Parker IQAN-LC6-X05 User manual

IQAN-LC6-X05
Instruction book
Publ no HY33-8409-IB/UK
Edition 2015-03-12

ii
Contents
Instruction book, IQAN-LC6-X05
Contents
1 Introduction . . . . . . . . . . . . . . . . . . . . . . . . . . . . . . . . . . . . . . . . . . . . . . . . . . . . 1
Safety symbols . . . . . . . . . . . . . . . . . . . . . . . . . . . . . . . . . . . . . . . . . . . . . . . . 1
2 Precautions . . . . . . . . . . . . . . . . . . . . . . . . . . . . . . . . . . . . . . . . . . . . . . . . . . . . 2
General safety regulations . . . . . . . . . . . . . . . . . . . . . . . . . . . . . . . . . . . . . . . 2
Construction regulations . . . . . . . . . . . . . . . . . . . . . . . . . . . . . . . . . . . . . 2
Safety during installation . . . . . . . . . . . . . . . . . . . . . . . . . . . . . . . . . . . . . 2
Safety during start-up . . . . . . . . . . . . . . . . . . . . . . . . . . . . . . . . . . . . . . . 3
Safety during maintenance and fault diagnosis . . . . . . . . . . . . . . . . . . . 3
3 Product description . . . . . . . . . . . . . . . . . . . . . . . . . . . . . . . . . . . . . . . . . . . . . 4
IQAN-LC6-X05 . . . . . . . . . . . . . . . . . . . . . . . . . . . . . . . . . . . . . . . . . . . . . . . . 4
The control lever's parts . . . . . . . . . . . . . . . . . . . . . . . . . . . . . . . . . . . . . 4
The IQAN-LC6-X05 control signals . . . . . . . . . . . . . . . . . . . . . . . . . . . . . 5
I/O overview, base . . . . . . . . . . . . . . . . . . . . . . . . . . . . . . . . . . . . . . . . . . . . . 5
H1-handle . . . . . . . . . . . . . . . . . . . . . . . . . . . . . . . . . . . . . . . . . . . . . . . . . . . . 6
The handle's parts . . . . . . . . . . . . . . . . . . . . . . . . . . . . . . . . . . . . . . . . . . 6
I/O overview, H1 handle . . . . . . . . . . . . . . . . . . . . . . . . . . . . . . . . . . . . . . . . . 7
Outputs . . . . . . . . . . . . . . . . . . . . . . . . . . . . . . . . . . . . . . . . . . . . . . . . . . 7
4 Safety . . . . . . . . . . . . . . . . . . . . . . . . . . . . . . . . . . . . . . . . . . . . . . . . . . . . . . . . . 8
IQAN-LC6-X05 . . . . . . . . . . . . . . . . . . . . . . . . . . . . . . . . . . . . . . . . . . . . . . . . 8
Primary and secondary signals . . . . . . . . . . . . . . . . . . . . . . . . . . . . . . . . 8
Use of limited signal range . . . . . . . . . . . . . . . . . . . . . . . . . . . . . . . . . . . 8
5 Mounting . . . . . . . . . . . . . . . . . . . . . . . . . . . . . . . . . . . . . . . . . . . . . . . . . . . . . . 9
Mounting the unit . . . . . . . . . . . . . . . . . . . . . . . . . . . . . . . . . . . . . . . . . . . . . . 9
Mounting considerations . . . . . . . . . . . . . . . . . . . . . . . . . . . . . . . . . . . . . 9
Mounting methods . . . . . . . . . . . . . . . . . . . . . . . . . . . . . . . . . . . . . . . . . 10
6 Installation . . . . . . . . . . . . . . . . . . . . . . . . . . . . . . . . . . . . . . . . . . . . . . . . . . . . 11
IQAN-LC6-X05 Base connector . . . . . . . . . . . . . . . . . . . . . . . . . . . . . . . . . . 11
Base connector pin assignments . . . . . . . . . . . . . . . . . . . . . . . . . . . . . 11
IQAN-LC6-X05 Handle connector . . . . . . . . . . . . . . . . . . . . . . . . . . . . . . . . 12
H1-Handle connector pin assignments . . . . . . . . . . . . . . . . . . . . . . . . . 12
Supply voltage . . . . . . . . . . . . . . . . . . . . . . . . . . . . . . . . . . . . . . . . . . . . . . . 13
Emergency stop . . . . . . . . . . . . . . . . . . . . . . . . . . . . . . . . . . . . . . . . . . 13
Connecting of supply voltage, IQAN module . . . . . . . . . . . . . . . . . . . . 13
Output signals . . . . . . . . . . . . . . . . . . . . . . . . . . . . . . . . . . . . . . . . . . . . . . . 14
Primary and secondary outputs . . . . . . . . . . . . . . . . . . . . . . . . . . . . . . 14
Connecting of IQAN-LC6-X05 base outputs . . . . . . . . . . . . . . . . . . . . . 14
Connecting of -H1 handle outputs . . . . . . . . . . . . . . . . . . . . . . . . . . . . . 15
LC6-H1 handle loss of ground . . . . . . . . . . . . . . . . . . . . . . . . . . . . . . . 15
Handle considerations . . . . . . . . . . . . . . . . . . . . . . . . . . . . . . . . . . . . . . . . . 16
Recommended handle specification . . . . . . . . . . . . . . . . . . . . . . . . . . . 16
Environmental specification . . . . . . . . . . . . . . . . . . . . . . . . . . . . . . . . . 16
Appendix A . . . . . . . . . . . . . . . . . . . . . . . . . . . . . . . . . . . . . . . . . . . . . . . . . . . 17
IQAN-LC6-X05 Technical Overview . . . . . . . . . . . . . . . . . . . . . . . . . . . . . . . 17
IQAN-LC6-X05, base and -H1 handle . . . . . . . . . . . . . . . . . . . . . . . . . . 17
Appendix B . . . . . . . . . . . . . . . . . . . . . . . . . . . . . . . . . . . . . . . . . . . . . . . . . . . 20
Dimensioning of the IQAN-LC6-X05 . . . . . . . . . . . . . . . . . . . . . . . . . . . . . . 20

1
Safety symbols
1 Introduction
Instruction book, IQAN- LC6-X05
1Introduction
These instructions are to be used as a reference tool for the vehicle manufacturer’s
design, production, and service personnel.
The user of these instructions should have basic knowledge in the handling of
electronic equipment.
Safety symbols
Sections regarding safety, marked with a symbol in the left margin, must be read and
understood by everyone using the system, carrying out service work or making changes
to hardware and software.
The different safety levels used in this manual are defined below.
WARNING
Sections labeled WARNING with a caution symbol in the left margin, indicate that a
hazardous situation exists. If precautions are not taken, this could result in death, injury,
or property damage.
NOTICE
Sections labeled NOTICE with a notice symbol in the left margin, indicate there is
important information about the product. Ignoring this could result in less than optimal
performance, or damage to the product.
Contact the manufacturer if there is anything you are not sure about or if you have any
questions regarding the product and its handling or maintenance.
The term "manufacturer" refers to Parker Hannifin Corporation.

2
General safety regulations
2 Precautions
Instruction book, IQAN- LC6-X05
2 Precautions
General safety regulations
Work on the hydraulics control electronics may only be carried out by trained
personnel who are well-acquainted with the control system, the machine and its safety
regulations.
WARNING
Mounting, modification, repair and maintenance must be carried out in accordance
with the manufacturer's regulations. The manufacturer has no responsibility for any
accidents caused by incorrectly mounted or incorrectly maintained equipment. The
manufacturer does not assume any responsibility for the system being incorrectly
applied, or the system being programmed in a manner that jeopardizes safety.
WARNING
Damaged product may not be used. If the control system shows error functions or if
electronic modules, cabling or connectors are damaged, the system shall not be used.
WARNING
Electronic control systems in an inappropriate installation and in combination with
strong electromagnetic interference fields can, in extreme cases, cause an unintentional
change of speed of the output function.
NOTICE
As much as possible of the welding work on the chassis should be done before the
installation of the system. If welding has to be done afterwards, the electrical
connections on the system must be disconnected from other equipment. The negative
cable must always be disconnected from the battery before disconnecting the positive
cable. The ground wire of the welder shall be positioned as close as possible to the
place of the welding. The cables on the welding unit shall never be placed near the
electrical wires of the control system.
Construction regulations
WARNING
The vehicle must be equipped with an emergency stop which disconnects the supply
voltage to the control system's electrical units. The emergency stop must be easily
accessible to the operator. The machine must be built if possible, so that the supply
voltage to the control system's electrical units is disconnected when the operator leaves
the operator’s station.
Safety during installation
WARNING
Incorrectly positioned or mounted cabling can be influenced by radio signals which can
interfere with the functions of the system.

3
General safety regulations
2 Precautions
Instruction book, IQAN- LC6-X05
Safety during start-up
WARNING
The machine's engine must not be started before the control system is mounted and its
electrical functions have been verified.
Ensure that no one is in front, behind or nearby the machine when first starting up the
machine.
Follow the instructions for function control in the Start-up section.
Safety during maintenance and fault diagnosis
WARNING
Ensure that the following requirements are fulfilled before any work is carried out on
the hydraulics control electronics.
• The machine cannot start moving.
• Functions are positioned safely.
• The machine is turned off.
• The hydraulic system is relieved from any pressure.
• Supply voltage to the control electronics is disconnected.

4
IQAN-LC6-X05
3 Product description
Instruction book, IQAN- LC6-X05
3 Product description
IQAN-LC6-X05
The IQAN-LC6-X05 is a mini-coordinate joystick that incorporates ergonomic design
with ruggedness, functionality, light weight and high flexibility for mobile market
applications. The unit is designed for withstand aggressive conditions in different type
of mobile equipment. The LC6 has a compact ergonomic design and small dimensions
make it ideal for armrest and panel mounting. The designation -X05 (X crossed
outputs, 0- 5Vdc) represents the analog output signals. The joystick has one primary
and one secondary output per axis in the 0-5V range
.
The IQAN-LC6-X05 parts.
The control lever's parts
Control lever -LC6-X05 consists of:
1 U0-handle.
2 Bellows.
3 Mounting flange.
4 Lower enclosure.
5 Connector C1 for supply voltage, primary and secondary analog outputs
NOTICE
In order to increase the safety of the LC6-X05, the primary (10%-90% VS) and
secondary (90%-10% VS) analog outputs can be compared e.g. to verify center
position. See safety chapter for more information.
1
2
3
4
5

5
I/O overview, base
3 Product description
Instruction book, IQAN- LC6-X05
The IQAN-LC6-X05 control signals
The IQAN-LC6 is used to control the object in four directions:
• the lever is moved to the right/left, direction X +/-.
• the lever is moved forward/back, direction Y +/-.
• handle option -H1R1, the rocker is moved up/down, direction Z1 +/-.
• handle option -H1R1K1, the ring is moved right/left, direction Z2 +/-.
The control signal is proportional to the lever's working range.
The control signal is transferred from the IQAN-LC6-X05 via a cable to the valve
driver electronics, an expansion module, or IQAN master unit.
IQAN-LC6-X05 in a typical system
I/O overview, base
Outputs
The IQAN-LC6-X05 joystick base has four (4) analog outputs for use as command
signals.
IQAN-LC6-X05 outputs per axis.
(2) Primary analog outputs VOUT-XA and VOUT-YA, 10% - 90% Vs
(2) Secondary analog outputs VOUT-XB and VOUT-YB, 90% - 10% Vs
CAN
Local I/O
IQAN-MD4 Expansion units IQAN-LC6-X05 joysticks
VOUT-YB
VOUT-XB
VOUT-XA
VOUT-YA
LC6-X05
GROUND
POWER +5Vdc
GROUND
POWER +5Vdc
Vdc
out
90% Vs
50% Vs
10% Vs
-100% 100%
Neutral
position
Output A
Output B
Deflection

6
H1-handle
3 Product description
Instruction book, IQAN- LC6-X05
H1-handle
The IQAN-LC6-X05 is designed to be used with the ergonomic (H1) handle. The H1
handle has a connector C2 that is separate from the base connector.
The ergonomic handle has a 3rd proportional function rocker and a unique, patent
pending, rotary knob function that adds a fourth proportional function integrated in the
handle. The design gives the user a benefit to control all joystick proportional functions
without changing their grip on the handle, and makes the LC6 ideal for repetitive,
precise motion control during extended periods in mobile applications.
To extend operating life the housing of both handle and base is made of a corrosive-free
material, and is specially adapted for moisture drainage to protect the the system
electronics. The H1 handle uses a bellow that can be quickly changed without
removing the handle to simplify field replacement. The cable between base and handle
is routed directly through the base plate, eliminating the risk of damage and simplifying
field service, while the use of a single circuit board and Hall effect sensors minimise
the number of components and moving parts.
WARNING
If handle is disassembled there is a risk of pinching the cables when the handle is
reassembled.
The IQAN-LC6-X05 H1 handle parts.
The handle's parts
H1 handle consists of:
1 Handle, -H1-R1K1 shown, (other configurations are possible).
2 Proportional rocker, (-H1 handle rocker has primary and secondary outputs).
3 Proportional knob (-H1 handle knob has primary and secondary outputs).
4 Connector C2 for supply voltage, primary and secondary analog outputs
12
3
4

7
I/O overview, H1 handle
3 Product description
Instruction book, IQAN- LC6-X05
I/O overview, H1 handle
Outputs
Analog
The IQAN-LC6-X05 H1handle has two(2) or four (4) analog outputs from knob and/or
rocker, for use as command signals.
H1 handle outputs per Z axis.
(2) Primary analog outputs VOUT-Z1P and VOUT-Z2P, 10%-90% Vs
(2) Secondary analog outputs VOUT-Z1S and VOUT-Z2S, 90% - 10% Vs
VOUT-Z2S
VOUT-Z1S
VOUT-Z1P
VOUT-Z2P
H1
GROUND
POWER +5Vdc
Vdc
out
90% Vs
50% Vs
10% Vs
-100% 100%
Neutral
position
Output A
Output B
Deflection

8
IQAN-LC6-X05
4 Safety
Instruction book, IQAN- LC6-X05
4Safety
IQAN-LC6-X05
Primary and secondary signals
The IQAN-LC6-X05 has two signals outputs for each axis. The signals are antivalent,
meaning that the secondary output when correct will be the "mirror image" of the
primary signal.It is recommended to compare the signals in the controller to detect fault
and protect against unwanted movement.
Use of limited signal range
The analog outputs of the IQAN-LC6-X05 use limited signal range to provide an
additional method for error detection. The operating signal range for primary and
secondary outputs are 10%-90% Vs and 90%-10% Vs respectively. Vs (power supply)
is 5Vdc. This allows the controller to detect if a wire is pulled loose or making contact
with a powered wire. Detecting wiring faults can protect against unintended movement.
WARNING
Risk of injury! Do not use in areas with high magnetic fields.
The IQAN-LC6-X05 is based on hall effect sensors. The LC6 is designed with
magnetic deflection to reduce the influence of external magnetic fields, but exposure to
high external magnetic fields may lead to unwanted activation of the output signals.
For maximum allowed external magnetic field, see Appendix A, on page 17.

9
Mounting the unit
5 Mounting
Instruction book, IQAN- LC6-X05
5 Mounting
Mounting the unit
NOTICE
The IQAN-LC6-X05 unit should be mounted according to the following instructions.
Mounting considerations
• The control lever must be built in so that it is protected against direct pressurized
liquid spray (above flange) and excessive mechanical forces.
• The machine manufacturer must consider the need of a protective catch, or similar,
to prevent unintentional working of the lever.
NOTICE
Take careful consideration when positioning the unit.
• Mount the unit so that it is not exposed to external heat, e.g. from the engine or
heater.
• Mount the unit so there is no risk that the harness can be folded, crushed, worn or
damaged in any way.
• Locate the harness so there is no pressure on the connector.
• Use ergonomics. The control lever should be mounted at a height so that there is no
pressure on the driver's arm and shoulders. IQAN-LC6 should be mounted at an
angle so that the driver's wrist is held normally. The IQAN-LC6-X05 and a well
designed handle, such as the H1, combined with moveable arm rests, can provide
good ergonomics.
Ergonomic positioning of joystick
• The control lever IQAN-LC6-X05 with 3rd axis is intended to be positioned so that
the rocker is manoeuvered with the thumb.
Actuating proportional rocker with thumb.
15

10
Mounting the unit
5 Mounting
Instruction book, IQAN- LC6-X05
Mounting methods
• Control lever IQAN-LC6-X05 must only be mounted using screws through the
flange.
Mounting the IQAN-LC6-X05 with screws.
Mounting hole dimentions for the IQAN-LC6-X05.

11
IQAN-LC6-X05 Base connector
6 Installation
Instruction book, IQAN- LC6-X05
6 Installation
IQAN-LC6-X05 Base connector
a.Kit contains parts for both connectors, C1 and C2
Base connector pin assignments
Connector kit Parker no. 20077764ª C1
Housing Molex no. 43020-0801
Pin type Molex no. 43031-0008
Recommended cable 0.50 mm2 (20 AWG)
Crimping tool Molex no. 63819-0000 or
Molex no. 64016-0201
Prototype cable Parker no. 20077763ª
Symbol Pin No. Function
Power 5 X sensor power supply Vs, +5Vdc
GND 1 X sensor power supply ground , 0Vdc
Power 7 Y sensor power supply Vs, +5Vdc
GND 3 Y sensor power supply ground , 0Vdc
VOUT-XA 2 X primary signal
VOUT-XB 6 X secondary signal
VOUT-YA 4 Y primary signal
VOUT-YB 8 Y secondary signal
VOUT-YB
VOUT-XB
VOUT-XA
VOUT-YA
LC6-X05
GROUND
POWER +5Vdc
GROUND
POWER +5Vdc

12
IQAN-LC6-X05 Handle connector
6 Installation
Instruction book, IQAN- LC6-X05
IQAN-LC6-X05 Handle connector
a.Kit contains parts for both connectors, C1 and C2
H1-Handle connector pin assignments
Connector kit Parker no. 20077764ª C2
Housing Molex no. 43020-0601
Pin type Molex no. 43031-0008
Recommended cable 0.50 mm2 (20 AWG)
Supplied on handle types H1-R1K0, H1-R1K1
Prototype cable Parker no. 20077763ª
Symbol
H1-R1K0
Pin No.
H1-R1K1
Pin No.
Power 4 4
GND 1 1
VOUT-Z1P 2 2
VOUT-Z1S 5 5
VOUT-Z2P 3
VOUT-Z2S 6
VOUT-Z2S
VOUT-Z1S
VOUT-Z1P
VOUT-Z2P
H1
GROUND
POWER +5Vdc

13
Supply voltage
6 Installation
Instruction book, IQAN- LC6-X05
Supply voltage
WARNING
Before any installation of an IQAN system can take place, make sure the ignition lock
is turned off and the battery is disconnected.
Emergency stop
Make sure an Emergency Stop disconnecting the system power supply, is easily
accessible at any time. The IQAN module and standalone controller instruction books
show how to connect an emergency stop.
Connecting of supply voltage, IQAN module
The supply voltage, should be within the operating range, see Appendix A, on page 17.
Connect the supply voltage to POWER +5Vdc, pin C1:5, C1:7 and C2:4. The regulated
5Vdc is supplied from an IQAN module’s +VREF. The ground connection is made
from GND pin C1:1, C1:3 and C2:1 to the IQAN module’s -VREF.
NOTICE
Maximum load for the VREF position is different between types of IQAN modules.
Refer to the appropriate instruction book.
NOTICE
Do not exceed power supply limits for the joystick base and handle!
Reversed polarity, or supply voltage different from recommended operating conditions
will seriously damage the unit, see Appendix A, on page 17.
EXAMPLE
Connecting an IQAN-LC6-X05 to IQAN module.
+5 Vdc
GND
IQAN module +VREF
-VREF LC6-X05

14
Output signals
6 Installation
Instruction book, IQAN- LC6-X05
Output signals
Primary and secondary outputs
The IQAN-LC6-X05 has two sensors for each axis that have thier output signals
mirrored. The two outputs allow the user to set up controller logic that monitors the
integrity of the two joystick signals to ensure that the joystick is operating properly. It
is possible to use only one signal but it is recomended to use both.
Connecting of IQAN-LC6-X05 base outputs
When you connect the IQAN-LC6-X05 joystick to a module or standalone controller,
you should use both primary and secondary signals from the joystick. The primary
signal for the axis is connected to a VIN, voltage input and the secondary signal for the
axis is connected to a separate VIN on the controller module.
Connect each primary axis 10%-90% Vs output signal to VIN, and connect the
corresponding secondary axis 90%-10% Vs output signal to another VIN.
WARNING
The previous example is presented with limited information to explain the use of
primary and secondary signals from the IQAN-LC6-X05. Safety considerations such as
the use of an ’operator present’ switch to enable outputs etc. are always recommended.
EXAMPLE
Connecting an IQAN-LC6-X05 to a module.
to valve section controlled
to valve section controlled
VOUT-YB
VOUT-XB
VOUT-XA
VOUT-YA by Y axis of joystick
by X axis of joystick
IQAN module
LC6-X05
VIN
VIN
VIN
VIN

15
Output signals
6 Installation
Instruction book, IQAN- LC6-X05
Connecting of -H1 handle outputs
When you connect the IQAN-LC6-X05 joystick handle functions to a module or
standalone controller you may have proportional outputs from rocker and knob. You
should use both primary and secondary signals from the rocker or knob. The primary
signal for the axis is connected to a VIN, voltage input and the secondary signal for the
axis, if used, is connected to a separate VIN on the controller module.
Connect each primary output 10%-90% Vs output signal to VIN, and optionally
connect the corresponding secondary output 90%-10% Vs output signal to another
VIN.
WARNING
The previous example is presented with limited information to explain the use of
primary and secondary signals from the -H1 handle rocker and knob. Safety
considerations such as the use of an ’operator present’ switch to enable outputs etc. are
always recommended.
LC6-H1 handle loss of ground
When using only one of the two possible axis on the -H1 handle, either rocker or knob,
the primary signal from the axis not in use must be pulled to ground through a 10k-50 k
ohm resistor for safety reasons. If this is not done the connected output will have a
unintentional activation if the ground connection to the handle is lost
Connect the primary output pin from the unused axis, through a resistor, to ground.
WARNING
Possible unintentional activation of the connected axis if the ground connection is lost!
If the supply ground is disconnected from the handle sensors, the output from the
connected axis will be around 3.6 V if unused output is not grounded.
EXAMPLE
Connecting -H1 rocker and knob outputs to a module.
EXAMPLE
Grounding one of the signals from an unused axis.
to valve section controlled
to valve section controlled
VOUT-Z1B
VOUT-Z2B
VOUT-Z1A
VOUT-Z2A
by knob of joystick
by rocker of joystick
IQAN module
H1 handle
VIN
VIN
VIN
VIN
to valve section controlled
VOUT-Z1B
VOUT-Z2B
VOUT-Z1A
VOUT-Z2A
by rocker of joystick
IQAN module
H1 handle
VIN
VIN
10K
to
50K

16
Handle considerations
6 Installation
Instruction book, IQAN- LC6-X05
Handle considerations
Recommended handle specification
The IQAN-LC6-X05 will accept OEM specified handles. These handles will need to be
adapted to mount on the joystick stem. The maximum weight of any handle fitted to the
IQAN-LC6-X05 should not exceed 85g. The center of gravity (COG) of the handle
shall not be more than 57mm above the flange mounting surface. This recommendation
results in a handle that generates a maximum moment of 0,05 Nm with a maximum tilt
of 20° of the joystick base. The following formula is used to determine the lever
moment force. distance (0.057m) x weight (0,085kg) x constant (9.81g) = force
(0,047Nm).
WARNING
Risk of injury! Exceeding the recommended handle specifications could cause
unintended movement of the joystick.
Environmental specification
Any handle used with the IQAN-LC6-X05 should be a sealed type that is rated IP65-
IP67 for outdoor use. Additionally, the joystick must always have a bellow installed to
ensure that it will meet the environmental specification for sealing above the flange.
When using a handle from a different manufacturer than Parker, be sure to include a
suitable bellow made of a material that is able to withstand the stresses of outdoor use
in mobile hydraulic machinery.
NOTICE
Failure to use a properly fitted bellow of the correct material will cause the unit to not
meet its environmental specification and may result in damage to the IQAN-LC6-X05
joystick.

17
IQAN-LC6-X05 Technical Overview
Appendix A
Instruction book, IQAN-LC6-X05
Appendix A
IQAN-LC6-X05 Technical Overview
IQAN-LC6-X05, base and -H1 handle
Absolute Maximum Ratingsa
a.The “Absolute Maximum Ratings” table lists the maximum limits to which the device can be sub-
jected without damage. This doesn´t imply that the device will function at these extreme con-
ditions, only that, when these conditions are removed and the device operated within the
“Recommended Operating Conditions”, it will still be functional and its useful life won’t have been
shortened.
Ambient temperature -40 to 70 °C
Storage temperature -40 to 85°C
Maximum overvoltage on any pin 10V for max 60 minutes
External magnetic field 15 mT
Environmental ratings
TA= -40 to 85 °C (unless otherwise specified)
Climate environment
Enclosure, water & dust protection
Salt mist
Damp heat cyclic
Damp heat steady state
Heat, operation
Heat, storage
Cold
Change of temperature
IEC 60529:2001, IP65 (with sealed handle and bellow)
IEC 60068-2-52:1996 Kb, 72 h
IEC 60068-2-30:1985 Db, +55°C, 95% RH, 6 cycles
IEC 60068-2-78:2001, +40°C, 93% RH, 21 days
IEC 60068-2-2:1993-01 Bb, +85°C, 72 hours
IEC 60068-2-2:1993-01 Bb, +100°C, 72 hours
IEC 60068-2-1:1993-02 Ab, -40°C, 16 hours
IEC 60068-2-14:1984 Nb, - 30°C to +85°C, 100 x 4 hours
Mechanical environment
Random vibration
Bump
IEC 60068-2-64:2008 Fh, 15 - 1000 Hz, 11.6 Grms, 3 x 10 h
IEC 60068-2-29:1987 Eb, 40 g, 6 ms, 1000 * 6 dir
EMC
Radiated emission
Conducted susceptibility
Radiated susceptibility
Conducted transients susceptibility
ESD, Operation
ESD, Handling
ISO 13766/ISO 14982
ISO 11452-4:2005, 1 - 200 MHz, 1 kHz, 80% AM, 100 mA
ISO 11452-2:2004, 200-2000 MHz, 1kHz, 80% AM, 100 V/m
ISO 7637-3:2007, Level 3
ISO 10605:2001, 8 kV (contact), 25 kV (air)
ISO 10605:2001, 4 kV (contact)
Base - Electrical characteristics
Voltage supply on Vs 4.5 to 5.5 V
Current supply, VS = 5V max. 45 mA, typ. 34 mA (base only)
Number of VOUT 4, antivalent signals
VOUT minimum position, VS = 5V 500 mV ±100 mV (over expected life)
VOUT centre position, VS = 5V 2500 mV ±220 mV (over expected life)
VOUT maximum position, VS = 5V 4500 mV ±100 mV (over expected life)
VOUT maximum linearity error 200 mV
VOUT antivalent tracking 200 mV
VOUT resolution 12 bits = 1.22 mV
Response time 4 ms

18
IQAN-LC6-X05 Technical Overview
Appendix A
Instruction book, IQAN-LC6-X05
Minimum resistive load 1 kohm
Maximum resistive load 24 kohm
Maximum capacitive load 100 nF
Maximum continuous voltage 5.5 V
Protection SCG
Base - Mechanical characteristics
Weight .24 kg (with -H1R1K1 handle)
Angle of movement ±20°
Spring option nn (medium)
Deflection moment, neutral
Deflection moment, fully activated
0.10 Nm
0.16 Nm
Mechanical strength XY, working 10 Nm
Mechanical strength XY, one time 15 Nm
Mechanical strength twist, working 2 Nm
Mechanical strength twist, one time 5 Nm
Expected life 5x106full cycles
(One cycle: Center pos. to full +direction and back, center pos. to full -
direction and back)
Option R1 (Rocker)
Voltage supply on Vs 4.5 to 5.5 V
Current supply, VS = 5V max. 23 mA, typ. 17 mA
Number of VOUT 2, antivalent signals
VOUT minimum position, VS = 5V 500 mV ±100 mV (over expected life)
VOUT centre position, VS = 5V 2500 mV ±220 mV (over expected life)
VOUT maximum position, VS = 5V 4500 mV ±100 mV (over expected life)
VOUT maximum linearity error 200 mV
VOUT antivalent tracking 200 mV
VOUT resolution 12 bits = 1.22 mV
Response time 4 ms
Minimum resistive load 1 kohm
Maximum capacitive load 100 nF
Maximum continuous voltage 5.5 V
Current supply, VS = 5V max. 23 mA, typ. 17 mA
Protection SCG
Angle of movement ±20°
Deflection moment, neutral 0.008 Nm
Deflection moment, fully activated 0.012 Nm
Expected life 5x106full cycles
(One cycle: Center pos. to full +direction and back, center pos. to full -
direction and back)
Base - Electrical characteristics
Table of contents
Other Parker Video Game Controllers manuals
Popular Video Game Controllers manuals by other brands
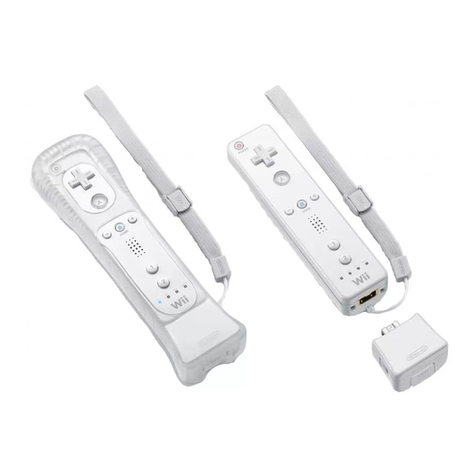
Nintendo
Nintendo Wii MotionPlus Operation manual

Bosch
Bosch Rexroth 4THE5 Series instruction manual
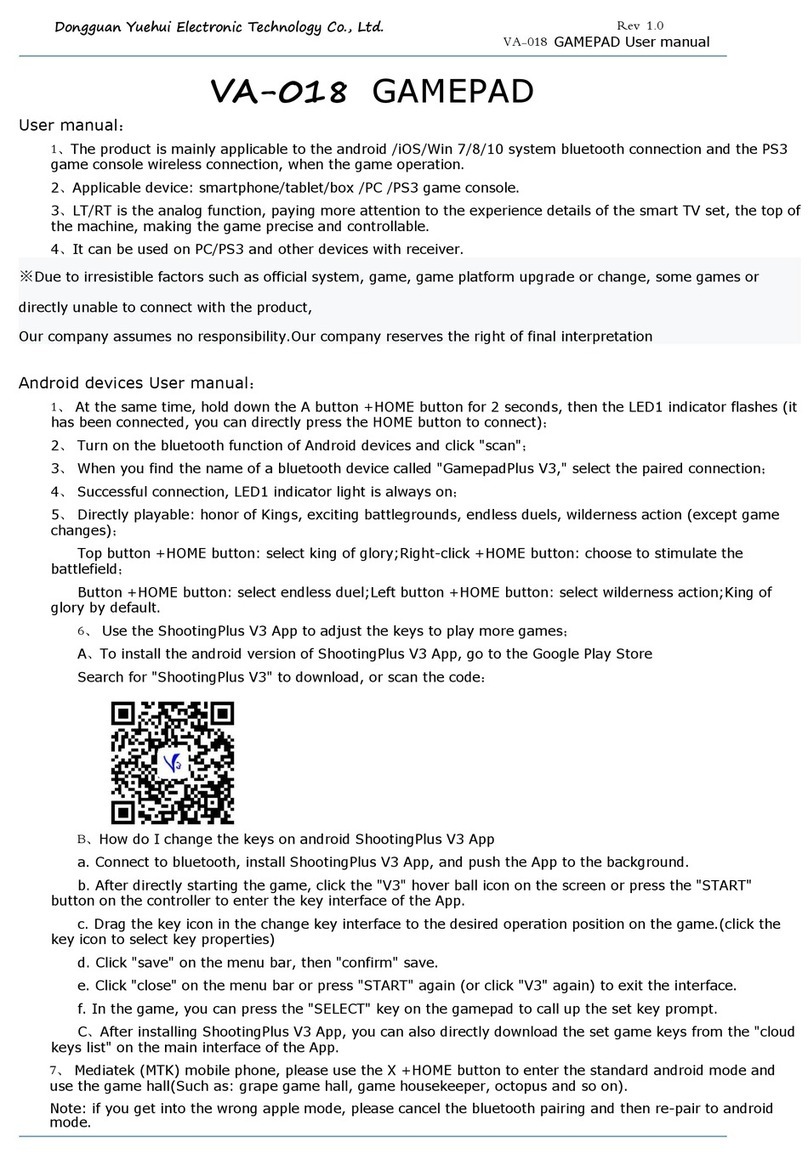
Dongguan Yuanfeng Technology
Dongguan Yuanfeng Technology VA-018 user manual
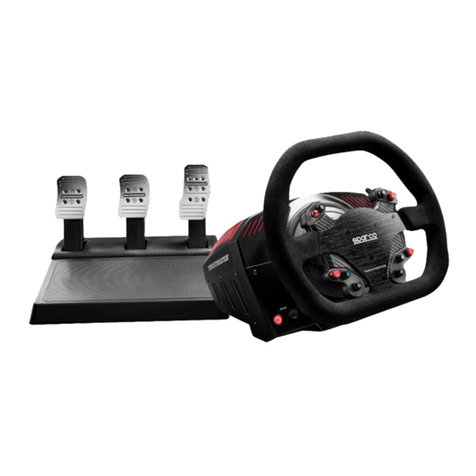
Thrustmaster
Thrustmaster TS-XW RACER Sparco P310 Competition Mod user manual
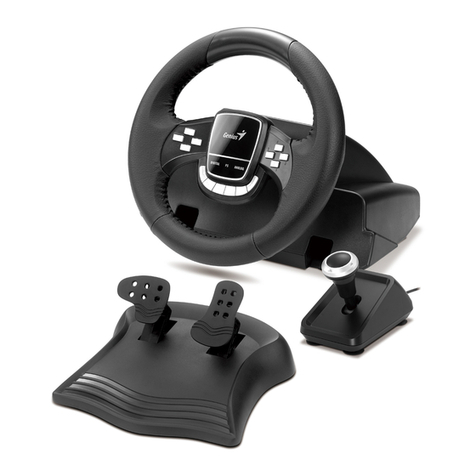
Genius
Genius TWINWHEEL 900FF installation guide
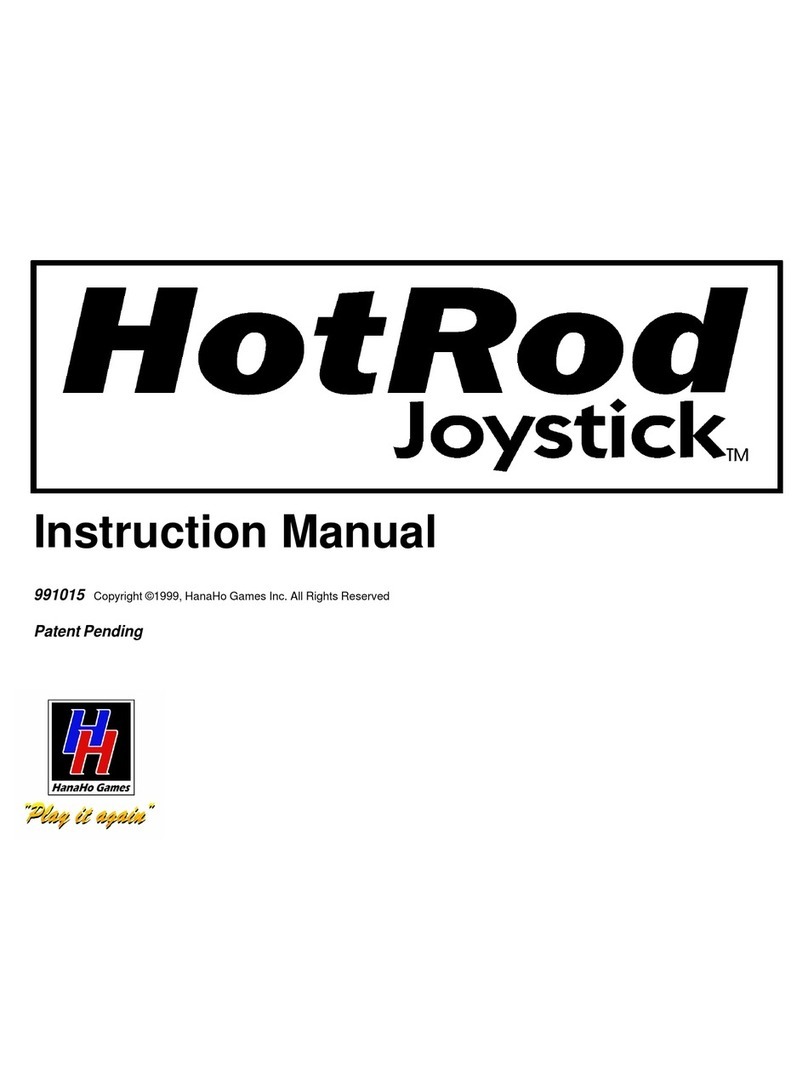
HanaHo Games
HanaHo Games HotRod Joystick instruction manual