ProFire PF2100F User manual

PF2100F MANUAL REV 1.0

DO NOT SERVICE UNLESS AREA IS KNOWN TO BE NON-HAZARDOUS
DO NOT OPEN WHEN ENERGIZED
SUBSTITUTION OF COMPONENTS MAY IMPAIR THE SUITABILITY FOR
USE IN CLASS 1, DIVISION 2
REPLACEMENT FUSES MUST BE CERAMIC
THIS EQUIPMENT IS SUITABLE FOR USE IN CLASS 1, DIVISION 2,
GROUPS ABCD OR NON-HAZARDOUS LOCATIONS ONLY.
WARNING: EXPLOSION HAZARD
DO NOT DISCONNECT WHILE CIRCUIT IS LIVE UNLESS AREA IS KNOWN
TO BE NON-HAZARDOUS OR EQUIVALENT
WARNING: EXPLOSION HAZARD
SUBSTITUTION OF COMPONENTS MAY IMPAIR SUITABILITY FOR
CLASS 1, DIVISION 2.
MUST CONFORM TO THE DIRECTIONS IN THIS MANUAL
THE UNIT MUST BE PROPERLY CONNECTED TO EARTH-GROUND FOR
EFFECTIVE IONIZATION OPERATION
ELECTRICAL DEVICES CONNECTED TO THE CONTROLLER MUST MEET
ELECTRICAL STANDARDS AND BE WITHIN VOLTAGE LIMITS
FOR ANY QUESTIONS PLEASE CALL 1 855 PRO FIRE
WARNING
Class 1, Division 2, Grp
ABCD
IEC Ex nA IIC
IP54
NEMA Type 4x
CSA C22.2 No. 0-M91
CSA C22.2 No. 0.4-04
CSA C22.2 No. 94-91
CSA C22.2 No. 142-M1987
CSA C22.2 No. 213-M1987
CSA E60079-0:2007
CSA E60079-15:2005
UL 508, 17th Edition
ANSI-ISA-12.12.01-2007
UL 60079-0:2005
UL 60079-15:2002
APPROVALS
MC#248705
( 776-3473 )

•Designed for the natural draft-re, tube heater industry
•Meets or exceeds all relevant codes and standards
•Easy installation with clearly marked component I/O
•Easily accessible removable terminal connections
•Rapid 3 second shut-down on ame-out
•DC voltage spark ignition
•Low-power design to accommodate solar panel
or TEG applications
•Auto-relight or manual operation
•Transient protected and fail-safe circuits
GENERAL FEATURES
ENCLOSURE
CIRCUT BOARDS
Polyester
309 x 234 x 134 mm (12.15” x 9.23” x 5.28”)
overall dimensions 2.3 kg (5 lb)
CSA and UL compliant for Class 1, Division 2 locations
Enclosure type 4, 4X, 12, 13
All solid state
CSA compliant for Class 1, Division 2 locations
Certied for use on B.149 compliant valve trains
IGNITION BASE AND COIL
For non-hazardous mounting area only
Ignition coil mounted in the 2100 is optionally available.
POWER REQUIREMENTS
10VDC to 28VDC (voltage must match solenoid rating) 5A MAX
POWER COMSUMPTION 12V 24V
Controller only, display ON 2.6 W 2.8 W
Controller only, display OFF 1.1 W 1.4 W
TEMPERATURE RATING
(6) Digital inputs for safety interlock device connections
(5) Digital outputs
(1) 4-20mA output
(1) Flame-rod input
(3) Thermocouple inputs
See Section 1.3 for thermocouple inputs
Only equivalent fuse should be used to replace a blown fuse.
Factory fuse: LittleFuse 0314005.HXP
(5A, 250V Ceramic, Fast Blow)
FUSE
INPUTS & OUTPUTS
-40°C to +55°C (Tested to -60°C)
-40˚F to +130°F (Tested to -76°F)


1
1Installation
•The control panel can be mounted on the unit skid or on a
building wall providing it does not infringe on a Class 1,
Division 1 area.
•Use control panel mounting tabs to mount in a location that
faces away from the burner housing so the operator is facing
both the enclosure and the burner housing while operating.
Other considerations may include panel access, trafc,
wire-runs and visibility.
•The control panel should be mounted about 1.5m (5’) above
ground level.
•If an external ignition coil is used, it must be mounted in a
Class 1, Division 2 enclosure or a non-hazardous location,
ideally inside the burner housing.
1.1 Mounting Locations
Any design used, should be approved by a qualied inspector
and approved by the gas authority having jurisdiction at the site
where the system is to be installed.
Additional P&ID and wiring diagrams are provided in a separate
application note.
1.2 P&ID and Wiring Diagram

21Installation
E
E
A
GROUND
COIL +
ION +
ION -
COIL -
+
-
-
+
ABCD
D
B C
A
1.3.1 External Coil

3
1Installation
A
A
B
COIL +
ION +
ION -
COIL -
+
-
-
+
ABCD
GROUND
1.3.2 Internal Coil

41Installation
1.4 Terminal Description
CONNECTION DESCRIPTION EXPECTED CONNECTIONS RATINGS
12/24VDC Input power 10VDC - 28VDC, 5A MAX Input power from a DC source 10VDC - 28VDC
Internally fused at 5A
Common Common Ground from DC source Internally connected
to EGND
EGND Earth Ground Earth or Chassis ground Internally connected
to Common
4-20mA Out + 4-20mA output intended to drive a
proportional control valve. This out-
put will be connected to a Current
to Pressure converter which will
drive a proportional control valve.
A software control loop is impli-
mented to tune the ame to match
the demand. Proportional control is
optional.
A resistance of 120Ω to 250Ω is expected.
4-20mA Out - Ground Ground return for the 4-20mA output
HighTemp_TC +
(YELLOW)
Thermocouple input. High Temp
shutdown thermocouple.
“TYPE K” thermocouple must be connected between
the “+” and “-” terminals and must not be electrically
connected to ground.
An uninterrupted connection using “TYPE K” thermocouple
wire is required for an accurate reading.
HighTemp_TC -
(RED)
Thermocouple Input. Negative
terminal of High Temp Shutdown
thermocouple.
Process_TC +
(YELLOW)
Thermocouple input.
Process thermocouple.
“TYPE K” thermocouple must be connected between
the “+” and “-” terminals and must not be electrically
connected to ground.
An uninterrupted connection using “TYPE K” thermocouple
wire is required for an accurate reading.
Process_TC -
(RED)
Thermocouple Input. Negative
terminal of Process thermocouple.

5
1Installation
CONNECTION DESCRIPTION EXPECTED CONNECTIONS RATINGS
AUX_TC +
(YELLOW)
Thermocouple Input Pilot
Thermocouple.
A “TYPE K” thermocouple must be connected between
the “+” and “-” terminals and must not be electrically
connected to ground.
An uninterrupted connection using “TYPE K” thermocouple
wire is required for an accurate reading.
AUX_TC -
(RED)
Thermocouple Input. Negative
terminal of Auxiliary thermocouple.
High Fire/Main + Positive terminal
of the High Fire / Main valve
Solenoid valves must be connected between the “+” and “-”
terminals. The negative terminal is not directly connected to ground
so a common return wire for the High Fire, Low Fire and Pilot
valves cannot be used.
Maximum continu-
ous current is 2A. If
“Low Power” mode is
enabled, a peak load of
4A is permitted.
High Fire/Main - Negative terminal
of the High Fire / Main valve
Low Fire + Positive terminal
of the Low Fire valve
Solenoid valves must be connected between the “+” and “-”
terminals. The negative terminal is not directly connected to ground
so a common return wire for the High Fire, Low Fire and Pilot
valves cannot be used.
Low Fire - Negative terminal
of the Low Fire valve
Pilot + Positive terminal
of the Pilot valve
Solenoid valves must be connected between the “+” and “-”
terminals. The negative terminal is not directly connected to ground
so a common return wire for the High Fire, Low Fire and Pilot
valves cannot be used.
Pilot - Negative terminal
of the Pilot valve
Ion + Flame Detection Input.
Connected to a Flame-rod.
A Kanthal rod should be placed directly in the pilot ame and
connected to this input. The pilot assembly must be grounded for
the ame detection to function properly. Input is protected from
high voltage and can be connected in series with the high voltage
terminals of an external ignition coil, allowing a single ame-rod to
be used for both ignition and ame detection.
A 65VAC signal is ap-
plied to the ame rod.
The source impedance
is very high so there is
no danger of sparking.
Ion - Ground Ground return for ame detection. Must be connected to the
burner housing.
1.4 Terminal Description Continued...

61Installation
CONNECTION DESCRIPTION EXPECTED CONNECTIONS RATINGS
Coil + Driver for the low voltage primary of
the ignition coil.
The primary of the ignition coil should be connected to this termi-
nal. The 12/24VDC input power will be applied for 1 ms and turned
off for 50 ms while sparking.
This output is pro-
tected by a 250mA
thermal fuse.
Coil - Ground Ground return for the ignition coil.
Status + The status “+” and “-” contacts will
be closed when the system is run-
ning and opened when the system
is shutdown.
Dry contact output to indicate system status to an external device.
ie. PLC.
250VAC/DC, 200mA,
15Ω
Status -
Start + Remote start input from an external
device. ie. PLC.
Dry contact switch is expected. The input is internally pulled up to
9VDC via a 3.75kΩ resistance. Jumper “+” and “-” if not used.
Start - Ground Ground return for switch. All switches can use a single
common ground return.
ESD + External Shutdown input. Dry contact switch is expected. The input is internally pulled up to
9VDC via a 3.75kΩ resistance. Jumper “+” and “-” if not used.
ESD - Ground Ground return for switch. All switches can use a single common
ground return.
Proof of
Closure +
Proof of Closure from main valve(s). Dry contact switch is expected. The input is internally pulled up to
9VDC via a 3.75kΩ resistance. Jumper “+” and “-” if not used.
Proof of
Closure -
Ground Ground return for switch. All switches can use a single common
ground return.
High
Pressure +
Input from a mechanical
pressure switch.
Dry contact switch is expected. The input is internally pulled up to
9VDC via a 3.75kΩ resistance. Jumper “+” and “-” if not used.
1.4 Terminal Description Continued...

7
1Installation
CONNECTION DESCRIPTION EXPECTED CONNECTIONS RATINGS
High
Pressure -
Ground Ground return for switch. All switches can use a single common
ground return.
Low
Pressure +
Input from a mechanical
pressure switch.
Dry contact switch is expected. The input is internally pulled up to
9VDC via a 3.75kΩ resistance. Jumper “+” and “-” if not used.
Low Pressure - Ground Ground return for switch. All switches can use a single common
ground return.
Level + Input from a oat-switch
mounted in the bath.
Dry contact switch is expected. The input is internally pulled up to
9VDC via a 3.75kΩ resistance. Jumper “+” and “-” if not used.
Level - Ground Ground return for switch. All switches can use a single common
ground return.
1.4 Terminal Description Continued...

81Installation
Provides high-temp shutdown. 20 AWG or larger “TYPE K”
extension wire must be used. System will shutdown if an
open circuit, short-circuit or short-to-ground is detected.
Should be placed in the same thermowell as PROCESS
THERMOCOUPLE.
Provides a ame detection indication based on the temperature of
the pilot. The system will shutdown if an open circuit is detected.
Primary temperature control device provides high-temp shut-
down. 20 AWG or larger “TYPE K” extension wire must be
used. System will shutdown if an open circuit or short circuit
is detected. Should be placed in the same thermowell as
HIGH TEMPERATURE THERMOCOUPLE.
“TYPE K”
“TYPE K”
“TYPE K”
ALL THERMOCOUPLES MUST BE ISOLATED FROM THE GROUND
1.5 Thermocouples
PROCESS THERMOCOUPLE
HIGH TEMPERATURE THERMOCOUPLE
PILOT THERMOCOUPLE (AUX)
* TE101 and TE102 may be different elements in the same
head of a “TYPE K” thermocouple
* For all thermocouples, avoid locating extension wire near
high-voltage lines. Shield if necessary.

9
2Control & Programming
2.1 Keypad Layout
1
2
3
4
5
6
7
8
1
2
8
7
6
5
4
RUN LIGHT
MENU NAVIGATION
STOP BUTTON
DISPLAY WINDOW
MODE BUTTON
PILOT BUTTON
IGNITE BUTTON
MAIN BUTTON
The system must be in manual mode in order to access the menus.
Press the “MENU” button to step through the menus. When the desired
menu is displayed, press the “OK” button to enter that menu. Once in the
menu, the “MENU” button will step through the parameters.
While viewing the desired parameter use the and buttons to adjust
the setting and “OK” to accept the change. To exit back to the “Ready”
screen, press the “OK” button without making any changes. From the
“Ready” screen, the and buttons will scroll through the current
system status.
2.2 Menu Operation
3

10 2Control & Programming
MENU
MENU
MENU
MENU
MENU
System History
Logging
MENU
MENU
READY
2 - HISTORY
Modbus Enable/Address
6-EXPANSION MODULES
MENU OK
MENU MENU MENU
MENU
CYCLE THROUGH WITH MENU BUTTON, CONFIRMING WITH OK BUTTON
1 - SETPOINTS
NAVIGATION
WILL CYCLE
NAVIGATION
WILL CYCLE
OPERATE USING
SELECTED BUTTONS
READ ONLYREAD ONLY
Pilot Low Setpoint
Pilot High Setpoint
Pilot Low Setpoint
Pilot High Setpoint
MENU
MENU
OK
OK
MENU
OK MENU
OK MENU
OK
MENU
OK
3 - SYSTEM INFO
4-20mA Output Status
Ambient Temp
Input Voltage
Commission Date
MENU
Location
STATUS
HOLD FOR 3
OK
SECONDS TO CLEAR
Control State
OK
Auto Mode
4 - SYSTEM SETUP
Level Event Restart
Pilot Timeout
MENU
MENU
MENU
MENU
MENU
MENU
OK
OK
OK
OK
OK
OK
OK
OK
OK
OK
OK
High Temp ESD Setpoint
5 - CONTROL SETUP
MENU OK
MENU MENU
MENU
OK MENU
OK
OK
OK
Password Enable (menus 1-3)
Spark Mode
High Temp Setpoint
High Temp TC Reading
Flame Fails
ReLights
Display Sleep
Pilot Power Setting
Commission Date Entry
Reset to Factory Defaults
Commission Location Entry
Main Power Setting
System Voltage
Temperature Display Units
MENU
MENU
MENU
MENU
MENU
MENU
MENU
2.3 Menu Map

11
2Control & Programming
MENU
MENU
MENU
MENU
MENU
System History
Logging
MENU
MENU
READY
2 - HISTORY
Modbus Enable/Address
6-EXPANSION MODULES
MENU OK
MENU MENU MENU
MENU
CYCLE THROUGH WITH MENU BUTTON, CONFIRMING WITH OK BUTTON
1 - SETPOINTS
NAVIGATION
WILL CYCLE
NAVIGATION
WILL CYCLE
OPERATE USING
SELECTED BUTTONS
READ ONLYREAD ONLY
Pilot Low Setpoint
Pilot High Setpoint
Pilot Low Setpoint
Pilot High Setpoint
MENU
MENU
OK
OK
MENU
OK MENU
OK MENU
OK
MENU
OK
3 - SYSTEM INFO
4-20mA Output Status
Ambient Temp
Input Voltage
Commission Date
MENU
Location
STATUS
HOLD FOR 3
OK
SECONDS TO CLEAR
Control State
OK
Auto Mode
4 - SYSTEM SETUP
Level Event Restart
Pilot Timeout
MENU
MENU
MENU
MENU
MENU
MENU
OK
OK
OK
OK
OK
OK
OK
OK
OK
OK
OK
High Temp ESD Setpoint
5 - CONTROL SETUP
MENU OK
MENU MENU
MENU
OK MENU
OK
OK
OK
Password Enable (menus 1-3)
Spark Mode
High Temp Setpoint
High Temp TC Reading
Flame Fails
ReLights
Display Sleep
Pilot Power Setting
Commission Date Entry
Reset to Factory Defaults
Commission Location Entry
Main Power Setting
System Voltage
Temperature Display Units
MENU
MENU
MENU
MENU
MENU
MENU
MENU

12 2Control & Programming
2.4.2 (MENU 2) History
No adjustments are available in the History menu; the items are display only.
ON SCREEN DESCRIPTION FUNCTION RANGE DEFAULT SETTING USER SETTING
ReLight = x Displays the number of relights Incremented when an automatic
ignition attempt is made.
0 to 1000 0
FlmFails = x Displays the number of ame
fails
When all retries attempts have failed,
the unit shuts down and increments
the Flame Fail counter
0 to 1000 0
Resets = x Displays the number of resets. This number will increment every time
the board is reset by a power loss or by
pressing the reset button
0 to 1000 0
2.4.1 (MENU 1) Setpoints
Can only be accessed in manual mode. High Temp Setpoint is adjusted in MENU 5 - Control Setup (level 2 password)
ON SCREEN DESCRIPTION FUNCTION RANGE DEFAULT SETTING USER SETTING
Pilot Low
Setpoint 200˚C
Low setpoint for pilot
thermocouple.
When the Pilot temperature rises above
this setpoint, the status contacts will
close and the ame light will come on.
0 to 1350˚C
(32 to 2462˚F)
200˚C
(392˚F)
Pilot High
Setpoint 600˚C
High setpoint for pilot
thermocouple.
When the pilot temperature is above
this setpoint and the Spark Mode is
set to “Spark Only <PHI” the system
will stop sparking. The “Pilot Timeout”
timer will start counting down when
the pilot temperature drops below this
setpoint.
0 to 1350˚C
(32 to 2462˚F)
600˚C
(1,112˚F)
Hold to reset history.
+

13
2Control & Programming
2.4.2 (MENU 2) History Continued...
ON SCREEN DESCRIPTION FUNCTION RANGE DEFAULT SETTING USER SETTING
ESDs = x Displays the total number of
ESDs
This number will increment any time a
fault causes the system to shutdown.
0 to 1000 0
HPR ESDs = x Displays the total number of
High Pressure ESDs
This number will increment any time
the system is shutdown due to High
Pressure contact opening.
0 to 1000 0
LPR ESDs = x Displays the total number of Low
Pressure ESDs
This number will increment any time
the system is shutdown due to Low
Pressure contact opening.
0 to 1000 0
LVL ESDs = x Displays the total number of
Level ESDs
This number will increment any time
the system is shutdown due to Level
contact opening.
0 to 1000 0
Open TC = x Displays the total number of
Thermocouple ESDs
This number will increment any time
the system is shutdown due to a ther-
mocouple fault.
0 to 1000 0
TERMCRD = x Displays the total number of
Terminal Card ESDs
This number will increment any time
the system is shutdown due to a fault
from the Terminal Card.
0 to 1000 0
Sys ERR = x Displays the total number of
System Error ESDs
This number will increment any time
the system is shutdown due to a com-
munication failure between the Door
and Terminal Cards.
0 to 1000 0
Logging Event Log This is a log of recent events. Press
OK to enter the log and use the up and
down keys to navigate through the log.
Press OK again to exit.
To clear the history and log press and
hold Up, Down, OK and Menu for 5
seconds
N/A N/A

14 2Control & Programming
2.4.3 (MENU 3) System Info
No adjustments are available in the System Info menu; the items are display only.
ON SCREEN DESCRIPTION FUNCTION RANGE DEFAULT SETTING USER SETTING
4-20mA Output
x%
Current status of the
4-20mA Output
0% = 4mA
100% = 20mA
N/A N/A
Ambient
Temp xC (xF)
Displays the ambient
temperature
This is the ambient temperature
sampled on the board at the point
where the thermocouples connect and
is used for cold junction compensation
of the thermocouples
-55˚C to 65˚C
(-70˚F to 150˚F)
N/A
System
Voltage
xx.x V
Displays the voltage applied to
the system
Measures the input voltage to the system. 8V to 35V N/A
Commission
Date:
01-JAN-2010
Date that the system was
commissioned (if entered by
user)
Data entry is done in menu 4. DD-MON-
YYYY
01-JAN-2010
Location: Displays the installed location of
the system (if entered by user)
Data entry is done in menu 4. N/A N/A
CONTROL
STATE IDLE
Shows the current state of the
rmware control system
Used in troubleshooting. N/A N/A

15
2Control & Programming
This menu always is password protected. The password is Cannot be accessed while BMS is running.
2.4.4 (MENU 4) System Setup
ON SCREEN DESCRIPTION FUNCTION RANGE DEFAULT SETTING USER SETTING
Auto Mode =
OFF
Enables unit to recover from a
power cycle, low pressure or
high voltage event.
ON : Remain in auto mode after and re-
start after a power cycle, low pressure,
low voltage or high voltage event.
OFF : Unit will switch to manual mode
and shutdown after a power cycle, low
pressure, low voltage or high voltage
event.
ON or OFF Off
Level Restart Enables the unit to recover from
a Level event.
ON : Remain in auto mode after and
restart after a Level event.
OFF : Unit will switch to manual mode
and shutdown after a Level event.
ON or OFF OFF
Pilot Timeout
2 minutes
Flame Fail Timer. Adjusts the time between the pilot
temperature dropping below the high
setpoint and shutdown.
2 to 120
minutes
2 minutes
Spark Mode
Spark Only <
PHI
Sets Spark Mode Spark Only < PHI :
The systme will spark any time the
temperature drops below the pilot high
setpoint and the system is in Auto
mode.
Always Sparking :
When the system is in Auto mode it
will spark continually in a set pattern of
2 seconds on and 8 seconds off.
Spark Only
< PHI,
Always
Sparking
Spark Only < PHI
Alarm Type
No Alm when OFF
Status contact operation. Alarm When OFF :
The status contacts will open when
the unit is remote stopped.
No Alarm When OFF :
The status contacts will remain closed
when the unit is remote stopped.
Alarm
When Off
or
No Alm
When OFF
No Alm When
OFF

16 2Control & Programming
2.4.4 (MENU 4) System Setup Continued...
ON SCREEN DESCRIPTION FUNCTION RANGE DEFAULT SETTING USER SETTING
Password = OFF Password - when ON Menu
1, 2 and 3 become password
protected.
NOTE: Menu 4, 5 and 6 are
always password protected.
ON = Menu 1,2,3 access restricted
OFF = Menu 1.2.3 access open
The Level 1 password is
ON or OFF OFF
Display
Always ON
Sleep Mode for the Display. Allows the Display to turn off after
10 min to save power.
Always ON/
OFF after
10 min
Always ON
Pilot Solenoid
PWM 60%
Enables the Low Power mode for
the Pilot solenoid.
Indicates the percentage of ON time
for the solenoid drive circuits. 20% is
the lowest power setting.
OFF, 80%,
60%, 40%,
20%
60%
Main Solenoid
PWM 60%
Enables the Low Power mode for
the Main solenoid
Indicates the percentage of ON time
for the solenoid drive circuits. 20% is
the lowest power setting.
OFF, 80%,
60%, 40%,
20%
60%
System
Voltage =24V
Congures the expected input
voltage for the system
Used by the system to determine the
over and under voltage lockout points.
At 12V the valid input range is 9.5V to
17V. At 24V the valid input range is
19V to 34V.
12V or 24V 24V
Temp Display
= Celsius
Congures the temperature
units used by the system
All display temperatures will be
converted to the chosen unit.
Fahrenheit
or Celsius
Celsius
Commission
Date:
01-JAN-2010
Date that the system was
commissioned
This is a user modied parameter. DD-MON-
YYYY
01-JAN-2010
Commission
Loc:
Displays the installed location
of the system
This is a user modied parameter. N/A
Restore Factory
Defaults = NO
Restore all settings to the
factory default
All parameters will be reset to the
default settings.
YES or NO NO
Table of contents
Other ProFire Control Panel manuals
Popular Control Panel manuals by other brands
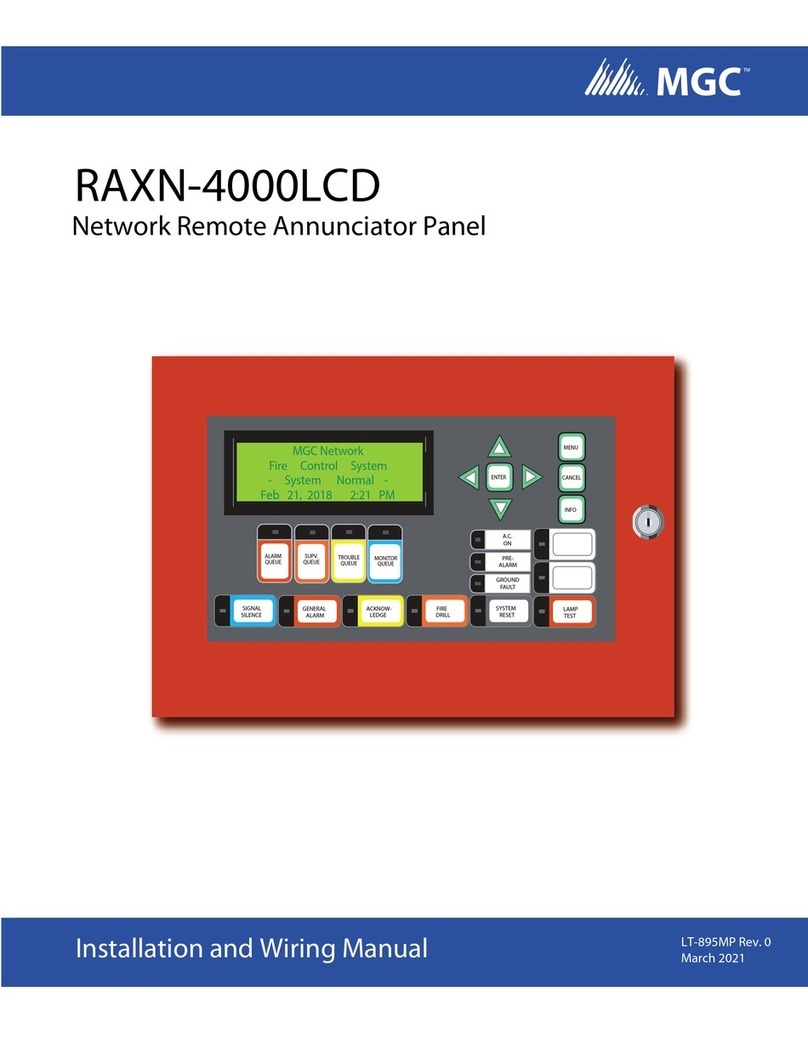
MGC
MGC RAXN-4000LCD Installation and wiring manual
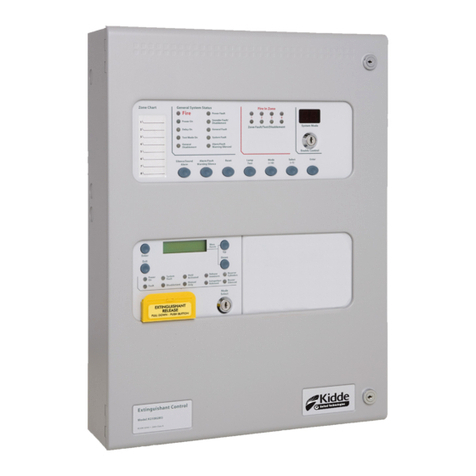
Kidde
Kidde 23911-K087 (4+1) Operation and maintenance manual
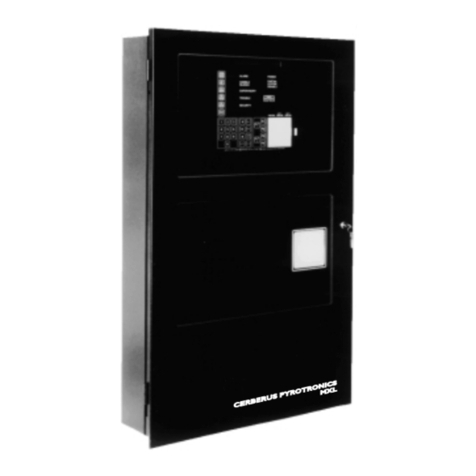
Siemens
Siemens Cerberus PYROTRONICS MXL Operation, installation, and maintenance manual
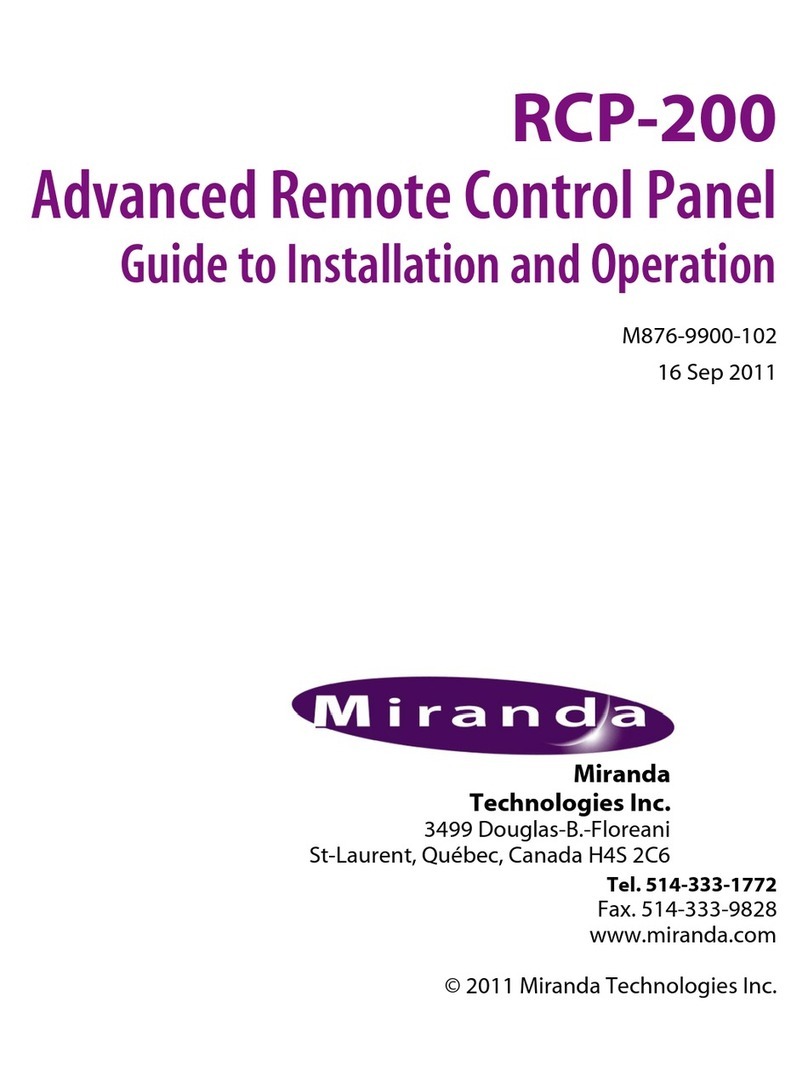
Miranda
Miranda RCP-200 Guide to installation and operation
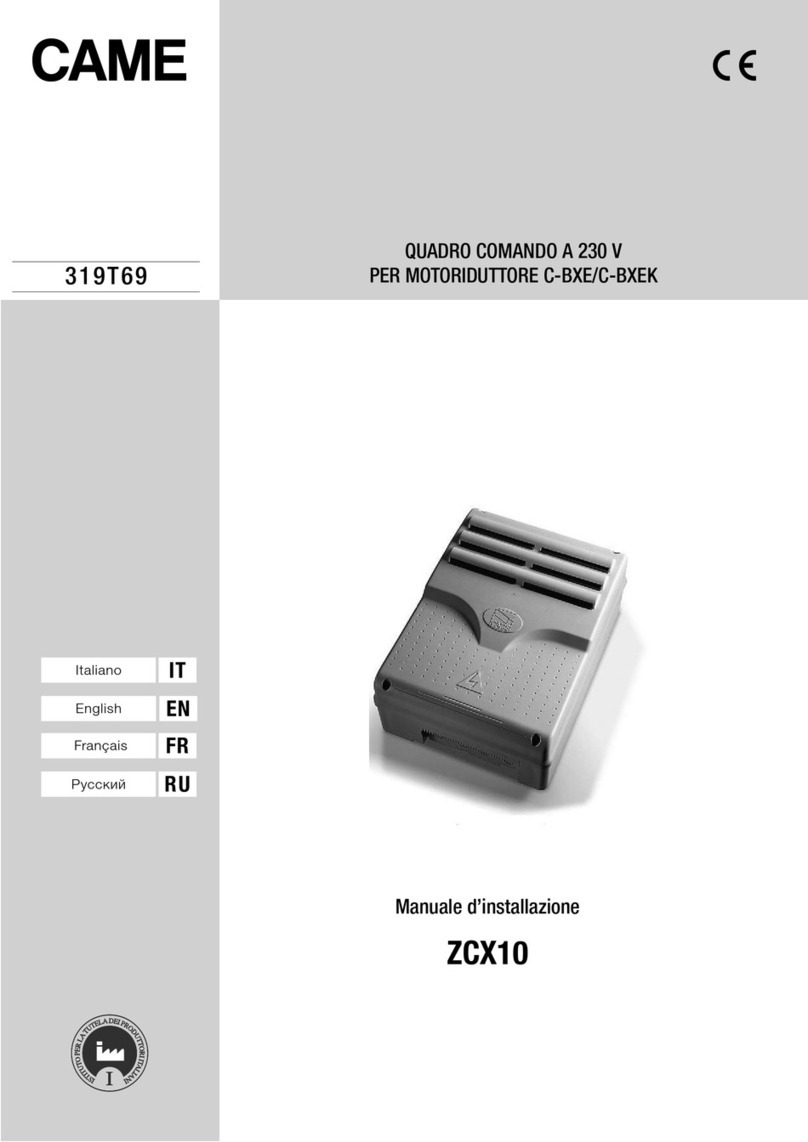
CAME
CAME ZCX10 installation manual
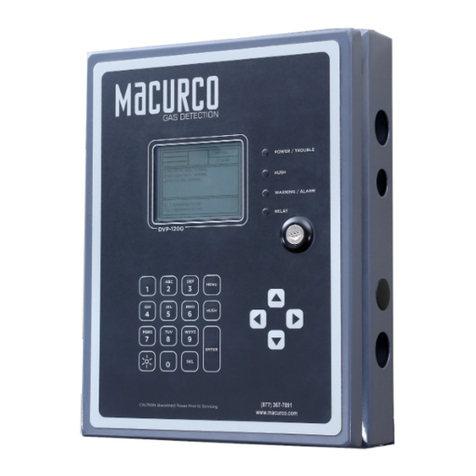
Macurco
Macurco DVP-1200 manual