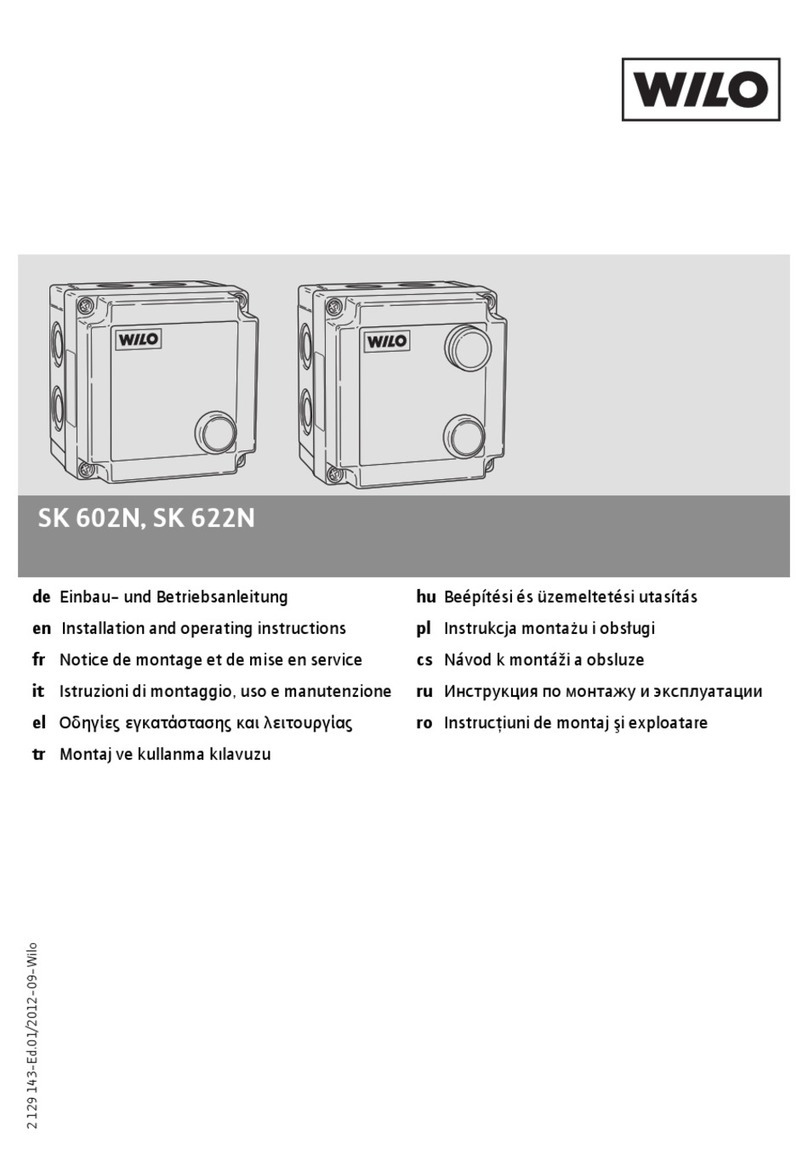
Wilo
Wilo SK 602N Installation and operating instructions
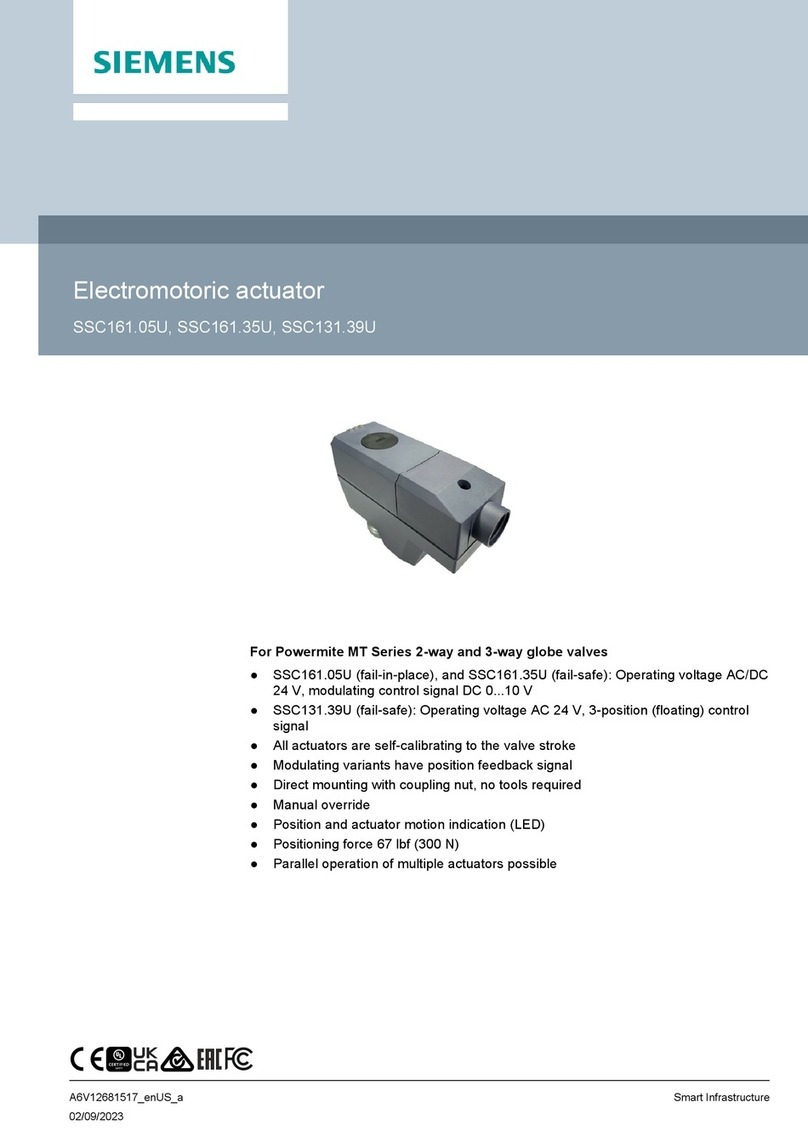
Siemens
Siemens SSC161.05U quick start guide
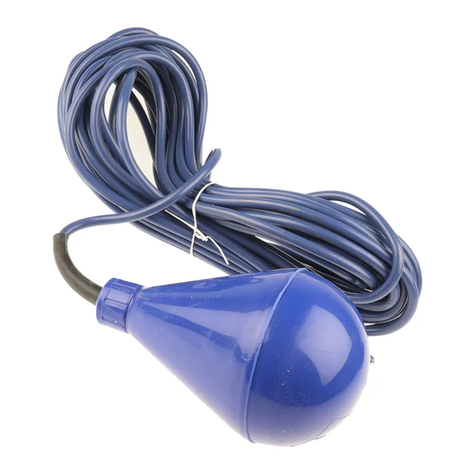
Xylem
Xylem Flygt ENM 10 Installation, Operation and Maintenace Manual
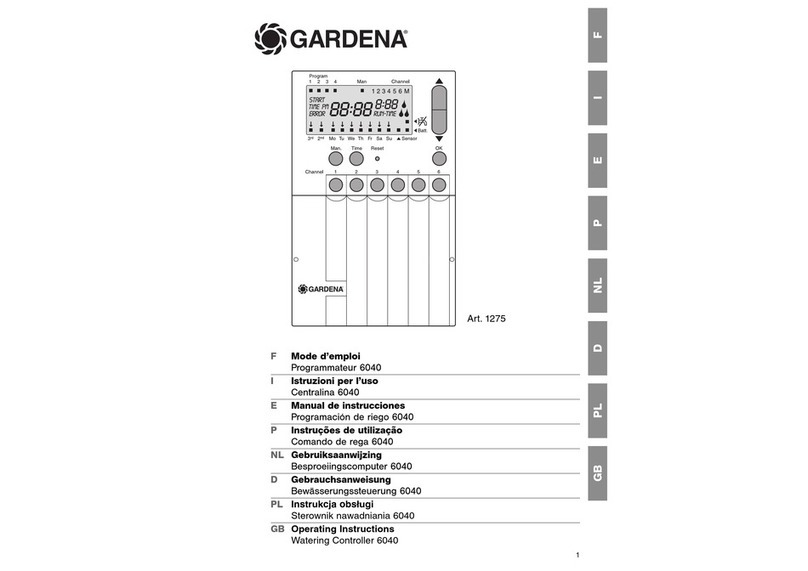
Gardena
Gardena Watering Controller 6040 operating instructions
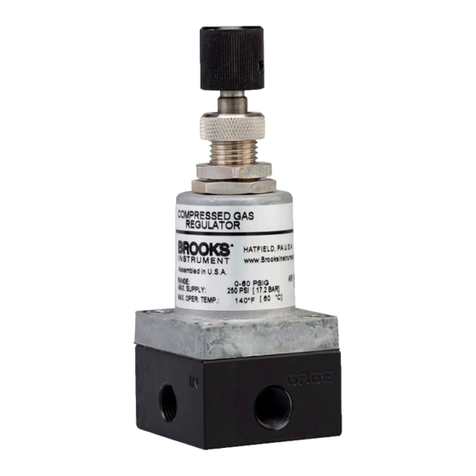
Brooks Instrument
Brooks Instrument 8601 Installation & operation manual
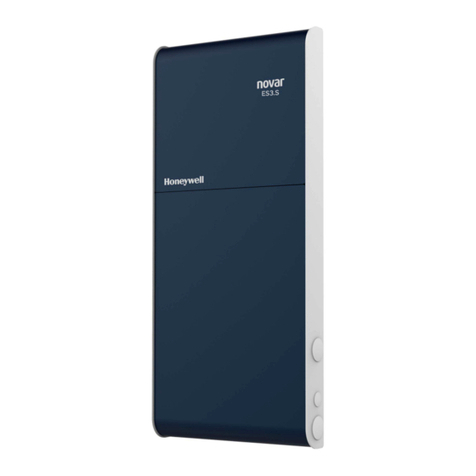
Honeywell
Honeywell Novar ES3.S Mounting and wiring instructions
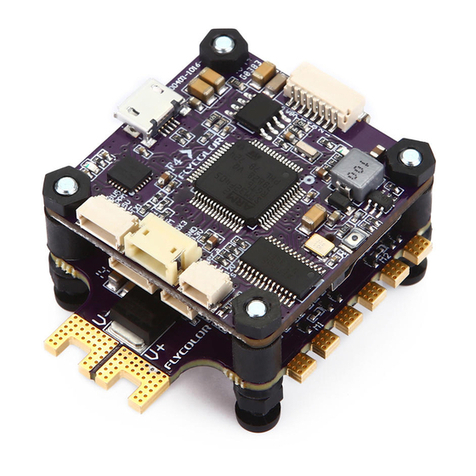
Flycolor
Flycolor Raptor S-Tower F4 user manual