PiezoDrive PDUS210 User manual

PDUS210 V4
1
Modified 6/02/2021
PDUS210
210 Watt Ultrasonic Driver

PDUS210 V4
2
Modified 6/02/2021
Contents
Safety Warnings...............................................................................................................................3
Revision History...............................................................................................................................3
Quick Start Recommendations ........................................................................................................3
Delivery Contents (Standard)...........................................................................................................3
Overview..........................................................................................................................................4
Electrical Specifications ...................................................................................................................5
Standard Output Voltage Ranges ....................................................................................................5
Mechanical Specifications................................................................................................................7
PDUS210-FLEX Specifications........................................................................................................8
Introduction to Ultrasonic Transducers ............................................................................................8
PDUS210 Operation ......................................................................................................................10
Choosing the Voltage Range.........................................................................................................14
Front Panel ....................................................................................................................................16
Rear Panel.....................................................................................................................................17
Overload Protection.......................................................................................................................18
Desktop Software...........................................................................................................................19
PDUS210-FLEX Operation............................................................................................................29
Handheld Controller.......................................................................................................................31
RS485 Interface.............................................................................................................................33
Warranty and Service ....................................................................................................................34

PDUS210 V4
3
Modified 6/02/2021
Safety Warnings
High Voltage
This product produces potentially lethal voltages up to 282 Vrms.
Observe Low-Voltage (as per ANSI C84.1-1989) safety precautions, e.g.
●Use an observer trained in low-voltage rescue
●Do not operate with exposed conductors
●Use appropriate signage, etc.
Revision History
Date
Manual
Changes
6/02/2020
R8
Added recommended impedance range
31/10/2020
R7
Added support for external transformers
Minimum frequency changed to 6 kHz
Added frequency range specifications
Added 175V version
15/01/2020
R6
Added notes to “Standard Output Voltage Ranges”
Quick Start Recommendations
Most users will need to read the following sections in detail to gain an understanding of transducer
characteristics and the various operating modes. That is, read the following sections in order.
If you already have expert knowledge of ultrasonic transducers and their different operating
modes, go straight to the section on Desktop Software.
Delivery Contents (Standard)
PDUS210 Amplifier (in chosen configuration)
Handheld controller
Handheld controller cable (DSUB9 3ft)
280W Desktop power supply
IEC Power cable suited to the destination shipping address
USB Cable (Type A)
3 Way plug-in screw terminals for output (Amphenol TJ0331530000G)
4 Way plug-in screw terminal for RS-485 connector (Amphenol TJ0431530000G)

PDUS210 V4
4
Modified 6/02/2021
Overview
The PDUS210 is a complete solution for driving precision and high-power ultrasonic actuators.
Functions include high-speed resonance tracking of both series or parallel resonance modes,
vibration amplitude control, and analysis functions such as impedance and frequency response
measurement. The PDUS210 is well suited to both OEM product integration and laboratory use for
research and development. Applications include ultrasonic drilling and cutting, medical devices,
dental devices, ultrasonic testing, liquid cavitation, and vaporization.
The PDUS210 is controlled via USB and the included software package. An RS485 interface also
provides a straight-forward method to control and monitor the amplifier for automatic test and OEM
applications.
The PDUS210 generates a pure sine-wave output which avoids the excitation of secondary
resonance modes by the drive harmonics. This makes it ideal for operating at the electrical parallel
resonance, or ‘anti-resonance’. This operating point is close to the mechanical resonance
frequency but is less sensitive to changes in load dissipation, which is useful in precision
machining applications where constant vibration amplitude is desired.
The PDUS210 is available with standard output voltage ranges from 17 Vrms to 282 Vrms, and
current ranges from 0.7 Arms to 11 Arms. These ranges are optimized for load impedances
ranging from 1.5 Ohms to 400 Ohms at resonance. For research and development applications, a
reconfigurable version is available (PDUS210-FLEX), this version uses external output matching
transformers to allow operation at any of the available output voltage ranges.

PDUS210 V4
5
Modified 6/02/2021
Electrical Specifications
Specification
Value
Notes
Output Voltage
0 –800 Vp-p
See standard voltage ranges
Output Current Max
0 –32 Ap-p
See standard voltage ranges
Load Impedance
1–5
See standard voltage ranges
Output Waveform
Sine wave
DC Output Voltage
Zero
DC offset possible
Output Isolation
Isolated or grounded
Max Output Power
210 W
With optimal load impedance
Internal Power Dissipation
130 W
Maximum
Frequency Range
See table below
6kHz to 500kHz with modifications
Power Supply
48 V, 280 Watt
Controller
Phase tracking and
power control
2ms frequency update rate
Resonance or anti-resonance
Interface
USB, RS485
Digital IO
4 DIO
For manual control
Standard Output Voltage Ranges
The following table lists the specifications of each model variant, including: the maximum output
voltage, the maximum output current, optimal load impedance and the recommended frequency
range.
Order Code
Voltage
pk-pk
Voltage
RMS
Amps
pk-pk
Amps
RMS
Optimal
Load Ohms
Load Range
Ohms*
Frequency
kHz
PDUS210-800
800
282
2
0.71
400
260 –840
20 –200
PDUS210-600
600
212
2.6
0.92
225
146 –472
20 –200
PDUS210-400
400
141
4
1.4
100
65 –210
20 –200
PDUS210-200
200
70
8
2.8
25
16 –52
20 –200
PDUS210-175
175
62
9.1
3.2
19.1
12 –40
10 - 100
PDUS210-100
100
35
16
5.7
6.25
4 –13
20 –200
PDUS210-50
50
17
32
11.3
1.56
1 - 3
20 –200
Note: The output voltage resolution and tolerance is 8 bits, or 256 levels. Therefore, the smallest
possible change in voltage is full-scale range / 256. The minimum output voltage is also limited by
resolution. When the amplifier is enabled and the output voltage is set to zero volts, the actual
output voltage may be up to 2% of the full-scale range.
* The load impedance range is the range of impedances which guarantee more than 100W of
power supplied to the load. Higher or lower impedances can be driven but with reduced power.

PDUS210 V4
6
Modified 6/02/2021
The relationship between maximum achievable power and the load impedance is plotted in the
following figure. In this plot, the impedance is normalized by the optimal impedance; that is,
For example, the optimal impedance of the PDUS210-400 is 100 Ohms, so with a 50 Ohm load,
the normalized impedance is 0.5, From the plot, it can observed that greater than 100 W can be
achieved with a normalized impedance from 0.65 to 2.1, which for the PDUS210-400, is 65 Ohms
to 210 Ohms.
Figure 1. Maximum output power versus normalized impedance
The impedance ranges for other common power levels are listed in the following table. For
example, all amplifiers will supply more than 150W with a normalized load impedance between
0.71 and 1.4. For the PDUS210-400, this is equivalent to 71 Ohms and 140 Ohms.
Minimum Power
Lower Bound
Upper Bound
150W
100W
50W
Table 1. Minimum achievable power versus load impedance.

PDUS210 V4
7
Modified 6/02/2021
Mechanical Specifications
Specification
Value
Notes
Enclosure Dimensions
227 x 168 x 54 mm
L x W x H
Mass
1.4 kg
Temperature Range
0C - 50C
Humidity
Non-condensing

PDUS210 V4
8
Modified 6/02/2021
PDUS210-FLEX Specifications
The PDUS210-FLEX is identical to the standard PDUS210 except that it requires an external
transformer connected between the amplifier and transducer using the supplied cable. This allows
the user to switch between different output voltage ranges by changing the external transformer.
Please refer to the section PDUS210-FLEX Operation for instructions.
The PDUS210-FLEX must be purchased with at least one external transformer. The available part
numbers and specifications are:
Order Code
Turns
Ratio
Voltage
pk-pk
Voltage
RMS
Amps
pk-pk
Amps
RMS
Optimal
Load Ohms
Load Range
Ohms*
Frequency
kHz
TX210-800
18.18
800
282
2
0.71
400
260 –840
20 –200
TX210-600
13.64
600
212
2.6
0.92
225
146 –472
20 –200
TX210-400
9.09
400
141
4
1.4
100
65 –210
20 –200
TX210-200
4.55
200
70
8
2.8
25
16 –52
20 –200
TX210-175
3.98
175
62
9.1
3.2
19.1
12 –40
10 - 100
TX210-100
2.27
100
35
16
5.7
6.25
4 –13
20 –200
TX210-50
1.14
50
17
32
11.3
1.56
1 - 3
20 –200
Table 2. External transformer specifications (only for the PDUS210-Flex)
A kit containing six transformers ranging from 17Vrms to 282Vrms is also available (TX210-Kit1).
This includes the following output voltage ranges: 17, 35, 70, 141, 212, and 282 Vrms.
Figure 2. Output transformer (e.g. TX210-800)
Specification
Value
Notes
Input Connector
Plug-in screw terminal
Connecting cable supplied
Output Connectors
Identical to PDUS210
See “Front Panel” section
Transformer Dimensions
104 x 57 x 51 mm
L x W x H
Mass
0.2 kg
Table 3. External transformer mechanical specifications

PDUS210 V4
9
Modified 6/02/2021
Introduction to Ultrasonic Transducers
An introduction to the behaviour and operation of ultrasonic transducers can be viewed at the
following link. Please familiarize yourself with these concepts before operating the PDUS210.
https://www.piezodrive.com/ultrasonic-drivers/intro-ultrasonic/
The most important concept to understand is the relationship between the electrical and
mechanical impedance response of a transducer. Figure 3 plots the mechanical and electrical
frequency response of an ultrasonic transducer.
The impedance minima at
is known as the series resonance, which is approximately equal to
the mechanical resonance frequency. At this frequency, the impedance phase response has a
high positive slope and a value of approximately zero degrees. In this mode, the current is
approximately proportional to the vibration amplitude, so current control is used to maintain
constant vibration amplitude. If the mechanical load does not vary significantly, constant voltage
amplitude is also appropriate.
The impedance maxima at
is known as the parallel resonance, which also has an electrical
phase of approximately zero degrees but a high negative slope. In this mode, the voltage is
approximately proportional to the vibration amplitude, so constant voltage results in approximately
constant vibration amplitude regardless of mechanical load variations.
Figure 3. Electrical and mechanical frequency response of an ultrasonic transducer

PDUS210 V4
10
Modified 6/02/2021
PDUS210 Operation
Overview
The operating principle of the PDUS210 is summarized in Figure 4. The transducer is connected
on the right hand side to the output transformer. The transformer converts the internal +/-24V drive
voltage to the desired output voltage range, for example +/-200V. By default, the output
connection to the transducer is electrically isolated from ground but the negative output can also
be internally grounded using the jumper shown.
During operation, the voltage and current in the transducer is used to estimate the phase . The
measured phase is then used to control the frequency of the signal generator by comparing it to
the phase set point . The frequency controller stabilizes the feedback loop and controls the
settling time of the closed loop system. The feedback gain is normally determined experimentally
by slowly increasing the gain until the desired performance is reached or the response begins to
become unstable.
The signal generator has a variable amplitude and the frequency is normally controlled by the
phase control loop. It is connected to the power amplifier, which drives the output transformer and
transducer.
Figure 4. Internal PDUS210 operation (in constant voltage, resonance tracking mode).
Resonance Tracking
The resonance tracking system of the PDUS210 is illustrated Figure 3. The phase detector (M)
measures the impedance phase angle between the primary voltage and current. The phase
controller varies the drive frequency to maintain a constant phase set point , which is
usually equal to zero.
To operate at a series resonance (impedance minima), the phase controller gain must be positive
to create a stable operating point.
To operate at a parallel resonance (impedance maxima), the phase controller gain must be
negative to create a stable operating point.
Transducer
Ground
Connection
Transformer
Transformer
Transformer
Power
Amplifier
Transformer
Phase
Setpoint
Signal
Generator
Frequency
Controller
Phase Detector

PDUS210 V4
11
Modified 6/02/2021
Applications with high losses, i.e. low quality factor, may have a non-zero impedance phase angle
at resonance, e.g. 45 degrees. In such cases, an impedance response should be performed first,
to identify the desired operating phase that corresponds to the desired mechanical resonance.

PDUS210 V4
12
Modified 6/02/2021
Control of Vibration Amplitude
Power ultrasonic applications can be categorized as either constant mechanical load, or variable
mechanical load. The requirements for both of these cases are described in the following.
Constant Mechanical Load
Constant load applications are the simplest case and include, for example, ultrasonic cleaners,
ultrasonic mixers, and any other application where the mechanical load does not vary significantly.
These applications can be operated with constant voltage at either the series or parallel
resonance.
Variable Mechanical Load
Applications with variable mechanical load include ultrasonic drills and cutters where the
mechanical load conditions are variable during operation. These applications generally require
some form of amplitude control in order to: 1) maintain vibration amplitude when the mechanical
load dissipation increases; and 2) to avoid vibration amplitude increasing when the mechanical
load dissipation is removed.
To achieve approximately constant vibration amplitude, a transducer can be driven with constant
voltage at the parallel resonance frequency, or constant current at the series resonance
frequency.
Constant voltage is the natural operating mode of the PDUS210 but constant current can also be
achieved by enabling the current tracking mode. The operation of current tracking mode is
illustrated in Figure 5. Current tracking mode has the same frequency control loop as Figure 4 but
it also has an additional feedback loop that varies the voltage to maintain a constant load current.
The current set point is and the controller is .
Current tracking mode is most useful for achieving constant vibration amplitude in transducers
operated at the series resonance mode (impedance minima).
Figure 5. Phase and current control loop in the PDUS210 driver.
Phase
Setpoint
Signal
Generator
Frequency
Controller
Transducer
Ground
Connection
Transformer
Transformer
Transformer
Power
Amplifier
Transformer
Phase and Current Detector

PDUS210 V4
13
Modified 6/02/2021
Power Control
When operating with constant voltage or current, a limit can be set on the maximum power
dissipation in the load. This power is the sum of dissipation in the mechanical load and the
transducer itself.
In some applications, such as welding, it may be preferable to control the dissipated power rather
than the vibration amplitude. The PDUS210 has a power control function that varies the voltage to
maintain a constant power dissipation in the load. As shown in the Figure 6, the power control loop
includes the power measurement which is compared to the power set-point . The gain of the
controller is tuned experimentally to provide a fast transient response and stability.
Figure 6. Phase and power control loop in the PDUS210 driver.
Phase
Setpoint
Signal
Generator
Frequency
Controller
Transducer
Ground
Connection
Transformer
Transformer
Transformer
Power
Amplifier
Transformer
Phase and Power Detector

PDUS210 V4
14
Modified 6/02/2021
Choosing the Voltage Range
The PDUS210 is available in voltage ranges from 17 Vrms to 282 Vrms, which suit load load
impedances ranging from 1.5 to greater than 400 . The optimal choice is determined by the
transducer impedance at resonance, and the choice of series or parallel resonance. If the load
impedance is unknown, or a range of load impedances are expected, the PDUS210-Flex
configuration is recommended with the transformer kit (TX210-Kit1), please refer to the section

PDUS210 V4
15
Modified 6/02/2021
PDUS210-FLEX Specifications.
The first step is to measure the impedance of the transducer at the series and parallel resonance.
This can be performed with an impedance analyser or simply a signal generator and oscilloscope.
If possible, these tests should be performed at moderate power with both minimum and maximum
load conditions, i.e. using a PDUS210 driver. Fill out the values in the table below:
Unloaded
Fully Loaded
Series Resonance
:
:
Parallel Resonance
:
:
Table 4. Operating impedance at resonance
Series Resonance
For operation at the series resonance, the most suitable amplifier has an optimal impedance which
is close to, or slightly greater than the fully loaded impedance. Since transducer impedance tends
to increase with applied power, an amplifier with a higher optimal impedance is recommended. If
the amplifier has a higher optimal impedance than the load, the current limit will be reached before
the voltage limit, and the maximum achievable output power is:
where is the maximum driver current.
Parallel Resonance
For operation at the parallel resonance, the most suitable amplifier has an optimal impedance
which is close to, or slightly less than the fully loaded impedance. Since transducer impedance
tends to reduce with applied power, an amplifier with a lower optimal impedance is recommended.
If the amplifier has a lower optimal impedance than the load, the voltage limit will be reached
before the current limit, and the maximum achievable output power is:
where
is the maximum driver voltage.
Custom Voltage Range
Custom voltage ranges and optimal impedances are available to provide maximum power for a
specific transducer.

PDUS210 V4
16
Modified 6/02/2021
Front Panel
Label
Function
ON
Power indicator
OVL
Indicates an overload or shutdown state, see overload protection
USB
USB 2.0 Type-B device connector
L1
Uncommitted LED indicator
L2
USB Activity indicator
RS485
Isolated RS485 interface, suits Amphenol TJ0431530000G connector
GND is the isolated ground.
Test
+/-4V Input produces full-range output voltage. Test use only.
Aux
Connected to ADC converter, not presently used
Current Mon
Output current monitor, AC coupled. The gain is
V/A
Volt Mon
Output voltage monitor, AC coupled. The gain is
V/V
LEMO HV Output
Suits LEMO 0B.302 Connector (e.g. FGG.0B.302.CLAD42)
Screw HV Output
Suits Amphenol TJ0331530000G connector
The sensitivity of the current and voltage monitors are determined by the peak-to-peak output
voltage range. For example, the peak-to-peak output voltage range of the PDUS210-400 is 400 V,
so the current gain is 1.056 V/A, and the voltage gain is 0.01265 V/V.

PDUS210 V4
18
Modified 6/02/2021
Overload Protection
There are three types of overload protection:
Hardware Overload
This overload is triggered when the current to the power amplifier exceeds 5.7 Amps average.
When triggered, the power amplifier is shutdown, causing the ‘Overload’front panel LED to
illuminate. To restart the amplifier, an enable command is required.
At power-on, the power amplifier is shutdown by default and requires an enable command to start.
Load Power Dissipation Overload
This overload is triggered when the real power dissipated by the load exceeds the threshold
defined in the user interface. An enable command is required to clear this overload.
Amplifier Power Dissipation Overload
This overload is triggered when the real power dissipated by the amplifier exceeds 130 Watts. An
enable command is required to clear this overload. Triggering this overload usually means that the
load impedance is poorly matched to the output voltage and current range of the amplifier.
Thermal Overload
This overload is triggered when the heatsink temperature exceeds 70C. An enable command is
required to clear this overload. Check the fan and heatsink for blockages.

PDUS210 V4
19
Modified 6/02/2021
Desktop Software
Installation
Download the latest software from www.piezodrive.com and run the executable, which will extract
the desktop software to the selected folder. Go into the folder and launch the executable
(piezodrive.exe).
First Connection
The PDUS210 uses the HID device class to communicate over USB. For the first connection, the
amplifier should be powered on before connecting it to the PC. After this first connection, widows
will assign the appropriate driver.
To power
supply
Output
USB
Test load
(not included)

PDUS210 V4
20
Modified 6/02/2021
Firmware Update
After the first connection, the amplifier’s firmware needs to be updated to ensure compatibility
between the amplifier and desktop software. The firmware also needs to be updated after
downloading a new version of the desktop software. The desktop software will automatically
download the latest compatible version of the firmware; thus, it is import to check for new desktop
software periodically at: https://www.piezodrive.com/ultrasonic-drivers/pdus210-ultrasonic-driver/
The procedure for firmware update is:
To update the firmware, click on the settings tab, then
click the ‘Update Firmware’switch. When the update
firmware switch is on, the desktop software will begin
downloading the latest firmware.
Once the firmware has been downloaded, the software
will prompt you to restart your amplifier (turn the power
switch off and on). If your amplifier was already turned off,
simply turn it on.
Once the amplifier is reset, the desktop software will start
the transfer. Do not interrupt this transfer. If the transfer
fails or the device is not found, start the firmware update
process again.
Offline Firmware Update
If an internet connection is not available or you do not
have access to Google servers. You can manually
download the latest firmware from www.piezodrive.com.
To ensure compatibility, also download the latest version
of the desktop software.
To perform a manual firmware update, press the ‘Load’
button at the bottom of the settings tab. Use the file
browser to select the downloaded firmware. The software
will now show the ‘File Loaded’ status. Click the update
firmware switch and restart the PDUS210 when
prompted. This update process has an identical result to
the online procedure.
1
2
3
4
5
1
2
3
Other manuals for PDUS210
2
This manual suits for next models
15
Table of contents
Other PiezoDrive Amplifier manuals
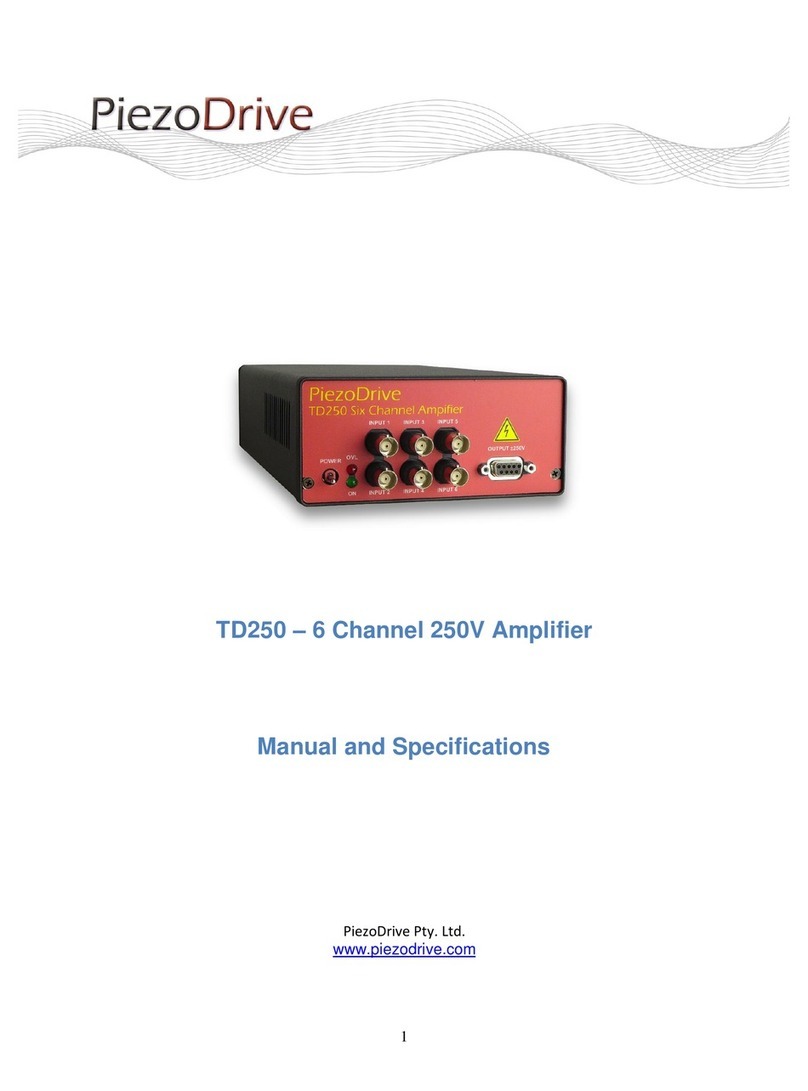
PiezoDrive
PiezoDrive TD250 User manual
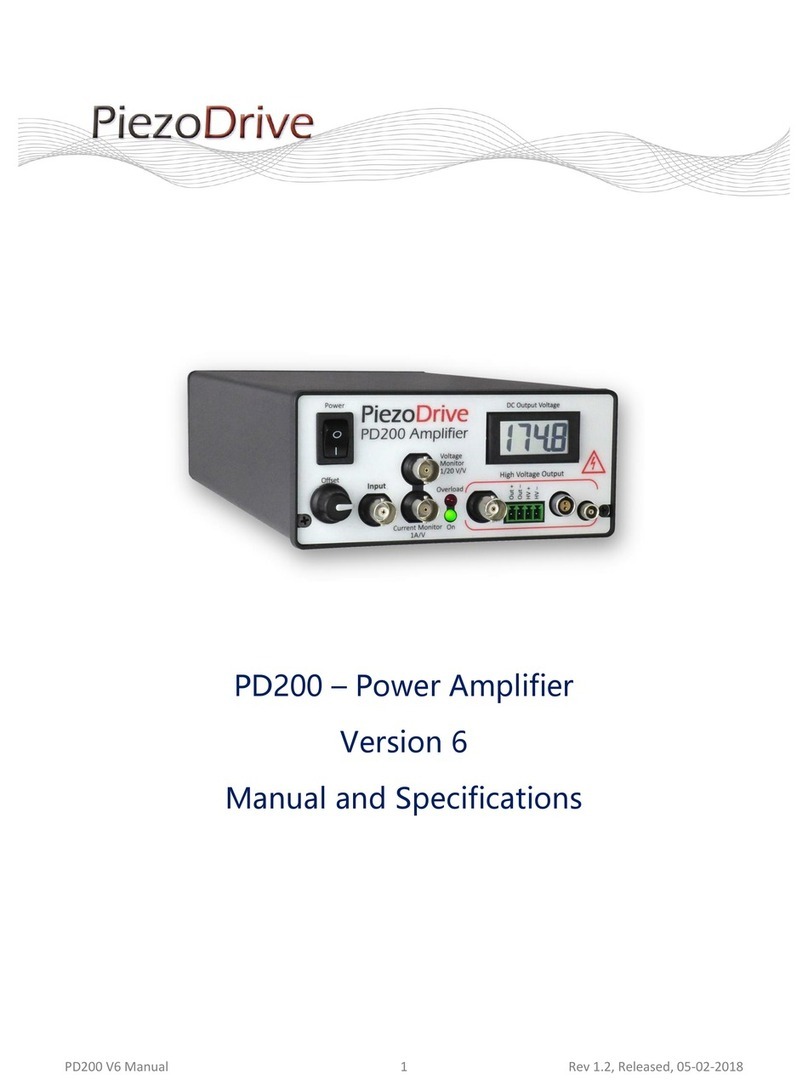
PiezoDrive
PiezoDrive PD200 User manual
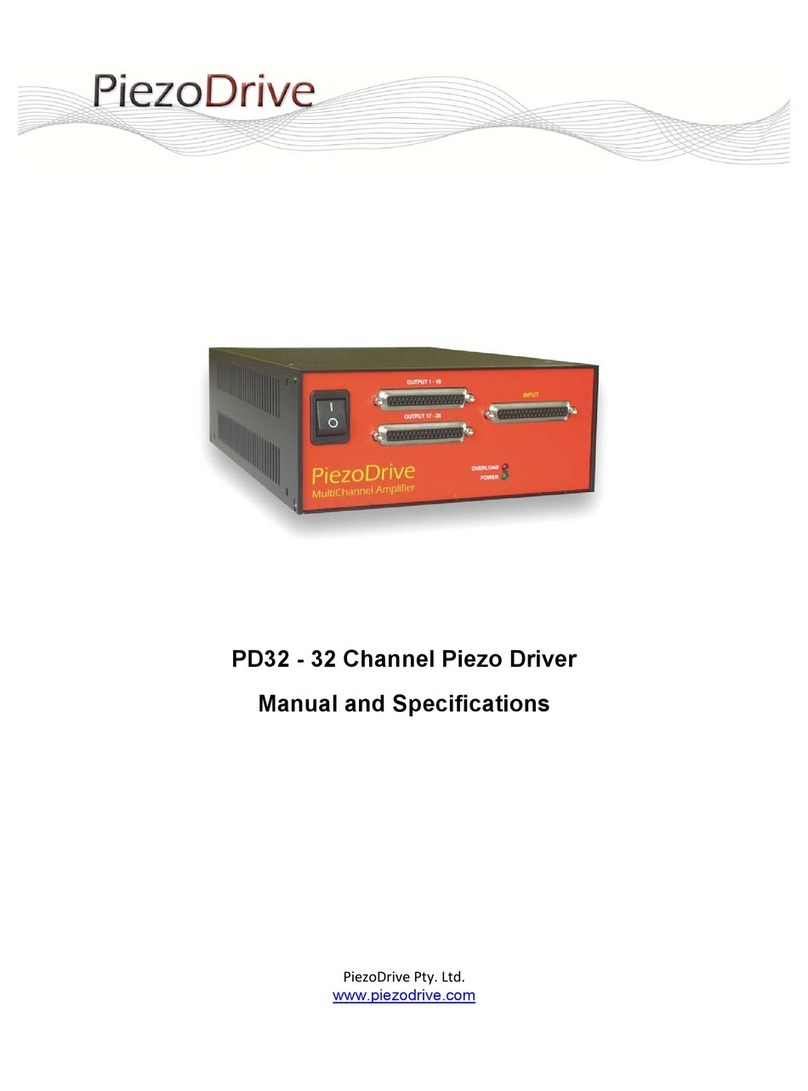
PiezoDrive
PiezoDrive PD32 User manual
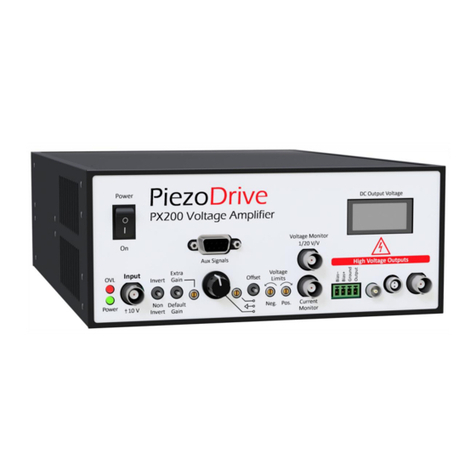
PiezoDrive
PiezoDrive PX200 User manual
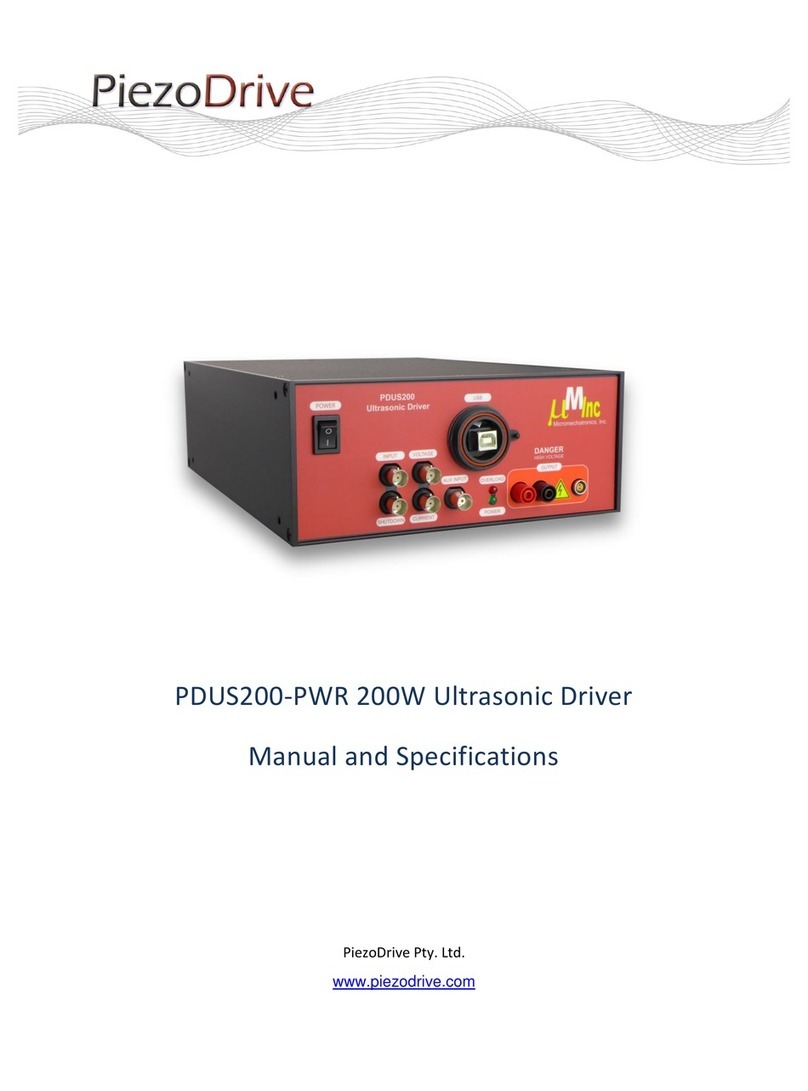
PiezoDrive
PiezoDrive PDUS200-PWR User manual
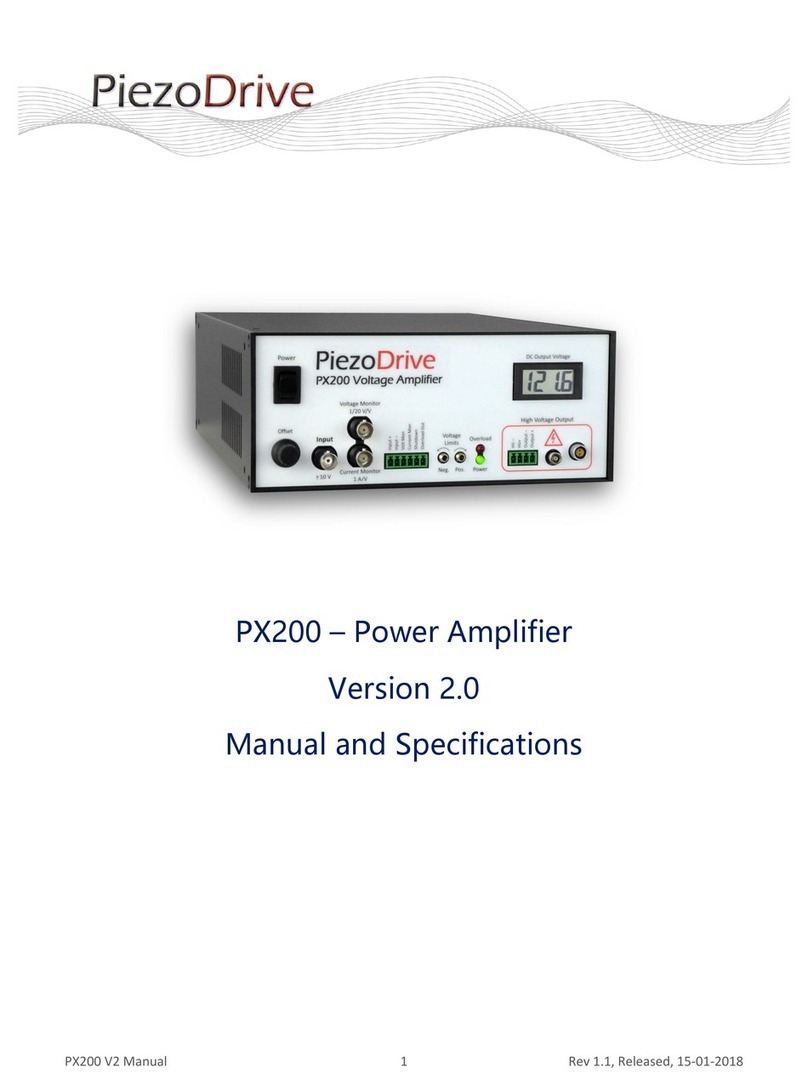
PiezoDrive
PiezoDrive PX200 User manual
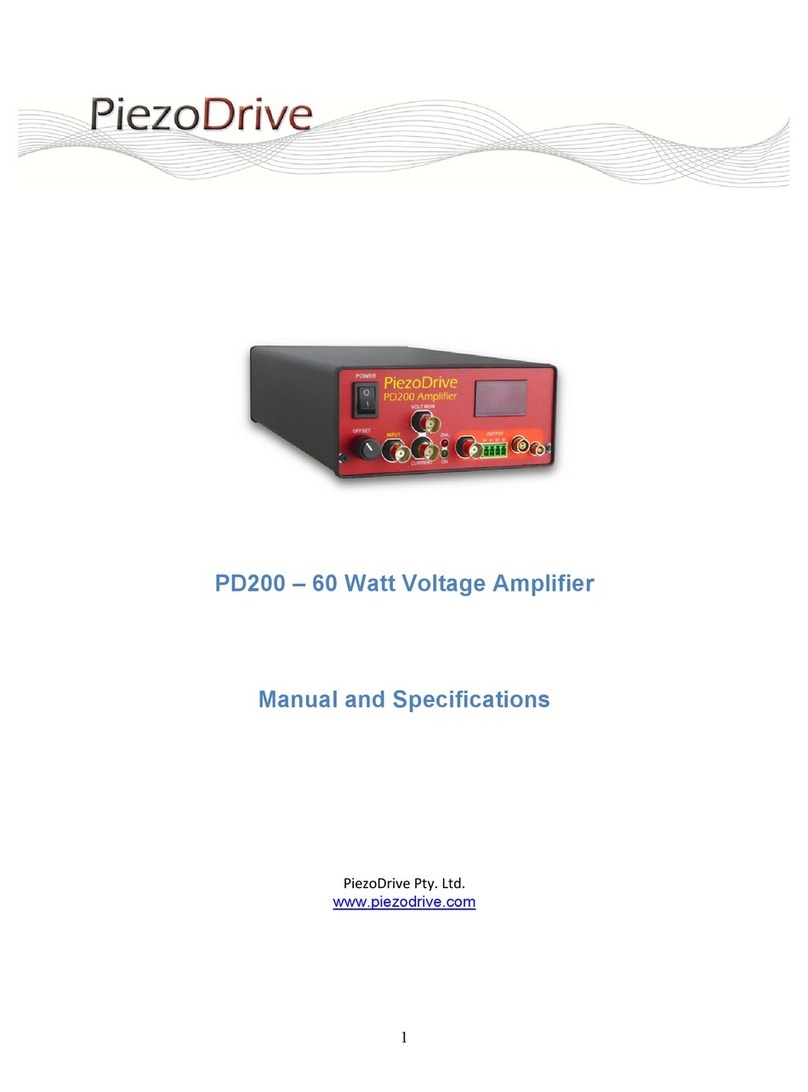
PiezoDrive
PiezoDrive PD200 User manual
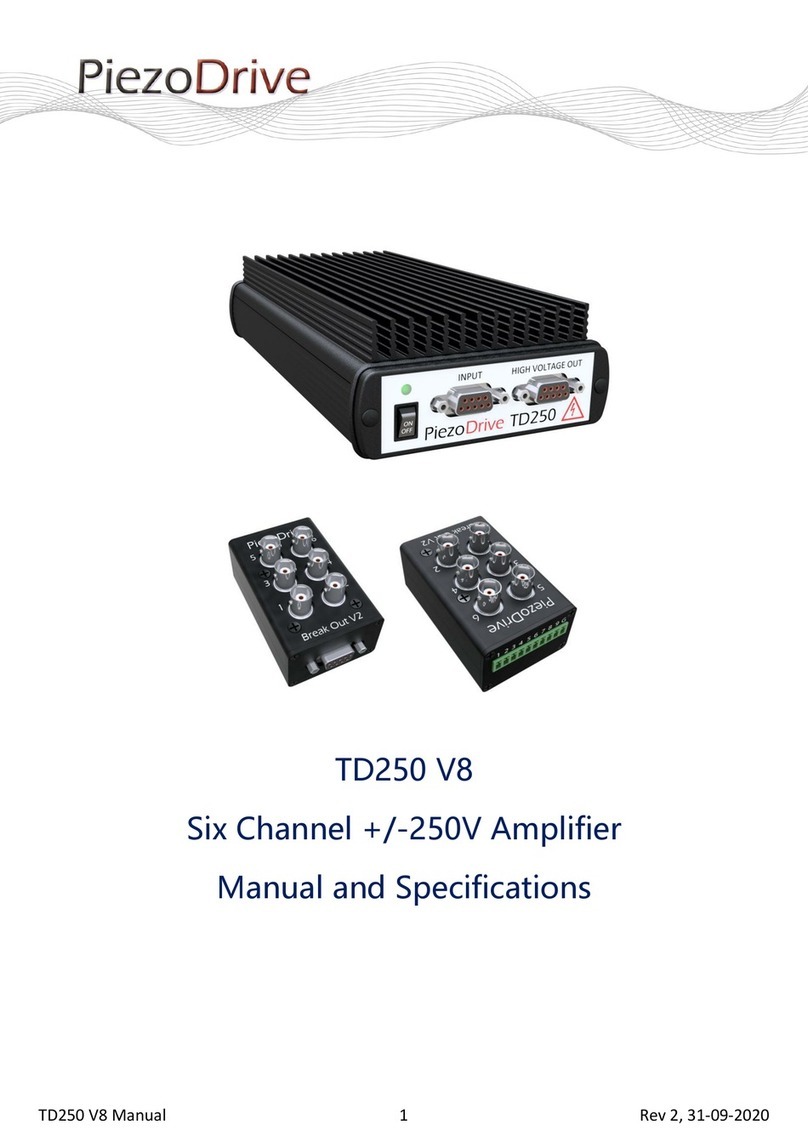
PiezoDrive
PiezoDrive TD250 V8 User manual
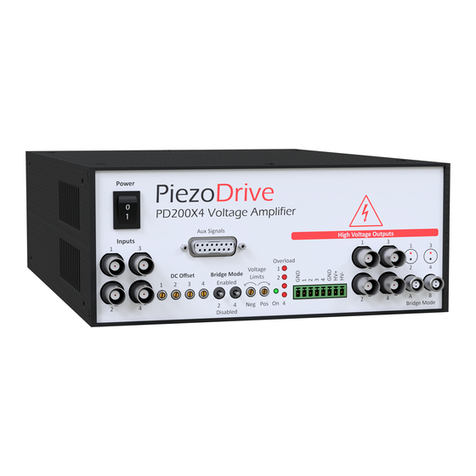
PiezoDrive
PiezoDrive PD200X4-V0,200 User manual