Oceanic Systems 5700 User manual

Air Volume Monitor
Part Numbers: 5700
USER MANUAL
Document revision 1.00

1
CONTENTS
1. OVERVIEW
1.1 FRONT PANEL LAYOUT
1.2 DIAGNOSTIC LEDs
2.DIMENTIONS & CONNECTIONS
2.1 3 & 4 WIRE CONNECTIONS
3. CONFIGURATION
2.1 ACCESSING MENUS
2.2 RANGE KEY - PARAMETERS
2.3 OUTPUT KEY - PARAMETERS
2.4 DISPLAY KEY - PARAMETERS
2.5 ALARM KEY - PARAMETERS
4. ALARM TEST MODE
5. MANUAL ZERO
6. PASSWORD OPERATION
7. CALIBRATION MODE
6.1 OUTPUT RANGE CONFIGURATION
6.2 SENSOR SPAN CALIBRATION PROCEDURE
6.3 CALIBRATION MODE OUTPUT FREEZE
8. PID CONTROL MODE
9. REMOTE DISPLAY
10. COMMUNICATIONS
1. SPECIFICATIONS

OVERVIEW
1
2
These sensors are wall, or panel backplate, mount air pressure / velocity sensors that provides
an output signal of 0-10V and 4-20mA.
The units also features MODBUS communication and an adjustable alarm relay output.
The red LED display shows the actual pressure or velocity/volume in the selected units
depending on the settings. All necessary adjustments can be made via the front membrane
keyboard, the layout of which is shown below.
1.1 FRONT PANEL LAYOUT

3
1.2 DIAGNOSTIC LEDs
The red and green LEDs on the keyboard as well as the right hand decimal point on the display
indicate various conditions as shown below.
Green LED ON
Red LED OFF Normal operation
Green LED OFF
Red LED ON Alarm condition – see alarm section
Both LEDs ashing together The display is temporarily showing an alter-
native value.
Green LED ashing Red LED off
Red LED ashing Green LED off See 2.3 output scaling mode.
Right hand decimal point lit
The user has entered the correct password
and the password is still active allowing
parameters to be changed.
Right hand decimal point ashing twice per
second Calibration mode.
Right hand decimal point ashing rapidly up and down keys can now be used to adjust
the calibration of the sensor.
Display shows O LOA d or U LOAd See section 2.2 Over pressure protection

DIMENTIONS & CONNECTORS
2
4

5
2.1 3 & 4 WIRE CONNECTIONS

6
3.1 ACCESSING MENUS
There are menus under the following keys:
(Output)
(Range)
(Display)
(Alarm)
(Control) Pressed together.
To access a menu, hold down the key until the LED display changes (approx 1 second). The
display will now show a parameter and its value. The same menu key is then used to step
through all the available parameters within the menu. After the last parameter has been
displayed the sensor will return to normal operation.
The keys are used to change the value of a parameter once selected.
To save the new value, simply step through to the next parameter.
To cancel the new value, press the zero key.
A parameter is indicated by either a single letter or a group of letters. The following tables
show how each parameter is displayed when the menu keys are pressed.
2.0 CONFIGURATION
3
>0<
>0<

7
3.2 RANGE KEY PARAMETERS
Note: A short press on this key will display the Full Scale Range of
the sensor in the selected display units. Sensors with a -/+ range will show Pn
indicating that the P and n parameters both need to be checked to see the
range.
INDICATOR PARAMETER RANGE
SSoftware Version (e.g. 1.15)
Ad Network Address 1-254
A2 Auto-Zero On or Off
PPositive Range
nNegative Range
OPP Over-Pressure Protection 1 (On) or 0 (Off)
FZero Offset
tSet Point
Sn MODBUS Smoothing d or o
AdJ Internal/External Controls I or E
A2t Auto-Zero Time 1-99 hours
FF MODBUS oat format 0 - 3
Software Version
This displays the current software version used. This manual relates to software version 3.87.
Network Address
This is the Modbus network address assigned to the instrument.
Auto-Zero
When set to ON, the internal electronic air valve will remove air pressure from the sensor
periodically, and the sensor will be zeroed. During this period the Output Signal, the Display
and the Modbus registers will be held at their current values.
Positive Range
This is the Positive Range of the sensor and is displayed in Pascals (Pa). This range can be
adjusted within certain limits (Consult CMR).

8
Negative Range
This is the Negative Range of the sensor and is displayed in Pascals
(Pa). This range can be adjusted within certain limits (Consult CMR).
Over-Pressure Protection
When set to 1 (ON), the internal electronic air valve will remove air pressure from the sensor
when an over-pressure condition is detected.
After a 1 second delay the air valve will return to its normal operation. If the over-pressure
condition is still present at this time the air valve will remove the air pressure once again. This
routine will continue until the over-pressure condition is removed. If the over-pressure condition
is positive, the display will show O LOAd , and the output will go to 10V. If the over-pressure
condition is negative, the display will show U LOAd , and the output will go to 0V.
Zero Offset
A zero offset in Pa can be entered. This value is added to the sensor reading so that for example,
if -5.0 is entered the sensor will now read -5.0Pa with no pressure applied to the instrument. For
sensor ranges of less than 1000Pa an offset of +/-199.9Pa can be entered. For sensor ranges of
1000Pa or more an offset of +/-1999Pa can be entered.
Set Point
This parameter is to maintain compatibility with earlier versions of the software. For new
projects use the PID setpoint.
Modbus Smoothing
Sets the smoothing of the values read over the Modbus network.
When set to ‘d’ (Display) the display smoothing value is used.
If set to ‘o’ (Output) the output smoothing value is used.

9
Internal / External Controls
When set to ‘I’ (Internal), then the network address, range, output smoothing, output mode,
small value shut off, mag factor and alarm threshold are set by the internal controls. The values
will be viewable on the display but cannot be changed by the keyboard.
If set to ‘E’ (External), then the internal controls are ignored and all values are set using the
membrane keyboard.
Changing this value from ‘E’ (External) to ‘I’ (Internal) will cause the previously entered values
for the settings listed above to be over written with the values set at that time on the internal
controls.
To avoid accidentally changing this value, the procedure for changing it is different. With the
display showing AOJ, hold down the key until AOJ ashes. The keys can now be
used to toggle the value.
Auto-Zero Time
Time in hours between auto-zero cycles.
Factory set to 1, but can be increased up to a maximum of 99.
Float Format
Selects the format used to represent oating point values in the modbus registers. See the
Modbus Communications Specication for exact details.

10
3.3 OUTPUT KEY PARAMETERS
Note: Under normal operation a short press on this key will display
either Lin or Root, indicating the output mode. If PID control mode is
set then this key instead switches the display to show the current percentage
value of the control output for a few seconds.
INDICATOR PARAMETER RANGE
So Output Smoothing 0-99
L i n ro o t Output Mode
EOutput Scaling Mode F or L or Fac
F
Mag Factor or K Factor
(depends on E parameter
setting)
0-99.99
_Duct Width 0-9999mm
IDuct Height 0-9999mm
rRoom Size 0-999m3
SSmall Value Shut Off 0.00 - 99.99%
oOutput Re-Scaling
bFL Bidirectional ow 0 or 1
Output Smoothing
This will set the smoothing of the output signal and the Modbus registers.
The value of between 0 and 99 represents a time constant of between 0
and 10 seconds.
Output Mode
This will set the output signal to be in either linear (Pressure) or square root (Flow) mode.
Output Scaling Mode
The sensor can be set to measure air velocity or volume by using one of
three different methods.
If set to ‘F’ (Mag Factor Method) then the sensor measures the differential pressure and uses
the magnication factor and air density constant to calculate velocity. The volume is then
calculated using the duct dimensions.
If set to Fac (K factor method) then the sensor measures the differential pressure and uses
the K factor to directly calculate the volume. This method is used when a K factor has been
supplied by, for example, a fan manufacturer.

11
If set to ‘L’ (Direct Entry Method), then the sensor uses a look up table to convert the differential
pressure to velocity or volume. The look up table can have from 1 to 8 points. Each point consists
of a pressure and an associated velocity or volume gure. If the look up table only has 1 point
then the output from the sensor will be linear against square rooted pressure. For applications
where the velocity or volume is not linear additional correction points maybe added.
Single Point Example (Direct Entry Method):
Sensor Range = 100Pa
It is known that for a duct volume of 1.000m3/s the differential pressure is 25Pa.
1. Set the display units to m3/s (See the key for description).
2. Hold the key to enter menu.
3. Press key and set the Lin / Root parameter to root.
4. Press key and set the E parameter to L.
5. With the display showing Lin 0, hold the key until the green LED ashes.
Use the keys to set the display to 25.0. Press the key when
done.
6. With the display showing Lin 0, hold down the key until the red LED ashes.
Use the to set the display to 1.000. Press the key when
done.
7. Press the zero key to exit the menu.
To nd out the full scale range of the sensor in m3/s press the key briey.
In this example 2.000 m3/s will be displayed.
When 100Pa is applied, 2.000 m3/s is displayed, with a 10V and 20mA output.
When 25Pa is applied, 1.000 m3/s is displayed with a 5V and 12mA output.
Multi Point Example (Direct Entry Method):
With the sensor set up as for the single point example, an applied
pressure of 50Pa would display a volume of 1.414 m3/s. If the application
>0<

12
is not linear and has for example a volume of 1.700 m3/s at 50Pa, then
another Lin point can be added to correct for this error.
1. Follow the single point example until the display shows Lin.0 (Note that the decimal point in
front of the 0 is lit, showing that Lin 0 is already set up).
2. The keys can be used to scroll from Lin 0 to Lin 7. If the decimal point in front of the Lin
number is lit then this means that the Lin point has already been set up. A short press on the
key or the key briey shows the pressure or volume setting for the Lin point.
3. To set another point, select Lin 1. Hold the key until the green LED ashes and then set
to 50.0 Pa. Press the key when done.
4. Hold the key until the red LED ashes and then set to 1.700 m3/s.
Press the key when done.
Please note that Lin points do not have to be entered in order.
Eg: If there are Lin points at 25, 50 and 75Pa, Lin.1 could be 75Pa,
Lin.2 could be 25Pa and Lin.3 could be 50Pa.
Clearing a Lin Point
If a Lin point has been set up, but is no longer required it can be cleared by holding down the
key, whilst changing its pressure or volume values.
Using alternative units
The Lin point volume values must be entered in m3/s. The sensor can still be set to display m3/h
or l/s, but the volumes must be converted to m3/s before setting the Lin points.
To use the sensor for measuring velocity, the Lin point volume values can be entered directly as
m/s.

13
Mag Factor (F Parameter)
E parameter is set to F.
This will set the desired Magnication Factor of the measurement device. Measured pessure (Pa)
is divided by this value. Eg: Typically Oval Flowprobes = Mag 1.5 (150Pa / 1.5 = 100Pa)
K Factor – (F parameter)
E parameter is set to Fac.
The sensor can be set to display volume in cubic metres per second, cubic metres per hour, litres
per second or as Air Changes per hour but the K factor must be set in m3/s. If the K factor has
been supplied in m3/h then divide the supplied value by 3600 to get m3/s. If the K factor has
been supplied in l/s then divide the supplied value by 1000 to get m3/s.
Duct Width
This parameter will allow the Duct Width to be entered in millimetres (mm).
Note. If the duct is circular this value represents the diameter (Not used for velocity).
Duct Height
This parameter will allow the Duct Height to be entered in millimetres (mm).
Note. If the duct is circular this value must be entered as zero (Not used for velocity).
Air Density
The default value of 1.200kg/m3 can be used for the majority of applications. (Please note that
versions of software prior to V3.50 used Air Density Factor and should be set to 1.291)
Room Size
The size of a room can be entered in cubic meters (m3), if air change rate needs to be measured.
If air change rate is not being measured then this value is not used.
Small Value Shut Off
This clamps the display and signal output to zero if the pressure reading is less than this setting
which is in % of full scale pressure range.
Output rescaling
Note that this function only works if the instrument is set to measure velocity or volume.
It is possible to rescale the output so that 10V and 20mA is equal to a different value. This is
particularly useful when the output is connected to an external system (BMS / PLC / Chart
Recorder) which already has input scaling set.

14
The output scaling can be changed by adjusting the parameter on the menu. If this value
is 0 then it is ignored, and the full scale output of the sensor will be the value shown when the
key is pressed.
If for example the value shown when pressing the key is 2.000 m3/s and a value of
4.000m3/s for at 10V/20mA is preferred then the oparameter could be changed to 4.000.
Pressing the key still shows 2.000 m3/s as this is still the maximum volume the sensor can
measure, but 2.000 m3/s will now output 5V/12mA.
Bidirectional Flow Enable
Factory set to 0, bidirectional ow measurement disabled.
It is possible to measure airow in both directions. To achieve this, the parameter must be
set to 1 and the Output Range (see section 6) must be set to 5-10V or 12-20mA. Zero ow will
output 5V/12mA. Full scale forward ow will output 10V/20mA and full scale reverse ow will
output 0V/4mA. The display will show a negative reading for a reverse ow.
When bidirectional ow is enabled, the small value shutoff will operate in a band either side of
zero.

3.4 DISPLAY KEY PARAMETERS
Note: A short press on this key will display the displayed units.
These are shown as indicated below.
INDICATOR PARAMETER RANGE
Sd Display Smoothing 0-99
Display Units:
PA Pascals
hPA hecta Pascals (mbar)
3PA kilo Pascals
nnPS metres per second
IPS litres per second
n n3S cubic metres per second
n n3h cubic metres per hour
Acr Air changes per hour
dP Decimal point 0-4
PoS Display polarity (+)
nEg Display polarity (-)
LEd Display Activation 1 or t
brt Display Brightness L or H
L2 b Leading zero blanking 1-4
Display Smoothing
This will set the smoothing of the Display.
The value of between 0 and 99 represents a time constant of between 0 and 10 seconds.
Decimal Point
The number of digits to be displayed after the decimal point.
Display Polarity
This is normally set to positive.
If set to negative, the display will show a negative reading for a positive signal.
For example:
If a 0-1000Pa 0-10V sensor is used to measure a negative pressure by sucking on the negative
15

16
nipple, the output signal will be between 0 and 10V for 0 to 1000Pa. The display can be made to
read 0 to -1000Pa by setting the display polarity to negative.
If PID control is being used and the display polarity is set to negative then the setpoint is also
negated internally. So for the above example, if it is required to control at –500Pa on the
display, then the setpoint needs to be entered as –500Pa. Internally the sensor is measuring and
controlling +500Pa but the display and setpoint both show –500Pa.
It is not recommended to set the display polarity to negative if the alarm function is required, as
the alarm thresholds are not changed by the display polarity setting.
Display Activation
When set to ‘!’ the sensor display is always on.
If set to ‘t’ the sensor is switched on when a key is pressed and will automatically switch off
after 2 minutes of keyboard inactivity.
Display Brightness
When set to ‘L’ the display has low brightness.
If set to ‘H’ the display has high brightness.
Leading Zero Blanking
This is the minimum number of digits that will be displayed. The table below shows how a value
of 1 would be displayed depending on the number of decimal places and the L2 b setting.
L2 b
Decimal places
01234
1 1 1.0 1.00 1.000 1.0000
201 01.0 01.00 1.000 1.0000
3001 001.0 01.00 1.000 1.0000
40001 001.0 01.00 1.000 1.0000

3.5 ALARM KEY PARAMETERS
INDICATOR PARAMETER RANGE
LLow Alarm
HHigh Alarm
tAlarm Timer 1 0-999 seconds
t. Alarm Timer 2 0-999 seconds
rL Relay Energization
UUnits dU or PEr (%)
AF Alarm Function 0 - 3
Sr Self Reset 0 or 1
Ar Alarm Reset b o r rb
bU Buzzer Function 0 – 3
rb Remote buzzer - O I P
rA Remote alarm indication - O F LH
rt Re-alarm timer 0-999 minutes
tU Timer units Sor h
r⌟P Relay pulse Oor I
Low Alarm
The low alarm threshold. See Units below.
If a low alarm is not required then it can be turned off by pressing the RANGE
key while the Low threshold is being displayed. The display will then show L OFF.
High Alarm
key while
The high alarm threshold. See Units below.
If a high alarm is not required then it can be turned off by pressing the RANGE
the low threshold is being displayed. The display will then show H OFF.
17

18
Alarm Timer 1 & 2
Alarm delays in seconds. See Alarm Function below.
Relay Energization
nd The relay is normally de-energized and will energize when in alarm.
nE The relay is normally energized and will drop out when in alarm.
The front panel LED is red when in alarm regardless of the relay
energization.
Units
dU The alarm thresholds are displayed in the same units as currently
selected for display.
PEr The alarm thresholds are displayed as a percentage of the full scale
range of the sensor.
Self Reset
See the description of alarm functions 2 and 3.
Alarm Reset
For alarm modes 2 & 3, this sets the function of the key. If set to then the buzzer and the
relay will be reset. If set to then only the buzzer is reset.
Internal Buzzer Function
0 = The internal buzzer is disabled.
1= The internal buzzer sounds continuously when in alarm.
P= The internal buzzer pulses on and off when in alarm.
Remote Buzzer Function & Remote Alarm Indiation
See remote display section
Re-alarm timer
The re-alarm timer can be set between 1 and 999 minutes. If the re-alarm timer is set to zero
then it is disabled. The re-alarm timer starts when the mute is operated. If the alarm condition
is still present when the re-alarm timer expires, the buzzer and the relay are turned on again.
Timer Units
SThe alarm timers are in seconds and the re-alarm timer is in minutes.
hThe alarm timers and re-alarm timer are in hours.
Relay Pulse
If this parameter is set to 1 then the relay will pulse on and off when in alarm.

19
Alarm Function
0 MODBUS SET ALARM
The sensor does not generate any alarms in alarm mode zero. The alarm relay, the
internal buzzer and the remote display alarm are driven directly via MODBUS. See
MODBUS communications specication.
1 INTERNALLY SET ALARM
This is only used for applications where the keyboard and display are not tted. The
alarm pot on the PCB sets a threshold as a percentage of the full scale range of the
sensor. The relay is energised if the signal is below this threshold for longer than 10
seconds. The internal buzzer doesn’t function in this mode.
2 KEYBOARD SET ALARM
If the signal is outside of either of the thresholds for longer than the Timer 1 setting
then the relay is set, the buzzer sounds and the keyboard LED changes from Green to
Red.
If the key is pressed the buzzer will go off, the relay will be reset if the
parameter is set to , the keyboard LED stays red.
When the signal has come back into threshold for longer than the Timer 2 setting and
the Sr setting is 1, the alarm will be reset. If Sr is 0 then the alarm will not reset until
the key is pressed.
3 KEYBOARD SET ALARM – STAGE 1/STAGE 2
If the signal is outside of either of the thresholds for longer than the Timer 1 setting
then the buzzer sounds and the keyboard LED changes from Green to Red. Timer 2 then
starts and if the signal is still out of threshold when Timer 2 expires then the relay is
set.
Pressing the key before Timer 2 expires will reset the buzzer. The relay will still
be set when Timer 2 expires.
Pressing the key after Timer 2 expires will reset the buzzer and will also reset the
relay if the parameter is set to rb.
If = 1, the alarm will reset automatically when the signal has come back into
threshold.
If Sr = 0, the alarm will reset automatically if the signal comes back within threshold
before Timer 2 expires. The key will need to be pressed to clear the alarm once
Timer 2 has expired.
Table of contents
Other Oceanic Systems Measuring Instrument manuals
Popular Measuring Instrument manuals by other brands
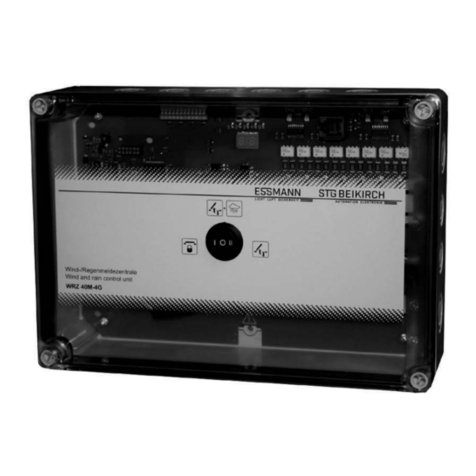
Essmann
Essmann WRZ 40M-4G Technical information and operating instruction

Middle Atlantic Products
Middle Atlantic Products RackLink owner's manual
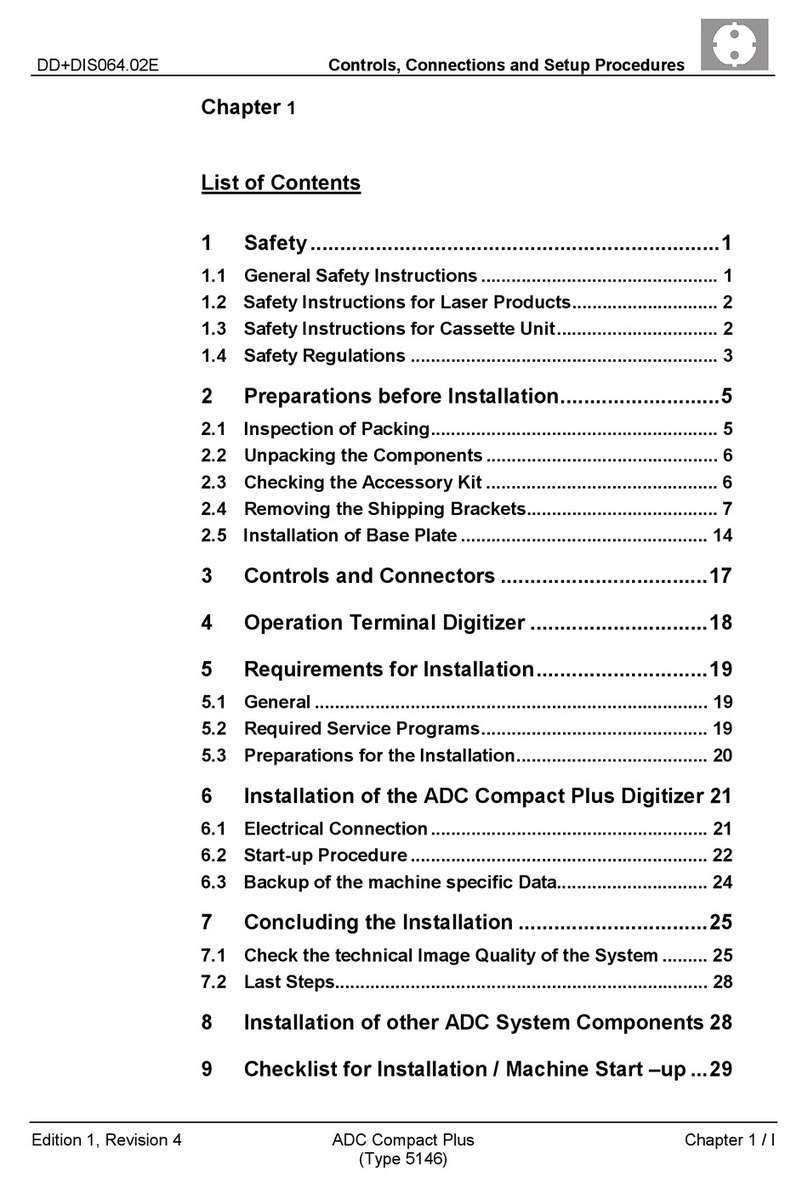
AGFA
AGFA ADC Compact Plus manual
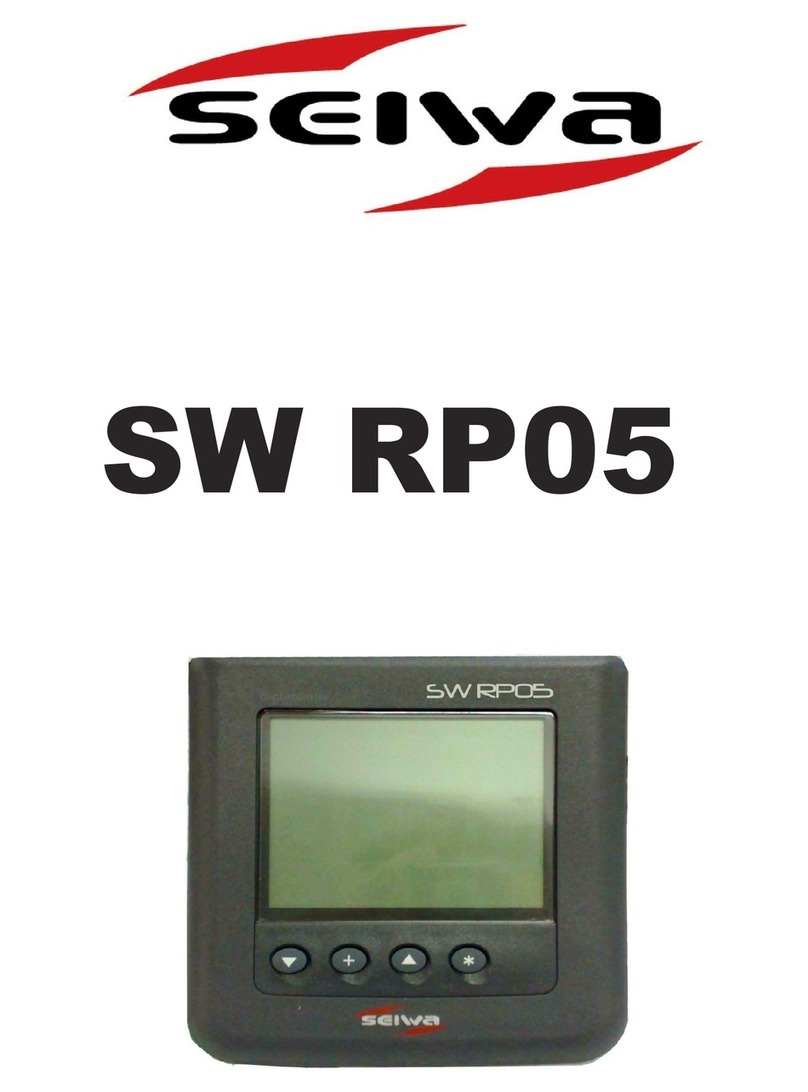
Seiwa
Seiwa SW RP05 operating instructions
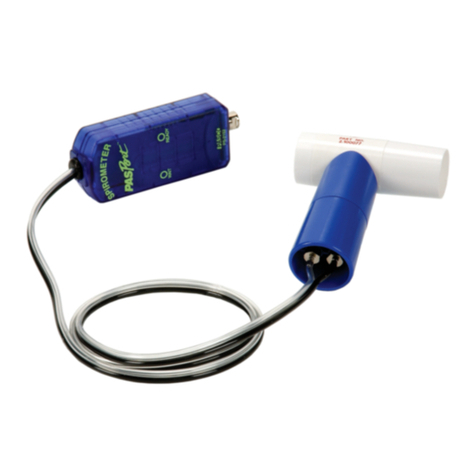
PASCO
PASCO PASPORT PS-2152 instruction manual
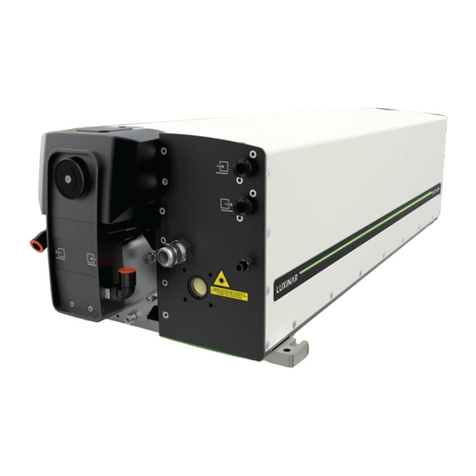
Luxinar
Luxinar SR AOM Series user manual
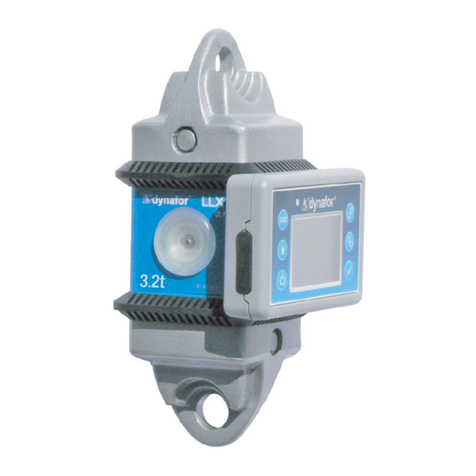
Tractel
Tractel Dynafor LLX2 1 t Operation and maintenance manual
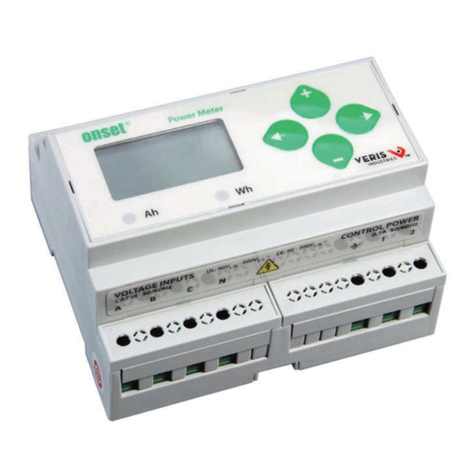
Onset
Onset T-VER-AH02 installation guide
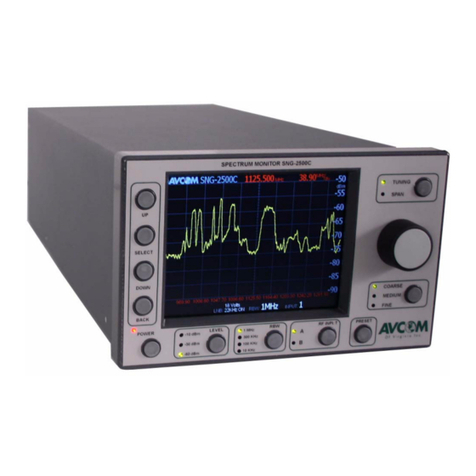
AVCOM
AVCOM SNG-2500C user guide
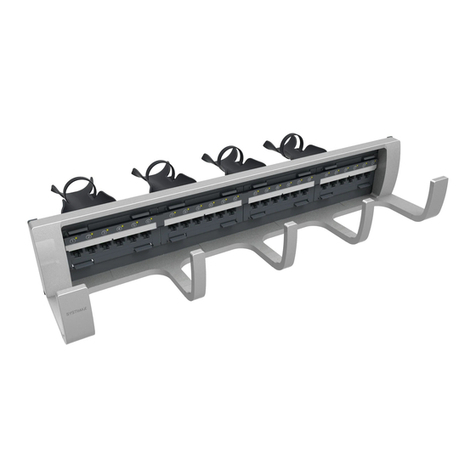
CommScope
CommScope SYSTIMAX 360 PATCHMAX instruction sheet
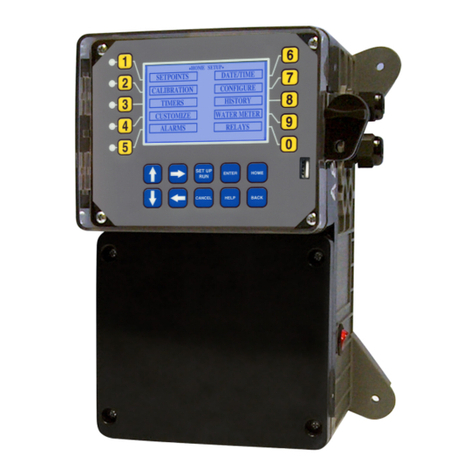
ARJAY ENGINEERING
ARJAY ENGINEERING 4500-RMS user manual

TECALEMIT
TECALEMIT TecSonic 225800200 operating manual