Peak PCAN-MicroMod FD User manual

PCAN-MicroMod FD
User Manual
User Manual 1.1.1 © 2020 PEAK-System Technik GmbH

Relevant products
Product designation Model Part no.
PCAN-MicroMod FD IPEH-003080
Imprint
PCAN® is a registered trademark of PEAK-System Technik GmbH. CANopen®, CANopen FD®, and CiA® are
registered EU trademarks of CAN in Automation e.V. Arm and Cortex are registered trademarks of Arm
Limited (or its subsidiaries) in the United States and/or elsewhere.
Other product names in this document may be the trademarks or registered trademarks of their
respective companies. They are not explicitly marked by ™ or ®.
© 2020 PEAK-System Technik GmbH
Duplication (copying, printing, or other forms) and the electronic distribution of this document is only
allowed with explicit permission of PEAK-System Technik GmbH. PEAK-System Technik GmbH reserves
the right to change technical data without prior announcement. The general business conditions and
the regulations of the license agreement apply. All rights are reserved.
PEAK-System Technik GmbH
Otto-Roehm-Strasse 69
64293 Darmstadt
Germany
Phone: +49 6151 8173-20
Fax: +49 6151 8173-29
www.peak-system.com
info@peak-system.com
Document version 1.1.1 (2020-10-21)
Essential changes in this document are listed in Appendix E on page34.
Relevant products PCAN-MicroMod FD
User Manual 1.1.1 © 2020 PEAK-System Technik GmbH
2

Contents
Imprint 2
Relevant products 2
Contents 3
1 Introduction 5
1.1 Features Overview 5
1.2 Operation Requirements 6
1.3 Scope of Supply 7
2 Electrical Connection 8
2.1 Connectors 8
2.2 Circuitry 12
3 Operation 14
3.1 Status LEDs 14
3.2 Reserved CAN ID 7E7h 15
3.3 Overview of Services 15
4 Configuration Program 17
4.1 Prerequisites for the Configuration Transfer 17
4.2 Installing the Configuration Program 17
5 Firmware Update 19
6 Technical Specifications 20
Appendix A CE Certificate 23
Appendix B Dimension Drawings 24
Appendix C CPU Adapter for 2.54mm Pitch 25
C.1 Description CPU Adapter 25
C.2 Pin Assignment CPU Adapter 26
C.3 Dimension Drawings CPU Adapter 30
Appendix D Minimum Circuitry 32
PCAN-MicroMod-FD_MinimumCircuitryDiagram 33
Contents PCAN-MicroMod FD
User Manual 1.1.1 © 2020 PEAK-System Technik GmbH
3

1 Introduction
The PCAN-MicroMod FD is a small plug-in board with CAN and CAN FD connection on
the one side and various physical inputs and outputs on the other side. The logical
linking of both sides is done by the microcontroller NXP LPC54618. With the MicroMod
FD, electronics developers can easily integrate I/O functionality with CAN connection
into their project.
The PCAN-MicroMod FD is configured using the supplied Windows software. In addi-
tion to simple I/O mapping to CAN IDs, function blocks are also available for
processing the data. The configuration created on the computer is transferred via
the CAN bus to the MicroMod FD which then runs as an independent CAN node.
Multiple modules can be configured independently on a CAN bus.
For the PCAN-MicroMod FD, ready-to-use motherboards in an aluminum housing and
an Evaluation Board for the development of own applications are available.
This document describes the hardware and the functions of the plug-in board PCAN-
MicroMod FD. Separate documents exist for the motherboards from PEAK-System
(e.g. Analog1) and for the Evaluation Board.
1.1 Features Overview
Plug-in board with 2 double pin strips of 50 pins each, 50 mil pitch (1.27mm)
NXP LPC54618 microcontroller with Arm® Cortex® M4 core
1 Introduction PCAN-MicroMod FD
User Manual 1.1.1 © 2020 PEAK-System Technik GmbH
5

High-speed CAN connection (ISO 11898-2)
Complies with CAN specifications 2.0A/B and FD
CAN FD bit rates for the data field (max. 64bytes) from 20kbit/s up to
10Mbit/s
CAN bit rates from 20kbit/s up to 1Mbit/s
Microchip CAN transceiver MCP2558FD
8 analog inputs
Measuring range unipolar 0 to 3V
Resolution 12bits, sample rate 1kHz
8 digital inputs
8 digital outputs
2 frequency outputs
Selective configuration of up to 16 devices in a CAN network based on the module
ID
Supply voltage 3.3V
Dimensions 33 x 36 mm
Extended operating temperature range from −40 to 85°C (−40 to 185 °F)
1.2 Operation Requirements
Board with socket strips or hole grid for mounting the PCAN-MicroMod FD (Evalu-
ation Board, motherboard from PEAK-System or self-development), see also
Appendix B Dimension Drawings on page24.
Possible socket strip (2pieces) as counterpart to the PCAN-MicroMod FD: Amtek
5PS3MSA44-225GONPNRU-00
For the creation and transfer of a configuration:
Computer with Windows 10, 8.1 (32/64-bit) and a PC-CAN interface from PEAK-
System
(Recommendation: PC-CAN interface with CAN FD capability, e.g. PCAN-USB FD)
1 Introduction PCAN-MicroMod FD
User Manual 1.1.1 © 2020 PEAK-System Technik GmbH
6

1.3 Scope of Supply
PCAN-MicroMod FD plug-in board
Configuration software for Windows
Manual in PDF format
Optional: Pin adapter for 100 mil pitch
1 Introduction PCAN-MicroMod FD
User Manual 1.1.1 © 2020 PEAK-System Technik GmbH
7

2 Electrical Connection
This chapter covers the signal assignment of the pins on the PCAN-MicroMod FD and
its possible circuitry.
2.1 Connectors
The PCAN-MicroMod FD has two double pin rows (A, B) with 50 pins each (first column
in the following tables). Thus, the MicroMod FD can be plugged onto boards with
matching socket strips (50-mil/1.27-mm grid, see also Appendix B Dimension Draw-
ings on page24).
Possible socket strip (2pieces) as counterpart to the PCAN-MicroMod FD: Amtek
5PS3MSA44-225GONPNRU-00
On request, PEAK-System offers an adapter for circuit boards with 100-mil/2.54-mm
grid). See also Appendix C CPU Adapter for 2.54mm Pitch on page25.
The MicroMod FD has a white mark on the upper left corner (pin A1) for better orient-
ation when plugged in.
Attention! Electrostatic discharge (ESD) can damage or
destroy components on the circuit board. Take precautions to
avoid ESD when handling the circuit board.
2 Electrical Connection PCAN-MicroMod FD
User Manual 1.1.1 © 2020 PEAK-System Technik GmbH
8

Pin layout of the two double pin headers, direction of view from above through the circuit board
(orientation when plugged in).
Pin MMFD Designation Function
A1 GND Ground
A3 LED-A_red
Open-drain outputs for external status LEDs
A5 LED-A_green
A7 LED-B_red
A9 LED-B_green
A11 FC1_I2C-SDA I²C 1: identification of the motherboard type via external EEPROM
A13 FC1_I2C-SCL
A15 Reserved
A17 Reserved
A19 Ext-CAN-Sel# Alternative, external CAN transceiver is used if put on ground
A21 Reserved
A23 Reserved
A25 Reserved
A27 Dout-0
Digital outputs 0 to 7 for switching external output drivers, 3.3 V level
Static state: 0, 1
PWM at 1 – 10,000 Hz (common frequency for all outputs)
A29 Dout-1
A31 Dout-2
A33 Dout-3
A35 Dout-4
A37 Dout-5
A39 Dout-6
A41 Dout-7
A43 CAN-H High-speed CAN ISO 11898-2: differential signal High
A45 CAN-L High-speed CAN ISO 11898-2: differential signal Low
A47 Reset-in# Module reset, Low-active, internal pull-up 10kΩ to 3.3V
A49 GND Ground
2 Electrical Connection PCAN-MicroMod FD
User Manual 1.1.1 © 2020 PEAK-System Technik GmbH
9

Pin MMFD Designation Function
A2 GND Ground
A4 Reserved
A6 Reserved
A8 Reserved
A10 Reserved
A12 Reserved
A14 Reserved
A16 Reserved
A18 Reserved
A20 Reserved
A22 Reserved
A24 Reserved
A26 Reserved
A28 Reserved
A30 Reserved
A32 Boot-CAN# CAN bootloader is started if put on ground during start-up
(CAN pins: A43, A45)
A34 Reserved
A36 Reserved
A38 Reserved
A40 Reserved
A42 Ext-CAN_M1
Connection to alternative, external CAN transceiver (is enabled by pin
A19)
A44 Ext-CAN_M0
A46 Ext-CAN_TxD
A48 Ext-CAN_RxD
A50 GND Ground
Pin MMFD Designation Function
B1 GND Ground
B3 FC0_V24_TxD
Serial RS-232 interface for firmware updates
B5 FC0_V24_RxD
B7 FC0_V24_RTS
B9 FC0_V24_CTS
2 Electrical Connection PCAN-MicroMod FD
User Manual 1.1.1 © 2020 PEAK-System Technik GmbH
10

Pin MMFD Designation Function
B11 Reserved
B13 Reserved
B15 ID_Bit-0# Module ID (4 bits → values 0 – 15):
- Pin open (internal pull-up): 0
- Pin on ground: 1
B17 ID_Bit-1#
B19 ID_Bit-2#
B21 ID_Bit-3#
B23 Vbus
Connection to a USB host (PC) for firmware updateB25 USB1_P
B27 USB1_N
B29 Reserved
B31 Din-0
Digital inputs 0 to 7, level 3.3V
Inputs 0 to 5: measurment of the frequency or the duty cycle possible
B33 Din-1
B35 Din-2
B37 Din-3
B39 Din-4
B41 Din-5
B43 Din-6
B45 Din-7
B47 3V3in Supply voltage input 3.3V DC, 100mA (connected to B48)
B49 GND Ground
Pin MMFD Designation Function
B2 GND Ground
B4 Boot-Serial# Bootloader is started if put on ground during start-up
(RS-232 pins: B3, B5, B7, B9)
B6 Boot-USB# USB bootloader is started if put on ground during start-up
(USB pins: B23, B25, B27)
B8 Fout-0 Frequency outputs 0 and 1, level 3.3V
B10 Fout-1
B12 Reserved
B14 Reserved
B16 Reserved
B18 Reserved
2 Electrical Connection PCAN-MicroMod FD
User Manual 1.1.1 © 2020 PEAK-System Technik GmbH
11

Pin MMFD Designation Function
B20 Reserved
B22 Reserved
B24 Reserved
B26 Reserved
B28 Ain-0
Analog inputs 0 to 7, resolution 12 bits
B30 Ain-1
B32 Ain-2
B34 Ain-3
B36 Ain-4
B38 Ain-5
B40 Ain-6
B42 Ain-7
B44 Vref-out Reference voltage 3.0V, can be connected to pin B46 as internal refer-
ence
B46 Vref-in Reference voltage input for 12-bit ADC, pin B44 recommended as source
B48 3V3in Supply voltage input 3.3V DC, 100mA (connected to B47)
B50 GND Ground
2.2 Circuitry
For the basic operation of the PCAN-MicroMod FD, a minimal circuitry with the
following components is required:
Voltage supply 3.3V DC
CAN connection (CAN-High, CAN-Low)
Pull-down for module ID inputs
Feedback of the analog reference voltage
Push button to ground for CAN flash mode (with pull-up resistor)
Reset push button to ground
The minimum circuitry is shown in the circuit diagram in Appendix D Minimum
Circuitry on page32.
2 Electrical Connection PCAN-MicroMod FD
User Manual 1.1.1 © 2020 PEAK-System Technik GmbH
12

Acomprehensive circuit example can be found in the circuit diagram for the separ-
ately available Evaluation Board. The circuit diagram is part of the corresponding
user manual PCAN-MicroMod FD Evaluation Board.
Tip: When designing the circuitry for the PCAN-MicroMod FD,
also observe the protection against overvoltage and reverse
polarity at inputs.
2 Electrical Connection PCAN-MicroMod FD
User Manual 1.1.1 © 2020 PEAK-System Technik GmbH
13

3 Operation
3.1 Status LEDs
Positions of status LEDs on the PCAN-MicroMod FD
LED A (upper left) Status Description
No function Reserved
LED B (upper right) Status Description
Green blinking (1Hz) Normal operation
Green flickering Receiving config-
uration
Green and red blinking
alternately
No valid config-
uration
Orange quick blinking
(4Hz) CAN Bootloader
Ready for transfer. New firmware can be transferred to
the PCAN-MicroMod FD via CAN bus using the Windows
program PEAK-Flash.
Red on Firmware error The PCAN-MicroMod FD does not have a valid firm-
ware.
Power LED (lower loca-
tion) Status Description
Green on Power Supply The supply voltage of 3.3V is applied to the PCAN-
MicroMod FD.
3 Operation PCAN-MicroMod FD
User Manual 1.1.1 © 2020 PEAK-System Technik GmbH
14

3.2 Reserved CAN ID 7E7h
To configure the PCAN-MicroMod FD, the 11-bit CAN ID 7E7h is used. Accordingly, the
PCAN-MicroMod FD Configuration program exchanges data with the module via the
CAN bus. When designing your CAN network, make sure not to use the CAN ID 7E7h in
any way.
3.3 Overview of Services
The PCAN-MicroMod FD provides various functions, called services. The availability of
services depends on the used motherboard.
Service Remark
Symbols
(CAN messages)
Definition of the CAN messages used by the PCAN-MicroMod FD with
Symbol names (CAN ID) and Variables resulting from Signals within the
data bits. Signals can contain initial values and timeout periods (e.g. for
CAN problems).
Digital Inputs
Assigned CAN messages can also be transmitted event-controlled. For
this purpose, the type of signal change (positive edge, negative edge or
both edges) is set as trigger.
Digital Outputs A Signal has influence either on the state of a digital output or on the
duty cycle at a preset frequency.
Analog Inputs An A/D value can be adjusted with scale and offset. Furthermore, a soft-
ware low-pass can be activated.
Analog Outputs
This service is only available with a D/A converter being applied to the
PCAN-MicroMod FD (e.g. using the Analog1 motherboard). A D/A value
can be adjusted with scale and offset.
Frequency Outputs Frequency and duty cycle are controlled independently with one Signal
each.
Digital Functions
The digital inputs can be logically combined with each other. The result
can be passed on to a Signal, to a digital output, or internally as feed-
back to an input.
Statistics Statistical data generated by the PCAN-MicroMod FD about the
processing and the environment can be passed to Signals.
3 Operation PCAN-MicroMod FD
User Manual 1.1.1 © 2020 PEAK-System Technik GmbH
15

Service Remark
Curve Definitions/Curves
(characteristic curves) Analog input data can be converted with the help of curves.
Rotary Encoders The service can process the signals of manual encoders connected to
digital inputs (standard quadrature with 2 bits, max. 500 pulses/sec.).
Functions
A collection of functions that convert one Signal value and place the
result on another Signal. Excerpt from the collection: Mult, Mod, And,
Hysteresis, Limit, RS Flip Flop, Switch Delay, Greater Than.
Find more details about the functionality and the application of the services in the
help of the PCAN-MicroMod FD Configuration program.
3 Operation PCAN-MicroMod FD
User Manual 1.1.1 © 2020 PEAK-System Technik GmbH
16

4 Configuration Program
With the enclosed configuration program PCAN-MicroMod FD Configuration for
Windows you can create, edit, and then transfer configurations to one or more PCAN-
MicroMod FD via CAN.
4.1 Prerequisites for the Configuration Transfer
Windows 10, 8.1 (32/64-bit)
PC-CAN interface from PEAK-System, e.g. PCAN-USB FD
CAN bus connection between the PCAN-MicroMod FD and the CAN interface of the
PC
On a computer without PCAN environment, you can create and edit a configuration
with the program and transfer the configuration later to the MicroMod FD using
another computer with PC CAN interface.
4.2 Installing the Configuration Program
The installation program for PCAN-MicroMod FD Configuration is located on the
supplied Product DVD.
Steps of the software installation:
1. Insert the Product DVD into the computer drive and execute the navigation
program either on request or manually (Intro.exe).
2. Klick on English >Tools.
4 Configuration Program PCAN-MicroMod FD
User Manual 1.1.1 © 2020 PEAK-System Technik GmbH
17

3. In the list, find the PCAN-MicroMod FD Configuration entry and click on Install.
4. Follow the instructions of the installation program.
Retrieve further information about the use of PCAN-MicroMod FD Configuration in
the provided help that you can reach via the program (e.g. with the |F1|key).
4 Configuration Program PCAN-MicroMod FD
User Manual 1.1.1 © 2020 PEAK-System Technik GmbH
18

5 Firmware Update
Different ways are available in order to update the firmware on the PCAN-MicroMod
FD.
Way Pins for transfer Pin for flash mode File
type Required supplements
RS-232 B3: TxD, B5: RxD B4 Hex Flash program Flash Magic for
Windows
CAN A43: CAN-H, A45: CAN-L A32 (LED A blinks
quickly orange) Binary
PC-CAN interface from PEAK-
System
PEAK-Flash for Windows (freely
available)
USB B23: Vbus, B25: USB1_P,
B27: USB1_N B6 Binary None (mass storage device in
operating system)
* Must be connected to ground during switch-on.
Tip: In order to update the firmware, we recommend the use
of the Evaluation Board for the PCAN-MicroMod FD (IPEH-
003081 or kit IPEH-003082). This simplifies the connection of
the cabling on the one hand and the setting of the flash mode
on the other hand.
5 Firmware Update PCAN-MicroMod FD
User Manual 1.1.1 © 2020 PEAK-System Technik GmbH
19

6 Technical Specifications
Supply
Supply voltage 3.3 V DC
Current consumption 180 mA max.
Connectors
Connection strips 2 double strips, each with 50 pins
Grid 50 mil (1.27 mm)
See also Appendix B Dimension Drawings on page24
Control and Communication
Microcontroller NXP LPC54618, Arm® Cortex® M4 Core
Standard firmware Configuration via reserved CAN ID 7E7h
CAN
Channels 1
Specification ISO 11898-2, CAN 2.0 A/B and CAN FD
Transceiver Microchip MCP2558FD
Nominal bitrates 20 kbit/s – 1 Mbit/s
CAN FD data bitrates 20 kbit/s – 10 Mbit/s
Galvanic isolation none
Termination none
6 Technical Specifications PCAN-MicroMod FD
User Manual 1.1.1 © 2020 PEAK-System Technik GmbH
20
Other manuals for PCAN-MicroMod FD
3
This manual suits for next models
1
Table of contents
Popular Microcontroller manuals by other brands

Emerson
Emerson White-Rodgers 21D83M-843 installation instructions
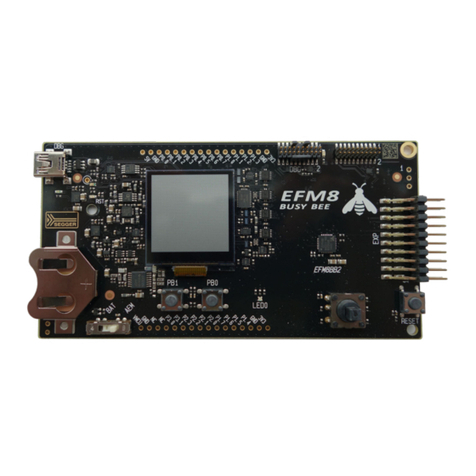
Silicon Laboratories
Silicon Laboratories EFM8BB2-SLSTK2021A user guide
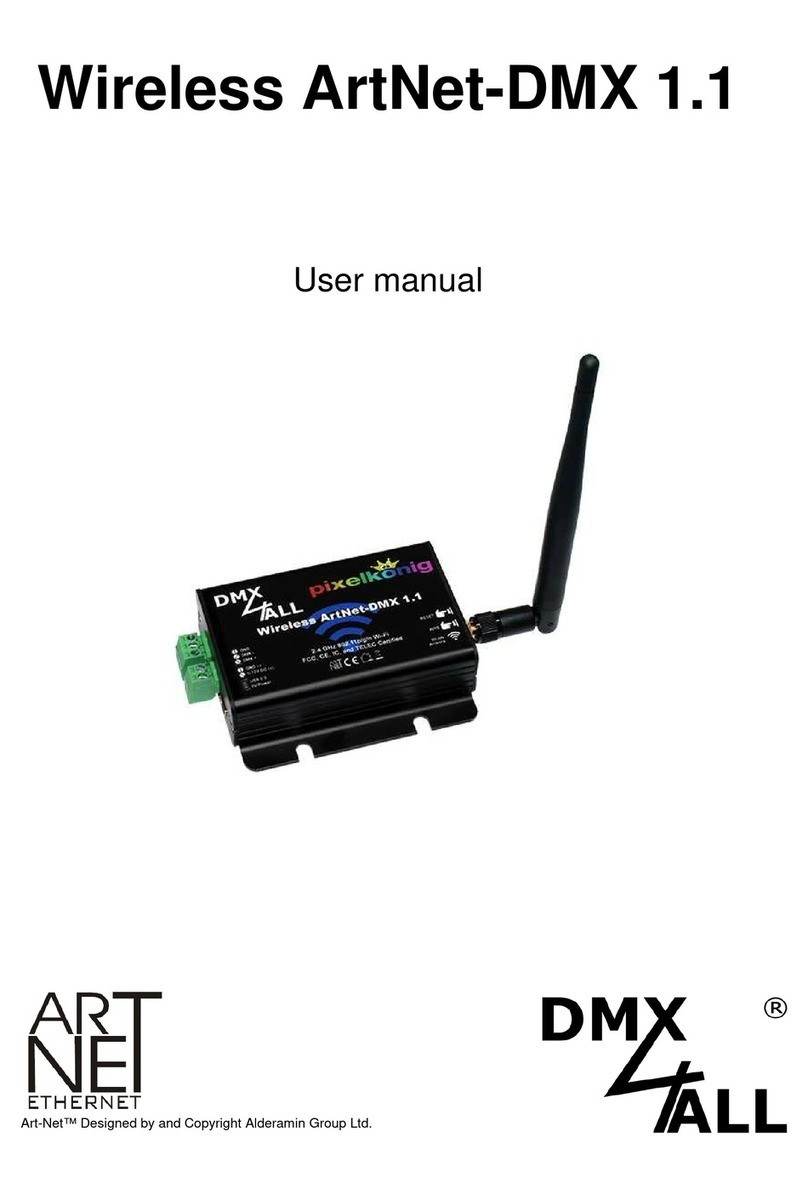
DMX4ALL
DMX4ALL ArtNet-DMX STAGE-PROFI 1.1 user manual
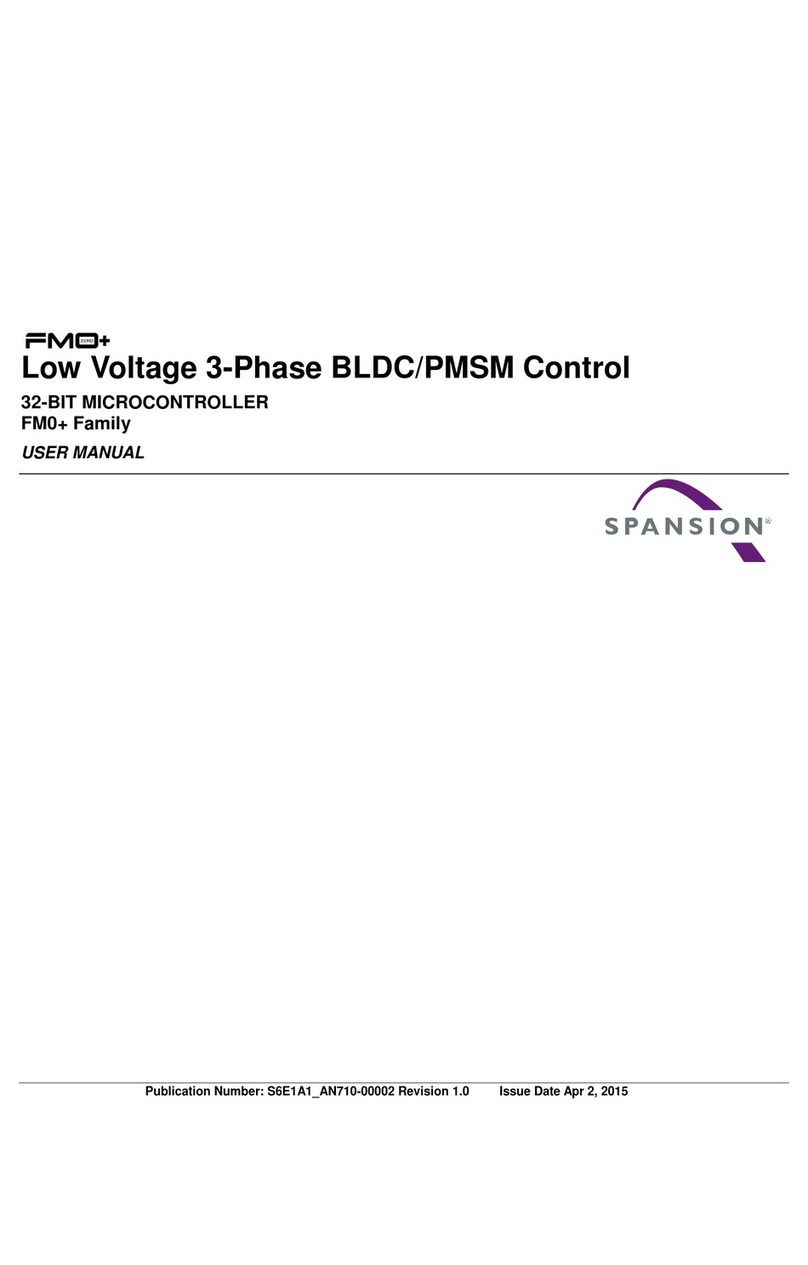
Spansion
Spansion FMO+ Series user manual

ST
ST EVLKST8500GH868 user manual
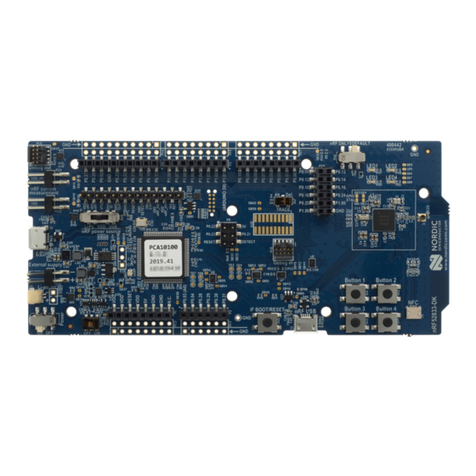
Nordic Semiconductor
Nordic Semiconductor nRF52833 DK user guide