OKM 5410 Series User manual


Safety Precautions
Precautions listed below are specified to use this product safely, as
well as to prevent users, other persons or facilities and equipment
from injury or damage. In addition. this Instruction Manual uses
the following illustrations to clarify the seriousness of hazard or
damage and degree of urgency when this product is misused.
Warning
This indicates that if ignored, may lead to
imminent risk of death or serious injury,(*1)
or material damage.
Precaution
This indicates that if ignored, may lead
to the user suffering injury,(*2) or valve
damage.
*1: Serious injury means a person suffers aftereffects and needs hospitalization and
long-term hospital visit for medical treatment.
*2: personal injury means an injury without hospitalization or long-term hospital visit for
medical treatment.
●Types of indications are explained below
This symbol indicates the "prohibition"
items, which must not conduct.
This symbol indicates the "mandatory"
items, which must not conduct.
Important items for handling of this product are shown below.
1
●Contents
Before Using 1
Structural Drawing 2
Stocking, Handling, Un-packing 4
Piping Work 1
-Cares Before Installation Valve To Pipings 5
Piping Work 2
-Cares After Installation Valve To Pipings 7
Check-up, Maintenance 1
-Periodic Check-up, Removal From Piping 9
Check-up, Maintenance 2
-Exchange The Seat-ring 10
Check-up, Maintenance 3
-Exchange The Grand Packing・Gasket 11
Check-up, Maintenance 4
-Removing The Actuator 13
Check-up, Maintenance 5
-Set The Actuator 14
Trouble Shooting-For Valve Body Trouble 15
Trouble Shooting-For Actuator Trouble 17

2

3

1, Stocking
Stocking(packed) :
Valve to kept/stored indoors under cool and dark
condition (temp:-5˚C 〜60˚C, humidity: less than 70%),
if valve not installed to pipings immediately after
delivery.
Stocking (un-packed) :
When valve to be stored without packing, any
excessive force to its actuator part to be avoided.
Cover-sheet to be put onto valve at dusty place. (Fig.2)
Stocking :
Apply anti-rust to the plated-parts (indicators, bolts
nuts worm shafts, etc…) once a year if valve is stored
for one year or longer.
2, Handling
Cares while handing :
When valve to be kept /stored under packed condition,
package(s) to be put on stable place so that collapse
of package(s) to be avoided. Upon carriage, valve to
be nicely loaded so that any collapse to valve could
be avoided. When valve to be carried after removing
packing, excessive force to valve to be avoided and
cover-sheet to be put onto valve in dusty-place. (Fig.3)
Trucking :
To use truck with canopy is recommended if possible.
Cover valve to prevent dust if a truck with no canopy
is used.
Sipping(seaborne) :
Use a container for shipping to protect valve from sea
breeze. Sea breeze will damage valve.
3, Un-packing
Un-packing :
Un-packing of valve to be recommended before its
installation to pipings. If valve stored being unpacked
for long,dust or foreign matter will get into the valve. If
will cause malfunctions. (Fig.4)
Check disc position :
Make sure if valve is in the closed position when
package is opened.
Fig.2
Fig.3
Fig.4
4

1, Checking Valve Body
Check sizes and material :
Sizes & Specifications of Trim Materials are indicated
on package and valve, and re-confirmation of sizes/
specifications before its installation to pipings is
recommended.
Check piping sizes :
Check the valve sizes fit the piping sizes. (Fig.5)
Check the number and the sizes of bolts :
Before using bolts and nuts, apply a seizure preventive
to bolts and nuts.
2
,
Welding Before Installation To Pipings
Cares when welding flanges :
Installation of the valve immediately after welding of
the flange to be avoided, and installation to be made
only after welded-part cooled down.
Welding of flange or reparing works through welding,
while keeping the valve installed to pipings, to be
avoided. (Fig.6)
Make sure welding work is completely done before
installation the valve to the piping. Flanges to check
and confirm on deflection or miscenter-alignment of
flange and no spatter sticked.
3, Check Piping Flanges
Make sure no deflection or damage to piping :
Make sure no deflection or miscenter-alignment of
flanges and no score or spatter stacked. Clean spatter
stacked on the edge of the flanges completely in order
not to damage the seat-ring.
Cleaning :
Flange surface is to be air-purged for cleaning. If
rust or foreign matter is sticking on the surface of the
flanges, wash the surface of the flanges in detergent.
After washing, make sure no detergent remains on the
seat-ring. If detergent remains on the seat-ring, it will
damage the seat-ring.
Make sure that no oil or detergent sticks to EPDM seat.
Fig.5
Fig.6
5

Fig.7
Fig.8
Fig.8-1
Fig.9
4,
Cares Before Installation Valve To Piping
Installation place :
Application to heavy-vibrant positions to be avoided.
To keep enough space for maintenance work. (Fig.7)
lInstallation work :
Connect the valve and the piping flanges correctly.
Forcing the valve to insert between the piping flanges
to be avoided.
Gasket packing :
The insertion between the valve and the piping-flanges
shall be needed the gaskets. In inserting,adjust
both the valve and the gasket to the center of the
flanges accurately. Keep space of about 3mm to 5mm
between the valve to the piping-gasket (the flanges) on
each side. (Fig.8)
Do not insert the valve between the piping flanges
forcefully. And also, do not use the flexible material
such as rubber to the gasket, otherwise, we
recommend the joint seat as the piping-gasket.
Further, in using the special gasket such as the spiral
gasket, please contact to sales person in charge.
Disc position :
Keep the valve in closed position when installation to
the pipings.
Installation the valve to ab ent pipe :
Upon installation of the valve to the pipings, no define
limitation of direction of the valve being installed but,
under such condition as illustrated in Fig.8-1, direction
of stem to be cared.
Installation the valve to a return valve to a return valve, etc... :
When the valve to be installed directly to return valve,
pumps, etc…, there may be cases in which disc
touches to other upon its full opening. In this case,
short-pipe to be fixed before installation of the valve.
(Fig.9)
6

1,
Installation Procedures To Pipings
1. Cleaning:
Remove foreign matter from part of the valve touches
surface of flanges by air blow.
2. Check the valve position :
Make sure the disc is in the closed position.
3. Suspend (Support) the valve :
Insert bolts into lower flange holes, and then put nuts
on either side of the bolts to support the valve.
4. Set jack bolts :
Keep space of about 3mm to 5mm between the valve
and the flanges on each side. (Fig.10)
5. Insert the valve :
Do not insert the valve between the piping flanges
forcefully.
6. Center the valve to the piping flanges :
Insert bolts into the flange holes to suspend the
valve,then center the valve to the flanges accurately.
7. Tighten up bolts:
Firstly, as Fig.10-1 (top and bottom),tighten the bottom
of the bolt A and B not to drop the valve. Then insert
other bolts. (Fig.10-1)
Tightening piping bolts is doing evenly and diagonally.
Unbalanced fastening among bolts causes any
leakage. From 1 to 8 is shown example of the order of
fastening bolts. (Fig.10-2)
8. Check the disc movement :
After installation of the valve,operate the valve (from/to
open and close) to make sure the disc dose not touch
any part of the pipings.
※
In case of that flow medium is steam, install the stem side as
the upstream of flow direction.
※
Regarding Model 541R and 541M,install the stem side as the
upstream of flow direction.
Fig.10
Fig.10-1
Fig.10-2
7

2,
Cares After Installation to Pipings
Check leakage :
Before operation of the valve, pressure inside the pipings
to be raised and to make sure no-leakage between the
piping-flanges and the valve. When gas used as fluid,
use soaped water for checking leakage. However,
pressure inside the pipings not to be raised beyond the
valve specifications, and set the disc of the valve in the
open position while checking the leakage. (Fig.11)
Treatment for leakage:
In case of leakage, reduce the pressure firstly, and
then tightening the flange bolt again. Tightening bolts
is doing evenly and diagonally. Unbalanced fastening
among bolts causes any eakage.
3, Other Points to be cared
Trial run (Check-up run) :
Operate the valve by manual before operating.
Cares while operating the valve with a hand wheel :
Be sure to turn the hand wheel by the hand. Do not
turn the hand wheel with a wrench or lever in order not
to cause trouble.( Fig.12)
Do not use blank flange :
Keep the valve fully opened while pressure test, etc.
Do not use the fully closed valve as a blind flange.
Cares after pipings :
Regarding motorized valve, in operating by manual hand
wheel, make sure the main power is off before operating.
After returning electric operation mode, remove the lever
and put on the main power. (Fig.12-1)
Operating more than two actuators by one switch shall
cause malfunction due to wrap around circuit. So, Operate
one by one, and also,set up the relay nterface. (Fig.12-2)
Precaution
Opening/Closing the valve in short time causes the water
hammer which may damage the valve or the other instrument.
Please contact the person in charge if you use such a way.
In case that actuator and valve is soused by corrosive
fluid directly, protect with protection cover.
In case that control valve is installed to upstream side,
vibration of turbulent may damage it, so get space
from 3D to 5D.
Fig.11
Fig.12
Fig.12-1
Fig.12-2
8

1, Checkup
Periodic checkup :
Inspect the disc or seat-ring at least once a year.
Make sure no disc is corroded or weared. (Fig.13)
Long no use after installation :
If the valve is not to be used for extended periods
after installation, open and close it manually or
automatically at least once two weeks.
Trouble happened :
If valve operates inproperly, foreign matter or damage
to seat-ring or something may be of the cause of the
problem. Please see the trouble shooting chart shown
in P.15.
2,
Removal From Pipings
Warning
Check pressure inside pipings before
removing the valve from pipings :
When the valve removes from pipings, make sure the
pressure inside the pipings is lowered.
In case of fluid remaining inside the pipings, drain it
out from the pipings. (Fig.14)
How to remove the valve from the pipings :
Set the valve in the closed position, then pull out
bolts and nuts. In doing this, remain a few bolts and
nuts in the lower holes of flanges to support the
valve. For easy-removal work,inserting jack bolts is
recommended.
Fig.13
Fig.14
9

10

11

12

1,
How to remove the Actuator from the valve
Fix the valve body by a vice before disassembling
the valve.
1. Lever type (Fig.23)
1. Removing the upper bolt :
Remove the bolt-ⓐwhich fixes the name plate of the
Leverⓑ.
2. Removing the Lever :
Hold the lever notch and then holdit up and remove it.
3. Removing the Indicator :
Remove two boltsⓒfixes up the indicatorⓓAnd
then strike the pinⓔsets the indicator by the plastic
hummer,and remove the pin and the indicator.
2. Gear type (Fig.24)
1. Removing the bolt :
Remove the boltⓐfixes the actuator and the body.
2. Removing the actuator :
Hold up the actuator and removeit from the body.
※For air-cylinder or electric motor type, contact your OKM
sales representative.
13

1,
How to set the actuator on the valve
Fix the valve body by a vise before setting.
1. Lever type (Fig.25)
1. Check the disc position :
Open the valve fully.
2. Fix the indicator :
After inserting the pinⓔinto the hole on the valve
neck, put the indicatorⓓthrough the pinⓔ. Then, fix
the indicator to the valve body by two boltsⓒ.
3. Set the lever :
Set the leverⓑto the letter (S) marked on the indicator.
And then, fix the name plate to the indicator by the
boltⓐ.
4. Check the disc movement :
Turn the lever to make sure if the lever can operate
smoothly and the nose of the lever can point at
graduation on the indicatorⓓaccurately. After
checking the above(lever position), keep the valve in
almost fully closed position.
2.Gear operation type (Fig.26)
1. Check the disc position :
Open the valve fully.
2. Removing the actuator :
Keep the valve fully opened by turning the handwheel.
3. Set the actuator :
Connect and fix the gear operator to the upper shaft
with four boltⓐ.
4. Opening or closing adjustment
[How to set Opening point] Release lock nutⓑ, tighten the
adjustment bolt until it slightly stops, then, quarter-turn
the adjustment bolt, tighten the lock nutⓑ.
[How to set closing point] Release lock nutⓒ, open the valve
fully by turning the handwheel after checking the disc
touches the rubber seat fully, tighten the adjustment
boltⓒuntil it slightly stops, then, quarter-turn the
adjustment boltⓒtighten the lock nutⓒ.
5. Check the valve:
Make sure if the valve can operate smoothly by turning
handwheel. After checking, keep the valve in almost
closed position.
※For air-cylinder or electric motor type, contactyo ur OKM
sales representative.
14

15

16

17

18

Tokyo Office
Hatchobori FRONT 3F, 2-20-9, Hatchobori, Chuo-ku, Tokyo 104-0032, Japan
Phone: 81-3-3206-1871 Fax: 81-3-3206-1873
Osaka Office
Higobashi Center Building 10F, 1-9-1, Edobori, Nishi-ku, Osaka-shi, Osaka 550-0002, Japan
Domestic Sales Department Phone: 81-6-6445-1223 Fax: 81-6-6445-1333
Overseas Sales Department[P2] Phone: 81-6-6445-0501 Fax: 81-6-6445-1333
Nagoya Sales Office
Hashimoto Building 5F, 1-9-10, Ikeshita, Chikusa-ku, Nagoya-shi, Aichi 464-0067, Japan
Phone: 81-52-752-8831 Fax: 81-52-752-8833
Hiroshima Sales Office
Otemachi Chuo Building 3F, 3-8-1, Otemachi, Naka-ku, Hiroshima-shi, Hiroshima 730-0051, Japan
Phone: 81-82-246-7532 Fax: 81-82-246-7597
Fukuoka Sales Office
Toshiba Fukuoka Building 16F, 2-4-1, Nagahama, Chuo-ku, Fukuoka-shi, Fukuoka 810-0072, Japan
Phone: 81-92-716-7090 Fax: 81-92-716-7091
Head Office and Shiga Factory
446-1, Otani, Hino-cho, Gamo-gun,
Shiga 529-1608, Japan
Phone: 81-748-52-2131
Fax: 81-748-52-8154[P1]
http://www.okm-net.co.jp/
Pioneering the future of uid control
TD-HIP-1711-01-J-PR
This manual suits for next models
1
Popular Control Unit manuals by other brands
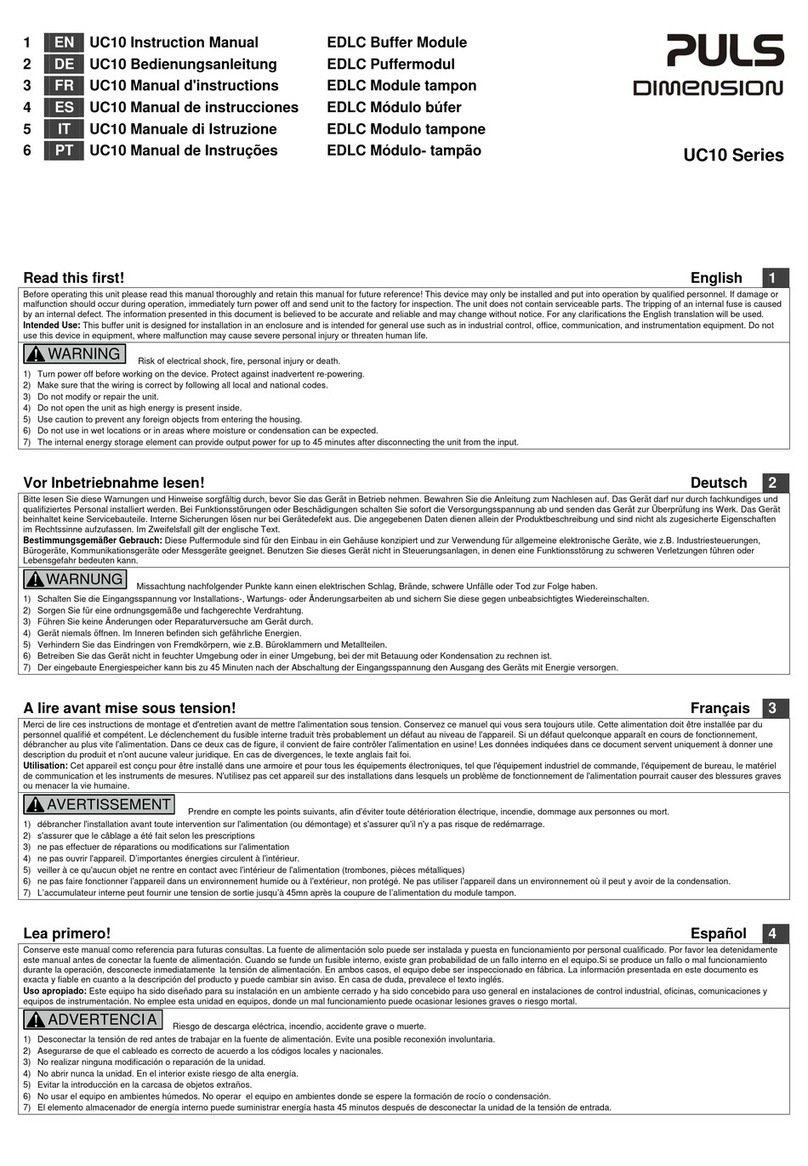
Puls
Puls DIMENSION UC10 Series instruction manual
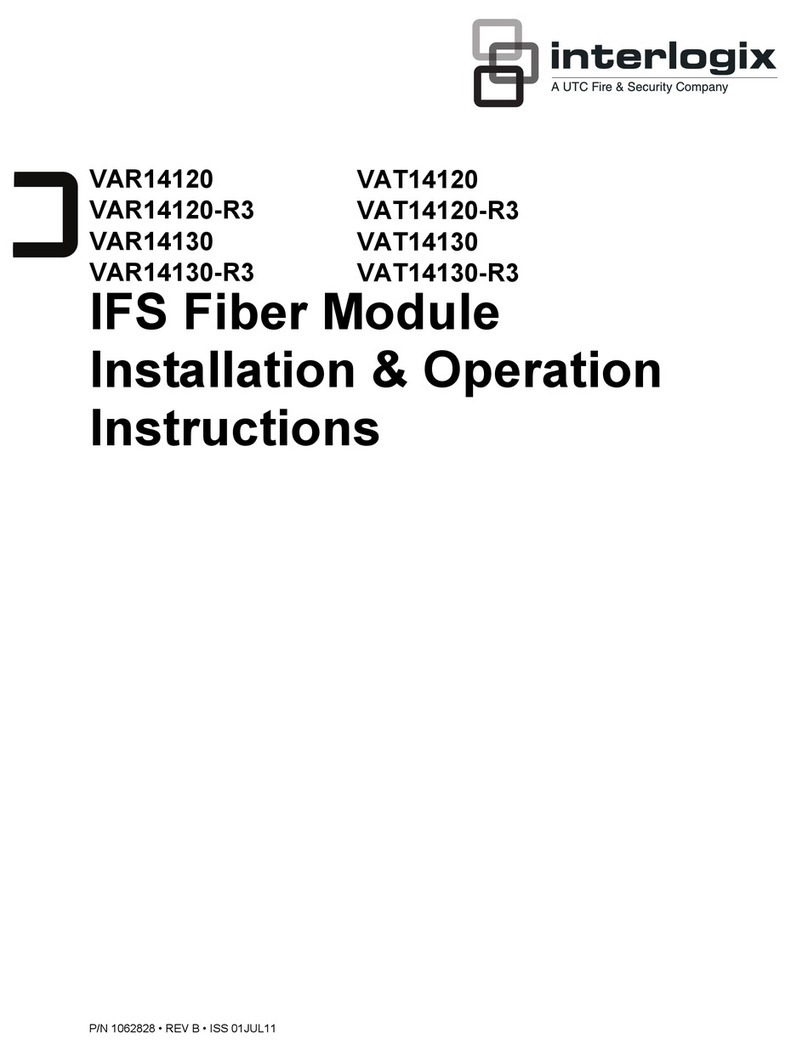
UTC Fire and Security
UTC Fire and Security interlogix VAR14120 Installation & operation instructions
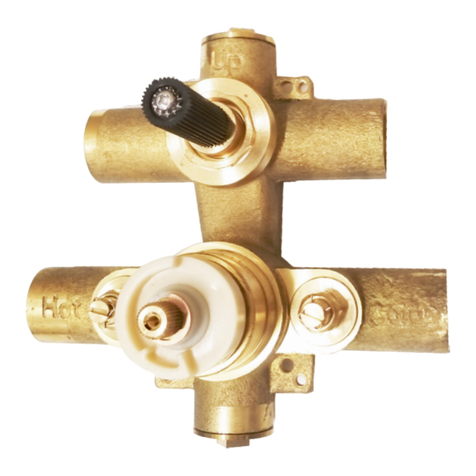
Aura
Aura ASR1202-OO installation manual
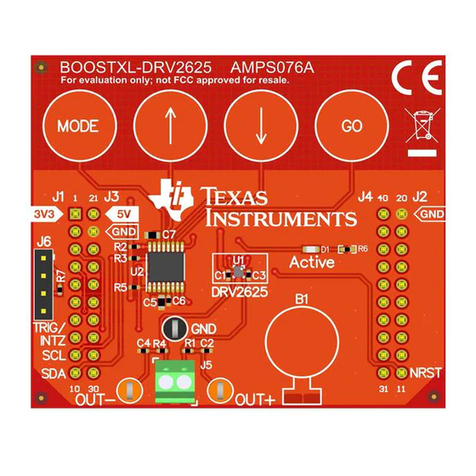
Texas Instruments
Texas Instruments DRV2625 Haptics BoosterPack user guide
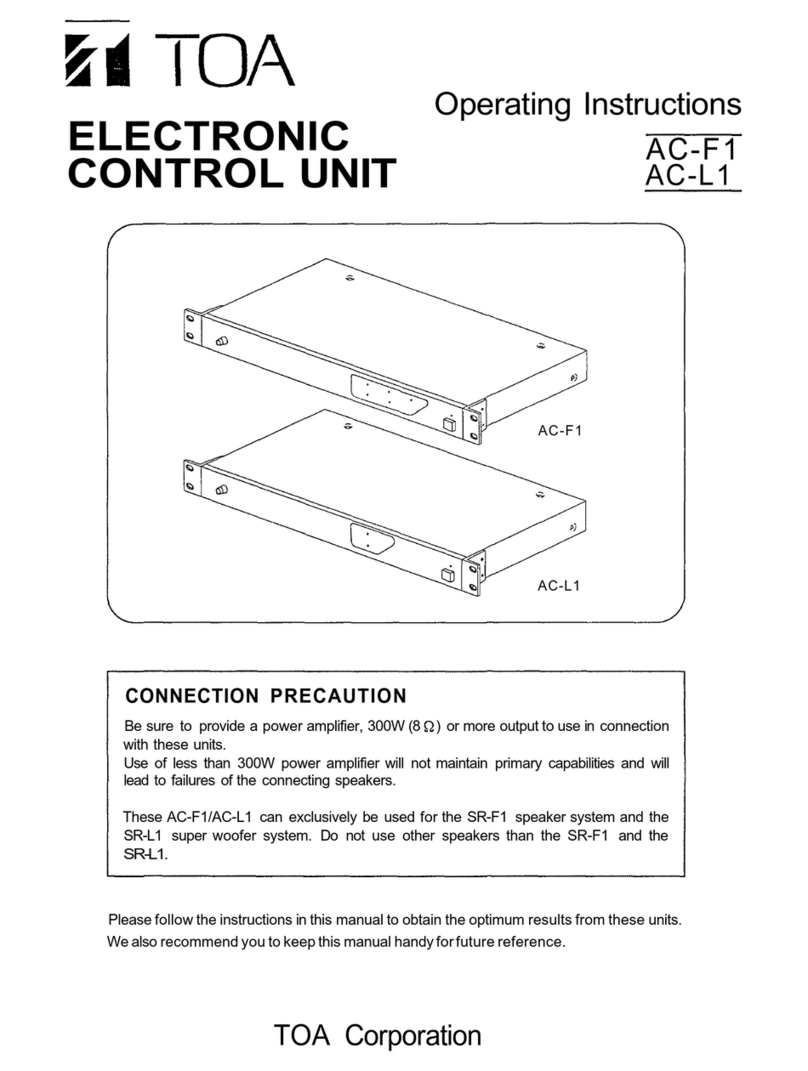
Toa
Toa AC-F1 operating instructions
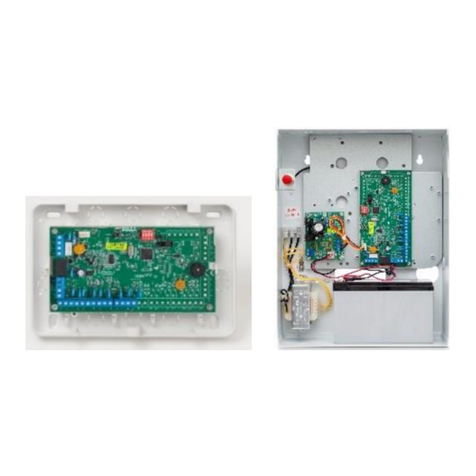
Pima
Pima ZEX508 installation instructions