H2flow FlowVis DN50 User manual

FlowVis®
FlowVis®
Flow Meter - Metric Models
English
Rev.4.5.1M
Operating Manual
DN40/50/80/100 models
DESCRIPTION
FlowVis® is a revolutionary, patented solution for accurate and
reliable flow rate measurement in fresh water applications
such as swimming pools, spas, fountains, water features,
irrigation systems, well water and solar systems.
Using a design that is based on ‘mass flow’ principles, the
FlowVis® provides many benefits that include:
• Ease of installation without the need to have 15x of
straight pipe
• Installation flexibility that allows orientation in any
position, e.g., horizontal, vertical or even upside-down
• Long life without sticking floats or paddle wheels
• Combined Flow Meter and Check Valve for DN40 and
DN50/65.
CONCEPT
As flow increases, the flapper moves forward toward its
fully open position. The flapper’s angular position is directly
related to flow rate through the valve body / tee. A calibrated
scale on the valve’s lid provides a highly accurate reading of
the flow rate.
Calibrated Scale
Flow
www.h2flow.net •Tel: (+1) 419-841-7774 • www.drydenaqua.com
IMPORTANT NOTE: For the most up-to-date version of this manual, please visit www.h2flow.net/product-literature
SERVICE REPAIR KIT
A service repair kit is available for all models:
- DN 40 and DN 50/65 (Art.Nr. 90024)
- DN 80 and DN 100 (Art.Nr. 90025)
The repair kit comprises:
• 1 x o-ring
• 1 x spring
• 1 x flapper and indicator arm (only 90024)
• 1 x pivot pin
For all other parts, please contact H2flow at (+1) 419-
841-7774 (International).

www.h2flow.net •Tel: (+1) 419-841-7774 • www.drydenaqua.com
Position & Chlorine Feeders
2
IMPORTANT NOTE: Before installing the FlowVis®, please refer to the section on Page 3
regarding chlorine feeders.
Installation of FlowVis® should be in accordance with the following instructions.
Normal plumbing procedures such as cleaning, priming and gluing of fixtures should be
followed in order to avoid leaks.
Unlike other flow meters, FlowVis® is not aected by flow stream disturbances caused by its
proximity to pumps, elbows, tees, valves, etc. FlowVis® does not require specific straight pipe
lengths before or after its point of installation, and can be installed close to, or even adjacent to,
other plumbing fittings. FlowVis® can be installed either horizontally or vertically.
NOTE: When selecting
a physical location to
install FlowVis®, be sure
to allow accessibility to
read the scale on the lid.
Pay particular attention to the system’s direction of flow and make sure that the arrow on the lid
of the FlowVis® is pointing in the correct direction. For the DN80 and DN100 versions, the Tee
will have an additional arrow on one of its bosses. In the event that the FlowVis® is inadvertently
glued into the plumbing in the wrong direction, simply remove the (8) screws holding the lid in
place and rotate the entire lid assembly by 180˚.
NOTE: Always remove the FlowVis® lid assembly prior to gluing in the valve body.
NOTE: The above graphic only relates to applications that use erosion style chemical feeders. In all other circumstances, the FlowVis® can
be installed in any of the locations shown.
Installation locations
Corrosion Resistant Check Valve
Filter Heater
Chlorinator
1
2
3
4
5
1 = Best
2 = Very Good
3 = OK, but not ideal
4 = Bad
5 = Really bad
INSTALLATION

CHLORINE FEEDERS
IMPORTANT DISCLAIMER
Material selections such as Viton and Hastelloy c-276 ensure that FlowVis® will provide many years of trouble-free
operation in normally treated, sanitized pool water conditions. However, certain brands and designs of inexpensive
chlorine feeders are known to fail and release high concentrations of chlorine or even chlorine gas into the
surrounding filtration system. When this occurs, any equipment that comes into contact with these abnormal levels
of chemicals will experience rapid and catastrophic damage. Inspection of any failed components will quickly and
conclusively confirm the cause of the damage and, under these circumstances, the product’s warranty will be void.
Under no circumstances should FlowVis® be used as a ‘check valve’ to prevent the eects of these Chlorine Feeders
damaging other equipment such as Heaters.
www.h2flow.net •Tel: (+1) 419-841-7774 • www.drydenaqua.com
Installation & Tightening Lid Screws
3
TIGHTENING LID SCREWS
When removing and re-installing the FlowVis® lid assembly, it is important to adhere to the following procedure:
1. Make sure that the o-ring on the underside of the lid is undamaged, lubricated with silicone (such as Boss 820)
and is in-place without twists.
2. Ensure flapper hinge pin is centered.
3. Carefully lower the lid onto its valve body (or Tee in the case of the DN80
and DN100 models), making sure that the o-ring stays in place.
4. Insert by hand the (8) stainless steel screws but do not tighten at this
stage.
5. Using a hand Phillips-head screwdriver, slowly tighten the screws in a
diagonal pattern, per the sequence to the right. Do not fully tighten one
screw before proceeding to the next, i.e., pull them down slowly multiple
times to avoid stressing and cracking the lid. Screws should be tightened
to a final torque of 34 Nm.
1
2
3
5
4
6
7
8

www.h2flow.net •Tel: (+1) 419-841-7774 • www.drydenaqua.com
4
Operation & Maintenance
OPERATION
The FlowVis® is factory-calibrated to be extremely accurate across its full operating range. Any perceived ‘inaccuracy’
is related to the viewing angle at which the scale is being read. To avoid so-called ‘parallax error’, it is important to
position your eye so that you are looking squarely at the tip of the indicator arm. To achieve this, simply move your
head so that you just lose sight of the vertical leading edge of the red arm.
Vertical leading edge
NOTE: Slowly move
your head in this
direction to the
point where the
leading edge of the
indicating arm is
not visible.
(1) (2)
(3)
(1) Indicator arm is
being viewed too far
forward / near the
rear of the lid.
(2) Indicator arm
is being viewed
correctly.
(3) Indicator arm is
being viewed too far
back / front of the lid.
MAINTENANCE
Although FlowVis® is designed to be maintenance-free, periodic checks should be made to the following:
Condition Check for Remedy
Leak around lid seal O-Ring Failure Replace O-Ring
Leak from lid Cracks in lid Order new lid from supplier
Higher flow reading than normal Broken or weak spring Replace spring
Lower flow reading than normal Indicator arm stuck due to debris Remove lid and clear debris
Flow indicator stuck at one position Debris between indicator arm and lid Remove lid and clear debris
Indicator always at max flow when pump
running Broken spring Replace spring
Flapper seal crinkled Chlorinator check valve failure
Repair chlorinator, order FlowVis® Service
Repair Kit. Consider moving FlowVis® to a
dierent location (see ‘Chlorine Feeders’
section on pg. 3).

www.h2flow.net •Tel: (+1) 419-841-7774 • www.drydenaqua.com
5
Head Loss Data
HEAD LOSS DATA
Head Loss (DN40):
0.00
0.02
0.04
0.06
0.08
0.10
0.12
0.14
5 7 9 11 13 15 17 19 21
Head Loss -Bar
Flow Rate m3/h
Head Loss (Bar) -DN40
0.00
0.02
0.04
0.06
0.08
0.10
0.12
0.14
0.16
5 7 9 11 13 15 17 19 21 23 25
Head Loss -Bar
Flow Rate m3/h
Head Loss (Bar) -DN50
Head Loss (DN50):
0.000
0.005
0.010
0.015
0.020
0.025
20 22 24 26 28 30 32 34 36 38 40 42 44 46 48 50
Head Loss -Bar
Flow Rate m3/h
FlowVis Head Loss (Bar) -DN80
Head Loss (DN80):
0.004
0.006
0.008
0.010
0.012
0.014
34 36 38 40 42 44 46 48 50 52 54 56 58 60 62 64 66 68 70
Head Loss -Bar
Flow Rate m3/h
FlowVis Head Loss (Bar) -DN100
Head Loss (DN100):

Warranty & Technical Data
TECHNICAL DATA
Item Material / Comments
Lid Polycarbonate
Valve Body (DN40 and DN50/65) CPVC
Lid Screws 304 Stainless Steel
O-ring Silicone Lubricated Elastomer
Scale label, Product label Polycarbonate
Pivot Pin Hastelloy c-276
Spring Hastelloy c-276. 316 Stainless Steel prior to Nov. 2015
DN80 and DN100 Tee and reducing bushings PVC
Indicator Arm ABS
Flapper DN40 and DN50/65 PPEPS
Flapper Seal DN40 and DN50/65 Viton
Lower Flapper (DN80 and DN100 only) ABS
Interconnecting link (DN80 and DN100 only) 316 Stainless Steel
Lower Retaining Pins (DN80 and DN100 only) 316 Stainless Steel
Materials used:
Function Models Comments
Max working pressure All models 3.5 Bar
Accuracy FV-C-M-DN40 and FV-C-M-DN50/65 Average: 97.9% / 98% / 97.5%
Accuracy FV-M-DN80 and FV-M-DN100 Average: 98.6% in straight pipe
Min / Max operating ambient temp All models 0˚C / 60˚C
Periodic calibration All models None required
Design life All models Greater than 5 years
Operational Data:
WARRANTY
For a copy of the FlowVis warranty, please contact the factory.
This manual suits for next models
4
Table of contents
Other H2flow Measuring Instrument manuals
Popular Measuring Instrument manuals by other brands
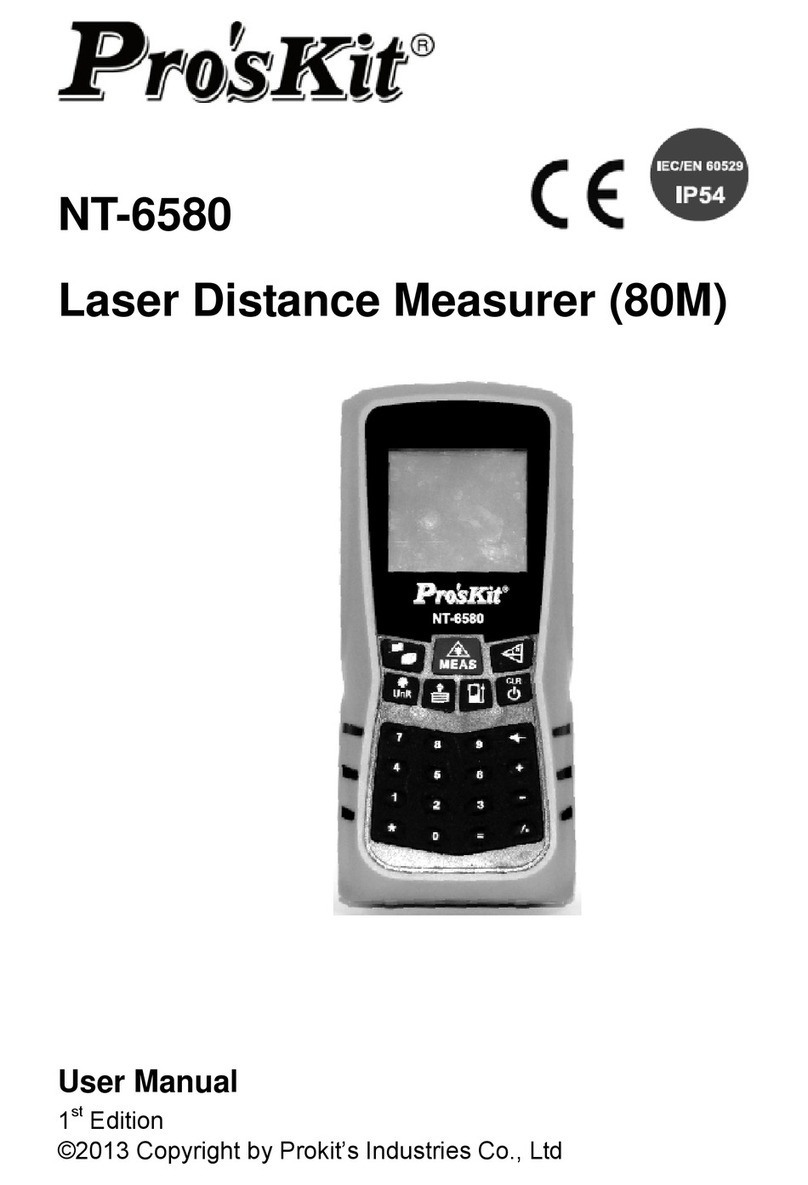
Pro's Kit
Pro's Kit NT-6580 user manual
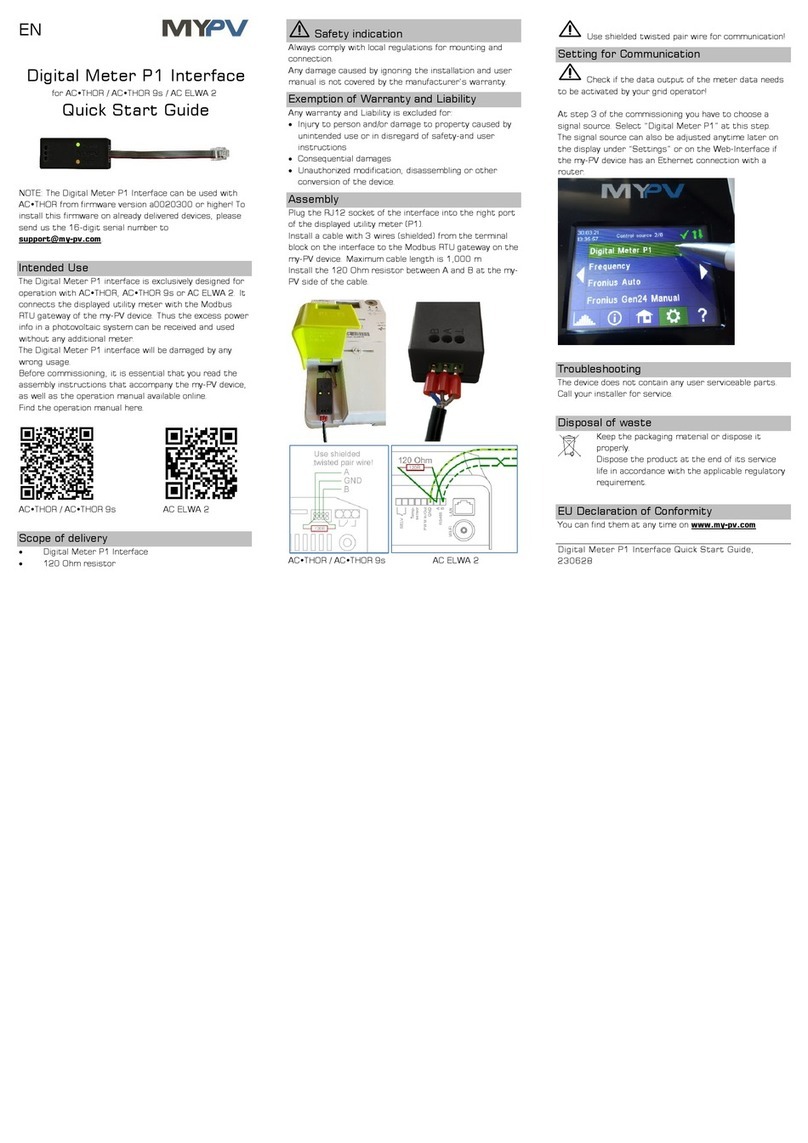
MYPV
MYPV Digital Meter P1 interface quick start guide
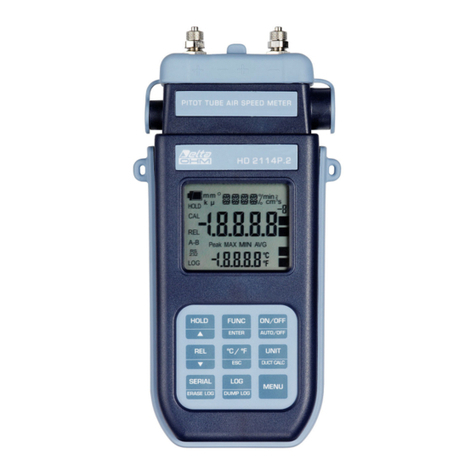
Delta
Delta HD2114P.0 operating manual
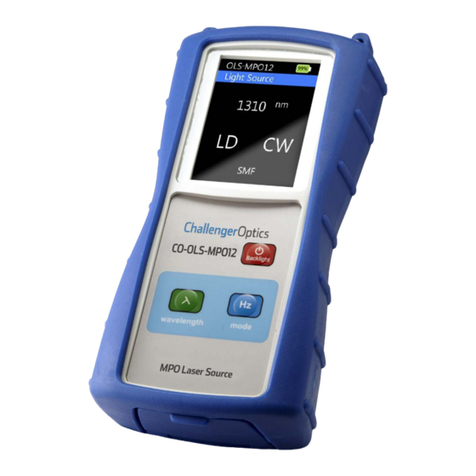
Challenger Optics
Challenger Optics CO-OLS-MPO12 operating manual
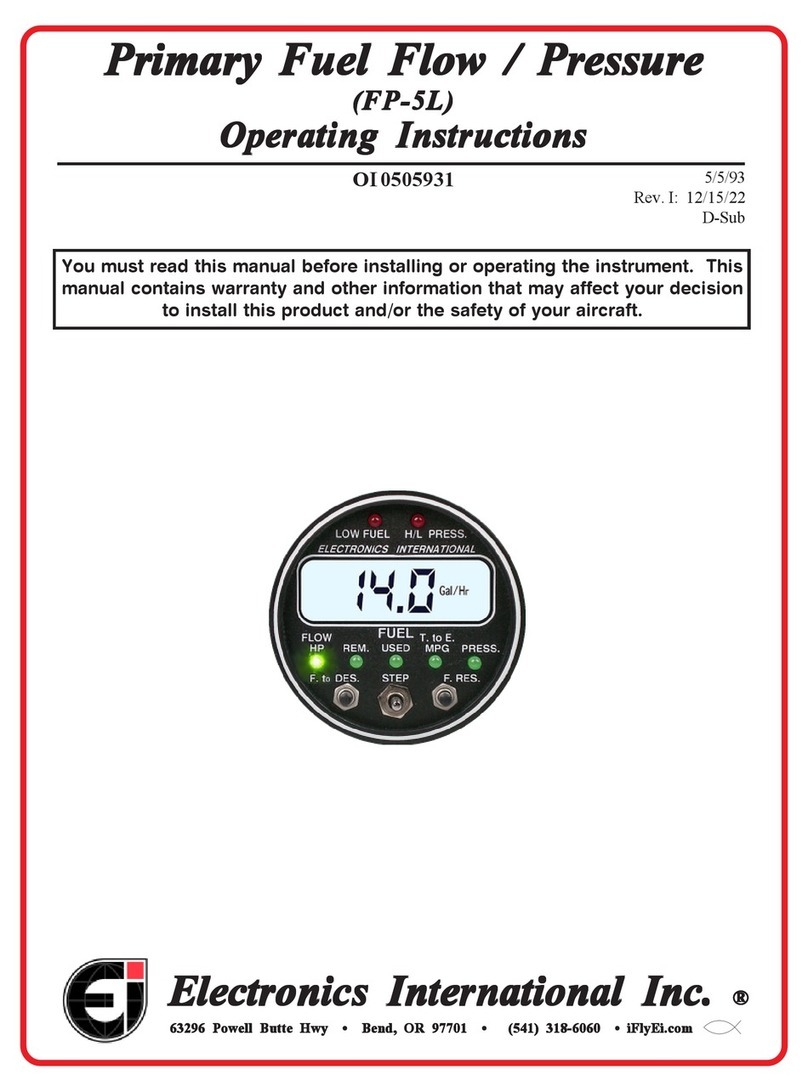
Electronics International Inc
Electronics International Inc FP-5L operating instructions
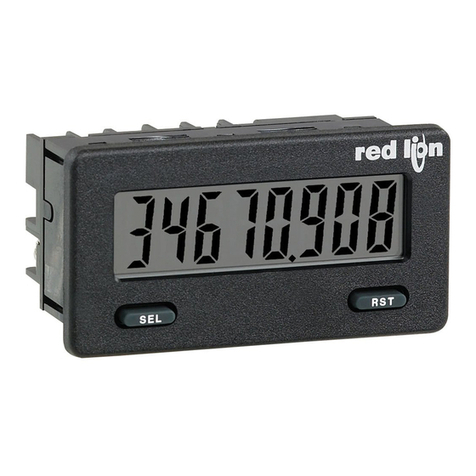
red lion
red lion CUB5R manual
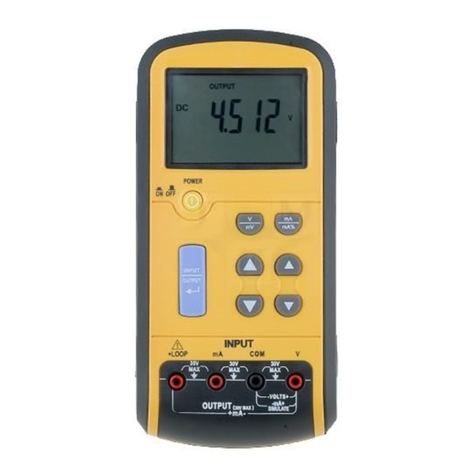
Axio MET
Axio MET AX-C800 Operation manual
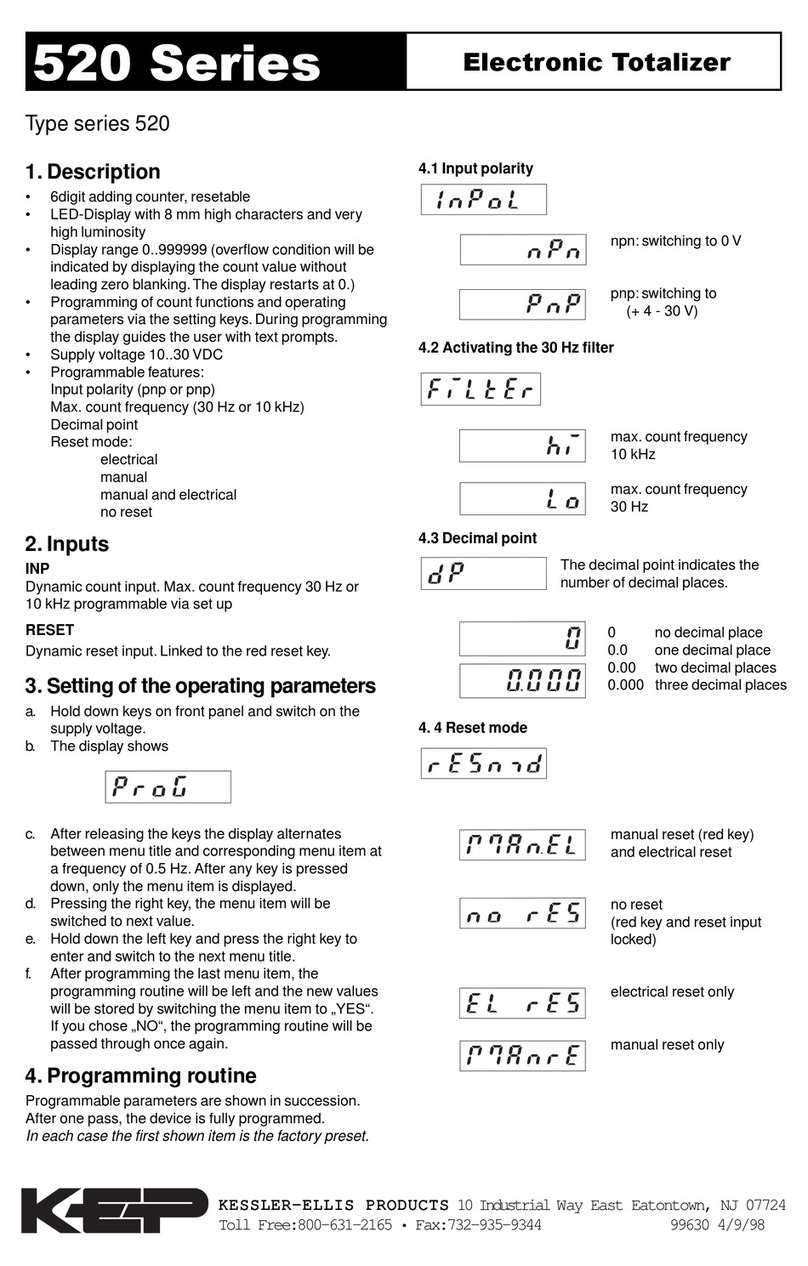
KEPCO
KEPCO 520 Series manual
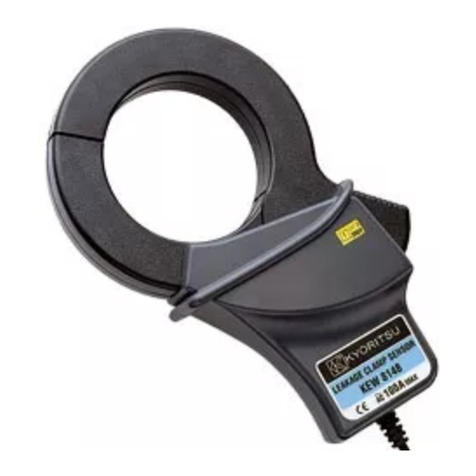
Kyoritsu Electrical Instruments Works, Ltd.
Kyoritsu Electrical Instruments Works, Ltd. KEW8146 instruction manual
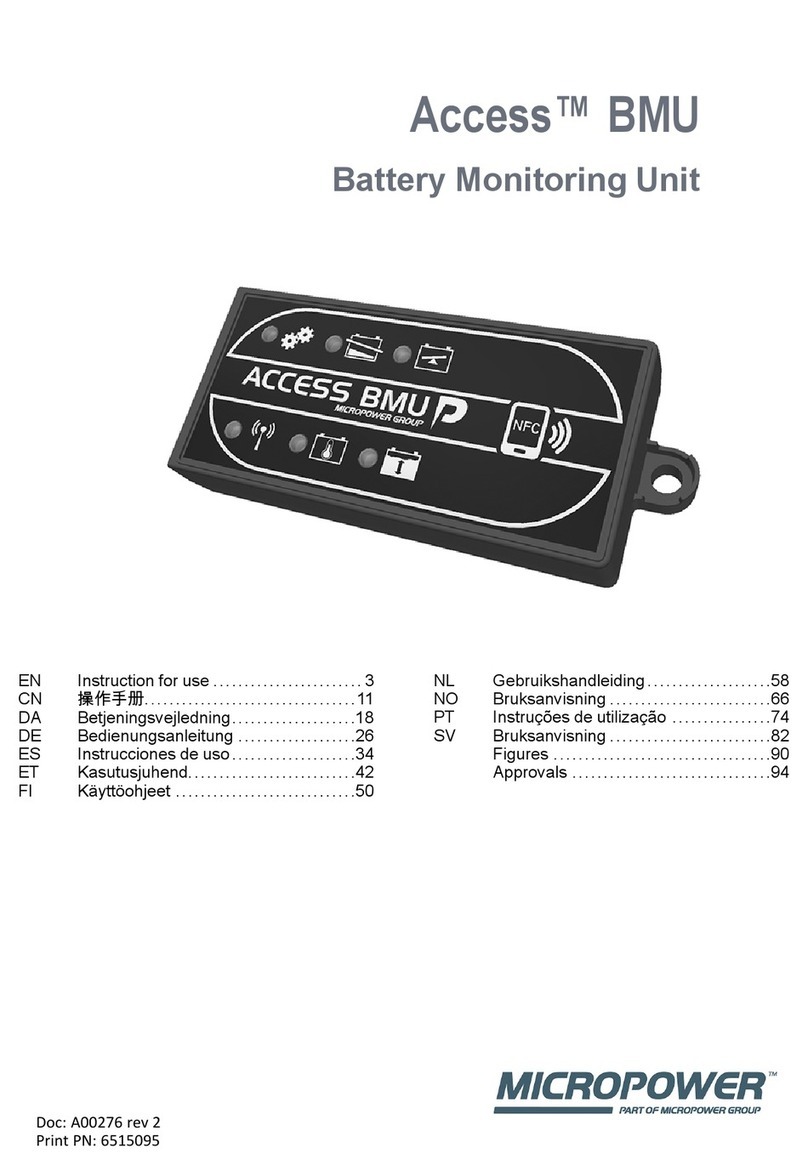
MICRO-POWER
MICRO-POWER Acess BMU Series Instructions for use
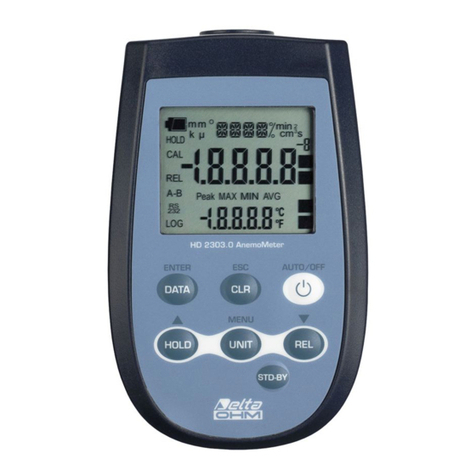
Delta OHM
Delta OHM HD2303.0 manual
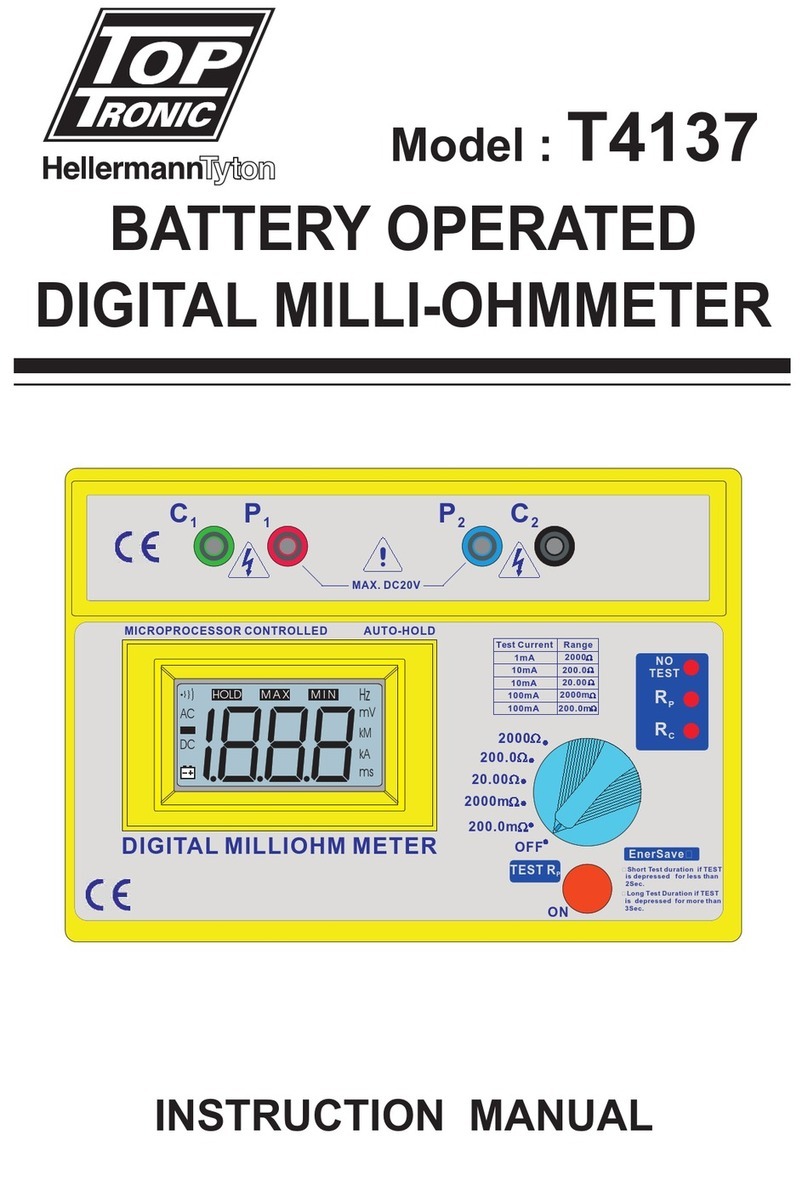
Top Tronic
Top Tronic T4137 instruction manual