Omnitec Design Omniaire 18000 User manual

Operation and Maintenance Manual
18000
HEPA Air Filtration Machine

CONFORMS TO UL STD 507
CERTIFIED TO CAN/CSA STD
C22.2 NO. 113-M1984
WARNING
Do not use with combustible or explosive material. Do not expose to water or rain. Connect
only to grounded outlet with GFCI device. Disconnect power for cleaning and servicing.
This equipment to be operated only by trained personnel.
Safety Warning Instructions:
READ AND SAVE THESE INSTRUCTIONS
This equipment to be operated only by trained personnel.
Do not use with combustible or explosive material.
Do not expose to water or rain.
Connect only to grounded outlet with GFCI device.
Disconnect power for cleaning and servicing.
Do not operate if cord or plug is damaged. Contact a authorized service facility for examination and/or repair.
Do not run cord under carpeting. Do not cover cord with throw rugs, runners, or similar coverings. Arrange cord away
from traffic areas and where it is not a tripping hazard.
Avertissement de sécurité Instructions:
LIRE ET CONSERVER CES INSTRUCTIONS
Cet équipement doit être utilisé que par un personnel formé.
Ne pas utiliser avec des matières combustibles ou explosives.
Ne pas exposer à l’eau ou à la pluie.
Connectez uniquement à une prise mise à la terre avec un dispositif GFCI.
Coupez l’alimentation électrique pour le nettoyage et l’entretien.
Ne pas utiliser si le cordon ou la fiche est endommagé. Contactez un centre de service autorisé pour examen et / ou
réparation.
Ne pas passer le cordon sous un tapis. Ne pas couvrir le cordon avec des carpettes, les coureurs, ou revêtements simi-
laires. Éloigner le cordon des endroits passants et où il n’est pas un risque de déclenchement.

The OmniAire 18000 is our largest portable HEPA air system with a 18,000 CFM air flow capacity. The
OA18000 is a modular air filtration machine with a unique versatility in setup and number of optional filters to assist
you on your projects. The OmniAire 18000 can be used to purify and re-circulate air or create positive or negative air
pressure containment areas. It is used for mold, asbestos & lead abatement projects, construction sites, restoration
projects, water or fire damage clean-up and many other applications.
Blower Cabinet Features
The OmniAire 18000 modular system consists of Blower cabinet and three Filter cabinets, all connected by flex hoses.
The cabinets are easy to transport and setup at any type of projects, including high-rise buildings and HAZMAT
removal jobs. The Blower cabinet contains twin 22 vane-axial blowers with 7.5 HP motors and controls and operates
on a 3-phase 480 VAC/60HZ/30 AMP power source. The portable blower cabinet is mounted on (4) 4” heavy duty
casters with brakes. The reinforced steel internal frame enables the blower unit to be moved by forklift or crane.
HEPA Cabinet Features
Each Filter cabinet contains 3 filters, which could be 99.99% HEPA or bag filters. The individual filter cabinets each have
a differential pressure gauge to measure loading of the filters with particulates. Filter cabinets are mounted on casters
with brakes, weigh 200 lbs. when fully loaded with HEPA filters. Options such as HEPA, Carbon, and Bag filters allow
flexibility from project to project. Three (3) flex hoses connect the modular filter cabinets to the blower cabinet. Hoses
are 18” dia, 25’ long.
OmniAire 18000 Specifications
For Blower Unit: Quantity (1)
Airflow - 18000 cfm*
Power Requirement - 480V/60 Hz/3 phase/30 amp.
Controls - Dual motor starter boxes with 16A disconnects w/lockout feature, overload protection, contactor and ON/
OFF switch. Power ON Indicator and hour meter.
Blowers - (2) 22” Vaneaxial fans with 7.5 hp motors.
Blower Cabinets - Aircraft grade aluminum, closed end rivet construction. All seams are silicone sealed before riveting.
(4) - 4” locking casters for ease of movement, 900Lbs., 30” wide, 48” long, 72” high
Exhaust – (2) 24” diameter rings. Inlet (3) – 18” dia
contaminated
containment area
positive pressure
clean contained area
clean
ltered
air
sealed contaminated
containment area
sealed
clean room
clean
ltered
air
recirculation
sealed contaminated
clean
ltered
air
contaminated
air
negative pressure
sealed contaminated
sealed
clean room
clean
ltered
air
negative pressure
contaminated room
clean
ltered
air
contaminated
air
contaminated
air
contaminated
air
contaminated
containment area
positive pressure
clean contained area
clean
ltered
air
sealed contaminated
containment area
sealed
clean room
clean
ltered
air
recirculation
sealed contaminated
clean
ltered
air
contaminated
air
negative pressure
sealed contaminated
sealed
clean room
clean
ltered
air
negative pressure
contaminated room
clean
ltered
air
contaminated
air
contaminated
air
contaminated
air
To create NEGATIVE PRESSURE inside the containment,
more air has to be exhausted out than leaks into the
containment. Place the machine inside the containment
and hook a flexible duct to the outlet ring of the
machine exhausting to outside the containment.
(See Above) All of the air being exhausted has been
treated by the HEPA filter so no contaminants are being
exhausted from the containment.
To create POSITIVE PRESSURE inside the containment,
more air has to be pumped in than leaks out of the
containment. Place the machine outside the containment
and hook a flexible duct to the outlet ring of the machine
ducting the exhaust into the containment. (See Above)
Application Examples

OmniAire 18000 Specifications (continued)
For Filter Cabinets: Quantity (3)
Powder coated galvanized steel, closed end rivet construction. All seams are silicone sealed before riveting.
200 lbs. Ea. (with filters), 26” wide, 80” high, and 28” long, (4) 3” locking casters for ease of movement.
Outlet connection 18” dia ring, Inlet (3) 12” dia. rings
Filter’s dust loading gauge - 0”-5” WC
Filtration Stages
• Final stage HEPA Filter 99.99%, 0.3µ,
• Primary/secondary MERV 9 polypad filter
• Optional OdorGuard 600 carbon filter
• Optional MERV 14 multi-pocket bag filter
Flexible hoses – (3) 18” dia hoses, 25’ long, Vinyl material, wire reinforced, rated at operation of 10” WC of vacuum. *
Airflows are based on blower manufacturer curves. Different HEPA filters may cause the flow to vary.
If the filter is not seated correctly then remove the filter tabs, reposition the filter, and reinstall the filter tabs before
operation to ensure that there is no bypass around the filter. If the filter tabs are loose, verify that the filter is in the
correct position and retighten the filter tab nuts.
Important Instructions
Read all the instructions before using this machine.
• Connect ONLY to outlets that are properly grounded.
• Do not operate blower with damaged cord or plug or after it has been damaged in any manner.
• Place cord out of the path of foot and equipment traffic to avoid trip hazard.
• To shut down the blower unit, turn both motors off and then unplug the cord.
• Do not locate the blower cabinet outdoors, use only in DRY locations.
• The motor and the protection circuit has arcing or sparking parts inside. Avoid operating in an environment with
flammable liquids, gas, or paint.
• Do not use to exhaust combustible or explosive gases or operate in hazardous atmosphere.
• Do not insert or allow foreign objects to enter intake or outlet openings as this may cause electrical shock or fire and
will damage the blower.
• DO NOT BLOCK OFF blower cabinet INTAKES or operate HEPA filter cabinets above 4.0” WC of vacuum to prevent
possible damage to the blower cabinet, HEPA filters and the HEPA cabinets. All three blower intake connections to
HEPA cabinets must have hoses rated to operate at 10” WC vacuum or more.
• DO NOT operate the system without all 9 HEPA filters securely in place.
• Always unplug unit when not in use.
• Use the OA18000 only as prescribed, any other use may cause fire, shock or injury to persons.
SAVE THESE INSTRUCTIONS
WARNING: GROUNDING INSTRUCTIONS - This appliance must be grounded. In the event of a malfunction or
breakdown, grounding will reduce the risk of electric shock by providing a path of least resistance for electric current.
This appliance is equipped with a cord having an appliance-grounding conductor and/or a grounding plug. The
plug must be plugged into an appropriate outlet that is installed and grounded in accordance with all local codes
and ordinances.
WARNING
Improper connection of the appliance-grounding conductor can result in a risk of electric shock. Check with a
qualified electrician or service representative if you are in doubt whether the appliance is properly grounded. Do not

modify the plug provided with the appliance; if it will not fit the outlet, have a proper outlet installed by a qualified
technician.
Introduction
OmniAire 18000 consists of a blower unit and three HEPA cabinets. The HEPA cabinets must be connected to the
blower unit with three flexible hoses at all time for the system to operate properly.
The Blower unit contains two 22” vaneaxial blowers with direct drive motors. Two motor starter enclosures are
mounted on the front of the blower cabinet. One power cord connects the unit to 240 VAC/3 phase/50-amp power
supply. The intake side of the Blower unit has (3) 18” rings for flex hoses from HEPA cabinets. The exhaust side of the
machine has (2) – 24” rings which could be left open or ducted.
Each HEPA cabinet holds three HEPA filters and pre-filters. The HEPA filters are secured with 4 tabs to maintain a tight
seal to prevent any air bypass around HEPA filters. Each HEPA cabinet has a vacuum gage, 0’-5” WC, to measure
pressure drop across the filters, representing loading of filters with dust. All three HEPA filters must be installed and
function properly for the system to operate. The function of the prefilter is to capture larger dust particles and to
extend the operation of the HEPA. The dense, orange side of pre-filter must face the HEPA.
All three HEPA cabinets must be connected to blower cabinet to assure proper operation of the whole system. The
hoses have to be rated to operate at minimum of 10” WC of vacuum.
Unpacking and Preparation
• Check the HEPA cabinets for any distortion or damage.
• The motor blower unit has reinforced frame mounted inside the cabinet and the entire unit can be safely lifted off the
pallet with a fork lift. The weight is over 900 lbs.
• Each filter cabinet contains three HEPA filters and weighs approximately 200 lbs. The construction of the filter cabinet
is designed to be moved around with a fork lift as well.
• Remove the primary/secondary filters and check the HEPA filters for any visible damage and see that it is seated
properly.
The HEPA must be seated well against the internal housing flange and the bottom supports. The tabs must be tight to
compress the HEPA gasket to the HEPA filter.
NOTE: If any one of the HEPA filters is leaking or has a bypass, the whole system will fail the required DOP efficiency
test.
The blower cabinet with motor controls should be inspected for visible damages. The intake plenum which operates
under vacuum must be well sealed.
Inspect flex hoses for cuts, tears and breaks. The hoses must be secured to the rings on the HEPA cabinets and the
blower cabinet with clamps to prevent any air leaks. The ducting operates under negative pressure of 2“-4” WC and
any small openings or cuts will allow contaminants to enter the purified air. Periodically check the silicone seal around
all the rings.
Operation
The OmniAire 18000 offers many variations for the set-up of the blower and filter cabinets. To protect the blower
cabinet from contamination of asbestos or other hazardous materials, the unit could be operating in a clean
environment while the filter cabinets could be inside the containment area connected by flex ducting. For Asbestos
and mold abatement, the machine must be operated with all HEPA filters in place. Also, it is recommended to use
the primary/secondary filter and replace it frequently to extend the life of the HEPA. Check that the blower cabinet is
connected to three HEPA filter cabinets and the filters are properly installed.

It is important to closely monitor the differential pressure gauge, 0”-5” WC on each of the HEPA filter cabinets
to not exceed the safe operating DP of 4” WC. Operating at a higher differential pressure could reduce the
required efficiency of the HEPA filters and release contaminants downstream. (See Replacement of Filters
below). Our powerful blowers are capable of producing up to 9” WC negative pressure when the HEPA filters
are fully loaded with dust.
To Start the Machine
With flex hoses connected, move the HEPA cabinets to desired positions and block the wheels. The hoses should be
running straight to minimize airflow resistance.
To turn the machine on, plug the power cord into a 480VAC, 60Hz, 30Amp outlet or hard wired to a generator.
To start blower #1, place the motor starter disconnect switch handle in the ON position and then push the START
pushbutton. Let the blower run for about 10 seconds. Then turn ON blower #2. Check the DP indicator on each of the
filter cabinets. When filters are clean, the DP gauge will read about 2.1” WC. As the filters fill with dust the efficiency of
the filters is maintained, but the air flow will decrease, and the vacuum reading will increase. Change the primary/
secondary filter frequently to protect the HEPA and to get more air flow. The HEPA filter must be replaced before the DP
gauge reaches 4.0” WC.
Check the vacuum reading on all HEPA cabinets. Note the vacuum reading while all filters are clean. With all clean
filters, the flow should be evenly distributed, and the DP gauge should read about 1.8”-2.0” WC. The filters will gradually
load with dust and the gauge reading will increase. Loading may not be evenly distributed as some HEPA cabinets
may be in an area with more dust.
DO NOT OPERATE THE HEPA CABINETS ABOVE 4.0” WC.
NOTE:
• Primary filters can be changed while the machine is running.
• The OA18000 can run with a single blower but all (3) HEPA cabinets must be connected to the blower cabinet.
• As the filters fill with dust, the efficiency of the filters are maintained, but the air flow will decrease and the vacuum
reading will increase.
• Change the primary filters frequently to protect the HEPA and to get more air flow. When the vacuum reaches about
3.5” WC with a clean prefilter, the HEPA filter will have to be replaced to increase the air flow.
To turn OFF the machine
Push the STOP pushbutton for each blower. Then turn the motor starter disconnect switch handle to the OFF position
to prevent unauthorized operation of the equipment. The disconnect switch handle can be padlocked. Please see the
manual for motor switch disconnect switch handle instructions.
WARNING
The HEPA filters and the cabinets are designed to operate at maximum of 4.5” WC of vacuum. When filters get fully
loaded with dust, the blowers are capable of generating 9” WC of vacuum and may destroy the HEPA, and potentially
the integrity of the HEPA cabinets. The vacuum reading on individual HEPA cabinets must be monitored and not to
exceed 4.0” WC.
Troubleshooting
Your Omnitec Design machine is designed and engineered to provide years of trouble-free service. Occasionally
problems occur. Here are some helpful tips and solutions to common issues.
Unit does not start
Check that the unit is plugged in and there is 480VAC available and verify power is available. Check that the motor
starter disconnect switch handle is in the ON position, then push START on the pushbutton. Test one blower at a time

to determine which one is failing to start.
Machine starts but shuts down
Check that the unit is plugged in and there is 480VAC/30Amps available power. Check that the motor starter
disconnect switch handle is in the ON position, then push START on the pushbutton. Test one blower at a time to
determine which one is failing to start.
Each motor blower has a separate starter cabinet with overload protection which may be set to low. Unplug the
power cord. Open the motor starter as described above and check the overload protection setting. The dial knob
should point to 11Amps. Push the RESET button. (See photos for adjusting the setting).
INSERT PHOTO
Blower starts yet no air flow
If the blower is running yet no air is coming from the outlet, it indicates the blower is running backward. To reverse the
operation of the blower, your qualified electrician will need to swap any 2 phases on the power cord connection or
in the motor starter enclosure. To proceed, unplug the unit from the power source. Turn the motor starter disconnect
switch handle to the OFF position to unlatch the internal interlock. Remove the two screws to open the enclosure. Test
the performance of both blowers individually to insure proper operation.
Machine starts to vibrate
Vibration could be caused by an imbalance of the propeller which runs at 3000 RPM. Please refer to the attached
Aerovent maintenance manual for cleaning and repairs.
Insert photo of motor starter with arrows pointing to the adjustment overload setting and reset button HERE
Maintenance
The OA18000 is easy to maintain. The HEPA cabinets are epoxy powder coated and can be easily cleaned.
Periodically examine the flex ducts for tears and rips. The ducting operates under negative pressure of 2“-4” WC and
any small openings or cuts will allow contaminants to enter the purified air.
When HEPA filters are removed, inspect the silicone seal inside the unit plenum and around the filter flange. Before
installing new HEPA filters, check the silicone seal around the filter flange and the forward, upper and lower corners of
the cabinets.
Check the flex hose connection rings on the blower units and filter cabinets to insure a silicone seal is around the inside
and outside of the ring where it is attached to the cabinet. The silicone seal will prevent contaminated air seeping into
filtered air.
Lubrication
The vaneaxial blowers require periodic lubrication. Grease fittings are easily accessible by removing the exhaust rings
door. Check the Aerovent manual for the maintenance schedule and the type of lubricants.
Filter Changes
Change the primary/secondary filters when…
Visual inspection - white filter side surface is loaded with dust and it starts to show on the orange side.
Pressure gauge – reading increased by 0.3” WC since the last clean pre-filter was installed.
Change the HEPA filter when…
Holes or cracks are found in HEPA filter media.
Air flow from the machine is not sufficient.

The pressure gauge reading, with clean HEPA filters is about 1.8”-2.0” WC, The HEPA filter will need to be replaced when
the pressure gauge reads 3.5” WC with a clean primary/secondary filter.
During your projects, your HEPA filter purifies the air and gradually becomes loaded with sub-micron particulates.
Even when the HEPA filter is fully loaded, the filter is still removing particulates from the air at the rated efficiency yet, at
a reduced airflow. This will affect the ability of the machine to provide positive or negative
pressure within the containment.
To replace the HEPA filter, turn the blower unit OFF. Open the door and remove the pre-
filter. You will see 4 filter tabs holding the HEPA filter in place (see photo). These tabs are
secured with 1/4-20 Nylock nuts, which require a 7/16” wrench or socket. Remove all (4)
filter tab retaining nuts, remove the filter and set aside. Slide the HEPA filter out along the
filter guides and remove it from the machine. ALWAYS TREAT THE USED HEPA FILTER AS
HAZMAT AND PROCESS IT ACCORDING TO YOUR ESTABLISHED HAZMAT PROCEDURES.
To replace the HEPA filter, ensure that the gasket on the HEPA filter faces inward toward
the flange, slide the filter in place along the filter guides and re-install the filter tabs and filter tab securing nuts. The
nuts should initially be tightened to where the stud is flush with the end of the nut. This will compress the gasket on the
filter approximately 1/2 of the thickness. This allows for the filter to be reseated and tightened later if necessary.
Bag Filter Replacement (if used)
The bag filter housing can be installed in the place of the HEPA filter using the filter tabs and nylock nuts. The bag filter
is secured inside the housing with (4) P-clips. To remove the filter, turn the P-clips 90 degrees and pull it out. Then install
the new bag filter and secure it using the P-clips.
Please note the bag filters have a large dust holding capacity and require replacement when the airflow of the
machine drops below required minimum flow or the DP gauge reaches 3.5” WC. Even when the filter is fully loaded, it
is still removing the particulates from the air at the rated efficiency but at a reduced airflow. Typically bag filters do not
require the use of prefilters.
Vapor Trap Filters
Activated carbon filters are designed to remove odors and gaseous pollutants from air. These filters are an effective
and quick solution to your VOC’s and odor problems. The selection of the carbon filter depends on the type and
amount of the gaseous pollutants. You will need to determine the requirements of your application. The Vapor Trap is
a disposable V-Bank, 24”x24”x12” filter and contains 36lb of activated granular carbon. It can be installed in place of a
HEPA filter. We recommend using our primary/secondary filter in front of the Vapor Trap to extend its odor absorption
capacity.
filter tab

Ordering Info Part #
OmniAire 18000 Blower OA18000B
HEPA Cabinet (3 required) OA18000F
HEPA Filter 99.99%, 0.3µ OAH2424G
Primary/Secondary Filter (qty 20) OAP2424
OdorGuard 600 Carbon Filter OG2424D
Carbon Vapor Trap, Disposable V-Bank, 36lbs of Carbon OCVT2424
Bag Filter Housing with one bag filter HBF2200
Bag Filter, MERV15 OBF10
PVC Hose, Wire Reinforced Flexible Duct, 18” x 25’ OARD18
Clamp S.S. with Worm Drive, 18” to 20” dia QCW18
Quick Clamp to 14” dia, Stainless Steel, Worm Drive, Quick Adjusting QCW14

LIMITED WARRANTY REGISTRATION
The undersigned has read and understood the above Warranty and Limitation of Warranty and Limitation of Remedy.
PRODUCT # SERIAL #
PURCHASED FROM DATE
CUSTOMER INFORMATION
COMPANY PHONE
STREET
CITY STATE ZIP CODE
BY DATE
PLEASE SEND TO:
Omnitec Design Inc 4640 Campus Place Ste. 100 Mukilteo, WA 98275
Omnitec Design Inc. LIMITED WARRANTY
Omnitec Design Inc warrants, for a period of twelve (12)
months from the date of purchase, that all Products,
component parts and accessories, excluding filters,
will be free from defects in material and workmanship
under normal use and service.
THE PURCHASER’S SOLE AND EXCLUSIVE REMEDY
UNDER THIS WARRANTY IS LIMITED TO THE REPAIR OR
REPLACEMENT OF DEFECTIVE PARTS F.O.B., Omnitec
Design Inc 4640 Campus Place Ste. 100, Mukilteo, WA
98275 Phone: 425-290-3922
In order to keep this warranty in effect for the
aforementioned twelve-month period, the purchaser
must (i) promptly, i.e., immediately upon discovery,
inform Omnitec Design Inc’s customer service of any
defects, and (ii) properly use and maintain the Product
prior to the discovery of any defect.
This warranty does not cover normal wear and tear or
defects caused by (i) improper or negligent handling or
unauthorized modifications; (ii) defective or improper
premises, chemical, or electrical influences; or (iii)
weather or other forces of nature.
In order to provide the best customer service possible,
Omnitec Design Inc requests that purchaser completes
the enclosed LIMITED WARRANTY REGISTRATION FORM
and returns it to Omnitec Design Inc within 30 days of
purchase date.
LIMITATIONS OF WARRANTY
THIS WARRANTY IS EXPRESSLY IN LIEU OF ANY AND ALL
OTHER WARRANTIES AND OBLIGATIONS OF Omnitec
Design Inc OR ITS SUPPLIERS, EXPRESS OR IMPLIED,
AND Omnitec Design Inc EXPRESSLY DISCLAIMS ANY
WARRANTY OF MERCHANTABILITY OR FITNESS FOR
ANY PARTICULAR PURPOSE.
LIMITATION OF REMEDY
Under no circumstances shall Omnitec Design Inc
or any supplier of Omnitec Design Inc be liable for
any loss or damage, including, but not limited to, loss
or damage arising out of the failure of the Products to
operate for any period of time, inconvenience, the use
of rental or replacement equipment, loss of profits or
other economic loss, or general, direct, special, indirect,
incidental or consequential damages or property
damages.
PRODUCT SUITABILITY
Many states and localities have their own varied
codes and regulations governing sales, construction,
installation, and/or use of Products for certain purposes.
While Omnitec Design Inc attempts to assure that its
Products comply with such codes, it cannot guarantee
compliance, and cannot be responsible for how the
Products are installed or used. Omnitec Design Inc
recommends that, before purchasing and using a
Product, purchasers review the Product application, and
federal, state and local regulations, to be sure that the
Products, installation, and use will comply with them.
Table of contents
Popular Fan manuals by other brands
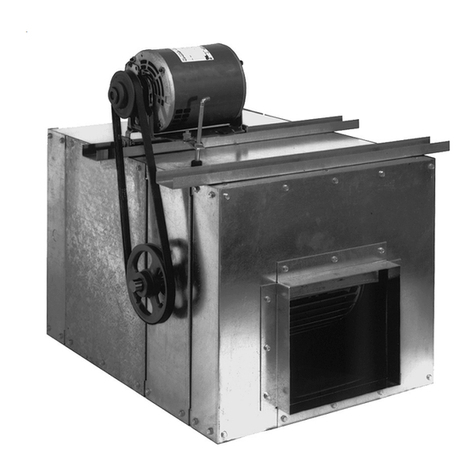
COOK
COOK SDB Installation, operation and maintenance manual
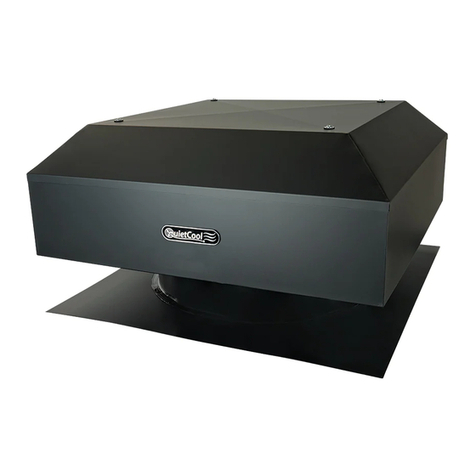
QuietCool
QuietCool AFR SMT ES-2.0 owner's guide
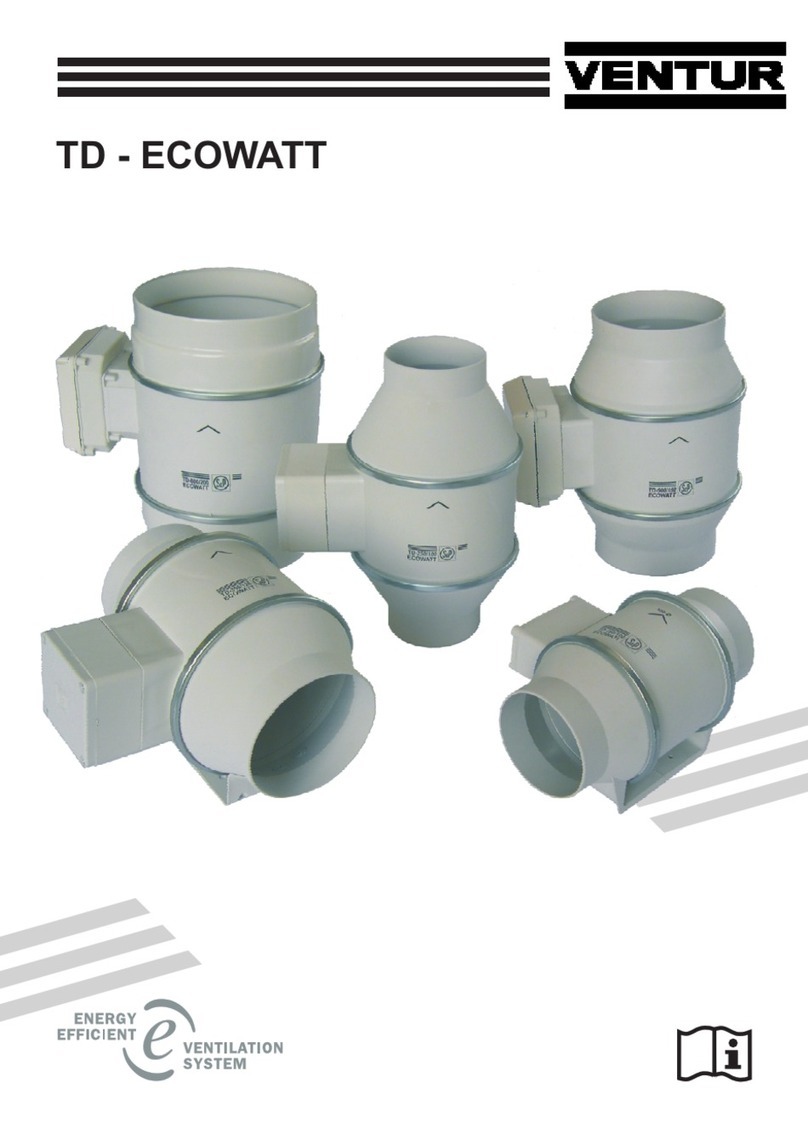
Ventur
Ventur TD - ECOWATT Series instruction manual
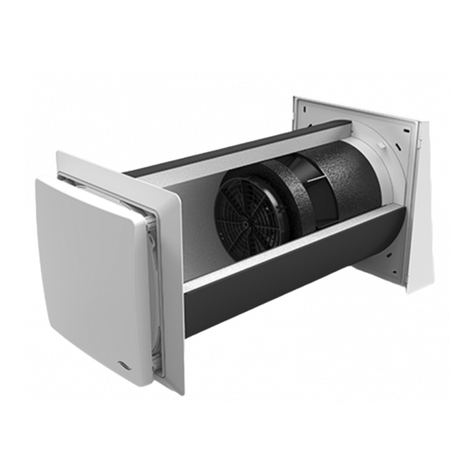
inVENTer
inVENTer iV-Office Installation and operating instructions

Westinghouse
Westinghouse 72249 manual
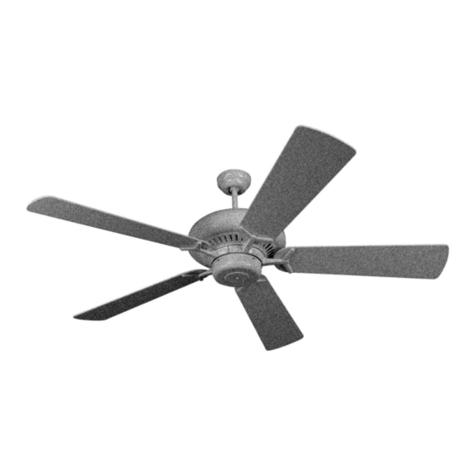
Monte Carlo Fan Company
Monte Carlo Fan Company 5GP60 Series owner's manual