PCB Piezotronics IMI SENSORS 682C13 User manual

Model 682C13
ICP® VIBRATION TRANSMITTER
Installation and Operating Manual
For assistance with the operation of this product,
contact the PCB Piezotronics, Inc.
Toll-free: 800-959-4464
24-hour SensorLine: 716-684-0001
Fax: 716-684-3823
E-mail: [email protected]
Web: www.imi-sensors.com

Manual 21354 Rev E
ECN 50523
Repair and Maintenance
PCB guarantees Total Customer Satisfaction through its
“Lifetime Warranty Plus” on all Platinum Stock Products
sold by PCB and through its limited warranties on all other
PCB Stock, Standard and Special products. Due to the
sophisticated nature of our sensors and associated
instrumentation, field servicing and repair is not
recommended and, if attempted, will void the factory
warranty.
Beyond routine calibration and battery replacements
where applicable, our products require no user
maintenance. Clean electrical connectors, housings, and
mounting surfaces with solutions and techniques that will
not harm the material of construction. Observe caution
when using liquids near devices that are not hermetically
sealed. Such devices should only be wiped with a
dampened cloth—never saturated or submerged.
In the event that equipment becomes damaged or ceases
to operate, our Application Engineers are here to support
your troubleshooting efforts 24 hours a day, 7 days a
week. Call or email with model and serial number as well
as a brief description of the problem.
Calibration
Routine calibration of sensors and associated
instrumentation is necessary to maintain measurement
accuracy. We recommend calibrating on an annual basis,
after exposure to any extreme environmental influence,
or prior to any critical test.
PCB Piezotronics is an ISO-9001 certified company whose
calibration services are accredited by A2LA to ISO/IEC
17025, with full traceability to SI through N.I.S.T. In
addition to our standard calibration services, we also offer
specialized tests, including: sensitivity at elevated or
cryogenic temperatures, phase response, extended high
or low frequency response, extended range, leak testing,
hydrostatic pressure testing, and others. For more
information, contact your local PCB Piezotronics
distributor, sales representative, or factory customer
service representative.
Returning Equipment
If factory repair is required, our representatives will
provide you with a Return Material Authorization (RMA)
number, which we use to reference any information you
have already provided and expedite the repair process.
This number should be clearly marked on the outside of
all returned package(s) and on any packing list(s)
accompanying the shipment.
Contact Information
PCB Piezotronics, Inc.
3425 Walden Ave.
Depew, NY14043 USA
Toll-free: (800) 828-8840
24-hour SensorLine: (716) 684-0001
Repair inquiries: rma@pcb.com
For a complete list of distributors, global offices and sales
representatives, visit our website, www.pcb.com.
Safety Considerations
This product is intended for use by qualified personnel
who recognize shock hazards and are familiar with the
precautions required to avoid injury. While our equipment
is designed with user safety in mind, the protection
provided by the equipment may be impaired if equipment
is used in a manner not specified by this manual.
Discontinue use and contact our 24-Hour Sensorline if:
Assistance is needed to safely operate equipment
Damage is visible or suspected
Equipment fails or malfunctions
For complete equipment ratings, refer to the enclosed
specification sheet for your product.
Definition of Terms and Symbols
The following symbols may be used in this manual:
DANGER
Indicates an immediate hazardous
situation, which, if not avoided, may
result in death or serious injury.

Manual 21354 Rev E
ECN 50523
CAUTION
Refers to hazards that could damage
the instrument.
NOTE
Indicates tips, recommendations and
important information. The notes
simplify processes and contain
additional information on particular
operating steps.
The following symbols may be found on the equipment
described in this manual:
This symbol on the unit indicates that
high voltage may be present. Use
standard safety precautions to avoid
personal contact with this voltage.
This symbol on the unit indicates that
the user should refer to the operating
instructions located in the manual.
This symbol indicates safety, earth
ground.

Manual 21354 Rev E
ECN 50523
PCB工业监视和测量设备 - 中国RoHS2公布表
PCB Industrial Monitoring and Measuring Equipment - China RoHS 2 Disclosure Table
部件名称
有害物质
铅(Pb)
汞
(Hg)
镉
(Cd)
六价铬(Cr(VI))
多溴联苯 (PBB)
多溴二苯醚(PBDE)
住房
O
O
O
O
O
O
PCB板
X
O
O
O
O
O
电气连接器
O
O
O
O
O
O
压电晶体
X
O
O
O
O
O
环氧
O
O
O
O
O
O
铁氟龙
O
O
O
O
O
O
电子
O
O
O
O
O
O
厚膜基板
O
O
X
O
O
O
电线
O
O
O
O
O
O
电缆
X
O
O
O
O
O
塑料
O
O
O
O
O
O
焊接
X
O
O
O
O
O
铜合金/黄铜
X
O
O
O
O
O
本表格依据 SJ/T 11364 的规定编制。
O:表示该有害物质在该部件所有均质材料中的含量均在 GB/T 26572 规定的限量要求以下。
X:表示该有害物质至少在该部件的某一均质材料中的含量超出 GB/T 26572 规定的限量要求。
铅是欧洲RoHS指令2011/65/ EU附件三和附件四目前由于允许的豁免。
CHINA RoHS COMPLIANCE

Manual 21354 Rev E
ECN 50523
Component Name
Hazardous Substances
Lead (Pb)
Mercury (Hg)
Cadmium (Cd)
Chromium VI
Compounds
(Cr(VI))
Polybrominated
Biphenyls (PBB)
Polybrominated
Diphenyl Ethers
(PBDE)
Housing
O
O
O
O
O
O
PCB Board
X
O
O
O
O
O
Electrical Connectors
O
O
O
O
O
O
Piezoelectric Crystals
X
O
O
O
O
O
Epoxy
O
O
O
O
O
O
Teflon
O
O
O
O
O
O
Electronics
O
O
O
O
O
O
Thick Film Substrate
O
O
X
O
O
O
Wires
O
O
O
O
O
O
Cables
X
O
O
O
O
O
Plastic
O
O
O
O
O
O
Solder
X
O
O
O
O
O
Copper Alloy/Brass
X
O
O
O
O
O
This table is prepared in accordance with the provisions of SJ/T 11364.
O: Indicates that said hazardous substance contained in all of the homogeneous materials for this part is below the limit
requirement of GB/T 26572.
X: Indicates that said hazardous substance contained in at least one of the homogeneous materials for this part is above the limit
requirement of GB/T 26572.
Lead is present due to allowed exemption in Annex III or Annex IV of the European RoHS Directive 2011/65/EU.

SENSORS AND INSTRUMENTATION FOR MACHINE CONDITION MONITORING
682 Series 4-20mA Din Rail ICP®Signal Conditioner
Operating Guide with Enclosed Warranty Information
3425 Walden Avenue, Depew, New York 14043-2495
Phone (716) 684-0003
Fax (716) 684-3823
Toll Free Line 1-800-959-4IMI
MANUAL NUMBER: 60419
MANUAL REVISION: B
ECN NUMBER: 46422

PAGE 2
SENSORS AND INSTRUMENTATION FOR MACHINE CONDITION MONITORING
Table of Contents
Introduction...................................................................................................................... Page 3
Block diagram............................................................................................................ Page 3
General Features........................................................................................................................................... Page 4
Installation and Wiring..................................................................................................... Page 5
Configuring the 682BX3 .................................................................................................. Page 9
ESD Sensitivity............................................................................................................... Page 12
Ordering Information ...................................................................................................... Page 13
Warranty/Servicing
Warranty, Service & Return Procedure .......................................................................... Page 14
Customer Service........................................................................................................... Page 15

PAGE 3
SENSORS AND INSTRUMENTATION FOR MACHINE CONDITION MONITORING
Introduction
The 682 Series is a 4-20mA Din Rail Signal Conditioner designed to interface with IMI Sensor’s ICP®
Accelerometer. Acceleration, Velocity, or Displacement can be converted to a 4-20mA signal by simple DIP
Switch selection internal to the Din Rail enclosure. An additional standard feature of the 682 Series is the ability to
convert the temperature output from an accelerometer (when equipped) to 4-20mA. Signal Filtering can be easily
configured in the field by installing factory calibrated Filter Modules into sockets located inside the enclosure.
Block Diagram

PAGE 4
SENSORS AND INSTRUMENTATION FOR MACHINE CONDITION MONITORING
General Features
External transmitters, signal conditioners, and ICP®power supplies can be eliminated by direct
connection of the sensor to the Din Rail Signal Conditioner.
Optional 500Vdc Input to Output Electrical Isolation.
Selectable 24Vdc Unregulated, 18Vdc regulated, 4mA excitation to power sensor
4-20mA Output Signals for Vibration and Temperature.
Selectable 0-5 or 0-10Vdc Output Signal for Vibration.
Internal DIP switch selectable vibration ranges include:
Acceleration (g’s)
Velocity (in/sec)
Displacement (mils p-p)
5.00
0.50
10.0
10.00
1.00
20.0
20.00
2.00
40.0
Internal DIP switch selection for Peak or RMS.
Utilization of Filter Modules for field configuration of High and Low pass 2-pole filtering.
Analog output signal connections (RV) for conducting frequency analysis and machinery diagnostics.
LED indicators for Power, Sensor Fault, Acceleration, Velocity, and Displacement.
Electronic Sensor Fault Indication via 4-20mA output by providing a 0mA signal.
Configurable for ICP®Sensor Power disable to accommodate existing applications.
Removable Terminal Blocks for easy wiring.
35mm (1.38in.) Din Rail Mount configuration.
Space saving 22.5mm (0.9in.) wide design.

PAGE 5
SENSORS AND INSTRUMENTATION FOR MACHINE CONDITION MONITORING
Installation and Wiring
Installation
The 682 Series is designed to be mounted on a 35mm Din Rail. Do not install in a harsh area where it can be
exposed to cleaning fluids or machine oils. IMI Sensors recommends mounting the 682BX3 in a type NEMA 4
enclosure to protect the electronics from contamination.
Dimension Drawing
The Power LED is Green which turns on when the unit is powered. The Fault LED is red which turns on when the
sensor input is either open or shorted. The Acceleration, Velocity, and Displacement LED is Green which turns on
when the corresponding dip switches shown on page 8 are set.

PAGE 6
SENSORS AND INSTRUMENTATION FOR MACHINE CONDITION MONITORING
Connector and Pinout Diagram
The 682 Series uses plug-in type screw terminal connectors for all input and output connections.
Strip off 8mm of insulation from the connection wire ends. Using a screwdriver, remove the terminal block from
the enclosure in either the up or down direction, terminate the wire in the correct location. Do not exceed a torque
of 0.5Nm. Re-install the terminal block.
This easy to assemble connection method allows devices to be exchanged easily and the electrical connection to
be visibly isolated.
Pin Location Diagram
WARNING
AC and DC input signals and power supply voltages could be hazardous. DO NOT
connect live wires to screw terminal plugs, and DO NOT insert, remove, or handle screw
terminal plugs with live wires connected.

PAGE 7
SENSORS AND INSTRUMENTATION FOR MACHINE CONDITION MONITORING
Pin Descriptions:
DC Power –Pins 1 to 3:
Pin 1 +Power
Pin 2 -Power/Common
Pin 3 Earth Ground
ICP®Accelerometer –Pins 4 to 6:
Pin 4 Shield
Pin 5 + ICP®Accelerometer
Pin 6 - ICP®Accelerometer
Temperature Sensor –Pins 7 to 8:
Pin 7 + Temperature Sensor
Pin 8 - Temperature Sensor (- ICP®Accelerometer)
Raw Vibration (RV) –Pins 9 to 10, and BNC Jack:
Pin 9 + RV
Pin 10 - RV
4 to 20mA Temperature Output –Pins 11 to 12:
Pin 11 + 4 to 20mA Temperature Output
Pin 12 - 4 to 20mA Temperature Output
4 to 20mA Vibration Output –Pins 13 to 14:
Pin 13 + 4 to 20mA Vibration Output
Pin 14 - 4 to 20mA Vibration Output
0-5/10Vdc Vibration Output –Pins 15 to 16:
Pin 15 + 0-5/10Vdc Vibration Output
Pin 16 - 0-5/10Vdc Vibration Output
Notes:
Pins 3 and 4 are tied together but are NOT tied to the grounding tab on the back of the enclosure.
Land the accelerometer cable’s shield on Pin 4.
Tie Pin 3 to either din rail ground or Earth ground with the use of an external wire.

PAGE 8
SENSORS AND INSTRUMENTATION FOR MACHINE CONDITION MONITORING
Typical Wiring Diagram
682 Series
Signal
Conditioner
Signal Conditioner
Power
Supply
682A01
Power
Supply

PAGE 9
SENSORS AND INSTRUMENTATION FOR MACHINE CONDITION MONITORING
To Maintain Conformance, Earth Ground, Power Supply Common, and I/O Shields must
be connected together.
Note: If using the 682 Power Supply, mount the 682 Signal Conditioner to the left of the power supply with a
recommended minimum separation distance of 4” where applicable.
Configuring the 682 Series
Internal PC Board Diagram
The Internal PC Board Diagram shows
the location of the internal DIP Switch,
Filter Modules, and Sensor Power
Select Jumper. The DIP switch is used
to configure the signal conditioner for
various sensor and vibration ranges.
The Filter Modules are installed to set
the High and Low cutoff frequencies.
The Jumper selects unregulated,
regulated, or no ICP®power to the
accelerometer.
The PC Board is accessible through
the front of the indicator by removing
the Screw Terminal Connectors and
disengaging the tabs on the TOP and
BOTTOM of the meter with a
screwdriver. Once disengaged, the PC
Board can be slid out for configuration.
DIP Switch and Filter Module Descriptions:
S1 and S2: Acceleration Mode
S3 and S4: Velocity Mode
S5 and S6: Displacement Mode
S7: RMS
S8: Peak
S9: 20g, 2ips, 40mils

PAGE 10
SENSORS AND INSTRUMENTATION FOR MACHINE CONDITION MONITORING
S10: 10g, 1ips, 20mils
S11: 5g, 0.5ips, 10mils
S12: Off = 0-5Vdc Output, On = 0-10Vdc Output
Internal DIP Switch Setting
The Internal DIP Switch of the 682 Series must be configured for the Full Scale Output of the ICP®Sensor
connected to it. This is accomplished by removing the front cover and sliding the PC Board out of the Signal
Conditioner. Once removed, the DIP switch should be configured per one of the conditions in the following table.
Range Setting
S1
S2
S3
S4
S5
S6
S7
S8
S9
S10
S11
5g RMS
ON
ON
OFF
OFF
OFF
OFF
ON
OFF
OFF
OFF
ON
5g Peak
ON
ON
OFF
OFF
OFF
OFF
OFF
ON
OFF
OFF
ON
10g RMS
ON
ON
OFF
OFF
OFF
OFF
ON
OFF
OFF
ON
OFF
10g Peak
ON
ON
OFF
OFF
OFF
OFF
OFF
ON
OFF
ON
OFF
20g RMS
ON
ON
OFF
OFF
OFF
OFF
ON
OFF
ON
OFF
OFF
20g Peak
ON
ON
OFF
OFF
OFF
OFF
OFF
ON
ON
OFF
OFF
0.5 in/sec RMS
OFF
OFF
ON
ON
OFF
OFF
ON
OFF
OFF
OFF
ON
0.5 in/sec Peak
OFF
OFF
ON
ON
OFF
OFF
OFF
ON
OFF
OFF
ON
1.0 in/sec RMS
OFF
OFF
ON
ON
OFF
OFF
ON
OFF
OFF
ON
OFF
1.0 in/sec Peak
OFF
OFF
ON
ON
OFF
OFF
OFF
ON
OFF
ON
OFF
2.0 in/sec RMS
OFF
OFF
ON
ON
OFF
OFF
ON
OFF
ON
OFF
OFF
2.0 in/sec Peak
OFF
OFF
ON
ON
OFF
OFF
OFF
ON
ON
OFF
OFF
10 mils p-p
OFF
OFF
OFF
OFF
ON
ON
OFF
OFF
OFF
OFF
ON
20 mils p-p
OFF
OFF
OFF
OFF
ON
ON
OFF
OFF
OFF
ON
OFF
40 mils p-p
OFF
OFF
OFF
OFF
ON
ON
OFF
OFF
ON
OFF
OFF
S12
OFF
0-5Vdc Output
S12
ON
0-10Vdc Output
Note: Factory Default Setting is 1.0in/sec Peak, 0-5Vdc Output
Filter Module Location
The Filter Modules are utilized to set the cutoff frequency of the internal band pass filter circuit. The 682 Series
comes standard with Modules preinstalled. If a different cutoff frequency is desired, the preinstalled module can
be removed by simply pulling it out of the MOD socket, and replacing it with a different module. The module is
labeled with the type of filter, Low Pass or High Pass, and the cutoff frequency. Module location is as follows:
MOD1: Low Pass (LP) Filter Module Location
MOD2: High Pass (HP) Filter Module Location
Warning: Do not make any adjustments to the internal potentiometers. These potentiometers are used for
factory calibration and adjusting them will require return of the 682 Series unit to the factory for recalibration.

PAGE 11
SENSORS AND INSTRUMENTATION FOR MACHINE CONDITION MONITORING
Sensor Power Jumper Configuration:
(Factory Default)
Note: If there is no DC bias on the input signal, this will trigger the
Open/short detection which subtracts 4mA from output

PAGE 12
SENSORS AND INSTRUMENTATION FOR MACHINE CONDITION MONITORING
Warning 1 –ESD sensitivity
The power supply/signal conditioner should not be opened by anyone other than qualified service
personnel. This product is intended for use by qualified personnel who recognize shock hazards and are familiar
with the safety precautions required to avoid injury.
Warning 2 –ESD sensitivity
This equipment is designed with user safety in mind; however, the protection provided by the equipment may be
impaired if the equipment is used in a manner not specified by PCB Piezotronics, Inc.
Caution 1 –ESD sensitivity
Cables can kill your equipment. High voltage electrostatic discharge (ESD) can damage electrical devices.
Similar to a capacitor, a cable can hold a charge caused by triboelectric transfer, such as that which occurs in the
following:
Laying on and moving across a rug,
Any movement through air,
The action of rolling out a cable, and/or
Contact with a non-grounded person.
The PCB solution for product safety:
Connect the cables only with the AC power off.
Temporarily “short” the end of the cable before attaching it to any signal input or output.
Caution 2 –ESD sensitivity

PAGE 13
SENSORS AND INSTRUMENTATION FOR MACHINE CONDITION MONITORING
ESD considerations should be made prior to performing any internal adjustments on the equipment. Any
piece of electronic equipment is vulnerable to ESD when opened for adjustments. Internal adjustments should
therefore be done ONLY at an ESD-safe work area. Many products have ESD protection, but the level of
protection may be exceeded by extremely high voltage.
Ordering Information
IMI Part Number: 682A X3
Frequency Response/Isolation*
0 3Hz to 10kHz (Standard)
1 3Hz to 1kHz
2 10Hz to 10kHz
3 10Hz to 1kHz
4 3Hz to 10kHz with 500Vdc I/O Isolation
5 3Hz to 1kHz with 500Vdc I/O Isolation
6 10Hz to 10kHz with 500Vdc I/O Isolation
7 10Hz to 1kHz with 500Vdc I/O Isolation
Ordering Example: 682B13
This is a 4-20mA Din Rail ICP®Signal Conditioner with the following:
Frequency Response: 3Hz to 1kHz
I/O Isolation: None
*Additional Options Available –Please Inquire

PAGE 14
SENSORS AND INSTRUMENTATION FOR MACHINE CONDITION MONITORING
Warranty
IMI instrumentation is warranted against defective material and workmanship for 1 year unless otherwise
expressly specified. Damage to instruments caused by incorrect power or misapplication, is not covered by
warranty. If there are any questions regarding power, intended application, or general usage, please consult with
your local sales contact or distributor. Batteries and other expendable hardware items are not covered by
warranty.
Service
Because of the sophisticated nature of IMI instrumentation, field repair is typically NOT recommended and may
void any warranty. If factory service is required, return the instrumentation according to the “Return Procedure”
stated below. A repair and/or replacement quotation will be provided prior to servicing at no charge. Before
returning the unit, please consult a factory IMI applications engineer concerning the situation as certain problems
can often be corrected with simple on-site procedures.
Return procedure
To expedite returned instrumentation, contact a factory IMI applications engineer for a RETURN MATERIAL
AUTHORIZATION (RMA) NUMBER. Please have information available such as model and serial number. Also,
to insure efficient service, provide a written description of the symptoms and problems with the equipment to a
local sales representative or distributor, or contact IMI if none are located in your area.
Customers outside the U.S. should consult their local IMI distributor for information on returning equipment. For
exceptions, please contact the International Sales department at IMI to request shipping instructions and an RMA.
For assistance, please call (716) 684-0003, or fax us at (716) 684-3823. You may also receive assistance via e-
mail at imi@pcb.com or visit our web site at www.pcb.com.

PAGE 15
SENSORS AND INSTRUMENTATION FOR MACHINE CONDITION MONITORING
Customer Service
IMI, a division of PCB Piezotronics, guarantees Total Customer Satisfaction. If, at any time, for any reason, you
are not completely satisfied with any IMI product, IMI will repair, replace, or exchange it at no charge. You may
also choose, within the warranty period, to have your purchase price refunded.
IMI offers to all customers, at no charge, 24-hour phone support. This service makes product or application
support available to our customers, day or night, seven days a week. When unforeseen problems or emergency
situations arise, call the IMI Hot Line at (716) 684-0003, and an application specialist will assist you.
3425 Walden Avenue, Depew, NY 14043-2495
Phone: (716) 684-0003
USA Fax: (716) 684-3823
INTL Fax: (716) 684-4703
ICP®is a registered trademark of PCB Group, Incorporated,
which uniquely identifies PCB sensors that incorporate built-in microelectronics.
Table of contents
Other PCB Piezotronics Transmitter manuals
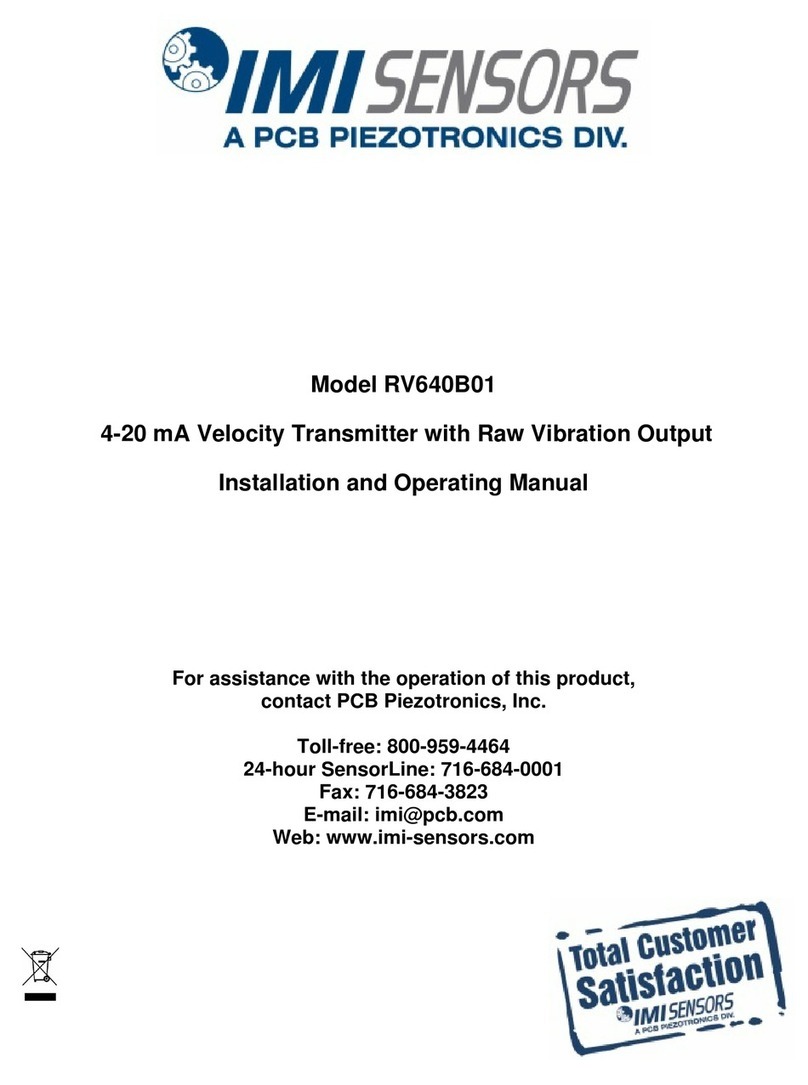
PCB Piezotronics
PCB Piezotronics IMI SENSORS RV640B01 User manual
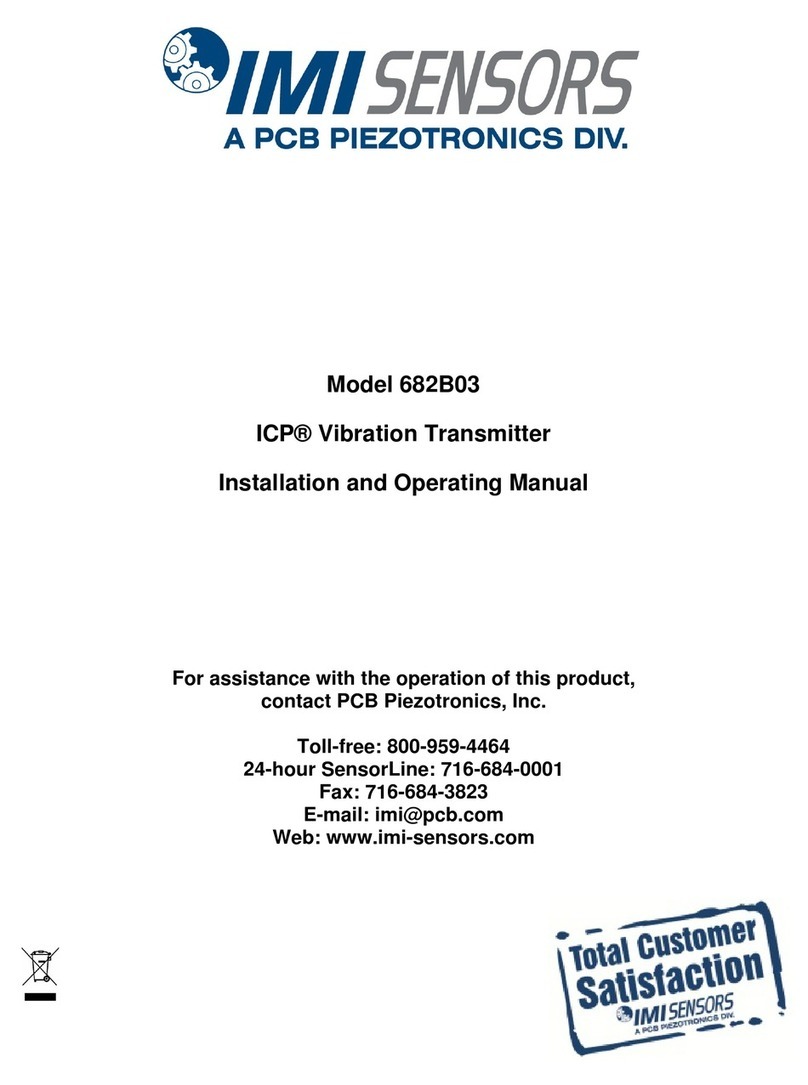
PCB Piezotronics
PCB Piezotronics 682B03 User manual
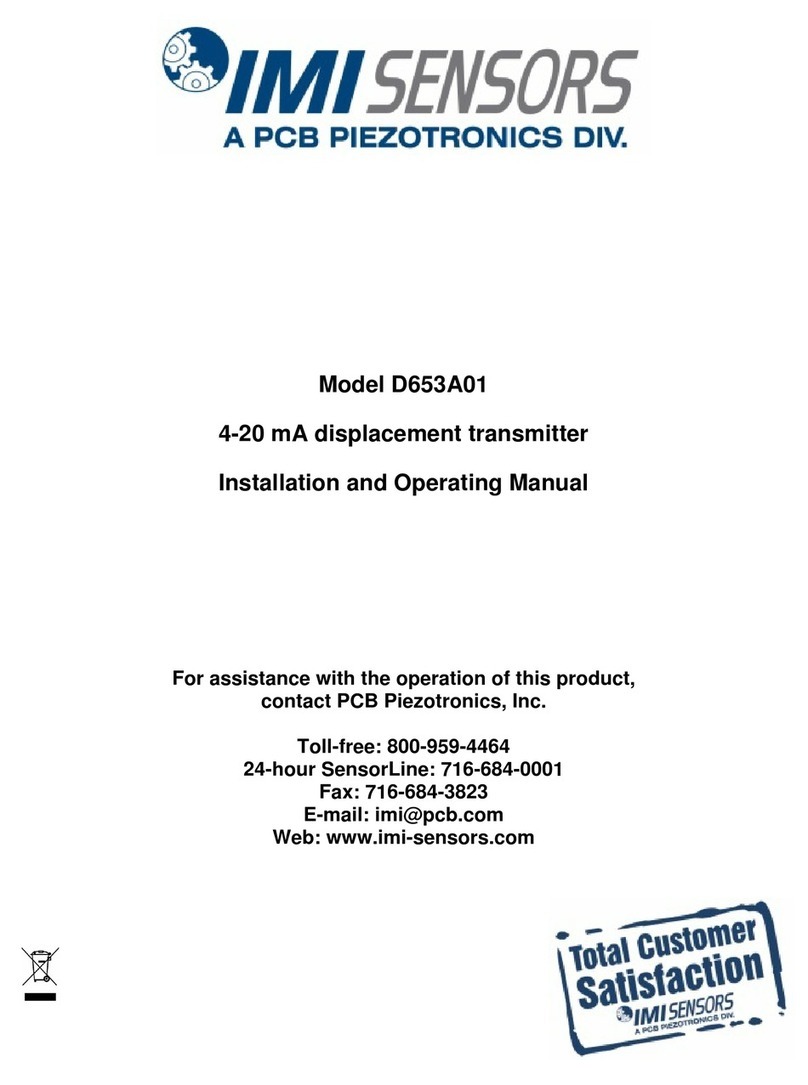
PCB Piezotronics
PCB Piezotronics IMI SENSORS D653A01 User manual
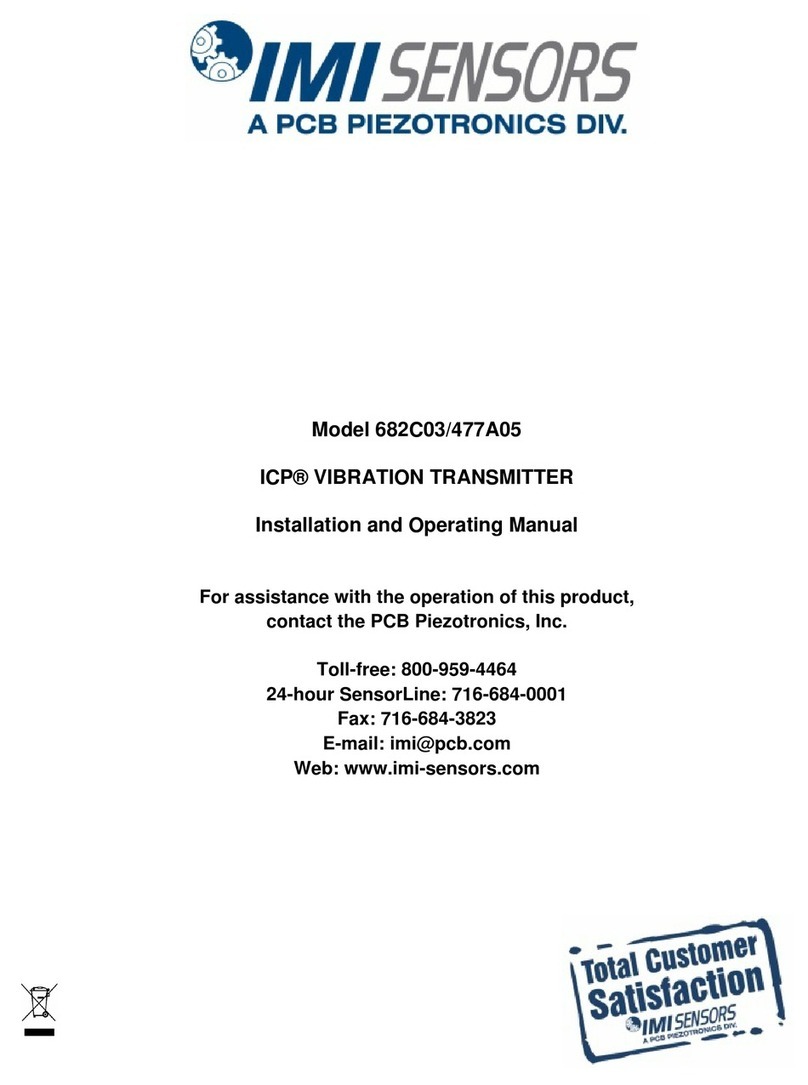
PCB Piezotronics
PCB Piezotronics 477A05 User manual
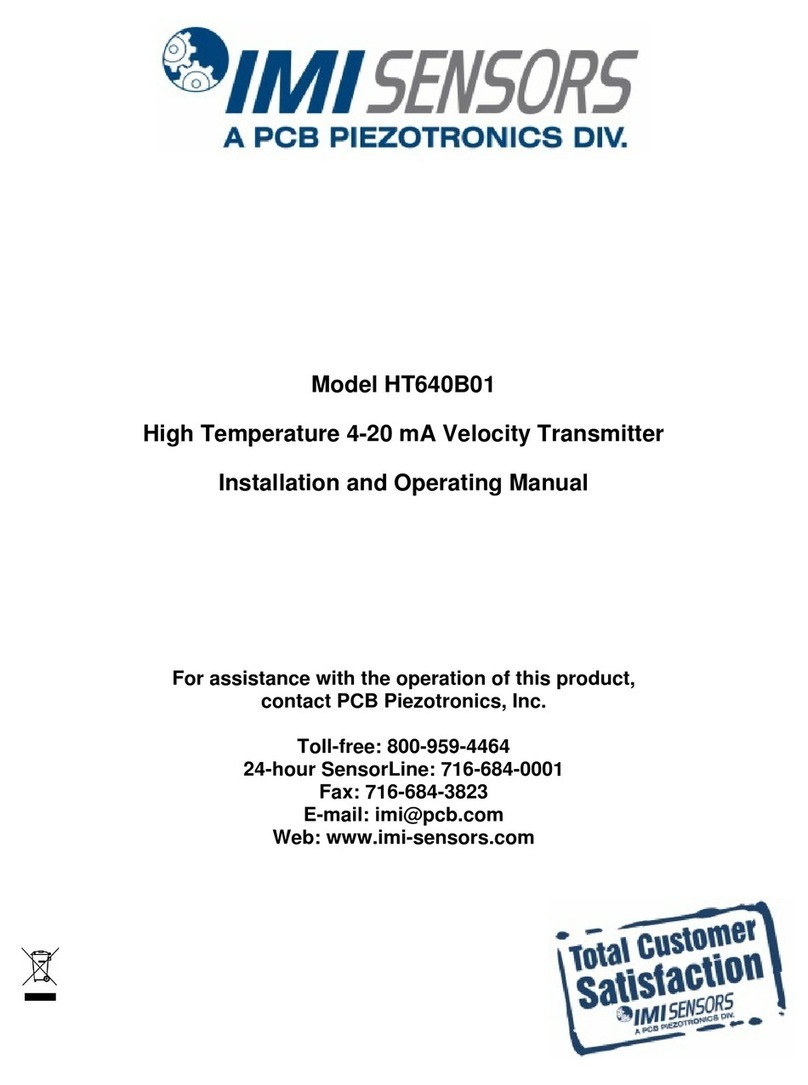
PCB Piezotronics
PCB Piezotronics IMI SENSORS HT640B01 User manual
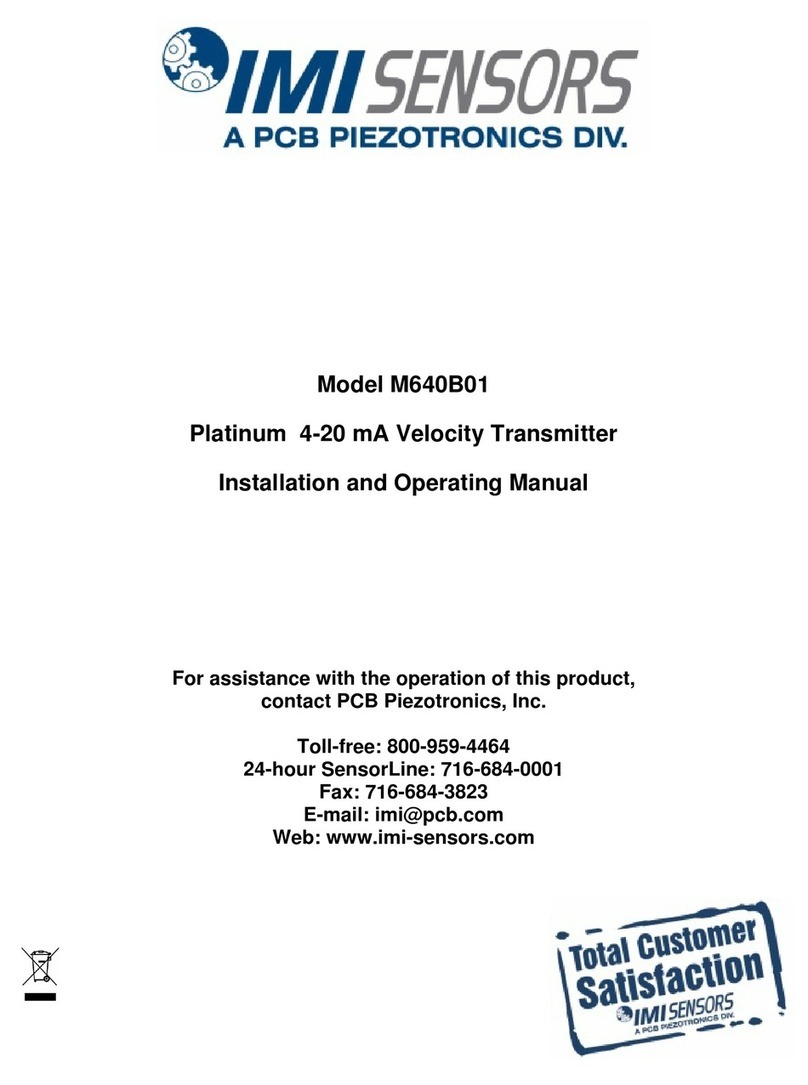
PCB Piezotronics
PCB Piezotronics IMI Sensors M640B01 User manual
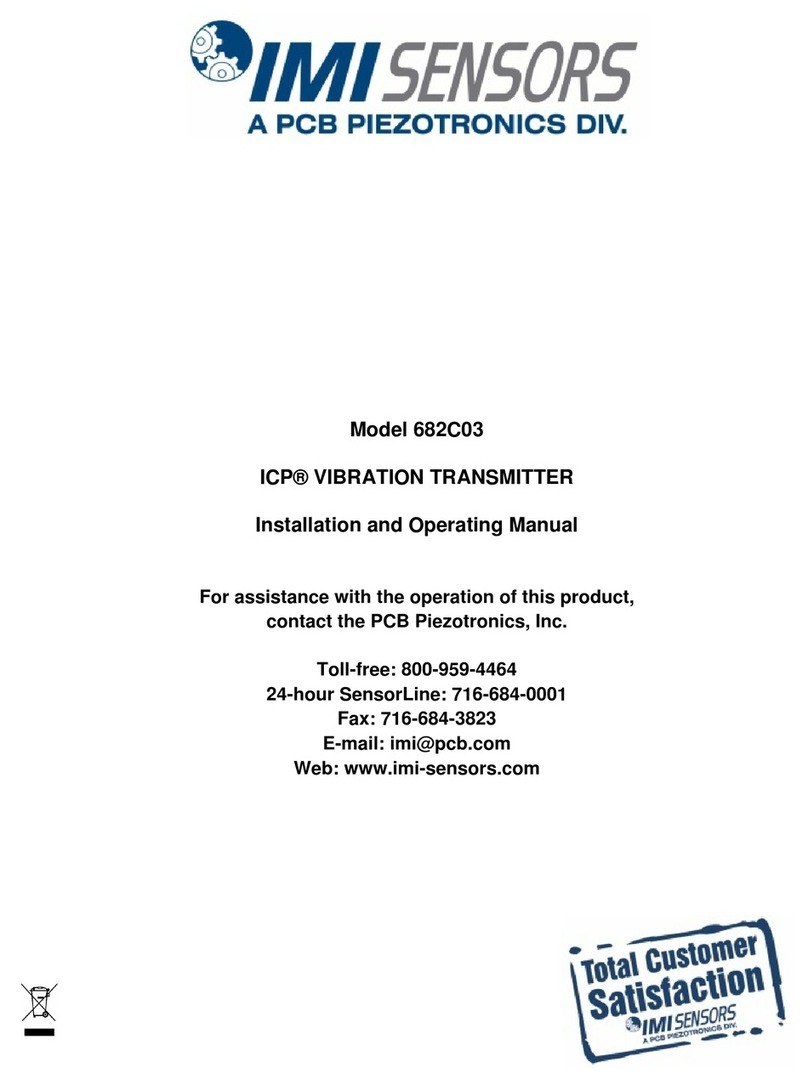
PCB Piezotronics
PCB Piezotronics IMI SENSORS 682C03 User manual
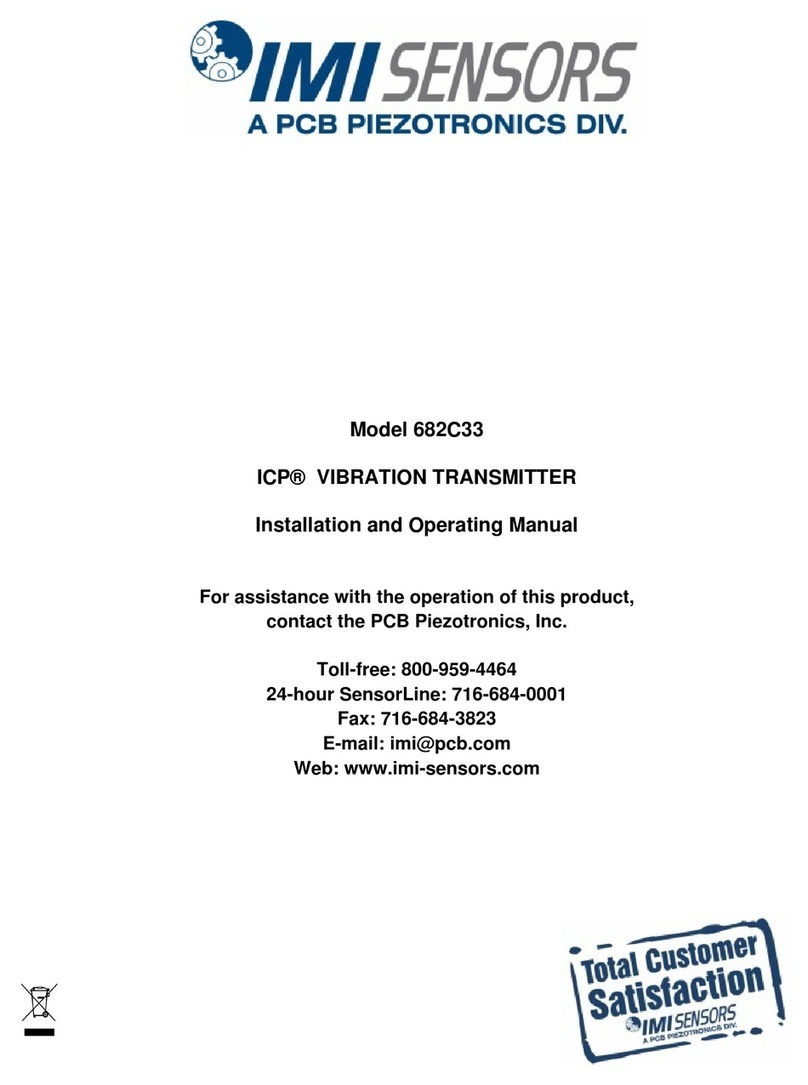
PCB Piezotronics
PCB Piezotronics IMI Sensors 682C33 User manual
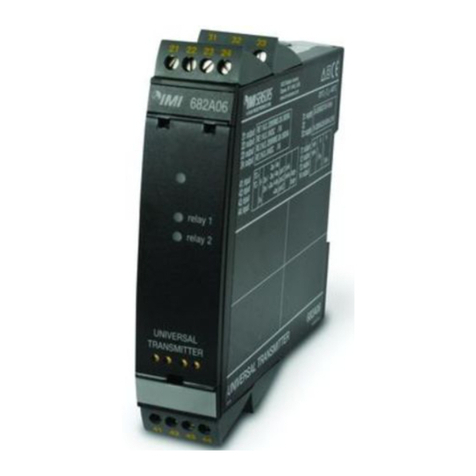
PCB Piezotronics
PCB Piezotronics 682A06 User manual
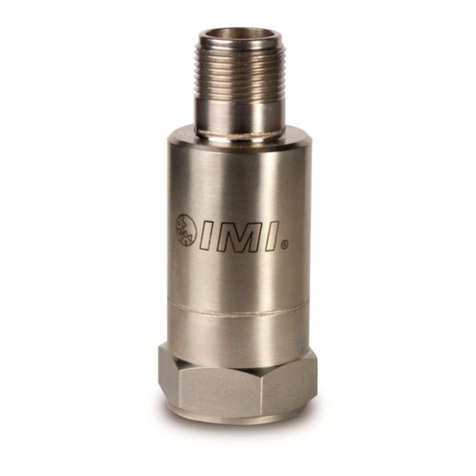
PCB Piezotronics
PCB Piezotronics IMI SENSORS 640B01 User manual