GF MSA 2 MULTI User manual

Instruction manual
Bedienungsanleitung
GF Piping Systems
MSA 2 MULTI Electrofusion Unit
MSA 2 MULTI
Elektroschweissgerät


Operating Instructions MSA 2 MULTI General Information
1
Index Page
IGeneral Information 3
Warning notice 3
1Introduction 4
1.1Product description 4
1.2Components description 5
1.2.1Operation Controls 5
1.2.2Display 6
1.2.3Ambient Temperature Sensor 6
1.2.4USB Interface 6
1.2.5Power Cable 6
1.2.6Welding Cable 7
1.3Barcode Reader Scanner 7
1.4Extension Cables for Power Supply 7
1.5START/STOP Card 8
2Fusion process 9
2.1Switching On 9
2.2Material selection 9
2.3Overview of operating procedure 11
2.4Connect fitting 12
2.5Enter operator code/job number 12
2.6Enter fusion data 13
2.7Preparation 15
2.8Fusion process 16
2.8.1Welding phase 16
2.8.2Cooling time 17
3Configuration settings 18
4Data Management 19
4.1Protocol view 20
4.2Protocol export 21
5Error messages 22
6Technical characteristics 23
6.1Standards 23
7Maintenance 24
7.1Cleaning 24
7.2Fusion Cables 24
7.3Function Check-up 24
7.4Spare parts 24
8Accident Prevention 25
8.1Operating the Unit 25
8.2Check before Operation 25
8.3Protection of the Unit 25
8.4Defect Unit 26
8.5Opening the Unit 26

General Information Operating Instructions MSA 2 MULTI
2
8.6Working with safety in mind 26
8.7Other disposal 26

Operating Instructions MSA 2 MULTI General Information
3
I General Information
Dear Customer,
Thank you for choosing this product. The electrofusion unit MSA
2 MULTI is designed according to newest technology. Using it
for purposes other than those described in this manual may
cause injury to the operator or to other people. It may also cause
damage of the machine or other equipments.
To prevent problems, the machine should only be used when in
perfect working conditions; following the safety instructions;
keeping on hand the technical documentation.
Anyway, the manufacturer reserves the right to make technical
changes to MSA 2 MULTI which may result in differences from
the pictures and information contained in this manual.
To point out relevant aspects operating this electrofusion unit,
symbols are frequently used. The following table contains their
explanation.
Warning notice
Warning notices are used to inform about possible injuries or
damage to properties. Please read carefully and always consider
these warnings!
Symbol Meaning
Danger
Imminent danger! Failure to comply could result in
death or extremely serious injuries.
Warning
Possible danger!
Failure to comply could result in serious injuries.
Caution
Dangerous situation!
Failure to comply could lead to injury or damage to
property.

Introduction Operating Instructions MSA 2 MULTI
4
1 Introduction
1.1 Product description
The MSA 2 MULTI is an electrofusion control unit for the
electrofusion jointing of PE, PP-R, PB and PP pipes.
Fusion parameters input can be accomplished with a fusion
barcode according to ISO/TR 13950 standard or manually.
The internal processor controls the values of welding
parameters, set the power output accordingly and, thanks to the
messages shown in the graphical display, guides the operator
to successfully execute all the necessary operations.
In addition, the MSA 2 MULTI is tracking and storing in the
internal memory up to 500 welding protocols, that can be
browsed by the user even days or months after the welding
execution.
To ensure high quality fusion cycles, depending on the ambient
temperature, the machine is adjusting automatically the welding
time, for the correct distribution of the energy to the fitting.

Operating Instructions MSA 2 MULTI Introduction
5
1.2 Components description
1.2.1 Operation Controls
There are seven buttons the user can press to operate the
machine. START (green button) and STOP (red button) are the
most important, used to get a confirmation or a stop for all the
actions. The remaining (blue) are auxiliary buttons used for
menu navigation and data entry.
Button Description
() Moves the cursor to previous field,
increases set values, scrolls characters
() Moves the cursor to next field, decrement
set values, scrolls characters in reverse
order
() Moves the cursor to the left
() Moves the cursor to the right
MENU Enters into additional menus
STOP/ESC
(O) Stops any operation and the process; goes
back to previous step
START/OK
(I) Confirms inserted data and starts welding

Introduction Operating Instructions MSA 2 MULTI
6
1.2.2 Display
The graphical display is the main user interface of the welding
machine. It shows the steps to be executed in sequence, the
fusion data, possible errors and alarm messages.
It is possible to change its brightness using the andbuttons
and then save permanently the new value pressing the
button, in case of limited visibility due to weather conditions. The
operation can be done only when the display shows the fitting
icon
1.2.3 Ambient Temperature Sensor
The outside sensor measures the ambient temperature, to check
the temperature is in the permitted range (between -20° C and
50° C) and adjust the fusion time according to the external
conditions.
1.2.4 USB Interface
The USB type-A interface available on the rear of the machine is
the interface used to upgrade the software version, perform the
calibration of the unit and export the protocols. The connector is
protected against dust and water by a cap, which ensures an
IP67 protection factor when properly fixed.
1.2.5 Power Cable
The power cable is delivered with an earthed plug for being
connected to power supply at 230V/50Hz.
The power source can be either the mains or a generator. In the
latter case there are no deterministic rules to select the right
generator output power. Requirements will vary depending on
the efficiency of the generator as well as other factors, like the
power needed by the fitting.

Operating Instructions MSA 2 MULTI Introduction
7
1.2.6 Welding Cable
The fusion cable shall be connected to the fitting pins. As
standard the terminals are supplied with straight female
connectors, Ø4mm.
1.3 Barcode Reader Scanner
The barcode scanner allows a quick reading of welding
parameters by reading the related barcode, pointing the barcode
(at a distance of 10-15 cm) and pressing its button.
The successful reading is confirmed by special acoustic tones
and a display change. In case of drawbacks, to check if the
barcode reader is damaged, you can try to read for test purpose
the code printed below, when the machine shows the barcode
symbol.
If this code is read successfully, the issue is not on the barcode
reader. After usage, remember to place the barcode scanner
into its protective case.
1.4 Extension Cables for Power Supply
To avoid excessive dissipation or brown out, on Extension
cables, use cables with section:
4mm² for cables 10m full-run;
6mm² for cables 30m full-run.

Introduction Operating Instructions MSA 2 MULTI
8
1.5 START/STOP Card
START / STOP card can be used as alternative to the buttons
on the keypad. For instance, you can confirm the commands or
start the welding process by scanning the START bar code on
the card.
The STOP barcode can be used instead to go back to the
previuos step.

Operating Instructions MSA 2 MULTI Fusion process
9
2 Fusion process
2.1 Switching On
Before connecting the machine to the power source, please
read the chapter 6 ‘Technical characteristics‘ and check the
input voltage. If a generator is used, this has to be started
before connecting the electro-fusion unit and must supply a
constant output voltage! Any sudden changes could
compromise the correct welding result and/or damage the
control unit.
Connect the machine to the power mains or generator when the
generator is already started. At power on the display shows the
machine information: model, version and serial number.
2.2 Material selection
The first step is the plastic material selection: the MSA 2 MULTI
can weld PE, PP-R, PP/PVDF or PB INSTAFLEX fittings. As the
fusion parameters change depending on the material, the user
has to set the proper one. This shall be done reading with the
scanner the desired barcode, out of the 4 shown below
This must be done, when the display is showing the “connect
fitting” window:
MSA 2 MULTI
V 2.01
S156A6308001

Fusion process Operating Instructions MSA 2 MULTI
10
As soon as the MSA 2 MULTI has captured the code, it will
change the icon accordingly. For PE:
t = ----s
Vo= --.-V
R = --.--
25°C
12/06/12 15:50
For INSTAFLEX BIG
t = ----s
Vo= --.-V
R = --.--
INSTAFLEX
25°C
12/06/12 15:50
For SEADRAIN t = ----s
Vo= --.-V
R = --.--
SeaDrain
25°C
12/06/12 15:50
For PP-R t = ----s
Vo= --.-V
R = --.--
25°C
12/06/12 15:50
If the machine is switched off, the last setting will be shown at
the next power-on.
PB
PE
PP
PP-R

Operating Instructions MSA 2 MULTI Fusion process
11
2.3 Overview of operating procedure
The welding workflow is shown in the picture below
t = ----s
Vo= --.-V
R = --.--
12/06/12 15:50 25°C
t = ----s
Vo= --.-V
R = 07.45
------
------
12/06/12 15:50 25°c
t = 0040s
Vo= 39.5V
R = 07.45
12/06/12 15:50 25°C
t = 0020s
Vo= 39.7V
E = 003.1kJ
N 150
t = 0040s
Vo= 39.6 V
E = 007.5kJ
N 150
= 10’
N 150
Next paragraphs describe step by step the interactions with the
electrofusion unit.
Prepare the
welding and
connect the fitting
Read the fusion
parameters
Start the fusion
Fusion in progress
Fusion completed
automatically
Cooling time

Fusion process Operating Instructions MSA 2 MULTI
12
2.4 Connect fitting
The first step the operator has to connect the fitting.
As soon as a fitting presence is recognized, the MSA 2 MULTI
moves automatically forward, asking for the fusion parameters in
case of PB/PP-R/PE material.
This is also pointed out by a double short tone of the MSA 2
MULTI and the barcode scanner.
In case of PP, as there may be multiple coils connected in
parallel, the MSA 2 MULTI will show how many are present: to
do that, the user has to connect the coils one after the other, and
the unit will add a bullet, on the screen to report the coil is ok
(connected properly, no short or open circuit) or not.
t = ----s
Vo= --.-V
R = 07.45
------
------
12/06/12 15:50
25°C
2.5 Enter operator code/job number
At the beginning the user can add some work site information,
like the operator code and the job number for the next welding.
The reading of the operator code can be set as mandatory or left
optional.
When the leads are properly connected to the fitting, the control
unit checks the fitting resistance and displays it to the user.
Before the acquisition of the fusion parameters, the user can
read with the scanner the operator badge (ISO 12176-3
compliant) and the job number.

Operating Instructions MSA 2 MULTI Fusion process
13
t = ----s
Vo= --.-V
R = 07.45
------
------
12/06/12 15:50 25°C
The information will be shown above the barcode icon, in place
of the dash (‘-‘) symbols
t = ----s
Vo= --.-V
R = 07.45
JSMITH
A116…
12/06/12 15:50 25°C
In case the operator code is mandatory the first row ‘----‘ will
blink and the MSA 2 MULTI will not move forward, blocking the
acquisition of the fusion parameters.
2.6 Enter fusion data
After that, the user can insert the fusion parameters.
This is done reading the barcode onto the fitting with the
scanner.
If fusion parameters are not acquired, there might be several
reasons:
The barcode reader may be operated in a wrong way: try to
put it closer to the barcode
The barcode may be damaged
The data are not the expected ones (prolonged tone
generated by the machine): the barcode read does not
contain fusion parameters
If the barcode cannot be read with a scanner for any reason, the
data can be entered manually.

Fusion process Operating Instructions MSA 2 MULTI
14
In case of manual mode, the machine works in different ways,
depending on the material selection.
If the material selection is PE or PP-R, then time and voltage
values must be entered, pressing the START/OK ( I ) button to
go in “edit” mode and then using () and () to select the
required digits and () () to change field. Once the values are
entered, must be pushed START/OK ( I )
If the mode is PP, the manual mode is based on a list of
selectable items the user can see pressing the START button.
With () and () he can choose the fitting, confirming with the
START/OK button.
SeaDrainplus
d= 1. 5”x4
12/06/12 15:50
If the mode is PB (INSTAFLEX), then the manual mode is also
based on a list of selectable items the user can see pressing the
START button. With () and () he can choose the fitting type,
confirming with the START/OK button.
INSTAFLEX
d125
12/06/12 15:50
As soon as the data are correctly read from the barcode or
selected manually, the machine confirms with a double acoustic
tone and show on the display a summary of the captured fusion
parameters: time, voltage and expected coil resistance.
t = 0040s
Vo= 39.5V
R = 07.45
12/06/12 15:50 25°C

Operating Instructions MSA 2 MULTI Fusion process
15
When the operator confirms his intent of starting the fusion
process, pressing the START/OK ( I ) button, the unit will start to
weld.
In case of inconsistency between measured versus read
parameters the machine shows a message screen, with the
error message like the following one (fitting resistance too high
in respect to the nominal value).
E-10
12/06/12 15:50 25°C
2.7 Preparation
As soon as the operator confirms with the START/OK button,
before starting the fusion process, the MSA 2 MULTI shows a
reminder to the operator to be sure that pipes have been
scraped, cleaned, aligned following the instructions of the fitting
manufacturers.
12/06/12 15:50 25°C

Fusion process Operating Instructions MSA 2 MULTI
16
2.8 Fusion process
2.8.1 Welding phase
During the fusion process, the display shows the information
concerning the output voltage, the remaining fusion time and the
applied energy.
t = 0020s
Vo= 39.7V
E = 003.1kJ
N 150
The machine adjusts the fusion time according to the external
temperature and barcode information. Therefore the final fusion
time values might be slightly different from the nominal values,
captured from the barcode.
The fusion process can be stopped at any time by the operator
by pushing STOP/ESC (O). Then the fusion process
immediately stops and an error message occurs (see ‘Error
Messages’ chapter).
Stopping the on-going fusion process will result in a suspicious
welding: the responsability will be in charge of the operator.
When the fusion operation is going to finish, a repeated acoustic
signal alerts the user that the process is near to complete. As soon
as the fusion process is correctly concluded, the display shows
briefly the information concerning the real fusion time, the average
voltage and the total energy applied to the jointing. These data will
be part of the welding protocol stored into the internal memory.
t = 0040s
Vo= 39.6 V
E = 007.5kJ
N 150
PE

Operating Instructions MSA 2 MULTI Fusion process
17
2.8.2 Cooling time
After the completion of the process, the fusion summary and the
remaining cooling time, if defined in the barcode, are displayed
alternately. Messages are active till the user will press the
STOP/ESC (O) button, to proceed with the next welding.
= 40’
N 150
Remove the external clamp only when the cooling time is
expired!
The fitting area is hot! Pay attention during the removal of the
cables.
When the cooling time is going to finish or finished, an acoustic
signal alerts the user the process is near to complete.

Configuration settings Operating Instructions MSA 2 MULTI
18
3 Configuration settings
The MSA 2 MULTI does not need any configuration. Only
possible change is the date/time adjustment, to adapt to different
time zones.
To enter into this menu, press twice the MENU button. The
calendar menu allows date and time modification.
They are shown in the format: Day / Month / Year hour:minutes
:
13/06/12
17:46
MENU
START/OK ( I ) must be pressed to go in “edit mode”. Then the
desired values can be selected by ()()while the cursor
position can be changed by ()(). When insertion is
completed, press
START/OK ( I ) to confirm the setting. To cancel instead the
operation press STOP/ESC (O).
Since the MSA 2.0/2.1 has to be calibrated regulary, the user
can check in advance the expiring revision date. Just pressing
three times the MENU button the user can access such
information (mm/yy).
08/12
MENU
Table of contents
Languages:
Other GF Measuring Instrument manuals
Popular Measuring Instrument manuals by other brands
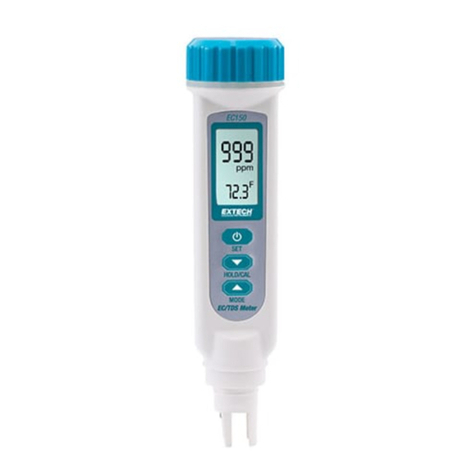
Extech Instruments
Extech Instruments EC150 user guide
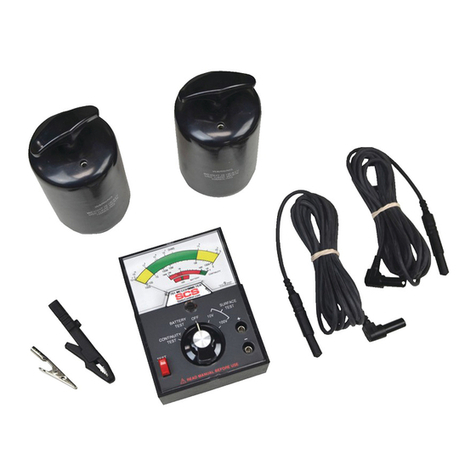
SCS
SCS 701 Operation and maintenance
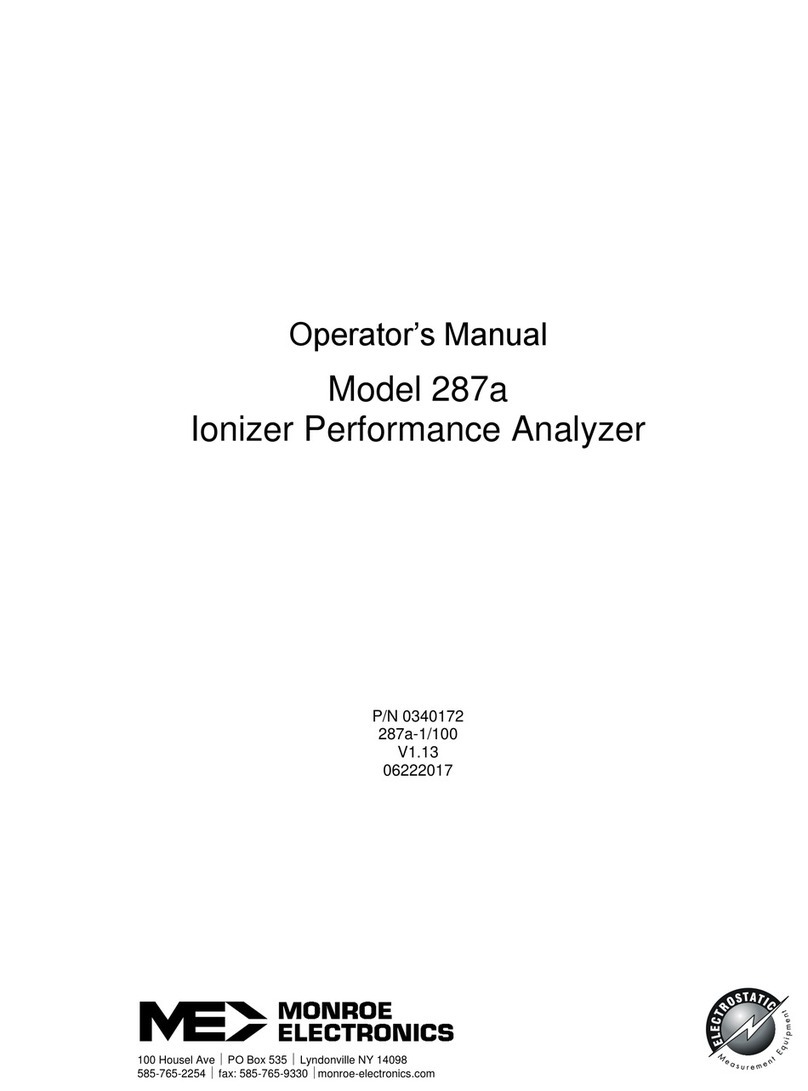
Monroe Electronics
Monroe Electronics 287a Operator's manual
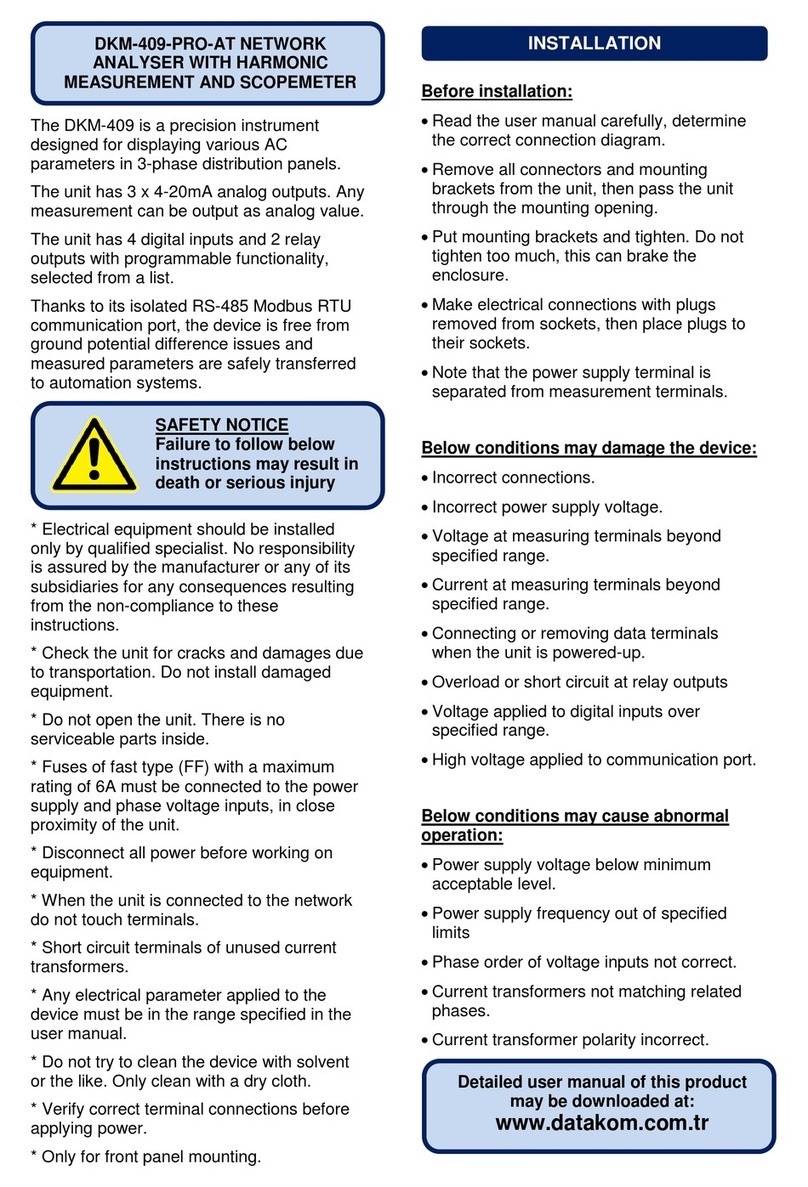
Datakom
Datakom DKM-409-PRO-AT manual
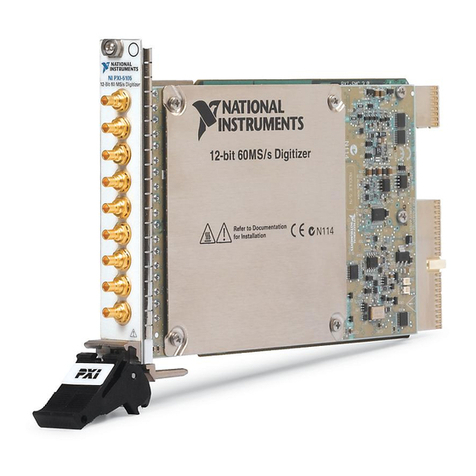
National Instruments
National Instruments NI 5102 Getting started guide

Agilent Technologies
Agilent Technologies B1500A Training manual