Novatech DDS9m User manual

NOVATECH INSTRUMENTS
1
DDS9m Manual
INSTRUCTION MANUAL
Model DDS9m 170MHz 4-Channel Signal Generator Module
DDS9m
Table of Contents
Section
Page
Contents
1.0
. . . . . . . . . . . . . . . . . . . . . . . . . . . . .
2
. . . . . . . . . . . . . . . . . . . . . . . . .
Description
2.0
. . . . . . . . . . . . . . . . . . . . . . . . . . . . .
2
. . . . . . . . . . . . . . . . . . . . . . .
Specifications
3.0
. . . . . . . . . . . . . . . . . . . . . . . . . . . . .
2
. . . . . . . . . . . . . . . . .
Hardware Installation
4.0
. . . . . . . . . . . . . . . . . . . . . . . . . . . . .
7
. . . . . . . . . . . . . . . . . . . . . . . . . . .
Operation
5.0
. . . . . . . . . . . . . . . . . . . . . . . . . . . . .
10
. . . . . . . . . . . . . . . . . .
Theory of Operation
6.0
. . . . . . . . . . . . . . . . . . . . . . . . . . . . .
11
. . . . . . . . . . . . . . . . . . . . .
Performance Test
7.0
. . . . . . . . . . . . . . . . . . . . . . . . . . . . .
12
. . . . . . . . . . . . . . . . . . . . . . . . . .
Calibration
--
. . . . . . . . . . . . . . . . . . . . . . . . . . . . . . .
14
. . . . . . . . . . . . . . . . . . . . . . . . . . .
Warranty
INSTRUMENTS

2
DDS9m Manual
1.0
DESCRIPTION
1.1 The Model DDS9m is a four-channel
D
irect
D
igital
S
ynthesizer (DDS) on a small printed wiring
module with RS232 serial control. The DDS9m pro-
vides four independent sine wave and LVCMOS
output signals, which can be set from 0.1Hz to
171MHz in 0.1Hz steps when using the internal
VCTCXO clock (LVCMOS is optimized for outputs
greater than 1MHz and less 125MHz).
1.2 The DDS9m can also be used with an External
Clock input. An on-board programmable frequency
multiplier generates the master clock allowing user
configured frequency ranges. The multiplier can be
disabled for direct inputs up to 500MHz for opti-
mum phase noise performance. When used with the
same external clock source, multiple DDS9m are
phase synchronous.
2.0
SPECIFICATIONS
2.1 OUTPUTS
TYPES: Four Sine and LVCMOS simultaneously (four
frequencies.)
IMPEDANCE: Sine: 50Ω; LVCMOS:50Ω.
RANGE: 0.1Hz to 171MHz in 0.1Hz steps (Sine out, int.
clock).
SINE AMPLITUDE: approximately 1Vpp (+4dBm @
35MHz) into 50Ω. Programmable from 0/1024 to 1023/
1024 of Full Scale (10-bits).
PHASE: Each channel 14-bits programmable.
FLATNESS: ±3dB from 1kHz to 150MHz referenced to
amplitude at 35MHz, fullscale.
2.2 LVCMOS AMPLITUDE
Voh >=2.4V and Vol <=0.4V whenseries terminated. Rise
and fall times <1.5ns. (1MHz< Fout<125MHz)
2.3 CONTROL
Output frequencies, amplitudes (10-bits) and phases (14-
bits) are controlled by an RS232 serial port at 19.2kbaud.
All settings (except table mode data) can be saved in
non-volatile (EEPROM) memory via the RS232 port.
2.4 ACCURACY AND STABILITY
Accuracy: <±1.5ppm at 10 to 40oC. Stable to an addi-
tional ±1ppm per year, 18 to 28oC. (Internal Clock)
2.5 EXTERNAL CLOCK IN
LEVEL: 0.2 to 0.5Vrms Sine or Square Wave. 50Ω.
FREQUENCY: 10MHz to 125MHz with multiplier of 4 to
NOVATECH INSTRUMENTS
20 enabled. Direct input of 1MHz to 500MHz.
2.6 SPECTRAL PURITY
(Typ. 50Ωload, internal
clock, full-scale output)
Phase Noise: <-120dBc, 10kHz offset, 5MHz out.
Spurious: <-60dBc below 10MHz (typ. 300MHz span)
<-60dBc below 40MHz
<-55dBc below 80MHz
<-50dBc below 160MHz
Harmonic: <-65dBc below 1MHz
<-55dBc below 20MHz
<-45dBc below 80MHz
<-35dBc below 160MHz
(channel-channel isolation: <-60dBc)
2.7 TABLE MODE
On-board 4Mb static ram holds up to 32,768 profile
points in table mode allowing a different output in 100µs
increments. Channels 0 and 1 only.
2.8 POWER REQUIREMENTS
+3.14V to +3.46VDC@<750mA. Battery back-up 3.0V
nominal at <400µA (2-AA, LR6, typical).
2.9 SIZE
82.6mm by88.9mm circuit board. Max. height 10mm.
2.10 CONNECTORS
MCX for Sine Outputs and EXT CLK IN. 2-pin header for
+3.3V power and external back-up battery. 24-pin header
for high speed control. DE9 for Serial Control. 2-pin wire-
points for LVCMOS outputs.
3.0 HARDWARE INSTALLATION
WARNING:
The DDS9m contains static sensitive components.
Before opening the package, follow appropriate
static precautions. Failure to follow static
precautions may damage the DDS9m.
3.1 Power Connection. Figure 1, Connection
Placement Diagram, shows a top view of the
DDS9m module. The required power of +3.3Volts
DC is applied through a 2-pin connector (mates with
Amp 640621-2). If you are using a Novatech Instru-
ments supplied connector, Red is +3.3VDC and
Black is the common return.
3.2 The quality of your power supply may affect the
performance of the DDS9m. The supply should be
free of ripple and noise (<50mV). Even though

3
DDS9m Manual
extensive filtering is used on the DDS9m board, a
quiet and well regulated power supply will ensure
optimum performance. If switching power supplies
are used, please verify that your system noise
requirement is met.
3.3
RS232 Installation.
To use the DDS9m in the
RS232 mode, connect your host computer to the 9-
pin female RS232 connector on the DDS9m. If you
are using a PC, a 9-pin monitor extension cable used
as an RS232 cable will allow direct connection to
the DDS9m without the use of a null modem cable
or gender changer. If you are using a different com-
puter, terminal or other control source, please note
that the data
TO
the DDS9m is on pin 3; the data
FROM
the DDS9m is on pin 2 and the
COMMON
return is on pin 5. Set your host to 19.2 kbaud, 8 bits,
1 stop bit, no parity and no hardware flow control.
See Table 2 for RS232 Serial Commands.
3.4 You may use a USB to RS232 adapter cable
with computers that do not provide a serial port. Fol-
low the manufacturer’s installation instructions
when using a USB adapter.
3.5 Commands are not case sensitive. There must
be a space after each command except R,CLR,S
and QUE. End with any combination of CR, LF or
CRLF. Illegal commands will result in an error
code being returned per Table 1.
3.6 The “QUE” command returns five hexadecimal
strings reflecting the present state of the DDS9m.
NOVATECH INSTRUMENTS
See page 9 for an explanation of the values that
make up these strings. Note that the frequency set-
tings will be scaled as discussed below if an external
clock is used.
3.7 The
“B”
command can cause erroneous opera-
tion and must be used with care. Detailed knowledge
of the operation of the Analog Devices AD9959
DDS generator is required. Since all registers are
accessible, it is possible to set the board into a non-
functional mode, requiring a reset. Application Note
AN001 shows an example of the command for set-
ting frequency.
NOTE:
The program
SOF8
is available for the DDS9m.
This program provides a graphical interface for all
the serial commands, allowing simple control of the
DDS9m. The
SOF8
CD contains multiple versions
of the software. Be sure to read the README file to
see which is appropriate for your instrument.
3.8
Internal Clock.
If you plan to use the DDS9m
internal clock, which is the default setup mode, no
action is required. If the DDS9m was previously set
to use the external clock, send the serial command
“C i” to reselect the internal clock. If you wish to
maintain this setting, use the save command “S”.
3.9
External Clock
. If you are providing your own
clock source, send the serial command “C e”.
Apply your clock to the External Clock Input MCX
on the board. Note that phase noise and stability are
dependent upon your supplied clock. See specifica-
tions for signal levels required and acceptable fre-
quency range. If you wish to maintain this setting,
use the save command “S”.
3.10 The external clock can also be used with Kp=1
for direct connection to the DDS generator. With
Kp=1, the PLL multiplier is disabled. Use this direct
input, up to 500MHz, for optimum phase noise per-
formance.
NOTE:
When using an external clock, frequency scaling of
the “Fn” command may be required. Please see
Operation, Section 4, for details.
Table 1:
RS232 Error Codes
Error Code
Meaning
OK Good command received (not sent for
R, CLR and QUE)
?0 Unrecognized Command
?1 Bad Frequency
?2 Bad AM Command
?3 Input line too long
?4 Bad Phase
?5 Bad Time
?6 Bad Mode
?7 Bad Amp
?8 Bad Constant
?f Bad Byte

NOVATECH INSTRUMENTS
4
DDS9m Manual
Table 2:
RS232 Serial Commands
RS232 Command
Function
Fn xxx.xxxxxxx
Set Frequency of output “n” in MHz to nearest 0.1Hz. Decimal point required.
n=0, 1, 2, 3. Maximum setting: 171.1276031MHz. Single tone mode.
Pn N
Set Phase of output “n.” N is an integer from 0 to 16383. Phase is set to N*360
o
/
16384 or N*
π
/8192 radians. Sets the relative phase of the frequency output
depending upon the value of n=0, 1, 2, 3. Single tone mode.
E x
Serial echo control. x=D for Echo
D
isable, x=E for Echo
E
nable
C x
Select clock source. x=E for
E
xternal clock, x=I for
I
nternal Clock. May require
adjustment of Kp and external filtering of output when an external clock is used.
R
Reset. This command resets the DDS9m. EEPROM data is preserved and, if valid,
is used upon restart. This is the same as cycling power.
CLR
Clear. This command clears the EEPROM valid flag and restores all factory
default values.
A x
CMOS output control. x=E for LVCMOS
E
nable, x=D for LVCMOS
D
isable.
S
Saves current state into EEPROM and sets valid flag. State used as default upon
next power up or reset. Use the
“CLR”
command to return to default values.
QUE
Return present frequency, phase and status. Returns a character string of all inter-
nal settings.
M N
Mode command. Mode ‘0’ is single tone on all channels (default). If N=a, then the
phase is automatically cleared during each command; if N=n, then the phase is not
cleared (default). See Section 4 for details.
Vn N
Set voltage level of output “n.” In default, the amplitude is set to the maximum:
approximately 1V
pp
(+4dBm) into 50
Ω.
N can range from 0 (off) to 1023 (no
decimal point allowed). Voltage level is scaled by N/1023. n=0, 1, 2, 3 to set the
amplitude on frequency 0, 1, 2 or 3. If N >=1024, the scaling is turned off and the
selected output is set to full scale.
Vs N
Set the output scaling factor. N=1 for full scale, N=2 for half scale, N=4 for one
quarter scale and N=8 for one eighth scale. All channels are scaled equally.
Kp aa
Set the DDS on-chip PLL reference multiplier constant. Must be one Hexadecimal
byte as two characters. Legal values are 1 (bypass PLL) and 4 to 20 (01
h
, 04
h
to
14
h
). Values of Kp times clock frequency must not be between 160MHz and
255MHz (for internal clock, this disallows 5<=Kp<= 9). (see paragraph 4.12 for
other considerations)
I x
Set the I/O update pulse method. If x=a, then an I/O update is issued
a
utomatically
at the end of each serial command (default). If x=m, then a
m
anual I/O update
pulse is expected to be sent by a subsequent
‘I p’
command. See section 4.
B aa[bb[cc[dd[ee[ff[gg]]]]]]
This
B
yte command allows each register in the DDS chip to be set. Different
registers require a various number of bytes to be written depending upon the
function. Please consult the Analog Devices AD9959 data sheet for details. Note
that it is possible to set the DDS chip into a non-functional mode, requiring a
power cycle to recover. All values are in hexadecimal and no error checking, other
than correct format, is performed.

NOVATECH INSTRUMENTS
5
DDS9m Manual
Table 3: Mounting Hole Locations
Hole (CCW) X,Y mm X,Y inch
1 5.08, 3.81 0.20, 0.15
2 78.7, 3.81 3.10, 0.15
3 78.7, 85.1 3.10, 3.35
4 22.9, 85.1 0.90, 3.35
5 5.08, 85.1 0.20, 3.35
+3.3V DC
RS232
EXT CL
K
BATT B.U.
HIGH SPEED
INTERFACE
VTUNE
SINE OUTs
LVCMOS OUTs (MCXs)
(WIRE PTs)
0,0
(MCX)
115.2kBaud Select
12
3
4
5
3V DC
Lower Left Corner of board (as shown by 0,0) is origin of X,Y coordinates for hole location.
Figure 1: Component Placement

NOVATECH INSTRUMENTS
6
DDS9m Manual
Table 4:
High Speed Interface Connector Pinout, P1.
WARNING:
The parallel inputs are 3.3V CMOS compatible. Applying 5V logic signals to these inputs will permanently
damage the DDS9m. If your system is 5V, it is suggested that VHC buffers powered by 3.3V be placed
between the DDS9m and your system. You may use the 3.3 V on pin 2 of P4 for this power (up to 50mA).
Pin
Number
Function
Type
Pin
Number
Function
Type
1
Ground (Power Supply Com-
mon)
PS
2
+3.3 V (Power Supply Refer-
ence, 50mA max)
O
3
Ground (Power Supply Com-
mon)
PS
4
SER-
I
5
no connect
--
6
no connect
-
7
no connect
-
8
no connect
-
9
RES-
I
10
IRQ-
I/O
11
EN-
O
12
SDATA
I/O
13
SCLK
I
14
IOUD
I/O
15
SYNO
O
16
SYNI
I
17
no connect
-
18
P0
I
19
P1
I
20
P2
I
21
P3
I
22
SD3
I
23
SD2
I
24
SD1
I

7
DDS9m Manual
3.11
High Speed Interface Installation.
The
DDS9m can also be controlled by using connections
to the 24-pin (12x2) header. See Table 4 for connec-
tor pinout and pin descriptions. Use of this port
requires detailed knowledge of the AD9959 DDS
generator IC. You can use the ‘B’ command to test
your operation.
NOTE:
The table mode or table RAM is not accessible from
the high speed port. The high speed port controls
only the DDS ASIC.
NOTE:
For maximum interface speed, the high-speed inputs
do not have additional protection against ESD
damage beyond that provided by the CMOS inputs
(+/-2kV, Human Body Model. +/-200 V, machine
model) and
47Ω
series resistors.
3.12 All of the inputs are 3.3V VHCMOS compati-
ble and require:
Vil <= 0.4 volts
Vih >= 2.7 volts
3.13 Cin on each pin is approximately 10pF (appli-
cation cable capacitance not included). The input
pins are series terminated with a 47Ωresistor. It is
recommended that a series termination resistor of
50-100Ωbe used at each signal line source to pre-
vent reflections and ringing. The exact value will be
determined by your application circuitry and
cabling.
3.14 SER-, pin 4 of P1 must be held low to select
the high-speed interface. During initialization, EN-,
pin 11 of P1, is held high. When initialization is
complete it returns low.
3.15 Signal Outputs. There are eight signal outputs
on the DDS9m: four channels of Sine and the corre-
sponding LVCMOS/TTL. The Sine outputs are pro-
vided on MCX connectors (Johnson Components,
133-3701-133 or equivalent)on the board edge.
Simply connect your 50Ωapplication cable to
appropriate output. The LVCMOS outputs are on
wirepoints near the MCX outputs. The square pad is
the LVCMOS output and the round pad is ground. If
NOVATECH INSTRUMENTS
you are not using the LVCMOS/TTL output, it is
suggested that it be disabled by sending the “A D”
(default is disabled) command for best system noise
performance.
3.16
Mounting.
Five mounting holes are provided
on the board. These holes are electrically connected
to circuit common and may be used for shield con-
nections. Clearance is provided for up to 3mm diam-
eter screws. Please allow at least 3 mm clearance on
the bottom side when mounting to a conductive
chassis or case. Refer to Table 3 and Figure 1 for
locations.
NOTE:
The DDS9m is cooled by convection. Verify that
there is adequate free air flow around the board
when mounting in an enclosure. Approximately 2
Watts are dissipated.
4.0
Operation
4.1
Power on reset.
After power is applied, the
DDS9m takes approximately 500ms to initialize.
Commands sent during this time will be ignored or
may cause erroneous operation.
4.2 Specifications are met within 15 minutes of
power-up in stable environment.
4.3 After the DDS9m has been installed in the cus-
tomer application system, all that is required for
operation is to send the appropriate serial commands
per Table 2.
4.4 The user host computer software must properly
format the serial commands. Incorrect formatting
will result in an error code being returned. See Table
1 for a list of error codes.
4.5 For maximum interface speed, it is suggested
that Echoing be disabled by the “E d” command.
This will allow the host to send characters at a faster
rate. Note that no flow control is provided. Depend-
ing upon your host, the DDS9m may not be able to
keep up with serial characters. The DDS9m will
respond with an “OK” for a correctly received data
command. You will have to verify correct operation
at your host rate.

8
DDS9m Manual
4.6 A special baud rate command is available if you
wish to set a different baud rate. The value set by
this command is volatile and not saved in EEPROM.
Upon power up, reset or clear, the DDS9m defaults
to 19.2kBaud.
Kb 78 ;9.6kBaud
Kb 3c ;19.2kBaud
Kb 1e ;38.4kBaud
Kb 14 ;57.6kBaud
Kb 0a ;115.2kBaud
NOTE:
A jumper is provided to select 115.2kBaud as the
default Baud Rate. Refer to Figure 1 for location.
When the 2mm jumper is moved so the header pins
are open, 115kBaud is selected. It is suggested that
the jumper be left on a free pin for future use.
4.7 If you are using an external clock, the value sent
to the DDS9m in the “Fn” command must be
scaled. The output frequency of the DDS9m when
used with an external clock is given by:
F
out
= (F
command
)*(K
pe
*F
ext clk
)
/
(K
pi
*F
int clk
)
Where Kpe is the value of Kp set by the cus-
tomer, and Kpi is the internal default Kp (0x0f).
4.8 The nominal Internal Clock has a value of
28,633,115.306666667Hz. Best performance is
obtained when the External Clock input frequency
times the Reference PLL multiplier (Kp) is close to
the default value (429.4967296MHz, max:
500MHz), as the on-board low-pass filters are opti-
mized for that range.
4.9 For an example of scaling, suppose an external
clock of 10.000MHz is used and an output of
1.544MHz is desired, with Kpe=Kpi=15:
F
command
= (1.544)*(15*28,633,115.306666667)
/
(15*10,000,000)
= 4.4209530
4.10 The command then sent to the DDS9m for the
1.544MHz output, with a 10MHz external clock,
will be (assuming Kp is unchanged):
NOVATECH INSTRUMENTS
Fn 4.4209530
where ‘n’ is your selected channel
NOTE:
You must account for your clock frequency error and
calculation roundoff when using an external clock.
4.11 Beginning with Software Revision 2.1, it is
possible to control the internal range bit on the DDS
ASIC.
4.12 For normal operation the Kp command is
unmodified. However, if it is desired that the clock
multiplier gain bit be set HIGH (for Kp*[Ext Clk
Freq] from 255 and 500 MHz), add hexadecimal
0x80 to the Kp value to be set. For the bit to be
forced LOW (100 to 160 MHz), add hexadecimal
0x40 to the Kp value to be set.
4.13 Since the resolution of the DDS9m is 32-bits,
the typical fractional frequency error (∆
f/f)
for out-
put frequencies in the MHz range will be less than
0.1ppm, even when exact values are not possible.
NOTE:
The “B”command can be used to test AD9959 DDS
chip programming as it allows access to all internal
registers. While not a real-time simulation, each
“B”
command functions as an input by putting a
data byte directly into the AD9959 via an SPI port,
and then pulses the IOUD line. This is similar to a
procedure that a customer control circuit might
perform. The “B” command values are not saved in
RAM, so they will not show in the “QUE” command
output nor can they be saved in EEPROM. Consult
the Analog Devices AD9959 data sheet for detailed
information regarding the internal AD9959 register
functions.
Typical
∆
f/f for External Clock of 10.0MHz
Kp
Desired
Fout
Command
∆
f/f
15 1.544MHz Fn 4.4209530 2.19x10-8
20 1.544MHz Fn 3.3157148 1.43x10-8
15 2.048MHz Fn 5.8640620 1.45x10-8
20 2.048MHz Fn 4.3980465 2.02x10-8

NOVATECH INSTRUMENTS
9
DDS9m Manual
POWER
LOGIC
32-Bit
DDS,
LP Filter,x4 AMP,x4 Sine
OUT
Buffer,x4 LVCMOS
OUT
POWER
FILTERS &
+5V
-5V
Master
Clock
EXT
CLK
IN
CLK SEL
Figure 3.
Simplified System Block Diagram
DDS9m Module
RS232
µ
C
System Control
+1.8V
REGULATOR
Voltage
Control
AD9959
+3.3V
+3.3V
“Que” command output (all values are hexadecimal) values:
05F5E100 0000 0000 03FF 00000000 00000000 000301
05F5E100 0000 0000 03FF 00000000 00000000 000301
05F5E100 0000 0000 03FF 00000000 00000000 000301
05F5E100 0000 0000 03FF 00000000 00000000 000301
80 BC0000 0000 6102 21
Description:
Line 1:
“05F5E100”,
frequency in 0.1Hz steps per LSB;
“0000”
, phase setting;
“03FF”
, amplitude setting
(default is scaling off);
“0000”
, linear ramp rate;
“00000000”
, rising delta frequency;
“00000000”
, falling
delta frequency,
“000301”
, channel function register.
The last line gives the status of AD9959 registers and internal software registers:
“80”
, channel select register
(CSR);
“BC0000”
, function register 1 (FR1);
“0000”
, function register 2 (FR2); “
6102”
, internal
µ
C control
registers;
“21”
, software revision as x.y, Rev 2.1 in this example. Consult the Analog Devices AD9959 data sheet
for meaning of registers. Each line is terminated by a carriage return/line feed (CRLF) pair.

10
DDS9m Manual
4.14 Phase relationships are maintained by appro-
priate use of the “M” and “I” commands. The “M”
command has special modes “M a” and “M n”.
“M a” means automatically clear phase at the end
of each command. This will clear the phase register
each time any command is performed. This is
important when all outputs must be phase aligned.
However, it may cause a phase discontinuity in the
output.
4.15 The “M n” command turns off the automatic
clearing of the phase register. This is the default
mode. In this mode, the phase register is left intact
when a command is performed. Use this mode if you
want frequency changes to remain phase synchro-
nous, with no phase discontinuities.
4.16 Further control of phase relationships and tim-
ing of command execution can be exercised by
using the “I m”, “I a” and “I p” commands.
The default mode is “I a” in which a command is
parsed and executed immediately following the end
of the serial input sequence. In the “I m” mode, an
update pulse will not be sent to the DDS chip until
an “I p” command is sent. This is useful when it is
important to change all the outputs to new values
simultaneously.
4.17 For applications which require precise ampli-
tude matching between the channels, the recom-
mended method is to use the “Vn N” command to
adjust the channels to match the other. This com-
mand provides 10-bits of adjustment range.
4.18 High Speed Interface Operation. When the
high speed interface (P1) mode is chosen, the opera-
tion of the DDS9m is completely dependent upon
the user supplied interface circuitry. The on-board
microprocessor and software are disabled in parallel
operation. Therefore, no error conditions are
detected or reported.
NOTE:
The AD9959 pins MASTER_RESET,
PWR_DWN_CTL, CS* are set by the on-board
microcomputer at power-up and are not accessible
on the high speed interface. The table mode or table
RAM isnot accessible from the high speed interface.
NOVATECH INSTRUMENTS
4.19 The on-board Voltage Controlled Temperature
Compensated Crystal Oscillator (VCTCXO) can be
adjusted approximately +/-5ppm from nominal by
applying a 0 to 5Volt signal on P5. Your voltage con-
trol must be capable of sourcing and sinking 0.5mA.
Nominal voltage is approximately 2.5 Volts. This
feature is useful for applications which require
Phase Locking to external sources, using customer
supplied circuitry.
4.20
Other Modes
. The DDS9m can be pro-
grammed by using the “B” command to perform
many other outputs. The “B” command can be used
to gain control over the on-board AD9959 DDS
ASIC. Refer to the Analog Device data sheet for
detailed information when using the “B” command.
5.0
Theory of Operation
5.1 Please refer to the simplified System Block Dia-
gram in Figure 3 for the following discussion.
5.2 At every cycle of the DDS9m master clock, the
32-bit DDS integrated circuit increments the phase
of an internal register by a value determined by the
frequency setting loaded into the on-chip registers.
This digital phase value is converted on-chip to a
sinusoidal amplitude level and delivered to on-chip
10-bit digital-to-analog converters. The analog sig-
nals from these converters are filtered by differential
7th-order elliptical low pass filters, amplified and
sent to the MCX receptacles.
5.3 The frequency generated by the DDS IC is
determined by the 32-bit frequency word loaded into
the frequency register on the DDS9m. The output
frequency is given by:
F
out
= F
setting
*Kp*F
clock
/2
32
Hz
Where: Fclock = 28,633,115.306666667 Hz (int.)
Fsetting = Binary value in DDS IC.
(Fsetting ranges from 0 to 231-1)
Kp = PLL Multiplier (1 or 4 to 20)
This reduces to:
F
out
= F
setting
MHz

11
DDS9m Manual
for the internal (default) clock and the default PLL
Multiplier (Kp=15) settings.
5.4 Since the DDS IC is a sampled data system, the
output frequency is limited to a maximum of 1/2 the
system clock frequency (Fsetting<=231-1). While it is
possible to generate an output near 50% of the clock,
the distortion may be unacceptable. Therefore, the
output is limited to approximately 40% of the sys-
tem clock and steep output filters are provided on
board: in this case 7th-order elliptical low pass fil-
ters.
5.5 If you are using an external clock and a Kp
which give a clock substantially lower than the
429.497MHz default internal clock, you may need
to filter the Outputs to obtain acceptable distortion
for your application. For best performance, set the
corner frequency at 40% or less of your external
clock frequency times Kp. The lower your filter as a
percentage of your clock frequency, the lower the
distortion.
NOTE:
Since filtering occurs before the signal is level
shifted to LVCMOS, the LVCMOS outputs may be
erratic or distorted when using low clock
frequencies. If you require an LVCMOS level signal
when using low clock frequencies, it is
recommended that you use an external comparator
or level shifter connected to the output of your
external filter.
5.6 For example, if you are using a 10MHz external
clock, with the default reference multiplier (Kp) of
15, then the internal clock is 150MHz. An optimal
filter for this frequency would then be approxi-
mately 60MHz (40% of 150MHz).
NOTE:
Per the Analog Devices AD9959 data sheet, your
value of Kp times your selected clock frequency must
not be between 160MHz and 255MHz. For the
internal clock, values of Kp from 5 to 9 should not
be used. You may also need to set the “VCO gain
control” bit in register FR1 as indicated by the
AD9959 data sheet. See paragraph 4.12.
NOVATECH INSTRUMENTS
6.0
PERFORMANCE TEST
6.1 Install the DDS9m as directed in the Serial
Operation part of Section 3. Connect your host con-
troller and operate the DDS9m per Section 4. The
test limits assume a stable environment of 18-28oC.
NOTE:
Allow the DDS9m to warm up for at least 15 minutes
before performing any measurements. For best
results, the DDS9m should be verified in its installed
environment.
6.2 See Table 3 for a list of recommended test
equipment to perform the following measurements.
6.3
Verify Frequency Accuracy.
To verify the fre-
quency of the DDS9m, set the output sequentially to
each value in Table 4, with the clock source set to
internal. Connect the recommended frequency
counter set to 50Ωtermination and 0.1Hz resolution.
Verify the limits show in Table 4. Test all channels
to verify functionality of all outputs. If you do not
use an external reference for the frequency counter,
be sure to add the error of your counter to the toler-
ance. (LSD =
L
east
S
ignificant
D
igit on counter).
Table 3: Recommended Test Equipment
Item
Minimum
Specification
Recommended
Oscilloscope 300MHz, 50ΩTektronix
TDS3032B
50ΩTermination 50Ω, ±1% Tektronix
011-0049-01
Frequency
Counter 180MHz HP53132A
Counter Time
Base 10MHz,
<±0.1ppm Novatech
Instruments
Model 2960AR
External Clock 400MHz Novatech
Instruments
Model 440A
Table 4: Frequency Test Points
Frequency
Tolerance
100 kHz ±0.15 Hz ±1 LSD
1 MHz ±1.5 Hz ±1 LSD
10 MHz ±15 Hz ±1 LSD

12
DDS9m Manual
6.4 Sine Out Amplitude Verification. Set the fre-
quency of the DDS9m to 10MHz. Connect the
DDS9m to the oscilloscope set for 50Ωtermination.
Set the oscilloscope to measure to amplitude using
at least 16 averages. Verify a reading of 1Vpp
±0.25Vpp. Repeat for the other outputs.
6.5 Level Command Test. Leave the output fre-
quency set to 10MHz. Send the commands “Vn
512” to each channel, where ‘n’ is your selected
channel number. Verify that the amplitude on each
channel decreases by one-half. Send the “R” com-
mand to reset the levels before performing the next
tests.
6.6 Output Flatness Verification. Verify that the
outputs are flat with frequency by performing the
following test: Connect the DDS9m to the oscillo-
scope set for 50Ωtermination. Use the same settings
as Sine Out Amplitude Verification. Note the volt-
age reading.
6.7 Set the DDS9m to the values of Table 4. Verify
that the oscilloscope amplitude reading remains
within ±3dB (1.414 to 0.707) of the value noted in
the previous paragraph. (limit upper frequency
to150MHz)
6.8 Repeat the output flatness verification test for
each output.
6.9 External Clock Input Verification. Set the fre-
quency output to 10.000MHz by sending the com-
mand “F0 10.7374182” (scaled per section
4.0). Connect a 400MHz external clock source via a
short coaxial cable to the external clock MCX. Send
the command “Kp 01”. Send the command “C
e” to select the external clock input.
6.10 Verify an output of 10.0000000MHz, ±0.1Hz.
You must account for any frequency errors in your
external clock source.
NOVATECH INSTRUMENTS
6.11 Return the DDS9m to normal operation and
default values by sending the “CLR” command.
6.12 This concludes the verification test of the
DDS9m.
7.0
CALIBRATION
7.1 The DDS9m has two adjustable components:
Y2, frequency, and R22, output amplitude. Calibra-
tion should be performed only if the DDS9m fails
the performance test or if the unit has been repaired.
Routine adjustments are not recommended nor gen-
erally required. This procedure assumes that the
DDS9m has failed the performance test or has been
repaired.
7.2 Before proceeding with calibration, send the
‘CLR’ command to set the DDS9m to factory
default values.
WARNING:
Calibration should be performed only by qualified
personnel. The on-board components are static
sensitive.
7.3 The adjustments shown are set to 1/2 the speci-
fication values.
NOTE:
Allow the DDS9m to warm up for at least 15 minutes
before performing any adjustments. For optimum
performance the DDS9m should be calibrated in an
environment similar to its installation.
7.4
Frequency Adjust, Y2.
Set the output of the
DDS9m to 10.0000000MHz using the command
“F0 10.0000000”. Connect output of channel 0
to your frequency counter set for 50Ωtermination.
Adjust Y2 using a non-metallic adjustment tool for
10.000000MHz, ±7.5Hz.
7.5
Amplitude Adjust, R22.
Connect the output of
channel 0 to the oscilloscope set to measure ampli-
tude, with a minimum of 16 averages. Set for 50Ω
termination. Set the output to 35MHz by sending the
command “F0 35.0000000”. Adjust R22 for
1.00Vpp ±0.05Vpp. This completes the calibration
of the Model DDS9m.
30 MHz ±45 Hz ±1 LSD
50 MHz ±75 Hz ±1 LSD
100 MHz ±150 Hz ±1 LSD
170 MHz ±255 Hz ±1 LSD
Table 4: Frequency Test Points
Frequency
Tolerance

13
DDS9m Manual
8.0
Appendix A. Table Mode Details.
8.1 The Model DDS9m contains on-board static
RAM capable of storing up to 32,768 profile points.
Each point contains phase, frequency, amplitude and
dwell time information. The on-board microcom-
puter reads this RAM and programs the DDS ASIC
per the profile point data. The profile can be set to
loop continuously or to hold at the last point, until
interrupted by a subsequent command.
NOTE:
Channels 0 and 1 can be set with the table mode.
8.2 The table mode is toggled on and off by an ‘M
t’ command from the serial port and executes cus-
tomer provided profile points. ‘M 0’ always turns
off the table and returns to single tone mode. The
DDS9m starts execution of the profile immediately
upon a receipt of ‘M t’ following an ‘M 0’.
8.3 The command sequence (
bold
) is of this form
(comments after the ‘;’ are not sent to the DDS9m,
but are here for explanation purposes):
M 0 ;turns off running table mode
t0 0000 aabbccdd,eeff,gghh,ii
;F0 profile point 0, on output 0
t1 0000 aabbccdd,eeff,gghh,ii
;F1 profile point 0, on output 1
t0 0001 aabbccdd,eeff,gghh,ii
;F0 profile point 1
t1 0001 aabbccdd,eeff,gghh,ii
;F1 profile point 1
...
t0 3fff aabbccdd,eeff,gghh,ii
;F0 profile point 0x3fff
t1 3fff aabbccdd,eeff,gghh,ii
;F1 profile point 0x3fff
M t ;begin execution of table
;‘0000’ two byte RAM address, T0 and T1 must
be paired with same address
;‘aabbccdd’ four bytes frequency,hexadecimal,
MSB first, 4 bytes. 0.1Hz resolution on LSB
;‘eeff’ phase offset, hexadecimal, MSB first,
NOVATECH INSTRUMENTS
only 14-bits active, top two bits are ignored
;‘gghh’ amplitude scale, MSB first, only 10-bits
active. Amplitude is scaled per above.
;‘ii’ dwell time, MSB first, in increments of
100µs. 0x00=loop back to start, 0xff=hold present
setting. Each T0-T1 pair must have the same dwell.
8.4 The ‘,’ (comma) in each record is used as a
delimiter and must be included as shown. The inputs
are not case sensitive. Subsequent ‘M t’ com-
mands will toggle the execution of the table on and
off. Upon execution of the table, the output will
always begin with address 0000 and progress until it
encounters an 0xff or 0x00 in a dwell position. The
last record in a table mode will be executed for
100µs if the dwell is set to 00.
NOTE:
Each record must be terminated with an 0x00 or 0xff
in the dwell position to indicate the end of your data.
8.5 The current values stored in RAM can be read
back by the “Dn aaaa” command. N=0 or 1 and
“aaaa” is the address.
8.6 The RAM table is backed-up by a “supercap”
for a minimum of 10 minutes. This allows for short
power interrupts without losing the table informa-
tion. A battery holder, with the appropriate connec-
tor, for two AA (LR-6) cells is provided with the
DDS9m. These cells will retain the RAM for
approximately one year with no power applied.

NOVATECH INSTRUMENTS
14
DDS9m Manual
WARRANTY
NOVATECH INSTRUMENTS warrants that all instruments it manufactures are free from defects in
material and workmanship and agrees to replace or repair any instrument found defective during a
period of one year from date of shipment to original purchaser.
This warranty is limited to replacing or repairing defective instruments that have been returned by
purchaser, at the purchaser's expense, to NOVATECH INSTRUMENTS and that have not been
subjected to misuse, neglect, improper installation, repair alteration or accident. NOVATECH
INSTRUMENTS shall have the sole right to final determination regarding the existence and cause of a
defect.
This warranty is in lieu of any other warranty, either expressed or implied, including but not limited to
any warranty of merchantability or fitness for a particular purpose. In no event shall seller be liable for
collateral or consequential damages. Some states do not allow limitations or exclusion of consequential
damages so this limitation may not apply to you.
All instruments manufactured by NOVATECH INSTRUMENTS should be inspected as soon as they
are received by the purchaser. If an instrument is damaged in shipment the purchaser should
immediately file a claim with the transportation company. Any instrument returned to NOVATECH
INSTRUMENTS should be shipped in its original shipping container or other rigid container and
supported with adequate shock absorbing material.
This warranty constitutes the full understanding between NOVATECH INSTRUMENTS and the
purchaser and no agreement extending or modifying it will be binding on NOVATECH
INSTRUMENTS unless made in writing and signed by an authorized official of NOVATECH
INSTRUMENTS
NOVATECH INSTRUMENTS
United States of America
VOICE: 206.301.8986
http://www.novatechsales.com
sales@novatechsales.com
Popular Control Unit manuals by other brands
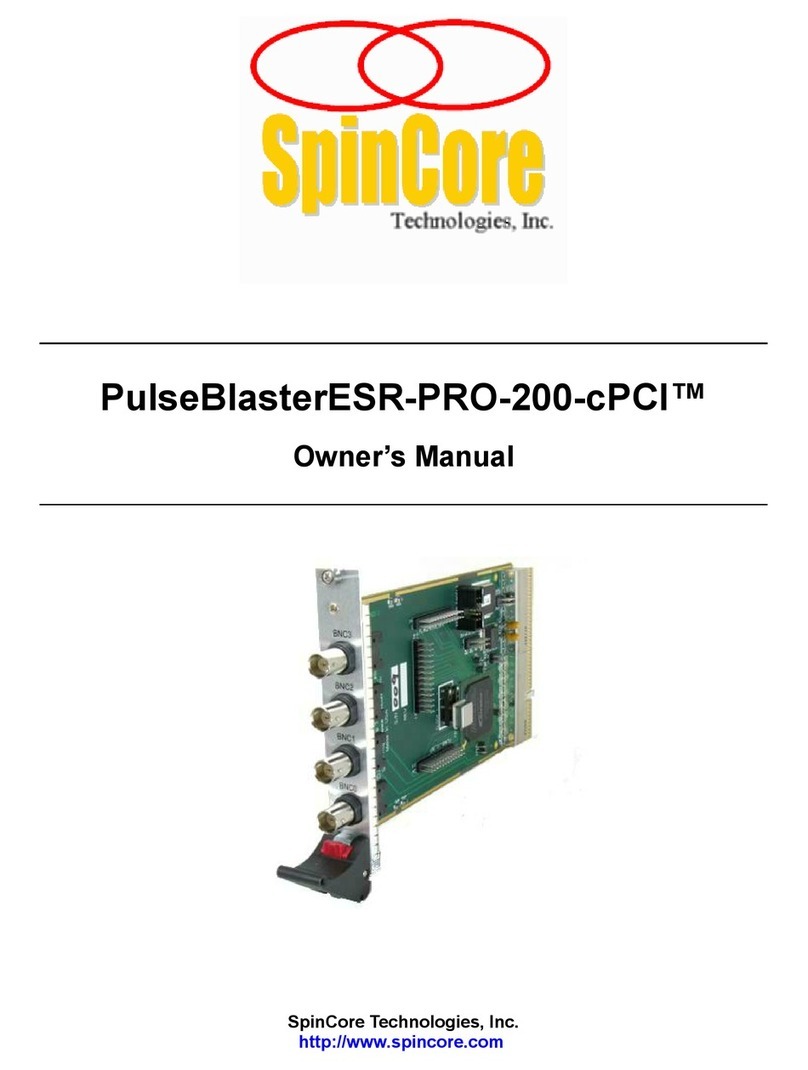
SpinCore Technologies
SpinCore Technologies PulseBlasterESR-PRO-200-cPCI owner's manual
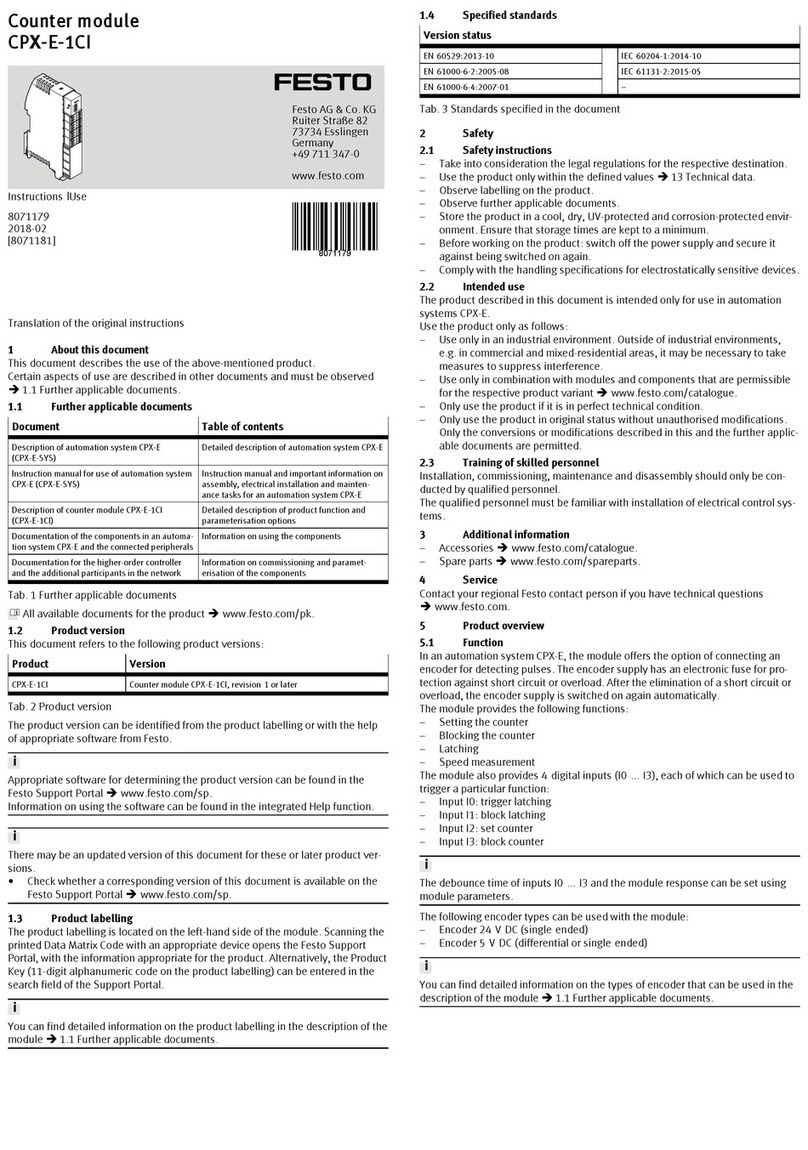
Festo
Festo CPX-E-1CI Instructions for use
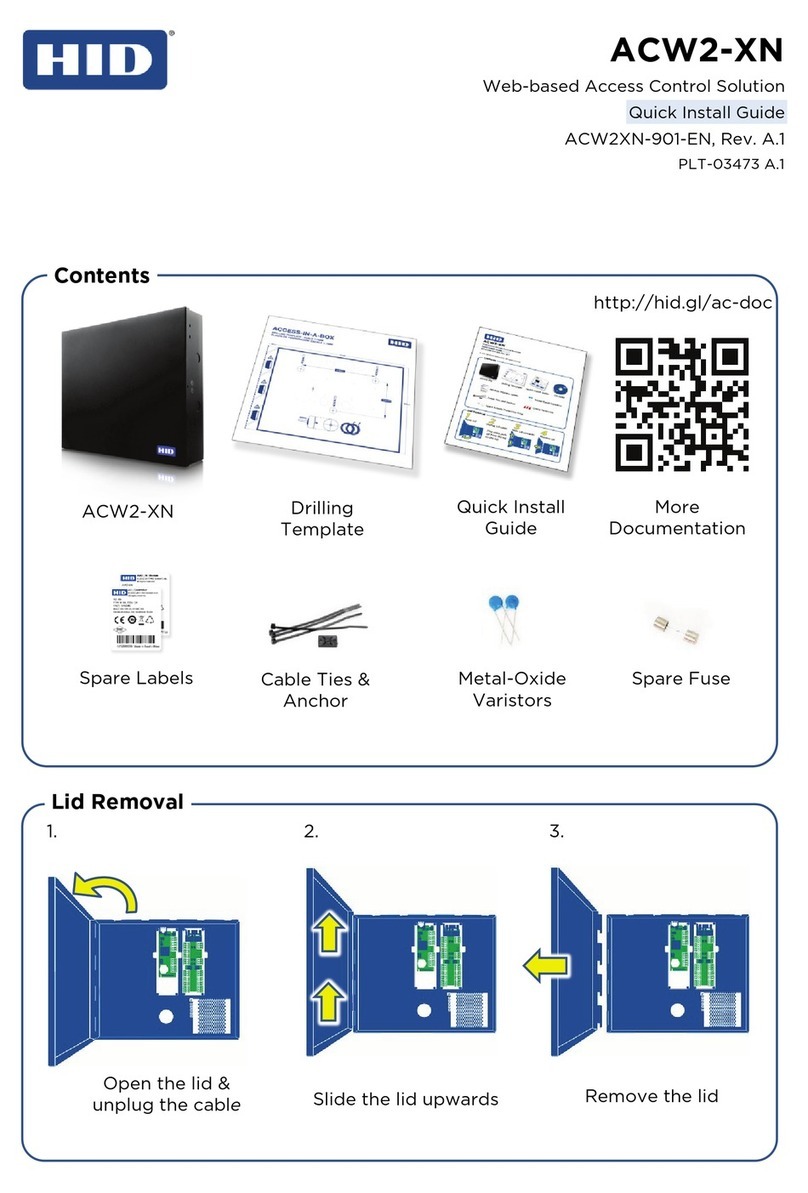
HID
HID ACW2-XN Quick install guide

Honeywell
Honeywell ControlEdge 900 platform user guide
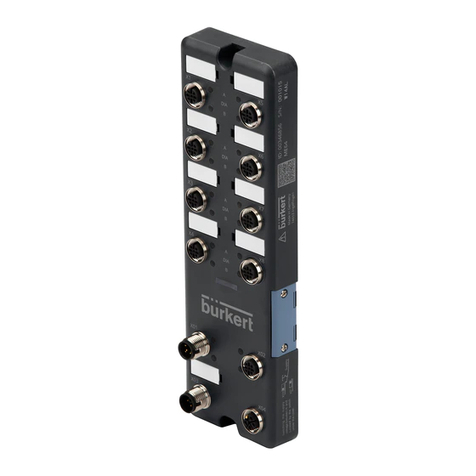
Burkert
Burkert FieldConnect ME64 operating instructions
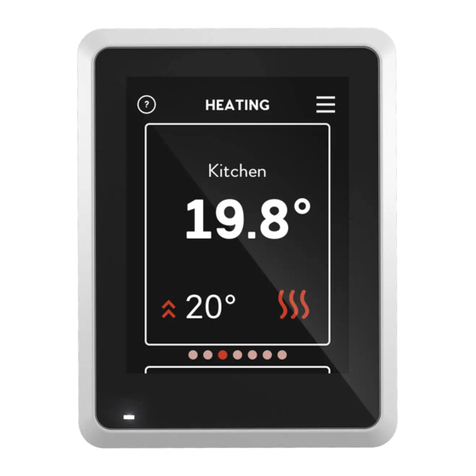
Nibe
Nibe RMU S40 Installer manual