ORKEL MP2000-X User manual

Table of contents
1 General 11
1.1 Introduction 11
1.1.1 Foreword 11
1.1.2 Disclaimer 11
1.1.3 Range of use 12
1.2 Control before delivery 12
1.2.1 Preparation at customer location 12
1.3 Identification of the machine 12
1.4 The operators manual 13
1.4.1 How to use this manual 13
1.5 Warranty 13
1.6 Declaration of conformity 14
2 Safety 15
2.1 Introduction 15
2.2 Symbols 15
2.2.1 Warning, danger and caution 15
2.3 Emergency stop 17
2.4 To the operator 18
2.4.1 Exercise of security 18
2.4.2 Personal protection 19
2.4.3 Personal safety 19
2.4.4 Safe operation 19
2.4.5 Important issues 19
2.4.6 Danger zones 19
2.5 Precautions 20
2.5.1 Know your machine 20
2.5.2 Equipment control 20
2.5.3 Cleaning 20
2.5.4 Environmental protection 20

2.6 Break-in period 20
3 Settings and hydraulic adjustments 22
3.1 Main parts 23
3.1.1 Principle of operation 23
3.2 Hydraulics 23
3.2.1 Guidelines for hydraulic adjustments 24
3.2.2 Tank valves MP2000-X 24
3.3 Feed hopper 24
3.3.1 Control panels 24
3.3.2 Settings 24
3.4 Elevator and sub conveyor 25
3.4.1 Settings 25
3.5 Chamber 25
3.5.1 Opening speed settings 25
3.5.2 Chamber pressure settings 25
3.6 Plastic tying unit 26
3.6.1 Principle of operation 26
3.6.2 Brake and feed speed 26
3.6.3 Settings 27
3.6.4 Remote control 28
3.7 Wrapping table 28
3.7.1 Wrapping settings 28
3.7.2 Film cutter settings 29
3.7.3 Wrapping table tilt speed 30
3.7.4 Wrapping table ultrasonic sensor 30
3.7.5 Microsonic sensor (S1) 30
3.8 Drawbar 31
3.8.1 Telescopic drawbar 31
4 Operation 32
4.1 Safety 33

4.1.1 Safe work routine 33
4.1.2 Operator safety 33
4.1.3 Other people's safety 33
4.1.4 Assembly on site 33
4.1.5 Elements of hazard during operation 34
4.1.6 Danger zones during operation 34
4.1.7 Risk of overturning 34
4.1.8 Leaving the machine 34
4.2 Connection and setting up the machine 34
4.2.1 Rig up 34
4.2.2 Telescopic drawbar and feed hopper F10 35
4.2.3 Lever/Controls overview 36
4.2.4 Lever list 36
4.2.5 Leveling the machine 37
4.2.6 Placing the tractor with telescopic drawbar 37
4.2.7 Power take off 37
4.2.8 PTO Speed 37
4.2.9 Electrical power source 37
4.2.10 Hydraulic connections 37
4.2.11 Oil temperature 38
4.2.12 Stairs 38
4.3 Daily checklist 38
4.3.1 Daily checklist prior to startup 38
4.3.2 Checkpoints while baling 39
4.4 Break-in period 39
4.4.1 Precautions during the break-in period 39
4.4.2 After the first 50 hours of operation 39
4.5 Automatic operation 40
4.6 Film roller storage 41
4.7 Wrapping arms 42
4.7.1 Wrapping arm emergency stop 42
4.7.2 Installing a new film roller in the wrapper 42

4.8 Parking brake 44
4.9 Operators platform 44
4.10 Compressed air cleaner system 44
4.10.1 Mode of operation 45
4.10.2 Recommendations 45
5 Transport 47
5.1 Transport safety 47
5.1.1 Speed limit 47
5.1.2 On road preparation 47
5.1.3 Lifting points 47
5.1.4 Strapping and tie down 48
5.1.5 Dismantling the machine 48
5.2 Highway use 49
5.2.1 Transport preparation, Telescopic drawbar and feed
hopper F10 49
6 Control system 50
6.1 User interface 50
6.1.1 Main page 50
6.1.2 Icons for starting program sequences 51
6.1.3 Menu 51
6.1.4 User settings [Language and screen] 52
6.1.5 System information 53
6.1.6 Manual controls 53
6.1.7 Machine settings 55
6.1.8 Quick settings 56
6.1.9 Presets 57
6.1.10 Sensors 57
6.1.11 Messages 58
6.1.12 Time and date 59
6.1.13 User data 59
6.1.14 Weighing system 61
6.1.15 Reset 61

6.1.16 Software 61
6.1.17 Settings and explanations 63
7 Maintenance and mechanical adjustments 65
7.1 Safety 66
7.1.1 Before maintenance 66
7.1.2 Safety precautions during maintenance and mechanical
adjustments 66
7.1.3 Elements of hazard during maintenance 67
7.1.4 Control after repair or maintenance 67
7.2 Electrics 67
7.2.1 Fuses 68
7.3 Wheels 68
7.4 Chains 68
7.4.1 Chain tensioner A 68
7.4.2 Chain tensioner B and C 69
7.5 Feed hopper 70
7.5.1 Tightening the feed hopper belts F10 70
7.5.2 Ball bearings 71
7.6 Drive chains 71
7.6.1 Drive chains overview 71
7.6.2 Drive chains tensioning 72
7.7 Elevator and sub conveyor 72
7.7.1 Conveyor belts and feeder carrier 72
7.7.2 Adjusting the conveyor chains 73
7.7.3 Chain tensioner, sub conveyor 74
7.7.4 Chain tensioner, elevator F10 74
7.7.5 Ball bearings elevator 74
7.8 Baling chamber 75
7.8.1 Inspection 75
7.8.2 Adjusting the front chamber belt 75
7.8.3 Adjusting the rear chamber belt 76

7.8.4 Adjusting the chamber belt tensioner 79
7.8.5 Replacing chamber belt 79
7.9 Plastic tying unit 80
7.9.1 Control and maintenance 80
7.10 Wrapping table 81
7.10.1 Inspection 81
7.10.2 Adjusting the wrapping table belt 82
7.11 Frame, drawbar, attachments 84
7.11.1 Frame 84
7.11.2 Main components, fastening points 84
7.12 Chamber roller bushings 84
7.12.1 Wear inspection 84
7.12.2 Permissible wear 85
7.12.3 Remove sprockets 86
7.13 Hydraulics 87
7.13.1 Hydraulics oil 87
7.13.2 Hoses and connections 87
7.13.3 Hydraulic pump, gearbox 87
7.13.4 Heat exchanger 88
7.14 Oil change and oil filter 88
7.14.1 Changing oil and filter 89
7.15 Welding and grinding 90
7.15.1 Precautions when welding 90
7.16 Service history 91
8 Lubrication 92
8.1 Lubrication system, beka max EP 1 92
8.1.1 Oil lubrication, mode of operation 92
8.1.2 Grease lubrication, mode of operation 92
8.1.3 Beka max grease lubrication system 94
8.2 Refilling lubricants 94

8.2.1 Refilling the oil reservoir 95
8.2.2 Adjusting the amount of grease 95
8.2.3 Bleeding the grease system 95
8.3 Electric pump and main distributor 96
8.4 Troubleshooting for Beka max 96
8.5 Oil temperature 97
8.6 Approved lubricants 97
8.6.1 Hydraulics 97
8.6.2 Chain lubrication 97
8.6.3 Greasing 97
8.6.4 Gearbox and gears for hydraulic motors 98
8.7 Manual lubrication charts 99
8.7.1 The compactor 99
8.7.2 Feed hopper F10 100
8.7.3 Telescopic drawbar 101
8.8 Lubrication list - Manual greasing points 102
9 Preservation 103
9.1 Cleaning 103
9.1.1 Using high pressure washer 103
9.2 Storage 103
9.2.1 Long time storage 103
9.2.2 Oil filling in the grease lubrication storage 103
10 Electrics 104
10.1 Main power supply, e-stop switches and electrical
cabinet 105
10.2 Electrical cabinet power supply rail 106
10.3 Sensors and manual controls 107
10.4 Valves, fan motors and pumps 108
10.5 Inputs and outputs 109
10.5.1 IO block 1 109
10.5.2 IO block 2 109

10.5.3 IO block 3 110
10.5.4 IO block 5 110
10.5.5 IO block 6 111
10.5.6 IO block 7 112
10.6 Power supply 112
10.6.1 Supply block 1 112
10.6.2 Supply block 2 113
10.7 Inputs and outputs sorted by number 114
10.7.1 IO list 1 114
10.7.2 IO list 2 115
10.7.3 IO list 3 116
10.8 Inputs and outputs sorted by type 116
10.8.1 Inductive sensors 116
10.8.2 Other sensors and switches 117
10.8.3 Directional valves 117
10.8.4 Sensors, 7-lead cable 118
10.8.5 Film system remote control 118
10.8.6 Radio remote control 118
10.8.7 Proportional valves 118
10.8.8 Valves 118
10.8.9 Cable detection 119
10.9 Sensor overview 120
10.10 Sensor list and function 121
11 Hydraulics 123
11.1 Hydraulic diagram 123
11.1.1 Complete diagram 124
11.1.2 Wrapping table, chamber and elevator control 125
11.1.3 Plastic tying unit, sub conveyor and feed hopper 126
11.1.4 Hydraulic diagram list 126
11.2 Valve overview 128
11.2.1 Valve chart for MP2000-X 128

11.2.2 Valve list for MP2000-X 129
12 Specifications 130
12.1 Electrical system 130
12.2 Power take off 130
12.3 Lubrication system beka-max 130
12.4 Hydraulic system 131
12.5 Wheels and tyres 131
12.6 Dimensions and weight 131
12.6.1 Measurements 131
12.6.2 Power requirements 131
12.6.3 Dimensional sketch F10, operating mode 132
12.6.4 Dimensional sketch F10, transport mode 133
Glossary 134
Index 136

1 General
1.1 Introduction 11
1.1.1 Foreword 11
1.1.2 Disclaimer 11
1.1.3 Range of use 12
1.2 Control before delivery 12
1.2.1 Preparation at customer location 12
1.3 Identification of the machine 12
1.4 The operators manual 13
1.4.1 How to use this manual 13
1.5 Warranty 13
1.6 Declaration of conformity 14
1.1 INTRODUCTION
1.1.1 Foreword
The products from Orkel AS are well known for their high quality, reliability and strength. We will therefore
congratulate you, choosing one of our products.
To fulfill our own goals, regarding quality and strength, Orkel AS has implemented a continuing product-
developing process. All compactors undergo a thorough quality control before leaving the factory.
Read thoroughly, and familiarize yourself with our recommendations, regarding machine - safety, use and
maintenance. Make daily maintenance a routine. By doing this, the machine will be safe to operate, and
you will contribute to a longer machine lifespan and an effective utilization of the machine.
With regards
Orkel AS
1.1.2 Disclaimer
The original parts used in an Orkel® machine are designed and built to provide optimal fit, function, safety,
and structural integrity. For this reason, Orkel® DOES NOT in any circumstance approve of the use of after-
market, gray market, or imitation parts.
The information provided by Orkel® hereunder is provided “as is, where is” and with all faults, and the
entire risk associated with such information is entirely with the Buyer.
Orkel® does not grant, explicitly or implicitly, to any party any patent rights, licenses, or any other IP
rights, whether with regard to such information itself or anything described by such information.
Information provided in this document is proprietary to Orkel®, and Orkel® reserves the right, at its sole
discretion, to make any changes or modification to the information in this document or to any products
and services at any time without notice.
Orkel® does not assume responsibility for any damages associated with the machine or failure caused by
incorrect use of the machine. Neither do we assume responsibility for any changes to the product made
after initial delivery.
1 GENERAL 11

1.1.3 Range of use
The MP2000-X compactor is designed for compressing soft organic materials to bales wrapped in plastic
film for storage or transport. The compactor must only be used for this purpose.
NOTE: Other materials can also be compressed, but have to be confirmed by Orkel AS in each case. This due to
warranty legislations.
1.2 CONTROL BEFORE DELIVERY
This machine is tested, controlled and has passed final inspection, before leaving the factory.
1.2.1 Preparation at customer location
Orkel AS will set-up the machine for the customer if requested/agreed. An introduction course, both in
handling and operating the compactor will be held at site if requested/agreed. During commissioning and
start-up period, we’re offering our technical assistance and answering all questions regarding the com-
pactor start-up.
NOTE: Please see the delivery - warranty formula in section 1.1 "Forms and reports"
1.3 IDENTIFICATION OF THE MACHINE
A sticker describing the serial number is located on the right side of the machine. In addition, the number
is also imprinted on top of the frame. See Figure 1.1.
The serial number must always be provided when contacting your dealer, either it’s for ordering parts or
technical assistance.
The serial number is the safest way to identify your machine. Do not remove or change the serial number.
Figure 1.1 :
Serial number location
1 GENERAL 12

1.4 THE OPERATORS MANUAL
1.4.1 How to use this manual
This manual is organized after the «see—think—use»-principle. The content and explanations are
arranged in smaller sequential operations, and the main chapters are arranged according to the normal
use of the machine (Example: Setup —> Operation —> Maintenance).
Chapter overview:
1. GENERAL This chapter contains some of the formularities associated with a new compactor. Quality
control, identification the machine, and copies of the delivery and warranty forms.
2. SAFETY This chapter consist of the general safety measures one have to consider at all times when
dealing with the machinery. More specific safety measures and warnings are listed and explained
when relevant.
3. SETTINGS AND HYDRAULIC ADJUSTMENTS An introduction to the functionality of the machine. Fur-
thermore, it explains how and where one can adjust the hydraulics to achieve the wanted func-
tionality. Topics organized and gathered for every machine module. Same order as in chapter 7
"Maintenance and mechanical adjustments".
4. OPERATION Describes the rig up process, what to consider prior to and during operation. It also spe-
cifies the running in period.
5. TRANSPORT States all the safety measures and preparations necessary for successful and safe
transport of the compactor.
6. CONTROL SYSTEM Gives a detailed overview of the control system and its functions.
7. MAINTENANCE AND MECHANICAL ADJUSTMENTS A detailed overview of the necessary maintenance
and procedures for mechanical adjustments. Topics organized and gathered for every machine mod-
ule. Same order as in chapter 3 "Settings and hydraulic adjustments".
8. LUBRICATION Explains oil and grease lubrication functionality, settings, troubleshooting and shows
detailed lubrication charts for manual lubrication.
9. PRESERVATION Washing, and other preparations prior to and during long time storage.
10. ELECTRICS Electric schematics.
11. HYDRAULICS Hydraulic diagrams.
12. SPECIFICATIONS An overview over the general machine capacities and performances.
1.5 WARRANTY
Orkel AS recommends that you study the document «Warranty conditions» for detailed information
regarding warranty terms and conditions. This document can be found enclosed in the binder delivered
with the compactor. You can also contact our after sales department.
1 GENERAL 13

1.6 DECLARATION OF CONFORMITY
1 GENERAL 14

2 Safety
2.1 Introduction 15
2.2 Symbols 15
2.2.1 Warning, danger and caution 15
2.3 Emergency stop 17
2.4 To the operator 18
2.4.1 Exercise of security 18
2.4.2 Personal protection 19
2.4.3 Personal safety 19
2.4.4 Safe operation 19
2.4.5 Important issues 19
2.4.6 Danger zones 19
2.5 Precautions 20
2.5.1 Know your machine 20
2.5.2 Equipment control 20
2.5.3 Cleaning 20
2.5.4 Environmental protection 20
2.6 Break-in period 20
2.1 INTRODUCTION
This operator’s safety manual is made to describe safe and good routines when operating the compactor.
On the other hand, it is not possible to describe every operational and safety matters that may arise. Care-
fully consider all your actions, if it is posing a safety hazard to you, or others close to the compactor! • Acci-
dents may kill you or make you disabled. • Accidents can be avoided.
2.2 SYMBOLS
This symbol means:
lATTENTION!
lBE CAUTIOUS!
lCONSERNFORYOURPERSONALSAFETY!
When you see this symbol in the operator’s manual, be aware that violation of instructions given, can
cause you or others in the working area of the machine, being injured or killed.
2.2.1 Warning, danger and caution
Each time you see the words and symbols as shown below, please note the different directions they sym-
bolize. The pictograms are used in this manual or/and on the machine.
2 SAFETY 15

The symbol and the word DANGER,
state a direct or immediate dan-
gerous situation that will cause
DEATH OR SERIOUS INJURY if not
avoided.
The symbol and the word WARNING, indic-
ates a potentially hazardous situation. If
you fail to comply with instructions given it
could result in personal injury or loss of life.
Do not start operating the machine
until you have read and understood
the safety precautions.
Always stop the tractor engine or external
power unit before; lubricating, adjusting,
maintaining or repairing the machine. Also,
remove the ignition key to prevent acci-
dental start.
Ensure that there are no people
between tractor and machine during
connecting and disconnecting.
Never allow children to stay near the
machine during operation. Young children
can do unpredictable things
Danger rotating parts. Keep clear of
moving/rotating parts in chamber.
Operator or others close to the machine
must be aware when the bale is unloaded
from the wrapper table. Bales dropped
may roll more than 10 m, or even dropped
prematurely.
Always use the hydraulic securing
valves on the chamber door lifting
cylinders, to ensure that the
chamber door stays in open position
during maintenance or repair.
The net or widefilm is cut with a sharp
knife. Be careful when loading a new roller,
or if any adjustment is done to the knife
system.
All parking of the machine must be
on a firm levelled ground, and
secured with wheel chocks.
Unauthorized personell are not allowed
closer than 5 meters, when the machine is
operating or when maneuvering.
Danger. Film holder/cutter has a
sharp knife and there is a risk of
cutting/crushing injury. Always keep
closed when the machine is not
operating.
Keep clear! Do not enter below bunker or
frame when operating the compactor.
2 SAFETY 16

Noise zone. Use ear protection. Stairway. Access only for operators or
mechanics.
Make sure the transmission is run-
ning with the correct speed and
direction. Wrong speed and/or
direction can damage machinery and
may cause great danger to persons
nearby. The machine is designed for
a PTO-speed of 850 rpm.
Stay clear, rotating machinery.
Strapping point. Lifting point.
Jacking point. Hydraulics securing valves, locking the tail-
gate lifting cylinders.
Between the tractor and the machine, there is a rotating PTO-
shaft. No one is allowed to stand between the tractor and the
machine while the engine is running. Do not wear loose clothes,
scarfs etc.
Warning signs, indicating danger or warning attached to the machine, must not be removed or
painted over. Unreadable signs shall be replaced by new ones. These can be ordered from Orkel
AS.
2.3 EMERGENCY STOP
The machine is equipped with 5 manual emergency stop buttons. Four are accessible from ground level
and one on top of the machine as indicated on Figure 2.1.
2 SAFETY 17

Figure 2.1 :
Red circles indicates emergency stop locations. Two more buttons are located on
the opposite side, ground level.
When an emergency stop button has been triggered, the emergency stop button has to be reset so that
the machine can be started from the control panel.
Figure 2.2 :
Mushroom head type emergency stop button. Twist the head to reset.
2.4 TO THE OPERATOR
2.4.1 Exercise of security
lAs operator, it is your responsibility that you read and understand the safety instructions given in
this operator’s safety manual.
lThese instructions must be followed without exception. The operator is the key to safety on this
machine, not only for you, but also for others in the compactors working area.
lFollow the safety instructions, and you will experience the compactor as a safe and secure place to
work.
2 SAFETY 18

2.4.2 Personal protection
The Compactor might generate a lot of dust and noise, depending on which material being com-
pressed. For your own health, we recommend that operators use personal protective equip-
ment, such as safety goggles, dust/filter mask, and ear-protection during operation.
2.4.3 Personal safety
Use all available protective and safety equipment. Provide good lighting in the area where the machine is
positioned. All covers must remain intact and attached during operation. If pressing of flammable mater-
ials, a fire extinguisher must be in close proximity.
2.4.4 Safe operation
Persons under 16 years of age should under no circumstances operate this machine.
Personnel under influence of alcohol or other drugs must not operate this machine.
2.4.5 Important issues
Be aware of children and other unauthorized persons in close proximity to the machine. Never allow
unqualified persons to operate this machine.
2.4.6 Danger zones
Only operators and maintenance personnel are allowed “inside” the danger zone! All others
must be turned away, due to their own safety!
The entire left side of the compactor is a blind spot for the operator.
2 SAFETY 19

2.5 PRECAUTIONS
2.5.1 Know your machine
Know your machine. Learn all the functions and actuating mechanisms, and familiarize where the emer-
gency stop switches are located. Learn the machines capacity and limitations, to avoid unnecessary down-
time and mechanical brake-down.
IMPORTANT: If any dangerous situations occur, shut down the power take off (PTO) right away.
2.5.2 Equipment control
Before starting up, make sure that the machine and its equipment is in place and in good working order!
See chapter 7 "Maintenance and mechanical adjustments".
2.5.3 Cleaning
A good cleaning of the machine increases durability and safety. Therefore, keep all surfaces clean, remove
dirt, oil-spills and other remains.
2.5.4 Environmental protection
Hazardous waste, such as rubber, oil and other materials that could harm the environment, must be dis-
posed at approved disposal centres.
2.6 BREAK-IN PERIOD
Check Check points
Do not run compactor at maximum capacity the first 25 hours of operation
Be observant – monitor that functions are working correctly.
Check for abnormal sounds from the machinery
Fine tune the process to be carried out so that the compactor can reach maximum capa-
city, based on material being baled.
2 SAFETY 20
Table of contents
Other ORKEL Garbage Disposal manuals
Popular Garbage Disposal manuals by other brands
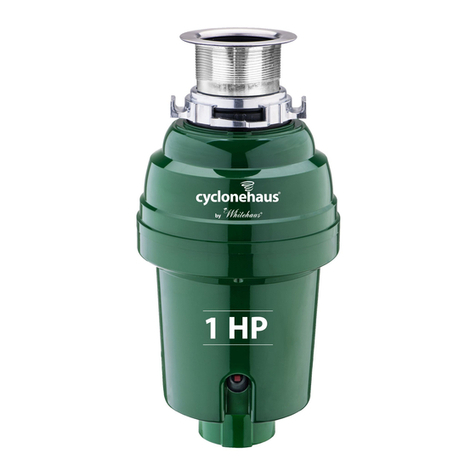
Whitehaus
Whitehaus WH007 Product installation manual

Weber mt
Weber mt 0116533 Operating and maintenance manual

Meiwa
Meiwa KP30 Safety and operation/maintenance and parts manual

KitchenAid
KitchenAid KCDI075VA Limited warranty
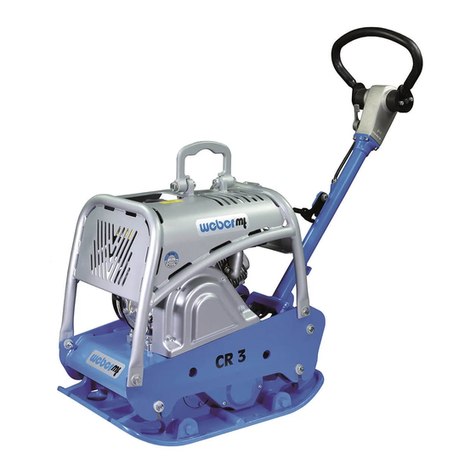
Weber mt
Weber mt CR 3-II Hd Operating and maintenance manual
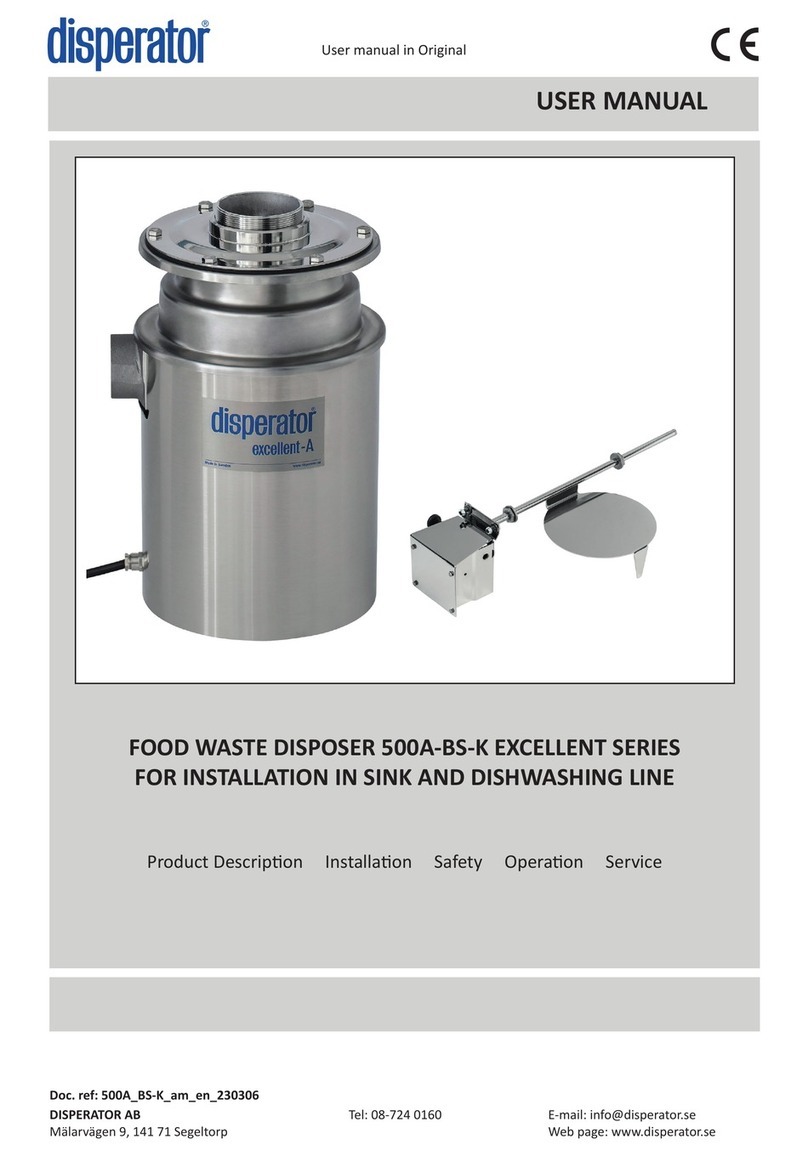
disperator
disperator Excellent 500A-BS-K Series user manual