Nexen ECLIPSE User manual

1FORM NO. L-21004-K-0914
FLANGE MOUNTED, AIR RELEASED,
SPRING ENGAGED SERVO BRAKE
Sizes 2, 3, 4 and 5
ECLIPSE PRODUCTS
User Manual

FORM NO. L-21004-K-0914 2
Copyright 2014 Nexen Group, Inc.
Nexen Group, Inc.
560 Oak Grove Parkway
Vadnais Heights, Minnesota 55127
ISO 9001 Certified
This document is the original, non-translated, version.
Conformity Declaration: In accordance with Appendix II B of CE Machinery Directive (2006/42/EC):
A Declaration of Incorporation of Partly Completed Machinery evaluation for the applicable EU directives was
carried out for this product in accordance with the Machinery Directive. The declaration of incorporation is set
out in writing in a separate document and can be requested if required.
This machinery is incomplete and must not be put into service until the machinery into which it is to be
incorporated has been declared in conformity with the applicable provisions of the Directive.
Read this manual carefully before installation and operation.
Follow Nexen’s instructions and integrate this unit into your
system with care. This unit should be installed, operated and
maintained by qualified personnel ONLY. Improper installation
can damage your system, cause injury or death. Comply with
all applicable codes.
DANGER
In accordance with Nexen’s established policy of constant product improvement, the specifications contained in this
manual are subject to change without notice. Technical data listed in this manual are based on the latest information
available at the time of printing and are also subject to change without notice.
Technical Support: 800-843-7445
(651) 484-5900
www.nexengroup.com

3FORM NO. L-21004-K-0914
Table of Contents
General Specifications ------------------------------------------------------------------------------------------------------------------------- 4
General Safety Precautions ------------------------------------------------------------------------------------------------------------------ 4
Installation:
Mounted on the Shaft End of a Motor ----------------------------------------------------------------------------------------5
Installation - Mounted between a Gear Reducer and a Motor ------------------------------------------------------7
Lubrication -----------------------------------------------------------------------------------------------------------------------------------------8
Air Connections ---------------------------------------------------------------------------------------------------------------------------------8
Operation ------------------------------------------------------------------------------------------------------------------------------------------9
Brake Assembly --------------------------------------------------------------------------------------------------------------------------------9
Bearing, O-Ring, Seals and Wave Spring Assembly ----------------------------------------------------------------------------10
Friction Facing Assembly ------------------------------------------------------------------------------------------------------------------12
Troubleshooting --------------------------------------------------------------------------------------------------------------------------------12
Replacement Parts List----------------------------------------------------------------------------------------------------------------------13
Accessories--------------------------------------------------------------------------------------------------------------------------------------13
Warranty ------------------------------------------------------------------------------------------------------------------------------------------14

FORM NO. L-21004-K-0914 4
WARNING
GENERAL SPECIFICATIONS
Size
Min Holding
Torque
Torsional Rigidity
(Estimated)
Inertia
(Calculated) Weight
Min. Disengagement
Air Pressure
Size 2 2.25 Nm
[1.66 ft*lb]
6180 Nm/RAD
[4550 ft*lb/RAD]
0.00002 kg*m^2
[0.0005 lb*ft^2]
1.1 kg
[2.4 lbs]
5.5 bar
[80 psi]
Size 3 8 Nm
[5.90 ft*lb]
9613 Nm/RAD
[7090 ft*lb/RAD]
0.00005 kg*m^2
[0.0012 lb*ft^2]
1.5 kg
[3.2 lbs]
5.5 bar
[80 psi]
Size 4 22 Nm
[16.2 ft*lb]
23,796 Nm/RAD
[17,550 ft*lb/RAD]
0.00031 kg*m^2
[0.0074 lb*ft^2]
3 kg
[8.5 lbs]
5.5 bar
[80 psi]
Size 5 45 Nm
[33 ft*lb]
36,184 Nm/RAD
[26,690 ft*lb/RAD]
0.00114 kg*m^2
[0.0271 lb*ft^2]
6.3 kg
[13.8 lbs]
5.5 bar
[80 psi]
GENERAL SAFETY PRECAUTIONS
CAUTION
Watch for sharp features when
interacting with this product. The parts
have complex shapes and machined
edges.
This product is capable of emitting
a spark if misused, therefore it is not
recommended for use in any explosive
environment.
CAUTION CAUTION
Use appropriate guarding for moving
components. Failure to guard could
result in serious bodily injury.
The temperature limits for the product
are 4.5-104 degree Celsius (40-220
degree F).
Pneumatic units accept an optional solenoid valve (normally closed) controlled by 24VDC at 104 mA. Solenoid valves are
fitted with 18” flying leads standard. To order the solenoid valve (optional), please refer to Nexen product #964650.
CAUTION
Use appropriate guarding for moving
components. Failure to guard could
result in serious bodily injury.
WARNING
Ensure proper guarding of the product is
used. Nexen recommends the machine
builder design guarding in compliance
with OSHA 29 CFR 1910 “Occupational
Safety and Health Hazards”.

5FORM NO. L-21004-K-0914
INSTALLATION
MOUNTED ON THE SHAFT END OF A MOTOR
NOTE: Refer to Figures 1, 2, 3.
1. Insert the Keyless Bushing (Item 7) into the Servo
Brake.
2. Turn the Keyless Bushing (Item 7) counterclockwise
to maximize the Keyless Bushing’s inside diameter.
Note: Do not lubricate either the Keyless Bushing
or the Shaft. The use of any lubricant on the
contact surfaces could result in Bushing failure. If
necessary, clean the Shaft with a non-petroleum
based solvent, such as isopropyl alcohol.
3. Insert the Motor Shaft into the Keyless Bushing (Item
7) until the Flanges of the Motor and Brake meet.
4. Loosely bolt the Flanges together on at least two
diagonally opposite corners using customer supplied
fasteners.
5. Remove the Access Plug (Item 14) from the access
slot in the Input Flange (Item 10). Use an open end
adjustable wrench to grasp the end of the brake shaft
on its flat surface and hold it stable while you tighten
the Keyless Bushing (Item 7) with the supplied wrench.
Refer to Table 1 for the recommended torque values.
NOTE: The wrench that is supplied with Servo
Brake sizes 2 and 3 is designed to accept a
3/8” drive, extension handle. The wrench that is
supplied with Servo Brake size 4 and 5 is designed
to accept a 1/2” drive, extension handle.
6. Torque the customer supplied fasteners that join the
Flanges together to the recommended values on Table
2.
7. Insert the Access Plug (Item 14) into the access slot
in the Input Flange (Item 10).
FIGURE 2
Access Plug
(Item 14) Customer Supplied
Fastener
Exhaust Valve
(Item 23)
Square Motor
with
Attached Flange
Bushing
(Item 7)
Brake
Input Flange
(Item 10)
FIGURE 1
continued...
Input
Flange
(Item 10)
Supplied
Wrench
DANGER
Support the load before disengaging
the brake. Failure to support the load
could result in serious bodily injury.
CAUTION
Do not over-torque the Fasteners.
Over tightening can lead to premature
bearing failure. Finger tighten only.
CAUTION
Overtightening the Bushing can damage the
Bushing or the Shaft. Combine length of
the torque wrench with the Nexen Wrench to
determine the proper torque values.

FORM NO. L-21004-K-0914 6
MOUNTED ON THE SHAFT END OF A MOTOR (continued)
8. Standard Configuration:
Attach the Quick Exhaust Valve (Item 23) to the brake.
Use Teflon tape and/or pipe sealant on the threads.
With Optional Solenoid:
If you are using the optional Solenoid Valve (Part
#964650), the Quick Exhaust Valve is unnecessary.
Assemble the optional Solenoid Valve directly to the
brake using the supplied fittings. Use Teflon tape and/
or pipe sealant on the threads. The fitting for the air
line itself is O-ring sealed and does not require tape
or sealant.
Note: The Servo Brake will disengage if you
depress the domed button on top of the Solenoid
Valve (if air pressure is supplied). The LED will
illuminate when the Solenoid Valve is actuated
and the Servo Brake is disengaged. Unit has been
designed to release before (at or below) 5.5 bar [80
psi]. Required disengagement pressure higher than
5.5 bar [80 psi] may indicate improper assembly.
NOTE: Align the air inlet ports in the down position
to allow condensation to drain out of the air
chamber.
9. Assemble the air line to the valve
10. Connect the lead wires from the valve to the brake
control connection points on the Motor Drive or the
PLC. Refer to Table 3.
Lead Wire Cable:
Brown wire = positive
White wire = common
Green wire = ground
11. Assemble the Gear Reducer or the load to the Brake
Shaft.
FIGURE 3 Optional Solenoid Valve Part #964650.
Exhaust
Silencer
To Brake
Air Supply
Tube Fitting
Manual
Override
DIN
Connector
Lead Wires
DANGER
Support the load before disengaging
the brake. Failure to support the load
could result in serious bodily injury.

7FORM NO. L-21004-K-0914
NOTE: Refer to Figure 4
1. To mount the Servo Brake to the Motor refer to the
INSTALLATION section.
2. Insert the Brake Shaft into the customer supplied gear
reducer coupling. Use the supplied key, if required.
3. Use customer supplied screws, washers and nuts to bolt
the flanges together. Apply Loctite®242 to the threads
of the screws. For recommended torque values, refer
to Table 2.
4. Tighten the Coupling. Refer to the instructions that
are supplied with the Gear Reducer.
5. Install any plugs or related items that are detailed in the
Gear Reducer instructions.
TABLE 3
TABLE 1
INSTALLATION
MOUNTED BETWEEN A GEAR REDUCER AND A MOTOR
TABLE 2
Access Plug
(Item 14) Customer Supplied
Fastener
Square Motor
with
Attached Flange
Bushing
(Item 7)
Input Flange
(Item 10)
Gear
Reducer
Exhaust Valve
(Item 23)
Brake
FIGURE 4
Size 2
Size 3
Size 4
Size 5
M5
M6
M8
M10
Socket Head
Cap Screw
(Customer Supplied)
Brake
Model
7 Nm
(63 in/lb)
12 Nm
(107 in/lb)
29 Nm
(260 in/lb)
58 Nm
(520 in/lb)
Recommended
Fastening
Torque
Size 2
Size 2
Size 3
Size 4
Size 5
Size 5
6mm-10mm
11mm-16mm
11mm-16mm
19mm-25mm
19mm-25mm
28mm-32mm
Shaft
Size
Brake
Model
17.0 N-m (150 in/lb)
22.6 N-m (200 in/lb)
22.6 N-m (200 in/lb)
84.4 N-m (750 in/lb)
84.4 N-m (750 in/lb)
113.0 N-m (1000 in/lb)
Recommended
Bushing
Torque
76.2 mm (3.0 in)
76.2 mm (3.0 in)
76.2 mm (3.0 in)
101.6 mm (4.0 in)
101.6 mm (4.0 in)
101.6 mm (4.0 in)
Supplied
Wrench
Length
13.6 N-m (120 in/lb)
18.0 N-m (160 in/lb)
18.0 N-m (160 in/lb)
65.0 N-m (575 in/lb)
65.0 N-m (575 in/lb)
86.0 N-m (760 in/lb)
Torque Required
Using
Supplied Wrench
Standard Coil:
24VDC
2.5 Watts
Power
Voltage
235 Ohms
Resistance Current CV
.100 Amps .08
OPTIONAL SOLENOID VALVE SPECIFICATIONS
DANGER
Support the load before disengaging
the brake. Failure to support the load
could result in serious bodily injury.

FORM NO. L-21004-K-0914 8
NOTE
Nexen pneumatically actuated devices require clean, pressure regulated air for maximum performance and
life. All seals in Nexen Pneumatically operated devices are lubricated for life and do not require additional
lubrication.
However, some customers prefer to use an air line lubricator, which injects oil into the pressurized air,
forcing an oil mist into the air chamber. This is acceptable, but care must be taken to ensure once an air mist
lubrication system is used, it is continually used over the life of the product as the oil mist may wash free the
factory installed lubrication.
Locate the lubricator above and within ten feet of the product, and use low viscosity oil such as SAE-10.
Synthetic lubricants are not recommended.
Nexen product’s bearings are shielded and pre-lubricated, and require no further lubrication.
LUBRICATOR DRIP RATE SETTINGS
1. Close and disconnect the air line from the unit.
2. Turn the Lubricator Adjustment Knob counterclockwise three
complete turns.
3. Open the air line.
4. Close the air line to the unit when a drop of oil forms in the
Lubricator Sight Gage.
5. Connect the air line to the unit.
6. Turn the Lubricator Adjustment Knob clockwise until
closed.
7. Turn the Lubricator Adjustment Knob counterclockwise one-
third turn.
8. Open the air line to the unit.
AIR CONNECTIONS
NOTE
For quick response, Nexen recommends a quick
exhaust valve and short air lines between the
Control Valves and the unit. Align the air inlet ports
to a down position to allow condensation to drain
out of the air chambers of the product.
LUBRICATION
CAUTION
These settings are for Nexen supplied
lubricators. If you are not using a Nexen
lubricator, calibration must follow the
manufacturer’s suggested procedure.
CAUTION
Low air pressure will cause slippage and
overheating. Excessive air pressure will
cause abrupt starts and stops, reducing
product life.
All Nexen pneumatically actuated devices require clean
and dry air, which meet or exceeds ISO 8573.1:2001
Class 4.4.3 quality.
Air
Supply
Brake
Inlet
Gauge
Regulator
Filter
Dryer
Typical Brake Control Circuit
3/2 (3 Way)
N.C. Valve
Quick
Exhaust Valve
AIR PRESSURE:
8 BAR (120 PSI) ABSOLUTE MAX
0 BAR (0 PSI) ABSOLUTE MIN
The following is a common air supply scheme used with
this product. This is an example and not an all-inclusive
list. All air circuits to be used with this product must be
designed following ISO 4414 guidelines.

9FORM NO. L-21004-K-0914
Output
Shaft
Piston
Bearing
Keyless
Bushing
Female
Pilot
Male
Pilot
O-ring
Seals
Air
Chamber
Friction
Facing
Air to
Brake
Wave
Spring
FIGURE 5
BRAKE ASSEMBLY
Quick Exhaust Valve
and/or
Optional Solenoid Valve
Input
Flange
Dowel
Pin
WARNING
Never exceed maximum operating speeds
listed for your product. (See Table 4).
OPERATION
CAUTION
CAUTION
TABLE 4
The temperature limits for this product
line are 4.5-104 Degree Celsius (40-
220 Degree F).
Never exceed life of facing material. Facing
life depends on the volume of material and
the total energy over the life of the unit.
Expected life (in hrs) can be found by:
Time=Volume/(Power*Wear Rate).
Sizes Max RPM
Size 2-5 10,000

FORM NO. L-21004-K-0914 10
BEARING, O-RING, SEALS AND WAVE SPRING ASSEMBLY
SIZES 2, 3, 4, 5
NOTE: Refer to Figures 6 and 7
1. Alternately and evenly, remove the four Socket Head
Cap Screws (Item 11) and separate the Air Chamber
(Item 6) from the Input Flange (Item 10).
2. Remove the Output Shaft (Item 1) from the Ball
Bearing (Item 2) by pressing in on the output shaft.
Remove the dowel pin (Item 21) by pressing the Dowel
Pin into the Air Chamber (Item 6).
3. Remove the Piston (Item 5) and Wave Spring (Item 9)
from the Air Chamber (Item 6). You may need to apply
compressed air to the air inlet to remove the Piston.
4. Remove the old O-ring Seals (Items 3, 4) from the
Piston.
5. Press the Bearing (Item 2) out of the Air Chamber
(Item 6).
6. Clean the bearing bore of the Air Chamber (Item 6)
with fresh solvent, removing all old Loctite®.
7. Apply continuous bead of Loctite®680 around the
inner circumference of the Air Chamber (Item 6)
bearing bore.
8. Carefully align the outer race of the new Bearing (Item
2) with the bore of the Air Chamber (Item 6).
9. Supporting the Air Chamber (Item 6) and pressing on
the outer race of the new Bearing (Item 2), press the
new Bearing into the Air Chamber.
10. Visually inspect the inner diameter grooves and the
outer diameter grooves of the Piston (Item 5) for
debris. Clean as necessary.
11. Coat the O-ring contact surfaces of the Air Chamber
(Item 6), the Piston (Item 5), and the O-ring Seals
(Items 3, 4) with a thin film of O-ring lubricant and
install the new O-ring Seals.
12. Slide the Piston (Item 5) into the Air Chamber
(Item 6).
13. Install the replacement Dowel Pin (Item 21) so that it
is flush with the outer edge of the Air Chamber (Item
6).
14. Clean the friction surface of the Air Chamber (Item 6)
with solvent.
Item 8
Item 9
Item 7
Item 10
Item 14
Item 11
Item 6
Item 2
Item 3
Item 5
Item 4
Item 1
Item 20
Item 23
Item 21
FIGURE 6
FIGURE 7
(continued...)
CAUTION
Working with spring or tension loaded
fasteners and devices can cause injury.
Wear safety glasses and take the
appropriate safety precautions.

11 FORM NO. L-21004-K-0914
TABLE 5
15. Support the inner race of the new Ball Bearing (Item
2) and press the Output Shaft (Item 1) into the new
Bearing (Item 2) and Air Chamber (Item 6).
16. Place the Friction Facing (Item 8) into the Air Chamber
(Item 6) so that the angled surfaces match up with the
wall of the Air Chamber and the tapered disc of the
Output Shaft (Item 1). The gap in the Friction Facing
must straddle the Dowel Pin (Item 21).
17. Replace the Wave Spring (Item 9) and Input Flange
(Item 10).
Note: Keep the Wave Spring centered relative
to the Friction Facing. If the Wave Spring is not
centered, the brake could fail to disengage during
operation.
18. Apply a drop of Loctite®242 to the threads of the
Socket Head Cap Screws (Item 11).
19. Reinstall and tighten the four Socket Head Cap
Screws (Item 11), securing the Air Chamber (Item
6) to the Input Flange (Item 10). Alternate as you
tighten the four Socket Head Cap Screws so that the
input flange remains evenly parallel to the Air Chamber
and does not pinch the Wave Spring (Item 9). Refer
to Table 5 for the recommended assembly torque
values.
Note: The Servo Brake could fail to disengage if
the Wave Spring becomes pinched between the
Friction Facing and the Input Flange.
BEARING, O-RING, SEALS AND WAVE SPRING ASSEMBLY (continued...)
Size 2
Size 3
Size 4
Size 5
M4
M5
M6
M8
Socket Head
Cap Screw
(Item 11)
Brake
Model
4.2-5.4 Nm
(37-48 in/lb)
7.0-9.2 Nm
(62-81 in/lb)
9.2-11.9 Nm
(81-105 in/lb)
26.2-34.0 Nm
(232-301 in/lb)
Recommended
Assembly
Torque

FORM NO. L-21004-K-0914 12
NOTE: Refer to Figures 8 and 9
1. Alternately and evenly, remove the four Socket Head
Cap Screws (Item 11) and separate the Air Chamber
(Item 6) from the Input Flange (Item 10).
2. Remove the Input Flange (Item 10) and the Wave
Spring (Item 9).
3. Remove and replace the Friction Facing (Item 8) in the
Air Chamber (Item 6). Make certain that the angled
sides mate with the wall of the Air Chamber and the
tapered disc of the Output Shaft (Item 1). The gap in
the Friction Facing must straddle the Dowel Pin (Item
21).
4. Replace the Wave Spring (Item 9) and Input Flange
(Item 10).
Note: Keep the Wave Spring centered relative to the
Friction Facing. If the Wave Spring is not centered,
the brake could fail to disengage.
5. Apply a drop of Loctite®242 to the threads of the
Socket Head Cap Screws (Item 11).
6. Reinstall and tighten the four Socket Head Cap
Screws (Item 11), securing the Air Chamber (Item 6)
to the Input Flange (Item 10). Alternate as you tighten
the four Socket Head Cap Screws so that the input
flange remains evenly parallel to the air chamber and
does not pinch the Wave Spring (Item 9). Refer to
Table 5 for the recommended assembly torque values.
Note: The Servo Brake could fail to disengage if
the Wave Spring becomes pinched between the
Friction Facing and the Input Flange.
FRICTION FACING ASSEMBLY
Item 8
Item 9
Item 7
Item 10
Item 14
Item 11
FIGURE 8
TROUBLESHOOTING
Failure to engage (brake).
Failure to disengage.
Loss of torque.
Weak or broken wave spring.
Control valve malfunction - air not getting to the
brake
.
After re-assembly, the Input flange is pinching the
spring.
Air is leaking around the O-ring seals.
Friction Facing is worn or dirty.
Probable Cause
Problem Solution
Replace the wave spring.
Check for low air pressure or replace the
control valve.
NOTE: Unit has been designed to release
before (at or below) 5.5 Bar [80 psi].
Required disengagement pressure higher
than 5.5 bar [80 psi] may indicate
improper assembly.
Carefully reinstall Flange.
Replace the O-rings.
Replace the friction facing.
Item 6
Item 2
Item 3
Item 5
Item 4
Item 1
Item 20
Item 23
Item 21
FIGURE 9
CAUTION
Working with spring or tension loaded
fasteners and devices can cause injury.
Wear safety glasses and take the
appropriate safety precautions.

13 FORM NO. L-21004-K-0914
REPLACEMENT PARTS LIST
ITEM DESCRIPTION QTY
1 Output Shaft 1
2 Ball Bearing 1
3 O-ring Seal 1
4 O-ring Seal 1
5 Piston 1
6 Air Chamber 1
7 Keyless Bushing 1
8 Friction Facing 1
9 Wave Spring 1
10 Input Flange 1
11 Socket Head Cap Screw 4
12 Solenoid Valve (Optional) 1
14 Access Plug 1
20 Square Key 1
21 Dowel Pin 1
23 Quick Exhaust Valve, Eclipse 1
Item 1
Item 2
Item 3
Item 5
Item 4
Item 8
Item
11
Item 9
Item 7
Item 10
Item 14
Item 23
FIGURE 10
Item 20
Item 21
Item 6
ACCESSORIES
DESCRIPTION PROD. NO.
Optional Solenoid Valve.......................................................................................................................................................................................................964650
The Item or “Balloon” Number for all Nexen Products is
used for part identification on all Product Parts List, Product
Price List, Unit Assembly Drawings, Bills of Materials, and
Instruction Manuals.
When ordering replacement parts, specify model
designation, item number, part description, and quantity.
Purchase replacement parts through your local Nexen
Distributor.

FORM NO. L-21004-K-0914 14
Nexen Group, Inc.
560 Oak Grove Parkway
Vadnais Heights, MN 55127
800.843.7445
Fax: 651.286.1099
www.nexengroup.com
ISO 9001 Certified
WARRANTY
Warranties
Nexen warrants that the Products will (a) be free from any defects in material or workmanship for a period of 12 months
from the date of shipment, and (b) will meet and perform in accordance with the specifications in any engineering drawing
specifically for the Product that is in Nexen’s current product catalogue, or that is accessible at the Nexen website, or that is
attached to this Quotation and that specifically refers to this Quotation by its number, subject in all cases to any limitations
and exclusions set out in the drawing. NEXEN MAKES NO OTHER WARRANTY, EXPRESS OR IMPLIED, AND ALL
IMPLIED WARRANTIES, INCLUDING WITHOUT LIMITATION, IMPLIED WARRANTIES OF MERCHANTABILITY AND
FITNESS FOR A PARTICULAR PURPOSE ARE HEREBY DISCLAIMED. This warranty applies only if: (a) the Product
has been installed, used and maintained in accordance with any applicable Nexen installation or maintenance manual
for the Product; (b) the alleged defect is not attributable to normal wear and tear; (c) the Product has not been altered,
misused or used for purposes other than those for which it was intended; and (d) Buyer has given written notice of the
alleged defect to Nexen, and delivered the allegedly defective Product to Nexen, within one year of the date of shipment.
Exclusive Remedy
The exclusive remedy for the Buyer for any breach of any warranties provided in connection with this agreement will be,
at the election of Nexen: (a) repair or replacement with new, serviceably used, or reconditioned parts or products; or (b)
issuance of credit in the amount of the purchase price paid to Nexen by the Buyer for the Products.
Agent's Authority
Buyer agrees that no agent, employee or representative of Nexen has authority to bind Nexen to any affirmation,
representation, or warranty concerning the Products other than those warranties expressly set forth herein.
Limitation on Nexen’s Liability
TO THE EXTENT PERMITTED BY LAW NEXEN SHALL HAVE NO LIABILITY TO BUYER OR ANY OTHER PERSON
FOR INCIDENTAL DAMAGES, SPECIAL DAMAGES, CONSEQUENTIAL DAMAGES OR OTHER DAMAGES OF
ANY KIND OR NATURE WHATSOEVER, WHETHER ARISING OUT OF BREACH OF WARRANTY OR OTHER
BREACH OF CONTRACT, NEGLIGENCE OR OTHER TORT, OR OTHERWISE, EVEN IF NEXEN SHALL HAVE
BEEN ADVISED OF THE POSSIBILITY OR LIKELIHOOD OF SUCH POTENTIAL LOSS OR DAMAGE. For all of
the purposes hereof, the term "consequential damages" shall include lost profits, penalties, delay damages, liquidated
damages or other damages and liabilities which Buyer shall be obligated to pay or which Buyer may incur based upon,
related to or arising out of its contracts with its customers or other third parties. In no event shall Nexen be liable for any
amount of damages in excess of amounts paid by Buyer for Products or services as to which a breach of contract has
been determined to exist. The parties expressly agree that the price for the Products and the services was determined
in consideration of the limitation on damages set forth herein and such limitation has been specifically bargained for and
constitutes an agreed allocation of risk which shall survive the determination of any court of competent jurisdiction that
any remedy herein fails of its essential purpose.
Inspection
Buyer shall inspect all shipments of Products upon arrival and shall notify Nexen in writing, of any shortages or other failures
to conform to these terms and conditions which are reasonably discoverable upon arrival without opening any carton
or box in which the Products are contained. Such notice shall be sent within 14 days following arrival. All notifications
shall be accompanied by packing slips, inspection reports and other documents necessary to support Buyer's claims. In
addition to the foregoing obligations, in the event that Buyer receives Products that Buyer did not order, Buyer shall return
the erroneously shipped Products to Nexen within thirty (30) days of the date of the invoice for such Products; Nexen
will pay reasonable freight charges for the timely return of the erroneously shipped Products, and issue a credit to Buyer
for the returned Products at the price Buyer paid for them, including any shipping expenses that Nexen charged Buyer.
All shortages, overages and nonconformities not reported to Nexen as required by this section will be deemed waived.
Limitation on Actions
No action, regardless of form, arising out of any transaction to which these terms and conditions are applicable may be
brought by the Buyer more than one year after the cause of action has accrued.
Table of contents
Other Nexen Engine manuals
Popular Engine manuals by other brands

ATIKA
ATIKA MHB 80 Original instructions

BRP
BRP ROTAX 125 MAX DD2 evo Installation instructions and operators manual
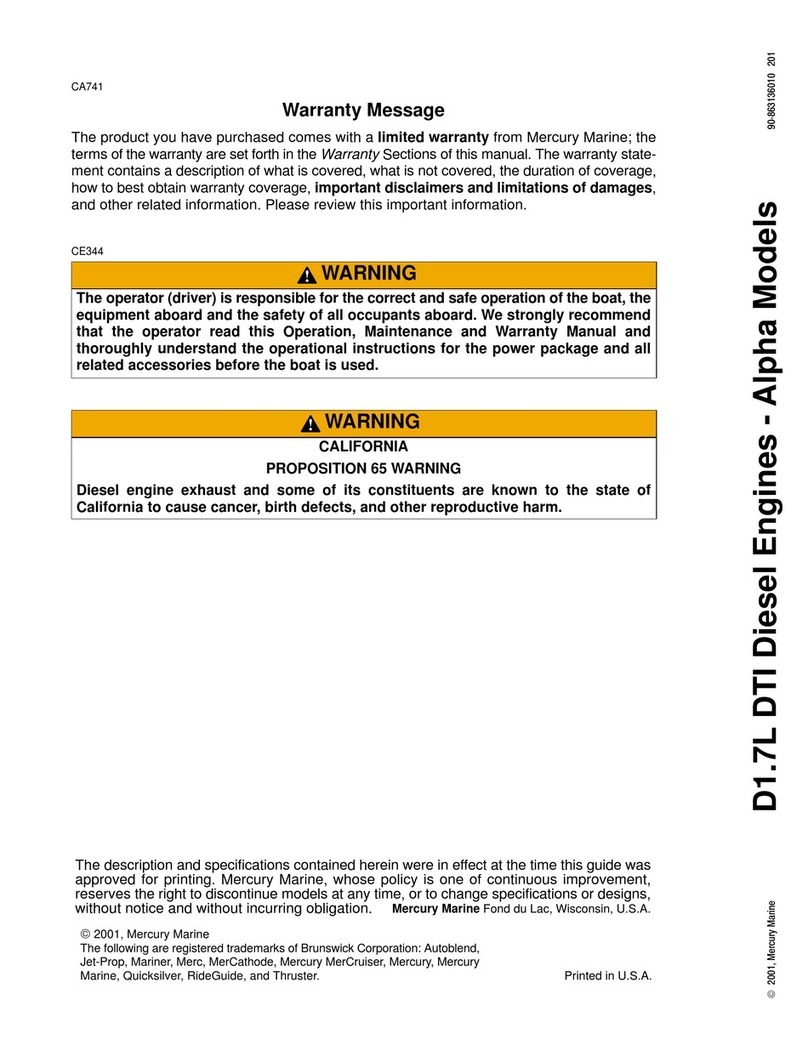
Mercury
Mercury D1.7L DTI Alpha Operation, maintenance and warranty manual
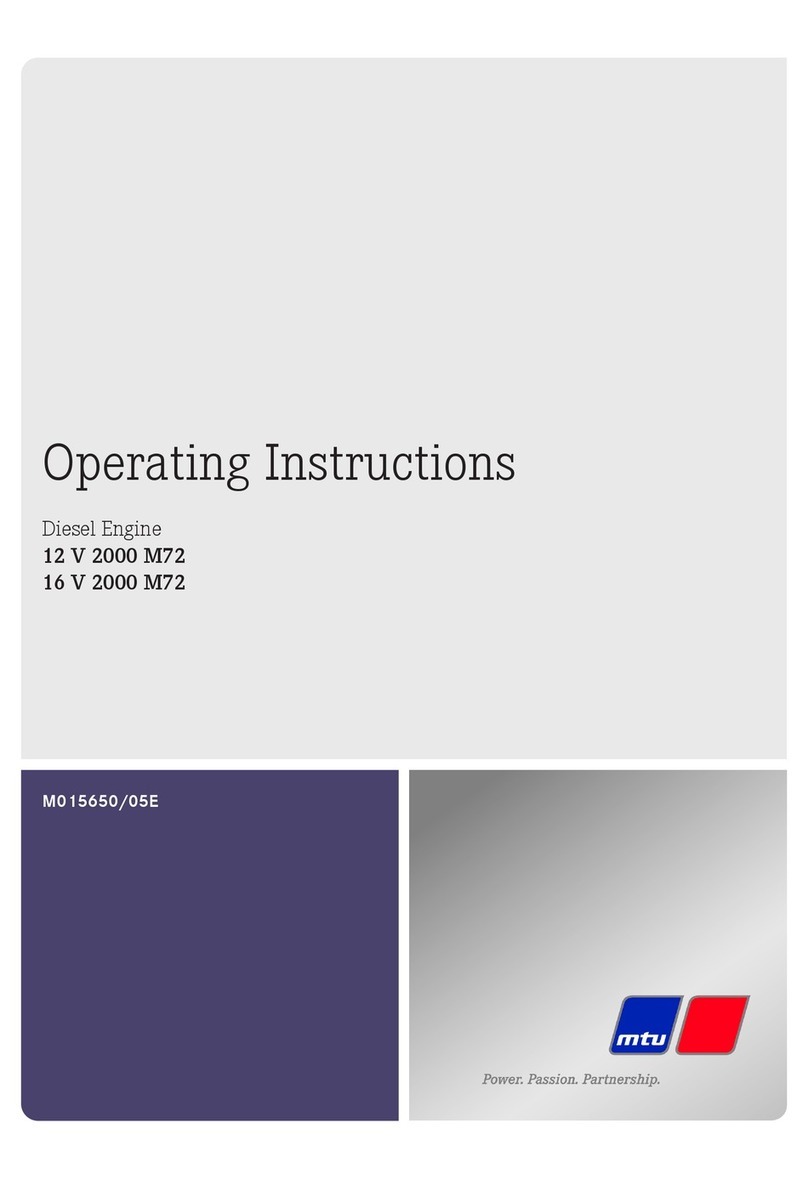
MTU
MTU 12 V 2000 M72 operating instructions

Baumer Hübner
Baumer Hübner ME 11 Installation and Operating Instrucitons
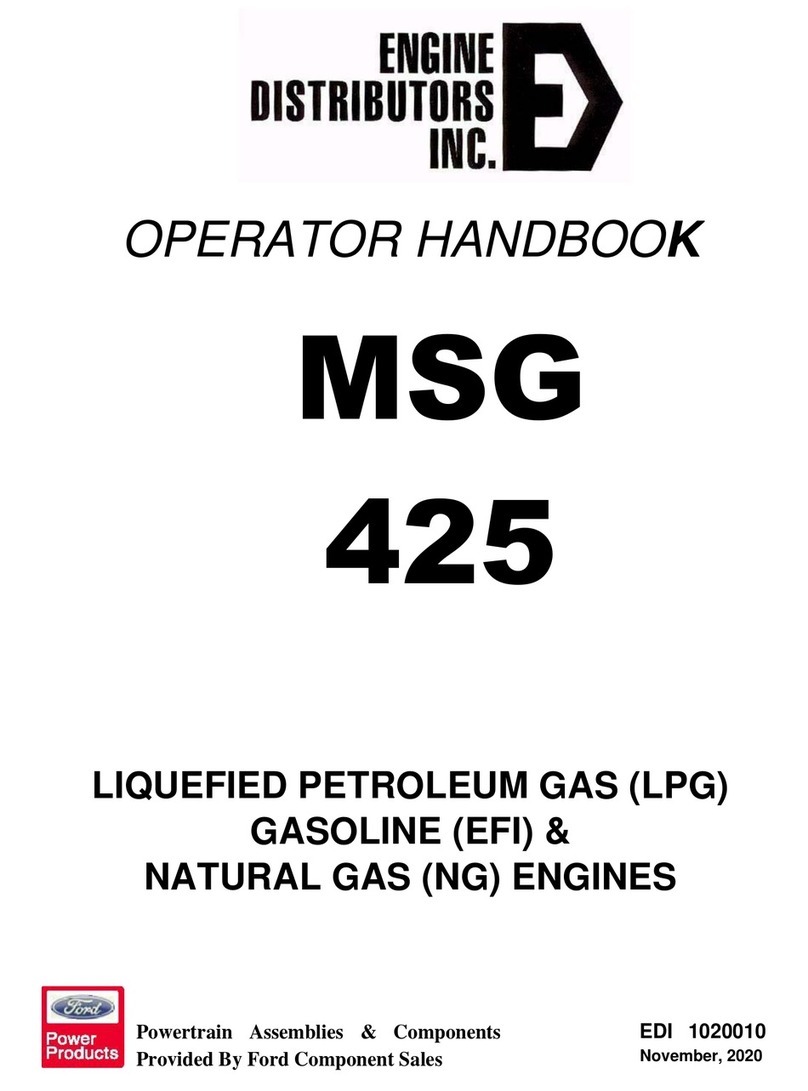
Engine distributors
Engine distributors MSG 425 Operator's handbook