PI V-412.056211E1 PIMAG User manual

V412M0005EN ‒ 3/27/2019
User Manual
V-412.XX6211E1 PIMAG® HIGH-LOAD LINEAR STAGE
MOTION | POSITIONING

Contents
1 Legal Information.........................................................................................................4
2 About this Document..................................................................................................5
2.1 Objective and Target Group..............................................................................5
2.2 Explanation of Symbols....................................................................................5
2.2.1 Typographic Conventions................................................................. 5
2.2.2 Symbols Used.................................................................................... 5
2.3 Figures................................................................................................................6
2.4 Downloading Manuals...................................................................................... 6
3 Safety............................................................................................................................7
3.1 Intended Use......................................................................................................7
3.2 General Safety Instructions.............................................................................. 7
3.3 Organizational Measures.................................................................................. 7
3.3.1 User Manual....................................................................................... 7
3.3.2 General Personnel Qualification.......................................................7
4 Product Description..................................................................................................... 8
4.1 Model Overview.................................................................................................8
4.2 Product Labeling................................................................................................8
4.2.1 Type Plate........................................................................................... 9
4.3 Scope of Delivery...............................................................................................9
4.4 Overview.......................................................................................................... 10
4.4.1 Base Body......................................................................................... 10
4.4.2 Drive.................................................................................................. 10
4.4.3 Drag chain......................................................................................... 11
4.4.4 Linear Encoder Connector............................................................... 11
4.4.5 Purge Air System..............................................................................11
4.5 Suitable Electronics......................................................................................... 12
4.6 Accessories...................................................................................................... 12
5 Unpacking.................................................................................................................. 13
6 Installation................................................................................................................. 14
6.1 Mounting the V-412.xx6211E1.........................................................................14
6.2 Connecting the V-412.xx6211E1 to the Protective Earth Conductor............ 15
6.3 Building a Multi-Axis System......................................................................... 17
6.4 Mounting the Load onto the V-412.xx6211E1................................................ 20
6.5 Connecting the V-412.xx6211E1......................................................................21
7 Startup / Operation................................................................................................... 23
7.1 Starting and Operating the V-412.xx6211E1.................................................. 23
8 Maintenance...............................................................................................................25
8.1 Cleaning............................................................................................................25
8.2 Moving the Motion Platform by Hand........................................................... 25
CONTENTS V412M0005EN ‒ 3/27/2019
2MOTION | POSITIONING

9 Troubleshooting......................................................................................................... 26
10 Transportation............................................................................................................27
10.1 Attaching the Transport Safeguard................................................................ 27
10.2 Preparing the V-412.xx6211E1 for Transportation......................................... 27
11 Customer Service Department.................................................................................28
12 Technical Data............................................................................................................ 29
12.1 Specifications...................................................................................................29
12.2 Maximum Ratings........................................................................................... 31
12.3 Ambient Conditions and Classifications........................................................31
12.4 Dimensions...................................................................................................... 32
13 Old Equipment Disposal........................................................................................... 34
14 Appendix.................................................................................................................... 35
14.1 Pin Assignment................................................................................................35
14.1.1 Drive Connector............................................................................... 35
14.1.2 Encoder connector...........................................................................36
14.2 Reference point switch specifications............................................................36
14.3 Limit switch specifications..............................................................................37
14.4 NTC temperature sensor.................................................................................37
15 EU Declaration of Conformity...................................................................................40
CONTENTS V412M0005EN ‒ 3/27/2019
3MOTION | POSITIONING

1 Legal Information
The following company names and brands are registered trademarks of Physik Instrumente
(PI) GmbH & Co. KG:
PI®, PIC®, NanoCube®, PICMA®, PIFOC, PILine®, NEXLINE®, PiezoWalk®, PicoCube®,
PiezoMove®, PIMikroMove, NEXACT®, Picoactuator®, PInano®, NEXSHIFT®, PITOUCH®,
PIMag®, PIHera, Q-Motion®
The patents held by PI can be found in our list at http://www.physikinstrumente.com/en/
about-pi/patents.
© 2019 Physik Instrumente (PI) GmbH & Co. KG, Karlsruhe, Germany. The text, photographs,
and drawings in this manual are protected by copyright. With regard thereto, Physik
Instrumente (PI) GmbH & Co. KG reserves all rights. The use of any text, images and
drawings is permitted only in part and only when indicating the source.
Original instructions
First print: 3/27/2019
Document number: V412M0005en, ASt
Subject to change. This manual is superseded by any new release. The latest versions of the
user manuals are available for download (p. 6) at www.pi.ws.
Publisher:
PI miCos GmbH
Freiburger Strasse 30
79427 Eschbach
Germany
www.pi.de
Customer service department:
Physik Instrumente (PI) GmbH & Co. KG
Auf der Roemerstrasse 1
76228 Karlsruhe
Germany
www.pi.de
1 LEGAL INFORMATION V412M0005EN ‒ 3/27/2019
4MOTION | POSITIONING

2 About this Document
2.1 Objective and Target Group
This user manual contains the information needed for the intended use of the
V-412.xx6211E1.
Basic knowledge of closed-loop systems, motion control concepts, and applicable safety
measures is assumed.
2.2 Explanation of Symbols
This chapter explains the symbols and markings used by PI in their user manuals.
2.2.1 Typographic Conventions
Symbol / Label Meaning
1.
2.
Action consisting of several steps whose sequential order must be ob-
served
■ List item
p. 5 Cross-reference to page 5
RS-232 Labeling of an operating element on the product (example: socket of
the RS-232 interface)
Start > Settings
Menu path in the PC software (example: to open the menu, the
Start
and
Settings
menus must be clicked successively)
POS? Command line or a command from PI's General Command Set (GCS)
(example: command to get the axis position)
Device S/N
Parameter name (example: parameter where the serial number is stor-
ed)
5Value that must be entered or selected via the PC software
2.2.2 Symbols Used
Symbol / Label Meaning
General hazard symbol
DANGER
Dangerous situation
Failure to observe can lead to death or serious injury.
►Measures for avoiding the risk.
WARNING
Dangerous situation
Failure to observe can lead to serious injury.
►Action to take to avoid the risk.
2 ABOUT THIS DOCUMENT V412M0005EN ‒ 3/27/2019
5MOTION | POSITIONING

CAUTION
Dangerous situation
Failure to observe can lead to minor injury.
►Actions to take to avoid the risk.
NOTICE
Dangerous situation
Failure to observe can lead to material damage.
►Action to take to avoid the risk.
Information
Additional information on the V-412.xx6211E1 that can affect your application.
2.3 Figures
For better understandability, the colors, proportions and degree of detail in illustrations can
deviate from the actual circumstances. Photographic illustrations may also differ and must
not be seen as guaranteed properties.
2.4 Downloading Manuals
The latest versions of the user manuals can be downloaded (p. 6) at www.pi.ws.
For products that are supplied with software (data storage device in the scope of delivery),
access to the manuals is protected by a password. Protected content is only displayed on the
website after entering the access data. You need the data storage device for the product to
get the access data.
If a manual is missing or problems occur with downloading, contact our customer service
department (p. 28).
Downloading Manuals
1. Open the website www.pi.ws.
2. If the product was shipped with a data storage device: Log into the website:
a) Click Login.
b) Enter the login data.
The login data is in the [...]_Releasenews_[...].pdf in the Manuals directory on the
data storage device.
If necessary: Follow the link and register yourself to get the login data.
c) Click Login or press the Enter key.
3. Search for the product:
a) Click Search.
b) Enter the product number up to the period (e.g., V-412) into the search field.
c) Click Start search or press the Enter key.
d) If necessary: Click Load more results at the bottom of the list.
4. Click the corresponding product in the list of search results.
5. Click the Downloads tab.
➔The manuals are shown under
Documentation
.
6. Click the desired manual and save it.
2 ABOUT THIS DOCUMENT V412M0005EN ‒ 3/27/2019
6MOTION | POSITIONING

3 Safety
3.1 Intended Use
The V-412.xx6211E1 is a laboratory device as defined by DIN EN 61010-1. It is intended for
indoor use and use in an environment that is free of dirt, oil, and lubricants.
In accordance with its design, the V-412.xx6211E1 is intended for positioning, adjusting and
shifting loads in one axis at various velocities. The V-412.xx6211E1 is not intended for
applications in areas, in which a failure would present severe risks to human beings or the
environment.
The positioner is intended for operation with a horizontally aligned motion axis. A vertically
aligned motion axis may only be operated with suitable gravity compensation (not in the
scope of delivery).
The intended use of the V-412.xx6211E1 is only possible when completely mounted and
connected. The thermal protection sensor built into the V-412.xx6211E1's motor must be
evaluated and monitored. The V-412.xx6211E1 must be operated with suitable
electronics (p. 12). The electronics are not in the scope of delivery of the V-412.xx6211E1.
The V-412.xx6211E1 may not be used for purposes other than those stated in this user
manual. The V-412.xx6211E1 may only be used in compliance with the technical
specifications and instructions in this user manual.
3.2 General Safety Instructions
The V-412.xx6211E1 is built according to state-of-the-art technology and recognized safety
standards. Improper use of the V-412.xx6211E1 may result in personal injury and/or damage
to the V-412.xx6211E1.
►Use the V-412.xx6211E1 only for its intended purpose and if it is in perfect condition.
►Read the user manual.
►Eliminate any faults and malfunctions that are likely to affect safety immediately.
The operator is responsible for correct installation and operation of the V-412.xx6211E1.
3.3 Organizational Measures
3.3.1 User Manual
►Always keep this user manual available with the V-412.xx6211E1. The latest versions of
the user manuals can be downloaded (p. 6) at www.pi.ws.
►Add all information from the manufacturer such as supplements or technical notes to the
user manual.
►If you give the V-412.xx6211E1 to a third party, also include this user manual as well as
other relevant information provided by the manufacturer.
►Only use the device on the basis of the complete user manual. Missing information due to
an incomplete user manual can lead to serious or fatal injuries and damage to equipment.
►Only install and operate the V-412.xx6211E1 after you have read and understood this user
manual.
3.3.2 General Personnel Qualification
The V-412.xx6211E1 may only be installed, started up, operated, maintained, and cleaned by
authorized and appropriately qualified personnel.
3 SAFETY V412M0005EN ‒ 3/27/2019
7MOTION | POSITIONING

4 Product Description
4.1 Model Overview
PIMag®high-load linear stage, xx mm travel range, 116 mm width, 400 N load capacity,
incremental linear encoder with sin/cos signal transmission, 20 µm signal period, drag
chain, ironless 3-phase linear motor, to 300 V
Product number Travel range: xx
V-412.036211E1 52 mm (2")
V-412.056211E1 102 mm (4")
V-412.096211E1 204 mm (8")
V-412.136211E1 305 mm (12")
V-412.176211E1 407 mm (16")
V-412.216211E1 508 mm (20")
V-412.256211E1 610 mm (24")
4.2 Product Labeling
1
1
2
1
3
3
4
5
6
Figure 1: Product labels on the V-412.xx6211E1
1. Warning symbol: Risk of crushing
2. Type plate
3. Connector labels
4. Warning symbol: Electrostatic-sensitive device
5. Optional protective earth connector
6. Functional earth
4 PRODUCT DESCRIPTION V412M0005EN ‒ 3/27/2019
8MOTION | POSITIONING

4.2.1 Type Plate
Figure 2: Type plate of the V-412.xx6211E1
1. Data matrix code (example; contains the serial number)
2. Product number (example)
3. Serial number (example), individual for each V-412.xx6211E1
Meaning of the position (counting from the left):
1 = internal information,
2 and 3 = year of manufacture,
4 to 9 = consecutive numbers
4. Warning and conformity symbols (old equipment disposal (p. 34), CE mark (p. 40))
4.3 Scope of Delivery
Product number Description
V-412.xx6211E1 Linear stage according to the order (p. 8)
For V-412.xx6211E1 with xx = 03, 05, 09, 13:
V412B0036
Mounting kit for mounting the
V-412.xx6211E1, consisting of
■10 socket head screws, ISO 4762 M6×30
■2 dowel pins, ISO 8734, 4m6 × 12
For V-412.xx6211E1 with xx = 17, 21, 25:
V412B0037
Mounting kit for mounting the
V-412.xx6211E1, consisting of
■16 socket head screws, ISO 4762 M6×30
■2 dowel pins, ISO 8734, 4m6 × 12
V412M0005 User manual for the V-412.xx6211E1 (this
document)
4 PRODUCT DESCRIPTION V412M0005EN ‒ 3/27/2019
9MOTION | POSITIONING

4.4 Overview
1
2
5
3
4
Figure 3: Elements of the V-412.xx6211E1
1. Base body with drive
2. Motion platform
3. Drive and linear encoder connector
4. Purge air connector
5. Drag chain
4.4.1 Base Body
The base body is the basis of the positioner. The V-412.xx6211E1 is mounted onto a surface
via the base body (p. 14).
The base body comprises the following subassembly (subassemblies):
Drive
The drive of the positioner is a 3-phase magnetic linear motor. The linear motor transfers the
drive force to the motion platform directly and free of friction.
Reference Point Switch
The reference point switch is a sensor whose fixed position serves as the reference point for
incremental sensor signals.
Limit switches
The limit switches are sensors at each end of the travel range that enable the electronics to
abort motion in order to prevent the motion platform from colliding with the mechanical
hard stop.
Incremental linear encoder
An incremental linear encoder is a sensor that measures the position of the motion platform
incremental to a known reference point. Optical linear encoders measure the actual position
directly. Therefore, errors in the drive, such as nonlinearity, backlash or elastic deformations
cannot influence the measurement of the position.
4.4.2 Drive
The drive generates the torque required for the dynamics of the motion platform.
The drive comprises the following subassembly (subassemblies):
4 PRODUCT DESCRIPTION V412M0005EN ‒ 3/27/2019
10 MOTION | POSITIONING

Motor
The motor generates the torque required for the dynamics of the motion platform.
4.4.3 Drag chain
The drag chain (also: energy chain or energy supply chain) guides and protects the
V-412.xx6211E1's flexible cables and lines.
4.4.4 Linear Encoder Connector
The linear encoder connector transmits the V-412.xx6211E1's sensor signals.
4.4.5 Purge Air System
The purge air system protects the drive and guides of the V-412.xx6211E1 against
surrounding dust.
The purge air system comprises the following subassembly (subassemblies):
Passive dust protection
The passive dust protection consists of covering strips that seal the openings on the side of
the V-412.xx6211E1's base body and therefore reduces the amount of dust that can
penetrate.
Active dust protection
4 PRODUCT DESCRIPTION V412M0005EN ‒ 3/27/2019
11 MOTION | POSITIONING

The active dust protection consists of a purge air connector on the base body of the
V-412.xx6211E1, which creates a slight overpressure in the V-412.xx6211E1 and therefore
reduces the amount of dust that can penetrate.
4.5 Suitable Electronics
The V-412.xx6211E1 must be connected to suitable electronics that supply the necessary
voltage for operating and if required, to evaluate the sensor and limit switch signals. The
following electronics are suitable:
Product number Description
ACS modular controller
To order, contact our customer service department (p. 28).
4.6 Accessories
Drag chains for XY mounting
Lower linear stage Travel range of the lower lin-
ear stage / mm
Suitable drag chain
V-412.03xxxxE1 52 V-417.E1XYH03
V-412.05xxxxE1 102 V-417.E1XYH05
V-412.09xxxxE1 204 V-417.E1XYH09
V-412.13xxxxE1 305 V-417.E1XYH13
V-412.17xxxxE1 407 V-417.E1XYH17
V-412.21xxxxE1 508 V-417.E1XYH21
V-412.25xxxxE1 610 V-417.E1XYH25
To order, contact our customer service department (p. 28).
4 PRODUCT DESCRIPTION V412M0005EN ‒ 3/27/2019
12 MOTION | POSITIONING

5 Unpacking
The positioner is delivered with the transport safeguard installed.
12
Figure 4: V-412.xx6211E1 with transport safeguard
1. Transport safeguard
2. Wing screw with M6×10 thread
CAUTION
Risk of crushing by moving parts!
Risk of minor injuries from crushing between the moving parts of the V-412.xx6211E1 or the
load and a fixed part or obstacle.
►Transport the V-412.xx6211E1 only when the transport safeguard is attached.
►Bring the V-412.xx6211E1 to the intended place of use. Remove the transport safeguard
afterwards.
Unpack the V-412.xx6211E1 and remove the transport safeguard
1. Unpack the V-412.xx6211E1 with care.
2. Compare the contents with the scope of delivery according to the contract and the
delivery note.
3. Inspect the contents for signs of damage. If any parts are damaged or missing, contact
our customer service department (p. 28) immediately.
4. If the V-412.xx6211E1 was supplied with ESD protective caps on the connectors: Do not
remove the ESD protective caps.
5. Remove the transport safeguard:
a) Unscrew and remove the wing screw.
b) Remove the transport safeguard.
6. Keep all packaging materials in case the product needs to be returned.
5 UNPACKING V412M0005EN ‒ 3/27/2019
13 MOTION | POSITIONING

6 Installation
6.1 Mounting the V-412.xx6211E1
Overview
Figure 5: Mounting the V-412.xx6211E1 onto an underlying surface
Tools and Accessories
■Screw set for mounting the V-412.xx6211E1 (p. 9)
■Suitable screwdriver
Requirements
✓You have read and understood the general safety instructions (p. 7).
✓You have provided a suitable surface with the holes necessary for the screws and if
required, locating pins (p. 32).
■The flatness of the surface is ≤ 2 μm.
■For applications with large temperature changes: The surface should have the same or
similar thermal expansion properties as the V-412.xx6211E1.
✓You have accounted for the space required to route cables without bending and
according to regulations.
DANGER
Risk of electric shock if the protective earth conductor is not connected!
If the protective earth conductor is missing or not properly connected, risk of dangerous
touch voltages on the V-412.xx6211E1 in the event of malfunction or failure of the system. If
there are touch voltages, touching the V-412.xx6211E1 leads to serious injuries or death by
electric shock.
►Connect the V-412.xx6211E1 to a protective earth conductor before startup.
►Do not remove the protective earth conductor during operation.
►If the protective earth conductor has to be removed temporarily (e.g., for modifications),
reconnect the V-412.xx6211E1 to the protective earth conductor before restarting.
6 INSTALLATION V412M0005EN ‒ 3/27/2019
14 MOTION | POSITIONING

CAUTION
Risk of crushing by moving parts!
Risk of minor injuries from crushing between the moving parts of the V-412.xx6211E1 or the
load and a fixed part or obstacle.
►Use safeguards to protect limbs in areas where they could be caught by moving parts.
►Maintain the safety distances according to DIN EN ISO 13857 when installing protective
structures.
NOTICE
Damage due to collisions!
Collisions can damage the V-412.xx6211E1, the load to be moved, and the surroundings.
►Make sure that collisions are not possible between the V-412.xx6211E1, the load to be
moved, and the surroundings in the motion range of the V-412.xx6211E1.
►Do not place any cables or other objects in areas where they could be caught by moving
parts.
NOTICE
Excessively long screws and locating pins
Screws and locating pins that are inserted too deeply can damage the V-412.xx6211E1.
►Pay attention to the depth of the mounting and locating holes (p. 33) in the
V-412.xx6211E1.
►Only use screws and locating pins of the correct length for the respective mounting holes.
Mounting the V-412.xx6211E1 on a Surface
1. If necessary: Insert the locating pins into the corresponding holes in the surface.
2. Align the V-412.xx6211E1 on the surface so that the corresponding mounting holes in the
V-412.xx6211E1 and the surface are aligned.
3. Place the V-412.xx6211E1 onto the surface so that the locating pins can be inserted into
the corresponding locating holes of the V-412.xx6211E1.
4. If necessary: Allow access to the mounting holes in the base body of the V-412.xx6211E1.
Possible measures:
■Temporary startup of the V-412.xx6211E1 (p. 23) and commanding the motion
platform to a suitable position
■Push the motion platform by hand (p. 25)
5. Tighten the screws in all accessible mounting holes completely.
Recommended torque: 3 Nm
6. If necessary: Repeat steps 4 to 5 for all concealed mounting holes.
7. Check that the V-412.xx6211E1 is fixed firmly to the surface.
6.2 Connecting the V-412.xx6211E1 to the Protective Earth Conductor
The V-412.xx6211E1 must be connected to the protective earth conductor via the drive
connector.
It is only necessary to connect the V-412.xx6211E1's base body to the protective earth
conductor when the following conditions are met:
■The electronics do not guarantee safe connection of the drive connector to the ground
potential.
6 INSTALLATION V412M0005EN ‒ 3/27/2019
15 MOTION | POSITIONING

Overview
Figure 6: Protective earth connector on the V-412.xx6211E1
1. Connector for the protective earth conductor on the V-412.xx6211E1, indicated by the
protective earth symbol
2. Safety washer
3. Flat washer
4. Protective earth conductor lug
5. Screw, ISO 7045 M4×8
Tools and Accessories
■Suitable protective earth conductor:
■Cable cross section ≥ 0.75 mm2
■Contact resistance <0.1 Ω at 25 A at all connection points relevant for attaching the
protective earth conductor
■Suitable screwdriver
Requirements
✓You have read and understood the general safety instructions (p. 7).
DANGER
Risk of electric shock if the protective earth conductor is not connected!
If the protective earth conductor is missing or not properly connected, risk of dangerous
touch voltages on the V-412.xx6211E1 in the event of malfunction or failure of the system. If
there are touch voltages, touching the V-412.xx6211E1 leads to serious injuries or death by
electric shock.
►Connect the V-412.xx6211E1 to a protective earth conductor before startup.
►Do not remove the protective earth conductor during operation.
►If the protective earth conductor has to be removed temporarily (e.g., for modifications),
reconnect the V-412.xx6211E1 to the protective earth conductor before restarting.
Information
►Observe the applicable standards for connecting the protective earth conductor.
Connecting the V-412.xx6211E1 to the Protective Earth Conductor
1. If necessary, attach a suitable cable lug to the protective earth conductor.
2. Attach the cable lug of the protective earth conductor to the protective earth connection
as shown in the illustration of the V-412.xx6211E1.
3. Tighten the screw with a torque of 1.2 Nm to 1.5 Nm.
6 INSTALLATION V412M0005EN ‒ 3/27/2019
16 MOTION | POSITIONING

4. Make sure that the contact resistance is <0.1 Ω at 25 A at all connection points relevant for
attaching the protective earth conductor.
6.3 Building a Multi-Axis System
The V-412.xx6211E1 can be used in XY systems.
Designations in these instructions:
■Lower positioner: Forms the basis of the multi-axis system, is attached to an underlying
surface
■Upper positioner: Forms the upper axis of the multi-axis system, is attached to the lower
positioner rotated by 90°
Tools and Accessories
■Hex key AF3
■Hex key AF4
■Hex key AF6
■PH2 screwdriver
■Suitable drag chain (p. 12), depends on the travel range of the lower positioner.
NOTICE
Excessively long screws and locating pins
Screws and locating pins that are inserted too deeply can damage the V-412.xx6211E1.
►Pay attention to the depth of the mounting and locating holes (p. 33) in the
V-412.xx6211E1.
►Only use screws and locating pins of the correct length for the respective mounting holes.
Building a Multi-Axis System
1. Attach the connector box for the additional drag chain to the connector box for the lower
V-412. The screws are integrated in the connector box of the additional drag chain and
can be reached through the openings on the outside.
2. Fix the holder for the additional drag chain to the drag chain holder of the lower V-412
with two M4×40 screws.
6 INSTALLATION V412M0005EN ‒ 3/27/2019
17 MOTION | POSITIONING

3. Mount the upper V-412 onto the lower V-412.
a) Insert two 4 mm h7 × 12 mm locating pins into the motion platform of the lower V-412.
b) Align the upper V-412 to the lower V-412.
c) If necessary: Push the motion platform of the upper V-412 to access the mounting
holes in the base body.
d) Insert two M6×30 screws into the mounting holes in the upper V-412 and tighten them.
6 INSTALLATION V412M0005EN ‒ 3/27/2019
18 MOTION | POSITIONING

e) Push the motion platform of the upper V-412 to the negative end of the travel range.
f) Push the retaining plate under the drag chain. Align the retaining plate to the mounting
hole of the upper V-412.
g) Insert two M6×30 screws into the mounting holes in the upper V-412 and tighten them.
12
3
3
4. In addition to the V-412.xx6211E1 with xx = 21, 25, 33:
Fix the short retaining plate to the base body of the upper V-412 with an M6×30 screw and
a cap nut.
6 INSTALLATION V412M0005EN ‒ 3/27/2019
19 MOTION | POSITIONING

6.4 Mounting the Load onto the V-412.xx6211E1
Overview
1
1
1
1
2
3
Figure 7: Mounting the load onto the V-412.xx6211E1
1. Screws
2. Load
3. Motion platform of the V-412.xx6211E1
Tools and Accessories
■At least 3 screws with suitable dimensions (p. 33)
■Suitable tool for tightening the screws
■Optional: 2 suitably dimensioned dowel pins as locating pins for aligning the load on the
V-412.xx6211E1
Requirements
✓You have read and understood the general safety instructions (p. 7).
✓You have mounted the V-412.xx6211E1 on the surface (p. 14) properly.
✓The V-412.xx6211E1 is not connected to the electronics.
✓You have prepared the load so that it can be fixed to the mounting holes on the motion
platform:
6 INSTALLATION V412M0005EN ‒ 3/27/2019
20 MOTION | POSITIONING
This manual suits for next models
6
Table of contents
Other PI Engine manuals
Popular Engine manuals by other brands
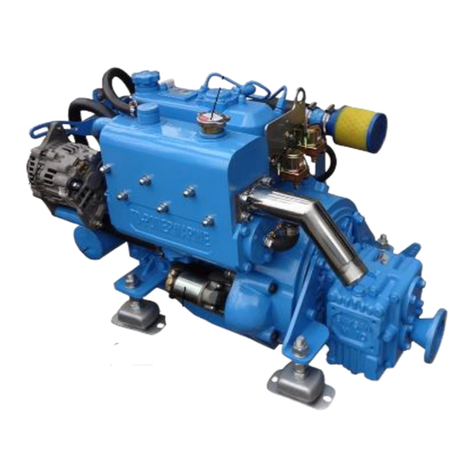
Marine Power Solutions
Marine Power Solutions MP-214 Operation manual

Vortex
Vortex MINI ROK owner's manual

SOMFY
SOMFY LV25 installation guide
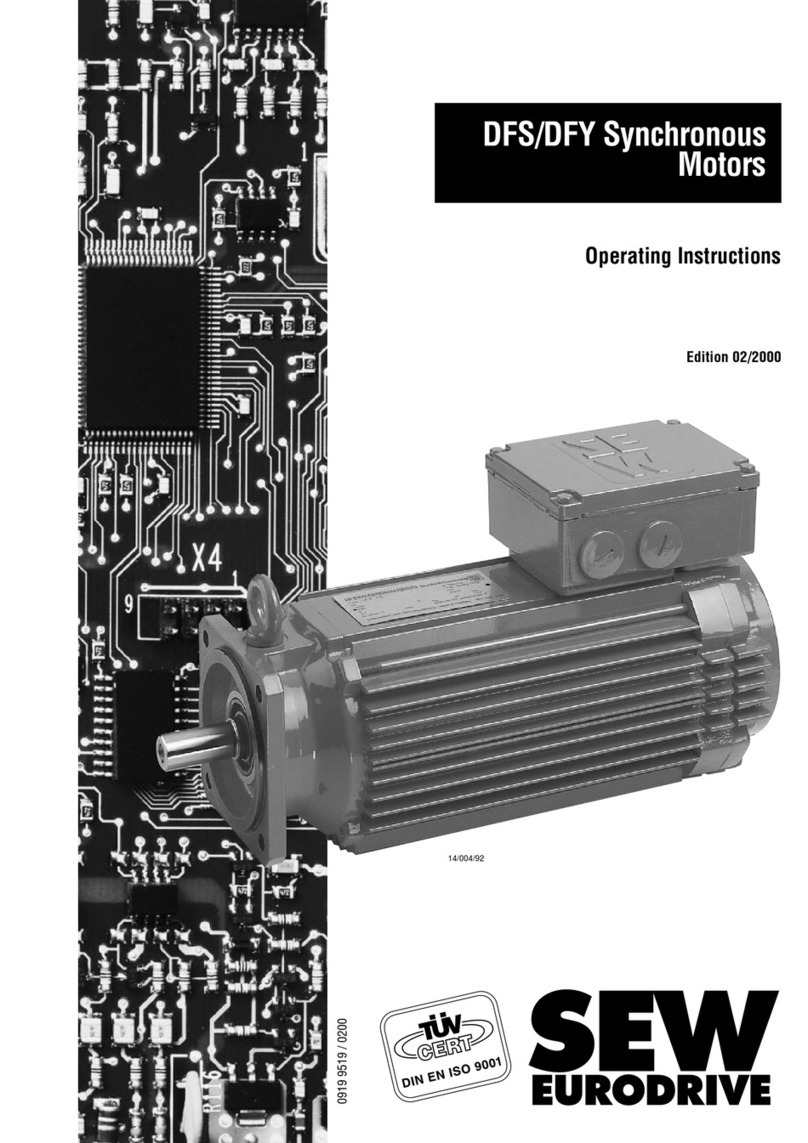
SEW-Eurodrive
SEW-Eurodrive DFS Series operating instructions

Briggs & Stratton
Briggs & Stratton Vanguard 50000 operating & maintenance manual
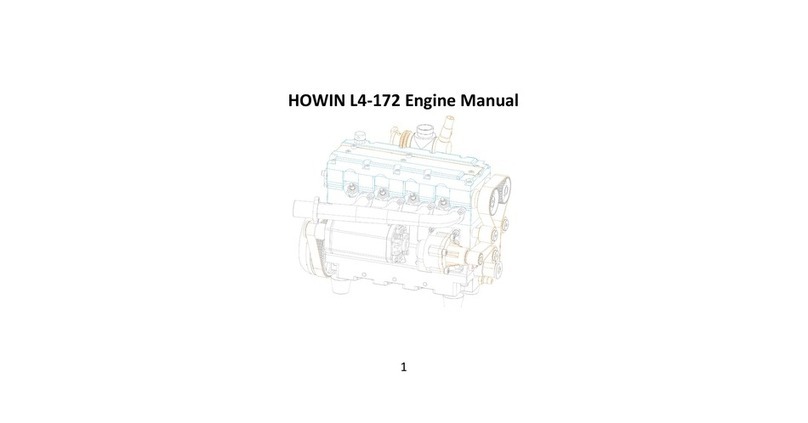
HOWIN
HOWIN L4-172 manual