PCB Piezotronics 962 User manual

MODEL 962
TR A N S I E N T RE C O R D E R IN S T R U C T I O N MA N U A L
Software Version 7A+
©2015 PCB Load & Torque
Manual 60809 Revision NR

RS Products from PCB Load & Torque Toll-Free in USA 866-684-7107 716-684-0001 www.pcb.com
MODEL 962 RECORDER OPERATION MANUAL 2
TABLE OF CONTENTS
GENERAL GUIDELINES.......................................................................................................................................5
WARNING SYMBOLS AND TERMS ....................................................................................................................5
1.0 Product INTRODUCTION...............................................................................................................................5
1.1 Equipment...............................................................................................................................................5
1.2 Important Features..............................................................................................................................6
1.2.1 Display Modes.....................................................................................................................................6
1.2.2 Input Channels .....................................................................................................................................6
1.2.3 Limit Results Data/XY Graphic Plot Data...........................................................................................6
1.2.4 USB Ports ............................................................................................................................................6
1.2.5 Instrument Operating Status.................................................................................................................6
2.0 SAFETY PRECAUTIONS................................................................................................................................6
3.0 OVERVIEW......................................................................................................................................................6
3.1 Specifications......................................................................................................................................6
3.2 Dimensions .........................................................................................................................................7
3.3 Connector Panel .................................................................................................................................7
3.4 Connector Pinouts...............................................................................................................................7
3.4.1 TTL/IO Pinouts....................................................................................................................................7
3.4.2 Channel 1 & Channel 2 Pinouts...........................................................................................................8
3.4.3 Connecting a High Level Device.........................................................................................................8
3.5 Battery Use & Recharging ..................................................................................................................8
3.6 Calibration Shunt Resistors ................................................................................................................8
3.7 File Types............................................................................................................................................8
3.8 Keypad................................................................................................................................................8
4.0 SCREENS AND MENUS.................................................................................................................................9
4.1 Introductory Screen.............................................................................................................................9
4.2 Main Screen........................................................................................................................................9
4.3 Setup Menu.........................................................................................................................................10
4.3.1 Channels Setup.....................................................................................................................................10
4.3.2 Units of Measure..................................................................................................................................11
4.3.3 Direction ..............................................................................................................................................11
4.3.4 Set Torque Limits ................................................................................................................................12
4.3.5 Set Recording Time .............................................................................................................................12
4.3.6 Set Auto Options..................................................................................................................................13
4.3.7 Torque-Force Points.............................................................................................................................13
4.3.8 Analysis Setup .....................................................................................................................................14
4.3.9 Set Report Format................................................................................................................................16
4.4 Calibration Menu.................................................................................................................................16

RS Products from PCB Load & Torque Toll-Free in USA 866-684-7107 716-684-0001 www.pcb.com
MODEL 962 RECORDER OPERATION MANUAL 3
4.4.1 ZERO Only..........................................................................................................................................16
4.4.2 AUTO Calibration ...............................................................................................................................16
4.4.3 MANUAL Calibration.........................................................................................................................17
4.4.4 Add/Edit Torque/Force Transducer .....................................................................................................17
4.5 Print/Disk Menu...................................................................................................................................18
4.5.1 Printer...................................................................................................................................................18
4.5.2 USB Drive............................................................................................................................................18
4.5.3 USB Host.............................................................................................................................................19
4.6 Utility Menu .........................................................................................................................................19
4.6.1 Set Date and Time................................................................................................................................19
4.6.2 Clear Results........................................................................................................................................19
4.6.3 Install Defaults.....................................................................................................................................20
4.6.4 Check for Smartducers.........................................................................................................................20
4.6.5 Set 962 Serial Number.........................................................................................................................20
4.6.6 Mode....................................................................................................................................................20
4.6.7 Set Analog Outputs..............................................................................................................................20
4.6.8 Diagnostics Menu ................................................................................................................................21
4.6.9 Change Password.................................................................................................................................21
5.0 Using FastPlot2..............................................................................................................................................21
5.1 Start FastPlot2 ....................................................................................................................................21
5.2 MainView Tab .....................................................................................................................................21
5.3 ToolsView Tab ....................................................................................................................................22
5.4 SetupView Tab....................................................................................................................................22
5.5 RundownView Tab..............................................................................................................................23
5.6 ReportView Tab ..................................................................................................................................24
5.7 Exit FastPlot2......................................................................................................................................24
5.8 Installations of Software Upgrade.......................................................................................................25
6.0 M-Alpha Analysis ...........................................................................................................................................25
6.1 M-Alpha Overview...............................................................................................................................25
6.2 M-Alpha Analysis Procedure...............................................................................................................25
7.0 MAINTENANCE...............................................................................................................................................25
7.1 Battery Use & Re-Charging ................................................................................................................25
7.2 Handling & Placement.........................................................................................................................26
8.0 TROUBLE SHOOTING....................................................................................................................................26
9.0 CALIBRATION / REPAIR SERVICES ............................................................................................................27
10.0 WARRANTY ..................................................................................................................................................27
11.0 Sample Test Setups.....................................................................................................................................27
11.1 Torque-Tension Testing....................................................................................................................27
11.1.1 Scope..................................................................................................................................................27

RS Products from PCB Load & Torque Toll-Free in USA 866-684-7107 716-684-0001 www.pcb.com
MODEL 962 RECORDER OPERATION MANUAL 4
11.1.2 Torque-Tension Testing Equipment Setup ........................................................................................28
11.1.3 Test Procedure ...................................................................................................................................28
11.2 Power Tool Testing...........................................................................................................................29
11.2.1 Scope..................................................................................................................................................29
11.2.2 Power Tool Testing Equipment Setup ...............................................................................................29
11.2.3 Setup Menu for Power Tool Testing..................................................................................................29
11.2.4 Power Tool Verification Procedure....................................................................................................30
12.0 QUICK REFERENCE ....................................................................................................................................30
12.1 Add/Edit Transducers........................................................................................................................30
12.2 Setup a Test......................................................................................................................................30
12.3 Calibrate Transducers.......................................................................................................................30
12.4 Perform a Test ..................................................................................................................................31
12.5 Save Rundown..................................................................................................................................31
12.6 Update Report...................................................................................................................................31
12.7 View a Plot ........................................................................................................................................31
12.8 Export Data .......................................................................................................................................31
12.9 Clear Results.....................................................................................................................................31
12.10 View Diagnostics.............................................................................................................................31

RS Products from PCB Load & Torque Toll-Free in USA 866-684-7107 716-684-0001 www.pcb.com
MODEL 962 RECORDER OPERATION MANUAL 5
GENERAL GUIDELINES
Operators should read this manual and become thoroughly famil-
iar with its contents before attempting to operate the Model 962
recorder. Following the safety considerations and operation in-
structions outlined in this manual will minimize the possibility of
accidents or injury. Although the procedures covered in this
manual have proven safe in use, PCB Load & Torque assumes no
responsibility for personal injury or damage to equipment result-
ing from their application. After reading this manual, personnel
should review all instructions concerning safety procedures pro-
vided at the installation location. It is not possible to cover all
safety considerations in this manual; therefore, always be alert
and work safely. Only qualified system operators should per-
form the procedures covered in this manual.
WARNING SYMBOLS AND TERMS
This symbol on the unit indicates that the user
should refer to the operating instructions locat-
ed in the manual.
This symbol on the unit indicates that high
voltage may be present. Use standard safety
precautions to avoid personal contact with this
voltage.
This system indicates safety, earth ground.
1.0 PRODUCT INTRODUCTION
The Model 962 Portable Data Recorder manufactured by PCB
Load & Torque, is a battery-operated, transient recorder with two
transducer inputs that can be used with torque-only, torque-angle,
or load transducers. It can serve as a portable threaded fastener
laboratory for measuring fastener torque, angle of turn, and
clamp load. Ideal for performing fastener analysis, for auditing
and certifying power tools, and for testing hand torque wrenches;
Model 962 is a cost effective, versatile, and easy-to-use recorder
that can collect numeric peak data, XY graphic plots, and store
the data to a thumb drive or PC. The data can be easily displayed
or printed on the PC running FastPlot2 software. The alphanu-
meric setup and calibration menus assure ease of operation. The
unit can be used with all RS Technologies' rotary torque-angle
and clamp force transducers and other conventional and industry-
standard strain gage transducers.
The Model 962 can print out a numeric data report that contains
basic information about the test along with time and date-
stamped data for peak torque, angle of turn, clamp load, and
torque at tension data. Statistics including high, low, mean, ±3
Sigma, etc. are calculated and included on this report. The nu-
meric test data and the graphic data can be uploaded to a com-
puter via the USB port using the FastPlot2 data transfer and plot-
ting utility. FastPlot2 can also provide additional graphic analy-
sis.
1.1 Equipment
Please review the packing list to ensure that all equipment or-
dered has been received. Depending on the order, it may include
any or all of the following (*indicates option at extra cost):
•Model 962 Recorder
•USB Cable (type A/B)
•FastPlot2 Software
•Battery Charger Module
•Carrying Case with Strap
•Calibration Certificates (for instrument & optional
transducers)
•Torque/Torque-Angle Sensor(s)*
•Fastener Load Washer(s)*
•Clamp Load Cell(s)*
•Transducer Cable*
•Load Cell Cable*
•Transducer Junction Box*
In the event that some equipment is missing or damaged, please
contact the freight carrier, your customs broker and the PCB
Load & Torque factory.
Indicates a potentially dangerous situation, which can lead to mi-
nor or moderate injury or property damage. It may also be used to
alert against unsafe practices.
CAUTION
Indicates a potentially dangerous situation, which can lead to se-
vere personal injury or death. Always read the associated infor-
mation very carefully before performing the indicated procedure.
WARNING
Indicates an imminently dangerous situation, which can lead to
severe personal injury or death.
DANGER

RS Products from PCB Load & Torque Toll-Free in USA 866-684-7107 716-684-0001 www.pcb.com
MODEL 962 RECORDER OPERATION MANUAL 6
1.2 Important Features
The Model 962 has some important features which may be help-
ful to understand prior to use.
1.2.1 Display Modes
The Model 962 has two display operating modes: Peak mode will
display the Peak values for torque, angle, and load; Track mode
will display the torque or load currently being applied to the
transducer or load cell. Press the TASK button to toggle between
the peak and track modes.
1.2.2 Input Channels
Channel 1 is primarily designed to measure torque or torque and
angle. Channel 1 is the trigger channel. You will set a threshold
or cycle start value for Channel 1 that will initiate the recording
cycle. Channel 2 is primarily designed for load measurement
using a clamp load cell or fastener load washer. You cannot
trigger the recording process using Channel 2.
1.2.3 Limit Results Data/XY Graphic Plot Data
The Model 962 generates two kinds of data. The numeric limit
results data, which includes time/date stamped peak torque, angle
at peak, peak clamp, etc., is stored on-board the Model 962. Af-
ter 3 runs are recorded, the Model 962 will calculate statistics for
the recorded limits data and display some of which on the Main
Screen. It will provide all statistics on the limit results printout
and in a file that can be uploaded to a PC via FastPlot2.
The other form of data is the XY graphic plot data which in-
cludes all of the data samples recorded during the test. This data
is used to construct various graphs and plots either displayed on
the screen or after being uploaded to a PC. This graphic data is
saved either onto a USB drive or uploaded after each run to a PC.
1.2.4 USB Ports
There are two USB ports provided on the Model 962. The USB
A port is used to store data onto a USB memory stick/thumb
drive or to send reports and graphs to a HP Deskjet USB printer.
The USB B port is used to exchange information between the
Model 962 and a desktop or laptop PC using the FastPlot2 appli-
cation provided with the 962.
1.2.5 Instrument Operating Status
The lower left corner of the Main Screen will show the operating
status of the Model 962. It will read one of the following:
“Ready” indicates that the instrument is armed and ready to
begin a new test once the threshold/cycle start value for Channel
1 is reached. The Model 962 is put into Ready status either au-
tomatically through test setup, or manually by pressing the
MAIN key.
“Incyc” means the Model 962 is in a recording cycle.
“Done” indicates that recording has been completed.
2.0 SAFETY PRECAUTIONS
3.0 OVERVIEW
3.1 Specifications
Table 1 - Specifications
The Model 962 should not be opened by anyone other than factory
personnel. There are no user serviceable parts inside of the Mod-
el 962 recorder. Attempting to service the Model 962 will void the
warranty and could result in damage to the recorder.
CAUTION
Cables can damage your equipment. High voltage electrostatic
discharge can damage electrical devices. Similar to a capacitor, a
cable can hold a charge caused by tribo-electric transfer, such as
that which occurs in the following:
1. Laying on and moving across a rug.
2. Any movement through air.
3. The action of rolling out a cable.
4. Contact with a non-grounded person.
The solutions for ensuring product safety:
1. Connect the cables only with power switched OFF.
2. Temporarily “short” the end of the cable before attaching
it to any signal input or output.
CAUTION
Torque and Force Input Channels
Input Range
:
±
2.5 mV/V,
±
4.5 mV/V,
±
2.5 VDC
Excitation
:
5 VDC, 120 mA Maximum
Resolution
:
18-bit
Non
-
Linearity:
0.25% Maximum (F.S.)
Frequency R
e-
sponse:
10 kHz
Positive Voltage
Peak Trap Circuit: 7µs Reset Time
Peak Threshold:
Software Programmable
Peak Reset: Manual or Software Programmable (Automatic
Reset)
Angle Input
Channel
Type:
Quadrature A/B Track
Excitation:
5 VDC
Input Frequency:
1000 kHz maximum
Display
Viewing Area:
4.85 in x 2.68 in (123 mm x 68 mm)
Resolution:
240 x 128 Pixels, Backlit LCD
Battery
Indication:
Battery Low Indication
Battery Life:
8 Hours Maximum, Continuous Use
Charge Time:
3.5 Hours Maximum
General
Temperature
Range:
+32
°
F to +122
°
F (0
°
C to +50
°
C) Non-Condensing
Weight:
6.0 Lb (2.7 kg)

RS Products from PCB Load & Torque Toll-Free in USA 866-684-7107 716-684-0001 www.pcb.com
MODEL 962 RECORDER OPERATION MANUAL 7
3.2 Dimensions
3.3 Connector Panel
The following describes the connector panel features.
TTL/IO: RS232 port provides for connection to data
recorders or other devices.
Channels 1 & 2:
Typical setup is Channel 1 is set to torque
with a torque-only or torque-angle trans-
ducer, and Channel 2 is set to force with a
clamp load cell or fastener load cell.
ON/OFF
Switch: The power switch turns the Model 962 on
and off.
Battery
Charger Indi-
cator LED:
LED will be lit when the internal battery is
charging
Battery
Charger Jack: Receptacle for the battery charger.
USB Port A:
Provides for connection to a local USB
printer (HP DeskJet compatible), or a flash
drive memory stick to store numeric data,
graphical data, test setups, and torque
transducer/load cell definitions.
USB Port B:
Provides for connection to a desktop or
laptop PC to upload recorded data, test
setups, and tool definitions, or to download
test setups, tool definitions, or program
updates, using included FastPlot2 soft-
ware.
3.4 Connector Pinouts
This section describes the pinouts for the TTL/IO and channel
connectors.
3.4.1 TTL/IO Pinouts
Pin
Function
Pin
Function
1 DGnd 14 Din4
2 RX1 15 DOut4
3 TX1 16 N.C.
4 RTS1 17 +5VDC
5 CTS1 18 DIn0
6 DSR1 19 DOut0
7 DGnd 20 DTR1
8 DCD1 21 DGnd
9 Analog_Out 22 RI1
10 DGnd 23 DIn1
11 DOut1 24 DIn2
12 DOut2 25 DIn3
13 DOut3
Figure 1 - Dimensions
Table 2 – Mating Connectors
3.07 in
(77.9 mm)
8.50 in
(215.9 mm)
10.12
in
(257.0 mm)
TTL/IO
CH 2 CH 1
CHARGER
USB A USB B
TTL/IO
Channel 2
Channel 1
ON/OFF
Switch
Battery
Charger
Indicator
LED
Battery
Charger
Jack
USB
Port A
USB
Port B
Figure 2 – Connector Panel
Mating Connectors
Channel 1, Channel 2
:
DB, 15 Pins
TTL/IO
:
DB, 25 Pins
USB Port A
:
A Type
USB Port B:
B Type
Table 3 – TTL/IO Pinout
16
17
18
19
20
14
15
21
22
23
24
25
1
2
5
4
3
6
7
8
9
10
11
12
13
Figure 3 – DB 25 Pinout

RS Products from PCB Load & Torque Toll-Free in USA 866-684-7107 716-684-0001 www.pcb.com
MODEL 962 RECORDER OPERATION MANUAL 8
3.4.2 Channel 1 & Channel 2 Pinouts
Pin
Function
Pin
Function
1 -Signal 9 +Excitation
2 +Signal 10 -Excitation
3 GS1 (see below) 11 GS3
4 GS2 (see below) 12 GS4 (see below)
5 Analog Ground 13 Shunt
6 Transducer Type 14 Encoder A *
7 Encoder 5V * 15 Encoder B *
8 Digital Ground
* Channel 1 only
A jumper MUST be added when wiring a connector for the
Model 962 in order to scale the output of the transducer or input
device properly unless the device output is ±2.5 VDC. The
proper jumper positions are detailed in Table 4a below.
Jumper Position
Signal Level
3 & 12 Up to 2.5 mV/V
4 & 12 Up to 4.5 mV/V
None Up to 2.5 VDC
3.4.3 Connecting a High Level Device
When connecting a high level input signal (±2.5 VDC) to the
Model 962, connect a jumper between pins 1-5 on the DB 15
connector. Then connect the high level signal to pins 2 (+) and 1
(-) (also see Table 4).
3.5 Battery Use & Recharging
The Model 962 can operate for up to 8 hours on a fully charged
internal battery. Battery and charger specs are list in Table 5.
NOTE: It is recommended that the instrument operate on battery
power alone to minimize the interference of electrical
noise in the acquired data.
3.6 Calibration Shunt Resistors
Calibration shunt resistors are used to scale the output values of
the sensors used. The sensor’s calibration value is matched to a
calibration shunt resistor and can be found on the sensor’s cali-
bration certificate. Attach the resistor(s) as shown in Figure 5.
3.7 File Types
There are four types of data that the Model 962 uses to store and
upload its setup and recorded data, numeric results data, graphic
plot data, test setup data, and tool definition data. The files can
be saved on a USB flash drive or downloaded to a PC via the
FastPlot2 software. The following describes the file types used
in the Model 962.
.results: File type that contains the numerical test results and the
statistical summary data for the test. (Also can be in
the form of M*.* when saved to the USB flashdrive)
.test:
File type that contains all of the data points used to
make up the data plots for the individual test. (Also
can be in the form of D*.* when saved to the USB
flashdrive)
.stp: File type that contains individual test setup data.
.xdf: File type that contains individual tool definition data.
NOTE: Limit results and XY plot data files saved to a flashdrive
are saved in a format based on the date and time. For ex-
ample, a limit results file is saved as Mmmddyym.mss,
where M = file type (limit results), mm = month, dd=day,
yy=year, m.m = minute, ss=second. A XY plot data file is
saved as Dmmddyym.mss using the same convention.
3.8 Keypad
The Model 962 software utilizes easy to use menu driven naviga-
tion. Navigation and input of data is performed using the keypad
located on the front of the meter. See Figure 6 below.
Table 4 – Channel 1 & Channel 2 Pinouts
1 2 5
43 6 7 8
9 10
13
12
11
14
15
Figure 4 – DB 15 Pinout
TTL/IO
CH 2 CH 1
CHARGER
USB A USB B
Channel 2 Calibration
Shunt Resistor
Channel 1 Calibration
Shunt Resistor
Figure 5 – Calibration Shut Resistors
Battery/Charger
Battery:
10.8 VDC NiMH 2700 mAh
Charger:
18 VDC 1000 mA
Table 5 – Battery/Charger
SETUP
MAIN
PRINT
UTILS
STORE
CAL
ESC
ENTER
TASK
RECALL
7
A
4
A
1
A
-
A
8
A
9
A
5
A
2
A
0
A
6
A
3
A
.
Figure 6 – Model 962 Keypad
Table 4a – Connector Jumper Position

RS Products from PCB Load & Torque Toll-Free in USA 866-684-7107 716-684-0001 www.pcb.com
MODEL 962 RECORDER OPERATION MANUAL 9
The following describes the operations of the individual buttons
on the keypad.
MAIN:
When Auto Reset is disabled, this button sets
the Model 962 to be ready to perform a test.
When not in the Ready mode no data can be
collected. Must be on the MAIN SCREEN to
use this button. See Section 4.2.
SETUP:
Press this button to enter the SETUP MENU.
The SETUP MENU displays options to create
and edit recording parameters along with vari-
ous data analysis settings. Must be on the
MAIN SCREEN to use this button. Refer to
Section 4.3.
PRINT:
Press this button to enter the PRINT /DISK
MENU. The PRINT/DISK MENU displays
options to print or transfer numeric results, XY
data, test setups, and tool definitions.
UTILS:
Press this button to enter the UTILITY MENU.
The UTILITY MENU displays options to
change settings, clear memory, and perform
diagnostic functions.
STORE: Press this button to manually update the numer-
ical test results file. Must be on MAIN
SCREEN and AutoStore must be disabled.
CAL:
Press this button to enter the CALIBRATION
MENU. The CALIBRATION MENU displays
options to calibrate the transducers to the Mod-
el 962 as well as add and edit transducers to the
tool libraries.
ARROWS
(): Use the up and down arrow buttons to navigate
through various menus or setup screens.
ESC: Press this button to escape from a screen to the
previous screen.
ENTER: Press this button to save changed settings in
various screens.
TASK: Press this button to toggle between Peak and
Track display modes. Must be on the MAIN
SCREEN to use this button. See Section 4.2.
RECALL: This button has no currently assigned function.
1-9,.,-:Use these buttons to enter numeric data in vari-
ous setup fields.
4.0 SCREENS AND MENUS
The Model 962 software utilizes various screens and menus to
set up and perform the test, and to analyze the recorded data.
The following sections give a brief overview of the various
screens and menus.
4.1 Introductory Screen
When the Model 962 is powered up (using the “rocker-style”
power switch located on the connector panel) the Introductory
Screen is displayed. See Figure 7.
NOTE: The version number may be needed for some technical
support.
The Introductory Screen will remain active for a few seconds,
after which a calibration screen asking that you “zero” (refer to
Figure 30) the enabled channels is displayed or the Model 962
will search to see if any “smart” transducers that include an ID
chip are connected (refer to Section 4.6.4).
4.2 Main Screen
The MAIN SCREEN is the screen that is shown when a test is
performed. It will appear automatically after the powering up
sequence and acts as a “home” screen to activate the various
menus available in the Model 962. The MAIN SCREEN con-
tains the real-time plot data along with channel and statistical
values. See Figure 8 below.
The top section of the screen displays either the peak or track
data readings from the enabled channels. The meter is in the
peak mode if “pk” is visible in the top right corner of the MAIN
SCREEN as shown in Figure 8. If “pk” is not visible then the
meter is in track display mode.
MODEL 962 RECORDER
Torque-Angle Monitor
VERSION 7F-R1
PCB Load & Torque
24350 Indoplex Circle
Farmington Hills, MI 48335
Tel: 248-888-8260
Fax: 248-888-8266
Figure 7 – Introductory Screen
Figure 8 – MAIN SCREEN

RS Products from PCB Load & Torque Toll-Free in USA 866-684-7107 716-684-0001 www.pcb.com
MODEL 962 RECORDER OPERATION MANUAL 10
The Model 962 can toggle between Peak and Track display
modes by pressing the TASK button when the MAIN SCREEN
is displayed. The Peak and Track modes are described below.
Peak Display
Mode:
Displays the maximum data the chan-
nel read on the previously recorded
rundown.
Track Display
Mode:
Displays the real-time data that the
channel is currently reading. Track
Display Mode data does not get saved
to memory.
NOTE: Only data for enabled channels will be displayed.
The MAIN SCREEN (see Figure 9) includes a real-time plot to
graphically display the current test data as it is being recorded.
Along the right side of the screen are the statistical values calcu-
lated on the test cycles saved for Channel 1. The number of run-
downs from which the statistics are calculated is displayed in the
bottom right corner Cyc#.
NOTE: A minimum of 3 cycles need to be saved in order to
view the statistics.
Data recording can only be performed when viewing the MAIN
SCREEN and when in the Ready mode. The Model 962 is in the
Ready mode when “Ready” is displayed in the bottom left corner
of the MAIN SCREEN as shown in Figure 9. The screen will
display “Done” if not in the Ready mode.
NOTE: If Auto Reset is disabled, press the MAIN button when
viewing the MAIN SCREEN to set the Model 962 to
Ready mode. If Auto Reset is enabled the meter will
automatically switch to the Ready mode after a set
amount of time (refer to Section 4.3.6).
NOTE: The Model 962 does not have to be in the Ready mode
to read Track Data to the screen.
NOTE: The Model 962 must be displaying the Main Screen
before starting up the FastPlot2 software (refer to Sec-
tion 6 for more on FastPlot2).
4.3 Setup Menu
The SETUP MENU displays options to create and edit recording
parameters along with various data analysis settings. This menu
can be viewed by pressing the SETUP button when on the MAIN
SCREEN. See Figure 10.
4.3.1 Channels Setup
Configure the data acquisition channels in the SETUP MENU by
pressing the 1 button on the keypad. The CHANNELS SETUP
screen is where the channel type is specified and the transducer is
selected. See Figure 11.
Navigate the CHANNELS SETUP screen using the Arrow ()
buttons on the keypad. Press ESC to exit back to the SETUP
MENU.
The Channel 1 Configuration is described below.
Type:
Press the 1 button on the keypad to toggle the
Channel 1 type between TORQUE and
FORCE. This should match to the sensor
type connected to Channel 1.
Angle: Press the 2 button on the keypad to ENABLE
or DISABLE the ability to measure Angle on
Channel 1.
Angle
Count:
Press the 3 button on the keypad to toggle the
Angle Count setting between ONEWAY and
TWOWAY.
Transducer:Press the 4 button on the keypad to select a
transducer from a user-defined transducer
library (refer to Figure 33).
1) Channels SetupSETUP MENU
2) Units: Nm, N, mm
3) Direction: CW
4) Set Torque Limits
5) Set Recording Time
6) Set Auto Options
7) Torque-Force Pts
8) Analysis Setup
9) Set Report Format
Make Selection or <ESC>: Exit.
Ready
Figure 9 – MAIN SCREEN – Ready Mode
Figure 10 – SETUP MENU
Channel 1 CHANNELS SETUP
1) Type: TORQUE
2) Angle: ENABLED
3) Angle Count: TWOWAY
4) Transducer: 03923
Channel 2
5) Inputs: ENABLED
6) Type: FORCE
7) Transducer: 59810
Make Selection or <ESC>: Exit.
Figure 11 – CHANNELS SETUP Screen

RS Products from PCB Load & Torque Toll-Free in USA 866-684-7107 716-684-0001 www.pcb.com
MODEL 962 RECORDER OPERATION MANUAL 11
Set the Angle Count to ONEWAY to allow for angle measure-
ments to be positive for both clockwise (CW) and counter-
clockwise (CCW) movements. Set the Angle Count to TWO-
WAY to allow for positive and negative angle measurements.
Figure 12 illustrates the difference between ONEWAY and
TWOWAY Angle Counts.
NOTE: Most test setups will require the Angle Count to be set
to TWOWAY.
NOTE: Angle measurements can only be performed with torque
transducers with angle measuring capabilities. Angle
values will read zero if the torque transducer cannot
read angle or if the channel type is set to force even if
Angle is set to ENABLE.
After a transducer has been selected, the channel precision needs
to be set. Channel precision refers to how many digits to the
right of the decimal place will be visible. The SET CHANNEL
PRECISION screen is shown in Figure 13
Navigate the SET CHANNEL PRECISION screen using the
Arrow () buttons on the keypad. Use the numeric buttons on
the keypad to input the values. Press the ENTER button to save
the values and press ESC to exit back to the CHANNELS SET-
UP screen.
NOTE: A transducer definition will need to be set up prior to
being able to select one from the library.
The Channel 2 Configuration is described below.
Inputs:
Press the 5 button on the keypad to ENABLE
or DISABLE Channel 2 data acquisition. If
there is no sensor attached to Channel 2 then it
should be set to DISABLED.
Type:
Press the 6 button on the keypad to toggle the
Channel 2 type between TORQUE and
FORCE. This should match to the sensor type
attached to Channel 2.
Transducer:
Press the 7 button on the keypad to select a
transducer from a user-defined transducer
library (refer to Figure 33). Set CHANNEL
PRECISION after selecting a transducer (see
Figure 13).
NOTE: A typical setup is Channel 1 set to torque and Channel 2
is set to force. Depending on application, channels can
be set to either both torque or both force. Never set
Channel 1 to force while having Channel 2 set to torque.
NOTE: A transducer definition will need to be set up prior to
being able to select one from the library. Refer to Sec-
tion 4.4.4.
4.3.2 Units of Measure
The displayed and recorded units of measure are established in
the SETUP MENU by pressing the 2 button on the keypad. Re-
peatedly pressing the 2 button will toggle through the available
unit choices. The units displayed are the units that the meter is
currently set for. Table 6 shows the order of the available units
as they are toggled.
4.3.3 Direction
The angle direction that is considered positive is set in the SET-
UP MENU by pressing the 3 button on the keypad. Repeatedly
pressing the 3 button will toggle between CW and CCW. If CW
is selected, then clockwise will be considered the positive angle
direction. If CCW is selected, then counter-clockwise will be
considered the positive angle direction.
NOTE: Use CCW when recording loosening of right-handed
threads or when tightening left-handed threads.
Torque
Load
Dimension
lbft lb In
lbin lb In
ozin Oz In
Nm N mm
kNmm N mm
kgcm kg mm
kgm kg mm
Table 6 – Units
Figure 12 – Angle Count
SET CHANNEL PRECISION
CAL Tq (Nm): 15.0
Input Torque: 1
Angle: 0
Set No. of Places Aft Decimal.
<Arrow Keys>: Select Item.
<ENT>: Save <ESC>: Exit.
Figure 13 – SET CHANNEL PRECISION Screen

RS Products from PCB Load & Torque Toll-Free in USA 866-684-7107 716-684-0001 www.pcb.com
MODEL 962 RECORDER OPERATION MANUAL 12
4.3.4 Set Torque Limits
Set the Torque Limits by pressing the 4 button on the keypad
when viewing the SETUP MENU. The Torque Limits set the
recording parameters and visual target values for the real-time
plot on the MAIN SCREEN. See Figure 14 below.
Navigate the Set Torque Limits screen using the Arrow ()
buttons on the keypad. Use the numeric buttons on the keypad to
input the values. Press the ENTER button to save the values and
press ESC to exit back to the SETUP MENU.
NOTE: Setup values entered into the Model 962 will not be
saved unless the ENTER button is pressed.
The recording window is set using the Cycle Start, Cycle End,
and the Cycle End Time parameters. The recording cycle starts
once the Channel 1 data point designated by Cycle Start is meas-
ured. The recording cycle ends once the Channel 1 data set falls
below the Cycle End value for the time set by Cycle End Time.
This sequence is illustrated in Figure 15. The Cycle Start and
Cycle End parameters are described below.
Cycle Start:
The Channel 1 data point that triggers the start
of the data recording. This data point also
designates the starting point for measuring
angle.
Cycle End:
The Channel 1 data point that triggers that
begins the sequence for ending the data re-
cording. This value should be less than the
Cycle Start value.
Cycle End
Time:
The time value that the Channel 1 data pint
must be below the Cycle End value to end the
data recording.
NOTE: Data recording will end when either the Channel 1 input
drops below Cycle End for the length of the time in Cy-
cle End Time, or when the Full Scale data recording
time (see Section 4.3.5) is completed, whichever comes
first.
The Low, Target, and High Torque parameters are described
below.
Low Torque:
The Channel 1 data point that signifies the
minimum acceptable peak value. This
value is used to calculate The Cpk statistic.
Must be greater than Cycle Start.
Target Torque:
The Channel 1 data point that signifies the
target peak value. This value is displayed
on the real-time plot on the MAIN
SCREEN. Must be greater than Low
Torque and less than High Torque.
High Torque:
The Channel 1 data point that signifies the
maximum acceptable peak value. This
value is used to calculate the Cpk statistic
and is used to scale the real-time plot on
the MAIN SCREEN. Must se greater than
Target Torque.
Some additional features of the MAIN SCREEN are shown in
Figure 16 below.
4.3.5 Set Recording Time
Set the Recording Time by pressing the 5 button on the keypad
when viewing the SETUP MENU. The Recording Time parame-
ters establish a length for the recording window. See Figure 17.
Set Torque Limits
Cycle Start (Nm): 5.0
Cycle End (Nm): 4.0
Cycle End Time (sec): 2.0
Low Torque (Nm): 20.0
Target Torque (Nm): 25.0
High Torque (Nm): 30.0
<Arrow Keys>: Select Item.
<ENT>: Save <ESC>: Exit.
RECORDING TIME
Full Scale (sec): 10.0
Advance Time (sec): 2.0
<Arrow Keys>: Select Item.
<ENT>: Save <ESC>: Exit.
Figure 14 – Set Torque Limits Screen
Figure 15 – Recording Window Parameters
Figure 16 – MAIN SCREEN
High
Torque
Target
Torque
Cycle
Start
Cpk
Stat.
Figure 17 – RECORDING TIME Screen

RS Products from PCB Load & Torque Toll-Free in USA 866-684-7107 716-684-0001 www.pcb.com
MODEL 962 RECORDER OPERATION MANUAL 13
Navigate the Recording Time screen using the Arrow () but-
tons on the keypad. Use the numeric buttons on the keypad to
input the values. Press the ENTER button to save the values and
press ESC to exit back to the SETUP MENU.
NOTE: Input values will not be saved unless the ENTER button
is pressed.
The Recording Time parameters are described below and illus-
trated in Figure 18.
Full
Scale:
This value sets the duration of the test in sec-
onds. Be sure this value is set to a time period
long enough to record the entire test including
the Advance Time.
Advance
Time:
This value designates a portion of the Full Scale
time to record data prior to the Cycle Start value.
Any time set aside for recording prior to Cycle
Start must be accounted for when setting the
Full Scale time.
NOTE: The Recording Window is made up of parameters from
the Set Torque Limits (refer to Section 4.3.4) and the
Recording Time. If the Recording Time is not long
enough to capture the entire parameters set by the
Torque Limits the Recording Window will end when
the Recording Time runs out.
4.3.6 Set Auto Options
The Auto Options are set in SETUP MENU by pressing the 6
button on the keypad. This menu is illustrated in Figure 19.
Navigate the AUTO OPTIONS screen using the Arrow ()
buttons on the keypad. Press ESC to exit back to the SETUP
MENU. The Auto Options parameters are described as follows.
Auto
Reset:
When ENABLED, automatically resets the
Model 962 to the Ready mode after the test is
performed and the amount of time set in the Re-
set Time field elapses. When DISABLED, press
the MAIN button on the keypad to reset the
Model 962 to the Ready mode.
Reset
Time:
Amount of time designated in seconds that the
Model 962 will wait after a test to set the re-
corder back into the Ready mode. This parame-
ter is available only if the Auto Reset is ENA-
BLED.
AutoStore
Results:
When ENABLED, the numerical results of the
last recorded test are automatically stored into
the results memory. When DISABLED, the
STORE button on the keypad must be pressed to
store the numerical results of the last test into
the results memory (refer to Figure 6).
AutoStore
XYData:
When ENABLED, the XY (plot) data from the
last recorded test are automatically stored to a
USB drive placed in the USB A port (refer to
Figure 2). When DISABLED, the PRINT but-
ton on the keypad must be pressed to open the
PRINT/DISK MENU and store the graphic data
to the USB drive, or to the connected PC.
AutoSend
at EOT:
When ENABLED, a data packet is automatical-
ly sent via the RS232 port of the IO connector at
the end of each recorded test. The data packet
contains the numeric peak value results of the
test. Data is sent using 38400 baud, no parity, 8
bits, and 1 stop bit. When DISABLED, no End
Of Test data will be sent to the PC.
4.3.7 Torque-Force Points
The Torque-Force Points are set in SETUP MENU by pressing
the 7 button on the keypad. The Torque-Force Points are used to
pull a torque value at a specified load or a load value at a speci-
fied torque from the current test and place it in the results file.
NOTE: This feature is available only if Channel 2 is ENABLED
(refer to Section 4.3.1). To view data on the results re-
port, make sure that Torque-Force is ENABLED in the
REPORT FORMAT screen (refer to Section 4.3.9).
Enable desired options:
AUTO OPTIONS
1) Auto Reset: ENABLED
2) Reset Time (sec): 10
3) AutoStore Results: DISABLED
4) AutoStore XYData: DISABLED
5) AutoSend at EOT: DISABLED
Make Selection or <ESC>: Exit.
Select Point Type: FORCE
Set Torque-Force Points
FORCE-PT0 (N): 26689
FORCE-PT1 (N): 0
FORCE-PT2 (N): 0
FORCE-PT3 (N): 0
FORCE-PT4 (N): 0
PT=0 to Disable
<Arrow Keys>: Select Item.
<ENT>: Save <ESC>: Exit.
Figure 18 – RECORDING TIME Parameters
Figure 19 – AUTO OPTIONS Screen
Figure 20 – Set Torque-Force Points Screen

RS Products from PCB Load & Torque Toll-Free in USA 866-684-7107 716-684-0001 www.pcb.com
MODEL 962 RECORDER OPERATION MANUAL 14
Navigate the Set Torque-Force Points screen using the Arrow
() buttons on the keypad. Use the numeric buttons on the
keypad to input the values. Press the ENTER button to save the
values and press ESC to exit back to the SETUP MENU.
NOTE: Input values will not be saved unless the ENTER button
is pressed.
The Torque Force parameters are described below.
Select Point
Type:
With the box around the Select Point Type
field, press the ENTER button on the key-
pad to toggle between TORQUE and
FORCE. If TORQUE is selected then load
values will be pulled out of the data file at
the designated torque value. If FORCE is
selected then torque values will be pulled
out of the data file at the designated load
value. See Figure 21.
FORCE /
TORQUE PTS
0-4:
Using the numeric buttons on the keypad,
input the designated torque or force points.
Set the point to 0 (zero) to disable the
point.
4.3.8 Analysis Setup
Access the ANALYSIS MENU from the SETUP MENU by
pressing the 8 button on the keypad. Specialized data analysis
can be performed on the test data when the parameters from the
ANALYSIS MENU are set (see Figure 22). The results of the
analysis are placed in the results file.
4.3.8.1 Measurement Window Feature
This feature is used when testing may produce an initial spike
that should not be captured as the peak value, such as when using
an impulse-type tool. A window can be programmed at the end
of the data recording that will be used to determine the peak val-
ue. For example, if 5 seconds of data are recorded and the
Measurement Window is set to 4 seconds, only the last 4 seconds
of data will be used to determine the peak value; any peak torque
that occurs during the first 1 second of data is ignored. Set this
window by pressing the 1 button on the keypad from the
ANALYSIS MENU to display the screen shown in Figure 23.
The Measurement Window parameters are described below.
Window
Type:
Press the 1 button on the keypad to toggle be-
tween TIME, ANGLE, and OFF. Set the Win-
dow Type to TIME or ANGLE to set a window at
the end of the recording time. Set the Window
Type to OFF to disable this feature.
Window
Size:
Press the 2 button on the keypad to set the Win-
dow Size in units of either seconds or degrees.
Once a value has been input press the ENTER
button on the keypad to save the entry.
4.3.8.2 M-Alpha Feature
Enable the M-Alpha torque-angle signature analysis method by
pressing the 2 button while in the ANALYSIS MENU. The M-
Alpha method is used to estimate the amount of clamp load
(force) in a bolted joint by studying the torque-angle relationship.
See Figure 24.
NOTE: To view data on the results report, make sure that M-
alpha Data is ENABLED in the REPORT FORMAT
screen (refer to Section 4.3.9).
1) Measurement Window
ANALYSIS MENU
2) M-Alpha
3) Friction Coefficient
Make Selection or <ESC>: Exit.
1) Window Type: TIME
Measurement Window Parameters
2) Window Size (sec): 1.0
Make Selection or <ESC>: Exit.
Figure 21 – Torque-Force Points
Figure 22 – ANALYSIS MENU
Figure 23 – Measurement Window Parameters Screen
Figure 24 – M-Alpha Parameters Screen
1) Lower Tangent Tq: ENABLED
M-Alpha Parameters
2) Percent of Peak: 80
Make Selection or <ESC>: Exit.

RS Products from PCB Load & Torque Toll-Free in USA 866-684-7107 716-684-0001 www.pcb.com
MODEL 962 RECORDER OPERATION MANUAL 15
The M-Alpha parameters are described below.
Lower
Tangent
Tq:
Press the 1 button on the keypad to ENABLE or
DISABLE this function. When ENABLED, the
clamp angle (see Figure 25) from the M-Alpha
process will be included on the results file.
Percent
of Peak:
When the Lower Tangent Tq is set to ENABLE
press the 2 button on the keypad to set the Per-
cent of Peak to establish a point to project a tan-
gent line through using the peak torque value as
the second point (see Figure 25). It is important
that both the Peak and the Percent of Peak val-
ues lie within the elastic tightening zone. Once a
value has been input press the ENTER button on
the keypad to save the entry.
NOTE: For more information on the M-Alpha Torque-Angle
Signature Analysis Methods refer to Section 7.
4.3.8.3 Friction Coefficient
Enable friction coefficient analysis by pressing the 3 button
while in the ANALYSIS MENU. See Figure 26. The Reference
Friction Parameters are used to calculate the Reference friction
coefficient per the DIN 946 specification.
NOTE: This feature is only available when Channel 2 is enabled
and set to FORCE. To view data on the results report,
make sure that Friction Data is ENABLED in the RE-
PORT FORMAT screen (refer to Section 4.3.9).
NOTE: The Reference friction coefficient of the DIN 946 speci-
fication is calculated with the same equations used for
the Total friction coefficient of the ISO 16047 specifica-
tion.
Navigate the Reference Friction Parameters screen using the Ar-
row () buttons on the keypad. Use the numeric buttons on the
keypad to input the values. Press the ENTER button to save the
values and press ESC to exit back to the SETUP MENU.
NOTE: Input values will not be saved unless the ENTER button
is pressed.
The Friction parameters are described below.
Calc
Friction
At:
With the box around the Calc Friction At field,
press the ENTER button on the keypad to toggle
between FORCE and TORQUE. If FORCE is
selected, then a clamp load value will be specified
at which the Reference friction coefficient is cal-
culated. If TORQUE is selected, then a torque
value will be specified at which the Reference
friction coefficient is calculated.
Clamp /
Torque:
Use the numeric buttons to enter a value at which
the Reference friction coefficient will be calculat-
ed. Once a value has been input press the ENTER
button on the keypad to save the entry.
Nominal
Dia: The nominal diameter of the fastener being tested
(see Figure 27).
Pitch: Thread pitch of the fastener being tested (see Fig-
ure 27).
Bearing
Dia: The bearing diameter of either the bolt head or nut
(whichever one is being turned (see Figure 27).
Thru Dia: The through hole diameter of the washer (see Fig-
ure 27).
NOTE: Thread Pitch is determined as the length or width of the
thread. For example, a metric fastener may be specified
as a M10 x 1.5. M10 indicates nominal diameter of 10
mm and the thread pitch of 1.5 mm. For English fasten-
ers, an additional calculation is needed to determine
thread pitch. For example, an English fastener may be
specified as a 3/8-20 with 3/8 being the nominal diame-
ter (3/8-inch = 0.375 in) and 20 indicating 20 threads
per inch. To determine the thread pitch, divide 1 by the
threads per inch to get the width of the threads in inches
(1 / 20 = 0.05 in).
Figure 25 – M-Alpha Analysis
Figure 26 – Reference Friction Parameters Screen
Figure 27 – Fastener Dimensions for Friction Calculations
Reference Friction Parms
Calc Friction at: FORCE
Clamp (N): 26689
Nominal Dia (mm): 10.00
Pitch (mm): 1.50
Bearing Dia (mm): 15.00
Thru Dia (mm): 10.50
<Arrow Keys>: Select Item.
<ENT>: Save <ESC>: Exit.

RS Products from PCB Load & Torque Toll-Free in USA 866-684-7107 716-684-0001 www.pcb.com
MODEL 962 RECORDER OPERATION MANUAL 16
4.3.9 Set Report Format
The results file can be customized to show as much or as little
data as needed. Set the REPORT FORMAT in the SETUP
MENU by pressing the 9 button on the keypad. See Figure 28.
Press the keypad number that corresponds with the report data to
ENABLE/DISABLE the data. ENABLE the data to include it in
the results file. DISABLE the data to omit it from the results
file.
4.4 Calibration Menu
The CALIBRATION MENU displays options to calibrate the
attached transducers to the meter, “zero” the channels, add trans-
ducers to the library, or edit existing transducers in the library.
This menu can be viewed by pressing the CAL button when on
the MAIN SCREEN. See Figure 29.
Calibration operations scale the output of the transducer to the
meter to insure that the voltage readings by the meter translate to
the proper torque or load measurements.
4.4.1 ZERO Only
ZERO the data acquisition channels in the CALIBRATION
MENU by pressing the 1 button on the keypad. See Figure 30.
The CHANNELS SETUP ZERO screen is where the enabled
channels zeroing operation is performed. This includes sending
zero volts through the attached unloaded transducers and record-
ing the output. The Model 962 uses this output as the reference
for unloaded conditions and makes sure that no artificial offsets
are present in the collected data.
Unload the enabled channels and press the ENTER button on the
keypad to perform the operation.
NOTE: It is recommended that a ZERO operation be performed
after the channels are calibrated.
4.4.2 AUTO Calibration
AUTO Calibration refers to the operation of automatically cali-
brating the transducer to the Model 962 using the shunt calibra-
tion method. The operation consists of the meter using a preci-
sion resistor (mounted on the binding posts of the meter) to simu-
late an output signal and scaling the simulated output to the de-
fined calibration value. The AUTO CALIBRATION MENU is
accessed through the CALIBRATION MENU by pressing the 2
button on the keypad. See Figure 31.
From the AUTO CALIBRATION MENU press the 1 button on
the keypad to AUTO calibrate Channel 1 and press the 2 button
on the keypad to AUTO calibrate Channel 2. When prompted
make sure the appropriate channel is unloaded and then press the
ENTER button on the keypad. The Model 962 will perform a
zero balance check and display “Zero Taken”, it will then per-
form an automatic shunt calibration and should display “Shunt
Calibration Successful”. This procedure should be performed for
both channels if enabled.
NOTE: An error will occur if an acceptable voltage change be-
tween the zero and shunted reading is not measured. In
the case of an error, the AUTO calibration will be
aborted. If an error occurs check to make sure the
transducers connections are tight and also check to see
that the shunt calibration resistors are installed correctly.
Torque (Nm): CALIBRATION MENU
Model: 03923 PPR: 1440
F.S.: 67.0 CAL: 68.0
CH2-Force (N):
Model: 59810
F.S.: 25000 CAL: 23830
UNLOAD TRANSDUCERS!
Press <ENT>: for ZERO.
Enable desired report data:
REPORT FORMAT
1) Enabled Channels: ENABLED
2) Test Setup: ENABLED
3) Standard Results: ENABLED
4) Torque-Force: DISABLED
5) Friction Data: DISABLED
6) M-alpha Data: DISABLED
Make Selection or <ESC>: Exit.
Figure 28 – REPORT FORMAT Screen
1) ZERO Only CALIBRATION MENU
2) AUTO Calibration
3) MANUAL Calibration
4) Add/Edit Torque Transducer
5) Add/Edit Force Transducer
Make Selection or <ESC>: Exit.
Figure 29 – CALIBRATION MENU
Figure 30 – CALIBRATION MENU ZERO Screen
1) Torque Channel
CALIBRATION MENU
2) CH2-Force Channel
Make Selection or <ESC>: Exit.
Figure 31 – AUTO CALIBRATION MENU

RS Products from PCB Load & Torque Toll-Free in USA 866-684-7107 716-684-0001 www.pcb.com
MODEL 962 RECORDER OPERATION MANUAL 17
The CALIBRATION MENU will display automatically after this
operation.
NOTE: It is recommended that a ZERO operation be performed
after a calibration operation (refer to Section 4.4.1).
4.4.3 MANUAL Calibration
MANUAL Calibration refers to the operation of manually cali-
brating the transducer to the Model 962. The operation consists
of the meter sending a zero voltage through the attached trans-
ducer to get a baseline. A calibration load is then applied to the
transducer. The resulting output signal is read by the Model 962
and used to scale the meter’s gain. The MANUAL CALIBRA-
TION MENU is accessed through the CALIBRATION MENU
by pressing the 3 button on the keypad. See Figure 32.
From the MANUAL CALIBRATION MENU press the 1 button
on the keypad to MANUALLY calibrate Channel 1 or press the 2
button on the keypad to MANUALLY calibrate Channel 2.
When prompted make sure the appropriate channel is unloaded
and then press the ENTER button on the keypad. The Model 962
will perform a zero balance check and display “Zero Taken”.
Manually apply the calibration load load to the transducer and
press the ENTER button on the keypad. The voltage difference
will be measured and the outputs will be scaled accordingly.
This procedure should be performed for both channels if enabled.
NOTE: The MANUAL Calibration can be performed if an au-
tomatic shunt calibration is not possible, or if you have
access to a certified load or torque application device. It
requires accurate calibration loading to ensure accurate
results.
NOTE: It is recommended that a ZERO operation be performed
after a calibration operation (refer to Section 4.4.1).
4.4.4 Add/Edit Torque/Force Transducer
The Model 962 allows for storage of transducer definitions for
ease of transducer selection when setting up a test. Adding and
editing stored transducers can be accessed through the CALI-
BRATION MENU by pressing the 4 key for torque transducers
or 5 key for load cells on the keypad. See Figure 33.
Navigate the Add/Edit Transducer screen using the Arrow ()
buttons on the keypad. Place the box around a currently defined
transducer and press the ENTER button to edit the definition.
See Figure 34. Place the box around a blank space (at end of list)
and press the ENTER button to add a new definition. Press the
ESC button to exit back to the CALIBRATION MENU.
NOTE: The load cell definition screens are identical to the
torque screens except they do not have a field for Pulses
Per Rev (PPR).
Navigate the DEFINE TOOL MENU screen using the Arrow
() buttons on the keypad. Place the box around a field and
use the numeric buttons to input the definitions. The transducer
definition parameters are described below.
Model No: Define the transducer with a model number
(up to 5 digits).
Serial No: Define the transducer with a serial number (up
to 8 digits).
FS Tq/Force:
Input the full scale torque or load value of the
transducer. This value can be found on the
unit’s calibration certificate. Make sure the
proper units are current (refer to Section
4.3.2)
Cal Tq/Force:
Input the calibration torque or load value of
the transducer. This value can be found on
the unit’s calibration certificate. Make sure
the proper units are current (refer to Section
4.3.2)
Model# (Nm) (Nm) PPR
F.S. Cal
02727 813.5 813.8 2898
03922 15.0 15.0 1440
03923 67.8 68.0 1440
12548 67.8 68.1 1440
39050 136.0 136.0 0
39225 0.0 0.0 0
<Arrow Keys>: Select Tool.
<ENT>: Select <ESC>: Exit.
DEFINE TOOL MENU
Model No: 03922
Serial No: 51069
FS Tq (Nm): 15.0
Cal Tq (Nm): 15.0
Pulses Per Rev: 1440
PPR=0 FOR TOOLS W/NO ANGLE
<Arrow Keys>: Select Item.
<ENT>: Save <ESC>: Exit.
Figure 33 – Add/Edit Torque Transducer Screen
Figure 34 – DEFINE TOOL MENU Torque Screen
Figure 32 – MANUAL CALIBRATION MENU
1) Torque Channel
CALIBRATION MENU
2) CH2-Force Channel
Make Selection or <ESC>: Exit.

RS Products from PCB Load & Torque Toll-Free in USA 866-684-7107 716-684-0001 www.pcb.com
MODEL 962 RECORDER OPERATION MANUAL 18
Pulses Per
Rev:
Input the pulses per revolution to define the
angle encoder of the torque transducer. This
value can be found on the unit’s calibration
certificate. This value is not applicable for
load cells.
NOTE: Input values will not be saved unless the ENTER button
is pressed.
4.5 Print/Disk Menu
The PRINT/DISK MENU displays options to print, save, and
download the test data. View this menu by pressing the PRINT
button on the keypad when on the MAIN SCREEN. See Figure
35.
4.5.1 Printer
To print directly from the Model 962, press the 1 button while in
the PRINT/DISK MENU to open the PRINTER MENU. See
Figure 36. The numerical results file or various test plots can be
directly printed to a USB HP Desk Jet-compatible printer con-
nected to the USB A port.
4.5.1.1 Print Results
Press the 1 button on the keypad when in the PRINTER MENU
to print the Limit Results file directly to a HP Desk Jet-
compatible printer connected to the USB A port.
4.5.1.2 Print XY Plot
Press the 2 button on the keypad when in the PRINTER MENU
to open the SELECT XY PLOT MENU. See Figure 37.
Press the numeric number button on the keypad corresponding to
the desired test plot to view the plot on screen. Once the plot is
displayed on the screen, press the PRINT button on the keypad to
send the plot directly to a printer or press the ESC button on the
keypad to escape back to the SELECT XY PLOT MENU.
NOTE: XY Plot choices depend on meter setup. If angle is not
enabled, the angle choices are not displayed. If a load
cell is not being used, the load/force choices are not dis-
played.
4.5.2 USB Drive
To save data to a USB flash drive from the Model 962, press the
2 button while in the PRINT/DISK MENU to open the USB
DISK DRIVE MENU. See Figure 38. The results files, run-
down files, setup files, and tool definitions can be saved to a
USB flash drive via the USB A port. Using this menu, test set-
ups and tool definitions can be uploaded from a flash drive to the
Model 962.
The USB drive options are described below.
Results File
Disk:
Press the 1 button on the keypad to save
the currently stored numeric data results to
a USB flash drive in port USB A (refer to
Figure 2).
1) Printer PRINT/DISK MENU
2) USB Drive
3) USB Host
Make Selection or <ESC>: Exit.
Figure 35 – PRINT/DISK MENU
1) Print Results PRINTER MENU
2) Print XY Plot
Make Selection or <ESC>: Exit.
1) InpTq vs. Time
SELECT XY PLOT
2) InpTq vs. Angle
3) RPM vs. Time
4) RPM vs. Angle
5) InpTq, Angle vs. Time
6) InpTq, CH2-Force vs. Time
7) InpTq, CH2-Force vs. Angle
8) CH2-Force vs. InpTq
Make Selection or <ESC>: Exit.
Figure 36 – PRINTER MENU
Figure 37 – SELECT XY PLOT MENU
1) Results File Disk
USB DISK DRIVE MENU
2) Current Rundown Disk
3) Current Setup Disk
4) Tool Definitions Disk
5) Disk Current Setup
6) Disk Tool Definitions
Make Selection or <ESC>: Exit.
Figure 38 – USB DISK DRIVE MENU

RS Products from PCB Load & Torque Toll-Free in USA 866-684-7107 716-684-0001 www.pcb.com
MODEL 962 RECORDER OPERATION MANUAL 19
Current
Rundown
Disk:
Press the 2 button on the keypad to save
the XY data of the current test to a USB
flash drive in port USB A.
Current Setup
Disk:
Press the 3 button on the keypad to save
the current test setup to a USB flash drive
in port USB A.
Tool Definitions
Disk:
Press the 4 button on the keypad to save
the transducer libraries to a USB flash
drive in port USB A.
Disk
Current Setup:
Press the 5 button on the keypad to upload
the test setup from the USB flash drive in
USB A port into the Model 962.
Disk
Tool
Definitions:
Press the 6 button on the keypad to upload
the transducer definitions from the USB
flash drive in the USB A port into the
Model 962.
4.5.3 USB Host
To send the data to a PC from the Model 962, press the 3 button
while in the PRINT/DISK MENU to open the USB HOST
MENU. See Figure 39. The results files, rundown files, setup
files, and tool definitions can be uploaded to a connected PC via
the USB B port.
NOTE: FastPlot2 software must be installed on the PC to trans-
fer data with the Model 962.
The USB Host menu options are described below.
Results File
Host:
Press the 1 button on the keypad to send the
numeric data results to a PC via the USB B
port.
Current
Rundown
Host:
Press the 2 button on the keypad to send the
current XY data to a PC via the USB B port.
Current Setup
Host: Press the 3 button on the keypad to send the
current test setup to a PC via the USB B port.
Tool
Definitions
Host:
Press the 4 button on the keypad to send the
transducer libraries to a PC via the USB B
port.
NOTE: For more information on the FastPlot2 software refer to
Section 6.
4.6 Utility Menu
The UILITY MENU displays options to manage miscellaneous
Model 962 settings. This menu can be viewed by pressing the
SETUP button when on the MAIN SCREEN. See Figure 40.
4.6.1 Set Date and Time
To set the date and time on the Model 962, press the 1 button on
the keypad while in the UTILITY MENU to open the SET
DATE AND TIME screen. See Figure 41.
Navigate the SET DATE AND TIME screen using the Arrow
() buttons on the keypad. Use the numeric buttons on the
keypad to input the values. Press the ENTER button to save the
values and press ESC to exit back to the UTILITY MENU.
NOTE: Input values will not be saved unless the ENTER button
is pressed.
4.6.2 Clear Results
To clear the numeric results file on the Model 962, press the 2
button on the keypad while in the UTILITY MENU to open the
CLEAR RESULTS screen. Refer to Figure 42.
1) Set Date and Time
UTILITY MENU
2) Clear Results
3) Install Defaults
4) Check for Smartducers-OFF
5) Set 962 Serial Number
6) Mode: STANDARD
7) Set Analog Outputs
8) Diagnostics Menu
9) Change Password
Make Selection or <ESC>: Exit.
1) Results File Host
USB HOST MENU
2) Current Rundown Host
3) Current Setup Host
4) Tool Definitions Host
Make Selection or <ESC>: Exit.
Figure 39 – USB HOST MENU
Figure 40 – UTILITY MENU
SET DATE AND TIME
Month (1-12): 3
Day (1-31): 14
Year (xx): 14
Hour (0-23): 12
Min (0-59): 3
<Arrow Keys>: Select Item.
<ENT>: Save <ESC>: Exit.
Figure 41 – SET DATE AND TIME Screen

RS Products from PCB Load & Torque Toll-Free in USA 866-684-7107 716-684-0001 www.pcb.com
MODEL 962 RECORDER OPERATION MANUAL 20
Press the ENTER button on the keypad to clear the numeric re-
sults file. Press the ESC button to exit back to the UTILITY
MENU.
NOTE: Be sure to print or save the numeric results file prior to
clearing the results.
4.6.3 Install Defaults
To set the Model 962 back to factory preset condition, press the 3
button on the keypad while in the UTILITY MENU to open the
INSTALL DEFAULTS screen. See Figure 43.
NOTE: This operation will erase all of the settings and trans-
ducer definitions. Make sure this information is saved
or documented prior to installing defaults.
NOTE: The password is set in the Change Password screen (re-
fer to Section 4.6.9). The default password is 268.
Use the numeric buttons on the keypad to input the password. If
any of the information is incorrect an error will appear and the
Model 962 will return to the UTILITY MENU.
4.6.4 Check for Smartducers
To set the Model 962 to check for transducers with Auto-ID
chips, press the 4 button on the keypad while in the UTILITY
MENU to toggle this mode between ON and OFF.
NOTE: This feature is typically enabled only if the Model 962
will be used with multiple transducers that have Auto-
ID chips to simplify the setup and calibration.
4.6.5 Set 962 Serial Number
To set the serial number on the Model 962, press the 5 button on
the keypad while in the UTILITY MENU to open the SET 962
SERIAL NO screen. See Figure 44.
Use the numeric buttons on the keypad to input the serial num-
ber. Press the ENTER button to save the values and press ESC
to exit back to the UTILITY MENU.
NOTE: Input values will not be saved unless the ENTER button
is pressed.
4.6.6 Mode
To change the mode of the Model 962 to GMPT, press the 6 but-
ton on the keypad while in the UTILITY MENU to toggle this
mode between STANDARD and GMPT.
NOTE: GMPT mode is for a very specific application and will
not record data unless commended by a tool station con-
troller. This mode should typically be set to STAND-
ARD.
4.6.7 Set Analog Outputs
To enable and set up the analog output on the IO connector on
the Model 962, press the 7 button on the keypad while in the
UTILITY MENU to open the SET OUTPUTS screen. See Fig-
ure 45. The Model 962 can thus be set up to transmit real-time
the output signal from Channel 1, or the Angle on Channel 1, or
the output signal of Channel 2.
CLEAR RESULTS
Clear all results?
<ENT>: Clear <ESC>: Exit.
INSTALL DEFAULTS
Password:
CAUTION: Installing Defaults
WILL Erase Current Settings
SET 962 SERIAL NO
Serial No:
<ENT>: Save <ESC>: Exit.
SET OUTPUTS
1) Output Channel: CHAN 1
2) Full Scale (Nm): 0.0
Full Scale is 10vdc Output
Make Selection or <ESC>: Exit.
Figure 42 – CLEAR RESULTS Screen
Figure 43 – INSTALL DEFAULTS Screen
Figure 44 – SET 962 SERIAL NO Screen
Figure 45 – SET OUTPUTS Screen
Table of contents
Popular Voice Recorder manuals by other brands
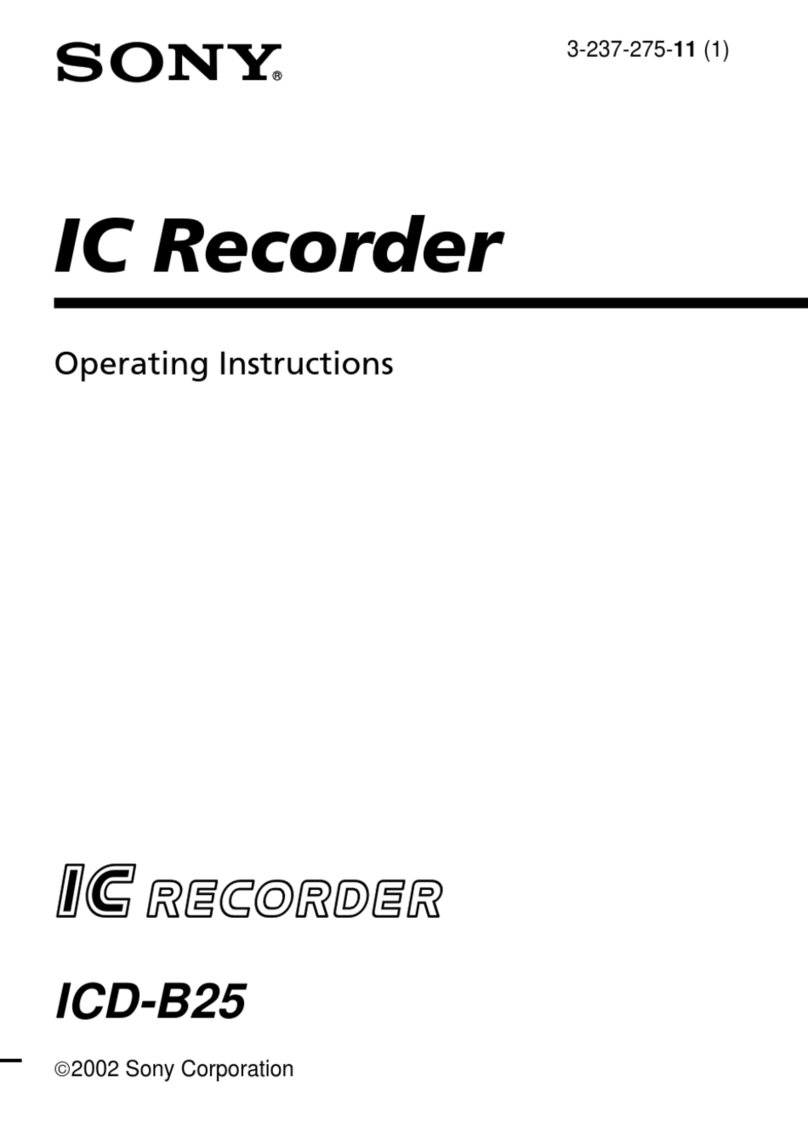
Sony
Sony ICD-B25 Operating Instructions (primary... operating instructions
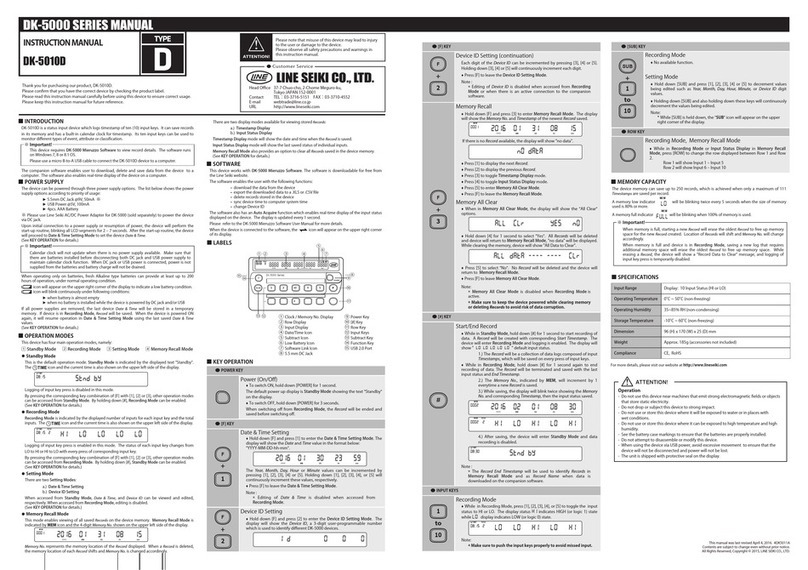
Line Seiki
Line Seiki DK-5010D instruction manual
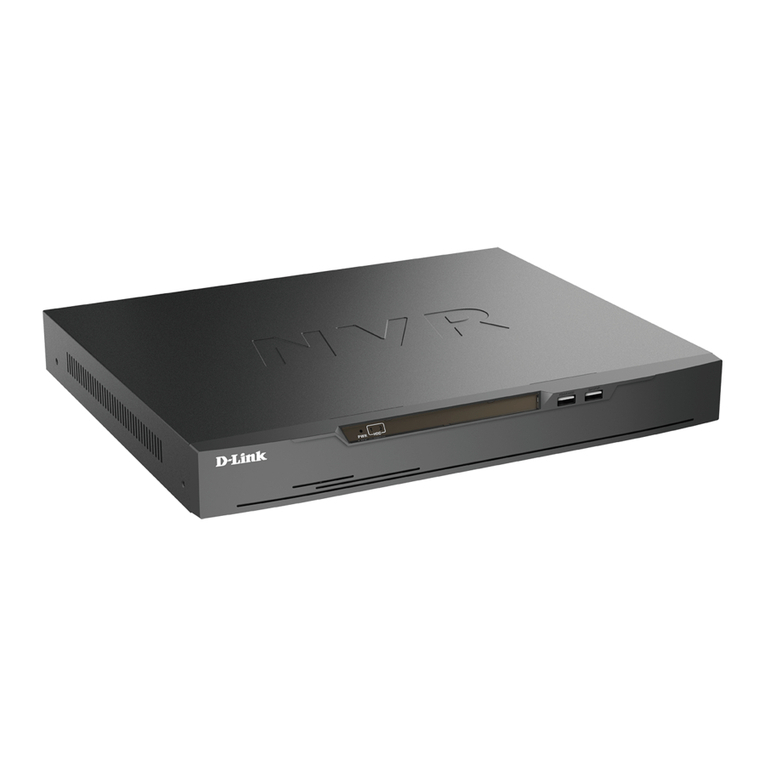
D-Link
D-Link JustConnect DNR-4020-16P Quick installation guide
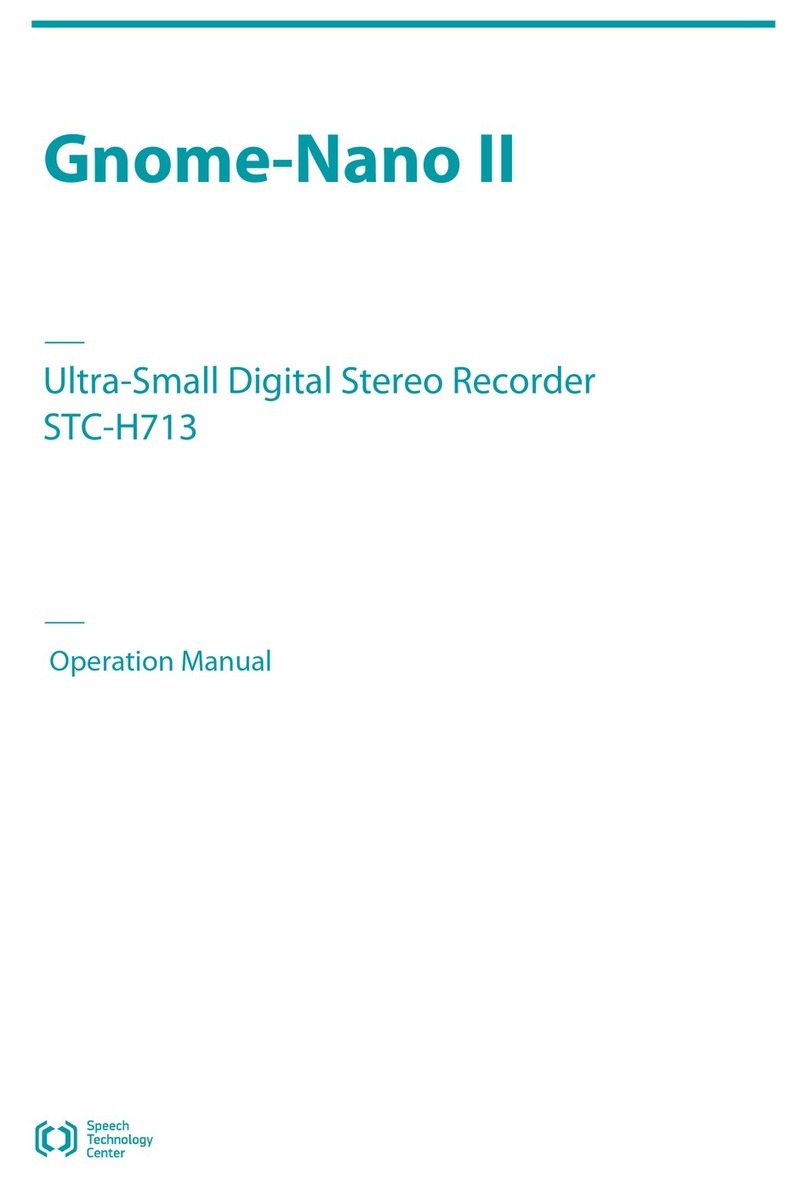
Speech Technology Center
Speech Technology Center Gnome-Nano II Operation manual
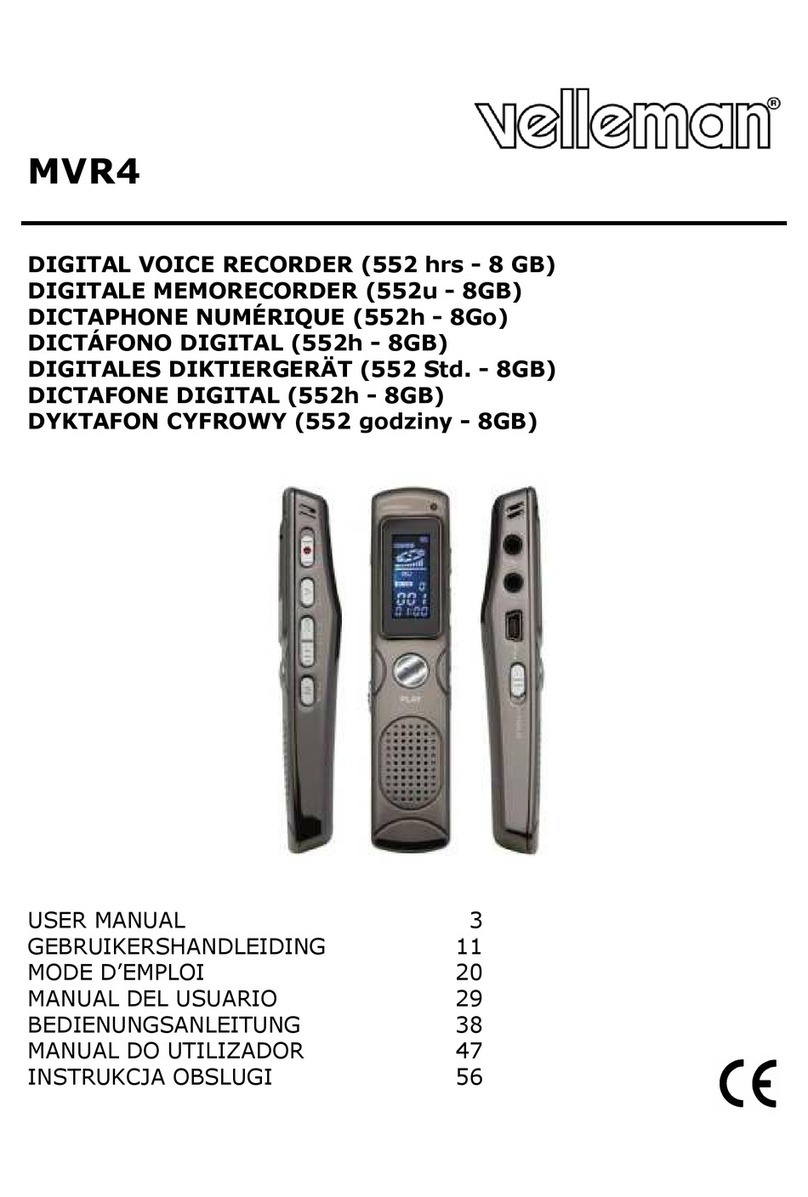
Velleman
Velleman MVR4 user manual

Plextalk
Plextalk DR-1 user guide