Pentair Hydromatic H-03-000 Manual

NOTE! To the installer: Please make sure you provide this manual to the owner of the equipment or to the responsible
party who maintains the system.
STANDARD ELECTRICAL
CONTROL PANEL
INSTALLATION AND SERVICE MANUAL
Item # H-03-000 | Part # 5625-000-1 | © 2012 Pentair Pump Group, Inc. | 10/31/12

2
Thank you for purchasing your
Hydromatic®control panel. To
help ensure years of trouble-
free operation, please read the
following manual carefully.
Before Operation:
Read the following instruc-
tions carefully. Reasonable care
and safe methods should be
practiced. Check local codes and
requirements before installation.
Attention:
This manual contains important
information for the safe use of
this product. Read this manual
completely before using this
product and refer to it often for
continued safe product use. DO
NOT THROW AWAY OR
LOSE THIS MANUAL. Keep it
in a safe place so that you may refer
to it often.
Unpacking Panel:
Remove panel from carton.
When unpacking unit, check for
concealed damage. Claims for
damage must be made at the
receiving end through the delivery
carrier. Damage cannot be
processed from the factory.
CALIFORNIA PROPOSITION
65 WARNING:
This product and
related accessories contain
chemicals known to the State of
California to cause cancer, birth
defects or other reproductive
harm.
WARNING: Before handling
these pumps and controls,
always disconnect the power
first. Do not smoke or use
sparkable electrical devices or
flames in a septic (gaseous) or
possible septic sump.
Electrical Connections:
The contractor must conform
to the latest requirements of the
National Electrical Code. All
conduit and cables shall be in
accordance with NEC Code
NFPA #70. To maintain UL and
CSA ENCL rating, use the same
type UL and CSA weatherproof
conduit hubs when connecting to
this enclosure. Prior to conducting
any installation, repair or service
with regard to the control panel,
refer to the schematic appropriate
for that panel. The schematic will
provide guidance with regard to
the terminal block connections.
CAUTION: Nonmetallic
enclosures do not provide
grounding conduit connections.
Use grounding bushing and
jumper wires.
Make the Following Electrical
Connections:
a. Connect the pump leads to
the control panel. If pump
is single phase and the panel
has start capacitor, start
relay and run capacitor, it is
critical that the pump leads
be connected properly. The
White, Black, and Red pump
leads must be connected to
the appropriate terminals
as directed by the panel
schematic and the label on
the back panel below the
terminals.
b. Connect the pump heat sensor
and seal failure leads (if
available on the pump) to the
General
Information
1. Check junction box for
moisture. Moisture may cause
chattering of relays/contactors.
2. If pump is single phase with
start capacitor, start relay
and run capacitor in panel.
Check that pump White,
Black, and Red power
wires are connected to panel
correctly.
3. WARNING! Live voltage can
kill! Check incoming power
voltage to make sure that
it is correct for panel and
pump model.
appropriate terminal blocks in
the control panel. If the heat
sensor lead from the pump
is wired as indicated, remove
jumpers as defined by the
schematic.
c. Connect all the float control
leads to the appropriate panel
terminals. Contractor must be
very careful in locating the
floats at the proper elevations.
The maximum distance from
the control panel to the floats
is the lesser of l00 feet,
or the maximum distance
recommended for the pump.
d. Before connecting power to the
control panel, make sure all
control switches (e.g. H-O-A
switch) and protective devices
(e.g. breakers) are in the Off
position. Now connect power
to the terminal block or the
circuit breaker as directed by
the schematic.
e. Control panel must be grounded
properly per NEC and/or local
codes. To facilitate this, a
ground lug is provided on the
control panel.
Pump
Operation

3
4. Energize control panel. (Turn
on power to panel.)
5. Check overload relay and
verify reset mode (if overload
is supplied).
6. WARNING! Live voltage
can kill! Check voltage to the
panel and at secondary of
control transformer using a
voltmeter. If no transformer is
supplied, check voltage at the
circuit breakers.
7. With H-O-A switch in hand,
check discharge to verify the
pump is running. Check for
flow. On three phase power,
check to see if each pump
has proper rotation. Wrong
rotation will give low flow.
8. Check full load current with
amp probe and compare it
with the nameplate rating. On
three phase pumps, check all
three phases. On single phase
pumps, check black pump lead.
9. Check operation of start relay,
if supplied on single phase
panels, per procedure in Item
#7 of Maintenance Instructions.
10.With H-O-A switch in Auto,
check float operation and
response to control panel to
the float operation. For
sequence of operation, refer to
design specification.
11.Make sure H-O-A switch is left
in the Auto position after
start-up is completed.
12.Make sure all conduits from
wet well to panel are sealed
below panel. Septic gases
will damage components in
panel.
Pump Start-Up:
Refer to pump Installation and
Service Manual.
WARNING: Before handling
these pumps and controls,
always disconnect the pow-
er first. Do not smoke or use
sparkable electrical devices or
flames in a septic (gaseous) or
possible septic sump.
The maintenance schedule
will vary with operating and
environmental conditions. It will
also vary with the specific type of
control supplied. The list herein is
a guide only.
1. Exercise breaker through
two cycles. Be careful not to
overexercise as the break-
er is not a switching device.
Excessive operations tend
to affect the trip curve of
the breaker.
2. Check contactors and relays
for excessive humming. This
can be accomplished by
turning pumps on and off
in the Hand mode with the
H-O-A switch.
3. Check pump run light(s) by
running pump(s) in Hand
mode. Check bulb(s) in any
other light(s).
4. With the power off, check
continuity of all control fuses.
5. Check voltage at primary
and secondary of control
transformer.
6. Check the pump full load
amps.
7. Check the start relay by
using an amp probe around
the red wire (start winding).
Amp probe should display a
very brisk action from zero
to locked rotor and back to
operating load. This action
occurs on pump start, and
the action must show no lazy
movement.
8. Check junction boxes for
moisture. Moisture may
cause chattering of relays
and contactors.
9. Check for moisture inside
control panel enclosure.
Moisture can cause damage to
electrical components. Check
door gasket for proper seal.
10.Check labels to verify they
have not been damaged.
11.Lubricate enclosure hinges.
12.Pull floats and check for
proper operation and ensure
there is no foreign buildup
on them.
Spare Parts List:
The following is a list of
recommended spare parts.
However, conditions of service
vary significantly and a general
list may not in its entirety be
applicable to a given installation.
The user should exercise judgment
in defining specific requirements
based on this guide.
1. Fuses for control transformer
primary and secondary.
2. Contactor.
3. Bulbs for any light requiring
a bulb.
4. Control transformer.
5. Alternator relay or duplex
alternator board, whichever is
required.
Pump
Maintenance
WARNING: Before handling
these pumps and controls,
always disconnect the pow-
er first. Do not smoke or use
sparkable electrical devices or
flames in a septic (gaseous) or
possible septic sump.
Pump
Troubleshooting

4
2. Check for heat sensor
trip in pump with a jumper
between HEAT SENSOR
1 and HEAT SENSOR 2
terminals.
3. Reset overload(s) if tripped.
4. Reset circuit breakers if
tripped.
3. Pump runs, but run light
does not energize.
a. Remove light and check
with ohmmeter.
b. Check run light wiring.
4. Pump runs but does not
pump down the wet well.
a.
On three phase only, pump
rotation may be wrong.
Wiring of pump to con-
trol panel may be reverse
sequenced.
b. Impeller may be dragging
in volute due to solids.
High amperage draw would
identify this.
c. Refer to the pump manual
for other possibilities such
as closed discharge gate
valve, etc.
5. Severe humming/chattering
of contactors and control
relays.
a. There may be low voltage.
Check voltage at primary
and secondary of control
transformer using a
voltmeter. This low voltage
condition may cause severe
chattering and burnout of
contactors and relays.
b. Contactor may have dust
around magnet of coil
structure. Dry or clean
as required.
c. Check voltage to the
control panel. Contactors
require a minimum of
1. Pump does not run in
Hand position.
a. Check pump circuit breaker
and control fuse for tripping
or blown condition.
b. Check incoming power
voltage and control circuit
voltage.
c. Check overload relay to see
if it is tripped. Reset relay
if tripped.
d. With the power off, check
motor heat sensor continuity.
e. Check wiring of pump to
control panel. It should
agree with the schematic.
f. Check contactor coil
resistance.
2. Pump does not run in
Auto position.
a. Check items (a.) through
(f.) per Item #1 above.
b. Floats may be miswired to
control panel. Check float
type (N.O. or N.C.) and
hook up by referring to the
schematic. If the start and
stop floats are hooked in
reverse, pump will short
cycle and will not pump the
level down.
c. Check pump controller
indicating lights.
1. Make sure there is power
to the controller.
2. Is water level in the
system high enough to
activate the floats?
3. If #1 and #2 check out,
shut power off to the
panel. Remove the OFF
FLOAT wires and run a
jumper between the OFF
FLOAT connections.
If OFF FLOAT light
comes on, the float is
“hung up” or the wiring
connections are loose.
1. Is water level in the
system high enough
to activate the lead
(ON) float?
2. If #1 checks out, shut
off power to the panel.
Remove the lead (ON)
float wires and run a
jumper between the LEAD
FLOAT (ON FLOAT)
connections. If one or two
pumps start, check the lead
(ON) float for “hang up” or
loose wiring connections.
1. Check Hand-Off-Auto
(H-O-A) switch for correct
position.
OFF
FLT
PUMP 1
CALL
LEAD
FLT
PUMP 2
CALL
DUPLEX
No Lights On
(No call from the floats)
PUMP 1
CALL
PUMP 2
CALL
OFF
FLT
LEAD
FLT
PUMP 1
CALL
OFF
FLT
PUMP 2
CALL
LEAD
FLT
DUPLEX ONLY
OR
“FLOAT” light ON, “LEAD FLOAT” light
ON, and either “PUMP 1” or “PUMP 2”
light ON tells you the lead float is calling
for pump.
All lights ON on pump controller tells
you all float circuits are good and the
problem lies elsewhere.
PUMP 1
CALL
OFF
FLT
PUMP 2
CALL
LEAD
FLT
DUPLEX
Off Float Light On

85% of full voltage to pull
in without chatter. If the
problem is a recurring
one, measure voltage with
recorder on a 24 hour basis.
d. Make sure the floats are
located away from any
turbulence.
e. Dry out the junction box
(if furnished); moisture
in the junction box may
cause relays to energize
intermittently.
6. Short cycling pump.
a. Check float controls.
7. Run light stays on.
a. Selector switch may be in
the Hand position.
8. Nuisance tripping of
overload on motor starters
or circuit breakers.
a. Check pump and draw with
amp probe and compare to
nameplate amps on pump.
b. The impeller may be locked
up due to excessive debris
or solids.
c. Possible motor failure (fault
in windings).
d. Pump may be miswired to
terminal block.
e. Voltage and current
unbalance. Three phase only.
Voltage unbalance on
three phase power sources
can cause motor current
to become unbalanced
and excessive heating will
result. Tripping of the
overload protectors and
premature motor failures
can be expected if the
current unbalance exceeds
five percent.
Percent Maximum Current
Current = Difference from x 100
Unbalance Average Current
_______________
Average Current
To determine if motor current
unbalance is a function of the
motor or the power supply:
1. Label the leads and
the terminals 1, 2, and
3 respectively.
2. Record the amperage
for each lead.
3. Move each lead to the
next terminal (1 to 2, 2
to 3, 3 to 1).
4. Again read the amperage
of each lead.
5. Move each lead to the
next terminal (1 to 3, 2
to 1, 3 to 2).
6. Again read the amperage
of each lead.
7. If the unbalance moves
with the motor leads,
the unbalance is caused
by the motor. If the
unbalance remains
with the terminals, the
unbalance is in the
power supply.
8. If the current unbalance
exceeds five percent,
nuisance tripping or
excessive heating will
result.
9. Connect leads for the
lowest percent of
current unbalance.
f. Connections and start
components. Single phase
only.
1. Disconnect all power
from the panel before
making these checks.
2. Motor winding resistance
readings.
a. Disconnect all three
motor leads from panel
terminal blocks.
5
b. Using a volt-ohmmeter,
with the scale set
on RX1, measure the
resistance between the
leads with the chart below.
Typical
Motor Resistance
Winding Leads Reading
Main Black to Lowest
White
Start Black to Next
Red Lowest
(Middle)
Both White to Highest
Red (Main & Start)
3. Capacitor check.
a. Make sure the capacitor
is discharged. Use
extreme caution as a
spark might occur.
b. Disconnect the capacitor
leads and connect an
analog-type volt-ohmmeter
to the capacitor terminals.
c. Set the meter on the
RX1,000 scale to check
the start capacitor. Set the
meter on the RX10,000
scale to check the
run capacitor.
d. The meter should indicate
low ohms when it is first
connected, but as the
capacitor becomes charged
(by the meter), it will
return to a reading of
infinity (open circuit).
4. Start relay check.
a. Check the start relay coil
resistance. It should be
3,000 to 15,000 ohms.
b. Install a clamp on amp
meter around the start
winding lead.

6
c. Set the amp meter
scale to at least 2 times
the pump motor full
load current.
d. Place the H-O-A switch
in the Hand position to
start the pump.
e. The meter should read
approximately 2 times
full load current during
starting.
f. After the motor has
started (within one
second) the current
should drop to a value
much less than full load
current.
Typical
Motor Voltage
Component Lead Mode Reading
Main Winding Black to Start Line Voltage
White
Main Winding Black to Run Line Voltage
White
Start Winding Black to Start Line Voltage
Red
Start Winding Black to Run 120%
Red Line Voltage
5. Motor voltage check:

7
THIS PAGE INTENTIONALLY LEFT BLANK

740 EAST 9TH STREET 490 PINEBUSH ROAD, UNIT #4
ASHLAND, OHIO, USA 44805 CAMBRIDGE, ONTARIO, CANADA N1T 0A5
419-289-1144 800-363-PUMP
WWW.HYDROMATIC.COM
Warranty Rev. 12/13
STANDARD LIMITED WARRANTY
Pentair Hydromatic®warrants its products against defects in material and workmanship for a period of 12 months
from the date of shipment from Pentair Hydromatic or 18 months from the manufacturing date, whichever
occurs first – provided that such products are used in compliance with the requirements of the Pentair Hydromatic
catalog and technical manuals for use in pumping raw sewage, municipal wastewater or similar, abrasive-free,
noncorrosive liquids.
During the warranty period and subject to the conditions set forth, Pentair Hydromatic, at its discretion, will repair
or replace to the original user, the parts that prove defective in materials and workmanship. Pentair Hydromatic
reserves the right to change or improve its products or any portions thereof without being obligated to provide such
a change or improvement for prior sold and/or shipped units.
Start-up reports and electrical schematics may be required to support warranty claims. Submit at the time of start up
through the Pentair Hydromatic website: http://forms.pentairliterature.com/startupform/startupform.asp?type=h.
Warranty is effective only if Pentair Hydromatic authorized control panels are used. All seal fail and heat sensing
devices must be hooked up, functional and monitored or this warranty will be void. Pentair Hydromatic will cover
only the lower seal and labor thereof for all dual seal pumps. Under no circumstance will Pentair Hydromatic be
responsible for the cost of field labor, travel expenses, rented equipment, removal/reinstallation costs or freight
expenses to and from the factory or an authorized Pentair Hydromatic service facility.
This limited warranty will not apply: (a) to defects or malfunctions resulting from failure to properly install, operate or
maintain the unit in accordance with the printed instructions provided; (b) to failures resulting from abuse, accident
or negligence; (c) to normal maintenance services and parts used in connection with such service; (d) to units that
are not installed in accordance with applicable local codes, ordinances and good trade practices; (e) if the unit is
moved from its original installation location; (f) if unit is used for purposes other than for what it is designed and
manufactured; (g) to any unit that has been repaired or altered by anyone other than Pentair Hydromatic or an
authorized Pentair Hydromatic service provider; (h) to any unit that has been repaired using non factory specified/
OEM parts.
Warranty Exclusions: PENTAIR HYDROMATIC MAKES NO EXPRESS OR IMPLIED WARRANTIES THAT EXTEND
BEYOND THE DESCRIPTION ON THE FACE HEREOF. PENTAIR HYDROMATIC SPECIFICALLY DISCLAIMS THE
IMPLIED WARRANTIES OF MERCHANTABILITY AND FITNESS FOR ANY PARTICULAR PURPOSE.
Liability Limitation: IN NO EVENT SHALL PENTAIR HYDROMATIC BE LIABLE OR RESPONSIBLE FOR
CONSEQUENTIAL, INCIDENTAL OR SPECIAL DAMAGES RESULTING FROM OR RELATED IN ANY MANNER TO
ANY PENTAIR HYDROMATIC PRODUCT OR PARTS THEREOF. PERSONAL INJURY AND/OR PROPERTY DAMAGE
MAY RESULT FROM IMPROPER INSTALLATION. PENTAIR HYDROMATIC DISCLAIMS ALL LIABILITY, INCLUDING
LIABILITY UNDER THIS WARRANTY, FOR IMPROPER INSTALLATION. PENTAIR HYDROMATIC RECOMMENDS
INSTALLATION BY PROFESSIONALS.
Some states do not permit some or all of the above warranty limitations or the exclusion or limitation of incidental or
consequential damages and therefore such limitations may not apply to you. No warranties or representations at any
time made by any representatives of Pentair Hydromatic shall vary or expand the provision hereof.
This manual suits for next models
1
Table of contents
Other Pentair Control Panel manuals

Pentair
Pentair Myers CGL-01SW Manual

Pentair
Pentair Hydromatic SPC-PANEL Manual
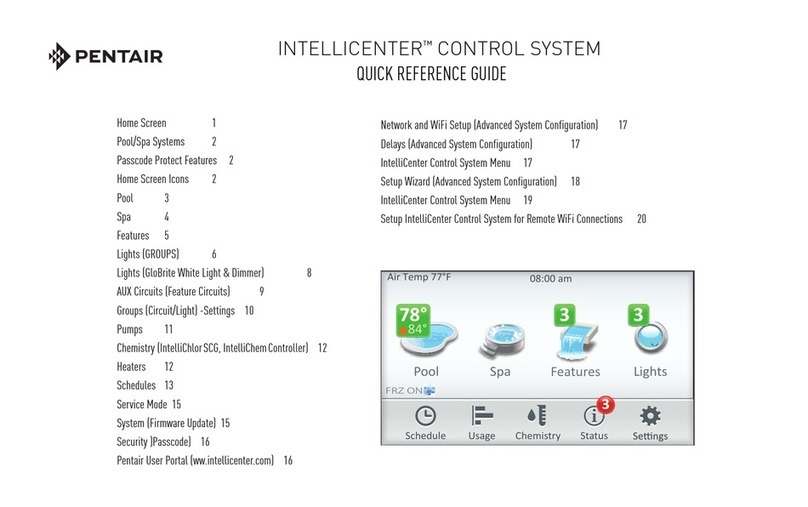
Pentair
Pentair INTELLICENTER User manual
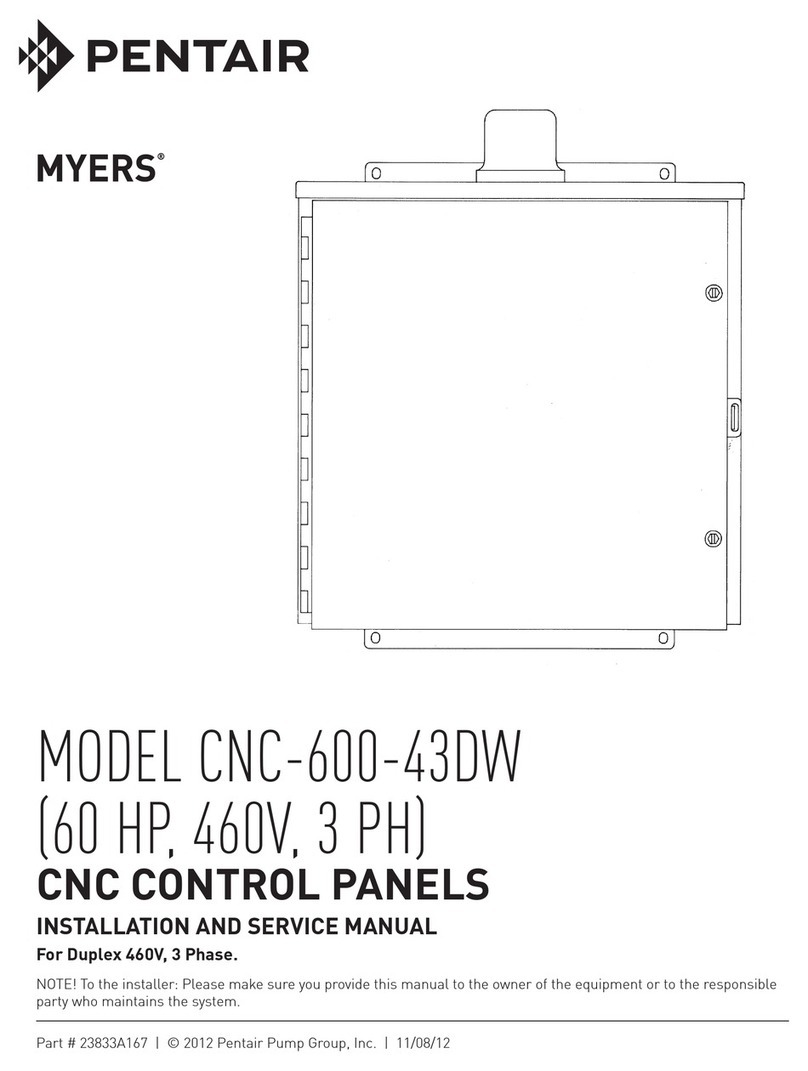
Pentair
Pentair MYERS CNC-600-43DW Manual

Pentair
Pentair ICHNDHLD User manual

Pentair
Pentair Hydromatic Manual
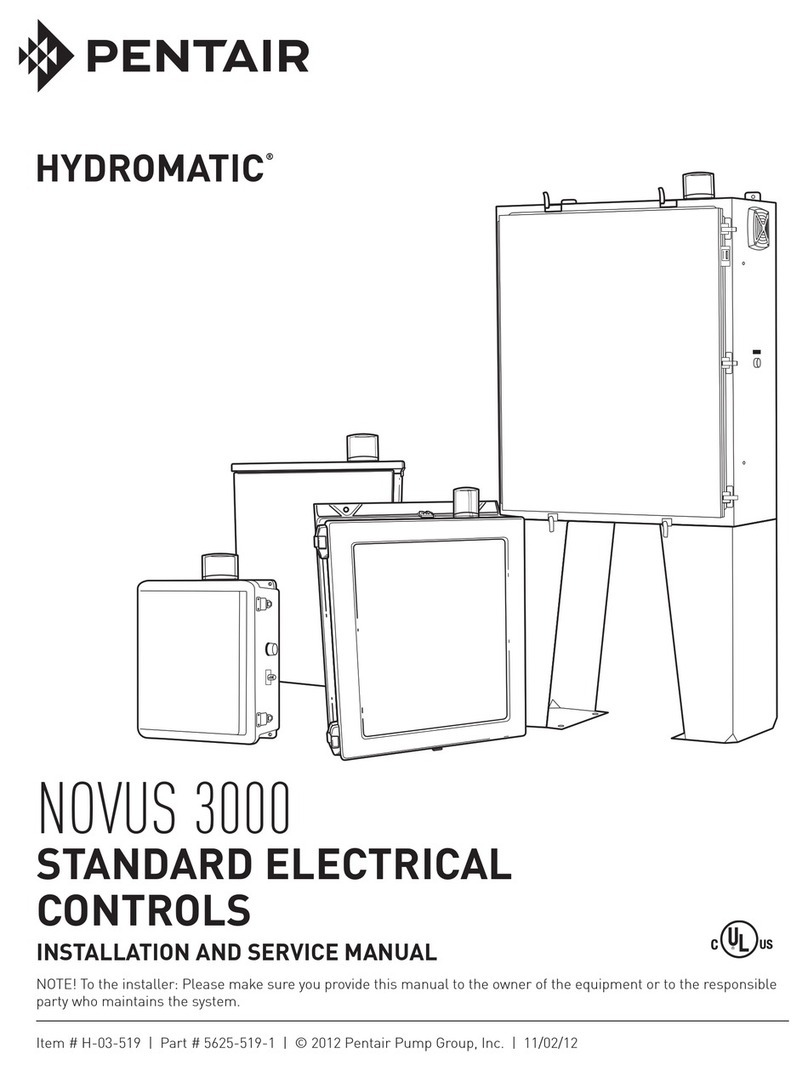
Pentair
Pentair Hydromatic NOVUS 3000 Series Manual

Pentair
Pentair FAIRBANKS NUJHUIS FBM20 Troubleshooting guide