PI 9350 User manual

MPI/PPI user manual
(english)
Art.Nr. 9350
Art.Nr. 9350.05M
Art.Nr. 9350.10M
Art.Nr. 9350.15M
11.02.2021
© PI 2021

index of contents
MPI/PPI
1 Description
2 System requirements
2.1 Operating system (s)
2.2 Software
2.3 Hardware
3 Installation
3.1 Hardware
4 Control elements
4.1 Display
5 Implementing
5.1 Programming software to use with direct access
5.1.1 PG2000 für S7 (V5.10)
5.1.2 PSet PG/PC interface
5.1.2.1 TCP/IP RFC1006 Communication
5.1.2.2 MPI setting
5.1.2.3 Profibus setting
5.1.2.4 TCP/IP RFC1006 setting
5.1.2.5 ProTool/Pro RunTime (RT) Configuration
5.1.3 SIMATIC Step© 7 Manager (v5.2 + SP1)
5.1.4 Windows Control Center (WinCC) (v6.0)
5.1.4.1 MPI Configuration
5.1.4.2 TCP/IP Configuration
5.1.4.3 Communication and fault diagnosis
5.1.5 Windows Control Center flexible 2004 (WinCC flexible) (v5.2.0.0)

5.1.6 ProTool/Pro v6.0 SP2
5.1.7 Microwin v3.2 (only for S7 200)
5.1.8 S7 for Windows v5.02
6 S7-Interface Configurator Help
6.1 Language selection:
6.2 User interface:
6.3 Bus configuration
6.4 Network settings
6.5 Parameterize TELEService
6.5.1 Index "Network":
6.5.2 Index "Modem":
6.5.3 Index "Serial parameter":
6.5.4 Index "Access Protection":
6.5.5 Index "GSM/ISDN/SMS":
6.5.6 Index "Internet/Mail":
6.6 Tuning
6.7 Factory defaults
6.8 PPI Boot off
6.9 Emergency-Loader
7 MPI cable manager
7.1 Description
7.2 Installation
7.3 Overview
7.3.1 Language
7.3.2 Interface
7.3.3 Update
7.3.4 Teleservice
7.3.4.1 Telephone book
7.3.4.2 Connect
7.3.4.3 Extra

7.3.4.3.1 „Setup“
7.3.4.3.2 „TS-function“
7.3.4.3.3 „configure adapter“
7.3.4.3.4 „Import parameter“
7.3.4.3.5 „Export parameter“
7.3.5 Tuning
8 Technical data
8.1 Pinning RS232
8.2 Pin assignment

MPI/PPI
1Description
The MPI/PPI-cable connects the programming device or the computer with the MPI-interface of
an S7-300/400 or with the PPI-interface of an S7-200 over the serial interface (COM-Port). The
cable recognizes automatically while attach on it on the PLC, which PLC-type is connected. At
the first access from the PD´s on the cable it recognizes the baud rate for communication with
the PLC. With the programming device PG-2000 or S7-for-windows the MPI/PPI-cable works up
to 115.2 kbaud on the computer side.
Here it can communicate with each member which is connected to the bus or even with the
backplane bus. It is the best to work over the S7-project.
The MPI/PPI-cable supplies itself from the PLC and didn´t need a foreign supply. All power
supplies are galvanic seperated. To reach high distance to an PLC with the MPI/PPI-cable you
need the MPI-NETZ-adapter to feed the cable with the 24VDC supply voltage.
2System requirements
2.1 Operating system (s)
Windows 98 + SE
Windows ME/NT/2000
Windows XP
Windows Vista
Windows 7
2.2 Software
PLC - programming software (eg PG2000, Step © 7, S7 for Windows, Microwin)
2.3 Hardware
9pin. or 25 pins. COM interface
24V power supply (MPI or PPI interface)
3Installation
3.1 Hardware
MPI/PPI standard mode:
The cable is plugged with the short cable side to the MPI- or PPI-port of the PLC. The MPI/PPI-
cable sources itself normally with the 24V of this port and do not need externel voltage. The
cable needs everytime a PLC of course the 24V supply or optionally the MPI-Netz-Adapter. The
longer cable side has to connect in the COM-port of your PD or PC.
As the cable has supply voltage, you can see in the display the version of the included firmware
and start with an internal test of the included parts. After this test the adaptor checks if he is
connected to a PLC and tries to recognize the baudrate of the connected bus. In the display of
the cable you can see all relevant information.
The cable detects automatically the baudrate parameters to the programming device when the
communication starts and will use them.
If your PD or PC has only a COM-port with 25pin, you can use a normal "mouse adapter" or our
article number 9359-9 to change the pins from 25 to 9pin.
If you will use the plc-programming-software PG2000 or S7-für-Windows the MPI/PPI-cable will
work with 115.2 kBaud on the PC-side.

MPI/PPI as TS-Adapter (TS = Tele Service):
The TS-possibility allows the connection of a modem, to make a connection with a 2nd Modem
and a PC to a S7-300/400. The Cable must be connected between the modem (with a special
adapter piece, no Gender-Changer) and the PLC.
To work with the MPI-Cable in his TS-function, you must make the following actions:
1) The cable must be configured as a TS-Adapter (instead of „PG“ or „Pg“ the LCD display
shows „TS“ or „Ts“). You can turn on/off these function with the free program „MPI cable
manager“.
2) The program inside of the cable must have a version greater than V1.45. This version
number will be displayed for a short time behind the plugging to a S7 PLC. You can update the
cable software with the free program „MPI cable manager“.
3) You need the TeleService-software from Siemens in your PC to work with the cable. The
configuration of the cable can be made with the TeleService-software from Siemens or with the
„MPI cable manager“.
4) The connection of the modem to the MPI-cable must made with a special adapter plug
(no Gender-Changer or so)
Order information for the special adapter:
Adapter for TS-function 9-pol Article-no. 9350-TS
The adapter for the TS-function only works with the MPI/PPI–Cable with the order-
number 9350 !
MPI/PPI as HMI-Adapter (HMI = Human Machine Interface):
The HMI-possibility allows the connection of a operator panel (who has not an internal MPI-port,
but the HMI-protocol and a RS232-interface) with a S7-300/400. The cable must be connected
between the operator panel and the PLC. The HMI-protocol must be a part of the operator
panel.
Behind the version V1.45 of the software inside the cable, you can use the cable as a HMI
adapter. Some operating panels are made to work with a Siemens-HMI-Adapter. The pining to
our cable is different. You may turn the wires 2 and 3 in a little adapter. Please look into the
handbook of the operator panel what you need for the correct pinning.
4 Control elements
4.1 Display
First line => #02PD00¯
Second
line => !02AG04°
Display description from left to right.
First line
#02 => In this example there are two active stations on the MPI – BUS
PD => letter definition of the PC - baud rate.

Display Descriptions
PD 115,2k or baud rate identification is active.
PU USB connection
P? Baud rate recognition and access way active.
TD 115,2k or baud rate recognition is active. (cable is configured as TS – adapter)
PG 19,2k
TS 19,2k (cable is configured as TS – adapter)
Pg 38,4k
Ts 38,4k (cable is configured as TS – adapter)
pG 57,6k
tS 57,6k (cable is configured as TS – adapter)
PM PPIMulti (187,5k)
00 => the station number of the MPI – cable. (Default is „0“)
(In the system configuration click on „Set PG/PC interface“. In the following dialog click
“properties”. Now you can change in the registry card “MPI” part “station-related” the
“adress” of the cable.)
(In the PG 2000 software you can find it by clicking on „Options“
„Interfaces“. Close to the bottom of the dialog you can change the „local address“
of the cable.)
¯=> if this sign appears in the top of the line, your cable is communicating with the PLC.
If this sign appears in the bottom of the line, your cable is communicating with the computer.
Second Line
!=> (Exclamation mark) specifies the connection type to the PLC.
Display Description
! Directly connected to the PLC.
? Not directly connected to the PLC.
! (inverse) Directly connected to the PLC with passive unit of the PLC.
? (inverse) Not direct connected to the PLC with passive unit of the PLC.
02 => is the station number of a connected and active PLC in the MPI - BUS.
Every 750 milliseconds (a ¾ second) another user will be displayed if more then one user
has been found.
AG =>The type of the protocol which is used for the cable to run up to the computer.
Display Description
AG Unknown because there is no connection or an older protocol version (before5.0)
is used.
Ag v5.1 Protocol
Ag v5.0 Protocol
04 => Shows the station number of the device, which is connected in that moment with the
computer software (in this example station number 04).
Configuration specific messages:
With the following baud rate settings, the menu message changes accordingly:

Baud rate – configuration 1. line 2. line
PPI 9,6k – (PPISER96) PPISER96 ACTIVE
PPI 19,2k – (PPISER19) PPISER19 ACTIVE
PPI 187,5k – (PPIMulti) ???PM? ????
PPILAN – (PPILAN) PPILAN ACTIVE
PPIUSB – (PPIUSB) PPIUSB ACTIVE
SONDSER SONDSER 19,2 kBaud 8N1
SONDUSB SONDUSB 38,2 kBaud 7E2
Description 8N1:
8 = Data bits
N = Parity
1 = Stop bit
5 Implementing
Connect your module as described in the chapter " Hardware installation " to the PLC and to the
programming device or to your computer.
If you want to respond to a PLC via the module you have to comply the
requirements as descript in the chapter "system requirements" . In addition,please
make sure that the module is properly connected
5.1 Programming software to use with direct access
After you have adjusted and connected the PLC-VCOM or the programming adapter to the
COM-port on your computer, you will be able to connect with your programming software
to the PLC and work with it.
How you have to adjust your programming software is described in the following points:
5.1.1 PG2000 für S7 (V5.10)
1. Start the PG 2000 software by using the desktop link or by using the application entry in the
start menu.

2. Choose from "View" => "S7-300/400"
In the menu “Options“ click “Interfaces“..
3. A dialog appears, in which you are able to
set the “AG-Interface” (COM-port) in the
section “Interfaces”.
4. Configure the baud rate in the section
“Bus access“ to “19,2k“. Below change the
value for PC - MPI to “187,5kBaud“.
5. Save your configuration by pressing “OK“.
6. Now the software is ready to establish a
connection to the PLC
Click the symbol “Open“ and afterwards
press “PLC”.
Alternative you can click:
„File“ => „Open“ => „PLC“
The connection between PG 2000 and the
PLC is now established.
A new window appears. Now you can edit
the blocks in the PLC.
5.1.2 PSet PG/PC interface

This step is required for the following software:
=> TIA-Portal
=> SIMATIC Step© 7 Manager
=> Windows Control Center (WinCC) (v6.0)
=> Windows Control Center flexible 2004 (WinCC flexible) (v5.2.0.0)
=> ProTool/Pro (v6.0 + SP2)
=> Microwin 3.2
1. Open the system configuration by using the
start menu.
2. Click on „Set PG/PC interface“.
3. A Dialog with a list box named
“Interface Parameter Assignment Used:”
appears. This box should offer following
entries
TIC ETH/USB(MPI) or
TIC ETH/USB.MPI.1
TIC ETH/USB(Profibus) or
TIC ETH/USB.Profibus.1
TIC ETH/USB(PPI) or
TIC ETH/USB.PPI.1
or some “TCP/IP” entries
If this is the case, please continue with the
step MPI settings or Profibus settings.
If so not please install the "TIC-driver" on
this PC and after a restart this entries
must exist. If you want to install the
TCP/IP-driver follow the link.
5.1.2.1 TCP/IP RFC1006 Communication

4. Press "Select" to add the RFC1006 required
elements to the PG / PC - interface
configuration.
5. In the dialog "Select", choose" TCP / IP" and
click on "Install".
6. After successful installation, click "Close".
7. Back to the “Set PG/PC interface“ dialog you will now find the desired entries called “PC -
Adapter(Auto)“ (not supported), “PC - Adapter(MPI)“ and “PC - Adapter(PROFIBUS)“. Now
you are able to configure the bus.
If you want to use the “MPI“communication type go ahead with step MPI setting .
The settings for "PROFIBUS" is explained in Profibus setting .
5.1.2.2 MPI setting
7. Select "TIC ETH/USB(MPI)" and click
"Properties".
8. Open the properties dialog
9. Is the device-type is not identical with
your used device, search for your device
with "Search Device". Select the device in
the result windows and click on the button
"Apply".

10. Activate the "Automatic-mode" when
you will be shure, that the connected PLC
sends cyclic bus-parameter-protocols.
When not please configure the bus by
hand.
11. Save your configuration with „OK“ and close
the „Set PG/PC–interface“ dialog with „OK“.
5.1.2.3 Profibus setting

12. Mark the entry „TIC ETH/USB(PROFIBUS)“
and click on „Properties“.
13. Open the properties dialog
14. Is the device-type is not identical with
your used device, search for your device
with "Search Device". Select the device in
the result windows and click on the button
"Apply".
15. Activate the "Automatic-mode" when
you will be shure, that the connected PLC
sends cyclic bus-parameter-protocols.
When not please configure the bus by
hand.
16. Save your configuration with „OK“ and close
the „Set PG/PC–interface“ dialog with „OK“.
5.1.2.4 TCP/IP RFC1006 setting
17. For this kind of communication you only have to install the corresponding software.
5.1.2.5 ProTool/Pro RunTime (RT) Configuration

18. If you want to use ProTool/Pro RunTime you
can set the "PG/PC Interface" by selecting the
entry "DPSONLINE". Therefore you have to
select "Access Point of Application" and
configure it as described above. The easiest
way is to use the S7-LAN/MPI-LAN/MPI-USB-
driver which supports USB and LAN products.
The interface configuration for these programs is finished.
Continue with the software which you want to use:
=> SIMATIC Step© 7 Manager (v5.2 + SP1)
=> Windows Control Center (WinCC) (v6.0)
=> Windows Control Center flexible 2004 (WinCC flexible) (v5.2.0.0)
=> ProTool/Pro (v6.0 + SP2)
=> Microwin 3.2
5.1.3 SIMATIC Step© 7 Manager (v5.2 + SP1)
Configurate the interface as described in Set PD/PC-Interface.
1. Klick in the drop - down menu "target
system" on "Display Accessible Nodes".
2. If you can see the list with possible Bus-
devices, a communication over the cable has
taken place. "Direct" connected devices will
be shown, also the conditions if it is an
"active" or "passive" assembly.
3. In this window you can edit each assembly
with his blocks.
5.1.4 Windows Control Center (WinCC) (v6.0)
Configurate the interface as described in Set PD/PC-Interface.
1. Start WinCC by using the desktop link or the program entry in the start menu.
2. Choose „New” in the menu „File” or click on the white („letter”) symbol to start a new
project.

3. The next dialog offers you
several project types “Single-User
Project”, “Multi-User Project” and
“Client Project”.
The next steps are the describing
for the “Single- User Project”.
4. “OK” leads you to a new dialog. Type in the “Project
Name” and the “Subfolder” of the project path.
The chosen configuration is confirmed with “Create”.
To use one of the other options please go ahead and read in the manual of
WinCC software.
5. Please wait until the project is created. The project content will be shown in the left part of
the main window.
6. For a proper working
communication with the PLC there
must be defined how the software
has to communicate with the PLC
Therefore you have to right-click
on “Tag Management” it opens the
context menu. Choose “New Driver
Connection … “.

7. In the „Add new driver“ dialog
select the driver which fits to your
PLC
For a S7 PLC choose „SIMATIC S7
Protocol Suite.chn“.
If you want to use an other PLC
please inform yourself first, which
driver fits with your PLC.
It is very important that the selected driver fits with the PLC otherwise the
connection cannot be established..
8. You should see now in the Explorer under the branch “Tag Management” the branch
“SIMATIC S7 PROTOCOL SUITE”. Expand the branch and many protocols for various
compounds will appear.
The General way of proceeding a new connection is to:
Right-click on the desired connection (MPI - > Picture: “MPI“, TCP/IP - > Picture: “TCP/IP“).
A context menu opens. Click on „New Driver Connection…”.
This manual describes the connection configurations:
for „MPI„ (MPI-II-cable, MPI-USB-cable, S7-USB-modul, S7-LAN-modul and MPI-LAN-
cable)
for „TCP/IP„ (only S7-LAN-modul and MPI-LAN-cable).
MPI
TCP/IP
5.1.4.1 MPI Configuration

9. Now you are able to type in the
name of the connection. With a
click on “Configuration“ a new
dialog will appear. Now you are
able to set the properties of the
connection.
Set up the station address of the
PLC (in this example "2“).
Confirm with "OK" until you are
back to the main window.
Read further "Communication and
fault diagnosis “ .
5.1.4.2 TCP/IP Configuration
10. A dialog appears where you
can configure the connection
parameters.
Set up the IP - Address of the
module and configure the rack
number as well as the slot number.
Confirm this configuration by
clicking “OK”.
Example configuration:
IP - address 192.168.1.55
Rack - Number: 0
Slot - Nr.: 2
11. With a right-click on the new connection you can start the properties dialog. In this dialog
please click on properties.

12. In this “Channel unit properties”
you are able to see all “available
connections”.
Choose the latest created
connection and click again on
„Properties”.
Now you can see all the variables
which has been created for this
connection.
In fact this connection is a new
connection so there should not be
any variable in the list.
To add a new variable click on
„New”.
13. Now you are able to set up the name of the variable and different more properties.
In our example, we assign the following values:
Name: „S7LAN_MW0“
Data type : „unsigned 16 - Bit value“
Length: „2“
Address: „MW0“
Format adaptation: „WordToUnsignedWord“
Click on „Choose” beside the Address to define the address from the variable.
Example configuration: The data area from the variable is set to „Mark“ and the address is
set to „Word”. The edit box „MW“ is set to „0”.
14. Confirm all open dialogs with „OK“ until you reach the main window.
15. The connection needs to know which network interface card it should be used to send
data via the Ethernet. Open the “System parameters“dialog from the context menu (right-
click on TCP/IP).
16. Choose from the registry card „Unit“ and set the “logical device name“ to your network
interface card (usually the name of the NIC begins with a „TCP/IP - > „).
17. Confirm with „OK“.
18. Now you are able to start the communication. Stop it by clicking on .
5.1.4.3 Communication and fault diagnosis
To clean up errors faster the WinCC Software offers a tool named "Channel Diagnosis”. This
tool analyses all connections from your WinCC software. For demonstration purposes please
stop the last started connection from your WinCC explorer.
19. Start the software "Channel Diagnosis“ by using your link in the start menu.

20. The tool could not detect a
running connection so it marked
the connection/s with a red ‘X’
(registry card
"Channels/Connections“).
Click on the last created, not active
connection (with the red ‘X’) and
some informations from the
connection will appear in the right
part of the dialog.
One of these counters is called
"Last Error Code“.
21. If you take a right-click on the
error value a window opens with
“Help”.
Click on the “Help” window and a
yellow window appears (tooltip)
with detailed error descriptions.
22. Lets see what happens if the
connection runs properly. Start the
connection from your WinCC
Explorer.
The "Channel Diagnosis“dialog
marks the connection with a green
hook if everything worked out.
5.1.5 Windows Control Center flexible 2004 (WinCC flexible) (v5.2.0.0)
Please make sure that the interface configuration is correct as described in PD/PC-
Set interface
1. Start the WinCC flexible 2004 software by using the desktop link or the program entry in
the start menu.

2. First you need to select “Create an empty project” on your first page.
3. In the "Device selection“mark the used
operator panel (example: "TP 170A“)
confirm with "OK“.
4. After the project has been created right-click
in the project window on “Connections“of the sub
menu “Communication“.
In the context menu click on “Add Connection“.
5. A new configuration window “Connections” opens in the right part of the main window. This
offers you different setting options.
Important for the connection is:
=> the communication driver (set up which PLC you are using (example: "SIMATIC S7
300/400“))
=> the Baud rate (Set this on "187 500")
=> the address of the terminal (HMI) (in this example "1“)
=> the Profile ("MPI“ for example)
=> the Highest Station Address (HSA) (e.g. "126“)
=> the address of the PLC (e.g. "2“)
This manual suits for next models
3
Table of contents
Other PI Cables And Connectors manuals
Popular Cables And Connectors manuals by other brands
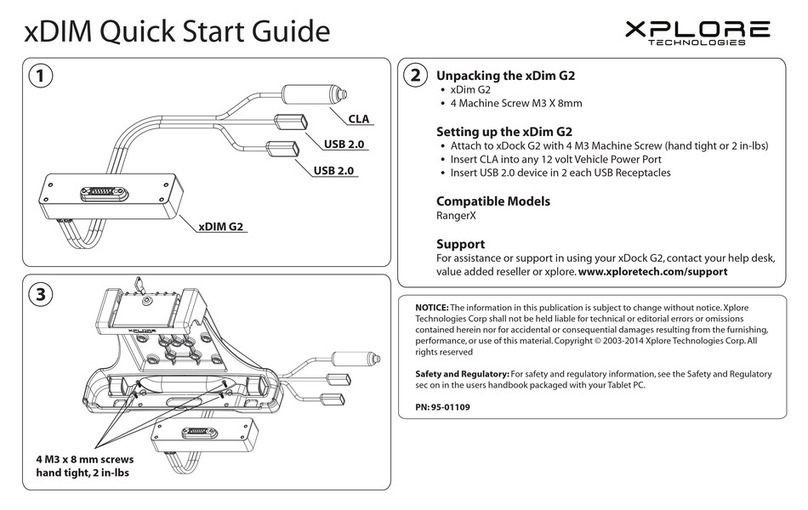
Xplore
Xplore xDIM quick start guide
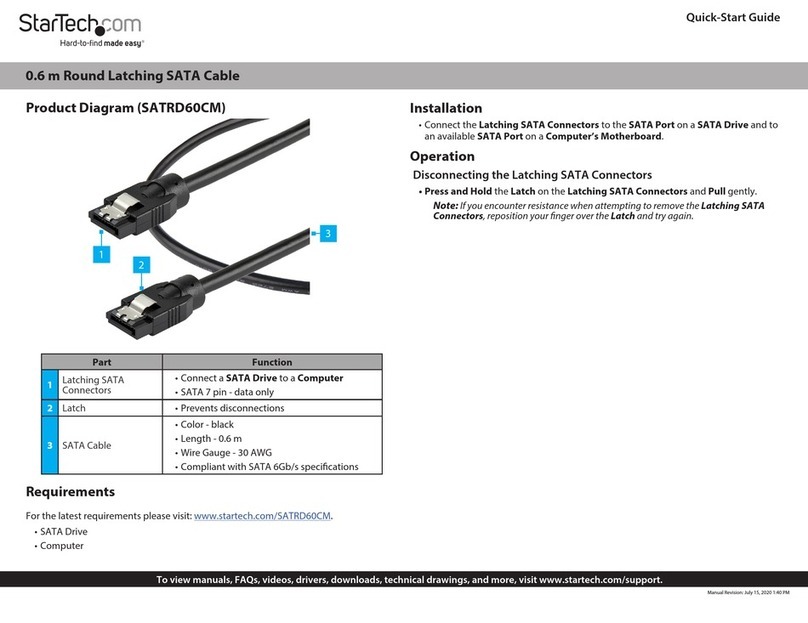
StarTech.com
StarTech.com SATRD60CM quick start guide
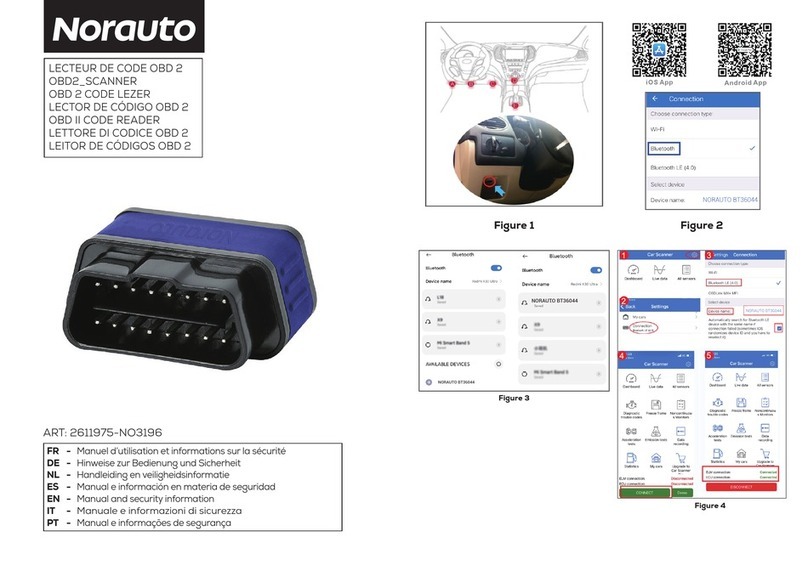
NORAUTO
NORAUTO NO3196 Installation Manual and Security Information
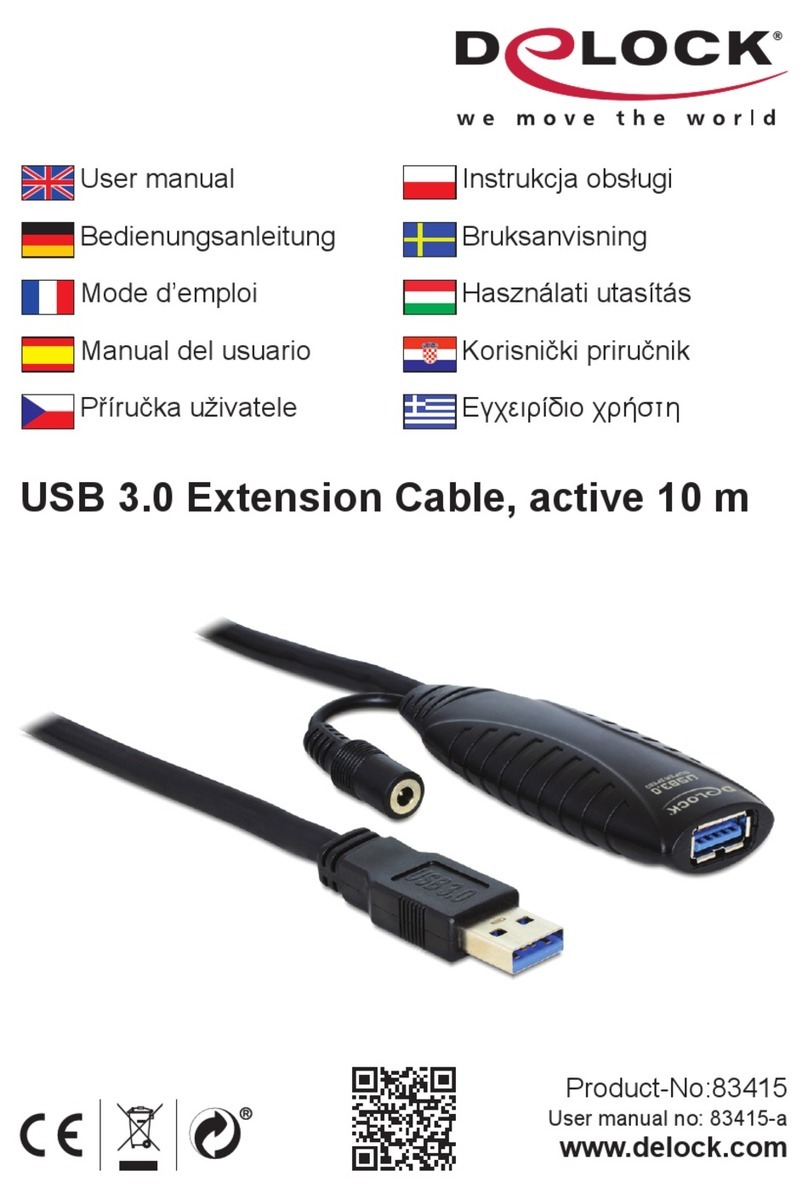
DeLOCK
DeLOCK 83415 user manual
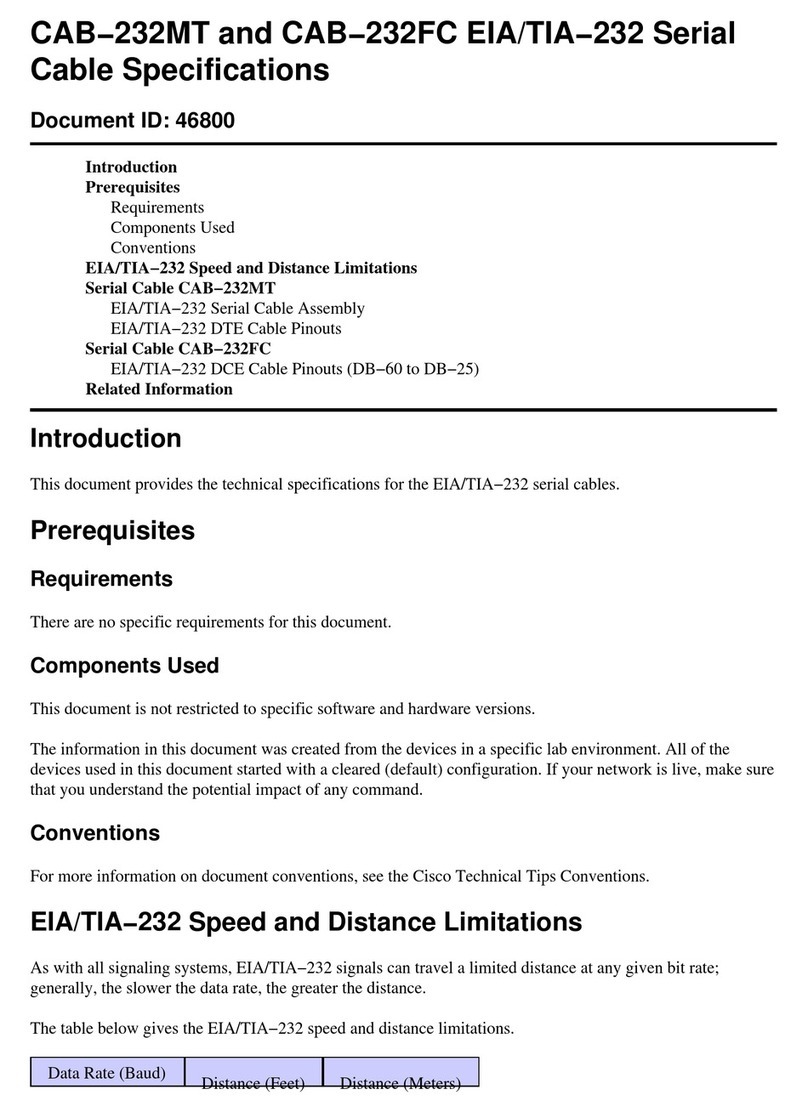
Cisco
Cisco EIA/TIA-232 Serial Cable CAB-232FC Specification sheet
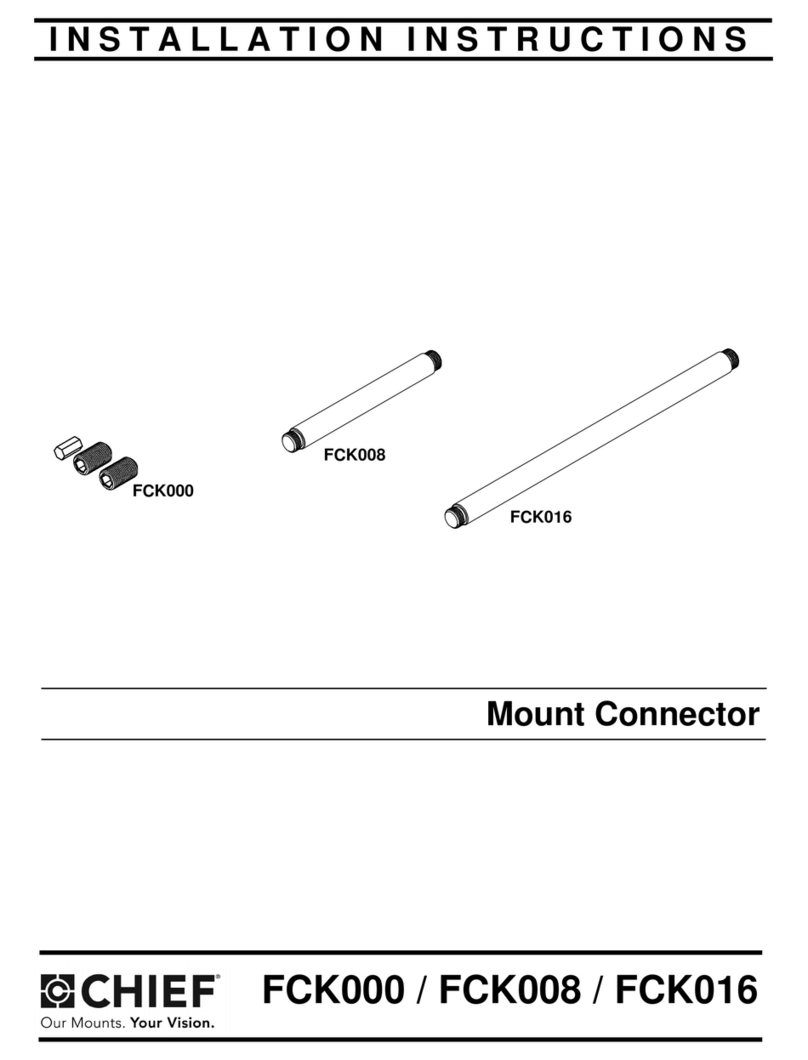
CHIEF
CHIEF Wall Mount PDWP MB 40 L installation guide
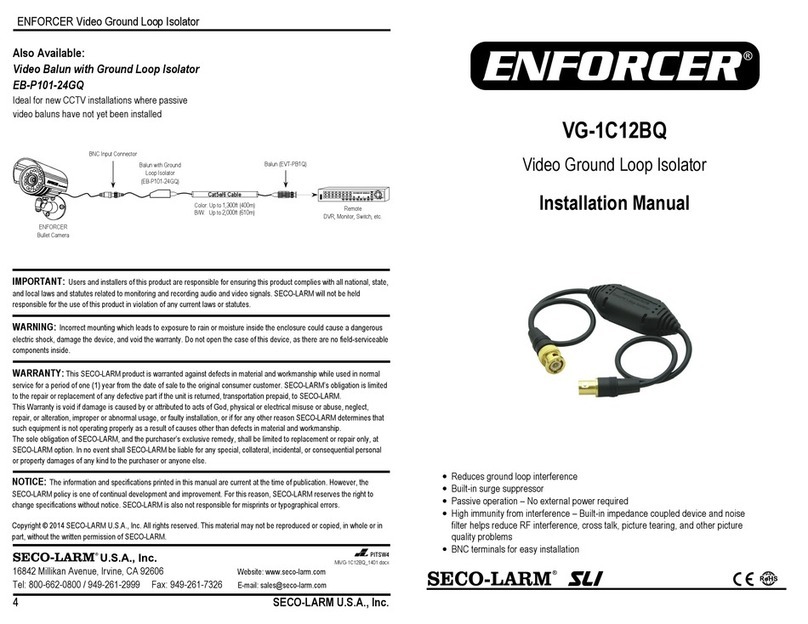
SECO-LARM
SECO-LARM ENFORCER VG-1C12BQ installation manual
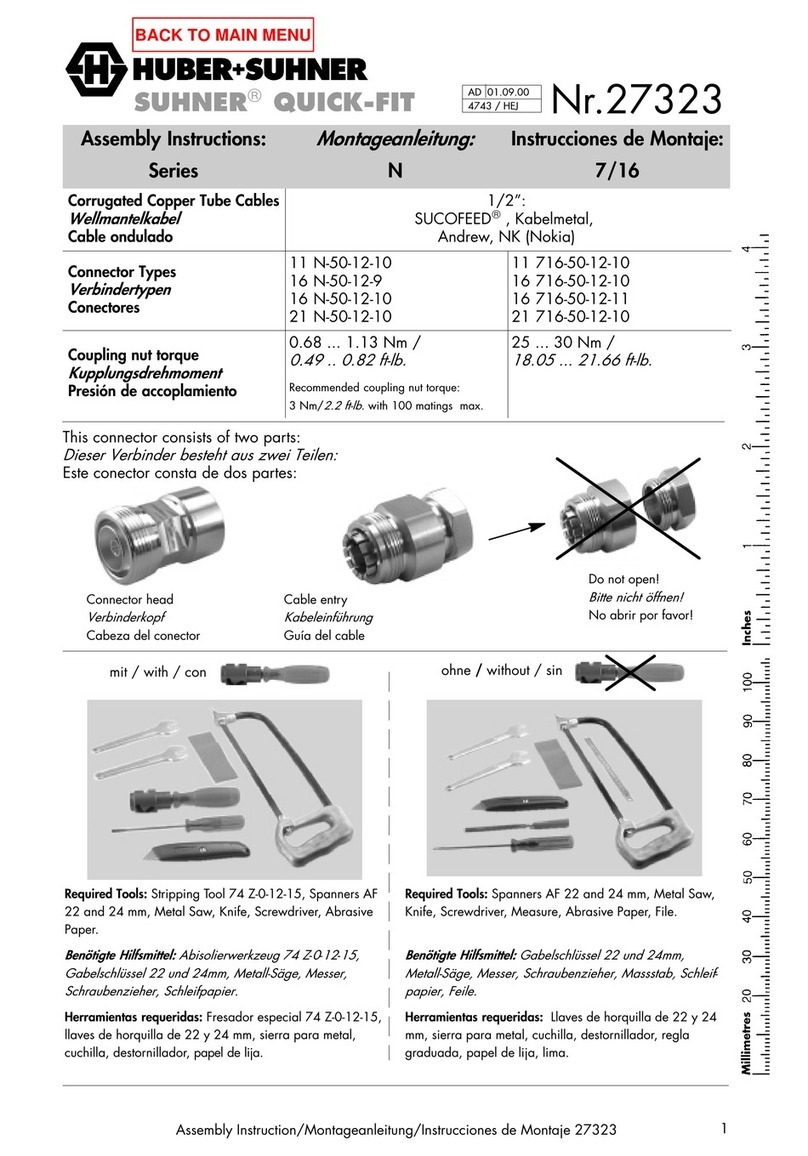
HUBER+SUHNER
HUBER+SUHNER 11 N-50-12-10 Assembly instructions
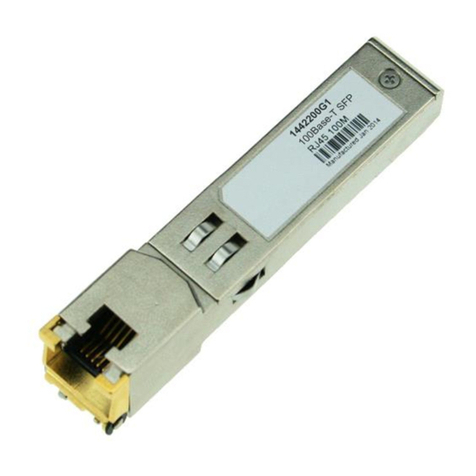
ADTRAN
ADTRAN 1442200G1 quick start guide
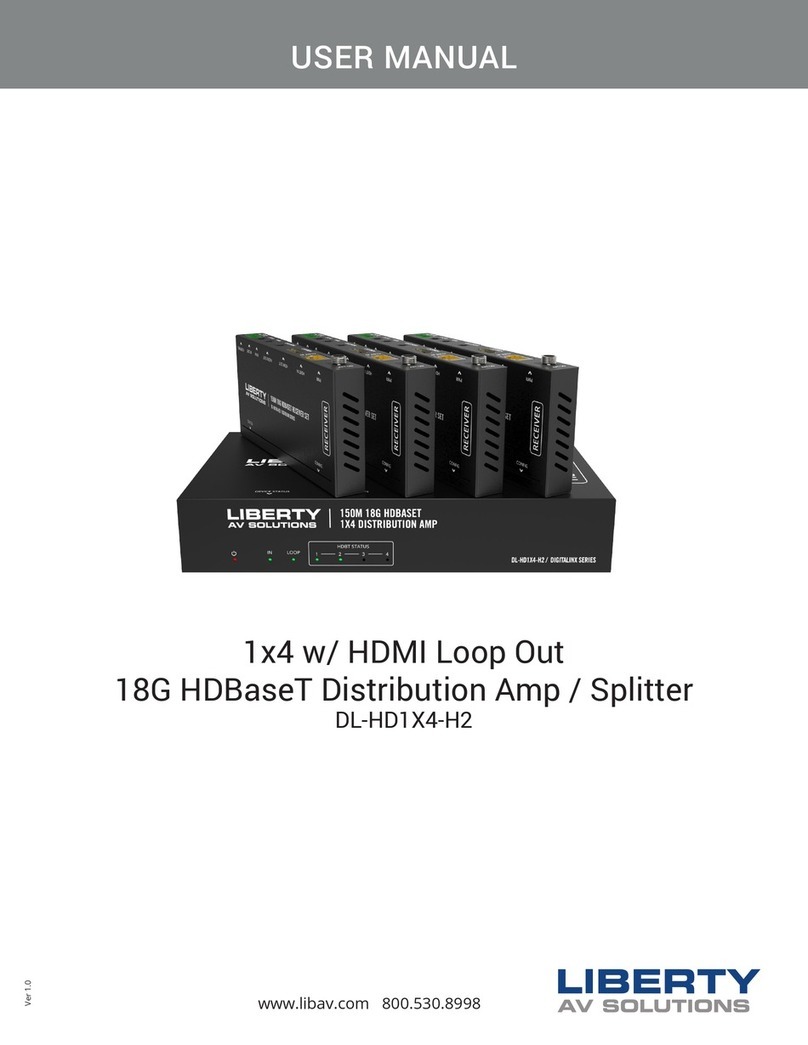
LIBERTY AV SOLUTIONS
LIBERTY AV SOLUTIONS DL-HD1X4-H2 user manual
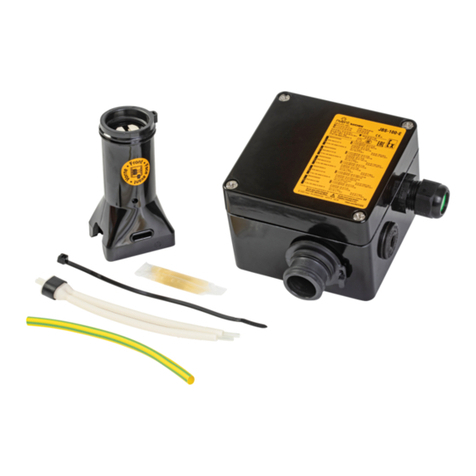
nvent
nvent JBS-100-STB installation instructions

Kanaan
Kanaan KN40546 user manual