Zonex System 2000 GEN II User guide

System 2000
GEN II
A MODULATING SYSTEM
Vote Based Auto Changeover VAV
Part #GENIIMAN
June 2014
Installation and Applications Manual

GEN II
QUICK START AND COMMISSIONING
Follow these Quick steps for a successful job
If you need additional information, please read the GEN II Manual
1. Install GEN II Controller in an easily accessible location for your customer.
2. Install an Independent 24 Volt 40 VA transformer, and connect to the TR1 and TR2 terminals
on the GEN IIcontroller.
3. Install the LAT sensor in the supply air, ahead of any bypass takeoffs. Wire sensor to the S S
terminals on the GEN II controller.
4. Install Dampers and Bypass Dampers.
5. Install all thermostat sub-bases.
6. Wire R & C Terminals from the GEN II Controller to the first sub-base – only (18 ga.
Thermostat wire).
7. Wire RX & TX Terminals from the GEN II Controller using Belden 8740 twisted pair wire to
the first thermostat sub-base – only.
8. Damper wiring – connect RO, RC, MC wires from each thermostat to its damper with 18 GA
thermostat wire.
9. Plug 1 MODSTAT into that sub-base.
10. Address that thermostat to #1 – see Pages 10-13 for MODSTAT installation, addressing and
operation.
11. Turn on GEN II Controller switch “E”. Power light should light up and then look at the Display
"O" on the GEN II Controller, and the number 01 appears on the Display. This indicates you
are communicating with the first thermostat.
12. If you don’t see the #1 and a 0 is displayed, check the address. If the address is #01, then
check wires for R&C polarity and RX TX for correct connections.
13. If #1 is displayed on the GEN II Controller, then daisy chain wires from Stat 01 to the next stat
and address it #2; then repeat the ON – Off switch operation and confirm the #2 shows up on
the display indicating the system is now communicating with 2 thermostats.
14. Continue adding MODSTATS, and confirm communication by repeating the ON – Off switch
operation until all stats are wired and the total number of thermostats on your job shows up
on the display on the GEN II Controller. (If you are adding stand-alone units to the GEN II
Controller, see #15. If not, skip to #16)
15. If there are any stand-alone units that are going to be managed by the GEN II Controller,
install DIGICOM / DIGIHP stats at this time. Continue the RX & TX daisy chain from the last
MODSTAT to the DIGICOM / DIGIHP and wire in the stand-alone unit at this time and
address the DIGICOM / DIGIHP (see Pages 14-17 for installation, addressing and
operation). Confirm communication by repeating the On – Off switch operation until all stats
are wired and the total number of thermostats on your job shows up on the display on the
GEN II Controller.
16. Go to any MODSTAT and make a Cool Call. Look at the GEN II Controller and confirm Y1
(yellow LED) and G (green LED) lights are on.
17. Turn off the Cool Call to be sure Y1 and G turn off at GEN II Controller.
18. Repeat with Heat Call for W1 (red LED).
19. Wire GEN II Controller to A/C unit.
20. Set stat to call for cool, and check register to be sure each damper opens and closes as you
make and satisfy calls.
For Advanced Feature Configuration or additional operating information, review the attached
GEN II Manual.

GEN II
QUICK START AND COMMISSIONING
The GEN II is equipped with a Digital Display (O) on the GEN II controller that constantly
displays Leaving Air Temperature from the unit. At startup, this display also reports the number
of thermostats communicating with the GEN II controller. The display and 3 buttons (N) beneath the
display provide the installing contractor the ability to tailor the system to your specific application.
The GEN II controller is shipped from the factory configured for basic Gas/Electric operation.
However, the following should be checked as part of the initial installation setup procedures:
1. EH jumper (A) is installed by the factory on one pin for normal gas heat operation where the fan
is controlled by the HVAC system fan control. When a fan output is required from the GEN II
controller on a call for heat, place the EH jumper over both pins for several seconds and then
remove. Place the jumper tab on one pin.
2. O/B and HP jumpers (B&C) should both be on one pin or removed for GE operation.
3. PRIORITY jumper (D) should be on one pin.
Note: If the Priority opposing zone strategy is to be used, this jumper position will be changed
after the initial system start-up is completed.
See Advanced Feature Configuration.
4. Set the power switch (E) to ON.
5. Set the NIGHT DAY switch (L) to the DAY position.
6. Set the fan jumper (M) to AUTO for intermittent operation or ON for constant ON operation in
the Occupied mode.
7. Place the LOCK – UNLOCK switch (P) in the UNLOCK position.
8. Place the TIME/TEMP jumper (Q) on the middle and upper pins to control Y2 and W2 staging
on run time and supply air temperature.

Table of Contents
Page
System Overview
....................................................................................................................................1
System Overview Diagram ..................................................................................................................1
General Sequence
of Operation............................................................................................................2
Gas Electric Operation
...........................................................................................................................3
Controller ID Diagram ..........................................................................................................................3
Installation Controller ...........................................................................................................................3
GE Controller Configuration .................................................................................................................
4
GE Advanced Configuration ................................................................................................................5
H&C Cut-out Temperature ...................................................................................................................
5
Electric Heat Fan .................................................................................................................................5
2nd Stage cut in ....................................................................................................................................5
Heat Pump Operation
.............................................................................................................................6
Controller ID Diagram ..........................................................................................................................6
Heat Pump Installation .........................................................................................................................
7
Basic Configuration ..............................................................................................................................
8
Heat Pump Advanced Configuration ...................................................................................................8
H&C Cut-out Temperature ...................................................................................................................
8
2nd Stage Cut-in ...................................................................................................................................9
Zone Therm
ostat – ModStat
ModStat Installation ...........................................................................................................................10
Wiring Diagram ..................................................................................................................................10
ModStat Configuration ..................................................................................................................11-
12
Supplemental Heat Applications ...................................................................................................
.....13
Zone Thermostats
– DIGICOM / DIGIHP
DIGICOM / DIGIHP Installation ....................................................................................................14-15
DIGICOM / DIGIHP Configuration ................................................................................................16-17
Voltage Polarity .................................................................................................................................17
System Start and Test .........................................................................................................................18
Troubleshooting ...................................................................................................................................18
Advanced Feature Configuration
Gas Electric and Heat Pump .............................................................................................................19
Occupied/Unoccupied Fan ................................................................................................................19
Opposing Call Changeover ...............................................................................................................19
Priority Demand ................................................................................................................................19
Thermostat Security – LOCK ............................................................................................................20
Air Balance ........................................................................................................................................20
Default Thermostat Set Points ..........................................................................................................21
Time Clock (GCLK) ...........................................................................................................................21
Zone Dampers
Round Dampers ................................................................................................................................22
Rectangular Dampers .......................................................................................................................23
D-Fuser .............................................................................................................................................24
Sizing ................................................................................................................................................25
Slaving Zone Dampers .....................................................................................................................25
Bypass Dampers
– Electronic
Bypass Dampers ...............................................................................................................................26
Slaving Bypass Dampers ..................................................................................................................27
Bypass Damper with Integrated Pressure Control........................................................................28-29

1
SYSTEM OVERVIEW
The SYSTEM 2000 GEN II is a commercial modulating or 2-position zone control system controlling
2-17 independent zones per unit. The GEN II controller is designed for Auto Change- over, multi-
stage Heat Pump (2C/3H) and Gas Electric (2C/2H) applications.
For modulating applications, the GEN II system uses the Zonex ModStat, which controls the “ST”
series, 3-wire, 24-volt, power open / power close round and rectangular dampers. For 2-position
damper applications, the GEN II system uses the Zonex MODS2 thermostat. The MODS2
thermostats control the TR round or TREC rectangular series, 2-wire, power close / spring open,
low pressure dampers. The TR / TREC series dampers are designed for systems 5 tons or less
(2000 CFM).
Sophisticated, integrated software allows for a wide range of system control and changeover
strategies, allowing the contractor to tailor the GEN II system to your specific application.
Additional features include LED status indication of all system functions, digital LAT display, fully
adjustable capacity control with on-board limit settings, and optional staging strategies. Night
setback operation is standard, with selectable 2-hour override at each stat, along with a unique
feature to remotely lock thermostats in the system.
The system provides the installing contractor with a simple startup diagnostic to minimize wiring
errors and speed installation.
GEN II is recognized as the Industry's easiest zone control system to install and wire. The GEN II
System operates over an unshielded two-wire data link, along with two 24 V power wires all daisy
chained from stat to stat with no home run wiring required. Three wires from the stat to actuator
control a modulating damper in each zone.
The GEN II system does not require a computer to set up or operate.

2
System 2000 GEN II offers the following additional control features:
1. Set Cooling and Heating capacity cut-out set points
2. Adjustable timing to initiate 2nd stage operation
3. Adjustable opposing call changeover timing
4. Priority demand votes on a stat-by-stat basis
5. Provide default occupied and unoccupied set points on every stat
6. Open all dampers for air balancing
System 2000 GEN II components:
• GEN II controller (includes integrated capacity control)
• Zone thermostats
• Power open / power close 24vac supply dampers
• Power open / power close 24vac bypass damper with static pressure control
• Communication cable (Belden 8740) twisted pair
• Time Clock (optional)
• 24vac 40va transformers: 1 to control system and dampers
1 for bypass damper and static pressure control
• Stand-alone thermostat – non-zoned system
GENERAL SEQUENCE OF OPERATION
When the GEN II controllers are powered up, the total number of addressed thermostats (ModStat,
MODS2, DIGICOM, DIGIHP) are determined and verified on the display. This confirms the
controller is communicating with all thermostats in the system. If there are no active heat or cool
calls detected, the supply dampers will modulate to 50% open (ModStat) or full open (MODS2) for
ventilation mode. Additional thermostats may be utilized to control stand-alone rooftop units with
DIGICOM / DIGIHP thermostats. The system blower operation can be configured for constant ON
or intermittent Auto. The controllers are shipped from the factory for Auto fan.
The System 2000 GEN II systems can be field configured for adjustable time based opposite call
changeover, vote based majority changeover, or priority vote changeover by thermostat
assignment. The GEN II controllers are shipped from the factory for 10-minute opposing call
changeover. The GEN II controllers “poll” the thermostats once per minute to determine the
thermostat demand status for heat and cool. The heat and cool changeover functions will operate
by the type of changeover selected on the controller. When the GEN II controllers change modes,
a 5-minute purge cycle is initiated before the changeover is completed.
On active heat or cool calls, the non-calling zones will modulate to the close position, or close 100%
depending on the thermostat being used. When the last calling zone is satisfied in either heat or
cool mode, the GEN II controllers will terminate the HVAC outputs after the next “poll”; and the
blower output will be de-energized (unless controller is configured for constant fan) for a 5-minute
purge cycle. During the purge cycle no heat or cool calls are recognized.
When the system is in the heating mode and calls for cooling are received, an opposing call timer
strategy operates. This timer is adjustable from 5–30 minutes. The factory default is 10 minutes.
At the end of the selected time period, if the opposing call is 3 degrees away from set point, heating
is turned off. After a 5-minute purge cycle, Cooling is turned on until the cool call is satisfied. If
necessary, GEN II will return to the heating mode. If all calls have been satisfied, dampers will
modulate to the 50% open position for ventilation. If the opposing zone strategy is not desired, this
feature may be disabled.
This mode may be enhanced by adding Priority votes to each thermostat in the system, thereby
weighting certain zones more than others. This Priority mode allows you to select 0, 1, or 2
additional votes for a thermostat that has unusual loads, like a conference room.

3
GAS ELECTRIC OPERATION
General Installation Instructions
GEN II Controller
1. Install the GEN II controller on an interior wall where the ambient temperature is between 32°-
120°F (0°- 48°C) non-condensing. This controller is to be installed in an accessible interior
area; not in attics or above ceilings.
2. The controller is to be powered by a dedicated 24vac 40va transformer.
The transformer secondary is wired to TR1 TR2 on the controller (G).
The secondary voltage to the controller must be 24 to 28vac.
LEGEND
A EH Jumper (Set Up Fan Operation for
Electric Heat)
B O/B Jumper (Heat Pump Only –
Reversing Valve Operation)
CH/P Jumper (Jump for Heat Pump
Operation)
D Priority Jumper (Allows for Priority Vote
Setup)
E On / Off Switch
F R C Power to ModStats (18 ga.
Thermostat wire)
G 24-Volt Transformer
H TC – TC Time Clock Terminals
I Unit Terminals
J S S Terminals – Leaving Air Sensor
(LAT)
K RX – TX Communications Wire
L Day / Night Switch
M Fan Jumper (Continuous or Auto)
N Up / Down / Set Buttons (High Limit,
Low Limit, Set)
O Digital Display (Leaving Air Temperature
and configuration)
P Lock / Unlock (Lock Thermostats)
Q Staging Strategy (Time / Temperature or
Time Only)
TERMINAL FUNCTIONS / CONNECTIONS
TX / RX – Data Transmit / Receive
S S – Leaving / Supply Air Sensor Input
G – Fan Output
W2 – Auxiliary / Emergency Heat
O/B – Reversing Valve Output
Y2 – Stage 2 Cool Output
Y1 – Stage 1 Cool Output
R – 24vac from Unit Transformer
TC / TC – Time Clock Input for Occupied /
Unoccupied Operation
TR1 / TR2 – 24vac Power Input / Common
R / C – Stat Power Daisy Chain Stat to Stat
(18 ga. Thermostat wire)

4
3. Install the leaving air sensor (LAT) in the supply air, ahead of the bypass take-off. Sensor wires
are connected to the S S terminals on the controller (J). The LAT sensor leads may be
extended using standard 18/2 thermostat wire.
4. The leaving air sensor (LAT) is calibrated to the controller at the factory. However, the
calibration should be checked as part of the system setup procedures. If adjustments are
required, use the Blue potentiometer labeled R44 located in the upper left hand corner of the
GEN II controller. Screw the pot clockwise to lower the display temperature and counter -
clockwise to raise the temperature. NOTE: The display will update every 10 seconds.
5. Confirm you have connected the RX TX communication wires and Rand C from the
thermostats to the controller (F&K), F = (R C), K = (TX RX). (Communication wire maximum is
4,000 ft. from the Command Center to the farthest ModStat, DIGICOM or DIGIHP.)
6. Connect the output wires from the controller to the HVAC system using standard 18 ga.
thermostat wire.
The LAT sensor leads may be extended using standard 18/2 thermostat wire.
Gas Electric - Basic GEN II Controller Configuration
The GEN II is equipped with a Digital Display (O) on the GEN II controller that constantly
displays Leaving Air Temperature from the unit. The display and 3 buttons beneath the display
provide the installing contractor the ability to tailor the system to your specific application.
The GEN II controller is shipped from the factory configured for basic Gas/Electric operation.
However, the following should be checked as part of the initial installation setup procedures:
1. EH jumper (A) is installed by the factory on one pin for normal gas heat operation where the fan
is controlled by the HVAC system fan control. When a fan output is required from the GEN II
controller on a call for heat, place the EH jumper over both pins for several seconds and then
remove. Place the jumper tab on one pin.

5
2. O/B and HP jumpers (B&C) should both be on one pin or removed, for GE operation.
3. PRIORITY jumper (D) should be on one pin.
Note: If the Priority opposing zone strategy is to be used, this jumper position will be changed
after the initial system start-up is completed.
See Advanced Feature Configuration.
4. Set the power switch (E) to ON.
5. Set the NIGHT DAY switch (L) to the DAY position.
6. Set the fan jumper (M) to AUTO for intermittent operation or ON for constant ON operation in
the Occupied mode.
7. Place the LOCK – UNLOCK switch (P) in the UNLOCK position.
8. Place the TIME/TEMP jumper (Q) on the middle and upper pins to control Y2 and W2 staging
on run time and supply air temperature.
GEN II Gas Electric Advanced Feature Configuration
Gas Electric Capacity Control -Cool and Heat cut-out temperature adjust
The factory setting for the Cool and Heat cut-out temperatures is 45°- 145°F (7°- 62°C). This can
be easily changed with the following procedure:
1. Cool cut-out temp – Press the DN button (N);“C” will be displayed and then the cut-out
temperature.
2. LOWER – Press the DN button; after the “C” is displayed, continue to hold the DN button until
the desired temperature is displayed; then release.
NOTE: The controller will not change the Cool cut-out lower than 40°F (4°C).
3. RAISE – Press the DN button; after “C” is displayed, immediately release the DN button and
press the UP button. Hold until the desired temperature reading is displayed, and release.
4. Press the DN button to verify the new cool cut-out temperature.
Heat cut-out temperature - Press and hold the UP button; after the “H” is displayed, use the same
procedure as above to raise or lower the displayed temperature.
Electric Heat - Fan Configuration
EH jumper (A) is installed by the factory on one pin for normal gas heat operation where the fan is
controlled by the HVAC system fan control. When a fan output is required from the GEN II
controller on a call for heat, place the EH jumper over both pins for several seconds and then
remove. Place the jumper tab on one pin.
2nd Stage Heat and Cool Cut-in Configuration
The GEN II controller is set up at the factory to stage Y2 and W2 cut-in operation based on a 3-
minute time delay and supply air temperature. This is done with a jumper which is placed on the
middle and upper pins on TIME/TEMP (Q), and the cut-in delay set at 03 (3 min) in the controller
program. The cut-in temperatures are fixed in the controller program at 57°F (13°C) and higher for
Y2 and 120°F (48°C) and lower for W2. The Y2 and W2 cut-in delay sequence can be field
adjusted (see below).
Adjust 2nd Stage Cut-in Time Delay
1. To increase the Y2 and W2 cut-in delay, press and hold the SET and DN buttons (N)
simultaneously. When 03 appears in the display, release the buttons and immediately press
the UP button and hold until the desired delay time is displayed, and release. The time delay
is fully adjustable from 3 - 20 minutes. To verify the change, press and hold the SET and DN
buttons simultaneously until the delay time is shown, and release.

6
2. To decrease the Y2 and W2 cut-in delay, press and hold the SET and DN buttons (N)
simultaneously. When delay time appears in the display, release the buttons and immediately
press the DN button and hold until the desired delay time is displayed, and release. To verify
the change, press and hold the SET and DN buttons until the delay time is shown, and release.
Configure 2nd Stage Cut-in For Time Delay and Thermostat Demand Only
1. Place the 2nd stage configuration jumper (Q) on the middle and lower pins - TIME.
2. If the cut-in time delay must be changed from the factory setting of 03 (3 min), follow the above
procedures to raise or lower the time delay value.
3. Verify time delay value by pressing the SET and DN buttons simultaneously.
HEAT PUMP OPERATION
TERMINAL FUNCTIONS / CONNECTIONS
TX / RX – Data Transmit / Receive
S S – Leaving / Supply Air Sensor Input
G – Fan Output
W2 – Auxiliary / Emergency Heat
O/B – Reversing Valve Output
Y2 – Stage 2 Cool Output
Y1 – Stage 1 Cool Output
R – 24vac from Unit Transformer
TC / TC – Time Clock Input for Occupied /
Unoccupied Operation
TR1 / TR2 – 24vac Power Input / Common
R / C – Stat Power Daisy Chain Stat to Stat
(18 ga. Thermostat wire)
LEGEND
A EH Jumper (Set Up Fan Operation for
Electric Heat)
B O/B Jumper (Heat Pump Only –
Reversing Valve Operation)
CH/P Jumper (Jump for Heat Pump
Operation)
D Priority Jumper (Allows for Priority Vote
Setup)
E On / Off Switch
F R C Power to ModStats (18 ga.
Thermostat wire)
G 24-Volt Transformer
H TC – TC Time Clock Terminals
I Unit Terminals
J S S Terminals – Leaving Air Sensor
(LAT)
K RX – TX Communications Wire
L Day / Night Switch
M Fan Jumper (Continuous or Auto)
N Up / Down / Set Buttons (High Limit,
Low Limit, Set)
O Digital Display (Leaving Air Temperature
and configuration)
P Lock / Unlock (Lock Thermostats)
Q Staging Strategy (Time / Temperature or
Time Only)

7
General Installation Instructions
GEN II Controller
1. Install the GEN II controller on an interior wall where the ambient temperature is between 32°-
120°F (0°- 48°C) non-condensing. This controller is to be installed in an accessible interior
area; not in attics or above ceilings.
2. The controller is to be powered by a dedicated 24vac 40va transformer.
The transformer secondary is wired to TR1 TR2 on the controller (G).
The secondary voltage to the controller must be 24 to 28vac.
3. Install the LAT air sensor in the supply air between the indoor coil and electric strip heat
elements.
4. The leaving air sensor (LAT) is calibrated to the controller at the factory. However, the
calibration should be checked as part of the system setup procedures. If adjustments are
required, use the Blue potentiometer labeled R44 located in the upper left hand corner of the
GEN II controller. Screw the pot clockwise to lower the display temperature and counter -
clockwise to raise the temperature. NOTE: The display will update every 10 seconds.
5. Confirm you have connected the RX TX communication wires and Rand C from the
thermostats to the controller (F&K), F = (R C), K = (TX RX). (Communication wire maximum is
4,000 ft. from the Command Center to the farthest ModStat, DIGICOM or DIGIHP.)
6. Connect the output wires from the controller to the HVAC system using standard 18 ga.
thermostat wire.
The LAT sensor leads may be extended using standard 18/2 thermostat wire.
Heat Pump operation “O” reversing valve
Cool Call – When a majority active cool call is received by the GEN II controller, Y1, O/B and G
LEDs are illuminated; and the outputs are energized (within 1.5 to 3 minutes). After 3 minutes, if
the leaving air temperature is 58°F (14°C) or above, Y2 will energize for 2-stage systems. If the
supply air temperature drops one degree below the Cool cut-out temperature, Y1 and Y2 will de-
energize for 4 minutes.
“B” reversing valve – Sequence of operation is the same: O/B is energized in the heat mode.
Heat Call - When a majority active heat call is received by the GEN II controller, Y1 and G LEDs are
illuminated; and the outputs are energized (within 1.5 to 3 minutes). If after 3 minutes the leaving
air temperature is 94°F (34°C) or less, Y2 will energize. If after 6 minutes of run time the leaving air
temperature is 91°F (32°C) or less, W2 will energize. If the supply air temperature exceeds 126°F
(52°C), Y1, Y2 and W2 (if energized) will drop out; and Y1 can then energize after a 4-minute time
delay. NOTE: If the system fan is configured for “AUTO” on the GEN II controller, the “G” output
will be de-energized in the temperature cut-out mode.
When the last active call satisfies, the GEN II controller goes into a 5-minute purge cycle with all
supply dampers closing; then all dampers modulate open for ventilation.
Emergency Heat -The GEN II emergency heat operation can be selected from any ModStat for
the entire control system. When the system operation mode is changed to Emergency Heat on a
given ModStat, the GEN II controller will recognize the mode change on the next system poll. The
thermostat which was used to select Emergency Heat does not have to make a heat call for the
GEN II controller to respond to the change. Once the GEN II controller changes the mode to
Emergency Heat, any ModStat in the system can make an emergency heat call. When the
controller receives a heat call in this mode, the compressor(s) are locked out and W2 is energized.
The GEN II controller will continue to make consecutive Emergency Heat calls until the ModStat(s)
have been changed back to the AUTO or HEAT mode.

8
To select Emergency Heat on any ModStat:
1. Press and hold the ModStat Menu button
2. When the mode display indicates Emg, release the Menu button; and immediately press and
hold the Select button to set the mode.
Heat Pump operation “B” reversing valve
By placing the O/B jumper (B) on both pins, the GEN II controller is configured for “B” reversing
valve operation. The operation and setup procedures are the same as with “O” mode reversing
valve, except the reversing valve will be energized for heat operation.
GEN II Heat Pump Basic Configuration
The GEN II controller is shipped from the factory
for Gas Electric operation.
The controller must be field configured for Heat
Pump operation.
Heat Pump configuration:
1. Switch controller to OFF (E).
2. Set the O/B jumper (B) on one pin for “O”
reversing valve (energizes for cool) or
set the O/B jumper (B) on both pins for “B”
reversing valve (energizes for heat).
3. Set the HP jumper (C) on both pins for Heat
Pump operation.
4. Set the Priority jumper (D) on one pin.
5. Set the TIME / TEMP jumper (Q) on the
middle and upper pins.
6. Set NIGHT / DAY switch (L) for DAY position.
7. Set LOCK / UNLOCK switch (P) to UNLOCK.
8. Switch the controller to ON (E).
9. Press the UP button (N), and verify the “H”
(cut-out) temperature reads 126°F (52°C) on the controller display (O).
NOTE: The heat cut-out temperature must not be changed from the factory setting.
GEN II Heat Pump Advanced Feature Configuration
Heat Pump Capacity Control - Cool and Heat cut-out temperature adjustment
When the GEN II controller is configured for Heat Pump (HP jumper (C) on both pins), the Cool and
Heat cut-out temperatures are 45°- 126°F (7°- 52°C). The cut-out temperatures can be changed
with the following procedure:
Heat cut-out temp – To eliminate the possibility of the Heat Pump tripping out on high head
pressure or short cycling in the heat mode, the heat cut-out temperature should never be changed
from the factory setting of 126°F (52°C).
1. Cool cut-out temp – Press the DN button (N); “C” will be displayed, then the cut-out
temperature.
2. LOWER – Press the DN button. After the “C” is displayed, continue to hold the DN button until
the desired temperature is displayed; then release.
NOTE: The controller will not change the Cool cut-out lower than 40°F (4°C).

9
3. RAISE – Press the DN button. After “C” is displayed, immediately release the DN button, and
press the UP button. Hold until the desired temperature reading is displayed; then release.
4. Press the DN button to verify the new cool cut-out temperature.
2nd Stage Heat and Cool Cut-in Configuration
The GEN II controller is set up at the factory to stage Y2 and W2 cut-in operation based on a 3-
minute time delay and supply air temperature. This is done with a jumper which is placed on the
middle and upper pins on TIME/TEMP (Q), and the cut-in delay set at 03 (3 min) in the controller
program. The cut-in temperatures are fixed in the controller program at 57°F (13°C) and higher for
Y2 and 120°F (48°C) and lower for W2. The Y2 and W2 cut-in delay sequence can be field
adjusted (see below).
Adjust 2nd Stage Cut-in Time Delay
1. To increase the Y2 and W2 cut-in delay, press and hold the SET and DN buttons (N)
simultaneously. When 03 appears in the display, release the buttons and immediately press
the UP button and hold until the desired delay time is displayed, and release. The time delay
is fully adjustable from 3 - 20 minutes. To verify the change, press and hold the SET and DN
buttons simultaneously until the delay time is shown, and release.
2. To decrease the Y2 and W2 cut-in delay, press and hold the SET and DN buttons (N)
simultaneously. When delay time appears in the display, release the buttons and immediately
press the DN button and hold until the desired delay time is displayed, and release. To verify
the change, press and hold the SET and DN buttons until the delay time is shown, and release.
Configure Y2 and W2 cut-in for time delay and thermostat demand only
1. Place the 2nd stage configuration jumper (Q) on the middle and lower pins - TIME.
2. If the Y2 cut-in time delay must be changed from the factory setting of 03 (3 min), follow the
above procedures to raise or lower the time delay value.
NOTE: The cut-in delay timing for W2 (Aux Heat) is set for approximately 3 minutes in the
control program and cannot be manually changed.
3. Verify time delay value by pressing the SET and DN buttons simultaneously.

10
Zone Thermostat - ModStat
Installation
Wiring
All 24-volt and communication wiring connections are made to terminal blocks on the thermostat
sub-base. The communication terminal block (RX TX/RX TX) is designed as a junction for two sets
of 22 ga. solid copper, twisted pair communications cable. The cable should be daisy chained from
thermostat to thermostat (use Belden 8740).
1. Install the thermostat sub-base on an interior wall away from direct sunlight, supply air currents,
or any heat generating source. Mounting screws and anchors are provided. The sub-base
may be installed on a vertical 2x4 electrical box.
2. Connect the control wires from the ModStat's R & C, to the GEN II controller (F). Verify R & C
polarity is the same on each thermostat (18 ga. Thermostat wire).
3. On the ModStat, connect the damper output wires from C-MC, RC and RO to the actuator
motor terminals. NOTE: For MODS2, terminal RO is not used.
4. Connect the RX TX communication wires on the right hand terminal block; there are 2 sets of
RX TX terminals to make the daisy chain wiring easier.
NOTE: The communication wire must be twisted pair Belden 8740, 8450 (shielded) or
82442 (plenum rated).

11
Configuration
Addressing
Each thermostat must have a unique address from 1-17.
1. Press and hold the Menu button until you see the system mode display on the lower right begin
to change modes; then press and hold the Heat/Cool button with the Menu button.
2. When the display shows “address,” release the Menu and Heat/Cool buttons, and press the UP
or DN button until the correct address is displayed in the upper right of the display.
3. After setting the address, the thermostat will automatically go back to normal operation; and the
set point temperature will replace the address number just programmed.
Display Temperature Calibration
Thermostats are calibrated at the factory and should require no further adjustment. However, the
display space temperature may be field calibrated by the following procedure:
1. Press and hold the Heat/Cool and Select buttons together; then press and release the UP
button to increase the display temperature by one degree.
2. To lower the temperature display, press the DN button once, after pressing the Heat/Cool and
Select buttons. This makes a 1-degree change.
Adjusting Set Points
The Heat or Cool set points can be displayed by pressing the Heat/Cool button; the set point will be
indicated on the upper right of the display.
The Heat and Cool set points can be individually set for the Occupied and Unoccupied modes.
Occupied Mode: H & C settings - Function switch (L) in the DAY position, or time clock in
Occupied.
Unoccupied Mode: H & C settings – Function switch (L) in the NIGHT position, or time clock
in Unoccupied.

12
Heat - If “Heat Setting” is displayed on the top right of the display, simply press the UP or DN button
to change the heat set point. If “Cool Setting” is displayed and you want to change the Heat set
point, press the Heat/Cool button twice to change from “Cool Setting” to “Heat Setting”. Then press
the UP or DN button to change the set point.
Cool - If “Cool Setting” is displayed on the top right of the display, simply press the UP or DN button
to change the cool set point. If “Heat Setting” is displayed and you want to change the Cool set
point, press the Heat/Cool button twice to change from “Heat Setting” to “Cool Setting”. Then press
the UP or DN button to change the set point.
Changing Mode
The thermostats are auto changeover, but specific modes may be selected. Auto mode is the
default.
Heat only –Press and hold the Menu button and note the mode display begin to change. Press
the Select button when Heat is displayed.
Emergency Heat -Press and hold the Menu button and note the mode display begin to change.
Press the Select button when Emg is displayed.
Cool only -Press and hold the Menu button and note the mode display begin to change. Press the
Select button when Cool is displayed.
System Off - Press and hold the Menu button and note the mode display begin to change. Press
the Select button when Off is displayed.
Auto mode – Press and release the Menu button.
Override
When the thermostat displays “Unoccupied” (top of display), a 2-hour temporary override may be
initiated by pressing the Override/Select button. When additional override time is required, press
the Override/Select button again.
Reheat
The ModStat can be field configured for reheat operation, including Fan Powered Boxes. To set
the ModStat for Reheat, press and hold the Heat/Cool and Select buttons together and then press
the Menu button; release all three buttons and the °symbol will appear next to the heat and cool set
point temperature display.
NOTE: An air proving switch must be wired into the AUX output to protect the electric heating
devices.
Heat Call – The ModStat will send a signal for demand heating when the space temperature drops
1° below the heat set point temperature. If the temperature drops 2° below the heat set point
temperature, the AUX output will energize for auxiliary heat. The thermostat will end the active call
when the space temperature meets the heat set point.
When configured for Reheat, if the space temperature drops below the heat set point, the ModStat
will modulate the damper to 40% open. When the temperature drops one more degree, the AUX
terminal energizes the duct heat strip. The heat call will terminate when the space temperature
reaches the heat set point temperature. The “AUX” output will de-energize, and the damper will
modulate closed. If the system goes into the ventilation mode, the damper will then modulate open.

13
SUPPLEMENTAL HEAT APPLICATIONS MODSTAT
NOTE: A larger transformer may be needed to power fan relay and/or heat strip relay.
SUBBASE
ModStat Terminal Designations
TX – Data transmit
RX – Data receive
AUX – Reheat/AUX Heat Fan
RO – Run Open, damper
RC – Run Closed, damper
R– 24vac power input
C-MC – 24vac power common
{twisted pair}
{18 ga. stat wire}

14
DIGICOM / DIGIHP THERMOSTATS
DESCRIPTION
The Zonex Systems DIGICOM (2H, 2C) and DIGIHP (3H, 2C) are
microprocessor based, auto changeover, stand-alone thermostats used to
control stand alone units with no dampers in the system. The DIGICOM is
the Gas Electric version and has two-stage heat / cool outputs with
selectable fan operation. The DIGIHP Heat Pump thermostats have two-
stage cool and three-stage heat outputs with selectable fan. The DIGICOM
and DIGIHP thermostats have a large, easy-to-read LCD display with a
distinctive grey backlight. The display backlight is continuously illuminated
in the Occupied mode and goes off in the Unoccupied mode.
The DIGICOM and DIGIHP are very easy to configure through the system program or to make
manual adjustments using the buttons located on the front cover.
These thermostats feature an onboard thermistor for precise temperature measurement. In the
event of power loss, the Heat and Cool set points are stored in a non-volatile memory, without the
need for battery backup.
The space ambient temperature is continually displayed with large, easy-to-read numbers. The
DIGICOM temperature display range is 45° - 95°F (7°- 35°C) and the DIGIHP temperature display
range is 55°- 95°F (12°- 35°C). Fan Mode, Heat or Cool set points and operation modes are all
indicated on the display.
Programmed set points can be manually adjusted at the thermostat or electronically locked through
the system program to provide limited manual set point adjustment. Two-hour override is provided
for after-hours temporary operation with a touch of a button.
INSTALLATION
Thermostat and terminal base
1. The thermostat is to be installed on the interior wall, away from drafts, supply air currents and
direct sunlight or any heat generating source.
2. To remove the thermostat cover, grasp the cover at the top and pull straight off; do not pivot the
cover from the base.
3. Install the thermostat terminal base to the wall using the provided anchors and screws. The
thermostat can also be mounted on a 2x4 electrical box using two #6-32” screws.
Wiring
The Zonex Systems DIGICOM and DIGIHP thermostats have been specifically designed to make
wall mounting and wire connections very easy. The thermostat terminal base has two separate
terminal blocks: the left side terminal block is for the 24vac control circuits, and the right side
terminal block is for the RX TX communication circuits. There are two sets of RX TX terminals on
the base to make daisy chain wiring from device to device straightforward and simple.

15
Wiring (Continued)
1. Use minimum 18-gauge AWG thermostat wire for the 24vac control circuits. The load on these
circuits must not exceed 1 amp. The voltage range on R and C must not exceed 28vac. Check
Polarity before applying the transformer wire to R and C. Refer to the Polarity Check diagram
on Page 17.
2. Connect the communication wires to the RX TX terminals. There are 2 sets of RX TX terminals
for “daisy chain” installation of this circuit. The communication wire specification is twisted pair
(Belden 8740) or shielded twisted pair wire (Belden 8450).
NOTE: When using shielded twisted pair wire (Belden 8450), just connect the shield conductors
together, as there is no electrical connection on the thermostat base terminals. The shield will be
landed on the GEN II controller on the G or TR2 terminal.
DIGICOM
Fig. 1
DIGIHP
Fig. 2
Blower Fan Relay
For electrical heat applications, which require a fan output on a call for heat, see Fig. 3.
Fig. 3

16
Configuration
1. Set the unique address for each thermostat from 01 to 20.
2. Press and hold the Menu button until you see the system mode display on the lower right begin
to scroll and change modes; then press and hold the Heat/Cool button with the Menu button.
3. When the display shows “address” and the set point temperature changes to the address
number, press the UP or DN button to raise or lower the number.
MANUAL ADJUSTMENTS
Heat and Cool Set point Display
Press the Heat/Cool button to display the Heat or Cool set point temperatures.
Temperature Set points
COOL Set point
1. Press the Heat/Cool button to display the Cool set point on the upper right.
2. Press the UP or DN buttons to change the Cool set point.
HEAT Set point
1. Press the Heat/Cool button to display the Heat set point on the upper right.
2. Press the UP or DN buttons to change the Heat set point temperature.
FAN Mode
To change the FAN operation to AUTO or On, press the UP and DN buttons together once to
toggle fan operation.
HVAC System Mode
To select Heat, Cool, Auto, Emergency Heat (HP only) or OFF, press and hold the Menu
button; and when the desired mode is displayed, press and hold the Select button; then release
both to confirm mode.
Override
When the system is in the Unoccupied mode, the thermostat provides a 2-hour override for after-
hours system operation. To select the 2-hour override, press the Select button and note “Override”
indicated on the display, along with the backlight coming on. When additional override is required,
press the Select button again.
Calibration
When re-calibration is required, press and hold the Heat/Cool and Select buttons simultaneously
(the screen will flash). Then press the UP button once to increase temperature 1°, or press the DN
button once to decrease the temperature 1°. If additional calibration is required, repeat this step.
Reversing Valve Mode – Heating
DIGIHP (O&B) is factory set at “O” and can be field configured for “B” reversing valve operation.
For “B” mode reversing valve (reversing valve energized in the heat mode), press and hold the
Heat/Cool and Select buttons; then press and release the Menu button once. Release the
Heat/Cool and Select buttons. The °symbol next to the set point display should disappear.
(To set from “B” to “O”, reverse the procedure.)
THERMOSTAT OPERATION
Display
The grey display backlight is constantly illuminated in the Occupied mode. The display backlight
goes off when in the Unoccupied mode. When in the Unoccupied mode, if any button is pressed,
the backlight will illuminate for 5 seconds. If the thermostat is placed in the override mode, the
backlight will illuminate until the 2 hours times out. To terminate override, press the Select button
again.
COOL – DIGICOM / DIGIHP: The thermostat will make a Y1 cool call when the space temperature
rises 1° above the cool set point. Y2 will energize when the space temperature rises 2° above the
cool set point. When the room temperature is less than 2° above the cool set point, Y2 de-
Table of contents
Other Zonex Control System manuals
Popular Control System manuals by other brands
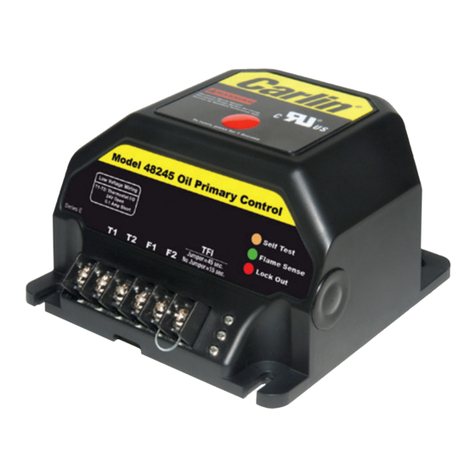
Carlin
Carlin 48245 manual
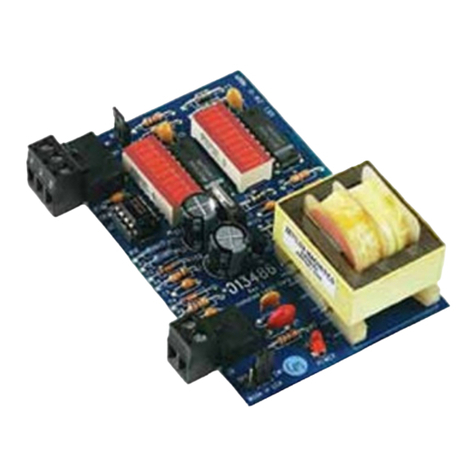
Automated Logic
Automated Logic DIAG485 Technical instructions
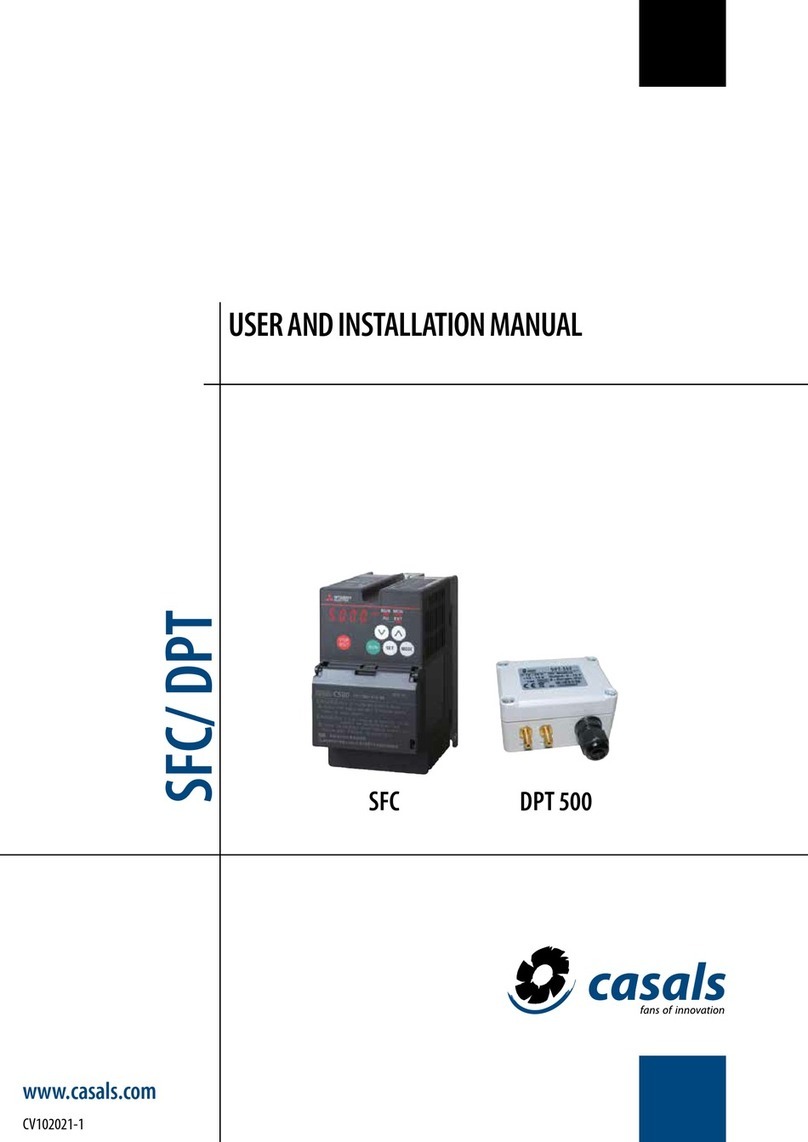
Casals
Casals SFC User and installation manual
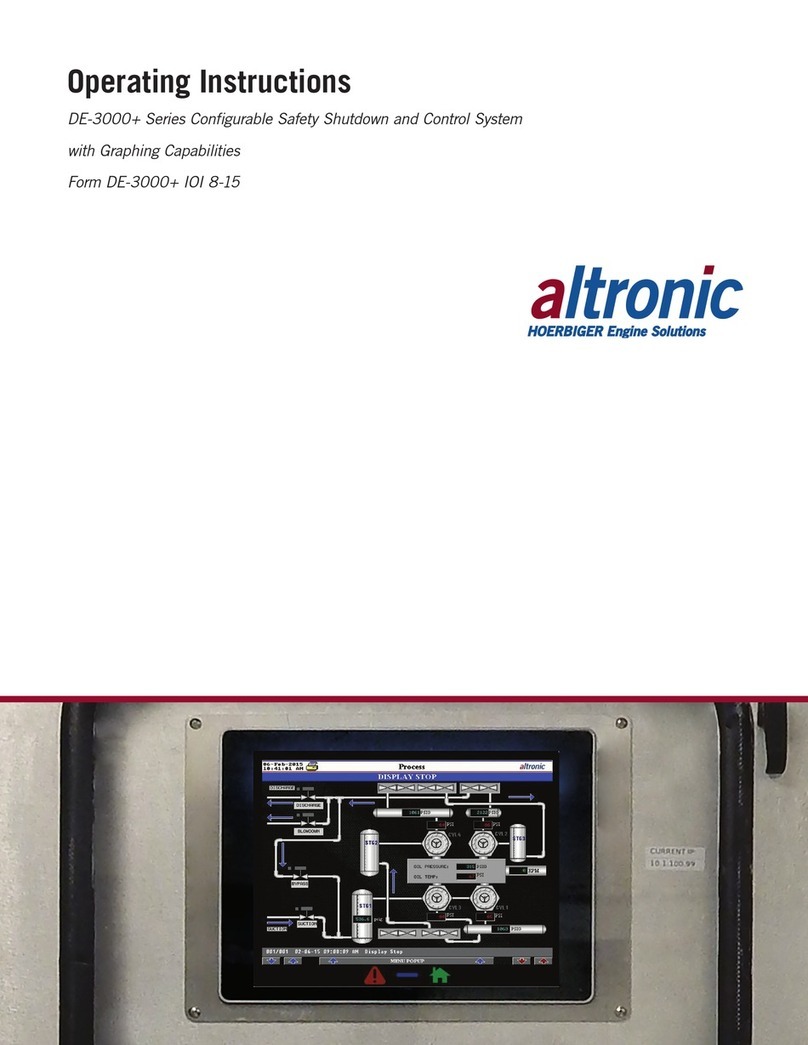
Altronic
Altronic DE-3000+ Series operating instructions
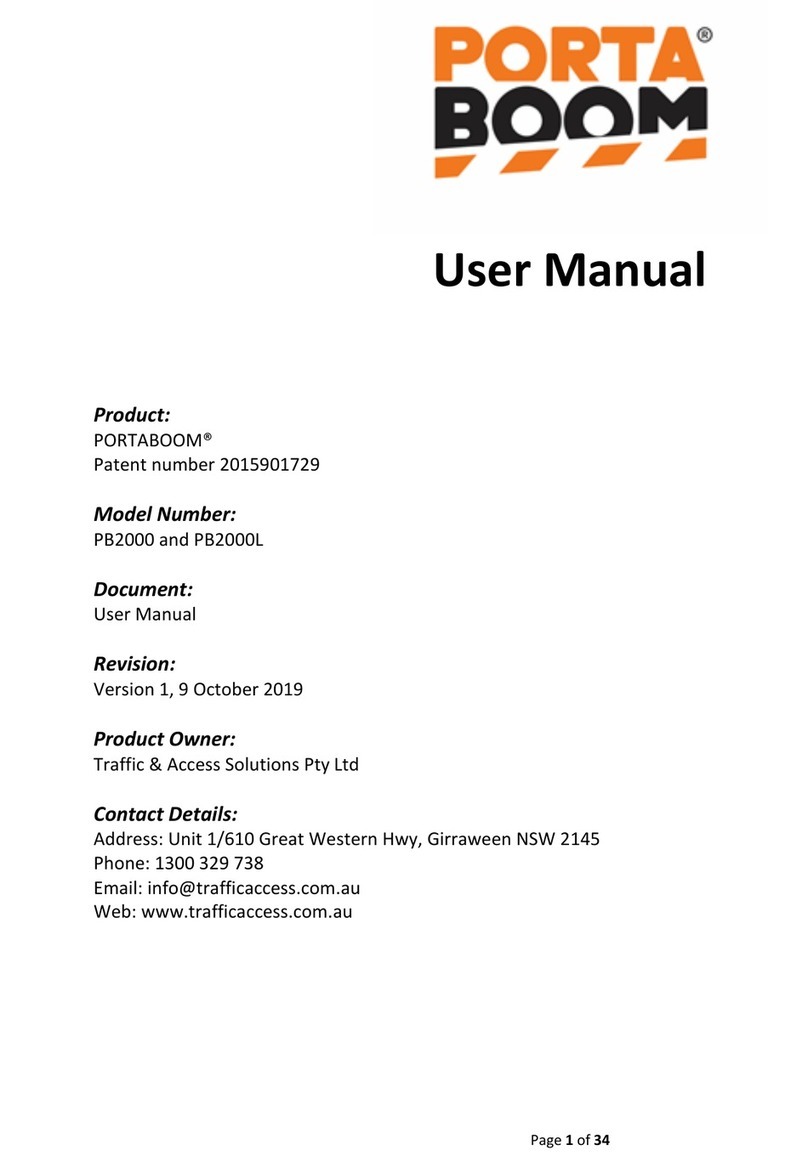
Traffic & Access Solutions
Traffic & Access Solutions Portaboom PB2000 user manual
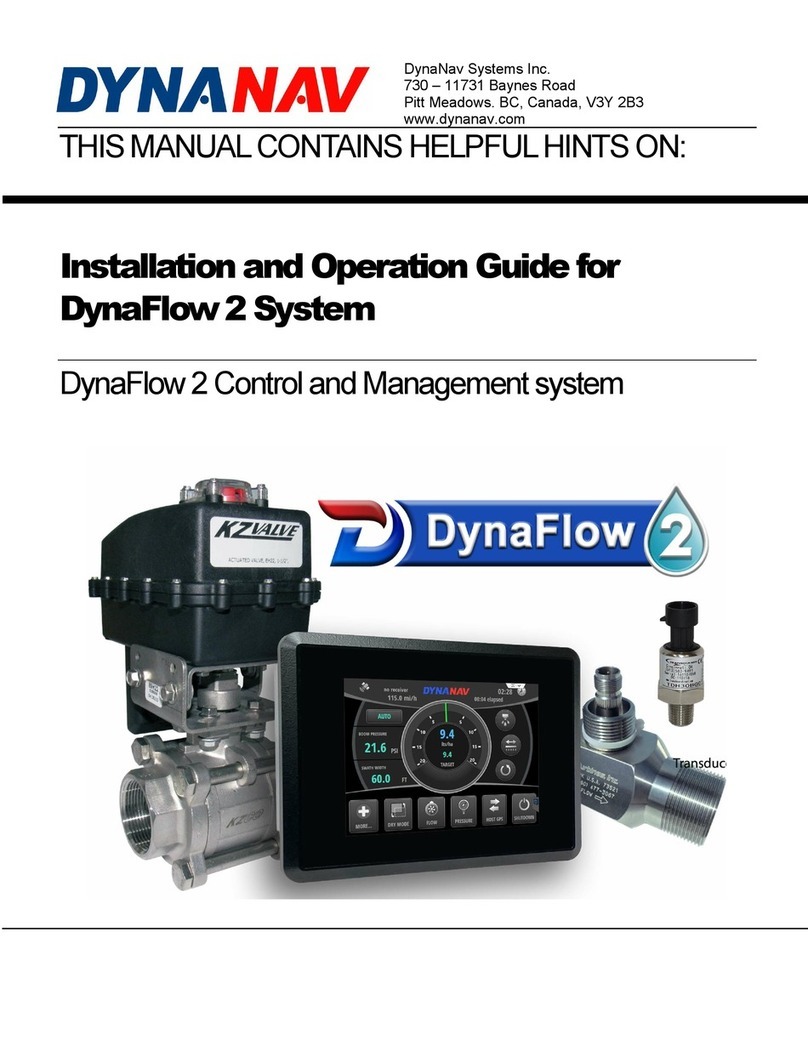
DYNANAV
DYNANAV Dynaflow 2 Installation and operation guide