Novanta IMS Liberty MDrive Ethernet TCP/IP User manual

Hardware Manual
Liberty MDrive Ethernet TCP/IP
NEMA 17 (42 mm) with M12 Circular Connectors
Publication IMS-MN-LMDE42C_A
02/2022
REACH IP20/IP65
LISTED
TM

2
For information on the availability of products, go to https://novantaims.com/
The information contained in the present document is subject to change without notice. The
technical characteristics of the devices described in the present document also appear online.
The characteristics that are presented in the present document should be the same as those
characteristics that appear online. In line with our policy of constant improvement, we may
revise content over time to improve clarity and accuracy. If there is a difference between the
document and online information, use the online information as reference. All details provided
are technical data which do not constitute warranted qualities.
Some of the product designations are registered trademarks of their respective owners, even if
this is not explicitly indicated.
The information provided in this documentation contains general descriptions and/or technical
characteristics of the performance of the products contained herein. This documentation is
not intended as a substitute for and is not to be used for determining suitability or reliability
of these products for specific user applications. It is the duty of any such user or integrator to
perform the appropriate and complete risk analysis, evaluation and testing of the products with
respect to the relevant specific application or use thereof.
Neither Novanta IMS nor any of its affiliates or subsidiaries shall be responsible or liable for
misuse of the information contained herein. If you have any suggestions for improvements or
amendments or have found errors in this publication, please notify us.
You agree not to reproduce, other than for your own personal, noncommercial use, all or part of
this document on any medium whatsoever without permission of Novanta IMS, given in writing.
You also agree not to establish any hypertext links to this document or its content.
Novanta IMS does not grant any right or license for the personal and noncommercial use of the
document or its content, except for a non-exclusive license to consult it on an “as is” basis, at
your own risk. All other rights are reserved.
All pertinent state, regional, and local safety regulations must be observed when installing
and using this product. For reasons of safety and to help ensure compliance with documented
system data, only the manufacturer should perform repairs to components.
When devices are used for applications with technical safety requirements, the relevant
instructions must be followed. Failure to use Novanta IMS software or approved software with
our hardware products may result in injury, harm, or improper operating results.
Failure to observe this information can result in injury or equipment damage.

3
IMS-MN-LMDE42C_A
Table of Contents
Safety Information 5
Important Information...............................................................................................................5
Qualification of Personnel........................................................................................................5
CyberSecurity Standards and Certification ......................................................................5
Intended Use.................................................................................................................................6
Product Related...........................................................................................................................6
About this Manual 8
Introduction...................................................................................................................................8
Terminology Derived from Standards .................................................................................8
Writing Conventions and Symbols.......................................................................................9
Documentation and Literature References ......................................................................10
Website Directory ......................................................................................................................10
Documentation Feedback ......................................................................................................10
Chapter 1: Introduction 11
About This Product ...................................................................................................................12
Unit Overview ..............................................................................................................................12
Components and Interfaces...................................................................................................13
Name Plate.................................................................................................................................... 15
Part Number Identification.....................................................................................................16
Chapter 2: Technical Data 19
Certifications............................................................................................................................... 20
Environmental Conditions ..................................................................................................... 20
Mounting Data.............................................................................................................................22
Mechanical Data ........................................................................................................................ 24
Electrical Data ............................................................................................................................ 28
Rotary Motor Data .................................................................................................................... 32
External Linear Actuator Data ............................................................................................. 33
Electric Cylinder Data.............................................................................................................. 35
Chapter 3: Engineering 36
External Power Supply Units .................................................................................................37
Auxiliary Power Supply........................................................................................................... 40
Wiring and Shielding................................................................................................................ 40
Ground (Earth) Design.............................................................................................................41
Monitoring Functions............................................................................................................... 42

4IMS-MN-LMDE42C_A
Liberty MDrive Ethernet TCP/IP
Chapter 4: Installation 43
Electromagnetic Compatibility, EMC................................................................................. 45
Mechanical Installation............................................................................................................ 46
Electrical Installation................................................................................................................ 48
Supply Voltage VDC Connection........................................................................................ 49
Multifunction Interface Connection.................................................................................... 50
Signal Input Circuits ..................................................................................................................52
Signal Output Circuit ............................................................................................................... 54
Analog Input ............................................................................................................................... 55
Communication Interface Connection .............................................................................. 56
Checking Wiring ........................................................................................................................ 56
Chapter 5: Configuration 57
Preparing for Configuration .................................................................................................. 59
Installing the LSS....................................................................................................................... 59
Chapter 6: Operations 60
Basics..............................................................................................................................................61
Software Operation Modes ................................................................................................... 63
Operation by hMT Modes....................................................................................................... 65
I/O Operation.............................................................................................................................. 67
Appendix A: Diagnostics and Troubleshooting 69
Operation State and Error Indication ................................................................................ 69
Error Codes...................................................................................................................................71
Appendix B: Accessories and Spare Parts 72
Accessories...................................................................................................................................72
Appendix C: Service, Maintenance, and Disposal 75
Service Address ......................................................................................................................... 76
Replacing Units .......................................................................................................................... 76
Shipping, Storage, and Disposal...........................................................................................77
Appendix D: LMD with Absolute Encoder 78
Overview....................................................................................................................................... 78
Unboxing Procedure ................................................................................................................ 78
Connection of the Multifunction Interface ...................................................................... 78
ICP0531 Encoder Back-up Battery Pack .......................................................................... 79
Glossary 83

5
IMS-MN-LMDE42C_A
SAFETY INFORMATION
Important Information
Notice
Read these instructions carefully, and look at the equipment to become familiar with the device before
trying to install, operate, service, or maintain it. The following special messages may appear throughout
this documentation or on the equipment to warn of potential hazards or to call attention to information that
clarifies or simplifies a procedure.
The addition of this symbol to a “Danger” or “Warning” safety label or message
indicates that an electrical hazard exists which will result in personal injury if the
instructions are not followed.
This is the safety alert symbol. It is used to alert of potential personal injury hazards.
Obey all safety messages and labels that follow this symbol to avoid possible injury or
death.
DANGER
DANGER indicates a hazardous situation which, if not avoided, will result in death or serious injury.
WARNING
WARNING indicates a hazardous situation which, if not avoided, could result in death or serious injury.
CAUTION
CAUTION indicates a hazardous situation which, if not avoided, could result in minor or moderate injury.
NOTICE
NOTICE is used to address practices not related to physical injury.
Qualification of Personnel
Electrical equipment should be installed, operated, serviced, and maintained only by qualified
personnel. No responsibility is assumed by Novanta IMS for any consequences arising out of the
use of this material.
A qualified person is one who has skills and knowledge related to the construction and
operation of electro-mechanical equipment and its installation, and has received safety training
to recognize and avoid the hazards involved.
CyberSecurity Standards and Certification
Novanta follows local regulations and uses additional industry established frameworks to
conform to cyber security standards. Novanta also takes an active part in the evolution of
today’s industrial cyber security standards, contributing to these standards and frameworks.
In accordance with US California Senate Bill No. 327, and under direct guidance from Novanta,
Novanta IMS has implemented a level of cyber-secure protection in the LMD Ethernet-based
MDrive product line in order to protect these devices from outside cyber attacks. By choosing
to disable these features, the customer is acknowledging their acceptance of potential
unauthorized outside access.

6IMS-MN-LMDE42C_A
Intended Use
Liberty MDrive Ethernet TCP/IP
Intended Use
The product may only be used in compliance with all applicable safety regulations and
directives, the specified requirements, and the technical data.
Prior to using the product, perform a risk assessment in view of the planned application. Based
on the results, the appropriate safety measures must be implemented.
Since the product is used as a component in an entire system, ensure the safety of persons by
means of the design of this entire system (e.g., machine design).
Operate the product only with the specified cables and accessories. Use only genuine
accessories and spare parts.
DANGER
POTENTIAL FOR EXPLOSION
Install and use this equipment in non-hazardous locations only.
Failure to follow these instructions will result in death or serious injury.
Any use other than the use explicitly permitted is prohibited and can result in hazards.
Electrical equipment should be installed, operated, serviced, and maintained only by qualified
personnel.
Product Related
DANGER
HAZARD OF ELECTRICAL SHOCK, EXPLOSION, OR ARC FLASH
Remove all power from all devices before connecting or disconnecting inputs or outputs to any
terminal or installing or removing any hardware.
Failure to follow these instructions will result in death or serious injury.
When the system is started, the drives are usually out of the operator’s view and cannot be
visually monitored.
DANGER
EQUIPMENT OPERATION
Only start the system if there are no persons in the zone of operation.
Failure to follow these instructions will result in death or serious injury.
Drives may perform unintended movements because of incorrect wiring, incorrect parameter
settings, incorrect data, user programming bugs, or other errors. Further, interference (e.g.,
electromagnetic interference (EMI)) may cause unpredictable responses in the system.
WARNING
UNINTENDED MOVEMENT
• Carefully install the wiring in accordance with the electromagnetic compatibility (EMC)
requirements.
• Do not operate the drive system with unknown parameter settings or data.
Failure to follow these instructions can result in death, serious injury, or equipment damage.
The designer of any control scheme must consider the potential failure modes of control paths
and, for certain critical functions, provide a means to achieve a safe state during and after a
path failure. Examples of critical control functions are emergency stop, overtravel stop, power
outage, and restart.

7
Product Related
IMS-MN-LMDE42C_A
Liberty MDrive Ethernet TCP/IP
WARNING
LOSS OF CONTROL
• The designer of any control scheme must consider the potential failure modes of control paths and,
for certain critical control functions, provide a means to achieve a safe state during, and after a path
failure. Examples of critical control functions are emergency stop and overtravel stop.
• Separate or redundant control paths must be provided for critical control functions.
• System control paths may include communication links. Consideration must be given to the
implications of anticipated transmission delays or failures of the link.
• Each implementation of the product must be individually and thoroughly tested for proper
operation before being placed into service.
Failure to follow these instructions can result in death, serious injury, or equipment damage.
For USA: Additional information, refer to NEMA ICS 1.1 (latest edition), “Safety Guidelines for the
Application, Installation, and Maintenance of Solid State Control” and to NEMA ICS 7.1, (latest
edition), “Safety Standards for Construction and Guide for Selection, Installation, and Operation
of Adjustable-Speed Drive Systems”
Drives may perform unintended movements due to mechanical damage to connectors.
Mechanical damage to the connectors may cause erratic or uncontrolled operation. Installation
with a bent or broken mounting flange, motor shaft, or misaligned coupling may cause
unintended behavior and possible destruction of system components as a result.
WARNING
LOSS OF CONTROL, ERRATIC OPERATION AND DESTRUCTION OF MECHANICS
• Do not drop product.
• Leave product in protective packaging until ready for use.
• Carefully inspect connectors prior to installation in a system for mechanical damage.
• Carefully inspect motor shaft and ensure shaft rotates freely without binding.
Failure to follow these instructions can result in death, serious injury, or equipment damage.
Opening LMD heat sinks can affect factory-set encoder alignment and impact Hybrid Motion
Technology (hMT) performance. Tamper seals are used to ensure factory hardware settings
remain unaltered and match the encoder alignment set during the manufacturing process.
WARNING
UNINTENDED EQUIPMENT OPERATION
• Do not open the LMD device housing for any reason.
• Contact a Novanta IMS applications representative if the product exhibits unexplained, erratic, or
incorrect operation.
Failure to follow these instructions can result in death, serious injury, or equipment damage.
Radial (side) loading or axial (thrust) impacts on the shaft may result in premature bearing
failure.
NOTICE
EXCESSIVE RADIAL OR AXIAL LOADS
• Do not exceed the maximum radial or side load limits on the motor shaft.
• Do not apply force that will pull the shaft from the motor as that may compress the pre-load washer,
causing the rotor to move.
• Do not allow the shaft to be subject to impact forces or otherwise struck by external objects.
Failure to follow these instructions can result in equipment damage.
NOTE: For additional information, contact a Novanta IMS Applications representative.

8IMS-MN-LMDE42C_A
ABOUT THIS MANUAL
Introduction
Read and understand the material contained in this manual before working on LMD products for
the first time. Take particular note of the safety information (see “Safety Information” on page
5). Only qualified persons are allowed to work with the LMD product (see “Qualification of
Personnel” on page 5).
A copy of this manual must be available for personnel who work with LMD products.
The purpose of this manual is to show the capabilities of the LMD and how to use it safely and
properly. Follow the instructions within this manual to help:
• reduce risks,
• reduce repair costs and downtime of the LMD product,
• increase the service life of the LMD product, and
• increase reliability of the LMD product.
Terminology Derived from Standards
The technical terms, terminology, symbols and the corresponding descriptions in this manual,
or that appear in or on the products themselves, are generally derived from the terms or
definitions of international standards.
In the area of functional safety systems, drives and general automation, this may include, but
is not limited to, terms such as safety, safety function, safe state, fault, fault reset, malfunction,
failure, error, error message, dangerous, etc.
Among others, these standards include:
IEC/EN 61131-2:2007 Programmable controllers, Part 2: Equipment requirements and tests.
ISO 13849-1:2015 Safety of machinery: Safety-related parts of control systems. General principles for
design.
EN 61496-1:2013 Safety of machinery: Electro-sensitive protective equipment. Part 1: General requirements
and tests.
ISO 12100:2010 Safety of machinery: General principles for design - Risk assessment and risk reduction.
IEC/EN 60204-1:2006 Safety of machinery: Electrical equipment of machines - Part 1: General requirements.
ISO 14119:2013 Safety of machinery: Interlocking devices associated with guards - Principles for design
and selection.
ISO 13850:2015 Safety of machinery: Emergency stop - Principles for design.
IEC/EN 62061:2015 Safety of machinery: Functional safety of safety-related electrical, electronic, and
electronic programmable control systems.
IEC 61508-1:2010 Functional safety of electrical/electronic/programmable electronic safety-related systems:
General requirements.
IEC 61508-2:2010 Functional safety of electrical/electronic/programmable electronic safety-related systems:
Requirements for electrical/electronic/programmable electronic safety-related systems.
IEC 61508-3:2010 Functional safety of electrical/electronic/programmable electronic safety-related systems:
Software requirements.
IEC 61784-3:2016 Digital data communication for measurement and control: Functional safety field buses.
2006/42/EC Machinery Directive
2014/30/EU Electromagnetic Compatibility Directive
2014/35/EU Low Voltage Directive

9
Writing Conventions and Symbols
IMS-MN-LMDE42C_A
DocumentName
In addition, terms used in the present document may tangentially be used as they are derived
from other standards such as:
IEC 60034 series Rotating electrical machines
IEC 61800 series Adjustable speed electrical power drive systems
IEC 61158 series Digital data communications for measurement and control – Fieldbus for use in industrial
control systems
Finally, the term, “zone of operation” may be used in conjunction with the description of
specific hazards, and is defined as it is for a hazard zone or danger zone in the Machinery
Directive (2006/42/EC) and ISO 12100:2010.
NOTE: The aforementioned standards may or may not apply to the specific products cited
in the present documentation. For more information concerning the individual standards
applicable to the products described herein, see the characteristics tables for those product
references.
Writing Conventions and Symbols
Work Steps
Work steps must be performed consecutively. Work steps will be numbered in order of
expected operation.
A response to a work step may be indicated. This allows verification that the work step has
been performed correctly.
Unless otherwise stated, the individual steps must be performed in the specified sequence.
Bulleted Lists
The items in bulleted lists are sorted alphanumerically or by priority. Bulleted lists are
structured as follows:
• Item 1 of bulleted list
• Item 2 of bulleted list
–Subitem for 2
–Subitem for 2
• Item 3 of bulleted list
Parameters
Parameters are shown as follows
RC Motor Run Current
Units of Measure
Measurements are given in both imperial and metric values. Metric values are given in
parenthesis unless otherwise indicated.
Examples:
1.00 in (25.4 mm)
100 oz-in (70.6 N-cm)

10 IMS-MN-LMDE42C_A
Documentation and Literature References
DocumentName
Documentation and Literature References
This document should be used in conjunction with the following documents:
• Ethernet/IP Fieldbus Manual
• MODBUS/TCP Fieldbus Manual
• Profinet IP Fieldbus Manual
• MCode Programming and Reference Manual
• LMD Software Suite (LSS) Manual
The latest versions of these manuals can be downloaded from:
https://novantaims.com/dloads/product-literature/manuals-3/
Website Directory
NOTE: Direct links are subject to change as website and search engine updates occur. Each of
the websites below can also be accessed through menu options on the Novanta IMS Main Page:
https://novantaims.com/
Downloads:
https://novantaims.com/dloads/
Resources:
https://novantaims.com/resources/
Warranty:
https://novantaims.com/warranty-and-disclaimer/
Certifications and Listing Information:
https://novantaims.com/dloads/certificationssustainability/
Contact and Support:
https://novantaims.com/contacts/
CyberSecurity Information:
https://novantaims.com/all-products/cybersecurity/
Knowledge Based Solutions:
https://novantaims.com/resources/troubleshooting/
Documentation Feedback
To provide feedback on this or any Novanta IMS documentation, submit all comments,
corrections, or concerns to the following e-mail address.
documentati[email protected]om
Please include the following information:
• Document number and revision/print date
• Detailed description of the issue or concern
• Contact information

12 IMS-MN-LMDE42C_A
About This Product
Liberty MDrive Ethernet TCP/IP
About This Product
This manual is valid for the NEMA 17 (42mm) Liberty MDrive (LMD) Ethernet products with M12
circular connectors. This chapter lists the type codes for these products. The type code can be
used to identify whether the product is a standard product or a customized model.
Unit Overview
The LMD Ethernet TCP/IP consists of a stepper motor and integrated electronics. The product
integrates interfaces, drive and control electronics, and the power stage. There are three basic
control modes:
Closed Loop with hMT:Loop is closed by a 1000-line (4000 edge) magnetic encoder. May be
operated as:
•hMT off: standard encoder functions for position and stall monitoring
•hMT on: enhanced closed loop functions such as anti-stall and position maintenance.
Absolute with hMT:Closed loop with multi-turn absolute encoder, which will retain/update
position information upon loss/removal of power. Standard encoder and hMT features will
function as on a closed loop model. Refer to Appendix D on page 78 for details.
Open Loop:Standard open loop stepper control.
LMD Ethernet TCP/IP Products (LMDxE)
Included protocols on all Ethernet LMDxE devices include the Ethernet/IP, Profinet IO,
MODBUS/TCP, and MCode/TCP on a single device.
Setup parameters are set via the fieldbus interface using a software utility, available for
download from:
https://novantaims.com/dloads/
LMD Ethernet TCP/IP Protocols
Ethernet/IP
The LMD Ethernet may be used as a fully ODVA compliant Adapter class device on Ethernet/IP
networks.
MODBUS/TCP
The LMD Ethernet may be used in MODBUS/TCP networks, a standard open industrial
convention supported by a variety of machine components, such as programmable controllers,
drives and controls, I/O modules, and switches.
Profinet IO
The LMD Profinet may be used as an IO-DEVICE on Profinet networks with Siemens PLCs.
Motion commands, variables, and flags from the standard MCode control language are mapped
to input and output registers of the device. There are 38 output registers and 34 input registers.
MCode/TCP
The LMD Ethernet TCP/IP products are fully programmable motion control systems allowing
for complex program and I/O interaction. The following operating modes may be used
interchangeably:

13
Components and Interfaces
IMS-MN-LMDE42C_A
Liberty MDrive Ethernet TCP/IP
•Immediate Mode: In immediate mode, also known as streaming commands, the device will
respond to 1 and 2 character ASCII commands sent via the Ethernet interface, available as
part of the LSS.
•Program Execution Mode: In program execution mode, the device may be programmed with
multiple functions, subroutines, and process interactions using the MCode programming
language, which is made up of 1 and 2 character ASCII mnemonics. Stored programs may be
executed by:
–using an input configured as a start input
–upon start up by labeling a program “LB SU”
–immediate mode command.
Components and Interfaces
A
B
C
D
F
E
G
(A) Electronics housing
(B) Two phase stepper motor
(C) DC power interface
(D) Multifunction interface
(E) Ethernet RJ45 interface
(F) Protective earth
(G) LED indicators

14 IMS-MN-LMDE42C_A
Components and Interfaces
Liberty MDrive Ethernet TCP/IP
Components
Motor
The motor is a two phase brushless stepper motor. The step angle of the motor is 1.8°.
Electronics Housing
The electronics system is comprised of control electronics and power stage.
The drive system is controlled by streaming commands via the service interface, embedded
programming, or by pulse and direction input signals.
Interfaces
DC Power Supply Voltage
The supply voltage VDC supplies the control electronics and the power stage of the drive,
including a +12V to +24V Aux-Power input to supply power to logic circuits in the event of main
supply interruptions.
The ground connections of all interfaces are galvanically isolated with the exception of the
analog input. For more information on ground connections and protection against reverse
polarity, see “Ground (Earth) Design” on page 41.
Multifunction I/O Interface
The multifunction I/O interface operates at the following signal levels:
• +5V to +24V input signals (opto-isolated)
• 5.5 mA output signal (opto-isolated)
NOTE: For information on how to increase the Output current, refer to “Output 3”
Knowledge Based Solutions, available from:
https://novantaims.com/resources/troubleshooting/
• 12-bit analog signal (not isolated)
The +5V to +24V input signals are programmable as general purpose or to predefined
functions.
The output is a 5.5 mA signal output, which can be defined as a high speed trip.
The reference voltage or current that is applied to the analog input can be used for a number of
programmatically defined operations.
Ethernet Interface
The service interface provides a connection to an Ethernet network.
Commissioning software is used to configure the device IP address and subnet mask. The
Ethernet Interface is available via the LSS Ethernet firmware upgrades are performed through
the Ethernet Interface.
NOTE: Additional setup will be required for initial setup on devices with CyberSecurity enabled.
Devices with CyberSecurity enabled will have a “CSE” marking on the packaging and product
label. For additional information on CyberSecurity, refer to:
https://novantaims.com/all-products/cybersecurity/
Protective Earth
Protective earth provides a means of grounding to the device chassis.

15
Name Plate
IMS-MN-LMDE42C_A
Liberty MDrive Ethernet TCP/IP
Name Plate
The name plate has the following information:
(1) Part number
(2) Nominal voltage
(3) Max. Holding torque
(4) Maximum required input current
(5) Serial number
(6) Ethernet MAC address
(7) Date of manufacture
(8) Communication interface
(9) Data Matrix code
(10) CyberSecurity Enabled indication
(11) Ingress Protection Rating

16 IMS-MN-LMDE42C_A
Part Number Identification
Liberty MDrive Ethernet TCP/IP
Part Number Identification
LMD Rotary Motor
The following graphic displays a breakdown of the LMD rotary motor part number
identification.
Product
LMD = standard torque motor
Control Type
E = Ethernet
Feedback
O = Open loop (no encoder)
C = Closed loop (with encoder)
A = Absolute encoder
Size
42 = NEMA 17 (42 mm)
Length
1 = 1 stack
2 = 2 stacks
3 = 3 stacks
Variation
C = M12 Circular Connectors, IP20/IP651
LMD O E 42 1 C
1 Motor shaft is not sealed. For IP65 applications, the NEMA
flange must be properly sealed.

17
Part Number Identification
IMS-MN-LMDE42C_A
Liberty MDrive Ethernet TCP/IP
LMD External Linear Actuators
The following graphic displays a breakdown of the LMD external linear actuator part number
identification.
Linear actuator
-L = Linear
Connector Style
C = M12 Circular Connectors, IP20/IP651
Shaft style
3 = External
Screw lead / pitch (travel/rev)
A = 0.250" / 6.35mm
B = 0.125" / 3.175mm
C = 0.063" / 1.600mm
Screw end finish
M = Metric threaded
U = UNC threaded
S = Smooth
Z = None
Screw length
available in 0.1” increments
030 = Minimum 3.0" / 76.2mm
180 = Maximum 18.0" / 457.2mm
Nut
G = General purpose
A = Anti-backlash
Coating
T = Teflon®
Z = None
LMD O E 42 1 C -L A 3 M 030 G T
Product
LMD = standard torque motor
Control Type
E = Ethernet
Feedback
O = Open loop (no encoder)
C = Closed loop (with encoder)
A = Absolute encoder
Size
42 = NEMA 17 (42 mm)
Length
1 = 1 stack
1 Motor shaft is not sealed. For IP65 applications, the NEMA flange
must be properly sealed.

18 IMS-MN-LMDE42C_A
Part Number Identification
Liberty MDrive Ethernet TCP/IP
LMD Electric Cylinders (eCylinders)
The following graphic displays a breakdown of the LMD eCylinder part number identification.
Linear actuator
-C = Electric cylinder
Connector Style
C = M12 Circular Connectors, IP20/IP651
Nut
S = PEEK Blend
Lead / Pitch (travel/rev)
A = 0.100” / 2.54mm
B = 0.250” / 6.35mm
C = 0.500” / 12.70mm
D = 1.000” / 25.40mm
Stroke length
available in 0.1” increments
020 = Minimum 2.0" / 50.8mm
180 = Maximum 18.0" / 457.2mm
Mounts
M = Flange mounts
F = Foot mounts
Options
NN = Reserved
LMD O E 42 1 C -C S A 020 M NN
Product
LMD = standard torque motor
Control Type
E = Ethernet
Feedback
O = Open loop (no encoder)
C = Closed loop (with encoder)
A = Absolute encoder
Size
42 = NEMA 17 (42 mm)
Length
1 = 1 stack
1 Motor shaft is not sealed. For IP65 applications, the NEMA flange must be properly sealed.

19
IMS-MN-LMDE42C_A
Chapter 2:
Technical Data
What’s in this Chapter?
This chapter contains information on the ambient conditions and on the mechanical and
electrical properties of the device family and accessories.
This chapter includes the following topics:
Topic Page
Certifications 20
Environmental Conditions 20
Mounting Data 22
Mechanical Data 24
Electrical Data 28
Rotary Motor Data 32
External Linear Actuator Data 33
Electric Cylinder Specifications 35

20 IMS-MN-LMDE42C_A
Certifications
Liberty MDrive Ethernet TCP/IP
Certifications
Certification Regulation #
RoHS12011/65/EU
EMC 2004/108/EC
REACH EC 1907/2006
UL UL 1004-1, UL 1004-3
CSA C22.2 No. 100
CSA C22.2 No. 77
1 For additional information regarding RoHS certifications, contact a Service Representative at [email protected]om
or call +1 (860) 365-3907.”
A current list of certifications and compliance information can be viewed at:
https://novantaims.com/dloads/certificationssustainability/
Environmental Conditions
Ambient Operating Conditions
The maximum permissible ambient temperature during operation depends on the distance
between the devices and the required power. Reference “Installation” on page 43 for
pertinent instructions.
The following relative humidity is permissible during operation.
Operating temperature1[°C (°F)] -20 ... 50 (-4 ... 122) (no icing)
Temperature variation [°C (°F) min] 0.5
Humidity [%] 5 ... 95 (non-condensing)
1 If the product is to be used in compliance with UL 508C, note the information provided in chapter 3.6 “Conditions for UL 508C”.
Storage and Transport
The environment during transport and storage must be dry and free from dust. The maximum
vibration and shock load must be within the specified limits.
Temperature [°C (°F)] -25 ... 70 (-13 ... 158)
Temperature variation [°C (°F) min] -25 ... 30 (-13 ... 86)
Humidity [%] 5 ... 95 (non-condensing)
Temperature Maximums
Power stage1[°C (°F)] 85 (185)
Motor2[°C (°F)] 100 (212)
1 May be read via parameter
2 Measured on the surface of the motor laminations
Installation altitude
The installation altitude is defined as height above sea level
Installation altitude1[ft (m)] 3280 (1000)
1 Installation above 3280 (1000) may require derating output current and maximum ambient temperature.
Table of contents
Other Novanta Engine manuals
Popular Engine manuals by other brands
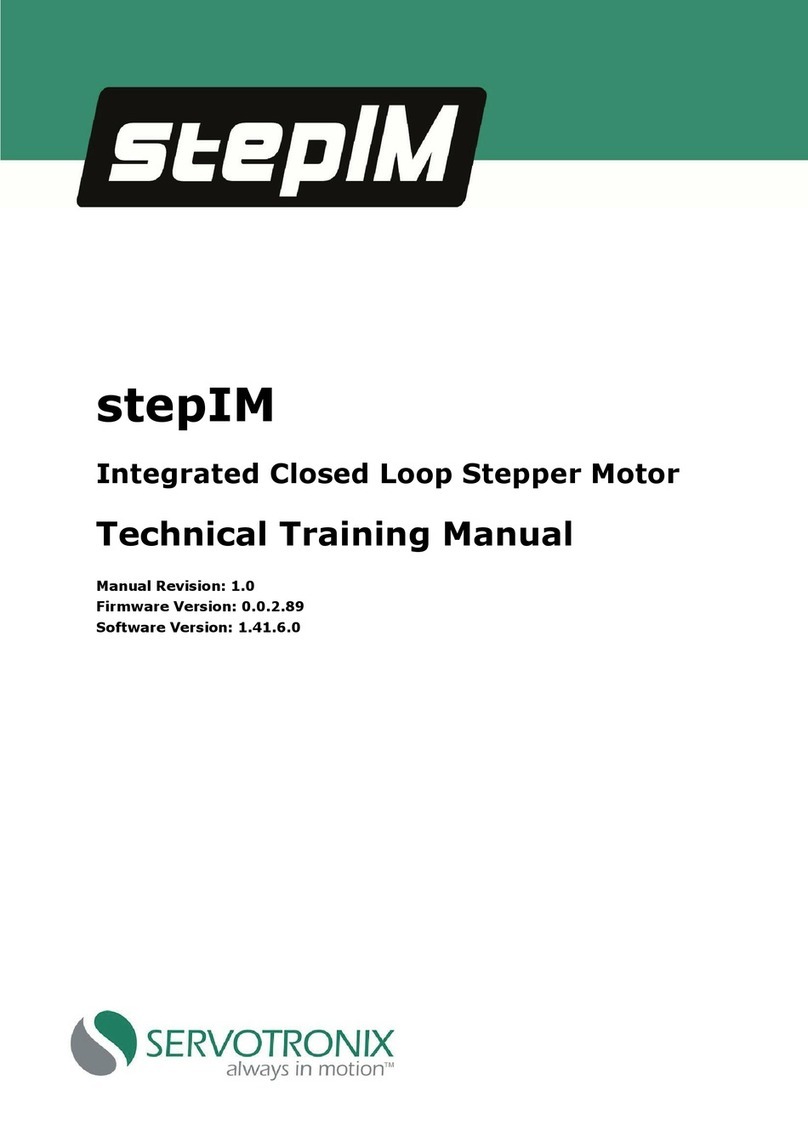
Servotronix
Servotronix stepIM Technical training manual
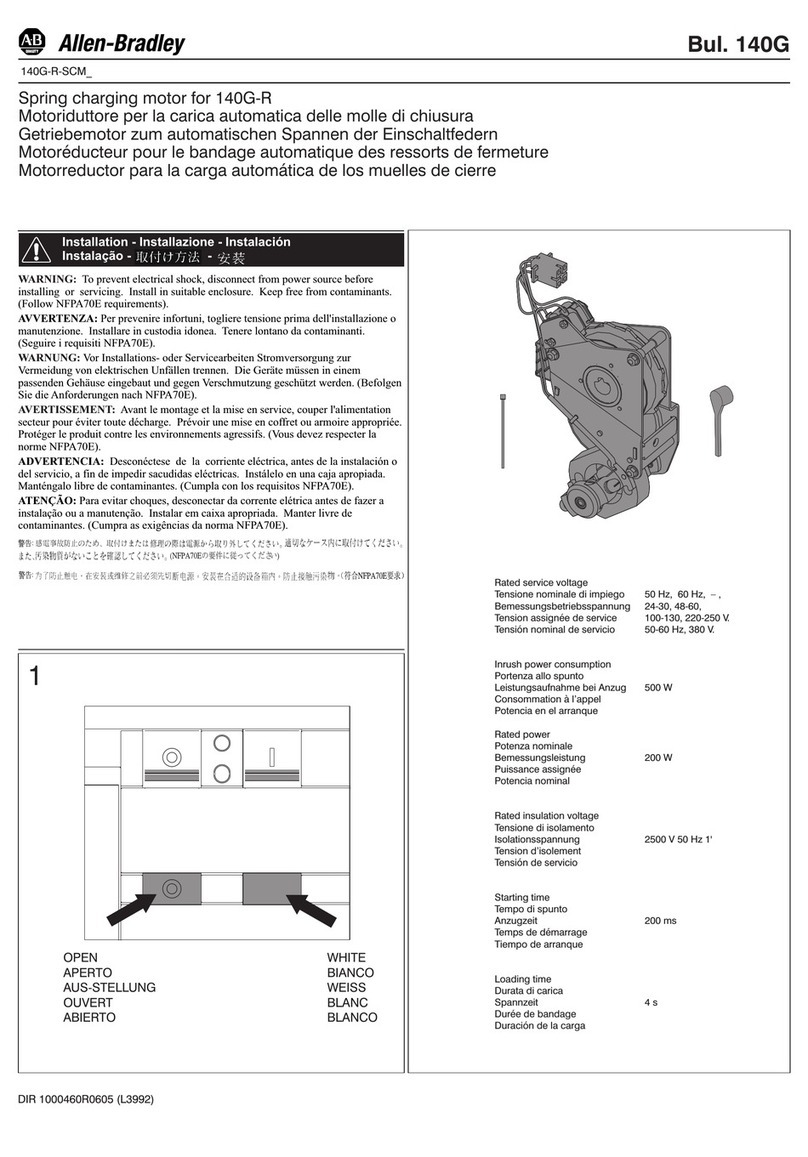
Rockwell Automation
Rockwell Automation Allen-Bradley 140G Series Installation
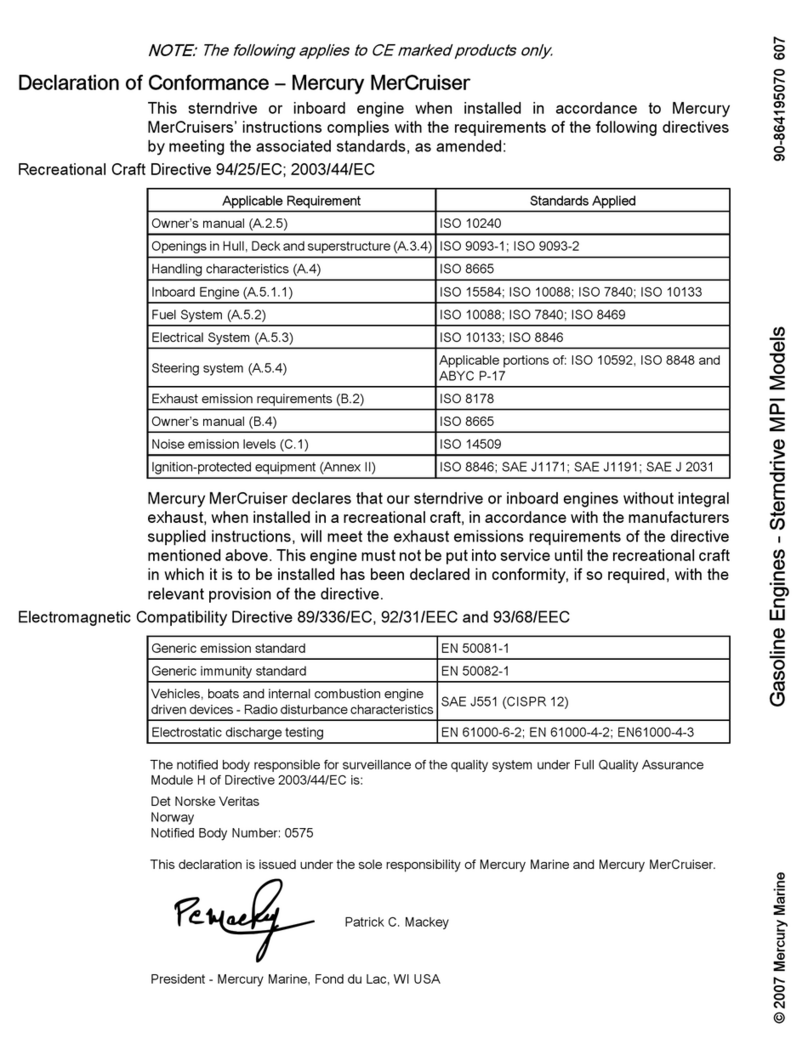
MerCruiser
MerCruiser Sterndrive 4.3 MPI user manual
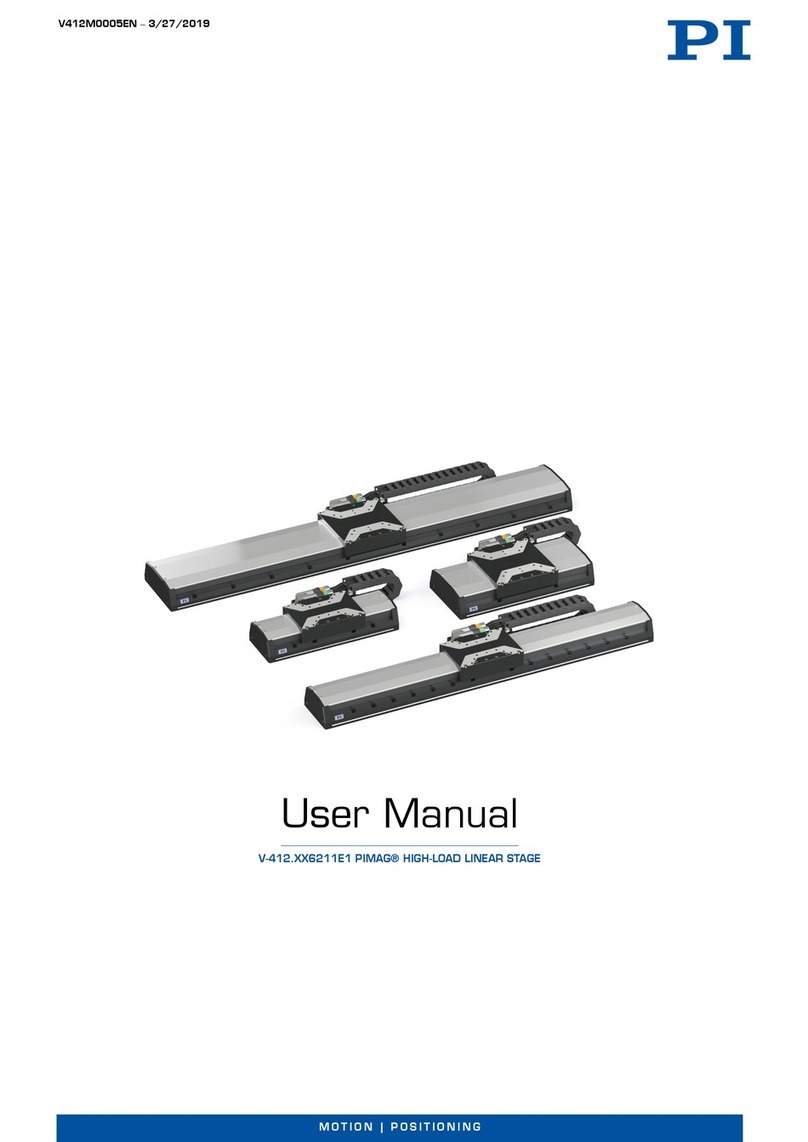
PI
PI V-412.056211E1 PIMAG user manual
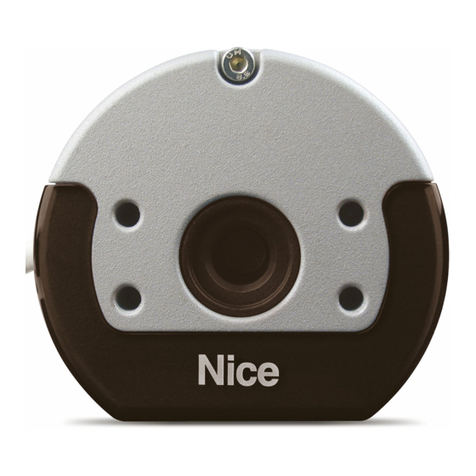
Nice
Nice Era Plus H Series Instructions and warnings for installation and use
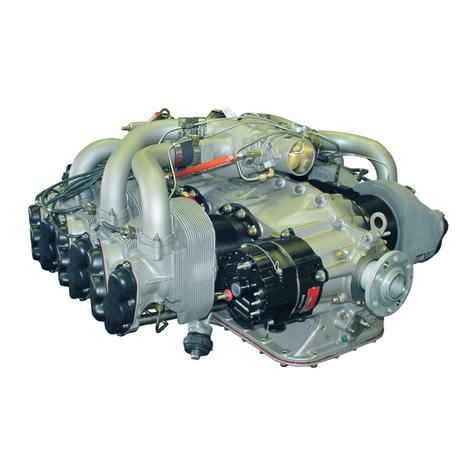
Continental Motors
Continental Motors TSIOL-550-C Operation, maintenance & installation manual
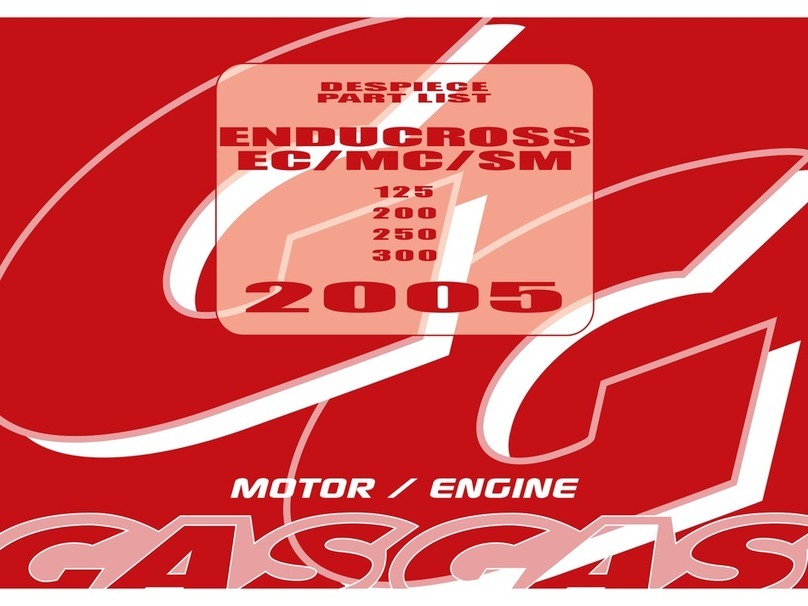
GAS GAS
GAS GAS ENDUCROSS EC 125 - PART LIST 2005 PART 1 parts list
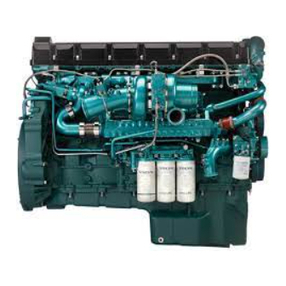
Volvo
Volvo D16F Service bulletin

Jiecang
Jiecang JCA user manual
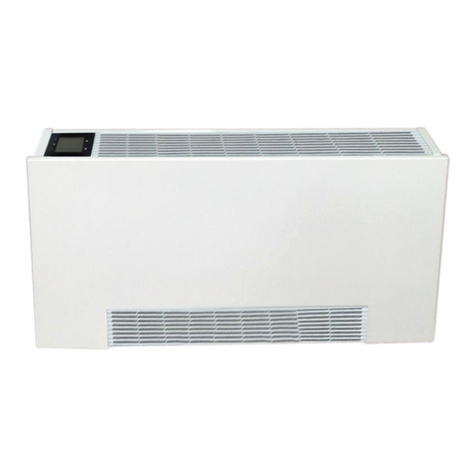
MDL Solutions
MDL Solutions PFWSL-01 Installation, operation & service manual

Briggs & Stratton
Briggs & Stratton 090000 Operator's manual

MOTO GUZZI
MOTO GUZZI BREVA V1100 Workshop manual