Portafill 4000T User manual

ii
4000T
4000T
USER MANUAL

iii
4000T
Introduction
This document has been created to ensure that the Equipment designed and constructed by
Portafill International Limited, is installed, put into use and operated efficiently and safely.
It is recommended that this manual is read carefully so as to educate on how to operate and service
your machine correctly.
Failure to do so could result in personal injury or damage to the equipment.
A copy of this manual must be kept at the Operational Site for easy reference.
REMEMBER - YOUR MACHINE IS ONLY AS SAFE AS THE OPERATOR!
Hazard control and accident prevention are dependent upon the awareness, concern, prudence,
and proper training of the personnel involved in the operation, transport, maintenance, and
storage of the equipment. Ensure that every operator is properly trained and thoroughly familiar
with all of the controls before operating the machine.
A replacement manual is available from your Authorised Dealer or by contacting Portafill
International Limited directly using the contact details shown at the start of this manual. Please
indicate the complete Model and Serial Number of your product when requesting replacement
manuals.
Whilst every effort has been made to ensure the accuracy of the information contained within this
manual, Portafill International Ltd can assume no responsibility for any errors, omissions, or their
consequences.
Please contact Portafill International Ltd regarding any part of this manual that requires further
clarification.
This Manual is structured by different sections as noted in the Contents Page. These are to help you
familiarize yourself with the Portafill 4000T and, most importantly, with the safe set-up, operating
and maintenance procedures.

iv
4000T
Declaration of Conformity
Declaration Number T 140
The undersigned representing the following supplier:
Portafill International Limited,
29 Farriter Road,
Cabragh,
Dungannon,
Co Tyrone
Northern Ireland
BT70 1TL
Hereby declares that the following equipment:
Model Portafill 4000T
Type Mobile, Diesel-Hydraulic Powered Screening Machine
Serial Number: T 140
Complies with the provisions of the following EC Directives.
2006/42/EC
Machine Safety Directive
2004/108/EC
Electromagnetic Compatibility Directive
2005/95/EC
Low Voltage Directive
Based on the following harmonized standards
BSEN 14121-1:2007
And therefore complies with the essential requirements of those directives.
Name and position of person signing for the manufacturer or authorized representative
Signed by:
Name: Malachy Rafferty
Title: Design Manager
Location: Portafill International Ltd
Date: September 2016

v
4000T
This machine is designed and engineered by:
Portafill International Limited,
29 Farriter Road, Cabragh,
Dungannon, Co Tyrone,
N. Ireland, BT70 1TL.
http://www.portafill.com
t: +44 28 8776 9467
f: +44 28 8776 9468
Copyright Notice
Information in this document is subject to change without notice. The names of companies,
products, people, characters and/or data mentioned herein are fictitious and are in no way
intended to represent any real individual, company, product or event unless otherwise noted.
Complying with all applicable copyright laws is the responsibility of the user. No part of this
document may be reproduced or transmitted in any form or by any means, electronic or
mechanical, for any purpose, without the express written permission of Portafill International Ltd.
If, however, your only means of access is electronic, permission to print one copy is hereby granted.
© 2016 Portafill International. All rights reserved.
NOTE- It is highly recommended that this manual is read carefully so as to educate on how to
operate and service your machine correctly. It is advised that any one operating this machine reads
and understands the Manual.

vi
4000T
SECTION 1 - MACHINE SAFETY .....................................................................................................................................10
1.1 SAFETY INTRODUCTION................................................................................................................................................... 10
1.2 OPERATION .................................................................................................................................................................. 10
1.3 MAINTENANCE.............................................................................................................................................................. 10
1.4 SIGNAL SYMBOL ............................................................................................................................................................ 12
1.5 SIGNAL WORDS............................................................................................................................................................. 12
1.6 SAFETY INSTRUCTIONS AND APPLICATIONS.......................................................................................................................... 12
1.7 SYSTEM LOCK-OUT PROCEDURE ....................................................................................................................................... 12
1.8 GENERAL SAFETY CONSIDERATIONS................................................................................................................................... 13
1.9 SAFETY CONSIDERATIONS DURING OPERATION.................................................................................................................... 13
1.10 SAFETY DURING MAINTENANCE OR SERVICE ..................................................................................................................... 14
1.11 SAFETY WHEN WORKING WITH HAZARDOUS CHEMICALS .................................................................................................... 15
1.12 SAFETY WHEN WORKING WITH BATTERIES ....................................................................................................................... 16
1.13 SAFETY DURING WORK ON ELECTRICAL SYSTEM ................................................................................................................ 16
1.14 SAFETY DURING WORK ON HYDRAULIC SYSTEM ................................................................................................................ 17
1.15 SAFETY DURING TRANSPORT.......................................................................................................................................... 17
1.16 SAFETY DURING MACHINE TRACKING .............................................................................................................................. 18
1.17 REMOTE RADIO PRECAUTIONS ....................................................................................................................................... 18
1.18 MACHINE LAYOUT AND LOCATION OF EMERGENCY STOP..................................................................................................... 19
1.19 INTERLOCK SWITCH...................................................................................................................................................... 19
1.20 MACHINE SAFETY LABELS.............................................................................................................................................. 20
1.21 MACHINE SERIAL PLATE................................................................................................................................................ 22
SECTION 2 - MACHINE FAMILIARISATION AND TECHNICAL INFO. ................................................................................23
2.1 MACHINE SPECIFICATION AND IDENTIFICATION.................................................................................................................... 23
2.2 SPECIFICATION .............................................................................................................................................................. 24
2.3 WORKING DIMENSIONS .................................................................................................................................................. 25
2.4 TRANSPORT DIMENSIONS................................................................................................................................................ 26
2.5 SOUND PRESSURE LEVELS................................................................................................................................................ 27
2.5.1 Conclusions........................................................................................................................................................ 27
SECTION 3 - APPLICATION & FUNCTIONS.....................................................................................................................28
3.1 MATERIAL MACHINE IS CAPABLE OF PROCESSING ................................................................................................................ 29
3.2 OPERATING TECHNIQUES ................................................................................................................................................ 29
3.3 EFFICIENT LOADING OF HOPPER/GRID ............................................................................................................................... 29
3.4 FEEDER SPEED............................................................................................................................................................... 29
3.5 DRUM MESH SELECTION................................................................................................................................................. 29
3.6 SCREEN SPEED .............................................................................................................................................................. 29
SECTION 4 - OPERATION & SET UP...............................................................................................................................30
4.1 ENGINE START UP PROCEDURE......................................................................................................................................... 31
4.2 MACHINE LAYOUT -FRONT /BACK /SIDES ........................................................................................................................ 32
4.3 REMOVING THE MACHINE FROM TRAILER........................................................................................................................... 33
4.4 UNLOADING 4000T ON LOW LOADER TRAILER ................................................................................................................... 34
4.5 LOADING 4000T ON LOW LOADER TRAILER ....................................................................................................................... 34
4.6 USING THE RADIO REMOTE CONTROL................................................................................................................................ 35
4.7 OPERATING INSTRUCTIONS .............................................................................................................................................. 35
4.8 PREPARING MACHINE FOR OPERATION .............................................................................................................................. 36
4.9 SET UP –CONTROL LEVERS FUNCTION .............................................................................................................................. 36
4.10 SET UP –MACHINE WORKING POSITION ......................................................................................................................... 37
4.11 SET UP –CONVEYORS TO WORKING POSITION .................................................................................................................. 38
4.12 OPERATING THE SCREEN ............................................................................................................................................... 42
4.13 LOAD SENSING ON 4000 MODELS.................................................................................................................................. 44
4.14 MOVING THE 4000T ABOUT SITE................................................................................................................................... 45
4.15 SET UP –MACHINE TRANSPORT POSITION ....................................................................................................................... 46

vii
4000T
SECTION 5 - MAINTENANCE.........................................................................................................................................51
5.1 OIL TYPES .................................................................................................................................................................... 52
5.2 MAINTENANCE SCHEDULES.............................................................................................................................................. 52
5.2.1 Maintenance Schedule –Daily 10 Hours........................................................................................................... 52
5.2.2 Maintenance Schedule –Weekly 50 Hours ....................................................................................................... 53
5.2.3 Maintenance Schedule –100 Hours.................................................................................................................. 53
5.2.4 Maintenance Schedule –250 Hours.................................................................................................................. 54
5.2.5 Maintenance Schedule –500 Hours.................................................................................................................. 54
5.2.6 Maintenance Schedule –1000 Hours................................................................................................................ 54
5.2.7 Maintenance Schedule –2000 Hours................................................................................................................ 55
5.3 ENGINE MAINTENANCE................................................................................................................................................... 55
5.4 HYDRAULIC RAM MAINTENANCE ...................................................................................................................................... 55
5.5 HYDRAULIC SYSTEM MAINTENANCE .................................................................................................................................. 56
5.6 HYDRAULIC TANK MAINTENANCE ..................................................................................................................................... 57
5.7 CHECKING AND ADDING HYDRAULIC OIL ............................................................................................................................ 58
5.8 CHANGING HYDRAULIC OIL.............................................................................................................................................. 58
5.9 CHANGING THE RETURN LINE FILTER ................................................................................................................................. 59
5.10 AIR CLEANER MAINTENANCE ......................................................................................................................................... 59
5.11 FUEL SYSTEM.............................................................................................................................................................. 60
5.12 BATTERY ROUTINE CHECKS............................................................................................................................................ 61
5.13 MAIN CONTROL PANEL WARNING LIGHTS........................................................................................................................ 61
5.14 AIR BREATHER RESTRICTION OPTIONS ............................................................................................................................. 62
5.15 TRACK MAINTENANCE .................................................................................................................................................. 62
5.16 TRACKS –GEAR BOX OIL............................................................................................................................................... 64
5.17 TRACKS –FAULT FINDING ............................................................................................................................................. 64
5.18 BEARING GREASING POINTS .......................................................................................................................................... 64
5.19 CONVEYOR BELT MAINTENANCE /ADJUSTMENT ............................................................................................................... 66
5.19.1 Belt Tensioning / Alignment ............................................................................................................................ 66
5.19.2 Wing Conveyor ................................................................................................................................................ 66
5.19.3 Oversize Conveyor ........................................................................................................................................... 67
5.19.4 Feeder Conveyor.............................................................................................................................................. 68
5.19.5 Transfer Conveyor ........................................................................................................................................... 68
5.19.6 Checking for Belt Damage............................................................................................................................... 69
5.20 SCREEN MAINTENANCE /MESH REPLACEMENT................................................................................................................. 69
5.21 MESH REMOVAL /REPLACEMENT................................................................................................................................... 70
5.22 DRUM DRIVE GEAR ALIGNMENT INSTRUCTIONS ................................................................................................................ 70
5.22.1 Drum Guide Wheel Adjustment ...................................................................................................................... 73
5.22.2 Daily Maintenance/ Check before Start Up..................................................................................................... 75
SECTION 6 –ELECTRICAL AND HYDRAULIC SCHEMATICS..............................................................................................76


9
4000T

10
4000T
1
Section 1 - Machine Safety
1.1 Safety Introduction
Portafill International advises extreme caution
while operating, maintaining and servicing all
components of this machine.
Failure to use adequate safety precautions to
prevent injury or death while performing
operations, maintenance or servicing is the
sole responsibility of the user.
WARNING: Always ensure that all personnel
are clear of the machine when moving,
tracking, maintaining, adjusting or carrying
out setting changes.
Only trained and competent personnel should
operate / maintain / service mobile track
equipment. If operating procedures are
unclear, contact your local distributor for
assistance prior to operating.
Refer to Safety section in the machine’s
operation manual.
1.2 Operation
Factory installed guarding must be in place
before operation. Maintenance and service
may require factory installed guarding to be
removed.
DO NOT OPERATE MACHINERY UNTIL ALL
GUARDING IS REPLACED AND SECURED.
Always read and understand the Operator’s
Manual before Operation / Service /
Maintenance of the machine.
For your protection be aware of all safety
decals positioned around the mobile screen.
These safety decals are positioned in
imminent hazard areas for your safety.
Keep personnel away from all conveyors. DO
NOT STAND OR WALK UNDER ANY
CONVEYORS and beware of loading and
discharge areas. These are extremely
hazardous areas due to falling objects and
moving equipment.
1.3 Maintenance
While maintenance and service functions are
being performed, the Portafill 4000T must be
shut down and secured so that no
unauthorized start-up and operation can
occur. Portafill International advises that the
ignition key be removed prior to any
maintenance or service practices.
Stop all process operations before attempting
adjustments. Remove process material before
adjustment procedures.
This manual is an important part of your
machine and should remain with the machine
when you sell it.

4000T
11
Reading your operator's manual will help you
and others avoid personal injury or damage to
the machine. Information given in this manual
will provide the operator with the safest and
most effective use of the machine. Knowing
how to operate this machine safely and
correctly will allow you to train others who
may operate this machine.
This manual and safety signs on your machine
may also be available in other languages (see
your authorised dealer to order).
Sections in your operator's manual are placed
in a specific order to help you understand all
the safety messages and learn the controls so
you can operate this machine safely. You can
also use this manual to answer any specific
operating or servicing questions.
RIGHT-HAND and LEFT-HAND sides are
determined by the direction of the material
flow through the machine.
READ THIS OPERATOR’S MANUAL BEFORE ATTEMPTING TO START YOUR MACHINE

12
4000T
1.4 Signal Symbol
This symbol means “Attention! Become
Alert! Your Safety is Involved” The symbol is
used with the following signal words to
attract your attention to safety messages
found on the decals on the machine and
throughout this manual. The message that
follows the symbol contains important
information about safety. To avoid injury and
possible death, carefully read the message. Be
sure to fully understand the causes of
possible injury or death.
1.5 Signal Words
The signal word is a distinctive word found on
the safety decals on the machine and
throughout this manual that alerts the viewer
to the existence and relative degree of the
hazard.
The signal word “DANGER” denotes that an
extremely hazardous situation exists on or
near the machine that will result in death or
irreparable injury if proper precautions are
not taken.
The signal word “WARNING” denotes a
hazard exists on or near the machine that
could result in injury or death if proper
precautions are not taken.
The signal word “CAUTION” is a reminder of
safety practices on or near the machine that
may result in personal injury if proper
precautions are not taken.
1.6 Safety Instructions and
Applications
The machine has been specifically designed to
separate aggregate materials including sand
and gravel, soil, quarry aggregate etc. It
should not be used for any other purpose
other than the intended use for which it was
designed. Unauthorised modification of the
machine or its attachments, or use of the
machine in any other applications, will void all
warranties provided by the manufacturer. The
manufacturer assumes no responsibility for
damage to the machine or for personal
injuries, resulting from the use of the machine
in unauthorized applications. Risks associated
with misuse of the machine rest exclusively
with the end user.
1.7 System Lock-Out Procedure
Where called for in this manual it may be
necessary to carry out a system shut out.
Under such circumstances, to properly
immobilise your machine, you must:
Position all hydraulic controls in the neutral
position
Ensure that all supports are securely fixed in
position
That the machine is switched off and the
ignition key is removed
That the power unit door is locked with a key
that should remain with the person during the
machine shut-out

4000T
13
1.8 General Safety Considerations
Your safety and the safety of others depend
significantly upon your knowledge and
understanding of all the correct operating
practices and procedures of this machine.
Individuals working near or around the
machine should be aware of the potential
risks including:
Falling or thrown debris from the machine,
particularly around the reject grid area and
the conveyor areas of the machine.
Injuries that could happen resulting from
loading or unloading the machine, transport
of the machine, machine set-up and machine
repair and maintenance operations.
Contact with hazardous substances such as
hydraulic fluid, diesel and oil.
This list is not exhaustive and anyone working
around the machine should be aware of the
possibility of dangerous circumstances and
the risk of injury arising from such conditions.
NEVER allow anyone to operate this machine
without proper instructions.
NEVER wear loose fitting clothing that could
get tangled in moving parts. For safety, long
hair should be tied back and no jewellery (e.g.
finger rings) should be worn.
ALWAYS wear protective clothing including a
hard hat, safety glasses, steel-toed boots,
high visibility jacket, hearing protection and
gloves. Loose or baggy clothing can get caught
in running machinery.
NEVER climb upon the machine while the
machine is in operation or moving.
NEVER make any modifications to the
machine that may compromise safety.
ALWAYS ensure that all the decals / stickers
on the machine are kept clean and can be
easily read. If decals become damaged then
replace them immediately. Replacements
Sticker Kits can be ordered directly from
Portafill International on request. It is
recommended that you specify Machine
Model & Serial Number.
1.9 Safety Considerations During
Operation
ALWAYS take care when working around
heavy equipment. Be vigilant of the risks
associated with working with heavy
equipment. Keep well clear of Screen and
Conveyors during operation.
ALWAYS keep clear of falling rock and debris.
NEVER operate the machine without all the
factory fitted guards and safety devices in
place. If a guard becomes defective or
damaged, repair or replace it before
operating the machine. If necessary, prevent
the machine from being used by
implementing a machine ‘lock-out’. To see
details on how to implement a system lock-
out please Refer to Section 1.7.
ALWAYS ensure that all emergency stops on
the machine are in working order prior to
machine operation. If necessary prevent the
machine from being used by implementing a
machine ‘lock-out’. To see details on how to
implement a system ‘lock-out’please refer to
Section 1.7.
ALWAYS switch off the machine and perform
a system lock-out before removing any
guards.
NEVER reach into an unguarded part of the
machine. Serious injury or death could result.

14
4000T
ALWAYS keep the machine in good operating
condition. Inspect the machine each day for
damage or defective components before
operation. If necessary prevent the machine
from being used by implementing a machine
‘lock-out’.
ALWAYS wear protective clothing including a
hard hat, safety glasses, steel toed boots, high
visibility jacket and gloves. Operating
equipment safely requires the full attention of
the operator. Do not wear radio or music
headphones while operating machine.
ALWAYS wear a suitable hearing protective
device such as earmuffs or earplugs to protect
against objectionable or uncomfortable loud
noises. Prolonged exposure to loud noise can
cause impairment or loss of hearing.
1.10 Safety During Maintenance or
Service
This machine has been manufactured to
exacting standards and constructed in
compliance with all applicable safety
regulations and specifications. Used and
maintained properly, this machine will
provide many years of service with minimal
operational interruptions. Care must be
exercised not to abuse the machine or affect
its performance in any way. Failure to
properly maintain and use the machine may
result in property damage, including machine
itself, and may result in serious personal
injuries or death.
ALWAYS maintain the machine in accordance
with the schedules described later in the
manual. When required perform maintenance
as needed.
NEVER attempt any service, maintenance or
general work on the machine whilst the unit is
operational. Shut down the machine
completely and perform the necessary lock
out safety procedure before attempting any
work on the machine. To see details on how
to implement a system lock out, please go to
Section 1.7.
NEVER make any modifications to any of the
safety features on the machine that may
adversely affect the safe operation of the
machine. Serious injury or death could result
if machine safety features have been
modified.
NEVER attempt any work on the machine if
you are not a fully trained and authorised
person. Do not carry out any work on the
hydraulic or electrical systems of the machine
unless you are fully trained, authorised and
have the required knowledge of the machine.

4000T
15
ALWAYS ensure that all maintenance and
service work is carried out on the machine
whilst the machine is on firm level ground.
Always ensure that the machine is secured
against sudden or unexpected movement or
shifting.
NEVER work under an unsecured or
unsupported machine.
ALWAYS use proper tools and lifting
equipment when working on the machine. If
removing sections of the machine using lifting
apparatus ensure that you use suitably rated
lifting gear. Lifting operations should only be
carried out by suitably trained individuals.
NEVER climb on the machine. Use proper
access ladders and platforms to access
difficult to reach parts of the machine. Falling
from the machine could result in serious
injury or death.
ALWAYS ensure that any guards or safety
devices removed prior to performing any
maintenance or service are properly refitted
and tested prior to placing the machine back
into the working environment.
Only qualified and trained personnel who are
aware and educated of the hazards involved
shall be allowed to perform maintenance.
1.11 Safety When Working with
Hazardous Chemicals
ALWAYS handle hazardous chemicals with
care. Direct exposure to hazardous chemicals
can cause serious injury. Potentially
hazardous chemicals used with equipment
include such items as lubricants, coolants,
paints, and adhesives. A Material Safety Data
Sheet (MSDS) provides specific details on
chemical products: physical and health
hazards, safety procedures, and emergency
response techniques. Check the MSDS before
you start any job using a hazardous chemical.
That way you will know exactly what the risks
are and how to do the job safely. Then follow
procedures and recommended equipment.
ALWAYS ensure that you dispose of any
waste generated during any maintenance or
service work properly and in accordance with
local regulations.
ALWAYS handle fuel with care: it is highly
flammable. Do not refuel the machine while
smoking or when near open flame or sparks.
Always stop engine before refueling machine.
Prevent fires by keeping machine clean of
accumulated grease and debris. Always clean
up spilled fuel.
ALWAYS be prepared if a fire starts. Keep a
first aid kit and fire extinguisher handy. Keep
emergency numbers for doctors, ambulance
service, hospital, and fire brigade near your
telephone.

16
4000T
ALWAYS remove paint before welding or
heating. Avoid potentially toxic fumes and
dust. Hazardous fumes can be generated
when paint is heated by welding, soldering, or
using a flame torch. Do all work outside or in
a well-ventilated area. Dispose of paint and
solvent properly. Remove paint before
welding or heating. If you sand or grind paint,
avoid breathing the dust. Wear an approved
respirator. If you use solvent or paint stripper,
remove stripper with soap and water before
welding. Remove solvent or paint stripper
containers and other flammable material
from area. Allow fumes to disperse at least 15
minutes before welding or heating.
1.12 Safety When Working with
Batteries
CAUTION: Battery gas can explode. Keep
sparks and flames away from batteries. Use a
flashlight to check battery electrolyte level.
Never check battery charge by placing a metal
object across the posts. Use a voltmeter or
hydrometer. Always remove grounded (-)
battery clamp first and replace it last.
CAUTION: Sulfuric acid in battery electrolyte
is poisonous. It is strong enough to burn skin,
eat holes in clothing, and cause blindness if
splashed into eyes.
Avoid the hazard by:
Filling batteries in a well-ventilated area.
Wearing eye protection and rubber gloves.
Avoiding breathing fumes when electrolyte is
added.
Avoiding spilling or dripping electrolyte.
Use proper jump-start procedure.
WARNING: Battery posts, terminals, and
related accessories contain lead and lead
compounds. Wash hands after handling.
1.13 Safety During Work on Electrical
System
ALWAYS disconnect battery ground cable (-)
before making adjustments on electrical
systems or welding on machine.
NEVER carry out any electrical work on the
machine unless you are suitably qualified and
trained electrician. All work should be carried
out in accordance with applicable electrical
engineering rules.

4000T
17
1.14 Safety During Work on Hydraulic
System
ALWAYS take care when working with the
hydraulic system and high-pressure fluids.
Escaping fluid under pressure can penetrate
the skin causing serious injury. Avoid the
hazard by relieving pressure before
disconnecting hydraulic or other lines. Tighten
all connections before applying pressure.
NEVER search for leaks using your hands.
Search for leaks with a piece of cardboard.
Protect hands and body from high-pressure
fluids. If an accident occurs, see a doctor
immediately. Any fluid injected into the skin
must be surgically removed within a few
hours or gangrene may result.
ALWAYS avoid heating near pressurized fluid
lines. Flammable spray can be generated by
heating near pressurized fluid lines, resulting
in severe burns to yourself and bystanders.
Do not heat by welding, soldering, or using a
flame torch near pressurised fluid lines or
other flammable materials. Pressurised lines
can be accidentally cut when heat goes
beyond the immediate flame area.
1.15 Safety During Transport
ALWAYS ensure that when transporting the
machine, that the vehicle being used is
specified for hauling the gross weight of the
machine. Failure to use a transportation
vehicle not specified to haul the gross weight
of the machine may result in serious personal
injuries or death.
ALWAYS adhere to applicable local and
national regulations concerning the
transportation of such machinery. Ensure
that all permits, licenses and endorsements
are obtained from applicable authorities
where necessary.
ALWAYS ensure that you have sufficient
clearing when passing under bridges, tunnels
or low hanging overhead cables.
ALWAYS transport the machine with the
conveyors and grid plates folded to the
transport position.
ALWAYS ensure that all machine accessories
are fixed securely in place before transporting
the machine.
NEVER use the machine as a transport device
for carrying other equipment.
NEVER load/unload the machine using the
radio controlled wireless control box
(Optional). Users are recommended to use
the standard hand held control box with
lead/socket supplied as standard. Failure to
use the standard hand held control box with
lead/socket might result in damage to the
machine during loading/unloading or personal
injuries or death.

18
4000T
1.16 Safety During Machine Tracking
Some machines are supplied with a tracked
undercarriage. These machines can be moved
about the site using a remote control. Two
different types of remote controls are
available, a radio remote and a corded
remote. These safety instructions apply to
both varieties.
A warning noise will sound and flashing
beacon will alert others in the vicinity of the
machine that the machine is preparing to
move or are being moved.
NEVER attempt to move the machine if these
warning devices fail to operate properly.
Never disable the warning devices on the
machine.
ALWAYS make sure you have a clear line of
sight in the direction the machine is travelling
prior to and when moving the machine.
ALWAYS make sure that the ground the
machine is travelling over is capable of
carrying the weight if the machine.
NEVER attempt to track a machine across a
slope. Doing so can cause the machine to tip
over, resulting in serious injury or death. The
machine is fitted with hydraulic brakes to
prevent roll back and these activate
automatically whenever the tracks are
disengaged.
NEVER allow an untrained operator to
operate the remote control unit and move
the machine.
NEVER attempt to move boulders or large
objects with the machine.
ALWAYS ensure that the machine has a clear
path free from debris in which to travel.
NEVER push or tow the machine as this can
damage the track gear box.
1.17 Remote Radio Precautions
NEVER attempt to use the Remote Control
Device during Blasting Operations.
ALWAYS ensure that the Remote Control
Functions are turned off prior and during
Blasting.

4000T
19
1.18 Machine Layout and Location of Emergency Stop
Familiarise yourself with E-Stop Location prior to operating machine see drawing.
EMERGENCY STOP LOCATION - Both Sides of
Power pack and both sides of oversize
conveyor. When the Emergency Stop Button
is pressed, the machine will shut off all
working components, i.e. the engine and
conveyors will stop.
The Emergency Stop Buttons can be reset by
twisting clockwise.
Familiarize yourself with E-Stop Location prior
to operating machine, see Location drawing
above.
1.19 Interlock Switch
The 4000T is also fitted with two interlock
switches on the main screen side door and
the feeder. The side door needs to be fully
closed and the switch engaged to ensure that
the machine starts. If the door is not closed
properly then the switch will be open and the
machine will not start. Likewise the
feeder/hopper needs to be fully moved back
to operating position and the switch engaged
to ensure the machine starts. If either of
these switches are not engaged then this
warning light will illuminate on the
engine control panel. If this light does
illuminate make sure that there is no dirt
preventing proper operation of the switches
and make sure that the door and/or feeder
and in the closed or operating position.
Emergency Stop locations
Emergency Stop locations
Warning Beacon

20
4000T
1.20 Machine Safety Labels
These labels are fitted to the machine for
your protection, so as to highlight and identify
hazards, it is advised that you make routine
checks on the condition of the stickers; all
unreadable or missing labels should be
replaced with new ones before operating
machine.
Each Label is part numbered and positioned
as shown below, so if and when required your
local dealer can be contacted in order to
purchase replacement labels/ stickers. Labels
are available in the local language of the
country in which the machine is dispatched.
P.001ENG
P.002ENG
P.003ENG
P.004ENG
Interlock Switches

4000T
21
P.006ENG
P.008ENG
P.009ENG
P.010ENG
P.011ENG
P.014ENG
P.016ENG
P.018ENG
P.027ENG
P.029ENG
P.036ENG
Table of contents
Popular Utility Vehicle manuals by other brands
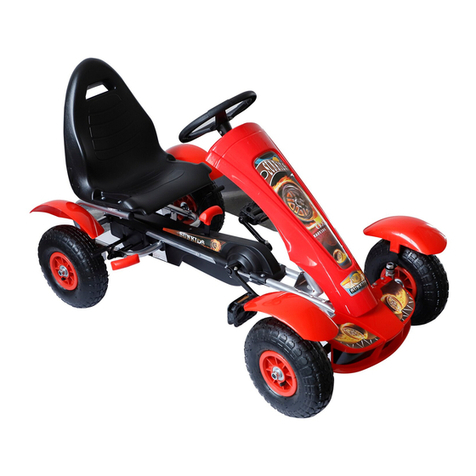
HOMCOM
HOMCOM 341-028 Operating instructions and assembly manual
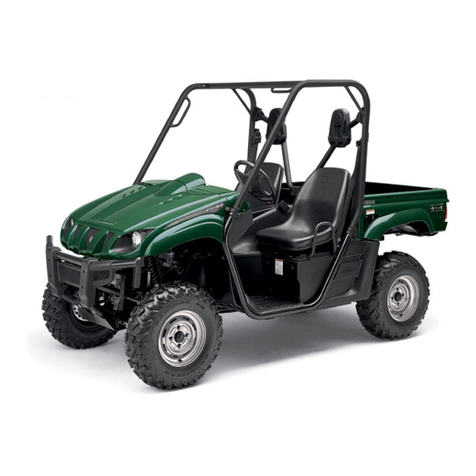
Yamaha
Yamaha Rhino YXR66FW owner's manual

GoKa Sports
GoKa Sports GK800 owner's manual
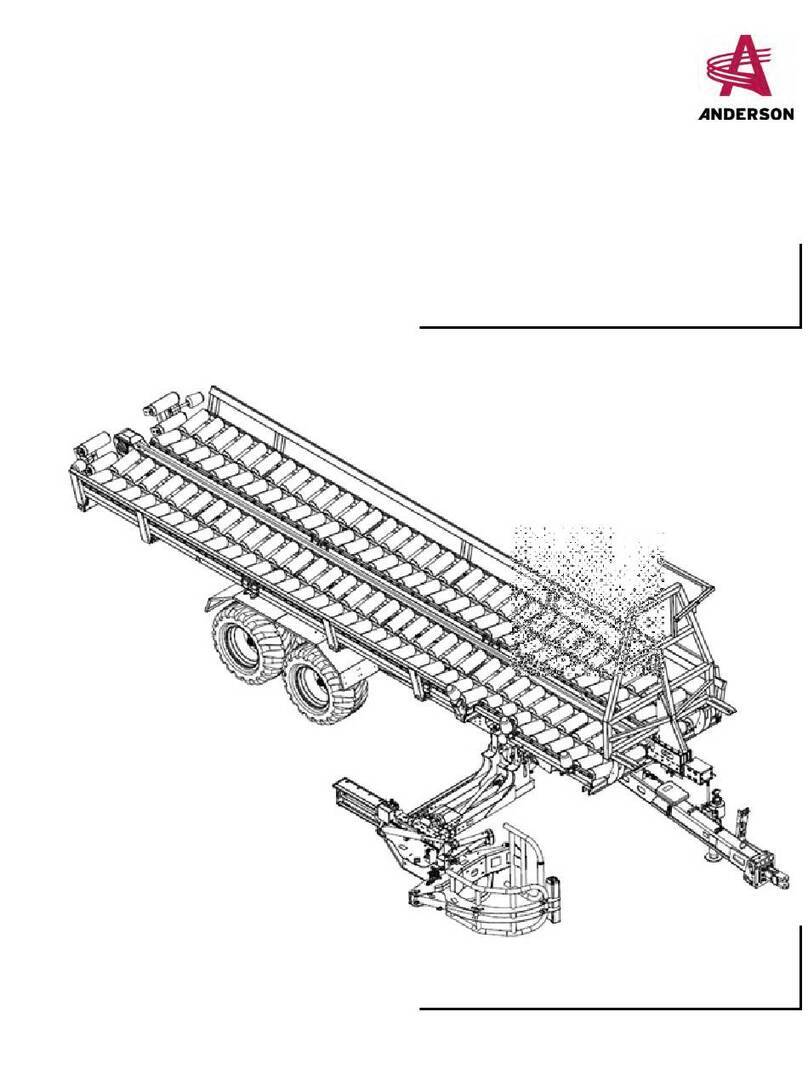
Anderson
Anderson RBMPRO 2000 Operator's manual
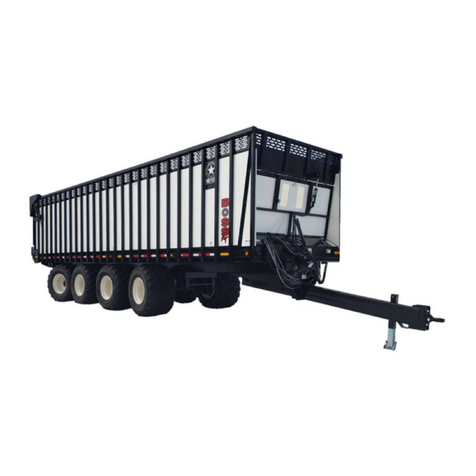
Meyer
Meyer BOSS RT FATBOY 1026RT RR Owner's/operator's manual

Etnyre
Etnyre Black-Topper BT-1 Distributors 2008 Updates & Service Material