Omega Technology Cleco 67EA Series User manual

For additional product information visit our website at:
https://dotcotool.com/product-category/cleco-tools/cleco-corded-electric-nutrunners-cleco-air-tools/
cleco-67-series-transducer-control-right-angle-corded-electric-nutrunners/
Service Manual
PL12EN-67EA
06/04/2013
67EA Series
Electronically Controlled Right Angle Nutrunner

Page 2
PL12EN-67EA
06/04/2013
Cleco®
General Information
For this Instruction Manual
This Instruction Manual is the Original Instruction Manual intended for all persons who will operate and maintain
these tools.
This Instruction Manual
provides important notes for the safe and efcient use of these tools.•
describes the function and operation of the 67EA series tools.•
serves as a reference guide for technical data, service intervals and spare parts ordering.•
provides information on optional equipment.•
Identication text:
67EA represents all models of the DC electric right angle nutrunner as described in this manual
Ú indicates a required action
• indicates a list
<..> indicates a reference number from the exploded parts drawings
Arial indicates an important feature or instruction written in Arial Bold
Identication graphic:
¢indicates a directional movement
òindicates a function or force
Copyright protection:
Apex Tool Group, LLC reserves the right to modify, supplement or improve this document or the product without
prior notice. This document may not be reproduced in any way, shape or form, in full or parts thereof, or copied
to another natural or machine readable language or to a data carrier, whether electronic, mechanical, optical or
otherwise without the express permission of Apex Tool Group, LLC.

Page 3
PL12EN-67EA
06/04/2013
Cleco®
Nomenclature
67 E A XXXX XXX
Tool Series
67
Motor Style
E = Brushless Electric Motor
Tool Type
A = Right Angle
Maximum Torque Nm (rounded to nearest 5 Nm)
235 = 230 Nm
255 = 255 Nm
310 = 310 Nm
340 = 335 Nm
460 = 460 Nm
570 = 570 Nm
730 = 730 Nm
860 = 860 Nm
1035 = 1035 Nm
1340 = 1340 Nm
1700 = 1700 Nm
2010 = 2000 Nm
Attachment
AL6 = 3/4" Square Drive - Right Angle
AM6 = 3/4" Square Drive - Right Angle
ML6 = 3/4" Square Drive - Right Angle
AH8 = 1" Square Drive - Right Angle

Page 4
PL12EN-67EA
06/04/2013
Cleco®
Contents
1 Safety 6
1.1 Warning and notes................................................................................................. 6
1.2 Basic requirements for safe working practices ...................................................... 6
1.3 Operator training.................................................................................................... 7
1.4 Personal protective equipment .............................................................................. 7
1.5 Designated use...................................................................................................... 7
1.6 Codes and standards ............................................................................................ 7
1.7 Noise and vibration................................................................................................ 7
2 Scope of supply, transport and storage 8
2.1 Items supplied ....................................................................................................... 8
2.2 Transport ...............................................................................................................8
2.3 Storage .................................................................................................................. 8
3 Product description 9
3.1 General description ............................................................................................... 9
3.2 Operation and functional elements........................................................................ 9
3.3 Dimensional data................................................................................................. 10
4 Accessories 12
5 Before initial operation 14
5.1 Ambient conditions .............................................................................................. 14
5.2 Power supply ....................................................................................................... 14
5.2.1 m-Pro-400GC series global controller ................................................................. 14
5.3 Tool cable connection .......................................................................................... 15
5.3.1 Cable connection to 67EA ................................................................................... 15
5.3.2 Cable connection to controller ............................................................................. 15
5.3.3 Apply power to the tool ........................................................................................ 15
6 First operation 16
6.1 Puting into use.....................................................................................................16
7 Troubleshooting 17
8 Maintenance 18
8.1 Service schedule ................................................................................................. 18
8.1.1 Calculating a customer specic maintenance plan.............................................. 19
8.2 Lubricants ............................................................................................................ 19

Page 5
PL12EN-67EA
06/04/2013
Cleco®
Contents
9 Repair instructions 20
9.1 Transducer identication...................................................................................... 20
9.2 Gear train lubrication ...........................................................................................20
9.3 Angle head lubrication ......................................................................................... 20
9.4 Throttle lever alignment ....................................................................................... 21
9.5 Pinion gear setting (right angle attachments) ...................................................... 21
9.6 Backlash shim assembly ..................................................................................... 22
9.7 45019123 Adapter assembly ............................................................................... 23
10 Spare parts
10.1 67EA(---)AL6 Series Right Angle Nutrunner........................................................ 24
10.2 67EA(---)AM6 Series and 67EA310ML6 Right Angle Nutrunner ......................... 26
10.3 67EA(----)AH8 Series Right Angle Nutrunner ...................................................... 28
10.4 67EA Series Handle Assembly ............................................................................ 30
10.5 67EA(---)AL6 Double Stage Gearing Assembly ..................................................32
10.6 67EA(---)AM6 Series and 67EA310ML6 Triple Stage Gearing ........................... 34
10.7 67EA860AH8 Single Stage Gearing.................................................................... 36
10.8 67EA(----)AH8 Series Double Stage Gearing...................................................... 38
10.9 48056032 AL6 Attachment (3/4” Square Drive)................................................... 40
10.10 45037012 ML6 Attachment (3/4” Square Drive) .................................................. 42
10.11 45017010 AL6 Attachment (3/4” Square Drive)...................................................44
10.12.1 35A56033 AH8 Attachment (1/2” Square Drive ) Anle Head Assembly............... 46
10.12.2 35A56033 AH8 Attachment (1” Square Drive) Output Gearing Assembly........... 48
11 Technical data 50
11.1 67EA Specications............................................................................................. 50
12 Service 51
12.1 Replacement parts .............................................................................................. 51
12.2 Tool repairs .......................................................................................................... 51
12.3 Warranty repairs .................................................................................................. 51
13 Disposal 52

Page 6
PL12EN-67EA
06/04/2013
Cleco®
Safety
1 Safety
1.1 Warnings and notes
Warning notes are identied by a signal word and a pictogram.
The signal word indicates the severity and probability of the impending danger.•
The pictogram indicates the type of danger.•
---------------------------------------------------------------------------------------------------------------------------------------
WARNING identies a potentially hazardous situation which, if not avoided, may result in serious
injury.
---------------------------------------------------------------------------------------------------------------------------------------
---------------------------------------------------------------------------------------------------------------------------------------
CAUTION identies a potentially hazardous situation which, if not avoided, may result in minor or
moderate injury or property and environmental damage.
---------------------------------------------------------------------------------------------------------------------------------------
---------------------------------------------------------------------------------------------------------------------------------------
NOTE identies general information which may include application tips or useful information but no
hazardous situations.
---------------------------------------------------------------------------------------------------------------------------------------
---------------------------------------------------------------------------------------------------------------------------------------
Important information that must be read and understood by all personnel installing, operating or
maintaining this equipment.
---------------------------------------------------------------------------------------------------------------------------------------
1.2 Basic requirements for safe working practices
All personnel involved with the installation, operation or maintenance of these tools must read and
understand all safety instructions contained in this manual. Failure to comply with these instructions
could result in serious injury or property damage.
These safety instructions are not intended to be all inclusive. Study and comply with all applicable
National, State and Local regulations.
---------------------------------------------------------------------------------------------------------------------------------------
Work Area:
ÚEnsure there is enough space in the work area.
ÚKeep the work area clean.
ÚKeep the work area well ventilated.
Personnel Safety:
ÚInspect the power cable for damage.
ÚMake sure the power cable is securely attached to the tool.
ÚEnsure a secure standing position and maintain balance.
ÚMake sure the throttle is positioned relative to the head so the throttle will not become wedged
against an adjacent object in the ON position due to torque reaction.
ÚIf the tool is to be reversed, locate the throttle in a neutral position to prevent entrapment.

Page 7
PL12EN-67EA
06/04/2013
Cleco®
Safety
1.2 Basic requirements for safe working practices (continued)
ÚKeep the tool clean and dry to provide the best possible grip.
ÚFirmly grasp the handle of the 67EA and apply the socket or bit to the application before starting.
ÚBe prepared for high short-term reaction torques.
Safety working with and around fastening tools:
ÚUse only power tool sockets and bits available from Apex Tool Group.
ÚInspect socket or bit for visible damage and cracks. Replace damaged items immediately.
ÚDisconnect the power supply before installing or replacing the socket or bit.
ÚDo not attach the socket or bit at a slant.
ÚMake sure the socket or bit is fully assembled on the drive and locked in postion.
---------------------------------------------------------------------------------------------------------------------------------------
1.3 Operator training
All personnel must be properly trained before operating the 67EA tools. The 67EA tools are to be
repaired by fully trained personnel only.
1.4 Personal protective equipment
When working
Wear eye protection to protect against ying metal splinters.•
Wear hearing protection•
Danger of injury by being caught by moving equipment.
Wear a hairnet•
Wear close tting clothing•
Do not wear jewelry•
1.5 Designated use
The 67EA is designed exclusively for fastening and releasing threaded fasteners. The 67EA is used in
conjunction wtih the following controllers:
Do not modify the 67EA, any guard or accessory.•
Use only with accessory parts which are approved by the manufacturer.•
Do not use as a hammer, pry-bar or any other improper usage.•
Do not use in areas where there is a risk of explosion.•
1.6 Codes and standards
It is mandatory that all national, state and local codes and standards be followed.
1.7 Noise and vibration
Noise level ≤ 75 dB(A) free speed (without load) according to ISO 12100: 2011
Vibration values < 2.5 m/s2according to ISO 12100: 2011
Nutrunner Controller
67EA series m-Pro-400GC controller with m-Pro-400-IT isolation transformer

Page 8
PL12EN-67EA
06/04/2013
2 Scope of supply, transport and storage
2.1 Items supplied
Check shipment for transit damage and ensure that all items have been supplied:
1 67EA
1 PL12EN-67EA instruction manual
1 Declaration of Conformity
1 Lubrication sheet
1 Warranty statement
2.2 Transport
Transport and store the 67EA in the original packaging. The packaging is recyclable.
2.3 Storage
For short term storage (less than 2 hours) and protection against damage:
ÚPlace the 67EA in a location on the workbench to avoid accidental depression of the button.
or
ÚSuspend the 67EA from a suitable balancer or tool positioner.
For storage longer than 2 hours:
ÚDisconnect the power supply from the 67EA
Cleco®
Scope of Supply, Transport and Storage

Page 9
PL12EN-67EA
06/04/2013
Cleco®
Product Description
3 Product description
3.1 General description
Right angle DC electric powered nutrunner•
Low inertia brushless motor•
Clockwise/counterclockwise rotation•
High visibility LEDs•
3.2 Operation and functional elements
This section describes the operational and functional elements of the 67EA.
61
24
5
3
Ref. Description
1 Power Connection
2 Start Button
3 Reversing Ring
4 LED Light Ring
5 Motor Assembly
6 Gearing
7 Right Angle Attachment
7

Page 10
PL12EN-67EA
06/04/2013
3.3 Dimensional data
Cleco®
Product Description
inches (mm)
25.80 (655)
Tool Cable
3.44
(87.4)
2.37 (60.2)
2.32 (58.9)
1.6
(40.6)
2.06 (52.3)
67EA235AL6
67EA255AL6
(3/4” Square Drive Output)
67EA310ML6
(3/4” Square Drive Output)
4.18
(106)
1.06
(26.9)
2.55 (65)
1.65
(42)
29.10 (739)
5.89
(150)
1.06
(26.9)
2.31 (58.7)
1.69 (42.9)

Page 11
PL12EN-67EA
06/04/2013
Cleco®
Product Description
3.3 Dimensional data (continued)
inches (mm)
67EA340AM6 67EA460AM6
67EA570AM6 67EA730AM6
(3/4” Square Drive Output)
3.07 (78)
2.13
(54.1)
31.35 (796)
6.39
(162)
1.38
(35.1)
2.75 (69.9)
1.88 (47.8)
9.34
(237)
0.70
(17.8)
24.69 (627)
0.88
(22.4)
3.00 (76.2)
3.25
(82.6)
1.81 (46)
2.29 (58.2)
1.41 (35.8)
67EA860AH8 67EA1035AH8
67EA1340AH8 67EA1700AH8
67EA2010AH8
(1” Square Drive Output)

Page 12
PL12EN-67EA
06/04/2013
Cleco®
Accessories
4 Accessories
Tool Cable (optional length)
Tool Cable - Inline Swivel (optional length)
Tool Cable - Right Angle Swivel (optional length)
Tool Cable Extension (optional length)
Refer to section 10.4 for part numbers
Tool and Cable Tester
Part Number: 961024
Tool and cable tester (tool memory programming)
Part Number: 542991
Tool and cable tester
Lever Extension Kit
Part Number: 541757 (non-swivel)
Part Number: 543414 (swivel)
Suspension Bail
Part Number: 1110909
Swivel Suspension Bail
Part Number: 35007004 (67EA...AL6)
Part Number: 48A17006 (67EA...ML6)
Part Number: 48A17006 (67EA...AM6)

Page 13
PL12EN-67EA
06/04/2013
Cleco®
Accessories
4 Accessories (continued)
Test Fixture
Part Number: 536185
Medium to Hard Torque
Belleville washer test xture is clamped in a vise
and used to test tools. Washers can be rearranged
to simulate “hard” or “soft” joints.
Range: 10 in.lbs (1.13Nm) - 100 ft.lbs. (135.6Nm)
Joint Simulator
Joint simulators are most frequently used to certify
the repeatability of nutrunners before being installed
on a production line and are also an excellent
means of testing nutrunners following repair.
The joint simulator can simulate and test the torque
output of nutrunners on both hard and soft joints.
Each joint simulator is supplied with a quantity of
spring washers which are used to test tool accuracy.
Torque per revolution is varied by stacking the
spring washers in different combinations.
Angle Head Cover
Part Number: 205838 (67EA...AL6)
Extension Assembly
Part Number: 48316033 (67EA...AL6)
Ft. Lbs. Nm in. mm in. mm in. mm
550006 12-220 15-300 10.4 264 16.0 406 26.5 667
Length
Torque Range
Width
Height
Part
Number

Page 14
PL12EN-67EA
06/04/2013
Cleco®
Before Initial Operation
5 Before initial operation
5.1 Ambient conditions
Ambient temperature: 32°F (0°C) to a maximum of 104°F (40°C)
Acceptable relative humidity: 0% to 80%, non-condensing
Working altitude up to 3281 ft. (1000m) above sea level
5.2 Power supply
Power for the 67EA series nutrunner is provided by networking it with a tool controller.
5.2.1 m-Pro-400GC series global controller
m-Pro-400GC
Series
Isolation Transformer
544185PT
Incoming
Power
115/230
VAC
67EA Series Nutrunner
Air-Lb Cable
Matrix Tool
Cable
542778-XM
Power
Cable

Page 15
PL12EN-67EA
06/04/2013
5.3 Tool cable connection
5.3.1 Cable connection to 67EA
Insert the tool connection end of the cable
into the 67EA handle. Align the key on the
cable connector with the switch actuator
on the tool handle. This will allow the
key to engage the mating slot inside the
handle. Thread the cable collar into the
tool handle and tighten securely.
5.3.2 Cable connection to controller
Connecttheotherendof thecable tothetool
connector on the controller. Make certain
the collar on the controller tool connector
is pushed in towards the controller. Align
the connector patterns of the tool cable
and controller connector. Push the cable
connector into the controller connector
and pull the collar towards the cable to
lock the cable connector in position.
5.3.3 Apply power to the tool
Refer to the controller manual for tool
operation.
Cleco®
Before Initial Operation
Switch Actuator
Key Cable
Collar
Collar
Connector
Patterns

Page 16
PL12EN-67EA
06/04/2013
Cleco®
First Operation
6 First operation
6.1 Putting into use
A reaction bar and bracket must always be used in high torque applications above 50 ft.-lbs. (68 Nm) or
in closed-quarter areas where entrapment and injury to hands or ngers could occur.
ÚMake sure the tool cable is securely attached to the tool and controller.
ÚMake sure controller is powered on and properly programmed (refer to controller manual)
ÚMake sure the reverse ring is in the correct position.
ÚPlace the socket or bit on the application and depress the switch actuator to start the rundown.
ÚWhen the tool shuts off, release the switch actuator.
ÚRemove the tool from the application.
Application
Spindle Rotation
Torque Reaction

Page 17
PL12EN-67EA
06/04/2013
Cleco®
Troubleshooting
7 Troubleshooting
Malfunction Possible causes Remedy
Start switch faulty Replace start switch
No speed (RPM) programmed Program a speed for all active stages
Controller is waiting for a Tool Enable
Make the Tool Enable connection or disable Tool
Enable if not required
Faulty cable Replace or repair cable
Bent pins in cable or tool Straighten pins or replace faulty connector
No speed programmed for Reverse Enter a speed (RPM) for Reverse
Faulty reverse switch Replace Start/Reverse switch assembly
Faulty cable Replace or repair cable
Bent pins in cable or tool Straighten pins or replace faulty connector
Tool shuts off at desired
torque but reports no angle
Angle Threshold value is set to high
Correct fastening strategy programming to
include a lowe Angle threshold value
Operator is releasing the start switch
before the controller stops the tool
Verify that the operator is keeping the start
switch depressed through the entire rundown
Rundown time exceeds the default
time value of 10 seconds
Increase the rundown timer to exceed the
rundown time required
Tool has reached Angle High Limit
before reaching the Torque target
Check the fastening strategy programming to
verify that the Torque target and Angle High Limit
are correct. If the parameters are correct, see if
something has changed in the assembly that
would cause an incorrect torque/angle
relationship.
Tool won't change speeds
Speeds are the same in all applicale
stages
Verify that all speeds and shift points are correct
in the stages that are being used.
All the lights on the tool
begin flashing when the
reverse collar/switch is put
in reverse
This is a normal function as set by
the default parameters. If the lights
are not flashing when the tool is in
reverse the "Blinking Lights in
Reverse" check box is not selected.
Check selections in the ADVANCED menu, Tool
Settings tab.
The tool tranducer is not returning to
a zero torque condition
Transducer has been over-stressed and needs
replacement
Faulty wiring in tool or cable
Check tool with different cable to see if the
condition remains. Transducer offset and full
scale voltages can be seen in the
DIAGNOSTICS menu.
Tool has not been accepted in the
TOOL SETUP screen
Verify that the tool has been accepted in the
TOOL SETUP screen. Before accepting the tool,
the message "Needs User Acceptance" should
appear in the tool overview screen. Verify that
the correct tool is highlighted when going to Tool
Settings to accept the tool.
Faulty cable is preventing the tool
from being "seen" by the controller
Replace or repair cable
Torque calibration factor in Tool
Settings in the TOOL SETUP menu
needs to be adjusted
Adjust torque calibration factor using the formula
below:
New Cal Facor = (External Reading/Tool
Reading) x Existing Torque Calibration Facor
Custom head has been added to the
tool and the tool needs updated tool
memory information
Tool memory must be programmed to
accommodate new attachment
Tool cable will not fit in tool
handle
Wrong cable. Tools used with Global
Controller utilize an Air-lb connector,
which has a smaller ID housing in the
tool than previous Matrix style
connector housings.
Utilize the correct cable for the tool being used.
Torque reported by the
controller doesn't match the
torque reported by an
external transducer
Tool does not start
Tool runs forward but not
Reverse
Tool shuts off prematurely
Warning message in the
RUN screen reports
"Transducer Offset Error"
"Tool Not Connected"
message appears in the
RUN screen

Page 18
PL12EN-67EA
06/04/2013
Cleco®
Maintenance
8 Maintenance
---------------------------------------------------------------------------------------------------------------------------------------
Danger of injury from accidental start up or electrical shock.
Disconnect the tool cable from the tool and controller before performing any maintenance.
---------------------------------------------------------------------------------------------------------------------------------------
8.1 Service schedule
Only qualied and trained personnel are permitted to perform maintenance on these tools.
Regular maintenance reduces operating faults, repair costs and downtime. In addition to the following
service schedule, implement a safety related maintenance program that takes the local regulations for
repair and maintenance for all operating phases of the tool into account.
This maintenance schedule uses values that are valid for most applications. For a specic maintenance
interval, refer to 8.1.1 Calculating a customer-specic maintenance plan.
Maintenance
Interval
Rundowns
Daily Daily
Visual inspection of all cables and connections
Visual inspection of the 67EA tool
Check the tool for excessive vibration or unusual noises
Visual inspection of all external components of the tool
W1 100,000
Inspect the tool cable for damage or wear
inspect the square drive output spindle for damage or wear
Inspect the tool cable connection for a secure fit
Check the maximum free speed
W2 500,000
Visual inspection of disassembled 67EA tool
Check individual parts for wear or damage and replace if necessary
Clean and lubricate angle head, gearing and motor bearings
Check and recalibrate transducer (67EA models)
W3 1,000,000
Visual inspection of disassembled 67EA tool
Check individual parts for wear or damage and replace if necessary
Clean and lubricate angle head, gearing and motor bearings
Check and recalibrate transducer (67EA models)
Designation

Page 19
PL12EN-67EA
06/04/2013
Cleco®
Maintenance
8.1.1 Calculating a customer specic maintenance plan
A service interval W(1, 2, 3) depends on the following factors:
8.2 Lubricants
For proper function and long service life, use of the correct grease is essential.
Grease lubricants recommended for this tool.
Example for service interval W2:
After 500,000 rundowns (V),
a specific rundown time of 1.8 seconds (T1)
with an actual fastening time of 3 seconds (soft joint) and
3 completed shifts per day and 750 rundowns per shift.
V x T1 500000 x 1.8
T2 x S x VS 3 x 3 x 750
You will need to perform the maintenance indicated as W2 after an operating time of 133 days.)
W (1, 2, 3) =
W2 =
= 133 (days)
Factor
Value assumed in
"Service Schedule"
Description
V
V1 = 100,000
V2 - 500,000
V3 = 1,000,000
Number of rundowns after a maintenance measure is prescribed by Apex
Tool Group.
T1 1.8 seconds Specific rundown time, measured in life and endurance tests.
T2 2 seconds Actual rundown time, depending on the hardness of the joint.
S1; 2; 3 Number of shifts per day.
VS 750 Number of rundowns per shift.
T2, S and VS are variable factors and can differ depending on the specific application.
Part No. Packaged Designation Vendor
544076 2 oz. (0.06 kg) Molytex EP2 Texaco
544077 16 oz. (0.45 kg) Molytex EP2 Texaco
540395 2 oz. (0.06 kg) Magnalube-G Carleton-Stuart Corp.
513156 16 oz. (0.45 kg) Magnalube-G Carleton-Stuart Corp.
541444 2 oz. (0.06 kg) Rheolube 363AX-1 Nye Lubricants, Inc.
541445 16 oz. (0.45 kg) Rheolube 363AX-1 Nye Lubricants, Inc.

Page 20
PL12EN-67EA
06/04/2013
Cleco®
Repair Instructions
9 Repair instructions
9.1 Transducer identication
Transducers are not interchangeable. Verify the part number stamped on the transducer with the
transducer part number indicated in the parts list to assure the correct transducer is being used.
9.2 Gear train lubrication
Lubricate the gearing components with the grease recommended on the gearing parts list pages.
DO NOT SUBSTITUTE GREASES
9.3 Angle head lubrication
Lubricate the angle head components with the grease recommended on the angle head parts list
pages.
DO NOT SUBSTITUTE GREASES
Part number
stamped on
this end
Idler
Gears
Pinion
Gears
Ring Gears
Grease Grease
542883-xxx 542884-xxx Part number
stamped on
this end
Pinion
Gears
Bevel
Gears
Grease
Grease
Bearings
This manual suits for next models
5
Table of contents
Other Omega Technology Power Tools manuals
Popular Power Tools manuals by other brands
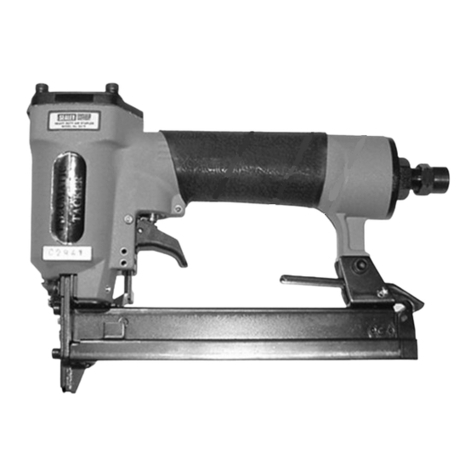
Sealey
Sealey SA79R instructions
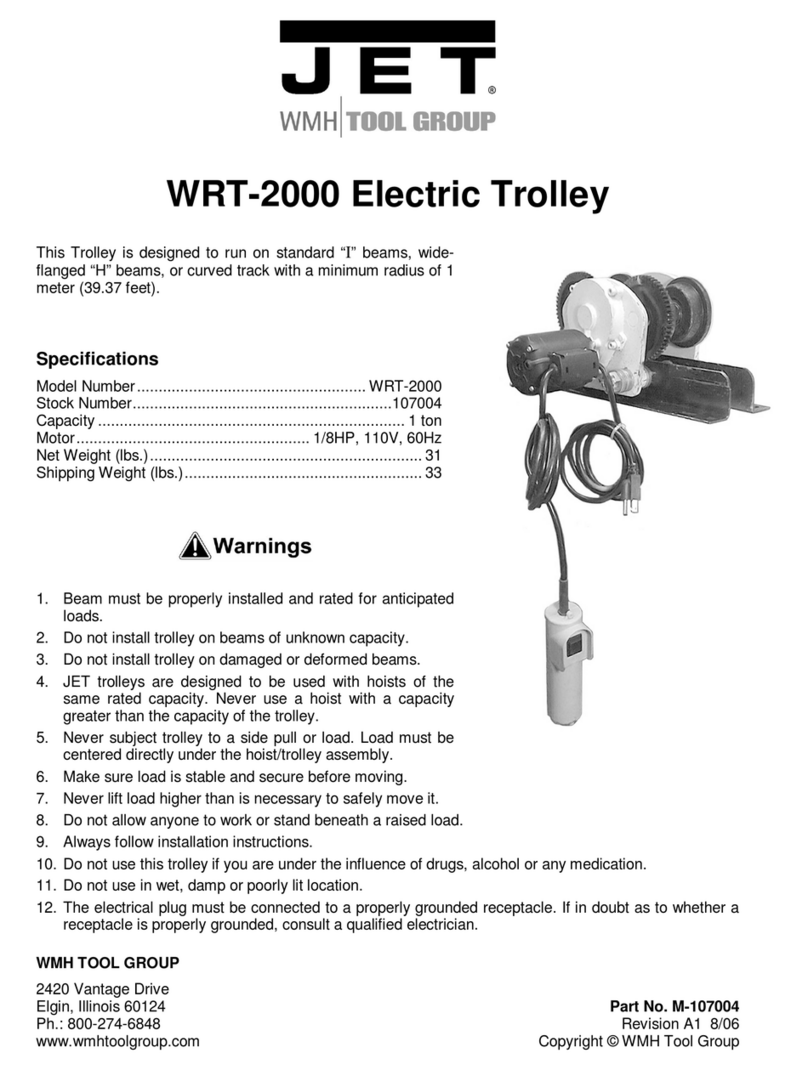
Jet
Jet WRT-2000 Specifications and parts list
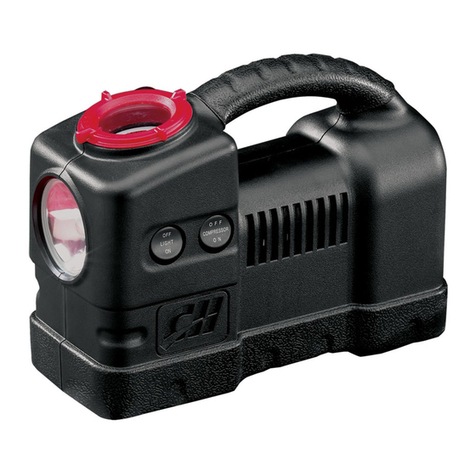
Campbell Hausfeld
Campbell Hausfeld RP3200 operating instructions

RIDGID
RIDGID RP 10-B operating instructions
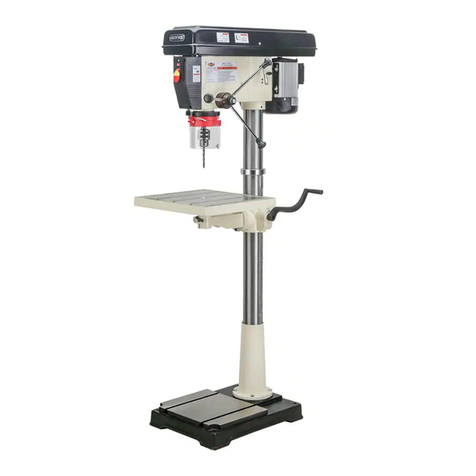
Shop fox
Shop fox SHOP FOX M1039 owner's manual
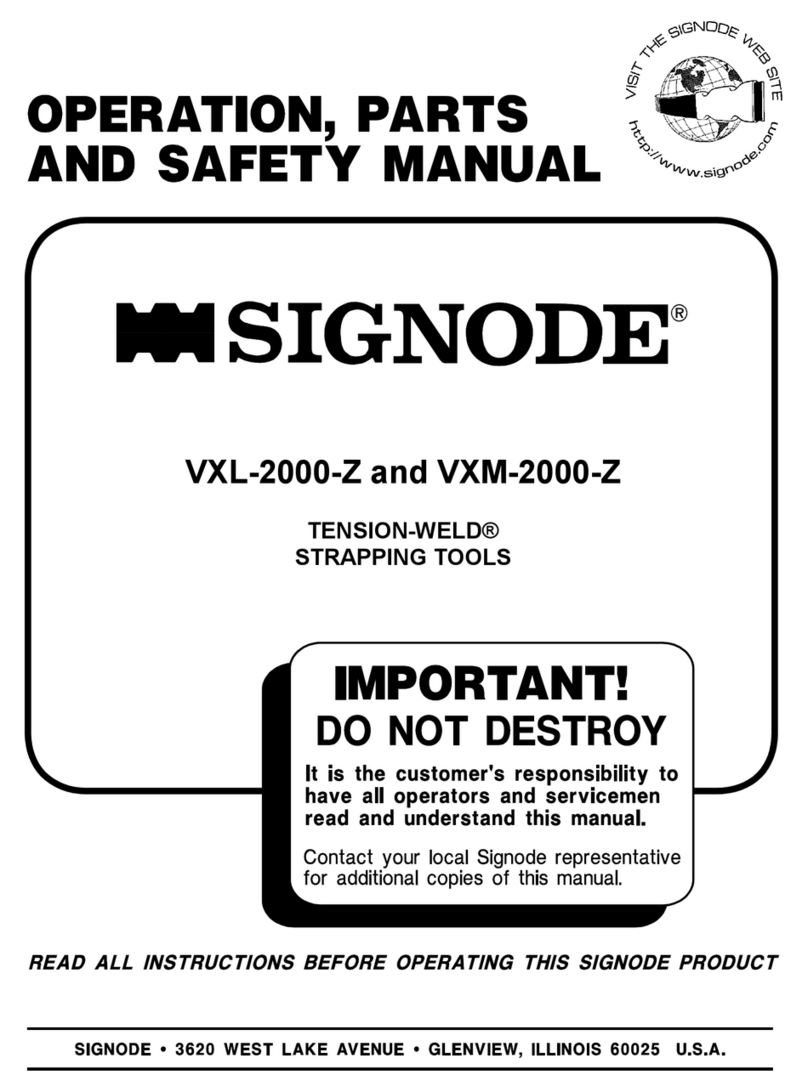
Signode
Signode TENSION-WELD VXL-2000-Z Operation, parts and safety manual