NPK GH Series User manual

HYDRAULIC HAMMER
SERVICE MANUAL
GH SERIES HAMMERS
GH06 GH3
GH07 GH4
GH1 GH6
GH2/GHS2
7550 Independence Drive
Walton Hills, OH 44146-5541
Phone (440) 232-7900
Toll-free (800) 225-4379
Fax (440) 232-6294
© Copyright 2009 NPK Construction Equipment, Inc. www.npkce.com H055-9640A.doc 03/09
“Use Genuine NPK Parts”

- 1-
SAFETY
Safety notices in NPK Instruction Manuals follow ISO and ANSI standards for
safety warnings:
DANGER (red) notices indicate an imminently hazardous situation
which, if not avoided, will result in death or serious injury.
WARNING (orange) notices indicate a potentially hazardous
situation which, if not avoided, could result in death or serious
injury.
CAUTION (yellow) notices indicate a potentially hazardous
situation, which, if not avoided, may result in minor or moderate
injury.
ATTENTION (blue) notices in NPK Instruction Manuals are an NPK
standard to alert the reader to situations which, if not avoided,
could result in equipment damage.
WARNING and BASIC OPERATING INSTRUCTIONS decals are included with each
NPK hammer and installation kit. Decals must be installed in the cab, visible to the
operator while operating the hammer.
STAY CLEAR, PRESSURE VESSEL, GAS PRESSURE and TOOL SHARPENING
decals are installed on all NPK hammer models. Keep them clean and visible. NPK will
provide decals free of charge as needed.
1. Operator and Service personnel must read and understand the NPK INSTRUCTION
MANUAL to prevent serious or fatal injury.
2. FLYING DEBRIS CAN CAUSE SERIOUS OR FATAL
INJURY.
•Keep personnel and bystanders clear of hammer
while in operation.
•Do not operate HAMMER without an impact
resistant guard between the HAMMER and
operator. NPK recommends LEXAN®or equivalent
material, or steel mesh. Some carrier
manufacturers offer demolition guards for their
machine. Check with the carrier manufacturer for
availability. If not available, please call NPK.
3. Do not hardface or sharpen the tool point with a cutting
torch. Excessive heat from torching or welding can cause embrittlement, breakage,
and flying pieces. Resharpen by milling or grinding only, using sufficient coolant.
ATTENTION

- 2-
SAFETY
4. Fully extend the tool while charging the HAMMER with nitrogen gas. Be sure that
the retaining pin is installed. STAY CLEAR OF TOOL POINT WHILE CHARGING.
5. Do not disassemble a HAMMER before discharging the hammer gas pre-charge.
6. USE NITROGEN GAS ONLY! Store and handle nitrogen tanks per OSHA
regulations.
7. Avoid high pressure fluids. Escaping fluid under pressure can penetrate the skin
causing serious injury. Relieve pressure before disconnecting hydraulic or other
lines.
8. Operate HAMMER from operator’s seat only.
9. Match HAMMER size to carrier according to NPK recommendations, see page 7.
The carrier must be stable during hammer operation and during transport.
10.Do not make any alterations to the TOOL without authorization from NPK
Engineering.
11.Use proper lifting equipment and tools when handling or servicing the HAMMER.
12.Wear ear protection if conditions warrant. Consult OSHA regulations.
13.Wear safety glasses at all times. Beware of flying debris.
14.If modifications are to be made, do not alter the HAMMER without authorization
from NPK Engineering!
15.Use only genuine NPK replacement parts. NPK specifically disclaims any
responsibility for any damage or injury that results from the use of any tool or parts
not sold or approved by NPK.
For further safety information, consult the AEM Hydraulic Mounted Breakers Safety
Manual, AEM form MB-140 (NPK P/N H050-9600), which is furnished with every NPK
hammer. To request an additional copy, please contact NPK at 800-225-4379 or
Internet at www.npkce.com.

- 3-
CONTENTS
SAFETY..................................................................................................................1
INTRODUCTION.....................................................................................................5
BASIC OPERATING INSTRUCTIONS....................................................................5
PRECAUTIONS FOR USING THE NPK HYDRAULIC HAMMER ..........................6
CARRIER MACHINE COMPATIBILITY ..................................................................7
HAMMER SPECIFICATIONS .................................................................................8
STRUCTURE..........................................................................................................9
HAMMER SERIAL NUMBER LOCATION...............................................................11
PRINCIPLE OF OPERATION .................................................................................12
HYDRAULIC INSTALLATION.................................................................................13
MOUNTING INSTALLATION..................................................................................17
ROUTINE INSPECTION AND MAINTENANCE......................................................18
WEEKLY INSPECTION ..........................................................................................19
CHANGING THE TOOL..........................................................................................20
TROUBLESHOOTING............................................................................................22
CHECKING THE HYDRAULIC PRESSURES ........................................................23
CHECKING THE HYDRAULIC FLOW TO THE HAMMER.....................................24
OIL LEAKAGE.........................................................................................................26
GAS LEAKAGE.......................................................................................................27
EXCESS OIL IN THE GAS HEAD INSPECTION PROCEDURE............................28
NITROGEN GAS PRESSURE................................................................................29
GAS CHARGING KIT..............................................................................................29
CHECKING THE GAS PRESSURE........................................................................30
GAS CHARGING THE HAMMER ...........................................................................32
REMOVAL AND MOUNTING OF HYDRAULIC HAMMER.....................................33
TOOLS REQUIRED FOR DISASSEMBLY .............................................................34
NPK START-UP KIT ...............................................................................................35
NPK ASSEMBLY LUBRICANT ...............................................................................36
DISASSEMBLY PROCEDURE...............................................................................37
DISCHARGING GAS PRESSURE..........................................................................38
DISASSEMBLING THE MAIN BODY......................................................................40
DISASSEMBLY OF MAIN VALVE ..........................................................................46
INSPECTION AND REPAIR AFTER DISASSEMBLY.............................................48
REPAIR SECTION INTRODUCTION......................................................................49
REPAIR TOOLS AND EQUIPMENT.......................................................................49
HAMMER SLEEVE AND PISTON RECONDITIONING TOOLS.............................50
MAIN BODY BORE REPAIR...................................................................................52
PISTON ACTIVE SEAL AREA REPAIR..................................................................62
PISTON TO SLEEVE RUNNING CLEARANCES...................................................63
REPAIR THE STRIKING END OF PISTON............................................................64
MAIN BODY SLEEVES...........................................................................................64
REPLACING THE SEALS.......................................................................................65
REASSEMBLY OF THE HAMMER.........................................................................67
STANDARD TOOLS ...............................................................................................83
ACCESSORY TOOLS.............................................................................................83

- 4-
CONTENTS
MAXIMUM TOOL TO TOOL BUSHING CLEARANCE ...........................................84
NPK HYDRAULIC HAMMER IMPACT BUSHINGS................................................86
TOOL INSPECTION................................................................................................87
CHISEL TOOL RESHARPENING...........................................................................88
STANDARD LENGTH FOR NPK TOOLS...............................................................89
RETAINING PIN......................................................................................................90
LUBRICATION........................................................................................................91
AUTOLUBE/UNDERWATER PORT IDENTIFICATION..........................................94
TOOL BUSHING REPLACEMENT .........................................................................95
TOOL HOLDER BUSHING BORE REPAIR............................................................98
TOOL HOLDER ......................................................................................................101
REPLACEMENT OF TIE RODS .............................................................................102
MAXIMUM ELONGATION OF TIE RODS...............................................................104
TORQUE CHART....................................................................................................105
TORQUE VALUES FOR HAMMER FASTENERS..................................................106
MOUNTING PLATE ................................................................................................107
WARRANTY REGISTRATION FOR NEW UNITS ..................................................108
WARRANTY STATEMENT.....................................................................................109
STORAGE OF HYDRAULIC HAMMER..................................................................110
DECIMAL CONVERSION CHART..........................................................................111
REBUILD SPECIFICATIONS CHECK SHEETS.....................................................112
NOTES....................................................................................................................119
SERVICE RECORD................................................................................................119

- 5-
INTRODUCTION
NPK is a leading manufacturer of boom mounted HYDRAULIC HAMMERS, and has
the most complete product line available anywhere. The success of NPK is due to
our commitment to quality, dependability and long life. The HYDRAULIC HAMMER
has many unique designed features and it is a company philosophy that the NPK
HYDRAULIC HAMMER can be brought to "like new” condition long after competitive
products are scrapped. You can feel confident that you have purchased the best
value available.
This comprehensive instruction manual contains instructions for repairing and
maintaining NPK HYDRAULIC HAMMERS. This manual includes helpful
information for obtaining the full potential and efficiency from NPK HYDRAULIC
HAMMERS. Please read this manual thoroughly to understand the NPK HAMMER
and its operating principles before using it.
For additional information or help with any problem encountered, please contact
your NPK authorized dealer.
Whenever repair or replacement of component parts is required, only NPK parts
should be used. NPK is not responsible for failures resulting from substitution of
parts not sold or approved by NPK.
BASIC OPERATING INSTRUCTIONS
•READ OPERATORS MANUAL
Do not pry with tool.
Apply down force perpendicular to work surface.
Avoid blank hammering.
Do not hammer continuously in the same position for more
than 30 seconds.
•Important:
It is imperative that grease is maintained in the tool bushing
contact area at all times. This may require hourly greasing
depending on job conditions.
Important:
The hammer must be in a vertical position with downforce
applied to push the tool all the way in. This prevents
grease from entering piston impact area.
USE A GOOD QUALITY, HIGH TEMPERATURE EP#2 GREASE CONTAINING
ANTIWEAR ADDITIVES.
If machine is equipped with an AUTOLUBE System, check grease reservoir
daily.
•PERFORM VISUAL INSPECTIONS DAILY
Do not operate with loose or missing fasteners, tie rods, etc.
•MAINTAIN A CLEAN HYDRAULIC SYSTEM
Keep hoses clean and capped when dismounting or storing hammer.
Change oil and filters as recommended by carrier manufacturer.
•DO NOT SUBMERGE HAMMER UNDERWATER
Unless modified for underwater operation.

- 6-
PRECAUTIONS FOR USING THE NPK
HYDRAULIC HAMMER
•Perform daily inspections.
•Avoid blank hammering.
•Do not hammer continuously in the same position for more than 30 seconds.
•Do not use the hammer to move material, pry material, or as a pick on material.
•Do not use the hammer underwater unless the hammer has been modified for
underwater operation.
•Prevent contamination from entering the hydraulic hoses when mounting or
dismounting the hammer from the carrier.
•Maintain a clean hydraulic system. Replace the filter element with a new one
and change hydraulic oil at specified intervals.
•Operate the hammer carefully. Do not hit the boom of the carrier with the
hammer.
•Operate the hammer in a safe manor. Read the NPK Hydraulic Hammer
Operators Manual.
If additional safety information is needed, consult the AEM Hydraulic Mounted Safety
Manual. To request a free copy, please contact NPK at 800-225-4379 or e-mail us at
www.npkce.com.

- 7-
CARRIER MACHINE COMPATIBILITY CHART
These carrier weight ranges are intended as a guideline only. Other factors, such as
stick length, counterweights, undercarriage, etc., must be taken into consideration.
Mounting a HAMMER that is too heavy for the carrier machine
can be dangerous and damage the machine. Verify carrier
stability with hammer before transport or operation.
Mounting a HAMMER that is too small for the carrier machine can damage the
HAMMER, cause tool breakage and void Warranties. Please consult NPK
Engineering for specific detailed information.
CARRIER WEIGHT lbs. (kg)
HAMMER MOUNTING RECOMMENDED RANGE
MODEL STYLE lb kg
GH06 Excavator 2,200 - 4,400 1,000 - 2,000
Skid Steer 2,400 - 3,500 1,100 - 1,600
GH07 Excavator 2,800 - 5,500 1,300 - 2,500
Skid Steer 3,000 - 5,500 1,350 - 2,500
GH1 Excavator 5,400 - 9,000 2,450 - 4,100
Skid Steer 5,000 - 7,500 2,300 - 3,400
GH2/GHS2 Excavator 6,600 - 12,000 3,000 - 5,500
Skid Steer 6,000 - 9,000 2,700 - 4,100
GH3 Excavator 8,800 - 15,000 4,000 - 7,000
Skid Steer 8,000 - 14,000 3,600 - 6,400
GH4 Excavator 13,000 - 22,000 6,000 - 10,000
GH6 Excavator 22,000 - 31,000 10,000 - 14,000
*Specifications are subject to change without notice.

- 8-
HAMMER SPECIFICATIONS
IMPACT TOOL
ENERGY DIA WORKING
HAMMER
MODEL CLASS
FREQUENCY WORKING
WEIGHT MOUNTING
STYLE LENGTH
ft lb bpm lbs (Kg) in (mm) in (mm)
GH06 150 480 – 1200 500 (225) Skid Steer 1.7 (42) 12.2 (311)
235 (107) Excavator
GH07 200 500 – 1200 550 (250) Skid Steer 1.9 (47) 13.1 (333)
270 (125) Excavator
GH1 350 550 – 1100 750 (340) Skid Steer 2.2 (57) 13.6 (346)
450 (205) Excavator
GH2/GHS2 500 500 – 1300 800 (365) Skid Steer 2.6 (66) 14.4 (367)
525 (240) Excavator
GH3 750 500 – 1150 1075 (490) Skid Steer 3.0 (76) 16.1 (408)
800 (365) Excavator
GH4 1300 400 – 1050 1250 (570) Excavator 3.4 (86) 18.0 (458)
GH6 2000 500 – 800 2150 (980) Excavator 4.2 (106) 20.0 (500)
GAS CHARGE
PRESSURE 5
OIL FLOW
HYDRAULIC
OPERATING
PRESSURE 1
CIRCUIT
RELIEF
minimum 2Cold 3Hot
4
HAMMER
MODEL
gpm (L/min) psi (bar) psi (bar) psi (bar) psi (bar)
GH06 2.5 – 7 (10 - 25) 1650 (115) 2150 (150) 350 (24) 405 (28)
GH07 4 – 9 (15 - 35) 1500 (105) 2000 (140) 350 (24) 405 (28)
GH1 7 – 13 (25 - 50) 1750 (120) 2250 (155) 350 (24) 405 (28)
GH2/GHS2 7 – 17 (25 - 65) 2250 (160) 2750 (190) 350 (24) 405 (28)
GH3 12 – 26 (45 - 100) 1900 (130) 2400 (165) 350 (24) 405 (28)
GH4 13 – 32 (50 - 120) 2200 (150) 2700 (185) 375 (26) 435 (30)
GH6 24 – 40 (90 - 150) 2400 (165) 2900 (200) 390 (27) 450 (31)
*Specifications are subject to change without notice.
NOTES:
1. Hydraulic operating pressure maximum is inlet pressure at the hammer with the oil
at operating temperature and with the gas charge set at the hot operating pressure.
See CHECKING THE HYDRAULIC PRESSURES section in this manual.
2. Circuit relief pressure is at least 500 psi (35 bar) above hammer operating pressure.
3. Cold gas charge is the initial set with the hammer at ambient temperature.
4. Hot gas charge is checked after 1 to 2 hours of running and with a system oil
temperature of 140°to 180°F (60°to 80°C). This is the preferred check.
5. Pressures listed are maximum. Use tolerance of minus 25 psi (2 bar).

- 9-
STRUCTURE
STRUCTURAL DRAWING
MODELS GH06 – GH3
A MAIN BODY
B DRAIN PLUG
C TOOL HOLDER
D RETAINING PIN
E RETAINING RING
F UPPER TOOL BUSHING (GH3 ONLY)
G LOWER TOOL BUSHING
J SPACER SECTION
L GAS HEAD
M CHARGE VALVE
N PISTON
P MAIN BODY SLEEVE (B)
R TOP NUT
U WASHER
V BOTTOM NUT
W VALVE BODY
Y VALVE BOTTOM CAP
Z VALVE SPOOL
AA PLUNGER BUSHING
BB PLUNGER
DD SWIVEL ELBOW
HH TOOL
30 GREASE FITTING

- 10 -
STRUCTURE
STRUCTURAL DRAWING
MODELS GH4 – GH6
A MAIN BODY
B DRAIN PLUG
C TOOL HOLDER
D RETAINING PIN
E RETAINING RING
F IMPACT BUSHING w/ UPPER TOOL BUSHING
G LOWER TOOL BUSHING
J SPACER SECTION
L GAS HEAD
M CHARGE VALVE
N PISTON
O MAIN BODY SLEEVE (A)
P MAIN BODY SLEEVE (B)
R TOP NUT
U WASHER
V BOTTOM NUT
W VALVE BODY
Y VALVE BOTTOM CAP
Z VALVE SPOOL
AA PLUNGER BUSHING
BB PLUNGER
DD SWIVEL ELBOW
HH TOOL
30 GREASE FITTING

- 11 -
HAMMER SERIAL NUMBER LOCATION
SERIAL NUMBER LOCATION (sn1)

- 12 -
PRINCIPLE OF OPERATION
OPEN VALVE
(1) UPSTROKE (2) VALVE SHIFT (3) POWER STROKE (4) IMPACT
N PISTON 33 NITROGEN GAS CHAMBER ABOVE PISTON
Z MAIN VALVE SPOOL 34 UPPER CHAMBER OF PISTON
BB PLUNGER 35 LOWER CHAMBER OF PISTON
HH TOOL 36 CHAMBER OF VALVE SPOOL
5 OUT PORT 37 NITROGEN GAS
6 IN PORT
(1) UPSTROKE OF PISTON
Hydraulic oil supplied by the carrier machine hydraulic pump enters the NPK HAMMER
"IN" port (6) and is directed through port (h1) to the top of the valve plunger, forcing the
main valve spool (Z) to the down position. Oil flows through the main valve spool (Z) to
the lower chamber of the piston (35). The oil pressure acts on the piston (N), raising the
piston up, compressing the nitrogen gas (37). Oil in the upper chamber of the piston (34)
is forced out the return line through port (h2).
(2) VALVE SHIFT
As the piston (N) rises, lower chamber (35) is opened to passage (h3) and oil flows into
the chamber (36) of the main valve spool (Z). Since the area acting on the main valve
spool (Z) in chamber (36) is greater than the area of the plunger (BB), the main valve
spool (Z) shifts up.
(3) POWER STROKE
With the main valve spool (Z) in the up position, chamber (35) is closed off from the "IN"
port (6) and opened to chamber (34) and the return line via passages (h4), (h5), and (h2).
The piston (N) is driven downwards by the compressed nitrogen gas (37) as the oil in
lower chamber (35) re-circulates to upper chamber (34). When the piston (N) opens
passage (h3) to upper chamber (34), the oil in main valve spool chamber (36) is switched
to low pressure and the main valve spool (Z) shifts down.
(4) IMPACT
The piston (N) impacts the tool (HH) and the main valve spool (Z) shifts to the down
position. High pressure oil is directed to the lower chamber of the piston (35) for the start
of another cycle.
AUTOMATIC ENERGY RECYCLING: Extremely hard material will impart greater rebound
energy to the piston (N) after it strikes the tool (HH). This will assist the incoming oil in raising
the piston (N) against the gas pressure in chamber (33). This reduces upstroke time and
therefore increases hammer frequency (beats per minute). The impact force of the hammer
remains the same on each impact.

- 13 -
HYDRAULIC INSTALLATION
NPK INSTALLATION KITS are available for virtually all compatible backhoe loaders,
excavators, and skid steers. Complete parts and instructions for the hydraulic
installation of the NPK HYDRAULIC HAMMER including valving and/or controls, hoses
and fittings, boom and stick tubing, and clamps are provided.
HAMMER KIT LINES
Typically, the pressure line is arranged on the left side of the boom and the return line
on the right side. Flow to the hammer is controlled from an auxiliary valve on the carrier
or from an NPK supplied valve. Hydraulic oil, generally, is routed back to the tank thru
the excavator’s oil cooler and filter.
HAMMER CONTROL VALVE
NPK uses two general types of control systems, depending upon the carrier model:
1. CONTROL SYSTEM USING THE CARRIER AUXILIARY OR SPARE VALVE
SECTION.
This type of installation utilizes an existing carrier valve. Any additional parts, such
as a mechanical linkage, hydraulic pilot actuators, flow control valves, etc. are
furnished in the NPK HYDRAULIC INSTALLATION KIT. Special hydraulic pressure
control valves are not required. The NPK HYDRAULIC HAMMER operating
pressure is self-regulating.
2. CONTROL SYSTEM USING THE NPK MULTIVALVE.
For carriers not equipped with a suitable auxiliary or spare valve section, the NPK
HYDRAULIC INSTALLATION KIT includes a solenoid operated, priority flow control
valve to operate the NPK HYDRAULIC HAMMER. The NPK MULTIVALVE is
specifically designed for the operation of boom mounted attachments.

- 14 -
HYDRAULIC INSTALLATION
PREVENTION OF CONTAMINATION
1. A hydraulic hammer is harder on oil than using a bucket, so the oil is apt to
deteriorate and breakdown sooner. Neglect of the oil system can not only damage
the hydraulic hammer but also cause problems in the carrier which could result in
damaged components. Care should be taken to check for contamination of the oil
and to change it if it is found contaminated. Oil sampling at regular intervals is
highly recommended.
When the hydraulic oil shows low viscosity and bubbles, this indicates that the oil is
deteriorated. If the oil is dark brown and gives off an offensive odor, it is severely
deteriorated. Change the oil immediately!
When the oil is clouded, or the oil filter often becomes clogged, it indicates that the
oil is contaminated. Change the oil immediately!
To change the contaminated hydraulic oil, drain the hydraulic system completely and
clean components. Do not mix new oil with the old.
2. Do not allow any contamination to mix with the oil. Take special care in preventing
contamination from entering the hydraulic system through the hose or tube
connection when changing the hydraulic hammer with the bucket.
3. Low oil level will cause heat build-up, resulting in deterioration of the oil. Also, it may
cause cavitation due to air mixing with the oil, leading to a damaged hydraulic
hammer and carrier components. Keep the oil at the proper level at all times.
4. Do not use the hydraulic hammer at an operating temperature higher than 180°F
(80°C). The proper operating oil temperature range is between 120°F (50°C) and
180°F (80°C). Since contaminated cooler fins causes reduced efficiency of the
cooler, keep the cooler fins clean at all times. Check the hydraulic oil cooling system
to be sure it is working effectively. The use of a heat gun is the best way to evaluate
if the cooler is working properly.
5. Water in the hydraulic oil will lead to damage of the hydraulic hammer and carrier.
Drain off water and foreign matter from the hydraulic tank at specified intervals.
When out of service, the hydraulic hammer should be stored indoors.
CHANGING THE FILTER ELEMENT AND HYDRAULIC OIL
Change the filter element and hydraulic oil at the intervals described in the operation
manual of the skid steer or excavator, when using a hydraulic implement. Another
method is to set up an oil sampling schedule and change accordingly.

- 15 -
HYDRAULIC INSTALLATION
HYDRAULIC QUICK DISCONNECTS
NPK recommends against the use of non-NPK quick disconnects on
hydraulic circuits operating NPK Products.
1. The hydraulic pulsations caused by hydraulic hammer operating can cause internal
pieces of non-NPK quick disconnect (32) to disintegrate. These pieces would
migrate into the hammer, causing damage.
2. If quick disconnects are used when the hammer is removed from the excavator, the
quick disconnects should be capped to keep them clean. If this is not done,
contamination in the disconnect will be flushed into the hammer when re-connected.
This, again, can cause damage.
3. Most quick disconnects create a restriction in the circuit. NPK Hammers are not
back pressure sensitive, but restrictions cause unnecessary heating of the oil. Also,
the pressure required to operate the hammer, plus the restriction in the disconnects
may push an older, low pressure, carrier machine to the limit of its hydraulic system.
This would interfere with proper hammer operation. However, the NPK approved
quick disconnects (DX) are properly sized so that the hammer operation is not
affected.
NOT RECOMMENDED CONNECTION
APPROVED CONNECTION (39) Non-NPK Quick Disconnects (32)
NPK APPROVED CONNECTION QUICK DISCONNECTS
CONTACT YOUR NPK DEALER FOR ADDITIONAL INFORMATION ABOUT
NPK QUICK DISCONNECTS (DX)

- 16 -
HYDRAULIC INSTALLATION
HYDRAULIC QUICK DISCONNECTS
If hydraulic quick disconnects (32) are used with the NPK Hammer, it is recommended
that the following precautions be followed.
1. Periodic inspection of both male and
female ends is recommended to ensure
the couplers are in good working
condition. Failure to inspect couplers
may result in pieces from a damaged or
failed coupler to be injected into the
hammer or parts of the coupler returned
to the machine.
2. Check for dirt, dust, and debris on both
couplers (32) before coupling.
3. Be sure that the couplers are completely
seated together (38).
4. When replacing couplers, be sure that
couplers are replaced as a set, male and
female. Do not use one new end and
one used end.

- 17 -
MOUNTING INSTALLATION
NPK Mounting Installation Kits include the parts required to adapt the NPK HYDRAULIC
HAMMER to the carrier. NPK mounting kits include the hammer mounting bracket, flow
control valve (if required), and hoses to connect to the carrier hydraulic system.
m1 Stick Pin (If Required)
m2 Link Pin (If Required)
m3 (Whip) Pressure Hose
m4 (Whip) Return Hose
m7 Top Bracket
m8 Hammer Bolt Package
m9 Klik Pin
*TORQUES OF ALL BOLTS SHOWN ARE WITH THREADS BEING LUBRICATED
WITH ANTI-SEIZE COMPOUND.
HAMMER BRACKET ADAPTER BRACKET
MODEL BOLT
DIA TORQUE
ft/lb (Nm) BOLT
DIA TORQUE
ft/lb (Nm)
GH06 1” 500 (678) 5/8” 165 (225)
GH07 1” 500 (678) 5/8” 165 (225)
GH1 1” 500 (678) 5/8” 165 (225)
GH2/GHS2 1” 500 (678) 5/8” 165 (225)
GH3 1-1/4” 1000 (1356) 5/8” 165 (225)
GH4 1-1/2” 1250 (1695) 5/8” 165 (225)
GH6 1-1/2” 1250 (1695) 1” 550 (745)
*Refer to NPK Installation Kit Manual for additional information.

- 18 -
ROUTINE INSPECTION AND MAINTENANCE
1. VISUAL INSPECTION
Detect a potential problem early.
TIE RODS AND FASTENERS
Inspect all fasteners and retighten as necessary. On GH06
through GH4 models, inspect tie rod assemblies for loose top
nuts. On the GH6 model, inspect tie rod assemblies for cracked
or missing lock plates and lock rings. If these parts are missing,
consult NPK Service Department at 800-225-4379. See pages
105 and 106 for torque values.
WELDS Check for cracks, repair as necessary, see page 107.
HOSES AND TUBING Check for oil leaks, loose clamps and
hose abrasion.
RUBBER MOUNTS Inspect for damage.
HYDRAULIC OIL
MAINTAIN A CLEAN HYDRAULIC SYSTEM
If non-petroleum oil is used, contact NPK Service Department for compatibility.
Keep hoses clean and capped when dismounting or storing hammer. Change oil
and filters as recommended by carrier manufacturer. Periodic oil sampling is
recommended.
2. DEMOLITION TOOL LUBRICATION
Important:
It is imperative that grease is maintained in the tool
bushing contact area at all times. This may require
hourly greasing depending on job conditions.
Important:
The hammer must be in a vertical position with
downforce applied to push the tool all the way in.
This prevents grease from entering piston impact area. Pump grease into grease
fitting (30) until grease is seen coming out between the tool and bushing.
USE A GOOD QUALITY, HIGH TEMPERATURE EP#2 GREASE CONTAINING ANTI-
WEAR ADDITIVES. NPK recommends a Lithium Base, Moly (Molybdenum
Disulfide) or other surface protecting additives, EP (Extreme Pressure), NLGI #2
Grease. A high drop point (350° to 400°) grease is desirable.
If machine is equipped with an AUTOLUBE System, check grease reservoir daily.
3. TOOL and TOOL BUSHING WEAR
Check the tool and tool bushings for damage, wear or deformation on a regular weekly
basis. Replace the tool and/or bushings when wear exceeds the maximum clearance
limit. See MAXIMUM TOOL TO TOOL BUSHING CLEARANCE, see pages 84 and 85.
Do not hardface or sharpen the tool point with a cutting torch.
Excessive heat from torching or welding causes
embrittlement, breakage, and flying pieces. Resharpen only
with a lathe or milling machine using sufficient cooling.
Please consult your authorized NPK Dealer or NPK Service Department for additional
information.
•DO NOT SUBMERGE HAMMER UNDERWATER
Unless modified for underwater operation.

- 19 -
WEEKLY INSPECTION
1. TIE RODS AND FASTENERS
Inspect tie rod assemblies for cracked or missing lock plates and lock rings. If lock
plates are missing, consult the NPK Service Department at 800-225-4379.
Inspect all fasteners and retighten as necessary, see pages 105 and 106.
2. WELDS
Check for cracks and repair as necessary, see page 107. Consult your authorized
NPK Dealer or NPK Service Department for additional information.
3. TOOL RETAINING PIN
Remove the retaining pin and inspect for peening caused by excessive blank
hammering. If necessary, grind edges smooth as shown in TOOL RETAINING PIN
INSPECTION, see page 90. The retaining pin must rotate freely.
4. DEMOLITION TOOL
Remove the demolition tool and inspect for peening caused by excessive blank
hammering. If necessary, grind edges smooth as shown in TOOL INSPECTION,
see page 87.
5. GAS CHARGE
Check and adjust, if required, see pages 29 through 32.
Other manuals for GH Series
1
This manual suits for next models
8
Table of contents
Other NPK Tools manuals
Popular Tools manuals by other brands
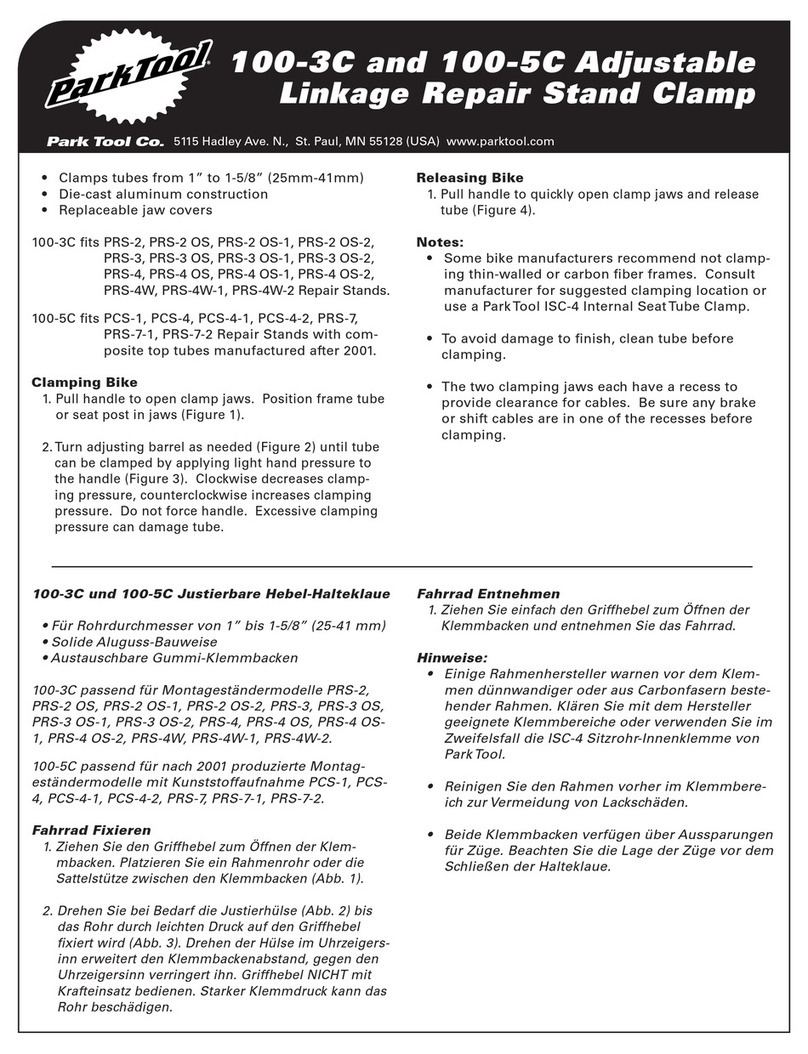
parktool
parktool 100-5C manual
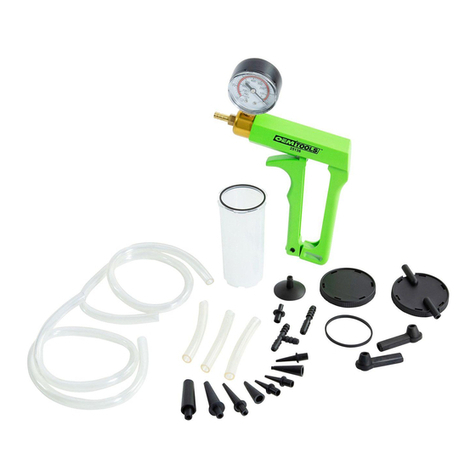
OEM Tools
OEM Tools 25136 Operating instructions and parts manual
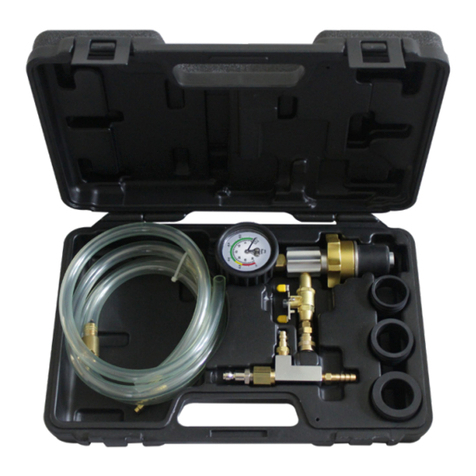
Master cool
Master cool 43012 manual
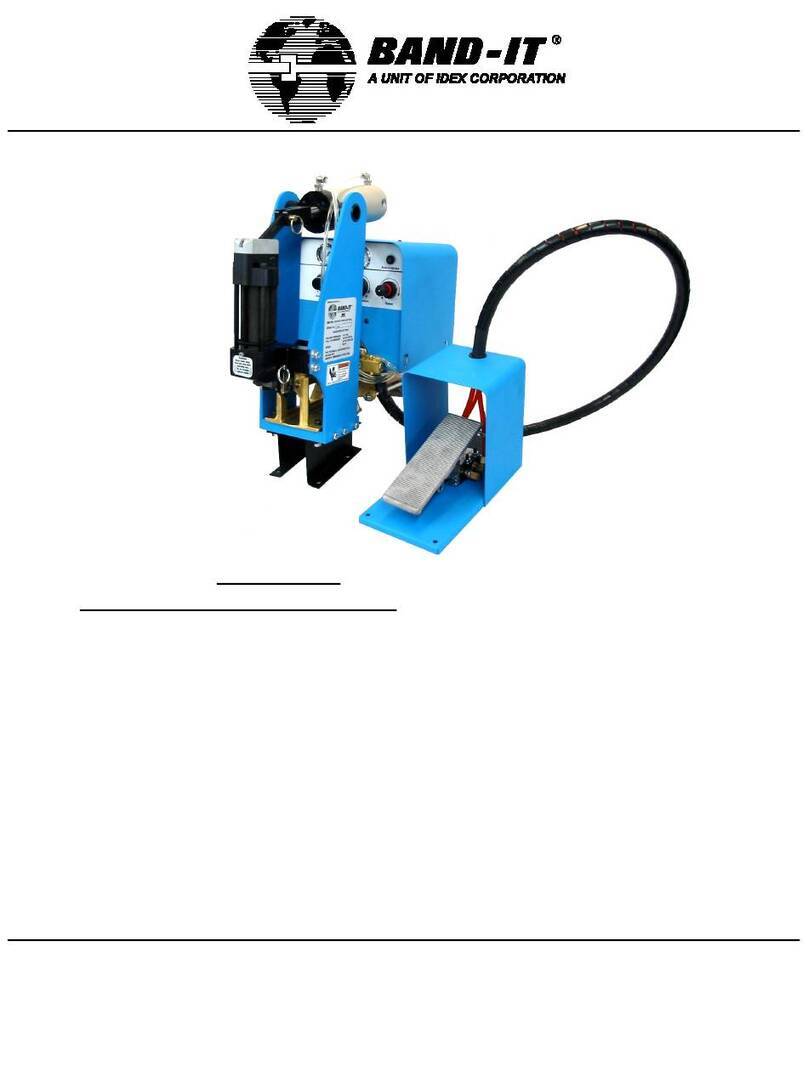
Band-it
Band-it GRSM17 Owner's Manual and Operating Instructions
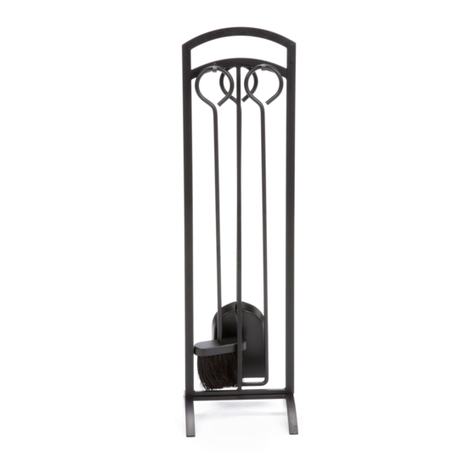
LOWE'S
LOWE'S Open Heart 15839L quick start guide

Sparta
Sparta Huskie Tools PRO LINE IL-7NDBG Operator's manual