SELTEX V350 User manual

SWING GATE OPENER
≦150kg
≦1.75m
≦150kg
≦1.75m
USER MANUAL
V350

03
03
03
04
04~07
08
09
10
11
12
13
14
15
16
16
17
17
17
17
17
18
19
20
..........................
......................................
.................................
.......................................
..........................................................
.....................................................
..............................................
.....................................................
...........................................
...........................................................
..................................................
.......................................................
.....................................
...............................
.............................................
...............................................
..........................................
.................
............................................
..............................................................
............................
.............................................
................
Important Safety Advice
Content of the Kit
Connection Diagram
Installation Guide
Actuator
Control box
AC cable wiring
Transformer
Connection PCBA
Actuator
Warning light
Photocells
Function of photocells
Opening/Closing learning
Remote learning
Remote control
Auto close function
Manual gates control on the PCBA
Clear RF memory
Reset
Setting of the Dip Switches
Specifications
Declaration of CE Conformity
2
Content

Content of the Kit
Important Safety Advice
1. Knowledge of relevant electro-technical regulations is required.
2. Training in use and maintenance of safety equipments is necessary.
3. Professional assistance is required when some mechanism adjustment is needed.
4. Always lay mains and control cables separately.
5. Test every equipment before initial operation.
6. Make familiar with the use of the system before initial operation.
3
Remote control Warning light Baery wire
x2
Control box Wire conduit
(PG11)
Connection Diagram
x2
Gate side brackets
Pillar side brackets
x2
x2
x2
Fixing bolts
Snap pins
Actuator
x2
Warning light
Control box
Photocells Photocells
Actuator Actuator

4
The maximum opening angle depends on the distance (D) between the gate hinge to the edge of the
pillar. The table below gives the opening angle according to (D)
Pillar
B
1
2
3
4
5
D
Actuator:
Installation Guide
Distance D (mm)
0 < D < 170
0 < D < 110
Angle (º)
90
100
0 < D < 60
D < 20
110
120
Distance D
(mm)
170
160
150
140
130
120
110
100
90
80
Angle max.
(º)
90
100
95
70
60
50
40
30
20
10
0
Distance B
(mm)
110
115
120
135
130
145
140
135
150
100
145
155
150
160
150
160
150
150
105
110
115
120
5
5
5
5
5
5
5
5
5
5
4 or 5
5
4
4 or 5
4
4
4
4
The bracket holes
(Gate side bracket)
INCORRECT
Pillar
hinge pin
> 170mm
CORRECT
Pillar
hinge pin
= 170mm
100mm
IMPORTANT:
If the hinge of your gate is more than 170mm from the edge of the pillar, it is necessary to adapt the
pillar to ensure the hinge is less than 170mm from the edge of the pillar, to reach a 90º opening.
Angle
Pillar
D

5
Pillar side:
Find the desired value B, according to the value D, as described in the previous table explaining the
opening angle. Make sure the pillar side bracket is placed horizontally, with the use of a spirit level, before
you drill the holes for the bracket.
Mark a line on the lower frame of your gate, as shown below, and allow a 16mm vertical distance as it’s
the height difference between the lowest part of the pillar side bracket, and the tallest part of the gate
side bracket, as shown below.
16mm
B
16mm
Use a spirit level to be sure
that the mounting bracket
can be placed horizontally.

6
1
2
3
4
5
Gate side:
Fasten the wing nut in this direction.
Make sure the gate side bracket is placed horizontally, with the use of a spirit level, before you drill the
holes for the bracket.
16mm
Use a spirit level to be sure that
the mounting bracket can be
placed horizontally.
Put the fixing bolt downwards through the hole of the actuator, and the hole of the pillar side bracket.
And use the snap pin to keep them in place.

7
bottom view
5mm
Normally the nut is at a distance of 5mm from the fully close position. You can drive the nut to this position,
in case the nut is not at the proper position.
- Move the nut with a battery. The below diagrams indicate which direction the nut moves when the motor
wires are connected directly to a 12VDC battery.
Black
Red
Red
Black

Control box:
2. Unfasten the two screws and remove the
cover.
3. Fix the control box on the wall.
※ M8 screws are suggested (not provided).
AC12V
Auto ClearRF2
J1
O / C
LED1
BAT
- +
1 2 3 4 5 6
ON
Lamp
RF1
DIP
LED O/C1 O/C2 GND ANT
-
M2
+
-
M1
+ -
Warm
+
+12VCOM
GND NC
Min. 60cm
AC12V
Auto ClearRF2
J1
O / C
LED1
BAT
- +
1 2 3 4 5 6
ON
Lamp
RF1
DIP
LED O/C1 O/C2 GND ANT
-
M2
+
-
M1
+ -
Warm
+
+12VCOM
GND NC
1. Use a screw driver to unfasten the screws
of the cover and open the control box.
8

2. AC cable goes at the left side of the control box through the wire conduit.
AC12V
Auto ClearRF2
J1
O / C
LED1
BAT
- +
1 2 3 4 5 6
ON
Lamp
RF1
DIP
LED O/C1 O/C2 GND ANT
-
M2
+
-
M1
+ -
Warm
+
+12V COM
GND NC
Connect the AC cable as shown below.
1. Mount the wire conduit at the left side of the control box.
AC12V
Auto ClearRF2
J1
O / C
LED1
BAT
- +
1 2 3 4 5 6
ON
Lamp
RF1
DIP
LED O/C1 O/C2 GND ANT
-
M2
+
-
M1
+ -
Warm
+
+12V COM
GND NC
AC cable wiring:
AC12V
Auto ClearRF2
BAT
- +
1 2 3 4 5 6
ON
RF1
DIP
3. Connect the AC plug to the power and check th if the LED on the board is ON.
9
AC12V
Auto ClearRF2
J1
O / C
LED1
BAT
- +
1 2 3 4 5 6
ON
Lamp
RF1
DIP
LED O/C1 O/C2 GND ANT
-
M2
+
-
M1
+ -
Warm
+
+12V COM
GND NC
AC12V
Auto ClearRF2
J1
O / C
LED
BAT
- +
1 2 3 4 5 6
ON
Lamp
RF1
DIP
LED O/C1 O/C2 GND ANT
-
M2
+
-M1+ -
Warm
+
+12V COM
GND NC
*If the LED is ON, remove the AC plug, and put back the cover of the transformer.

10
Use a screw driver to fasten the 4 screws of the control box.
Transformer:
AC12V
Auto ClearRF2
J1
O / C
LED1
BAT
- +
1 2 3 4 5 6
ON
Lamp
RF1
DIP
LED O/C1 O/C2 GND ANT
-
M2
+
-
M1
+ -
Warm
+
+12V COM
GND NC
Put back the cover.
Use a screw driver to fasten
the 2 screws of the cover.
AC12V
Auto ClearRF2
J1
O / C
LED1
BAT
- +
1 2 3 4 5 6
ON
Lamp
RF1
DIP
LED O/C1 O/C2 GND ANT
-
M2
+
-
M1
+ -
Warm
+
+12V COM
GND NC

J1
O / C
LED1
Lamp
LED O/C1 O/C2 GND ANT
-
M2
+
-
M1
+ -
Warm
+
+12V COM
GND NC
PCBA:
11
To transformer
(12V AC)
To backup battery
(12V DC)(Option) Dip Switches
Dual-gate operation manual button
Single-gate operation manual button
RF 2
AUTO
RF 1
Clear
For external LED display
Antenna
To external dual-gate operation
To external single-gate operation
※Remove this jumper when
photocells are connected.
※Put this jumper back if
photocells are removed.
Warning light
connection
See P.12
Motor
connection
See P.11
Photocells
connection
See P.13
- Black
+ Red
- Black
+ Red

Connect the four wires on the connector “-M2+” “-M1+”.
Actuator:
12
M1 M2
For gates that open outwards, as shown
below, connect the motor wires according to
the diagram above.
Outward opening
Inward opening
For gates that open inwards, as shown below,
connect the motor wires according to the
diagram above.
M1 M2
Motor 1 Motor 2
-
M2
+
-M1+
RedBlack Red
Black
Motor 1 Motor 2
-
M2
+
-M1+
BlackRed Black
Red

13
Warning light:
1. Open the warning light,
in this direction.
2. Remove the screws.
4. Fix the warning light on the pillar.
(screws not provided).
5. The warning light wires come out from here.
(wires not provided).
3. Connect the warning light
wires in the connector.
6. Close the warning light in this direction. 7. Connect the two wires on the connector “-Warm+”.
(wires not provided)
-
Warm
+

Photocells (optional):
See the picture on the right for installation.
14
Fix the photocells
on the pillar.
Min. 30cm
PHOTOCELL
TX
+12V GND +12V
GND COM
NC
※The short wire
connecting GND and
COM is not provided.
Connect the wires following the below diagram.
(wires not provided)
PHOTOCELL
RX
PHOTOCELL
TX
PHOTOCELL
RX
Sensor
+12V
+12VCOM
GND NC
Sensor
+12V
+12VCOM
GND NC
/ OR /
IPH6 IPH1

15
Select a proper installation site, where the transmitter and receiver can align well. Connect to the
opener’s PCBA as wiring diagram on page 13. Power on the system, try and see if it works properly by
intercepting the IR between transmitter and receiver for times. The relay in the receiver should respond
accordingly while LED switches ON and OFF.
During Opening:
When the loop of photocells is intercepted, system will:
A. ignore, if Motor 2 is activated. OR
B. half, if Motor 2 is not activated.
During Closing:
When the loop of photocells is intercepted, the system will stop closing the gate and then to open both
leaves simultaneously until the set position.
Before Opening and closing:
Both leaves of the gate won’t move until the photocells are well-aligned.
TX RX
This jumper is by default NC. Do not change at
will or the system might not function correctly.
Function of photocells:
*For IPH6, please note the following,

16
Opening / Closing learning:
Please proceed with this function before using this product; otherwise the system will drive the gates
improperly. E.g.: The gate can’t close completely or can’t open to the intended degree with some stroke
length left unused.
To activate this function, press “ Auto ” button on the PCBA until it starts the learning mode as
below:
- The system will close the gates first. Please remove any obstacles that could possibly block the gate.
Before the motors start, the warning light will blink first. Then Motor 2 will close first, and then Motor 1
will close 1 second later.
- Both M1 and M2 will take turn opening, and closing, and they will move together again, until they reach
the fully stop position.
- The warning light will stop blinking once the auto-learning finishes.
- After the learning process succeeds, the system is ready for use.
NOTE:
The Opening/Closing Learning might not be done successfully due to the over-weight of the gates. Then,
the Current Limit needs to be adjusted. Please refer to P10 of this manual. If any assistance is needed,
please contact the technicians of our agent.
Remote Learning (activation of remote control for gate operation)
To activate the remote control, please proceed with the following steps:
A. RF dual-gate learning (dual-gate operation):
- Press “RF2” key on the PCB for over 2 seconds while the PCB is on.
- You’ll see the LED light on (learning mode entered). Please press any key on the remote controls.
LED will now blink for 3 times (learning succeeds) or light is off after 10 seconds without blinking.
(learning fails, please try again the whole process).
- Please repeat Step 1 and 2 to activate another remote control; otherwise the unlearnt remote control
won’t be recognized by the system.
B. RF single-gate learning (single-gate operation):
- Proceed with “RF1” key on the PCB and another key on the remote control as Step 1~3 above.
AUTO
RF 2: Dual-gate
RF 1: Single-gate

17
Remote Control:
Each remote control has 4 keys. Choose two of them
to proceed with RF learning for gate control and
garden lamp control separately.
Operation (open, close and stop) by remote control:
The remote operation is very simple: one key press on the key will open the gate, the next press to stop,
next to close the gate, the next to stop...and so on.
When the gate is opening:
-The warning light will blink first, then Motor 1 opens, and later Motor 2 opens.
- If the gate hits something, motor will reverse a little with the warning light blinking until the next com
mand received.
When the gate is closing:
- The warning light will blink first, then Motor 2 closes, and later Motor 1 closes.
- If the gate hits something, motors will reverse for 3 seconds with the warning light blinking until the next
command received.
Auto close function:
30 seconds or 60 seconds later (only when this function is enabled, depending on your setting of key 1
of dip switch), the warning light will blink first, then Motor 2 closes, 4 seconds later Motor 1 closes. When
the process finishes, the warning light will be switched off.
Manual gates control on the PCBA:
- The operation is the same as using remote, one key press will open the gate, next to close the gate,
next to stop...and so on.
- Optional remote controls or external wall button is available.
(Connected to O/C & GND terminals)
Clear RF memory:
Press “ Clear ” key on the PCBA for over 2 seconds while the PCB is on.
You’ll see the LED blinking 5 times then the RF memory will be cleared.
Reset:
Press “ Clear ” key on the PCB and input AC power; keep pressing “ Clear ” key for over 2 seconds. You’ll
see the LED blink for 2 seconds and light on for 3 seconds then light off. Once the mentioned actions are
carried out, all RF data willl be cleared.
Dual-gate operation manual button
Single-gate operation manual button
RF 2: Dual-gate
AUTO
RF 1: Single-gate
Clear

18
Second highest current limit.
Minimum current limit.
Maximum current limit (means also the worst sensibility, which
could shorten the life of motor, please try lower current limit first)
Approx. current limit values for different dip switch setting:
Current limit
Auto-Close
Auto-Close timer
Gate Type
ON
1 2 3 4 5 6
DIP
ON
1 2 3 4 5 6
DIP
ON
1 2 3 4 5 6
DIP
ON
1 2 3 4 5 6
DIP
The default setting of dip switches:
Setting of the Dip Switches:
2.7A
Switch 5
4.0A
Switch 6
1.4A
Switch 4
1Auto-Close Yes No
2Auto-Close timer 60 Sec 30 Sec
3Gate Type Heavy Gate
4 ~ 6 Current Limit Selected Unselected
Light Gate
Key No. Function ON OFF
*Do not change the setting of Gate Type unless you have problem finishing the auto-learning process.

Specifications
Model
Input voltage
Power consumption
Duty cycle
Macimum gate weight
Macimum gate width
Speed
V350
12V DC
1.0 ~ 2.5A
150Kg Max. x 2
1.75M x 2
15.2mm/sec (no load)
Overload protection
Protection
Strock length
Current detection
IP44
379mm
20%
Actuator:
Model
Input
Output
Dimension
RF Remote
Recharging function
Approx. weight
GCG1-SWD2
110 / 230V AC ; 60 / 50Hz
12V DC / 72W Max.
433.92MHz w / Rolling code
Built-in (12V DC battery is optional)
2.6Kgs
220(L) x 240(W) x 90(H) mm
Control box:
19

Declaration of CE Conformity
20
The purchased gate opener kit “V350” is compliant with the following regulations, in terms of
the essential conformity requirements of the R&TTE directives of 2014/53/EU and related directives,
- EN301489-1 V1.9.2, 2011
- EN301489-3 V1.6.1, 2013
- EN300220-1 V2.4.1, 2012
- EN300220-2 V2.4.1, 2012
also based on the essential conformity requirements of EMC Directive of 2014/30/EU.
- EN55014-1: 2006 + A1: 2009 + A2: 2011
- EN55014-2: 1997 + A1: 2001 + A2: 2008
- EN61000-3-2: 2006 + A1: 2009 + A2: 2009 Class A
- EN61000-3-3: 2013
and in terms of the provisions of the relevant specific standards and the Directive 2014/35/EU.
- EN60335-1, 2012
- EN60335-2-103, 2003 + A11: 2009
- EN60950-1:2006+A11:2009+A1:2010+A12:2006+A2:2013
This manual suits for next models
1
Table of contents
Popular Gate Opener manuals by other brands
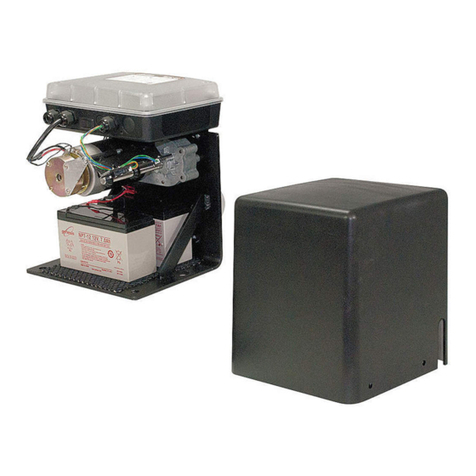
GTO
GTO GPX-SL25 installation manual
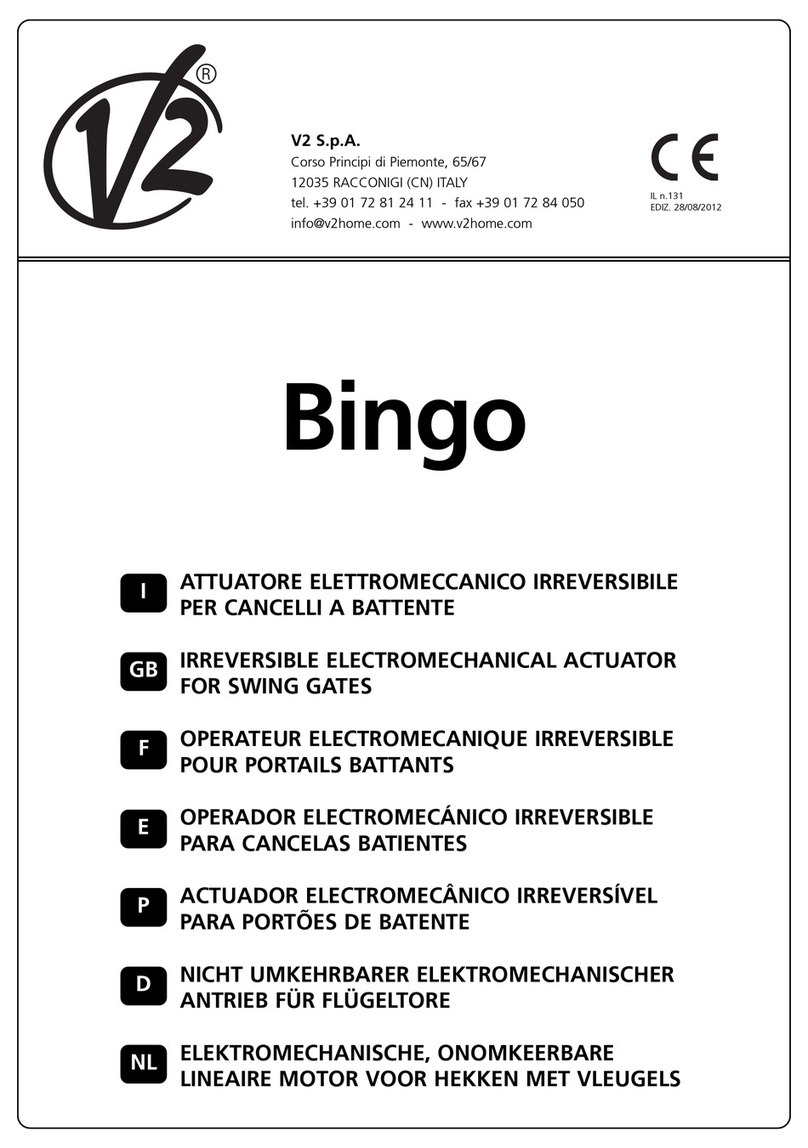
V2
V2 Bingo manual
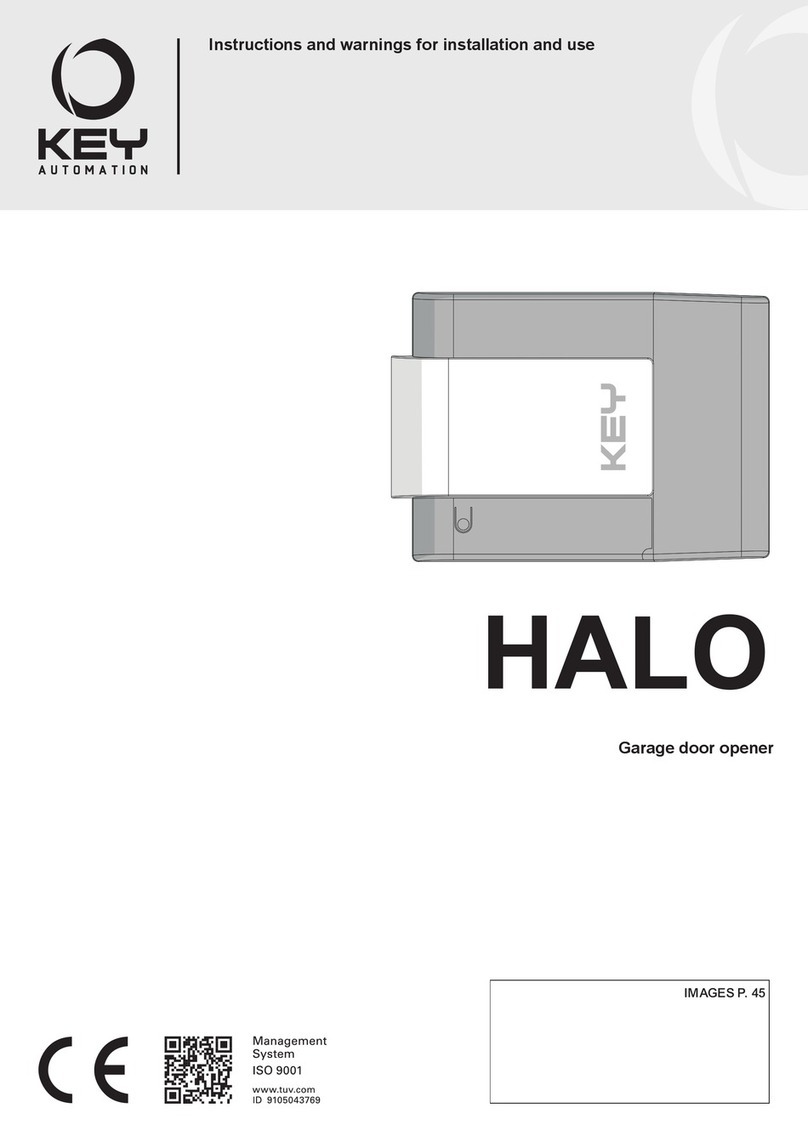
Keyautomation
Keyautomation HALO Instructions and warnings for installation and use
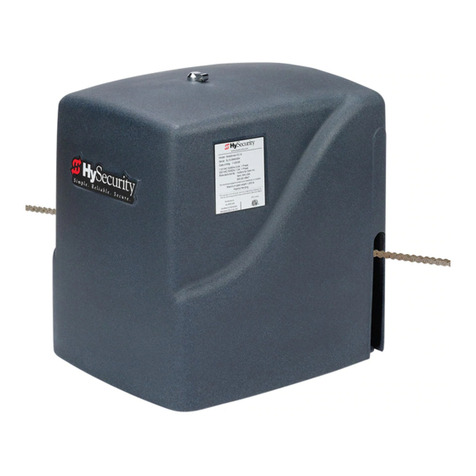
HySecurity
HySecurity SlideSmart DC 15 Installation and maintenance manual
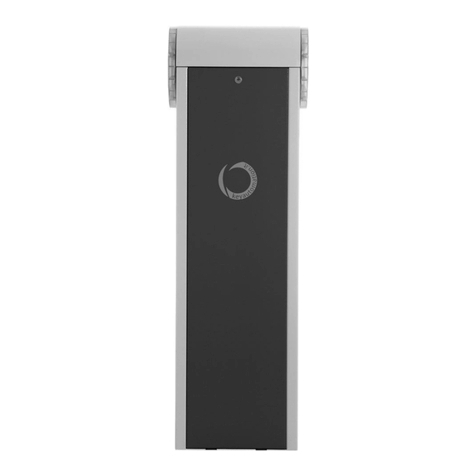
Keyautomation
Keyautomation BOOM GATE Instructions and warnings for installation and use
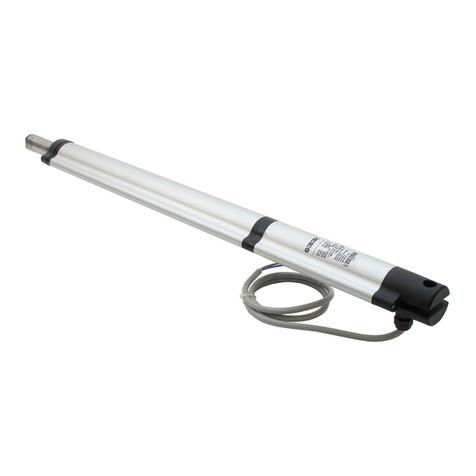
GiBiDi
GiBiDi MODO12 Instructions for installations
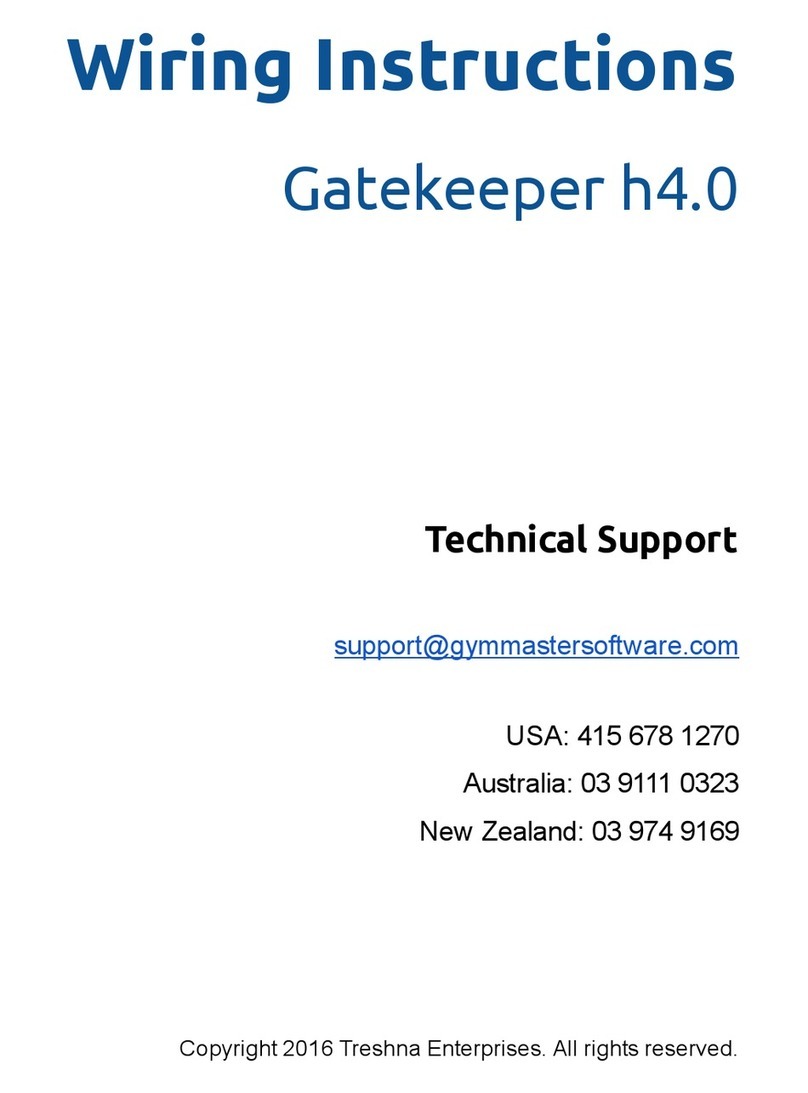
Gym Master
Gym Master Gatekeeper h4.0 Wiring instructions
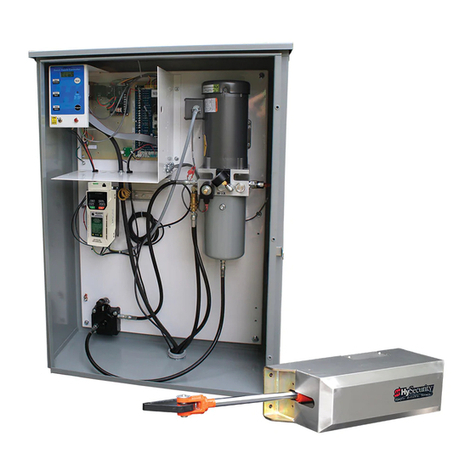
HySecurity
HySecurity HydraSwing 40 Programming and operations manual
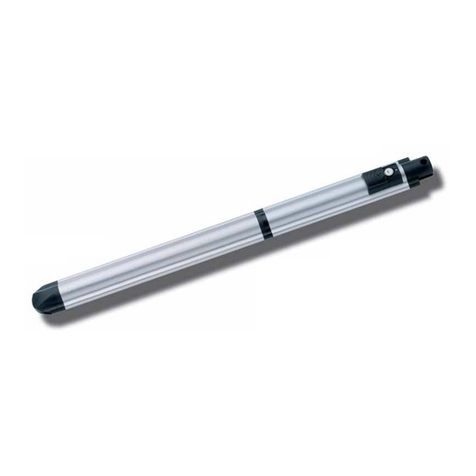
GiBiDi
GiBiDi MEKA BL 12 Instructions for installation
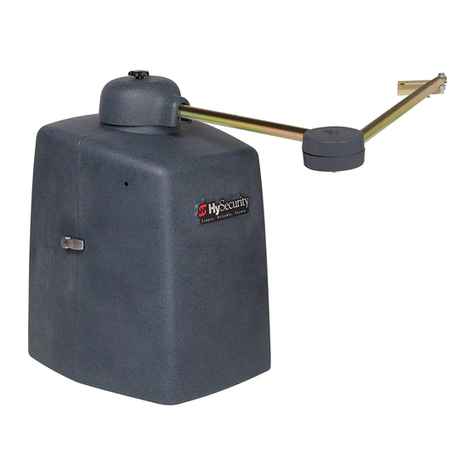
HySecurity
HySecurity SwingSmart DC 20 Installation and maintenance manual
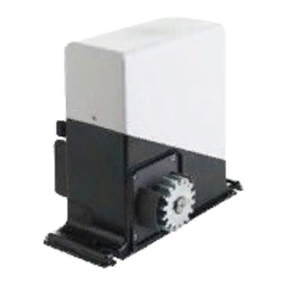
GiBiDi
GiBiDi Pass 4 Plus Instructions for installation
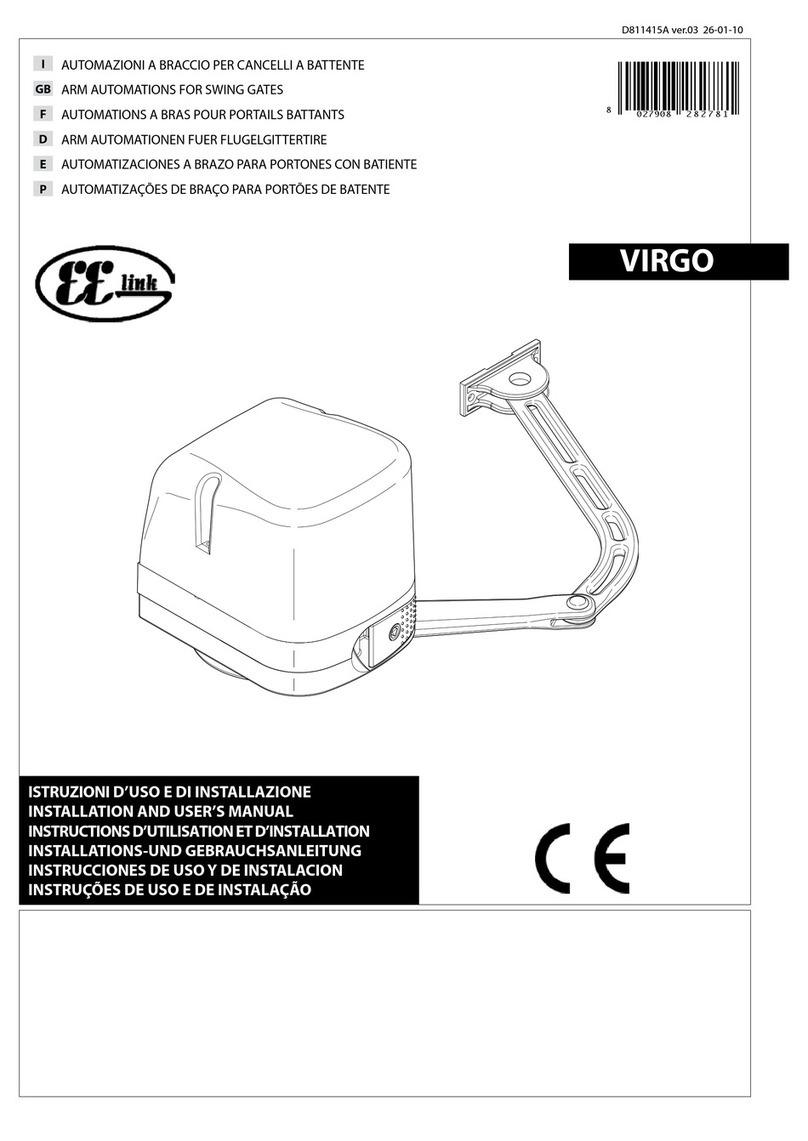
Eelink
Eelink Virgo Installation and user manual