Omega NOBEL 22 DV CSA Instructions for use

63 Morrow Road, Barrie, Ontario, Canada L4N 3V7 Phone: 1-800-668-8448 Fax: (705) 721-8646 www.omegacompressors.com
For us, it's not just business. It's personal.
Rotary Screw
Instruction & Maintenance Manual
Model: NOBEL 22 DV CSA
Please ensure to read this manual before installation and refer back to manual when performing maintence.
If you require assistance or have any questions regarding the installation or maintenance of your Omega Compressor please do not
heisatate to contact our Customer Service department at 1-800-668-8448.

3
EN
GENERAL INFORMATION
OUTFIT
The following accessories are supplied with the compressor:
• use and maintenance manual
• anti-vibration elements
• electric box panel key
• oil/condensate exhaust tube
Check that the above accessories are available. Once the goods have been delivered and accepted, no complaints are accepted.
CONDITION OF THE MACHINE WHEN SUPPLIED
Every compressor is shop tested and delivered ready to be installed and to be set at work.
The oil for first filling used is: FSN Original Oil.
INDEX
GENERAL INFORMATION...............................................3
OVERALL DIMENSIONS .................................................5
SAFETY INDICATIONS....................................................6
INSTALLATION ................................................................9
TECHNICAL FEATURES ............................................... 11
START-UP AND OPERATION........................................12
MAINTENANCE .............................................................25
TROUBLE SHOOTING ..................................................29
WIRING DIAGRAM ........................................................30
NOBEL DV 22 CSA - Cod.197EE0622ML - Rev.1 03/2019

5
1360
600
250
147,5
615
640
580
480 106
1365
880
535
1”1/4
50
665
EN
OVERALL DIMENSIONS
NOBEL DV 22 CSA - Cod.197EE0622ML - Rev.1 03/2019

6
6
EN
SYMBOLS USED IN THE MANUAL
Several symbols have been used inside the manual, which highlight dangerous situations, give practical advice or simple
information. These symbols are found at the side of a text, at the side of a figure or at the top of a page (in this case they refer
to all subjects considered on the entire page).
Pay attention to the meaning of the symbols.
SYMBOLS USED ON THE COMPRESSOR
Several different labels are applied to the compressor. Their function is most of all to highlight any hidden dangers and to indicate
correct behaviour during use of the machine or in particular situations.
It is of fundamental importance that they are respected.
ATTENTION!
Highlights an important description regarding:
technical interventions, dangerous conditions,
safety warnings, advice and/or very important
information.
MACHINE AT A STANDSTILL!
Every operation highlighted by this symbol must
only be carried out with the machine at a standstill.
REMOVE VOLTAGE!
It is compulsory to deactivate the electric power
supply to the machine before carrying out any
interventions on the machine.
SPECIALISED STAFF!
All interventions highlighted with this symbol
must be carried out exclusively by a specialised
technician.
Warning symbols Prohibition symbols
High temperature risk
Electric shock risk
Risk from hot or dangerous gases in the work
area
Pressurised container
Moving mechanical parts
Maintenance in progress
Machine with automatic start-up
Do not open hatches when the machine is
functioning
If necessary, always use the emergency stop
button and not the line isolating switch
Do not use water to put out fires on electrica
appliances
Obligation symbols
Carefully read the user instructions
GENERAL WARNINGS
• The rotating compressors are destined for arduous and continuous industrial use. They are particularly adapt for application
in industries where a large consumption of air is requested for long periods of time.
• The compressor must be used exclusively as indicated in this manual, which must be kept carefully in an easily accessible
place known to everyone, as it must remain with the machine for its entire duration.
• The company in which the compressor is to be installed must appoint a person in charge of the compressor itself. Controls,
adjustments and maintenance interventions are under his responsibility: if this person must be replaced, the substitute must
read the user and maintenance manual and any notes made regarding technical and maintenance interventions carried out up
to this time.
SAFETY REGULATIONS
read this page carefully before carrying out any intervention on the compressor
STORM 38 VS - Cod.197DD9910 - Rev.2 01/2016NOBEL DV 22 CSA - Cod.197EE0622ML - Rev.1 03/2019

7
1
3
4
6
2
5
4
20....
TYPE
Modello
CODE
Codice
S/N
L/MIN
CFM
bar =
psi =
Tank =
RPM
kg =
dB(A)
V = Hz = A = kW = HP =
EN
SAFETY REGULATIONS
read this page carefully before carrying out any intervention on the compressor
TO DO:
Make sure that mains voltage corresponds to the voltage indicated on CE plate and that cable of suitable cross-section are
used for electric connections.
Always check oil level before starting the compressor.
Be familiar with emergency stop control and all other controls.
Unplug the connector before any maintenance work, so to avoid accidental start.
Ensure that all parts have been correctly reassembled after any maintenance work.
Keep children and animals off the working area to avoid injuries caused by devices connected to the compressor.
Ensure that temperature of the working environment ranges between +2 and + 45 ºC. Compressor working temperature shall
range between 70÷85°C (20-25°C room temperature). Lower temperatures may causes condensate accumulation inside the
oil separator tank (inside the compressor).
Check for condensate and if necessary, drain it (see maintenance).
The compressor should be installed and operated in a non-explosive environment.
Allow at least 80 cm between the compressor and the wall so to allow free air flow to the fan.
Press the emergency button on the control panel only in case of actual need so as to avoid possible damages to people or the
very compressor.
When calling for technical assistance and/or advice, always mention model, code and serial number indicated on CE plate.
Always follow the maintenance schedule specified in the user’s guide.
DO NOT:
Do not touch inner parts and pipes as they are very hot during compressor operation and stay hot for a certain time after
compressor stops.
Do not position inflammable close to and onto the compressor.
Do not move the compressor when the tank is under pressure.
Do not operate the compressor if the power cable is damaged or defective or if connection is unstable.
Do not operate the compressor in wet or dusty environments.
Never aim the air jet at people or animals.
Do not allow unauthorized people to operate the compressor and give them all required instructions.
Do not hit fans with blunt objects as they might break during compressor operation.
Never operate the compressor without air filter.
Do not tamper with safety and adjusting devices.
Never operate the compressor when doors/panels are open or removed.
Do not strike the fans with contusive or metal objects as they could cause sudden breakage during functioning.
Do not allow the compressor to function without the filter and/or air pre-filter.
Do not tamper with safety and adjustment devices.
Never allow the compressor to function with the hatches/panels open or removed.
PRODUCT IDENTIFICATION
The compressor Your have purchased has its own CE plate showing the following data:
1. Manufacturer’s data.
2. Year of manufacture.
3. TYPE = name,
CODE = code,
SERIAL NO. = serial number (to be always mentioned when calling for technical assistance).
4. Tech data: air intake/air delivery, Max. operating pressure, Tank capcity , Rotations per minute, weight.
5. Voltage , frequency , absorption, power.
6. Noise level.
NOBEL DV 22 CSA - Cod.197EE0622ML - Rev.1 03/2019

9
1
13
11
15
1
10
14
8
7
5
6
1
17
18
2
3
10
12
4
16
20
12
9
1
19
EN
INSTALLATION
DESCRIPTION OF THE COMPRESSOR
ON GROUND
NOBEL DV 22 CSA - Cod.197EE0622ML - Rev.1 03/2019

10
10
2
3
EN
UNPACKING AND HANDLING THE MACHINE
When delivered, compressor top is protected by cardboard packing.
Wear suitable protective gloves and then cut outer straps and then remove cardboard from the top. Check the (outer) good
condition of the machine before moving the compressor. Visually check that no parts are damaged. Also ensure that all accessories
are available.
Lift the machine using a fork lift truck. Fit the anti-vibration elements into their proper seat and move the machine to the room
chosen for its location with maximum care.
Keep all packing materials at least for the warranty period for possible moving. In case of need, it will be safer for delivery to the
technical assistance dept.
Then, dispose of packing materials in compliance with current laws.
LOCATION (g. 2)
The room chosen for the installation of the compressor should meet
the following requirements and comply with what is specified in the
current safety and accident prevention regulations:
• low percentage of fine dust,
• proper room ventilation and size that allow room
temperature under 45° C. In the event of inadequate hot air
discharge, fit the exhaust fans as high as possible.
Condensate should be collected either into a container or a tank, or
a water/oil separator should be fitted.
CONDENSATE IS A POLLUTING MIXTURE! It must not be let into
the sewage.
The dimensions of the spaces are indicative only but it is advisable
to follow them as closely as possible.
INSTALLATION
DESCRIPTION OF THE COMPRESSOR
ELECTRICAL HOOK-UP (g. 3)
• The mains cable should have a cross-section suitable for the
machine power and should include no. 3 phase wires, no. 1 neutral
cable and no. 1 earth wire.
• Between the mains cable and the compressor control panel a
fused switch near the point where the cables go into the machine
is absolutely necessary. The switch should be at least at 1.7 m
from the ground.
• The switch (A) should be easily reached by the operator. The
cables should be of the approved type and installed with the following
grade of protection: minimum IP44.
N.B. To determine the cables cross-section follow the sizing
indications in compliance with the “VDE 0100, Part 430 and 523”
Standard, star-delta starter, 30 °C room temperature and cable length
lower than 50 meters.
1) Electrical equipment
2) Front panel
3) Lid
4) Electric fan
5) Oillter
6) Oilseparatorlter
7) Minimum pressure valve
8) Oil separator tank
9) Airlter
10) Air/Oil radiator
11) Electric motor
12) Control panel
13) Air intake outlet
14) Suction regulator
15) Screw compressor
16) Inverter
17) Thermostatic valve
18) Condensate separator
19) Safety valve
20) Emergency button
STORM 38 VS - Cod.197DD9910 - Rev.2 01/2016NOBEL DV 22 CSA - Cod.197EE0622ML - Rev.1 03/2019

11
NOBEL 22 DV CSA
kW/HP 22/30
bar g 7,5 9,5
type FS100
/
l/min 3600 3010
l/min 1170 1170
l 15 / 2
°C 8
kJ/h 75240
/
m3/h 3500
kW 0,65
mg/m3 2 - 4
type 180 B3B5
rpm 3600
kW 22
kW 25,7 25,1
kW/m3/min 7,12 8,21
% 92,7
IP 54
°C +2/+45
dB(A) 64 62
V/Ph/Hz 575/3~/60
V/Ph/Hz 24/1~/60
A29
-IP55 / F
- 1,15
°C 110
°C 105
A PTC
bar 14
mm 1365
mm 880
mm 1360
kg 650
G1-1/4“
EN
TECHNICAL FEATURES
Model
Technical features
Working pressure
Air-end
Transmission type
F.a.d. (ISO 1217 - Annex E) Max
F.a.d. (ISO 1217 - Annex E) Min
Oil quantity / topping-up
Max final air temperature above ambient
Re-claimable heat
Fan type
Fan flow rate
Rated motor power cooling fan
Oil carry over
Main electric motor
Main Motor speed
Nominal main motor power
Max. power absorbed,
ventilation included
Specific Power
Main Electrical Motor efficiency
Electrical box protection class
Min and Max working ambient temp.
Noise level (according Pneurop/Cagi
PN2CPTC2)
Electrical data
Voltage
Auxiliary voltage
Max. absorbed current,
ventilation included
Main motor enclosure/
Insualtion class
Main motor service factor
Protection devices
Max oil temperature
Pre-alarm Oil temperature
Motor thermal relay setting
Safety valve setting
Dimensions and weight
Length
Width
Height
Weight
Air outlet size
Direct
Radial
NOBEL DV 22 CSA - Cod.197EE0622ML - Rev.1 03/2019

12
12
4
EN
START-UP AND OPERATION
1 - CHECKS TO BE CARRIED OUT PRIOR TO START-UP
N.B.: The customer is responsible for installing the machine and making the required electrical and air connections.
Initial system start-up must be carried out by skilled personnel who will make the various checks required and follow
the respective instructions.
Each machine was thoroughly tested at the plant before shipping.
You should monitor the compressor during the first hours of operations to check for faults.
• Follow the installation prescriptions given in the previous chapters.
• Remove all packaging materials and tools.
• Connect the compressor to the distribution line as shown in paragraphs.
• Check the oil level in the tank: refer to section “Maintenance, oil control and topping up.” In the event of low oil level, top up
with FSN Original Oil.
• Check for correspondence between the compressor plate data with the actual specifications of the electrical system.
A variation of ± 5% with respect to the rated value is allowed.
• Connect the machine to the electrical system as described in the previous chapters.
Compliance with the correct voltage phase sequence is
fundamental since this defines the direction of rotation of
the motor. The direction of rotation must be that indicated
by the adhesive label located to the side of the screw unit
(see picture).
Note that even a few seconds of incorrect rotation may
cause serious damage.
A phase sequence checking device to prevent mistakes is
fitted in the electrical panel.
Now the machine is ready to go.
Before starting the machine read the following sections
and the chapter on maintenance operations for in-depth
knowledge of the machine.
STORM 38 VS - Cod.197DD9910 - Rev.2 01/2016NOBEL DV 22 CSA - Cod.197EE0622ML - Rev.1 03/2019

13
1
2
3
8
olio / oil
aria+olio / air+oil
aria / air
6
5
4
9
3
11
7
9
10
EN
START-UP AND OPERATION
WORKING CYCLE
• At the end of the starting cycle, the compressor reaches maximum operating speed and starts to compress air in the
tank (4).
• At a value of - 0.5 bar operating pressure, the compressor begins to modulate the motor rotation frequency (max. 100%, min.
50%) in such a way as to maintain constant the selected pressure depending on the flow of air.
• The compressed air cannot outlet of the minimum pressure valve (5) which is adjusted at about 4 bars.
• The compressed air compresses the oil inside the tank (4) and forces it to flow through the tubing (7) towards the thermostatic
filter (10). If the oil temperature is lower than the temperature calibration of the thermostatic element, the oil returns to the screw
through the hoses (9) . If the oil temperature is higher than the temperature calibration of the thermostatic element, the oil is
flowing in the radiator (8) where it is cooled.
• Subsequently, the oil passing through the pipe (9) reaches the compressor, mixing with the suction air and thereby creating
an air/oil mixture which ensures sealing and lubrication of the moving organs of the compressor.
• The air/oil mixture goes back to tank (4), where air and oil are first separated by centrifugation and then by the oil separator
filter (6).
• Therefore only air exits the tank (4), which through the tubing (3) reaches the air radiator (8) passing through the condensate
separator and going to the network.
• The condensate recovered in the condensate separator (8) is automatically released by the timed solenoid valve (12)
• Min. pressure valve (5) serves also as a check valve.
• Compressor delivers compressed air to outer air tank.
• Once min. value is reached, pressure gauge starts timer and powers off solenoid valve (1) of regulator.
• Regulator (2) closes and compressor stops compressing and starts idling.
• Timer continues counting until reaching set value and, if pressure is unchanged, stops the electric motor. If pressure drops to
minimum value set on controller, solenoid valve is powered and opens before timer counting is over.
• Regulator (2) opens and compressor operates under normal load; timer is reset.
• This cycle is automatically repeated.
NOBEL DV 22 CSA - Cod.197EE0622ML - Rev.1 03/2019

14
14
(6&
5(6(7
(17(5
ESC
RESET
ENTER
5
EN
START-UP AND OPERATION
COMMAND AND PROGRAMMING KEYPAD
1 Scroll menu \ change values keys
2 Enter key – to confirm settings
3 Esc key – to return to the previous menu
4 Reset – to silence the alarms
5 0 / Off key – shut-down - STOP
6 I / On key – start-up - START
Compressor Functioning
Start-up procedure:
Press the START (I) button. If no alarms are on, the start-up cycle activates:
Stand-by for start-up: the control unit is waiting to verify the following conditions before starting the compressor:
-If the machine was switched off or a previous stoppage was executed, the control unit waits 15 seconds before
starting the compressor.
-The control unit waits for the pressure to go below the value set in the “Load pressure” set before starting the
compressor. (“STAND -BY” is displayed)
- Star compressor start-up: the line and star remote control switch for the time defined in the parameter “Star/delta
time” (“NO LOAD ” is displayed)
-Transition from star to delta: the remote control switch for the line remains active, while the star relay is deactivated;
this phase lasts for the set time of 20 msec. (“NO LOAD ” is displayed)
-Fully operational compressor start-up: the line relay is maintained active and also the delta relay is activated; this
phase lasts for the time set in the parameter “Load delay”. (“NO LOAD ” is displayed)
-Compressor loading phase: the solenoid valve relay of the load is active. This phase lasts until the pressure
measured reaches the pressure set in the parameter "No load pressure". ("LOADED" is displayed)
-Compressor no load phase: the solenoid valve relay of the load is deactivated; this phase lasts as long as set in
the parameter “No load time”. After this, the cycle re-starts from the Start-up stand-by phase
(“NO LOAD ” is displayed)
2 - CONTROL PANEL
The compressor is fitted with a “control panel” for setting up and monitoring machine operation. The operating parameters were
entered by the Manufacturer during “testing”. The parameters were tested for several hours in the various operating conditions.
The features offered by this electronic control system includes:
• Fully automatic compressor operation.
• Real-time operating parameter display.
• Customization operating parameter.
• Programming of compressor operation on a daily or weekly basis.
• Programming and signalling of the Manufacturer’s maintenance schedule.
• Machine self-protection system to signal fault pre-alarms and automatically stop the machine in the event of serious problems.
• Remote machine control.
• Possibility of connecting the compressor to other similar compressors with the same controller for integrated management
of the set of machines.
• Remote compressor monitoring via personal computer and dedicated software (optional).
STORM 38 VS - Cod.197DD9910 - Rev.2 01/2016NOBEL DV 22 CSA - Cod.197EE0622ML - Rev.1 03/2019

15
(6&
5(6(7
(17(5
EN
START-UP AND OPERATION
Stoppage procedure:
- Press the STOP button (O) to activate the stoppage
procedure. The load solenoid valve is deactivated and the
no load cycle starts for the time set in the parameter
“Stoppage time” (“NO LOAD ” and then “STATUS -
OFF” are displayed)
Remote pressure
- By enabling remote pressure control using the parameter
“Enable remote”, the remote pressure digital input is is
enabled. The control unit in this configuration keeps the
remote input under control like an external pressure switch.
Furthermore, it is also controlled that this acts within the range
of the values set (load set, no load set or working and delta
pressure in the event of an inverter). If the set pressure is
surpassed due to an anomaly on the remote pressure control,
the control unit will take command of the compressor cycle by working with the internal set values, signalling a “Remote press.
err.”.
If the anomaly is solved, pressure control is again entrusted to the remote pressure input, (at this point the alarm can be reset).
ON/OFF remote
Using the “ON/OFF from remote” the compressor can be activated remotely, by pressing the Start (I) key. Provided no alarms
are on, remote start-up takes place. The remote command has less priority over the Start (I) and Stop (O) keys on the panel.
Compressor Functioning with an Inverter
Start-up procedure:
Press the START (I) button. If no alarms are on, the start-up cycle activates:
-Stand-by for start-up: the control unit is waiting to verify the following conditions before starting the compressor:
-If the machine was switched off or a previous stoppage was executed, the control unit waits 15 seconds before starting the
compressor.
-The control unit waits for pressure to go under the value set in the “Working Pressure-Working Delta/2” set before starting the
compressor. (“STAND-BY” is displayed)
-Compressor start-up: the line remote control switch is powered
-Fully operational compressor start-up: the line relay is maintained active and also the delta relay is activated; this phase lasts
for the time set in the parameter “Load delay”. (“NO LOAD ” is displayed)
-Compressor loading phase: the solenoid valve relay of the load is active. This phase lasts until the pressure measured
reaches that set in the parameter “Working Press. + Working Delta/2”.
(“LOADED ” is displayed)
-Compressor no load phase: the solenoid valve relay of the load is deactivated; this phase lasts as long as set in the parameter
“No load time”. After this, the cycle re-starts from the Start-up stand-by phase
(“NO LOAD ” is displayed)
In this phase, the control unit executes a control algorithm to keep the pressure as close as possible to the working pressure
by adapting the speed of the motor based on air consumption.
Dryer Functioning
For machines supplied with a dryer, the control unit can control the drying cycle.
Using the “Dryer ON” parameter, if its functioning is enabled, which can be continuous or linked to compressor motor functioning,
by setting the parameter “Functioning mode”
The dryer motor is activated if the temperature is over the total of the temperatures defined in the parameters
“Temperature OFF” and “Thermic drift” and deactivated if lower than the parameter “Temperature OFF”.
If the temperature remains outside the aforementioned limits for a time over that set in the parameter “Alarms delay”,
an alarm sounds (see ALARMS and WARNINGS paragraph)
To avoid damaging the motor due to over-frequent start-ups you can moderate re-starts for the time defined in the parameter
“Minimum time”. (see DRYER MENU paragraph)
Condensate Drainage Functioning
For machines requiring the condensate drainage function using the parameter “Condensate drainage ON”, the function
can be enabled and defined by setting the parameter “Functioning mode”
The drainage solenoid valve stays on for the time set in the “Interval” parameter and remains deactivated for the time defined
in the parameter “Opening time” (see the CONDENSATE DRAINAGE MENU paragraph).
NOBEL DV 22 CSA - Cod.197EE0622ML - Rev.1 03/2019

16
16
EN
Main Screen
The main screen summarises the current status of the machine
Current Air Cycle Status (1):
a) STAND-BY: on status but motor off.
b) STATUS-OFF: the motor is off and the load solenoid valve is disabled.
c) NO LOAD : the motor is on but the load solenoid valve is disabled.
d) LOADED: the motor is on and the load solenoid valve is enabled.
e) REMOTE-OFF: Remote program enabled in stand-by for the start-up remote command.
f) TIME-OFF: Start-up program enabled, in stand-by for start time.
START-UP AND OPERATION
070°C
003°C
STATUS-OFF
08.5->10.0
09.0
BAR
STATUS-OFF
09.0BAR
08.5->10.0
100%
t <= 4°C
4< t <= 6°C
6< t <= 8°C
8< t <=10°C
t>10°C
AUT.
R.
R
P
16:18:33
14-03-13
!
AUT.
R.
R
P
!
Screw Temperature Panel
Dryer Status Panel
Current Time and Date Panel
Air Cycle Status Summary Panel
:Current Pressure
:Pressure range set
:(functioning percentage indication)
:Graphical representation of the motor without
inverter
:Graphical representation of the motor with inverter
(indicazione percentual di funzionamento)
Machine Status Summary Panel
:If present, it indicates maintenance
is necessary on one or more
parts of the compressor
:If present, it indicates the
cooling fan is on
:If present, it indicates an alarm
is on
:If present, it indicates the remote
function is on
:If present, it indicates the
automatic start function is on
:If present, it indicates the dryer
function is on.
Negative when compressor dryer on
:If present, it indicates the
condensate drainage function is on.
Negative when the solenoid valve is on
:If present, it indicates functioning
with events programming
If activated, it indicates the dryer
temperature in two ways:
Graphic:
Text: indicates the temperature in
degrees
STORM 38 VS - Cod.197DD9910 - Rev.2 01/2016NOBEL DV 22 CSA - Cod.197EE0622ML - Rev.1 03/2019

17
(6&
5(6(7
(17(5
EN
Menus and Parameters
The menus are structured as vertical drop-down menus;
the title is on top and is followed by the list of parameters
or sub-menus available. If the menu contains more
items than the LCD display can show, two arrows (Up
and Down) appear on the right to indicate more items
are present.
Use the “Arrow up” and “Arrow down” keys to find
the parameter or sub-menu and highlight it to then open
it by pressing the “Enter” key; go back by pressing the
“Esc” key.
If you go to a parameter screen you can change its
value using the “Arrow up” and “Arrow down” keys
or you can make this value the default value using the
“Reset” key. By pressing the “Enter” key, you exit the
menu, saving the parameter value. Press the “Esc” key
to return to the previous menu only.
Some menus contain exceptions in relation to parameter
entries, which will be dealt with individually in the
following paragraphs.
START-UP AND OPERATION
NOBEL DV 22 CSA - Cod.197EE0622ML - Rev.1 03/2019

18
18
EN
START-UP AND OPERATION
08.5 BAR
Min:00.0
Max:12.0
01
00000=Oil hours
00000=Oil filter hours
00000=Air filter hours
00000=Oil separator hours
00000=Bearings lubric. hours
MAINTENANCE
00000=Line Hours
00000=Load Hours
00=No. starts in hours
00000=Load cycles
WORKING HOURS
AUT.
R.
R
P
!
070°C
003°C
STATUS-OFF
08.5->10.0
09.0
BAR
16:18:33
14-03-13
Menu
00 Utente
01 Support
02 Factory
03 Alarms Log
04 Info
00 USER
00
Name
Menu/Sub-menu
List
Sub-menus/Parameters
Loaded pressure
Parameter Name
Parameter Value
Upper Limit
Lower Limit
User Menu
00
No load pressure
01 Pressione carico
02
Pre. unit of measurement
03 Tem. unit of measurement
04 Language
05 Display contrast
01 Loaded pressure
Parameter
Selected
Parameters Index
Selected
Indicates further
list not displayed
If the compressor is OFF
it accesses the menus
If alarms sound, silence the
buzzer. If the cause of the alarm
is resolved, delete the warning
Displays the counters page for
hours of maintenance
Back to Main screen
Displays the counters page for
WORKING hours
Back to Main screen
Displays the counters page for
hours of maintenance
(After 15 sec it automatically goes back
to the main screen)
(After 15 sec it automatically goes back
to main screen)
Back to previous menu
Enters the menu/parameter
selected
Selects the menu/parameter
Back to previous menu
Enters the menu/parameter
selected
Selects the menu/parameter
Back to previous menu not
saved
Saves the parameter value and
goes back to previous menu
Changes the parameter
Sets parameter to
default value
Main Screen Machine report display screens
Main MenuSub-MenuParameter Screen
Back to Main screen
Displays the alarms on
page
(After 15 sec it automatically goes back
to the main screen)
emergency button pressed
phase sequence error
ALARMS ON
STORM 38 VS - Cod.197DD9910 - Rev.2 01/2016NOBEL DV 22 CSA - Cod.197EE0622ML - Rev.1 03/2019

19
EN
Password
Certain menus are password protected. A password is requested if you try to access the reserved areas.
Removal of menu protection persists until you go back to the main screen.
Main Menu
User: Menu containing the User parameters (see USER MENU paragraph).
Support: Menu containing the Support parameters (see SUPPORT MENU paragraph).
Password protected.
Factory: Menu containing the Factory parameters (see FACTORY MENU paragraph).
Password protected.
Alarms Log: List of last alarms.
Pressing “ENTER” on the highlighted alarm not only displays the type of alarm, but also the date, time, pressure and the
oil temperature in the instance in which the alarm occurred.
Info: Displays information on the board and firmware.
User Menu
No load pressure: Defines the pressure at which the compressor must run with no load. The maximum value you can
set is defined by the parameter “Maximum pressure” in the factory menu.
Loaded pressure: Defines the pressure necessary to restart the compressor. The recommended value is 1.5 bar lower
than that defined in the “No load pressure” parameter.
Pre. unit of measurement: Defines the pressure unit of measurement.
Tem. unit of measurement: Defines the temperature unit of measurement.
Language: Defines the language used in the menus.
Display contrast: Defines the display contrast level.
Display lighting: Defines the display backlighting level.
Time/Date setting: Sets the date and time. Entry is guided and the procedure is only complete when all the settings
are saved.
Start-up setting: Sub-menu where you can define 10 programs (0-9) per week for compressor start-up and stoppage.
The parameters you can set are the start time, stoppage time, no load pressure, loaded pressure and
the day of the week.
START-UP AND OPERATION
0000
0
0000
0
ENTER PASSWORD
Deletes operation and goes
back to previous menu
Confirms password
Changes digit
selected
Selects digit to
change
ENTER PASSWORD
NOBEL DV 22 CSA - Cod.197EE0622ML - Rev.1 03/2019

20
20
EN
Support Menu
Oil hours: Indicates the hours remaining before the oil needs to be changed.
Oil filter hours: Indicates the hours remaining before the oil filter needs to be changed.
Air filter hours: Indicates the hours remaining before the air filter needs to be changed.
Oil separator hours: Indicates the hours remaining before the oil separator filter needs to be changed.
Bearings lubric. hours: Indicates the hours remaining before the main electric motor bearing needs to be lubricated.
Fan temperature: Defines the working temperature of the cooling fan. The threshold set has a hysteresis that can be
changed by 10°C. e.g. if the operating temperature is set at 80°C, the fan will activate at 80°C and stop
at 70°C (screw unit supply temperature).
No load time: Defines the motor stoppage time from the moment the load solenoid valve was deactivated because
the desired pressure was reached.
Stoppage time: Defines the stoppage time of the compressor from the moment in which stoppage is requested using
the STOP(O) key. The solenoid valve is immediately deactivated.
Automatic start: If the compressor is on, it starts automatically after an electricity cut. The first start should be activated
by pressing the START (I) key on the panel.
Max start-up hours: Defines the maximum number of start-ups of the main electric motor within the arc of one hour. If
surpassed, the compressor will stay on (loaded or with no load depending on the pressure) until the
hour is up as calculated from first start-up and then returning to normal functioning.
Remote enabling: Remote command enabling.
Fan extra time: Defines the time in which the cooling fan stays on after the working temperature of the compressor has
returned within the safety limits.
Inverter: Sub-menu for inverter configuration (see INVERTER MENU paragraph).
Fan temperature hysteresis: Defines the delta temperature in which the main cooling fan must work.
Diagnostic: Using the diagnostic menu, you can control the various inputs and outputs of the control unit:
Input: the status of 9 digital inputs can be controlled
Output: using the right and left keys, you can move on the relay output you want to command, while using the
up and down buttons to activate the output
AN1: Indicates pressure in bar with centesimal precision
AN2: Indicates the temperature in °C Screw probe
AN3: Indicates the temperature in °C Dryer probe
INV: Indicates the inverter output automatically switches 4-20mA
Keeping the I key pressed, you can execute a motor start-up test. Pressing the 0 key, you can upload the default parameters
(there are 32 sets of parameters present). The Factory password is required. Press the RESET key to execute calibration of the
pressure transducer (the Factory password is required).
START-UP AND OPERATION
01 S
tart-up setting:
Programma 00
Program
01
Program
02
Program
03
Program
04
Program
05
Start-up on
Program0
00:00 ...
Start time
....
00:00 ...
Stop time
00.0BAR.
No load pressure
00.0BAR.
Loaded pressure
Lun Mar Mer Gio Ven Sab Dom
Back to previous menu not
saved
Saves the program and
goes back to previous menu
Changes the parameter
Selects the parameter
to change
Back to previous menu
Enters the program
selected
Selects the desired
program
Program 00
Mon Tues Wed Thurs Fri Sat Sun
STORM 38 VS - Cod.197DD9910 - Rev.2 01/2016NOBEL DV 22 CSA - Cod.197EE0622ML - Rev.1 03/2019

21
EN
Output configuration: Sub-menu that allows you to associate the outputs CN4-8 and CN4-9 with a function, choosing
from: “Pre-alarm”, “Control ON”, “Compressor ON”, “Motor running” and “Compress No Load/Loaded”
Comp. rotation man.: (to define).
Dryer: Sub-menu for dryer configuration (see DRYER MENU paragraph).
Condensate drainage: Sub-menu for dryer configuration (see CONDENSATE DRAINAGE MENU paragraph).
Inverter Menu
Enable Inverter: Inverter enabling.
% Min functioning: Defines the frequency minimum percentage at which the inverter must work.
The maximum is 100%
Inverter Integral: Defines the integral part on the PID calculation of the inverter percentage.
Inverter Proportional: Defines the proportional part on the PID calculation of the inverter percentage.
Inverter Differential: Defines the differential part on the PID calculation of the inverter percentage.
Pressure at 100%: The pressure at which the inverter can work up to 100%
Minimum pressure %: The pressure at which the inverter must work at the % Min functioning percentage set.
Dryer Menu
Dryer ON: Dryer Enabling.
Minimum time: Defines the minimum maintenance time of the deactivated dryer. It serves to protect the
dryer compressor from over-frequent start-ups.
Temperature OFF: Defines the value of the temperature at which the dryer compressor is deactivated.
Temp. differential: Defines the positive differential between the OFF temperature and the re-activation
temperature.
Temperature offset: Defines the difference between the temperature measured and the temperature displayed.
Functioning mode: Defines the functioning mode of the dryer:
Automatic: The compressor starts and stops based on the main motor of the compressor functioning.
START-UP AND OPERATION
CN4-8=
CN4-9=
Output Configuration
Emergta
Control ON
Back to previous menu not
saved
Saves the configuration and goes back
to the previously saved menu
Changes configuration
Selects the output
to change
Motor running
CN4-8=
CN4-9=
Output Configuration
EEmta
Control ON
Back to previous menu not
saved
Saves the configuration and goes back
to the previously saved menu
Changes configuration
Selects the output
to change
Emergency pressed premuta
NOBEL DV 22 CSA - Cod.197EE0622ML - Rev.1 03/2019

22
22
EN
Continuous: the dryer starts as soon as the compressor is switched on and will only stop when it is switched off.
Alarms Delay: Defines the delay with which the dryer alarms are displayed.
Alarm type: Defines the effects of the alarm on the compressor:
Alarm: blocks the compressor.
Warning: warning without blocking the compressor.
Extra run: Defines the time in which the dryer must continue to work, also after the compressor motor has stopped,
if the functioning mode is set to automatic.
Condensate Drainage Menu
Condensate drainage on: Condensate drainage enabling.
Interval: Defines the time in which the condensate drainage solenoid valve remains closed.
Opening time: Defines the time in which the condensate drainage solenoid valve must stay open.
Functioning mode: Defines the functioning mode of condensate drainage:
Automatic: condensate drainage only takes place when the compressor is on and in loaded mode.
Continuous: condensate drainage is always on.
Factory Menu
Oil pre-alarm: Defines the advance time with which an oil temperature pre-alarm should sound compared to the
maximum oil temperature.
Maximum temperature: Defines the surpassed maximum oil temperature value to generate an alarm and block the
compressor.
Minimum temperature: Defines the minimum oil temperature. If the oil temperature detected is lower, an alarm sounds
and the compressor is blocked.
Thermic drift: Defines the maximum variation per second of the oil temperature. If surpassed, an alarm sounds and
the compressor is blocked.
Max. Press. Alarm: Defines the permitted pressure of the compressor. If surpassed, an alarm sounds and the compressor
is blocked.
Maximum pressure:Defines the maximum pressure value which can be set in the parameter “No Load Pressure”.
Total Hours: Indicates the working hours of the main motor.
Loaded hours: Indicates the working hours the compressor is loaded.
AN3: Indicates the dryer probe temperature
INV: Indicates the inverter output automatically switches 4-20mA
Star/delta time: Defines the duration of the star phase during start-up of the main motor of the compressor.
Load delay: Defines the delay to enable the solenoid valve to command the calculated suction of the regulator from
the moment in which the motor is considered fully operational.
Inverter: Sub-menu for inverter configuration (see INVERTER MENU paragraph).
Load insertion temperature: Defines the screw oil probe temperature threshold in which the loaded command solenoid
valve of the suction regulator can work
Stand-by time: Defines the stand-by time in which the compressor cannot re-start after a stoppage or a re-start of the
control unit.
START-UP AND OPERATION
STORM 38 VS - Cod.197DD9910 - Rev.2 01/2016NOBEL DV 22 CSA - Cod.197EE0622ML - Rev.1 03/2019

23
(6&
5(6(7
(17(5
EN
Input configuration: Sub-menu allowing you to configure the logic of all the control unit inputs and associate a function
of your choice to input CN2-1, among: “oil filter, “air filter” and “air pressure switch”. By setting the
configuration equal to 1, the input logic will be denied. Vice versa, if left at 0 the logic will be normal.
Alarms and Warnings
All the alarms that occur are visually displayed on the main screen
in the “Alarms and Warnings Panel”, in the “Machine Status
Summary Panel” (see Main Screen paragraph) and acoustically
via the buzzer.
The acoustic alarm can be immediately silenced by pressing
the “RESET” key, while the alarm indication on the LCD will only
disappear if the cause of the alarm has been resolved.
The last 50 alarms are visible in the “Alarms log“ (see Main menu
paragraph) where you can check their chronological order, the
pressure and temperature in the instant in which they occurred.
The possible alarms are as follows:
Alarm! Minimum temp.: Having reached the oil minimum temperature, the alarm BLOCKS the compressor. To re-
start the compressor, you need to wait for the temperature to rise above the programmed value.
Alarm! Maximum temp.: Having reached the oil maximum temperature, the alarm BLOCKS the compressor. To re-start
the compressor, you need to wait for the temperature to go below the programmed value.
Warning! Pre-alarm temp.: Having reached the oil pre-alarm temperature, the alarm DOES NOT BLOCK the compressor.
Alarm! Temp. sen. fault: When an anomaly occurs on the oil temperature sensor (sensor short-circuits or open), the alarm
BLOCKS the compressor. To re-start the compressor, you need to replace the probe.
Alarm! Motor thermal switch: When the main motor thermal switch activates, the alarm BLOCKS the compressor. To
re-start the compressor, wait for the motor to cool down.
Alarm! Fan thermal switch: When the fan thermal switch activates, the alarm BLOCKS the compressor. To re-start the
compressor, wait for the fan to cool down.
Alarm! Max. press. alarm: aving reached the maximum permitted pressure, the alarm BLOCKS the compressor. To re-start
the compressor, you have to bring pressure under the maximum pressure programmed.
Alarm! Press. sen. fault: When a pressure sensor anomaly occurs (sensor broken or disconnected), the alarm BLOCKS
the compressor. To re-start the compressor, you need to reset the probe.
Alarm! Rotation direction err.: When a wrong sequence of the main motor phases occurs, the alarm BLOCKS the
compressor. To re-start, you need to check the phases sequence is right.
Alarm! Emergency button pressed: Having pressed the emergency button, the alarm BLOCKS the compressor. To re-
start, you need to reset the emergency button.
START-UP AND OPERATION
CN2= 1 2 4 5 6 7 8 9
IN = 0 1 0 1 0 0 0 0
CFG= 1 1 0 0 0 0 0 0
OUT= 1 0 0 1 0 0 0 0
CN2-1 =
1
Back to previous menu not
saved
Saves the configuration and goes back
to the previously saved menu
Changes configuration
Selects the configuration
of the input to change
Input current status
Input reference
Input configuration
Input final status
Function associated with input CN2-1
Air filter
Configure inputs
NOBEL DV 22 CSA - Cod.197EE0622ML - Rev.1 03/2019
Table of contents
Other Omega Air Compressor manuals
Popular Air Compressor manuals by other brands
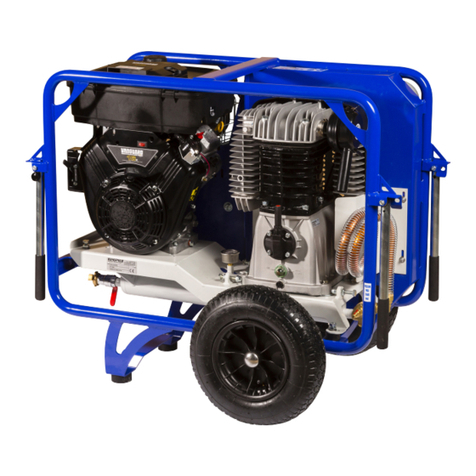
EUROPE PROJECTION
EUROPE PROJECTION EUROPRO 50TH user manual
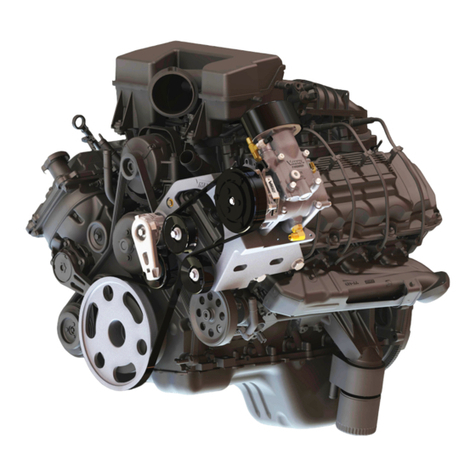
Vmac
Vmac VR70 installation manual
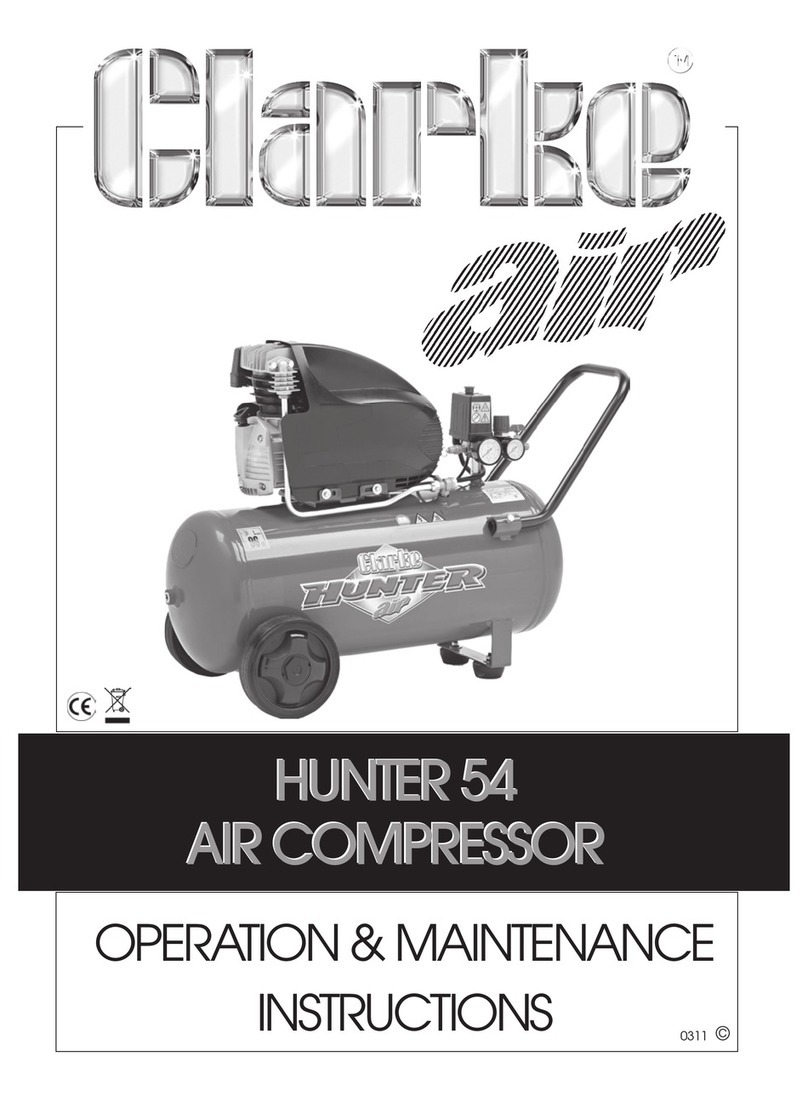
Clarke
Clarke Hunter 54 Operation & maintenance instructions
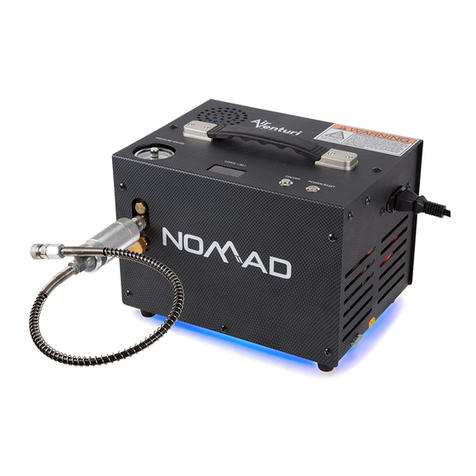
Air Venturi
Air Venturi Nomad II User instruction manual
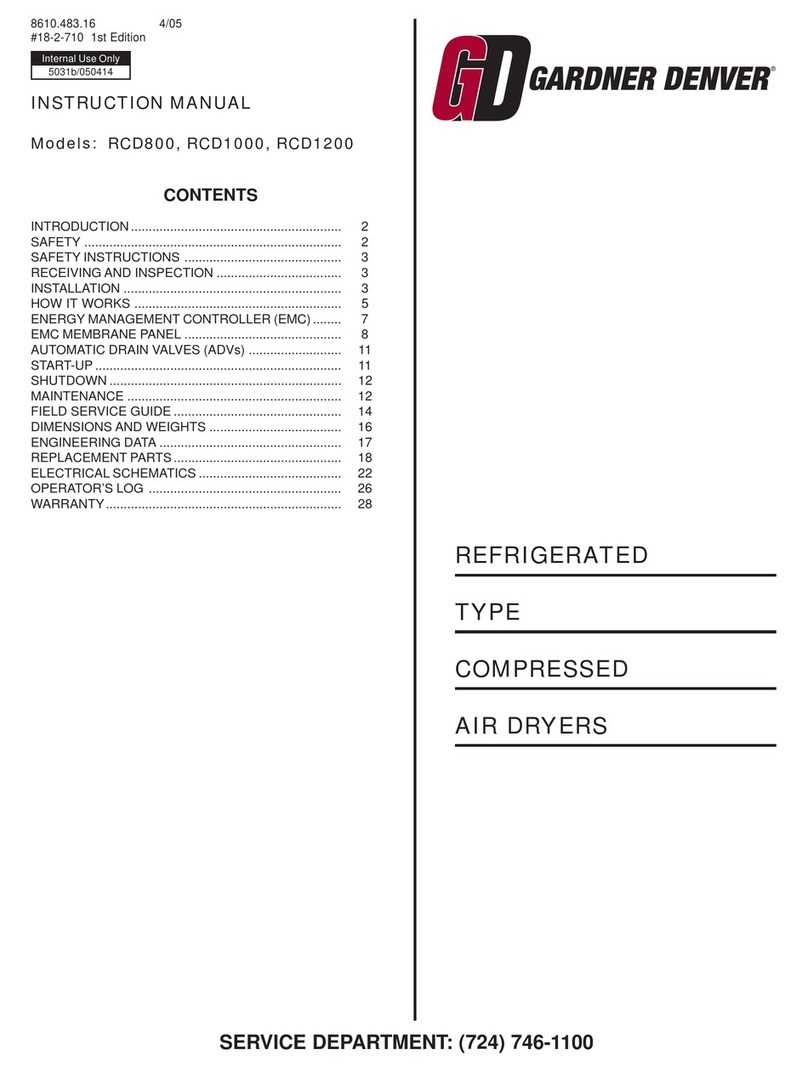
Gardner Denver
Gardner Denver RCD800 instruction manual

Doosan
Doosan Ingersoll Rand VHP300WIR operating & maintenance manual