OTC Tools 5203 User manual

Sheet No.
Issue Date: Rev. B, November 8, 2013
© Bosch Automotive Service Solutions LLC
Form No. 540669
1 of 2
Parts List and
Operating Instructions
for: 5203
655 Eisenhower Drive
Owatonna, MN 55060 USA
Phone: (507) 455-7000
Tech. Serv.: (800) 533-6127
Fax: (800) 955-8329
Order Entry: (800) 533-6127
Fax: (800) 283-8665
International Sales: (507) 455-7223
Fax: (507) 455-7063
Item Part
No. No. Qty. Description
1 541502 1 Handle
2 541515 1 Tray
3 541500 1 Saddle
4 541514 2 Lift Arm Support Strap
5 541513 2 Wheel
6 541511 1 Power Unit
7 541512 2 Caster Kit
Service Jack
Max. Capacity: 3 Tons
Application: Designed to lift a wide range of motor vehicles.
Item Part
No. No. Qty. Description
8 541517 1 Release Bracket
9 541516 1 Foot Pedal/Handle Mount
10 541521 1 Pump Plunger Pressure Regulator
11 541519 1 Pump Plunger/Cylinder Kit
12 541518 1 Release Valve Stem Assembly Kit
13 541520 1 Release Valve Stem Kit
14 541510 1 Seal Kit
541522 1 Hardware Kit
14
14
14
14
13
1
2
3
4
5
6
7
8
9
10
11
12
14

Safety Precautions
CAUTION: To prevent personal injury and/or damage to equipment,
• Read, understand, and follow all instructions, includingASME PALD Part 10 for service jacks.
If the operator cannot read these instructions, operating instructions and safety precautions
must be read and discussed in the operator’s native language.
• Before using the service jack to lift a vehicle, refer to the vehicle service manual to determine
recommended lifting surfaces on the vehicle chassis.
• Wear eye protection that meets ANSI Z87.1 and OSHA standards.
• Inspect the jack before each use; do not use the jack if it’s damaged, altered, or in poor
condition. Take corrective action if any of the following conditions are found: cracked or
damagedhousing;excessivewear,bending,orotherdamage;leakinghydraulicuid;scored
ordamagedpistonrod;loosehardware;modiedoralteredequipment.
• A load must never exceed the rated lifting capacity of the jack.
• Use the jack on a hard, level surface. The jack must be free to roll without any obstructions
while lifting or lowering the vehicle. The wheels of the vehicle must be in the straight-ahead
position and the hand brake released.
• Use the jack for lifting purposes only. Stay clear of a lifted load. Place support stands under
the axles before working on the vehicle.
• Center the load on the jack saddle. Off-center loads can damage seals and cause jack failure.
Lift only dead weight.
• Do not use blocks or other extenders between the saddle and the load being lifted.
• Do not modify the jack or use adapters unless approved or supplied by OTC.
• Lower the jack slowly and carefully while watching the position of the jack saddle.
• Useonlyapprovedhydraulicuid.Neverusebrakeuid.
Parts List & Operating Instructions Form No. 540669, Sheet 1 of 2, Back
Air can accumulate within a hydraulic system during shipment. This entrapped air causes the
jack to respond slowly or feel “spongy.” The following procedure bleeds air from the system.
1. Insert the handle into the handle mount and secure it with the screw provided.
2. Open the release valve by pulling on and turning the handle clockwise (CW).
3. Pump the handle up and down several times.
4. Release the handle, and it will automatically return to position with the release valve closed.
5. Test the jack for normal operation. If the lift pad doesn’t rise to the correct height, repeat
Steps 2–4. If this doesn’t solve the problem, call the OTC Technical Services Dept. at (800)
533-6127.
Bleeding Air from the System

Sheet No.
Issue Date: Rev. B, November 8, 2013
© Bosch Automotive Service Solutions LLC
Parts List & Operating Instructions Form No. 540669
To Lift a Load
1. Position the jack under the vehicle.
WARNING: To prevent personal injury and/or equipment damage,
•Use the manufacturer’s recommended lifting points on the chassis.
•Avoid wheel obstructions such as gravel, tools, or uneven expansion joints.
2. Pump the jack handle up and down, using the full stroke range of the piston, to
raise the saddle to the contact point.
3. Check the placement of the jack; the load must be centered on the jack saddle.
4. Finish lifting the vehicle by pumping the handle. Do not attempt to raise the jack
beyond its travel stops.
5. Place approved support stands under the vehicle at points that will provide stable
support. Before making repairs on the vehicle, lower it onto the support stands by
SLOWLY and CAREFULLY pulling on and turning the handle clockwise (CW).
To Lower a Load
Support stands should be holding the load during vehicle repairs. When ready to lower
the load:
1. Follow steps 1-4 of the "To Lift a Load" section above.
2. Lift the load just enough to remove the support stands.
3. Pull on and turn the jack handle clockwise (CW). The load will lower smoothly and
uniformly.
4. When the load and jack are completely lowered, release the handle. The handle
will automatically return to its position for lifting.
2 of 2
Operating Instructions

Parts List & Operating Instructions Form No. 540669, Sheet 2 of 2, Back
Preventive Maintenance
IMPORTANT: The greatest single cause of failure in hydraulic units is dirt. Keep the service jack clean and well
lubricated to prevent foreign matter from entering the system. If the jack has been exposed to rain, snow, sand, or grit,
it must be cleaned before it is used.
1. Store the jack in a well-protected area where it will not be exposed to corrosive vapors, abrasive dust, or any other
harmful elements.
2. Regularly lubricate the moving parts in the wheels, arm, handle, and pump roller pin.
3. Replacethehydraulicuidinthereservoiratleastonceperyear.Tocheckthehydraulicuidlevel,lowerthelifting
armcompletely.Removetherubberllerplugfromthepowerunit.Thehydraulicuidlevelshouldbeatthebottom
ofthellerplughole.Ifnecessary,addhydraulicuid,andinstallthellerplug. IMPORTANT: The use of alcohol or
hydraulicbrakeuidcoulddamagethesealsandresultinjackfailure.
4. Inspect the jack before each use. Take corrective action if any of the following problems are found:
a.cracked,damagedhousing c.leakinghydraulicuid e.loosehardware
b.excessivewear,bending,otherdamage d.scored,damagedpistonrod f.modiedequipment
5. Keep warning labels and instructional decals clean and readable. Use a mild soap solution to wash external surfaces
of the jack.
Troubleshooting Guide
Repairproceduresmustbeperformedinadirt-freeenvironmentbyqualiedpersonnelwhoarefamiliarwiththisequipment.
CAUTION: To prevent personal injury, all inspection, maintenance, and repair procedures must be performed
when the jack is free of a load (not in use).
Trouble Cause Solution
Jack does not lift
Jack lifts only partially
Jack advances slowly
Jack lifts load,
but doesn't hold
Jackleakshydraulicuid
Jack will not retract
Jack retracts slowly
1. Release valve is open.
2.Low/nohydraulicuidinreservoir.
3. Air-locked system.
4. Load is above capacity of jack.
5. Delivery valve and/or bypass valve not
working correctly.
6. Packing worn out or defective.
1. Verify the release valve is closed by position of the
handle. Release valve may need cleaning.
2.Fillwithapprovedhydraulicuidandbleedsystem.
3. Bleed system. (See “Bleeding Air from the system”
on back of page 1.)
4. Use correct equipment.
5. Clean to remove dirt or foreign matter. Replace
hydraulicuid.
6. Replace packing.
1.Toomuchornotenoughhydraulicuid. 1.Checkhydraulicuidlevel.
1. Pump not working correctly.
2. Leaking seals.
1. Rework pump.
2. Replace seals. (OTC Seal Kit No. 541510)
1. Cylinder packing is leaking.
2. Valve not working correctly (suction,
delivery, release, or bypass).
3. Air-locked system.
1. Replace packing.
2. Inspect valves. Replace if necessary.
3. Bleed system.
1. Worn or damaged seals. 1. Replace seals.
1. Release valve is closed. 1. Open the release valve by pulling on and turning
the handle clockwise (CW). May be necessary to
clean release valve.
1. Cylinder damaged internally.
2. Return spring(s) is damaged.
3. Link section is binding.
1. Send jack to OTC-authorized service center.
(Refer to OTC Form No. 104031.)
2. Replace return spring(s).
3. Lubricate link sections.
Other OTC Tools Jack manuals
Popular Jack manuals by other brands
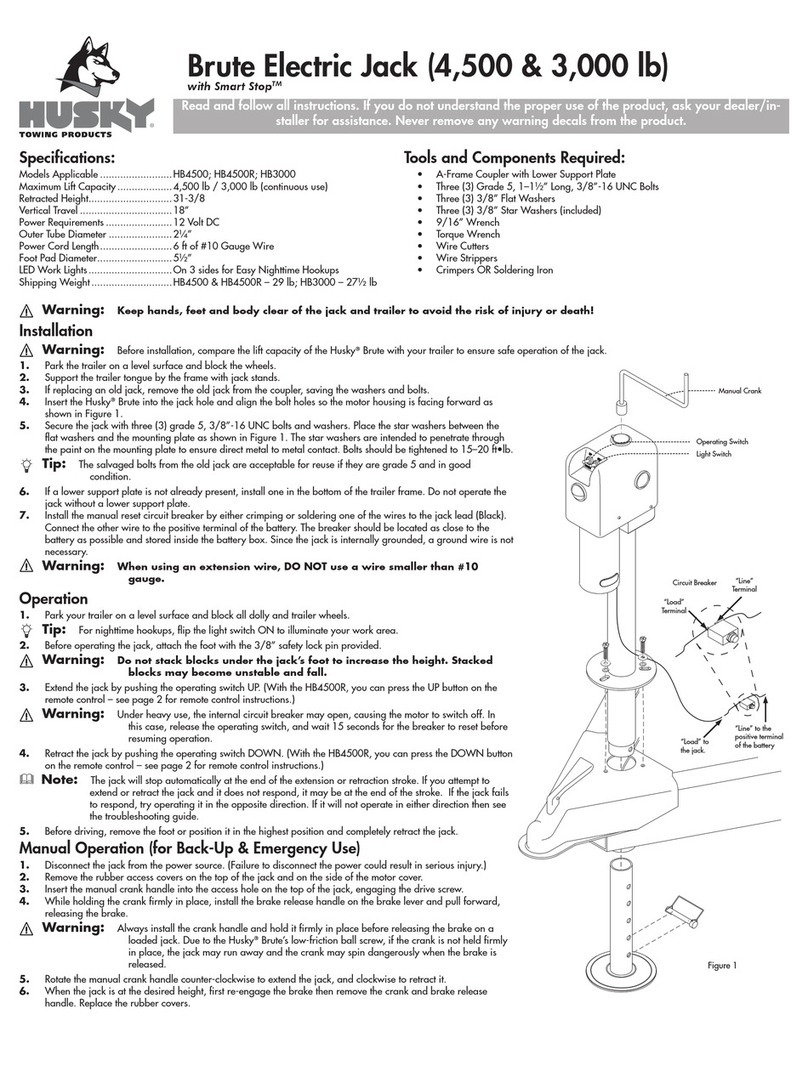
Husky
Husky HB4500 manual
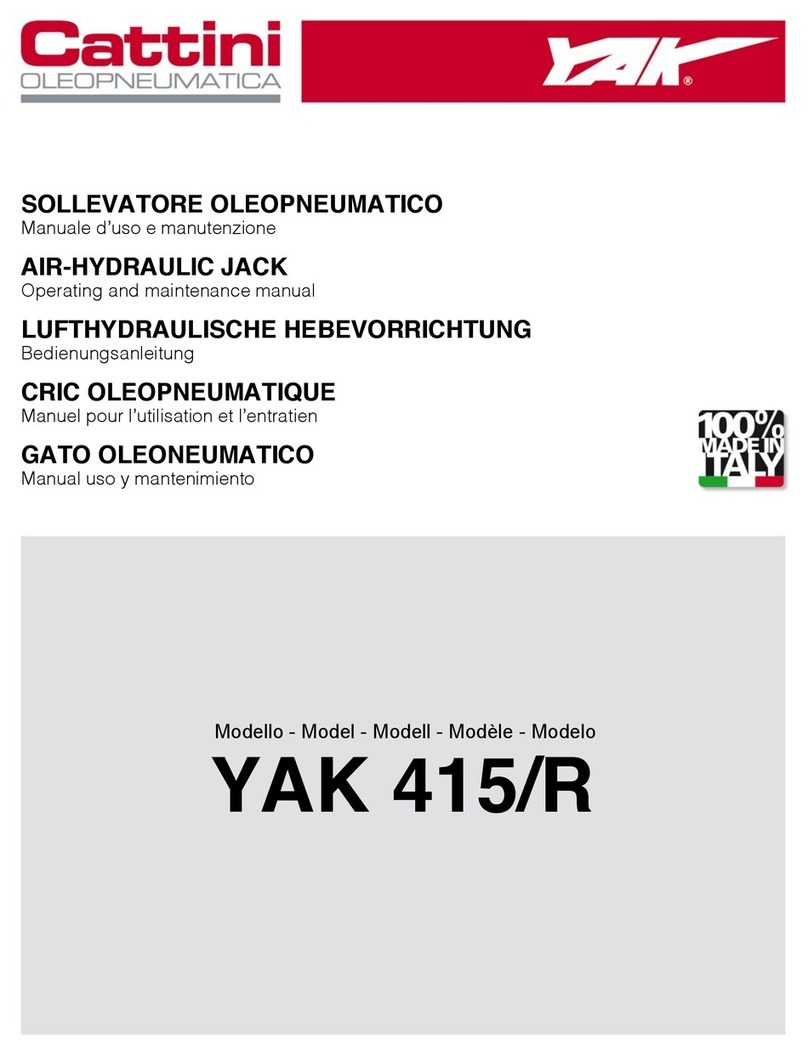
Cattini Oleopneumatica
Cattini Oleopneumatica YAK 415/R Operating and maintenance manual
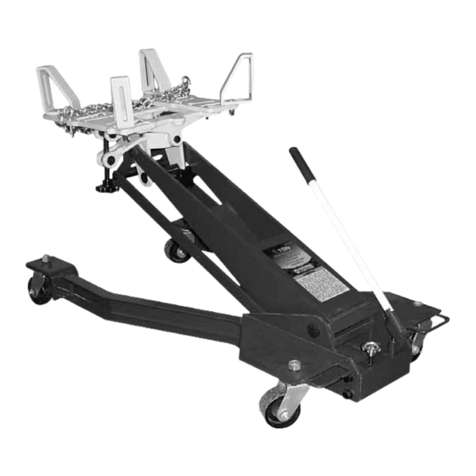
Napa
Napa 791-7170 Operating manual & parts list
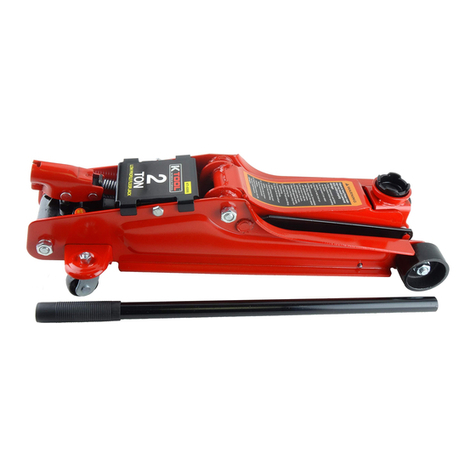
K Tool International
K Tool International KTI-63095 owner's manual

YATO
YATO YT-55600 manual
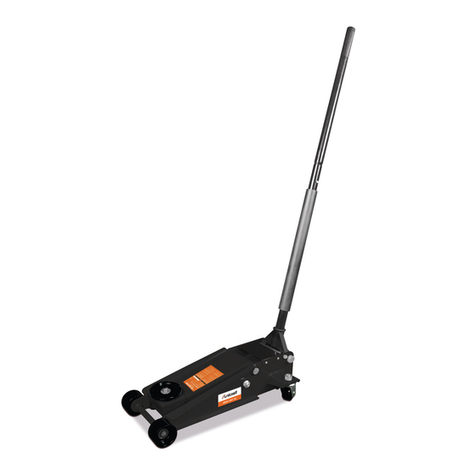
unicraft
unicraft SRWH 3001 SIL operating instructions
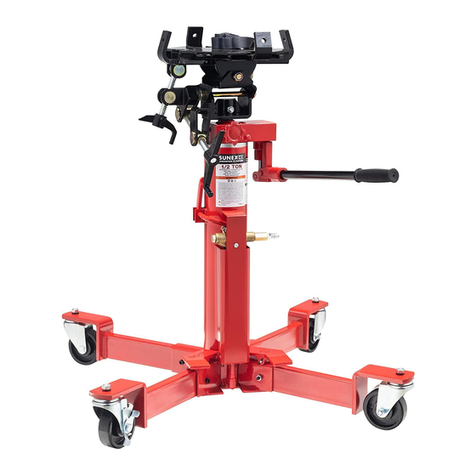
Sunex Tools
Sunex Tools 7796 owner's manual

Torin BIG RED
Torin BIG RED TH932001B owner's manual

Clarke
Clarke Strong-Arm CTJ1500QULP Operation & maintenance instructions
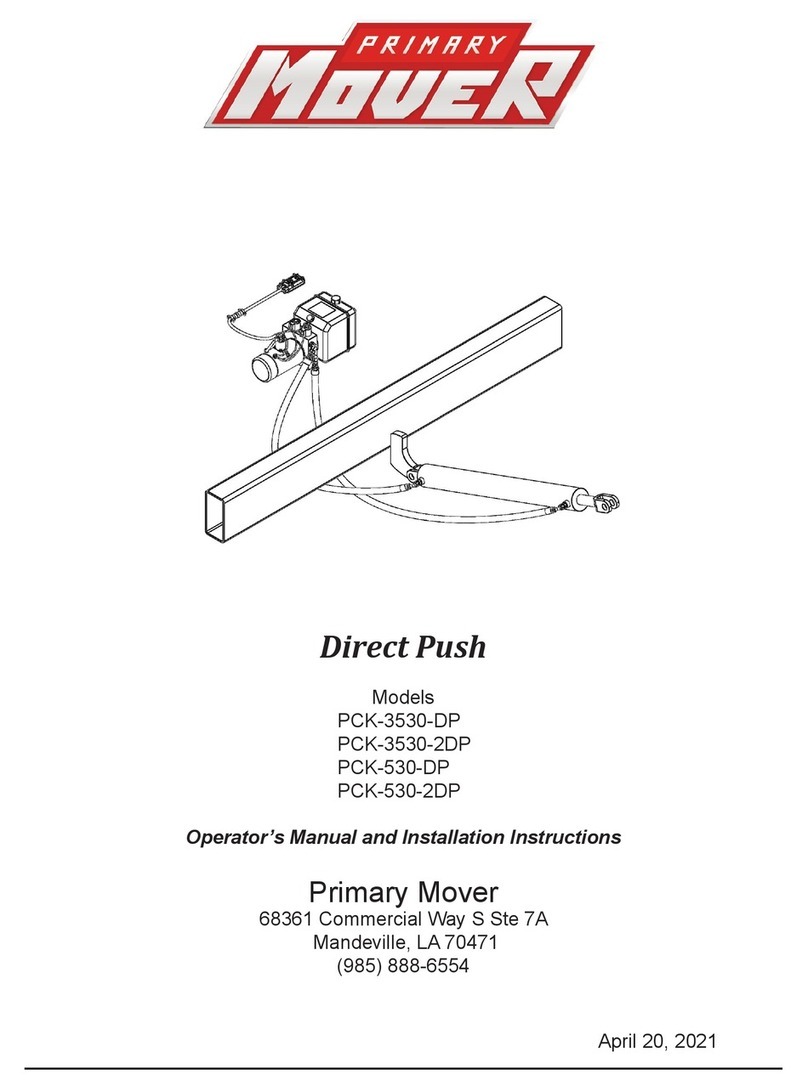
Primary Mover
Primary Mover PCK-3530-DP Operator's Manual and Installation Instructions
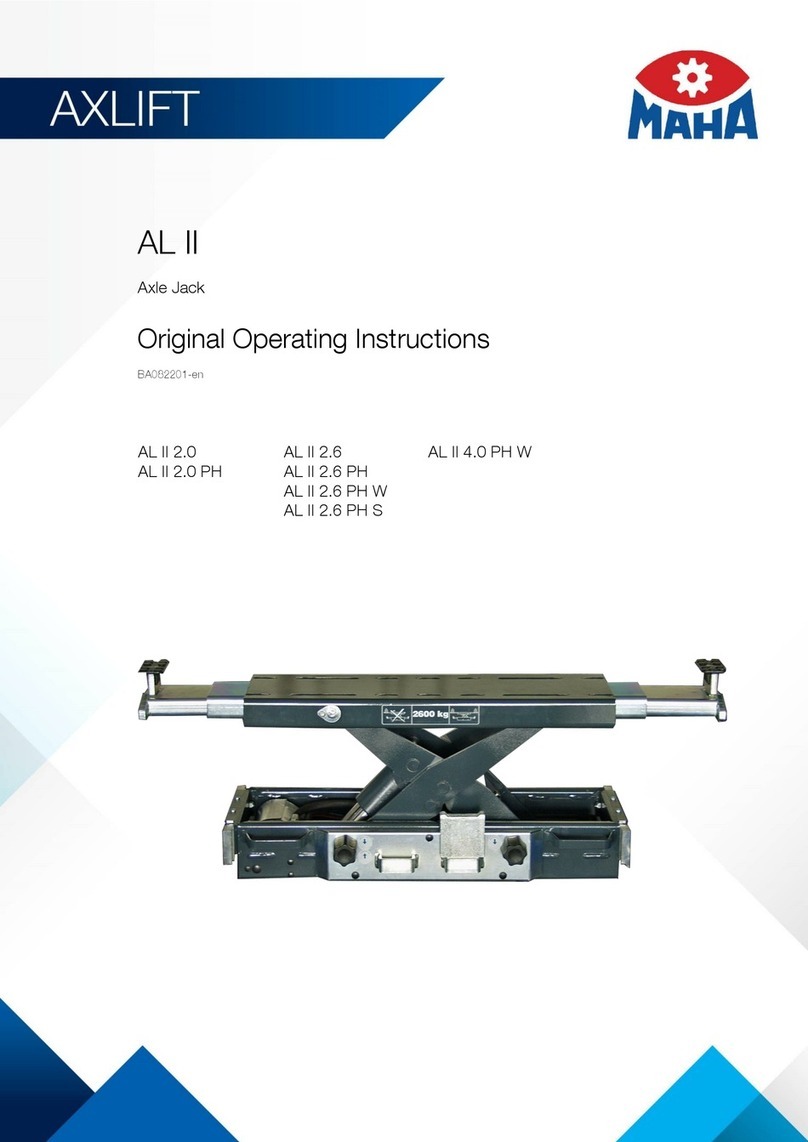
MAHA
MAHA AL II Series operating instructions
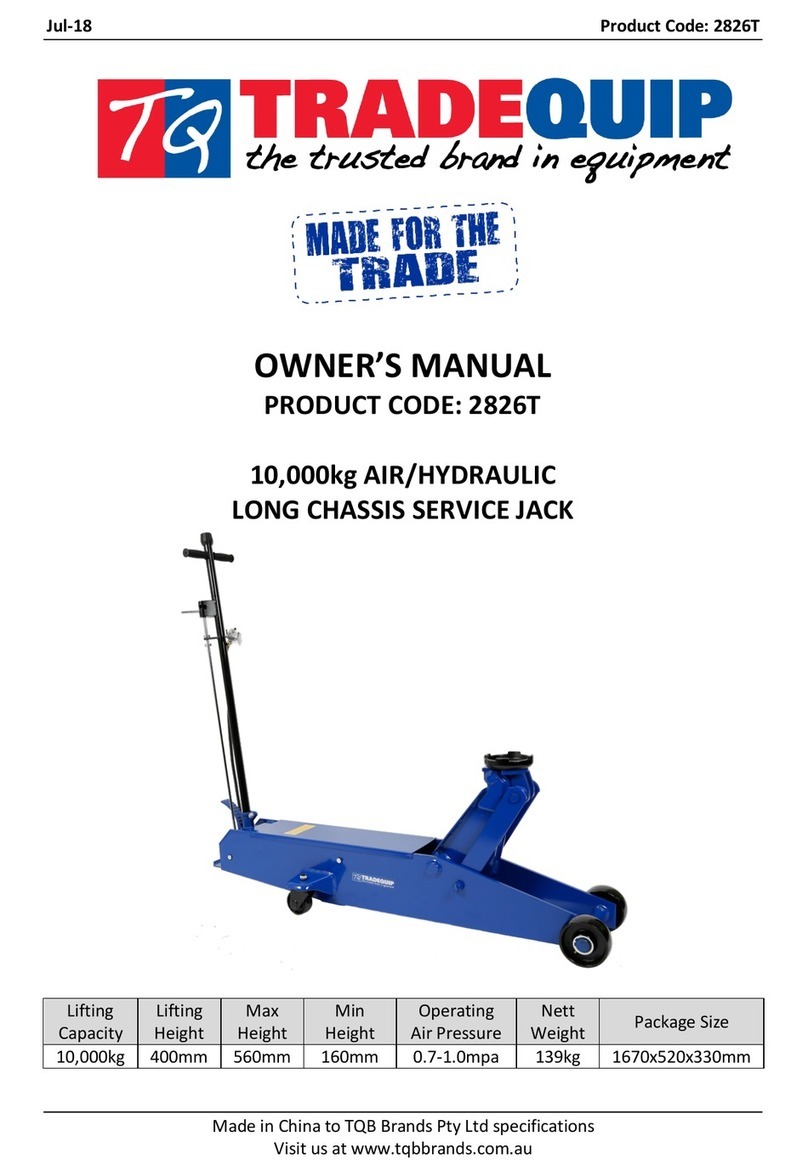
TradeQuip
TradeQuip 2826T owner's manual