ORTEC 2126 User manual

11
M
P
i
3
I
i
Model
2126
Constant
Fraction
Discriminator
User's
Manual
9231701A
8/93
ISO
9001
m
M

]
J
J
J
J
J
]
]
3
Table
of
Contents
]
3
3
3
3
J
"i
J
Page
1.
INTRODUCTION
i
2.
CONTROLS,
CONNECTORS
AND
INDICATORS
2.1
Front
Panel
2
3.
SETUP
INFORMATION
3.1
Attenuator
Module
3
3.2
Fraction
Module
3
3.3
Count
Rate
Range
3
3.4
Operating
Mode
3
3.5
Output
Width
Range
6
3.6
Standard/Alternate
Power
Supplies
6
3.7
Standard
Setup
6
4.
OPERATION
4.1
Power
Supply
6
4.2
Input
Signals
6
4.3
Operating
Mode
6
4.4
Delay
Cable
7
4.5
Walk
Trim
7
4.6
Threshold
Adjustment
7
4.7
Outputs
and
Width
Control
7
5.
CIRCUIT
DESCRIPTION
5.1
Power
Supply
9
5.2
Constant
Fraction
and
Threshold
Circuits
9
APPENDIX
A
SPECIFICATIONS
A.I
Inputs
A.2
Outputs
A.3
Controls
-
Front
Panel
A.4
Controls
-
Internal
A.5
Performance
A.6
Typical
Cable
Lengths
A.7
Power
Requirements
.
,
A.8
Physical
FIGURE
LISTING
Figure
2.1
Front
Panel
Figure
3.1
Internal
Controls
Figure
3.2
Options
for
Attenuator
Module
Figure
3.3
Constant
Fraction
Module
.
5
Figure
3.4
Leading
Edge
Module
Figure
4.1
Typical
Input
Signal
Figure
4.2
Walk
Inspect
Wave
Form
Using
Plastic
Detectors
..
.
8
Figure
4.3
Walk
Inspect
Wave
Form
for
Slow
Detectors
.
8
Figure
4.4
Typical
Negative
Output
Pulses
8
Figure
5.1
Timing
Signals
.
10

]
]
Section
1.
Introduction
I
I
The
Model
2126
is
a
200
MHz
Constant
Fraction
Discrimi
nator
in
a
single
width
NIM.
it
has
independent
controls
for
threshold,
walk,
output
pulse
width,
and
operating
mode,
and
provides
maximum
flexibility
for
use
in
any
timing
application.
The
2126
is
fully
dc
coupled
and
provides
two
count
rate
operating
ranges
for
use
over
a
wide
range
of
input
count
rates.
In
the
standard
count
rate
range,
the
2126
operates
to
150
MHz
with
the
front
panel
potentiometer
controlling
both
the
output
width
and
the
internal
dead
time.
Alterna
tively,
a
special
high
count
rate
range
can
be
selected
which
provides
operation
to
200
MHz
(typically
250
MHz)
with
fixed
output
width
and
deadtime.
The
50
ohm
input
of
the
2126
accepts
negative
pulses
with
amplitudes
up
to
-5
V.
Input
protection
is
provided
for
inputs
outside
the
expected
range.
An
internal
jumper
can
connect
a
X2
attenuator
to
the
input
to
extend
the
input
range
to
-10
V.
Three
operating
modes
are
provided.
In
addition
to
its
normal
Constant
Fraction
(CF)
timing
mode,
the
2126
provides
a
Constant
Fraction
with
Slow
Risetime
Reject
(SR)
timing
mode
and
a
Leading
Edge
(LE)
mode.
A
fraction
module
is
provided
and
set
for
0.4;
it
can
easily
be
changed
to
another
fraction,
if
desired.
An
alternate
plug-
in
module
allows
Leading
Edge
operation.
Two
independent
fast
negative-timing
outputs
and
two
independent
positive-timing
outputs
are
provided.
This
provides
maximum
flexibility
for
most
timing
applications.
In
addition,
an
LED
is
provided
to
indicate
the
presence
of
input
signals.
The
2126
can
operate
from
NIM
bins
with
the
standard
±
12
V
and
±
24
V
power
supplies.
If
a±
6
V
power
supply
is
available,
the
2126
can
be
configured
to
use
that
supply
for
much
of
its
power
requirements.
I
1
I
]
1
]
1
"i
J

Section
2.
Controls,
Connectors
and
Indicators
2.1
FRONT
PANEL
THRESHOLD
CONTROL
selects
threshold
for
sig
nal
acceptance
from
-5
mV
to
-1
V.
INPUT
accepts
-5
mV
to
-5
V
linear
pulses
(-10
mV
to-10
V
with
X2
attenuator
in
place).
Zin
=
50n.
OUTPUT
LED
indicates
2126
is
processing
pulses
WALK
ADJUST
CON
TROL
varies
relative
zero
cross
timing
to
provide
minimum
time
walk
-
OUTPUTS
-
Two
inde
pendent
outputs
provide
-16
mA
into
50
O
ioads.
-t-
OUTPUTS
-
Two
inde
pendent
outputs
provide
-I-
5
V
nominal
into
high
impedance
loads
COHSTA
PISCRIHMATOR
®
2126
®
IWESHDU)
INPUT
ADJUST
INSPECT
OUTPUTS
MODE
SWITCH
deter
mines
timing
mode.
SR
=
Slow
Reject,
OF
=
Con
stant
Fraction,
LE
=
Leading
Edge
WALK
INSPECT
OUT
PUT
displays
output
of
Constant
Fraction
com
parator.
Attenuated
ECL
leveis,
-85
mV
and
-190
mV.
DELAY
CONNECTORS
accept
external
delay
cables.
Cable
length
determines
delay.
WIDTH
CONTROL
varies
width
of
outputs
and
sets
channel
dead
time
in
NO
(Normal)
range.
Disabled
in
HR
(High
Rate)
range.
Figure
2.1
Front
Panel

Section
3.
Setup
Information
This
section
describes
the
function
of
the
various
jumpers
and
modules
mounted
on
the
printed
circuit
board
of
the
2126.
Any
adjustments
should
be
made
prior
to
installing
the
2126
in
a
NIM
bin
or
connecting
the
2126
to
a
power
source.
Remove
the
left
cover
of
the
2126
to
expose
the
circuit
board.
3.1
ATTENUATOR
MODULE
The
2126
is
provided
with
an
input
attenuator
module.
This
module
provides
the
choice
of
no
attenuation
or
X2
atten
uation
of
the
input
signal.
The
input
range
of
the
2126
is
-5
mV
to
-5
v.
If
the
peak
input
signal
is
expected
to
be
-5
V
or
less,
no
attenuation
should
be
selected.
For
applications
where
the
peak
input
signal
is
between
-5
V
and
-10
V,
the
X2
attentuation
should
be
selected.
The
attenuator
module
is
a
small
assembly
containing
two
resistors
and
a
short
jumper
wire
mounted
near
the
front
of
the
2126
(Figure
3.1).
The
attenuation
factor
can
be
changed
by
removing
the
module
from
the
socket,
rotating
it
180
degrees,
and
replacing
it
in
the
socket.
See
Figure
3.2
which
illustrates
the
two
choices
of
attenuation
provided
by
the
attenuator
module.
The
attenuator
module
is
shipped
from
the
factory
in
the
no
attenuation
position.
3.2
FRACTION
MODULE
In
timing
experiments,
one
of
the
important
variables
to
consider
is
the
fraction
of
the
input
signal
used
to
derive
the
constant
fraction
function.
Most
applications
provide
optimum
timing
with
a
fraction
of
0.4.
This
fraction
is
pro
vided
by
the
2126.
However,
the
2126
offers
the
user
an
easy
means
to
change
the
fraction.
The
fraction
module
is
located
immediately
below
the
attenuator
module
near
the
front
of
the
2126.
The
user
can
change
the
desi
red
fraction
in
two
ways.
Figure
3.3
illustrates
the
fraction
module
and
lists
values
for
two
resistors
that
can
be
changed
by
the
user
to
implement
different
values
for
the
fraction.
Alter
nately,
contact
the
factory
regarding
other
values
of
frac
tion
modules
available
on
special
order.
3.3
COUNT
RATE
RANGE
(NOrmal/HIgh
Rate)
Two
count
rate
ranges
are
provided
on
the
2126.
The
user
can
select
the
desired
count
rate
range
by
moving
a
jumper
mounted
on
the
circuit
board.
NOrmal
range
(NO)
is
intended
for
most
uses
of
the
2126.
It
provides
for
count
rates
up
to
150
MHz.
In
the
NOrmal
range,
the
front
panel
WIDTH
potentiometer
controls
the
width
of
the
negative
and
positive
timing
outputs
and
the
internal
deadtime
of
the
2126.
In
certain
extremely
high
rate
applications,
the
user
should
select
the
High
Rate
range
(HR).
This
range
provides
for
usable
count
rates
of
greater
than
200
MHz.
However,
certain
precautions
should
be
observed
in
using
the
HR
range
of
the
2126.
In
this
range,
the
front
panel
WIDTH
potentiometer
is
inactive.
The
width
of
the
negative
timing
outputs
and
the
internal
deadtime
of
the
2126
channel
are
internally
set
at
approximately
2
ns.
The
input
signal
should
be
approxirnately
2
ns
in
width
and
show
a
clean
return
to
the
baseline
in
order
to
fully
utilize
the
speed
of
the
HR
mode
of
the
2126.
In
addition,
the
user
should
verify
that
companion
NIM
modules
used
with
the
2126
in
its
HR
range
are
capable
of
accepting
negative
NIM
inputs
of
2
ns
width.
The
NO/HR
jumper
is
located
just
to
the
right
of
A2
on
the
2126.
See
Figure
3.1.
NO
is
the
upper
position
of
the
jumper.
HR
is
the
lower
position
of
the
jumper.
The
2126
is
shipped
in
the
NO
position.
3.4
OPERATING
MODE
(Constant
Fraction/Slow
Reject/
Leading
Edge)
The
2126
provides
three
operating
modes:
Constant
Frac
tion
(OF),
Constant
Fraction
with
Slow
Reject
(SR),
and
Leading
Edge
(LE).
See
Section
4.3
for
a
description
of
these
operating
modes.
3.4.1
The
Constant
Fraction
Mode
The
Constant
Fraction
(CF)
mode
is
intended
for
use
with
detectors
such
as
fast
plastic
detectors
which
exhibit
fast
rise
time
outputs
with
little
risetime
variation.
The
Constant
Fraction
with
Slow
Risetime
(SR)
mode
is
often
used
with
Germanium
detectors
which
exhibit
a
wide
range
of
rise
time
variation.
The
Leading
Edge
mode
is
used
with
detec
tors
which
provide
fast
outputs
with
little
amplitude
or
risetime
variation.
3.4.2
Constant
Fraction
and
Constant
Fraction
with
Slow
Reject
Modes
Both
Constant
Fraction
(CF)
and
Constant
Fraction
with
Slow
Reject
(SR)
modes
use
the
internal
fraction
module
supplied
with
the
2126.
To
use
either
mode,
verify
that
the
fraction
module
is
properly
installed
in
its
socket
near
the
front
of
the
2126
circuit
board.
Figure
3.3
shows
the
proper
installation
of
the
fraction
module.
With
the
fraction
module
installed,
the
front
panel
Mode
Switch
allows
selection
of
Constant
Fraction
(CF)
mode
or
Constant
Fraction
with
Slow
Reject
(SR).
3.4.3
Leading
Edge
Mode
To
select
the
Leading
Edge
Mode,
the
user
should
remove
the
fraction
module
from
its
socket
near
the
front
of
the
board
and
replace
it
with
the
Leading
Edge
module.
A
socket
is
provided
near
the
bottom
of
the
circuit
board
to
hold
the
unused
module.
The
front
panel
Mode
Switch
should
be
set
to
Leading
Edge
(LE)
to
use
the
Leading
Edge
mode.
Figure
3.4
shows
the
proper
installation
of
the
Leading
Edge
module.
Table
3.1
summarizes
the
module
and
switch
settings
for
the
three
operating
modes.

Figure
3.1
shows
the
Internal
layout
of
the
2126.
The
func
tion
of
the
internal
controls
and
their
normal
configuration
is
illustrated.
Table
3.1
Operating
Mode
Summary
Operating
Mode
Constant
Fraction
Constant
Fraction
with
Slow
Reject
Leading
Edge
Module
Fraction
Fraction
Leading
Edge
Front
Panel
Switch
CF
SR
LE
PC
Board
Attenuator
Module
NOrmal
or
High
Hate
Jumper
Plug
HR
«
Fraction
Module
tgcn
X5
X1
Input
power
selection
Jumper
Plug
A
=
±12
V
operation
8
=
±
6
V
operation
E
Leading
Edge
Module
in
spare
position
Output
Width
Range
Jumper
Plug
Figure
3.1
internal
Controls

}
J
J
J
JP1
JP1
<Z3>-
-CII>
5in
Kl
loofi
K)
0
0
0
0
(R5)
(R6)
PIN1
P.C.
BOARD
TOP
JP2
-CID-
H
h
H
h
-cn>-
0-
0
(KiooQj4^
(KEEl
.
(R5)
'(R6)
•
P.C.
BOARD
SIDE
P1N1
RN1
P.C.
BOARD
TOP
JP2
(a.)
NO
ATTENUATION
(b.)
X
2
ATTENUATION
-
P.C.
BOARD
EDGE
FRONT_
PANEL
I
Figure
3.2
Options
for
Attenuator
Module
JP1
icon
HI
MMi20o|^
P.C.
BOARD
•
P.C.
BOARD
SIDE
f,
R7
a
51fi
R8
a
5in
R9
=
50a/f
Rl0
=
50Q«f
±
^
ElO
.1
510
4.7
.2
240
10
.4
120
20
a.)
STANDARD
MODULE
(f
=
.4)
INSTALLED
b.)
R9&
RIO
VALUES
FOR
ALTERNATE
FRACTIONS
Figure
3.3
Constant
Fraction
Module,
Including
Resistor
Values
for
Field
Changes
JP1
j
]
P.C.
BOARD
TOP
0
0
0
0
-r-D-
0
0
H
f-
0
0
P1N1
H
H
T
1
oJ
l
0
0
A
fr
TsiHTn
PIN1
JP2
LEADING
EDGE
MODULE
IN
JP2
POSITION
n-TTrnmHl
0-CSE3-0
OCMDO
(KIBZEH)
PIN1
FRACTION
MODULE
IN
SPARE
POSITION
P.C.
BOARD
.EDGE
/
Figure
3.4
Leading
Edge
Module

3.5
OUTPUT
WIDTH
RANGE
(X1/X5)
Two
ranges
of
adjustment
are
provided
for
tfie
front
panel
WIDTH
potentiometer.
Since
the
WIDTH
potentiometer
controls
the
output
widths
as
well
as
the
internal
deadtime
of
the
2126,
the
proper
range
for
the
WIDTH
adjustment
should
be
selected.
Use
XI
for
fast
plastic
detectors
and
most
sodium
iodide
detectors.
Detectors
that
provide
input
signals
of
100
ns
width
or
greater,
or
that
cause
baseline
perterbations
extending
longerthan
100
ns,
should
use
the
X5
range.
The
X1/X5
jumper
is
located
below
A2.
See
Figure
2.2.
XI
is
to
the
right
and
X5
is
to
the
left.
The
X1/X5
jumper
is
shipped
in
the
XI
position.
3.6
STANDARD/ALTERNATE
POWER
SUPPLIES
The
2126
can
operate
from
Nlf^
bins
equipped
with
the
standard
±
12V
and
+
24
V
power
supplies
as
well
as
those
with
the
optional
±
6
V
power
supply.
Since
the
2126
draws
current
is
excess
of
the
single-width
NIfvl
module
limit
when
connected
to
a
±12
V
supply,
operation
of
the
2126
from
±
6
V
will
reduce
the
current
drawn
to
within
the
single-width
module
limits.
If
a
±
6
V
power
supply
is
available,
set
the
input
power
jumpers
to
the
6
V
position,
otherwise
use
the
12
V
position.
See
Figure
3.1.
The
6
V
position
for
both
jumpers
is
towards
the
bottom
of
the
module
and
is
labeled
"B".
The
12V
position
is
towards
the
top
of
the
module
and
is
labeled
"A".
3.7
STANDARD
SETUP
The
following
can
be
considered
a
standard
setup
and
is
shipped
from
the
factory
in
this
configuration:
Attenuator
module
Fraction
module
Timing
range
Operating
mode
Output
width
range
Power
supply
XI
(no
attenuation)
Constant
Fraction,
f
=
0.4
NO
(NOrmal)
OF
(Constant
Fraction)
XI
(2-100
ns)
±12V
Section
4.
Operation
4.1
POWER
SUPPLY
The
2126
is
intended
to
be
operated
in
a
NIM
bin
equipped
with
a
power
supply
providing
±
12
V
and
±
24
V.
Alter
nately,
a
N11^
bin
providing
±
12
V.±
24
V
and±
6
V
can
be
used.
See
Section
3.6.
For
lab
bench
testing,
a
NIM
power
supply
extension
cable
may
be
used.
However,
excessive
voltage
drops
in
the
extension
cable
may
be
encountered
due
to
the
relatively
high
current
requirements
of
the
2126.
For
use
in
experiments,
secure
installation
in
a
NIM
bin
is
recommended.
The
NIM
bin
power
supply
should
be
off
when
the
2126
orother
NIM
are
installed
or
removed
from
the
NIM
bin.
4.2
INPUT
SIGNALS
Typical
input
signals
to
the
2126
are
generated
by
scintilla
tion
detectors
utilizing
photomultiplier
tubes
or
solid
state
detectors
with
a
charge
sensitive
preamp
and
timing
filter
amplifier.
Such
signals
are
negative,
going
from
a
baseline
of
ground.
Rise
times
can
vary
from
1
ns
to
greater
than
100
ns,
and
widths
from
1
ns
to
greater
than
500
ns.
For
labora
tory
test
bench,
a
logic
pulser
can
be
used
as
an
input
to
the
2126.
See
Figure4.1
foratypical
inputsignal
produced
bya
logic
pulser.
4.3
OPERATING
MODE
Selection
of
operating
mode
depends
on
the requirements
of
the
given
experiment.
Some
general
compromises
worth
considering
are
discussed
in
the
following
paragraphs.
4.3.1
Constant
Fraction
(OF)
Mode
In
the
Constant
Fraction
(OF)
mode,
timing
is
derived
from
a
comparison
between
a
fixed
ratio
(40%
in
the
2126)
and
the
peak
amplitude
of
each
successive
pulse.
This
instan
taneous
self-reference
yields
a
time
mark
that
is
theoreti
cally
independent
of
the
pulse
height,
as
contrasted
to
the
behavior
of
the
leading
edge
mode.
In
the
2126,
the
ratio
reference
signal
is
taken
internally,
and
the
full
amplitude
pulse
is
delayed
for
the
comparison
by
an
external
cable
connected
between
the
two
front
panel
DELAY
connectors.
When
the
length
of
this
external
cable
is
chosen
to
gener
ate
a
time
delay
less
than
the
rise
time
of
the
input
pulse,
the
resulting
time
mark
is
stabilized
for
both
amplitude
and
rise
time
variations
of
that
pulse.
This
is
the
basis
for
ARC
(Amplitude
and
Rise
time
Compensated)
timing.
The
com
promise
in
Constant
Fraction
(and,also
ARC)
timing
is
the
ability
to
provide
proper
delays
for
the
rise
time
of
the
input
pulse
considering
either
rate
and
pile-up
effects
or
the
distortions
introduced
by
varying
wavefront
shapes
due
to
charge
collection
deficit,
ballistic
effects,
or
trapping
effects
in
the
detector.
It
is
these
accommodations
that
lead
to
empirical
determinations
of
the
optimum
delay
cable
length
for
a
given
detector
and
setup.
4.3.2
Constant
Fraction
With
Slow
Reject
(SR)
Mode
In
the
Constant
Fraction
with
Slow
Rise
time
reject
(SR)
mode,
a
further
accommodation
is
offered
for
the
longer
rise
times
of
solid
state
detectors.
The
timing
mark
for
the
Constant
Fraction
is
derived
from
the
slightly
delayed
pulse,
with
the
presumption
that
the
THRESHOLD
level
has
been
set
quite
low
and
this
level
is
exceeded
prior
to
the
derivation
of
the
timing
mark.
In
the
case
of
solid
state
detectors,
where
long
varying
wavefronts
of
the
input
pulse
are
common,
a
relatively
short
delay
cable
is
frequently
used
and
the
above
timing
premise
may
not
be
satisfied.
In
that
case,
the
amplitude
discriminator
keyed
to
the
THRESHOLD
setting
may
switch
late,
and
the
resulting
timing
will
represent
some
mix
of
the
intended
Constant
Fraction
timing
with
Leading
Edge
timing.
This
effect
causes
either
tailing
or
a
satellite
peak
in
a
time
spectrum.
In
the
SR
mode,
a
logic
alternation
causes
rejection
of
pulses
which
do
not
exceed
the
THRESHOLD
prior
to
the
derived
Constant
Fraction
timing
mark.
The
result
is
enhanced
timing
resolution
due
to
elimination
of
the
Lead
ing
Edge
errors,
but
with
some
loss
of
counting
efficiency.

J
J
1
]
]
1
4.3.3
Leading
Edge
(LE)
Mode
The
Leading
Edge
mode
Is
used
less
often
than
the
two
Constant
Fraction
modes.
It
Is
typically
used
for
detectors
with
fast
risetlmes
and
little
amplitude
variation.
Since
the
Constant
Fraction
function
Is
disabled
when
the
2126
Is
used
In
Leading
Edge
mode,
amplitude
and
risetlme
varia
tion
can
Introduce
timing
walk.
If
the
Input
signals
are
all
essentially
of
the
same
amplitude
and
risetlme,
the
Leading
Edge
mode
can
offer
good
timing
performance.
4.4
DELAY
CABLE
The
delay
cable
used
to
set
the
Constant
Fraction
timing
mark
should
provide
a
delay
less
than
the
known
rise
time
of
the
applied
input
pulse
for
full
compensation
of
both
amplitude
and
rise
time
variations
(for
a
fixed
shape).
For
fast
and
moderately
fast
detector
pulses
(up
to
10
ns
rise
time)
a
delay
of
nominally
75%
of
the
rise
time
is
most
effective.
For
solid
state
detectors,
a
delay
of
40%
of
the
pulse
rise
time
Is
commonly
used
for
the
reasons
given
above.
The
Internal
delay
of
the
2126
is
0.3
ns.
and
this
must
be
corrected
by
picking
a
suitable
cable.
For
example.
If
the
detector
rise
time
Is
4
ns.
a
3
ns
delay
would
be
recom
mended.
The
external
cable
length,
estimated
on
the
basis
of
4.8
ns
per
meter
for
RG-58
cable,
would
be:
External
Delay
Total
delay
-
Internal
Delay
L
=
4.8
3.0
-
0.3
ns
4.8
ns/m
4.8
56.3
cm
or
about
22
Inches
4.5
WALK
TRIM
The
adjustment
of
the
amplitude
sensitive
variation
of
the
timing
mark
(time
walk)
In
the
Constant
Fraction
and
CFRR
modes
remains
a
less
exact
procedure.
Proper
adjustment
is
possible
only
when
the
do
offset
present
on
the
Input
to
the
2126
Is
less
than
±
6
mV
do.
Thus
detector
leakage
or
dark
current
errors
must
be
minimized
before
attempting
adjustment.
Laboratory
trimming
of
the
unit
can
be
demonstrated
by
using
a
suitable
pulse
generator
with
a
known
fast,
clean
wavefront
and
a
delay
chosen
as
discussed
above.
A
very
broadband
50
ohm
attenuator
such
as
the
Hewlett
Packard
HP-3496.
or
one
whose
time
walk
Is
very
precisely
known,
should
be
used.
An
externally
triggered
oscilloscope
capa
ble
of
displaying
at
least
1
ns/dlvlslon
Is
also
necessary.
Step
attenuations
should
be
then
yield
a
stable
time
posi
tion
of
the
2126's
output
signal
when
starting
from
a
refer
ence
-5
V
peak
pulse
Input.
Care
must
be
taken
that
the
pulse
generator
offset
Is
small
and
does
not
change
for
different
attenuator
settings.
The
WALK
ADJUST
trimming
potentiometer
can
be
used
to
find
the
best
adjustment
of
the
finite
time
walk
over
a
narrower
amplitude
range
as
desired.
When
the
2126
Is
used
with
the
Intended
detector,
timing
resolution
may
be
trimmed
experimentally
by
successive
measurements
In
the
setup
at
hand.
A
qualitative
monitor
ing
Is
available
by
monitoring
the
front
panel
INSPECT
output
with
an
oscilloscope.
For
fast
detectors,
the
output
should
Indicate
an
attenuated
logic
low
ECL
level
(approx.
-0.19
V
dc.
Into500)'where
noise
just
disappears
Into
this
level
and
pulses
are
seen
as
transitions
to
logic
high
ECL
(approx.
-0.085
V
dc
into
50
fi
).
Reference
Figure
4.2.
For
slower
detectors,
a
noise
band
between
the
ECL
levels
may
be
seen,
with
transitions
to
ECL
logic
high
and
low
of
about
equal
intensity.
Reference
Figure
4.3.
4.6
THRESHOLD
ADJUSTMENT
The
2126
threshold
adjustment
can
be
used
as
a
lower
level
control
to
select
the
threshold
above
which
Input
pulses
will
generate
an
output
signal.
A
front
panel
test
point
Is
provided
to
allow
easy
measurement
of
the
selected
thre
shold
voltage.
As
a
general
rule
of
thumb,
select
a
thre
shold
voltage
as
high
as
possible
while
not
excluding
Input
signals
of
Interest.
Unless
experimental
conditions
dictate
otherwise,
do
not
use
minimum
settings
of
the
threshold,
since
Input
signals
often
show
ringing
or
baseline
perter-
batlons
which
may
generate
unwanted
outputs.
4.7
OUTPUTS
AND
WIDTH
CONTROL
The
2126's
negative
logic
outputs
are
Intended
to
drive
50
ohm
loads
through
any
reasonable
length
of
suitable
50
ohm
coaxial
cable
(such
as
RG-58).
Figure
4.4
shows
the
typical
negative
output
pulse
shapes
Into
50
ohm
loads,
with
the
WIDTH
control
set
to
minimum.
For
optimum
performance,
terminate
unused
negative
outputs
In
50
ohms.
Since
the
WIDTH
control
also
sets
the
DEAD
TIME
follow
ing
a
given
pulse
In
the
NOrmal
count
rate
range,
the
user
should
set
this
control
consistent
with
the
pulse
rate
requirements
of
the
given
experiment.
In
the
minimum
(fully
counterclockwise)
position
of
the
WIDTH
control,
a
count
rate
In
excess
of
150
MHz
can
be
expected
for
the
NOrmal
mode
of
the
2126.
The
WIDTH
control
of
the2126
is
Inoperative
In
the
High
Rate
mode.
The
2126's
positive
logic
outputs
are
designed
to
drive
relatively
high
Impedance
loads
with
logic
levels
of
nomi
nally
0
and
-t-
5
V.
Since
this
type
of
output
Is
inherently
slower
than
current
mode
outputs
(the
negative
outputs),
the
positive
outputs
may
not
provide
proper
logic
transi
tions
at
the
high
count
rates
the
2126
is
capable
of.
]
J
]

1
5nS
0.2V
i
■v^
Figure
4.1
Typical
Input
Signal
Produced
by
a
Logic
Pulser
Figure
4.2
Walk
Inspect
Wave
Form
Using
Plastic
Detectors
1
5nS—-
0.2V
t
V
Figure
4.3
Walk
Inspect
Wave
Form
for
Slow
Detectors
Figure
4.4
Typical
Negative
Output
Pulses
into
50
ohms
Load

Section
5.
Circuit
Description
The
2126
is
a
high
performance
Constant
Fraction
Discrim
inator
in
a
single
width
NlM.
lt
also
includes
a
power
supply
circuit
to
provide
logic
power
to
the
unit.
This
section
describes
the
operation
of
both
the
power
supply
and
the
Constant
Fraction
Discriminator.
5.1
POWER
SUPPLY
The
2126
consists
primarily
of
ECL
logic
which
uses
a
supply
voltage
of
-5.2
V.
In
addition,
a
TTL
supply
voltage
of
-f
5.0
V
is
required.
Two
methods
of
obtaining
these
voltages
are
provided,
selectable
by
a
jumper
plug.
When
the
2126
is
used
in
a
NIM
bin
with
the
standard
supply
voltages
of
±
12
V
and
±
24
V,
the
logic
supply
voltages
of
-5.2
and
+
5.0
V
are
provided
by
adjustable
three-terminal
regulators.
Q1
and
Q2,
together
with
their
associated
cir
cuitry,
provide
stable
well-regulated
logic
voltages.
If
a
±
6
V
NIM
power
supply
is
available,
the
2126
board-
mounted
jumpers
can
be
set
to
provide
the
required
logic
voltages
directly
from
the
±
6
V
supplies.
In
each
case,
a
diode
(D1
for
+
6
V,
D2
for
-6
V)
drops
the
power
supply
voltages
to
the
logic
voltages
required
by
the
2126.
In
either
case,
the
-2
V
ECL
pull-down
voltage
is
provided
by
an
additional
three-terminal
regulator
(Q3),
operating
from
the
-5.2
V
logic
supply.
5.2
CONSTANT
FRACTION
AND
THRESHOLD
CIRCUITS
The
input
signal
is
applied
directly
to
pin
10
of
the
thresh
old
comparator.
D1
provides
a
temperature
compensated
voltage
which
is
divided
to
produce-1
V
across
the
thresh
old
potentiometer
(RV1).
The
wiper
voltage
of
RV1,
which
varies
from
-5
mV
to
-1
V,
is
applied
to
pin
10
of
the
threshold
comparator.
The
constant
frac'i
.Ti
'unction
is
implemented
at
the
inputs
of
the
ultrafast
comparator
A4b.
The
input
attenuator
module
is
a
X2
attenuator
that
maintains
the
proper
50
ohm
input
impedance.
It
can
be
rotated
to
provide
no
attenuation
(short
between
the
input
and
pin
5
of
the
frac
tion
module)
or
X2
attenuation
(100
ohms
between
the
input
and
pin
5
of
the
fraction
module).
The
fraction
module
serves
to
attenuate
both
the
prompt
and
delayed
inputs
to
the
constant
fraction
comparator
(A4b)
while
providing
the
proper
50
ohm
input
impedance.
The
prompt
input
to
A4b
(pin
8)
is
attenuated
more
than
the
delayed
input
(pin
7)
resulting
in
the
fraction
f
=
0.4.
This
combina
tion
of
attenuation
and
delay
provides
the
following
signals
at
the
inputs
of
the
constant
fraction
comparator:
pin
8':
0.3
input
amplitude,
prompt
pin
7:
0.67
input
amplitude,
delayed
by
cable
selected
See
Figure
5.1
which
illustrates
the
signals
associated
with
the
constant
fraction
and
threshold
comparators.
Prior
to
the
application
of
an
input
signal,
the
inverting
output
of
A4b
(pin
2)
can
be
in
either
logic
state
depending
on
the
offset
voltage
applied
to
A4b
pin
8
by
the
WALK
ADJUST
potentiometer.
Upon
application
of
an
input
sig
nal,
A4b
pin
8
initially
is
lower
than
A4b
pin
7,
driving
the
inverting
output
A4b
pin
2
to
a
logic
high.
When
the
delayed
signal
arrives
at
A4b
pin
7,
it
causes
this
pin
to
become
more
negative
than
A4b
pin
8
which
causes
the
inverting
output
(A4b
pin
2)
to
fall
to
a
logic
low.
The
timing
of
this
low-going
sign
al
is
input
amplitude
independent.
The
inverting
output
of
the
threshold
comparator
(A4a
pin
15)
is
normally
a
logic
high.
When
an
input
signal
is
ap
plied,
the
inverting
output
of
A4a
goes
to
a
logic
low
when
the
input
signal
crosses
the
selected
threshold
voltage.
This
logic
transition
occurs
ahead
of
the
output
from
the
constant
fraction
comparator
since
the
input
to
the
con
stant
fraction
output
is
delayed
by
the
front
panel
delay
cable.
Thus,
the
10H209
OR/NOR
(A3b)
gate
has
a
high
input
from
the
threshold
comparator
and
an
indeterminant
input
from
the
constant
fraction
comparator
prior
to
the
application
of
an
input
signal.
When
an
input
is
applied,
A3b
pin
7
goes
low
if
the
threshold
is
crossed.
Shortly
later,
A3b
pin
5
goes
low
due
to
the
constant
fraction
compara
tor.
The
inverting
output
of
A3b
(pin
3)
goes
high
when
the
constant
fraction
comparator
fires
if
the
threshold
was
crossed.
This
logic
signal
is
the
clock
to
the
ultra
fast
11C70D
flip-flop
A2.
When
the
2126
is
used
in
the
Constant
Fraction
mode,
the
D
input
of
A2
(pin
11)
is
held
at
a
logic
low
by
A3a
pin
14.
After
the
preceding
signal
was
processed,
A2
was
left
in
the
SET
state
with
the
Q
output
high
and
the
Qbar
output
low.
When
the
clock
signal
arrives
at
A2
pin
7
from
A3
pin
3,
the
D
flip-flop
is
RESET
by
clocking
in
the
low
at
A2
pin
11,
the
outputs
are
ac'iv
-,d
the
channel
is
unable
to
process
further
inputs.
A2
is
SET
via
the
HR
or
NO
jumper,
thus
terminating
the
outputs
and
the
internal
deadtime.
In
the
NOrmal
mode
of
operation,
the
Q
output
of
A2
is
pulled
down
by
the
current
source
consisting
of
Q9
and
asso
ciated
bias
resistors.
The
line
driver/receiver
Ala
senses
the
falling
edge
of
A2
pin
2
and
drives
the
SET
input
of
A2
high,
thereby
SETting
A2
and
terminating
the
output.
The
front
panel
WIDTH
potentiometer
varies
the
current
source
Q9
and
thus
varies
the
rate
of
fall
of
A2
pin
2.
Thus,
the
width
of
the
one-shot
formed
from
A2
is
varied.
In
the
High
Rate
mode,
the
current
source
Q9
and
Ala
are
bypassed.
The
rising
edge
of
A2
Qbar
is
coupled
directly
to
the
SET
input
of
A2.
Thus,
the
propigation
delays
associated
with
A2
determine
the
output
widths
and
the
internal
deadtime.

In
the
Slow
Reject
mode,
the
circuit
functions
virtually
the
same.
The
D
input
of
A2
is
driven
by
A3a
pin
14,
which
now
has
a
low
going
logic
signal
driven
by
the
threshold
com
parator
through
A3a.
A
slight
delay
is
provided
by
R14
and
C7.
For
fast
risetime
signals,
the
D
input
of
A2
is
low
before
the
clock
drives
pin
7
high.
However,
slow
risetime
signals
cause
the
threshold
comparator
to
fire
slightly
later.
For
these
slow
risetime
signals,
the
falling
edge
of
the
signal
at
A2
pin
11
arrives
after
the
clock
at
pin
7
and
a
high
is
clocked
into
to
flip-flop.
Since
the
flip-flop
is
already
SET,
no
change
occurs
at
its
output
and
the
input
signal
is
ignored.
In
the
Leading
Edge
mode,
the
Constant
Fraction
compar
ator
(A4b)
is
disabled
in
a
state
that
permits
the
Leading
Edge
comparator
(A4a)
to
generate
the
clock
for
flip-flop
A2.
The
line
driver/receiver
A1
b
is
driven
by
the
Qbar
output
of
A2
and
serves
to
drive
the
two
independent
negative
out
puts
differentially.
It
also
toggles
A1
c,
the
one-shot
driving
the
front
panel
LED.
The
negative
output
transistors
are
conventional
differential
switches
with
the
collectors
driv
ing
the
50
ohm
outpUts
directly.
\
A4pin8
0.5V
t
A4pin7
O.svf
A4
pin15
1.0V
I
A4pin2
1.0V
{
2ns
Figure
5.1
Timing
Signals
10

Appendix
A.
Specifications
A.1
INPUTS
INPUT
-
Accepts
-5
mV
to
-5
V
(-10
mV
to
-10
V
with
internal
X2
attenuator)
linear
pulses;
rise
time
>
1
ns;
Z|n
=
50
ohms,
dc
coupled;
front
panel
BNC
connector
protected
to
±
100
V
(duration
limited).
DELAY-Two
BNC
connectors
between
which
a
delay
cable
is
connected
to
form
the
internal
constant
fraction
signal.
Recommended
lengths
are
based
upon
RG-58
cable
propagation
delay
of=4.8
ns/m
to
provide
a
delay
of
=
0.2
trise
for
germanium
detectors
and
=
0.8
tnse
for
most
other
detector
types.
A.2
OUTPUTS
WALK
INSPECT
-
Displays
output
signal
of
zero
crossing
discriminator
for
use
in
trimming
time
walk;
Zout=50
ohms.
NEGATIVE
OUTPUTS
-
2
independent
negative
current
outputs,
each
providing
-16
mA
into
50
ohms,
rise
time
=
1
ns;
dc
coupled
front
panel
BNC
connectors;
pulse
width
controlled
by
WIDTH
potentiometer
in
Normal
mode;
2
ns
nominal
in
High
Rate
mode.
POSITIVE
OUTPUTS
-
2
independent
positive
voltage
outputs,
each
providing
2
V
minimum
into
50
O,
4
V
min
imum
into
high
impedance,
rise
time
10
ns
or
less;
dc
coupled
front
panel
BNC
connectors;
pulse
width
con
trolled
by
WIDTH
potentiometer
in
Normal
mode,
unde
fined
in
High
Rate
mode.
A.3
CONTROLS
-
FRONT
PANEL
THRESHOLD
-
Front
panel
10-turn
potentiomenter
to
set
acceptance
threshold
for
input
pulses;
range
-5
mV
to
-1
V.
WALK
ADJUST
-
Front
panel
potentiometer
to
compen
sate
walk
of
the
internal
zero
crossing
discriminator.
WIDTH
-
Front
panel
10-turn
potentiometer
to
vary
inter
nal
deadtime
and
width
of
negative
outputs
in
Normal
mode.
Range
=
2-100
ns
or=
10-500
ns
as
determined
by
internal
jumper.
Inoperative
in
High
Rate
mode.
A.4
CONTROLS
-
INTERNAL
ATTENUATION
-
Board
mounted
DIP
jumper
selects
no
attenuation
or
X2
attenuation
of
input
signal.
FRACTION
-
Board
mounted
DIP
jumper
selects
value
of
constant
fraction;
0.4
standard,
other
values
available
by
special
order.
TIMING
MODE
-
Board
mounted
jumper
selects
Constant
Fraction
(CF)
or
Constant
Fraction
with
Slow
Risetime
Reject
(SR)
timing
mode.
OPERATING
MODE
-
Board
mounted
jumper
selects
Normal
(NO),
or
High
Rate
(HR)
operating
mode.
OUTPUT
WIDTH
RANGE
-
Board
mounted
jumper
se
lects
=
2-100
ns
(XI)
or
10-500
ns
(X5)
output
WIDTH
range.
POWER
SUPPLY
-
Board
mounted
jumpers
select
±
12
V
or
±
6
V
as
input
power
for
2126
logic.
A.S
PERFORMANCE
DYNAMIC
RANGE
-
1000;1
WALK
-
<
100
ps
for
a
1
ns
rise-time
pulse
over
a
100:1
dynamic
range
(referenced
to
-5
V)
in
the
CF
mode.
COUNTING
RATE
-
Normal
mode
to
150
MHz,
as
limited
by
deadtime;
High
Rate
mode
to
200
MHz.
PULSE
PAIR
RESOLUTION
-
Normal
mode
<
7
ns
as
limited
by
deadtime;
High
Rate
mode
<
5
ns.
THRESHOLD
STABILITY
-
Better
than
±
0.02%/°
C
(±200
ppm/°C)
TEMPERATURE
RANGE
-
0°C
to
+
50°C
THRESHOLD
LINEARITY
-
±
0.25%
integral
A.6
TYPICAL
CABLE
LENGTHS
(RG-58)
For
plastic,
Nal,
and
silicon
detectors
-
0.3
to
1.0
m
(1.0
to
3.3
ft.)
For
Planar
Ge
Detectors
-
1.0
to
2.0
m
(3.3
to
6.6
ft.)
For
Coaxial
Ge
Detectors
-
2.0
to
4.0
m
(6.6
to
13
ft.)
A.7
POWER
REQUIREMENTS
Power
jumpers
set
to
±12
V:
+12
Vdc
—
130
mA
-12Vdc
—350
mA*
Power
jumpers
set
to
±
6
V:
+12
Vdc—
20
mA
+6
Vdc—130
mA
-12
Vdc
—120
mA
-6
Vdc
—250
mA
*
Exceeds
the
NIM
power
allotment
for
a
single-width
module.
A.S
PHYSICAL
SIZE
-
Single
width
NIM
module
3.43
X
22.12
cm
(1.35X
8.71
in.)
perTID-20893
(rev.)
NET
WEIGHT
-
0.9
kg
(2.0
lbs.)
SHIPPING
WEIGHT
-
1.8
kg
(4.0
lbs.)
11
Table of contents
Other ORTEC Control Unit manuals
Popular Control Unit manuals by other brands

DoorHan
DoorHan CV01 owner's manual

Dungs
Dungs MV X Operating and assembly instructions

POLNA
POLNA BR 33 Installation, operation and maintenance manual
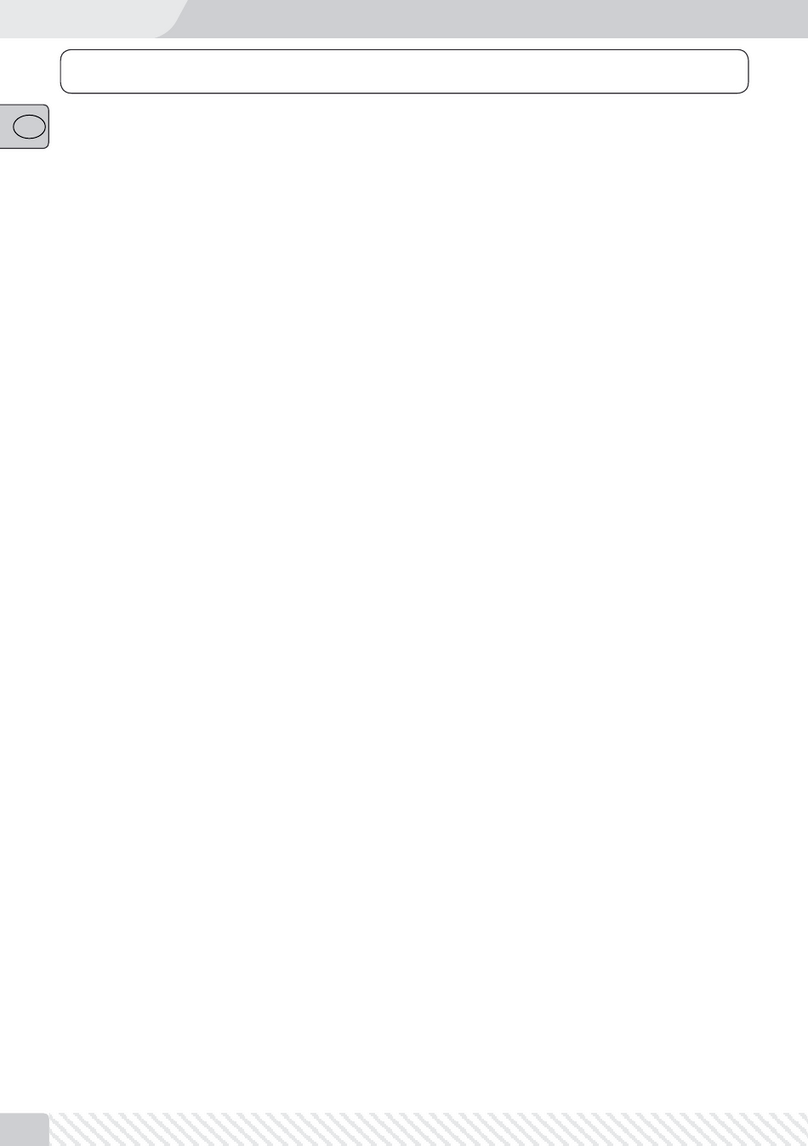
roco
roco multiMAUSPRO Getting started
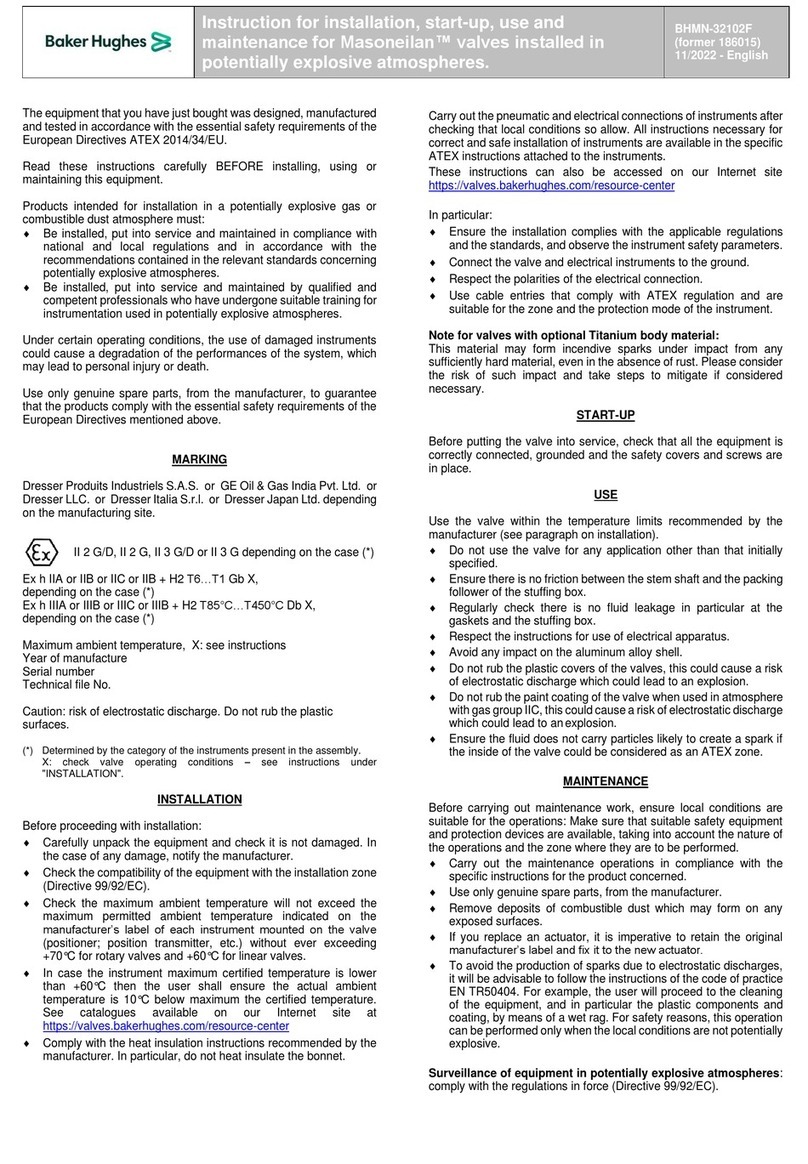
Baker Hughes
Baker Hughes Masoneilan Instructions for installation

Reliance electric
Reliance electric GV3000 instruction manual
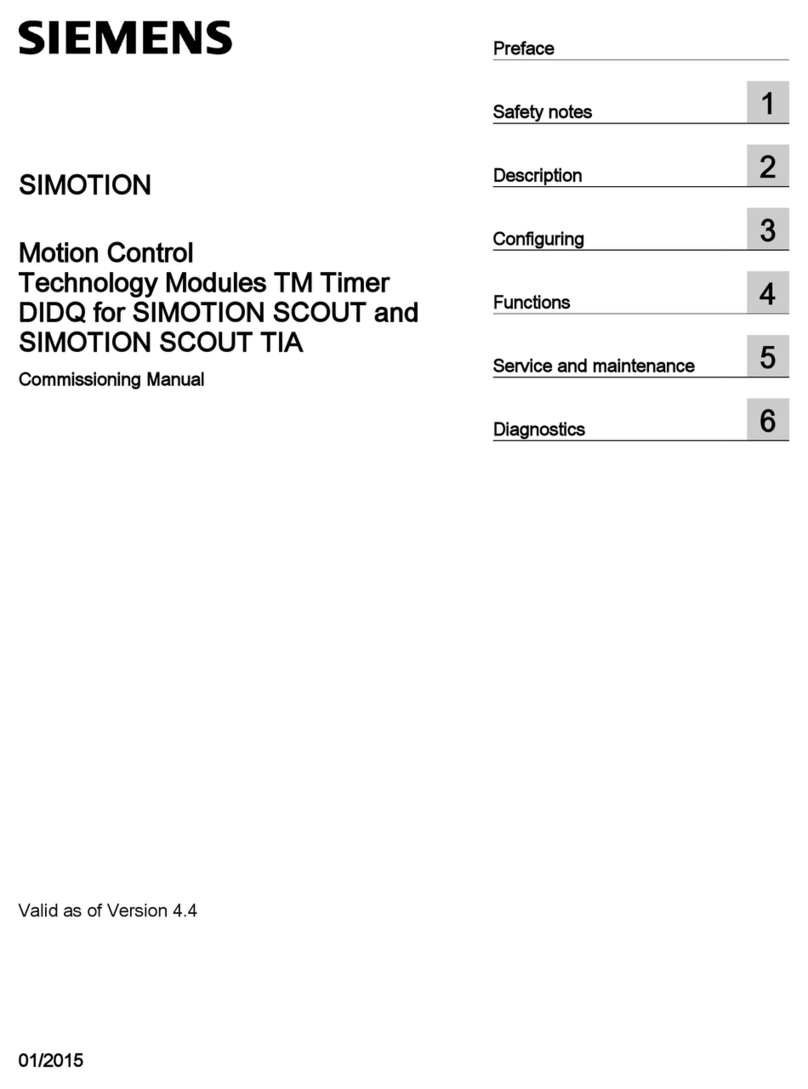
Siemens
Siemens TM Timer DIDQ Commissioning manual
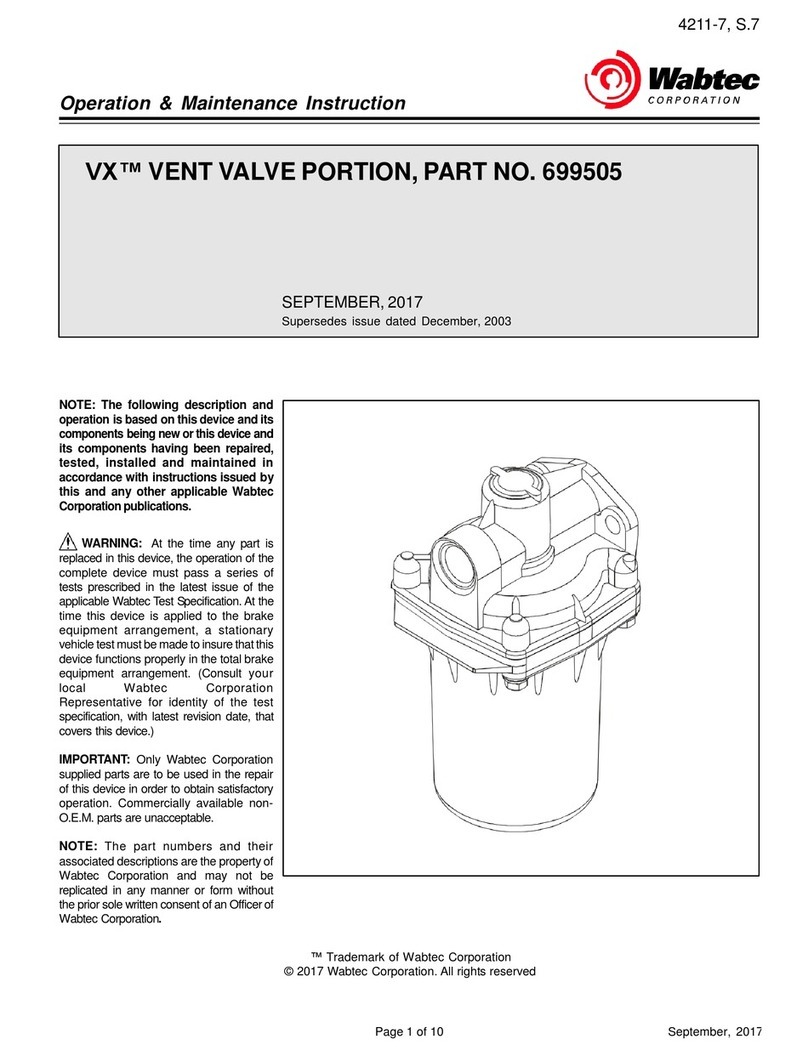
Wabtec
Wabtec VX Operation & maintenance instructions

YOKOGAWA
YOKOGAWA FA-M3 VITESSE F3CX04-0N user manual
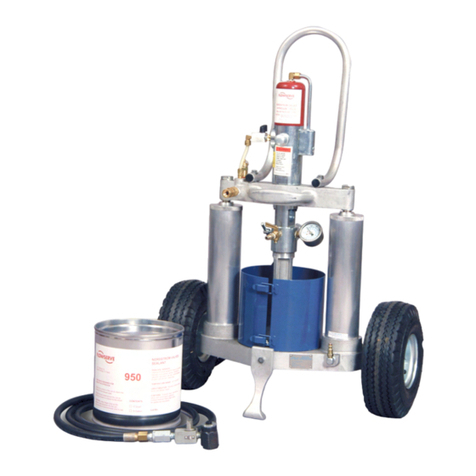
Flowserve
Flowserve NORDSTROM HYPREGUN PLUS 5Q Assembly, Operation and Maintenance Manual

urmet domus
urmet domus sinthesi 1158/82 Technical manual
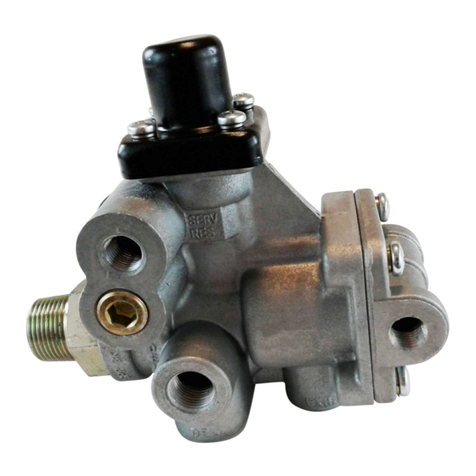
BENDIX
BENDIX SR-2 TRAILER SPRING BRAKE VALVE manual