Oxygen Automation HECTOR Technical document

ENGLISH
GENERAL SAFETY OBLIGATIONS
1)
WARNING!
It is important for the safety of
people to follow all instructions carefully.
Incorrect installation or incorrect use of the
product can lead to serious personal injury.
2) Read the instructions carefully before starting the
installation of the product..
3) The packaging materials must not be left within the
reach of children as a source of danger.
4) Keep the instructions.
5) This product has been designed and manufactured
exclusively for the use indicated in this documentation.
Any other use not expressly indicated could
compromise the integrity of the product and/or
represent a source of danger.
6) The manufacturer disclaims any liability arising from
misuse or use other than that for which the machine is
intended.
7) Do not install the appliance in an explosive
atmosphere: the presence of flammable gases or
fumes constitutes a serious safety hazard.
8) The mechanical construction elements must be in
accordance with the requirements of UN18612, CEN pr
EN 12604 and CEN pr EN 12605. For non-EU
countries, in addition to the national standard
references, the above standards must be followed to
obtain an adequate level of safety.
9) The manufacturer is not responsible for the non-
observance of Good Technique in the construction of
the closures to be motorized, as well as any
deformation that may occur during use.
10)The installation must be carried out in compliance
with standards UN18612, CEN pr EN 12453 and CEN
pr EN 12445. The safety level of the automation must
be C+E.
11)Before carrying out any intervention on the system,
disconnect the power supply.
12)Provide the automation power supply network with
an omnipolar switch with a contact opening distance
equal to or greater than 3mm. It is advisable to use a
6A thermomagnetic circuit breaker with omnipolar
interruption.
13)Check that there is a differential switch with 0.03A
threshold upstream of the system.
14) Check that the grounding system is correctly
installed and connect the metal parts of the lock to it.
15) The safety devices (e.g. photocells, sensitive edges,
etc.) allow to protect possible danger areas from
mechanical risks of movement, such as crushing,
conveying, shearing.
16) For each system it is essential to use at least one
light signal as well as a sign properly fixed on the frame
structure, in addition to the safety devices.
17) The manufacturer declines all responsibility for the
safety and proper functioning of the automation in the
event that non original components are used.
18) Use only original parts for maintenance.
19) Do not make any modifications to the components
of the automation system.
20) The installer must provide all information related to
the manual operation of the system in case of
emergency and provide the user of the system with the
"User Guide" enclosed with the product.
21) Do not allow children or persons to stand near the
product during operation.
22) Keep out of the reach of children radio remote
controls or any other impulse source, to prevent the
automation from being operated unintentionally.
23) The user must refrain from any attempt at repair or
direct intervention and contact qualified personnel only.
24) The passage between the leaves must take place
only when the gate is fully open.
25) Warning: Every six months, check the functioning of
the system (safety devices, actuator pushing force,
release device, etc.)
26)
Anything not expressly provided for in these
instructions is not permitted.
WARNINGS FOR THE INSTALLER

HYDRAULIC MOTOR HECTOR –HECTOR ADV
ENGLISH
Technische Daten
MODEL HECTOR
R
HECTOR
BA BC BAC
R
HECTOR ADV
BA BC
BAC
Hydraulic lock
No
yes yes ja
Open closed open-closed
No
yes
open
yes
closed
yes
open-closed
Slow travel
Hydraulic slow down (only closed)
Rodstroke
(MAX)
mm 270
mm 390
Rod linear speed
1,3 cm/sec.
Traction/ Thrust force to
15 bar
190 Kg.(1850 N)
220Kg.(224 N)
Pump flow-rate(I/m)
1
Hydraulic oil
Total 52-AT42
Operating ambient temperature
- 25° C +70° C
Protection class
IP 55
Motor weight
9 Kg.
10 Kg.
Power supply
Absorbed power
250 W
350 W
Absorbed current
1 A
1,9 A
Electric motor (rpm)
1400
Thermal protection
120°C
Capacitor
8 µF –400 V
10 µF –400 V

Always separate the connection cables for low-voltage
accessories from the 230 V power supply cables. use
separate sheats to avoid any interference..
Connect power cables hydraulic operator:
ENGLISH
These instructions apply to the following models: HECTOR und HECTOR ADV.
The models equipped with hydraulic locking (BA - BC - BAC) do not require the installation of an electric lock as they
guarantee mechanical locking of the leaf when the motor is not running.
The models without hydraulic lock (R) require the installation of electrical locks to guarantee mechanical locking of the
leaf. The Hector and Hector ADV hydraulic operators have been designed and manufactured for the automation of swing
gates.
1. DESCRIPTION AND TECHNICAL
SPECIFICATIONS
2. E
LECTRIC STANDARD DEVICES
123
MODELL DIMENSIONEN (mm)
270 Länge(A) Radstand (B)
390
1)Hydraulic operators
2)Photocells
3)
Electronic control box
5)
Receiver
6)Flashing lights
4) Key selector
7)
Electric lock
1.2 MOTOR DESCRIPTION
3. MOTOR’S INSTALLATION
3.1.
PRELIMINARY CHECKS
For a correct operation of the automation, the gate must
satisfy the following requirements:
-
robust and rigid leaf structure
-
the movement of the leaves must be regular and
uniform, and friction-free during the stroke
-
the hinges must be in very good condition
-
End-of-stroke mechanical stops positioned
Any factory work must be carried out before the
automation is installed. The condition of the gate structure
influences the reliability and safety of the automated
system.
hydraulic piston
Cylinder
force regulation valves
Pump
Power cable
Front linkage
Cover for stroke
Release kit
Rear connection
Rod end
Hub(C)
)
270
390

ENGLISH
3.2.
ACTUATOR FIXING
A)
Attach the rear linkage to the pillar following the
instructions in Tables A and B and change the length of the
attachment if necessary (Fig. 1). Compliance with the
dimensions indicated in the previous tables will ensure the
proper functioning of the automated system. In the case of
an iron pillar, carefully weld the rear attachment directly onto
the pillar. In the case of a masonry pillar, choose one of the
following solutions:
1) Insert a plate into the wall and then weld the rear
connection.
2) Fix the rear mounting plate to the abutment with screws
and dowels and then weld the rear connection to the plate
(fig. 2).
B)
Fasten the actuator to the rear connection (Fig. 2);
C)
screw the front linkage (rod end) in half on the
stem and tighten with the supplied nut (fig. 3);
D)
unlock the hydraulic actuator (Fig. 10);
E)
pull out the chrome-plated stem to full stop;
F)
Re-lock the actuator (Fig. 10);
G)
Mount the front linkage on the stem (Fig. 4);
H) Close the gate leaf and locate the position of the front
linkage on the leaf, keeping the actuator in a completely
horizontal position (Fig.4).
I) Temporarily fix the front attachment on the gate leaf with
two welding spots (protect the stem from welding slag):
L) Release the hydraulic operator, check that the gate is
free to open and stop manually on the pre-installed
mechanical limit stops; also check that the movement of the
leaf is fluid and without friction;
M) Temporarily disconnect the actuator from the coupling
and permanently weld the front connection to the sash
(Fig.5).
N) Position the cover on the actuator (Fig.7).
O) Lock the hydraulic actuator again and make the electrical
connections to the electronic devices according to the
instructions in the manual.
Dimensionen in mm.
Abb.1 TABELLE «A»
HECTOR
-
Befestigungswinkel
(*) rod stroke required to stem the hydraulic slowdown in the
closing (**) max dimensions.
TABLE «B»: 390- Fixing brackets
(*) HECTOR = 975 mm. Y HECTOR = 85mm.
NECTOR ADV 1215 mm HECTOR ADV= 110mm.
S < 0
S > 0
(*) rod stroke required to stem the hydraulic slowdown in the
closing (**) max dimensions.
If the dimensions of the pillar or the position of the hinge
(dimension D) cannot contain dimension A as desired, a
niche must be created on the pillar (Fig. 6), dimension A must
always be greater than dimension E.
OPENING
b
c(*)
TABLE «A» : 270 –Fixing brackets

Length dimension B=+ IOß mm
ENGLISH
3.3 FASTENING THE HYDRAULIC ACTUATOR WITH
OUTDOOR OPENING (Fig.8)
If the gate leaves are up to 2.3 m long, we recommend
the use of the 270 BAC (lock open / close) hydraulic
drive.
If the length of the gate leaf exceeds m. 2.3. the use of
the 270 R or 390 R (reversible) hydraulic drive is
recommended.
The fixing dimensions of the hydraulic actuator are
shown in Table C below.
When the gate is opened outwards, adjust the anti-crush
system as follows:
- Screw A = closing force control valve,
- Screw B = opening force control valve.
To decrease the tightening torque, turn the screw
counterclockwise;
To increase the torque, turn the screws clockwise.
TABLE «C»: HECTOR - Fixing brackets
OPENING
ANGLE
a
(mm)
b
(mm)
s
(mm)
d(**)
(mm)
c(**)
(mm)
90“
100
90
0
50
190
90°
110
100
O
60
210
90°
120
110
0
7O
200
90°
130
120
0
80
250
(*) rod stroke required without the hydraulic
slowdown (**) max dimensions

4.
ANTI-CRUSHING CONTROL SYSTEM
FINAL OPERATIONS –TEST
AUTOMATION
ENGLISH
5. MANUAL OPERATION AND RESET
5.1 MANUAL OPERATION
The Hector hydraulic operator is equipped with an anti-
crush safety feature that limits the force of the motor itself
in the event of an obstacle during gate movement. The
force is adjusted as follows:
- slide the release cap and lift it up,
- lift the base of the release unit;
- act on the control valves:
1) Valve "A" (valve A) to adjust the opening force
2) Valve "B" (valve B) for the regulation of the closing
force
3) Valve "C" (valve C) to unlock it completely
Turn the valve clockwise to increase torque and
counterclockwise to decrease torque.
The adjustment of torque limiters is subject to EN 12445
and EN 12453 in EU Member States.
In other states it is subject to local regulations.
4.2.
FINAL OPERATION
After adjusting the anti-crush system, follow these steps:
- Close the unlocking device
- remove the vent screw (Fig. 10).
4.3.
AUTOMATISM TEST
After installation proceed carefully with the test to
verify the functionality of the automation and all the
accessories connected with particular attention to
safety devices.
Give the "User Guide" to customer and explain the
correct use of the automated system and highlight
areas of potential danger from it.
If it is necessary to operate the gate manually in the
event of power failure or damage to the drive, the
release device must be operated as follows:
- Open the unlocking cover cap and insert
the special key provided;
- to unlock, turn the key counterclockwise;
- open or close the gate leaf manually.
5.2 AUTOMATED SYSTEM RESET
Before starting to reset the automated system after
manual unlocking, it is advisable to cut off the power
supply of the system to prevent an unintentional
impulse from operating the automated system.
The reset procedure must be carried out as follows:
- Turn the unlocking key clockwise until it locks
- close the lid of the unlocking system;
- reconnect the power supply to the automated system;
-Start the automation.
6.MAINTENANCE AND REPAIR
6.1 MAINTENANCE
A functional check of the system every six months is
recommended, with particular attention to the
efficiency of safety and release, including verification
of thrust force of the actuator; it is also good to check
the degree of functionality of the gate hinges. Also
check the oil level inside the tank.
In case of topping up with oil it is imperative to use
Total oil 52-AT42
Periodically check the correct adjustment of the
anti-crush safety (force control valves) and
the efficiency of the unlocking system.
6.2.REPAIR
Any repairs to the automatic system must be carried
out by specialised personnel only, possibly authorized.
Use original spare parts.
7.TROUBLESHOOTING
The gate won't move
mains power supply control
check that the operator is not unlocked
check force regulation valves
check oil level in the tank
check inrush capacitor efficiency
check electronic control unit functionality
The gate jerks
Close the door leaves during the
deceleration phase
Gate travel speed not constant
Check the dimensions of the opening angle
4.1 SETTING ANTI-CRUSHING SYSTEM (Fig.9)

ENGLISH
HYDRAULIC OPERATOR FOR SWING GATES
MOD. HECTOR and HECTOR ADV
Read the instructions carefully before use and keep them
for future reference.
GENERAL SAFETY RULES
The hydraulic drive guarantees a high degree of safety
when installed and used correctly. Some simple behavioural
norms can avoid random disadvantages:
- Do not pass through the doors when they are moving.
Wait for the doors to open completely before passing
through them.
- Do not stand between the doors.
- Do not stand and do not allow children, people or things to
stand close to the automation, avoiding it even more during
operation.
- Keep out of the reach of children, radio controls or any
other impulse source to prevent the automation from being
unintentionally triggered.
- Do not allow children to play with automation.
- Don't counteract the movement of the doors voluntarily.
- Do not allow branches or shrubs to interfere with the
movement of the doors.
- Keep the light signalling systems efficient and clearly
visible.
- Do not attempt to operate the doors manually until they
have been unlocked.
- In the event of a malfunction, unlock the leaves to allow
access and wait for the technical intervention of qualified
personnel.
- Once manual operation has been set up, before resuming
normal operation, disconnect the power supply to the
system.
- Do not make any modifications to the components of the
automation system.
- Refrain from any attempt at repair or direct intervention
and refer only to qualified personnel.
- Have the efficiency of the automation, safety devices and
earth connection checked at least every six months by
qualified personnel.
MANUAL OPERATION
In case it is necessary to manually operate the gate due to
power failure or automation failure,
it is necessary to temporarily open the unlocking group.
- Open the protective cap and insert the supplied key.
-
Rotate the key counterclockwise to unlock.
-
Turn the key clockwise to lock.
-
Perform the opening or closing manoeuvre on the leaf.
-
N.B.: on models without lock, the electric lock must be
released manually.
-
Normal operation must be restored by turning the
unlocking key clockwise until it stops. Close the protective
cap of the release unit.
These instructions apply to the following models:
HECTOR: WOL \ R - OL \ BA - CL \ BC - OCL \ BAC und
HECTOR ADV: WOL R - OL \
BA - CL BC - OCL BAC.
The actuator for swing gates is an hydraulic monobloc
consisting of an electric pump and an hydraulic piston that
transmits the movement to the leaf.
The models equipped with hydraulic lock do not need to
install the electric lock, ensuring the mechanical lock of the
leaf when the engine is not running.
The other models without hydraulic lock require one or
more electric locks to ensure the mechanical locking of the
leaf.
Depending on the model, leaves up to 6 m can be
automated.
The operation of the operators is managed by an
electronic control unit, enclosed in a container with an
adequate degree of protection against atmospheric
agents.
The doors are normally in the closed position.
When the electronic control unit receives an opening
command by means of the radio control or any other
impulse giver, it operates the hydraulic apparatus
obtaining the rotation of the doors, up to the opening
position that allows access.
If automatic operation has been set, the doors close
automatically after the selected pause time.
If semi-automatic operation has been set, a second
impulse must be sent to obtain reclosure.
A stop impulse (if provided) always stops the movement.
For the detailed behaviour of the automation in the
different operating logics, please refer to the installer
technician.
In the automations there are safety devices (photocells)
that prevent the movement of the doors when an obstacle
is in the area protected by them.
The actuator is fitted as standard with a hydraulic anti-
crush safety device that limits the torque transmitted to the
doors.
The light signal indicates the current movement of the
doors.
USER MANUAL

DECLARATION OF CONFORMITY FOR MACHINES
(DIRECTIVE 98/37 EEC)
Manufactured under the CE regulation and directive in ITALY and distributed in the EUROPEAN
UNION and OVERSEAS by OXYGEN AUTOMATION Sri, via Marzabotto, 40133 Bologna ITALIA
Declares that the hydraulic operator for swing gates Mod. HECTOR:
- is designed to be incorporated into machinery or assembled with other machinery in order to
constitute machinery within the meaning of Directive 98/37/EEC, as amended
- meets the essential safety requirements of the following other EU directives:
9/336 EEC and subsequent amendments 92/31 EEC;
93/68/EW73/23 EEC and subsequent amendment 93/68/EEC.
also declares that the machinery may not be put into service until the machinery into which it will be
incorporated or of which it will become a component has been identified and its conformity with the
conditions of Directive 98/37/EEC and subsequent amendments has been declared.
All rights reserved
www.oxygenautomation.com
This manual suits for next models
1
Table of contents
Popular Gate Opener manuals by other brands
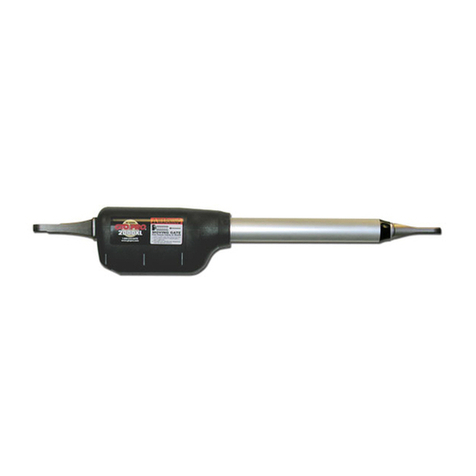
GTO
GTO SW-2000 installation manual
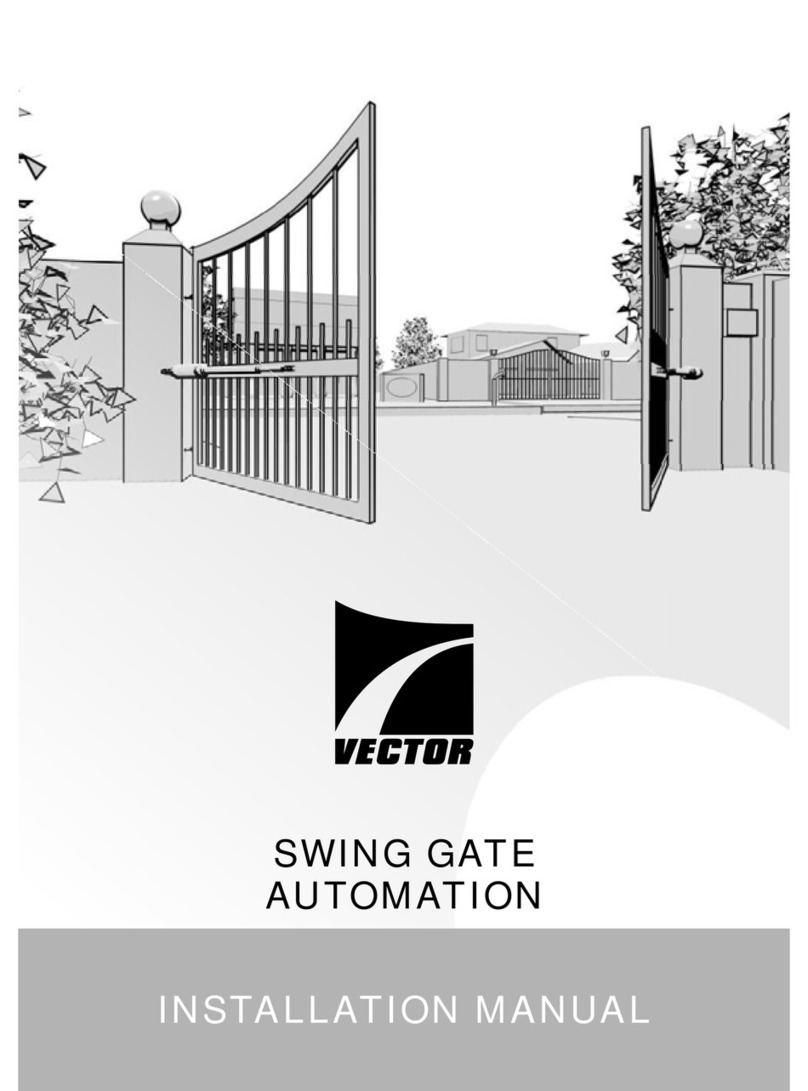
Vector
Vector V400 installation manual

Nice
Nice Slight Instructions and warnings for installation and use
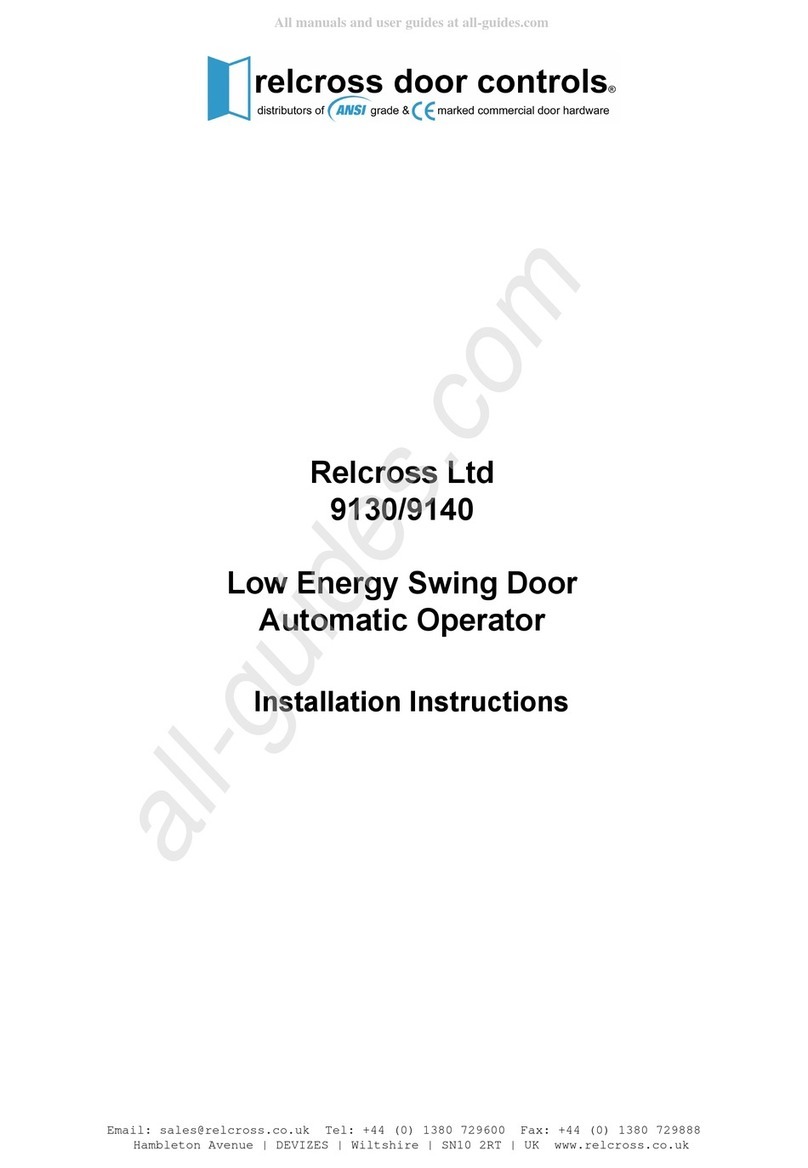
Relcross Door Controls
Relcross Door Controls 9130 installation instructions
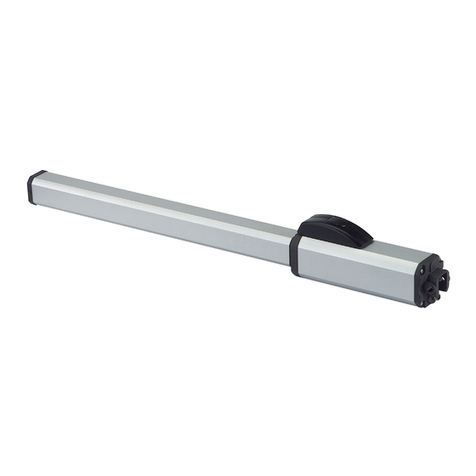
FAAC
FAAC 422 Standard user manual
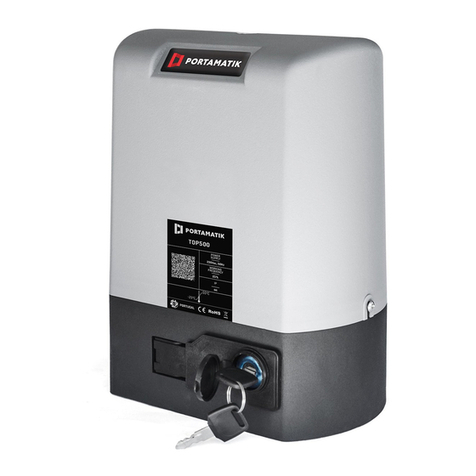
Portamatik
Portamatik TOP500 User's and installer's manual