NIPPON POP RIVETS AND FASTENERS PNT600 User manual

POP NUT TOOL
PNT600
INSTRUCTION MANUAL
The PNT600 is solely for use with Pop Nuts.
Read this manual thoroughly before you start and use the PNT600 according
to the instructions.
Store this manual where the person who uses the tool may refer to it easily.
NIPPON POP RIVETS AND FASTENERS LTD.

CONTENTS
SafetyPrecautions
・・・・1
1.Part names
・・・・4
2.Outlines
・・・・5
3.Specifications
・・・・6
4.Preparations for use
・・・・7
5.Precautions on use
・・・・11
6.How to use the PNT600
・・・・12
7.Maintenance and testing
・・・・15
8.Troubleshooting
・・・・22
9.Parts List
・・・・24
10.Cross-sectional diagram of the PNT600 ・・・・26

Safety Precautions
-Read all the safety precautions carefully before you use this tool and
observe them carefully in practice.
-The safety precautions are classified as follows:
WARNING!
Incorrect operation caused by failure to observe this type of precaution
could cause death or serious injury.
Caution!
Incorrect operation caused by failure to observe this type of precaution
could cause injury or physical damage.
-After reading this manual, keep it in a place where the actual user can
refer to it easily.
-Only use this tool for fastening appropriate Pop Nuts.
(Refer to the Pop Nut catalog to select appropriate Pop Nuts).
WARNING!
1. Use compressed air at a pressure of 0.49~0.59MPa (5.0~6.0kgf/cm2).
Use of compressed air at higher pressure could break the tool as well as
causing accident or injury.
2. Do not point this tool towards anybody else when you use it.
Accident or injury could result as bystanders are entangled or squashed by
the mandrel.
3. Wear safety goggles (satisfying JIS T8147).
If this tool breaks down, parts or pressurized oil could fly out, causing
accident or injury.
4. Before using this tool, check all its parts for damage. If you notice any
damaged parts, stop work and send the tool for repair.
Accident or injury could result if you use this tool while it is damaged.
5. Make sure the compressed air supply couplings are secure.
If the screw threads of the couplings do not match perfectly, or if they are
not screwed in far enough, the hoses and couplers etc. could come off while
the tool is in use, possibly causing accident or injury.
*Refer to section one (p.4) for details of part names.
*A warning label is stuck to the chamber of this tool. If the label is badly
damaged or if it peels off, contact your supplier or one of our offices to
obtain a replacement (a replacement fee will be charged).
1

Caution!
1. Before servicing this tool, replacing any of its parts, or otherwise
assembling or disassembling it, disconnect all compressed air couplings to
make sure it is not supplied with compressed air.
If you start to work on this tool while it is supplied with compressed air,
parts or oil could fly out or the tool could start moving unexpectedly,
causing accident or injury.
2. The fill screws must be fully tightened before you use this tool.
If any of the fill screws are loose or missing, oil can spurt out, causing
accident or injury.
3. Do not use this tool without its nose housing.
Your fingers could be trapped and injured by the exposed parts.
4. Only use parts that are provided or recommended by Nippon Pop Rivets
and Fasteners. Attach the appropriate parts to this tool for the Pop Nuts
you are using.
Other than reducing performance, using the wrong attachments could
cause malfunctions leading to accident or injury.
5. Do not alter the tool without permission from the manufacturer.
Resulting malfunctions could lead to accident or injury.
6. This tool should be serviced by a qualified technician who has a full
understanding of its functions and mechanisms. Even experienced
technicians should refer to this instruction manual and proceed carefully
as instructed.
If this tool is serviced by someone who lacks the required level of
knowledge and ability, performance could be reduced and malfunctions
could result, leading to accident or injury.
7. Order repairs to this tool from the manufacturer.
If the tool needs repairing, contact your supplier or the manufacturer.
If this tool is repaired by someone who lacks the required level of
knowledge and ability, performance could be reduced and malfunctions
could result, leading to accident or injury.
8. Keep the grip of the handle dry and clean at all times. It must be free of
oil and grease.
If the grip is slippery, the user could drop the tool.
9. Do not grip or turn the mandrel with your fingers etc. while the tool is
connected to its compressed air supply.
The mandrel could start moving and injure your fingers.
2

10. Never use organic solvents on the handle, rear case, front case and trigger
(these parts are all made of polycarbonate).
Breakage of these parts above could cause parts to fly off, causing accident or
injury.
11. Wear protective gloves while using this tool.
Your fingers or hands could get trapped or squashed in the mandrel, causing
accident or injury.
12. Beware of air venting from the air vent.
Cloudy air occasionally blows strongly out of the air vent, so keep your face
(particularly your eyes) away from the air vent. The exhaust air may also dirty
nearby objects, so care is required.
(This problem mainly occurs when the compressed air supplied contains oil or
moisture.)
*Refer to section one (p.4) for details of part names.
3

1. Part names
Front case
Warning label
WARNING!
-Use compressed air at 0.49~0.59MPa (5.0~6.0kgf/cm2).
Lock nut
Control knob
Thread size
(Rc 1/4)
Exhaust holes
Fill screw
Rear case
Mandrel
Nose piece
Trigger
Handle
Chamber
Coupler
(Plug)
Not attached
Exhaust hole
Hose
Coupler
(Socket)
Nose housing
If the compressed air used exceeds this pressure range, this tool will break
down and accident or injury could result.
-Do not point this tool towards anybody else while using or handling it.
-Before using this tool, check all its parts for damage. If you notice any damaged
parts, stop work and send the tool for repair.
-Fasten all compressed air couplings securely.
-Read the instruction manual thoroughly before you use this tool and follow the
instructions correctly.
4

2. Outline
The PNT600 is a small, light tool for fastening Pop Nuts. It is driven by
compressed air.
Table 2-1 lists the Pop Nuts which can be fastened using this tool. The nose
piece and mandrel must be changed to fit some sizes of Pop Nut. (See table 2-2)
Table 2-1 Pop Nuts which can be fastened using this tool Size
Pop nut type Material M3 M4 M5 M6 M8 M10
Steel ○○○○○
Alminum ○○○○○○
Standard nut Stainless ○○○○
Steel ○○○○○
Alminum ○○○○○○
Sealed nut Stainless ○○○○
Steel ○○○○○
Hexgonal nut Alminum ○○○○
Tetra nut Steel ○○○
Rollet nut Steel ○○○
Table 2-2 Nose piece Mandrel
Pop nut size
Nut tool
No.
No. I.D. No. Thread size
M3 PNT600‑3 PNT600‑02‑3 φ4.0 PNT600‑02‑3 M3×0.5
M4 PNT600‑4 PNT600‑02‑4 φ4.5 PNT600‑02‑4 M4×0.7
M5 PNT600‑5 PNT600‑02‑5 φ5.1 PNT600‑02‑5 M5×0.8
M6 PNT600‑6 PNT600‑02‑6 φ6.1 PNT600‑02‑6 M6×1.0
M8 PNT600‑8 PNT600‑02‑8 φ8.1 PNT600‑02‑8 M8×1.25
M10 PNT600‑10 PNT600‑02‑10 φ10.1 PNT600‑02‑10 M10×1.5
M4,M5,M6set PNT600
I.D.M8×1.0
Thread size
*Refer to section one (p.4) for details of part names.
*Refer to page 12 for details of nose piece and mandrel replacement.
5

3. Specifications
(Table 3-1) Specifications
Model PNT600
Weight 1.63kg
Overall length 288mm
Overall height 255mm
Stroke 1~6.5mm
Compressed air pressure req'd 0.49~0.59MPa (5.0~6.0kgf/cm2)
Pop-Nut which may be fastened See table 2-2 (p.5)
6

4. Preparations for use
(1) Check that the right nose piece and mandrel are fitted for the Pop Nut you are
going to use.
Adjust the protruding length of the mandrel.
(Refer to page 16 for details of replacement and adjustment).
(2) [1] The coupling diameter of the compressed air supply coupling is Rc 1/4.
Connect a joint or coupler of connection diameter R1/4 to supply compressed air.
(The coupler and joint are not provided.)
[2] An air filter, regulator and lubricator should be fitted in the air line between the
compressor and the tool, within 3m of the tool. Adjust the supply pressure and the
drip volume of the lubricator oil.
(Refer to the instruction manual for the tool model you are using for the adjustment
method and the lubricant oil to use).
-Compressed air pressure: 0.49~0.59MPa (5.0~6.0kgf/cm2).
-Oil drip volume from the lubricator: 1~2 drops/ 20 nuts fastened
Coupler(Plug)
Thread size R 1/4
Regulator
I.D.6mm Min.
Hose
3m Max.
Coupler(Socket)
A
ir filter
Compressor
Lubricator
Figure 4-1
Not attached
WARNING!
According to the actual operating temperature, use an air hose able to withstand
0.6MPa (6.1kgf/cm2) at the maximum ordinary operating pressure. Also make sure
the hose material is suitable for the operating environment (e.g. oilproof, wear and
abrasion resistance etc.).
*For details, refer to a hose manufacturer's catalog.
7

(3) Adjustment of the caulk stroke
Adjust the caulk stroke (the degree of fastening) to match the Pop Nut
size and the base material thickness you will be working with.
Procedure
(i) Standard stroke adjustment (Refer to p.10)
Refer to the t-m graph (where t is the base material thickness and m is
the caulk stroke) to find the standard stroke for the Pop Nut you are
using and the base material thickness.
(Standard stroke: the caulk stroke for the pop nut recommended by POP).
(Example)
Pop Nut
SPH625
Base material thickness
t1.5
3.3
1.5
Setting Stroke
3.3mm
Figure 4-2
8

(ii) Rough adjustment of caulk stroke (scale units: mm)
[1] Use the hexagonal wrench provided (1.5mm) to loosen the lock screw on the control
nut and turn the control knob to the right (increase) or left (decrease) to align the end of
the control nut with the scale. (The position of the scale becomes the caulk stroke.)
Tighten the lock screw.
Note: Never loosen the lock screw on the control knob as this will disturb the stroke.
Control nut
Graduation
Lock screw (1.5mm Hexa. wrench)
End of the control nut
Lock screw (Never loosen)
Control knob
Figure 4-3
[2] Fasten a pop nut without placing it into any base material and use calipers etc. to
measure the caulk stroke m. Calculate the difference between the measured caulking
stroke m and the standard stroke.
m:Setting Stroke
Figure 4-4
(iii) Fine adjustment of caulk stroke (Control knob turn adjustment: 1 turn = 0.8m, 1/4
0.2m)
Adjust the caulk stroke by the amount calculated in ii)-[2] above.
[1] Loosen the lock screw and turn the control knob to adjust by the calculated
discrepancy in the caulk stroke.
(Turning direction: to left (when the discrepancy is short) : the caulk stroke increases, to
right (when the discrepancy is excessive) : the caulk stroke decreases)
[2] Tighten the lock screw and measure the caulk stroke.
[3] Repeat steps [1] and [2] until the caulk stroke matches the standard stroke.
9

4. POP NUT t-m GRAPH (COMMON TO ALL POP NUT)
(1)t-mGRAPH (2)Generalformula
Set POP nut without material
(workpiece) and measure caulked
length to make it coincide with the
value in t-m graph.
(This formula can be used for POP
nuts that are not indicated in t-m
graph.)
t:Base material thickness (mm)
m:Caulk stroke (mm)
N:1/10 of POP part number
two-lowest-digit values.
Thread Size Setting Stroke:m
M3 1.2+(N−t)
M4 1.5+(N−t)
M5 1.9+(N−t)
M6 2.3+(N−t)
M8 2.7+(N−t)
M10 2.9+(N−t)
Notice: m' is the value when the
Pop Nut is fastened to base
material.
M3~M5:m’ = m-
(
0.1~0.2
)
(mm)
m
t
(mm)
315 325
415 425 435
515 525 535
625 640
825 840
Material
Thickness
Range for
Ehch size.
1025 1040
(Example)
325
5.0
Setting Stroke (Caulked Length)
1025 1040
825
4.0 625
3.0 515 840
415
315 640
2.0 525 535
425 435
325
1.0
1.0 2.0
3.0 4.0 5.0
Material Thickness
Thread size:M3
Max.Thickness:2.5mm
10

5. Precautions on use
The following precautions must be observed to ensure that the performance and
service life of this tool are maintained.
(1) Use the correct compressed air pressure
Use compressed air at a pressure in the range 0.49~0.59MPa (5.0~6.0kgf/cm2).
If the compressed air pressure used exceeds the range above, this tool will break
down and accident or injury could result. If the pressure is below the range, the tool
may be unable to fasten Pop Nuts fully.
Use a regulator to ensure compressed air supply in the correct pressure range. (See
p.7)
(2) Use an air filter
If the compressed air supplied contains dirt or moisture, it will have an adverse
effect on the tool, so use an air filter in the air supply. (See p.7)
(3) Use a lubricator
If the tool goes without an adequate supply of lubricant, its service life will be
shortened.
Install a lubricator within 3m of the tool and adjust its drip rate.
(Recommended drip volume = 1~2 drops for 20 fastenings).
*Refer to the instruction manual for the lubricator used for details of the
adjustment method and the correct lubricant oil to use.
(4) Parts to use (Nose piece, jaw pusher, jaws)
Replace these pieces with the appropriate versions for the Pop Nuts you are going to
use (see table 2-2). If you do not use the designated parts, the tool may be unable to
fasten the Pop Nuts.
(5) Hydraulic oil
Use the designated hydraulic oil.
Use one of the hydraulic oil brands specified in table 5-1. Use of any other oil could
cause a breakdown.
Table 5-1 Specified hydraulic oils
Company name Product name
Idemitsu Daphne Hydro 68
Mobile Mobile 26
Cosmo Cosmo Olpas 68
Esso Telesso 68
Nisseki FBK RO68
Mitsubishi Diamond Lube RO68 (N)
Showa Shell Shell Telus Oil C68
11

6. How to use the PNT600
Before you start fastening Pop Nuts with this tool, refer to the section "4.
Preparations for use" on pages six and seven.
Procedure
(1) Mounting
When the Pop Nut is gripped gently and pressed by the mandrel with a force of
approximately 0.5kN or more, the mandrel turns clockwise.
Screw the Pop Nut down onto the mandrel.
Once the flange of the Pop Nut comes into contact with the nose piece, the
clockwise rotation of the mandrel stops automatically.
Mandrel
Figure 6-1
Precautions on mounting
Keep pushing until the clockwise rotation of the mandrel stops automatically.
If the Pop Nut is not fully mounted, the caulk stroke will be inconsistent.
OK
NG
12

(2) Fastening and detachment
Push the Pop Nut perpendicularly into the hole in the base material and pull the
trigger (Figure 6-2).
Keep pulling the trigger throughout fastening and detachment.
Otherwise, detachment cannot be completed.
The Pop Nut is fastened and the tool automatically switches to counterclockwise
rotation to detach from the Pop Nut (Figure 6-3). Pull lightly
Trigger
Pull
Figure 6-3
Trigger
Keep pulling
Base material
Figure 6-2
Precautions on fastening
[1] Fit the flange of the Pop Nut closely against the base material.
OK NG
[2] Do not tilt the tool. NG
OK
[3] Double caulking (fastening a Pop Nut again after it has initially been fastened
once). If you try to refasten a Pop Nut that has already been fastened, either the tool
or the Pop Nut will break.
Precautions on tool detachment
Pull the tool throughout detachment.
Otherwise, the mandrel cannot detach without reverse rotation.
13

(3) Stopping the mandrel's counterclockwise rotation.
Release the trigger to stop the mandrel (Figure 6-4).
Figure 6-6
Figure 6-4
Release Trigger
Figure 6-5
Regular mandrel cleaning and lubricant
-Clean the mandrel after every 50~60 fastenings.(See Figures 6-5 and 6-6.)
After fastening tens of Pop Nuts, metal fragments can stick to the mandrel and it can
run short of lubrication, making it impossible to mount Pop Nuts smoothly.
If you continue to use the tool in this condition it will become impossible to mount Pop
Nuts at all and the mandrel will wear more rapidly.
(Figure 6-5) (Figure 6-6)
(4) What to do when the Pop Nut is not detached correctly
(i) If the reverse rotation of the mandrel stops before the Pop Nut is detached from the
mandrel (if you released the trigger too early).
Pull the trigger while pressing the control knob. Mandrel starts reverse rotation and
detaches the Pop Nut (Figure 6-7). Rotate
Trigger
Control knob
Nose housing
Lock pin holder
Ca
p
screw
Pull
While pressing
Figure 6-9
Figure 6-7 Figure 6-8
14
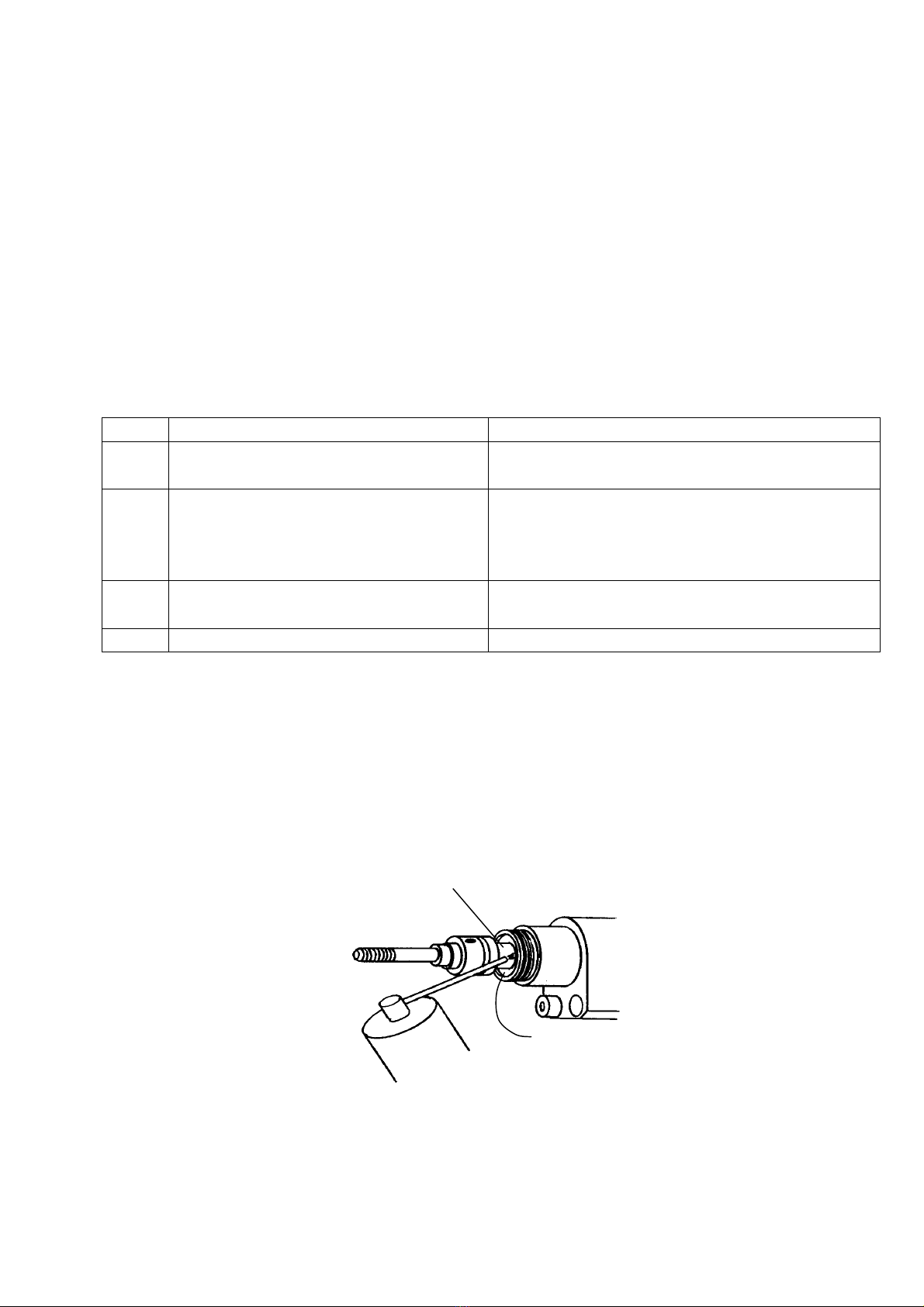
(ii) If the Pop Nut jams and the strength of the air motor is insufficient to detach the
mandrel.
[1] Detach the coupler to stop the supply of compressed air.
[2] Line up the female screw of the lock pin holder with the hole in the side of the nose
housing and screw the cap screw provided (M4×20) into the lock pin holder (Figure
6-8).
[3]Turn the body of the tool counterclockwise to detach it from the Pop Nut (Figure
6-9).
7. Maintenance and testing
(Table 7-1)
No. Item Purpose
1 Lubricant spray for rotating parts. -To prevent early loss of the mandrel
rotation force.
2 Replacement of mandrel and nose
piece and adjustment of mandrel
protrusion length.
-Replacement and adjustment to change
the Pop Nuts used.
-Replacement and adjustment in case of
breakage.
3 Control nut, T valve push rod
replacement. -Replacement and adjustment in case of
breakage.
4 Lubricant oil filling. -Resetting the caulk stroke.
1 Lubricant spray for rotating parts.
After fastening around 1,000 Pop Nuts, wear between the spin-pull head and the
spin-pull head case will start to cause heating, drying and rattling. Rotation will be
slower, with less torque.
Follow the procedure from 2-(i) to remove the nose housing and spray lubricant
between the spin-pull head and the spin-pull head case.
Spin pull head
Spin pull head case
Lubricant spray
Figure 7-1
15

2. Mandrel replacement, nose piece replacement and mandrel protrusion length
adjustment
Use the designated parts to match the Pop Nut you will be using. (See p.5 table 2-2)
Replace any parts that become worn or damaged.
(i) Mandrel replacement
Procedure
(1) Detach the coupler to stop the supply of compressed air.
(2) Use a 23mm spanner to unscrew and remove the nose housing.(See Figure 7-2)
Nose housing Figure 7-2
(3) Push the lock pin holder in with your finger while you turn the mandrel to the left
to remove it for replacement.
(4) Push the lock pin holder in with your finger while you screw the new mandrel into
the spin-pull head until it stops. Release the lock pin holder so that it returns to its
original position.
If the lock pin holder does not return to its original position, turn the mandrel slightly
to the left.
The lock pin holder will return to its original position. (See figure 7-3)
S
p
in
p
ull head case Lock pin holder
Mandrel
Push
Figure 7-3
(ii) Nose piece replacement, adjustment of the mandrel protrusion length Procedure
(1) Detach the coupler to stop the supply of compressed air.
(2) Use a 23mm and a 19mm spanner to loosen the lock nut and remove the nose piece
and the lock nut from the nose housing. Change the nose housing (Figure 7-4).
One thread
Nose piece Lock nut
Figure 7-4 Figure 7-5
16

(3) Screw the lock nut and nose piece into the nose housing.
(4) Screw a Pop Nut onto the mandrel and adjust the nose piece so that approximately
one thread of the mandrel screw thread extends beyond the Pop Nut (Figure 7-5).
(5) Screw the lock nut and the nose housing together to fasten the nose piece in the
place.
3. Replacement of the control nut and the T valve push rod
If the mandrel breaks or the screw thread of a Pop Nut is broken by an excessive
stroke, the control nut and valve push rod may be broken.
Procedure
(1) Detach the coupler to stop the supply of compressed air.
(2) Use a cross-head screwdriver to remove the truss machine screws and detach the
front case (Figure 7-2).
(3) Use the 1.5mm hexagonal wrench (provided) to loosen the lock screw on the control
nut and turn the control knob to the left until the control nut reaches the end of its
travel (Figure 7-3).
Control nut
Truss screw
Front case
Lock screw
Figure 7-3
Figure 7-2
(4) Press the control knob and line up the projection on the control nut with the mast
housing, then turn the control knob to the left to remove it. Remove these parts as an
assembly from the body of the tool (Figures 7-4 and 7-5).
(5) Use the 1.5mm hexagonal wrench to loosen the lock screws of the control knob and
the control nut and remove them from the push rod of the T valve (Figure 7-6).
Projection
Lock screw
Tvalve push rod
Control nut
Control knob
Mast housing
Press and turn
Figure 7-4
A
ssembly
Fi
g
ure 7-5
Figure 7-6
17

(6) Replace the broken parts and reassemble the assembly (Figure 7-5).
Push the control knob and control nut as far as they will go onto the push
rod of the T valve and tighten the lock screws to fasten them in place.
(7) Push the completed assembly into the body of the tool and reverse the
above procedure to reassemble all parts.
(8) Loosen the lock screw on the control nut and turn the control knob to the
right until the control nut stops at the end of its travel and then tighten the
lock screw (Figure 7-7).
(9) Fasten a Pop Nut (without inserting it into any base material) and check
the caulk stroke (A). The scale in this situation is set for 1mm, but the
stroke reading should normally be between 1mm and 2mm (Figure 7-8).
Note: For this fastening trial only, reconnect the coupler to deliver a supply
of compressed air. For all other steps the compressed air supply should be
disconnected.
Figure 7-8
A
: Setting Stroke
Lock screw
Figure 7-8
Figure 7-7
(10) Use the control knob to match the stroke with the scale, adjusting the
stroke to 1mm. (Minimum stroke adjustment).
Loosen the lock screw on the control knob (do not loosen the lock screw of
the control nut), then turn the control knob to the left by the amount of the
excess stroke. (one turn = 0.7mm, the screw pitch of the T valve push rod
and the control knob is 0.7mm), then tighten the lock screw again. (See
Figure 7-9)
Control nut
Figure 7-9
Lock screw
Lock screw
Control knob
18
Table of contents
Other NIPPON POP RIVETS AND FASTENERS Tools manuals