Omni Instruments TCW120B User manual

Ethernet controller TCW120B
Users manual
1. Short description
TCW120B is a multifunctional device for remote monitoring and management. It is an
Ethernet based controller, which is designed to work in IP-based networks and managed by
WEB interface or S MP programs. Its I/O interface - relay outputs, analog and digital inputs,
is suitable for solving specific problems in various fields such as remote control, alarm
systems, industrial process automation, control and management of computer networks etc.
High precision digital temperature sensor is option.
2. Features
•10 Mbit Ethernet connectivity
•Password protected web based configuration and control
•2 digital inputs, 2 analog inputs, 1 temperature sensor input
•Two 3A/24V relay outputs
•S MP v.1, SMTP, ICMP, VLA support
•Sending S MP Traps messages under certain conditions
•Sending E-mail messages under certain conditions
•Relay restart on ping/echo timeout
•TCW120B can be used as standalone device or as a part of monitoring and
management system
•MAC Address filtering
•Remote FTP firmware update
UK / Europe Office
Tel: +44 (0)845 9000 601
Fax: +44 (0)845 9000 602
info@omniinstruments.co.uk
www.omniinstruments.co.uk
Australia / Asia Pacific Office
Tel +61 (0)282 442 363
Fax +61 (0)294 751 278
info@omniinstruments.com.au
www.omniinstruments.com.au
USA / Canada Office
Tel +1-866-849-3441
Fax +1-866-628-8055
info@omniinstruments.net
www.omniinstruments.net
For pricing information contact Omni Instruments by phone on +44 845 9000 601 or via email at info@omni.uk.com

3. Technical parameters
Supply Voltage, VDC 12
Weight, g 120
Dimensions, mm 72 x 50 x 18
Operating temperature
, °C
Storage temperature , °C
0 ÷ 40
-40 ÷ 85
Analog input range, VDC
Ain1
Ain2
0 ÷
2
0
0 ÷ 100
Minimum high level input voltage, V 2.5
Maximum low
level input voltage
, V
0.8
Maximum input voltage for digital inputs, V 5.5
Max. switchable current (at 220 VAC) , А 3
Max. switchable voltage, VAC/VDC 250/110
4. Connectors
Inputs and outputs locations are shown below:
Connector 1 – 6-pin connector pinout is shown in the table below:
Pin description
1 Relay1 normally open
2 Relay1 common
3 Relay1 normally closed
4 Relay2 normally open
5 Relay2 common
6 Relay2 normally closed
Connector 2 – power connector.
Connector 3 – RJ45 Ethernet connector
Connector 4 – 6-pin connector pinout is shown in the table below:

Pin description
1 Digital input 1 ( in1)
2 G D
3 Digital input 2 ( in2)
4 Analog input 1 (Ain1)
5 G D
6 Analog input 2 (Ain2)
Connector 5 –3-pin connector pinout is shown in the table below:
Pin description
1 G D – Temp. Sensor
2 Data – Temp. Sensor
3 Vdd – Temp. Sensor
5. LE indicators
The following indicators show the status of the controller :
•Relay1/Relay2 (green) – these LEDs are illuminated whenever the corresponding
relay is activated
•Power (red) – this flashes when the power supply is turned on;
•Busy (yellow) – this LED indicates that someone is connected to the controller
through web interface;
• Link (green) – this LED is located on the Ethernet connector. It indicates that the
device is connected to the network ;
•Act (yellow) – this LED is located on the Ethernet connector. It flashes when activity
is detected on the network.
6. Example Applications
6.1 Remote control
The controlled device is connected in series with the relay contacts. Users can operate
TCW120B using a web browser or by using custom S MP applications. Both relay outputs are
managed independently of each other.

6.2 Remote monitoring
A relay output from the monitored device is connected to one of the digital inputs of
TCW120B. When an event occurs – the controller sends an E-mail message to a predefined
e-mail address. S MP Trap message is sent if custom S MP monitoring software is used.
6.3 ata acquisition
The TCW series Ethernet controllers are designed for use in data acquisition
systems(DAQ) . TCW120B uses S MP v.1 protocol for communication with monitoring and
management software applications.

7. Installation
Please follow the steps below for proper installation :
1. Mount the controller in a dry and ventilated place.
2. Connect the Ethernet port to a 10/100 Base T Ethernet connection. For direct
connection to a PC use a “crossover” cable.
3. Connect the I/O pins of the controller according to the required application.
4. Connect the power supply.
If the red LED is blinking, it indicates that the power supply is OK. By default TCW120B comes
with the following network settings:
IP:192.168.1.2 , Subnet Mask: 255.255.255.0 , Default Gateway: 192.168.1.1
Communication with TCW120B may be established by assigning a temporary IP address to
the configuration computer that is on the same network (for example 192.168.1. 3). To get
access to the web interface of the controller, you should type the following URL into the browser
: http://192.168.1 2 . If the network settings are correct, the “Login” page will appear.
8. Web-based setup.
The web based interface allows the TCW120B to be configured, controlled and monitored
via web browser. Recommended programs are Mozilla Firefox, Chrome and Internet Explorer 6
(or higher version) at 1024x768 resolution.
8.1 Login page
After opening the Login page, authorization data must be entered ( by default
username=admin , password=admin). It is recommended to change the username and password
to prevent unauthorized access to the controller.
Depending on the username and password, there are two access levels to the controller -
user and administrator. This is done to restrict the access to certain functions. Both access levels
are described in table below :
Administrator User
Account Administration
Monitoring
etwork Setup
I/O Setup
S MP Setup

The controller supports only one active session – only one user (administrator) can operate
the device. If another user tries to login, the following message appears: “Someone’s logged in”
The active session will be terminated automatically, if the current user stays inactive for 2
minutes.
8.2 Monitoring page
After successful authorization, the Monitoring page appears:
The Monitoring page provides information about the state of the digital and analog inputs of
the controller and the temperature (if temperature sensor is connected to the controller) .
To change the state of the relays , the “O /OFF” buttons should be pressed. If the Pulse
button is pressed the relay will pulse for the time specified in the “Pulse Duration” field in the
“I/O Setup ” page.

8.3 I/O setup page
The input and output settings are made in “I/O Setup” page. The following parameters can
be set up for both relays:
•escription – brief description of the output, maximum 11 characters should be used.
•Pulse uration – time for which the relay changes its state, by pushing the "Pulse" button
on "Monitoring" page.
•ICMP Mode – this is an operational mode, in which the controller restarts its relays, if no
ICMP echo-request (ping) or ICMP echo-reply (echo) is received from specified IP
Address for specified time (Ping timeout for restart ) . This mode can be activated for
each of the relays. Relay 1 will be restarted if no ping is present, аnd Relay 2 if no
echo is present.
•Ping time out for restart – timeout for restart for Relay 1 and Relay 2 .
•IP address - IP address of the host from which is expected ping or echo.
•Maximum number of restarts – maximum number of restarts after timeout for restart
has expired
In the configuration example above, the controller sends ping to the host with IP Address
192.168.32.10. If, within 10 seconds the controller receives no echo, Relay 2 will be restarted for
a period of 5 seconds as the maximum number of consecutive restarts is limited to 5.
One of the possibilities of TCW120B is to send e-mail messages when the status of digital
inputs igital Input 1 and igital Input 2 is changed. To do this, the following parameters must
be set:
•escription – brief description of the input, maximum 11 characters should be used.
•Subject – message subject, maximum 11 characters should be used
•Message – message body, maximum 22 characters should be used
Important! It is necessary to set SMTP server settings on " etwork Setup" page, to
successfully send e-mail messages.

In the example above, if an event occurs (closing contact) the controller will send e-mail
message to [email protected] with subject "Alarm 3" and the text "Alarm 3 activated".
Only the field “Description” can be changed for the Analog Input 1 and Analog Input 2.
Maximum 11 characters may be used.
8.5 Network Setup page
The etwork parameters are set on this page. The following parameters can be changed:
•IP configuration – IP Address configuration can be static or dynamic (DHCP)
•IP address, Subnet mask , efault gateway – these fields are active if IP address is
static
•Host Name
•MAC – device MAC address
If multiply TCW120B controllers are used on the same network, please change the IP address
after connecting the device to the network. This will avoid devices installed on the network with
the same factory default IP address at the same time. It may be necessary to clear the arp cache
each time you connect new device to the network. This is done by typing arp -d in the command
prompt of a Windows computer.

In order to reduce network traffic and to limit the access, the controller supports VLA and
MAC address filtering. In addition to the MAC address of the Default Gateway, another 2 MAC
addresses can be added to the filter. The filter is enabled by marking the appropriate check box
after the MAC address.
To set up the SMTP server the following fields should be completed
•Mailserver IP – IP address of SMTP mail server
•E-mail – sender e-mail
8.6 SNMP Setup page
TCW120B supports S MP v.1 that enables trap delivery to an S MP management
application. This enables the device to be part of large monitoring and control networks. The
possible settings are:
•SNMP Configuration – enable S MP v.1
•Read-Write community – performs client authentication
•Read-Only community – performs client authentication

S MP trap messages are sent for the following conditions:
-when event occurs on igital Input 1 or igital Input 2 (the signal changes its state)
-measured voltage on Analog Input 1 и Analog Input 2 is outside the predefined
range
-measured temperature Is outside the predefined range
-restart
Setting range for sending S MP trap messages is done only through S MP. The following
parameters can be changed:
•SNMP Traps – enable S MP trap messages
•IP address – IP address of the receiving host
•Community string – performs client authentication
•Trap Interval - time interval for S MP trap messages
•Max. number of Traps – maximum number of S MP trap messages sent, if trap
condition is present

9. SNMP setup
TCW120B can be configured and monitored through S MP (Simple etwork
Management Protocol). This could be done using every S MP v.1 compatible program.
Parameters that can be changed, are grouped according to their functions in the tables below.
To obtain a valid OID number it is necessary to replace the “x” symbol with the prefix
”.1.3.6.1.4.1.17095”. To save the changes you should set a value ”1” of the
configurationSaved (OID x.8.0).
9.1 product
OI Name Access escription Syntax
x.1.1.0 name read-only Device name String
x.1.2.0 version read-only Software version String
x.1.3.0 date read-only Date of the version String
9.2 SNMP Setup
OI Name Access escription Syntax
x.2.1.1.0 trapEnabled read-write TRAP messages enable/disable I TEGER { Yes(1), o(0) }
x.2.1.2.0 trapReceiverIPAddress read-write TRAP messages receiver address IpAddress
x.2.1.3.0 trapCommunity read-write TRAP community String (SIZE (0..13))
x.2.1.4.0 trapInterval read-write TRAP messages interval I TEGER (0..255)
x.2.1.5.0 max umberOfTraps read-write Maximum number S MP messages I TEGER (0..255)
x.2.1.6.0 digitalInput1State read-write Digital input 1 trap status I TEGER { O (1), OFF(0) }
x.2.1.7.0 digitalInput2State read-write Digital input 2 trap status I TEGER { O (1), OFF(0) }
x.2.1.8.1.0 voltage1minimum read-write Voltage1 lower range String (SIZE (0..13))
x.2.1.8.2.0 voltage1maximum read-write Voltage1 higher range String (SIZE (0..13))
x.2.1.9.1.0 voltage2minimum read-write Voltage2 lower range String (SIZE (0..13))
x.2.1.9.2.0 voltage2maximum read-write Voltage2 higher range String (SIZE (0..13))
x.2.1.10.1.0 temperatureMinimum read-write Temperature lower range String (SIZE (0..6))
x.2.1.10.2.0 temperatureMaximum read-write Temperature higher range String (SIZE (0..6))
x.2.2.0 S MPConfiguration read-write S MP Configuration I TEGER { E ABLED(1), DISABLED(0) }
x.2.3.0 readCommunity read-write S MP Read Community String (SIZE (0..13))
x.2.4.0 writeCommunity read-write S MP Write Community String (SIZE (0..13))

9.3 monitor
OI Name Access escription Syntax
x.3.1.1.0 relay_1 read-write relay 1 status I TEGER { O (1), OFF(0) }
x.3.1.2.0 relay_2 read-write relay 2 status I TEGER { O (1), OFF(0) }
x.3.1.3.0 pulse_1 read-write relay 1 pulse status I TEGER { O (1), OFF(0) }
x.3.1.4.0 pulse_2 read-write relay 2 pulse status I TEGER { O (1), OFF(0) }
x.3.2.1.0 voltage1 read-only Analog Input 1 voltage String (SIZE (0..4))
x.3.2.2.0 vol1int read-only Analog Input 1 voltage
(integer x100mV) I TEGER (0..65000)
x.3.2.3.0 voltage2 read-only Analog Input 2 voltage String (SIZE (0..4))
x.3.2.4.0 vol2int read-only Analog Input 2 voltage
(integer x100mV) I TEGER (0..65000)
x.3.3.1.0 digitalInput1 read-only igital Input 1 status I TEGER { O (1), OFF(0) }
x.3.3.2.0 digitalInput2 read-only igital Input 2 status I TEGER { O (1), OFF(0) }
x.3.4.0 temperature read-only temperature String (SIZE (0..4))
x.3.5.0 tempx10Int read-only Temperature (integer x 10) I TEGER (-550..1250)
9.4 network
OI Name Access escription Syntax
x.4.1.0 deviceIPAddress read-write Device IP address IpAddress
x.4.2.0 subnetMask read-write Subnet Mask IpAddress
x.4.3.0 gateway read-write Gateway IpAddress
x.4.4.0 deviceMACAddress read-write Device MAC Address OCTET STRI G (SIZE(6))
x.4.5.0 dhcpConfig read-write DHCP O /OFF I TEGER { O (1), OFF(0) }
x.4.6.1.1.0 filterMACAddress1 read-write MAC Filter 1 OCTET STRI G (SIZE(6))
x.4.6.1.2.0 filterMACEnable1 read-write MAC Filter 1 O /OFF I TEGER { E ABLED(1), DISABLED(0) }
x.4.6.2.1.0 filterMACAddress2 read-write MAC Filter 2 OCTET STRI G (SIZE(6))
x.4.6.2.2.0 filterMACEnable2 read-write MAC Filter 2 O /OFF I TEGER { E ABLED(1), DISABLED(0) }
x.4.6.3.1.0 filterMACAddress3 read-write MAC Filter 3 OCTET STRI G (SIZE(6))
x.4.6.3.2.0 filterMACEnable3 read-write MAC Filter 3 O /OFF I TEGER { E ABLED(1), DISABLED(0) }
x.4.7.1.0 smtpServerIPAddress read-write SMTP server IP address IpAddress
x.4.7.2.0 senderEmailAddress read-write Sender е-mail address String (SIZE (0..38))
x.4.8.1.0 VLA Status read-write VLA status I TEGER { E ABLED(1), DISABLED(0) }
x.4.8.2.0 VlanId read-write VLA ID I TEGER (0..4095)

9.5 inputs
OI Name Access escription Syntax
x.5.1.1.0 input1description read-write igital Input 1 description String (SIZE (0..10))
x.5.1.2.0 input1ActionEdge read-write Send e-mail condition RISI G-FALLI G
x.5.1.3.0 input1action read-write Send e-mail enable/disable I TEGER { SE D(1), DO TSE D(0) }
x.5.1.4.0 input1emailAddress read-write Recipient e-mail String (SIZE (0..38))
x.5.1.5.0 input1subject read-write Subject String (SIZE (0..10))
x.5.1.6.0 input1body read-write Message String (SIZE (0..21))
x.5.2.1.0 input2description read-write igital Input 2 description String (SIZE (0..10))
x.5.2.2.0 input2ActionEdge read-write Send e-mail condition RISI G-FALLI G
x.5.2.3.0 input2action read-write Send e-mail enable/disable I TEGER { SE D(1), DO TSE D(0) }
x.5.2.4.0 input2emailAddress read-write Recipient e-mail String (SIZE (0..38))
x.5.2.5.0 input2subject read-write subject String (SIZE (0..10))
x.5.2.6.0 input2body read-write Message String (SIZE (0..21))
x.5.3.0 voltage1description read-write Analog Input 1 description String (SIZE (0..10))
x.5.4.0 voltage2description read-write Analog Input 2 description String (SIZE (0..10))
9.6 outputs
OI Name Access escription Syntax
x.6.1.1.0 relay1description read-write Relay 1 description String (SIZE (0..10))
x.6.1.2.0 relay1pulseWidth read-write Relay 1 pulse width I TEGER (0..253)
x.6.1.3.0 relay1IcmpMode read-write Relay 1 - ICMP O /OFF I TEGER { O (1), OFF(0) }
x.6.1.4.0 relay1IcmpTimeout read-write Relay 1 - ICMP timeout I TEGER (0..65000)
x.6.1.5.0 relay1IpAddress read-write Relay 1 - ICMP IP address IpAddress
x.6.1.6.0 relay1 umOfRestarts read-write Relay 1 – maximum number of restarts I TEGER (0..253)
x.6.2.1.0 relay2description read-write Relay 2 description String (SIZE (0..10))
x.6.2.2.0 relay2pulseWidth read-write Relay 2 pulse width I TEGER (0..253)
x.6.2.3.0 relay2IcmpMode read-write Relay 2 - ICMP O /OFF I TEGER { O (1), OFF(0) }
x.6.2.4.0 relay2IcmpTimeout read-write Relay 2 - ICMP timeout I TEGER (0..65000)
x.6.2.5.0 relay2IpAddress read-write Relay 2 - ICMP IP address IpAddress
x.6.2.6.0 relay2 umOfRestarts read-write Relay 2 – maximum number of restarts I TEGER (0..253)
9.7 accounts
OI Name Access escription Syntax
x.7.1.1.0 admin ame read-write Username (Admin) String (SIZE (0..14))
x.7.1.2.0 adminPassword read-write Password (Admin) String (SIZE (0..14))
x.7.2.1.0 user ame read-write Username (User) String (SIZE (0..14))
x.7.2.2.0 userPassword read-write Password (User) String (SIZE (0..14))

9.8 Save changes
OI Name Access escription Syntax
x.8.0 configurationSaved read-write Save configuration changes I TEGER { SAVED(1), U SAVED(0) }
x.9.0 restartDevice read-write Restart device I TEGER { RESTART(1), CA CEL(0) }
10.Restoring Factory efault Settings
If the IP address or password are forgotten, TCW120B can be restored to its original
factory default settings. To do this, please follow the steps below:
- remove the power supply from the unit and open the plastic box
- press and hold the RESET button then turn on the power supply
- wait about 5 seconds and release the RESET button. The factory default settings are
shown in the table below:
User ame (Admin) admin
Password (Admin) admin
User ame (User) user
Password (User) user
IP Address 192.168.1.2
Subnet Mask 255.255.255.0
Default Gateway 192.168.1.1
S MPConfiguration enabled
readCommunity public
writeCommunity private

11.Firmware update
TCW120B supports remote firmware update. To do this please follow the steps below:
-Download the latest firmware version from www.teracom.cc . The extension of
the update file is .cod .
-Open Command Prompt window. In the example below in blue are the
commands that must be entered, and in red are the descriptions of these
commands :
C:\> -- go to the directory where the update file is located ( .cod extension)
C:\>ftp 212.73.154.53 -- FTP connection to the controller is made
Connected to 212.73.154.53.
220 Ready
User (212.73.154.53:(none)): admin -- enter username
331 Password required
Password: ***** -- enter password
230 Logged in
ftp> put tera_ipv1.32a.cod -- the update file is sent for update
200 Ok
150 Transferring data...
File is OK. Restarting Device... – 2 minutes after this message appears, the de ice will be
successfully updated
ftp: 329798 bytes sent in 92.44Seconds 3.57Kbytes/sec
ftp>
Re . 2 – April, 2011
O NOT TURN OFF THE POWER SUPPLY URING THESE 2 MINUTES!
TURNING OFF THE POWER SUPPLY WILL AMAGE THE EVICE!
For further information contact Omni Instruments by phone on +44 845 9000 601 or via email at [email protected].com
Table of contents
Popular Controllers manuals by other brands
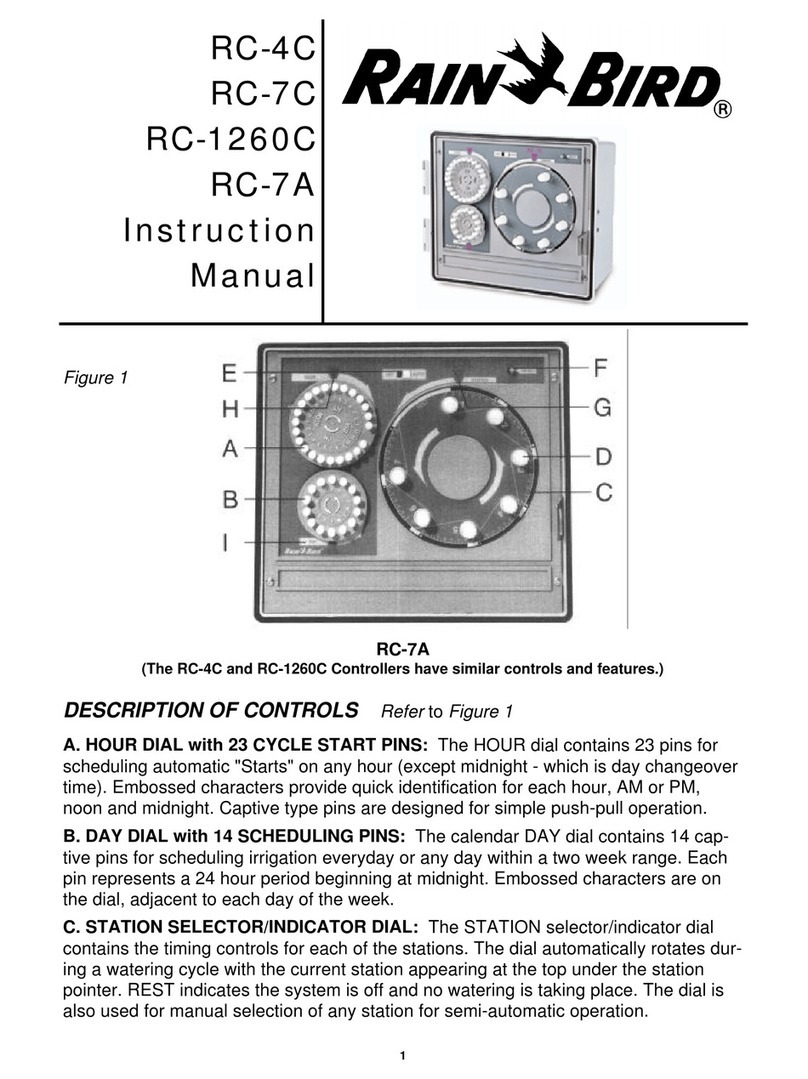
Rain Bird
Rain Bird RC-4C instruction manual
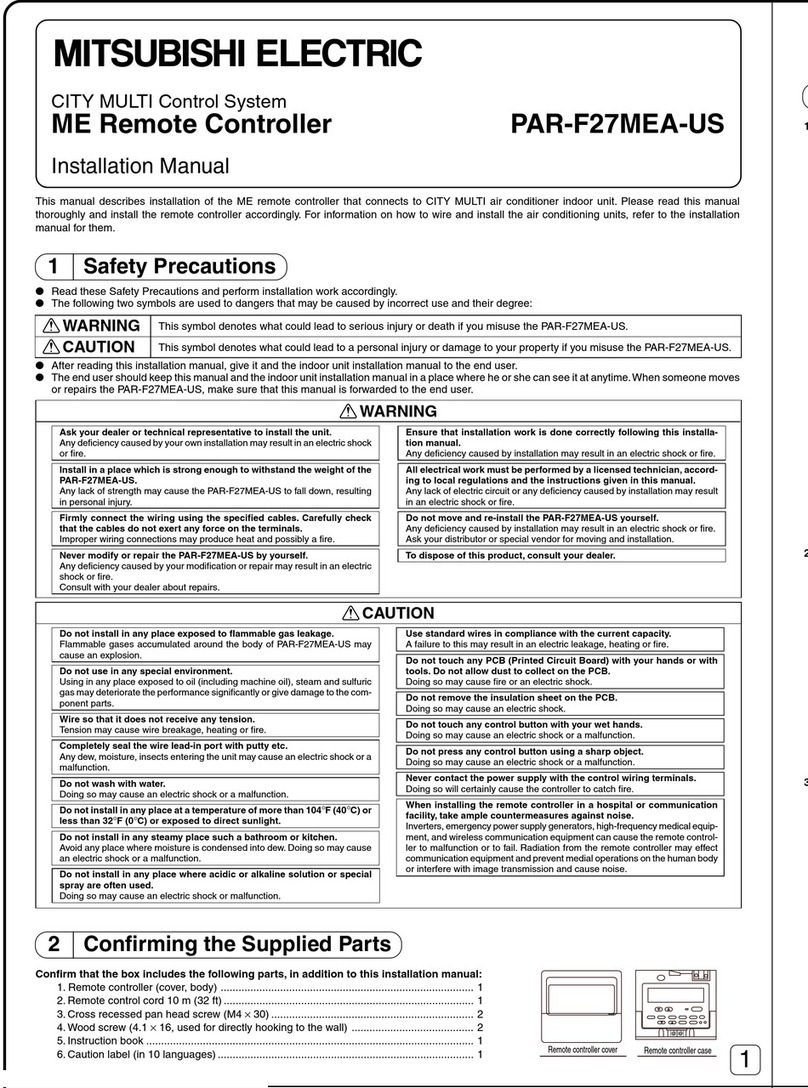
Mitsubishi Electric
Mitsubishi Electric PAR-F27MEA-US installation manual
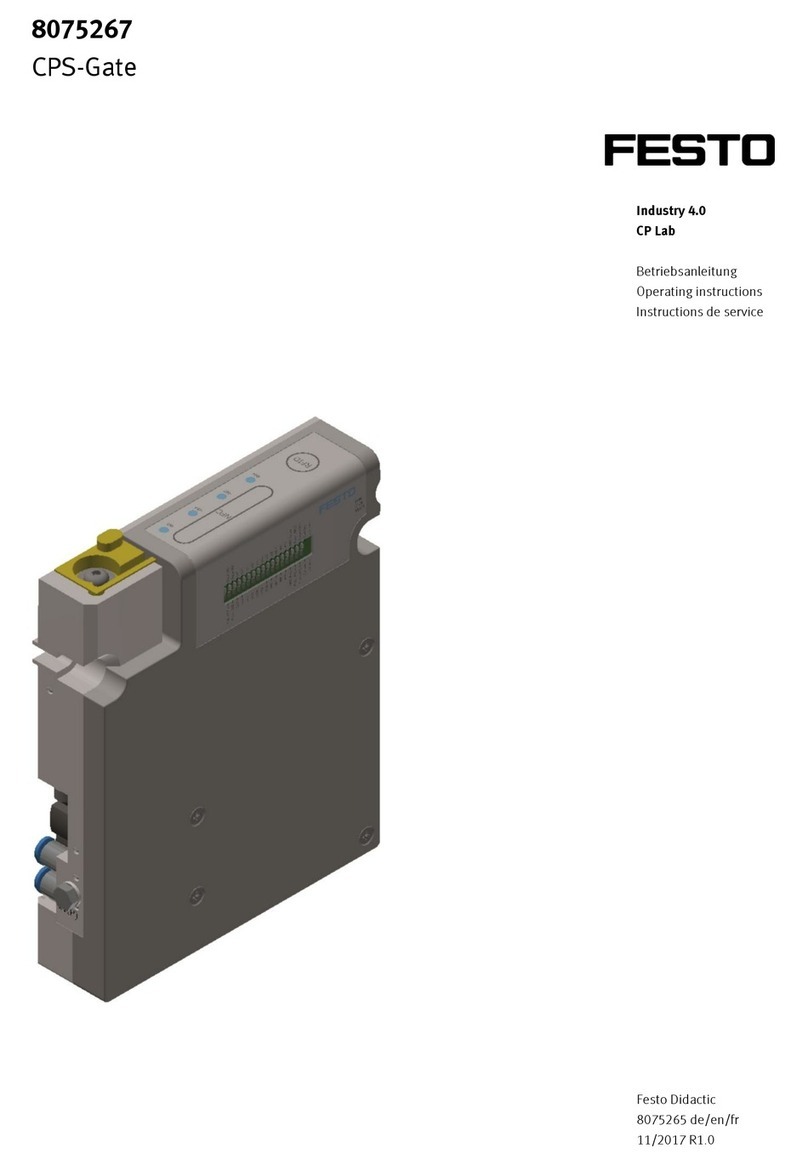
Festo
Festo CPS-Gate operating instructions
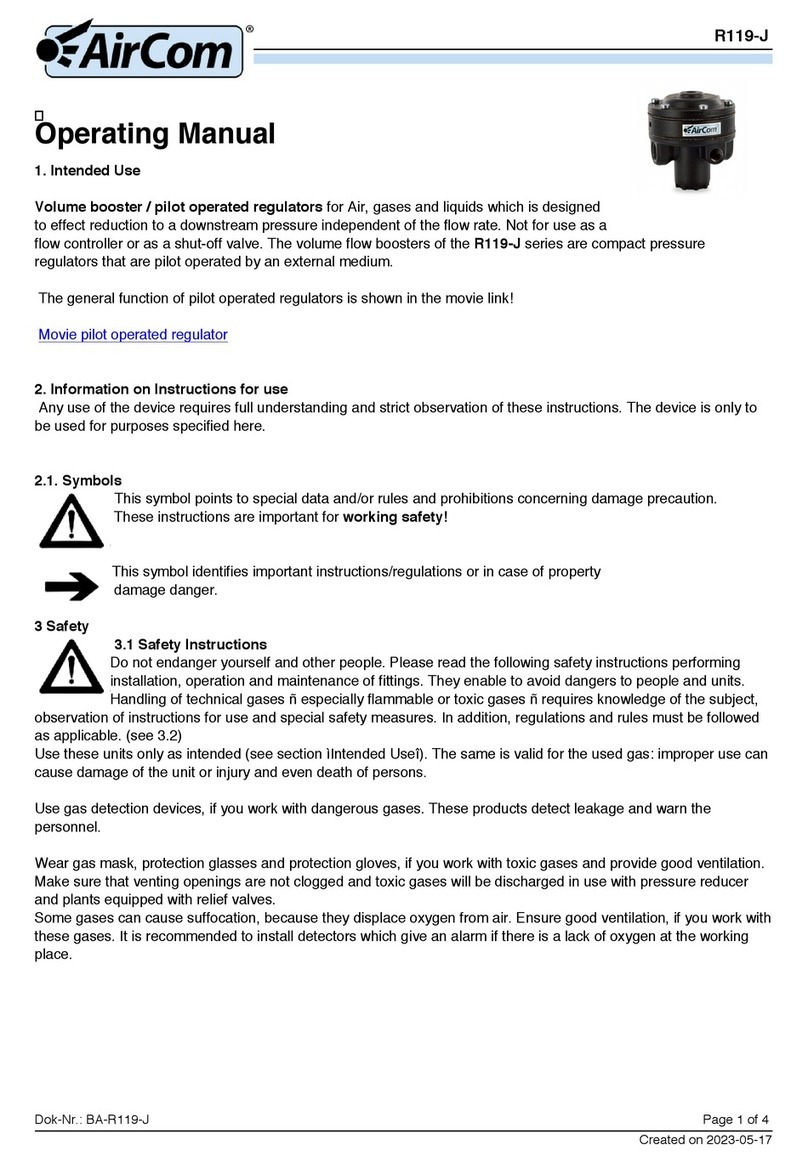
AirCom
AirCom R119-J operating manual
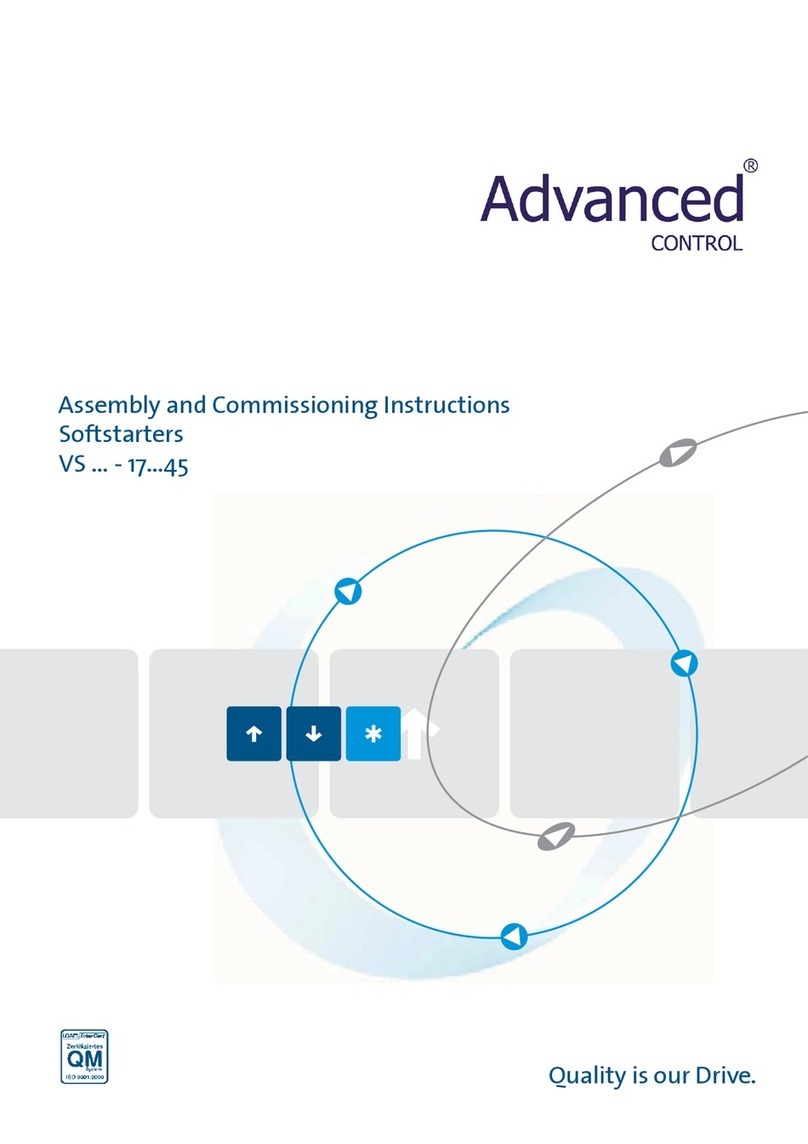
Advanced Control
Advanced Control VersiStart II Series Assembly and commissioning instructions

American Megatrends
American Megatrends MegaRAC MG9070 datasheet