ONEFINITY Elite Series Owner's manual

Installation and Operation Instructions
Onenity Elite Series

General Notes 3
Safety Rules 4-9
Description 10
Anatomy of the Onenity 11
Anatomy of the Z-Slider 12
Anatomy of the Power Supply Controller 13
Anatomy of the Onenity MASSO 14-15
Features and Specications 16
Elite Machine Dimensions 17
Assembling Instructions 18-33
Homing the Elite Onenity 34
Spindle/Router Installation 35-38
Wasteboard 39
Maintenance 40-41
Loading a program 42
Running G-Code 43-44
Resuming Program or Jump to Line 45
Wi-Fi Connectivity 46-47
Jogging 48
Feed Rate Override 49
Using the XYZ Touch Probe 50-52
F1 Screen 53
F2 Screen 54
F3 Screen 55
F4 Screen 56
F5 Screen 57
F6 Screen 58
Onenity Warranty Policy 59-60
Notes 61
Contact Us 62
Contents

This manual serves to familiarize you with your Onenity CNC machine and provide all neces-
sary information required to operate the machine safely and professionally.
This manual is applicable for the Onenity Elite Foreman, Journeyman and Woodworker
hereafter referred to as Onenity or Onenity Elite.
Please completely read this manual before the rst commissioning of your machine.
In order to minimize the risks of injury and/or material damages, please only commission the
machine and the corresponding control when you are sure that you have completely
understood these instructions!
Please contact us for any further questions. Please nd our contact info on page 36 of these
instructions.
Please always keep these instructions nearby the machine. You should always have them
readily available when you want to look up something.
Please only use this machine according to its intended use.
We cannot be held liable for persons or material damages which are caused by using the
machine other than the intended use, handling which does not comply with the common use
of a CNC machine or if safety regulations are not obeyed
In case of improper maintenance (refer to pages 40-41) and/or wrong operation of the indi-
vidual components your warranty claims are omitted.
We reserve the right to perform future technical enhancements on the machine and its com-
ponents.
General Notes

General Instructions:
These operating instructions explain the Onenity and the correct handling of the CNC sys-
tem. Please read these operating instructions and accompanying documents in their entirety
before commissioning of the system in order to become familiar with the characteristics and
the operation of the product. The improper operation of the CNC gantry milling system can
lead to damage to the product and property and can cause serious injuries, electric shock
and / or re. It is imperative to adhere to the safety instructions listed in these operating in-
structions at all times. Should you have any questions or concerns prior to initial use of the
CNC system or the need for further information, do not hesitate to contact us prior to the
commissioning of the CNC system.
Safety Instructions and Protective Measures:
(General Safety Warnings for the Use of Power Tools )
Work Area Safety
NOTICE: Keep work area clean and well lit. Cluttered or dark areas invite accidents.
Caution: Do not operate the power tool in explosive atmospheres, such as in the
presence of ammable liquids, gases or dust. Power tools create sparks which may
ignite the dust or fumes.
NOTICE: Keep children and bystanders at a distance while operating a power tool. Distrac-
tions can cause you to lose control and can result in accidents.
Caution: Operate the Onenity only in interior spaces on a solid, horizontal table or
workbench.
Electrical Safety:
Warning: Power tool plugs must match the outlet. Never modify the plug in any
way. Do not use any adapter plugs with grounded power tools. Unmodied plugs
and matching outlets will reduce the risk of electric defects and malfunctions.
Warning: Do not expose power tools to moisture. The power tool is only suitable for
indoor use. Water entering a laser tool will increase the risk of electric shocks.
Safety Rules

Personal Safety:
Caution: Stay alert, watch what you are doing and use common sense when operat-
ing a power tool. Do not use a power tool while you are tired and/or under the inu-
ence of drugs, alcohol or medication. A moment of inattention while operating a
power tool may result in serious personal injury.
NOTICE : All persons who operate the power tool must have read and fully understood all
relevant safety and operating instructions. Misunderstanding may result in personal injury.
Caution: Use personal protective equipment. Always wear eye protection. Protec-
tive equipment, such as a suitable dust mask or ear protection, reduces the risk of
injuries.
NOTICE: Dress properly. Do not wear loose clothing or jewelry. Pin your hair above your
shoulders so that it cannot get caught in the Ball Screws and linear guides or moving parts.
Caution: This tool is controlled by a computer. During operation, it cannot be con-
trolled directly. Lack of caution or expertise as well as program errors can lead to un-
expected movements.
Caution: Do not touch the insertion tools or motors as they can heat up signicantly
during operation.
Caution: Never place any parts of the tool or accessories in the mouth as this can
lead to serious injuries.
Protective Measures:
The Onenity has been constructed for advanced users and is only to be operated by techni-
cally skilled persons above the age of 16. The CNC gantry milling system as well as associated
tools, small parts and electrical components are to be stored outside the reach of children.
The operator is solely responsible for understanding and reading the machine user guide and
all relevant operating instructions in their entirety. These documents should always be stor-
age in immediate vicinity of the machine. The manufacturer`s instructions concerning the
CNC machine and the tools, such as the milling spindle, are to be adhered to. The CNC gantry
milling system is only to be used in a technically perfect condition which is to be ensured prior
to each operation. The emergency switch as well as, if applicable, additional safety devices,
always need to be easily accessible and fully functional. The use of liquids with the machine,
such as the application of a coolant pump, is prohibited as it can damage the electronics. The
use of lubrication systems is allowed. Please take into consideration that in this case the MDF
machine table is not used as its MDF panels can swell and, thus, be destroyed.
Safety Rules

Use of the Power Tool:
Caution: Do not alter or misuse the tool. Any alteration or modication is a misuse
and may result in serious personal injury.
Caution: Disconnect the plug from the power source before you make any adjust-
ments, change accessories, or store the tool. Such preventative safety measures re-
duce the risk of starting the power tool accidentally.
Caution: Store idle power tools out of the reach of children and do not allow persons
unfamiliar with the laser tool or these instructions to operate the power tool. Power
tools are dangerous in the hands of untrained users.
NOTICE: Use the power tools, accessories etc. in accordance with these instructions, taking
into account the working conditions and the work to be performed. Use of the power tool for
operations dierent from those intended could result in a hazardous situation with high proba-
bility of supercial injury.
NOTICE: Do not reach into the area of the rotating insertion tools. The proximity of the rotat-
ing tools to your hand may not always be obvious.
NOTICE: Never use dull or damaged insertion tools. Sharp bits must be handled with care.
Damaged bits can snap during use. Dull bits require more force to cut the tool, possibly causing
the bit to break.
NOTICE: The speed and feed of the bit when carving, routing or cutting is very important. Al-
ways observe the recommended speed and feed for the particular bit.
Caution: If the workpiece or bit becomes jammed or bogged down, turn the power
tool "OFF" by the switch. Wait for all moving parts to stop and unplug the tool, then
free the jammed material. If the switch to the tool is left "ON", the tool could restart
unexpectedly causing serious personal injury.
NOTICE: Do not leave a running tool unattended, turn power o. Only when tool comes to a
complete stop and is disconnected from the mains it is safe.
Caution: Do not touch the bit or collet after use. After usage bit and collet are too hot
to be touched with bare hands.
NOTICE: Do not allow familiarity gained from frequent use become commonplace. Always re-
member that a careless fraction of a second is sucient to inict severe injury.
Caution: When using the end mills, V-bits or cutters, always have the workpiece se-
curely clamped. Never attempt to hold the workpiece with your hands while using any
accessories. These tools can jam easily in the material, and can kickback, causing loss
of control resulting in serious injury.
Safety Rules

Care of the Power Tool:
NOTICE: Maintain the tools. Check for misalignment or binding of moving parts, breakage of
parts and any other conditions that may aect the power tool's operation. If damaged, have
the power tool repaired before use. Many accidents are caused by poorly maintained power
tools.
Additional Safety Instructions
Caution: Depending on the application eld of the machine (private or commercial),
observe the applicable occupational safety and health, safety and accident preven-
tion and environmental regulations.
Caution: Some dust created by cutting, milling or other construction activities con-
tains chemicals known to cause cancer, birth defects or other reproductive harm.
Some examples of these chemicals are: Lead from nonferrous metals with lead con-
tent, carbonate from carbon ber, arsenic and chromium from chemically treated lumber.
Your risk from exposures to these varies, depending on how often you perform this type of
work. To reduce your exposure to these chemicals, work in a well ventilated area, and work
with approved safety equipment, such as those dust masks that are specially designed to l-
ter out microscopic particles.
Safely dispose of milling debris — recycle or safely dispose of milling debris and dust, keeping
in mind ammability, (potential) spontaneous combustion, and chemical considerations.
Even natural materials can have surprising implications for disposing of them, e.g., walnut
wood dust is aleopathic (inhibits plant growth) and an irritant to the skin and breathing tract
and potentially poisonous to some animals in addition to the typical spontaneous combus-
tion hazard which sawdust poses.
Personal Protective Equipment:
When working with the CNC gantry system, the operator has to wear at least the following
personal protective equipment and has to be compliant with the below-mentioned safety as-
pects: - Safety googles for protecting the eyes against ying chips etc. - Ear protection for
protecting the ears against sound and noise. - No wearing of clothes which can get caught in
the machine, such as ties, scarves, wide sleeves etc. Additionally, jewelry and especially long
necklaces and rings are to be dispensed with. - Shoulder-length or longer hair is to be secured
with a hairnet or a hat to prevent it from getting caught in the linear guides and / or rotating
tools. Prior to all adjustments to the machine, its control or system-guided tools, such as the
Milling Motor, the Drag Knife or the Hot Wire Cutter, the plug is to be disconnected from the
power source. Never hold the workpiece to be processed with your hands. It is mandatory
that the workpiece is securely xed on the machine table. Otherwise there exists a high risk
of injuries!
Safety Rules

Emergency Stop Switch :
The emergency stop is located on the top of the Controller housing. In order to be able to inter-
vene at all times, the emergency stop has to be positioned in a suitable place. The controller
must be located so it can be reached from any possible operator position.
By pressing the emergency stop switch, the emergency stop is triggered. The control is inter-
rupted. Additionally, the control software receives the signal to stop the operating process. The
machine stops immediately.
ATTENTION! The emergency stop switch can only eect the stop of all components if these
components are electronically connected with the emergency stop switch.
If you want to use a system-guided tool, such as a milling and drilling motor, that features a sep-
arate ON / OFF switch and that is NOT controlled via the PC, you have to make sure that it is ex-
pertly connected with the emergency stop switch. If you do not comply with these require-
ments, the system-guided tool will continue to run although you have activated the emergency
stop switch leading to a high risk of personal injury and damage to property! If you have any
questions, please do not hesitate to contact us!
Residual Risk:
Despite all safety precautions against the contact with rotating or hot tools and the protection
from crushes, a residual risk remains due to a careless handling and automatic movements of
the CNC system.
Safety Rules

Read the following carefully before operating the machine.
1. Keep the working area clean and ensure adequate lighting is available.
2. Do not wear loose clothing, gloves, bracelets, necklaces or ornaments.
3. Do wear face, eye, respiratory and body protection devices as indicated for the operation
or environment.
4. Ensure that the power is disconnected from the machine before tools are serviced or any
attachment is to be tted or removed.
5. Never leave the machine with the power on.
6. Do not use dull, gummy or cracked cutting tools.
7. Ensure that the keys and adjusting wrenches have been removed and all the nuts and
bolts are secured.
8. Hearing protection — ear plugs or mus, for long jobs doubling up on ear plugs or mus
may be desirable. Hearing damage is cumulative and irreversible, so one should err on the
side of caution
9. Use care when handling endmills, both to avoid being cut, and to avoid damaging them.
Handling them with suitable gloves, or using a cloth to avoid contaminating them is recom-
mended. Inspect them carefully before each use and ensure that they are securely held by the
collet.
10. Never leave the machine running unattended/unsupervised.
11. Always inform someone before operating the machine and check in with them after suc-
cessfully completing work.
Workspace:
The workspace needs to provide enough space around the Onenity CNC for the machine to
work comfortably and to be able to fully use its traveling paths. Additionally, a safe distance
to possibly nearby positioned machines is to be maintained. The location of the machine as
well as the workplace surrounding the machine has to be suciently illuminated.
As with all machinery, there are certain hazards involved with the operation and use of your
machine. Using it with caution will considerably lessen the possibility of personal injury. How-
ever, if normal safety precautions are overlooked or ignored, personal injury to the operator
may result. If you have any questions relating to the installation and operation, do not use the
equipment until you have contacted your supplying distributor.
Safety Rules

The Onenity is a multifunctional CNC gantry milling system for the permanent and regular
processing of wood, plastics and non-ferrous metals.
Thanks to the innovative design, how and where you carve is limitless! Feel like carving
an intricate inlay into your dining table, no problem? Have a small shop where space
is limited, Onenity has been designed to be quickly dismantled and stored!
With Fast Travel Precision Ball Screws, gone are the stretchy belts and high mainte-
nance Lead Screws found on similarly priced machines. Hardened Steel Hollow Linear
Motion Shafts means no more plastic wheels that require frequent adjustment and a
powerful CNC controller with built in CAM software and HD Touch Display allows for opera-
tion without a computer!
The machine has three axes which are oset by 90°. This way, it is possible to travel to any
point within the working space. Each axis is equipped with up to two stepper motors and Infra-
red homing. The stepper motors drive the movable axes elements via precision ball screws.
The position of the axis is determined during the reference run (homing cycles), at the begin-
ning of the job, with the aid of the homing. The machine table may consist of any solid at
surface big enough to mount the Rails and Controller. The Onenity consists of the following,
sometimes optional, components: - Onenity Elite Foreman, Journeyman or Woodworker; -
Onenity MASSO electronic control unit, Power Supply Controller in a separate aluminum
housing, Z-Slider, Wire harness and Hardware.
Description

High Load
Linear Bearings
Powerful Controller
No Computer Required
15 Hi-Def
Onenity MASSO
Heavy Duty
Z-Slider
High Torque
Closed Loop Stepper Motors
Anatomy of the Onenity
Chrome Plated, Hardened Steel
Linear Shas
Precision, Fast Travel
Ball Screws
Important note: To learn all of the Onenity
MASSO controllers capabilities please visit:
https://www.masso.com.au/
Inferred
Homing Sensors

Anatomy of the Z-Slider
High Load
Linear Bearings
Spindle Mount
High Torque
NEMA 23 Motors
Chrome Plated, Hardened Steel
Linear Shas
Precision, Fast Travel
Ball Screws
Ball Screw
Coupler
Suckit Dust Boot
Mount
Ball Screw
Nut

Router Socket Fuse
(10 Amp)
Stepper Motor
Connector Ports
ON/OFF
Switch
Main Power Cord
Plug
Stepper Motor
Driver Fuses
(3 Amp)
Onenity MASSO
Power Connector
Anatomy of the Power Supply Controller
Auto On - O
Vacuum Socket
Main Power Fuse
(10 Amp)
Auto On - O
Router Socket
Vacuum Power Cord
Plug
Vacuum Socket Fuse
(10 Amp)

Tool Seer
Connector Port
Anatomy of the Onenity MASSO
Mounng
Bracket
B-Axis
Connector Port
Z-Axis
Connector Port
X-Axis
Connector Port
Spindle
Connector
Onenity MASSO
Power Connector
XYZ Probe
Connector Port
Laser
Connector Port
Y-Axis
Connector Port

Cycle Start
Switch
Anatomy of the Onenity MASSO
15” Touch
Display
Cycle Stop
Switch
Controlled
Stop Switch
Cover
Screws

Rapid Rate:
X Axis: 400 inches/min (accel 750 km/min2)
Y Axis: 400 inches/min (accel 750 km/min2)
Z Axis: 300 inches/min (accel 750 km/min2)
Cung Area Woodworker:
X Axis: 32- 1/4 inches
Y Axis: 32- 1/4 inches
Z Axis (Gantry Clearance): 5 inches
Cung Area Journeyman:
X Axis: 48- 1/8 inches
Y Axis: 32- 1/4 inches
Z Axis (Gantry Clearance): 5 inches
Cung Area Foreman:
X Axis: 48- 1/16 inches
Y Axis: 48– 3/4 inches
Z Axis (Gantry Clearance): 7 inches
Specicaons:
16mm Ball Screws on X and Y axis
16mm Ball Screw on Z axis
Chrome plated, hardened steel linear shas on all axis
5 motor driver channels
15 inch Onenity Masso
Up to 256 microstepping
250k steps/second on each motor output
Infrared homing sensors with auto squaring
Feature:
Advanced, custom designed, Onenity MASSO Touch
Massive 15-inch high denion industrial capacive touch LED screen
Rigid, high precision, hardened steel, linear moon Shas
High speed, long travel, Z-20 heavy duty Z-Slider
Powerful “an-skip,” closed loop stepper motors
Conveniently located Emergency Stop
Plug and Play wiring supported by drag chains
Wi-Fi enabled
Built in Auto on/o router outlet
Built in Auto on/o Vacuum outlet
Plug and play XYZ Probe (oponal)
Plug and play Tool Seer (oponal)
Power Loss Recovery
Jump to Line
Connuous and incremental jogging via touch screen
Feed Rate Override - Adjust feed rate during a carve
Mulple Work osets (G54-G59)
Micro Tramming
Quick and easy setup - start carving in under an hour
Solid, self supporng QCW with leveling feet (oponal)
7, 12 & 24 wa Laser (oponal—plug and play)
Fixed or Rolling - Folding Stand with wobble free leveling feet (oponal)
Spindle support with on board controls
Each unit fully producon tested with a test carve
A large “how to” library with a very helpful and supporve community
Powerful Carveco Maker Advanced 3D Cad Soware (1 year subscripon)
Specications and Features
General Disclaimer:
While Onenity has made every eort at the me of publicaon to ensure the accuracy of the informaon provided herein, product specicaons, conguraons, system/component/opons availability
are all subject to change without noce. Product design specicaons and colours are subject to change without noce and may vary from those shown. Errors and omissions excepted. Images displayed
are for illustraon purposes only. The images are intended to help illustrate the product and it’s funcons and are not indicave of actual relave dierences.

Elite Woodworker Dimensions
General Disclaimer: While Onenity has made every eort at the me of publicaon to ensure the accuracy of the infor-
maon provided herein, product specicaons, conguraons, system/component/opons availability are all subject to
change without noce. Product design specicaons and colours are subject to change without noce and may vary from
those shown. Errors and omissions excepted. Images displayed are for illustraon purposes only. The images are intended to
help illustrate the product and it’s funcons and are not indicave of actual relave dierences.
Important note: For Journeyman add 16 inches to all X dimensions., Foreman add 16 inches to X and Y dimensions

The following instructions detail how to install your Onenity Elite CNC Machine. Please read these
entire instructions carefully. If you have any problems or do not understand these instructions please
contact us at support@onenitycnc.com or 1-888 717 4242 for further assistance.
For step-by-step instructional video’s and how-to’s please visit our Youtube page at:
https://www.youtube.com/onenitycnc. Note: It is highly recommended that you view all of our
assembly videos prior to attempting to assemble your Onenity machine. Our assembly videos can
be found at: youtube.com/onenitycnc
Step 1: Set Y-Rails (Green Arrows) on the bench and place them close to where you would like them to
be installed. See below picture.
Important: The Y-Rail with the Drag Chain must be placed on the left side (Red Arrow)
Note: For illustrative purposes, the drag chains have been removed from certain pictures.
Step 2: Slide the Gantry assembly (Green Arrow) all the way to the front until it’s tight to the
Rail End (Blue Arrow). See below pictures. (Note: you can also turn the ball screw to get the
Gantry Assembly to move to the front). Important: Make sure they are all the way to the front!
Assembly Instructions

Foreman Version Only: When installing your Foreman onto a surface other than the QCW, the
supplied riser blocks (Red Arrows) are required. The Foreman Riser Blocks ensure that the Y-Axis
Gantry blocks clear the table surface.
Assembly Instructions

Step 3: Place the X-Rail (Green Arrow) on the Y-Rails Gantry Blocks (Blue Arrows)
Step 4: Adjust Y-Rails (Red Arrows) until the Gantry Assemblies (Green Arrows) are ush
with X-Rail Ends (Blue Arrows). Note: It is important that these parts are ush with each
other before fastening together.
Assembly Instructions
Table of contents
Other ONEFINITY Control System manuals
Popular Control System manuals by other brands
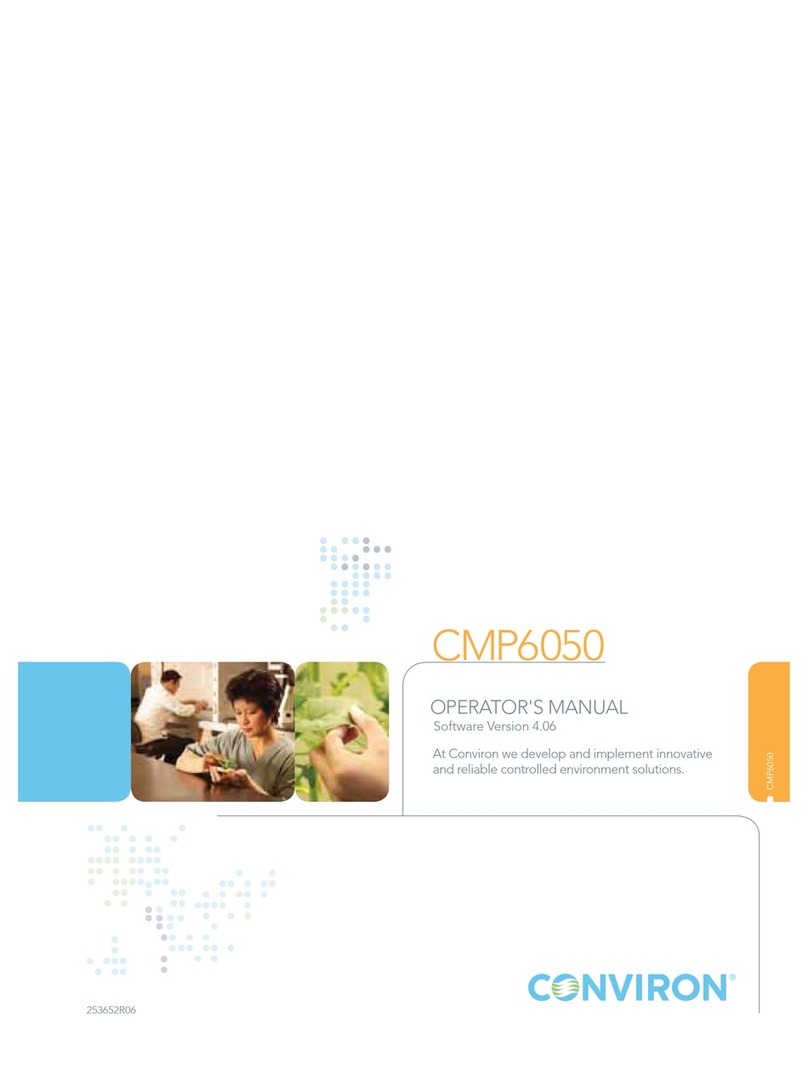
Conviron
Conviron CMP6050 Operator's manual
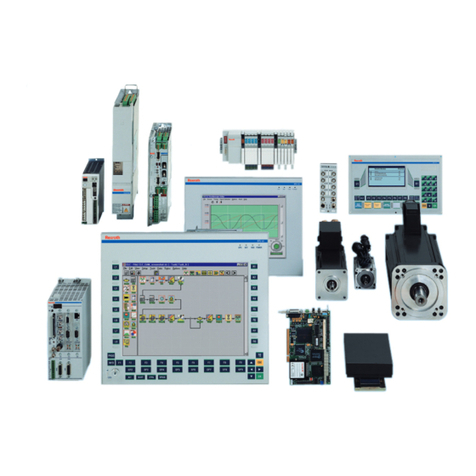
REXROTH
REXROTH VisualMotion 9 troubleshooting guide
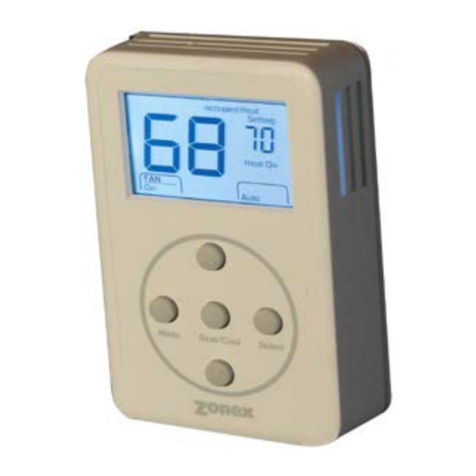
Zonex
Zonex System 2000 GEN II Installation and application manual
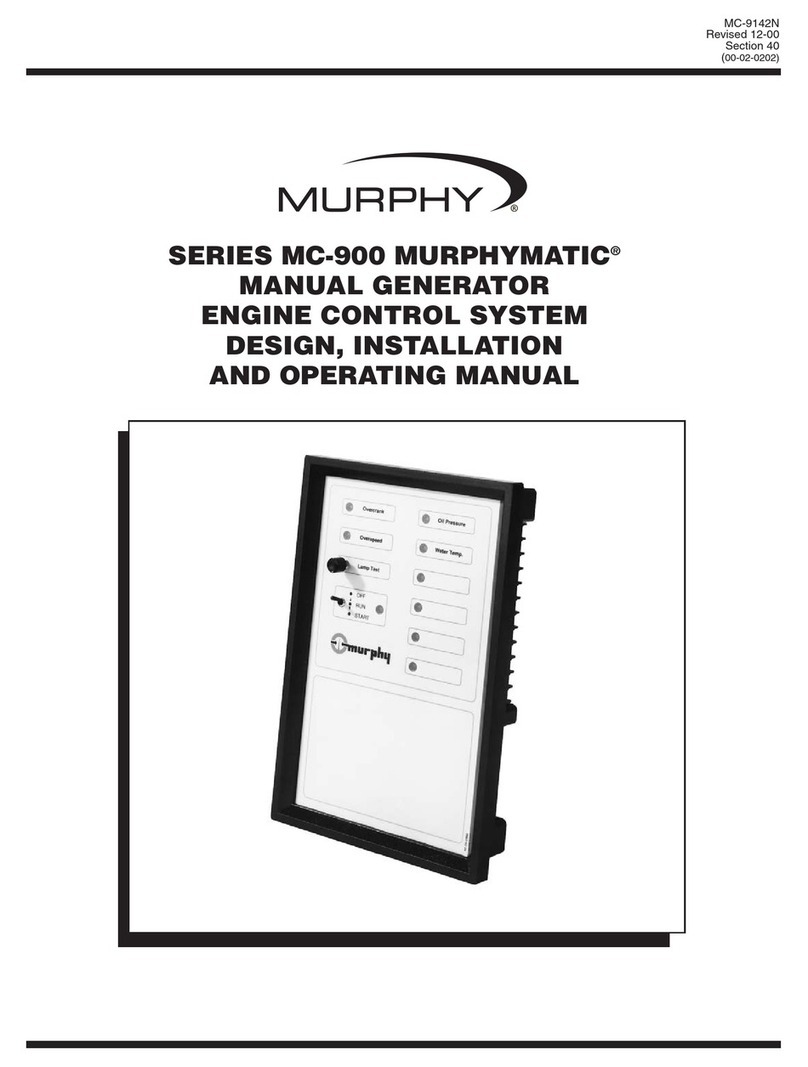
Murphy
Murphy MURPHYMATIC MC-900 Series Installation and operating manual
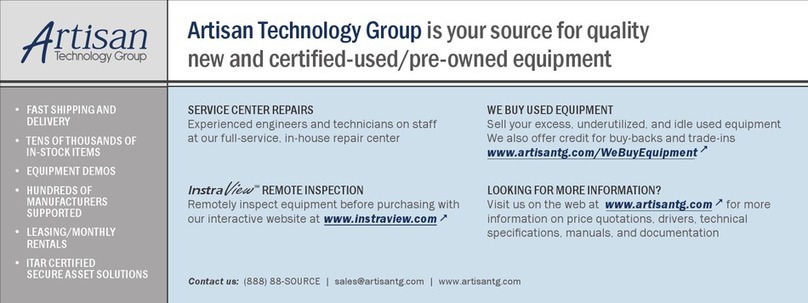
Measurement Computing
Measurement Computing CIO-DAS1401/12 user manual
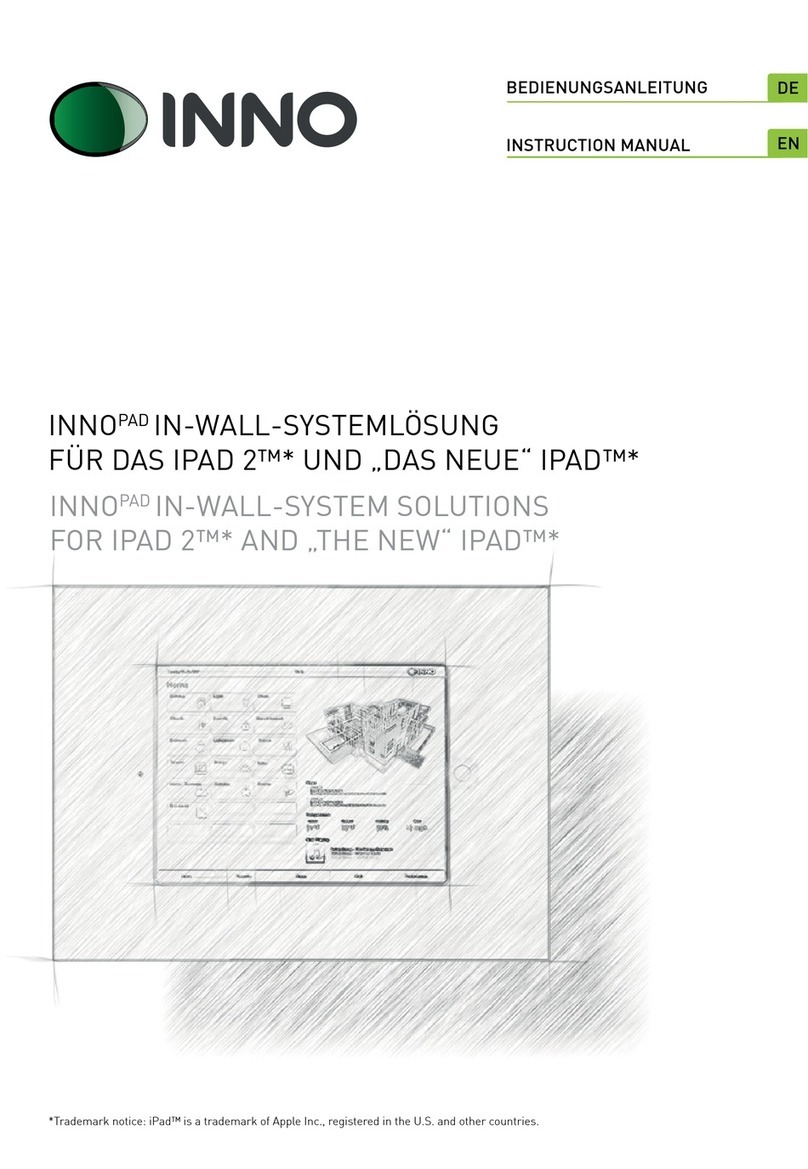
INNO
INNO INNOPAD instruction manual
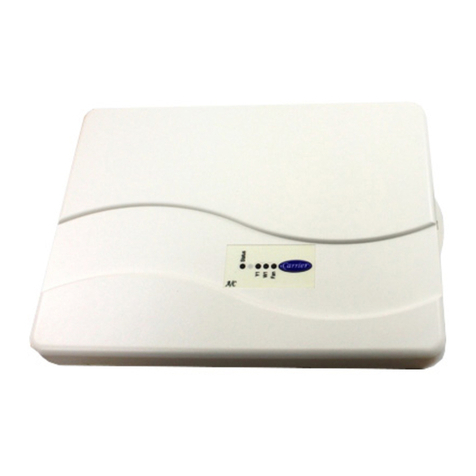
Carrier
Carrier ZONECC3ZAC01 Quick reference guide
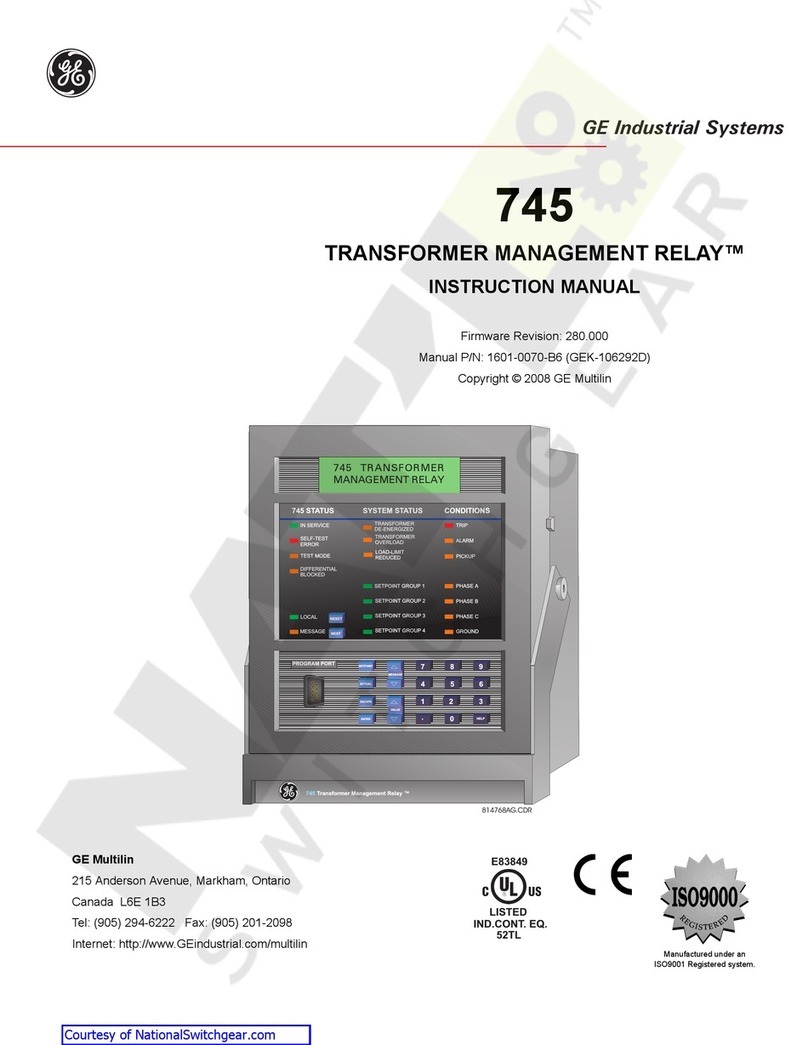
GE
GE TRANSFORMER MANAGEMENT RELAY 745 instruction manual

ELCOS
ELCOS CIM-130-KLRV Instruction and user's manual
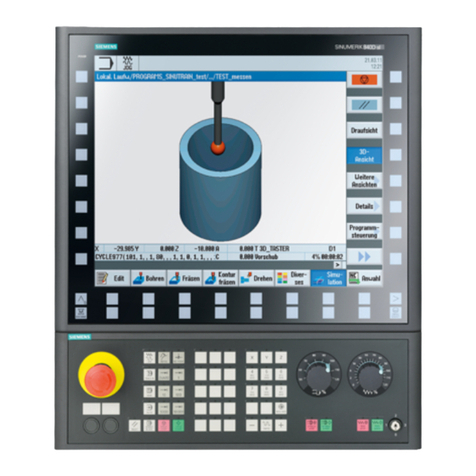
Siemens
Siemens SINUMERIK 840D sl Function manual
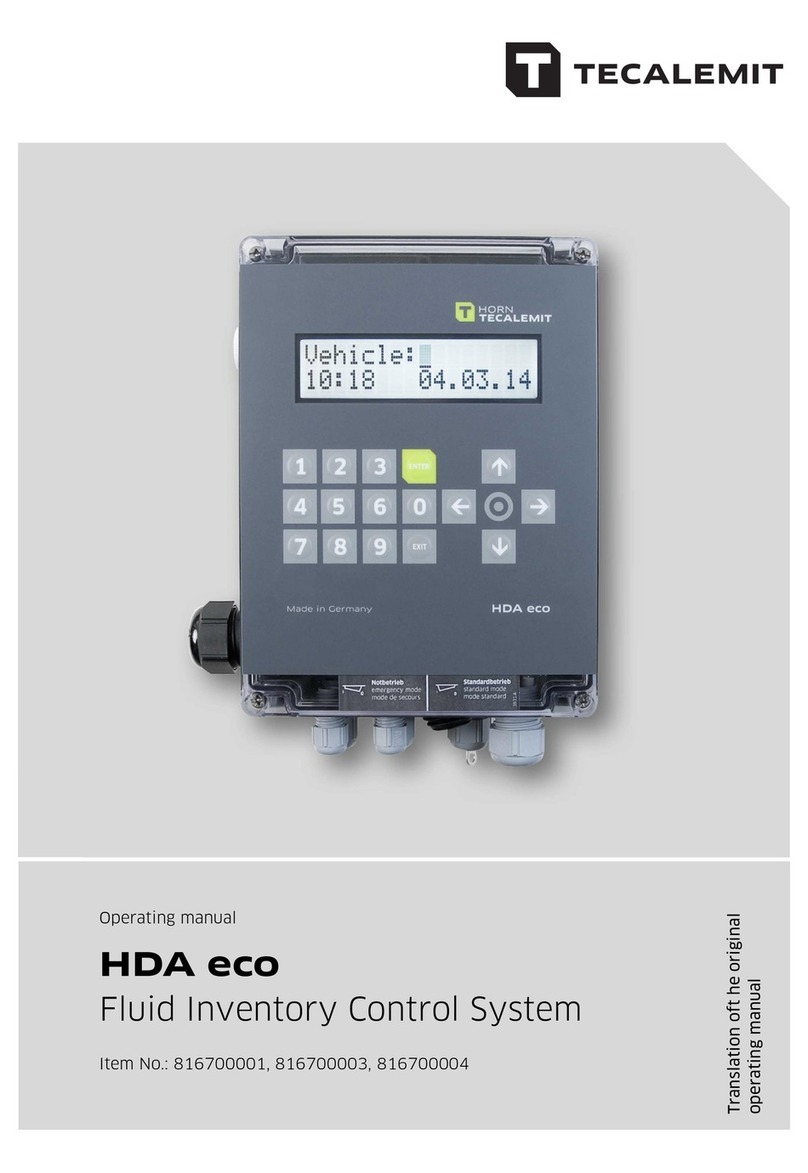
TECALEMIT
TECALEMIT HDA eco operating manual
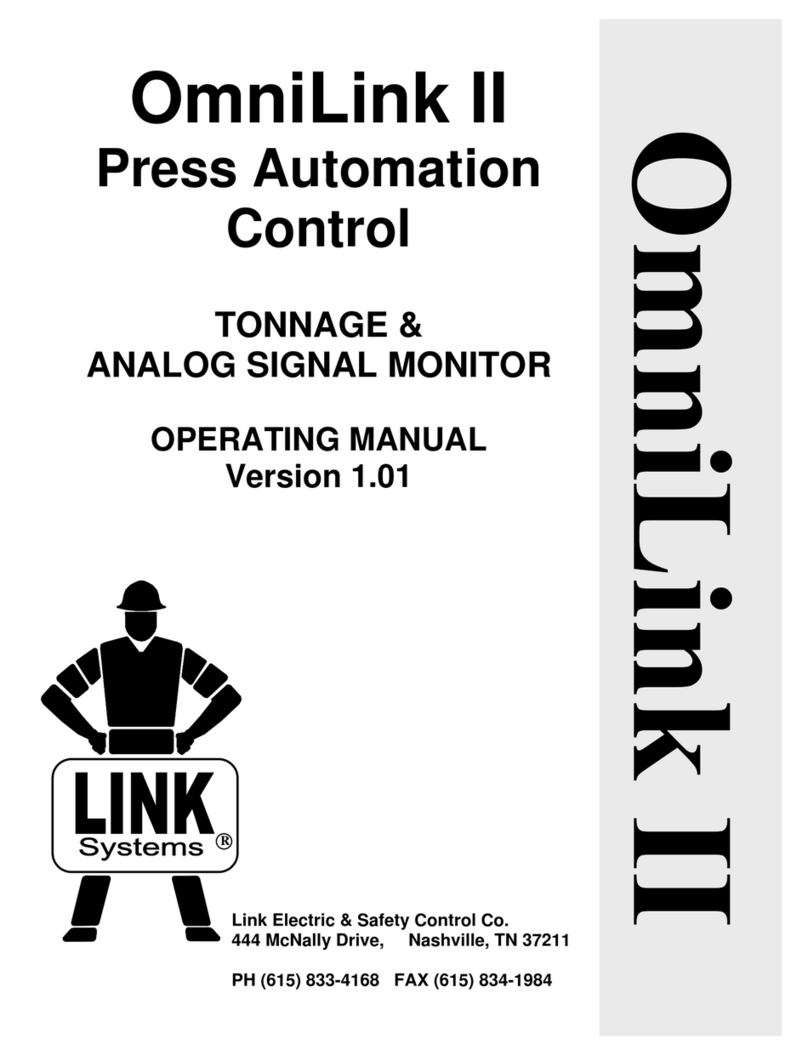
LINK ELECTRIC & SAFETY CONTROL COMPANY
LINK ELECTRIC & SAFETY CONTROL COMPANY OmniLink II operating manual